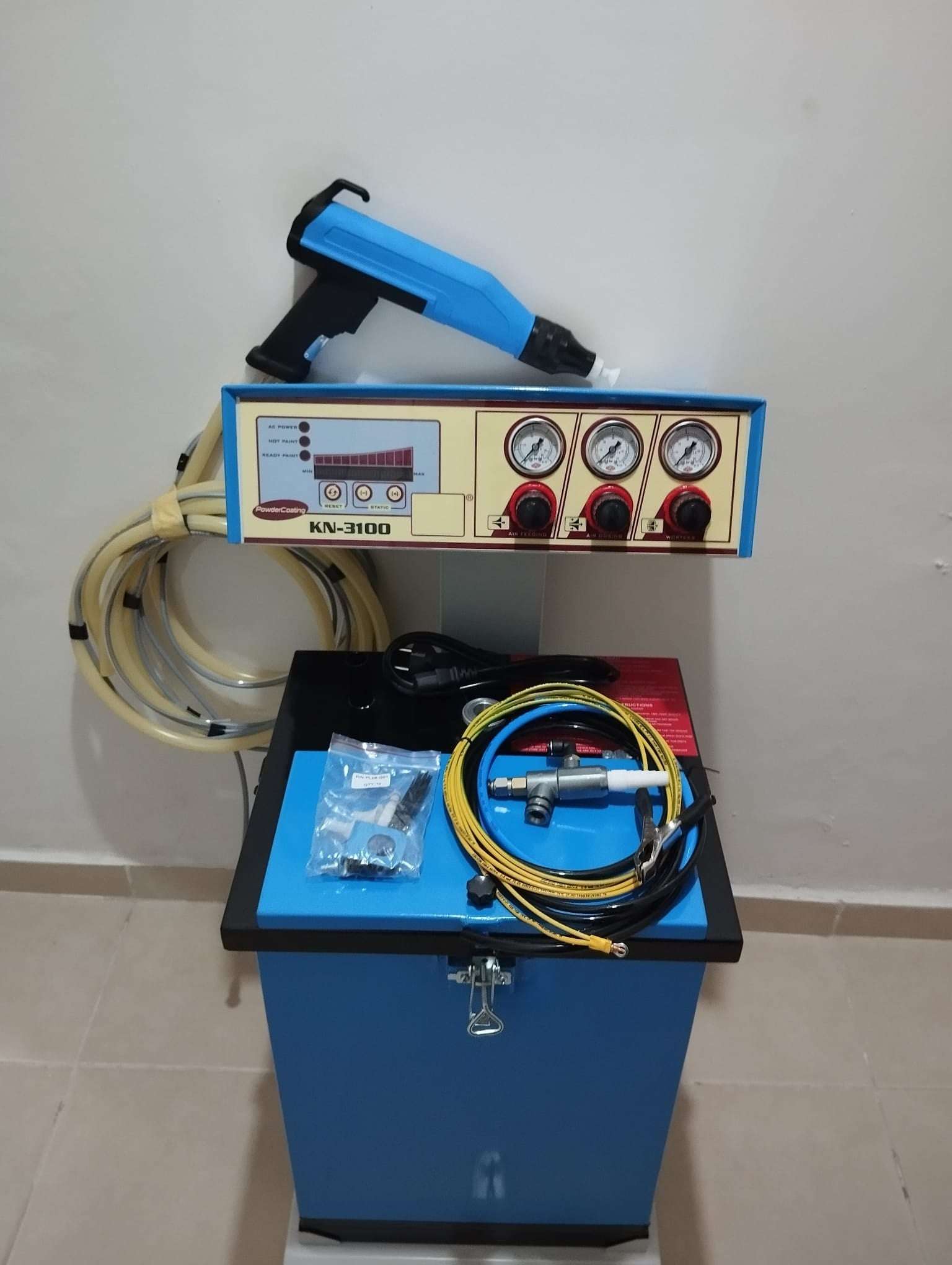
Le pistolet de poudrage est un outil utilisé dans de nombreuses industries, notamment l’automobile, l’aérospatiale, et la fabrication de meubles, pour appliquer des revêtements en poudre sur diverses surfaces. Cette méthode de revêtement est devenue de plus en plus populaire en raison de ses nombreux avantages par rapport aux méthodes traditionnelles telles que la peinture liquide.
Le principe de fonctionnement du pistolet de poudrage est relativement simple mais efficace. Il utilise de l’air comprimé pour projeter de manière électrostatique de fines particules de poudre sur la surface à revêtir. La poudre est chargée électriquement à l’aide d’un champ électrostatique, ce qui lui permet d’adhérer uniformément à la surface, même dans les zones difficiles d’accès. Une fois que la poudre est appliquée, la pièce est cuite dans un four pour polymériser le revêtement, créant ainsi une finition durable et résistante.
Les pistolets de poudrage sont disponibles dans une variété de modèles et de tailles pour s’adapter aux besoins spécifiques de chaque application. Ils peuvent être manuels ou automatiques, avec différentes configurations de buses et de réglages de débit d’air pour obtenir le meilleur résultat possible. De plus, les avancées technologiques ont permis le développement de pistolets de poudrage équipés de systèmes de contrôle avancés, tels que des écrans tactiles et des programmes de réglage automatique, pour une utilisation plus facile et plus précise.
Les avantages du pistolet de poudrage sont nombreux. Tout d’abord, il offre une couverture plus uniforme que la peinture liquide, réduisant ainsi les retouches et les reprises. De plus, il produit moins de déchets car la poudre non utilisée peut être récupérée et réutilisée, ce qui en fait une option plus écologique. De plus, le revêtement en poudre est plus résistant aux rayures, aux produits chimiques et à la corrosion que la peinture liquide, prolongeant ainsi la durée de vie de la pièce revêtue.
En conclusion, le pistolet de poudrage est un outil polyvalent et efficace pour l’application de revêtements en poudre dans une variété d’industries. Grâce à sa simplicité d’utilisation, à sa couverture uniforme et à sa durabilité accrue, il est devenu le choix préféré pour de nombreuses applications de revêtement.
Pistolet de Poudrage
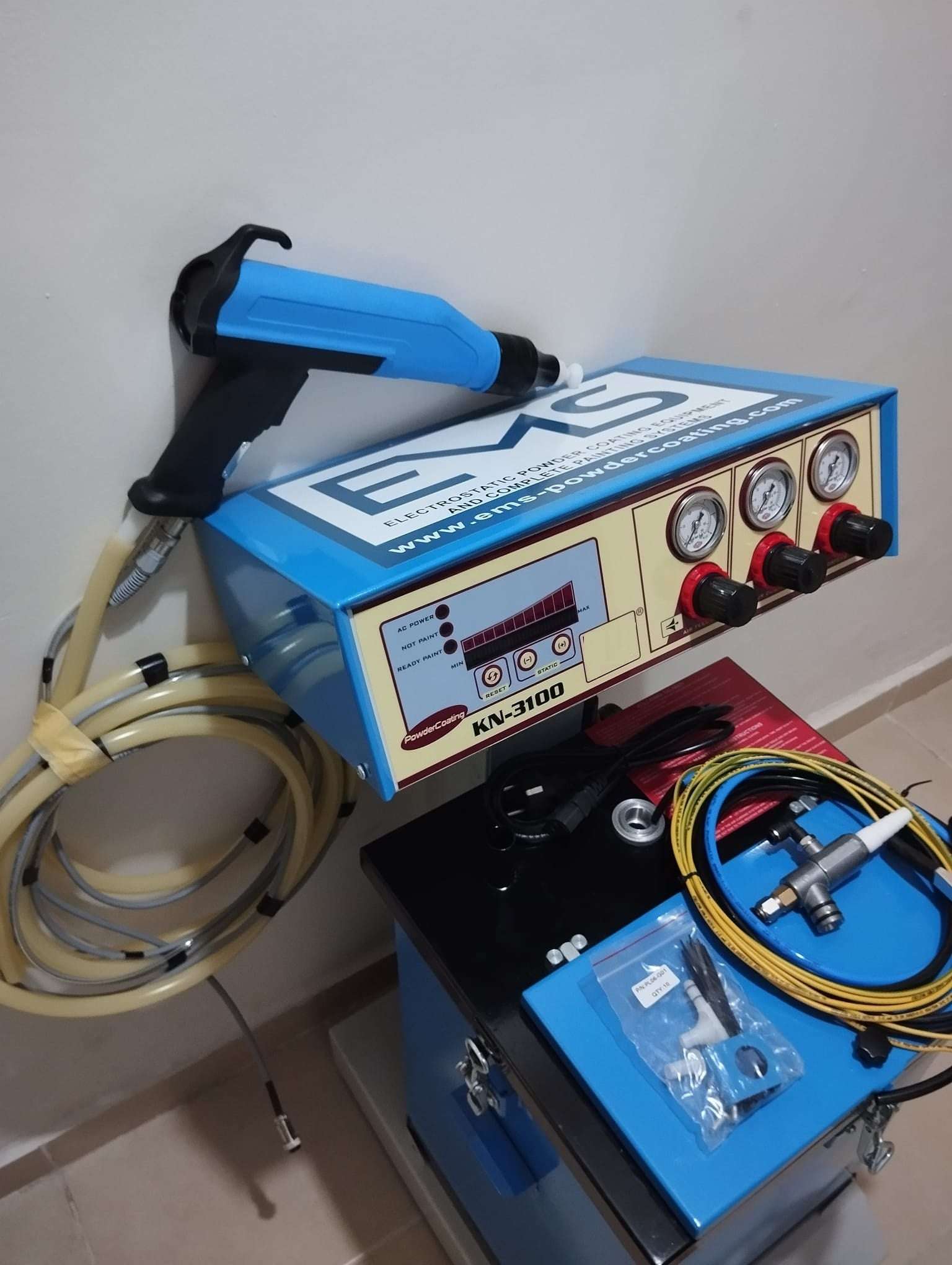
Le revêtement en poudre est une méthode de protection et de décoration des surfaces métalliques largement utilisée dans diverses industries telles que l’automobile, l’électroménager, le mobilier, et bien d’autres encore. Cette technique consiste à appliquer une fine couche de poudre de résine thermoplastique ou thermodurcissable sur la surface à revêtir.
Le processus de revêtement en poudre commence par la préparation de la pièce à traiter, incluant le nettoyage et parfois le traitement de surface pour assurer une adhérence optimale du revêtement. Ensuite, la poudre est projetée sur la surface à l’aide d’un pistolet de poudrage, où elle est électrostatiquement chargée pour adhérer uniformément à la pièce. Cette étape permet d’obtenir une couche de poudre homogène, même dans les creux et les recoins difficiles d’accès.
Une fois la poudre appliquée, la pièce est transférée dans un four où elle est soumise à une température élevée, généralement entre 150°C et 200°C selon le type de poudre utilisé. Ce processus de cuisson permet à la poudre de fondre et de se polymériser, formant ainsi un revêtement durable et résistant aux rayures, aux chocs, et aux produits chimiques.
Les avantages du revêtement en poudre sont nombreux. Il offre une excellente adhérence, une couverture uniforme, et une finition de haute qualité. De plus, il est écologique car il ne contient pas de solvants volatils et permet une récupération efficace des excès de poudre. Enfin, les pièces revêtues en poudre sont durables et nécessitent peu d’entretien, ce qui en fait un choix idéal pour de nombreuses applications industrielles et commerciales.
Application électrostatique
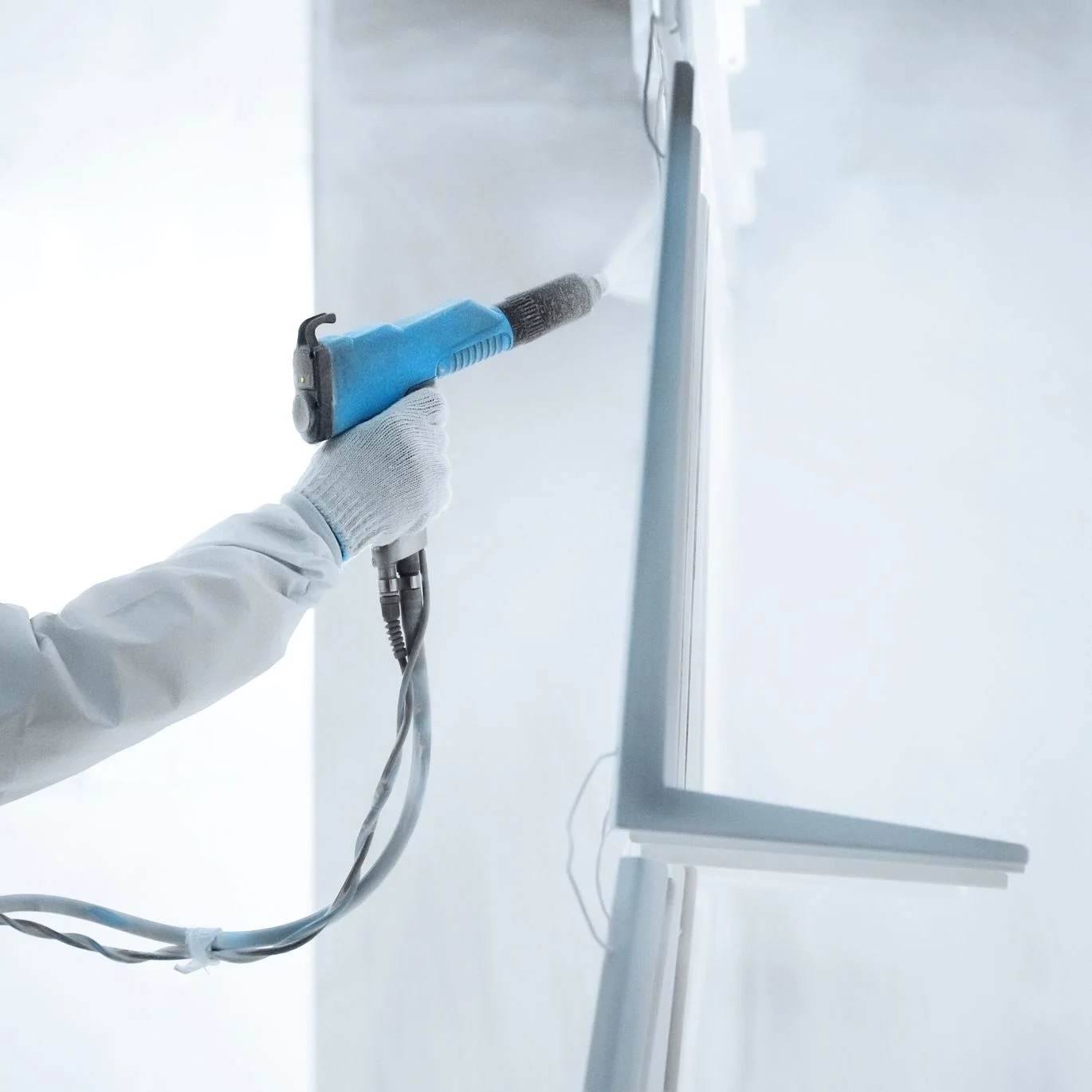
L’application électrostatique est une technique utilisée dans le processus de revêtement en poudre pour garantir une distribution uniforme de la poudre sur la surface à revêtir. Cette méthode exploite les propriétés électriques de la poudre et de la surface pour créer un champ électrostatique qui attire la poudre vers la pièce à revêtir.
Le principe de l’application électrostatique repose sur la charge électrique des particules de poudre et de la surface à revêtir. Les particules de poudre sont chargées électriquement à l’aide d’un pistolet de poudrage équipé d’un dispositif de charge, tel qu’un système de corona ou de triboélectrique. Lorsque la poudre est projetée vers la surface, elle est attirée par la pièce en raison de la différence de potentiel électrique entre les particules chargées et la surface neutre.
Cette attraction électrostatique permet une adhérence efficace de la poudre sur la surface, même dans les zones difficiles d’accès ou les recoins. De plus, elle favorise une distribution uniforme de la poudre, ce qui garantit une couverture homogène et une finition de haute qualité.
L’application électrostatique offre plusieurs avantages par rapport aux méthodes de revêtement traditionnelles. Elle permet une utilisation plus efficace de la poudre, réduisant ainsi les pertes et les coûts de production. De plus, elle offre une meilleure adhérence et une finition plus uniforme, ce qui réduit les retouches et les reprises. Enfin, elle est écologique car elle minimise les émissions de solvants et les déchets associés aux méthodes de revêtement liquide.
En conclusion, l’application électrostatique est une technique essentielle dans le processus de revêtement en poudre, offrant une distribution uniforme de la poudre et une finition de haute qualité tout en réduisant les coûts et les impacts environnementaux.
Surface à revêtir
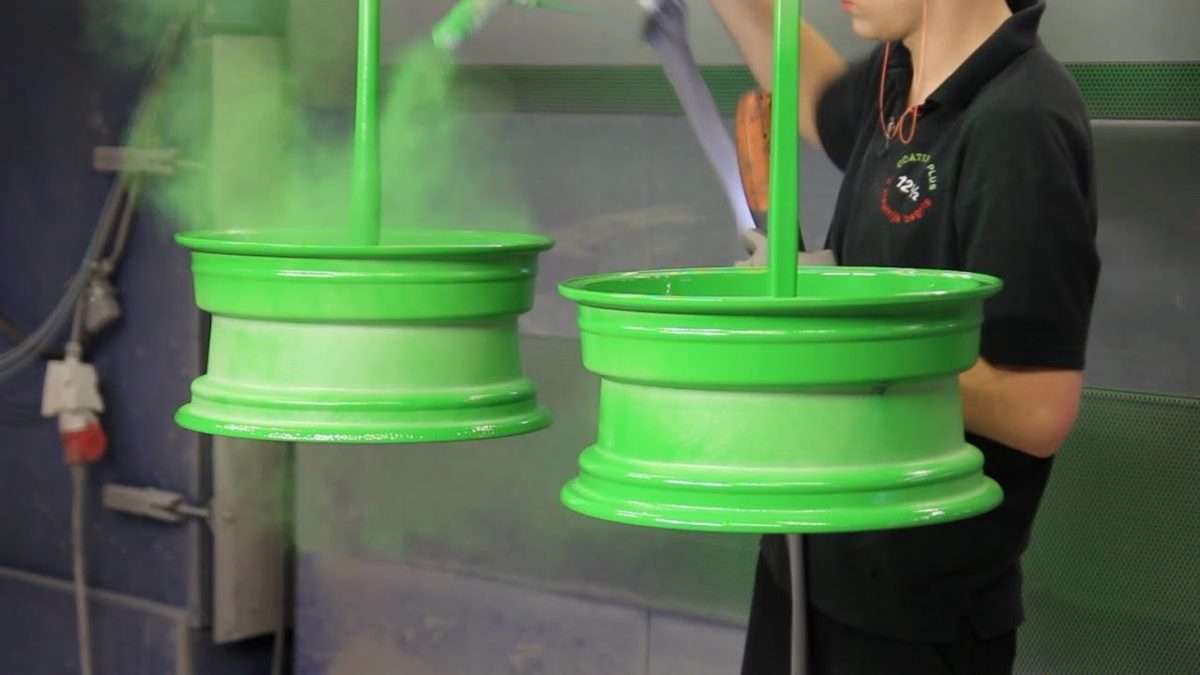
La surface à revêtir est la partie d’une pièce ou d’un objet qui est destinée à recevoir un revêtement protecteur ou décoratif, tel que le revêtement en poudre. La qualité de la surface à revêtir est essentielle pour assurer une adhérence optimale du revêtement et garantir la durabilité et la performance du produit final.
Avant d’appliquer un revêtement, il est crucial de préparer soigneusement la surface à revêtir. Cette préparation peut inclure plusieurs étapes, telles que le nettoyage pour éliminer la saleté, la graisse et d’autres contaminants, ainsi que le traitement de surface pour améliorer l’adhérence du revêtement. Le type de traitement de surface nécessaire dépend du matériau de la pièce, de l’environnement dans lequel elle sera utilisée, et des exigences spécifiques du revêtement.
Une fois que la surface est propre et préparée, elle est prête à recevoir le revêtement. Dans le cas du revêtement en poudre, la poudre est projetée sur la surface à l’aide d’un pistolet de poudrage, où elle est électrostatiquement chargée pour adhérer uniformément à la pièce. Cette étape nécessite une attention particulière pour garantir une couverture complète et uniforme de la surface, y compris dans les zones difficiles d’accès.
Une fois que le revêtement en poudre est appliqué, la pièce est transférée dans un four où elle est cuite à une température élevée pour polymériser le revêtement. Cette étape permet de durcir le revêtement et de le rendre résistant aux rayures, aux chocs, et aux produits chimiques, assurant ainsi sa durabilité et sa longévité.
En conclusion, la préparation de la surface à revêtir est une étape critique dans le processus de revêtement en poudre, influençant directement la qualité et la performance du revêtement final. En veillant à une préparation minutieuse de la surface, il est possible d’obtenir des résultats optimaux en termes d’adhérence, de durabilité et d’esthétique du revêtement.
Air comprimé
L’air comprimé est un élément essentiel dans le fonctionnement des pistolets de poudrage utilisés dans le processus de revêtement en poudre. Il s’agit d’air ambiant qui a été comprimé dans un réservoir à haute pression à l’aide d’un compresseur d’air. L’air comprimé est ensuite utilisé pour propulser la poudre du pistolet de poudrage vers la surface à revêtir.
Dans le contexte du pistolet de poudrage, l’air comprimé est utilisé pour créer un flux d’air à haute vitesse qui transporte les particules de poudre depuis le réservoir de poudre jusqu’à la buse du pistolet. Ce flux d’air permet de projeter la poudre sur la surface à revêtir avec précision et uniformité, assurant ainsi une couverture homogène et une finition de haute qualité.
La pression de l’air comprimé utilisé dans le pistolet de poudrage peut être ajustée en fonction des besoins spécifiques de l’application. Une pression plus élevée peut être nécessaire pour projeter la poudre sur de grandes surfaces ou à une distance plus importante, tandis qu’une pression plus faible peut être utilisée pour des travaux de précision ou pour des revêtements délicats.
Outre son utilisation dans les pistolets de poudrage, l’air comprimé est également largement utilisé dans de nombreuses autres applications industrielles, telles que l’alimentation des outils pneumatiques, le contrôle des processus de production, et la manipulation des matériaux en vrac.
En conclusion, l’air comprimé est un élément indispensable dans le processus de revêtement en poudre, permettant de propulser la poudre sur la surface à revêtir avec précision et uniformité. Grâce à sa polyvalence et à sa fiabilité, l’air comprimé est largement utilisé dans de nombreuses applications industrielles pour répondre à divers besoins en matière de propulsion et de contrôle.
Particules fines
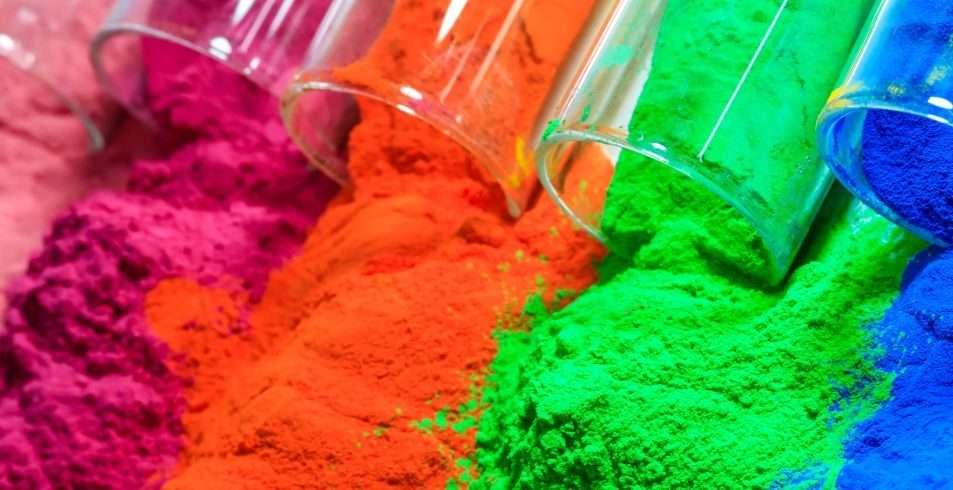
Les particules fines font référence aux grains de poudre utilisés dans le processus de revêtement en poudre. Ces particules sont généralement constituées de matériaux tels que des résines thermoplastiques ou thermodurcissables, des pigments et des additifs, qui sont broyés en une poudre fine et uniforme pour assurer une application précise et homogène sur la surface à revêtir.
La taille des particules fines est un facteur crucial dans le processus de revêtement en poudre, car elle influence directement la qualité et la performance du revêtement final. Des particules trop grosses peuvent entraîner une application inégale ou des irrégularités de surface, tandis que des particules trop fines peuvent causer des problèmes d’adhérence ou de dispersion.
Pour garantir une application efficace et uniforme de la poudre, il est important de choisir des particules fines de qualité et de contrôler leur taille et leur distribution. Les technologies de fabrication modernes permettent de produire des particules fines avec une taille de grain précise et une distribution étroite, garantissant ainsi une application homogène et une finition de haute qualité.
En outre, les particules fines peuvent également être soumises à divers traitements de surface pour améliorer leurs propriétés, telles que l’adhérence, la résistance à la corrosion, et la stabilité thermique. Ces traitements peuvent inclure des revêtements spéciaux, des agents de couplage, ou des modifications chimiques pour répondre aux exigences spécifiques de chaque application.
En conclusion, les particules fines jouent un rôle crucial dans le processus de revêtement en poudre, en influençant directement la qualité et la performance du revêtement final. Grâce à des techniques de fabrication avancées et à des contrôles de qualité rigoureux, il est possible d’obtenir des particules fines de haute qualité pour des applications de revêtement diverses et exigeantes.
Adhérence uniforme
L’adhérence uniforme fait référence à la capacité d’un revêtement, tel que celui appliqué avec un pistolet de poudrage, à se fixer de manière cohérente et homogène sur la surface à revêtir. Une adhérence uniforme est essentielle pour garantir la durabilité et la qualité esthétique du revêtement final.
Dans le contexte du pistolet de poudrage, l’adhérence uniforme est obtenue grâce à plusieurs facteurs, notamment la préparation minutieuse de la surface à revêtir, le contrôle précis de la dispersion de la poudre, et l’utilisation d’une application électrostatique pour assurer une répartition équilibrée de la poudre sur toute la surface.
La préparation de la surface à revêtir est une étape cruciale pour garantir une adhérence optimale du revêtement. Cela peut inclure le nettoyage de la surface pour éliminer les contaminants tels que la saleté, la graisse et la rouille, ainsi que le traitement de surface pour créer une texture appropriée et favoriser l’adhérence du revêtement.
Une fois la surface préparée, la poudre est appliquée à l’aide du pistolet de poudrage, où elle est électrostatiquement chargée pour adhérer à la surface. L’application électrostatique permet une répartition uniforme de la poudre sur toute la surface, y compris dans les zones difficiles d’accès ou les recoins, assurant ainsi une adhérence uniforme du revêtement.
Une fois le revêtement appliqué, la pièce est cuite dans un four pour polymériser le revêtement, assurant ainsi sa durabilité et sa résistance aux rayures, aux chocs, et aux produits chimiques. Ce processus de cuisson permet également de renforcer l’adhérence du revêtement à la surface, garantissant ainsi sa stabilité et sa longévité dans des conditions d’utilisation variées.
En conclusion, l’adhérence uniforme est un élément essentiel dans le processus de revêtement en poudre, garantissant la durabilité et la qualité esthétique du revêtement final. Grâce à une préparation minutieuse de la surface, à une application précise de la poudre, et à une cuisson adéquate du revêtement, il est possible d’obtenir une adhérence optimale sur une variété de surfaces et de substrats.
Cuire au four

La cuisson au four est une étape critique du processus de revêtement en poudre, nécessaire pour polymériser le revêtement appliqué sur la surface à revêtir. Cette étape permet de durcir le revêtement et de lui conférer les propriétés physiques et chimiques nécessaires pour assurer sa durabilité et sa résistance aux agressions extérieures.
Après avoir été appliqué sur la surface à l’aide d’un pistolet de poudrage, le revêtement en poudre est transféré dans un four spécialement conçu à cet effet. Le four est chauffé à une température prédéterminée, généralement comprise entre 150°C et 200°C, en fonction du type de poudre utilisé et des spécifications du revêtement.
Pendant la cuisson au four, le revêtement en poudre fond et se polymérise, formant ainsi une couche solide et durable sur la surface à revêtir. Ce processus de polymérisation permet au revêtement de se lier chimiquement à la surface, assurant ainsi une adhérence optimale et une protection efficace contre les rayures, les chocs, et les produits chimiques.
La durée de cuisson au four dépend de divers facteurs, tels que l’épaisseur du revêtement, le type de poudre utilisé, et les exigences spécifiques de l’application. Une fois la cuisson terminée, le revêtement est refroidi à température ambiante avant d’être inspecté et testé pour s’assurer de sa conformité aux normes de qualité et de performance.
En conclusion, la cuisson au four est une étape essentielle du processus de revêtement en poudre, permettant de durcir le revêtement et de lui conférer les propriétés nécessaires pour assurer sa durabilité et sa résistance aux agressions extérieures. Grâce à ce processus de cuisson contrôlé, il est possible d’obtenir des revêtements de haute qualité et de garantir leur performance dans une variété d’applications industrielles et commerciales.
Finition durable
La finition durable est un objectif clé dans le processus de revêtement en poudre. Elle fait référence à la capacité du revêtement à maintenir ses propriétés esthétiques et protectrices sur une longue période, même dans des conditions d’utilisation et d’exposition difficiles.
Le revêtement en poudre est réputé pour offrir une finition durable par rapport à d’autres méthodes de revêtement. Une fois appliqué et polymérisé, le revêtement forme une couche solide et uniforme sur la surface à revêtir. Cette couche est résistante aux rayures, aux chocs, à la corrosion, et aux produits chimiques, offrant ainsi une protection fiable contre les agressions extérieures.
La durabilité du revêtement en poudre est attribuable à plusieurs facteurs. Tout d’abord, le processus de cuisson au four permet une polymérisation complète du revêtement, assurant ainsi une liaison chimique forte avec la surface à revêtir. En outre, la sélection de poudres de haute qualité, associée à des techniques d’application précises, garantit une couverture uniforme et une adhérence optimale du revêtement.
En raison de sa durabilité, le revêtement en poudre est largement utilisé dans des environnements exigeants tels que l’industrie automobile, l’industrie de la construction, et l’industrie maritime. Il offre une protection durable contre la rouille, la corrosion, les intempéries, et autres agressions, prolongeant ainsi la durée de vie des pièces revêtues et réduisant les coûts d’entretien et de remplacement.
En conclusion, la finition durable est l’un des principaux avantages du revêtement en poudre, offrant une protection fiable et une esthétique de haute qualité dans une variété d’applications industrielles et commerciales. Grâce à sa résistance aux agressions extérieures et à sa longévité, le revêtement en poudre est un choix privilégié pour les projets nécessitant une performance optimale sur le long terme.
Pulvérisateur de poudre :
Un pulvérisateur de poudre est un équipement utilisé dans le processus de revêtement par poudre pour appliquer uniformément une fine couche de poudre sur la surface d’un matériau. Cet appareil est essentiel pour garantir une distribution homogène de la poudre et obtenir un revêtement de haute qualité.
Le pulvérisateur de poudre est généralement équipé d’un pistolet de pulvérisation, d’un système de charge électrostatique et d’un système de distribution de poudre. Le pistolet de pulvérisation est responsable de la projection de la poudre sur la surface à revêtir, tandis que le système de charge électrostatique charge les particules de poudre pour assurer leur adhérence à la surface. Le système de distribution de poudre contrôle le débit de poudre et garantit une application uniforme sur toute la surface.
Il existe différents types de pulvérisateurs de poudre, notamment les pulvérisateurs manuels, automatiques et robotisés. Les pulvérisateurs manuels sont souvent utilisés pour les petites productions ou les travaux de retouche, tandis que les pulvérisateurs automatiques et robotisés sont préférés pour les applications à grande échelle ou les opérations nécessitant une haute précision.
En résumé, le pulvérisateur de poudre est un élément essentiel dans le processus de revêtement par poudre, permettant une application précise et uniforme de la poudre sur la surface des pièces à revêtir. Avec ses différentes caractéristiques et configurations, il offre une solution efficace pour obtenir des revêtements de poudre de haute qualité dans une variété d’applications industrielles et commerciales.
Pulvérisateur de poudre :
Un pulvérisateur de poudre est un équipement utilisé dans le domaine du revêtement par poudre pour appliquer de manière uniforme une fine couche de poudre sur la surface d’un matériau. Il constitue un élément essentiel du processus de revêtement par poudre, permettant d’obtenir des finitions de haute qualité sur une variété de substrats.
Ce dispositif se compose généralement d’un pistolet de pulvérisation, d’un système de distribution de poudre, et souvent d’un système de charge électrostatique. Le pistolet de pulvérisation est responsable de projeter la poudre sur la surface à revêtir, tandis que le système de distribution de poudre contrôle le débit et la répartition de la poudre. Le système de charge électrostatique charge les particules de poudre, ce qui favorise leur adhérence à la surface du matériau, assurant ainsi une couverture uniforme et une bonne adhérence du revêtement.
Les pulvérisateurs de poudre peuvent être manuels, automatiques ou robotisés, en fonction des besoins spécifiques de l’application et du volume de production. Les pulvérisateurs manuels sont souvent utilisés pour les petites séries ou les retouches, tandis que les pulvérisateurs automatiques et robotisés sont plus adaptés pour les grandes productions nécessitant une haute précision et une productivité élevée.
En résumé, le pulvérisateur de poudre est un équipement indispensable dans le processus de revêtement par poudre, permettant d’appliquer efficacement et uniformément des revêtements de poudre sur une variété de substrats. Avec ses différentes configurations et fonctionnalités, il offre une solution polyvalente pour répondre aux besoins de revêtement dans diverses industries telles que l’automobile, l’aérospatiale, l’électronique, et bien d’autres encore.
L’application de poudre est une étape cruciale du processus de revêtement par poudre, où une fine couche de poudre est appliquée de manière uniforme sur la surface d’un matériau à revêtir. Cette étape vise à créer un revêtement protecteur, esthétique ou fonctionnel, selon les besoins spécifiques de l’application.
Le processus d’application de poudre peut être réalisé de différentes manières, en fonction des caractéristiques du matériau à revêtir, de la taille et de la forme des pièces, ainsi que des exigences de performance du revêtement. Les principales méthodes d’application de poudre comprennent :
- Pulvérisation électrostatique : Cette méthode utilise un pistolet de pulvérisation équipé d’une électrode chargée électriquement pour charger les particules de poudre. Les particules chargées sont attirées par la surface opposée chargée, assurant une couverture uniforme et une adhérence maximale du revêtement.
- Pulvérisation par air comprimé : Dans cette méthode, la poudre est pulvérisée à travers un pistolet de pulvérisation alimenté par de l’air comprimé. Cette technique est souvent utilisée pour les applications de revêtement de grande taille ou lorsque des motifs de pulvérisation complexes sont nécessaires.
- Pulvérisation par gravité : Cette méthode implique l’utilisation d’un pistolet de pulvérisation où la poudre est alimentée par gravité depuis un réservoir situé au-dessus du pistolet. Cette technique est adaptée aux petites applications et aux pièces de forme complexe.
- Pulvérisation par électrode rotative : Cette méthode utilise une électrode rotative pour charger les particules de poudre pendant leur passage à travers un champ électrique. Cela permet une application efficace de la poudre sur des surfaces tridimensionnelles et complexes.
- Pulvérisation par projection à jet : Cette méthode utilise un jet d’air comprimé pour projeter la poudre sur la surface à revêtir. Cette technique est souvent utilisée pour les applications de retouche ou pour les pièces de petite taille.
Quelle que soit la méthode utilisée, l’application de poudre nécessite une préparation minutieuse de la surface, un contrôle précis des paramètres de pulvérisation et une attention particulière à la qualité du revêtement. Un processus bien maîtrisé garantit des résultats de revêtement de haute qualité, offrant une protection efficace contre la corrosion, l’usure, les rayures et autres agressions environnementales, tout en assurant une esthétique optimale selon les besoins de l’application.
Un système de pulvérisation de poudre est un ensemble d’équipements et de composants utilisés dans le processus de revêtement par poudre pour appliquer uniformément une fine couche de poudre sur la surface d’un matériau à revêtir. Ce système est conçu pour garantir une application efficace et précise de la poudre, tout en assurant une adhérence optimale du revêtement et des résultats de haute qualité.
Les composants principaux d’un système de pulvérisation de poudre comprennent :
- Pistolet de pulvérisation : C’est l’élément principal du système, responsable de la projection de la poudre sur la surface à revêtir. Le pistolet de pulvérisation peut être équipé d’une électrode chargée électriquement pour la pulvérisation électrostatique ou fonctionner avec de l’air comprimé pour la pulvérisation par air.
- Unité de commande : Cette unité contrôle les paramètres de pulvérisation tels que la pression de l’air, le débit de poudre, la tension électrostatique, et d’autres paramètres pour garantir une application précise et uniforme de la poudre.
- Système de distribution de poudre : Ce système assure un flux régulier de poudre vers le pistolet de pulvérisation. Il peut inclure un réservoir de poudre, un système de transport de poudre (tel qu’une vis sans fin ou un système de venturi), et des dispositifs de régulation du débit.
- Système de filtration : Il s’agit d’un élément crucial du système qui élimine les impuretés de la poudre pour garantir une application de revêtement de haute qualité et éviter les obstructions dans le système de pulvérisation.
- Système de récupération de poudre : Ce système collecte l’excès de poudre qui n’a pas adhéré à la surface et le recycle pour une utilisation ultérieure, réduisant ainsi les déchets et les coûts de matières premières.
- Système de contrôle de l’environnement : Pour les applications en cabine ou en ligne, un système de contrôle de l’environnement peut être nécessaire pour assurer des conditions optimales telles que la température, l’humidité et la ventilation.
En résumé, un système de pulvérisation de poudre est une solution complète conçue pour faciliter le processus d’application de revêtement par poudre. En combinant des pistolets de pulvérisation de haute qualité, des unités de commande précises et des systèmes de distribution efficaces, il permet d’obtenir des revêtements de poudre de haute qualité dans une variété d’applications industrielles et commerciales.
Le revêtement en poudre est une méthode de revêtement de surface largement utilisée dans diverses industries pour appliquer un revêtement protecteur, esthétique ou fonctionnel sur une variété de substrats. Ce processus implique l’application d’une fine couche de poudre sur la surface d’un matériau, suivie de la fusion et de la polymérisation de la poudre pour former un revêtement durable et résistant.
Voici les étapes principales du processus de revêtement en poudre :
- Préparation de la surface : Avant l’application de la poudre, la surface du matériau à revêtir doit être soigneusement préparée pour garantir une adhérence optimale du revêtement. Cela peut impliquer le nettoyage de la surface pour éliminer les contaminants, la dégraissage pour enlever les résidus d’huile et de graisse, et le traitement de la surface pour améliorer l’adhérence du revêtement.
- Application de la poudre : Une fois que la surface est préparée, la poudre est appliquée sur la surface à l’aide d’un pulvérisateur de poudre. La poudre peut être projetée sur la surface par pulvérisation électrostatique, pulvérisation par air comprimé, pulvérisation par gravité ou d’autres méthodes, en fonction des besoins spécifiques de l’application.
