Une ligne de peinture en poudre automatique est un ensemble d’équipements automatisés conçus pour appliquer des revêtements en poudre sur des pièces ou des produits de manière efficace et uniforme. Ce type de ligne est souvent utilisé dans des environnements de production à volume élevé pour garantir une productivité accrue et une qualité constante du revêtement. Voici les éléments clés que l’on peut trouver dans une ligne de peinture en poudre automatique :
- Système de convoyage automatisé : Les pièces sont transportées de manière automatisée d’une étape à l’autre de la ligne grâce à des systèmes de convoyage tels que des chaînes, des convoyeurs à bande ou des chariots automatisés.
- Prétraitement automatisé : Les lignes de peinture en poudre automatisées peuvent inclure des stations de prétraitement automatisées pour nettoyer, dégraisser ou préparer les pièces avant l’application de la poudre.
- Cabine de pulvérisation automatisée : Des pistolets de pulvérisation automatisés sont utilisés pour appliquer la poudre de manière uniforme sur les pièces. Ces pistolets sont souvent montés sur des bras robotisés pour permettre une couverture précise de toutes les surfaces.
- Système de récupération de poudre automatisé : Un système automatique est mis en place pour récupérer l’excédent de poudre non adhérée aux pièces. Cela peut impliquer des systèmes de recyclage pour réutiliser la poudre.
- Four de polymérisation automatisé : Les pièces sont transportées automatiquement dans un four de polymérisation où la poudre fond et durcit pour former un revêtement solide.
- Système de contrôle de la qualité automatisé : Des systèmes de vision automatisés peuvent être utilisés pour inspecter visuellement les pièces et garantir la qualité du revêtement en poudre.
- Automatisation de la gestion de la poudre : Les lignes de peinture en poudre automatiques peuvent être équipées de systèmes de gestion de la poudre automatisés, y compris la distribution contrôlée de la poudre.
- Système de contrôle global : Un système de contrôle centralisé surveille et coordonne l’ensemble du processus, garantissant une séquence fluide et une cohérence dans l’application de la poudre.
- Système de filtration de l’air automatisé : Pour maintenir des conditions de travail sûres et respecter les normes environnementales, un système de filtration de l’air automatisé peut être intégré pour capturer les particules de poudre.
- Stockage automatisé des pièces : Les lignes de peinture en poudre automatisées peuvent être intégrées à des systèmes de stockage automatisés pour gérer les pièces à revêtir.
L’automatisation dans une ligne de peinture en poudre offre des avantages tels que la réduction des erreurs humaines, une productivité accrue, une qualité constante et une efficacité énergétique. Ces lignes automatisées sont couramment utilisées dans des environnements de production à grande échelle où la standardisation et la répétabilité sont essentielles.
Une ligne de peinture poudre automatique est un système hautement mécanisé conçu pour appliquer un revêtement en poudre sur des pièces métalliques ou d’autres matériaux. Ce type de ligne est couramment utilisé dans les industries de fabrication en série, où l’efficacité, la précision et la qualité de finition sont primordiales. Elle intègre plusieurs étapes cruciales, allant du prétraitement des pièces à leur polymérisation dans un four, tout en permettant une production rapide et une qualité constante.
Au cœur de la ligne de peinture poudre automatique, on trouve le système de poudrage électrostatique, qui permet à la poudre de se fixer sur la surface des pièces à traiter. Ce système utilise une charge électrique pour attirer les particules de poudre sur les pièces métalliques, créant ainsi une couche uniforme et bien adhérente. La précision de l’application est améliorée grâce à des pistolets de pulvérisation automatiques qui sont programmés pour diffuser la peinture de manière régulière et homogène, même sur des formes complexes.
L’une des caractéristiques majeures d’une ligne de peinture poudre automatique est son automatisation. Les pièces à peindre sont transportées à travers la ligne via des systèmes de convoyage automatisés, souvent constitués de chaînes de convoyeurs, qui déplacent les pièces d’une station à l’autre sans intervention manuelle. Cela permet une cadence de production élevée et réduit les risques d’erreur humaine, garantissant ainsi des résultats constants et une réduction des coûts de main-d’œuvre.
Le prétraitement des surfaces est une étape essentielle avant l’application de la poudre. Cette étape prépare les pièces en nettoyant et en dégraissant les surfaces pour éliminer toute saleté, huile ou oxydation. Dans une ligne automatique, cette étape se fait généralement via des cabines de lavage ou des tunnels de prétraitement, où les pièces sont immergées dans des solutions chimiques qui assurent une préparation optimale de la surface. Ce processus assure non seulement une bonne adhésion de la peinture en poudre, mais il contribue également à la durabilité du revêtement une fois polymérisé.
Une fois les pièces nettoyées, elles sont envoyées dans la station de poudrage, où des pistolets électrostatiques pulvérisent la peinture en poudre sur les surfaces. La poudre est projetée sous forme de fines particules qui se fixent sur les pièces grâce à la charge électrostatique générée par les pistolets. Les robots ou les bras articulés automatisés permettent de couvrir la pièce de manière précise et homogène, quelle que soit sa forme ou sa taille. Les systèmes de dépoussiérage peuvent également être intégrés dans cette étape pour éliminer l’excès de poudre non adhéré avant la cuisson, assurant ainsi un fini lisse et uniforme.
Après le poudrage, les pièces passent dans un four de polymérisation où elles sont chauffées à des températures élevées, généralement entre 160°C et 200°C, pour durcir la poudre et la transformer en un revêtement solide et résistant. Le four de polymérisation est souvent intégré directement dans la ligne de peinture, et les pièces peuvent être transportées à travers le four via des convoyeurs qui les déplacent progressivement, tout en maintenant une température constante et homogène à travers l’ensemble du processus.
L’un des avantages majeurs des lignes de peinture poudre automatiques est leur capacité à traiter une grande quantité de pièces de manière continue et rapide. Grâce à l’automatisation, il est possible de traiter de grandes séries de pièces avec un minimum d’interventions manuelles, ce qui réduit les coûts de production et améliore la productivité. Les systèmes automatisés permettent également d’optimiser l’application de la peinture en poudre, réduisant ainsi les pertes de matériau et augmentant le rendement.
Les contrôles et systèmes de supervision jouent un rôle crucial dans le bon fonctionnement de la ligne. Les capteurs et les dispositifs de surveillance sont utilisés pour assurer que chaque étape du processus se déroule correctement. Par exemple, des capteurs de température et d’humidité surveillent en permanence l’environnement de cuisson dans le four pour garantir que les conditions de polymérisation soient respectées. De même, des systèmes de vision industrielle peuvent être utilisés pour vérifier la qualité de l’application de la poudre et détecter tout défaut, comme une couverture inégale ou une accumulation excessive de peinture.
L’intégration de systèmes de récupération de poudre dans la ligne de peinture automatique permet également de maximiser l’efficacité des ressources. Les poudres excédentaires qui ne se fixent pas sur les pièces peuvent être récupérées et réutilisées, ce qui réduit les coûts de matière première et minimise le gaspillage. Ce processus est particulièrement important pour les industries soucieuses de l’environnement et de la réduction des déchets.
Une ligne de peinture poudre automatique est également conçue pour être flexible et adaptable aux besoins spécifiques de différents secteurs industriels. Que ce soit pour des petites pièces ou des produits volumineux, des métaux ou des plastiques, la ligne peut être configurée pour s’adapter à diverses tailles, formes et types de matériaux. Les paramètres de pulvérisation, tels que la pression de l’air, la vitesse de transport et le type de poudre, peuvent être ajustés pour chaque type de pièce, garantissant ainsi que la qualité de la finition soit toujours optimale.
L’un des défis des lignes de peinture poudre automatiques réside dans leur maintenance. Bien que l’automatisation réduise les besoins en intervention manuelle, une maintenance régulière est nécessaire pour garantir que tous les composants de la ligne fonctionnent correctement. Cela comprend le nettoyage des pistolets de pulvérisation, l’entretien des éléments chauffants dans les fours de polymérisation, ainsi que la vérification des systèmes de convoyage et des dispositifs de dépoussiérage. Une bonne gestion de la maintenance permet non seulement de prolonger la durée de vie de l’équipement, mais aussi de maintenir un niveau élevé de qualité dans les pièces traitées.
En résumé, une ligne de peinture poudre automatique est un système intégré, automatisé et hautement efficient pour appliquer des revêtements en poudre sur des pièces métalliques ou autres. Son efficacité, sa capacité à traiter des volumes élevés et sa qualité de finition en font une solution idéale pour les industries de production de masse. Grâce à l’automatisation, la récupération de poudre et la surveillance en temps réel, elle permet de produire des pièces de haute qualité tout en optimisant les coûts et les ressources, tout en répondant aux exigences modernes en matière de performance et de durabilité.
L’efficacité énergétique est un autre point clé dans les lignes de peinture poudre automatiques. En raison de l’importance de la consommation d’énergie, surtout au niveau des fours de polymérisation et des systèmes de séchage, les fabricants de ces lignes cherchent constamment à améliorer les performances thermiques des équipements. Les technologies modernes intègrent des systèmes de récupération de chaleur et des solutions d’isolation thermique avancées, permettant de réduire la perte d’énergie et de maximiser l’efficacité de la cuisson. Cela permet non seulement de réduire les coûts d’exploitation, mais également de respecter les normes environnementales strictes en matière de consommation énergétique et d’émissions.
L’adaptabilité des lignes de peinture poudre automatiques aux différents types de pièces est également un facteur important pour les industries diversifiées. Certaines lignes sont conçues pour traiter des pièces de petite taille, telles que des composants électroniques, tandis que d’autres sont capables de gérer des pièces volumineuses ou des structures métalliques complexes. Ces lignes peuvent être équipées de dispositifs ajustables pour modifier la position des pistolets de pulvérisation, la hauteur des pièces ou l’angle de pulvérisation, permettant ainsi une personnalisation du traitement en fonction de la géométrie et de la taille des objets à traiter.
Les systèmes de contrôle jouent également un rôle crucial dans la performance des lignes de peinture poudre automatiques. De nombreux équipements sont équipés de logiciels avancés qui permettent de suivre en temps réel le processus de peinture, d’optimiser les paramètres de pulvérisation et de polymérisation, et de générer des rapports détaillés pour chaque cycle de production. Ces systèmes offrent une visibilité totale sur la performance de la ligne et permettent une gestion proactive des processus. En cas de dysfonctionnement, les alertes automatiques permettent de minimiser les arrêts de production et d’effectuer des ajustements immédiats.
Une autre fonctionnalité intéressante des lignes de peinture poudre automatiques est la possibilité de les intégrer avec d’autres processus de fabrication, comme le prétraitement des pièces, le revêtement en métal liquide ou le décapage des surfaces. Cela crée une solution complète pour les entreprises qui souhaitent automatiser l’ensemble de leur chaîne de production de revêtements, de la préparation à la finition. Ces solutions intégrées permettent de gagner du temps, d’améliorer la cohérence de la qualité et de réduire les coûts de gestion des équipements.
Les fournisseurs de lignes de peinture poudre automatiques mettent également l’accent sur la sécurité des opérateurs. Avec l’automatisation des processus, il existe un moindre besoin d’intervention manuelle, ce qui réduit les risques liés à l’exposition aux produits chimiques ou à la chaleur intense des fours. De plus, des dispositifs de sécurité sont généralement intégrés dans les lignes pour détecter toute anomalie dans le processus de peinture ou dans le fonctionnement des équipements, garantissant ainsi un environnement de travail plus sûr.
Les avantages environnementaux d’une ligne de peinture poudre automatique sont également significatifs. L’application de peinture en poudre présente un faible taux de volatilisation de solvants, ce qui permet de réduire l’impact environnemental comparé aux systèmes traditionnels de peinture à base de solvants. En outre, la capacité de récupérer et de réutiliser la poudre excédentaire minimise le gaspillage de matériaux et contribue à une approche de production plus durable et éco-responsable. Cela permet également aux entreprises de se conformer aux normes environnementales en constante évolution et de répondre aux attentes croissantes des consommateurs en matière de pratiques de fabrication écologiques.
En termes de coût d’investissement, les lignes de peinture poudre automatiques peuvent représenter un investissement initial conséquent. Cependant, les avantages en termes de productivité, qualité et réduction des coûts opérationnels sur le long terme compensent souvent largement cet investissement initial. Les économies réalisées grâce à une utilisation plus efficace de la peinture, à la réduction des coûts de main-d’œuvre, et à la diminution des rebuts et des défauts de finition, permettent aux entreprises de rentabiliser rapidement leur équipement. De plus, les lignes modernes sont souvent conçues pour être modulables, ce qui permet d’ajouter des fonctionnalités ou des extensions à mesure que les besoins de production évoluent, sans nécessiter de remplacement complet des systèmes.
Les améliorations continues dans la conception des lignes de peinture poudre automatiques permettent d’offrir des solutions de plus en plus flexibles, capables de répondre à des besoins de production diversifiés et spécifiques. Par exemple, les lignes peuvent être adaptées pour traiter une large gamme de matériaux, y compris des alliages métalliques spécifiques, du plastique, du verre ou du bois, et sont capables de s’ajuster aux exigences de revêtements spéciaux pour des applications particulières, comme dans les secteurs de l’automobile, de l’électroménager, ou de la construction.
En conclusion, une ligne de peinture poudre automatique est une solution complète et performante pour les entreprises recherchant des processus de revêtement efficaces et rentables. Grâce à l’automatisation, à la récupération de poudre, à des technologies avancées de contrôle et à des systèmes intégrés, elle permet de produire des pièces de haute qualité en grande quantité tout en minimisant l’impact environnemental et les coûts de production. Adaptable, fiable et éco-efficiente, cette solution répond aux exigences de plus en plus strictes des industries modernes en matière de productivité, de durabilité et de performance.
Ligne de Peinture Poudre Automatique: Système de convoyage automatisé
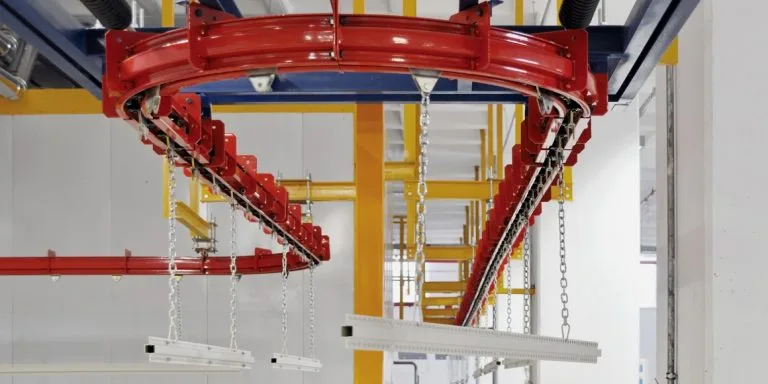
Un système de convoyage automatisé est un ensemble d’équipements et de technologies conçus pour déplacer des objets ou des produits d’un point à un autre de manière automatique, sans nécessiter une intervention humaine directe. Ces systèmes sont largement utilisés dans diverses industries pour améliorer l’efficacité, la précision et la productivité des processus de fabrication, d’assemblage, de stockage et de distribution. Voici quelques éléments clés associés à un système de convoyage automatisé :
- Convoyeurs : Les convoyeurs sont les composants centraux du système, et ils peuvent prendre différentes formes, notamment des convoyeurs à bande, à rouleaux, à chaînes, à vis, etc. Chaque type de convoyeur est adapté à des applications spécifiques.
- Système de contrôle : Un système de contrôle automatisé gère le fonctionnement du convoyeur. Il peut inclure des capteurs, des actionneurs et des logiciels pour surveiller et coordonner le mouvement des produits.
- Capteurs : Des capteurs sont utilisés pour détecter la présence, la position et d’autres caractéristiques des produits sur le convoyeur. Ces informations sont cruciales pour le bon fonctionnement du système.
- Actionneurs : Les actionneurs, tels que des moteurs électriques ou des vérins pneumatiques, sont responsables du mouvement des convoyeurs et du positionnement des produits.
- Logiciels de contrôle : Des logiciels de contrôle déterminent les itinéraires des produits, gèrent les arrêts et les départs, et coordonnent les mouvements pour assurer une séquence de production fluide.
- Système de convoyage modulaire : Certains systèmes sont conçus de manière modulaire, ce qui permet une flexibilité accrue pour s’adapter à différentes configurations d’usine et à des besoins changeants.
- Postes de transfert automatisés : Des postes de transfert automatisés permettent le transfert de produits d’un convoyeur à un autre, facilitant le changement de direction ou le passage d’une étape de production à une autre.
- Élévateurs et descenseurs automatiques : Certains systèmes de convoyage comprennent des dispositifs automatisés pour élever ou abaisser les produits en fonction des besoins de production.
- Système de pesée et d’étiquetage automatique : Certains convoyeurs intègrent des systèmes automatisés pour peser les produits et appliquer des étiquettes, ce qui est particulièrement utile dans les opérations d’emballage.
- Système de tri automatique : Des dispositifs de tri automatisés peuvent être intégrés pour diriger les produits vers différents itinéraires en fonction de critères prédéfinis.
Les systèmes de convoyage automatisé sont utilisés dans une variété d’industries, notamment la fabrication, la logistique, la distribution, l’automobile, l’aérospatiale et bien d’autres. Ils contribuent à accroître l’efficacité opérationnelle, à réduire les coûts de main-d’œuvre, et à améliorer la précision et la cohérence des processus industriels.
Ligne de Peinture Poudre Automatique: Prétraitement automatisé
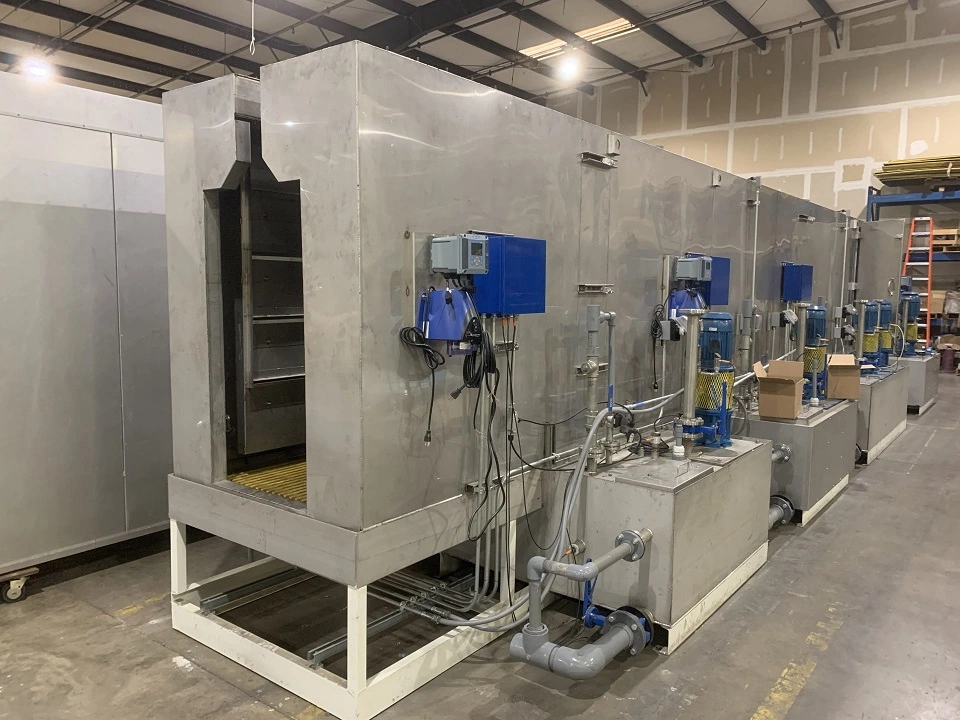
Le prétraitement automatisé fait référence à une série de processus automatisés utilisés pour préparer des matériaux ou des produits avant de les soumettre à une étape ultérieure du processus de fabrication. Le prétraitement peut inclure diverses étapes, selon les besoins spécifiques de l’application, mais il est généralement conçu pour assurer une surface propre, adhérente et prête pour le traitement suivant. Voici quelques éléments courants associés à un prétraitement automatisé :
- Nettoyage automatique : Des équipements automatisés, tels que des buses de pulvérisation ou des brosses rotatives, peuvent être utilisés pour nettoyer automatiquement les surfaces des pièces, éliminant les contaminants tels que la saleté, la graisse, les huiles, etc.
- Dégraissage automatique : Certains processus automatisés peuvent inclure des étapes de dégraissage, où des solutions chimiques ou des procédés mécaniques sont utilisés pour éliminer les résidus de graisse ou d’huile présents sur les pièces.
- Sablage automatisé : L’utilisation de dispositifs automatisés pour effectuer le sablage des surfaces peut être intégrée dans le prétraitement. Cela contribue à créer une texture de surface appropriée pour une adhérence optimale du revêtement.
- Préparation de surface : Certains prétraitements automatisés peuvent inclure des étapes de préparation de surface, telles que le traitement chimique pour améliorer l’adhérence du revêtement à venir.
- Système de séchage automatique : Après le nettoyage ou d’autres étapes du prétraitement, un système de séchage automatisé peut être utilisé pour s’assurer que les pièces sont complètement sèches avant de passer à la prochaine étape du processus.
- Contrôle de la qualité automatisé : Des systèmes automatisés de contrôle de la qualité peuvent être intégrés pour s’assurer que le prétraitement a été effectué correctement et que les pièces sont prêtes pour la phase suivante du processus.
- Système de convoyage automatisé : Les pièces à prétraiter peuvent être transportées automatiquement d’une étape à l’autre du processus de prétraitement grâce à un système de convoyage automatisé.
- Système de gestion de produits chimiques automatisé : Pour les processus de prétraitement impliquant des produits chimiques, des systèmes automatisés peuvent être utilisés pour doser, mélanger et appliquer les produits chimiques de manière précise.
- Équipements de protection individuelle (EPI) automatisés : Lorsque des produits chimiques ou des substances potentiellement dangereuses sont utilisés, des distributeurs automatisés d’équipements de protection individuelle, tels que des masques ou des gants, peuvent être intégrés.
Le prétraitement automatisé est souvent utilisé dans des environnements de production où la régularité, la rapidité et la précision sont essentielles. Il contribue à assurer la qualité du produit final en garantissant que les surfaces des pièces sont préparées de manière optimale pour les étapes de traitement ultérieures, telles que la peinture, le revêtement ou d’autres procédés spécifiques.
Cabine de pulvérisation automatisée
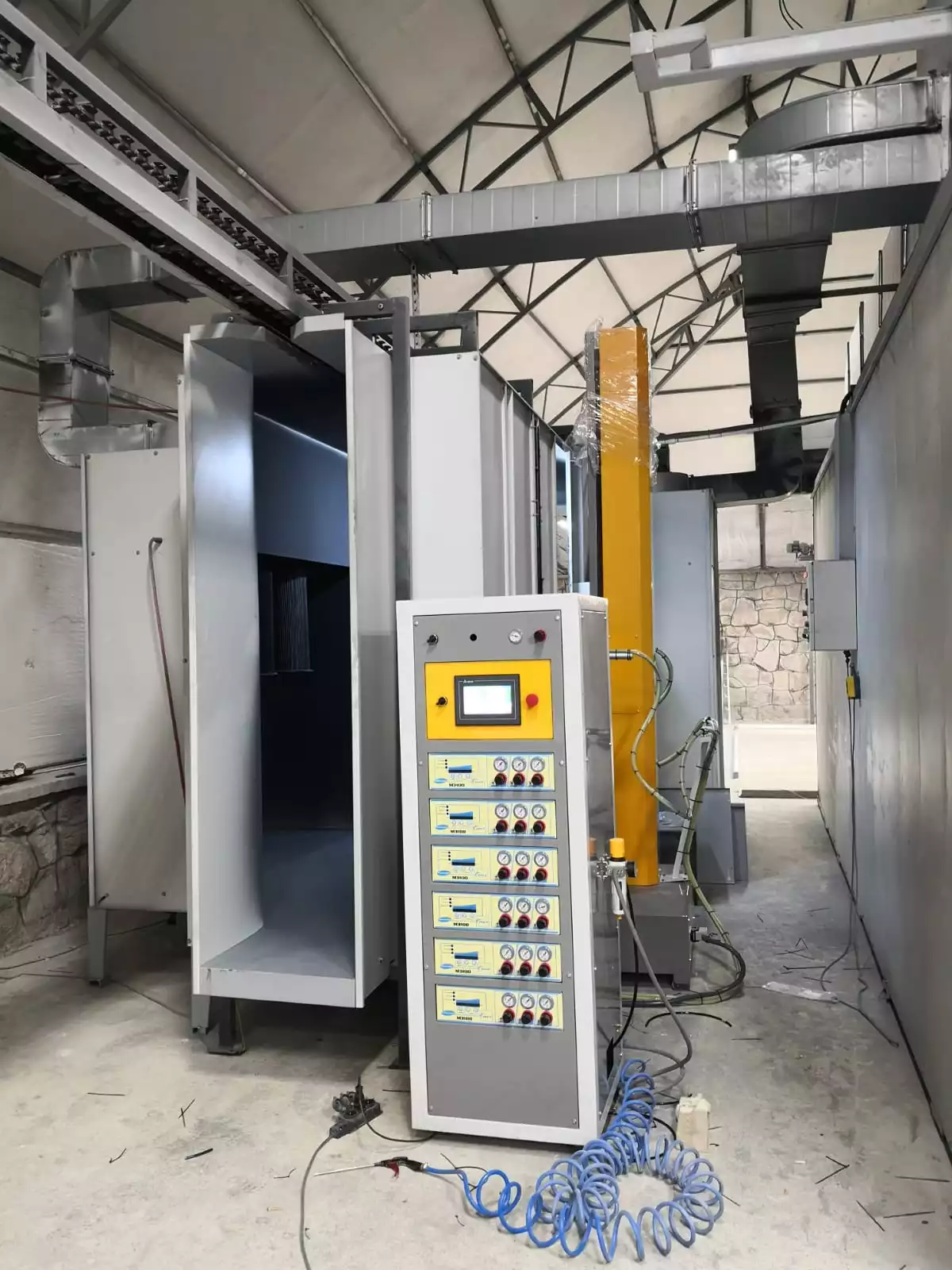
Une cabine de pulvérisation automatisée est une installation équipée d’équipements automatisés destinés à appliquer des revêtements, tels que de la peinture ou des revêtements en poudre, de manière précise et uniforme sur des objets ou des surfaces. Ces cabines automatisées sont souvent utilisées dans des environnements de production à volume élevé où la qualité, la cohérence et l’efficacité sont cruciales. Voici quelques éléments clés associés à une cabine de pulvérisation automatisée :
- Pistolets de pulvérisation automatiques : Des pistolets de pulvérisation automatisés, souvent montés sur des bras robotisés, sont utilisés pour appliquer de manière précise les revêtements sur les pièces. Ces pistolets peuvent être programmés pour suivre des trajectoires spécifiques, garantissant une couverture uniforme.
- Bras robotisés : Les bras robotisés sont utilisés pour déplacer les pistolets de pulvérisation de manière automatisée, permettant une flexibilité dans l’application du revêtement sur des surfaces complexes ou des pièces de formes variées.
- Système de contrôle automatisé : Un système de contrôle centralisé gère l’ensemble du processus de pulvérisation automatisée. Il peut inclure des logiciels de programmation pour définir les trajectoires des pistolets, la pression d’air, le débit de pulvérisation, etc.
- Système de dosage automatisé : Certains systèmes de pulvérisation automatisée intègrent des dispositifs automatisés de dosage de la peinture ou du revêtement pour garantir une quantité précise et constante est appliquée.
- Système de récupération de pulvérisation : Un système automatisé de récupération de pulvérisation peut être intégré pour recueillir l’excédent de revêtement non adhérée, contribuant ainsi à réduire le gaspillage et à économiser des matériaux.
- Système de filtration de l’air : Pour maintenir des conditions de travail sûres et respecter les normes environnementales, une cabine de pulvérisation automatisée peut être équipée d’un système de filtration de l’air pour capturer les particules de pulvérisation.
- Système de séchage ou de polymérisation intégré : Après l’application du revêtement, certaines cabines automatisées peuvent être équipées d’un système de séchage ou de polymérisation automatisé pour durcir le revêtement.
- Éclairage ajustable : Des systèmes d’éclairage ajustables sont souvent inclus pour assurer une visibilité optimale lors de l’inspection visuelle du processus de pulvérisation.
- Écrans de surveillance : Des écrans de surveillance peuvent être utilisés pour afficher en temps réel des informations sur le processus, telles que la quantité de revêtement appliqué, les erreurs éventuelles, etc.
- Système de nettoyage automatique : Certains systèmes de pulvérisation automatisée intègrent des dispositifs automatisés de nettoyage des buses et des pistolets après chaque cycle, assurant ainsi la propreté et la fiabilité du processus.
Les cabines de pulvérisation automatisées offrent des avantages tels qu’une application uniforme, une productivité accrue, une réduction des erreurs humaines et une consommation de matériaux plus efficace. Elles sont couramment utilisées dans des industries telles que l’automobile, l’aérospatiale, la fabrication de meubles et d’autres secteurs nécessitant une finition de haute qualité sur des pièces à grande échelle.
Système de récupération de poudre automatisé
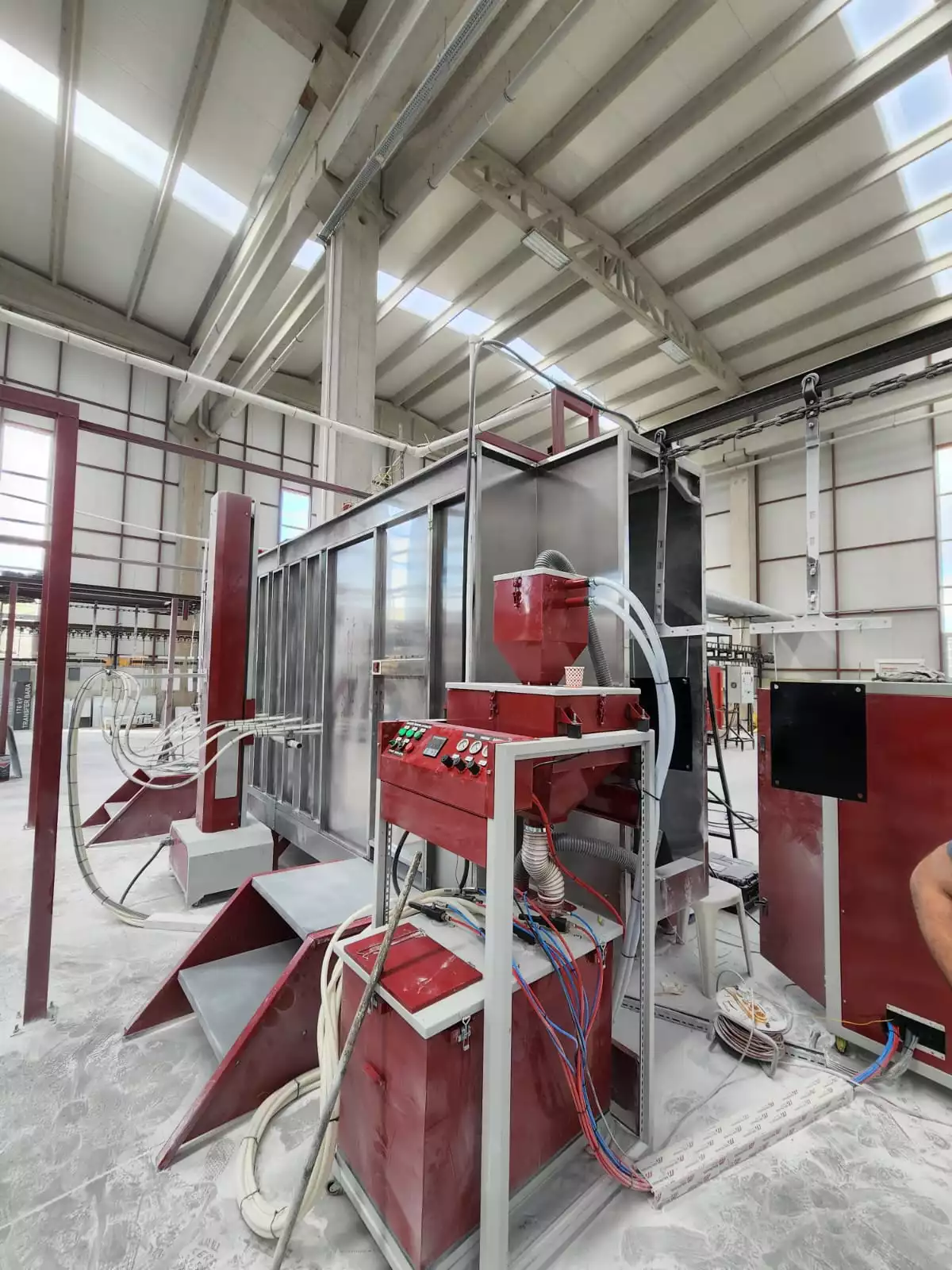
Un système de récupération de poudre automatisé est une composante essentielle dans les installations de revêtement en poudre, conçu pour récupérer et réutiliser la poudre non adhérée pendant le processus de pulvérisation. L’objectif est de minimiser le gaspillage de matériau et de maintenir une efficacité élevée dans l’application du revêtement en poudre. Voici quelques caractéristiques courantes associées à un système de récupération de poudre automatisé :
- Cyclone de récupération : Un cyclone est souvent utilisé pour séparer la poudre non adhérée de l’air après la pulvérisation. La poudre récupérée est ensuite dirigée vers un système de stockage ou de recyclage.
- Filtres à cartouche : Certains systèmes utilisent des filtres à cartouche pour collecter les particules de poudre non adhérée. Ces filtres peuvent être nettoyés ou remplacés automatiquement pour maintenir l’efficacité du processus.
- Système de tamisage automatique : La poudre collectée peut passer par un processus de tamisage automatisé pour éliminer les agglomérats et assurer la qualité de la poudre réutilisée.
- Transport pneumatique automatisé : Des systèmes pneumatiques peuvent être utilisés pour transporter automatiquement la poudre récupérée des zones de collecte vers les zones de stockage ou de recyclage.
- Système de stockage automatisé : La poudre récupérée peut être stockée de manière automatisée dans des silos ou des conteneurs spécifiques, prêts à être réintroduits dans le processus de pulvérisation.
- Système de dosage automatisé : Lors de la réintroduction de la poudre dans le processus de pulvérisation, un système automatisé dose la quantité appropriée pour maintenir la cohérence du revêtement.
- Système de contrôle automatisé : Un système centralisé de contrôle surveille et régule l’ensemble du processus de récupération de poudre, y compris la gestion des débits, la qualité de la poudre récupérée, et d’autres paramètres.
- Capteurs de niveau : Les capteurs de niveau peuvent être utilisés pour surveiller le niveau de poudre dans les silos de stockage, déclenchant des alertes ou des actions automatisées lorsque des ajustements sont nécessaires.
- Système de nettoyage automatisé : Certains systèmes intègrent des mécanismes automatisés de nettoyage pour assurer la propreté des conduits, des filtres et des autres composants du système.
- Système de surveillance en temps réel : Les systèmes modernes offrent souvent une surveillance en temps réel via des écrans d’interface utilisateur, permettant aux opérateurs de suivre le fonctionnement du système et de prendre des mesures correctives si nécessaire.
L’utilisation d’un système de récupération de poudre automatisé contribue à optimiser les ressources, à réduire les coûts de matières premières et à minimiser l’impact environnemental associé au processus de revêtement en poudre. Ces systèmes sont couramment utilisés dans diverses industries, notamment l’automobile, l’aérospatiale, et la fabrication de meubles.