- Fusion et polymérisation : Après l’application de la poudre, les pièces revêtues sont placées dans un four où la poudre est fondue et polymérisée pour former un revêtement solide et uniforme. Pendant ce processus, la poudre fondue s’écoule et se fusionne pour former un film continu sur la surface du matériau, assurant une adhérence maximale et une couverture uniforme.
- Refroidissement et durcissement : Une fois que la poudre a fondu et polymérisé, les pièces revêtues sont refroidies à température ambiante pour durcir le revêtement. Ce processus peut prendre quelques minutes à quelques heures, selon le type de poudre et les conditions de cuisson.
- Contrôle de la qualité : Enfin, les pièces revêtues sont soumises à un contrôle de qualité pour vérifier l’épaisseur du revêtement, l’adhérence, la résistance à la corrosion, et d’autres propriétés pour s’assurer que les revêtements répondent aux normes de qualité requises.
Le revêtement en poudre offre de nombreux avantages par rapport à d’autres méthodes de revêtement, notamment une excellente adhérence, une résistance élevée à la corrosion et à l’abrasion, une finition esthétique, et une capacité à couvrir des surfaces complexes de manière uniforme. Il est largement utilisé dans des applications telles que l’automobile, l’aérospatiale, l’électronique, les meubles, et bien d’autres encore, pour une protection durable et une finition de haute qualité.
L’équipement de pulvérisation de poudre est un ensemble d’outils, de dispositifs et de machines utilisés dans le processus de revêtement par poudre pour appliquer efficacement une fine couche de poudre sur la surface d’un matériau à revêtir. Cet équipement est essentiel pour assurer une application uniforme, précise et efficace de la poudre, garantissant ainsi des résultats de revêtement de haute qualité.
Voici les principaux composants de l’équipement de pulvérisation de poudre :
- Pistolet de pulvérisation : C’est l’élément central de l’équipement de pulvérisation de poudre, responsable de la projection de la poudre sur la surface à revêtir. Les pistolets de pulvérisation peuvent être équipés de diverses technologies, notamment la pulvérisation électrostatique, la pulvérisation par air comprimé, la pulvérisation par gravité, etc.
- Unité de commande : Cette unité contrôle les paramètres de pulvérisation tels que la pression de l’air, le débit de poudre, la tension électrostatique, etc. Elle permet de régler et d’optimiser les paramètres de pulvérisation en fonction des besoins spécifiques de l’application.
- Système de distribution de poudre : Ce système transporte la poudre depuis le réservoir de stockage jusqu’au pistolet de pulvérisation. Il peut comprendre des composants tels qu’une vis sans fin, un système de transport pneumatique ou un système de tamisage pour garantir un flux régulier de poudre.
- Système de filtration : Ce système élimine les impuretés de la poudre pour éviter les obstructions dans le système de pulvérisation et garantir une application de revêtement de haute qualité.
- Système de récupération de poudre : Ce système collecte l’excès de poudre qui n’a pas adhéré à la surface et le recycle pour une utilisation ultérieure, réduisant ainsi les déchets et les coûts de matières premières.
- Four de cuisson : Après l’application de la poudre, les pièces revêtues sont placées dans un four où la poudre est fondue et polymérisée pour former un revêtement solide et uniforme.
En résumé, l’équipement de pulvérisation de poudre est un ensemble complet de dispositifs conçus pour faciliter le processus d’application de revêtement par poudre. En combinant des pistolets de pulvérisation de haute qualité, des unités de commande précises et des systèmes de distribution efficaces, il permet d’obtenir des revêtements de poudre de haute qualité dans une variété d’applications industrielles et commerciales.
Technologie de pulvérisation de poudre
La technologie de pulvérisation de poudre est un domaine essentiel dans le processus de revêtement par poudre, visant à appliquer de manière uniforme et efficace une fine couche de poudre sur la surface d’un matériau à revêtir. Cette technologie comprend diverses méthodes et techniques pour assurer une application précise et une adhérence maximale du revêtement de poudre.
Voici quelques-unes des principales technologies de pulvérisation de poudre utilisées dans l’industrie :
- Pulvérisation électrostatique : Cette technologie utilise des pistolets de pulvérisation équipés d’une électrode chargée électriquement pour charger les particules de poudre pendant leur projection. Les particules chargées sont attirées par la surface opposée chargée, assurant une couverture uniforme et une adhérence maximale du revêtement.
- Pulvérisation par air comprimé : Dans cette méthode, la poudre est pulvérisée à travers un pistolet de pulvérisation alimenté par de l’air comprimé. Cette technique est souvent utilisée pour les applications de revêtement de grande taille ou lorsque des motifs de pulvérisation complexes sont nécessaires.
- Pulvérisation par gravité : Cette méthode implique l’utilisation d’un pistolet de pulvérisation où la poudre est alimentée par gravité depuis un réservoir situé au-dessus du pistolet. Cette technique est adaptée aux petites applications et aux pièces de forme complexe.
- Pulvérisation par électrode rotative : Cette technologie utilise une électrode rotative pour charger les particules de poudre pendant leur passage à travers un champ électrique. Cela permet une application efficace de la poudre sur des surfaces tridimensionnelles et complexes.
- Pulvérisation par projection à jet : Cette méthode utilise un jet d’air comprimé pour projeter la poudre sur la surface à revêtir. Cette technique est souvent utilisée pour les applications de retouche ou pour les pièces de petite taille.
Chaque technologie de pulvérisation de poudre présente des avantages et des inconvénients en fonction des besoins spécifiques de l’application, de la taille des pièces à revêtir, du type de poudre utilisée, et d’autres facteurs. En choisissant la technologie appropriée et en maîtrisant les paramètres de pulvérisation, il est possible d’obtenir des revêtements de poudre de haute qualité offrant une protection efficace et une esthétique optimale dans une variété d’applications industrielles et commerciales.
L’application de revêtement en poudre est une étape cruciale du processus de revêtement par poudre, qui consiste à appliquer uniformément une fine couche de poudre sur la surface d’un matériau à revêtir. Cette étape vise à créer un revêtement protecteur, esthétique ou fonctionnel, selon les besoins spécifiques de l’application.
Voici les étapes principales du processus d’application de revêtement en poudre :
- Préparation de la surface : Avant l’application de la poudre, la surface du matériau à revêtir doit être soigneusement préparée pour garantir une adhérence optimale du revêtement. Cela peut impliquer le nettoyage de la surface pour éliminer les contaminants, la dégraissage pour enlever les résidus d’huile et de graisse, et le traitement de la surface pour améliorer l’adhérence du revêtement.
- Application de la poudre : Une fois que la surface est préparée, la poudre est appliquée sur la surface à l’aide d’un pistolet de pulvérisation de poudre. La poudre peut être projetée sur la surface par pulvérisation électrostatique, pulvérisation par air comprimé, pulvérisation par gravité ou d’autres méthodes, en fonction des besoins spécifiques de l’application.
- Fusion et polymérisation : Après l’application de la poudre, les pièces revêtues sont placées dans un four où la poudre est fondue et polymérisée pour former un revêtement solide et uniforme. Pendant ce processus, la poudre fondue s’écoule et se fusionne pour former un film continu sur la surface du matériau, assurant une adhérence maximale et une couverture uniforme.
- Refroidissement et durcissement : Une fois que la poudre a fondu et polymérisé, les pièces revêties sont refroidies à température ambiante pour durcir le revêtement. Ce processus peut prendre quelques minutes à quelques heures, selon le type de poudre et les conditions de cuisson.
- Contrôle de la qualité : Enfin, les pièces revêtues sont soumises à un contrôle de qualité pour vérifier l’épaisseur du revêtement, l’adhérence, la résistance à la corrosion, et d’autres propriétés pour s’assurer que les revêtements répondent aux normes de qualité requises.
En résumé, l’application de revêtement en poudre est une étape essentielle du processus de revêtement par poudre, qui nécessite une préparation minutieuse de la surface, un contrôle précis des paramètres de pulvérisation et une attention particulière à la qualité du revêtement. Un processus bien maîtrisé garantit des résultats de revêtement de haute qualité, offrant une protection efficace contre la corrosion, l’usure, les rayures et autres agressions environnementales, tout en assurant une esthétique optimale selon les besoins de l’application.
Poudrage
Le poudrage est le processus consistant à appliquer une fine couche de poudre sur la surface d’un matériau à revêtir. Cette technique est largement utilisée dans l’industrie pour appliquer des revêtements protecteurs, décoratifs ou fonctionnels sur une variété de substrats.
Voici les principales étapes du processus de poudrage :
- Préparation de la surface : Avant le poudrage, la surface du matériau à revêtir doit être soigneusement nettoyée et préparée pour garantir une adhérence optimale du revêtement. Cela peut impliquer le nettoyage de la surface pour éliminer les contaminants, la dégraissage pour enlever les résidus d’huile et de graisse, et le traitement de la surface pour améliorer l’adhérence du revêtement.
- Application de la poudre : Une fois que la surface est préparée, la poudre est appliquée sur la surface à l’aide d’un dispositif de pulvérisation de poudre. La poudre peut être projetée sur la surface par pulvérisation électrostatique, pulvérisation par air comprimé, pulvérisation par gravité ou d’autres méthodes, en fonction des besoins spécifiques de l’application.
- Fusion et polymérisation : Après l’application de la poudre, les pièces revêtues sont placées dans un four où la poudre est fondue et polymérisée pour former un revêtement solide et uniforme. Pendant ce processus, la poudre fondue s’écoule et se fusionne pour former un film continu sur la surface du matériau, assurant une adhérence maximale et une couverture uniforme.
- Refroidissement et durcissement : Une fois que la poudre a fondu et polymérisé, les pièces revêtues sont refroidies à température ambiante pour durcir le revêtement. Ce processus peut prendre quelques minutes à quelques heures, selon le type de poudre et les conditions de cuisson.
- Contrôle de la qualité : Enfin, les pièces revêtues sont soumises à un contrôle de qualité pour vérifier l’épaisseur du revêtement, l’adhérence, la résistance à la corrosion, et d’autres propriétés pour s’assurer que les revêtements répondent aux normes de qualité requises.
Le poudrage est une méthode de revêtement efficace et polyvalente, offrant de nombreux avantages par rapport à d’autres méthodes de revêtement, notamment une excellente adhérence, une résistance élevée à la corrosion et à l’abrasion, une finition esthétique, et une capacité à couvrir des surfaces complexes de manière uniforme. Il est largement utilisé dans des applications telles que l’automobile, l’aérospatiale, l’électronique, les meubles, et bien d’autres encore, pour une protection durable et une finition de haute qualité.
Le pulvérisateur électrostatique est un outil essentiel dans le processus de pulvérisation de poudre, utilisé pour appliquer une fine couche de poudre sur la surface d’un matériau à revêtir. Contrairement aux méthodes de pulvérisation conventionnelles, un pulvérisateur électrostatique utilise la technologie électrostatique pour charger les particules de poudre pendant leur projection, ce qui permet d’obtenir une adhérence maximale du revêtement et une couverture uniforme de la surface.
Voici comment fonctionne un pulvérisateur électrostatique :
- Chargement des particules : Dans un pulvérisateur électrostatique, les particules de poudre sont chargées électriquement lorsqu’elles passent à travers le pistolet de pulvérisation. Une électrode chargée génère un champ électrique autour du pistolet, ce qui induit une charge électrique sur les particules de poudre pendant leur projection.
- Attraction électrostatique : Une fois chargées, les particules de poudre sont attirées par la surface opposée, qui est mise à la terre ou chargée de manière opposée. Cette attraction électrostatique garantit une adhérence maximale des particules de poudre sur la surface, même sur des surfaces complexes ou difficiles à atteindre.
- Application de la poudre : Le pulvérisateur électrostatique est utilisé pour projeter la poudre chargée sur la surface à revêtir. La poudre est pulvérisée sous forme de fine brume qui se dépose uniformément sur la surface, assurant une couverture complète et une adhérence optimale du revêtement.
- Contrôle des paramètres : Les paramètres du pulvérisateur électrostatique, tels que la pression d’air, le débit de poudre et la tension électrostatique, peuvent être ajustés pour optimiser les performances du pulvérisateur en fonction des besoins spécifiques de l’application.
Les pulvérisateurs électrostatiques sont largement utilisés dans diverses industries pour appliquer des revêtements en poudre sur une variété de substrats, y compris les métaux, le plastique, le bois et le verre. Leur capacité à produire des revêtements de haute qualité avec une adhérence maximale en fait un outil essentiel pour les applications où la durabilité, la résistance à la corrosion et l’esthétique sont des priorités.
Un système de revêtement en poudre est un ensemble complet d’équipements, de dispositifs et de procédés utilisés pour appliquer des revêtements en poudre sur divers substrats. Ces systèmes sont conçus pour assurer une application efficace, uniforme et de haute qualité des revêtements en poudre, tout en répondant aux exigences spécifiques de chaque application.
Voici les principaux composants d’un système de revêtement en poudre :
- Équipement de pulvérisation de poudre : Cet équipement comprend des pistolets de pulvérisation de poudre, des unités de commande, des systèmes de distribution de poudre, des systèmes de filtration et des systèmes de récupération de poudre. Ces composants permettent d’appliquer la poudre de manière uniforme et efficace sur la surface à revêtir.
- Four de cuisson : Une fois la poudre appliquée, les pièces revêtues sont placées dans un four où la poudre est fondue et polymérisée pour former un revêtement solide et durable. Les fours de cuisson peuvent être électriques, au gaz ou à infrarouge, selon les besoins spécifiques de l’application.
- Système de prétraitement : Avant l’application de la poudre, la surface du substrat peut nécessiter un traitement préalable pour garantir une adhérence optimale du revêtement. Les systèmes de prétraitement peuvent inclure le dégraissage, le sablage, le dérochage, la conversion de surface et d’autres processus de préparation de surface.
- Contrôle de la qualité : Les systèmes de revêtement en poudre sont équipés de dispositifs de contrôle de la qualité pour surveiller et évaluer divers paramètres du processus de revêtement, tels que l’épaisseur du revêtement, l’adhérence, la couleur, la brillance et la résistance à la corrosion.
- Équipement de manipulation : Pour manipuler et déplacer les pièces à travers le processus de revêtement, les systèmes de revêtement en poudre peuvent être équipés d’équipements de manutention tels que des convoyeurs, des chariots et des systèmes de levage.
En résumé, un système de revêtement en poudre est un ensemble complexe d’équipements et de processus conçus pour appliquer des revêtements en poudre de manière efficace, uniforme et de haute qualité. En combinant des équipements de pulvérisation de poudre de pointe, des fours de cuisson de précision et des systèmes de contrôle de la qualité, ces systèmes permettent d’obtenir des revêtements en poudre offrant une excellente protection contre la corrosion, l’usure et les intempéries, tout en offrant une finition esthétique et durable.
Le revêtement électrostatique est une méthode de revêtement utilisée dans diverses industries pour appliquer une fine couche de revêtement sur des surfaces métalliques, plastiques et autres substrats. Cette technique tire parti des propriétés électrostatiques pour assurer une application uniforme et efficace du revêtement, offrant ainsi une protection contre la corrosion, une résistance à l’usure et une esthétique améliorée.
Voici comment fonctionne le processus de revêtement électrostatique :
- Chargement des particules : Dans le processus de revêtement électrostatique, les particules de revêtement sont chargées électriquement lorsqu’elles passent à travers un pistolet de pulvérisation. Une électrode chargée génère un champ électrique autour du pistolet, ce qui induit une charge électrique sur les particules de revêtement pendant leur projection.
- Attraction électrostatique : Une fois chargées, les particules de revêtement sont attirées par la surface opposée, qui est mise à la terre ou chargée de manière opposée. Cette attraction électrostatique garantit une adhérence maximale des particules de revêtement sur la surface, même sur des surfaces complexes ou difficiles à atteindre.
- Application du revêtement : Le pistolet de pulvérisation est utilisé pour projeter les particules de revêtement chargées sur la surface à revêtir. Les particules sont attirées par la surface opposée chargée électriquement, assurant ainsi une couverture uniforme et complète de la surface.
- Fusion et polymérisation : Une fois que le revêtement est appliqué, les pièces revêtues sont placées dans un four où le revêtement est fondu et polymérisé pour former un film solide et uniforme. Pendant ce processus, le revêtement fond et se fusionne pour former une couche protectrice durable sur la surface du substrat.
- Refroidissement et durcissement : Une fois que le revêtement a fondu et polymérisé, les pièces revêtues sont refroidies à température ambiante pour durcir le revêtement. Ce processus peut prendre quelques minutes à quelques heures, selon le type de revêtement et les conditions de cuisson.
Le revêtement électrostatique est largement utilisé dans diverses industries, y compris l’automobile, l’aérospatiale, l’électronique et les équipements industriels, en raison de ses nombreux avantages, notamment une excellente adhérence, une distribution uniforme du revêtement, une efficacité de production élevée et une réduction des déchets. En optimisant les paramètres du processus de revêtement électrostatique et en utilisant des équipements de pointe, il est possible d’obtenir des revêtements de haute qualité offrant une protection efficace et une esthétique supérieure.
Pistolet de pulvérisation de poudre
Un pistolet de pulvérisation de poudre est un outil essentiel dans le processus de revêtement par poudre, utilisé pour projeter la poudre de revêtement sur la surface d’un matériau à revêtir. Cet équipement joue un rôle crucial dans l’application uniforme et précise du revêtement en poudre, garantissant ainsi des résultats de haute qualité.
Voici comment fonctionne un pistolet de pulvérisation de poudre :
- Alimentation en poudre : Le pistolet est connecté à un système d’alimentation en poudre qui fournit un flux contrôlé de poudre de revêtement vers le pistolet. La poudre peut être contenue dans un réservoir intégré au pistolet ou être alimentée à partir d’un réservoir externe via un système de tuyauterie.
- Charge électrostatique : Certaines conceptions de pistolets de pulvérisation de poudre utilisent la technologie électrostatique pour charger les particules de poudre pendant leur projection. Une électrode chargée génère un champ électrique autour du pistolet, ce qui induit une charge électrique sur les particules de poudre pendant leur projection. Cela permet d’obtenir une adhérence maximale du revêtement sur la surface à revêtir.
- Projection de la poudre : La poudre est projetée sur la surface à revêtir à travers une buse de pulvérisation située à l’extrémité du pistolet. La pression de l’air comprimé ou d’un gaz inerte est utilisée pour propulser la poudre à travers la buse, créant ainsi un nuage de poudre fine qui se dépose uniformément sur la surface.
- Réglages de pulvérisation : Les pistolets de pulvérisation de poudre sont équipés de divers réglages permettant de contrôler le débit de poudre, la forme du jet, la pression de l’air et d’autres paramètres de pulvérisation. Ces réglages peuvent être ajustés pour optimiser les performances du pistolet en fonction des besoins spécifiques de l’application.
- Maintenance et nettoyage : Pour assurer des performances optimales, les pistolets de pulvérisation de poudre doivent être entretenus régulièrement et nettoyés après chaque utilisation. Cela implique généralement le démontage du pistolet, le nettoyage des composants internes et externes, et la vérification de l’état général du pistolet.
En résumé, un pistolet de pulvérisation de poudre est un équipement essentiel dans le processus de revêtement par poudre, offrant une application précise et uniforme du revêtement en poudre sur une variété de substrats. En choisissant un pistolet de haute qualité et en suivant les bonnes pratiques d’utilisation et d’entretien, il est possible d’obtenir des résultats de revêtement de haute qualité, offrant une protection durable et une finition esthétique selon les besoins de l’application.
Application électrostatique
L’application électrostatique est une méthode de revêtement utilisée dans diverses industries pour appliquer des revêtements liquides ou en poudre sur une surface. Cette technique tire parti des propriétés électrostatiques pour garantir une application uniforme, efficace et précise du revêtement, offrant ainsi des avantages significatifs en termes de qualité et de performance du revêtement.
Voici comment fonctionne le processus d’application électrostatique :
- Chargement électrostatique : Dans le processus d’application électrostatique, le revêtement est chargé électriquement avant son application sur la surface à revêtir. Les particules de revêtement sont chargées positivement ou négativement à l’aide d’un champ électrique généré par un dispositif de charge électrostatique.
- Attraction électrostatique : Une fois chargées électriquement, les particules de revêtement sont projetées vers la surface à revêtir à travers un pistolet de pulvérisation ou un système d’application. En raison de leur charge électrique, les particules sont attirées par la surface opposée, qui est mise à la terre ou chargée de manière opposée, assurant ainsi une adhérence maximale du revêtement sur la surface.
- Application du revêtement : Le revêtement chargé est appliqué sur la surface à revêtir à l’aide d’un pistolet de pulvérisation, d’un électrostatiseur ou d’autres dispositifs d’application. Les particules de revêtement sont projetées sur la surface dans un flux contrôlé, assurant une couverture uniforme et complète de la surface.
- Fusion et polymérisation (le cas échéant) : Après l’application du revêtement, celui-ci peut nécessiter une étape de fusion et de polymérisation pour former un film solide et durable. Cette étape est généralement effectuée dans un four de cuisson où le revêtement est chauffé à une température spécifique pour fusionner les particules et former un film continu sur la surface.
- Contrôle de la qualité : Une fois le revêtement appliqué et durci, des contrôles de qualité sont effectués pour vérifier l’épaisseur du revêtement, l’adhérence, la résistance à la corrosion et d’autres propriétés du revêtement. Cela garantit que le revêtement répond aux normes de qualité requises et offre la protection et les performances souhaitées.
L’application électrostatique est largement utilisée dans des industries telles que l’automobile, l’aérospatiale, l’électronique, le mobilier et d’autres secteurs où des revêtements de haute qualité sont essentiels. En utilisant cette méthode, il est possible d’obtenir des revêtements uniformes, durables et esthétiques, offrant une protection efficace contre la corrosion, l’abrasion et d’autres formes de dégradation.
Revêtement par poudrage
Le revêtement par poudrage est une méthode de revêtement utilisée dans diverses industries pour appliquer un revêtement en poudre sur une surface. Cette technique est largement utilisée en raison de ses nombreux avantages, notamment une application uniforme, une adhérence supérieure, une efficacité de production élevée et une protection durable contre la corrosion, les rayures et d’autres dommages.
Voici comment fonctionne le processus de revêtement par poudrage :
- Préparation de la surface : Avant l’application de la poudre, la surface à revêtir doit être préparée en conséquence. Cela peut inclure le nettoyage, le dégraissage, le sablage et d’autres méthodes de préparation de surface pour garantir une adhérence optimale du revêtement.
- Application de la poudre : La poudre de revêtement est chargée dans un pistolet de pulvérisation de poudre, où elle est pulvérisée sous forme de fine brume sur la surface à revêtir. La poudre est projetée à travers une buse de pulvérisation à l’aide d’air comprimé ou d’un gaz inerte, créant ainsi un nuage de poudre qui se dépose uniformément sur la surface.
- Cuisson du revêtement : Une fois la poudre appliquée, les pièces revêtues sont placées dans un four de cuisson où le revêtement est fondu et polymérisé. Pendant ce processus, la poudre fond et se lie pour former un film solide et uniforme sur la surface du substrat.
- Refroidissement et durcissement : Une fois que le revêtement a fondu et polymérisé, les pièces revêtues sont refroidies à température ambiante pour durcir le revêtement. Ce processus peut prendre quelques minutes à quelques heures, selon le type de revêtement et les conditions de cuisson.
- Contrôle de la qualité : Une fois le revêtement durci, des contrôles de qualité sont effectués pour vérifier l’épaisseur du revêtement, l’adhérence, la couleur, la brillance et d’autres propriétés du revêtement. Cela garantit que le revêtement répond aux normes de qualité requises et offre la protection et les performances souhaitées.
Le revêtement par poudrage est largement utilisé dans des industries telles que l’automobile, l’aérospatiale, le mobilier, l’électronique et d’autres secteurs où des revêtements de haute qualité et durables sont nécessaires. En utilisant cette méthode, il est possible d’obtenir des revêtements uniformes et esthétiques offrant une excellente protection contre la corrosion, l’usure et d’autres dommages.
La pulvérisation de poudre est un processus utilisé dans l’industrie du revêtement pour appliquer un revêtement en poudre sur une surface. Cette méthode est largement utilisée en raison de sa simplicité, de son efficacité et de sa capacité à produire des revêtements de haute qualité avec une adhérence supérieure et une résistance accrue à la corrosion et à l’usure.
Voici comment fonctionne le processus de pulvérisation de poudre :
- Préparation de la surface : Avant d’appliquer la poudre, la surface à revêtir doit être préparée en conséquence. Cela peut inclure le nettoyage, le dégraissage et le traitement de surface pour éliminer les contaminants et assurer une adhérence optimale du revêtement.
- Application de la poudre : La poudre de revêtement est chargée dans un pistolet de pulvérisation de poudre, où elle est pulvérisée sous forme de fine brume sur la surface à revêtir. La poudre est projetée à travers une buse de pulvérisation à l’aide d’air comprimé ou d’un gaz inerte, créant ainsi un nuage de poudre qui se dépose uniformément sur la surface.
- Adhérence électrostatique : Dans certains cas, la poudre de revêtement est chargée électrostatiquement avant son application. Cela se fait en utilisant un champ électrique pour charger les particules de poudre, ce qui les rend attirées par la surface opposée, assurant ainsi une adhérence maximale du revêtement sur la surface.
- Cuisson du revêtement : Une fois la poudre appliquée, les pièces revêtues sont placées dans un four de cuisson où le revêtement est fondu et polymérisé. Pendant ce processus, la poudre fond et se lie pour former un film solide et uniforme sur la surface du substrat.
- Refroidissement et durcissement : Une fois que le revêtement a fondu et polymérisé, les pièces revêtues sont refroidies à température ambiante pour durcir le revêtement. Ce processus peut prendre quelques minutes à quelques heures, selon le type de revêtement et les conditions de cuisson.
- Contrôle de la qualité : Une fois le revêtement durci, des contrôles de qualité sont effectués pour vérifier l’épaisseur du revêtement, l’adhérence, la couleur, la brillance et d’autres propriétés du revêtement. Cela garantit que le revêtement répond aux normes de qualité requises et offre la protection et les performances souhaitées.
La pulvérisation de poudre est largement utilisée dans des industries telles que l’automobile, l’aérospatiale, le mobilier, l’électronique et d’autres secteurs où des revêtements de haute qualité et durables sont nécessaires. En utilisant cette méthode, il est possible d’obtenir des revêtements uniformes et esthétiques offrant une excellente protection contre la corrosion, l’usure et d’autres dommages.
Un système de poudrage électrostatique est un équipement utilisé dans le processus de revêtement par poudrage pour appliquer un revêtement en poudre sur une surface à l’aide de la technologie électrostatique. Ce système comprend plusieurs composants essentiels qui travaillent ensemble pour assurer une application efficace et uniforme du revêtement.
Voici les principaux composants d’un système de poudrage électrostatique :
- Pistolet de pulvérisation de poudre : Le pistolet de pulvérisation est l’élément central du système, utilisé pour projeter la poudre de revêtement sur la surface à revêtir. Il est équipé d’une buse de pulvérisation, d’un dispositif de charge électrostatique et de réglages pour contrôler le débit de poudre et d’air.
- Source d’alimentation en poudre : Le système comprend un réservoir ou une trémie qui contient la poudre de revêtement. La poudre est alimentée vers le pistolet de pulvérisation à travers un système de transport tel qu’une vis sans fin ou un système de fluidisation.
- Dispositif de charge électrostatique : Certains systèmes de poudrage électrostatique utilisent des dispositifs spéciaux pour charger électrostatiquement les particules de poudre pendant leur projection. Cela peut être réalisé à l’aide d’électrodes chargées ou d’autres méthodes de génération de champ électrique.
- Générateur haute tension : Pour charger électrostatiquement les particules de poudre, le système est équipé d’un générateur haute tension qui génère un champ électrique autour du pistolet de pulvérisation. Ce champ électrique induit une charge sur les particules de poudre, facilitant ainsi leur adhérence à la surface à revêtir.
- Système de contrôle et d’automatisation : Certains systèmes de poudrage électrostatique sont équipés de systèmes de contrôle et d’automatisation avancés pour réguler le débit de poudre, ajuster les paramètres de pulvérisation et surveiller les performances du processus de revêtement.
- Système de récupération de poudre : Après la pulvérisation, la poudre non utilisée est récupérée à l’aide d’un système de récupération de poudre. Cela peut inclure des dispositifs tels que des cabines de récupération de poudre, des cyclones et des filtres pour collecter la poudre excédentaire et la recycler pour une utilisation ultérieure.
En utilisant un système de poudrage électrostatique, il est possible d’obtenir des revêtements en poudre de haute qualité avec une adhérence supérieure, une distribution uniforme et une efficacité de production élevée. Ce système est largement utilisé dans des industries telles que l’automobile, l’aérospatiale, l’électronique et d’autres secteurs où des revêtements de haute qualité et durables sont nécessaires.
Un pistolet de peinture en poudre est un outil essentiel utilisé dans le processus de revêtement par poudrage pour appliquer un revêtement en poudre sur une surface. Ce pistolet est conçu pour pulvériser la poudre de revêtement de manière uniforme et contrôlée, assurant ainsi une couverture complète et une adhérence optimale du revêtement.
Voici les principaux composants et caractéristiques d’un pistolet de peinture en poudre :
- Buse de pulvérisation : Le pistolet est équipé d’une buse de pulvérisation spéciale qui permet de disperser la poudre de revêtement sous forme de fine brume sur la surface à revêtir. La taille et la forme de la buse peuvent être ajustées pour contrôler la distribution de la poudre et obtenir le bon motif de pulvérisation.
- Chambre de mélange : La poudre de revêtement est introduite dans la chambre de mélange du pistolet, où elle est mélangée à de l’air comprimé ou à un gaz inerte pour former un nuage de poudre. Cette chambre assure une distribution uniforme de la poudre et facilite son application sur la surface à revêtir.
- Dispositif de charge électrostatique : Certains pistolets de peinture en poudre sont équipés d’un dispositif de charge électrostatique qui charge les particules de poudre pendant leur pulvérisation. Cela améliore l’adhérence du revêtement sur la surface en créant une attraction électrostatique entre la poudre chargée et la surface opposée.
- Déclencheur et gâchette : Le pistolet est équipé d’un déclencheur et d’une gâchette qui permettent à l’opérateur de contrôler le débit de poudre et d’air pendant le processus de pulvérisation. En ajustant la pression sur la gâchette, l’opérateur peut réguler la quantité de poudre pulvérisée et obtenir le bon résultat.
- Poignée ergonomique : La poignée du pistolet est conçue pour offrir un confort optimal à l’opérateur pendant une utilisation prolongée. Elle est généralement ergonomique et dotée de revêtements antidérapants pour une prise en main sûre et confortable.
- Système de nettoyage : Après utilisation, le pistolet de peinture en poudre doit être nettoyé pour éliminer toute accumulation de poudre et maintenir ses performances. Certains modèles sont équipés de systèmes de nettoyage automatiques pour faciliter ce processus.
En utilisant un pistolet de peinture en poudre de haute qualité et correctement réglé, il est possible d’obtenir des revêtements uniformes, esthétiques et durables sur une variété de surfaces. Ces pistolets sont largement utilisés dans des industries telles que l’automobile, l’aérospatiale, le mobilier, l’électronique et d’autres secteurs où des revêtements de haute qualité sont essentiels.
Le processus de poudrage, également connu sous le nom de revêtement par poudrage, est une méthode de revêtement largement utilisée dans l’industrie pour appliquer un revêtement protecteur ou décoratif sur une variété de surfaces. Ce processus implique l’application d’une fine couche de poudre de revêtement sur la surface à l’aide d’un équipement spécifique, suivi d’une phase de cuisson pour fusionner et polymériser la poudre, formant ainsi un revêtement solide et durable.
Voici les étapes typiques du processus de poudrage :
- Préparation de la surface : Avant d’appliquer la poudre, la surface à revêtir est préparée en conséquence. Cela peut inclure le nettoyage, le dégraissage, le sablage et d’autres techniques de préparation de surface pour assurer une adhérence optimale du revêtement.
- Application de la poudre : La poudre de revêtement est chargée dans un pistolet de pulvérisation de poudre, où elle est pulvérisée sous forme de fine brume sur la surface à revêtir. La poudre est projetée à travers une buse de pulvérisation à l’aide d’air comprimé ou d’un gaz inerte, créant ainsi un nuage de poudre qui se dépose uniformément sur la surface.
- Adhérence électrostatique (optionnelle) : Dans certains cas, la poudre de revêtement est chargée électrostatiquement avant son application. Cela se fait en utilisant un générateur haute tension pour charger les particules de poudre, ce qui les rend attirées par la surface opposée, assurant ainsi une adhérence maximale du revêtement sur la surface.
- Cuisson du revêtement : Une fois la poudre appliquée, les pièces revêtues sont placées dans un four de cuisson où le revêtement est fondu et polymérisé. Pendant ce processus, la poudre fond et se lie pour former un film solide et uniforme sur la surface du substrat.
- Refroidissement et durcissement : Une fois que le revêtement a fondu et polymérisé, les pièces revêtues sont refroidies à température ambiante pour durcir le revêtement. Ce processus peut prendre quelques minutes à quelques heures, selon le type de revêtement et les conditions de cuisson.
- Contrôle de la qualité : Une fois le revêtement durci, des contrôles de qualité sont effectués pour vérifier l’épaisseur du revêtement, l’adhérence, la couleur, la brillance et d’autres propriétés du revêtement. Cela garantit que le revêtement répond aux normes de qualité requises et offre la protection et les performances souhaitées.
Le processus de poudrage est largement utilisé dans des industries telles que l’automobile, l’aérospatiale, le mobilier, l’électronique et d’autres secteurs où des revêtements de haute qualité et durables sont nécessaires. En utilisant cette méthode, il est possible d’obtenir des revêtements uniformes et esthétiques offrant une excellente protection contre la corrosion, l’usure et d’autres dommages.
Application industrielle de poudre
L’application industrielle de poudre, également appelée revêtement par poudrage, est un processus largement utilisé dans divers secteurs industriels pour appliquer des revêtements protecteurs ou décoratifs sur une variété de surfaces. Cette méthode offre de nombreux avantages par rapport aux autres méthodes de revêtement, notamment une excellente uniformité, une haute efficacité de production, une faible pollution et une durabilité accrue du revêtement.
Voici quelques-unes des applications industrielles courantes de la poudre :
- Automobile : Le revêtement par poudrage est largement utilisé dans l’industrie automobile pour protéger les pièces métalliques contre la corrosion, l’abrasion et d’autres dommages. Les composants tels que les châssis, les roues, les supports et les pièces de carrosserie peuvent être revêtus de revêtements en poudre pour améliorer leur durabilité et leur esthétique.
- Aérospatiale : Dans l’industrie aérospatiale, le revêtement par poudrage est utilisé pour protéger les composants critiques tels que les pièces de moteurs, les structures d’avions et les équipements électroniques contre les conditions environnementales extrêmes rencontrées dans l’espace et en vol.
- Mobilier : Les meubles métalliques et en bois peuvent être revêtus de revêtements en poudre pour améliorer leur résistance aux rayures, aux taches et à l’usure. Les revêtements en poudre offrent également une large gamme de couleurs et de finitions esthétiques pour répondre aux besoins des designers et des fabricants de meubles.
- Électronique : Dans l’industrie électronique, le revêtement par poudrage est utilisé pour protéger les cartes de circuits imprimés, les boîtiers métalliques et les autres composants électroniques contre l’humidité, la corrosion et les chocs électriques. Les revêtements en poudre peuvent également améliorer la dissipation thermique et la conductivité électrique des composants.
- Construction : Les structures métalliques telles que les pylônes, les ponts, les clôtures et les façades peuvent être revêtues de revêtements en poudre pour améliorer leur résistance aux intempéries, à la corrosion et à l’usure. Les revêtements en poudre offrent également une durabilité à long terme, ce qui réduit les besoins d’entretien et de maintenance.
- Équipement industriel : Les machines, les outils et les équipements industriels sont souvent revêtus de revêtements en poudre pour améliorer leur résistance à l’usure, à la corrosion et à la chaleur. Les revêtements en poudre peuvent également offrir des propriétés spécifiques telles que la conductivité électrique, la résistance aux produits chimiques et la résistance aux hautes températures.
En résumé, l’application industrielle de poudre est une méthode polyvalente et efficace pour protéger et décorer une large gamme de surfaces dans différents secteurs industriels. En utilisant cette méthode, il est possible d’obtenir des revêtements de haute qualité, durables et esthétiques, adaptés à diverses applications et environnements.
La poudre de pulvérisation est un matériau utilisé dans le processus de revêtement par poudrage pour appliquer un revêtement protecteur ou décoratif sur une variété de surfaces. Cette poudre est constituée de fines particules de résine polymère, de pigments, d’additifs et éventuellement de charges minérales, qui sont pulvérisées sur la surface à l’aide d’un pistolet de pulvérisation de poudre.
Voici quelques caractéristiques importantes de la poudre de pulvérisation :
- Composition : La poudre de pulvérisation est généralement composée d’une résine polymère qui forme la matrice du revêtement une fois fondu et durci. Cette résine peut être époxy, polyester, polyuréthane, polyéthylène, polypropylène ou d’autres types de résines en fonction des propriétés requises du revêtement. Des pigments sont également ajoutés pour donner à la poudre sa couleur et son aspect esthétique, tandis que des additifs peuvent être inclus pour améliorer les propriétés du revêtement, telles que la résistance aux UV, la résistance à la corrosion et la conductivité électrique.
- Granulométrie : La poudre de pulvérisation est disponible dans une gamme de granulométries différentes, qui déterminent la taille des particules de poudre. Une granulométrie plus fine permet d’obtenir un revêtement plus lisse et uniforme, tandis qu’une granulométrie plus grossière peut être utilisée pour des revêtements plus épais et texturés.
- Couleurs et finitions : La poudre de pulvérisation est disponible dans une large gamme de couleurs et de finitions pour répondre aux besoins esthétiques des applications spécifiques. Des pigments de différentes couleurs peuvent être mélangés pour créer des teintes personnalisées, tandis que des finitions telles que brillant, mat, métallisé, texturé et sablé peuvent être obtenues en utilisant des techniques de fabrication spéciales.
- Compatibilité : La poudre de pulvérisation doit être compatible avec le substrat sur lequel elle est appliquée, ainsi qu’avec le processus de cuisson utilisé pour polymériser le revêtement. Différents types de poudres sont disponibles pour différentes applications, y compris des poudres adaptées à des substrats métalliques, plastiques, en bois et autres.
- Adhérence : La poudre de pulvérisation doit avoir une bonne adhérence à la surface du substrat pour assurer la durabilité et la longévité du revêtement. Des propriétés d’adhérence optimales peuvent être obtenues en préparant correctement la surface avant l’application de la poudre, en utilisant des techniques de nettoyage, de dégraissage et de sablage appropriées.
- Écologie : La poudre de pulvérisation est souvent préférée à d’autres méthodes de revêtement en raison de son faible impact environnemental. Contrairement aux revêtements liquides qui peuvent contenir des solvants et des composés organiques volatils (COV), la poudre de pulvérisation ne génère pas de déchets liquides et peut être recyclée pour réduire les déchets et les coûts de production.
En résumé, la poudre de pulvérisation est un matériau polyvalent et efficace utilisé dans le processus de revêtement par poudrage pour fournir des revêtements protecteurs et décoratifs de haute qualité sur une variété de substrats industriels. Elle offre une large gamme de couleurs, de finitions et de propriétés pour répondre aux besoins spécifiques des applications industrielles.
Le revêtement par pulvérisation de poudre est une méthode de revêtement largement utilisée dans l’industrie pour appliquer un revêtement protecteur ou décoratif sur une variété de surfaces. Ce processus implique l’application d’une fine couche de poudre de revêtement sur la surface à l’aide d’un équipement spécifique, suivi d’une phase de cuisson pour fusionner et polymériser la poudre, formant ainsi un revêtement solide et durable.
Voici les principales étapes du processus de revêtement par pulvérisation de poudre :
- Préparation de la surface : Avant d’appliquer la poudre, la surface à revêtir est préparée en conséquence. Cela peut inclure le nettoyage, le dégraissage, le sablage et d’autres techniques de préparation de surface pour assurer une adhérence optimale du revêtement.
- Application de la poudre : La poudre de revêtement est chargée dans un pistolet de pulvérisation de poudre, où elle est pulvérisée sous forme de fine brume sur la surface à revêtir. La poudre est projetée à travers une buse de pulvérisation à l’aide d’air comprimé ou d’un gaz inerte, créant ainsi un nuage de poudre qui se dépose uniformément sur la surface.
- Adhérence électrostatique (optionnelle) : Dans certains cas, la poudre de revêtement est chargée électrostatiquement avant son application. Cela se fait en utilisant un générateur haute tension pour charger les particules de poudre, ce qui les rend attirées par la surface opposée, assurant ainsi une adhérence maximale du revêtement sur la surface.
- Cuisson du revêtement : Une fois la poudre appliquée, les pièces revêtues sont placées dans un four de cuisson où le revêtement est fondu et polymérisé. Pendant ce processus, la poudre fond et se lie pour former un film solide et uniforme sur la surface du substrat.
- Refroidissement et durcissement : Une fois que le revêtement a fondu et polymérisé, les pièces revêtues sont refroidies à température ambiante pour durcir le revêtement. Ce processus peut prendre quelques minutes à quelques heures, selon le type de revêtement et les conditions de cuisson.
- Contrôle de la qualité : Une fois le revêtement durci, des contrôles de qualité sont effectués pour vérifier l’épaisseur du revêtement, l’adhérence, la couleur, la brillance et d’autres propriétés du revêtement. Cela garantit que le revêtement répond aux normes de qualité requises et offre la protection et les performances souhaitées.
Le revêtement par pulvérisation de poudre est largement utilisé dans des industries telles que l’automobile, l’aérospatiale, le mobilier, l’électronique et d’autres secteurs où des revêtements de haute qualité et durables sont nécessaires. En utilisant cette méthode, il est possible d’obtenir des revêtements uniformes et esthétiques offrant une excellente protection contre la corrosion, l’usure et d’autres dommages.
La technologie électrostatique est une méthode de revêtement utilisée dans divers processus industriels, y compris le revêtement par pulvérisation de poudre, la peinture, la pulvérisation de liquides et d’autres applications. Cette technologie repose sur le principe de l’électrostatique, qui implique la création d’une charge électrique sur les particules de revêtement ou de pulvérisation, ainsi que sur la surface à revêtir, pour assurer une adhérence maximale et une distribution uniforme du revêtement.
Voici comment fonctionne la technologie électrostatique dans le contexte du revêtement par pulvérisation de poudre :
- Chargement des particules : Dans un système électrostatique, les particules de poudre de revêtement sont chargées électriquement avant d’être pulvérisées sur la surface à revêtir. Cela peut être réalisé en utilisant un générateur haute tension pour charger les particules de poudre, les rendant ainsi électriquement chargées.
- Champ électrostatique : Une fois chargées, les particules de poudre acquièrent une charge électrique et sont soumises à un champ électrostatique généré par le système. Ce champ électrostatique crée une force d’attraction entre les particules chargées et la surface opposée, assurant ainsi une adhérence maximale du revêtement sur la surface.
- Pulvérisation de la poudre : Les particules de poudre chargées électrostatiquement sont pulvérisées sur la surface à revêtir à l’aide d’un pistolet de pulvérisation de poudre. En raison de leur charge électrique, les particules sont attirées par la surface opposée, ce qui favorise une distribution uniforme du revêtement sur toute la surface.
- Cuisson du revêtement : Une fois la poudre appliquée, les pièces revêtues sont placées dans un four de cuisson où le revêtement est fondu et polymérisé. Pendant ce processus, la poudre fond et se lie pour former un film solide et uniforme sur la surface du substrat.
- Contrôle de la qualité : Une fois le revêtement durci, des contrôles de qualité sont effectués pour vérifier l’épaisseur du revêtement, l’adhérence, la couleur, la brillance et d’autres propriétés du revêtement. Cela garantit que le revêtement répond aux normes de qualité requises et offre la protection et les performances souhaitées.
La technologie électrostatique offre de nombreux avantages dans le processus de revêtement, notamment une adhérence améliorée, une distribution uniforme du revêtement, une réduction des pertes de poudre et une meilleure efficacité de production. Elle est largement utilisée dans diverses industries pour obtenir des revêtements de haute qualité et durables sur une variété de substrats.
Pistolet à peinture électrostatique
Un pistolet à peinture électrostatique est un outil utilisé dans le processus de revêtement par pulvérisation pour appliquer des revêtements liquides sur une variété de surfaces de manière efficace et uniforme. Contrairement aux pistolets à peinture conventionnels, les pistolets à peinture électrostatique utilisent la technologie électrostatique pour charger électriquement les particules de peinture, ce qui améliore l’adhérence et la distribution du revêtement.
Voici comment fonctionne un pistolet à peinture électrostatique :
- Chargement électrostatique : Le pistolet à peinture électrostatique utilise un générateur haute tension pour charger électriquement les particules de peinture au fur et à mesure qu’elles sont pulvérisées. Cette charge électrique crée un champ électrostatique autour des particules de peinture, les rendant attirées par la surface opposée.
- Pulvérisation de la peinture : La peinture liquide est introduite dans le pistolet à travers un système d’alimentation et est atomisée en fines particules par une buse de pulvérisation. Pendant ce processus, les particules de peinture sont chargées électrostatiquement, ce qui les fait se déplacer vers la surface opposée de manière uniforme.
- Adhérence et distribution : En raison de leur charge électrique, les particules de peinture sont attirées par la surface opposée, assurant ainsi une adhérence maximale du revêtement. Cette méthode de pulvérisation électrostatique permet une distribution uniforme de la peinture sur toute la surface, y compris les zones difficiles à atteindre.
- Cuisson ou séchage : Une fois la peinture appliquée, les pièces revêtues peuvent être placées dans un four de cuisson pour polymériser la peinture et former un revêtement solide et durable. Dans certains cas, la peinture peut être séchée à l’air ou à l’aide d’un dispositif de séchage infrarouge, en fonction des exigences du revêtement et des matériaux utilisés.
- Contrôle de la qualité : Une fois le revêtement appliqué et durci, des contrôles de qualité sont effectués pour vérifier l’épaisseur du revêtement, l’adhérence, la couleur, la brillance et d’autres propriétés du revêtement. Cela garantit que le revêtement répond aux normes de qualité requises et offre la protection et les performances souhaitées.
En résumé, les pistolets à peinture électrostatique offrent de nombreux avantages dans le processus de revêtement, notamment une meilleure adhérence, une distribution uniforme de la peinture, une réduction des pertes de peinture et une efficacité de production accrue. Ils sont largement utilisés dans diverses industries pour obtenir des revêtements de haute qualité et durables sur une variété de substrats.
Le revêtement de surface en poudre est une méthode de revêtement utilisée dans diverses industries pour appliquer un revêtement protecteur ou décoratif sur une variété de substrats. Contrairement aux revêtements liquides traditionnels, le revêtement en poudre est appliqué sous forme de poudre fine qui est ensuite fondue et polymérisée pour former un film solide et durable sur la surface du substrat.
Voici les principales étapes du processus de revêtement de surface en poudre :
- Préparation de la surface : Avant d’appliquer la poudre de revêtement, la surface du substrat est préparée en conséquence. Cela peut inclure le nettoyage, le dégraissage, le sablage et d’autres techniques de préparation de surface pour assurer une adhérence optimale du revêtement.
- Application de la poudre : La poudre de revêtement est appliquée sur la surface du substrat à l’aide d’un équipement de pulvérisation de poudre, tel qu’un pistolet de pulvérisation de poudre. La poudre est pulvérisée sous forme de fine brume sur la surface, où elle adhère électrostatiquement ou mécaniquement.
- Cuisson du revêtement : Une fois la poudre appliquée, les pièces revêtues sont placées dans un four de cuisson où le revêtement est fondu et polymérisé. Pendant ce processus, la poudre fond et se lie pour former un film solide et uniforme sur la surface du substrat.
- Refroidissement et durcissement : Une fois que le revêtement a fondu et polymérisé, les pièces revêtues sont refroidies à température ambiante pour durcir le revêtement. Ce processus peut prendre quelques minutes à quelques heures, selon le type de revêtement et les conditions de cuisson.
- Contrôle de la qualité : Une fois le revêtement durci, des contrôles de qualité sont effectués pour vérifier l’épaisseur du revêtement, l’adhérence, la couleur, la brillance et d’autres propriétés du revêtement. Cela garantit que le revêtement répond aux normes de qualité requises et offre la protection et les performances souhaitées.
Le revêtement de surface en poudre offre de nombreux avantages par rapport aux revêtements liquides traditionnels, notamment une meilleure adhérence, une résistance accrue à la corrosion, aux produits chimiques et aux rayures, ainsi qu’une plus grande durabilité et une finition de haute qualité. Il est largement utilisé dans des industries telles que l’automobile, l’aérospatiale, le mobilier, l’électronique et d’autres secteurs où des revêtements de haute qualité et durables sont nécessaires.
Machine de poudrage électrostatique
Une machine de poudrage électrostatique est un équipement utilisé dans le processus de revêtement par pulvérisation de poudre pour appliquer un revêtement uniforme et de haute qualité sur une variété de substrats. Cette machine utilise la technologie électrostatique pour charger électriquement les particules de poudre de revêtement, ce qui améliore leur adhérence et leur distribution sur la surface du substrat.
Voici comment fonctionne une machine de poudrage électrostatique :
- Chargement électrostatique : La machine de poudrage électrostatique utilise un générateur haute tension pour charger électriquement les particules de poudre de revêtement au fur et à mesure qu’elles sont introduites dans la chambre de pulvérisation. Cette charge électrique crée un champ électrostatique autour des particules de poudre, les rendant attirées par la surface opposée.
- Pulvérisation de la poudre : Les particules de poudre chargées électrostatiquement sont pulvérisées sur la surface du substrat à l’aide d’un pistolet de pulvérisation de poudre monté sur la machine. Les particules de poudre sont projetées à travers une buse de pulvérisation et se déplacent vers la surface opposée en raison de leur charge électrique, assurant ainsi une distribution uniforme du revêtement sur toute la surface.
- Adhérence et distribution : En raison de leur charge électrique, les particules de poudre sont attirées par la surface opposée, assurant ainsi une adhérence maximale du revêtement. Cette méthode de pulvérisation électrostatique permet une distribution uniforme de la poudre sur toute la surface du substrat, y compris les zones difficiles à atteindre.
- Cuisson du revêtement : Une fois la poudre appliquée, les pièces revêtues sont placées dans un four de cuisson où le revêtement est fondu et polymérisé. Pendant ce processus, la poudre fond et se lie pour former un film solide et uniforme sur la surface du substrat.
- Refroidissement et durcissement : Une fois que le revêtement a fondu et polymérisé, les pièces revêtues sont refroidies à température ambiante pour durcir le revêtement. Ce processus peut prendre quelques minutes à quelques heures, selon le type de revêtement et les conditions de cuisson.
Une machine de poudrage électrostatique offre de nombreux avantages dans le processus de revêtement, notamment une meilleure adhérence, une distribution uniforme du revêtement, une réduction des pertes de poudre et une efficacité de production accrue. Elle est largement utilisée dans diverses industries pour obtenir des revêtements de haute qualité et durables sur une variété de substrats.
Le revêtement en poudre métallique est une méthode de revêtement utilisée pour appliquer une finition métallique sur une variété de substrats. Contrairement aux peintures liquides traditionnelles, le revêtement en poudre métallique utilise des particules de poudre métallique qui sont pulvérisées sur la surface du substrat, puis fondues pour former un revêtement solide et durable.
Voici les principales étapes du processus de revêtement en poudre métallique :
- Préparation de la surface : Avant d’appliquer la poudre métallique, la surface du substrat est préparée en conséquence. Cela peut inclure le nettoyage, le dégraissage, le sablage et d’autres techniques de préparation de surface pour assurer une adhérence optimale du revêtement.
- Application de la poudre : La poudre métallique est pulvérisée sur la surface du substrat à l’aide d’un équipement de pulvérisation de poudre, tel qu’un pistolet de pulvérisation de poudre. La poudre est chargée électrostatiquement pour assurer une adhérence maximale sur la surface du substrat.
- Cuisson du revêtement : Une fois la poudre métallique appliquée, les pièces revêtues sont placées dans un four de cuisson où le revêtement est fondu et polymérisé. Pendant ce processus, la poudre métallique fond et se lie pour former un revêtement solide et durable sur la surface du substrat.
- Refroidissement et durcissement : Une fois que le revêtement a fondu et polymérisé, les pièces revêtues sont refroidies à température ambiante pour durcir le revêtement. Ce processus peut prendre quelques minutes à quelques heures, selon le type de revêtement et les conditions de cuisson.
- Finition : Une fois le revêtement durci, des finitions supplémentaires peuvent être appliquées pour améliorer les propriétés esthétiques et fonctionnelles du revêtement, telles que le polissage, le brossage, le vernissage ou d’autres traitements de surface.
Le revêtement en poudre métallique offre de nombreux avantages par rapport aux revêtements liquides traditionnels, notamment une meilleure adhérence, une résistance accrue à la corrosion et aux rayures, ainsi qu’une finition esthétique et durable. Il est largement utilisé dans des applications telles que l’automobile, l’aérospatiale, le mobilier, l’électronique et d’autres industries où des revêtements métalliques de haute qualité sont nécessaires.
L’application de peinture en poudre est un processus de revêtement utilisé pour appliquer une finition de peinture sur une variété de substrats. Contrairement aux peintures liquides traditionnelles, la peinture en poudre est appliquée sous forme de poudre fine qui est ensuite fondue et polymérisée pour former un film solide et durable sur la surface du substrat.
Voici les étapes principales du processus d’application de peinture en poudre :
- Préparation de la surface : Avant d’appliquer la peinture en poudre, la surface du substrat est préparée en conséquence. Cela peut inclure le nettoyage, le dégraissage, le sablage et d’autres techniques de préparation de surface pour assurer une adhérence optimale de la peinture.
- Application de la peinture en poudre : La peinture en poudre est appliquée sur la surface du substrat à l’aide d’un équipement de pulvérisation de poudre, tel qu’un pistolet de pulvérisation de poudre. La poudre est pulvérisée sous forme de fine brume sur la surface, où elle adhère électrostatiquement ou mécaniquement.
- Cuisson du revêtement : Une fois la peinture en poudre appliquée, les pièces revêtues sont placées dans un four de cuisson où le revêtement est fondu et polymérisé. Pendant ce processus, la poudre fond et se lie pour former un film solide et uniforme sur la surface du substrat.
- Refroidissement et durcissement : Une fois que le revêtement a fondu et polymérisé, les pièces revêtues sont refroidies à température ambiante pour durcir le revêtement. Ce processus peut prendre quelques minutes à quelques heures, selon le type de revêtement et les conditions de cuisson.
- Finition : Une fois le revêtement durci, des finitions supplémentaires peuvent être appliquées pour améliorer les propriétés esthétiques et fonctionnelles du revêtement, telles que le polissage, le brossage, le vernissage ou d’autres traitements de surface.
L’application de peinture en poudre offre de nombreux avantages par rapport aux peintures liquides traditionnelles, notamment une meilleure adhérence, une résistance accrue à la corrosion et aux rayures, ainsi qu’une finition esthétique et durable. Elle est largement utilisée dans des industries telles que l’automobile, l’aérospatiale, le mobilier, l’électronique et d’autres secteurs où des revêtements de haute qualité et durables sont nécessaires.
Un système de revêtement électrostatique est un ensemble d’équipements utilisé pour appliquer des revêtements de manière électrostatique sur une variété de substrats. Ce système utilise la technologie électrostatique pour charger électriquement les particules de revêtement, ce qui améliore leur adhérence et leur distribution sur la surface du substrat.
Voici les composants principaux d’un système de revêtement électrostatique :
- Générateur haute tension : C’est l’élément central du système électrostatique. Le générateur haute tension produit une tension électrique élevée qui est utilisée pour charger électriquement les particules de revêtement avant leur application sur la surface du substrat.
- Pistolet de pulvérisation électrostatique : Le pistolet de pulvérisation électrostatique est l’outil principal utilisé pour appliquer le revêtement sur la surface du substrat. Il est équipé d’une buse de pulvérisation et d’un système de charge électrostatique qui charge les particules de revêtement pendant leur application.
- Cabine de pulvérisation : La cabine de pulvérisation est l’enceinte où le processus de pulvérisation du revêtement a lieu. Elle est conçue pour contenir les particules de revêtement et pour fournir un environnement contrôlé pour assurer une application uniforme du revêtement sur le substrat.
- Système de contrôle : Le système de contrôle comprend divers dispositifs de contrôle et de surveillance, tels que des contrôleurs de débit, des régulateurs de pression et des indicateurs de tension, qui assurent le bon fonctionnement et la qualité du processus de revêtement.
- Four de cuisson : Une fois que le revêtement a été appliqué sur la surface du substrat, les pièces revêtues sont généralement placées dans un four de cuisson pour polymériser et durcir le revêtement. Le four de cuisson est un élément essentiel du processus de revêtement électrostatique.
- Système de récupération de poudre : Pour minimiser les pertes de poudre et réutiliser les excès de matériau, certains systèmes de revêtement électrostatique sont équipés d’un système de récupération de poudre qui récupère et recycle la poudre non utilisée.
Les systèmes de revêtement électrostatique sont largement utilisés dans diverses industries pour appliquer des revêtements de haute qualité et durables sur une grande variété de substrats. Ils offrent des avantages tels qu’une meilleure adhérence, une distribution uniforme du revêtement, une réduction des pertes de matériau et une efficacité de production accrue.
Le procédé de poudrage électrostatique est une méthode de revêtement utilisée pour appliquer une finition uniforme et durable sur une variété de surfaces. Ce processus repose sur l’utilisation de la charge électrostatique pour attirer et adhérer la poudre de revêtement sur la surface du substrat.
Voici les principales étapes du procédé de poudrage électrostatique :
- Préparation de la surface : Avant d’appliquer la poudre, la surface du substrat est nettoyée et préparée pour assurer une adhérence optimale du revêtement. Cela peut impliquer le dégraissage, le sablage et d’autres méthodes de préparation de surface.
- Application de la poudre : La poudre de revêtement est introduite dans le pistolet de pulvérisation, où elle est chargée électriquement par le générateur haute tension intégré au pistolet. Les particules de poudre chargées sont ensuite pulvérisées sur la surface du substrat à travers une buse de pulvérisation.
- Attraction électrostatique : Lorsque les particules de poudre chargées électrostatiquement sont pulvérisées, elles sont repoussées par les charges similaires et attirées par la surface opposée du substrat, qui est mise à la terre. Cela garantit une adhérence efficace de la poudre sur toute la surface, y compris les zones difficiles à atteindre.
- Cuisson du revêtement : Une fois la poudre appliquée, les pièces revêtues sont placées dans un four de cuisson où le revêtement est fondu et polymérisé. Pendant ce processus, la poudre fond et se lie pour former un film solide et uniforme sur la surface du substrat.
- Refroidissement et durcissement : Après la cuisson, les pièces revêtues sont refroidies à température ambiante pour durcir le revêtement. Ce processus peut prendre quelques minutes à quelques heures, selon le type de revêtement et les conditions de cuisson.
Le procédé de poudrage électrostatique offre de nombreux avantages, notamment une application uniforme du revêtement, une adhérence supérieure, une réduction des pertes de matériau et une efficacité de production accrue. Il est largement utilisé dans diverses industries pour appliquer des revêtements de haute qualité sur des pièces métalliques, plastiques et autres substrats.
Équipement de revêtement en poudre
L’équipement de revêtement en poudre comprend une variété d’outils et de machines spécialement conçus pour appliquer des revêtements en poudre sur différents types de surfaces. Ces équipements sont essentiels pour garantir un processus de revêtement efficace, précis et de haute qualité. Voici une description détaillée de certains des principaux équipements de revêtement en poudre :
- Cabine de poudrage : La cabine de poudrage est l’enceinte où le processus de pulvérisation de la poudre de revêtement a lieu. Elle est équipée de systèmes de ventilation pour évacuer les particules de poudre en suspension et fournir un environnement contrôlé pour garantir une application uniforme du revêtement.
- Pistolet de pulvérisation de poudre : Le pistolet de pulvérisation de poudre est l’outil principal utilisé pour appliquer la poudre de revêtement sur la surface du substrat. Il est équipé d’une buse de pulvérisation spéciale et d’un système de charge électrostatique pour garantir une distribution uniforme de la poudre sur toute la surface.
- Système de récupération de poudre : Pour minimiser les pertes de poudre et réutiliser les excès de matériau, certains équipements de revêtement en poudre sont équipés de systèmes de récupération de poudre. Ces systèmes collectent et recyclent la poudre non utilisée pour une utilisation ultérieure.
- Four de cuisson : Une fois que la poudre de revêtement a été appliquée sur la surface du substrat, les pièces revêtues sont placées dans un four de cuisson pour polymériser et durcir le revêtement. Le four de cuisson est un élément essentiel du processus de revêtement en poudre.
- Système de filtration d’air : Pour maintenir un environnement de travail propre et sûr, les équipements de revêtement en poudre sont souvent équipés de systèmes de filtration d’air pour éliminer les particules de poudre en suspension et les contaminants de l’air.
- Équipement de prétraitement : Avant d’appliquer le revêtement en poudre, la surface du substrat doit souvent être prétraitée pour assurer une adhérence optimale du revêtement. Cela peut impliquer des opérations telles que le dégraissage, le sablage, le dérochage et le traitement chimique de la surface.
Ensemble, ces équipements de revêtement en poudre forment un système complet et intégré qui permet d’appliquer efficacement et de manière cohérente des revêtements en poudre sur une variété de substrats. Ils sont largement utilisés dans diverses industries, notamment l’automobile, l’aérospatiale, le mobilier, l’électronique et bien d’autres, où des revêtements de haute qualité et durables sont nécessaires.
Technologie de revêtement en poudre
La technologie de revêtement en poudre est un procédé de revêtement utilisé pour appliquer une couche protectrice ou décorative sur une variété de substrats. Contrairement aux peintures liquides traditionnelles, ce processus repose sur l’utilisation de poudre de revêtement sous forme de particules fines, qui sont appliquées électrostatiquement ou par projection sur la surface du substrat. Voici une description détaillée de la technologie de revêtement en poudre :
- Préparation de la surface : Avant l’application de la poudre de revêtement, la surface du substrat est préparée en conséquence. Cela peut inclure le nettoyage, le dégraissage, le sablage et d’autres méthodes de préparation de surface pour assurer une adhérence optimale du revêtement.
- Application de la poudre : La poudre de revêtement est appliquée sur la surface du substrat à l’aide d’un équipement de pulvérisation de poudre, tel qu’un pistolet de pulvérisation de poudre. La poudre est soit électrostatiquement chargée avant d’être pulvérisée, soit projetée mécaniquement sur la surface du substrat.
- Attraction électrostatique : Lorsque la poudre de revêtement est appliquée électrostatiquement, les particules de poudre sont chargées électriquement avant d’être pulvérisées. Elles sont alors attirées par la surface opposée du substrat, qui est mise à la terre, assurant ainsi une adhérence uniforme sur toute la surface.
- Cuisson du revêtement : Une fois la poudre de revêtement appliquée, les pièces revêtues sont placées dans un four de cuisson où le revêtement est fondu et polymérisé. Pendant ce processus, la poudre fond et se lie pour former un film solide et uniforme sur la surface du substrat.
- Refroidissement et durcissement : Après la cuisson, les pièces revêtues sont refroidies à température ambiante pour durcir le revêtement. Ce processus peut prendre quelques minutes à quelques heures, selon le type de revêtement et les conditions de cuisson.
La technologie de revêtement en poudre offre de nombreux avantages par rapport aux peintures liquides traditionnelles, notamment une meilleure adhérence, une résistance accrue à la corrosion et aux rayures, ainsi qu’une finition esthétique et durable. Elle est largement utilisée dans des industries telles que l’automobile, l’aérospatiale, le mobilier, l’électronique et d’autres secteurs où des revêtements de haute qualité et durables sont nécessaires.
Pistolet de poudre électrostatique
Un pistolet de poudre électrostatique est un outil essentiel utilisé dans le processus de revêtement par poudrage électrostatique. Cet équipement est spécialement conçu pour appliquer de manière précise et efficace la poudre de revêtement sur une variété de substrats, en utilisant la technologie électrostatique pour assurer une distribution uniforme du matériau.
Voici comment fonctionne un pistolet de poudre électrostatique et ses principales caractéristiques :
- Charge électrostatique : Le pistolet de poudre électrostatique est équipé d’un générateur haute tension qui charge électriquement les particules de poudre de revêtement lorsqu’elles passent à travers le pistolet. Cette charge électrostatique confère aux particules une polarité positive ou négative, selon la configuration du pistolet.
- Pulvérisation de la poudre : Une fois chargées électrostatiquement, les particules de poudre sont pulvérisées sur la surface du substrat à l’aide d’une buse de pulvérisation spéciale située à l’extrémité du pistolet. La poudre est projetée avec précision sur la surface à revêtir, assurant une couverture uniforme et efficace.
- Attraction électrostatique : En raison de leur charge électrique, les particules de poudre sont attirées par la surface opposée du substrat, qui est mise à la terre. Cette attraction électrostatique garantit une adhérence optimale de la poudre sur toute la surface, y compris dans les zones difficiles à atteindre.
- Contrôle de la pulvérisation : Les pistolets de poudre électrostatique sont équipés de divers réglages permettant de contrôler le débit de poudre, la forme du jet et d’autres paramètres de pulvérisation. Cela permet d’adapter le processus de revêtement aux exigences spécifiques de chaque application.
- Ergonomie et facilité d’utilisation : Les pistolets de poudre électrostatique sont généralement conçus pour être ergonomiques et faciles à utiliser, ce qui permet aux opérateurs de travailler efficacement pendant de longues périodes sans fatigue excessive.
Les pistolets de poudre électrostatique sont largement utilisés dans de nombreuses industries pour appliquer des revêtements de haute qualité et durables sur une variété de substrats, notamment les métaux, le plastique, le bois et d’autres matériaux. Ils offrent une précision, une efficacité et une uniformité de revêtement supérieures par rapport aux méthodes de pulvérisation de peinture liquide traditionnelles.
Le revêtement en poudre polyester est l’une des options les plus courantes et les plus polyvalentes dans le domaine du revêtement par poudrage. Ce type de revêtement est fabriqué à partir de résines de polyester thermodurcissables, qui offrent une excellente adhérence, une durabilité exceptionnelle et une résistance aux intempéries, à la corrosion et aux rayures. Voici une description détaillée du revêtement en poudre polyester :
- Composition : Le revêtement en poudre polyester est principalement composé de résines de polyester thermodurcissables, qui sont mélangées avec des pigments, des charges et des additifs pour obtenir les propriétés souhaitées du revêtement. Ces résines réagissent chimiquement lorsqu’elles sont chauffées, formant un film polymère solide et durable.
- Application : Le revêtement en poudre polyester est appliqué sur la surface du substrat à l’aide d’un équipement de pulvérisation de poudre, tel qu’un pistolet de poudre électrostatique. La poudre est électrostatiquement chargée et pulvérisée sur la surface préparée, où elle adhère grâce à l’attraction électrostatique.
- Cuisson : Une fois appliquée, la poudre de revêtement en polyester est cuite dans un four de cuisson à des températures élevées, généralement entre 150 et 200 degrés Celsius. Pendant ce processus, les résines de polyester fondent et réagissent chimiquement pour former un film polymère solide et durable.
- Propriétés : Le revêtement en poudre polyester offre de nombreuses propriétés avantageuses, notamment une excellente résistance à la corrosion, aux UV et aux produits chimiques, ainsi qu’une bonne résistance aux chocs et aux rayures. Il est également disponible dans une large gamme de couleurs et de finitions, y compris les finitions mates, brillantes et texturées.
- Applications : En raison de ses excellentes propriétés et de sa polyvalence, le revêtement en poudre polyester est largement utilisé dans une variété d’applications industrielles et commerciales. Il est couramment utilisé pour le revêtement de pièces automobiles, de meubles d’extérieur, de clôtures, de luminaires, d’équipements électroménagers, de cadres de vélo et bien d’autres produits.
- Avantages environnementaux : Le revêtement en poudre polyester est également apprécié pour ses avantages environnementaux. Contrairement aux peintures liquides, il ne contient pas de solvants volatils et émet peu ou pas de composés organiques volatils (COV) lors de l’application. De plus, la poudre de revêtement excédentaire peut être récupérée et recyclée, ce qui réduit les déchets et les coûts de production.
En résumé, le revêtement en poudre polyester est un choix populaire et efficace pour une large gamme d’applications, offrant une combinaison unique de performance, de durabilité et de respect de l’environnement.
Le revêtement de protection en poudre est un procédé de revêtement utilisé pour appliquer une couche de protection sur une surface afin de la protéger contre diverses conditions environnementales, telles que la corrosion, l’abrasion, les rayures, les UV et les produits chimiques. Ce type de revêtement est particulièrement apprécié pour sa durabilité, sa résistance et sa capacité à fournir une protection à long terme. Voici une description détaillée du revêtement de protection en poudre :
- Composition : Le revêtement de protection en poudre est généralement composé de résines thermodurcissables telles que l’époxy, le polyester ou le polyuréthane, qui sont mélangées avec des pigments, des charges et des additifs spécifiques pour obtenir les propriétés souhaitées du revêtement.
- Application : Le revêtement de protection en poudre est appliqué sur la surface du substrat à l’aide d’un équipement de pulvérisation de poudre, tel qu’un pistolet de pulvérisation de poudre électrostatique. La poudre est projetée sur la surface préparée, où elle adhère grâce à l’attraction électrostatique ou mécanique.
- Cuisson : Une fois appliquée, la poudre de revêtement est cuite dans un four de cuisson à des températures élevées, généralement entre 150 et 220 degrés Celsius. Pendant ce processus, les résines thermodurcissables fondent et réagissent chimiquement pour former un film polymère solide et durable.
- Propriétés : Le revêtement de protection en poudre offre une large gamme de propriétés avantageuses, notamment une excellente résistance à la corrosion, aux UV, à l’abrasion, aux rayures et aux produits chimiques. Il est également disponible dans une variété de couleurs et de finitions pour répondre à des besoins esthétiques spécifiques.
- Applications : En raison de ses excellentes propriétés de protection et de sa durabilité, le revêtement de protection en poudre est largement utilisé dans de nombreuses industries pour protéger une grande variété de substrats, y compris les métaux, le plastique, le bois et le béton. Il est utilisé dans des applications telles que les pièces automobiles, les équipements industriels, les structures métalliques, les mobilier d’extérieur, les équipements électroniques, et bien d’autres.
- Avantages environnementaux : Le revêtement de protection en poudre présente également des avantages environnementaux par rapport aux peintures liquides traditionnelles, car il ne contient pas de solvants volatils et émet peu ou pas de composés organiques volatils (COV) lors de l’application. De plus, la poudre de revêtement excédentaire peut être récupérée et recyclée, ce qui réduit les déchets et les coûts de production.
En conclusion, le revêtement de protection en poudre est un choix efficace et durable pour assurer la protection à long terme des surfaces contre les dommages et la dégradation. Il offre une combinaison unique de performance, de durabilité et de respect de l’environnement, ce qui en fait une solution de revêtement idéale pour de nombreuses applications industrielles et commerciales.
Une machine de pulvérisation de poudre est un équipement utilisé dans le processus de revêtement par poudrage pour appliquer de manière précise et uniforme la poudre de revêtement sur une variété de substrats. Cette machine est essentielle pour garantir une application efficace du revêtement et une finition de haute qualité. Voici une description détaillée d’une machine de pulvérisation de poudre :
- Composants : Une machine de pulvérisation de poudre est généralement composée des éléments suivants :
- Pistolet de pulvérisation : Il s’agit de l’élément principal de la machine, responsable de la pulvérisation de la poudre sur la surface du substrat.
- Générateur de charge électrostatique : Pour les systèmes électrostatiques, un générateur de charge électrostatique est inclus pour charger les particules de poudre avant leur pulvérisation.
- Système de récupération de poudre : Certaines machines sont équipées d’un système de récupération de poudre pour collecter la poudre excédentaire et la réutiliser, ce qui réduit les déchets et les coûts.
- Unité de contrôle : Une unité de contrôle permet à l’opérateur de régler différents paramètres de pulvérisation, tels que le débit de poudre, la pression d’air, etc.
- Fonctionnement : Lorsque la machine de pulvérisation de poudre est en fonctionnement, la poudre de revêtement est introduite dans le système et transportée vers le pistolet de pulvérisation. Selon le type de système, la poudre peut être électrostatiquement chargée avant d’être pulvérisée ou simplement projetée mécaniquement. Le pistolet de pulvérisation est alors utilisé pour appliquer la poudre sur la surface du substrat de manière uniforme.
- Réglages : Les machines de pulvérisation de poudre offrent généralement une gamme de réglages pour permettre à l’opérateur d’ajuster divers paramètres en fonction des besoins spécifiques de l’application. Cela peut inclure le réglage du débit de poudre, de la pression d’air, de la forme du jet, etc.
- Applications : Les machines de pulvérisation de poudre sont utilisées dans une variété d’industries pour appliquer des revêtements de haute qualité sur une gamme diversifiée de substrats. Elles sont largement utilisées dans l’automobile, l’aérospatiale, la construction, le mobilier, l’électronique et de nombreuses autres industries.
- Avantages : Les machines de pulvérisation de poudre offrent plusieurs avantages par rapport aux méthodes de revêtement traditionnelles, notamment une application rapide et efficace, une finition uniforme, une réduction des déchets et des coûts de production, ainsi qu’une protection améliorée contre la corrosion et les rayures.
En résumé, les machines de pulvérisation de poudre sont des outils essentiels dans le processus de revêtement par poudrage, offrant une solution efficace et précise pour appliquer des revêtements de haute qualité sur une variété de substrats. Elles jouent un rôle crucial dans de nombreuses industries où des revêtements durables et esthétiques sont nécessaires.
La poudre de finition est un composant essentiel du processus de revêtement par poudrage, utilisée pour donner une touche finale à la surface revêtue. Elle est appliquée après la couche de base pour fournir des propriétés spécifiques à la surface et améliorer son aspect esthétique. Voici une description détaillée de la poudre de finition :
- Composition : La poudre de finition est généralement composée de résines thermodurcissables, de pigments, de charges, d’additifs et parfois de matériaux réactifs spécifiques. Ces composants sont mélangés pour obtenir les propriétés souhaitées de la poudre de finition, telles que la résistance aux UV, la résistance à la corrosion, la durabilité et l’aspect esthétique.
- Types : Il existe plusieurs types de poudres de finition disponibles, chacun offrant des propriétés et des finitions spécifiques :
- Poudres de finition transparentes : Utilisées pour protéger la couche de base et fournir une brillance ou une finition mate à la surface.
- Poudres de finition colorées : Offrent une gamme étendue de couleurs pour répondre aux besoins esthétiques spécifiques de l’application.
- Poudres de finition texturées : Produisent des finitions texturées telles que le martelé, le métallisé, le sablé ou le granité, pour ajouter du relief et de la dimension à la surface revêtue.
- Poudres de finition spéciales : Comprend des poudres de finition antimicrobiennes, ignifuges, conductrices, réfléchissantes ou thermochromiques, qui offrent des propriétés spécifiques supplémentaires à la surface revêtue.
- Application : La poudre de finition est appliquée sur la surface revêtue à l’aide d’un équipement de pulvérisation de poudre, tout comme la couche de base. Elle est pulvérisée uniformément sur la surface préparée et cuite dans un four de cuisson pour former un film polymère solide et durable.
- Fonctions : La poudre de finition remplit plusieurs fonctions importantes :
- Protection : Protège la couche de base contre les dommages mécaniques, la corrosion, les UV et les produits chimiques.
- Aspect esthétique : Améliore l’aspect visuel de la surface en fournissant une finition lisse, brillante et uniforme ou une finition texturée attrayante.
- Fonctionnalité : Peut ajouter des propriétés spécifiques à la surface, telles que l’antiadhérence, l’antidérapance, la conductivité électrique, etc.
- Applications : La poudre de finition est largement utilisée dans de nombreuses industries pour une variété d’applications, y compris l’automobile, le mobilier, l’électronique, l’aérospatiale, la construction, les appareils ménagers, les équipements sportifs et bien d’autres.
En résumé, la poudre de finition est un élément crucial du processus de revêtement par poudrage, offrant une protection, une esthétique et des fonctionnalités supplémentaires à la surface revêtue. Elle permet d’obtenir des résultats de haute qualité et répond aux exigences spécifiques des différentes applications industrielles et commerciales.
Revêtement en poudre thermoplastique
Le revêtement en poudre thermoplastique est une méthode de revêtement utilisée pour appliquer une couche de matériau thermoplastique sur une surface pour lui fournir des propriétés protectrices, décoratives ou fonctionnelles. Contrairement aux revêtements en poudre thermodurcissables, qui durcissent lors de la cuisson, les revêtements en poudre thermoplastiques fondent lorsqu’ils sont chauffés et se liquéfient. Voici une description détaillée du revêtement en poudre thermoplastique :
- Composition : Les revêtements en poudre thermoplastiques sont fabriqués à partir de polymères thermoplastiques, tels que le polyéthylène, le polypropylène, le PVC, le nylon, le polyuréthane, entre autres. Ces polymères sont moulés en poudre fine, parfois mélangés avec des pigments, des charges, des additifs ou des agents de stabilisation pour obtenir les propriétés souhaitées du revêtement.
- Application : Le processus d’application du revêtement en poudre thermoplastique est similaire à celui des revêtements en poudre thermodurcissables. La poudre est pulvérisée sur la surface du substrat à l’aide d’un équipement de pulvérisation de poudre, puis chauffée dans un four de cuisson à des températures suffisamment élevées pour faire fondre la poudre et la fusionner en un film continu.
- Fusion : Lorsque la poudre thermoplastique est chauffée, elle fond et se liquéfie, adhérant à la surface du substrat pour former un revêtement uniforme. Contrairement aux revêtements en poudre thermodurcissables, qui réticulent chimiquement lorsqu’ils sont chauffés, les revêtements en poudre thermoplastiques conservent leur capacité à se ramollir et à se solidifier à plusieurs reprises lorsqu’ils sont chauffés et refroidis.
- Propriétés : Les revêtements en poudre thermoplastiques offrent plusieurs avantages, notamment une excellente résistance à l’abrasion, une flexibilité, une adhérence, une résistance chimique et une résistance aux chocs. Ils peuvent également être recyclés et reformés plusieurs fois sans perdre leurs propriétés.