Four de polymérisation automatisé
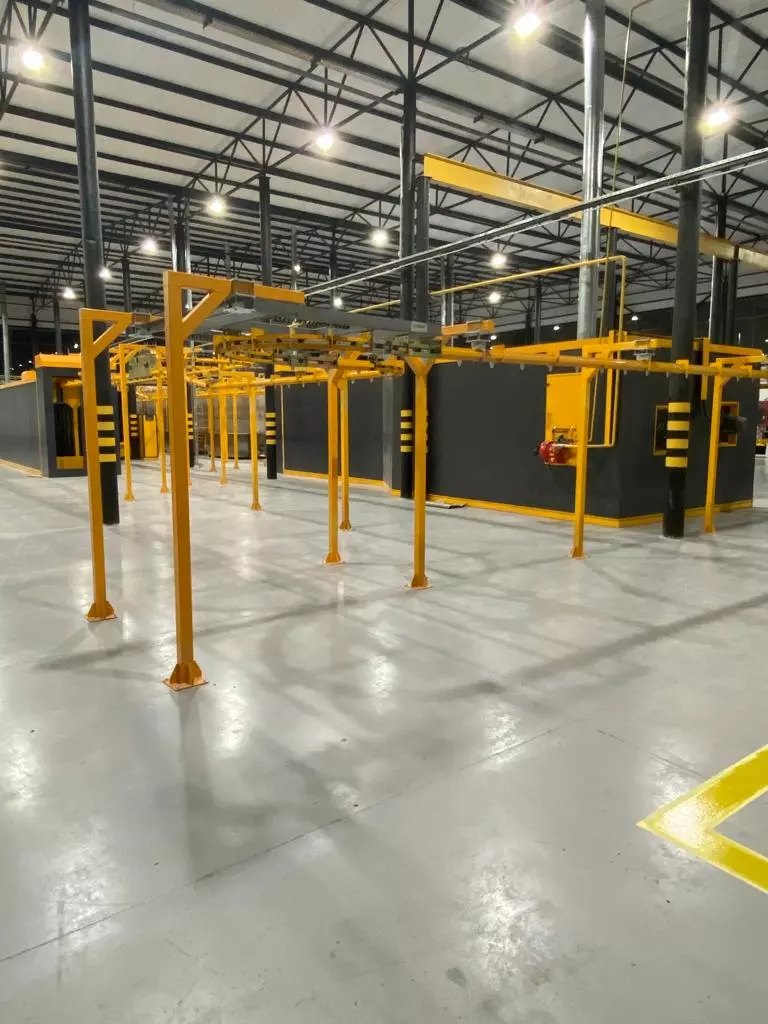
Un four de polymérisation automatisé est une installation utilisée dans le processus de revêtement en poudre pour durcir et fixer le revêtement appliqué sur les pièces. L’automatisation de ce type de four vise à améliorer l’efficacité, la cohérence et la productivité du processus de polymérisation. Voici quelques caractéristiques et éléments associés à un four de polymérisation automatisé :
- Système de convoyage automatisé : Les pièces revêtues en poudre sont généralement transportées automatiquement dans le four via un système de convoyage automatisé, tel qu’une chaîne, un convoyeur à bande ou un chariot automatisé.
- Contrôle de la température automatisé : Un système de contrôle de la température automatisé est utilisé pour maintenir des conditions thermiques précises à l’intérieur du four pendant le processus de polymérisation.
- Système de chauffage automatisé : Les fours de polymérisation sont équipés de systèmes de chauffage automatisés, tels que des éléments chauffants électriques ou des brûleurs à gaz, pour atteindre et maintenir la température requise.
- Système de refroidissement automatisé (si nécessaire) : Certains fours de polymérisation peuvent être équipés de systèmes de refroidissement automatisés pour abaisser la température des pièces après le durcissement du revêtement.
- Écrans de surveillance : Des écrans de surveillance permettent aux opérateurs de suivre en temps réel les paramètres du processus, tels que la température, le temps de cuisson et d’autres indicateurs clés.
- Système de contrôle du temps de cuisson : Le temps de cuisson est un paramètre critique dans le processus de polymérisation. Un système automatisé permet de programmer et de contrôler précisément la durée du processus.
- Système d’isolation thermique : Les fours de polymérisation automatisés sont souvent équipés d’une isolation thermique pour minimiser les pertes de chaleur et améliorer l’efficacité énergétique.
- Équipement de sécurité automatisé : Des dispositifs de sécurité automatisés, tels que des systèmes d’extinction d’incendie, peuvent être intégrés pour assurer la sécurité pendant le fonctionnement du four.
- Système de nettoyage automatique (si nécessaire) : Certains fours de polymérisation automatisés peuvent inclure des dispositifs automatisés de nettoyage pour maintenir la propreté et l’efficacité du four.
- Système d’évacuation des vapeurs : Les fours de polymérisation automatisés peuvent être équipés de systèmes d’évacuation des vapeurs pour éliminer les émissions potentielles résultant du processus de polymérisation.
L’automatisation de ces éléments dans un four de polymérisation contribue à assurer une polymérisation cohérente, à optimiser la productivité et à garantir la qualité constante du revêtement en poudre. Ces fours sont utilisés dans diverses industries, notamment l’automobile, l’aérospatiale, l’industrie des meubles et d’autres secteurs où le revêtement en poudre est appliqué sur des pièces métalliques ou d’autres substrats.
L’équipement de revêtement en poudre est utilisé pour appliquer une fine couche de poudre sur une surface métallique. Ce type de revêtement est appliqué par un procédé électrostatique et constitue une méthode très populaire pour la finition des pièces métalliques.
Ce type d’équipement peut être divisé en deux grandes catégories : automatiques et manuels. Les cabines automatiques sont plus populaires car elles offrent de meilleurs taux de production, mais elles sont également plus chères.
Une cabine à poudre est une enceinte dans laquelle se déroule le processus de revêtement en poudre. L’équipement de revêtement en poudre comprend un four dans lequel les pièces sont chauffées pour activer la poudre, un pistolet qui pulvérise ou brosse la poudre, une bande transporteuse qui déplace les pièces à travers le four et des pistolets de type cartouche pour appliquer des revêtements plus épais avec moins de pulvérisation.
Le revêtement en poudre est une technique utilisée pour donner une finition aux pièces métalliques. Cette technique est utilisée depuis de nombreuses années et reste aujourd’hui l’une des techniques les plus populaires.
L’équipement de revêtement en poudre comprend des cabines, des fours, des pistolets, des machines, des lignes et des convoyeurs. Une cabine peut être automatique ou manuelle. Une cabine automatique est plus chère qu’une cabine manuelle mais elle est aussi plus rapide et plus efficace
Peinture Poudre:
La peinture en poudre est un revêtement sec appliqué sous forme de poudre fine. Composée de pigments, polymères et charges, cette poudre est électrostatiquement chargée et adhère électrostatiquement à la surface métallique. Ce processus offre des avantages, tels qu’une application uniforme, une résistance à la corrosion et une efficacité environnementale en évitant l’utilisation de solvants. La poudre est ensuite polymérisée dans un four pour former un revêtement durable et est largement utilisée dans diverses industries pour ses propriétés esthétiques et protectrices.
Ligne de Peinture Automatique:
Une ligne de peinture automatique est un système industriel intégré pour l’application automatisée de revêtements, notamment la peinture en poudre. Elle comprend divers modules tels que la préparation de surface, la cabine de pulvérisation, le four de polymérisation, et des mécanismes de transport automatisés. L’automatisation améliore la précision, la productivité et la reproductibilité du processus de revêtement, tout en réduisant les coûts de main-d’œuvre. Ces lignes sont conçues pour garantir une application uniforme et efficace des revêtements sur des pièces variées, offrant ainsi une solution complète pour les besoins de peinture industrielle.
Revêtement par Poudrage:
Le revêtement par poudrage est une technique de finition de surface où une fine couche de poudre est appliquée sur un substrat. Cette méthode électrostatique utilise une charge électrique pour attirer la poudre vers la surface du matériau, assurant une distribution uniforme. Après l’application, la pièce est cuite dans un four pour permettre la fusion et la polymérisation de la poudre, formant ainsi un revêtement durable et résistant. Cette approche offre une excellente adhérence, une finition uniforme, une résistance à la corrosion et une variété de finitions esthétiques, en faisant un choix populaire dans l’industrie pour la protection et l’amélioration des surfaces.
Système de Peinture en Poudre:
Un système de peinture en poudre englobe l’ensemble des équipements et des processus nécessaires pour l’application efficace de revêtements en poudre. Il comprend typiquement une cabine de pulvérisation pour l’application de la poudre, un système de prétraitement pour la préparation de surface, un four de polymérisation pour le durcissement, des systèmes de transport automatisés et des dispositifs de contrôle de processus. Ces systèmes sont conçus pour assurer une performance optimale, une uniformité de revêtement, et une productivité élevée tout en respectant les normes de qualité. L’intégration de technologies avancées, telles que le contrôle automatisé, la récupération de poudre, et la surveillance en temps réel, contribue à optimiser l’efficacité du processus de peinture en poudre.
Équipement de Peinture Industrielle:
L’équipement de peinture industrielle englobe une variété d’outils et de machines spécialisés utilisés dans le processus de revêtement des surfaces dans des environnements industriels. Cela inclut des cabines de pulvérisation, des systèmes de prétraitement, des fours de polymérisation, des pistolets de pulvérisation automatique, des robots de revêtement, des transporteurs automatisés, des systèmes de filtration, et des dispositifs de contrôle de processus. L’objectif principal de cet équipement est d’assurer une application précise, uniforme et efficace des revêtements, répondant aux normes de qualité et de performance spécifiques à chaque industrie. L’innovation dans ces équipements vise à améliorer la productivité, la durabilité des revêtements, et à réduire l’impact environnemental du processus.
Cabine de Poudrage:
La cabine de poudrage est un composant clé d’une ligne de peinture en poudre. C’est l’enceinte où la poudre est appliquée sur la surface des pièces. Elle est conçue pour créer un environnement contrôlé, empêchant la dispersion non désirée de la poudre et assurant une application uniforme. Les parois de la cabine sont souvent équipées de filtres pour la récupération de la poudre excédentaire, contribuant ainsi à l’efficacité du processus et à la réduction des déchets. Des systèmes de ventilation sophistiqués garantissent une distribution optimale de la poudre, assurant une qualité constante du revêtement.
Four de Polymérisation:
Le four de polymérisation est une composante essentielle d’une ligne de peinture en poudre. Après l’application de la poudre, les pièces revêtues sont acheminées dans le four où la polymérisation se produit. Ce processus implique la fusion et la réticulation des particules de poudre, formant un revêtement solide, durable et résistant. La température et le temps de séjour dans le four sont soigneusement contrôlés pour garantir une polymérisation complète sans compromettre les propriétés du revêtement. Ces fours jouent un rôle crucial dans la création de revêtements de haute qualité offrant résistance à la corrosion, durabilité et esthétique.
Pistolaire Automatique:
Un pistolet automatique est un dispositif de pulvérisation automatisé utilisé dans les lignes de peinture en poudre. Équipé d’une électrode chargée, le pistolet applique électrostatiquement la poudre sur la surface des pièces à revêtir. L’automatisation de ce processus garantit une application uniforme de la poudre, améliorant l’efficacité et la précision. Les pistolets automatiques peuvent être programmés pour s’adapter à différentes géométries de pièces, assurant ainsi une couverture homogène sur des formes variées. L’utilisation de pistolets automatiques contribue à une productivité accrue, une réduction des erreurs humaines et une optimisation globale du processus de peinture en poudre.
Prétraitement de Surface:
Le prétraitement de surface est une étape cruciale dans le processus de peinture en poudre. Il vise à préparer la surface des pièces en éliminant les contaminants, l’oxydation et les impuretés, assurant ainsi une adhérence optimale du revêtement. Les méthodes de prétraitement comprennent souvent le dégraissage, le dérochage, la conversion chimique, et le rinçage. Ces procédés créent une surface propre et réactive, favorisant une liaison solide entre la poudre et la pièce. Un prétraitement efficace améliore la durabilité du revêtement, résiste à la corrosion et garantit la qualité constante du processus de peinture en poudre.
Transporteur à Chaîne:
Le transporteur à chaîne est un composant vital dans une ligne de peinture en poudre, responsable du déplacement des pièces à travers différentes étapes du processus. Il est équipé de chaînes robustes qui transportent les pièces de manière synchronisée, assurant ainsi une progression régulière. Ces transporteurs sont conçus pour supporter des charges variées et peuvent être intégrés avec des mécanismes de suspension adaptés à la géométrie des pièces. L’automatisation du transporteur à chaîne contribue à une efficacité accrue, un contrôle précis du temps de cycle et une optimisation globale de la ligne de peinture en poudre.
Cabine de Prétraitement:
La cabine de prétraitement est un élément clé dans le processus de peinture en poudre, dédiée à la préparation adéquate des surfaces des pièces avant l’application du revêtement. À l’intérieur de la cabine, les pièces subissent des étapes telles que le dégraissage, le dérochage, et parfois la conversion chimique. Ces processus éliminent les contaminants et créent une surface réceptive pour assurer une adhérence optimale du revêtement. Une cabine de prétraitement bien conçue garantit la qualité constante du processus, contribuant ainsi à la durabilité, à la résistance à la corrosion, et à l’uniformité du revêtement final.
Système de Récupération de Poudre:
Le système de récupération de poudre est une technologie intégrée dans une ligne de peinture en poudre pour minimiser les déchets. Il capture la poudre excédentaire lors de l’application, la sépare des particules non adhérées, et la recycle pour une utilisation ultérieure. Ceci non seulement réduit les coûts de matériaux, mais aussi diminue l’impact environnemental en limitant les déchets. Les systèmes modernes de récupération de poudre utilisent des filtres et des cyclones pour séparer la poudre, contribuant ainsi à une utilisation efficiente des matériaux et à une gestion durable du processus de peinture en poudre.
Contrôle de Processus Automatisé:
Le contrôle de processus automatisé dans une ligne de peinture en poudre implique l’utilisation de systèmes informatisés pour surveiller et réguler les différentes étapes du processus. Des capteurs, des caméras et des algorithmes sont utilisés pour recueillir des données en temps réel, permettant un ajustement automatique des paramètres tels que la pression d’air, la température du four, et la quantité de poudre appliquée. Cette automatisation assure une constance, une précision et une réactivité accrues, contribuant à la qualité uniforme du revêtement, à l’efficacité opérationnelle, et à la réduction des erreurs humaines.
Technologie de Revêtement:
La technologie de revêtement englobe les méthodes et les matériaux utilisés pour appliquer des revêtements protecteurs ou décoratifs sur des surfaces. Dans le contexte de la peinture en poudre, cette technologie inclut des formulations de poudre spécifiques, des techniques d’application électrostatique, et des processus de durcissement. L’évolution constante de cette technologie vise à améliorer l’adhérence, la résistance à la corrosion, la variété des finitions, tout en minimisant les impacts environnementaux. Des recherches continues favorisent le développement de revêtements plus durables, esthétiques et adaptés aux exigences spécifiques des industries variées.
Application Électrostatique:
L’application électrostatique est une technique clé dans le processus de peinture en poudre. Lors de cette étape, la poudre est chargée électrostatiquement à l’aide d’une électrode, puis appliquée sur la surface métallique préalablement mise à la terre. La charge électrostatique assure une adhérence efficace de la poudre sur la pièce, créant ainsi un revêtement uniforme. Cette méthode permet également de minimiser les pertes de poudre, car les particules non adhérées peuvent être récupérées et réutilisées. L’application électrostatique contribue ainsi à l’efficacité du processus, à la réduction des déchets, et à une qualité constante du revêtement.
Adhérence de la Poudre:
L’adhérence de la poudre est cruciale pour assurer la qualité et la durabilité du revêtement dans le processus de peinture en poudre. Elle dépend de plusieurs facteurs tels que la préparation de surface, la charge électrostatique lors de l’application, et la qualité de la poudre elle-même. Une bonne adhérence garantit que la poudre reste fixée à la surface de la pièce pendant le processus de polymérisation, formant ainsi un revêtement solide, résistant et uniforme. Des contrôles précis du processus, y compris la surveillance de la température et du temps de cuisson, contribuent à optimiser l’adhérence, assurant ainsi la qualité du revêtement final.
Cycle de Revêtement:
Le cycle de revêtement dans une ligne de peinture en poudre représente l’ensemble des étapes depuis la préparation de surface jusqu’à la polymérisation du revêtement. Il débute par le prétraitement de la pièce, inclut l’application de la poudre, le transport à travers la ligne automatisée, et se termine avec le durcissement dans le four. La gestion efficace de ce cycle est essentielle pour assurer la qualité, la productivité et la durabilité du revêtement. Des contrôles précis, une synchronisation optimale des étapes, et une surveillance constante contribuent à l’efficacité globale du processus de peinture en poudre.
Système de Filtration:
Le système de filtration est un élément essentiel d’une ligne de peinture en poudre, conçu pour maintenir la qualité de l’air à l’intérieur de la cabine de pulvérisation et du reste de l’environnement de travail. Il utilise des filtres spécifiques pour capturer les particules de poudre non adhérées et les contaminants, évitant ainsi leur dispersion dans l’atmosphère. Un système de filtration efficace contribue non seulement à la protection de l’environnement, mais aussi à la qualité du revêtement en minimisant les imperfections potentielles causées par des particules indésirables. Un entretien régulier de ces systèmes garantit leur performance optimale et le respect des normes environnementales.
Élimination des Déchets de Poudre:
L’élimination des déchets de poudre fait référence à la gestion des excédents de poudre qui ne sont pas adhérés à la surface des pièces pendant le processus de peinture en poudre. Les systèmes de récupération de poudre, tels que les cyclones et les filtres, permettent de séparer la poudre excédentaire, la rendant apte à être recyclée. La gestion efficace de ces déchets contribue à réduire les coûts en matériaux, à minimiser les impacts environnementaux, et à maintenir une efficacité économique dans le processus global de peinture en poudre.
Efficacité Énergétique:
L’efficacité énergétique dans une ligne de peinture en poudre se rapporte à l’utilisation judicieuse de l’énergie tout au long du processus. Cela inclut l’optimisation des fours de polymérisation, le contrôle précis des températures, et l’utilisation de technologies écoénergétiques. Les systèmes de récupération de chaleur, par exemple, peuvent être intégrés pour minimiser la consommation énergétique. Une approche axée sur l’efficacité énergétique non seulement réduit les coûts opérationnels, mais contribue également à des pratiques durables en minimisant l’empreinte carbone du processus de peinture en poudre.
Productivité de la Ligne:
La productivité de la ligne dans le contexte d’une ligne de peinture en poudre mesure l’efficacité globale du processus. Elle est influencée par des facteurs tels que le temps de cycle, la gestion des flux de travail, la fiabilité des équipements et l’automatisation des tâches. Une ligne de peinture productive maximise le rendement des pièces revêtues, réduit les temps d’arrêt, et optimise l’utilisation des ressources. L’intégration de technologies avancées, le suivi de la performance, et la maintenance proactive contribuent à maintenir une productivité élevée tout en maintenant des normes élevées de qualité de revêtement.
Revêtement en Poudre sans Solvant:
Le revêtement en poudre sans solvant est une approche respectueuse de l’environnement dans laquelle aucune substance chimique volatile n’est utilisée comme véhicule pour la poudre. Contrairement aux peintures liquides qui peuvent contenir des solvants volatils organiques, le processus de peinture en poudre sans solvant élimine cette composante, réduisant ainsi les émissions nocives dans l’air. Cette méthode contribue à la durabilité environnementale en minimisant la pollution atmosphérique, offrant une solution de revêtement plus écologique tout en maintenant les avantages de durabilité, d’adhérence et de résistance caractéristiques de la peinture en poudre.
Contrôle de la Qualité:
Le contrôle de la qualité dans une ligne de peinture en poudre implique la surveillance systématique de chaque étape du processus pour garantir que les pièces revêtues répondent aux normes spécifiées. Cela comprend l’inspection visuelle, la mesure de l’épaisseur du revêtement, la vérification de l’adhérence, et d’autres critères de performance. Des technologies telles que la spectroscopie et les caméras intelligentes sont souvent utilisées pour assurer une évaluation précise. Un contrôle de qualité rigoureux garantit la cohérence, la fiabilité et la conformité des revêtements, contribuant à la satisfaction du client et à la réputation de la ligne de peinture en poudre.
Système de Séchage:
Le système de séchage dans une ligne de peinture en poudre est responsable de l’élimination de l’humidité résiduelle après l’application de la poudre. Il est crucial pour préparer les pièces avant le processus de polymérisation. Ce système utilise généralement de l’air chaud circulant à travers la pièce pour accélérer le séchage. Un contrôle précis de la température et de la durée du séchage est essentiel pour assurer une surface sèche et prête à recevoir le revêtement polymérisé dans le four. Un séchage efficace contribue à la qualité du revêtement final et à la prévention de défauts potentiels.
Peinture sans Solvant:
La peinture sans solvant est une solution respectueuse de l’environnement, dépourvue de substances volatiles organiques. Contrairement aux peintures traditionnelles qui utilisent des solvants pour maintenir la consistance liquide, la peinture sans solvant utilise des composants non volatils, réduisant ainsi les émissions nocives dans l’air. Ce type de peinture offre des avantages en termes de qualité de l’air intérieur, de sécurité des travailleurs et de respect des normes environnementales. L’absence de solvants contribue également à la durabilité du revêtement, offrant une alternative écologique tout en conservant les propriétés protectrices et esthétiques nécessaires.
Équipement de Manipulation des Pièces:
L’équipement de manipulation des pièces dans une ligne de peinture en poudre englobe les dispositifs automatisés utilisés pour déplacer les pièces tout au long du processus. Cela inclut des systèmes de convoyeurs, des robots de manipulation, des chariots automatisés, et d’autres mécanismes adaptés à la géométrie des pièces. L’efficacité de cet équipement est cruciale pour assurer un flux de travail continu, une synchronisation précise des étapes, et une manipulation sécurisée des pièces. L’automatisation de la manipulation des pièces contribue à une productivité accrue, à la réduction des erreurs humaines, et à l’optimisation globale du processus de peinture en poudre.
Robot de Pulvérisation:
Un robot de pulvérisation est un dispositif automatisé équipé d’un pistolet de pulvérisation, utilisé pour appliquer la poudre de manière précise sur les surfaces des pièces. Ces robots offrent une grande flexibilité et une reproductibilité élevée, car ils peuvent être programmés pour s’adapter à différentes formes géométriques. L’utilisation de robots de pulvérisation contribue à une application uniforme de la poudre, à une réduction des erreurs humaines, et à une optimisation de la productivité. Ces robots peuvent être intégrés de manière stratégique dans une ligne de peinture en poudre pour améliorer l’efficacité du processus global.
Économie de Poudre:
L’économie de poudre dans le contexte d’une ligne de peinture en poudre se réfère à la gestion efficiente et à l’utilisation judicieuse de la poudre de revêtement. Cela implique la minimisation des pertes de poudre pendant l’application, la récupération et le recyclage des surplus, ainsi que l’optimisation des quantités de poudre utilisées pour chaque application. L’objectif est de réduire les coûts matériels, de minimiser les déchets et de promouvoir une utilisation durable des ressources. Les systèmes de récupération de poudre et les technologies de dosage précis contribuent à cette économie, garantissant une utilisation efficiente de la poudre tout au long du processus.
Revêtement Anticorrosion:
Le revêtement anticorrosion est un aspect essentiel dans le domaine de la peinture en poudre, visant à protéger les surfaces métalliques contre la corrosion. La poudre utilisée pour le revêtement est formulée avec des composants qui offrent une barrière efficace contre l’humidité et d’autres agents corrosifs. Lorsque correctement appliqué et polymérisé, le revêtement anticorrosion garantit une protection à long terme, prolongeant la durée de vie des pièces métalliques et réduisant les besoins de maintenance. Ceci est particulièrement crucial dans des environnements exposés aux intempéries ou à des conditions corrosives.
Temps de Cycle:
Le temps de cycle dans une ligne de peinture en poudre représente la durée totale nécessaire pour compléter le processus de revêtement d’une pièce, depuis la préparation de surface jusqu’à la sortie du four de polymérisation. Optimiser le temps de cycle est essentiel pour améliorer la productivité de la ligne. Cela implique l’efficacité des équipements, la synchronisation des étapes du processus, et la réduction des temps morts. Un temps de cycle bien géré contribue à une production rapide, à une utilisation efficace des ressources et à une livraison rapide des produits revêtus.
Revêtement Texturé:
Le revêtement texturé dans le contexte de la peinture en poudre se réfère à une finition de surface qui présente une texture tactile ou visuelle. Cette texture peut varier de légèrement rugueuse à très texturée, ajoutant un aspect esthétique distinctif aux pièces revêtues. La poudre utilisée pour ce type de revêtement est formulée pour créer cette texture souhaitée lors de la polymérisation. Les revêtements texturés sont souvent choisis pour des raisons esthétiques, mais ils peuvent également offrir une résistance accrue aux rayures et masquer certaines imperfections de surface.
Processus de Durcissement:
Le processus de durcissement est une étape clé dans la peinture en poudre, se produisant après l’application de la poudre sur la surface des pièces. Les pièces revêtues sont placées dans un four où la poudre est chauffée à des températures spécifiques, provoquant sa fusion, réticulation et durcissement. Ce processus transforme la poudre en un revêtement solide, durable et résistant. La précision des paramètres de température et de temps de durcissement est essentielle pour assurer la qualité du revêtement final en termes d’adhérence, de résistance chimique et de résistance mécanique.
Système de Surveillance:
Le système de surveillance dans une ligne de peinture en poudre utilise des capteurs, des caméras et d’autres dispositifs pour collecter des données en temps réel sur divers aspects du processus. Cela inclut la surveillance de la température, de la pression, de l’épaisseur du revêtement, et d’autres paramètres critiques. Ces données sont analysées pour garantir la conformité aux normes de qualité, pour ajuster les paramètres si nécessaire, et pour assurer la cohérence du processus. Un système de surveillance efficace contribue à la fiabilité du processus, à la détection précoce des problèmes potentiels, et à l’optimisation continue de la qualité des revêtements.
Système de Refroidissement:
Le système de refroidissement dans une ligne de peinture en poudre intervient après le processus de polymérisation, où les pièces revêtues sortent du four à des températures élevées. Ce système utilise des méthodes de refroidissement contrôlées pour abaisser progressivement la température des pièces, les rendant ainsi aptes à la manipulation et à l’emballage. Un refroidissement approprié est crucial pour éviter des déformations ou des dommages aux pièces. Les méthodes de refroidissement peuvent inclure des systèmes d’air pulsé, des chambres de refroidissement, ou d’autres dispositifs adaptés à la taille et à la géométrie des pièces revêtues.
Ligne de Peinture en Continu:
Une ligne de peinture en continu est une configuration où le processus de peinture en poudre est organisé de manière continue, sans interruption significative entre les étapes. Les pièces à revêtir sont transportées de manière fluide à travers différentes stations, telles que la préparation de surface, la cabine de pulvérisation, le four de polymérisation, et d’autres, sans arrêt majeur du flux de production. Ce type de configuration est conçu pour maximiser l’efficacité, réduire les temps d’arrêt et assurer une production constante de pièces revêtues.
Contrôle Dimensionnel:
Le contrôle dimensionnel dans une ligne de peinture en poudre implique la vérification des dimensions et de la géométrie des pièces revêtues. Des dispositifs de mesure précis, tels que des calibres, des scanners laser ou des systèmes de vision, sont utilisés pour s’assurer que les pièces respectent les spécifications dimensionnelles requises. Un contrôle dimensionnel rigoureux garantit la conformité aux normes de qualité, la précision des dimensions finales, et contribue à la satisfaction du client en fournissant des pièces revêtues conformes aux exigences.
Nettoyage des Surfaces:
Le nettoyage des surfaces est une étape préliminaire cruciale dans le processus de peinture en poudre. Il vise à éliminer les contaminants, les huiles, la rouille et d’autres impuretés de la surface des pièces à revêtir. Un nettoyage approfondi favorise une adhérence optimale de la poudre et garantit la qualité du revêtement final. Les méthodes de nettoyage peuvent inclure des procédés chimiques, tels que le dégraissage, des méthodes mécaniques, comme le grenaillage, ou une combinaison de plusieurs techniques pour préparer la surface de manière adéquate avant l’application de la poudre.
Étuvage:
L’étuvage est une étape complémentaire dans certaines lignes de peinture en poudre, intervenant après le nettoyage des surfaces. Cette étape consiste à chauffer les pièces à des températures modérées pour éliminer l’humidité résiduelle et assurer une surface parfaitement sèche avant l’application de la poudre. Un étuvage efficace contribue à une meilleure adhérence de la poudre, évitant ainsi des problèmes potentiels liés à l’humidité, tels que des bulles ou des défauts de revêtement. Cette étape préparatoire est particulièrement importante pour des pièces susceptibles d’accumuler de l’humidité pendant le processus de fabrication.
Système de Préchauffage:
Le système de préchauffage est une composante optionnelle dans certaines lignes de peinture en poudre, utilisée pour chauffer les pièces avant l’application de la poudre. Le préchauffage des pièces peut améliorer l’adhérence de la poudre en favorisant une surface légèrement chauffée. Cela peut être particulièrement bénéfique pour des pièces massives ou dans des environnements où la température ambiante peut affecter la qualité du revêtement. L’utilisation d’un système de préchauffage peut être soigneusement ajustée en fonction des spécificités des pièces et des conditions de production pour optimiser la qualité du revêtement final.
Revêtement Multicouche:
Le revêtement multicouche dans la peinture en poudre implique l’application successive de plusieurs couches de poudre sur une pièce. Chaque couche peut avoir des propriétés spécifiques, telles que des caractéristiques de couleur, de texture, ou des propriétés fonctionnelles distinctes. Ce processus permet d’obtenir des finitions complexes et de répondre à des exigences esthétiques ou techniques particulières. Chaque couche est polymérisée individuellement avant l’application de la suivante, assurant ainsi une adhérence et une intégrité entre les couches du revêtement final. Le revêtement multicouche offre une polyvalence dans la conception des finitions tout en maintenant les avantages de durabilité de la peinture en poudre.
Contrôle de l’Épaisseur du Revêtement:
Le contrôle de l’épaisseur du revêtement est une étape critique dans le processus de peinture en poudre, visant à garantir que la quantité de poudre appliquée est conforme aux spécifications. Des dispositifs tels que des instruments de mesure par ultrasons, des jauges magnétiques ou des systèmes optiques sont utilisés pour évaluer l’épaisseur du revêtement. Un contrôle précis assure la conformité aux normes de qualité, évite des problèmes tels que des surépaisseurs ou des sous-épaisseurs, et contribue à la durabilité du revêtement en garantissant une couche uniforme et adéquate.
Durabilité du Revêtement:
La durabilité du revêtement dans la peinture en poudre est la capacité du revêtement à maintenir ses propriétés protectrices et esthétiques au fil du temps dans des conditions d’utilisation variées. Cela inclut la résistance à la corrosion, la stabilité de la couleur, la résistance aux rayures et aux chocs, ainsi que d’autres caractéristiques spécifiques aux besoins de l’application. La durabilité est un aspect essentiel, garantissant la longévité du revêtement, réduisant les besoins de maintenance et assurant une performance constante des pièces revêtues dans divers environnements et conditions.
Contrôle de l’Humidité:
Le contrôle de l’humidité est une considération importante dans certaines lignes de peinture en poudre, en particulier lors de l’application sur des pièces métalliques susceptibles de retenir de l’humidité. Des dispositifs de contrôle de l’humidité, tels que des déshumidificateurs, peuvent être utilisés pour maintenir un environnement de travail sec. Cela contribue à prévenir les problèmes potentiels tels que la formation de bulles ou d’imperfections de revêtement liées à l’humidité. Le contrôle rigoureux de l’humidité assure une adhérence optimale de la poudre et contribue à la qualité du revêtement final.
Technologie de Masquage:
La technologie de masquage dans la peinture en poudre implique l’utilisation de matériaux ou de méthodes spécifiques pour protéger certaines zones des pièces contre l’application de la poudre. Cela permet de créer des zones non revêtues ou de maintenir des sections spécifiques dans des finitions différentes. Des techniques de masquage précises sont essentielles pour obtenir des designs complexes, des détails spécifiques ou pour éviter d’appliquer la poudre sur des zones critiques. Ces méthodes de masquage peuvent inclure l’utilisation de rubans, de pochoirs, ou d’autres matériaux spécifiques au processus de peinture en poudre.
Revêtement Transparent:
Le revêtement transparent dans la peinture en poudre est une finition qui ne modifie pas la couleur ou l’apparence naturelle du matériau sous-jacent. Il est conçu pour fournir une protection supplémentaire tout en conservant la transparence d’origine. Ce type de revêtement est souvent utilisé lorsque la préservation de l’apparence naturelle d’une surface est souhaitée, tout en offrant une résistance accrue aux éléments tels que la corrosion. Il est couramment utilisé dans des applications où la visibilité de la texture ou de la couleur du matériau est importante, comme dans le revêtement de surfaces métalliques décoratives.
Revêtement Isolant Électrique:
Le revêtement isolant électrique dans la peinture en poudre est conçu pour offrir une isolation électrique sur des composants ou des pièces spécifiques. Cette finition est formulée pour résister à des niveaux de tension électrique et à des conditions spécifiques. Elle est souvent utilisée dans des applications où une isolation électrique est cruciale pour éviter des courts-circuits, des interférences ou des défaillances électriques. Le revêtement isolant électrique peut être appliqué de manière ciblée sur des zones spécifiques des pièces, offrant ainsi une protection électrique tout en conservant d’autres propriétés du matériau sous-jacent.
Élimination des Impuretés:
L’élimination des impuretés dans une ligne de peinture en poudre est un processus visant à éliminer tout contaminant ou résidu indésirable des pièces avant l’application de la poudre. Cela peut inclure des étapes telles que le dépoussiérage, le nettoyage au moyen de solvants, ou d’autres méthodes spécifiques au type de pièces à revêtir. L’élimination efficace des impuretés est cruciale pour assurer une adhérence optimale de la poudre, éviter les défauts de revêtement, et garantir la qualité du résultat final.
Revêtement Antimicrobien:
Le revêtement antimicrobien dans la peinture en poudre intègre des agents spécifiques destinés à inhiber la croissance des micro-organismes, tels que les bactéries et les moisissures, sur la surface revêtue. Cette propriété confère au revêtement une protection supplémentaire contre les problèmes liés aux micro-organismes, tels que la dégradation de la surface et la propagation de germes. Les revêtements antimicrobiens sont couramment utilisés dans des environnements où la propreté et la prévention de la contamination bactérienne sont des préoccupations essentielles, comme dans les secteurs de la santé, de l’alimentation, et d’autres domaines sensibles
Innovation des Matériaux de Revêtement:
L’innovation des matériaux de revêtement dans la peinture en poudre englobe la recherche et le développement continus de nouvelles formulations de poudre. Cela inclut l’exploration de matériaux plus durables, écologiques, offrant des propriétés améliorées en termes de résistance, d’adhérence, de texture, et d’autres caractéristiques spécifiques aux besoins de l’application. L’innovation vise à améliorer la performance des revêtements, à réduire l’impact environnemental, et à répondre aux demandes croissantes de divers secteurs industriels. Les avancées constantes dans les matériaux de revêtement contribuent à une évolution continue de la peinture en poudre en tant que technologie de protection et de décoration de surfaces
Revêtement Résistant aux UV:
Le revêtement résistant aux UV dans la peinture en poudre est formulé pour offrir une protection contre les rayons ultraviolets (UV) du soleil. Cette caractéristique est essentielle pour prévenir la décoloration, le craquelage et d’autres effets indésirables causés par l’exposition prolongée aux UV. Les pièces revêtues de ce type de revêtement conservent ainsi leur apparence esthétique et leurs propriétés fonctionnelles plus longtemps, ce qui les rend adaptées à des applications extérieures où l’exposition aux conditions météorologiques est fréquente. Le revêtement résistant aux UV contribue à la durabilité et à la qualité à long terme des surfaces revêtues.
La peinture en poudre est une méthode de revêtement de surface qui utilise de la poudre sèche au lieu de peinture liquide. Ce procédé est devenu très populaire dans l’industrie en raison de ses nombreux avantages par rapport aux méthodes de peinture traditionnelles. L’équipement de poudrage joue un rôle crucial dans l’application de ce type de revêtement.