- Applications : Les revêtements en poudre thermoplastiques sont utilisés dans une variété d’applications industrielles et commerciales, y compris l’automobile, l’électronique, le mobilier, l’aérospatiale, les équipements sportifs, les appareils ménagers et bien d’autres. Ils sont particulièrement adaptés aux applications nécessitant une résistance élevée à l’usure, une flexibilité ou une résistance chimique.
- Avantages : Les revêtements en poudre thermoplastiques offrent plusieurs avantages par rapport aux revêtements liquides traditionnels, notamment une meilleure efficacité de la matière, une application plus propre, des temps de traitement plus courts, une meilleure adhérence et une plus grande résistance à l’usure.
En conclusion, le revêtement en poudre thermoplastique est une solution polyvalente et efficace pour fournir une protection durable et esthétique aux surfaces dans une variété d’applications industrielles et commerciales. Son processus d’application et ses propriétés uniques en font un choix attrayant pour de nombreux secteurs.
Application automatique de poudre
L’application automatique de poudre est un processus utilisé dans l’industrie du revêtement par poudrage pour appliquer de manière précise et efficace des revêtements en poudre sur des pièces ou des substrats. Cette méthode utilise des équipements automatisés pour pulvériser la poudre de manière uniforme sur la surface à revêtir. Voici une description détaillée de l’application automatique de poudre :
- Équipements : L’application automatique de poudre fait appel à une variété d’équipements automatisés, notamment des robots de pulvérisation, des pistolets de poudrage automatisés, des convoyeurs de pièces et des systèmes de contrôle intégrés. Ces équipements sont conçus pour fonctionner de manière coordonnée afin d’assurer une application précise et uniforme de la poudre sur les pièces.
- Préparation de la surface : Avant l’application de la poudre, la surface des pièces doit être préparée correctement pour garantir une adhérence optimale du revêtement. Cela peut impliquer le nettoyage, le dégraissage, le décapage chimique ou mécanique, ainsi que le prétraitement pour améliorer l’adhérence et la résistance à la corrosion.
- Système de transport : Les pièces à revêtir sont généralement transportées à travers le système d’application de poudre à l’aide de convoyeurs ou de systèmes de manipulation robotisés. Ces systèmes sont conçus pour déplacer les pièces de manière fluide et cohérente à travers les différentes étapes du processus de revêtement.
- Pulvérisation de la poudre : Une fois les pièces positionnées de manière appropriée, la poudre est pulvérisée sur leur surface à l’aide de robots de pulvérisation ou de pistolets de poudrage automatisés. Ces équipements sont programmés pour pulvériser la poudre de manière uniforme et contrôlée, en ajustant automatiquement des paramètres tels que la pression de l’air, le débit de poudre et la forme du jet en fonction des spécifications de revêtement.
- Cuisson : Après l’application de la poudre, les pièces revêtues sont transportées vers un four de cuisson où elles sont chauffées à des températures spécifiques pour fondre la poudre et la fusionner en un film continu. Ce processus de cuisson permet également de durcir le revêtement et d’améliorer ses propriétés physiques et chimiques.
- Contrôle qualité : Tout au long du processus d’application automatique de poudre, des systèmes de contrôle intégrés surveillent et vérifient la qualité du revêtement, en s’assurant qu’il respecte les spécifications de l’application. Cela peut inclure des systèmes de vision, des capteurs de couleur, des dispositifs de mesure de l’épaisseur du revêtement, entre autres.
- Avantages : L’application automatique de poudre offre plusieurs avantages par rapport aux méthodes manuelles, notamment une productivité accrue, une réduction des erreurs humaines, une uniformité de revêtement améliorée, une utilisation efficace de la poudre et une qualité de revêtement constante.
En résumé, l’application automatique de poudre est une méthode avancée et efficace pour appliquer des revêtements en poudre sur des pièces ou des substrats dans diverses applications industrielles. Elle permet d’obtenir des revêtements de haute qualité avec une productivité accrue et une efficacité opérationnelle optimisée.
Le revêtement de poudre lisse est une technique de revêtement par poudrage qui produit une surface finale uniforme et sans défauts. Ce processus est largement utilisé dans diverses industries pour fournir une finition esthétique et protectrice aux pièces et aux substrats. Voici une description détaillée du revêtement de poudre lisse :
- Préparation de la surface : Avant l’application de la poudre, la surface des pièces doit être préparée adéquatement. Cela implique généralement le nettoyage de la surface pour éliminer toute saleté, graisse, huile ou autres contaminants qui pourraient compromettre l’adhérence du revêtement. Des techniques de prétraitement telles que le décapage chimique, le sablage ou le dégraissage peuvent également être utilisées pour améliorer l’adhérence du revêtement.
- Application de la poudre : Une fois la surface préparée, la poudre est appliquée uniformément sur la pièce à l’aide d’un équipement de pulvérisation de poudre. Cette étape peut être effectuée manuellement ou automatiquement en fonction des besoins spécifiques de l’application. L’objectif est d’appliquer une couche de poudre uniforme et cohérente sur toute la surface à revêtir.
- Fusion : Après l’application de la poudre, les pièces revêtues sont placées dans un four de cuisson où la poudre est fondue et polymérisée pour former un film continu. Pendant le processus de fusion, la poudre liquéfiée se propage et s’étale pour former une couche lisse et uniforme sur la surface de la pièce. La température et le temps de cuisson sont soigneusement contrôlés pour garantir une fusion complète de la poudre sans surcuisson ni sous-cuisson.
- Refroidissement et durcissement : Après la fusion, les pièces revêtues sont refroidies à température ambiante pour durcir le revêtement. Pendant cette étape, le revêtement passe d’un état liquide à un état solide, formant une surface lisse et dure. Le temps de refroidissement dépend du matériau de la poudre utilisée et des spécifications du processus de revêtement.
- Inspection et finition : Une fois que les pièces revêtues ont refroidi, elles sont inspectées pour s’assurer qu’elles respectent les normes de qualité et les spécifications du client. Les retouches peuvent être effectuées si nécessaire pour corriger les défauts ou les imperfections. Une fois l’inspection terminée, les pièces revêtues sont prêtes à être expédiées ou utilisées dans leur application finale.
En résumé, le revêtement de poudre lisse est un processus efficace et polyvalent qui permet d’obtenir des finitions de haute qualité sur une variété de pièces et de substrats. Il offre une excellente résistance à la corrosion, à l’abrasion et aux intempéries, ainsi qu’une esthétique attrayante et uniforme.
Pulvérisation de poudre industrielle
La pulvérisation de poudre industrielle est une méthode utilisée dans l’industrie du revêtement pour appliquer des revêtements en poudre sur divers substrats et pièces. Cette technique est largement utilisée dans de nombreux secteurs pour fournir une protection efficace contre la corrosion, l’usure et les intempéries, ainsi que pour améliorer l’esthétique des produits finaux. Voici une explication détaillée de la pulvérisation de poudre industrielle :
- Préparation de la surface : Avant d’appliquer la poudre, la surface des pièces doit être préparée correctement pour assurer une adhérence optimale du revêtement. Cela implique généralement le nettoyage et le dégraissage de la surface pour éliminer toute saleté, huile ou autres contaminants. Des méthodes de prétraitement telles que le sablage, le décapage chimique ou le traitement de conversion peuvent également être utilisées pour améliorer l’adhérence du revêtement.
- Application de la poudre : Une fois la surface préparée, la poudre est appliquée sur les pièces à l’aide d’un équipement de pulvérisation de poudre. Cette étape peut être effectuée manuellement à l’aide de pistolets de poudrage ou automatiquement à l’aide de robots de pulvérisation. La poudre est électrostatiquement chargée pendant l’application
afin qu’elle soit attirée vers la surface des pièces, assurant une couverture uniforme et complète.
- Cuisson : Après l’application de la poudre, les pièces revêtues sont transportées dans un four de cuisson où elles sont chauffées à des températures spécifiques pour fondre la poudre et la fusionner en un film continu. Ce processus de cuisson permet également de durcir le revêtement et d’améliorer ses propriétés physiques et chimiques.
- Refroidissement et finition : Après la cuisson, les pièces revêtues sont refroidies à température ambiante. Une fois refroidies, elles peuvent être inspectées pour vérifier la qualité du revêtement et effectuer des retouches si nécessaire. Des méthodes de finition telles que le meulage, le polissage ou le revêtement supplémentaire peuvent également être utilisées pour améliorer l’esthétique ou les propriétés du revêtement.
- Applications industrielles : La pulvérisation de poudre industrielle est utilisée dans une variété d’applications industrielles, notamment dans les secteurs de l’automobile, de l’aérospatiale, des équipements lourds, de l’électronique, de l’ameublement, de la construction et bien d’autres. Elle est particulièrement appréciée pour sa capacité à fournir une protection durable contre la corrosion, l’usure et les intempéries, ainsi que pour sa polyvalence et sa rentabilité.
En résumé, la pulvérisation de poudre industrielle est un processus efficace et polyvalent qui permet d’appliquer des revêtements en poudre sur une grande variété de substrats et de pièces dans de nombreux secteurs industriels. Elle offre une excellente protection et une finition esthétique tout en étant économique et respectueuse de l’environnement.
La peinture en poudre est une technique de revêtement qui implique l’application d’une fine couche de poudre de résine pigmentée sur une surface métallique ou d’autres substrats. Cette poudre est ensuite fondue et solidifiée pour former un film de revêtement durable et résistant. Voici une explication détaillée de la peinture en poudre :
- Préparation de la surface : Avant d’appliquer la peinture en poudre, la surface des pièces doit être préparée en conséquence. Cela peut impliquer le nettoyage, le dégraissage, le sablage ou le décapage chimique pour éliminer les contaminants et assurer une bonne adhérence du revêtement.
- Application de la poudre : Une fois la surface préparée, la poudre de peinture est appliquée sur les pièces à l’aide d’un pistolet de pulvérisation. La poudre est généralement chargée électrostatiquement pour qu’elle adhère uniformément à la surface. Cette méthode permet une couverture efficace même sur des formes complexes et des zones difficilement accessibles.
- Cuisson : Après l’application de la poudre, les pièces revêtues sont placées dans un four où elles sont chauffées à des températures élevées. Pendant la cuisson, la poudre fond et se solidifie pour former un film continu et uniforme. Ce processus de cuisson permet également d’améliorer les propriétés du revêtement, telles que sa résistance à la corrosion, à l’abrasion et aux produits chimiques.
- Refroidissement et finition : Une fois la cuisson terminée, les pièces revêtues sont refroidies à température ambiante. Elles peuvent ensuite être inspectées pour vérifier la qualité du revêtement et effectuer des retouches si nécessaire. Des techniques de finition telles que le polissage ou le meulage peuvent également être utilisées pour améliorer l’aspect esthétique du revêtement.
- Avantages de la peinture en poudre : La peinture en poudre présente de nombreux avantages par rapport aux autres méthodes de revêtement, notamment une excellente résistance à la corrosion, une durabilité accrue, une large gamme de couleurs et de finitions, une application uniforme et une faible émission de composés organiques volatils (COV). De plus, les excédents de poudre peuvent être recyclés, ce qui en fait une option respectueuse de l’environnement.
En résumé, la peinture en poudre est une méthode de revêtement polyvalente et efficace largement utilisée dans de nombreux secteurs industriels pour fournir des finitions de haute qualité et durables sur une variété de pièces et de substrats.
La poudre de revêtement métallique est une formulation spéciale de poudre de revêtement qui contient des particules de métal pur ou allié. Cette poudre est utilisée dans le processus de revêtement par poudrage pour fournir une finition esthétique et fonctionnelle aux pièces et aux surfaces métalliques. Voici une explication détaillée de la poudre de revêtement métallique :
- Composition : La poudre de revêtement métallique est composée de particules de métal pur ou allié, généralement d’aluminium, de zinc, de cuivre, d’acier inoxydable ou d’autres métaux. Ces particules métalliques peuvent être combinées avec des résines polymères et des additifs pour améliorer les propriétés du revêtement.
- Aspect esthétique : Les revêtements métalliques offrent une esthétique distincte et attrayante, avec une brillance et une profondeur de couleur caractéristiques. Ils sont souvent utilisés dans les applications où l’aspect visuel est important, telles que les produits de luxe, les équipements décoratifs et les composants automobiles.
- Protection contre la corrosion : En plus de leur aspect esthétique, les revêtements métalliques offrent une excellente protection contre la corrosion. Les métaux tels que l’aluminium et le zinc ont des propriétés anticorrosion intrinsèques qui peuvent prolonger la durée de vie des pièces et des substrats revêtus.
- Applications : La poudre de revêtement métallique est largement utilisée dans une variété d’applications industrielles et commerciales. Elle est couramment utilisée pour revêtir des pièces et des composants dans les industries de l’automobile, de l’aérospatiale, de l’électronique, de la construction, des équipements de loisirs et bien d’autres.
- Processus de revêtement : La poudre de revêtement métallique est appliquée sur la surface des pièces à l’aide d’un équipement de pulvérisation de poudre. Une fois appliquée, la poudre est fondue et solidifiée lors du processus de cuisson pour former un film de revêtement durable et résistant.
- Finitions : Les revêtements métalliques peuvent être disponibles dans une variété de finitions, y compris des finitions brillantes, satinées, brossées ou texturées. Ces finitions peuvent être sélectionnées en fonction des préférences esthétiques du client et des exigences de l’application.
En résumé, la poudre de revêtement métallique est une option de revêtement polyvalente et attrayante qui offre à la fois une protection contre la corrosion et une esthétique supérieure. Elle est largement utilisée dans de nombreux secteurs pour fournir des finitions de haute qualité et durables sur une variété de substrats métalliques.
Application manuelle de poudre
L’application manuelle de poudre est une méthode courante pour appliquer des revêtements en poudre sur des pièces et des substrats dans divers secteurs industriels. Cette technique implique l’utilisation d’un pistolet de pulvérisation de poudre tenu à la main pour appliquer la poudre de revêtement de manière précise et contrôlée sur la surface des pièces. Voici une explication détaillée de l’application manuelle de poudre :
- Préparation de la surface : Avant d’appliquer la poudre, la surface des pièces doit être correctement préparée. Cela peut impliquer le nettoyage, le dégraissage et le séchage des pièces pour éliminer toute saleté, huile ou contaminants qui pourraient affecter l’adhérence du revêtement.
- Chargement de la poudre : La poudre de revêtement est chargée dans le réservoir du pistolet de pulvérisation. La poudre peut être préchargée dans le réservoir ou chargée manuellement à l’aide d’une trémie ou d’un récipient.
- Réglage du pistolet : Avant de commencer l’application, le pistolet de pulvérisation doit être réglé en fonction des spécifications du revêtement et des exigences de l’application. Cela peut inclure le réglage du débit d’air, de la pression de pulvérisation, de la quantité de poudre appliquée et de la forme du jet.
- Application de la poudre : Une fois le pistolet réglé, l’opérateur peut commencer à appliquer la poudre sur la surface des pièces en utilisant des mouvements fluides et réguliers. L’opérateur doit maintenir une distance constante entre le pistolet et la surface pour assurer une application uniforme.
- Contrôle de l’épaisseur du revêtement : Pendant l’application, l’opérateur doit surveiller et contrôler l’épaisseur du revêtement pour garantir une couverture adéquate tout en évitant les surcouches ou les sous-couches excessives.
- Cuisson : Une fois la poudre appliquée, les pièces revêtues sont transportées dans un four de cuisson où elles sont chauffées à des températures élevées pour fondre et solidifier la poudre. Ce processus de cuisson permet de former un revêtement uniforme et durable.
- Finition : Après la cuisson, les pièces revêtues peuvent être inspectées pour vérifier la qualité du revêtement et effectuer des retouches si nécessaire. Des techniques de finition telles que le meulage, le polissage ou le revêtement supplémentaire peuvent également être utilisées pour améliorer l’aspect esthétique du revêtement.
En résumé, l’application manuelle de poudre est une méthode efficace et polyvalente pour appliquer des revêtements en poudre sur une variété de substrats. Elle offre un contrôle précis sur le processus d’application et peut être utilisée pour des applications de petite à moyenne échelle dans divers secteurs industriels.
Poudre de revêtement anti-corrosion
La poudre de revêtement anti-corrosion est une formulation spéciale de poudre de revêtement conçue pour offrir une protection efficace contre la corrosion des surfaces métalliques exposées aux éléments environnementaux agressifs. Cette poudre contient généralement des additifs et des inhibiteurs de corrosion qui empêchent la formation de rouille et la détérioration des substrats métalliques. Voici une explication détaillée de la poudre de revêtement anti-corrosion :
- Formulation : La poudre de revêtement anti-corrosion est composée de résines polymères spéciales, de pigments anticorrosion tels que le zinc, l’aluminium ou le phosphate de zinc, ainsi que d’additifs inhibiteurs de corrosion. Ces composants travaillent ensemble pour former une barrière protectrice durable contre l’humidité, les produits chimiques et d’autres agents corrosifs.
- Protection multicouche : Les revêtements anti-corrosion peuvent être appliqués en plusieurs couches pour améliorer leur efficacité. Une couche de base anticorrosion est généralement suivie de couches supplémentaires de revêtements de finition pour fournir une protection supplémentaire et une esthétique améliorée.
- Adhérence et durabilité : La poudre de revêtement anti-corrosion adhère fermement à la surface métallique et forme un film continu et uniforme qui protège efficacement contre la corrosion. Ces revêtements sont résistants à l’abrasion, aux chocs et aux intempéries, ce qui garantit une durabilité à long terme dans des environnements extérieurs et industriels sévères.
- Applications : Les revêtements anti-corrosion sont largement utilisés dans une variété d’applications industrielles et commerciales, notamment dans les secteurs de l’automobile, de l’aérospatiale, de la construction navale, de l’énergie, de l’industrie chimique et pétrolière, ainsi que dans les infrastructures maritimes et côtières.
- Préparation de surface : Avant l’application du revêtement anti-corrosion, la surface métallique doit être correctement préparée pour assurer une adhérence optimale et une protection efficace contre la corrosion. Cela peut inclure le nettoyage, le dégraissage, le sablage, le décapage ou le traitement de conversion de la rouille pour éliminer les contaminants et les oxydations de surface.
- Processus d’application : La poudre de revêtement anti-corrosion peut être appliquée à l’aide de diverses techniques telles que la pulvérisation électrostatique, la pulvérisation manuelle ou automatique, ou l’immersion. Une fois appliquée, la poudre est fondue et solidifiée lors du processus de cuisson pour former un revêtement durable et résistant à la corrosion.
En résumé, la poudre de revêtement anti-corrosion est une solution efficace pour protéger les surfaces métalliques contre les effets nocifs de la corrosion. Elle offre une excellente adhérence, durabilité et résistance à une variété de conditions environnementales, ce qui en fait un choix idéal pour de nombreuses applications industrielles et commerciales nécessitant une protection à long terme contre la corrosion.
Le revêtement de poudre de polyuréthane est une méthode de revêtement utilisée pour protéger et embellir les surfaces métalliques et autres substrats. Ce type de revêtement offre une excellente résistance à l’abrasion, à la corrosion, aux produits chimiques et aux intempéries, ce qui en fait un choix populaire dans de nombreuses industries. Voici une explication détaillée du revêtement de poudre de polyuréthane :
- Composition : Le revêtement de poudre de polyuréthane est composé de résines de polyuréthane thermoplastique. Ces résines sont mélangées avec des pigments, des charges et des additifs pour créer une poudre fine qui peut être appliquée sur les substrats métalliques.
- Propriétés : Le polyuréthane est connu pour sa résistance exceptionnelle à l’abrasion, à la corrosion, aux produits chimiques et aux UV. Il offre également une excellente flexibilité, ce qui le rend adapté aux applications où le substrat est susceptible de se déformer ou de se plier. En raison de ses propriétés exceptionnelles, le revêtement de poudre de polyuréthane est souvent utilisé dans des environnements difficiles tels que les applications industrielles, les équipements lourds et les environnements extérieurs.
- Applications : Le revêtement de poudre de polyuréthane est largement utilisé dans de nombreux secteurs, y compris l’automobile, l’aérospatiale, les équipements industriels, les meubles d’extérieur, les équipements de jeu, les équipements médicaux et bien d’autres. Il est utilisé pour protéger les surfaces métalliques contre la corrosion, l’usure et les rayures, tout en offrant une finition esthétique attrayante.
- Processus d’application : Le revêtement de poudre de polyuréthane est appliqué à l’aide d’un équipement de pulvérisation de poudre, tel qu’un pistolet de pulvérisation électrostatique. Une fois la poudre appliquée, les pièces sont placées dans un four de polymérisation où elles sont chauffées à des températures élevées. Pendant le processus de cuisson, la poudre fond et se solidifie pour former un revêtement durable et résistant.
- Finitions : Le revêtement de poudre de polyuréthane est disponible dans une variété de finitions, y compris les finitions brillantes, satinées, mates et texturées. Ces finitions peuvent être sélectionnées en fonction des exigences esthétiques de l’application et des préférences du client.
En résumé, le revêtement de poudre de polyuréthane est une solution polyvalente et durable pour protéger les surfaces métalliques et autres substrats contre les dommages causés par l’abrasion, la corrosion et les produits chimiques. Il offre une excellente résistance et une esthétique attrayante, ce qui en fait un choix populaire dans de nombreuses industries.
Revêtement en poudre lisse
Le revêtement en poudre lisse est une technique de revêtement utilisée pour créer des surfaces lisses et uniformes sur une variété de substrats, notamment les métaux, le plastique et le bois. Cette méthode de revêtement offre une finition esthétique attrayante tout en fournissant une protection durable contre la corrosion, les rayures et l’usure. Voici une explication détaillée du revêtement en poudre lisse :
- Processus de revêtement : Le revêtement en poudre lisse commence par la préparation de la surface du substrat. Cela peut inclure le nettoyage, le dégraissage et le traitement de conversion pour éliminer les contaminants et assurer une adhérence optimale du revêtement. Une fois la surface préparée, la poudre de revêtement est appliquée uniformément sur le substrat à l’aide d’un équipement de pulvérisation de poudre.
- Application de la poudre : L’application de la poudre de revêtement peut être réalisée à l’aide de différentes techniques, telles que la pulvérisation électrostatique, la pulvérisation manuelle ou automatique, ou l’immersion. La poudre est chargée dans un pistolet de pulvérisation et projetée sur la surface du substrat, où elle adhère électrostatiquement avant d’être cuite pour former un revêtement durable.
- Cuisson : Une fois la poudre de revêtement appliquée, le substrat est placé dans un four de cuisson où il est chauffé à des températures élevées. Pendant le processus de cuisson, la poudre fond et se fond pour former un film solide et lisse sur la surface du substrat. La température et le temps de cuisson peuvent varier en fonction du type de poudre de revêtement utilisé et des spécifications du fabricant.
- Finition : Après la cuisson, le substrat revêtu est refroidi et inspecté pour assurer la qualité du revêtement. Des techniques de finition telles que le meulage, le polissage ou le sablage peuvent être utilisées pour améliorer l’aspect esthétique du revêtement et éliminer les imperfections éventuelles.
- Avantages : Le revêtement en poudre lisse offre plusieurs avantages par rapport aux autres méthodes de revêtement. Il produit une finition uniforme et sans défaut, résistante aux rayures, à l’abrasion et à la corrosion. De plus, il est respectueux de l’environnement car il ne contient pas de solvants volatils et génère peu de déchets.
En résumé, le revêtement en poudre lisse est une méthode efficace et polyvalente pour créer des surfaces esthétiques et durables sur une variété de substrats. Il est largement utilisé dans de nombreux secteurs industriels pour protéger les pièces et les composants contre les dommages et améliorer leur apparence visuelle.
L’ensemble d’application de poudrage est une technologie essentielle dans les industries modernes où les processus de revêtement par poudre jouent un rôle crucial. Ce système est conçu pour appliquer uniformément une poudre sèche sur des surfaces spécifiques, créant ainsi un revêtement durable et esthétiquement agréable. L’application de poudrage est largement utilisée dans des domaines variés, notamment l’automobile, l’aéronautique, la construction et les appareils ménagers, en raison de ses avantages en matière de durabilité, de résistance à la corrosion et de finition homogène.
Le principe de fonctionnement repose généralement sur un processus d’électrostatique, où la poudre, composée de particules polymères ou métalliques, est chargée électriquement avant d’être projetée sur une surface mise à la terre. Cette méthode garantit une adhésion optimale des particules de poudre, même sur des formes complexes ou irrégulières. Une fois appliquée, la poudre est thermiquement fixée dans un four, où elle fond et forme une couche homogène et résistante.
Les ensembles d’application de poudrage comprennent plusieurs éléments essentiels. Tout d’abord, il y a le pulvérisateur, qui peut être manuel ou automatique, équipé d’une buse spéciale pour assurer une distribution uniforme de la poudre. Ensuite, des systèmes de contrôle électronique permettent de réguler la pression d’air, le débit de poudre et les paramètres électrostatiques pour garantir une application précise et efficace. Les cabines de poudrage jouent également un rôle important en capturant l’excès de poudre, ce qui non seulement réduit les pertes de matériau, mais contribue également à maintenir un environnement de travail propre.
Un autre élément fondamental de l’ensemble est le système de récupération de poudre. Ce dispositif collecte et recycle la poudre non utilisée, offrant ainsi des avantages économiques et environnementaux. Les systèmes de récupération modernes utilisent des filtres à haute efficacité pour séparer la poudre des particules indésirables, permettant ainsi une réutilisation immédiate.
Les avantages de l’application de poudrage résident dans sa capacité à produire des finitions de haute qualité avec une efficacité accrue. Contrairement aux revêtements liquides traditionnels, les poudres ne contiennent pas de solvants, ce qui les rend plus respectueuses de l’environnement et moins nocives pour les opérateurs. De plus, le processus génère peu de déchets, car la plupart de la poudre non utilisée peut être récupérée et réutilisée. Enfin, les revêtements en poudre offrent une large gamme de textures et de couleurs, répondant ainsi aux exigences esthétiques et techniques des clients.
Cependant, la mise en œuvre de ces systèmes nécessite une expertise technique et un entretien régulier. Les paramètres de fonctionnement, tels que la tension électrostatique, la distance de pulvérisation et la température de durcissement, doivent être ajustés avec précision pour éviter des défauts tels que des bulles, des irrégularités ou une adhérence insuffisante. De plus, les ensembles d’application de poudrage doivent être régulièrement nettoyés pour éviter toute contamination croisée entre différentes couleurs ou types de poudre.
En conclusion, les ensembles d’application de poudrage représentent une technologie avancée qui allie performance, durabilité et respect de l’environnement. Leur adoption croissante dans diverses industries témoigne de leur efficacité et de leur polyvalence, faisant d’eux un pilier essentiel des processus de fabrication modernes.
Les innovations récentes dans le domaine des ensembles d’application de poudrage ont permis d’améliorer considérablement leur performance et leur adaptabilité. Par exemple, des systèmes automatisés dotés de capteurs intelligents et d’algorithmes de contrôle avancés permettent une optimisation en temps réel des paramètres de pulvérisation. Ces systèmes adaptatifs garantissent une couverture uniforme, même sur des géométries complexes, réduisant ainsi les retouches et augmentant la productivité.
Par ailleurs, les développements en matière de matériaux de poudrage ont élargi le champ d’application de cette technologie. Les nouvelles formulations de poudre, incluant des propriétés comme la résistance aux UV, l’anti-corrosion ou encore la conductivité électrique, permettent de répondre à des besoins spécifiques dans des secteurs de pointe tels que l’électronique ou les équipements médicaux. Ces poudres spécialisées, combinées à des ensembles d’application de haute précision, offrent des solutions sur mesure pour les exigences les plus strictes.
L’intégration des technologies numériques, notamment l’Internet des Objets (IoT), ouvre également de nouvelles perspectives. Les ensembles d’application modernes sont souvent équipés de dispositifs connectés qui collectent et analysent des données en continu. Ces systèmes permettent aux utilisateurs de surveiller les performances, de détecter les anomalies et de planifier la maintenance préventive, réduisant ainsi les temps d’arrêt et les coûts associés. Cette transformation numérique contribue également à une meilleure gestion des ressources, en optimisant la consommation de poudre et d’énergie.
Un autre axe d’évolution concerne la durabilité et l’impact environnemental. Les fabricants d’ensembles d’application de poudrage investissent dans le développement de systèmes à faible consommation énergétique et dans des technologies permettant une récupération encore plus efficace des poudres non utilisées. Ces efforts s’inscrivent dans une démarche globale de réduction des émissions de CO₂ et de minimisation des déchets industriels, en ligne avec les réglementations environnementales de plus en plus strictes à l’échelle mondiale.
Enfin, la formation et l’accompagnement des opérateurs jouent un rôle crucial dans la réussite de l’implémentation des ensembles d’application de poudrage. Même avec des équipements de pointe, l’expertise humaine reste essentielle pour configurer les systèmes, surveiller les processus et garantir un résultat final conforme aux spécifications. Les fabricants proposent désormais des programmes de formation complets, incluant des modules sur les techniques de pulvérisation, la maintenance et l’utilisation des systèmes automatisés.
Ainsi, l’avenir des ensembles d’application de poudrage s’annonce prometteur, porté par des innovations technologiques, une prise de conscience environnementale accrue et une recherche constante de performance et d’efficacité. Que ce soit dans l’industrie manufacturière traditionnelle ou dans des secteurs émergents, cette technologie continue de se positionner comme un choix incontournable pour les processus de revêtement modernes.
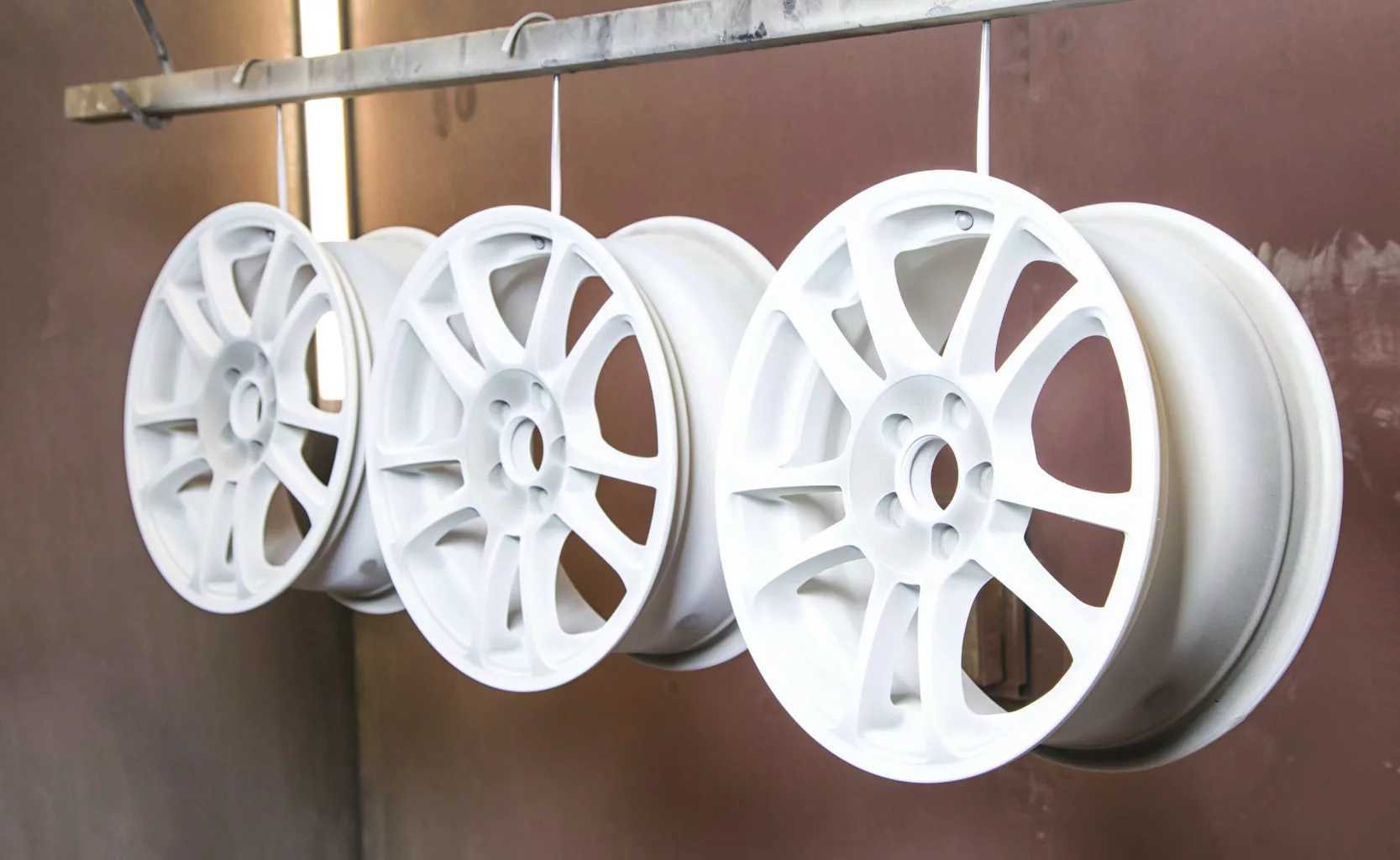
L’un des défis majeurs dans l’application de poudrage reste la gestion de la qualité du revêtement. La qualité du produit final dépend de plusieurs facteurs interconnectés, notamment la régularité de l’application, l’uniformité de la couverture et la bonne adhésion de la poudre sur la surface. À cet égard, les ensembles d’application de poudrage modernes sont de plus en plus équipés de technologies de contrôle qualité avancées. Ces systèmes intègrent des caméras haute résolution, des capteurs de température et d’humidité, et parfois même des dispositifs de mesure de l’épaisseur du revêtement en temps réel. Grâce à ces outils, les opérateurs peuvent ajuster immédiatement les paramètres de pulvérisation pour corriger toute irrégularité ou défaut, ce qui garantit un produit de qualité constante et réduit les risques de rejet ou de retouche.
La gestion de l’environnement de travail joue également un rôle essentiel dans l’efficacité de l’application de poudrage. Les environnements de pulvérisation doivent être soigneusement contrôlés pour éviter toute contamination ou variation des conditions qui pourrait affecter le processus. Les cabines de poudrage, les systèmes de filtration et les contrôles d’humidité et de température sont donc des éléments cruciaux. Des cabines de poudrage à haute efficacité équipées de filtres HEPA ou des systèmes de recyclage d’air optimisés permettent de maintenir un environnement propre et sécurisé. De plus, des équipements de protection individuelle (EPI) sont nécessaires pour garantir la sécurité des opérateurs, en particulier lorsque des poudres contenant des matériaux chimiques potentiellement dangereux sont utilisées.
L’optimisation de l’impact environnemental est un aspect qui continue de gagner en importance, particulièrement dans un contexte où la réglementation environnementale devient de plus en plus stricte. Les technologies d’application de poudrage ont donc évolué pour répondre à des exigences écologiques. Les nouvelles générations de poudres, par exemple, sont souvent exemptes de solvants et contiennent des composants moins polluants, contribuant ainsi à réduire l’empreinte carbone du processus de fabrication. De plus, l’optimisation du recyclage des poudres non utilisées et le système de récupération des excédents permettent de minimiser les déchets, ce qui est un aspect fondamental d’une production industrielle responsable.
Dans un contexte économique toujours plus compétitif, l’amélioration de la rentabilité est un enjeu majeur pour les industriels. Les ensembles d’application de poudrage sont conçus pour maximiser la productivité tout en réduisant les coûts opérationnels. L’automatisation de l’application, grâce à des robots de pulvérisation, permet d’atteindre des niveaux de précision et de rapidité inaccessibles à l’homme, tout en minimisant les erreurs. De plus, la possibilité de récupérer et de réutiliser la poudre non utilisée, combinée à une gestion plus précise des matériaux et de l’énergie, permet de réduire considérablement les coûts de production.
Les systèmes de poudrage à haute efficacité énergétique se sont aussi considérablement développés. Grâce à des améliorations dans la conception des équipements, les nouveaux ensembles consomment moins d’énergie, tout en offrant un rendement optimal. Cela se traduit par des économies significatives pour les entreprises, tout en contribuant à une réduction de l’empreinte énergétique de la production.
En outre, l’évolution de l’internet des objets (IoT) et de la connectivité dans les systèmes de pulvérisation permet désormais une gestion et un contrôle à distance plus poussés. Les utilisateurs peuvent accéder à des tableaux de bord et des rapports détaillés, analyser les performances en temps réel et ajuster les paramètres d’application depuis un poste centralisé. Cette connectivité assure non seulement un contrôle qualité plus rigoureux, mais permet également une meilleure planification de la maintenance et une gestion proactive des équipements.
Les ensembles d’application de poudrage ne sont pas seulement des outils de production, mais aussi des moteurs d’innovation. La recherche continue de nouveaux matériaux de poudrage, y compris des poudres thermodurcissables, des poudres métallisées ou encore des poudres céramiques, ouvre de nouvelles possibilités pour des applications de plus en plus diversifiées et complexes. Ces nouvelles poudres sont spécifiquement adaptées pour des secteurs tels que l’aérospatial, l’électronique de haute performance, et même les secteurs médicaux, où la précision et les propriétés spécifiques des revêtements sont cruciales.
En conclusion, l’évolution des ensembles d’application de poudrage reflète une quête constante de perfectionnement technique, d’efficacité économique et de responsabilité environnementale. Alors que l’industrie continue de se moderniser, les technologies de poudrage deviennent plus intelligentes, plus écologiques et plus rentables, répondant ainsi aux défis complexes du monde industriel moderne. Le progrès dans ce domaine promet de transformer non seulement la manière dont les revêtements sont appliqués, mais aussi l’ensemble des processus de production industrielle dans les années à venir.
Les ensembles d’application de poudrage jouent également un rôle clé dans l’esthétique et la durabilité des produits finis. La technologie permet de créer une vaste gamme de finitions, allant des surfaces texturées aux revêtements ultra-lisses, tout en garantissant une uniformité impeccable. Les innovations récentes dans les formulations de poudres offrent une palette quasi illimitée de couleurs, d’effets métalliques, de finitions mates ou brillantes, et même des revêtements fluorescents ou phosphorescents. Ces possibilités ouvrent la voie à des applications créatives dans des secteurs tels que le design, l’architecture et la fabrication de biens de consommation haut de gamme.
Dans le secteur industriel, la résistance chimique et mécanique des revêtements en poudre en fait une solution privilégiée pour les environnements exigeants. Les ensembles d’application de poudrage sont fréquemment utilisés pour protéger les structures métalliques contre la corrosion, les rayures, les intempéries et les produits chimiques agressifs. Des industries comme l’automobile, le ferroviaire et la construction en bénéficient particulièrement, car les revêtements en poudre prolongent la durée de vie des composants, réduisant ainsi les coûts de maintenance et de remplacement.
Un domaine en pleine expansion est celui des revêtements fonctionnels. Ces derniers ne se limitent pas à une fonction décorative ou protectrice, mais offrent des propriétés spécifiques pour des applications techniques avancées. Par exemple, des poudres conductrices d’électricité peuvent être utilisées dans la fabrication de composants électroniques, tandis que des poudres résistantes à la chaleur sont idéales pour les équipements soumis à des températures extrêmes, comme les fours industriels ou les moteurs d’avion. D’autres formulations innovantes incluent des propriétés antibactériennes pour les environnements médicaux et alimentaires, ou encore des capacités autonettoyantes pour des applications architecturales modernes.