Avantages du Revêtement en Poudre
- Durabilité et résistance : Le revêtement en poudre offre une finition robuste et durable qui résiste aux égratignures, à l’usure et aux conditions climatiques difficiles.
- Écologique : Contrairement aux peintures liquides, le revêtement en poudre ne contient pas de solvants ni de composés organiques volatils (COV), ce qui en fait une option respectueuse de l’environnement.
- Coût-Efficacité : Bien que l’investissement initial dans l’équipement puisse être élevé, les économies réalisées sur le long terme grâce à la réduction des déchets et à l’efficacité du processus compensent largement ce coût.
Applications Industrielles
Le revêtement en poudre est largement utilisé dans diverses industries, notamment l’automobile, l’électronique, les appareils électroménagers, et les équipements extérieurs. Ce procédé assure non seulement une finition esthétique, mais aussi une protection contre la corrosion et d’autres formes de dégradation.
Fours de polymérisation
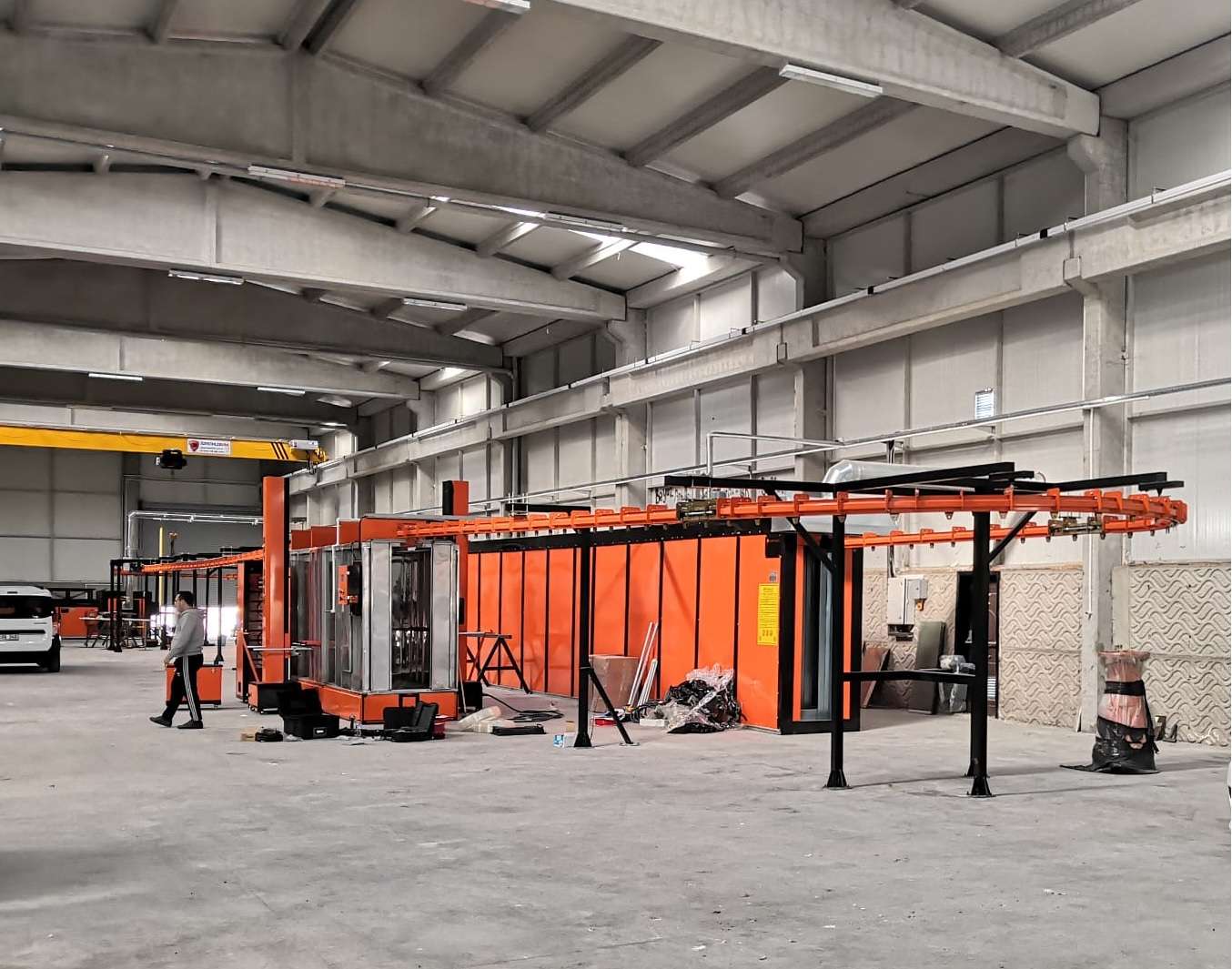
Les fours de polymérisation jouent un rôle essentiel dans le processus de revêtement en poudre, car ils permettent de chauffer la poudre appliquée pour qu’elle fonde et forme un film homogène et dur sur la surface de l’objet. Il existe plusieurs types de fours utilisés en fonction des besoins spécifiques de l’application.
Types de Fours
- Fours à convection : Ils utilisent l’air chaud pour transférer la chaleur à la pièce. Ces fours sont idéaux pour des charges lourdes et volumineuses.
- Fours infrarouges : Ils utilisent le rayonnement infrarouge pour chauffer directement la poudre, offrant un temps de polymérisation plus rapide.
- Fours à induction : Utilisés pour des applications spécifiques nécessitant un chauffage rapide et précis.
Caractéristiques Clés
Lors de la sélection d’un four de polymérisation, plusieurs caractéristiques doivent être prises en compte :
- Capacité de température : Doit correspondre aux exigences du type de poudre utilisée.
- Uniformité de la chaleur : Assure une répartition uniforme de la chaleur pour une finition uniforme.
- Efficacité énergétique : Les modèles économes en énergie permettent de réduire les coûts opérationnels.
Cabines de poudrage
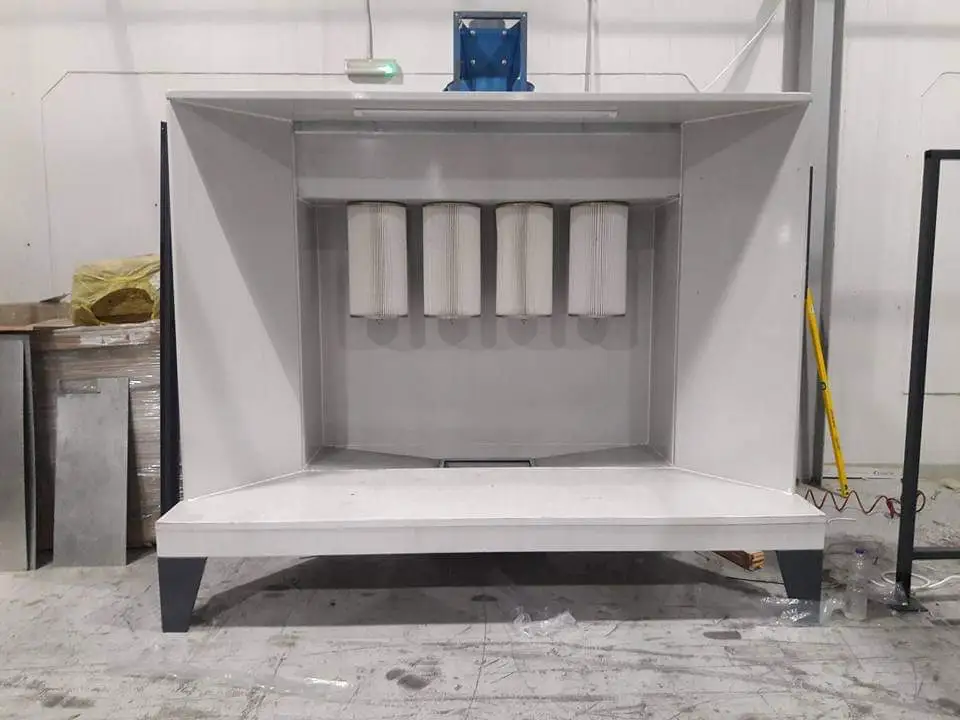
Les cabines de poudrage sont des environnements contrôlés où la poudre est appliquée sur les pièces. Elles sont conçues pour assurer une application efficace et sûre, tout en minimisant la contamination.
Conception et Structure
- Cabines ouvertes : Idéales pour les petites pièces et une production à petite échelle.
- Cabines fermées : Conviennent aux grandes pièces et à la production en série.
- Systèmes de récupération de poudre : Intégrés pour récupérer et réutiliser l’excès de poudre.
Importance de la Ventilation et de la Sécurité
Une ventilation adéquate est cruciale pour éviter l’accumulation de particules de poudre, réduisant ainsi les risques d’incendie et d’explosion. De plus, les cabines doivent être équipées de systèmes de filtration pour protéger les travailleurs contre l’inhalation de poudre.
Pistolets de pulvérisation
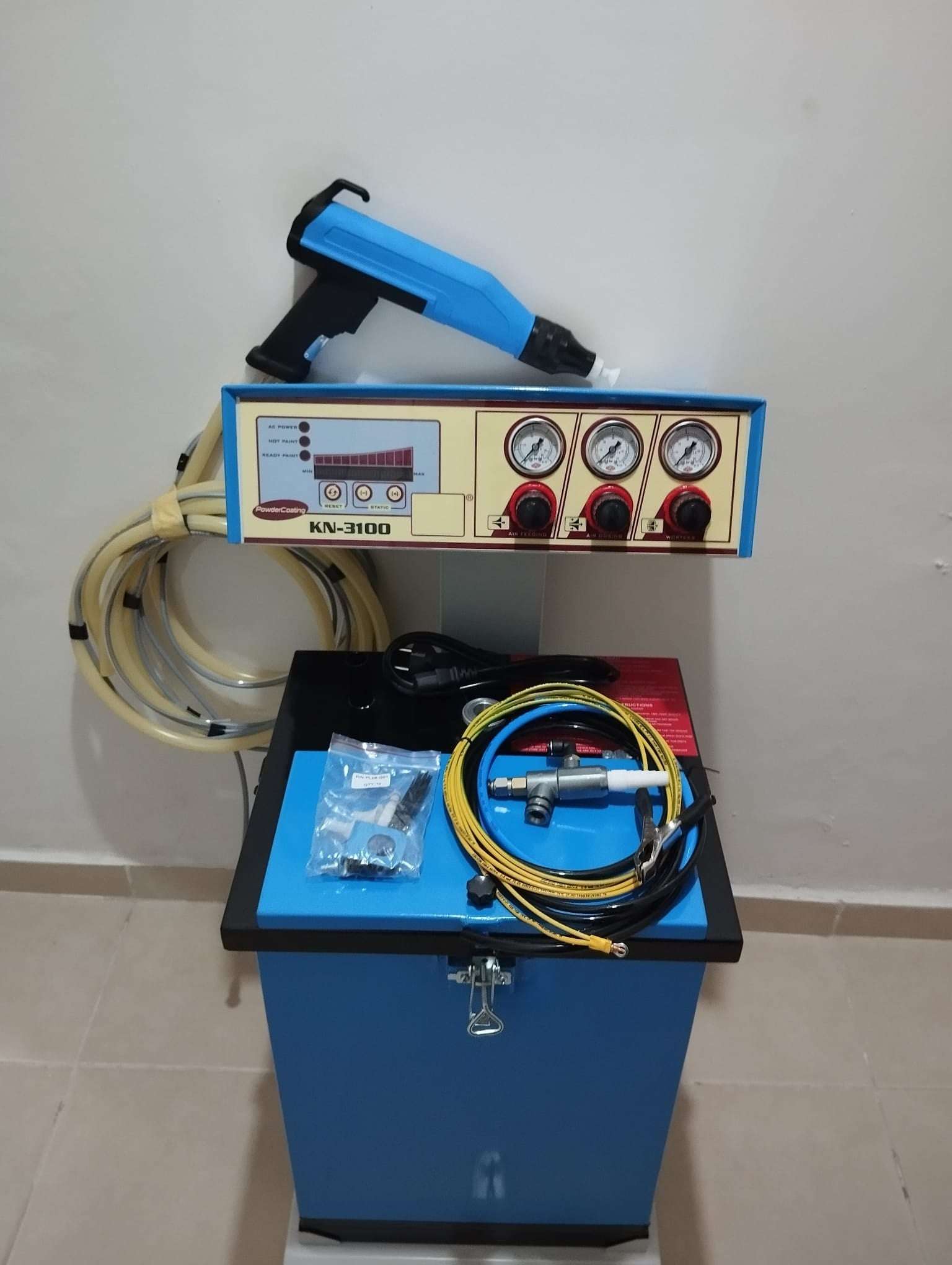
Les pistolets de pulvérisation de poudre sont des dispositifs utilisés pour appliquer la poudre sur la surface de l’objet. Ils utilisent un champ électrostatique pour attirer la poudre vers la pièce, assurant une couverture uniforme.
Types de Pistolets de Pulvérisation
- Pistolets à corona : Utilisent une charge électrique pour ioniser la poudre.
- Pistolets tribo : La poudre est chargée par friction, idéale pour les surfaces complexes.
Fonctionnement et Avantages
Les pistolets de pulvérisation sont appréciés pour leur capacité à appliquer la poudre de manière uniforme et efficace. Leur utilisation réduit le gaspillage de poudre et offre une finition de haute qualité.
Maintien de l’équipement de poudrage
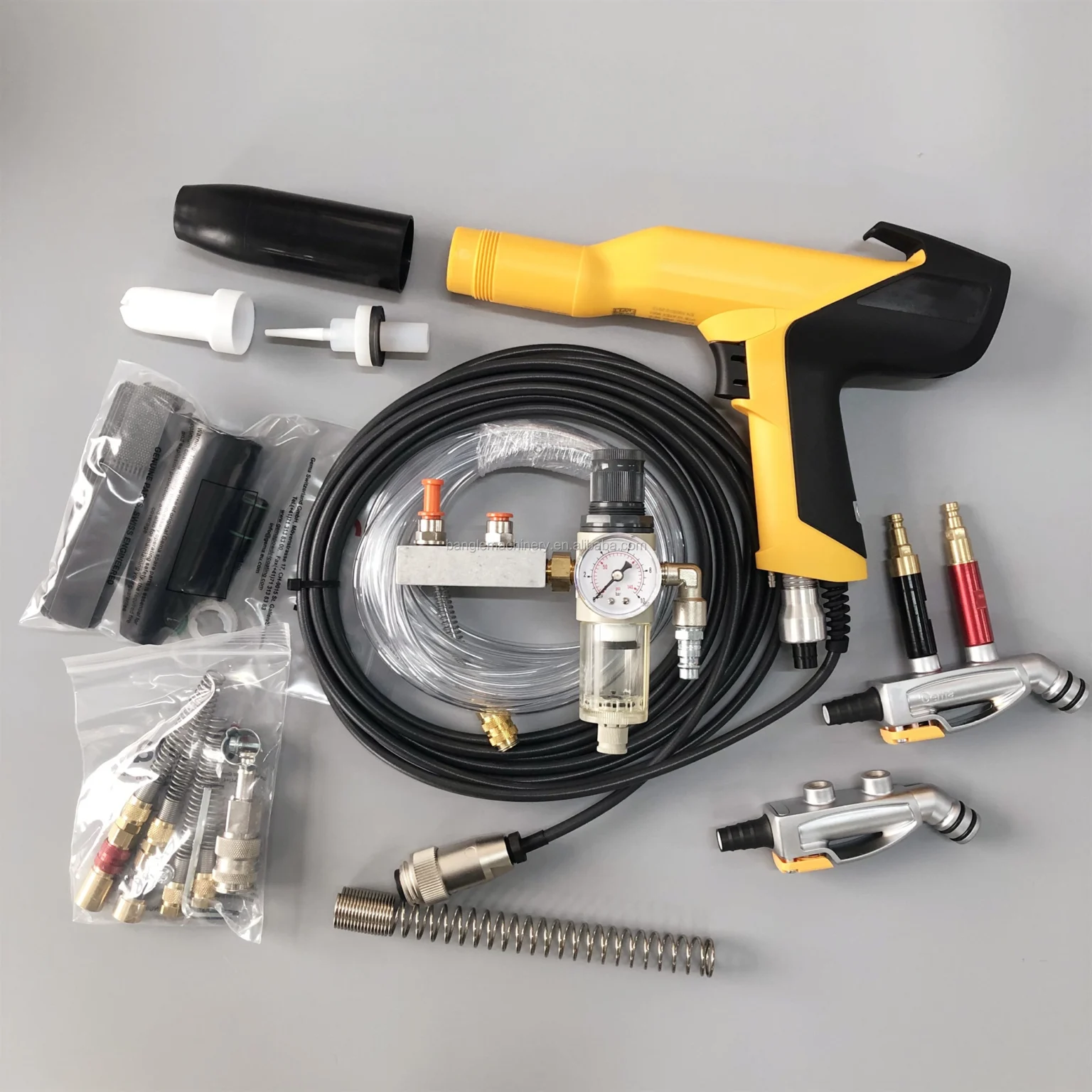
Le maintien de l’équipement de poudrage en bon état de fonctionnement est essentiel pour garantir une production continue et de haute qualité. Avoir des pièces de rechange à portée de main est crucial pour minimiser les temps d’arrêt.
Importance des Pièces de Rechange
Les pièces de rechange assurent la continuité des opérations en cas de défaillance de l’équipement. Cela inclut les filtres, les buses de pistolet, et les éléments chauffants.
Conseils d’Entretien
- Inspection régulière : Vérifiez les pièces pour détecter tout signe d’usure ou de dommage.
- Nettoyage : Maintenez les cabines et les pistolets propres pour éviter la contamination croisée.
- Formation du personnel : Assurez-vous que les opérateurs sont formés pour identifier et résoudre les problèmes potentiels.
Conseils d’entretien d’équipement
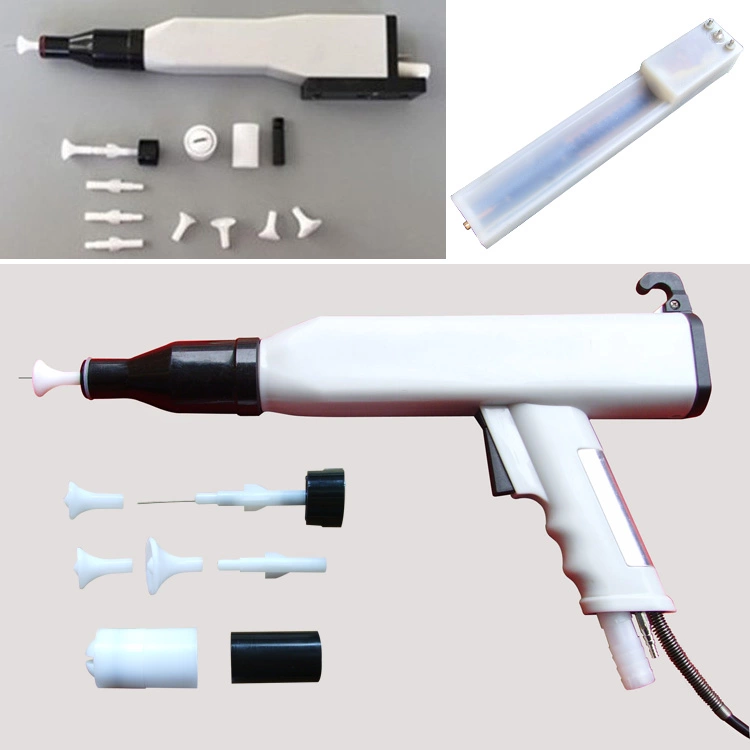
- Inspection Régulière
- Vérification Visuelle : Inspectez visuellement l’équipement régulièrement pour détecter des signes d’usure, de corrosion ou de dommages physiques. Cela inclut les câbles, les connexions électriques, et les composants mécaniques.
- Suivi des Composants : Tenez un registre des inspections régulières pour chaque pièce de l’équipement, ce qui vous permettra de détecter les tendances d’usure et de planifier les remplacements nécessaires.
- Nettoyage des Équipements
- Nettoyage des Pistolets de Pulvérisation : Démontage et nettoyage régulier des pistolets de pulvérisation pour éviter l’accumulation de poudre, qui peut obstruer les buses et affecter la qualité de l’application. Utilisez de l’air comprimé et des solvants recommandés pour le nettoyage.
- Entretien des Cabines de Poudrage : Nettoyez régulièrement l’intérieur des cabines pour éviter la contamination croisée des couleurs. Les systèmes de récupération de poudre doivent être vidés et nettoyés selon les instructions du fabricant.
- Filtres et Ventilation : Remplacez les filtres des systèmes de ventilation selon les recommandations du fabricant pour assurer une ventilation optimale et éviter l’accumulation de particules de poudre.
- Maintenance Préventive
- Lubrification des Composants Mécaniques : Appliquez régulièrement de la lubrification aux pièces mécaniques mobiles pour réduire l’usure et éviter les blocages.
- Calibration des Systèmes Électrostatiques : Assurez-vous que les systèmes de charge électrostatique sont correctement calibrés pour une application uniforme de la poudre. Vérifiez les connexions électriques et remplacez les pièces usées.
- Vérification des Températures de Four : Contrôlez régulièrement les températures des fours de polymérisation pour garantir qu’elles restent dans les limites recommandées pour la poudre utilisée. Des températures incorrectes peuvent entraîner des finitions de mauvaise qualité.
- Formation du Personnel
- Formation Continue : Assurez-vous que le personnel est correctement formé pour utiliser et entretenir l’équipement. Organisez des sessions de formation régulières pour actualiser les connaissances sur les nouvelles technologies et méthodes d’entretien.
- Sécurité au Travail : Éduquez le personnel sur les protocoles de sécurité, y compris l’utilisation d’équipements de protection individuelle (EPI) pour éviter les accidents et l’exposition aux particules de poudre.
- Gestion des Pièces de Rechange
- Inventaire des Pièces de Rechange : Maintenez un stock adéquat de pièces de rechange essentielles comme les buses de pulvérisation, les filtres, et les éléments chauffants pour réduire les temps d’arrêt en cas de panne.
- Commande de Pièces : Prévoyez à l’avance les commandes de pièces de rechange pour éviter les ruptures de stock qui pourraient perturber la production.
- Analyse des Performances
- Suivi des Indicateurs Clés : Surveillez les indicateurs de performance tels que l’efficacité énergétique, la qualité de la finition, et le taux de défauts pour identifier les domaines nécessitant des améliorations.
- Retour d’Expérience : Sollicitez des retours d’expérience du personnel opérant l’équipement pour identifier les problèmes récurrents et ajuster les procédures d’entretien en conséquence.
Conclusion
L’entretien adéquat des équipements de poudrage est essentiel pour garantir une production efficace, sûre et de haute qualité. En mettant en œuvre un programme de maintenance préventive et en formant le personnel aux meilleures pratiques, vous pouvez prolonger la durée de vie de vos équipements et optimiser vos opérations de revêtement en poudre. Assurez-vous de suivre les recommandations du fabricant pour chaque composant de l’équipement afin d’assurer leur bon fonctionnement.
N’hésitez pas à me dire si vous avez besoin de plus de détails sur un aspect particulier de l’entretien ou si vous souhaitez que d’autres sujets soient abordés.
Quelles pièces de rechange
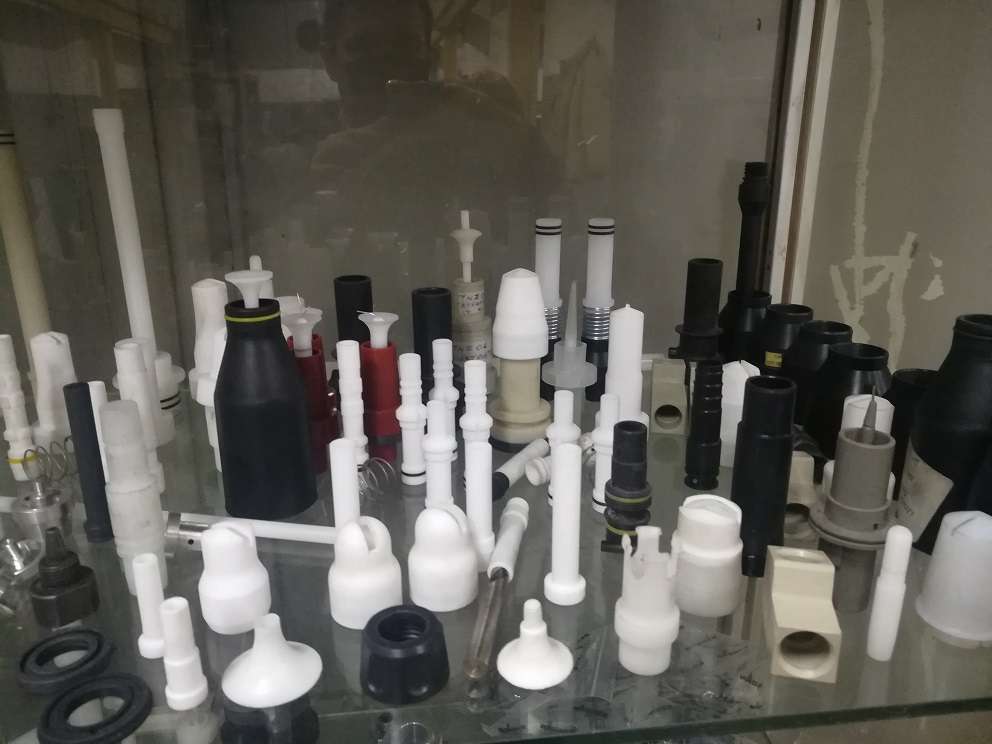
La maintenance efficace de l’équipement de poudrage implique la gestion proactive des pièces de rechange. Avoir les bonnes pièces à portée de main peut réduire considérablement les temps d’arrêt et maintenir la qualité de production. Voici une liste des pièces de rechange essentielles pour les équipements de poudrage :
Pièces de Rechange Essentielles pour l’Équipement de Poudrage
- Buses de Pistolet de Pulvérisation
- Types de Buses : Disponibles en différentes tailles et formes (rondes, plates, coniques) pour s’adapter aux divers types d’application et de finitions souhaitées.
- Usure : Les buses s’usent avec le temps en raison de l’abrasion de la poudre. Avoir des buses de rechange garantit que la qualité de la pulvérisation reste constante.
- Électrodes de Pistolet
- Fonction : Les électrodes chargent électrostatiquement la poudre pour l’application. Elles peuvent s’user ou s’endommager, ce qui affecte l’efficacité de l’application.
- Remplacement : Des électrodes de rechange sont cruciales pour maintenir une charge électrostatique efficace et une application uniforme.
- Filtres de Cabine
- Fonction des Filtres : Captent les particules de poudre en excès, évitant la contamination de l’air et l’accumulation de poudre à l’intérieur de la cabine.
- Types de Filtres : Incluent les filtres à cartouche et les filtres à sac, chacun ayant des besoins de remplacement réguliers pour garantir un environnement de travail propre et sûr.
- Pompes à Poudre
- Rôle des Pompes : Transportent la poudre du réservoir à l’applicateur. Les pompes peuvent s’user avec le temps et nécessitent des pièces de rechange comme des joints, des tuyaux, et des joints toriques.
- Maintenance : Un entretien régulier et la disponibilité de pièces de rechange sont essentiels pour éviter les interruptions de flux de poudre.
- Éléments Chauffants des Fours de Polymérisation
- Importance : Maintiennent la température nécessaire pour durcir la poudre. Les éléments chauffants peuvent s’user, nécessitant des remplacements pour maintenir la température uniforme dans le four.
- Types : Incluent les éléments chauffants électriques et les brûleurs à gaz.
- Joints et Joints Toriques
- Fonction : Assurent l’étanchéité des systèmes pneumatiques et hydrauliques. Les joints et les joints toriques peuvent se détériorer avec le temps, provoquant des fuites et des pertes d’efficacité.
- Disponibilité : Garder un stock de différents types et tailles de joints et de joints toriques est essentiel pour éviter les temps d’arrêt imprévus.
- Composants Électroniques
- Panneaux de Contrôle : Les cartes de circuits imprimés, les écrans de contrôle, et les capteurs peuvent nécessiter des remplacements en cas de panne.
- Capteurs et Commutateurs : Surveillent et contrôlent divers aspects de l’équipement. Les pièces de rechange aident à maintenir la précision et le contrôle des opérations.
- Pièces de Rechange pour Systèmes de Transport
- Chaînes et Rouleaux : Pour les systèmes de convoyage qui transportent les pièces à travers les différentes étapes du processus de revêtement.
- Moteurs et Réducteurs : Nécessitent des remplacements pour éviter les pannes des systèmes de transport.
- Agitateurs et Mélangeurs de Poudre
- Fonction : Maintiennent la poudre en mouvement pour éviter la sédimentation et assurer une distribution homogène. Les pièces mobiles, comme les pales d’agitation, peuvent s’user avec le temps.
Importance de la Gestion des Pièces de Rechange
Planification Proactive : Anticiper les besoins en pièces de rechange et maintenir un stock adéquat peut éviter des interruptions coûteuses de la production. Établir un calendrier de maintenance préventive permet de prédire les besoins en remplacements.
Fournisseurs de Confiance : Travailler avec des fournisseurs de pièces de rechange fiables garantit l’accès à des composants de haute qualité qui prolongent la durée de vie de l’équipement.
Consignation des Pièces : Mettre en place un système de consignation de pièces pour suivre l’utilisation des pièces de rechange et les réapprovisionner automatiquement.
Conclusion
La disponibilité de pièces de rechange essentielles et un programme de maintenance bien structuré sont cruciaux pour le bon fonctionnement des équipements de poudrage. La gestion proactive des pièces de rechange assure non seulement une production fluide mais aussi une qualité de revêtement constante. En ayant une stratégie d’entretien et de gestion des pièces bien définie, les entreprises peuvent réduire les temps d’arrêt et maximiser l’efficacité de leurs opérations de revêtement en poudre.
Si vous avez besoin de détails supplémentaires ou d’informations spécifiques sur l’un des composants ou des procédures, n’hésitez pas à me le faire savoir !
Pièces pour pistolets
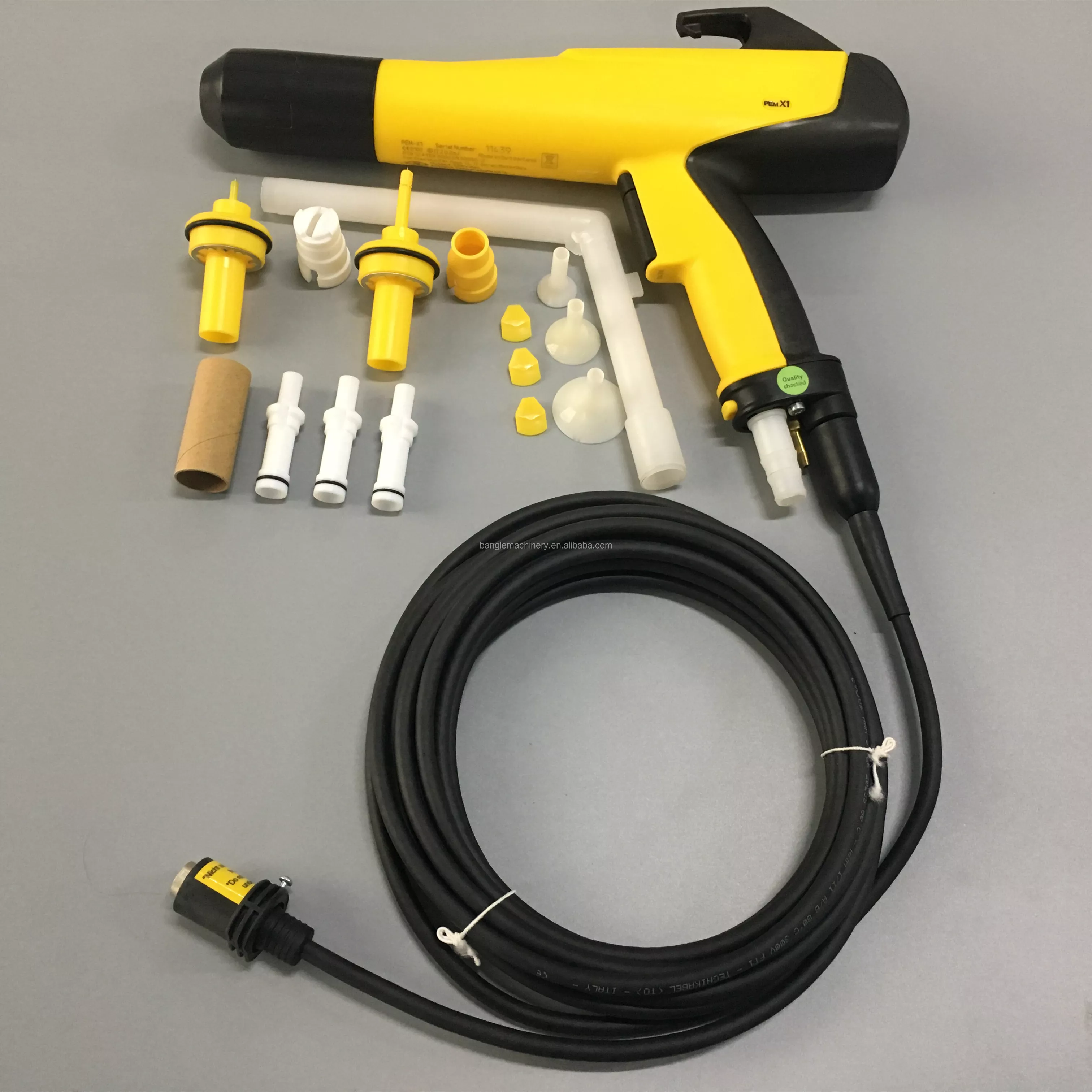
Lorsqu’il s’agit de l’entretien et de la maintenance des pistolets de pulvérisation pour le revêtement en poudre, il est essentiel de disposer d’un stock adéquat de pièces de rechange spécifiques pour éviter des interruptions de production et maintenir une application uniforme et de haute qualité. Voici une liste des principales pièces de rechange pour les pistolets de pulvérisation de poudre, avec une description de leur fonction et des raisons pour lesquelles elles sont importantes :
Pièces de Rechange Essentielles pour Pistolets de Pulvérisation
- Buses de Pulvérisation
- Fonction : Les buses contrôlent la taille et la forme du motif de pulvérisation de poudre, influençant directement la couverture et l’uniformité de l’application.
- Types : Disponibles en différentes formes et tailles, telles que rondes ou plates, pour diverses applications et finitions.
- Remplacement : Les buses s’usent avec le temps en raison de l’abrasion de la poudre, ce qui peut altérer le motif de pulvérisation. Un stock de buses de rechange garantit une qualité constante.
- Électrodes
- Fonction : Chargent électrostatiquement la poudre pour assurer une adhésion uniforme à la surface de l’objet à revêtir.
- Usure : Les électrodes peuvent se corroder ou s’user, ce qui réduit leur efficacité de charge et peut entraîner une mauvaise adhésion de la poudre.
- Remplacement Régulier : Disposer d’électrodes de rechange assure que le pistolet maintient une charge électrostatique optimale.
- Chambres de Charge
- Rôle : La chambre de charge est où la poudre est ionisée avant d’être pulvérisée. Elle joue un rôle clé dans le processus de charge électrostatique.
- Usure : L’accumulation de poudre peut affecter l’efficacité de la charge, nécessitant un nettoyage régulier et, parfois, le remplacement de la chambre.
- Joints et Joints Toriques
- Fonction : Assurent l’étanchéité des systèmes pneumatiques et empêchent les fuites d’air qui pourraient affecter la performance du pistolet.
- Importance : Les joints et joints toriques peuvent se détériorer avec le temps, provoquant des pertes de pression et une application inégale.
- Maintenance : Vérifiez régulièrement l’état des joints et remplacez-les pour éviter les dysfonctionnements.
- Housses de Pistolet et Capots
- Rôle : Protègent les composants internes du pistolet contre la poudre et la poussière.
- Remplacement : Les capots peuvent être endommagés ou usés avec le temps, nécessitant un remplacement pour maintenir le pistolet propre et fonctionnel.
- Flexibles de Poudre
- Fonction : Transportent la poudre du réservoir au pistolet de pulvérisation.
- Usure : Les flexibles peuvent se boucher ou s’user, affectant le flux de poudre.
- Entretien : Des flexibles de rechange sont essentiels pour garantir un flux continu et éviter les interruptions.
- Cartouches de Filtration
- Utilisation : Les cartouches filtrantes intégrées dans certains systèmes de pistolet purifient l’air comprimé utilisé pour la pulvérisation.
- Maintenance : Un remplacement régulier est nécessaire pour assurer la propreté de l’air comprimé et éviter la contamination de la poudre.
- Connecteurs et Raccords
- Rôle : Connectent les différentes parties du système de pulvérisation, y compris les flexibles et les réservoirs.
- Vérification : Les connecteurs et raccords doivent être contrôlés régulièrement pour s’assurer qu’ils ne sont pas desserrés ou usés, ce qui pourrait entraîner des fuites.
- Pompes et Régulateurs d’Air
- Fonction : Régulent la pression de l’air pour une pulvérisation efficace et contrôlée.
- Usure : Les pompes et régulateurs peuvent se détériorer, nécessitant des pièces de rechange pour maintenir la pression correcte.
- Disponibilité : Avoir des pompes et régulateurs de rechange est crucial pour éviter des variations de pression qui affectent la qualité de l’application.
- Unités de Contrôle
- Rôle : Les panneaux de contrôle électroniques et les unités de commande régulent le fonctionnement du pistolet, y compris le débit de poudre et la charge électrostatique.
- Maintenance : Des problèmes électriques peuvent survenir, nécessitant des pièces de rechange pour garantir un fonctionnement sans interruption.
Importance de la Gestion des Pièces de Rechange
- Réduction des Temps d’Arrêt : Avoir un stock de pièces de rechange critique permet de minimiser les interruptions de production en cas de panne ou de défaillance.
- Qualité de Production : L’utilisation de pièces usées ou endommagées peut affecter la qualité de la pulvérisation, entraînant des défauts dans le revêtement. Les pièces de rechange assurent que la qualité reste constante.
- Économies de Coût à Long Terme : En entretenant régulièrement les pistolets avec des pièces de rechange, vous réduisez les risques de dommages plus graves qui pourraient nécessiter des réparations coûteuses ou le remplacement complet de l’équipement.
- Amélioration de la Sécurité : Assurer le bon fonctionnement des composants critiques contribue à la sécurité globale de l’environnement de travail, en réduisant le risque de fuites, de surchauffe, ou d’autres dangers.
Conclusion
La disponibilité et la gestion proactive des pièces de rechange pour les pistolets de pulvérisation sont essentielles pour maintenir une production efficace et de haute qualité dans les opérations de revêtement en poudre. En investissant dans un programme de maintenance préventive et en gardant un stock adéquat de pièces critiques, vous pouvez prolonger la durée de vie de votre équipement et optimiser vos processus de production.
Si vous avez besoin de plus d’informations sur l’une de ces pièces ou d’une autre assistance, n’hésitez pas à me le faire savoir !
Fours à thermolaquage
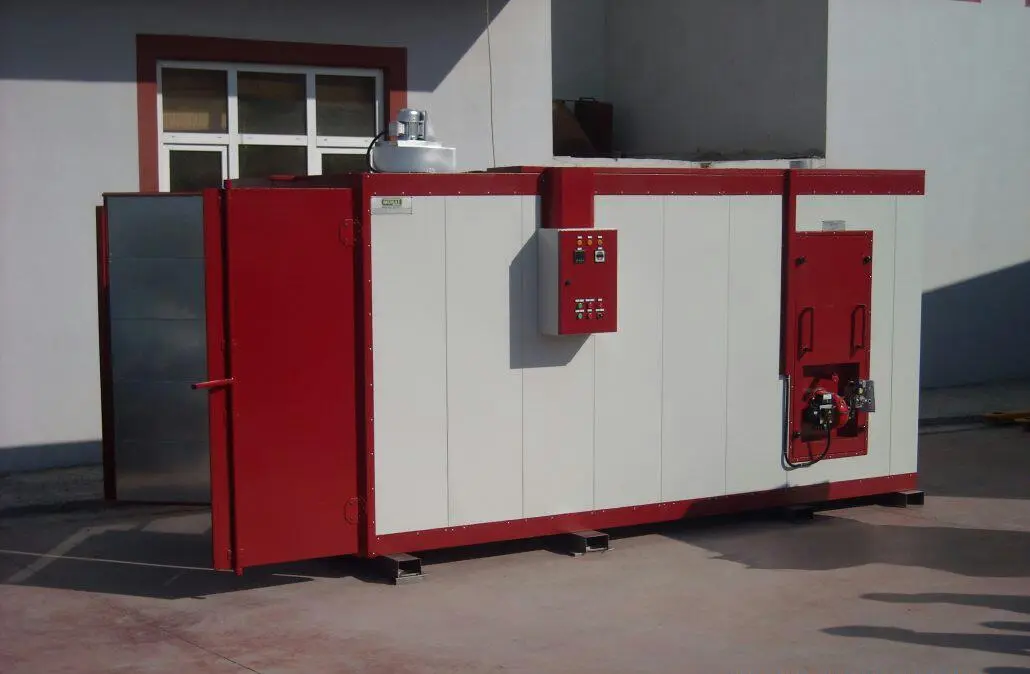
Les fours à thermolaquage, également appelés fours de polymérisation, jouent un rôle essentiel dans le processus de revêtement en poudre, en assurant une finition de qualité et durable. Ce procédé implique l’application de poudre thermodurcissable sur une surface qui est ensuite chauffée dans un four pour faire fondre et durcir la poudre, créant ainsi une couche uniforme et résistante. Voici un aperçu détaillé des fours à thermolaquage, de leur fonctionnement, des types disponibles, et des critères à considérer lors de leur sélection :
Fonctionnement des Fours à Thermolaquage
- Étapes du Processus de Thermolaquage
- Application de la Poudre : La poudre est appliquée sur la surface de l’objet à l’aide d’un pistolet de pulvérisation électrostatique. La charge électrostatique attire la poudre sur la surface, assurant une couverture uniforme.
- Polymérisation dans le Four : L’objet revêtu est ensuite placé dans un four à thermolaquage, où il est chauffé à une température spécifique pour fondre la poudre et la faire durcir.
- Durcissement : La chaleur permet aux particules de poudre de fusionner et de former une couche lisse et continue. Le processus de polymérisation dépend du type de poudre utilisée et des spécifications du fabricant.
- Caractéristiques des Fours à Thermolaquage
- Température : La plupart des poudres nécessitent des températures comprises entre 160°C et 230°C pour une polymérisation efficace.
- Durée : Le temps de polymérisation peut varier de 10 à 30 minutes, selon la taille de l’objet et le type de poudre.
- Uniformité de la Chaleur : Une distribution uniforme de la chaleur est cruciale pour éviter les défauts de surface, tels que des bulles ou des irrégularités.
Types de Fours à Thermolaquage
- Fours à Convection
- Principe : Utilisent l’air chaud pour chauffer les objets. Les ventilateurs répartissent la chaleur uniformément à l’intérieur du four.
- Avantages : Idéaux pour les objets volumineux et les lignes de production à grande échelle. Offrent une uniformité de chaleur efficace.
- Inconvénients : Peuvent être moins efficaces en termes de consommation d’énergie par rapport aux autres types de fours.
- Fours Infrarouges
- Principe : Utilisent des rayons infrarouges pour chauffer directement la surface de l’objet.
- Avantages : Réchauffement rapide, ce qui réduit le temps de polymérisation. Idéal pour les objets de formes complexes.
- Inconvénients : Moins efficace pour les objets très épais ou ceux avec des masses thermiques importantes.
- Fours à Induction
- Principe : Utilisent des champs électromagnétiques pour chauffer directement les objets métalliques.
- Avantages : Chauffage rapide et précis, idéal pour des applications spécifiques nécessitant un contrôle thermique précis.
- Inconvénients : Généralement plus coûteux et limités aux matériaux conducteurs.
- Fours Hybrides
- Principe : Combinent des technologies de chauffage à convection et infrarouge pour maximiser l’efficacité.
- Avantages : Permettent une flexibilité dans le traitement de différents types de pièces avec une consommation d’énergie optimisée.
- Inconvénients : Coût initial plus élevé dû à la complexité de la technologie intégrée.
Critères de Sélection d’un Four à Thermolaquage
- Capacité et Taille
- Dimensions du Four : Doivent correspondre à la taille des objets à traiter. Des fours plus grands sont nécessaires pour des pièces volumineuses ou des productions en série.
- Capacité de Charge : Évaluer la capacité de charge en termes de poids et de volume pour assurer que le four peut accueillir vos produits sans compromettre l’efficacité.
- Consommation Énergétique
- Efficacité Énergétique : Optez pour des modèles qui offrent une faible consommation d’énergie pour réduire les coûts d’exploitation.
- Isolation Thermique : Une bonne isolation aide à conserver la chaleur à l’intérieur du four, améliorant ainsi l’efficacité énergétique.
- Contrôle de Température
- Précision : La capacité à contrôler et maintenir précisément la température est essentielle pour la qualité de la finition.
- Systèmes de Contrôle Avancés : Recherchez des fours équipés de systèmes de contrôle numériques permettant un réglage précis et facile.
- Uniformité de la Chaleur
- Ventilation et Circulation d’Air : Assurez-vous que le four dispose de systèmes efficaces de circulation d’air pour garantir une distribution uniforme de la chaleur.
- Tests de Performance : Vérifiez les spécifications des tests de performance du fabricant pour l’uniformité thermique.
- Sécurité et Conformité
- Normes de Sécurité : Le four doit être conforme aux normes de sécurité locales et internationales, incluant des dispositifs de protection contre la surchauffe et des systèmes de verrouillage de sécurité.
- Émissions : Assurez-vous que le four respecte les réglementations concernant les émissions pour éviter les problèmes environnementaux.
Avantages des Fours à Thermolaquage
- Durabilité : Les finitions obtenues par thermolaquage sont extrêmement durables et résistantes aux éraflures, à la corrosion, et aux produits chimiques.
- Écologique : Ce procédé ne nécessite pas de solvants, ce qui réduit l’émission de composés organiques volatils (COV).
- Flexibilité de Design : Offre une large gamme de couleurs et de textures, ce qui permet une grande flexibilité en termes de design et de personnalisation.
Conclusion
Les fours à thermolaquage sont un élément crucial dans le processus de revêtement en poudre, assurant que la finition appliquée est à la fois esthétique et fonctionnelle. Le choix du bon type de four, combiné à une maintenance appropriée et à un contrôle rigoureux des paramètres de fonctionnement, peut considérablement améliorer la qualité de la production et réduire les coûts opérationnels.
Si vous avez besoin de plus de détails sur un aspect spécifique des fours à thermolaquage ou si vous souhaitez explorer d’autres éléments, n’hésitez pas à me le faire savoir !
Comparaison des Types de Fours à Thermolaquage
Lorsqu’il s’agit de choisir un four à thermolaquage pour le revêtement en poudre, il est crucial de comprendre les différences entre les différents types de fours disponibles. Chaque type de four a ses propres avantages et inconvénients, qui peuvent influencer la qualité de la finition, l’efficacité énergétique, le coût d’exploitation, et la flexibilité d’application. Voici une comparaison détaillée des principaux types de fours à thermolaquage :
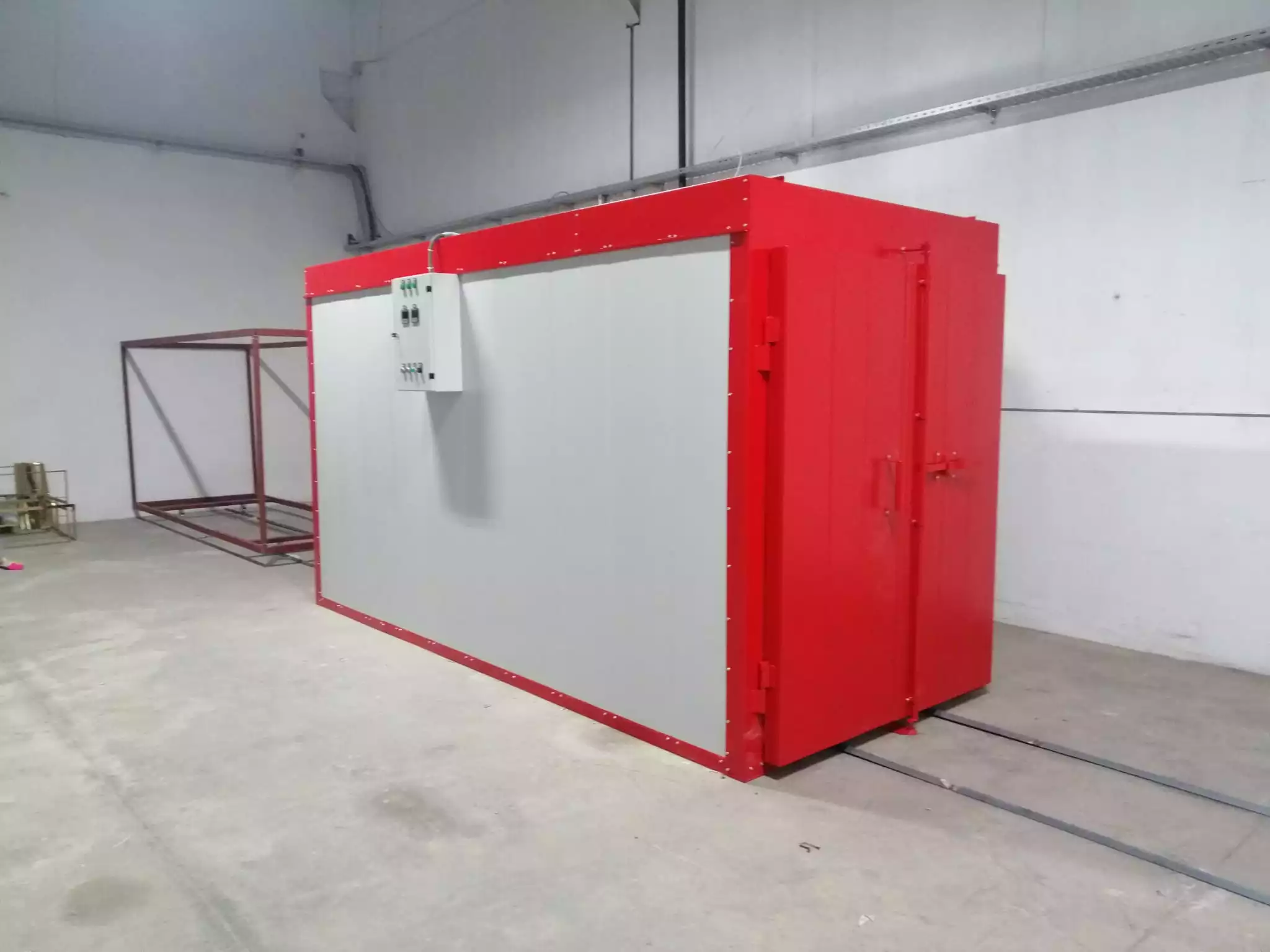
1. Fours à Convection
Principe de Fonctionnement :
Les fours à convection chauffent l’air à l’intérieur du four, qui est ensuite distribué uniformément autour des pièces à l’aide de ventilateurs. Ce type de four est l’un des plus couramment utilisés dans l’industrie du thermolaquage.
Avantages :
- Uniformité de la Chaleur : Grâce à la circulation d’air, les fours à convection offrent une distribution uniforme de la chaleur, réduisant les risques de défauts dans le revêtement.
- Adaptabilité : Convient à une large gamme de tailles et de formes de pièces, y compris les objets volumineux.
- Coût Initial : Généralement, ces fours ont un coût initial plus bas par rapport aux autres technologies de chauffage plus avancées.
Inconvénients :
- Consommation Énergétique : Peut être moins efficace en termes d’énergie par rapport aux fours infrarouges ou à induction, surtout pour les grandes charges.
- Temps de Chauffage : Le temps de montée en température peut être plus long, ce qui peut affecter la rapidité du cycle de production.
2. Fours Infrarouges
Principe de Fonctionnement :
Les fours infrarouges utilisent des rayons infrarouges pour chauffer directement la surface des pièces. Ce type de chauffage est basé sur le transfert de chaleur par rayonnement.
Avantages :
- Rapidité de Chauffage : Les fours infrarouges chauffent rapidement les surfaces, ce qui réduit considérablement le temps de cycle.
- Efficacité Énergétique : Consomment généralement moins d’énergie puisqu’ils chauffent directement la pièce sans chauffer tout le volume d’air autour.
- Finitions Complexes : Idéal pour les pièces avec des formes complexes et des géométries difficiles, où un chauffage direct est avantageux.
Inconvénients :
- Uniformité de la Chaleur : Peut avoir des difficultés à chauffer uniformément des pièces très épaisses ou denses, car la chaleur ne pénètre pas aussi profondément.
- Coût Initial : Le coût d’installation peut être plus élevé, surtout si une personnalisation spécifique est requise pour l’application.
3. Fours à Induction
Principe de Fonctionnement :
Les fours à induction utilisent des champs électromagnétiques pour chauffer les objets métalliques directement. Ce type de chauffage est extrêmement rapide et précis.
Avantages :
- Précision : Offre un contrôle précis de la température, idéal pour des applications nécessitant une gestion thermique rigoureuse.
- Rapidité : Très rapide à chauffer, ce qui réduit les temps de cycle de production.
- Efficacité Énergétique : Chauffe directement le matériau conducteur, ce qui réduit les pertes énergétiques.
Inconvénients :
- Limitation des Matériaux : Ne peut être utilisé que sur des matériaux conducteurs, ce qui limite son utilisation aux métaux.
- Coût Élevé : Le coût initial est généralement plus élevé que les autres types de fours, et le coût de l’équipement peut être prohibitif pour certaines petites et moyennes entreprises.
4. Fours Hybrides
Principe de Fonctionnement :
Les fours hybrides combinent la technologie de convection et infrarouge pour offrir une flexibilité et une efficacité accrues.
Avantages :
- Flexibilité : Peut traiter une variété de pièces et de matériaux, maximisant ainsi la polyvalence des applications.
- Efficacité Améliorée : Combine les avantages des deux systèmes de chauffage pour une efficacité énergétique et de traitement améliorée.
- Optimisation de la Qualité : Peut offrir une meilleure qualité de finition en ajustant les méthodes de chauffage selon les besoins.
Inconvénients :
- Coût Initial : L’investissement initial peut être élevé en raison de la complexité accrue du système.
- Maintenance : Peut nécessiter un entretien plus régulier et complexe en raison de la présence de deux systèmes de chauffage différents.
Tableau Comparatif
Voici un tableau qui résume les principales caractéristiques de chaque type de four à thermolaquage :
Type de Four | Avantages | Inconvénients | Applications Idéales |
---|---|---|---|
Convection | – Uniformité de chaleur<br>- Adaptabilité<br>- Coût initial bas | – Consommation énergétique<br>- Temps de chauffage long | Objets volumineux, production en série |
Infrarouge | – Chauffage rapide<br>- Efficacité énergétique<br>- Finitions complexes | – Uniformité pour pièces épaisses<br>- Coût initial | Pièces complexes, temps de cycle rapide |
Induction | – Précision thermique<br>- Rapidité<br>- Efficacité énergétique | – Limité aux matériaux conducteurs<br>- Coût élevé | Applications précises, matériaux conducteurs |
Hybride | – Flexibilité<br>- Efficacité améliorée<br>- Qualité optimisée | – Coût initial élevé<br>- Maintenance complexe | Diversité de matériaux et de formes |
Conclusion
Le choix du type de four à thermolaquage dépend de plusieurs facteurs, notamment la nature des pièces à traiter, les exigences de production, le budget disponible, et l’efficacité énergétique souhaitée.
- Fours à Convection : Recommandés pour les opérations à grande échelle nécessitant une uniformité de chaleur sur des pièces volumineuses.
- Fours Infrarouges : Idéaux pour des cycles de production rapides et des pièces de formes complexes.
- Fours à Induction : Conviennent aux applications nécessitant un contrôle thermique précis, mais limités aux métaux.
- Fours Hybrides : Offrent une polyvalence maximale pour traiter divers matériaux et formes.
En évaluant soigneusement vos besoins spécifiques et en tenant compte des avantages et des inconvénients de chaque type de four, vous pouvez faire un choix éclairé qui optimisera vos opérations de revêtement en poudre. Si vous avez besoin de plus d’informations ou de conseils supplémentaires, n’hésitez pas à demander !
Exemples d’applications
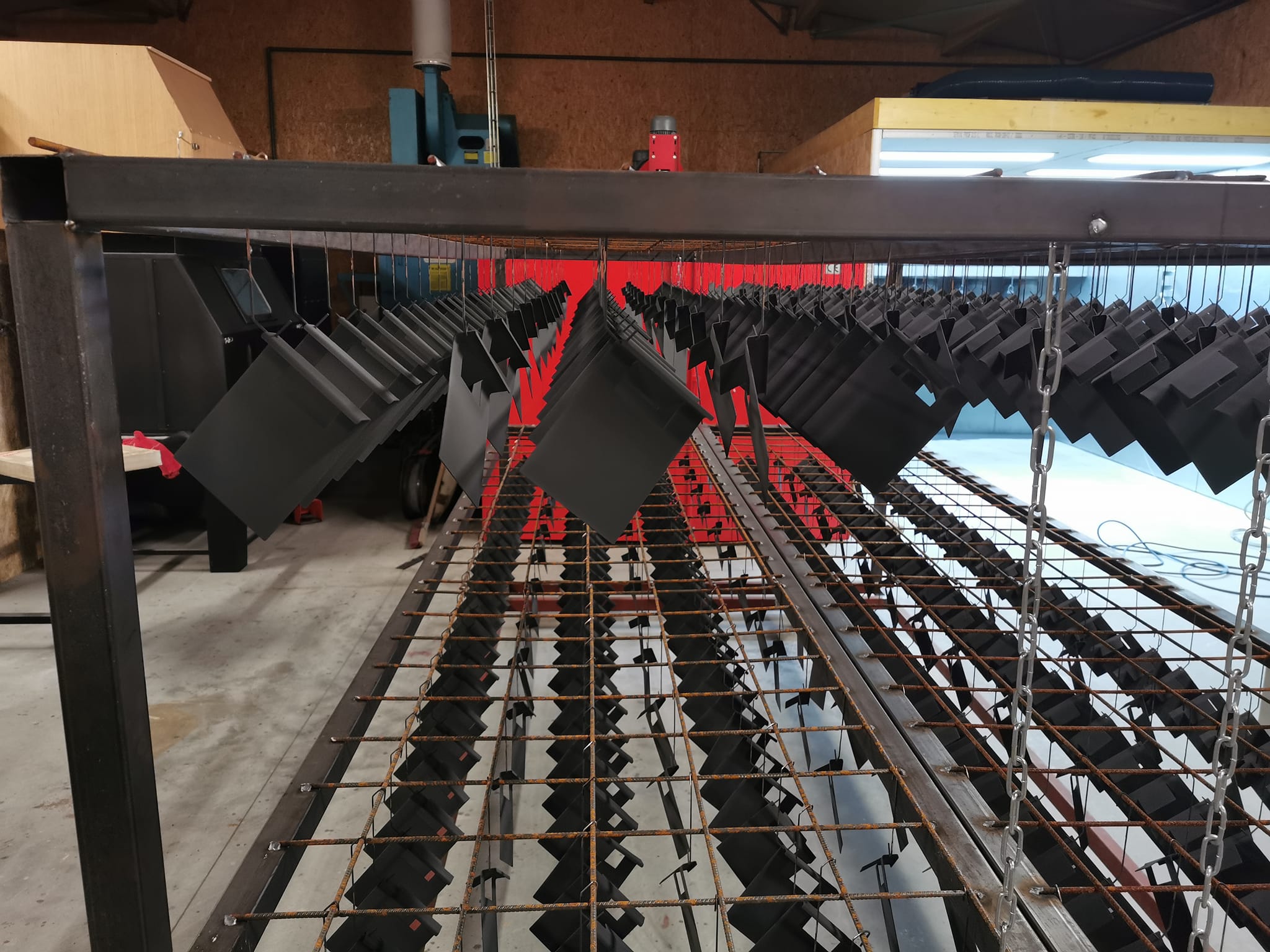
Les fours à thermolaquage sont utilisés dans une variété d’industries en raison de leurs capacités à fournir des finitions durables, esthétiques, et résistantes. Voici quelques exemples d’applications industrielles et commerciales où les fours à thermolaquage sont couramment utilisés :
Exemples d’Applications des Fours à Thermolaquage
1. Industrie Automobile
- Composants Peints : Les pièces automobiles comme les jantes, les châssis, et les éléments de suspension sont souvent thermolaqués pour améliorer leur résistance à la corrosion et leur apparence esthétique.
- Accessoires et Pièces : Les rétroviseurs, poignées de porte, et autres accessoires sont également revêtus pour offrir une protection supplémentaire contre les rayures et les intempéries.
2. Équipements Électroménagers
- Appareils de Cuisine : Les fours, réfrigérateurs, et autres appareils ménagers utilisent le thermolaquage pour protéger les surfaces métalliques contre l’usure et offrir des finitions brillantes et colorées.
- Machines à Laver et Sèche-linge : Les panneaux extérieurs de ces appareils bénéficient du revêtement en poudre pour leur résistance accrue à l’humidité et aux produits chimiques ménagers.
3. Mobilier Métallique
- Meubles de Bureau : Les cadres de chaises, bureaux, et autres meubles de bureau en métal utilisent le thermolaquage pour améliorer la durabilité et offrir une finition élégante.
- Mobilier d’Extérieur : Les meubles d’extérieur, tels que les chaises de jardin et les tables, sont thermolaqués pour résister aux intempéries et aux rayons UV, ce qui prévient la décoloration et la corrosion.
4. Industrie Électronique
- Boîtiers d’Équipements : Les boîtiers pour ordinateurs, téléviseurs, et autres appareils électroniques bénéficient du thermolaquage pour protéger les composants internes de la poussière et de l’humidité.
- Composants Intérieurs : Les dissipateurs de chaleur et autres pièces métalliques internes sont également revêtus pour améliorer leur longévité et leur performance thermique.
5. Équipements de Construction
- Machines de Chantier : Les pièces de machines telles que les grues, bulldozers, et excavateurs sont souvent thermolaquées pour résister aux environnements difficiles et prolonger leur durée de vie.
- Outils et Équipements : Les outils manuels et électriques, ainsi que les équipements de sécurité, utilisent le thermolaquage pour offrir une résistance accrue à l’usure et une meilleure apparence.
6. Industrie du Transport
- Vélos et Motocyclettes : Les cadres de vélos et de motos sont thermolaqués pour améliorer la résistance à la rouille et offrir une finition durable.
- Trains et Wagons : Les composants métalliques des trains, comme les bogies et les structures de carrosserie, sont revêtus pour protéger contre la corrosion et améliorer l’apparence.
7. Infrastructure et Urbanisme
- Poteaux de Signalisation et Barrières de Sécurité : Utilisent le thermolaquage pour garantir une longue durée de vie et une visibilité accrue grâce à des couleurs vives et durables.
- Équipements de Jeux et Parcs : Les structures de jeux pour enfants et les équipements de parcs sont revêtus pour assurer sécurité et durabilité contre les éléments extérieurs.
8. Industrie de l’Aéronautique
- Composants Intérieurs et Extérieurs : Les avions utilisent le thermolaquage pour les composants intérieurs, comme les panneaux et les sièges, ainsi que pour les pièces extérieures, comme les capots et les structures de fuselage.
- Finitions Anti-Corrosion : Le revêtement en poudre est utilisé pour protéger les pièces critiques contre la corrosion due à l’exposition aux éléments.
Avantages du Thermolaquage pour ces Applications
- Résistance aux Intempéries et à la Corrosion : Le revêtement en poudre offre une protection exceptionnelle contre la rouille, la corrosion, et les éléments extérieurs, prolongeant ainsi la durée de vie des pièces revêtues.
- Durabilité et Résistance : Les finitions obtenues par thermolaquage sont extrêmement durables et résistantes aux éraflures, aux chocs, et aux produits chimiques.
- Flexibilité Esthétique : Une large gamme de couleurs et de finitions est disponible, permettant aux designers de personnaliser l’apparence des produits selon les besoins spécifiques.
- Écologique : Le processus de thermolaquage est respectueux de l’environnement car il ne nécessite pas de solvants et réduit les émissions de composés organiques volatils (COV).
Conclusion
Les fours à thermolaquage jouent un rôle clé dans diverses industries, fournissant des solutions de revêtement efficaces et durables pour une multitude d’applications. En sélectionnant le bon type de four et en optimisant les paramètres de processus, les entreprises peuvent garantir des résultats de haute qualité et économiquement viables.
Si vous avez besoin de plus d’informations sur une application spécifique ou souhaitez discuter d’autres aspects du thermolaquage, n’hésitez pas à me le faire savoir !
Coût des fours
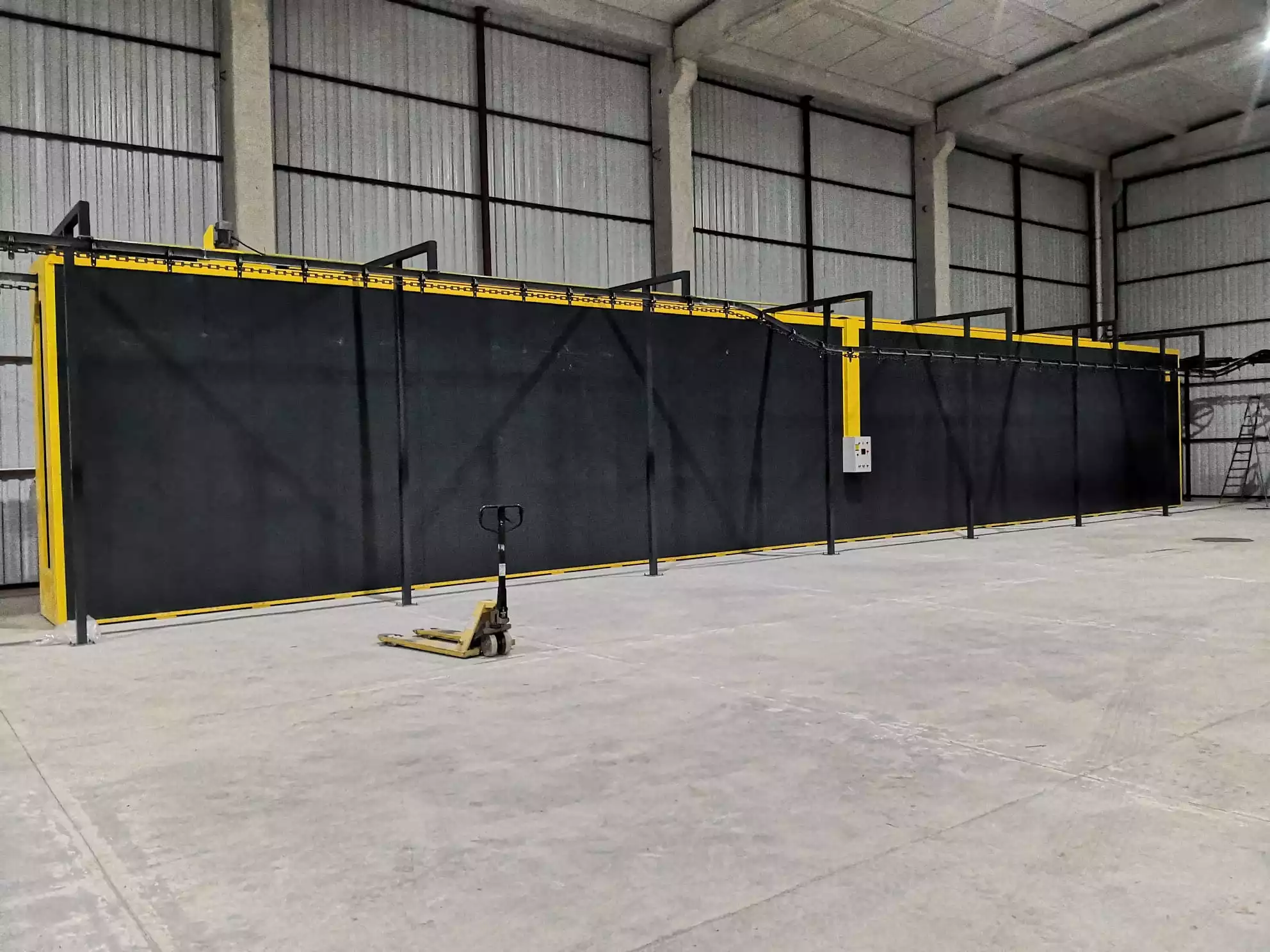
Le coût des fours à thermolaquage peut varier considérablement en fonction de plusieurs facteurs, notamment la taille, la capacité, le type de technologie utilisée, et les caractéristiques spécifiques du four. Voici une analyse détaillée des coûts associés aux différents types de fours à thermolaquage, ainsi que des facteurs qui influencent ces coûts.
Facteurs Influant sur le Coût des Fours à Thermolaquage
- Taille et Capacité
- Petits Fours de Laboratoire : Les petits fours utilisés pour des tests et des productions en faible volume sont généralement moins coûteux, avec des prix pouvant commencer autour de 5 000 à 15 000 euros.
- Fours de Production Moyenne : Ces fours, utilisés pour des productions à échelle moyenne, coûtent généralement entre 20 000 et 50 000 euros.
- Grands Fours Industriels : Les grands fours utilisés pour des productions industrielles de masse peuvent coûter entre 50 000 et 200 000 euros, voire plus selon la capacité et les spécifications.
- Type de Technologie
- Fours à Convection : Ces fours sont souvent moins chers en termes de coût initial, avec des prix pouvant varier de 10 000 à 100 000 euros, selon la taille et les caractéristiques.
- Fours Infrarouges : En raison de leur technologie de chauffage rapide et ciblé, les fours infrarouges peuvent être plus coûteux, généralement entre 15 000 et 150 000 euros.
- Fours à Induction : Les fours à induction, qui nécessitent des composants spécifiques pour chauffer les matériaux conducteurs, peuvent coûter entre 20 000 et 200 000 euros.
- Fours Hybrides : En combinant plusieurs technologies, les fours hybrides peuvent être les plus chers, avec des prix allant de 30 000 à 250 000 euros, en fonction des caractéristiques intégrées.
- Caractéristiques Spécifiques
- Contrôles Avancés : Les systèmes de contrôle numérique et les automatisations intégrées augmentent généralement le coût des fours, ajoutant entre 5 000 et 20 000 euros au prix de base.
- Isolation et Efficacité Énergétique : Les fours dotés d’une isolation thermique avancée pour améliorer l’efficacité énergétique peuvent avoir un coût initial plus élevé.
- Options Personnalisées : Les personnalisations spécifiques pour répondre à des besoins uniques d’application peuvent ajouter des coûts supplémentaires.
- Marque et Fabricant
- Réputation de la Marque : Les fours fabriqués par des entreprises réputées et établies dans l’industrie peuvent coûter plus cher en raison de leur fiabilité et de leur qualité éprouvée.
- Service et Support : Les fournisseurs offrant des services après-vente étendus et un support technique peuvent justifier des prix plus élevés.
- Installation et Maintenance
- Coûts d’Installation : L’installation professionnelle d’un four, surtout pour les grandes installations industrielles, peut ajouter de 2 000 à 10 000 euros au coût total.
- Entretien et Réparations : Les coûts d’entretien continu, y compris le remplacement des pièces et les réparations, doivent être pris en compte dans le calcul des coûts à long terme.
Coût Global de Possession
En plus du coût initial du four, il est important de considérer le coût global de possession, qui inclut :
- Consommation Énergétique : Les fours plus efficaces peuvent réduire les coûts opérationnels à long terme en consommant moins d’énergie.
- Durabilité et Longévité : Investir dans un four de haute qualité peut offrir des économies à long terme grâce à une durée de vie prolongée et à une fiabilité accrue.