Parallèlement, les exigences croissantes en matière de personnalisation poussent les fabricants à développer des ensembles d’application de poudrage plus flexibles et modulaires. Ces systèmes sont conçus pour passer rapidement d’une configuration à une autre, permettant ainsi des séries de production à petite échelle ou des lots personnalisés. Cette flexibilité est particulièrement précieuse dans des secteurs comme la fabrication de meubles, où les clients recherchent souvent des finitions uniques adaptées à leurs goûts spécifiques.
En termes de maintenance et de durabilité opérationnelle, les ensembles d’application de poudrage modernes intègrent des fonctionnalités de diagnostic avancé. Les capteurs intégrés surveillent en permanence l’état des composants critiques, comme les buses, les pompes à poudre ou les systèmes de filtration. En cas d’usure ou de dysfonctionnement, les utilisateurs sont immédiatement alertés, ce qui permet de planifier des interventions ciblées avant qu’un problème ne devienne critique. Cela réduit non seulement les temps d’arrêt imprévus, mais prolonge également la durée de vie des équipements, garantissant un retour sur investissement maximal.
Un autre aspect essentiel est la formation continue des opérateurs. Les fabricants d’ensembles d’application de poudrage reconnaissent que la technologie seule ne suffit pas à garantir des performances optimales. Des programmes de formation approfondis, incluant des modules sur l’entretien des équipements, l’optimisation des processus et la résolution des problèmes courants, permettent aux équipes de production de tirer pleinement parti de la technologie. En outre, certains fabricants proposent désormais des simulateurs numériques, permettant aux opérateurs de s’entraîner dans des environnements virtuels avant d’intervenir sur des systèmes réels.
Enfin, l’évolution des cadres réglementaires, notamment en matière de sécurité et d’environnement, influence fortement le développement des ensembles d’application de poudrage. Par exemple, dans de nombreux pays, les restrictions sur l’utilisation de composés organiques volatils (COV) et de substances chimiques dangereuses ont poussé l’industrie à adopter des formulations de poudres plus sûres et des équipements plus respectueux de l’environnement. De même, les normes de sécurité pour les zones où les poudres inflammables sont manipulées ont conduit à des avancées significatives dans la conception des cabines de poudrage et des systèmes de ventilation.
En résumé, les ensembles d’application de poudrage continuent d’évoluer pour répondre aux besoins diversifiés des industries modernes. Qu’il s’agisse de créer des produits visuellement attrayants, de protéger des équipements critiques ou de répondre à des exigences environnementales et réglementaires, ces systèmes restent au cœur des processus industriels de revêtement. À mesure que la technologie progresse, on peut s’attendre à ce que de nouvelles innovations émergent, rendant les ensembles d’application de poudrage encore plus performants, polyvalents et essentiels pour une production durable et efficace.
Système de Revêtement en Poudre
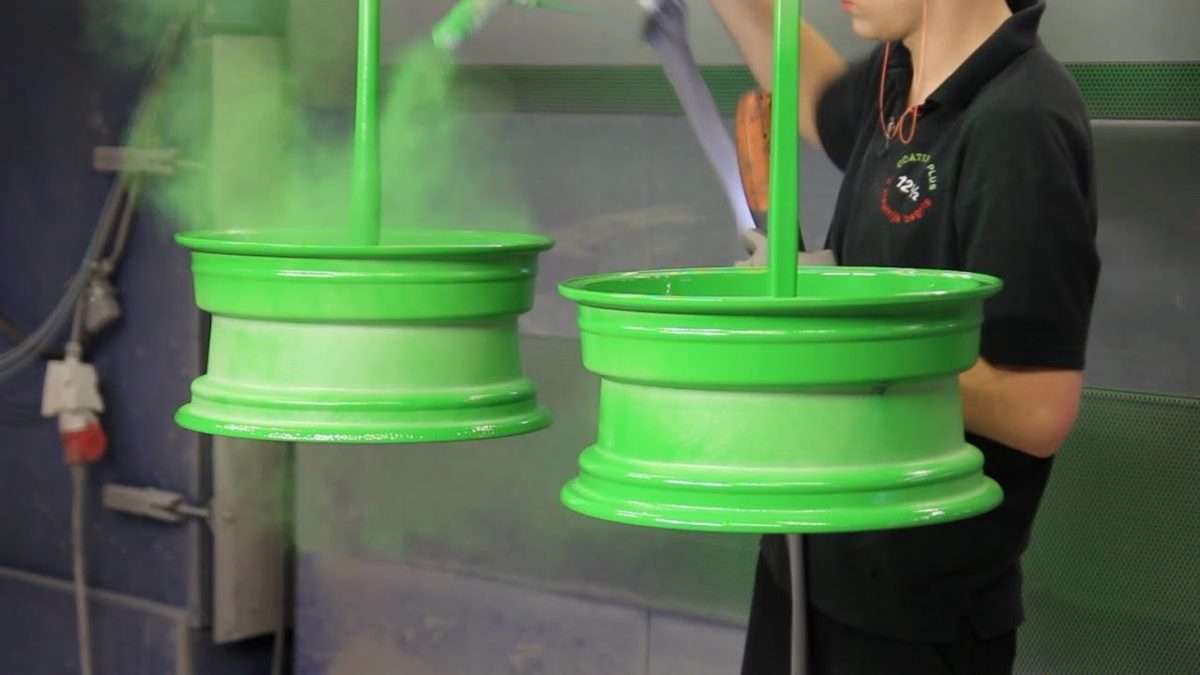
Un système de revêtement en poudre constitue une technologie clé dans les processus de finition industrielle, offrant une solution durable, esthétique et respectueuse de l’environnement pour la protection et la décoration des surfaces. Basé sur l’application de particules de poudre sèche, ce système est utilisé dans divers secteurs, allant de l’automobile à l’aérospatiale, en passant par l’électronique et la construction. Les avantages qu’il offre, tels qu’une résistance accrue aux conditions environnementales et une finition uniforme, en font une méthode privilégiée par les entreprises cherchant à allier performance et durabilité.
Le fonctionnement d’un système de revêtement en poudre repose généralement sur la technique d’électrostatique. La poudre, composée de particules polymères ou métalliques, est chargée électriquement à l’aide d’un pulvérisateur, puis appliquée sur une surface conductrice mise à la terre. Cette méthode garantit une adhésion optimale des particules, même sur des formes complexes. Une fois appliquée, la poudre est thermiquement durcie dans un four, où elle fond pour former une couche homogène, résistante et durable.
Les principaux composants d’un système de revêtement en poudre comprennent un pulvérisateur, une cabine de pulvérisation, un four de durcissement et un système de récupération de poudre. Le pulvérisateur peut être manuel ou automatique, équipé de technologies avancées pour assurer une application uniforme. Les cabines de pulvérisation sont conçues pour capturer l’excès de poudre et réduire les pertes, tandis que le four joue un rôle crucial dans le durcissement, où la température et le temps sont précisément contrôlés pour garantir des propriétés mécaniques et esthétiques optimales au revêtement. Les systèmes de récupération de poudre, quant à eux, permettent de recycler la poudre non utilisée, réduisant ainsi les coûts et l’impact environnemental.
L’un des avantages majeurs des systèmes de revêtement en poudre est leur respect de l’environnement. Contrairement aux peintures liquides traditionnelles, les poudres ne contiennent pas de solvants ni de composés organiques volatils (COV), ce qui réduit les émissions nocives. De plus, la possibilité de récupérer et de réutiliser la poudre excédentaire contribue à limiter les déchets industriels. Ces caractéristiques font des systèmes de revêtement en poudre un choix de plus en plus prisé dans les industries soucieuses de leur empreinte écologique.
Les systèmes modernes intègrent des technologies avancées pour améliorer leur efficacité et leur flexibilité. Par exemple, l’automatisation et la robotisation permettent de traiter rapidement de grandes quantités de pièces tout en maintenant une précision élevée. Les capteurs intelligents et les systèmes connectés permettent un contrôle en temps réel des paramètres critiques tels que la tension électrostatique, le débit de poudre et la température de durcissement. Ces innovations garantissent une qualité constante et réduisent les retouches ou les rejets.
En termes d’applications, les systèmes de revêtement en poudre sont extrêmement polyvalents. Ils sont utilisés pour protéger les surfaces métalliques de la corrosion, augmenter leur résistance à l’usure ou leur conférer des propriétés spécifiques, comme la conductivité électrique ou la résistance aux rayures. Les formulations avancées de poudre permettent également de créer des effets visuels uniques, comme des finitions métallisées, mates ou texturées, répondant aux besoins esthétiques des clients. De plus, des poudres fonctionnelles, comme celles ayant des propriétés antibactériennes ou résistantes aux UV, ouvrent de nouvelles possibilités dans des secteurs spécialisés comme le médical et l’architecture.
Cependant, pour garantir des performances optimales, il est crucial de respecter des paramètres précis lors de l’utilisation d’un système de revêtement en poudre. Des variables telles que la distance de pulvérisation, la tension électrostatique et la température du four doivent être soigneusement ajustées en fonction des propriétés de la poudre et du substrat. Une formation approfondie des opérateurs est donc essentielle pour éviter des défauts tels que des bulles, des irrégularités de texture ou une adhésion insuffisante.
Les défis associés à ces systèmes incluent également la nécessité d’un entretien régulier pour prévenir les pannes et garantir la longévité des équipements. Les composants tels que les buses de pulvérisation, les filtres de récupération et les systèmes de ventilation doivent être nettoyés et inspectés régulièrement pour éviter tout problème. Les fabricants proposent souvent des contrats de maintenance et des diagnostics connectés pour assurer un fonctionnement optimal.
Enfin, l’avenir des systèmes de revêtement en poudre est marqué par une intégration croissante de technologies numériques et de nouvelles formulations de poudre. Les systèmes connectés permettent une surveillance et une gestion à distance, tandis que les progrès dans les matériaux de poudrage offrent des propriétés toujours plus adaptées aux besoins spécifiques des industries modernes. Cette combinaison de performance, de durabilité et de flexibilité promet de faire des systèmes de revêtement en poudre un pilier des processus de fabrication durable et innovante.
Les systèmes de revêtement en poudre représentent une technologie en constante évolution, soutenue par des innovations techniques et des avancées dans les formulations de poudres. Ces innovations répondent aux exigences croissantes des industries modernes, telles que la durabilité accrue, la personnalisation des finitions, et le respect des réglementations environnementales.
Optimisation des Systèmes pour les Petites Séries et la Personnalisation
Avec la montée en puissance de la fabrication personnalisée et de la production en petites séries, les systèmes de revêtement en poudre évoluent pour offrir une flexibilité accrue. Les nouvelles configurations permettent de passer rapidement d’une couleur ou d’une texture à une autre, sans perte significative de temps ou de matière. Des systèmes de nettoyage automatique des cabines et des conduits facilitent cette transition, réduisant les délais d’arrêt entre deux séries.
La personnalisation est particulièrement recherchée dans les secteurs tels que la décoration intérieure, où des finitions uniques et des effets spéciaux, comme les poudres à effet nacré ou métallique, ajoutent une valeur esthétique élevée. Ces solutions permettent aux entreprises de répondre à des demandes spécifiques, tout en maintenant un niveau de productivité et de rentabilité élevé.
Revêtements Multifonctionnels et Applications Innovantes
Les progrès dans la formulation des poudres ont conduit à la création de revêtements multifonctionnels qui vont au-delà de la simple protection ou décoration. Par exemple :
- Revêtements isolants thermiques : Utilisés dans l’aérospatiale et l’automobile, ils protègent contre les températures extrêmes.
- Revêtements anti-corrosion avancés : Idéaux pour les infrastructures maritimes ou les pipelines industriels, ces revêtements prolongent la durée de vie des structures métalliques.
- Propriétés antibactériennes : Essentielles pour le secteur médical et alimentaire, ces revêtements offrent une protection contre les germes et micro-organismes.
- Poudres photoluminescentes ou phosphorescentes : Utilisées dans les secteurs de la sécurité ou du design, elles permettent une visibilité accrue dans l’obscurité.
Ces innovations permettent de répondre à des besoins spécifiques dans des environnements exigeants, tout en renforçant la position des systèmes de revêtement en poudre comme une solution incontournable.
Systèmes Connectés et Automatisés : Vers une Industrie 4.0
Les systèmes de revêtement en poudre s’intègrent de plus en plus dans l’écosystème de l’Industrie 4.0 grâce à l’utilisation de capteurs intelligents, d’outils d’analyse de données et de technologies IoT (Internet des Objets). Ces fonctionnalités connectées offrent :
- Surveillance en temps réel : Les opérateurs peuvent suivre les performances des équipements, détecter les anomalies et optimiser les processus à distance.
- Maintenance prédictive : Grâce aux algorithmes d’intelligence artificielle, les systèmes peuvent prédire les pannes potentielles et suggérer des interventions ciblées avant qu’un problème ne survienne.
- Rapports automatisés : Les systèmes génèrent des rapports détaillés sur la consommation de poudre, l’efficacité énergétique et la qualité des revêtements, aidant les entreprises à identifier les opportunités d’amélioration.
L’automatisation des systèmes va de pair avec l’utilisation de robots dans les cabines de pulvérisation. Ces robots garantissent une application uniforme et rapide, tout en s’adaptant à des géométries complexes. Ils réduisent également la dépendance à la main-d’œuvre humaine dans les tâches répétitives et augmentent la sécurité en limitant l’exposition des opérateurs à la poudre.
Considérations Environnementales et Développement Durable
Le respect de l’environnement est une priorité dans le développement des systèmes de revêtement en poudre. Les poudres modernes sont formulées pour minimiser leur impact environnemental tout en répondant aux exigences des normes internationales comme REACH ou RoHS.
Parmi les efforts notables :
- Formulations sans solvants : Les poudres ne contiennent pas de composés organiques volatils (COV), réduisant ainsi la pollution de l’air.
- Systèmes de récupération efficaces : Les équipements modernes récupèrent jusqu’à 98 % de la poudre excédentaire, limitant le gaspillage.
- Réduction de l’énergie consommée : Les fours de durcissement de nouvelle génération utilisent des technologies comme la conduction thermique avancée ou les infrarouges pour réduire les besoins énergétiques.
En outre, certains fabricants développent des poudres biodégradables ou fabriquées à partir de matériaux recyclés, ajoutant une dimension écologique supplémentaire aux revêtements.
Défis et Opportunités à Venir
Malgré ses nombreux avantages, l’adoption des systèmes de revêtement en poudre peut rencontrer certains défis :
- Investissement initial élevé : Les équipements de pulvérisation, les cabines et les fours représentent un coût important pour les entreprises, en particulier pour les petites structures.
- Limitations des substrats : Bien que les progrès permettent d’appliquer des poudres sur des matériaux comme le bois ou le plastique, les métaux restent les substrats les plus adaptés.
- Formation nécessaire : La maîtrise des équipements modernes et des paramètres complexes nécessite une formation approfondie des opérateurs.
Cependant, les opportunités offertes par cette technologie sont immenses. Avec l’essor de la fabrication additive et de l’impression 3D, les revêtements en poudre pourraient jouer un rôle crucial dans le traitement de pièces complexes produites par ces méthodes. De plus, les avancées dans les formulations de poudres fonctionnelles et les technologies d’automatisation continueront de repousser les limites des applications possibles.
Les systèmes de revêtement en poudre sont devenus une solution incontournable dans les processus industriels, combinant efficacité, durabilité et respect de l’environnement. Leur fonctionnement repose sur l’application de particules fines de poudre, généralement chargées électrostatiquement, sur une surface conductrice. Ce procédé garantit une adhérence homogène, même sur des géométries complexes, avant que la poudre ne soit thermiquement durcie pour former une couche protectrice et esthétique. Contrairement aux peintures liquides, ces systèmes n’utilisent pas de solvants, éliminant ainsi les émissions de composés organiques volatils et réduisant les risques pour l’environnement et la santé humaine.
La technologie évolue constamment, intégrant des équipements de plus en plus précis et adaptables. Les pulvérisateurs modernes offrent un contrôle précis du débit et de la charge électrostatique, permettant d’appliquer la poudre avec une grande régularité. Les cabines de pulvérisation, équipées de systèmes de récupération, maximisent l’efficacité en recyclant la poudre non utilisée, ce qui réduit les pertes et les coûts. Les fours de durcissement, quant à eux, bénéficient de technologies avancées pour optimiser la consommation énergétique, garantissant un durcissement uniforme sans compromettre la qualité du revêtement.
Les avantages offerts par les systèmes de revêtement en poudre ne se limitent pas à leurs performances mécaniques et esthétiques. Ils ouvrent également la voie à des applications innovantes grâce à des formulations spécialisées. Des revêtements antibactériens sont développés pour les environnements médicaux et alimentaires, tandis que des poudres résistantes aux rayons UV ou à la chaleur trouvent leur utilité dans les secteurs de la construction et de l’aérospatiale. Les finitions disponibles vont des textures rugueuses aux surfaces lisses et brillantes, en passant par des effets métalliques ou nacrés, permettant de répondre à des besoins esthétiques et fonctionnels variés.
La personnalisation est un aspect central des systèmes modernes. Les clients peuvent choisir parmi une palette étendue de couleurs et d’effets visuels, adaptés à des applications spécifiques ou à des designs uniques. Cela est particulièrement pertinent dans des secteurs comme le mobilier ou l’électronique, où la différenciation esthétique joue un rôle clé. De plus, les systèmes récents permettent de passer rapidement d’une couleur ou d’une texture à une autre, sans temps d’arrêt significatif, grâce à des mécanismes de nettoyage automatisés et à une conception modulaire des équipements.
Les innovations numériques transforment également la manière dont ces systèmes sont utilisés et gérés. Les capteurs intelligents intégrés dans les équipements surveillent en temps réel des paramètres critiques comme la température, la tension électrostatique ou le débit de poudre. Les données collectées permettent une optimisation continue des processus, réduisant les déchets et augmentant la qualité des revêtements. Ces technologies connectées facilitent également la maintenance prédictive, alertant les opérateurs avant qu’une panne ne survienne, ce qui minimise les interruptions et maximise la productivité.
Malgré ses nombreux avantages, cette technologie comporte des défis. Le coût initial des équipements reste élevé, ce qui peut être un frein pour certaines entreprises, notamment les petites structures. Par ailleurs, bien que des progrès aient été réalisés pour élargir la gamme des matériaux compatibles, les métaux demeurent les substrats les plus adaptés. Les substrats comme le bois ou les plastiques nécessitent des préparations spécifiques pour garantir une bonne adhésion de la poudre, ce qui peut augmenter les coûts et la complexité du processus.
Les préoccupations environnementales continuent de guider le développement de systèmes de revêtement en poudre. Les fabricants cherchent à réduire davantage l’empreinte écologique de leurs produits en améliorant les taux de récupération de poudre, en diminuant la consommation énergétique des fours et en développant des formulations de poudres à base de matériaux recyclés ou biodégradables. Ces efforts contribuent à aligner la technologie avec les normes internationales en matière de durabilité et à répondre aux attentes croissantes des consommateurs et des régulateurs.
Le potentiel d’innovation reste immense. L’intégration avec des technologies émergentes comme la fabrication additive offre des perspectives fascinantes, notamment pour le revêtement de pièces imprimées en 3D. Les applications industrielles pourraient également s’étendre grâce à des revêtements fonctionnels dotés de propriétés encore plus spécifiques, comme la conductivité électrique ou la résistance à des environnements chimiques extrêmes. En parallèle, la robotisation croissante promet d’améliorer encore davantage la précision et la rapidité des applications, tout en réduisant les risques pour les opérateurs humains.
Ainsi, les systèmes de revêtement en poudre ne cessent de démontrer leur pertinence dans un large éventail de secteurs, tout en s’adaptant aux exigences des marchés modernes. Leur capacité à combiner performance, esthétique et durabilité en fait une solution de choix pour les entreprises cherchant à optimiser leurs processus tout en répondant aux enjeux environnementaux et économiques actuels.
L’avenir des systèmes de revêtement en poudre est marqué par des avancées technologiques constantes et une adaptation aux besoins évolutifs des industries. Ces systèmes continuent de s’imposer comme des solutions fiables et polyvalentes, grâce à leur capacité à répondre simultanément à des exigences de qualité, de personnalisation et de durabilité. Les fabricants investissent massivement dans la recherche et le développement pour améliorer les performances des poudres et des équipements associés, en tenant compte des évolutions des normes environnementales et des attentes des consommateurs.
Les nouvelles formulations de poudres repoussent les limites des applications possibles. Par exemple, des revêtements à hautes performances capables de résister à des conditions environnementales extrêmes sont désormais disponibles pour les secteurs pétrolier, gazier et maritime. Ces poudres, conçues pour offrir une protection exceptionnelle contre la corrosion et l’abrasion, prolongent la durée de vie des structures tout en réduisant les coûts de maintenance. En parallèle, des poudres fonctionnelles émergent, comme celles intégrant des propriétés autolubrifiantes ou capables de dissiper la chaleur, ouvrant la voie à des applications spécifiques dans des domaines tels que l’électronique et l’ingénierie mécanique.
Dans le contexte de l’Industrie 4.0, l’automatisation et la connectivité transforment les processus de revêtement en poudre. Les systèmes intégrés permettent une personnalisation de masse tout en maintenant des niveaux élevés d’efficacité et de contrôle qualité. Les robots pulvérisateurs, équipés de capteurs avancés, peuvent ajuster automatiquement les paramètres en fonction des caractéristiques des pièces, garantissant une application parfaite même pour les formes les plus complexes. Ces robots sont capables de traiter des séries variées, passant rapidement d’un type de produit à un autre, ce qui est particulièrement utile dans les secteurs où la diversification des produits est cruciale.
Les cabines de pulvérisation évoluent également, devenant plus efficaces et faciles à entretenir. Les systèmes modernes utilisent des flux d’air optimisés pour minimiser la perte de poudre, tandis que des filtres de haute performance capturent les particules excédentaires pour les recycler. Ces améliorations contribuent à réduire l’impact environnemental et les coûts opérationnels, tout en maintenant un environnement de travail sûr et propre pour les opérateurs.
Le développement durable reste au cœur des préoccupations des fabricants et des utilisateurs de systèmes de revêtement en poudre. Les initiatives visant à rendre ces systèmes plus écologiques incluent l’optimisation des processus de durcissement pour réduire la consommation énergétique, ainsi que l’utilisation de matières premières renouvelables ou recyclées dans la fabrication des poudres. De plus, les recherches sur les revêtements biodégradables ou solubles dans l’eau gagnent en importance, bien qu’ils en soient encore à un stade préliminaire de développement.
En termes d’application, les systèmes de revêtement en poudre sont désormais présents dans des domaines inattendus. Par exemple, dans le secteur de l’art, les artistes utilisent des poudres spéciales pour créer des œuvres aux finitions uniques et durables. Dans l’industrie de la santé, des revêtements antibactériens spécifiques sont appliqués sur des dispositifs médicaux pour réduire le risque d’infection. Dans la construction, les architectes intègrent des revêtements en poudre dans les projets de façades et de structures, tirant parti de leur résistance aux intempéries et de leurs propriétés esthétiques.
La formation et l’expertise des opérateurs jouent un rôle clé dans la réussite des applications de revêtement en poudre. Bien que les systèmes automatisés réduisent la dépendance à l’intervention humaine, il reste essentiel de comprendre les principes fondamentaux du procédé pour optimiser les réglages, résoudre les problèmes potentiels et maintenir les équipements en bon état de fonctionnement. Les fabricants proposent de plus en plus des programmes de formation spécifiques, allant des bases du procédé aux techniques avancées de diagnostic et d’entretien.
En conclusion, les systèmes de revêtement en poudre représentent une technologie essentielle pour les industries modernes, offrant une combinaison unique de qualité, d’esthétique et de durabilité. Grâce à des innovations continues dans les équipements, les formulations de poudres et les procédés, ces systèmes s’adaptent aux défis de l’industrie contemporaine, tout en répondant aux attentes croissantes en matière de durabilité et de performance. Leurs possibilités d’évolution et d’application demeurent vastes, promettant un avenir riche en opportunités pour les secteurs qui les adoptent.
Pistolet de Poudrage
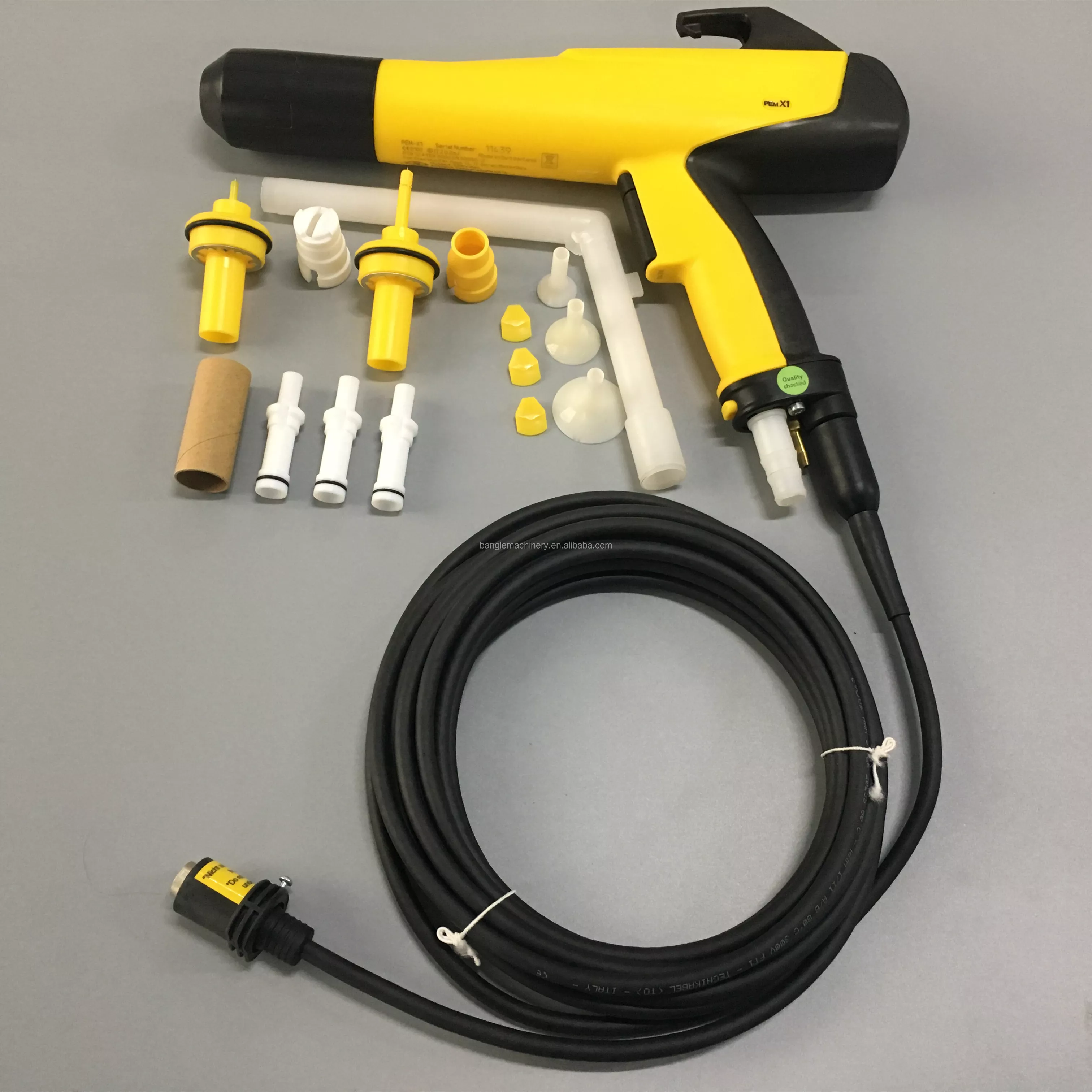
Le pistolet de poudrage est un outil essentiel dans les systèmes de revêtement en poudre, permettant l’application précise de la poudre sur des surfaces à traiter. Cet appareil fonctionne généralement en générant une charge électrostatique qui attire les particules de poudre sur la surface à revêtir, assurant ainsi une couverture uniforme et une adhésion optimale. Le pistolet de poudrage se distingue par sa capacité à appliquer la poudre de manière contrôlée et efficace, ce qui en fait un équipement incontournable dans les processus industriels de peinture en poudre, de protection anticorrosion et de décoration.
Le fonctionnement d’un pistolet de poudrage repose sur un système électrostatique qui charge les particules de poudre, généralement composées de résines et de pigments, lorsqu’elles sont envoyées à travers une buse. La pièce à traiter est généralement mise à la terre pour favoriser l’attraction des particules de poudre, ce qui permet une couverture uniforme de la surface, même dans les zones difficiles d’accès. L’utilisation de cette charge électrostatique permet également de minimiser le gaspillage de poudre, car les particules excédentaires sont souvent récupérées pour être réutilisées dans un système de récupération intégré.
Les pistolets de poudrage sont disponibles sous différentes configurations, allant des modèles manuels aux systèmes automatisés. Les pistolets manuels sont souvent utilisés pour des applications de petite à moyenne taille, offrant une grande flexibilité et un contrôle précis de l’application. Ils permettent à l’opérateur d’ajuster la pulvérisation en fonction des besoins spécifiques du projet. En revanche, les pistolets automatisés sont souvent utilisés dans des lignes de production à grande échelle, où la répétabilité et l’efficacité sont cruciales. Ces systèmes automatisés utilisent des robots pour diriger le pistolet de poudrage avec une grande précision, garantissant une couverture homogène et un temps de cycle réduit.
Un autre aspect important des pistolets de poudrage modernes est leur capacité à s’adapter à différents types de poudres. En effet, selon la formulation de la poudre, il peut être nécessaire d’ajuster les paramètres du pistolet, comme le débit d’air, la pression ou la tension électrostatique. Les pistolets de poudrage de haute qualité disposent de systèmes de réglage fin permettant de personnaliser ces paramètres pour obtenir les meilleurs résultats possibles en fonction du type de surface et de la poudre utilisée. Par exemple, les poudres thermodurcissables nécessitent un contrôle précis de la température et de la pression pour garantir un durcissement optimal, tandis que les poudres métalliques peuvent exiger un contrôle plus strict de la charge électrostatique pour éviter les risques de surpulvérisation.
Les pistolets de poudrage sont également conçus pour être ergonomiques et faciles à utiliser. Ils sont souvent équipés de poignées antidérapantes et de systèmes de déclenchement qui permettent une application confortable pendant de longues périodes de travail. Les modèles plus avancés disposent de dispositifs de contrôle de la pulvérisation qui permettent de moduler la quantité de poudre appliquée et de contrôler la largeur du jet, assurant ainsi une couverture uniforme même sur des surfaces complexes ou irrégulières.
L’entretien des pistolets de poudrage est un aspect essentiel pour garantir leur longévité et leur performance. En raison de l’accumulation de poudre et des résidus, il est nécessaire de nettoyer régulièrement les buses et les filtres du pistolet pour éviter les obstructions et maintenir un débit constant. Certains pistolets sont équipés de systèmes de nettoyage automatiques ou semi-automatiques, permettant de simplifier cette tâche et de réduire le temps d’arrêt des équipements. Un nettoyage régulier est crucial pour assurer une performance constante et prévenir les défauts d’application, comme les irrégularités dans la couverture de la poudre.
L’optimisation de l’utilisation des pistolets de poudrage repose également sur l’adaptation des paramètres en fonction du type de pièce à revêtir. Par exemple, la distance entre le pistolet et la surface, l’angle de pulvérisation et le débit d’air peuvent être ajustés pour garantir que chaque pièce reçoive une couverture uniforme et que la poudre soit correctement fixée avant le durcissement. Les systèmes modernes de pistolets de poudrage intègrent souvent des dispositifs de contrôle numériques, permettant de paramétrer facilement ces réglages pour différents types de pièces ou d’applications.
En plus de leurs fonctions de base, les pistolets de poudrage peuvent être utilisés dans des applications spécialisées telles que le revêtement de pièces complexes, la protection contre la corrosion dans les environnements industriels sévères, et la création de finitions décoratives uniques. Grâce à leur capacité à travailler avec une large gamme de poudres, y compris des poudres métalliques, des poudres à effet spécial ou des poudres résistantes aux UV, ces outils sont d’une grande polyvalence et répondent aux besoins d’industries variées, telles que l’automobile, l’aérospatiale, les équipements de loisirs et la construction.
En conclusion, le pistolet de poudrage est un instrument essentiel pour l’application de revêtements en poudre dans les processus industriels. Grâce à sa précision, sa polyvalence et sa capacité à s’adapter à différents types de poudres et de surfaces, il permet d’obtenir des résultats de haute qualité tout en réduisant les déchets et en augmentant l’efficacité. Les innovations continues dans le domaine des pistolets de poudrage, telles que l’intégration de technologies intelligentes et de systèmes de nettoyage automatisés, contribuent à renforcer leur rôle central dans l’industrie moderne.
Les progrès technologiques continuent de pousser l’évolution des pistolets de poudrage, particulièrement en ce qui concerne la gestion de la consommation de poudre et l’amélioration de la qualité du revêtement. Les derniers modèles de pistolets incluent des fonctionnalités avancées, telles que des contrôles électroniques et des affichages numériques, qui permettent de suivre et d’ajuster en temps réel les paramètres de pulvérisation. Ces outils offrent ainsi une flexibilité accrue dans la gestion des différentes applications de revêtement et une précision plus grande dans le résultat final.
L’un des domaines de recherche et d’innovation est l’optimisation de l’efficacité énergétique des pistolets de poudrage. Par exemple, des technologies avancées sont utilisées pour minimiser l’énergie nécessaire à la pulvérisation tout en maximisant la quantité de poudre qui adhère à la surface. L’un des aspects clés de cette évolution est l’amélioration de la gestion de l’air comprimé. De nouveaux systèmes permettent un contrôle plus précis du débit d’air, ce qui réduit les coûts énergétiques tout en maintenant une application efficace et uniforme. Cette approche contribue à la réduction de l’empreinte carbone des processus industriels et améliore la rentabilité des systèmes de revêtement en poudre.
Les pistolets de poudrage de demain incluront probablement une plus grande intégration avec les systèmes automatisés et connectés. L’utilisation d’outils numériques et de capteurs intelligents permettra d’optimiser encore davantage le processus de revêtement. Par exemple, grâce à l’intelligence artificielle, les pistolets pourront analyser en temps réel les conditions de surface et ajuster automatiquement les paramètres de pulvérisation pour assurer une couverture parfaite. Ces systèmes intelligents pourront aussi anticiper des déviations dans le processus, comme une perte de charge électrostatique ou une variation de l’humidité de l’air, et ajuster les paramètres de pulvérisation pour compenser ces effets.
En parallèle, l’automatisation des lignes de revêtement en poudre devrait se développer davantage avec l’intégration de robots autonomes équipés de pistolets de poudrage. Ces robots sont capables de naviguer de manière autonome autour des pièces, en optimisant leur trajectoire pour garantir une application uniforme du revêtement. Cette approche réduit le besoin de main-d’œuvre humaine pour les tâches répétitives et augmente l’efficacité de la production, tout en améliorant la sécurité des opérateurs.
La durabilité reste également un aspect important dans l’évolution des pistolets de poudrage. Avec la croissance des préoccupations écologiques et la pression des réglementations environnementales, les fabricants de pistolets cherchent à améliorer l’impact environnemental de leurs produits. Cela inclut la réduction des déchets de poudre et la mise au point de modèles qui consomment moins d’énergie. En outre, des recherches sont en cours pour développer des pistolets fabriqués à partir de matériaux durables, résistants à l’usure et facilement recyclables.
Un autre domaine d’innovation est l’amélioration de l’ergonomie et du confort d’utilisation. Les pistolets de poudrage de dernière génération sont conçus pour réduire la fatigue des opérateurs lors des longues sessions de travail. L’amélioration de la conception des poignées et l’ajout de systèmes de réduction des vibrations rendent l’utilisation plus agréable et plus sécurisée. Les fabricants intègrent également des systèmes qui permettent une prise en main plus facile et un contrôle plus précis, ce qui diminue les risques d’erreurs humaines et améliore la qualité des revêtements.
L’une des applications les plus innovantes des pistolets de poudrage se trouve dans l’industrie de la réparation et de la rénovation. Dans ces domaines, les pistolets sont utilisés pour appliquer des revêtements sur des pièces usées ou corrodées, leur permettant de retrouver une apparence et une fonctionnalité proches de l’état neuf. En outre, les pistolets de poudrage peuvent être utilisés dans des secteurs spécialisés comme l’industrie du meuble ou la décoration d’intérieur, où des revêtements décoratifs personnalisés sont de plus en plus demandés.
Les pistolets de poudrage se sont donc diversifiés et sont aujourd’hui essentiels dans des secteurs aussi variés que l’automobile, l’aérospatiale, l’électronique, l’ameublement et bien d’autres. Leurs capacités à appliquer des revêtements avec précision et à s’adapter à des besoins variés de production et de personnalisation font d’eux des outils de choix pour les industries modernes. De plus, la tendance vers des solutions plus écologiques et plus efficaces, combinée à l’intégration des technologies numériques et de l’automatisation, annonce une évolution continue de cette technologie. Les pistolets de poudrage de demain seront probablement encore plus intelligents, plus durables et plus adaptés aux exigences complexes de la production industrielle de demain.
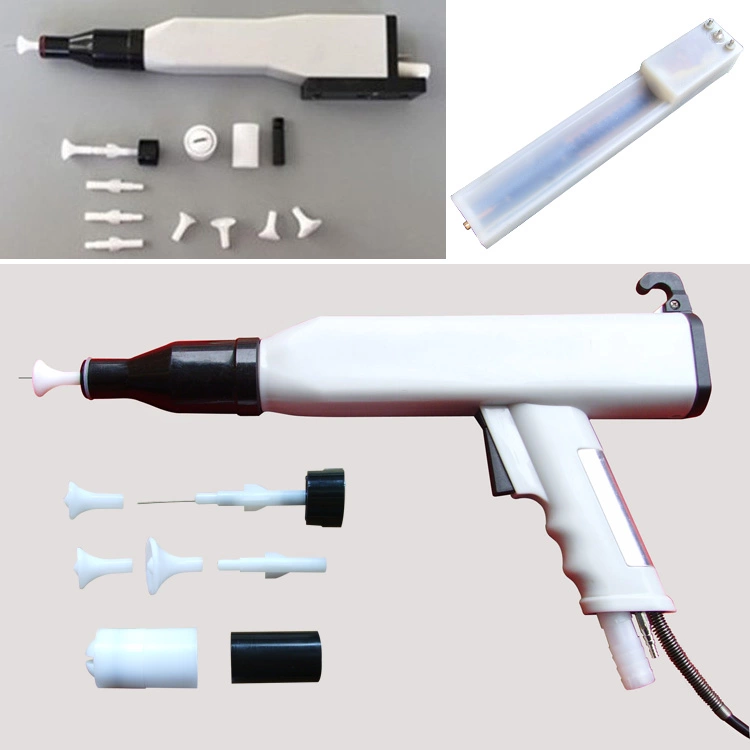
Les pistolets de poudrage, avec leurs caractéristiques toujours plus avancées, continuent de jouer un rôle clé dans la transformation numérique et l’optimisation des processus industriels. Leur évolution permet de répondre à des besoins de plus en plus spécifiques, où la précision, la rapidité et la flexibilité sont des critères incontournables. Par exemple, dans des secteurs comme l’aérospatial ou l’électronique, où les pièces nécessitent des revêtements aux propriétés uniques (résistance à la chaleur, isolation électrique, ou conductivité), les pistolets de poudrage sont désormais capables de travailler avec des matériaux de plus en plus complexes. Ces innovations ouvrent la voie à des applications nouvelles, tout en renforçant la performance des systèmes existants.