- Retour sur Investissement (ROI) : Calculer le retour sur investissement en fonction de l’augmentation de la productivité, de l’amélioration de la qualité des produits, et de la réduction des déchets.
Estimation des Coûts par Type de Four
Type de Four | Coût Estimé | Applications |
---|---|---|
Convection | 10 000 à 100 000 euros | Production à grande échelle |
Infrarouge | 15 000 à 150 000 euros | Cycles rapides, formes complexes |
Induction | 20 000 à 200 000 euros | Applications précises, métaux |
Hybride | 30 000 à 250 000 euros | Flexibilité maximale |
Conseils pour Optimiser l’Achat
- Évaluation des Besoins Spécifiques
- Analysez vos besoins spécifiques en matière de production pour choisir le type de four le plus adapté à votre activité.
- Considérez la capacité requise, le type de pièces à traiter, et les exigences de qualité.
- Comparaison des Fournisseurs
- Demandez des devis à plusieurs fournisseurs pour comparer les options disponibles.
- Évaluez les offres en fonction des coûts initiaux et des coûts d’exploitation à long terme.
- Considérations Financières
- Recherchez des options de financement ou des subventions industrielles qui pourraient alléger le coût initial d’achat.
- Prenez en compte les incitations fiscales pour l’achat d’équipements éco-énergétiques.
- Préparation pour l’Entretien
- Assurez-vous d’avoir un plan de maintenance préventive en place pour minimiser les coûts de réparation imprévus.
- Investissez dans la formation du personnel pour garantir une utilisation optimale et sûre de l’équipement.
Conclusion
Le choix et l’achat d’un four à thermolaquage impliquent une analyse approfondie des coûts, des besoins spécifiques, et des caractéristiques des différentes technologies disponibles. En considérant à la fois le coût initial et les coûts à long terme, vous pouvez faire un choix éclairé qui améliorera la qualité de votre production et maximisera le retour sur investissement. Si vous avez besoin de conseils supplémentaires ou d’une assistance pour un cas spécifique, n’hésitez pas à me le faire savoir !
Temps installation four
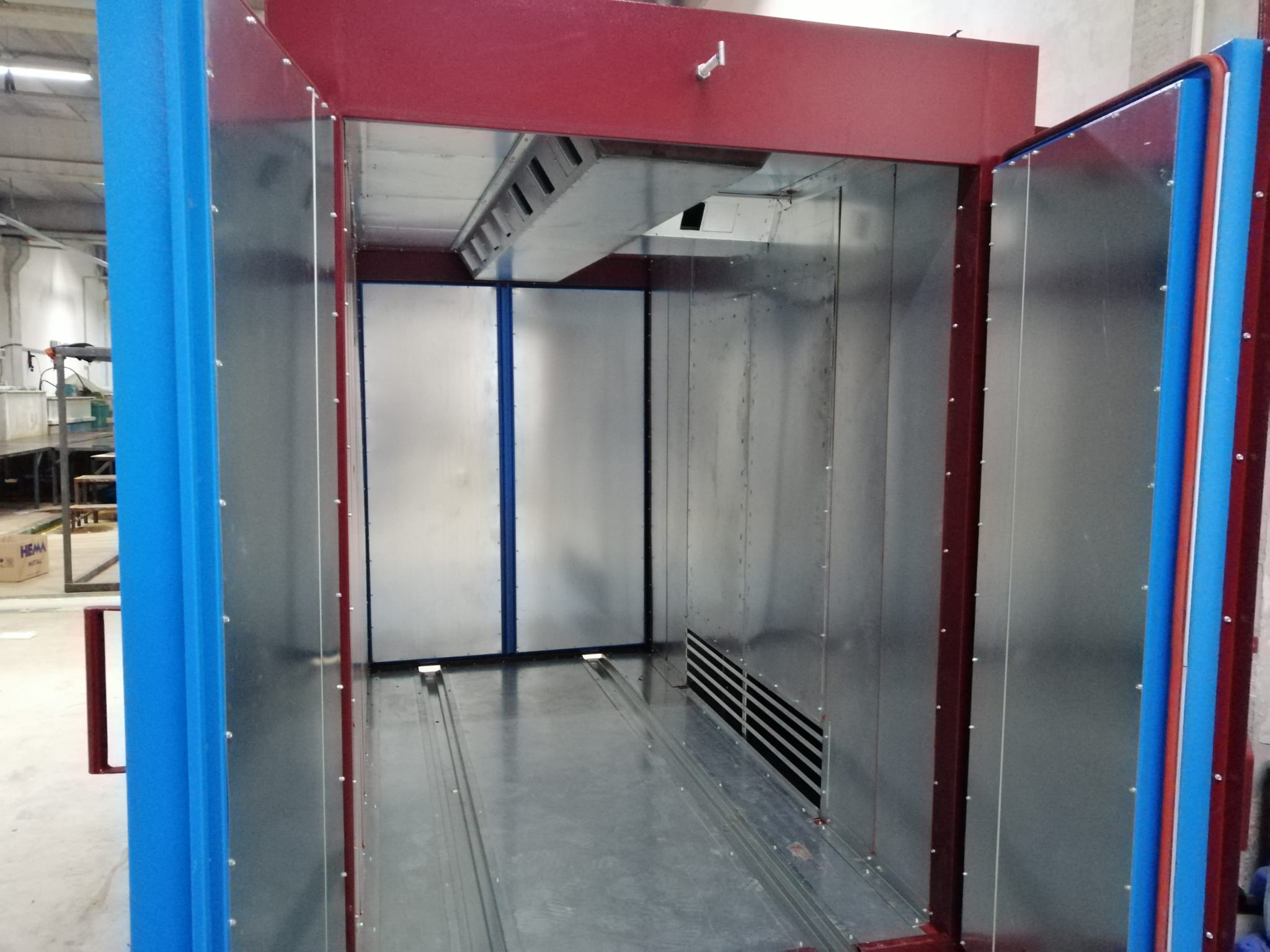
L’installation d’un four à thermolaquage est un processus qui nécessite une planification minutieuse et une coordination efficace. Le temps requis pour installer un four peut varier considérablement en fonction de plusieurs facteurs, notamment la taille du four, la complexité du système, et les conditions spécifiques du site d’installation. Voici une analyse détaillée des différents aspects qui influencent le temps d’installation d’un four à thermolaquage :
Facteurs Influant sur le Temps d’Installation
- Taille et Complexité du Four
- Petits Fours de Laboratoire : Les petits fours, souvent utilisés pour des tests ou de petites productions, peuvent être installés en quelques jours. La simplicité de ces unités signifie qu’elles nécessitent moins de travail pour l’installation.
- Fours de Production Moyenne : Les fours de taille moyenne, utilisés pour des productions à échelle moyenne, peuvent prendre de 1 à 2 semaines pour être installés, en fonction de leur configuration et des besoins de connexion.
- Grands Fours Industriels : Les installations industrielles de grande envergure, qui incluent des systèmes complexes, peuvent nécessiter entre 2 et 4 semaines pour une installation complète. Cela inclut souvent la construction de structures de support et l’intégration dans des lignes de production existantes.
- Type de Technologie
- Fours à Convection : Ces fours, avec des systèmes de ventilation et de circulation d’air, peuvent être relativement simples à installer, mais le temps peut augmenter avec la taille et les spécificités de l’installation.
- Fours Infrarouges : L’installation de systèmes infrarouges peut être plus rapide que d’autres technologies, mais nécessite une attention particulière à l’alignement des émetteurs infrarouges pour garantir une distribution homogène de la chaleur. L’installation typique peut prendre environ 1 à 2 semaines.
- Fours à Induction : Ces fours nécessitent une installation spécialisée en raison des systèmes électromagnétiques complexes. L’installation peut prendre de 2 à 3 semaines, en particulier si des modifications structurelles sont nécessaires.
- Fours Hybrides : Les fours qui combinent plusieurs technologies de chauffage peuvent nécessiter un temps d’installation plus long, souvent de 3 à 4 semaines, en raison de la complexité accrue de l’équipement et de l’intégration requise.
- Préparation du Site
- Infrastructure Électrique : La préparation et la mise à jour des installations électriques pour accueillir un four à thermolaquage peuvent prendre plusieurs jours à quelques semaines, selon la nécessité de nouvelles connexions ou de mises à niveau.
- Systèmes de Ventilation : La mise en place ou la modification des systèmes de ventilation existants pour répondre aux normes de sécurité peut prolonger le temps d’installation. Cela est particulièrement crucial pour les grands fours industriels.
- Fondations et Structures de Support : Pour les grands fours, il peut être nécessaire de construire des structures de support ou de renforcer le sol, ce qui ajoute au temps total d’installation.
- Personnel et Logistique
- Disponibilité de l’Équipe : La disponibilité d’une équipe qualifiée pour réaliser l’installation joue un rôle clé dans le temps nécessaire. Un personnel expérimenté peut accélérer le processus.
- Logistique de Transport : La livraison des composants du four au site d’installation peut également affecter le calendrier global, surtout si des éléments personnalisés ou de grande taille doivent être transportés.
- Tests et Mise en Service
- Tests de Fonctionnalité : Une fois le four installé, il est crucial de réaliser des tests de fonctionnalité pour s’assurer que toutes les parties de l’équipement fonctionnent correctement et en toute sécurité. Cela peut prendre 2 à 5 jours supplémentaires.
- Formation du Personnel : La formation des opérateurs et du personnel de maintenance peut ajouter quelques jours au processus global d’installation. Cela garantit que le personnel est capable d’opérer le four efficacement et en toute sécurité.
Estimation Générale du Temps d’Installation
Type de Four | Temps d’Installation Estimé |
---|---|
Petits Fours de Laboratoire | 1 à 3 jours |
Fours de Production Moyenne | 1 à 2 semaines |
Grands Fours Industriels | 2 à 4 semaines |
Fours à Convection | 1 à 3 semaines |
Fours Infrarouges | 1 à 2 semaines |
Fours à Induction | 2 à 3 semaines |
Fours Hybrides | 3 à 4 semaines |
Conseils pour Optimiser l’Installation
- Planification Précoce
- Évaluation du Site : Effectuez une évaluation précoce du site pour identifier les besoins en infrastructure et anticiper les défis potentiels.
- Coordination Logistique : Coordonnez à l’avance la livraison des composants et la disponibilité du personnel d’installation pour éviter les retards.
- Engagement de Professionnels
- Entreprises Spécialisées : Collaborez avec des entreprises spécialisées dans l’installation de fours industriels pour assurer une installation efficace et conforme aux normes.
- Support Technique : Assurez-vous d’avoir un support technique disponible pour résoudre rapidement les problèmes qui pourraient survenir pendant l’installation.
- Intégration avec les Systèmes Existants
- Systèmes de Production : Intégrez le four dans les systèmes de production existants pour minimiser les interruptions et maximiser l’efficacité.
- Mise en Réseau : Assurez-vous que le four est compatible avec les systèmes de contrôle et de gestion de la production pour un fonctionnement optimal.
- Préparation pour les Tests
- Élaboration de Procédures de Test : Établissez des procédures de test claires pour vérifier le bon fonctionnement du four après l’installation.
- Formation et Sécurité : Formez le personnel aux pratiques de sécurité et à l’utilisation de l’équipement avant la mise en service.
Une ligne de peinture poudre automatique est un système de traitement de surface utilisé principalement pour appliquer une finition de peinture en poudre sur des produits métalliques ou autres matériaux. Contrairement à la peinture liquide traditionnelle, la peinture en poudre est constituée de pigments et de résines qui sont projetés sur la surface d’un objet sous forme de poudre sèche. Cette technique est utilisée pour offrir une finition durable, résistante aux rayures, aux intempéries et aux produits chimiques.
Le processus commence par le nettoyage des pièces à peindre. Celles-ci passent par une série de stations de lavage, qui peuvent inclure le dégraissage, la déphosphatation et le rinçage. Cela permet d’assurer une surface propre et prête à recevoir la peinture en poudre. Ensuite, les pièces sont séchées avant d’être transportées vers la cabine de pulvérisation, où la peinture en poudre est projetée à l’aide de pistolets électrostatiques. Ces pistolets chargent électriquement la poudre, ce qui permet à cette dernière d’adhérer à la surface des pièces. Cette étape est cruciale pour garantir une application uniforme de la peinture.
Une fois que la poudre est appliquée, les pièces sont envoyées à un four de cuisson. La chaleur fait fondre la poudre, qui se transforme en une couche solide et lisse. La température et le temps de cuisson doivent être soigneusement contrôlés pour obtenir la bonne épaisseur de la couche et pour que la finition soit durable. Le processus est généralement rapide, avec des temps de cuisson allant de 10 à 30 minutes, selon le type de peinture et la taille des pièces.
L’un des principaux avantages de la peinture en poudre est qu’elle ne nécessite pas de solvant, ce qui la rend plus respectueuse de l’environnement que les peintures liquides. De plus, le processus est plus efficace car la poudre non utilisée peut souvent être récupérée et réutilisée. Ce type de ligne de peinture est particulièrement adapté pour des applications industrielles de masse, comme celles utilisées pour peindre des composants automobiles, des meubles métalliques, des appareils électroménagers, et d’autres produits nécessitant une finition robuste et esthétiquement agréable.
L’automatisation de ces lignes de peinture permet de réduire les erreurs humaines, d’assurer une plus grande uniformité de la finition et d’augmenter la productivité. Les systèmes automatisés sont souvent équipés de technologies avancées telles que des robots pour la manipulation des pièces, des systèmes de contrôle de la qualité pour surveiller l’épaisseur de la peinture et des outils de gestion des couleurs pour garantir une reproduction fidèle des teintes.
En outre, les lignes de peinture poudre automatiques peuvent être adaptées à des besoins spécifiques. Par exemple, elles peuvent être conçues pour traiter des pièces de formes complexes ou pour fonctionner à des vitesses de production élevées. Des systèmes de gestion de la circulation de l’air et de filtration de la poussière sont également installés pour maintenir une qualité d’air optimale dans les ateliers et éviter la contamination de la peinture.
Ce type de ligne de peinture est essentiel dans de nombreux secteurs industriels où l’apparence et la durabilité des produits sont primordiales. Les innovations récentes, telles que l’intégration de technologies de contrôle numérique et de l’Internet des objets (IoT), rendent ces systèmes encore plus intelligents et adaptatifs, permettant un meilleur suivi des performances et une optimisation des processus de production.
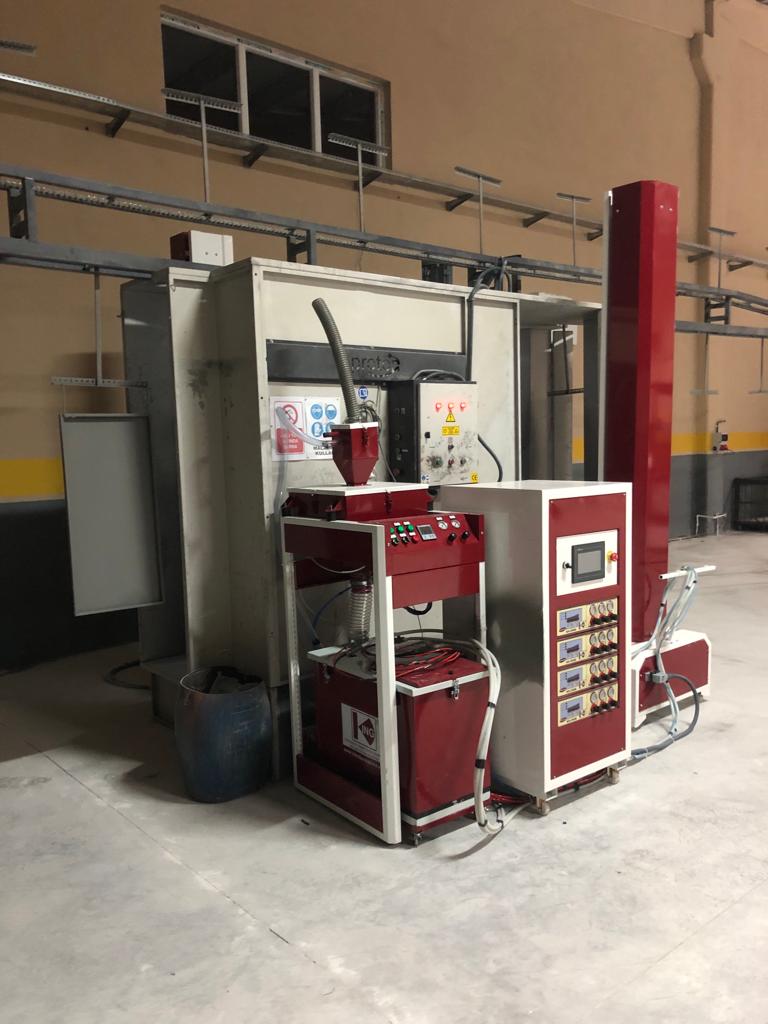
En plus des avantages environnementaux et de productivité, les lignes de peinture poudre automatiques offrent également des bénéfices en termes de flexibilité et de personnalisation des produits finis. Grâce aux avancées technologiques, il est possible de régler précisément les paramètres de l’application, comme la quantité de poudre, la pression d’air, et la vitesse de pulvérisation. Cela permet d’obtenir des finitions variées, adaptées aux exigences spécifiques des clients. Que ce soit pour une finition mate, brillante, ou satinée, ou pour une couleur personnalisée, ces lignes peuvent répondre à une large gamme de besoins industriels et esthétiques.
Les technologies modernes utilisées dans ces lignes incluent souvent des systèmes de récupération de poudre qui optimisent l’utilisation des matériaux et minimisent les déchets. Une partie de la poudre non utilisée est collectée et réintégrée dans le processus, ce qui permet de réduire le coût des matières premières tout en respectant l’environnement. Cette récupération de la poudre est facilitée par des filtres et des systèmes de ventilation sophistiqués qui maintiennent un environnement de travail propre et sécurisé, en évitant l’accumulation de poussières potentiellement dangereuses.
Une autre caractéristique importante des lignes de peinture poudre automatiques est leur capacité à traiter des pièces de tailles et de formes variées. Certaines lignes sont équipées de convoyeurs à chaîne ou de systèmes robotisés qui permettent de déplacer les pièces de manière fluide à travers les différentes étapes du processus, garantissant ainsi un traitement efficace. Les robots peuvent être programmés pour effectuer des mouvements complexes, assurant une application de peinture homogène même sur des objets de géométrie irrégulière.
Les lignes de peinture poudre automatiques sont aussi de plus en plus intégrées dans des systèmes de production de plus grande envergure, dans le cadre de lignes de production entièrement automatisées. Ces systèmes sont conçus pour fonctionner en coordination avec d’autres machines, telles que les presses, les machines d’assemblage, et les tests de qualité, créant ainsi un flux de travail ininterrompu. Cela permet non seulement d’augmenter la vitesse de production mais aussi de réduire les coûts de main-d’œuvre tout en maintenant un niveau de qualité élevé.
En termes de maintenance, bien que ces lignes automatisées nécessitent un investissement initial plus important, elles sont généralement conçues pour être robustes et nécessitent moins d’entretien que les systèmes manuels ou semi-automatiques. Les composants sont souvent équipés de capteurs et de systèmes d’alerte précoce qui signalent toute anomalie avant qu’elle ne devienne un problème majeur, ce qui permet de réduire les arrêts imprévus et d’optimiser les coûts d’exploitation.
Cependant, l’implantation d’une ligne de peinture poudre automatique ne se fait pas sans défis. Il est essentiel de former le personnel à l’utilisation des équipements et aux spécificités de chaque étape du processus. Une mauvaise gestion des paramètres de pulvérisation ou une application incorrecte de la peinture peut entraîner des défauts esthétiques ou une mauvaise adhésion de la peinture, ce qui pourrait compromettre la qualité du produit final. C’est pourquoi un suivi rigoureux et un contrôle de qualité constant sont nécessaires tout au long du processus de production.
À mesure que la technologie continue d’évoluer, l’avenir des lignes de peinture poudre automatiques semble prometteur. Des innovations telles que l’intégration de la réalité augmentée pour le contrôle de qualité, l’utilisation de systèmes de vision par caméra pour l’inspection des surfaces, et l’amélioration continue des matériaux de peinture en poudre permettront d’augmenter encore l’efficacité et la durabilité de ces systèmes. En outre, avec la demande croissante de produits respectueux de l’environnement et l’optimisation des coûts, l’utilisation de la peinture poudre devrait continuer à se développer dans de nouveaux secteurs, offrant des solutions plus écologiques et plus rentables pour l’industrie.
Ainsi, une ligne de peinture poudre automatique devient un atout stratégique pour les entreprises cherchant à allier haute qualité, efficacité, et respect de l’environnement, tout en répondant à une production de masse avec des exigences strictes de finition
L’optimisation de l’efficacité énergétique est également un domaine clé où les lignes de peinture poudre automatiques connaissent des avancées significatives. Les systèmes modernes sont conçus pour minimiser la consommation d’énergie tout en maximisant la performance. Par exemple, les fours de cuisson sont désormais équipés de technologies plus avancées, comme des récupérateurs de chaleur, qui permettent de réutiliser l’énergie dégagée lors du processus de cuisson pour préchauffer l’air ou les pièces avant leur entrée dans le four. Cela réduit la consommation d’énergie et permet de réaliser des économies sur les coûts opérationnels.
De plus, les nouvelles générations de lignes de peinture poudre sont de plus en plus modulaires et évolutives. Cela signifie que les entreprises peuvent adapter leurs installations en fonction des besoins changeants du marché ou de la production. Par exemple, il est possible d’ajouter de nouvelles stations de pulvérisation, de changer les robots pour des modèles plus performants, ou même d’intégrer des fonctionnalités comme la peinture en poudre à base de matériaux recyclés, sans nécessiter de réaménagement complet de la ligne. Cette flexibilité est un avantage majeur dans un environnement industriel en constante évolution.
Les lignes de peinture poudre automatiques jouent également un rôle essentiel dans la réduction de l’empreinte carbone des processus de fabrication. En éliminant la nécessité de solvants et en produisant moins de déchets, elles contribuent à une production plus propre et plus durable. De plus, la possibilité de choisir des peintures à faible émission de composés organiques volatils (COV) renforce encore l’engagement en faveur de l’environnement. Cela devient de plus en plus important à mesure que les réglementations environnementales se renforcent dans de nombreux pays et que les entreprises cherchent à répondre aux demandes croissantes des consommateurs pour des produits plus écologiques.
Les technologies numériques et l’Internet des objets (IoT) jouent également un rôle central dans la gestion et l’optimisation des lignes de peinture poudre automatiques. En intégrant des capteurs et des dispositifs de surveillance en temps réel, il devient possible de suivre chaque étape du processus, de la pulvérisation à la cuisson, en passant par l’inspection de la qualité. Ces systèmes collectent des données sur des paramètres clés tels que la température, l’humidité, la vitesse de pulvérisation, et même la qualité de la surface peinte, permettant aux opérateurs d’identifier immédiatement toute anomalie ou variation par rapport aux normes de qualité.
Ces informations sont ensuite analysées à l’aide de logiciels sophistiqués qui fournissent des recommandations sur les ajustements à apporter pour améliorer les performances de la ligne. Par exemple, si la couverture de peinture est insuffisante ou si des irrégularités apparaissent sur la surface, des ajustements peuvent être effectués instantanément, réduisant ainsi les défauts et le gaspillage. Ces systèmes de contrôle avancés contribuent non seulement à maintenir une qualité constante mais aussi à améliorer la traçabilité des produits et à optimiser les processus de maintenance prédictive.
Un autre aspect intéressant de l’évolution des lignes de peinture poudre automatiques est l’intégration de la robotique avancée. Les robots modernes ne sont plus seulement utilisés pour appliquer la peinture, mais ils sont également capables de manipuler et de positionner les pièces dans la cabine de peinture, de les inspecter avant et après le processus, et même d’effectuer des ajustements en temps réel. L’intelligence artificielle (IA) joue un rôle clé dans cette évolution, permettant aux robots de “communiquer” entre eux et de prendre des décisions autonomes pour améliorer l’efficacité du processus. Cela peut inclure la modification de l’angle de pulvérisation en fonction de la forme de la pièce ou l’adaptation de la pression de l’air pour optimiser la couverture de peinture.
Les lignes de peinture poudre automatiques ne sont donc pas simplement des outils de production; elles deviennent des systèmes intelligents qui peuvent s’adapter, apprendre et évoluer en fonction des besoins de l’entreprise. La digitalisation de ces lignes offre également des opportunités pour la maintenance prédictive et l’analyse des performances, permettant de réduire les temps d’arrêt non planifiés et de prolonger la durée de vie des équipements.
En résumé, les lignes de peinture poudre automatiques sont devenues un élément indispensable de l’industrie moderne, combinant efficacité, flexibilité, et respect de l’environnement. Grâce aux progrès continus en matière de robotique, d’automatisation, et d’analyse de données, elles permettent aux entreprises de répondre à une demande croissante pour des produits finis de haute qualité tout en optimisant les coûts, la consommation d’énergie, et l’impact environnemental. Le futur de ces technologies semble prometteur, avec des solutions toujours plus intelligentes, durables et adaptées aux besoins spécifiques des industries.
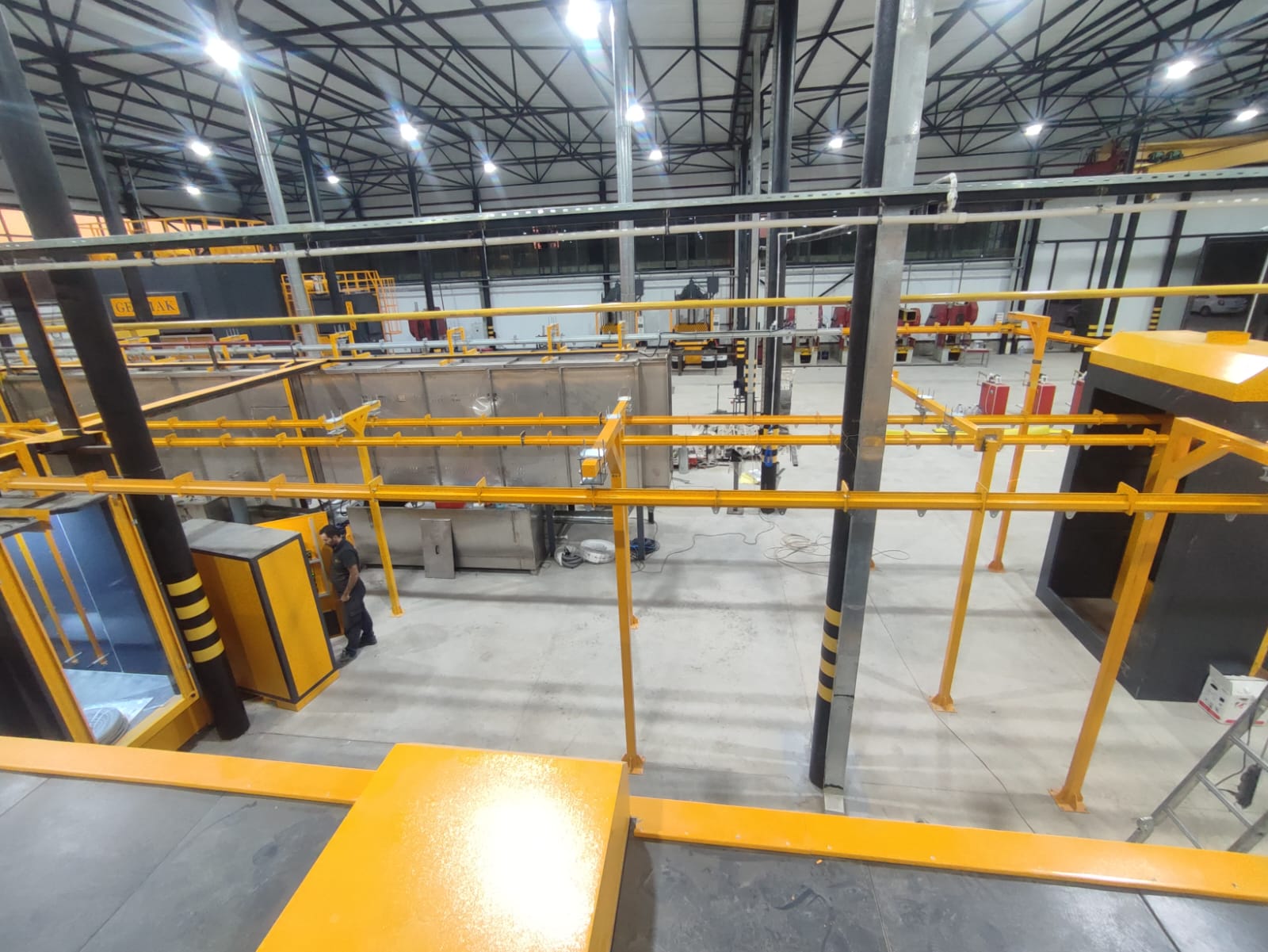
Le futur des lignes de peinture poudre automatiques se dirige vers une intégration encore plus poussée des technologies d’intelligence artificielle (IA) et de machine learning. Ces technologies permettront une gestion encore plus proactive des lignes de production. Par exemple, grâce à l’analyse des données en temps réel, les systèmes pourraient détecter des tendances dans les anomalies de qualité avant qu’elles ne se manifestent de manière évidente, en ajustant automatiquement les paramètres de pulvérisation, la température du four, ou même les vitesses de convoyage. Cette approche prédictive aidera non seulement à maintenir une qualité constante, mais aussi à réduire les coûts de maintenance et à éviter les arrêts imprévus.
Les systèmes d’intelligence artificielle pourraient également apprendre et s’adapter à différents types de produits ou matériaux, permettant une plus grande diversité de finition sans nécessiter d’interventions manuelles complexes. Par exemple, une ligne de peinture poudre automatique pourrait être capable de traiter une gamme plus large de matériaux (aluminium, acier inoxydable, plastique, etc.) en ajustant automatiquement la composition de la peinture ou les paramètres de cuisson pour s’adapter à chaque substrat. Cela ouvrirait la porte à des lignes de production plus flexibles et polyvalentes, capables de répondre à une variété de demandes sans avoir besoin de configurations spécifiques pour chaque produit.
De plus, l’intégration de la réalité virtuelle (RV) et de la réalité augmentée (RA) pourrait révolutionner la formation des opérateurs et le contrôle qualité dans ces lignes automatisées. Par exemple, les opérateurs pourraient utiliser des lunettes de réalité augmentée pour visualiser les conditions de production en temps réel, recevoir des alertes instantanées concernant des défauts potentiels, ou même ajuster certains paramètres à distance. Cela permettrait une intervention rapide et précise, réduisant les risques d’erreurs humaines tout en améliorant l’efficacité générale du processus. Les techniciens de maintenance pourraient également utiliser des outils de RA pour effectuer des réparations ou des ajustements sur les équipements, avec des instructions détaillées affichées directement sur leurs lunettes ou écrans.
Dans un autre domaine d’innovation, les lignes de peinture poudre automatiques pourraient bénéficier d’une meilleure gestion des déchets grâce à l’amélioration des systèmes de récupération de la poudre. Alors que la récupération des matériaux non utilisés a déjà fait d’énormes progrès, l’avenir pourrait voir l’introduction de technologies permettant de recycler la peinture en poudre de manière plus efficace, en particulier lorsque des couleurs spécifiques sont utilisées. Cela pourrait inclure des procédés de séparation des pigments et des résines qui permettraient de réutiliser la poudre de manière plus sélective et précise, contribuant à la réduction des coûts et à un usage encore plus responsable des ressources.
En outre, avec la montée des préoccupations liées au changement climatique et à l’impact environnemental de la fabrication, les lignes de peinture poudre automatiques pourraient également évoluer pour intégrer des technologies plus écologiques. L’usage de peintures en poudre à base de matériaux biosourcés ou recyclés pourrait se généraliser, réduisant ainsi l’empreinte carbone des produits finis. Des recherches sont actuellement en cours pour développer des peintures en poudre encore plus durables, avec des compositions qui consomment moins d’énergie pour leur fabrication et offrent des performances accrues en termes de résistance et de longévité.
L’intégration des principes de l’économie circulaire pourrait aussi se renforcer. Par exemple, des systèmes de collecte et de réutilisation des eaux de lavage et des solvants (lorsque nécessaires dans certains processus de nettoyage) pourraient être installés pour limiter l’impact environnemental. Ces innovations permettent non seulement de réduire les coûts d’exploitation mais aussi de répondre aux exigences croissantes en matière de responsabilité environnementale.
Enfin, dans une perspective d’internationalisation et d’expansion des marchés, les lignes de peinture poudre automatiques pourraient devenir plus interconnectées à l’échelle mondiale. Grâce aux avancées en matière de technologies cloud et d’analyse de données massives (big data), les fabricants pourront suivre à distance les performances de leurs lignes de peinture dans différentes régions du monde. Cela offrirait la possibilité d’une gestion centralisée et d’une optimisation globale des processus de production. Par exemple, un fabricant ayant plusieurs sites de production pourrait centraliser le suivi des performances des lignes de peinture et, grâce à l’analyse des données, appliquer des ajustements sur tous les sites pour harmoniser la qualité et les performances de production.
L’automatisation et l’intelligence artificielle pourraient également offrir une plus grande transparence dans le processus de production, permettant un suivi détaillé et une traçabilité complète des produits. Cela pourrait être particulièrement utile dans les secteurs où la qualité et la certification sont cruciales, comme l’industrie automobile ou aéronautique, où les clients exigent des rapports détaillés sur chaque étape du processus de fabrication. La transparence accrue et la possibilité de retracer chaque produit avec précision garantiront la conformité aux normes et renforceront la confiance des consommateurs et des partenaires commerciaux.
En conclusion, les lignes de peinture poudre automatiques, en constante évolution, continuent d’offrir des solutions novatrices pour les industries modernes. Elles sont de plus en plus intelligentes, écologiques, flexibles et interconnectées, permettant non seulement de répondre aux exigences de qualité et d’efficacité des processus de production, mais aussi de s’adapter aux nouveaux défis environnementaux et économiques. L’avenir de cette technologie semble prometteur, avec de nouvelles avancées qui continueront de redéfinir le paysage de la production industrielle.
Chaîne de Poudrage Automatique
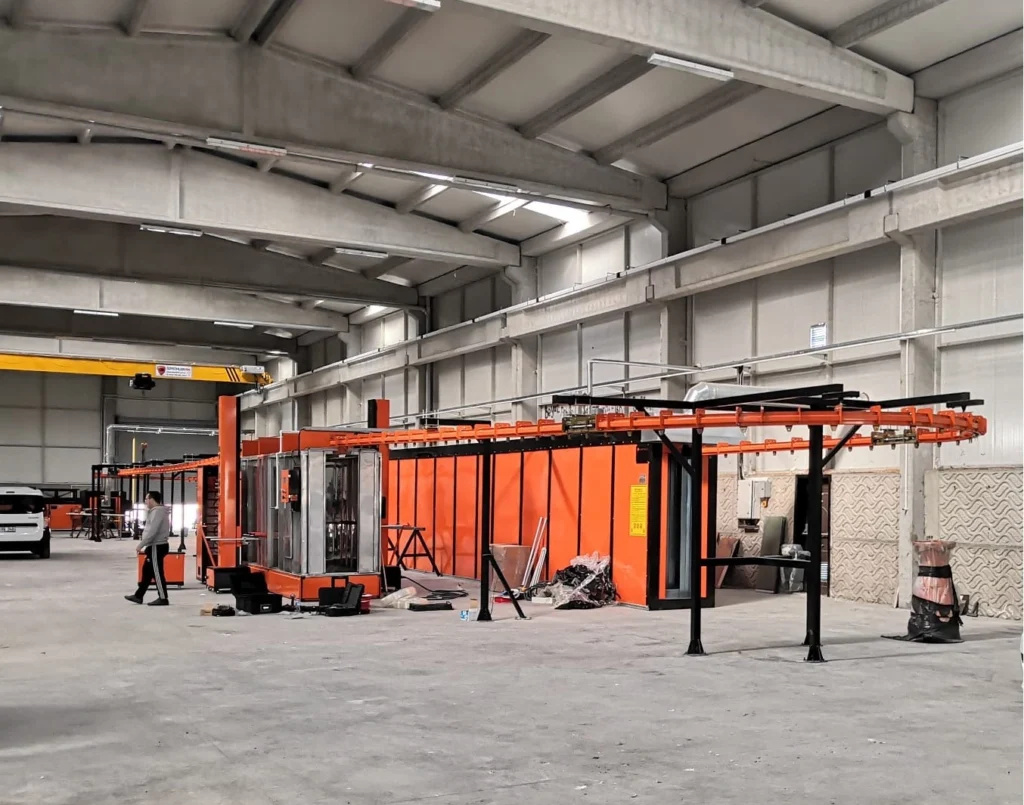
Une chaîne de poudrage automatique est un système industriel utilisé pour appliquer une couche uniforme de poudre, généralement sur des pièces métalliques, plastiques ou autres matériaux. Ce processus est souvent employé pour fournir une finition esthétique et protectrice, particulièrement dans des applications où une résistance accrue aux rayures, aux conditions climatiques et à l’usure est requise. Le poudrage, contrairement à la peinture liquide traditionnelle, utilise des poudres sèches qui sont projetées sur la surface de l’objet à l’aide de pistolets électrostatiques. Ce processus est non seulement efficace, mais il est aussi respectueux de l’environnement, car il ne nécessite pas de solvants.