Un autre aspect crucial du développement des pistolets de poudrage est la réduction des coûts liés à la consommation de poudre. Les systèmes de récupération et de recyclage de la poudre sont de plus en plus perfectionnés, permettant de récupérer et réutiliser jusqu’à 90% de la poudre excédentaire. Cette réduction du gaspillage est particulièrement bénéfique pour les entreprises soucieuses de réduire leurs coûts opérationnels et d’optimiser leur chaîne de production. De plus, en récupérant la poudre excédentaire, les entreprises contribuent également à la réduction des déchets industriels, un objectif essentiel dans le cadre des démarches de durabilité et de responsabilité environnementale.
La question de la sécurité des opérateurs reste également primordiale dans le contexte des systèmes de revêtement en poudre. Les pistolets de poudrage de dernière génération sont équipés de dispositifs qui minimisent les risques d’exposition à la poussière et aux substances potentiellement dangereuses. Des systèmes de filtration d’air de haute performance sont intégrés dans les cabines de poudrage pour protéger les opérateurs des inhalations de particules fines. En outre, des mesures de sécurité électroniques sont souvent présentes pour empêcher toute application incorrecte de la poudre, réduisant ainsi les risques de défauts dans le revêtement et garantissant un environnement de travail plus sûr.
En ce qui concerne la gestion de la couleur et des effets décoratifs, les pistolets de poudrage ont également progressé. De nouveaux modèles permettent une plus grande flexibilité dans l’application de couleurs complexes, y compris les dégradés ou les effets métalliques et nacrés, qui sont particulièrement populaires dans les secteurs de la mode et du design. Cette capacité à appliquer des couleurs variées avec une grande précision est un atout majeur pour les industries où l’apparence visuelle des produits est aussi importante que leurs caractéristiques fonctionnelles. L’automatisation et la robotisation jouent ici un rôle central, car elles permettent de maintenir une régularité dans l’application des couleurs et des finitions, tout en accélérant le processus.
L’intégration des pistolets de poudrage dans des chaînes de production entièrement automatisées est une tendance qui se renforce avec la montée en puissance de l’industrie 4.0. Les pistolets sont désormais connectés à des systèmes de contrôle centralisés qui permettent aux opérateurs de surveiller en temps réel les paramètres de pulvérisation, d’ajuster la pression, la vitesse de l’air, et la charge électrostatique, et de détecter les anomalies avant qu’elles n’affectent la qualité du revêtement. Ces systèmes de surveillance avancée permettent non seulement de garantir une qualité constante mais aussi d’optimiser les temps de production, de réduire les erreurs humaines et d’augmenter la rentabilité globale des installations.
Les applications des pistolets de poudrage vont bien au-delà des industries traditionnelles. Par exemple, dans le secteur de la mode, des créateurs utilisent ces systèmes pour appliquer des poudres spéciales sur des accessoires ou des vêtements, donnant ainsi un aspect unique et innovant à leurs créations. Les progrès dans la formulation des poudres permettent même d’obtenir des effets tactiles, comme des textures douces ou rugueuses, élargissant ainsi les horizons créatifs des designers.
L’avenir des pistolets de poudrage sera également marqué par l’émergence de nouveaux matériaux de revêtement. Les poudres nanostructurées, par exemple, offrent des propriétés exceptionnelles, telles que des résistances accrues aux chocs, à l’usure ou aux températures extrêmes. L’utilisation de poudres avec des nanoparticules permet de créer des revêtements plus résistants tout en réduisant leur épaisseur, ce qui peut offrir des avantages considérables en termes de poids et de performance pour des applications spécifiques, comme dans l’industrie automobile ou aérospatiale.
La réduction de l’empreinte carbone et l’optimisation des processus en vue de la production durable continueront d’être des priorités. Les pistolets de poudrage, en raison de leur faible émission de substances volatiles et de leur efficacité dans l’utilisation de la poudre, sont déjà en avance dans le domaine de la réduction des impacts environnementaux. Cependant, avec les recherches en cours sur les technologies vertes, il est probable que de nouvelles générations de pistolets et de poudres émergent, encore plus efficaces, à la fois économiquement et écologiquement.
En conclusion, les pistolets de poudrage continuent de s’adapter aux évolutions technologiques, aux exigences des industries modernes et aux préoccupations environnementales. Ils se présentent comme des outils de plus en plus sophistiqués, permettant non seulement des applications de revêtements de haute qualité mais aussi une gestion optimisée des ressources et de la production. Grâce à l’automatisation, aux innovations en matière de contrôle qualité, à la durabilité accrue des matériaux et à une meilleure sécurité, ces équipements s’affirment comme des éléments clés dans les chaînes de production du futur. Les industries peuvent ainsi répondre à la demande croissante de produits performants, durables et esthétiques, tout en minimisant leur impact écologique et en maximisant leur rentabilité.
Machine de Poudrage
Les machines de poudrage sont des équipements industriels essentiels dans le domaine du revêtement en poudre, utilisées pour appliquer une fine couche de poudre sur une surface avant le durcissement thermique. Elles permettent de garantir un revêtement uniforme et de haute qualité tout en optimisant la consommation de poudre et en minimisant les déchets. Ces machines varient considérablement en termes de taille, de technologie et de capacité, en fonction des besoins spécifiques de chaque industrie. Elles jouent un rôle crucial dans de nombreux secteurs, tels que l’automobile, l’électroménager, la construction, l’aérospatiale, et bien d’autres, où des revêtements protecteurs ou décoratifs sont nécessaires.
Le fonctionnement d’une machine de poudrage repose sur un système de pulvérisation, généralement assisté par un dispositif électrostatique. Ce processus commence par le dépôt de la poudre sur la pièce à traiter. La machine utilise un compresseur d’air pour propulser la poudre à haute pression à travers un pistolet de poudrage ou une buse. La charge électrostatique appliquée sur la poudre permet à celle-ci d’adhérer à la surface à revêtir, qui est mise à la terre pour maximiser l’attraction des particules. Ce procédé est non seulement efficace pour appliquer une couche uniforme de revêtement, mais il réduit également le gaspillage de poudre, car les particules excédentaires peuvent être récupérées et réutilisées.
Les machines de poudrage modernes sont de plus en plus sophistiquées, intégrant des technologies avancées pour améliorer leur efficacité, leur flexibilité et leur performance. L’un des développements majeurs dans ce domaine est l’automatisation des systèmes de poudrage. Les lignes de production automatisées utilisent des robots ou des dispositifs mobiles pour déplacer les pièces dans les machines de poudrage. Ces robots sont capables de pulvériser la poudre avec une grande précision, ce qui garantit une couverture homogène, même pour des pièces de formes complexes ou difficiles à atteindre. Cette automatisation permet non seulement d’améliorer la qualité du revêtement mais aussi de réduire les coûts de main-d’œuvre et de production.
En parallèle, les machines de poudrage sont équipées de systèmes de contrôle numérique qui permettent de réguler de manière précise les différents paramètres du processus, tels que la pression d’air, la vitesse de la poudre et la charge électrostatique. Ces contrôles garantissent une application optimale de la poudre, en fonction du type de surface, de la poudre utilisée et des spécifications du revêtement souhaité. Ces ajustements permettent également de minimiser les erreurs humaines et d’assurer une qualité constante du revêtement à chaque cycle de production.
L’efficacité énergétique des machines de poudrage est un autre aspect clé de leur évolution. De nouvelles technologies permettent de réduire la consommation d’énergie tout en maintenant une application efficace de la poudre. Par exemple, l’optimisation des flux d’air et l’amélioration des moteurs des compresseurs permettent de réduire la quantité d’énergie nécessaire pour pulvériser la poudre, tout en maintenant une efficacité maximale. De plus, l’intégration de systèmes de récupération de la poudre excédentaire, qui permet de recycler la poudre non utilisée et de la réinjecter dans le système, contribue également à la réduction des coûts et des déchets.
La conception des machines de poudrage a également évolué en réponse aux préoccupations concernant la sécurité et l’ergonomie. Les machines modernes sont équipées de systèmes de filtration de haute performance pour éviter que les poussières de poudre ne s’échappent et ne contaminent l’air ambiant. De plus, des dispositifs de sécurité intégrés, tels que des arrêts automatiques ou des capteurs de détection de défaillances, garantissent que la machine fonctionne correctement et en toute sécurité. Ces machines sont également conçues pour être plus ergonomiques, ce qui facilite leur utilisation et leur entretien. Par exemple, des panneaux de contrôle plus intuitifs et des interfaces numériques simplifient l’ajustement des paramètres, tandis que des systèmes d’autonettoyage facilitent l’entretien.
Les machines de poudrage sont également conçues pour être plus polyvalentes, capables de travailler avec une large gamme de poudres. Les formulations de poudres ont évolué pour inclure des poudres époxy, polyester, hybrides et thermodurcissables, chacune ayant des propriétés spécifiques adaptées à différentes applications. Certaines machines de poudrage sont dotées de systèmes de dosage et de distribution de poudre spécialement conçus pour manipuler des poudres à effets spéciaux, comme les poudres métalliques ou les poudres à effet nacré. Ces machines sont souvent équipées de buses et de têtes de pulvérisation spéciales pour garantir que la poudre est appliquée de manière uniforme et avec l’effet désiré.
Un autre aspect important des machines de poudrage modernes est la gestion des différentes tailles de pièces. Les machines sont désormais capables de traiter des pièces de tailles variées, allant des petites pièces de composants électroniques aux grandes structures métalliques. Elles peuvent être équipées de systèmes de convoyage ou de dispositifs mobiles permettant de transporter efficacement les pièces à travers le processus de poudrage, tout en optimisant la distance et l’angle de pulvérisation pour une couverture maximale. Certains modèles sont également modulables, ce qui permet d’adapter la machine aux besoins spécifiques de production.
Les machines de poudrage de demain seront probablement encore plus intelligentes et intégrées aux systèmes de production industriels. L’Internet des objets (IoT) et l’intelligence artificielle (IA) devraient jouer un rôle important dans l’avenir des machines de poudrage. Par exemple, les machines pourraient être équipées de capteurs intelligents capables de surveiller en temps réel la qualité du revêtement, d’ajuster les paramètres de pulvérisation en fonction des conditions environnementales et d’envoyer des alertes aux opérateurs en cas de dysfonctionnement. L’analyse des données en temps réel pourrait également aider à anticiper les besoins de maintenance et à optimiser les processus pour améliorer la rentabilité et la durabilité des équipements.
La durabilité et l’efficacité des machines de poudrage sont également renforcées par des innovations en matière de matériaux. Les fabricants conçoivent des machines à partir de matériaux plus résistants à l’usure, capables de supporter des conditions de travail difficiles tout en prolongeant la durée de vie des équipements. Cela contribue non seulement à réduire les coûts de maintenance, mais aussi à réduire l’impact environnemental des machines.
En conclusion, les machines de poudrage jouent un rôle central dans la fabrication de produits de haute qualité, durables et esthétiques. Grâce à l’intégration de technologies avancées, telles que l’automatisation, la connectivité, et l’optimisation de l’énergie, ces équipements sont devenus plus efficaces, plus intelligents et plus respectueux de l’environnement. Leur capacité à s’adapter à une large gamme de poudres et de pièces, tout en garantissant un revêtement uniforme et durable, les rend indispensables dans de nombreuses industries. Avec la montée en puissance de l’industrie 4.0, l’avenir des machines de poudrage promet d’être marqué par une connectivité accrue, une personnalisation poussée et une gestion encore plus fine des processus de production.
L’évolution continue des machines de poudrage laisse entrevoir un avenir où l’intelligence artificielle (IA) et l’automatisation joueront un rôle prédominant dans leur performance et leur efficacité. Les machines seront non seulement capables de collecter et d’analyser des données en temps réel sur la qualité du revêtement, mais elles pourront également anticiper des ajustements nécessaires avant qu’un problème n’apparaisse. Par exemple, des capteurs intégrés pourront détecter des variations minimes dans la couverture de poudre et ajuster instantanément les paramètres de pulvérisation pour garantir une application homogène. Ce système d’auto-optimisation pourrait permettre de réduire les défauts de production, minimiser le gaspillage et augmenter la rentabilité.
L’intégration de l’Internet des Objets (IoT) dans les machines de poudrage ouvrira également la voie à des processus de production plus transparents et interconnectés. En collectant des données sur l’état de chaque machine et de chaque cycle de poudrage, les opérateurs pourront accéder à des tableaux de bord détaillant l’efficacité en temps réel. Cette visibilité accrue leur permettra de prendre des décisions éclairées pour améliorer la productivité, éviter les temps d’arrêt et planifier plus efficacement les opérations de maintenance. Par ailleurs, l’IoT permettra aux machines de communiquer entre elles pour ajuster les paramètres de production en fonction des besoins d’ensemble de la ligne de production.
Le rôle de la maintenance prédictive deviendra également plus significatif. En analysant les données recueillies par les capteurs, les algorithmes d’IA pourront détecter des anomalies avant qu’elles n’entraînent une défaillance majeure, permettant ainsi de planifier une intervention avant que des problèmes graves ne surviennent. Cela réduira non seulement les coûts liés aux réparations d’urgence, mais également les temps d’arrêt imprévus, garantissant ainsi une production plus fluide et efficace.
Les machines de poudrage futures seront également conçues pour une meilleure intégration avec des processus de fabrication personnalisée et à faible volume. Cela est particulièrement pertinent dans des secteurs comme l’aérospatiale ou la fabrication de produits de luxe, où la demande pour des solutions de revêtement uniques et de haute qualité est croissante. Par exemple, des machines capables de traiter des séries limitées avec des réglages rapides et faciles pour s’adapter à différentes spécifications de produit deviendront plus courantes. La possibilité de changer rapidement entre différents types de poudres ou de couleurs sans compromettre la qualité du revêtement sera cruciale pour répondre à ces besoins spécifiques.
En parallèle, l’efficacité des matériaux de revêtement continue de progresser. Les poudres plus avancées, y compris les poudres thermoplastiques ou à base de nanomatériaux, offrent des performances améliorées en termes de résistance aux températures extrêmes, aux produits chimiques et à l’usure. De telles poudres nécessitent des machines de poudrage adaptées pour garantir une application précise et uniforme. Les nouvelles formulations permettent également de réduire l’épaisseur du revêtement tout en maintenant des propriétés de protection optimales, ce qui réduit les coûts et le poids des pièces traitées.
Une autre tendance importante est l’augmentation des préoccupations environnementales. Les machines de poudrage sont de plus en plus conçues pour minimiser leur impact écologique. Les systèmes de filtration d’air et de gestion des poussières deviennent plus performants, permettant de capturer presque 100% des particules fines et de réduire les émissions dans l’environnement. De plus, les machines modernes utilisent des technologies qui permettent de récupérer la poudre excédentaire pour la réutiliser, diminuant ainsi le gaspillage de matériau. Cela est d’autant plus important dans un contexte où les entreprises cherchent à améliorer leur empreinte écologique, à respecter les normes environnementales strictes et à réduire les coûts liés à la consommation de matière première.
Les machines de poudrage modernes deviennent également plus intuitives et accessibles pour les opérateurs. Les interfaces numériques de plus en plus sophistiquées permettent un contrôle facile et précis des paramètres du processus. Des écrans tactiles, des systèmes de contrôle à distance et des applications mobiles permettent de configurer et de surveiller les machines sans avoir besoin d’être sur place. Ces innovations facilitent la formation des opérateurs, améliorent la réactivité et la flexibilité sur le site de production, et assurent un contrôle constant de la qualité du revêtement.
En outre, l’adoption croissante des technologies de réalité augmentée (RA) et de réalité virtuelle (RV) pourrait également transformer le secteur du poudrage. Ces technologies permettraient aux opérateurs de visualiser en temps réel l’application du revêtement et de détecter tout problème potentiel avant que le produit ne soit soumis à un durcissement. La RA pourrait être utilisée pour guider l’opérateur à travers les réglages des machines, améliorant ainsi la précision et réduisant les erreurs humaines. La RV pourrait, quant à elle, offrir des formations immersives pour les nouveaux opérateurs, les préparant à des situations réelles de production sans les risques associés.
L’avenir des machines de poudrage sera donc marqué par une convergence de technologies avancées, telles que l’intelligence artificielle, l’automatisation, l’IoT, et les matériaux de haute performance. Ces évolutions permettront non seulement d’améliorer l’efficacité et la flexibilité des systèmes de poudrage, mais aussi de réduire leur impact environnemental et d’augmenter la durabilité des produits finis. Avec ces avancées, les machines de poudrage continueront d’être des instruments clés dans la fabrication industrielle, permettant aux entreprises de répondre aux défis complexes de demain tout en offrant des produits de plus en plus performants et respectueux de l’environnement.
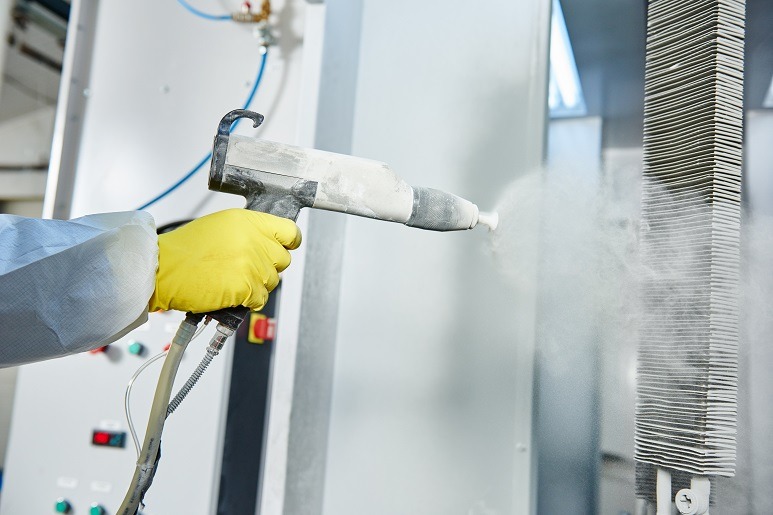
En poursuivant cette évolution, les machines de poudrage de demain seront non seulement plus intelligentes, mais aussi plus autonomes et intégrées dans des environnements de production intelligents. L’intégration de systèmes de gestion de la production en temps réel, permettant une surveillance continue de l’état des machines, optimisera encore davantage la gestion des flux de travail. Ces systèmes pourraient prédire les besoins en maintenance avant que des pannes ne surviennent, ou même ajuster les paramètres de production en fonction de l’analyse des performances passées. Ce niveau de sophistication offre un potentiel considérable pour améliorer l’efficacité globale des chaînes de production, réduire les coûts de fonctionnement et prolonger la durée de vie des équipements.
Dans les environnements industriels de plus en plus connectés, les machines de poudrage seront en mesure de dialoguer avec d’autres machines et systèmes au sein d’une usine. Par exemple, elles pourraient être connectées à des systèmes ERP (Enterprise Resource Planning) pour synchroniser les besoins en matériaux et les exigences de production. Cela permettrait une planification plus fluide des commandes et une gestion optimale des ressources, en garantissant une traçabilité complète de la production, de l’application de la poudre à la finalisation du produit.
Les machines de poudrage de demain se caractériseront aussi par une modularité accrue. La possibilité d’ajuster facilement la configuration des machines selon les besoins spécifiques de production deviendra un élément clé dans les usines modernes. Par exemple, il sera possible d’adapter rapidement la machine pour travailler avec des poudres de différentes compositions, pour traiter des objets de tailles variées ou pour répondre à des exigences de finitions spécifiques. Cette flexibilité sera particulièrement avantageuse dans les environnements de production en petite série ou sur mesure, où la capacité à ajuster rapidement les machines sans nécessiter des temps d’arrêt prolongés est essentielle.
Les applications futures des machines de poudrage iront au-delà des secteurs traditionnels pour inclure des domaines émergents, comme la fabrication de dispositifs médicaux ou les industries liées à la fabrication additive (impression 3D). Dans la fabrication de dispositifs médicaux, les poudres spécifiques utilisées, comme celles à base de polymères ou de céramiques, nécessitent des machines adaptées à ces matériaux. Les machines de poudrage devront donc évoluer pour répondre à des spécifications extrêmement strictes en termes de pureté, de précision et de contrôle des paramètres de pulvérisation. Les avancées en matière de poudres bioactives, par exemple, permettront la création de revêtements antibactériens ou biocompatibles sur des implants médicaux, et les machines devront être capables d’appliquer ces revêtements avec une extrême précision.
L’industrie de l’impression 3D, quant à elle, pourrait bénéficier des machines de poudrage adaptées à la fabrication de pièces par fusion sélective de poudre (SLS). Dans ce cas, les machines devront non seulement pulvériser la poudre de manière uniforme sur la surface de la pièce, mais aussi être capables de travailler avec des poudres métalliques, plastiques ou céramiques dans un environnement de production intégré. La compatibilité entre les procédés de poudrage et les technologies de fabrication additive pourrait permettre la création de pièces plus complexes et plus fonctionnelles, tout en optimisant le processus de production.
Les préoccupations environnementales continueront d’influencer les évolutions futures des machines de poudrage. Les fabricants chercheront à concevoir des équipements encore plus économes en énergie et à limiter leur empreinte écologique. Des progrès sont attendus dans les systèmes de gestion des déchets de poudres et les dispositifs de recyclage, avec l’objectif de réduire encore davantage le gaspillage. Les machines pourraient également intégrer des technologies de filtration plus avancées pour capter les microparticules et réduire leur dispersion dans l’environnement, tout en augmentant la qualité de l’air dans les installations de production.
Enfin, à mesure que les machines de poudrage se digitalisent, la formation des opérateurs deviendra plus facile et plus accessible. L’utilisation de simulateurs et de plateformes de réalité augmentée permettra aux employés de se familiariser avec les différents modèles de machines et d’apprendre à optimiser les processus sans risquer de commettre des erreurs en production. De plus, des formations interactives en ligne, combinées à des systèmes de support à distance, permettront aux opérateurs d’accéder à l’expertise technique et de résoudre rapidement les problèmes, quel que soit l’endroit où ils se trouvent.
En somme, l’avenir des machines de poudrage est indéniablement orienté vers des solutions plus intelligentes, plus flexibles, et plus respectueuses de l’environnement. L’optimisation des processus de production grâce à l’automatisation, l’analyse de données en temps réel et l’intégration avec des systèmes de gestion de la production intelligents transformera la manière dont les industries utilisent ces machines. Avec un accent croissant sur la durabilité et l’efficacité, les machines de poudrage continueront de jouer un rôle central dans les chaînes de production de demain, tout en offrant des produits finis de qualité supérieure, toujours plus innovants et respectueux des normes écologiques.
Machine Thermolaquage
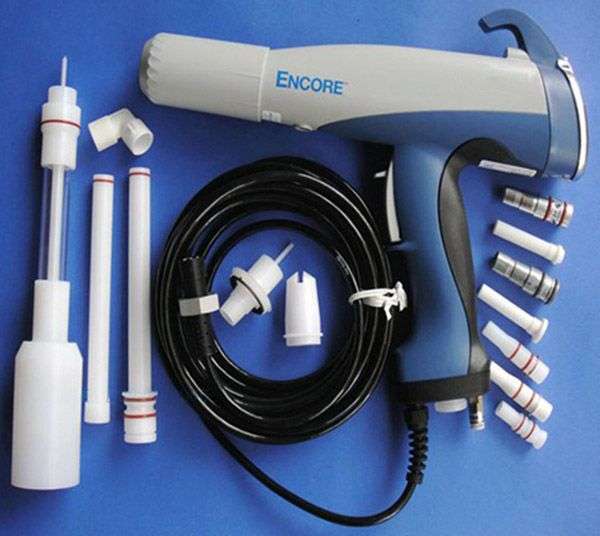
Les machines de thermolaquage, également connues sous le nom de machines de peinture en poudre, jouent un rôle essentiel dans le processus de revêtement des surfaces, particulièrement dans les secteurs industriels où les exigences de durabilité, de résistance aux conditions environnementales et d’esthétique sont cruciales. Le thermolaquage est un procédé de revêtement qui consiste à appliquer une poudre électrostatique sur une surface, puis à la durcir dans un four à haute température, formant ainsi un revêtement solide et résistant. Ces machines sont utilisées pour appliquer des revêtements sur une variété de matériaux, notamment les métaux, le plastique et d’autres matériaux industriels, dans des secteurs aussi variés que l’automobile, l’électroménager, la construction et la décoration.
Le principe de fonctionnement des machines de thermolaquage repose sur deux étapes principales : l’application de la poudre et le durcissement thermique. Dans la première phase, la poudre est pulvérisée sur la pièce à revêtir à l’aide d’un pistolet électrostatique, qui charge la poudre positivement. La pièce, quant à elle, est mise à la terre, créant une attraction électrostatique entre la surface et la poudre, ce qui permet une adhésion uniforme de la poudre à la surface de la pièce. Après application, la pièce est ensuite transférée dans un four à haute température, où la poudre fond et se lie chimiquement avec la surface pour former un film solide et durable.
Les machines de thermolaquage modernes sont équipées de plusieurs technologies avancées pour améliorer l’efficacité du processus et garantir un revêtement uniforme et de haute qualité. Un aspect clé de ces machines est la régulation précise des paramètres de pulvérisation, tels que la pression d’air, la vitesse de la poudre et la charge électrostatique. Ces réglages sont essentiels pour optimiser l’adhésion de la poudre à la pièce, minimiser le gaspillage et assurer une couverture complète de la surface, même sur des géométries complexes. De plus, la récupération de la poudre excédentaire est un autre élément important dans les machines modernes de thermolaquage. Cela permet de réduire le coût de la matière première et de minimiser les déchets, contribuant ainsi à une production plus écologique.
Les machines de thermolaquage sont également conçues pour être modulables et flexibles, afin de répondre aux besoins variés des différentes industries. Elles peuvent être adaptées à des lignes de production à grande échelle, permettant de traiter un grand nombre de pièces de manière continue et efficace. Ces machines sont souvent intégrées dans des systèmes de production automatisés, où les pièces sont transportées à travers les différentes étapes du processus, du prétraitement à la pulvérisation de la poudre, puis au durcissement dans le four. L’automatisation permet de réduire les interventions humaines, d’améliorer la constance de la qualité du revêtement et de réduire les coûts de main-d’œuvre.
Une autre caractéristique des machines de thermolaquage est la capacité de traiter une large gamme de matériaux et de poudres. Les poudres utilisées peuvent varier en fonction des propriétés spécifiques requises pour le revêtement, telles que la résistance aux rayures, aux produits chimiques, aux UV ou aux conditions climatiques extrêmes. Les machines de thermolaquage modernes sont conçues pour travailler avec différents types de poudres, telles que les poudres époxy, polyester, hybrides et thermodurcissables, chacune ayant des caractéristiques spécifiques adaptées à des applications particulières. De plus, ces machines peuvent être configurées pour appliquer des couches de différentes épaisseurs, selon les exigences du produit final.
Les systèmes de contrôle des machines de thermolaquage sont de plus en plus sophistiqués, permettant aux opérateurs de surveiller et d’ajuster les paramètres de pulvérisation en temps réel. Les machines sont souvent équipées de dispositifs de contrôle numérique qui affichent des informations détaillées sur les performances de la machine et les conditions du processus. Cela permet une gestion plus précise et une meilleure reproductibilité des résultats, tout en facilitant le diagnostic des problèmes potentiels et la maintenance préventive. Certains modèles avancés sont également dotés de systèmes de surveillance à distance, permettant aux opérateurs et aux gestionnaires de surveiller les opérations à distance via des interfaces mobiles ou des systèmes de gestion en cloud.
Les machines de thermolaquage modernes sont également de plus en plus efficaces sur le plan énergétique. Le processus de durcissement dans le four nécessite une source de chaleur, et les progrès technologiques ont permis de réduire la consommation d’énergie de ces systèmes. Des fours à chaleur recirculée ou des technologies de chauffage à infrarouge, par exemple, sont utilisés pour optimiser l’efficacité thermique et réduire les coûts énergétiques. De plus, l’intégration de systèmes de récupération de chaleur permet de recycler l’énergie utilisée dans le four, contribuant ainsi à réduire l’empreinte carbone du processus.
Les préoccupations environnementales ont également conduit à des innovations dans le domaine du thermolaquage. Les machines de thermolaquage sont maintenant conçues pour minimiser les émissions de poussières et les résidus dans l’air, grâce à des systèmes de filtration avancés. Ces systèmes de filtration sont capables de capturer les microparticules de poudre qui ne se déposent pas sur la surface de la pièce, réduisant ainsi la pollution de l’air et contribuant à un environnement de travail plus sûr. En outre, les fabricants de machines de thermolaquage s’efforcent d’utiliser des matériaux et des procédés de fabrication plus écologiques, tout en garantissant des performances élevées.
Les machines de thermolaquage sont aussi de plus en plus intelligentes, intégrant des technologies de l’Internet des Objets (IoT) pour collecter des données en temps réel sur les performances du système. Ces données peuvent être utilisées pour ajuster automatiquement les paramètres de la machine, mais aussi pour surveiller l’état des composants de la machine, ce qui permet d’anticiper les besoins en maintenance et de prolonger la durée de vie des équipements. L’analyse de ces données peut aussi être utilisée pour optimiser les processus de production, identifier les tendances et améliorer la qualité globale des produits finis.
L’avenir des machines de thermolaquage sera marqué par une intensification de l’automatisation et de la personnalisation. Les machines de thermolaquage seront capables de s’adapter à des demandes de production plus spécifiques, en offrant des options de personnalisation accrues, notamment en termes de couleurs, de textures et d’effets. Cela sera particulièrement utile dans des secteurs comme la décoration intérieure ou la fabrication de produits haut de gamme, où l’esthétique et les finitions sont primordiales. En outre, le développement de nouvelles poudres et de nouvelles technologies de pulvérisation ouvrira la voie à des applications innovantes dans des domaines comme l’aérospatiale, l’électronique, et la production de dispositifs médicaux.
En conclusion, les machines de thermolaquage sont des équipements industriels polyvalents et essentiels, qui continuent d’évoluer pour répondre aux besoins de production modernes. Leur capacité à appliquer des revêtements de haute qualité, durables et esthétiques sur une variété de matériaux, combinée à des technologies de pointe en matière de contrôle, d’automatisation et d’efficacité énergétique, fait d’elles des outils indispensables dans de nombreuses industries. L’avenir du thermolaquage sera marqué par une intégration accrue des technologies avancées, telles que l’intelligence artificielle, l’IoT et la personnalisation, contribuant à des processus de production plus intelligents, plus efficaces et plus écologiques.
L’évolution des machines de thermolaquage s’oriente vers un renforcement de la durabilité et de l’efficacité des processus industriels. Les avancées technologiques visent à rendre les équipements encore plus adaptés aux défis de l’industrie moderne, tout en répondant aux préoccupations écologiques croissantes. Le besoin d’une production plus verte et durable pousse les fabricants à intégrer des solutions innovantes et écologiques dans leurs machines, afin de réduire les impacts environnementaux.
L’un des domaines clés dans lequel ces machines continueront d’évoluer est l’amélioration de l’optimisation énergétique. Le chauffage des fours, étape indispensable dans le processus de thermolaquage, représente une part significative de la consommation d’énergie dans les systèmes de poudrage. Dans l’avenir, il est probable que les machines de thermolaquage utiliseront des technologies de pointe, telles que des systèmes à induction ou des chauffages à ondes de haute fréquence, qui permettent un contrôle plus précis de la température et une réduction des pertes thermiques. Cette évolution réduira la consommation d’énergie et contribuera à un processus de fabrication plus respectueux de l’environnement.
Les machines de thermolaquage devraient également devenir plus interconnectées grâce à l’Internet des Objets (IoT). Ce développement permettra une gestion en temps réel de la production, avec des retours d’information instantanés sur l’état des équipements, la qualité du revêtement et l’utilisation des matériaux. Les données collectées seront analysées pour offrir une maintenance prédictive, anticipant les pannes et minimisant les arrêts de production. De plus, des systèmes de contrôle en ligne permettront de réguler les paramètres du processus en fonction des conditions spécifiques de chaque pièce à traiter, offrant ainsi des solutions sur mesure adaptées à chaque production.
Une autre tendance émergente concerne la personnalisation des machines de thermolaquage pour répondre aux demandes spécifiques des différents secteurs. Par exemple, dans le secteur automobile, les machines devront être capables de traiter une large gamme de matériaux et de revêtements, avec des exigences strictes en matière de finition, de résistance et de performance. Pour répondre à ces besoins, les machines de thermolaquage seront capables de gérer des poudres haute performance, adaptées à des applications nécessitant des revêtements résistants aux températures extrêmes, aux produits chimiques ou aux conditions climatiques sévères. La flexibilité des machines à ajuster rapidement les paramètres pour différentes applications sera un atout majeur pour les industries à la recherche de solutions sur mesure.
Dans le secteur de la construction, par exemple, les machines de thermolaquage devront également être en mesure d’appliquer des revêtements sur des surfaces de grande taille, comme les éléments en acier ou en aluminium des structures de bâtiments. Ce type de production nécessitera des systèmes de poudrage à grande échelle, capables de traiter des volumes importants tout en maintenant une qualité uniforme. Les machines devront être conçues pour maximiser l’efficacité tout en minimisant l’empreinte environnementale, grâce à des systèmes de recyclage de la poudre excédentaire et des dispositifs de filtration avancés pour réduire les émissions de poussière.
Le secteur des dispositifs électroniques et médicaux représente également un marché en croissance pour les machines de thermolaquage. Les revêtements appliqués sur ces produits doivent répondre à des normes strictes en termes de pureté, de fonctionnalité et d’esthétique. Pour ces applications de niche, les machines devront être capables de travailler avec des poudres spéciales, telles que des poudres conductrices ou biocompatibles, tout en assurant un processus de revêtement précis et fiable. L’automatisation et la possibilité de contrôler des paramètres très fins, comme l’épaisseur de la couche et l’uniformité de l’application, seront des facteurs cruciaux pour garantir la qualité des produits finis.
Les machines de thermolaquage de demain seront également plus autonomes. L’intégration de technologies d’intelligence artificielle (IA) pourrait transformer le rôle des opérateurs, qui passeront de simples superviseurs à des gestionnaires de processus automatisés. Les machines pourront non seulement ajuster automatiquement les paramètres de fonctionnement en fonction des conditions de la production, mais aussi anticiper et résoudre des problèmes avant même qu’ils ne surviennent. Par exemple, si un défaut est détecté dans l’application du revêtement ou si des écarts par rapport aux normes de qualité sont identifiés, les machines pourront ajuster les réglages pour corriger ces anomalies, améliorant ainsi la qualité du produit final et réduisant les rebuts.
La connectivité accrue des machines permettra aussi aux opérateurs de suivre les performances à distance. Grâce à des systèmes cloud et des interfaces mobiles, il sera possible de superviser plusieurs lignes de production depuis n’importe quel endroit, et ce, en temps réel. Cette connectivité facilitera la gestion à distance et permettra une réactivité accrue face à des événements imprévus, tout en rendant les opérations de maintenance et de gestion des stocks plus efficaces.
En ce qui concerne les innovations matérielles, le développement de nouvelles poudres thermolaquées sera essentiel pour étendre les capacités des machines. De nouvelles formulations de poudres, qui offrent des propriétés telles que des revêtements autonettoyants, des résistances accrues aux rayures ou une meilleure durabilité face aux UV, deviendront de plus en plus populaires. Ces poudres spécifiques, adaptées à des besoins industriels particuliers, poseront de nouveaux défis pour les machines de thermolaquage, qui devront être capables de traiter ces matériaux tout en maintenant une performance optimale.
Les innovations dans le domaine de l’intelligence numérique et de la simulation de processus ouvrent également de nouvelles perspectives. Par exemple, des logiciels avancés pourraient être utilisés pour simuler le processus de thermolaquage avant même que la production ne commence. Ces simulations permettront aux fabricants d’optimiser le processus de revêtement en réduisant les erreurs, en ajustant les paramètres avant le début de la production et en améliorant la qualité des revêtements. Cela contribuera à un gain de temps et de ressources, tout en améliorant l’efficacité des lignes de production.
En conclusion, les machines de thermolaquage continueront d’évoluer pour répondre aux défis technologiques, économiques et environnementaux des secteurs industriels. Ces équipements deviendront plus intelligents, plus écologiques et plus adaptés aux exigences spécifiques de chaque domaine d’application. Grâce à l’intégration de technologies avancées comme l’intelligence artificielle, la connectivité IoT, la personnalisation et l’optimisation énergétique, les machines de thermolaquage du futur transformeront les processus de production en garantissant des produits de haute qualité, tout en réduisant les coûts et l’impact environnemental.
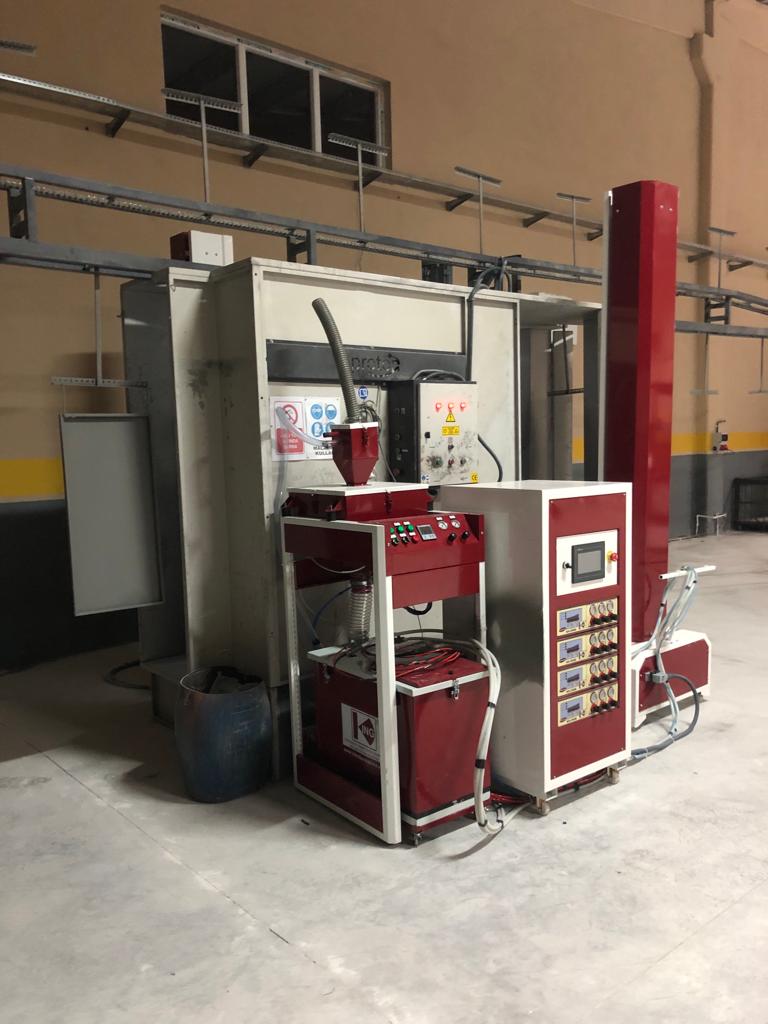
L’évolution des machines de thermolaquage se poursuit avec une attention particulière portée à l’intégration de technologies de pointe qui transformeront encore plus radicalement leur fonctionnement dans les années à venir. Une des innovations clés sera l’utilisation accrue de l’intelligence artificielle (IA) et du machine learning pour la gestion proactive de la production. L’IA pourra non seulement optimiser les paramètres en temps réel, mais aussi prédire les besoins en maintenance ou ajuster les processus de manière dynamique, en fonction des variations dans la production. Cela rendra les machines plus autonomes, réduisant la nécessité d’interventions humaines tout en garantissant une qualité constante et élevée du revêtement.