La chaîne de poudrage automatique commence par un processus de préparation des pièces. Les objets à traiter, qui peuvent être de diverses tailles et formes, passent généralement par une série d’étapes de nettoyage. Cela inclut le dégraissage, la déphosphatation et parfois un rinçage. Ces étapes sont cruciales pour garantir une adhérence optimale de la poudre sur la surface des pièces. Le nettoyage est effectué à l’aide de systèmes de lavage à haute pression, parfois combinés avec des produits chimiques spécifiques, pour éliminer toute impureté, graisse ou saleté.
Une fois les pièces nettoyées et séchées, elles sont transportées vers la cabine de poudrage. Dans cette étape, des pistolets électrostatiques projetant la poudre sont utilisés. Ces pistolets chargent la poudre électriquement, ce qui permet à cette dernière de s’accrocher à la surface des pièces. Cette application est précise, et la poudre est appliquée de manière homogène, même sur des formes complexes. Il est possible de contrôler avec précision le débit de la poudre, la pression de l’air et l’angle de pulvérisation pour garantir une couverture uniforme, quel que soit le type de produit à traiter.
La couche de poudre ainsi appliquée est ensuite durcie dans un four de cuisson. La température et le temps de cuisson sont des éléments critiques, car ils permettent à la poudre de fondre et de se lier à la surface du matériau, créant ainsi une finition solide et durable. La durée du passage dans le four peut varier en fonction du type de poudre utilisée, de la taille des pièces et de la spécificité du produit. Les fours modernes sont souvent équipés de systèmes de contrôle de la température pour garantir une cuisson homogène et une finition optimale.
L’un des grands avantages de la chaîne de poudrage automatique est la possibilité de récupérer la poudre excédentaire, ce qui réduit les coûts et minimise les déchets. Les systèmes de récupération de poudre collectent la poudre non utilisée, la filtrent et la réinjectent dans le système pour être utilisée à nouveau. Cela permet d’optimiser l’efficacité de la production tout en respectant des normes environnementales strictes. Les installations modernes sont équipées de filtres à haute efficacité pour assurer que la qualité de la poudre récupérée reste constante.
Le poudrage est un processus particulièrement adapté aux lignes de production automatisées. Il permet une production rapide, avec une faible intervention manuelle, tout en assurant une finition de qualité constante. Cela est particulièrement important dans des industries comme l’automobile, la fabrication de meubles en métal, ou encore l’électroménager, où des volumes élevés de pièces doivent être traitées avec une qualité irréprochable. L’automatisation du processus réduit les risques d’erreurs humaines, assure une couverture uniforme de la peinture et améliore la productivité globale.
L’un des principaux avantages de la chaîne de poudrage automatique est son faible impact environnemental. Contrairement à la peinture liquide, qui utilise des solvants, le poudrage ne nécessite aucun produit chimique volatile. La peinture en poudre est également non toxique, et son application ne produit pas de fumées dangereuses. De plus, étant donné qu’il n’y a pas d’évaporation de solvants, il y a moins de déchets produits pendant le processus, et la gestion des déchets est simplifiée grâce à la récupération de la poudre excédentaire. Ces aspects font du poudrage une méthode de finition plus respectueuse de l’environnement et conforme aux réglementations de plus en plus strictes en matière de pollution et de santé publique.
Une autre caractéristique des chaînes de poudrage automatiques modernes est leur grande flexibilité. Elles peuvent être adaptées à différents types de produits et à des exigences spécifiques en matière de finition. Les installations peuvent être configurées pour traiter une large gamme de pièces de différentes tailles, formes et matériaux. Cela est rendu possible grâce à des équipements modulaires et des robots capables de manipuler des pièces de géométries complexes. Par exemple, des robots peuvent être utilisés pour positionner les pièces de manière optimale pour le poudrage, en garantissant une application uniforme sur toutes les surfaces, même celles qui sont difficiles d’accès.
Le développement de technologies avancées, comme les robots à bras articulés ou les robots collaboratifs (cobots), permet également d’améliorer l’efficacité et la précision du processus. Ces robots peuvent être programmés pour s’adapter à différents types de pièces, changer de mode de pulvérisation en fonction de la forme ou de la taille de la pièce, et même détecter les imperfections de la surface avant ou après le poudrage. Ces systèmes intelligents, couplés à des capteurs de haute précision, permettent d’améliorer la qualité de la finition, de réduire le gaspillage de poudre et de garantir une productivité accrue.
Le contrôle de la qualité est un autre domaine dans lequel les chaînes de poudrage automatiques ont fait de grands progrès. Les systèmes de vision par caméra et les capteurs permettent une surveillance en temps réel de la qualité de la couche de poudre appliquée. Ces dispositifs peuvent détecter toute irrégularité dans la couverture, comme des zones non couvertes ou une épaisseur de couche inégale, et ajuster automatiquement les paramètres de pulvérisation pour corriger ces défauts. Cela garantit une finition uniforme et de haute qualité, sans nécessiter d’interventions manuelles après coup.
L’évolution future des chaînes de poudrage automatiques sera probablement marquée par une intégration accrue de technologies telles que l’intelligence artificielle et l’Internet des objets (IoT). Ces technologies permettront un suivi plus précis du processus et une gestion de la production plus intelligente. Par exemple, des capteurs IoT pourraient collecter des données sur chaque étape du processus de poudrage et envoyer des alertes en cas d’anomalies. De plus, grâce à l’IA, les lignes de production pourraient apprendre des performances passées et optimiser en temps réel les paramètres de l’application pour maximiser l’efficacité et la qualité.
En termes d’impact environnemental, des progrès sont également attendus. Des recherches sont en cours pour développer des poudres plus écologiques, fabriquées à partir de matériaux biosourcés ou recyclés, qui pourraient remplacer les poudres traditionnelles. Ces innovations contribueront à réduire l’empreinte carbone des processus de production tout en maintenant des performances élevées. L’intégration de solutions de récupération et de recyclage plus avancées pourrait également améliorer la durabilité du processus en maximisant l’utilisation des matériaux et en réduisant les déchets.
En résumé, les chaînes de poudrage automatiques représentent une avancée majeure dans le domaine de la finition industrielle. Elles offrent des solutions rapides, efficaces, écologiques et flexibles pour la production de pièces de haute qualité. Grâce à l’automatisation, à la récupération de poudre, et aux nouvelles technologies, elles sont prêtes à évoluer pour répondre aux défis futurs, en offrant des solutions encore plus intelligentes, durables et performantes pour l’industrie moderne.
L’extension des capacités des chaînes de poudrage automatiques continuera de s’étendre avec l’introduction de nouvelles technologies destinées à améliorer la personnalisation et la réactivité des systèmes de production. Les avancées dans la robotique collaborative, par exemple, permettent une interaction plus fluide entre les machines et les opérateurs humains. Ces robots, conçus pour travailler en sécurité à côté des opérateurs, permettront d’ajuster et de maintenir les chaînes de poudrage de manière plus souple et réactive tout en assurant un haut niveau d’automatisation. Cela permet d’augmenter la flexibilité des lignes de production, en adaptant rapidement les réglages aux besoins de différents types de produits.
De plus, la mise en réseau des différentes installations de production grâce à des solutions numériques va transformer la manière dont les chaînes de poudrage automatiques sont gérées. En connectant les chaînes de poudrage à des plateformes cloud, les entreprises pourront centraliser le contrôle et la supervision des opérations de production. Cela permettra une gestion plus agile des chaînes de production réparties géographiquement, tout en favorisant une collaboration entre les sites. Les données collectées à partir de chaque installation permettront d’identifier les meilleures pratiques et d’harmoniser les processus à l’échelle mondiale, augmentant ainsi l’efficacité et la constance de la production.
L’intégration des technologies de maintenance prédictive, également alimentée par l’Internet des objets (IoT), contribuera à améliorer la longévité des équipements. Les capteurs IoT placés sur les éléments critiques des chaînes de poudrage, tels que les moteurs, les convoyeurs ou les systèmes de pulvérisation, permettront de détecter en temps réel des signes d’usure ou des dysfonctionnements avant qu’ils n’entraînent des pannes majeures. Par exemple, un capteur pourrait détecter une variation inhabituelle de la température dans le four de cuisson et avertir immédiatement l’opérateur, permettant ainsi une action préventive avant qu’un problème ne perturbe la production.
L’intelligence artificielle et l’apprentissage machine seront également déterminants pour automatiser davantage le processus de décision. En utilisant des algorithmes de machine learning, les systèmes de contrôle des chaînes de poudrage pourront ajuster les paramètres de manière autonome en fonction des variables observées, comme les conditions climatiques (humidité, température) ou les types de matériaux traités. Ces ajustements automatisés contribueront à maintenir une qualité constante tout au long du processus, en ajustant par exemple le flux de poudre ou les réglages des pistolets électrostatiques pour compenser les variations dans la production.
À mesure que la production mondiale se tourne vers des pratiques plus durables, les chaînes de poudrage automatiques seront de plus en plus appelées à adopter des matériaux écologiques et à respecter des critères de plus en plus stricts en matière de durabilité. Les peintures en poudre à base de matériaux recyclés, mais aussi des solutions innovantes telles que l’utilisation de nanotechnologies dans la formulation des poudres, ouvriront la voie à de nouvelles applications. Ces technologies permettront non seulement de réduire l’impact environnemental, mais également d’augmenter les performances des finitions en termes de résistance à l’usure, de durabilité et de résistance aux conditions extrêmes (chaleur, humidité, produits chimiques).
Par ailleurs, les chaînes de poudrage automatiques devront s’adapter à l’évolution des attentes des consommateurs en matière de personnalisation. L’essor de l’industrie 4.0, avec sa capacité à produire des articles en petites séries avec des exigences de personnalisation élevées, entraînera une demande croissante pour des lignes de production flexibles capables de gérer des commandes spéciales, des couleurs personnalisées ou des textures spécifiques. L’intégration de solutions de gestion de la production intelligente et de systèmes de suivi des commandes en temps réel permettra aux entreprises de répondre à ces demandes tout en maintenant une efficacité de production élevée.
L’avenir des chaînes de poudrage automatiques pourrait aussi inclure l’optimisation des processus grâce à l’utilisation de la réalité augmentée (RA). Les opérateurs pourraient, par exemple, utiliser des lunettes de RA pour recevoir des informations contextuelles en temps réel, comme des diagnostics de machines, des instructions de maintenance ou des données sur la qualité de la finition des pièces. La RA pourrait également être utilisée pour former les opérateurs plus efficacement en leur offrant une simulation des processus de poudrage, ce qui permettrait de réduire les temps de formation et d’améliorer les performances des opérateurs.
L’expansion de la production intelligente avec des lignes de poudrage automatiques connectées et dotées de capacités de décision autonomes ouvrira également la voie à des innovations dans la chaîne logistique. L’intégration de l’IA et du machine learning pourrait permettre une gestion optimisée des stocks de poudres, une planification plus précise des cycles de production et une réduction des ruptures de stock. Cela favorisera une production plus fluide, réduisant les coûts d’inventaire et permettant une meilleure gestion des flux de matières premières.
En outre, avec l’accent croissant sur la transparence et la traçabilité, particulièrement dans des secteurs comme l’automobile ou l’aéronautique, les chaînes de poudrage automatiques devront offrir des solutions de suivi détaillé. L’enregistrement des données à chaque étape du processus de poudrage permettra de garantir que chaque pièce respecte les standards de qualité et de conformité, et ce, de manière vérifiable. Ces solutions de traçabilité renforcent non seulement la qualité, mais aussi la confiance des clients, qui peuvent être assurés que chaque produit est fabriqué selon des normes strictes.
Finalement, alors que les chaînes de poudrage automatiques deviennent de plus en plus complexes et sophistiquées, elles joueront un rôle crucial dans l’évolution de la production industrielle mondiale, en offrant des solutions plus écologiques, plus flexibles, et plus intelligentes. Grâce à la convergence de la robotique, de l’intelligence artificielle, des technologies de l’information et des matériaux durables, ces chaînes continueront de répondre aux défis de production contemporains tout en permettant aux entreprises de répondre à des exigences de plus en plus strictes en matière de qualité, de coût et de durabilité.
Systèmes de Poudrage
Les systèmes de poudrage sont des équipements industriels utilisés pour appliquer des couches de peinture en poudre sur une large gamme de pièces et de surfaces. Ces systèmes sont essentiels dans de nombreux secteurs industriels, notamment dans la fabrication automobile, l’électroménager, le mobilier métallique, et bien d’autres. Le processus de poudrage est particulièrement apprécié pour ses avantages en termes de durabilité, de qualité de finition, d’efficacité énergétique et d’impact environnemental réduit par rapport à la peinture traditionnelle à base de solvants.
Le système de poudrage commence par un processus de préparation des pièces à traiter. Celles-ci sont d’abord nettoyées pour éliminer toute impureté, graisse, ou oxydation qui pourrait empêcher la bonne adhésion de la poudre. Les méthodes de nettoyage peuvent inclure des bains de dégraissage, des jets à haute pression, ou des procédés de sablage. Le nettoyage est crucial, car toute contamination sur la surface peut entraîner une mauvaise adhésion de la poudre et nuire à la finition finale. Après cette étape, les pièces sont séchées pour éliminer toute humidité qui pourrait interférer avec l’application de la poudre.
Une fois la pièce préparée, elle est transférée dans la cabine de poudrage, où l’application de la poudre a lieu. Le système de poudrage utilise généralement des pistolets électrostatiques pour appliquer la poudre. Ces pistolets chargent électriquement la poudre de manière à ce qu’elle s’attache à la surface de la pièce, ce qui permet une couverture uniforme même sur des surfaces complexes et difficiles d’accès. Les pistolets de poudrage sont souvent réglables, permettant aux opérateurs de contrôler la quantité de poudre projetée, l’intensité de la charge électrostatique et la pression de l’air pour ajuster la couverture en fonction du type de matériau et de la forme de la pièce. Ce système permet une application précise et économique, car une partie de la poudre non utilisée peut être récupérée et réutilisée.
L’application de la poudre est suivie par le processus de durcissement, généralement dans un four de cuisson. Les pièces sont transportées dans le four, où la poudre est chauffée à une température précise, généralement entre 180 et 200°C, pour fondre et se lier à la surface de la pièce. Ce processus, appelé polymérisation, permet à la poudre de durcir, créant ainsi une finition lisse, uniforme et résistante aux conditions difficiles telles que l’humidité, les rayures et les produits chimiques. La durée et la température de cuisson doivent être scrupuleusement contrôlées pour garantir une finition de qualité et éviter des défauts comme des bulles, des irrégularités ou des déformations des pièces.
Une caractéristique importante des systèmes de poudrage est leur faible impact environnemental par rapport aux systèmes de peinture liquides. La peinture en poudre ne contient pas de solvants et émet très peu de COV (composés organiques volatils) dans l’air. En outre, la poudre excédentaire peut être récupérée, filtrée et réutilisée, ce qui permet de minimiser les déchets et de réduire les coûts. Cette capacité de récupération est rendue possible grâce à des systèmes de filtration et de collecte qui captent la poudre non utilisée et la renvoient dans le processus. Cela non seulement réduit les coûts liés à la consommation de peinture, mais permet également de respecter des normes environnementales strictes.
Les systèmes de poudrage modernes sont conçus pour être très flexibles et adaptés à des applications variées. Ils peuvent traiter une grande variété de pièces, qu’il s’agisse de grandes surfaces planes ou de petites pièces complexes. Certains systèmes sont dotés de robots ou de bras articulés qui peuvent déplacer les pièces et les orienter de manière optimale pour le poudrage. Ces robots permettent de traiter des pièces de différentes tailles et formes sans nécessiter de modifications complexes du système. Ils permettent également de réduire l’intervention humaine, ce qui augmente la sécurité et l’efficacité du processus.
De plus, l’intégration des systèmes de contrôle numériques dans les installations de poudrage a considérablement amélioré la précision et l’efficacité du processus. Les systèmes de gestion et de contrôle modernes permettent de surveiller et d’ajuster automatiquement des paramètres clés, tels que la pression de pulvérisation, la quantité de poudre appliquée, et la vitesse de passage des pièces. Grâce à ces systèmes intelligents, les entreprises peuvent garantir une finition uniforme et de haute qualité tout en optimisant la consommation de matériaux.
Les systèmes de poudrage sont également utilisés dans des applications de personnalisation, où la demande pour des finitions uniques et variées est de plus en plus forte. Les fabricants peuvent choisir parmi une large gamme de couleurs, textures et effets, allant des finitions mates aux finitions métalliques ou brillantes, pour répondre à des besoins spécifiques. De plus, certaines poudres spéciales sont disponibles pour des applications nécessitant des propriétés particulières, comme une résistance accrue à la chaleur, aux produits chimiques ou à l’abrasion. Les avancées dans la formulation des poudres permettent également de répondre aux exigences des industries de pointe, telles que l’aéronautique et l’automobile, où des critères stricts en matière de performance et de durabilité sont nécessaires.
Les innovations en matière de systèmes de poudrage continuent de progresser. L’adoption de la technologie de l’Internet des objets (IoT) permet aux équipements de poudrage de collecter et de partager des données en temps réel, ce qui offre une plus grande transparence et une gestion de la production améliorée. Par exemple, grâce à des capteurs intégrés, les systèmes peuvent surveiller la qualité de l’application de la poudre, détecter les anomalies et envoyer des alertes aux opérateurs avant qu’un problème ne survienne. Cela permet une gestion proactive des défauts, réduisant ainsi les risques de retouches et d’ajustements en cours de production.
L’intelligence artificielle (IA) et l’analyse prédictive joueront également un rôle de plus en plus important dans l’optimisation des processus de poudrage. Les algorithmes d’IA peuvent analyser les données collectées par les capteurs pour détecter des modèles et des tendances, permettant ainsi aux systèmes de faire des ajustements autonomes et de prédire les problèmes avant qu’ils ne surviennent. Par exemple, un système pourrait ajuster automatiquement les paramètres de pulvérisation en fonction des conditions environnementales changeantes (humidité, température), assurant une application de poudre parfaite à chaque cycle.
À long terme, les progrès dans la fabrication de peintures en poudre écologiques et durables, telles que celles à base de matériaux biosourcés, permettront de réduire encore davantage l’empreinte carbone des systèmes de poudrage. L’essor de ces matériaux, couplé à des techniques de production plus efficaces, contribuera à la création de systèmes encore plus respectueux de l’environnement, tout en maintenant les standards de qualité nécessaires aux industries.
En conclusion, les systèmes de poudrage représentent une solution moderne, efficace et durable pour l’application de finitions de haute qualité. Grâce à l’automatisation, à l’intelligence artificielle, à l’intégration de l’IoT et aux innovations en matière de matériaux, ces systèmes continuent de transformer les processus industriels en offrant des solutions plus flexibles, plus écologiques et plus rentables. Ils répondent aux défis actuels de la production de manière innovante tout en garantissant une performance optimale et une réduction de l’impact environnemental.
Systèmes de poudrage
Les systèmes de poudrage continueront d’évoluer avec la montée en puissance des technologies de l’industrie 4.0, qui apporteront des améliorations supplémentaires en matière de productivité, de contrôle qualité et de personnalisation. L’intégration de la robotique avancée, des capteurs intelligents, et de l’intelligence artificielle ouvrira la voie à des processus de poudrage encore plus automatisés et adaptatifs. Ces avancées permettront d’optimiser chaque aspect du processus, depuis l’application de la poudre jusqu’à la cuisson, tout en garantissant une réduction continue des coûts opérationnels.
L’un des axes d’évolution des systèmes de poudrage sera l’amélioration de la flexibilité pour s’adapter à des volumes de production de plus en plus variés, y compris des séries de production petites et moyennes. Cela est particulièrement important dans des secteurs comme l’automobile, où les exigences de personnalisation des pièces se multiplient, ou dans l’industrie du mobilier, où les tendances changent rapidement. Les lignes de production devront être capables de gérer des demandes fluctuantes et des configurations de pièces diverses sans interrompre la production.
Les systèmes de poudrage seront également capables de répondre aux demandes croissantes de recyclage et de durabilité. En plus de récupérer et de réutiliser la poudre excédentaire, les avancées en matière de gestion des déchets et de recyclage des matériaux de revêtement permettront de réduire encore davantage les déchets produits durant le processus. Des innovations dans les technologies de filtration permettront une collecte plus efficace de la poudre excédentaire et de la poudre non adhérée, minimisant ainsi les pertes et contribuant à une économie circulaire. L’intégration de nouvelles poudres à base de matériaux recyclés et biosourcés permettra de renforcer la durabilité des produits finis tout en réduisant l’empreinte environnementale des processus de production.
Les améliorations dans les technologies de surveillance et de contrôle qualité seront un autre domaine clé pour les systèmes de poudrage de demain. Les capteurs avancés et les systèmes de vision intelligente permettront une inspection en temps réel de la qualité du poudrage. Par exemple, des caméras et des capteurs de surface pourraient analyser la couverture de la poudre, identifier les irrégularités ou les défauts dans l’application, et ajuster immédiatement les paramètres de pulvérisation pour rectifier les problèmes sans intervention humaine. Ces systèmes intelligents permettront également de garantir que les spécifications de chaque pièce sont respectées, assurant une qualité constante tout au long de la production.
Les innovations en matière de matériaux de poudrage seront également déterminantes pour l’avenir des systèmes de poudrage. Les peintures en poudre modernes évoluent pour offrir une plus grande résistance aux conditions extrêmes, qu’il s’agisse de températures élevées, de produits chimiques agressifs ou d’humidité. Les poudres hautement spécialisées seront capables de fournir des finitions fonctionnelles tout en conservant des caractéristiques esthétiques, offrant ainsi une meilleure performance pour des applications dans des secteurs exigeants comme l’aéronautique, le secteur militaire, ou l’électronique. Des formulations de poudres innovantes peuvent également offrir des propriétés antibactériennes, autonettoyantes ou même des capacités de détection de chaleur ou de rayonnement, ce qui est particulièrement utile pour certaines applications industrielles avancées.
Les systèmes de poudrage continueront d’intégrer des technologies permettant une gestion plus précise de l’énergie et de la consommation des ressources. La réduction de la consommation énergétique est essentielle, surtout dans des processus comme la cuisson de la poudre, où les fours peuvent consommer une quantité importante d’énergie. Les nouvelles technologies permettront d’optimiser les cycles de chauffage et de refroidissement dans les fours de manière à réduire la consommation d’énergie, tout en maintenant une qualité de finition optimale. Les systèmes à haute efficacité thermique, couplés avec des technologies de récupération de chaleur, permettront de réduire l’empreinte carbone globale des lignes de production.
Dans le domaine de la connectivité, les systèmes de poudrage seront de plus en plus interconnectés avec d’autres équipements de production dans une usine intelligente. L’intégration des systèmes ERP (Enterprise Resource Planning) et MES (Manufacturing Execution Systems) avec les lignes de poudrage permettra de mieux coordonner la production, de suivre en temps réel l’avancement des commandes et d’optimiser la gestion des stocks de matières premières et des produits finis. De cette manière, les entreprises pourront réagir plus rapidement aux fluctuations de la demande, gérer les plannings de production avec plus de souplesse, et réduire les délais de livraison tout en améliorant l’efficacité globale.
Le suivi et la traçabilité des produits finiront également par devenir une exigence indispensable dans les industries les plus strictes. Les systèmes de poudrage automatisés seront capables de collecter des données précises sur chaque étape du processus, y compris l’application de la poudre, la cuisson et les résultats de contrôle qualité. Ces informations seront stockées dans une base de données centralisée et pourront être facilement consultées à des fins de contrôle qualité, de conformité réglementaire, ou pour des audits internes. Cette traçabilité permettra non seulement de renforcer la confiance des clients, mais aussi d’améliorer la gestion des risques, en garantissant que toutes les pièces respectent les normes strictes de qualité.
Enfin, les défis liés à la personnalisation, à la flexibilité et à l’évolution des attentes des consommateurs, notamment dans des secteurs comme le design de produits de consommation, rendront les systèmes de poudrage plus modulables. L’émergence de solutions de finition multi-variantes permettra de répondre à des demandes diversifiées en matière de textures, de couleurs et de finitions, avec une plus grande rapidité d’exécution. Les systèmes de poudrage deviendront des outils polyvalents et réactifs, capables de réaliser des productions sur mesure sans compromettre l’efficacité des processus industriels.
En résumé, les systèmes de poudrage continuent de se perfectionner, non seulement en termes d’automatisation et de performance, mais aussi en matière d’efficacité énergétique, de durabilité et de personnalisation. L’évolution des technologies telles que l’intelligence artificielle, l’IoT et la robotique ouvrira la voie à une production encore plus intelligente, plus écologique et plus réactive. En répondant aux exigences croissantes de l’industrie moderne en matière de flexibilité, de qualité et de durabilité, les systèmes de poudrage continueront d’être un pilier essentiel dans le développement des processus industriels du futur.
À mesure que la concurrence dans les secteurs industriels s’intensifie et que les attentes des clients évoluent, l’innovation continue dans les systèmes de poudrage sera essentielle pour maintenir un avantage compétitif. Les entreprises devront constamment rechercher des moyens d’améliorer la vitesse de production, la qualité de la finition, ainsi que l’efficacité des processus tout en respectant des critères environnementaux de plus en plus stricts. Les systèmes de poudrage devront répondre à des critères de performance de plus en plus exigeants, notamment en matière de personnalisation des produits, de réduction des coûts, et de durabilité.
Un domaine clé dans cette évolution sera l’amélioration de la vitesse de traitement tout en garantissant la qualité. Les nouveaux systèmes de poudrage, grâce à une automatisation accrue et à des algorithmes d’optimisation, seront capables d’ajuster rapidement leurs paramètres pour accélérer le cycle de production. Par exemple, la vitesse d’application de la poudre pourrait être ajustée en temps réel en fonction de la forme et des dimensions des pièces, ce qui permettrait de réduire le temps de production sans compromettre la couverture ou la finition. Ces gains en termes de rapidité seront essentiels dans des industries comme l’automobile ou l’électronique, où la demande pour des délais de fabrication de plus en plus courts est un impératif.
L’intégration de l’analyse des données en temps réel et de la gestion de la production par des plateformes cloud facilitera également la coordination entre les différentes étapes de la production. Ces plateformes permettront aux opérateurs de suivre l’état de la ligne de production, d’identifier des tendances et de détecter des anomalies qui pourraient nécessiter des ajustements avant que des défauts ne surviennent. Par exemple, une plateforme cloud pourrait alerter les opérateurs si un des pistolets de poudrage montre des signes d’usure ou si la température du four commence à dévier des paramètres souhaités, permettant ainsi d’éviter des interruptions de production coûteuses.
En matière de personnalisation, les systèmes de poudrage modernes seront capables de gérer une grande variété de finitions, de textures et de couleurs tout en maintenant une grande précision. L’adoption de technologies comme la réalité augmentée (RA) et la simulation virtuelle permettra aux opérateurs de prévisualiser les résultats de différentes options de finition avant même que la poudre ne soit appliquée. Cela pourrait offrir une plus grande liberté pour le design de produits personnalisés et contribuer à un contrôle qualité plus strict, en vérifiant la conformité des pièces avant la cuisson.
De plus, avec l’augmentation de la demande pour des produits personnalisés, les systèmes de poudrage devront être capables de s’adapter facilement aux petites séries et aux productions sur demande. Cela implique non seulement une flexibilité dans le réglage des équipements de poudrage, mais aussi une capacité à gérer des stocks de matières premières plus diversifiés, et à produire des finitions de haute qualité même pour des volumes de production réduits. L’utilisation de technologies telles que les “usines intelligentes” permettra de mieux gérer ces transitions entre les différents types de production tout en maintenant une qualité uniforme.
L’aspect écologique des systèmes de poudrage continuera également d’évoluer. Outre la réduction des émissions de COV et des déchets de poudre, de nouvelles initiatives écologiques pourront inclure l’utilisation de poudres fabriquées à partir de matériaux durables et recyclés, ou l’adoption de technologies de recyclage encore plus efficaces. La mise en œuvre de technologies de réduction de la consommation d’énergie, comme les systèmes de récupération de chaleur ou l’optimisation thermique des fours de cuisson, jouera un rôle important pour réduire l’empreinte carbone des systèmes de poudrage. De plus, l’usage de matériaux et de processus respectueux de l’environnement dans la fabrication des systèmes eux-mêmes (p. ex. en utilisant des matériaux recyclés pour les composants de machines) sera un autre levier pour réduire l’impact global des opérations.
Une autre avancée importante concernera la réduction des risques et des coûts liés aux arrêts imprévus. En intégrant des systèmes de maintenance prédictive, les chaînes de poudrage pourront surveiller en permanence l’état des équipements et anticiper les pannes avant qu’elles ne se produisent. Par exemple, des capteurs de température et de vibrations pourront analyser les moteurs des pistolets de poudrage ou les convoyeurs et envoyer des alertes lorsque des signes de dégradation sont détectés. Cette capacité à prévoir les défaillances permettra non seulement de maintenir la production en continu, mais aussi de prolonger la durée de vie des équipements, réduisant ainsi les coûts de maintenance et d’achat de nouvelles pièces.
Les chaînes de poudrage deviendront de plus en plus intégrées au sein de chaînes de production globales et interconnectées. L’utilisation de technologies telles que la blockchain pour garantir la traçabilité des produits sera de plus en plus courante. Cela offrira une plus grande transparence et une meilleure gestion des processus, car chaque étape de production, depuis l’application de la poudre jusqu’au durcissement, sera enregistrée et vérifiable. Cette capacité à assurer la traçabilité des matériaux, des produits et des processus améliorera non seulement la conformité réglementaire, mais aussi la confiance des clients en garantissant la qualité des produits finis.
À mesure que les systèmes de poudrage s’intègrent davantage dans des environnements de production globalement connectés, l’interopérabilité des équipements et des systèmes deviendra essentielle. Les plateformes numériques et les outils de gestion intégrée permettront aux entreprises de synchroniser leur production à l’échelle mondiale, de coordonner les opérations de poudrage avec d’autres procédés de fabrication (comme le moulage ou l’assemblage), et d’optimiser l’ensemble de la chaîne de valeur, de la production des matières premières à la distribution des produits finis.
En conclusion, les systèmes de poudrage continueront d’évoluer dans le cadre d’une révolution industrielle marquée par l’innovation technologique, la personnalisation des produits, et une prise de conscience accrue des enjeux environnementaux. Ces systèmes offriront des solutions plus flexibles, plus rapides et plus écologiques, tout en garantissant une qualité constante et des coûts réduits. L’adoption de technologies avancées comme l’intelligence artificielle, la robotique et l’IoT changera la manière dont les entreprises abordent la production, tout en renforçant leur compétitivité sur des marchés mondiaux de plus en plus exigeants.
Ligne Thermolaquage
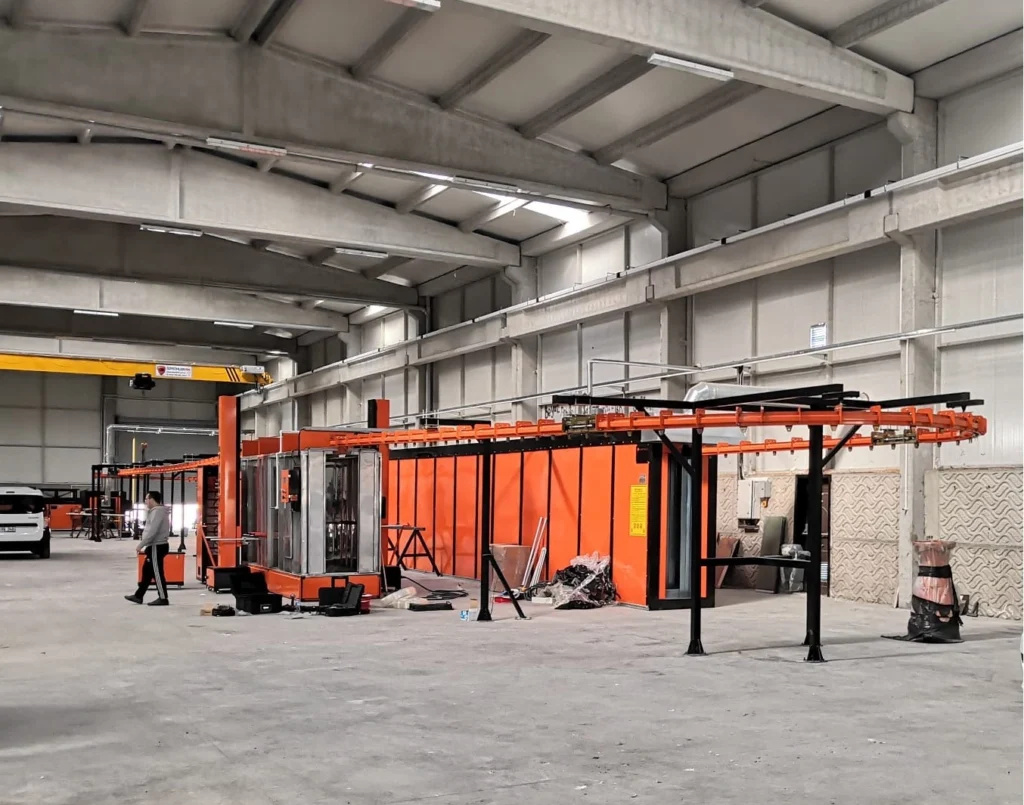
Une ligne de thermolaquage est un système automatisé conçu pour appliquer des revêtements en poudre (thermolaquage) sur des surfaces métalliques ou autres matériaux, dans le but de les protéger et de leur donner une finition esthétique durable. Ce procédé est largement utilisé dans diverses industries telles que l’automobile, l’électroménager, l’ameublement métallique, les constructions métalliques et bien d’autres secteurs où la qualité de la finition est essentielle. Le thermolaquage est une alternative respectueuse de l’environnement par rapport à la peinture liquide traditionnelle, en raison de l’absence de solvants et d’une consommation d’énergie plus faible.
Fonctionnement de la ligne de thermolaquage
Une ligne de thermolaquage se compose de plusieurs étapes, allant du nettoyage des pièces à la finition par cuisson. Le processus commence par la préparation des pièces à traiter. Cela inclut le nettoyage et la dégraissage des pièces métalliques afin d’éliminer les impuretés comme la rouille, les huiles ou les graisses, qui pourraient empêcher l’adhérence de la poudre. Cette étape est cruciale pour garantir la qualité du revêtement final. Les méthodes de nettoyage comprennent généralement des bains chimiques, du sablage, ou des jets de haute pression, selon le type de surface et le niveau de contamination.
Une fois les pièces nettoyées, elles sont séchées et envoyées vers la cabine de thermolaquage, où le revêtement en poudre est appliqué. Ce revêtement est composé de résines thermodurcissables, qui fondent sous l’effet de la chaleur pour créer une finition dure et résistante. L’application de la poudre se fait généralement par pulvérisation électrostatique. Dans ce processus, des pistolets de pulvérisation chargent électriquement les particules de poudre, qui s’attachent à la surface des pièces métalliques également chargées, assurant ainsi une couverture uniforme. Ce système électrostatique permet d’obtenir une finition de haute qualité, sans gaspillage de matériau, car la poudre excédentaire peut être récupérée et réutilisée.
L’une des caractéristiques du thermolaquage est la possibilité de recouvrir des pièces de formes complexes ou de surfaces irrégulières. L’adaptabilité des pistolets de pulvérisation et la capacité à ajuster l’intensité de la charge électrostatique permettent d’atteindre une couverture uniforme sur des pièces difficiles à traiter. Cette capacité de contrôle précis est un des atouts majeurs du thermolaquage, qui offre une finition de qualité supérieure, même sur des géométries complexes.
Cuisson et durcissement
Une fois la poudre appliquée, les pièces doivent être durcies dans un four de cuisson. Ce four est essentiel pour polymériser la poudre, c’est-à-dire la faire fondre et la faire adhérer de manière permanente à la surface des pièces. La température du four est généralement réglée entre 180 et 200°C, selon le type de poudre utilisée. La durée de la cuisson varie en fonction de la taille des pièces, de leur épaisseur et des spécifications du fabricant, mais elle dure généralement entre 15 et 30 minutes. La cuisson permet au revêtement en poudre de durcir et de former une couche lisse, durable et résistante aux abrasions, aux chocs et aux intempéries.
Le processus de cuisson est également une étape clé pour garantir une finition uniforme et de qualité. La température, le temps et la circulation de l’air dans le four doivent être rigoureusement contrôlés pour éviter les défauts, tels que les zones mal recouvertes, les bulles d’air ou les irrégularités dans le revêtement. Les fours modernes sont dotés de systèmes de contrôle numérique et de surveillance thermique, qui ajustent automatiquement la température pour garantir une cuisson homogène des pièces et une qualité constante du revêtement.
Avantages du thermolaquage
L’un des avantages majeurs du thermolaquage est sa durabilité. Les revêtements en poudre sont beaucoup plus résistants aux conditions environnementales que les peintures liquides. En effet, le thermolaquage offre une meilleure résistance aux rayures, à l’humidité, aux produits chimiques, aux UV et aux conditions climatiques extrêmes. Cela en fait un choix idéal pour les pièces exposées à des conditions difficiles, comme les pièces automobiles, les structures métalliques extérieures, ou les équipements industriels.
De plus, le thermolaquage est plus écologique que les peintures traditionnelles, car il ne nécessite pas de solvants et émet moins de COV (composés organiques volatils), ce qui le rend conforme aux normes environnementales strictes. L’absence de solvants réduit également les risques pour la santé des opérateurs. La poudre excédentaire peut être récupérée et réutilisée grâce à des systèmes de collecte sophistiqués, ce qui permet de minimiser les déchets et de réduire les coûts de production.
Le thermolaquage offre également une grande diversité de finitions. La poudre utilisée peut être formulée pour obtenir une large gamme de textures, allant des finitions mates aux brillantes, en passant par des textures spéciales comme l’effet sablé, métallisé ou hammertone (effet martelé). Ces finitions sont non seulement esthétiques, mais elles améliorent également les propriétés techniques du produit, en fonction des exigences spécifiques de chaque application.
Flexibilité et automatisation des lignes de thermolaquage
Les lignes de thermolaquage modernes sont hautement automatisées, ce qui leur permet de traiter de grandes quantités de pièces de manière rapide et efficace. L’automatisation garantit également une précision constante dans l’application du revêtement. Les robots de pulvérisation sont souvent utilisés pour assurer une application uniforme et optimale de la poudre, en particulier sur des pièces complexes ou de grande taille. Ces robots peuvent être programmés pour s’adapter à différents types de pièces, ajustant automatiquement la pression de pulvérisation, l’intensité de la charge électrostatique et la distance entre le pistolet et la surface pour garantir la meilleure couverture possible.
Les systèmes de contrôle intelligents intégrés dans les lignes de thermolaquage surveillent en temps réel les paramètres de production, tels que la température du four, la quantité de poudre utilisée, et l’humidité de l’air dans la cabine de pulvérisation. Ces systèmes peuvent effectuer des ajustements automatiquement pour optimiser le processus et garantir une qualité constante des pièces traitées.
Les lignes de thermolaquage modernes peuvent également être configurées pour être modulaires et flexibles, permettant aux entreprises de s’adapter à différents types de production. Par exemple, une ligne de thermolaquage peut être configurée pour des productions à grande échelle ou pour des petites séries, avec une capacité de changement rapide entre les différents types de pièces ou de finitions.
Maintenance et optimisation des performances
Une maintenance régulière des équipements est cruciale pour garantir le bon fonctionnement d’une ligne de thermolaquage. Les principaux éléments à entretenir incluent les pistolets de pulvérisation, les systèmes de filtration de l’air, les convoyeurs et le four de cuisson. Les pistolets de pulvérisation doivent être nettoyés régulièrement pour éviter l’encrassement et garantir une application uniforme de la poudre. Les systèmes de filtration de l’air doivent être vérifiés pour s’assurer qu’ils fonctionnent efficacement et qu’ils n’introduisent pas de particules de poussière dans la cabine de pulvérisation.
Les fours de cuisson, quant à eux, nécessitent un entretien régulier des éléments chauffants et des capteurs de température pour garantir une cuisson homogène des pièces. Une surveillance continue de la température et de l’humidité dans le four est essentielle pour éviter toute variation qui pourrait affecter la qualité du revêtement.
Enfin, des logiciels de gestion de maintenance assistée par ordinateur (GMAO) sont de plus en plus utilisés pour suivre l’état des équipements et planifier les opérations de maintenance préventive. Cela permet de réduire les risques de panne, d’améliorer la disponibilité des équipements et de prolonger la durée de vie des installations.
Perspectives d’avenir
L’avenir des lignes de thermolaquage repose sur l’intégration de technologies avancées, telles que l’intelligence artificielle, l’Internet des objets (IoT), et la robotique avancée. Ces technologies permettront d’améliorer encore l’automatisation, la personnalisation et la gestion des processus. Par exemple, l’utilisation de capteurs IoT pour suivre en temps réel l’état des équipements permettra de mieux prédire les besoins en maintenance et d’optimiser les performances de la ligne.
Les lignes de thermolaquage seront également de plus en plus écologiques, avec des systèmes de récupération de chaleur plus performants et des technologies de recyclage des matériaux de revêtement de plus en plus avancées. L’utilisation de poudres plus durables, fabriquées à partir de matériaux recyclés ou biosourcés, continuera de croître, répondant ainsi aux exigences environnementales croissantes des consommateurs et des régulateurs.
En conclusion, les lignes de thermolaquage continueront de jouer un rôle essentiel dans la production de pièces métalliques de haute qualité, en offrant des solutions de revêtement durables, esthétiques et respectueuses de l’environnement. Grâce à l’innovation technologique, à l’automatisation accrue et à l’amélioration continue des procédés, elles deviendront plus efficaces, flexibles et écologiques, répondant ainsi aux exigences des industries modernes.
Les lignes de thermolaquage se développeront encore davantage avec l’introduction de technologies de pointe, intégrant des processus automatisés plus sophistiqués, une gestion de la production en temps réel et des systèmes intelligents permettant une optimisation continue. La numérisation des lignes permettra un contrôle plus précis des paramètres de production, en surveillant les conditions environnementales, la qualité de l’application de la poudre, et la performance des équipements. L’intégration de l’intelligence artificielle dans les systèmes de thermolaquage pourrait permettre des ajustements instantanés en fonction de l’analyse des données, garantissant ainsi des performances optimales et une qualité constante.
L’une des prochaines étapes pour l’évolution de ces systèmes sera l’adoption de solutions de maintenance prédictive. En surveillant en permanence les conditions des équipements et en analysant les données recueillies par des capteurs intelligents, les entreprises pourront anticiper les défaillances avant qu’elles ne surviennent. Cela pourrait significativement réduire les temps d’arrêt et les coûts de maintenance, tout en prolongeant la durée de vie des composants critiques des lignes de thermolaquage.
Les innovations dans la gestion énergétique continueront de façonner l’avenir du thermolaquage. Les entreprises chercheront à réduire encore leur consommation d’énergie, en optimisant l’efficacité des systèmes de chauffage du four et en adoptant des technologies de récupération thermique plus avancées. L’objectif sera de limiter l’empreinte carbone tout en maintenant des performances élevées. Cela pourrait inclure des avancées dans les systèmes de chauffage à haute efficacité et l’intégration d’énergies renouvelables dans les processus de production, contribuant ainsi à une approche plus verte et durable de la finition des produits.
Les progrès dans la recherche de nouvelles formulations de poudre pourraient également jouer un rôle clé dans l’avenir du thermolaquage. Les poudres utilisées aujourd’hui, bien que déjà performantes, continueront de se perfectionner pour répondre à des critères de plus en plus stricts en termes de résistance, d’esthétique et de respect de l’environnement. Par exemple, des poudres plus résistantes aux rayons UV, à la corrosion ou aux produits chimiques agressifs trouveront leur place dans des applications de plus en plus diverses, allant de l’électronique à la construction. Les recherches permettront également d’améliorer la compatibilité des poudres avec différents types de matériaux et de surfaces, tout en respectant des normes environnementales plus strictes.
L’essor des lignes de thermolaquage se traduira également par des systèmes plus flexibles et adaptés aux besoins de personnalisation. Dans un environnement de production de plus en plus exigeant, la capacité à traiter des petites séries avec des variations de finition spécifiques sera un atout précieux. Les systèmes de thermolaquage devront pouvoir s’adapter rapidement aux variations de produit, de couleur ou de texture, sans sacrifier la productivité. L’intégration de solutions modulaires, où les différentes étapes du processus peuvent être ajustées facilement en fonction des demandes du marché, deviendra un impératif pour répondre aux exigences croissantes des consommateurs et des industries.
La flexibilité accrue des lignes de thermolaquage se traduira par des changements dans la gestion des stocks et des flux de production. En permettant un ajustement rapide aux besoins de la production, ces lignes permettront de mieux répondre aux demandes fluctuantes du marché, d’optimiser les délais de livraison et de réduire les coûts de stockage. Les nouvelles technologies, comme les systèmes de gestion de production basés sur le cloud et l’Internet des objets (IoT), faciliteront la coordination entre les différentes étapes de la fabrication, permettant aux entreprises de suivre en temps réel les stocks de matière première et les pièces en cours de traitement.
Les lignes de thermolaquage continueront à se perfectionner pour répondre aux besoins croissants d’industries soucieuses de respecter des normes environnementales strictes. En plus de réduire l’utilisation de solvants et d’émettre moins de COV, les systèmes de thermolaquage deviendront de plus en plus efficaces dans la gestion des déchets. La collecte et la réutilisation de la poudre excédentaire seront optimisées, et des systèmes de filtration plus performants permettront de garantir une qualité de finition optimale tout en minimisant les pertes. Cette démarche s’inscrit dans une tendance plus large visant à rendre les processus industriels plus écologiques, tout en maintenant une rentabilité élevée.
De plus, la demande croissante pour des solutions de finition durable et esthétiquement variée dans de nombreux secteurs tels que l’automobile, l’électroménager et la construction, va stimuler le développement de nouvelles textures et finitions. Le thermolaquage, grâce à sa polyvalence, continuera de se diversifier pour offrir des finitions métallisées, satinées, texturées, ou même holographiques, en fonction des besoins spécifiques des marchés. Les possibilités seront presque illimitées en termes de personnalisation des produits, et la ligne de thermolaquage sera essentielle pour produire ces finitions avec une haute précision et une efficacité maximale.
L’avenir des lignes de thermolaquage sera également marqué par une collaboration accrue entre les fabricants d’équipements et les utilisateurs finaux. Les entreprises pourront travailler en partenariat pour développer des solutions de finition sur mesure qui répondent à des besoins spécifiques tout en restant compétitives sur le plan des coûts et de la performance. Cette collaboration rapprochée permettra d’identifier rapidement les défis techniques et d’apporter des améliorations continues aux systèmes, favorisant ainsi une production plus fluide et plus rentable.
Enfin, la traçabilité des processus deviendra un élément central dans les lignes de thermolaquage. L’implémentation de technologies comme la blockchain permettra d’assurer une transparence totale tout au long de la chaîne de production, depuis l’application de la poudre jusqu’à la cuisson des pièces. Cela garantira non seulement la qualité du produit fini, mais aussi la conformité aux normes de sécurité et aux exigences des clients. Grâce à des bases de données centralisées et à l’analyse des données de production, il sera plus facile d’assurer un suivi précis des pièces et de garantir une gestion plus efficace des ressources.
En résumé, l’évolution des lignes de thermolaquage se caractérisera par l’intégration de technologies innovantes qui amélioreront l’efficacité, la flexibilité et la durabilité du processus. Les systèmes de thermolaquage deviendront plus intelligents, écologiques et réactifs, permettant de répondre à des exigences de production toujours plus complexes. Grâce à des avancées dans les matériaux, les technologies de production et la gestion de la qualité, ces lignes continueront de jouer un rôle clé dans de nombreuses industries, offrant des solutions de finition de haute qualité, durables et personnalisées.
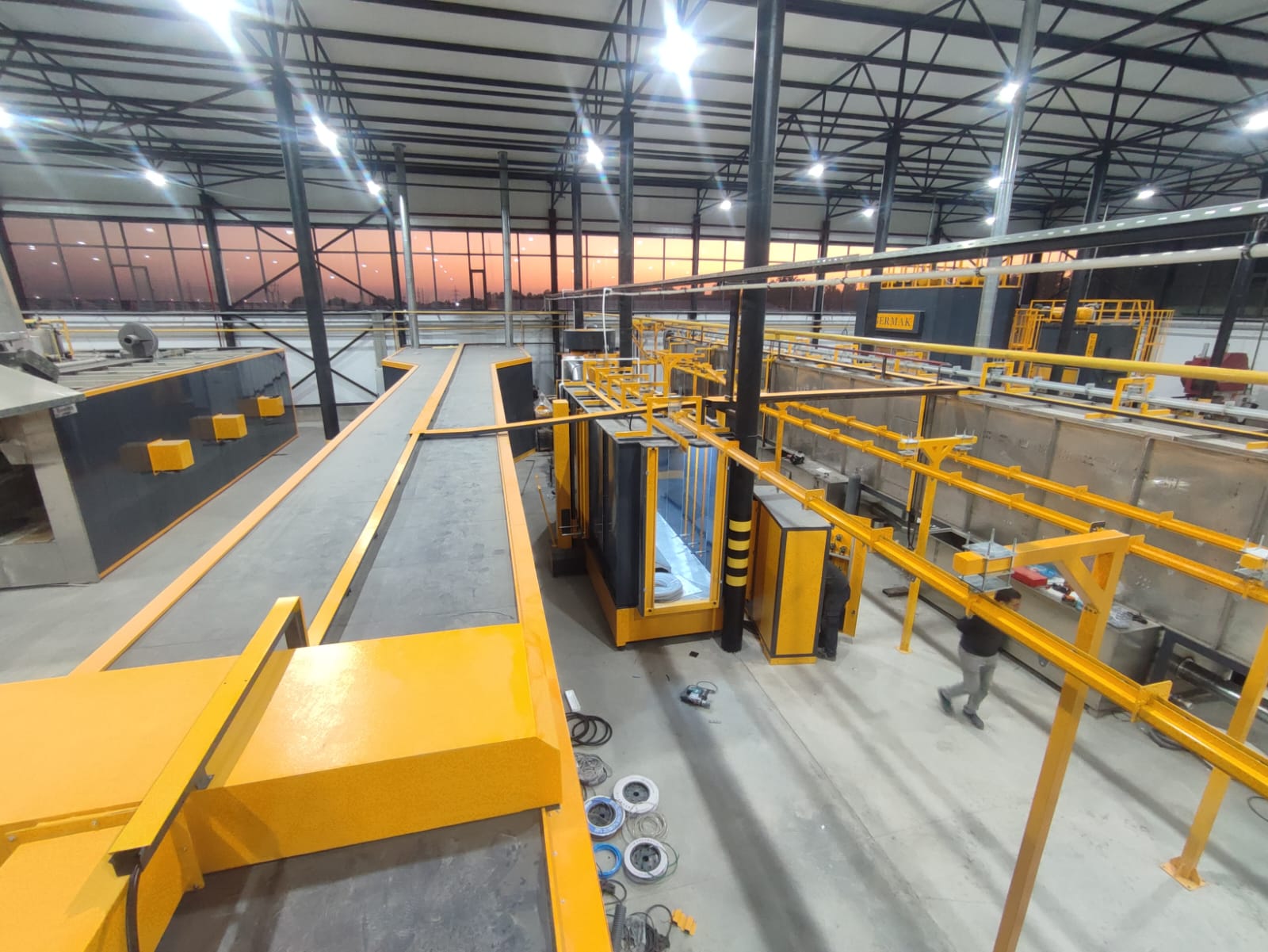
Le développement des lignes de thermolaquage s’accompagnera également d’une amélioration de l’ergonomie et de la sécurité des opérateurs. Les avancées technologiques permettront de réduire l’intervention humaine dans les phases les plus dangereuses du processus, comme la manipulation de matériaux ou le contrôle des équipements dans des environnements à haute température. L’automatisation avancée des lignes permettra de minimiser les risques liés aux expositions à des produits chimiques ou à des conditions de chaleur extrêmes. Par ailleurs, des capteurs de sécurité et des dispositifs de surveillance permettront de détecter rapidement toute anomalie dans les équipements, garantissant ainsi la sécurité des employés et la continuité des opérations.
Les lignes de thermolaquage seront également de plus en plus intégrées dans des environnements de production intelligents. En combinant des systèmes de gestion de la production basés sur l’IoT et des outils d’analyse de données avancées, les processus de thermolaquage pourront être supervisés de manière plus proactive. La collecte de données en temps réel à partir de l’ensemble de la chaîne de production, y compris des capteurs intégrés dans les pistolets de pulvérisation, les fours de cuisson et les systèmes de ventilation, permettra d’optimiser en permanence les paramètres de fonctionnement. Ces données permettront aussi de mieux comprendre les tendances de consommation de la poudre et de l’énergie, d’identifier les inefficacités et d’apporter des ajustements pour réduire les coûts.
Les interactions entre les lignes de thermolaquage et d’autres systèmes de production, comme les lignes d’assemblage ou de prétraitement, deviendront plus fluides grâce à l’adoption des technologies de l’industrie 4.0. L’intégration de robots collaboratifs (cobots) et de systèmes de transport automatisés au sein des lignes de thermolaquage rendra le processus de finition plus flexible et plus réactif aux besoins de production. Ces systèmes intelligents pourront ajuster les flux de production en fonction des priorités et des demandes du marché, réduisant ainsi les délais de fabrication et améliorant l’efficacité globale du processus.
Une autre tendance importante dans l’évolution des lignes de thermolaquage est la capacité à personnaliser les produits en fonction des spécifications exactes des clients. Cela est particulièrement pertinent dans des secteurs comme l’automobile, où les consommateurs recherchent des finitions de plus en plus uniques. Les lignes de thermolaquage seront capables de gérer une gamme plus large de couleurs, textures et effets visuels tout en maintenant une qualité constante et un processus de production rapide. De plus, grâce à l’automatisation avancée et aux logiciels de gestion de la production, il sera possible de traiter des petites séries ou des séries personnalisées avec la même efficacité que pour des productions à grande échelle.
Les applications de thermolaquage ne se limiteront plus uniquement aux produits métalliques classiques. À mesure que de nouveaux matériaux, tels que les plastiques renforcés ou composites, gagnent en popularité, les lignes de thermolaquage devront s’adapter pour traiter ces matériaux. Cela nécessitera l’introduction de nouvelles technologies de pulvérisation, de température et de gestion thermique, afin d’assurer une finition de haute qualité même sur des matériaux qui ne sont pas traditionnellement utilisés pour le thermolaquage. L’extension des capacités des lignes de thermolaquage vers ces nouveaux types de matériaux offrira des possibilités accrues pour divers secteurs d’activité, notamment l’aérospatial, les industries de l’énergie et la construction.
La gestion des émissions et des impacts environnementaux continuera de jouer un rôle central dans l’évolution des lignes de thermolaquage. L’intensification de la réglementation en matière d’environnement pousse les fabricants à investir dans des technologies propres et des procédés à faible émission de carbone. Cela comprend l’optimisation de la consommation d’énergie, l’utilisation de matériaux recyclables, ainsi que des solutions permettant de récupérer et de traiter les émissions de gaz dans le four de cuisson. Les systèmes de filtration de l’air deviendront de plus en plus sophistiqués, avec des filtres et des technologies de purification qui permettront de réduire encore davantage les émissions et de garantir un environnement de travail plus sûr et plus propre.
Les entreprises continueront à rechercher des lignes de thermolaquage plus efficaces en termes de coûts et de ressources, afin de rester compétitives tout en répondant aux normes de qualité de plus en plus exigeantes. Cela impliquera l’utilisation de méthodes de production à faible coût et à haute efficacité énergétique, ainsi que l’amélioration de la gestion des déchets. De nouvelles techniques de gestion de la poudre excédentaire et des systèmes de recyclage plus avancés permettront de réduire les coûts de matériaux et d’optimiser l’utilisation des ressources.
À l’avenir, les lignes de thermolaquage auront également la possibilité de s’adapter aux changements dans les préférences des consommateurs, notamment en matière de conception de produits. Les consommateurs sont de plus en plus exigeants en matière de durabilité, d’esthétique et de personnalisation. Les lignes de thermolaquage devront donc offrir des solutions plus flexibles, capables de répondre à une demande croissante de produits uniques, tout en maintenant des délais de production courts. La capacité à personnaliser des produits en fonction des tendances de consommation, tout en minimisant l’impact environnemental, deviendra un avantage compétitif majeur.
En conclusion, l’avenir des lignes de thermolaquage sera marqué par une convergence de technologies avancées, visant à améliorer l’efficacité, la durabilité et la flexibilité du processus. Grâce à des innovations continues dans la robotique, l’automatisation, la numérisation et les matériaux, ces systèmes deviendront des éléments clés dans des processus de fabrication de plus en plus personnalisés, durables et écologiques. L’intégration de solutions intelligentes permettra d’optimiser la production tout en réduisant les coûts et en répondant aux attentes des consommateurs. Ces lignes, à la pointe de la technologie, continueront de jouer un rôle central dans des secteurs variés, offrant des solutions de finition de haute qualité et contribuant à des processus industriels plus verts et plus performants.
Ligne de Poudrage
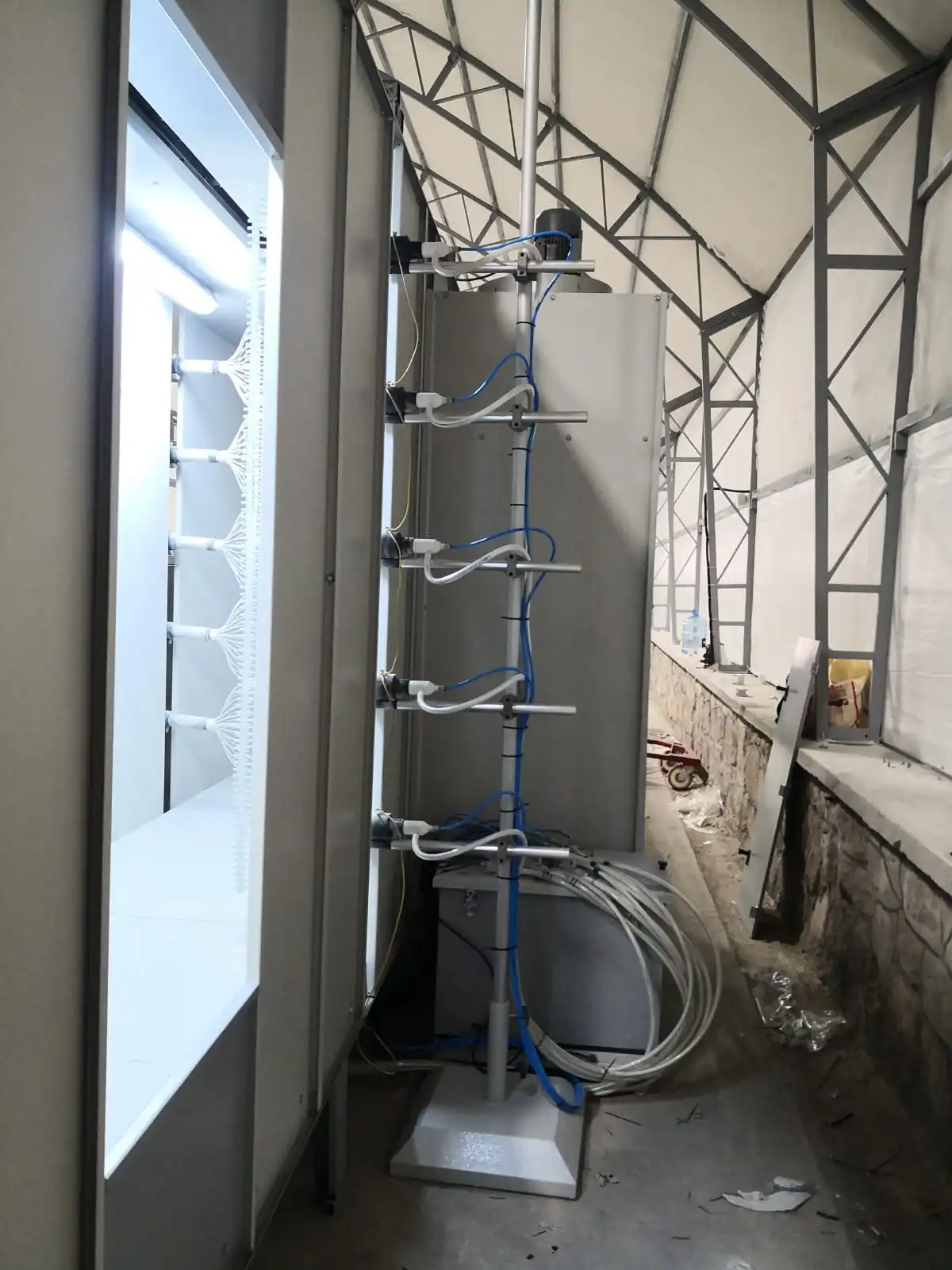
Une ligne de poudrage est un système automatisé conçu pour appliquer un revêtement en poudre sur des pièces métalliques ou autres matériaux dans le but d’obtenir une finition uniforme, esthétique et durable. Ce procédé est utilisé dans diverses industries, telles que l’automobile, l’électroménager, l’ameublement métallique et bien d’autres secteurs nécessitant des surfaces protégées contre l’usure, la corrosion ou les conditions climatiques extrêmes. Le poudrage est une méthode de finition largement prisée en raison de sa qualité de revêtement élevée, de son respect de l’environnement et de son efficacité.
Le fonctionnement d’une ligne de poudrage commence par la préparation des pièces à traiter. Avant d’appliquer la poudre, les pièces doivent être soigneusement nettoyées pour éliminer toute saleté, huile, rouille ou autres contaminants susceptibles d’empêcher l’adhérence du revêtement. Le nettoyage est généralement réalisé par des techniques telles que le sablage, le nettoyage chimique ou les jets de haute pression. Après cette étape, les pièces sont séchées avant d’être envoyées vers la cabine de poudrage.
Dans la cabine de poudrage, la poudre est appliquée sur les pièces à l’aide de pistolets de pulvérisation. Ces pistolets utilisent souvent une technologie de pulvérisation électrostatique, où la poudre est chargée électriquement et attire les pièces également chargées. Ce système électrostatique garantit une couverture uniforme et une adhérence optimale de la poudre sur la surface des pièces, ce qui permet d’obtenir un revêtement de haute qualité sans gaspillage de matériau. L’un des avantages de la pulvérisation électrostatique est qu’elle permet de traiter des pièces de formes irrégulières ou complexes en assurant une couverture uniforme, même dans les zones difficiles à atteindre.
Une fois la poudre appliquée, les pièces doivent être durcies dans un four de cuisson pour que la poudre fonde et adhère de manière permanente à la surface. La température du four est généralement comprise entre 180 et 200°C, et la durée de la cuisson varie selon la taille des pièces et le type de poudre utilisée, mais elle dure habituellement entre 15 et 30 minutes. Ce processus permet de former une finition lisse et résistante aux rayures, à la corrosion, aux produits chimiques et aux conditions climatiques extrêmes.
Le poudrage présente de nombreux avantages par rapport aux méthodes traditionnelles de peinture liquide. L’un des principaux avantages est qu’il ne nécessite pas de solvants, ce qui en fait un procédé plus respectueux de l’environnement. En l’absence de solvants, les émissions de composés organiques volatils (COV) sont considérablement réduites, ce qui permet de respecter des normes environnementales strictes. De plus, la poudre excédentaire peut être récupérée et réutilisée, ce qui permet de minimiser le gaspillage et de réduire les coûts de production.
Un autre avantage du poudrage est sa durabilité. Les revêtements en poudre sont particulièrement résistants aux rayures, aux chocs, aux UV, à l’humidité et à la corrosion. Cela en fait une solution idéale pour les pièces qui doivent résister à des conditions difficiles, telles que les équipements extérieurs, les pièces automobiles ou les composants industriels. Le revêtement en poudre est également plus épais que la peinture liquide, ce qui renforce la protection des pièces.
Le processus de poudrage offre également une grande flexibilité en termes de finitions. Les poudres sont disponibles dans une large gamme de couleurs, de textures et d’effets, allant des finitions mates aux brillantes, métalliques, texturées ou même transparentes. Cette flexibilité permet de répondre aux besoins spécifiques des clients en matière de design et de finition, tout en maintenant une performance technique élevée. De plus, le poudrage permet d’obtenir des surfaces lisses et uniformes sans les coulures ou les défauts souvent associés à la peinture liquide.
Les lignes de poudrage modernes sont équipées de systèmes automatisés avancés, permettant de traiter une grande quantité de pièces de manière rapide et efficace. Ces systèmes sont souvent dotés de robots de pulvérisation qui appliquent la poudre de manière uniforme et précise sur les pièces. Les robots sont programmés pour ajuster la pression de pulvérisation, l’intensité de la charge électrostatique et la distance entre la buse et la pièce, en fonction de la forme et des caractéristiques de la surface à traiter. Cela garantit une application optimale du revêtement, même sur des pièces de grande taille ou de formes complexes.
L’automatisation de la ligne de poudrage améliore non seulement la qualité du revêtement, mais permet également d’augmenter la productivité en réduisant les temps de cycle et en minimisant les erreurs humaines. En utilisant des systèmes de gestion avancés, les lignes de poudrage peuvent suivre les pièces tout au long du processus, du nettoyage à la cuisson, en garantissant une traçabilité complète et une gestion optimale des ressources.
Une autre caractéristique importante des lignes de poudrage modernes est leur capacité à s’adapter à différents types de produits et à répondre à des exigences de production variées. Les lignes de poudrage peuvent être configurées pour traiter des petites séries ou des productions à grande échelle. En fonction des besoins, elles peuvent être équipées de stations de nettoyage modulaires, de pistolets de pulvérisation interchangeables et de systèmes de cuisson flexibles. Cette adaptabilité permet de répondre aux demandes des industries qui nécessitent des volumes de production importants ainsi que des personnalisations spécifiques.
La maintenance des lignes de poudrage est également un élément clé pour garantir leur performance et leur durabilité. Les composants des lignes, tels que les pistolets de pulvérisation, les systèmes de filtration et les convoyeurs, doivent être entretenus régulièrement pour éviter les pannes et assurer un fonctionnement optimal. Les systèmes de contrôle intelligents, qui surveillent en temps réel les conditions de production, permettent de détecter rapidement toute anomalie et de prévenir les dysfonctionnements, minimisant ainsi les interruptions et les coûts de maintenance.
En ce qui concerne l’avenir des lignes de poudrage, plusieurs tendances se dessinent. L’un des principaux domaines d’innovation est l’intégration de technologies avancées, telles que l’intelligence artificielle, la robotique et l’Internet des objets (IoT). Ces technologies permettront d’améliorer l’automatisation des lignes de poudrage, de rendre les systèmes plus réactifs aux changements de production et d’optimiser les processus en temps réel. L’utilisation de robots collaboratifs (cobots) et de capteurs intelligents permettra de créer des lignes de poudrage encore plus flexibles, capables de s’adapter à des produits de tailles et de formes variées, tout en maintenant un haut niveau de qualité.
Une autre tendance importante est l’optimisation de la consommation énergétique des lignes de poudrage. Les fabricants cherchent à rendre les procédés plus efficaces, en particulier en ce qui concerne les systèmes de chauffage du four de cuisson. L’amélioration de l’efficacité énergétique contribuera non seulement à réduire les coûts de production, mais aussi à limiter l’empreinte carbone des lignes de poudrage. L’intégration de solutions de récupération thermique et de gestion énergétique intelligente permettra d’optimiser les coûts tout en respectant les normes environnementales de plus en plus strictes.
Enfin, la demande pour des revêtements de plus en plus durables et respectueux de l’environnement continuera de croître. Les lignes de poudrage évolueront pour utiliser des poudres plus écologiques, fabriquées à partir de matériaux recyclés ou biosourcés. Ces poudres offriront des performances similaires ou supérieures à celles des poudres traditionnelles, tout en répondant aux attentes croissantes des consommateurs et des régulateurs en matière de développement durable.
En conclusion, les lignes de poudrage sont essentielles pour la production de pièces avec des finitions de haute qualité, durables et esthétiques. Avec l’adoption de technologies avancées, l’automatisation accrue et l’amélioration continue des procédés, ces lignes deviendront plus efficaces, flexibles et écologiques. Elles continueront de répondre aux besoins des industries modernes, offrant des solutions de finition performantes tout en respectant des normes environnementales strictes.
L’évolution des lignes de poudrage se dirigera également vers une intégration plus poussée de la numérisation et des outils de gestion de la production basés sur l’intelligence artificielle (IA) et l’analyse de données. Ces technologies permettront aux lignes de poudrage de devenir encore plus autonomes et réactives aux besoins de production, en ajustant automatiquement les paramètres tels que la vitesse de la ligne, l’application de la poudre et la cuisson en fonction des données en temps réel. Cela contribuera à réduire les erreurs humaines et à optimiser les processus, en s’assurant que chaque pièce est traitée de manière optimale.
L’utilisation de l’intelligence artificielle dans les lignes de poudrage peut également permettre de prédire et d’anticiper les besoins de maintenance. En analysant les données des capteurs installés sur les différents équipements de la ligne, l’IA peut identifier des signes précoces de défaillance et recommander des actions préventives. Cette maintenance prédictive permet non seulement de réduire les temps d’arrêt mais aussi de prolonger la durée de vie des équipements. La maintenance en temps réel est un avantage important pour minimiser les coûts et garantir une production continue sans interruptions non planifiées.
Une autre évolution majeure des lignes de poudrage concerne la personnalisation et la flexibilité accrues qu’elles offriront. L’adoption de processus modulaires, où des unités spécifiques (comme les stations de poudrage, les systèmes de cuisson ou de filtration) peuvent être ajoutées ou modifiées selon les besoins de production, permettra aux fabricants de mieux s’adapter aux demandes changeantes du marché. En fonction des commandes, il sera possible de configurer rapidement les lignes pour produire différentes finitions, de tailles variées, ou même des séries limitées de produits. Cette flexibilité sera un atout majeur pour répondre aux attentes des consommateurs modernes, notamment dans des secteurs comme l’automobile ou le design d’intérieur, où la personnalisation et l’innovation sont des critères clés.
Le recyclage de la poudre excédentaire, déjà un avantage du poudrage, deviendra encore plus sophistiqué avec les nouvelles technologies de récupération et de gestion des matériaux. Des systèmes de récupération automatisés permettront de collecter la poudre excédentaire sans risque de contamination, et de la réutiliser pour la production, réduisant ainsi le gaspillage et optimisant les coûts. Les lignes de poudrage seront également équipées de systèmes de filtration de plus en plus performants, capables de capturer même les particules les plus fines, garantissant une qualité constante et réduisant l’impact environnemental du processus.