Dans le domaine de la personnalisation, les machines de thermolaquage deviendront de plus en plus flexibles et capables de répondre à des besoins de production très variés. L’adaptation rapide des machines à différentes tailles, formes et types de pièces est essentielle dans des secteurs comme l’automobile, l’aéronautique et l’électronique, où des exigences spécifiques en matière de revêtement sont fréquentes. Des systèmes automatisés, comme des robots de manipulation, pourraient être intégrés pour charger et décharger les pièces, permettant ainsi de traiter une plus grande variété d’articles tout en réduisant les délais de production.
Les machines de thermolaquage du futur seront également plus « écologiques » grâce à des processus améliorés de récupération de la poudre excédentaire et à l’utilisation de technologies de réduction des émissions polluantes. Par exemple, la récupération de la poudre non utilisée, associée à un contrôle plus rigoureux du flux d’air, minimisera la dispersion de la poudre dans l’environnement, réduisant ainsi le gaspillage de matériau et la pollution. L’amélioration des systèmes de filtration et des techniques de récupération d’énergie, comme les échangeurs thermiques ou les systèmes de récupération de chaleur, contribuera également à une consommation d’énergie plus rationnelle et à un moindre impact environnemental.
L’amélioration de l’expérience utilisateur à travers l’interface des machines sera un autre aspect clé du développement des machines de thermolaquage. Les systèmes d’interface utilisateur seront plus intuitifs, permettant une gestion simple et efficace des paramètres de production. Des écrans tactiles et des logiciels sophistiqués permettront aux opérateurs de contrôler facilement les réglages de la machine et d’ajuster rapidement les paramètres en fonction des spécifications de chaque projet. De plus, la réalité augmentée (RA) pourrait être utilisée pour fournir des informations en temps réel sur le processus de production, permettant aux opérateurs de visualiser et de diagnostiquer des problèmes de manière plus efficace.
Avec la montée de la fabrication additive (impression 3D), une nouvelle dimension pourrait être ajoutée aux machines de thermolaquage. En effet, certaines applications nécessiteront des revêtements ultra-précis et résistants pour des pièces imprimées en 3D. La thermolaquage pourrait offrir une solution parfaite pour protéger ces pièces tout en optimisant leur résistance aux conditions extérieures. L’intégration des machines de thermolaquage avec les technologies de fabrication additive pourrait faciliter la production de pièces complexes tout en offrant une finition de haute qualité, durable et esthétique.
L’avenir des machines de thermolaquage inclut aussi la mise en place de processus de production plus rapides. Les fabricants rechercheront des moyens d’accélérer le processus de durcissement de la poudre tout en maintenant des niveaux de qualité élevés. Cela pourrait inclure l’optimisation des fours de durcissement avec des technologies de chauffage plus efficaces, comme l’infrarouge à haute intensité, qui permet un durcissement plus rapide et plus uniforme sans compromettre la qualité du revêtement. De plus, les pièces pourraient être durcies à des températures plus basses grâce à des avancées dans les formulations de poudres, ce qui permettrait de réduire la consommation d’énergie et d’accélérer le processus de production.
Les machines de thermolaquage seront également de plus en plus adaptées aux nouvelles exigences légales et réglementaires, notamment en matière de sécurité, de santé au travail et de protection de l’environnement. Les réglementations concernant les émissions de poussières et de produits chimiques de plus en plus strictes entraîneront une innovation continue dans les systèmes de filtration et de récupération des particules fines. De même, des procédés plus écologiques, comme l’utilisation de poudres sans solvants et moins toxiques, deviendront la norme dans les industries. Les machines devront également être conformes aux nouvelles directives relatives à la gestion des déchets et au recyclage des matériaux, contribuant ainsi à une économie circulaire.
Une autre tendance importante sera l’intégration des machines de thermolaquage dans des chaînes de production plus larges et interconnectées. L’automatisation et la robotisation, associées à des systèmes de gestion de la production en temps réel, permettront aux machines de thermolaquage de communiquer avec d’autres machines et équipements de la chaîne de production. Cette intégration fluide permettra de maximiser l’efficacité et d’optimiser la planification et la gestion des stocks. Les informations collectées par les machines seront intégrées dans des systèmes ERP (Enterprise Resource Planning) pour améliorer la coordination et la traçabilité du processus de fabrication.
Enfin, la formation et la mise à jour continue des opérateurs deviendront essentielles dans un environnement de production de plus en plus numérisé. Les systèmes de formation basés sur la réalité virtuelle (VR) ou la réalité augmentée (AR) permettront aux opérateurs d’acquérir des compétences de manière plus interactive et immersive, tout en réduisant les risques d’erreur. Ces technologies permettront également de simuler des scénarios complexes, comme des pannes ou des ajustements de processus, et ainsi d’optimiser les interventions humaines dans les situations de production réelles.
En résumé, les machines de thermolaquage de demain se caractériseront par une forte intégration de technologies avancées, telles que l’intelligence artificielle, la réalité augmentée, et l’Internet des objets, rendant le processus de thermolaquage plus flexible, rapide, écologique et intelligent. Ces innovations ouvriront de nouvelles opportunités dans des secteurs en croissance, tout en contribuant à une production plus durable, plus efficace et mieux adaptée aux besoins spécifiques des différents marchés. Les progrès technologiques permettront également de minimiser l’impact environnemental des procédés tout en garantissant des produits de qualité supérieure, répondant aux exigences de plus en plus strictes des industries modernes.
Pistolet de Poudrage Électrostatique
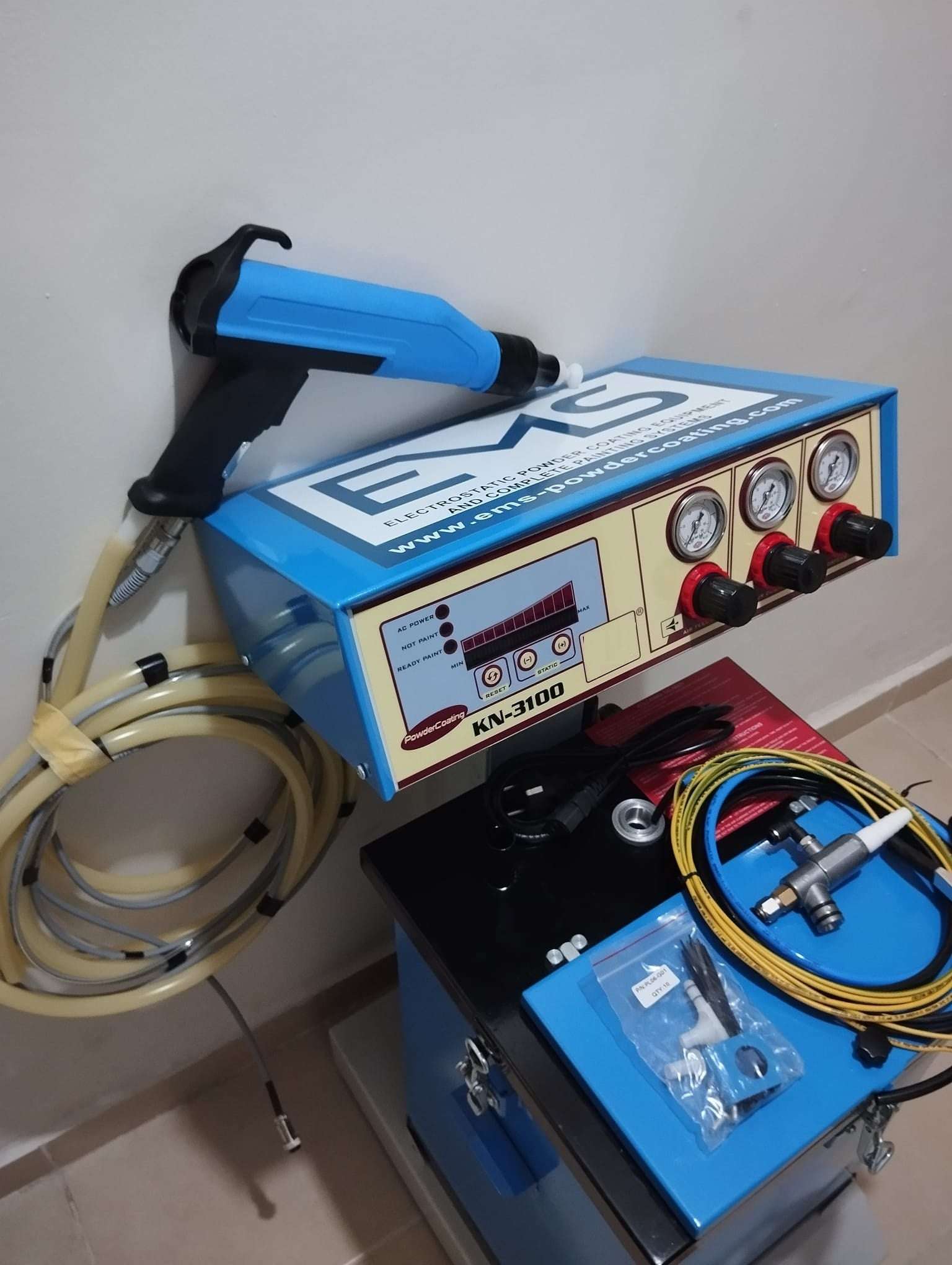
Le pistolet de poudrage électrostatique est un outil essentiel dans le processus de thermolaquage, permettant l’application uniforme de poudres de revêtement sur diverses surfaces. Ce type de pistolet utilise le principe de l’électrostatique pour charger la poudre avant de la pulvériser sur la pièce à recouvrir. Le revêtement en poudre est chargé électriquement, ce qui crée une attraction entre la poudre et la surface de l’objet à traiter, facilitant ainsi une couverture uniforme, même sur des formes complexes ou difficiles d’accès. Cette méthode est largement utilisée dans l’industrie pour des applications allant de la peinture de pièces automobiles à la finition de produits électroniques, en passant par les équipements industriels et les applications de décoration.
Le fonctionnement du pistolet de poudrage électrostatique repose sur deux principes fondamentaux : la pulvérisation de la poudre et la charge électrostatique. Lorsque la poudre est transportée par un flux d’air comprimé, elle passe par un pistolet équipé d’un électrode qui charge négativement les particules de poudre. La pièce à recouvrir, généralement mise à la terre, attire alors les particules chargées, permettant à la poudre de se déposer de manière uniforme et d’adhérer fermement à la surface. Cette application électrostatique permet un meilleur contrôle de la quantité de poudre utilisée, réduisant ainsi les déchets et augmentant l’efficacité du processus.
Les pistolets de poudrage électrostatique modernes sont équipés de technologies avancées pour améliorer la qualité de l’application. L’un des éléments clés est la régulation précise du flux de poudre, qui peut être ajusté en fonction de la taille de la pièce et du type de revêtement souhaité. Les pistolets sont souvent équipés d’un système de contrôle du flux d’air, permettant d’ajuster la pression d’air et la vitesse de pulvérisation. Ces réglages sont essentiels pour garantir une couverture uniforme, éviter les coulures et maximiser l’efficacité du processus de poudrage.
Les pistolets de poudrage électrostatique sont également conçus pour être très efficaces sur le plan énergétique. Grâce à la charge électrostatique, la poudre est attirée directement sur la surface, ce qui minimise le gaspillage de matériel et réduit les pertes. De plus, les pistolets modernes sont souvent dotés de systèmes de récupération de poudre excédentaire, permettant de recycler la poudre non utilisée, réduisant ainsi les coûts liés à l’achat de nouvelles poudres et minimisant l’impact environnemental du processus.
L’un des avantages majeurs de l’utilisation de pistolets de poudrage électrostatique est la capacité de travailler avec une grande variété de matériaux et de finitions. Les poudres utilisées peuvent être de différentes compositions, telles que l’époxy, le polyester, les poudres hybrides ou les poudres thermodurcissables. Chaque type de poudre a des propriétés spécifiques adaptées à des besoins particuliers, comme la résistance aux rayures, la protection contre les produits chimiques ou la résistance aux conditions climatiques extrêmes. Les pistolets électrostatiques sont capables de traiter ces différentes poudres en ajustant les paramètres de pulvérisation, garantissant ainsi la meilleure qualité de revêtement pour chaque application.
Les pistolets de poudrage électrostatique sont également adaptés à des conditions de production variées, allant de petites séries à des lignes de production automatisées à grande échelle. Dans des environnements de production en série, les pistolets peuvent être intégrés à des systèmes automatisés qui permettent un transport continu des pièces, de la préparation à l’application de la poudre, et au durcissement dans le four. L’automatisation permet de réduire les coûts de main-d’œuvre tout en maintenant une qualité constante et élevée.
En termes de conception, les pistolets de poudrage électrostatique sont de plus en plus ergonomiques, avec des caractéristiques qui facilitent l’utilisation prolongée par les opérateurs. Ces caractéristiques incluent des poignées ajustables, des poids légers et un contrôle facile des réglages à travers des interfaces numériques ou des écrans tactiles. De plus, les pistolets modernes sont souvent dotés de mécanismes anti-statique pour réduire les risques d’accumulation de poudre sur les parties non métalliques de l’appareil, ce qui améliore la sécurité et réduit l’entretien.
Les innovations dans la technologie des pistolets de poudrage électrostatique portent également sur l’amélioration de la précision et de la qualité de l’application. Des modèles récents intègrent des systèmes de gestion des flux d’air et de poudre plus sophistiqués, permettant un meilleur contrôle de la distribution de la poudre. Cela assure non seulement une finition plus lisse et uniforme, mais permet également de réduire les imperfections comme les coulures, les zones sans poudre et les irrégularités dans l’épaisseur du revêtement. Des systèmes de diagnostic intégrés permettent aux opérateurs de surveiller les performances du pistolet et de détecter les dysfonctionnements en temps réel, ce qui permet d’agir rapidement pour éviter les problèmes de qualité.
Un autre aspect de l’innovation dans les pistolets de poudrage électrostatique concerne l’optimisation de l’énergie. Les fabricants de ces appareils cherchent constamment à réduire la consommation énergétique tout en maintenant l’efficacité du processus. Les pistolets sont désormais conçus pour minimiser l’utilisation d’air comprimé, maximiser l’efficience de la charge électrostatique et offrir une application plus précise de la poudre. Cela contribue à une meilleure efficacité énergétique et à une réduction des coûts de production à long terme.
Les préoccupations environnementales et la réglementation croissante en matière de sécurité et de gestion des déchets ont également conduit à des améliorations dans la conception des pistolets de poudrage électrostatique. Les dispositifs modernes sont équipés de systèmes de filtration de l’air et de récupération de poudre, réduisant ainsi l’exposition des opérateurs aux poussières et minimisant les déchets. De plus, les matériaux et technologies de production des pistolets sont de plus en plus respectueux de l’environnement, contribuant à des pratiques de fabrication plus durables.
Les pistolets de poudrage électrostatique sont de plus en plus utilisés dans des applications de haute technologie, comme le revêtement de composants électroniques, de dispositifs médicaux ou d’équipements spécialisés dans des secteurs exigeants. Dans ces secteurs, les exigences en matière de précision, de résistance et de finition sont extrêmement élevées, et les pistolets électrostatiques doivent être capables de produire des revêtements d’une grande qualité tout en garantissant la sécurité et la fiabilité des produits finis. L’adaptabilité des pistolets modernes permet de répondre à ces défis, avec des réglages précis pour chaque type de matériau et de revêtement, tout en garantissant une productivité maximale.
En conclusion, les pistolets de poudrage électrostatique jouent un rôle crucial dans la production de revêtements de haute qualité, en particulier dans des industries où la précision, l’efficacité et la durabilité sont essentielles. Grâce à des innovations constantes en matière de technologie de pulvérisation, d’automatisation, d’efficacité énergétique et de respect de l’environnement, ces appareils sont appelés à devenir encore plus performants, permettant aux fabricants de répondre aux exigences de production modernes tout en garantissant une finition impeccable. Ces pistolets restent au cœur de nombreuses applications industrielles et continueront d’évoluer pour satisfaire les besoins toujours plus exigeants des industries de demain.
L’évolution des pistolets de poudrage électrostatique continue de répondre à l’augmentation des exigences en matière de performance, d’efficacité et de durabilité. À mesure que les industries recherchent des solutions plus efficaces et écologiques, ces pistolets s’adaptent pour répondre aux besoins spécifiques de chaque secteur tout en offrant des avantages distincts.
Une des avancées importantes dans la conception des pistolets de poudrage électrostatique réside dans la miniaturisation et l’ergonomie des appareils. Les pistolets plus compacts et plus légers sont désormais capables de maintenir un haut niveau de performance tout en étant plus faciles à utiliser, en particulier dans des environnements de production où la mobilité et la flexibilité sont cruciales. Ces modèles permettent aux opérateurs de travailler pendant des périodes prolongées sans ressentir de fatigue excessive, ce qui améliore à la fois la productivité et le confort de travail.
L’un des développements futurs clés des pistolets de poudrage électrostatique concerne leur capacité à s’adapter à une gamme encore plus large de matériaux et de types de poudre. Alors que les poudres à base d’époxy et de polyester dominent actuellement le marché, de nouvelles formulations de poudres, telles que des poudres nanotechnologiques ou à base de céramique, sont de plus en plus utilisées dans des applications spécialisées. Les pistolets de poudrage devront évoluer pour traiter efficacement ces nouvelles poudres, qui peuvent offrir des propriétés spécifiques comme une meilleure résistance à la chaleur, une conductivité thermique plus élevée ou des caractéristiques esthétiques avancées. L’adaptation à ces nouveaux matériaux nécessitera l’intégration de technologies permettant un contrôle plus précis de la pulvérisation et de la charge électrostatique, tout en maintenant une application uniforme et de qualité.
Une autre avancée technologique est l’intégration de la connectivité et de la numérisation dans les pistolets de poudrage électrostatique. La communication en temps réel avec d’autres systèmes de production, tels que les lignes de poudrage automatisées, peut améliorer considérablement l’efficacité de la chaîne de production. Par exemple, les pistolets pourraient être dotés de capteurs intelligents capables de surveiller en permanence les conditions de pulvérisation, comme la pression de l’air, la vitesse de la poudre ou la température de l’objet à recouvrir. Ces capteurs pourraient fournir des informations instantanées à un système centralisé, permettant d’ajuster automatiquement les paramètres pour assurer une application optimale de la poudre. L’intelligence artificielle pourrait être utilisée pour anticiper les besoins de maintenance ou de calibration, réduisant ainsi les temps d’arrêt et améliorant la qualité des revêtements.
Les pistolets de poudrage électrostatique sont également de plus en plus dotés de technologies de diagnostic et de surveillance de la qualité, facilitant la détection des anomalies pendant le processus de poudrage. Ces systèmes intelligents peuvent alerter les opérateurs en cas de dysfonctionnement, comme une pulvérisation irrégulière ou un problème de charge électrostatique, permettant une intervention rapide avant que le défaut n’affecte la production en cours. Cette approche préventive améliore la qualité et l’efficacité du processus tout en réduisant les coûts associés aux erreurs de production.
Une autre tendance croissante est l’optimisation du pistolet pour des applications de revêtement de haute précision, en particulier dans des secteurs tels que l’aéronautique, l’électronique et l’automobile, où des tolérances strictes en matière de finition sont souvent requises. Les pistolets de poudrage électrostatique devront offrir une précision accrue pour garantir une couverture uniforme sur des surfaces de tailles et de formes variées, tout en respectant des exigences strictes en termes d’épaisseur de la couche de poudre. L’ajustement précis de la taille des particules de poudre, du débit d’air et de la charge électrostatique sera essentiel pour atteindre ces niveaux de précision.
L’adoption de technologies respectueuses de l’environnement est également un facteur déterminant dans le développement futur des pistolets de poudrage électrostatique. En plus de la réduction de la consommation de poudre et de la récupération de poudre excédentaire, de nouvelles techniques de filtration et de gestion des déchets seront mises en œuvre pour minimiser l’impact écologique. Par exemple, des filtres de haute technologie pourraient être utilisés pour capturer les particules fines qui échappent au processus de pulvérisation, contribuant ainsi à une atmosphère de travail plus saine et à une réduction de l’empreinte environnementale du processus. En parallèle, les fabricants chercheront à réduire l’utilisation de produits chimiques et de solvants nocifs dans les poudres, en favorisant des formulations plus écologiques et biodégradables.
Les innovations en matière de sécurité et de confort pour les opérateurs ne seront pas en reste. Les nouveaux modèles de pistolets de poudrage électrostatique intégreront des systèmes de protection renforcés contre les risques d’exposition à la poudre, notamment des mécanismes de sécurité intégrés pour éviter les décharges électriques accidentelles et des systèmes de ventilation adaptés pour réduire les risques d’inhalation de poussière. Les pistolets seront également conçus pour être plus faciles à nettoyer et entretenir, grâce à des matériaux antiadhésifs et des conceptions modulaire qui faciliteront le démontage et le nettoyage des composants internes.
L’intégration de la réalité augmentée (RA) et de la réalité virtuelle (RV) dans les pistolets de poudrage électrostatique pourrait également changer la façon dont les opérateurs interagissent avec ces appareils. Ces technologies pourraient offrir des formations immersives et des outils de dépannage en temps réel, permettant aux opérateurs d’acquérir des compétences plus rapidement et de résoudre les problèmes de manière plus efficace. En fournissant des instructions détaillées et des simulations en temps réel, la RA et la RV peuvent également réduire les erreurs humaines, améliorer la précision de l’application de la poudre et renforcer la sécurité des opérateurs.
Enfin, la durabilité et la longévité des pistolets de poudrage électrostatique continueront de s’améliorer grâce à l’utilisation de matériaux avancés résistants à l’usure, à la corrosion et à la chaleur. Cela permettra d’augmenter la durée de vie des pistolets, réduisant ainsi les coûts liés à l’entretien et au remplacement des équipements. L’optimisation de la conception des pistolets permettra également de simplifier les réparations et de faciliter la gestion des pièces de rechange.
En conclusion, les pistolets de poudrage électrostatique du futur seront plus intelligents, plus écologiques et plus performants que jamais. Ils intégreront des technologies avancées comme l’intelligence artificielle, la connectivité IoT, la réalité augmentée et des matériaux de pointe pour offrir une expérience utilisateur améliorée et une productivité accrue. Ces pistolets seront non seulement plus efficaces, mais aussi plus adaptés aux nouvelles exigences des industries modernes, contribuant ainsi à des processus de fabrication plus rapides, plus précis et plus durables. Les progrès continus dans ce domaine permettront aux entreprises de répondre aux défis de la production moderne tout en garantissant des revêtements de haute qualité, adaptés à des besoins de plus en plus spécifiques.
Les pistolets de poudrage électrostatique continueront également à évoluer en termes de personnalisation pour répondre aux besoins de plus en plus diversifiés des industries modernes. Les différents secteurs, qu’il s’agisse de l’automobile, de l’électronique, de l’aéronautique ou de l’architecture, exigent des solutions de revêtement qui soient non seulement fonctionnelles mais aussi esthétiques et résistantes à des conditions spécifiques. En réponse à ces exigences, les pistolets de poudrage vont intégrer des ajustements de configuration plus poussés, permettant de passer plus facilement d’une application à une autre, tout en maintenant des standards de qualité élevés.
Un exemple de cette personnalisation accrue pourrait être l’adoption de systèmes de pulvérisation intelligents qui s’adaptent automatiquement aux caractéristiques de la pièce à traiter. Par exemple, un pistolet équipé de capteurs pourrait ajuster sa pulvérisation en fonction de la taille et de la forme de la pièce, optimisant ainsi l’utilisation de la poudre et réduisant les erreurs humaines. Ce type de système pourrait également ajuster la charge électrostatique en fonction de la conductivité de la surface, garantissant une couverture optimale sur des matériaux variés, tels que le métal, le plastique, ou d’autres substrats moins conventionnels.
Dans la même veine, les pistolets de poudrage électrostatique pourraient être connectés à des bases de données en ligne ou à des systèmes de gestion de la production pour fournir des informations en temps réel sur le processus de poudrage. Ces informations peuvent inclure des données sur la consommation de poudre, les paramètres de pulvérisation ou encore l’état de la machine, permettant ainsi une gestion plus efficace du processus de production. Par exemple, l’utilisation de la connectivité sans fil pourrait permettre aux opérateurs de surveiller à distance l’ensemble du processus et de faire des ajustements instantanés, même si la production se déroule dans un autre endroit de l’usine ou à l’extérieur de l’établissement.
Les pistolets de poudrage électrostatique du futur devront également intégrer des dispositifs de contrôle et de régulation thermique plus avancés. La gestion de la température est essentielle pour garantir que la poudre se fixe correctement à la surface et pour éviter les défauts comme les taches ou l’inconsistance dans le revêtement. Des systèmes de chauffage plus sophistiqués, capables de s’ajuster en fonction des conditions ambiantes, seront nécessaires pour garantir une application homogène de la poudre, en particulier dans les environnements où la température varie beaucoup. Cela pourrait inclure des éléments chauffants intégrés dans la buse du pistolet ou un contrôle plus raffiné des températures de la pièce et de la poudre avant l’application.
La question de la maintenance des pistolets de poudrage sera aussi un domaine clé d’innovation. Les pistolets de demain seront conçus pour nécessiter moins d’entretien grâce à des composants plus résistants et des technologies de nettoyage plus efficaces. Le nettoyage des pistolets, une tâche essentielle dans le processus de poudrage pour garantir la qualité du revêtement, pourrait être automatisé à l’aide de technologies telles que les jets de vapeur ou les systèmes de nettoyage à ultrasons intégrés. En réduisant le temps et les efforts nécessaires pour maintenir le pistolet en bon état de fonctionnement, les fabricants pourront améliorer leur productivité et réduire les risques d’erreurs dues à des outils mal entretenus.
L’optimisation des pistolets de poudrage électrostatique en termes de sécurité des opérateurs continuera également à progresser. Les normes de sécurité deviendront plus strictes, en particulier dans les environnements où des risques d’explosion sont présents en raison de la concentration élevée de poudres et de solvants. Les pistolets de poudrage seront équipés de dispositifs de sécurité supplémentaires pour minimiser le risque de décharges électrostatiques accidentelles. Les systèmes de protection contre les risques d’explosion pourraient inclure des interrupteurs automatiques, des dispositifs de décharge ou des matériaux antistatiques utilisés dans la fabrication des pistolets, réduisant ainsi les dangers pour les opérateurs.
Les systèmes de sécurité seront également renforcés par des alertes en cas de détection d’anomalies dans le fonctionnement de l’appareil, qu’il s’agisse de variations soudaines de pression, de flux d’air, de niveau de poudre ou de charge électrostatique. Des capteurs intelligents seront intégrés pour garantir que le pistolet fonctionne toujours dans des conditions optimales et que tout problème est rapidement détecté et corrigé. Cela permettra d’assurer non seulement la sécurité des travailleurs, mais aussi d’optimiser le processus de production pour garantir des produits finis de la plus haute qualité.
Enfin, l’extension de l’utilisation de la réalité virtuelle (RV) et de la réalité augmentée (RA) dans l’industrie du poudrage pourrait transformer la manière dont les opérateurs sont formés et comment les procédures sont suivies. Par exemple, les opérateurs pourraient utiliser des casques de réalité virtuelle pour s’exercer à des simulations réalistes du processus de poudrage avant d’intervenir dans la production réelle, réduisant ainsi les risques d’erreurs humaines et améliorant l’efficacité du processus d’apprentissage. De même, la réalité augmentée pourrait offrir un guide visuel en temps réel directement sur l’écran de l’opérateur, montrant les ajustements nécessaires sur le pistolet de poudrage en fonction des conditions de production, ce qui faciliterait le processus de décision et améliorerait la précision du travail.
En conclusion, les pistolets de poudrage électrostatique continueront de se perfectionner grâce à une combinaison d’avancées technologiques visant à améliorer la performance, la flexibilité, la sécurité et l’efficacité environnementale. L’intégration de la connectivité, de l’intelligence artificielle, de la réalité augmentée et de systèmes de maintenance automatisés marquera la prochaine étape dans l’évolution de ces outils. Ces innovations permettront aux fabricants de répondre à des exigences de production de plus en plus complexes, tout en offrant des solutions respectueuses de l’environnement et plus sûres pour les opérateurs. Grâce à ces progrès, les pistolets de poudrage électrostatique joueront un rôle essentiel dans la production industrielle du futur, où la qualité, la rapidité et la durabilité seront au cœur de chaque processus de fabrication.
Ensembles Manuels
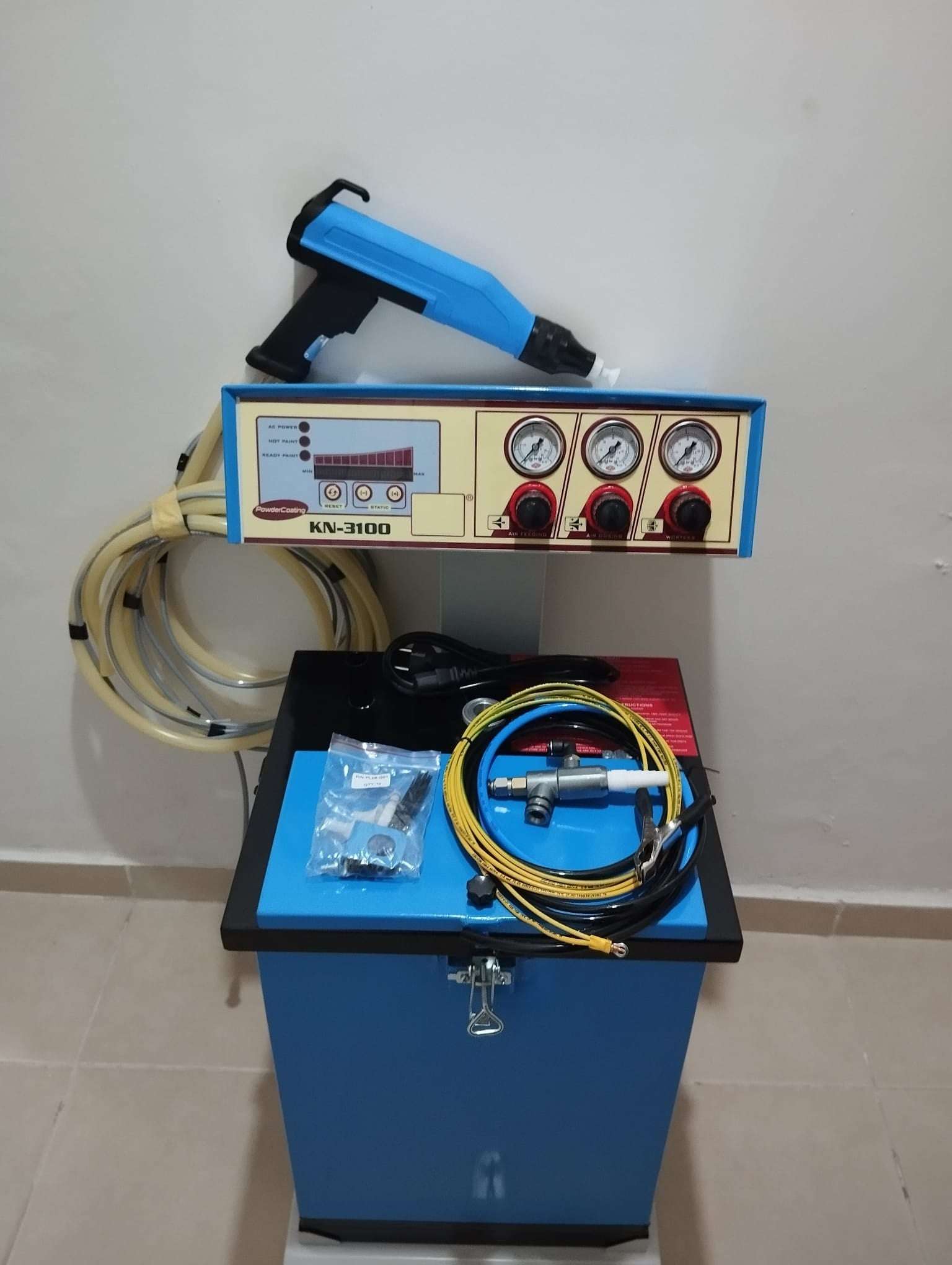
Les ensembles manuels de poudrage électrostatique sont des outils polyvalents et essentiels dans de nombreuses applications industrielles, permettant l’application de revêtements en poudre sur des surfaces variées à l’aide d’une approche simple mais efficace. Ces ensembles sont conçus pour offrir aux opérateurs un contrôle précis de l’application de la poudre, tout en permettant une grande flexibilité d’utilisation. Contrairement aux systèmes automatisés, les ensembles manuels offrent l’avantage d’être mobiles et adaptables, ce qui les rend idéaux pour des applications à faible ou moyenne échelle, des retouches ou des pièces aux formes complexes.
Le principe de fonctionnement d’un ensemble manuel de poudrage repose sur une combinaison de charge électrostatique et de pulvérisation contrôlée. L’opérateur tient généralement un pistolet de poudrage électrostatique qui utilise un générateur de charge pour électro-statiquement charger la poudre avant de la pulvériser sur la pièce. Ce processus permet à la poudre de se fixer de manière uniforme et précise sur la surface de la pièce, même si celle-ci présente des contours irréguliers ou difficiles d’accès. Cette application est rendue possible grâce à la charge électrostatique qui attire la poudre vers la surface, réduisant ainsi le gaspillage et améliorant l’efficacité de l’application.
Les ensembles manuels de poudrage se composent généralement de plusieurs éléments clés : le pistolet de pulvérisation, un générateur de charge électrostatique, un réservoir ou une cuve pour la poudre et des accessoires divers. Le pistolet, qui est souvent léger et ergonomique, est conçu pour être facile à manipuler et à orienter, ce qui permet à l’opérateur de contrôler la direction et l’intensité de la pulvérisation. Le générateur de charge électrostatique, qui est souvent intégré au pistolet ou séparé, fournit une charge négative à la poudre, tandis que la pièce à revêtir est mise à la terre pour créer une attraction électrostatique qui permet à la poudre de se déposer de manière homogène sur la surface.
Le réservoir de poudre est une autre composante essentielle de l’ensemble. Il est conçu pour contenir la poudre de manière sécurisée et pour alimenter le pistolet en continu durant le processus de pulvérisation. Ce réservoir est généralement équipé de dispositifs permettant de réguler le débit de poudre afin d’assurer une application uniforme. Le système peut également comporter des dispositifs de récupération de poudre excédentaire, permettant de réduire le gaspillage de matière et de minimiser les coûts liés à la consommation de poudre.
L’un des principaux avantages des ensembles manuels est leur flexibilité. En effet, ces systèmes sont adaptés à un large éventail d’applications, allant des petites séries de production aux retouches, en passant par les pièces de forme irrégulière ou de taille variable. Ils sont également utilisés dans des situations où l’automatisation n’est pas viable ou nécessaire, par exemple lorsqu’un ajustement précis ou une intervention rapide est nécessaire. De plus, le contrôle manuel permet à l’opérateur de moduler l’intensité de l’application en fonction des besoins, garantissant ainsi un revêtement uniforme, sans excédent ou manque de matière.
Les ensembles manuels sont également très prisés dans les environnements où une finition esthétique est primordiale. Par exemple, dans l’industrie automobile ou dans la fabrication d’équipements de consommation, où la qualité du revêtement doit être irréprochable, ces ensembles permettent de réaliser des finitions soignées et personnalisées. L’opérateur peut ajuster le flux de poudre, la pression de l’air et la charge électrostatique pour obtenir des effets particuliers, comme des finitions brillantes, mates, ou texturées, selon les spécifications du produit final.
En termes d’efficacité énergétique, les ensembles manuels de poudrage électrostatique sont conçus pour optimiser l’utilisation de la poudre et de l’air comprimé. La charge électrostatique permet de réduire les pertes de matière en attirant la poudre vers la surface de manière ciblée. Cela se traduit par un revêtement plus uniforme et une réduction du gaspillage de poudre. De plus, certains ensembles manuels modernes sont dotés de systèmes de filtration permettant de recycler la poudre excédentaire ou les poussières fines, ce qui réduit les coûts de production et l’impact environnemental du processus.
L’ergonomie des ensembles manuels est également un élément crucial dans leur conception. Les pistolets sont souvent conçus pour être légers et bien équilibrés, avec des poignées confortables et des systèmes de réglage faciles à utiliser. L’interface de contrôle permet à l’opérateur de modifier rapidement les paramètres de pulvérisation (tels que la pression d’air ou la quantité de poudre) pour s’adapter aux conditions de production spécifiques, qu’il s’agisse de la taille de la pièce à traiter ou de la finition recherchée.
Les ensembles manuels de poudrage sont également adaptés aux environnements de travail divers, y compris ceux où les exigences en matière de sécurité et de nettoyage sont strictes. Par exemple, dans les industries où des substances potentiellement dangereuses ou toxiques sont utilisées, les ensembles manuels sont souvent équipés de dispositifs de sécurité pour prévenir les accidents, comme des systèmes anti-décharge et des protections contre l’inhalation de poussières. De plus, le nettoyage de l’ensemble manuel est facilité par des matériaux antiadhésifs et des mécanismes de démontage rapide, permettant ainsi de maintenir une qualité constante de l’application de poudre, tout en réduisant le temps d’entretien nécessaire.
Un autre aspect important des ensembles manuels est leur coût, qui est souvent inférieur à celui des systèmes automatisés de poudrage. Cela en fait une solution idéale pour les petites entreprises ou les ateliers ayant des besoins de production plus modérés ou variés. Les ensembles manuels sont également plus accessibles pour des travaux de retouche ou des applications ponctuelles, où l’achat d’un système automatisé ne serait pas rentable.
En termes d’évolution, on peut s’attendre à ce que les ensembles manuels de poudrage électrostatique intègrent des technologies de plus en plus sophistiquées. Par exemple, des capteurs intelligents pourraient être utilisés pour fournir des données en temps réel sur l’application de la poudre, permettant ainsi une régulation automatique des paramètres pour garantir un revêtement optimal. De plus, les innovations dans les matériaux et les technologies de charge électrostatique pourraient améliorer encore la qualité de l’application, tout en réduisant la consommation d’énergie et de poudre.
Les ensembles manuels continueront aussi d’évoluer pour répondre aux nouvelles préoccupations environnementales et aux exigences de durabilité. La réduction de l’empreinte écologique des processus de poudrage sera au cœur de ces améliorations, avec des systèmes de recyclage de la poudre plus efficaces et l’utilisation de poudres plus écologiques, qui ne compromettent pas la qualité du revêtement.
En conclusion, les ensembles manuels de poudrage électrostatique sont des outils essentiels qui offrent une grande souplesse d’utilisation tout en garantissant des résultats de haute qualité. Grâce à leur efficacité, leur flexibilité, leur ergonomie et leur coût relativement faible, ils constituent une solution idéale pour des applications de poudrage variées. Avec l’intégration continue de technologies avancées et de solutions écologiques, ces ensembles seront appelés à répondre aux exigences croissantes de l’industrie tout en offrant des solutions de revêtement plus durables, efficaces et sûres.
Les ensembles manuels de poudrage électrostatique continueront à jouer un rôle crucial dans l’optimisation des processus de fabrication dans divers secteurs industriels. Leur capacité à s’adapter à une large gamme de tailles de pièces, de types de revêtements et de conditions de production les rend incontournables dans de nombreux environnements de travail. En particulier, leur utilisation sera de plus en plus répandue dans les secteurs nécessitant des applications de revêtement sur des surfaces irrégulières ou de formes complexes, où les systèmes automatisés ne peuvent pas toujours offrir la même flexibilité.
À mesure que la technologie progresse, l’ergonomie des ensembles manuels sera également améliorée pour réduire davantage la fatigue des opérateurs et améliorer leur confort au travail. Les pistolets seront encore plus légers et mieux équilibrés, avec des poignées et des commandes optimisées pour une prise en main plus naturelle et un meilleur contrôle. L’intégration de matériaux avancés, comme des composites légers ou des alliages résistants à l’usure, permettra de prolonger la durée de vie des pistolets tout en maintenant des performances de haute qualité.
Les innovations dans la gestion des flux d’air et de poudre, ainsi que dans la précision de la pulvérisation, permettront également d’augmenter l’efficacité des ensembles manuels. De plus, avec l’intégration de systèmes de contrôle plus avancés, les opérateurs pourront bénéficier d’un contrôle plus fin de la distribution de la poudre, de la pression d’air et de la charge électrostatique. Cela permettra non seulement d’améliorer la qualité des revêtements, mais aussi de réduire encore le gaspillage de poudre et de matières premières, ce qui contribuera à une meilleure rentabilité du processus de production.
Un autre aspect intéressant des ensembles manuels est leur capacité à répondre à des besoins spécifiques de personnalisation. Par exemple, certains pistolets peuvent être configurés avec des buses et des accessoires interchangeables, permettant de modifier le modèle de pulvérisation en fonction de la taille et de la forme de la pièce à recouvrir. Ce niveau de personnalisation est un atout majeur dans des secteurs comme l’automobile, la fabrication de meubles, ou l’aéronautique, où chaque pièce peut nécessiter un traitement particulier.
La surveillance et le contrôle à distance via des systèmes numériques deviendront aussi un élément clé des ensembles manuels de poudrage. Ces pistolets pourront être connectés à des plateformes de gestion de production, offrant aux superviseurs un accès en temps réel aux performances de chaque unité de poudrage. Cela permet non seulement d’améliorer l’efficacité globale, mais aussi de simplifier le processus de maintenance, avec des alertes envoyées en cas de besoin de nettoyage ou de réparation. Ces données de performance peuvent également être utilisées pour améliorer la formation des opérateurs, en leur fournissant des informations en temps réel sur leur efficacité et la qualité de l’application.
Les ensembles manuels continueront aussi à répondre aux préoccupations environnementales croissantes. En plus de l’optimisation de la récupération de poudre excédentaire, des matériaux de poudrage plus écologiques seront utilisés. Les fabricants de poudres s’efforcent de réduire la présence de solvants et d’additifs chimiques dans les poudres, en privilégiant des formulations plus durables et respectueuses de l’environnement. Ces poudres à faible émission, souvent sans COV (composés organiques volatils), seront de plus en plus populaires dans les industries qui souhaitent se conformer aux normes environnementales strictes tout en garantissant la qualité de leurs produits.
La maintenance et la durabilité des ensembles manuels sont également un domaine d’évolution importante. L’accent sera mis sur la conception de pièces plus robustes et faciles à entretenir. Les composants seront conçus pour être facilement accessibles et remplaçables, réduisant ainsi le temps d’immobilisation et améliorant la rentabilité de l’équipement à long terme. Les ensembles manuels de poudrage pourront également être dotés de systèmes d’auto-diagnostic, capables d’identifier rapidement les problèmes de performance ou de fonctionnement, permettant ainsi des interventions précises et efficaces pour éviter les pannes et maintenir des standards de qualité élevés.
L’introduction de fonctionnalités de sécurité avancées sera également une priorité. Les dispositifs de sécurité se diversifieront pour protéger les opérateurs contre les risques potentiels liés à la poudre et aux décharges électrostatiques. Des capteurs intelligents pourraient être installés pour détecter des anomalies dans le processus, comme des fuites de charge ou une pulvérisation irrégulière, et alerter immédiatement l’opérateur ou le superviseur pour éviter des accidents. Des protections supplémentaires pourraient être intégrées pour empêcher toute exposition excessive aux particules de poudre, en particulier dans les environnements de travail à forte concentration de substances chimiques ou dans des espaces confinés.
Les ensembles manuels de poudrage seront également de plus en plus associés à des logiciels de simulation et de formation. Grâce à la réalité augmentée (RA) et à la réalité virtuelle (RV), les opérateurs pourront simuler l’application de la poudre dans des conditions de production variées avant de commencer à travailler sur les équipements réels. Cela facilitera la formation et aidera les opérateurs à se familiariser avec les réglages et les techniques spécifiques à chaque application, réduisant ainsi les erreurs et améliorant l’efficacité de l’ensemble du processus de poudrage.
En conclusion, les ensembles manuels de poudrage électrostatique continueront à évoluer pour offrir des solutions de revêtement plus performantes, plus écologiques et plus sûres. Avec l’intégration de technologies avancées, des fonctionnalités de personnalisation et une meilleure ergonomie, ces ensembles permettront de répondre aux besoins de production diversifiés tout en garantissant une qualité optimale. Leur flexibilité, leur facilité d’utilisation et leur efficacité énergétique resteront des facteurs clés qui assureront leur rôle central dans l’industrie du poudrage pour les années à venir.
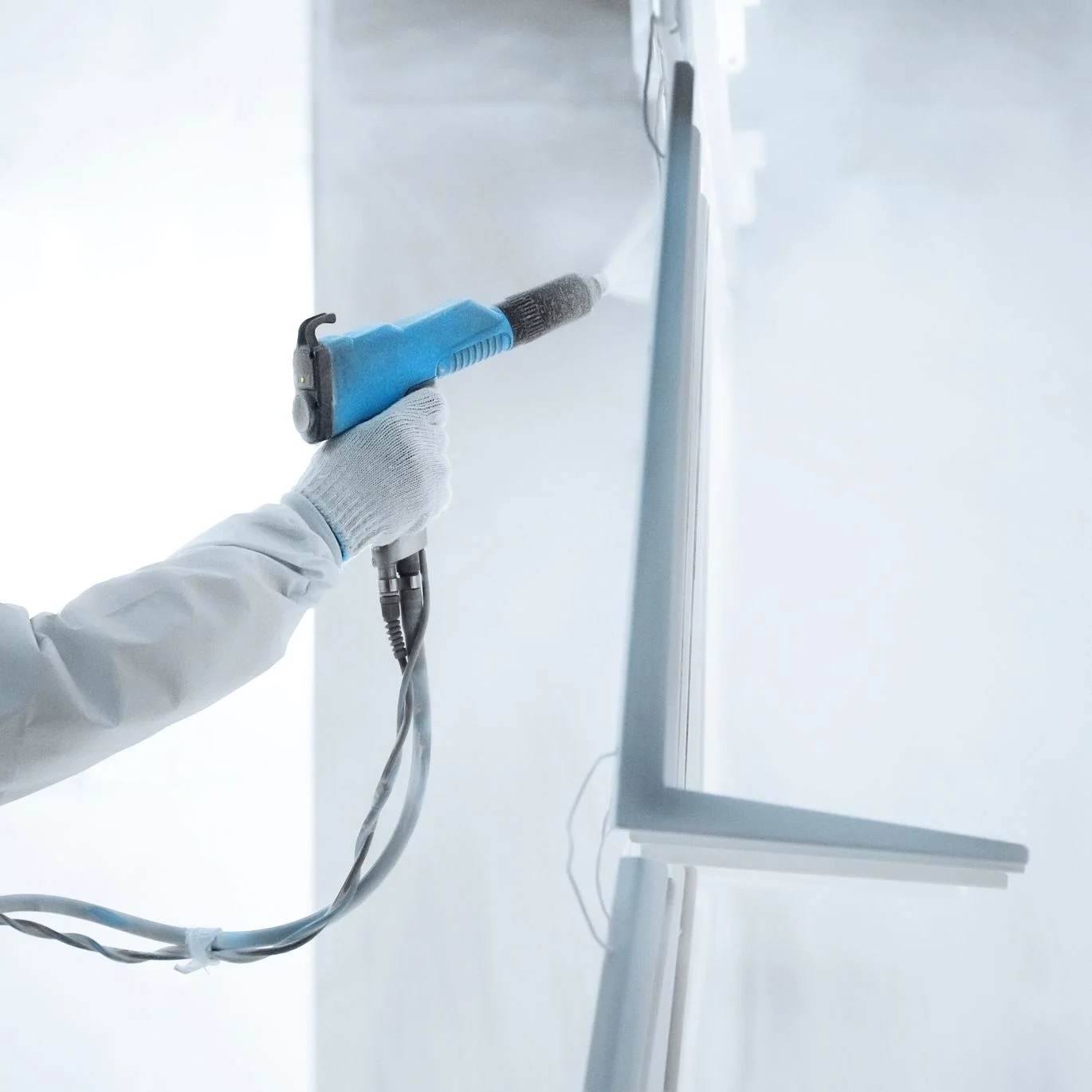
Les ensembles manuels de poudrage électrostatique continueront également de se perfectionner pour offrir encore plus de polyvalence dans leur utilisation. Un domaine de développement intéressant concerne la possibilité d’adapter les ensembles à des types de poudre et de matériaux encore plus variés. Alors que les poudres traditionnelles à base de polyester ou d’époxy sont largement utilisées, de nouveaux types de poudres, comme celles à base de matériaux thermoplastiques ou même des poudres métalliques spécifiques pour des applications particulières, devraient devenir plus courantes. Les ensembles manuels devront être adaptés pour garantir une application de qualité et une efficacité optimale avec ces nouveaux matériaux, ce qui nécessitera des ajustements au niveau des buses, des systèmes de filtration, et des réglages de charge électrostatique.
Les innovations dans les technologies de gestion de l’air comprimé, un élément essentiel du processus de poudrage, continueront également à améliorer l’efficacité des ensembles manuels. L’optimisation des flux d’air et de la pression peut jouer un rôle déterminant dans la qualité du revêtement, en permettant une pulvérisation plus uniforme et plus précise. L’amélioration de ces systèmes pourrait permettre une réduction de la consommation d’air comprimé tout en augmentant l’efficacité du processus de poudrage, ce qui réduirait les coûts opérationnels pour les utilisateurs.
La connectivité des ensembles manuels évoluera également avec l’intégration de solutions numériques plus poussées. L’ajout de systèmes de gestion à distance et de connectivité IoT (Internet des objets) permettra de suivre et de contrôler en temps réel tous les paramètres du processus de poudrage, comme la pression d’air, la vitesse de pulvérisation, ou encore l’épaisseur du revêtement. Grâce à ces technologies, les opérateurs pourront ajuster à distance les paramètres de l’équipement, ce qui leur permettra de réagir rapidement aux variations de la production ou à des conditions de travail changeantes. Cette connectivité facilitera également la collecte de données pour les analyses de performance, permettant d’optimiser la productivité, de réduire les erreurs humaines et de prévoir les besoins en maintenance avant qu’ils ne deviennent critiques.
L’intégration de l’intelligence artificielle (IA) et de l’analyse prédictive dans les ensembles manuels pourrait offrir de nouveaux niveaux d’automatisation et de gestion du processus de poudrage. Par exemple, des algorithmes intelligents pourraient être utilisés pour surveiller en temps réel les performances de l’équipement, identifier des anomalies et recommander des ajustements pour optimiser l’application de la poudre. Ces systèmes pourraient analyser des paramètres complexes comme la charge électrostatique, la distribution de la poudre, et la température de l’environnement pour s’assurer que le processus de poudrage fonctionne toujours à son maximum d’efficacité.
L’amélioration de l’interface utilisateur des ensembles manuels de poudrage sera également au cœur de l’innovation. À mesure que la technologie devient plus sophistiquée, il devient essentiel que les opérateurs puissent accéder facilement aux informations et ajuster les paramètres sans confusion. Des écrans tactiles, des interfaces graphiques intuitives, ou même des interfaces vocales pourraient être intégrés pour simplifier l’expérience utilisateur. Cela permettra aux opérateurs de suivre l’évolution du processus en temps réel, d’obtenir des données précises et de procéder à des ajustements rapides sans interrompre la production.
Dans le domaine de la sécurité, de nouvelles protections seront mises en place pour minimiser les risques liés à l’utilisation des ensembles manuels. Les risques d’incendie ou d’explosion dus à la poussière de poudre seront gérés plus efficacement grâce à l’introduction de systèmes de détection d’étincelles et de mécanismes d’arrêt automatique en cas d’anomalie. Ces systèmes de sécurité pourraient être couplés à des alertes en temps réel, envoyées à l’opérateur ou au superviseur, afin de prévenir tout accident avant qu’il ne se produise.
L’évolution des normes environnementales continuera de stimuler le développement des ensembles manuels, en particulier en ce qui concerne la réduction des émissions de COV et le recyclage de la poudre excédentaire. De plus en plus de poudres à faible impact environnemental, telles que celles qui utilisent des matériaux recyclés ou des produits biodégradables, seront disponibles. Les ensembles manuels devront être capables de traiter ces nouveaux matériaux tout en maintenant un haut niveau de performance. Le recyclage des poudres excédentaires pourrait également devenir une fonctionnalité standard dans de nombreux ensembles manuels, permettant non seulement de réduire les coûts, mais aussi de minimiser l’empreinte écologique de l’industrie du poudrage.
En termes de maintenance, l’automatisation des processus de nettoyage et de détection des défaillances deviendra un atout majeur. Les ensembles manuels seront équipés de systèmes auto-nettoyants ou de dispositifs facilitant le nettoyage rapide, réduisant ainsi les temps d’arrêt entre les applications. Des capteurs de maintenance intégrés permettront de prévoir les périodes où des ajustements ou des réparations sont nécessaires, avant même que l’équipement ne tombe en panne, ce qui garantira un fonctionnement optimal à tout moment.
Enfin, les ensembles manuels de poudrage continueront à être adoptés par une large gamme d’industries, y compris des secteurs en pleine croissance comme la fabrication d’équipements électroniques, les technologies de l’énergie renouvelable, et la production de dispositifs médicaux. Chacune de ces industries a des exigences spécifiques en termes de revêtement, ce qui stimule la recherche et l’adaptation continue des équipements. L’évolution des ensembles manuels permettra de mieux répondre aux besoins de ces secteurs tout en améliorant les performances des processus de revêtement.
En conclusion, les ensembles manuels de poudrage électrostatique continueront à se transformer grâce à l’adoption de technologies de pointe. Ces outils polyvalents et efficaces seront plus intelligents, plus sûrs et plus écologiques. Leur évolution permettra non seulement d’améliorer la qualité et l’efficacité du revêtement, mais aussi de garantir une plus grande flexibilité et rentabilité dans des secteurs toujours plus exigeants.
Les Ensembles Automatiques
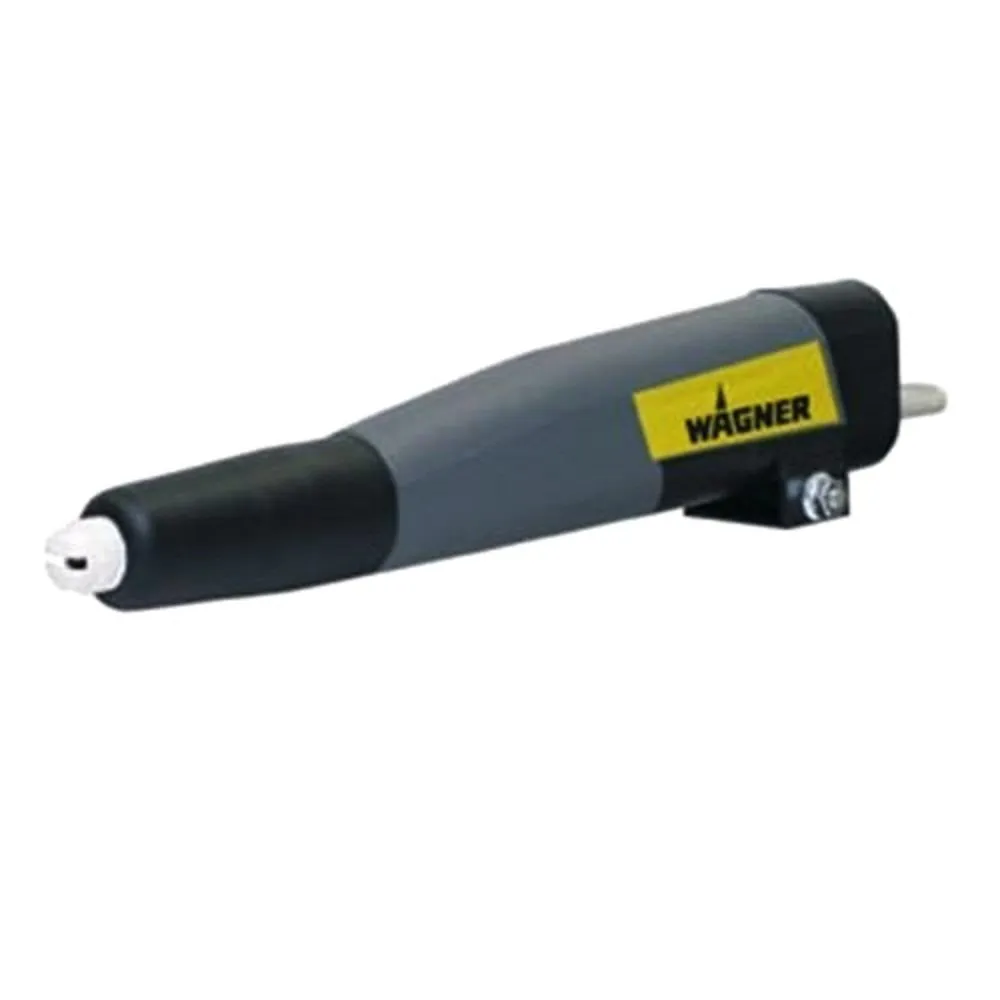
Les ensembles automatiques de poudrage électrostatique représentent une avancée majeure dans le domaine du revêtement industriel, offrant une solution hautement efficace et précise pour l’application de poudre sur des surfaces diverses. Ces systèmes sont conçus pour automatiser le processus de pulvérisation de poudre, assurant ainsi une production à grande échelle avec une uniformité et une reproductibilité accrues. En combinant des technologies avancées de contrôle, de gestion de l’air comprimé et de distribution de la poudre, les ensembles automatiques de poudrage permettent de maximiser la qualité du revêtement tout en réduisant le gaspillage de matériaux et d’énergie.
Le principe de fonctionnement des ensembles automatiques repose sur un processus de pulvérisation électrostatique où la poudre est chargée électrostatiquement et projetée sur la pièce à revêtir. Le système automatise cette procédure en coordonnant les différentes étapes, de l’alimentation en poudre à la distribution de la charge électrostatique, jusqu’à l’application de la poudre sur la surface cible. Le revêtement est ainsi appliqué de manière uniforme, même sur des pièces de formes complexes ou irrégulières, ce qui en fait une solution idéale pour les productions à grande échelle.
Les ensembles automatiques de poudrage sont composés de plusieurs éléments clés qui collaborent pour garantir des performances optimales. Le cœur de ces systèmes est constitué d’un pistolet ou d’un groupe de pistolets de pulvérisation, souvent montés sur des robots ou des convoyeurs, qui permettent une application précise et uniforme de la poudre. Ces pistolets sont alimentés en poudre depuis un réservoir central, et le flux de matière est régulé pour assurer une pulvérisation constante et contrôlée. La charge électrostatique est générée par un générateur dédié, qui polarise la poudre avant son application sur la pièce, garantissant ainsi une adhésion efficace.
Un autre composant important des ensembles automatiques est le système de transport, qui peut inclure des convoyeurs, des robots articulés ou des rails suspendus. Ces systèmes permettent de déplacer les pièces à revêtir de manière continue et régulière à travers la zone de poudrage, optimisant ainsi le temps de production et garantissant une couverture uniforme. Les robots, par exemple, peuvent être programmés pour ajuster automatiquement la trajectoire du pistolet en fonction des dimensions et de la forme des pièces, assurant ainsi une couverture complète et précise.
Les systèmes de contrôle, basés sur des logiciels sophistiqués, jouent également un rôle essentiel dans l’efficacité des ensembles automatiques de poudrage. Ces systèmes de contrôle permettent une régulation fine de tous les paramètres de pulvérisation, comme la pression d’air, la vitesse de transport, l’intensité de la charge électrostatique et la quantité de poudre appliquée. Grâce à ces contrôles automatisés, les opérateurs peuvent garantir que chaque pièce reçoit un revêtement conforme aux spécifications techniques, tout en optimisant les paramètres de production pour minimiser les pertes de matériau et réduire les coûts opérationnels.
Les avantages des ensembles automatiques de poudrage sont multiples. Tout d’abord, ils permettent une production rapide et continue, idéale pour les lignes de fabrication à grande échelle. Le fait que le processus soit automatisé garantit une cohérence de la qualité des revêtements, réduisant ainsi les variations liées aux erreurs humaines. Cette uniformité est particulièrement importante dans des industries telles que l’automobile, où chaque pièce doit être revêtue de manière identique pour répondre aux normes de qualité strictes.
De plus, l’automatisation permet d’améliorer la sécurité du processus de poudrage. Les systèmes automatiques sont équipés de dispositifs de sécurité sophistiqués, comme des capteurs de détection de défauts ou des systèmes de gestion des risques d’explosion dus à la poussière. L’automatisation réduit également le risque de contact direct des opérateurs avec les produits chimiques ou les poussières de poudres, ce qui contribue à créer un environnement de travail plus sûr.
L’efficacité énergétique est un autre avantage clé des ensembles automatiques. Ces systèmes sont conçus pour optimiser l’utilisation de l’air comprimé et de la poudre, réduisant ainsi les pertes et les coûts liés aux matières premières. De plus, la capacité à récupérer la poudre excédentaire et à la recycler dans le système contribue à minimiser les déchets et à réduire l’empreinte écologique du processus de poudrage. Cette efficacité énergétique est également renforcée par l’utilisation de générateurs de charge électrostatique de plus en plus performants, qui permettent d’optimiser la pulvérisation tout en réduisant la consommation d’énergie.
Les ensembles automatiques de poudrage sont également extrêmement polyvalents et peuvent être adaptés à une large gamme d’applications industrielles. En fonction des besoins spécifiques, ces systèmes peuvent être modifiés pour traiter des pièces de différentes tailles et formes, et peuvent également être équipés de diverses buses de pulvérisation et systèmes de gestion de l’air comprimé pour répondre à des exigences de finition particulières. Certains systèmes automatiques sont également capables de pulvériser des poudres thermoplastiques, métalliques ou spécifiques à des applications hautes performances, comme celles utilisées dans les secteurs de l’aéronautique ou des équipements de haute technologie.
La maintenance des ensembles automatiques est facilitée grâce à leur conception modulaire et à l’utilisation de technologies de diagnostic avancées. Les systèmes de contrôle peuvent détecter automatiquement les anomalies et alerter les opérateurs sur les besoins de maintenance, ce qui permet d’éviter les pannes imprévues et de minimiser les temps d’arrêt. De plus, les composants peuvent être facilement remplacés ou entretenus sans perturber la production, ce qui améliore la durée de vie des équipements et réduit les coûts de maintenance.
L’aspect connecté des ensembles automatiques devient également un facteur clé de leur succès. En intégrant des technologies de l’Internet des objets (IoT) et des systèmes de gestion de production intelligents, les ensembles automatiques de poudrage peuvent être connectés à des réseaux de gestion de la production. Cela permet aux responsables de suivre en temps réel l’état des équipements, d’obtenir des rapports détaillés sur les performances et d’ajuster les paramètres de production à distance. Cette connectivité permet également de collecter des données sur la performance et la qualité des revêtements, ce qui facilite la mise en place de stratégies d’amélioration continue.
Dans les années à venir, l’évolution des ensembles automatiques de poudrage se concentrera sur l’intégration de technologies encore plus avancées. L’intelligence artificielle (IA) pourrait jouer un rôle dans l’ajustement dynamique des paramètres de pulvérisation, en fonction des conditions de production ou des variations dans la qualité de la poudre. De plus, les améliorations dans les systèmes de recyclage et de gestion des déchets de poudre pourraient contribuer à rendre ces systèmes encore plus écologiques et rentables.
Les ensembles automatiques seront également appelés à s’adapter à des besoins de personnalisation toujours plus exigeants. Par exemple, dans des secteurs comme la fabrication d’équipements médicaux ou de composants électroniques, les revêtements doivent répondre à des spécifications très strictes en termes de finition, de résistance et de durabilité. Les ensembles automatiques évolueront pour offrir des solutions capables de satisfaire ces besoins spécifiques, avec une précision accrue et des options de traitement des surfaces de plus en plus spécialisées.
En conclusion, les ensembles automatiques de poudrage électrostatique continueront de transformer le secteur industriel en offrant des solutions de revêtement à la fois plus efficaces, plus sécurisées et plus écologiques. Leur capacité à répondre aux besoins de production à grande échelle, tout en maintenant une qualité de revêtement constante, fera d’eux un choix privilégié dans une multitude d’industries. Avec l’intégration de technologies avancées et une attention croissante portée à la durabilité et à l’efficacité énergétique, les ensembles automatiques de poudrage continueront à évoluer pour répondre aux défis de l’industrie du revêtement dans les années à venir.
Les ensembles automatiques de poudrage continueront à évoluer en réponse aux défis croissants de l’industrie et aux besoins toujours plus exigeants des clients. L’une des principales évolutions à attendre est l’intégration de technologies de pointe telles que l’intelligence artificielle et le machine learning pour optimiser le processus de poudrage. Ces technologies permettront une adaptation dynamique en temps réel des paramètres du système, en fonction de l’analyse des conditions environnementales, de la température ou de l’humidité, ce qui pourrait rendre les systèmes plus réactifs et précis. L’intelligence artificielle pourrait également être utilisée pour prédire les variations de qualité et optimiser les processus de maintenance en anticipant les défaillances avant qu’elles ne se produisent, ce qui permettrait de minimiser les interruptions de production et de prolonger la durée de vie de l’équipement.
L’automatisation de la gestion de la poudre, y compris son recyclage et son acheminement, deviendra un élément clé dans la réduction des coûts opérationnels et de l’empreinte écologique. Les systèmes automatiques de poudrage intègrent de plus en plus de mécanismes pour récupérer la poudre excédentaire, la filtrer et la réintroduire dans le processus, ce qui permet de maximiser l’utilisation des matériaux et de réduire le gaspillage. Cela contribuera également à réduire les déchets de poudre, qui peuvent être coûteux et nuisibles pour l’environnement. À mesure que les technologies de recyclage se perfectionnent, les ensembles automatiques deviendront plus efficaces sur le plan énergétique et plus respectueux de l’environnement, répondant ainsi aux normes environnementales de plus en plus strictes.
Un autre domaine de développement important est la connectivité accrue des ensembles automatiques. L’Internet des objets (IoT) et les systèmes de gestion en cloud permettront de suivre chaque étape du processus de poudrage, de la réception de la poudre à son application sur la pièce. Les opérateurs et gestionnaires de production pourront accéder à des données en temps réel concernant la qualité du revêtement, les performances des équipements et les rendements de la production. Cela permettra non seulement de détecter rapidement tout problème ou anomalie dans le processus, mais aussi d’optimiser l’ensemble du cycle de production en analysant les données pour repérer les inefficacités et améliorer les processus.
La mise en œuvre de la réalité augmentée (RA) et de la réalité virtuelle (RV) pourrait également changer la manière dont les opérateurs interagissent avec les ensembles automatiques de poudrage. Ces technologies pourraient être utilisées pour former les opérateurs plus rapidement et de manière plus immersive, leur permettant de comprendre les principes de fonctionnement des systèmes et de se familiariser avec les procédures de maintenance et de dépannage dans des environnements virtuels avant d’interagir avec les équipements réels. La RA pourrait également offrir des instructions en temps réel et superposer des informations utiles, telles que des données sur l’état de la machine ou des alertes de maintenance, directement sur les équipements lors de l’inspection.
En termes de flexibilité, l’avenir des ensembles automatiques de poudrage sera également marqué par leur capacité à s’adapter à des productions de plus en plus variées. Avec l’essor de la personnalisation de masse et de la production de petites séries, les systèmes de poudrage automatiques devront pouvoir traiter une plus grande diversité de pièces et de formes, tout en maintenant des standards de qualité élevés. L’automatisation devra être assez flexible pour s’adapter rapidement aux changements dans les types de produits, les matériaux de revêtement et les exigences des clients, ce qui pourrait impliquer l’intégration de systèmes plus modulaires, capables de s’ajuster à des besoins spécifiques.
Les progrès dans la technologie des buses et de la distribution de la poudre joueront également un rôle central dans cette évolution. Des buses de pulvérisation de plus en plus sophistiquées et efficaces permettront de réduire les pertes de poudre tout en garantissant une couverture uniforme, même sur des surfaces complexes. La pulvérisation à basse pression, l’utilisation de technologies sans air et les systèmes à haute efficacité énergétique contribueront à réduire la consommation d’énergie et à améliorer la précision des applications de poudre. De plus, les systèmes de contrôle de la forme du jet et de la taille des particules de poudre permettront d’ajuster avec précision la qualité du revêtement pour chaque type de pièce.
Les ensembles automatiques de poudrage continueront également à améliorer l’ergonomie et la convivialité. Bien que ces systèmes soient de plus en plus sophistiqués, l’accent sera mis sur l’amélioration de l’interface utilisateur, afin que les opérateurs puissent interagir facilement avec des équipements complexes. Les écrans tactiles, les interfaces intuitives et les systèmes de gestion via des applications mobiles ou des plateformes basées sur le cloud offriront une plus grande simplicité dans la gestion de la production, tout en permettant de surveiller à distance les systèmes.
Dans le même temps, les considérations de durabilité continueront de façonner l’évolution des ensembles automatiques. Les fabricants seront incités à développer des matériaux et des technologies plus durables pour la fabrication des équipements, réduisant ainsi les coûts de production et l’impact environnemental. L’utilisation de matériaux recyclés ou durables pour la construction des pièces d’équipement, ainsi que l’intégration de processus de fabrication plus écologiques, seront des priorités pour répondre aux exigences de plus en plus strictes des régulations environnementales mondiales.
L’avenir des ensembles automatiques de poudrage semble donc prometteur. L’intégration de technologies avancées permettra d’optimiser davantage la production tout en offrant des solutions plus écologiques, plus efficaces et plus sûres. Les entreprises qui adoptent ces technologies bénéficieront d’une meilleure qualité de revêtement, d’une productivité accrue et d’une réduction des coûts opérationnels. Avec ces innovations, les ensembles automatiques continueront de jouer un rôle essentiel dans l’industrie, en répondant aux exigences de qualité, de rapidité et de flexibilité d’un marché mondial en constante évolution.
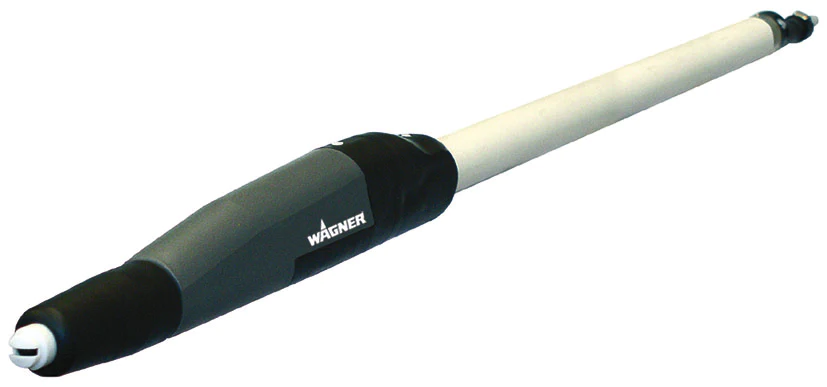
À mesure que l’automatisation des systèmes de poudrage progresse, de nouvelles tendances émergeront, redéfinissant le paysage de la production industrielle. Les ensembles automatiques deviendront de plus en plus interconnectés, permettant aux usines de fonctionner dans un cadre de production 4.0, où les données en temps réel, l’analyse prédictive et la maintenance préventive joueront un rôle clé dans l’optimisation des performances des lignes de production.
L’intégration de la réalité augmentée et de l’intelligence artificielle (IA) dans les ensembles automatiques va permettre d’améliorer la gestion de la production à un niveau encore plus avancé. L’IA sera capable d’analyser une grande quantité de données issues des capteurs, des caméras et des systèmes de contrôle pour identifier des tendances, ajuster les paramètres de pulvérisation de manière autonome et détecter des anomalies avant qu’elles ne deviennent des problèmes majeurs. Cela permettra de réduire considérablement les interruptions imprévues et de maintenir une production constante, augmentant ainsi la rentabilité tout en minimisant les coûts de maintenance.
Les ensembles automatiques seront également conçus pour répondre à des exigences de plus en plus variées en matière de production, de personnalisation et de qualité. Dans des secteurs tels que l’automobile, l’aérospatiale, l’électronique et l’industrie des équipements médicaux, les pièces à revêtir ont des caractéristiques très spécifiques qui nécessitent des solutions de poudrage sur mesure. Les ensembles automatiques de poudrage devront offrir une flexibilité accrue, permettant une transition rapide entre différents types de poudres, de formes de pièces et de finitions. Cela peut inclure des mécanismes permettant d’adapter rapidement la vitesse de pulvérisation, la pression de l’air ou la charge électrostatique en fonction des besoins de chaque production.
Les innovations dans les technologies de poudrage permettront de traiter une plus grande diversité de matériaux, y compris les poudres innovantes comme les poudres conductrices, thermoconductrices ou même des poudres spécifiques pour des applications dans des environnements extrêmes, comme l’aérospatiale ou la production de dispositifs électroniques. Ces technologies offriront de nouvelles possibilités pour des applications de revêtement plus spécialisées et plus efficaces, garantissant des performances exceptionnelles pour des applications exigeantes.
De plus, l’optimisation des processus de recyclage des poudres excédentaires continuera d’être un domaine clé d’innovation. Les ensembles automatiques de poudrage intégreront des technologies permettant de récupérer, de filtrer et de réintroduire la poudre excédentaire dans le cycle de production de manière encore plus efficace. Ce recyclage de la poudre permet non seulement de réduire les coûts de matériaux, mais aussi de limiter l’impact environnemental en minimisant les déchets. Les avancées dans ce domaine feront partie d’un effort plus large pour rendre les processus industriels plus durables et moins consommateurs de ressources.
L’automatisation du nettoyage des équipements sera un autre aspect essentiel. Les systèmes automatisés de nettoyage des buses, des canaux de poudre et des autres composants des ensembles de poudrage permettront de réduire le temps d’arrêt nécessaire pour l’entretien, ce qui est particulièrement important pour les environnements de production à haute cadence. Ces systèmes de nettoyage automatisés garantiront que les équipements restent performants et maintiennent une qualité de pulvérisation constante, sans risquer la contamination croisée entre différentes couleurs ou types de poudres.
Les ensembles automatiques de poudrage vont également bénéficier d’une meilleure intégration avec les systèmes de gestion de la production (MES – Manufacturing Execution System) et les systèmes ERP (Enterprise Resource Planning). Cette intégration permettra une gestion plus fluide et plus précise des processus de production, offrant une visibilité complète sur chaque étape du cycle de production, de la réception des matériaux à l’expédition des produits finis. L’interconnexion des systèmes favorisera également une gestion optimisée des stocks de poudre et des consommables, contribuant à une réduction des coûts et une meilleure planification de la production.
Un autre aspect à considérer dans l’évolution des ensembles automatiques est l’amélioration continue de la précision des revêtements. Alors que les exigences de qualité deviennent de plus en plus strictes, ces systèmes devront être capables d’appliquer des revêtements d’une uniformité parfaite, indépendamment des variations de température, d’humidité ou d’autres facteurs externes. L’intégration de technologies avancées de contrôle de la qualité en ligne, telles que des caméras et des capteurs de mesure de l’épaisseur du revêtement, permettra de garantir des résultats de qualité constante et d’appliquer des ajustements automatiques pour compenser toute variation.
Les ensembles automatiques de poudrage se dirigeront également vers des solutions plus compactes et modulaires. Les fabricants cherchent à optimiser l’espace dans les usines, ce qui signifie que les équipements devront devenir plus compacts tout en offrant une flexibilité maximale pour s’adapter à différents types de productions. Les systèmes modulaires permettront de personnaliser l’équipement en fonction des besoins spécifiques de chaque production, facilitant ainsi les mises à niveau et l’adaptation aux évolutions du marché.
Enfin, la durabilité des équipements sera de plus en plus au cœur des préoccupations. Les entreprises, soumises à des régulations environnementales de plus en plus strictes, seront poussées à adopter des pratiques plus responsables en matière de gestion des ressources et des déchets. Les fabricants de systèmes automatiques de poudrage devront prendre en compte ces exigences en concevant des équipements avec une plus grande longévité, en réduisant leur consommation d’énergie et en choisissant des matériaux recyclables pour la fabrication des machines.
En conclusion, les ensembles automatiques de poudrage continueront à évoluer pour répondre aux besoins d’une production industrielle de plus en plus exigeante en matière de qualité, de flexibilité, de rapidité et de durabilité. L’intégration de technologies avancées comme l’intelligence artificielle, la connectivité, et l’automatisation des processus de nettoyage et de maintenance permettra de renforcer leur efficacité, de réduire les coûts et d’améliorer la sécurité. L’industrie du poudrage électrostatique automatisé se dirige vers une nouvelle ère de production intelligente, plus écologiquement responsable et plus rentable, capable de répondre aux exigences de marchés toujours plus diversifiés et compétitifs.
Le Revêtement en Poudre
L’équipement de revêtement en poudre est utilisé pour appliquer une fine couche de poudre sur une surface métallique. Ce type de revêtement est appliqué par un procédé électrostatique et constitue une méthode très populaire pour la finition des pièces métalliques.
Ce type d’équipement peut être divisé en deux grandes catégories : automatiques et manuels. Les cabines automatiques sont plus populaires car elles offrent de meilleurs taux de production, mais elles sont également plus chères.
Une cabine à poudre est une enceinte dans laquelle se déroule le processus de revêtement en poudre. L’équipement de revêtement en poudre comprend un four dans lequel les pièces sont chauffées pour activer la poudre, un pistolet qui pulvérise ou brosse la poudre, une bande transporteuse qui déplace les pièces à travers le four et des pistolets de type cartouche pour appliquer des revêtements plus épais avec moins de pulvérisation.
Le revêtement en poudre est une technique utilisée pour donner une finition aux pièces métalliques. Cette technique est utilisée depuis de nombreuses années et reste aujourd’hui l’une des techniques les plus populaires.
L’équipement de revêtement en poudre comprend des cabines, des fours, des pistolets, des machines, des lignes et des convoyeurs. Une cabine peut être automatique ou manuelle. Une cabine automatique est plus chère qu’une cabine manuelle mais elle est aussi plus rapide et plus efficace