En parallèle, l’optimisation des consommations d’énergie dans les lignes de poudrage continuera de progresser. En plus des améliorations des fours de cuisson, les technologies de chauffage à haute efficacité, l’optimisation des circuits de ventilation et de la gestion de la chaleur permettront de réduire la consommation d’énergie de manière significative. Les solutions de récupération de chaleur, comme les échangeurs thermiques ou les systèmes de recyclage de chaleur, contribueront à une utilisation plus économique de l’énergie et à une réduction des coûts opérationnels. Cette tendance vers des lignes de poudrage plus écologiques et économes en énergie correspond aux préoccupations croissantes concernant le changement climatique et la nécessité de rendre les processus industriels plus durables.
Le développement des lignes de poudrage va également se concentrer sur l’amélioration de l’expérience utilisateur pour les opérateurs et les gestionnaires de production. Les interfaces de contrôle deviendront plus intuitives, offrant des outils de gestion visuels et interactifs, et permettant aux opérateurs de suivre l’ensemble du processus de production en temps réel. Les tableaux de bord numériques, associés à des logiciels de gestion, permettront de superviser les performances, de détecter les anomalies et de prendre des décisions éclairées pour optimiser la production. Ces améliorations rendront les opérations plus transparentes et permettront de réagir rapidement aux problèmes.
Les matériaux et les poudres utilisées dans les lignes de poudrage continueront à évoluer pour répondre à des exigences toujours plus strictes en matière de performance et de respect de l’environnement. Des recherches sont en cours pour développer des poudres qui soient à la fois plus résistantes, plus légères, plus durables et plus écologiques. Par exemple, des poudres biosourcées ou à base de matériaux recyclés pourraient se multiplier, offrant ainsi des solutions plus responsables sans sacrifier la qualité du produit fini. La recherche dans ce domaine permettra de concevoir des produits finis plus durables, résistants aux intempéries et aux conditions climatiques extrêmes, tout en étant plus faciles à appliquer.
Les exigences croissantes en matière de durabilité et de respect de l’environnement se traduiront également par une réglementation de plus en plus stricte sur les produits chimiques utilisés dans le processus de poudrage. Les lignes de poudrage devront s’adapter à des normes environnementales de plus en plus exigeantes, ce qui les poussera à utiliser des poudres à faible émission de COV et à gérer les déchets de manière plus efficace. Cela encouragera le développement de nouvelles technologies qui réduiront les émissions et amélioreront la gestion des produits chimiques, tout en permettant aux entreprises de maintenir des performances élevées.
En termes de diversification des applications, les lignes de poudrage trouveront de plus en plus de débouchés dans des secteurs innovants comme les énergies renouvelables, la construction durable et l’électronique. Les panneaux solaires, les éoliennes et les batteries, par exemple, bénéficient grandement des propriétés de protection offertes par le poudrage, qui améliore leur longévité et leur performance en les protégeant contre les éléments naturels. De plus, dans le domaine de l’électronique, les pièces métalliques et plastiques peuvent être protégées avec des revêtements en poudre qui offrent à la fois des propriétés de protection et une finition esthétique.
Les nouvelles applications dans des secteurs variés élargiront le champ d’utilisation des lignes de poudrage, augmentant ainsi la demande pour des systèmes plus flexibles, plus modulaires et capables de gérer des revêtements complexes et diversifiés. Cette évolution entraînera des investissements dans des technologies de pointe et dans la recherche et le développement de nouveaux matériaux et procédés.
En conclusion, l’avenir des lignes de poudrage s’annonce passionnant, marqué par des progrès significatifs dans l’automatisation, la numérisation et la durabilité. L’adoption de technologies avancées, telles que l’intelligence artificielle, la robotique et l’Internet des objets, permettra de rendre ces lignes plus efficaces, flexibles et respectueuses de l’environnement. Les innovations dans les matériaux, les procédés et la gestion de la production contribueront à améliorer la qualité des revêtements tout en réduisant les coûts et l’impact écologique. Les lignes de poudrage continueront à jouer un rôle clé dans la fabrication de produits finis de haute qualité et à répondre aux besoins de secteurs industriels de plus en plus diversifiés.
L’avenir des lignes de poudrage va également être marqué par un développement plus poussé de la connectivité et de l’intégration des systèmes. L’utilisation des technologies basées sur le cloud et des réseaux industriels permettra aux lignes de poudrage de fonctionner dans des environnements de production interconnectés. Cela facilitera la gestion des processus de manière centralisée et le partage de données en temps réel entre différents sites de production, créant ainsi une approche plus cohérente et synchronisée de la production à l’échelle mondiale. Ces systèmes permettront une gestion optimisée des stocks de poudre, une analyse continue des performances et une réduction des risques d’interruptions liées à des erreurs humaines ou des défaillances de processus.
En outre, avec l’essor de la fabrication additive (impression 3D), les lignes de poudrage pourraient trouver de nouvelles applications en tant que procédé de finition pour des objets fabriqués en 3D. Ce type de technologie est déjà utilisé dans certaines industries, comme l’aérospatiale ou l’automobile, où des composants complexes sont imprimés puis finis avec des revêtements en poudre pour en améliorer la résistance et l’aspect. L’intégration des lignes de poudrage avec des imprimantes 3D pourrait permettre de créer des solutions de finition plus rapides et plus efficaces pour des pièces plus complexes et sur mesure.
Le développement de nouvelles applications sera également influencé par les demandes croissantes des consommateurs pour des produits esthétiquement attractifs et techniquement performants. Par exemple, les industries du design de produits et de l’ameublement recherchent des finitions qui offrent non seulement une protection mais aussi des propriétés décoratives avancées. Les lignes de poudrage devront être capables de traiter des textures uniques, des couleurs personnalisées et des effets spéciaux, comme des finitions métalliques, nacrées ou chromées, pour répondre à ces attentes. La capacité à produire des revêtements à la fois fonctionnels et esthétiques augmentera la demande pour des lignes de poudrage capables d’offrir cette double performance.
Un autre facteur clé influençant l’évolution des lignes de poudrage sera la nécessité d’une gestion plus fine des résidus et des déchets issus du processus. La gestion des poussières et autres résidus, qui peut parfois être un défi dans les procédés de poudrage, sera améliorée grâce à des systèmes de filtration plus avancés. Ces systèmes, souvent dotés de filtres HEPA ou de technologies de purification de l’air, permettront de garantir que l’air dans les installations reste propre tout en récupérant la poudre excédentaire pour la réutilisation. En plus de réduire l’impact environnemental, ces systèmes permettront aux entreprises de réaliser des économies substantielles en réutilisant la poudre, contribuant ainsi à une gestion plus responsable des matériaux.
L’interaction avec les clients et la capacité à personnaliser les produits de manière encore plus dynamique est également un domaine dans lequel les lignes de poudrage se développeront. Les solutions de finition en poudre ne se limiteront plus à des revêtements standards, mais proposeront des solutions sur mesure, permettant aux clients de choisir la texture, la couleur, l’effet et même la résistance particulière de leurs produits. Des outils de simulation en temps réel permettront de prévisualiser les effets et de tester virtuellement les finitions avant leur application sur les pièces. Cette capacité à offrir une personnalisation à la fois esthétique et fonctionnelle positionnera les lignes de poudrage comme une solution incontournable pour les industries qui cherchent à répondre à des besoins spécifiques des consommateurs.
En parallèle, l’évolution vers des lignes de poudrage plus petites et plus modulaires deviendra de plus en plus courante. Ces solutions, plus accessibles et flexibles, permettront aux petites entreprises ou aux fabricants de niches de bénéficier des avantages du poudrage tout en réduisant les coûts d’investissement et les exigences d’espace. L’optimisation des coûts et l’amélioration de la flexibilité permettront de démocratiser l’accès à cette technologie, qui était autrefois réservée aux grandes productions industrielles. Les équipements modulaires permettront d’adapter les lignes de poudrage aux besoins spécifiques de chaque entreprise, que ce soit en termes de type de produit, de volume ou de variété de finition.
Dans le secteur des transports, les lignes de poudrage joueront un rôle clé dans la fabrication de composants automobiles, aérospatiaux et ferroviaires. Les pièces soumises à de fortes contraintes, comme celles utilisées dans les véhicules électriques, les moteurs d’avions ou les trains, bénéficieront grandement de la résistance et de la durabilité offertes par les revêtements en poudre. Les lignes de poudrage devront donc s’adapter à des besoins de plus en plus exigeants, en offrant des finitions capables de résister à des conditions extrêmes de chaleur, de pression, de corrosion et d’usure.
L’évolution des lignes de poudrage sera également influencée par les attentes grandissantes des consommateurs et des industriels en matière de durabilité et de réduction de l’empreinte carbone. L’adoption de pratiques de fabrication plus respectueuses de l’environnement, y compris l’utilisation de poudres fabriquées à partir de matériaux recyclés, continuera de croître. Cela encouragera les fabricants à adopter des technologies propres, à réduire les déchets et à recycler autant que possible les matériaux utilisés dans le processus. Les lignes de poudrage devront ainsi s’adapter pour intégrer des systèmes de gestion des déchets de plus en plus sophistiqués, permettant non seulement de réduire l’impact environnemental mais aussi d’améliorer l’efficacité et la rentabilité du processus.
Enfin, l’intégration d’outils de simulation numérique et de réalité augmentée pour la formation et la maintenance des opérateurs sera une autre évolution clé. Ces technologies permettront aux opérateurs de se former de manière plus interactive et immersive, tout en réduisant les risques d’erreurs humaines. La réalité augmentée pourra également être utilisée pour fournir un support en temps réel lors des processus de maintenance, guidant les techniciens dans les réparations et les réglages nécessaires, améliorant ainsi la productivité et réduisant le temps d’indisponibilité des lignes.
En conclusion, les lignes de poudrage continueront à se développer en parallèle avec l’évolution des technologies et des besoins industriels. L’automatisation, la numérisation et la durabilité seront au cœur de cette évolution, offrant des solutions plus efficaces, plus écologiques et plus flexibles. Les avancées dans la robotique, l’intelligence artificielle, la gestion des matériaux et la personnalisation permettront de répondre aux demandes croissantes pour des produits finis de haute qualité et à la fois esthétiques et fonctionnels. L’avenir des lignes de poudrage est prometteur et jouera un rôle clé dans la fabrication de produits industriels et de consommation respectueux de l’environnement, tout en offrant des solutions de finition de plus en plus sophistiquées.
Système automatique de récupération de la peinture en poudre
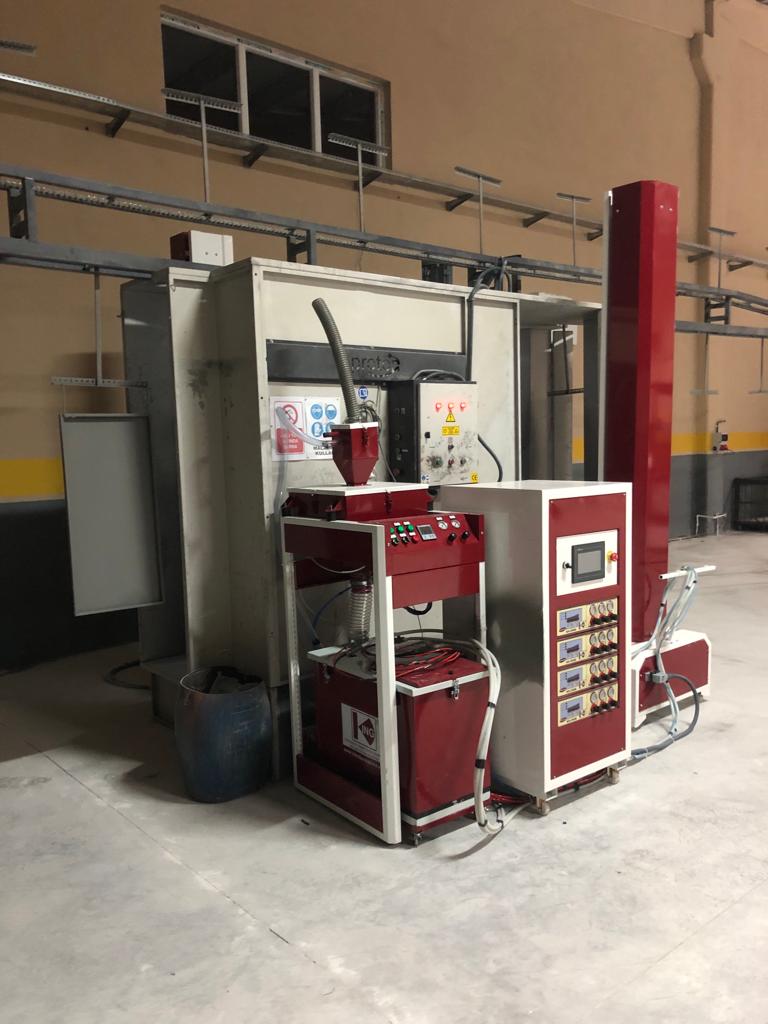
Un système automatique de récupération de la peinture en poudre est une technologie clé qui permet d’optimiser l’application de revêtements en poudre, en récupérant la poudre excédentaire pour la réutiliser dans le processus de poudrage. Cela permet de réduire les coûts de production, de minimiser le gaspillage et de rendre le processus de finition plus respectueux de l’environnement. Ce type de système est largement utilisé dans les lignes de poudrage automatiques et les installations de thermolaquage, où l’efficacité et la rentabilité sont essentielles.
Le principe de fonctionnement d’un système automatique de récupération de la peinture en poudre repose sur l’utilisation de dispositifs de collecte et de filtration qui aspirent la poudre excédentaire, généralement dans une cabine de poudrage. Une fois récupérée, la poudre est filtrée pour éliminer les impuretés, la poussière et les autres contaminants avant d’être renvoyée vers le réservoir de stockage pour être réutilisée dans le processus de pulvérisation. Ce processus garantit que la poudre excédentaire ne soit pas gaspillée, ce qui réduit non seulement les coûts associés à l’achat de nouveaux matériaux, mais aussi l’impact environnemental du procédé.
Les systèmes automatiques de récupération de la peinture en poudre sont souvent intégrés dans des lignes de production automatisées où la pulvérisation est effectuée à l’aide de pistolets électrostatiques. La pulvérisation électrostatique est utilisée pour charger la poudre et l’attirer sur les pièces à traiter, mais une partie de la poudre se dépose sur les surfaces environnantes de la cabine. Un système de récupération efficace permet d’aspirer cette poudre excédentaire, de la filtrer et de la réintroduire dans le circuit, réduisant ainsi le gaspillage et assurant une utilisation maximale des matériaux.
Les composants clés d’un système de récupération de peinture en poudre comprennent des aspirateurs, des filtres à poudre, des convoyeurs, des systèmes de collecte de poudre et des réservoirs de stockage. Les aspirateurs sont utilisés pour aspirer la poudre excédentaire qui se dépose dans la cabine de poudrage. Une fois collectée, la poudre passe par un système de filtration où les impuretés et autres particules indésirables sont éliminées. Les filtres peuvent être constitués de toiles ou de cartouches qui capturent la poudre tout en permettant à l’air propre de s’échapper, évitant ainsi que la poussière ne se répande dans l’atelier.
Les systèmes de récupération peuvent être de type cyclonique, où la poudre est séparée de l’air par un mouvement de rotation, ou de type à filtre, où l’air est filtré avant de passer par un système de récupération. Une fois filtrée, la poudre est stockée dans un réservoir, prête à être réutilisée pour d’autres cycles de poudrage. Cela permet une gestion efficace des matériaux, réduisant les besoins en poudre neuve et garantissant une production plus économique.
L’un des avantages principaux des systèmes automatiques de récupération de la peinture en poudre est leur capacité à réduire considérablement les coûts de production. Dans un processus de poudrage traditionnel, une grande partie de la poudre utilisée pour le revêtement est perdue sous forme de poussière ou de surplus. Un système de récupération bien conçu permet de récupérer une proportion significative de cette poudre excédentaire, réduisant ainsi la quantité de poudre neuve nécessaire. Cela représente une économie importante pour les entreprises, en particulier dans des secteurs où la poudre utilisée est coûteuse, comme l’automobile, les équipements industriels ou l’électroménager.
Un autre avantage majeur de ces systèmes est qu’ils contribuent à la réduction de l’empreinte écologique de l’industrie. En récupérant et en réutilisant la poudre excédentaire, ces systèmes diminuent la quantité de déchets générés par le processus de poudrage, ce qui est favorable à l’environnement. De plus, la réduction de la demande en poudre neuve aide à minimiser la consommation de ressources et les émissions associées à la production de la peinture en poudre. L’utilisation de tels systèmes permet donc non seulement de réaliser des économies, mais aussi de répondre aux normes environnementales strictes qui sont de plus en plus imposées aux industriels.
Les systèmes automatiques de récupération de la peinture en poudre sont conçus pour être faciles à intégrer dans des lignes de production existantes, qu’elles soient petites ou à grande échelle. Grâce à leur flexibilité, ces systèmes peuvent être adaptés aux différents types de lignes de poudrage, qu’il s’agisse de petites installations artisanales ou de grandes chaînes de production industrielles. Les technologies modernes permettent même d’intégrer ces systèmes à des lignes de poudrage entièrement automatisées, où la récupération de poudre est totalement gérée par des dispositifs contrôlés à distance et supervisés par des logiciels de gestion de la production.
En outre, la maintenance des systèmes automatiques de récupération de la peinture en poudre est relativement simple. Les filtres doivent être régulièrement nettoyés ou remplacés pour assurer un fonctionnement optimal, et les réservoirs de stockage doivent être vidés et vérifiés pour s’assurer qu’ils ne contiennent pas de contaminants ou d’humidité qui pourraient affecter la qualité de la poudre. Certains systèmes sont équipés de capteurs qui permettent de surveiller l’état des filtres et des réservoirs en temps réel, ce qui permet aux opérateurs de planifier la maintenance avant qu’un problème ne survienne, réduisant ainsi les temps d’arrêt.
Les innovations dans ce domaine incluent également des systèmes de filtration de plus en plus performants, capables de capter même les particules de poudre les plus fines. Ces filtres avancés permettent de garantir que la poudre récupérée soit aussi pure que possible et prête à être réutilisée sans perte de qualité. De plus, certains systèmes sont équipés de technologies permettant de séparer les poudres de différentes couleurs ou types, ce qui permet une récupération et une réutilisation sélective de la poudre, en particulier pour les lignes de production où différents types de finition sont utilisés.
Les systèmes de récupération de peinture en poudre modernes sont également dotés de logiciels de gestion qui permettent de suivre en temps réel l’efficacité de la récupération de poudre et d’optimiser la production. Ces logiciels peuvent ajuster automatiquement les paramètres du système, comme la vitesse d’aspiration et la filtration, pour garantir une efficacité maximale. Grâce à l’intégration de ces technologies numériques, les entreprises peuvent améliorer non seulement la qualité de leur production, mais aussi la gestion de leurs ressources et la performance de leurs lignes de production.
En termes de tendances futures, la recherche et le développement se concentreront probablement sur l’amélioration de l’efficacité énergétique des systèmes de récupération, en réduisant la consommation d’énergie nécessaire à l’aspiration et à la filtration de la poudre. L’automatisation des systèmes sera également un axe important, avec des robots et des systèmes d’intelligence artificielle qui permettront de surveiller et de contrôler de manière encore plus précise le processus de récupération, en rendant les systèmes encore plus autonomes.
Le développement de technologies de récupération de peinture en poudre plus écologiques, utilisant des matériaux recyclés et réduisant l’empreinte carbone des installations, sera également un point de focalisation. Les innovations dans la conception des filtres et des systèmes de collecte visent à rendre ces processus encore plus propres et à optimiser l’utilisation des ressources, garantissant ainsi une production plus durable et responsable.
En conclusion, les systèmes automatiques de récupération de la peinture en poudre sont essentiels pour améliorer l’efficacité et la durabilité des processus de poudrage. En permettant de récupérer et de réutiliser la poudre excédentaire, ces systèmes non seulement réduisent les coûts et les déchets, mais contribuent également à la réduction de l’impact environnemental de la production industrielle. À mesure que les technologies continuent de progresser, ces systèmes deviendront de plus en plus intelligents, efficaces et écologiques, offrant des solutions de finition plus durables et économiques pour une gamme de secteurs industriels.
Les perspectives futures des systèmes automatiques de récupération de la peinture en poudre sont étroitement liées aux évolutions technologiques en matière de durabilité, d’efficacité et de flexibilité. L’intégration accrue de l’Internet des objets (IoT) dans ces systèmes permettra une gestion plus précise et plus réactive des processus de récupération de poudre. Les capteurs intelligents, couplés à des algorithmes avancés d’analyse des données, fourniront des informations détaillées sur l’état des filtres, la qualité de la poudre récupérée et l’efficacité globale du système. Cette technologie permettra non seulement de mieux gérer les flux de production, mais aussi de minimiser les erreurs humaines et les risques de défaillances techniques.
Un autre domaine d’innovation dans les systèmes de récupération de peinture en poudre concerne l’utilisation de la robotique. Des robots autonomes pourraient être déployés pour superviser et optimiser les différentes étapes du processus de récupération. Ces robots seraient capables d’effectuer des tâches de maintenance, de nettoyage et de remplacement des filtres, réduisant ainsi les besoins en main-d’œuvre et permettant aux opérateurs de se concentrer sur des tâches plus stratégiques. En outre, ces robots pourraient être équipés de caméras et de capteurs pour détecter les anomalies ou les zones nécessitant une attention particulière, assurant ainsi un fonctionnement optimal en continu.
Dans le domaine de la personnalisation des produits finis, les systèmes de récupération de peinture en poudre évolueront pour gérer des poudres de plus en plus diversifiées, avec des propriétés particulières. Par exemple, la demande croissante pour des finitions haut de gamme, comme les effets métalliques, nacrés ou fluorescents, nécessitera des systèmes capables de séparer et de récupérer efficacement des poudres ayant des caractéristiques distinctes. Cela pourrait inclure la mise en place de systèmes de récupération adaptés à chaque type de poudre spécifique, garantissant que les poudres récupérées ne soient pas mélangées entre elles et conservent leurs propriétés uniques. Ce niveau de personnalisation et de séparation des poudres permettrait de maintenir une qualité optimale dans les produits finis tout en optimisant les coûts.
Parallèlement à cela, le recyclage des poudres et des matériaux excédentaires va devenir encore plus sophistiqué grâce à l’amélioration des technologies de tri. Les systèmes de tri optique et de séparation magnétique pourraient être utilisés pour trier les différentes poudres en fonction de leur couleur ou de leurs propriétés chimiques, permettant une réutilisation de poudre encore plus fine et plus spécifique. Cette approche pourrait également s’étendre à la récupération des poudres à base de matériaux écologiques ou biosourcés, qui exigent des procédés de récupération encore plus soignés pour éviter la contamination croisée avec d’autres types de peinture.
L’intégration de l’intelligence artificielle (IA) dans les systèmes de récupération de peinture en poudre permettra de rendre les opérations plus autonomes et intelligentes. L’IA pourrait analyser en temps réel les performances des systèmes de récupération, ajustant automatiquement les paramètres de filtration, d’aspiration et de réintroduction de la poudre pour garantir une efficacité optimale. L’IA pourra également prédire les besoins en maintenance en identifiant les signes précurseurs de défaillance avant qu’ils n’affectent la production. Ce type de surveillance proactive améliorera non seulement la durée de vie des équipements, mais réduira aussi les interruptions et les coûts de maintenance, contribuant ainsi à une gestion plus efficace de l’ensemble du système de production.
L’optimisation des consommations d’énergie dans les systèmes de récupération de peinture en poudre sera également un axe majeur de développement. De nouveaux systèmes de filtration et de ventilation plus performants et moins énergivores permettront de réduire les coûts énergétiques tout en garantissant une qualité de filtration optimale. Les systèmes de récupération seront de plus en plus conçus pour maximiser l’efficacité énergétique, intégrant des technologies telles que la récupération de chaleur, qui permettront de réutiliser l’énergie excédentaire produite par le processus, tout en améliorant la durabilité du système.
Les systèmes automatiques de récupération de la peinture en poudre devront également s’adapter aux nouvelles réglementations environnementales. En réponse aux préoccupations croissantes concernant les émissions de CO2 et la gestion des déchets industriels, les fabricants devront répondre à des normes strictes en matière de gestion des poussières et des déchets générés par le processus de poudrage. Cela pourrait inclure des systèmes plus avancés de filtration et de captage des poussières fines, permettant de garantir que les installations de poudrage respectent les normes environnementales les plus strictes. Les progrès technologiques dans ce domaine permettront également de réduire l’empreinte carbone de l’ensemble du processus de production.
Un autre aspect de l’évolution des systèmes de récupération de peinture en poudre concerne l’intégration de ces technologies dans des processus de production plus complexes. À mesure que l’automatisation et l’optimisation des lignes de production se développent, les systèmes de récupération de poudre devront être capables de s’intégrer dans des environnements de production encore plus complexes, où les lignes de poudrage interagiront avec d’autres processus automatisés, tels que le nettoyage des pièces, le contrôle qualité ou l’emballage. L’intégration de ces technologies dans des systèmes de production connectés permettra de suivre l’ensemble de la chaîne de production en temps réel, garantissant une gestion fluide et continue des opérations.
En conclusion, les systèmes automatiques de récupération de peinture en poudre continueront à évoluer pour devenir plus efficaces, plus intelligents et plus respectueux de l’environnement. Les technologies d’automatisation, d’intelligence artificielle, de robotique et d’efficacité énergétique seront au cœur de cette transformation, permettant aux entreprises de produire plus efficacement tout en réduisant leurs coûts et leur impact écologique. Ces systèmes contribueront à l’amélioration continue de la qualité des produits finis, tout en offrant une solution économique et durable pour le secteur du poudrage.
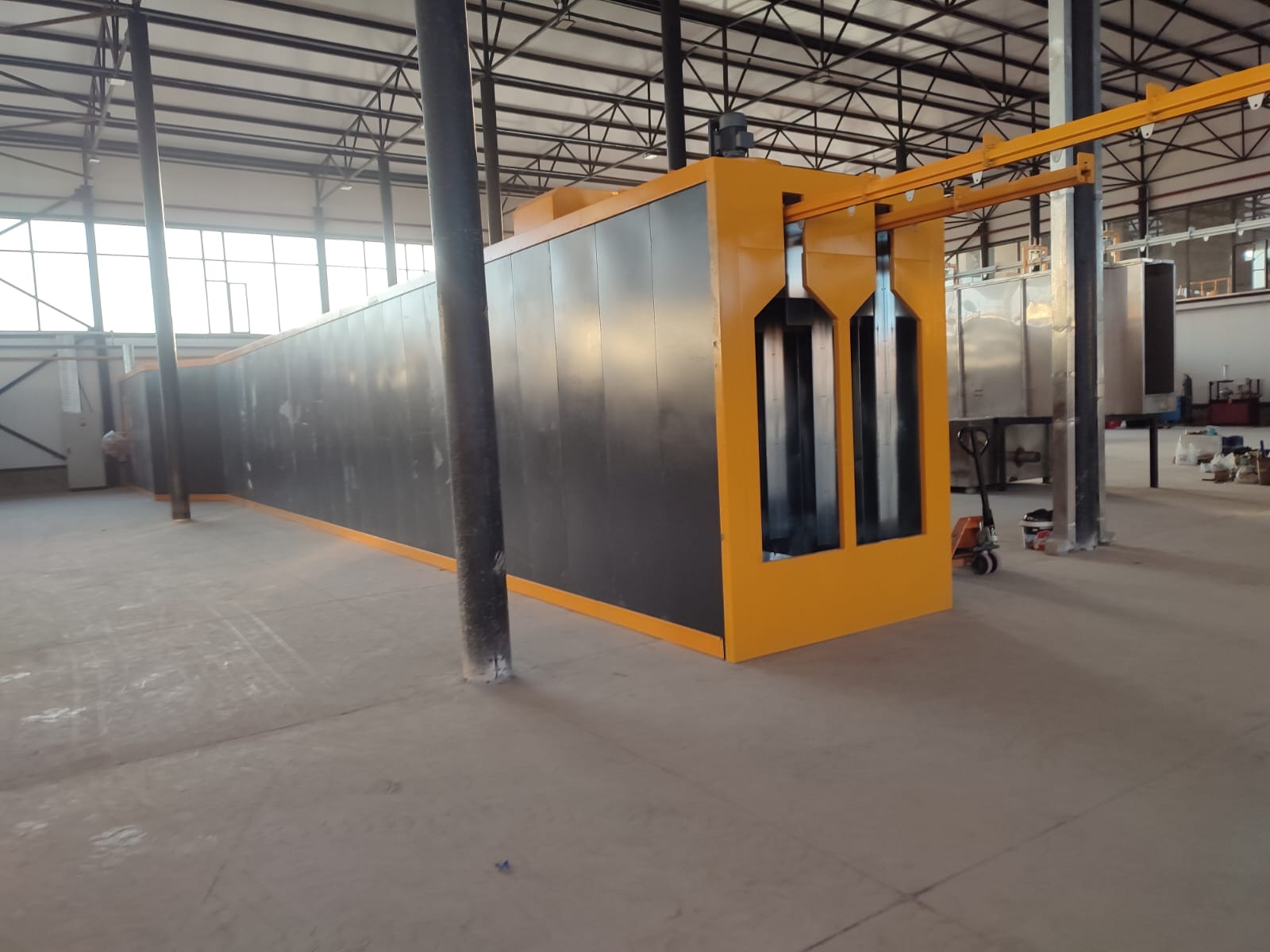
L’évolution des systèmes automatiques de récupération de la peinture en poudre ne se limitera pas uniquement à des avancées technologiques, mais s’étendra également à l’adoption de nouvelles stratégies de gestion et de production. Dans un contexte où la compétitivité et l’efficacité sont de plus en plus essentielles pour les entreprises industrielles, l’intégration de ces systèmes dans des environnements de production lean (sans gaspillage) sera cruciale. Ces systèmes permettront de réduire le temps d’arrêt des machines, d’optimiser l’utilisation des matériaux et d’améliorer la productivité en minimisant les déchets tout en assurant une finition de haute qualité.
L’un des aspects essentiels de cette évolution réside dans la flexibilité accrue des systèmes de récupération. Alors que les lignes de production deviennent de plus en plus diversifiées et polyvalentes, les systèmes devront être capables de s’adapter à une large gamme de couleurs et de types de poudres. Cela pourrait se traduire par l’introduction de systèmes modulaires qui permettent de changer rapidement les types de poudres, les filtres et les configurations de récupération en fonction des besoins spécifiques des clients ou des exigences de production. Cette flexibilité serait un atout précieux pour les industries qui produisent une variété de produits avec des finitions différentes, comme l’automobile, l’électroménager, les meubles et les composants électroniques.
Par ailleurs, l’évolution des systèmes de récupération de peinture en poudre impliquera aussi une approche de plus en plus collaborative entre les fabricants de ces équipements et les utilisateurs finaux. Les entreprises demanderont des solutions sur mesure, adaptées à leurs besoins spécifiques en termes de volume, de types de produits et d’exigences techniques. En réponse, les fabricants de systèmes de récupération devront proposer des solutions personnalisées qui intègrent non seulement les technologies les plus avancées mais aussi un support technique et une formation adaptés aux utilisateurs. Cela inclut une meilleure assistance dans la mise en place des systèmes, ainsi que dans leur maintenance préventive pour garantir un fonctionnement optimal tout au long de leur durée de vie.
L’intégration de technologies de gestion de la production, telles que les systèmes ERP (Enterprise Resource Planning) et MES (Manufacturing Execution Systems), avec les systèmes de récupération de peinture en poudre, permettra une gestion encore plus fluide et centralisée des opérations. Ces systèmes, qui collectent et analysent des données en temps réel, permettront de surveiller les performances des systèmes de récupération, de prévoir les besoins en maintenance, et de suivre l’utilisation des matériaux pour optimiser les coûts. En cas de panne ou d’anomalie dans le processus, ces systèmes seront capables de détecter rapidement le problème et d’alerter les responsables de la production, ce qui permettra une résolution plus rapide et une réduction des temps d’arrêt.
Les systèmes de récupération devront également répondre aux exigences croissantes des consommateurs en matière de transparence et de durabilité. Les entreprises sont de plus en plus appelées à fournir des informations détaillées sur l’impact environnemental de leurs processus de production. Dans ce contexte, les fabricants de systèmes de récupération de peinture en poudre devront offrir des solutions qui non seulement respectent les normes environnementales en vigueur, mais qui vont au-delà des exigences de base. Cela pourrait inclure des certifications écologiques pour les équipements, des rapports détaillés sur la consommation d’énergie et de matériaux, ainsi que des données sur l’empreinte carbone du processus de poudrage.
Avec l’essor des normes mondiales en matière de durabilité et de responsabilité sociale des entreprises (RSE), les fabricants de poudre et les industries utilisatrices devront se conformer à des standards plus stricts concernant la qualité et l’origine des matériaux utilisés. Les poudres écologiques, biodégradables ou à base de ressources renouvelables devraient connaître une croissance importante, et les systèmes de récupération devront être capables de traiter ces nouvelles matières sans compromettre leur efficacité. En conséquence, des investissements dans des équipements plus adaptés à ces matériaux seront nécessaires pour répondre à cette demande.
L’un des aspects les plus prometteurs de l’évolution des systèmes de récupération de peinture en poudre sera l’adoption croissante de l’impression 3D et des procédés de fabrication additive dans le cadre des lignes de production. Bien que les applications principales de la fabrication additive soient souvent dans la création de pièces uniques ou de prototypes, il existe un potentiel important pour utiliser les systèmes de poudrage pour appliquer des revêtements de finition sur ces objets imprimés en 3D. Dans ce contexte, les systèmes de récupération de peinture en poudre joueront un rôle crucial en permettant de maintenir des niveaux de matériaux optimaux tout en gérant la diversité des formes et des tailles des objets imprimés. Les lignes de poudrage devront évoluer pour s’adapter aux spécifications particulières des pièces imprimées en 3D, qui peuvent avoir des géométries complexes et des exigences uniques en termes de finition.
La connectivité des équipements via le cloud et les réseaux industriels permettra une gestion à distance des systèmes de récupération de peinture en poudre. Les entreprises pourront surveiller, analyser et optimiser leurs lignes de production à partir de n’importe quel endroit, offrant ainsi une plus grande réactivité et flexibilité. Ces systèmes seront capables d’envoyer des alertes automatiques en cas de dysfonctionnements ou de performances en baisse, ce qui permettra une gestion proactive de la production. De plus, l’analyse des données collectées permettra d’effectuer des ajustements en temps réel pour améliorer l’efficacité du système et réduire les coûts opérationnels.
Les nouveaux systèmes pourraient également intégrer des technologies de réalité augmentée (RA) pour la formation et la maintenance des opérateurs. Par exemple, en cas de besoin de maintenance, des lunettes de réalité augmentée pourraient fournir aux techniciens des instructions étape par étape en temps réel, ce qui simplifierait le processus de réparation et accélérerait le retour à la production. Ces technologies permettront aux entreprises de maintenir un haut niveau de compétence parmi leurs opérateurs tout en réduisant les erreurs humaines et en améliorant la sécurité des installations.
En conclusion, les systèmes automatiques de récupération de peinture en poudre seront essentiels pour aider les industries à répondre aux défis de la production moderne. Avec une attention accrue à l’efficacité, à la durabilité et à l’intégration technologique, ces systèmes transformeront les processus de finition en poudre, en les rendant plus intelligents, plus économes en ressources et plus respectueux de l’environnement. Grâce à l’innovation continue, l’adoption de nouvelles technologies et l’amélioration de la connectivité, les systèmes de récupération de peinture en poudre joueront un rôle clé dans l’industrie manufacturière de demain, offrant une solution plus durable, rentable et adaptable à l’échelle mondiale.
Cabine de Poudrage Automatique
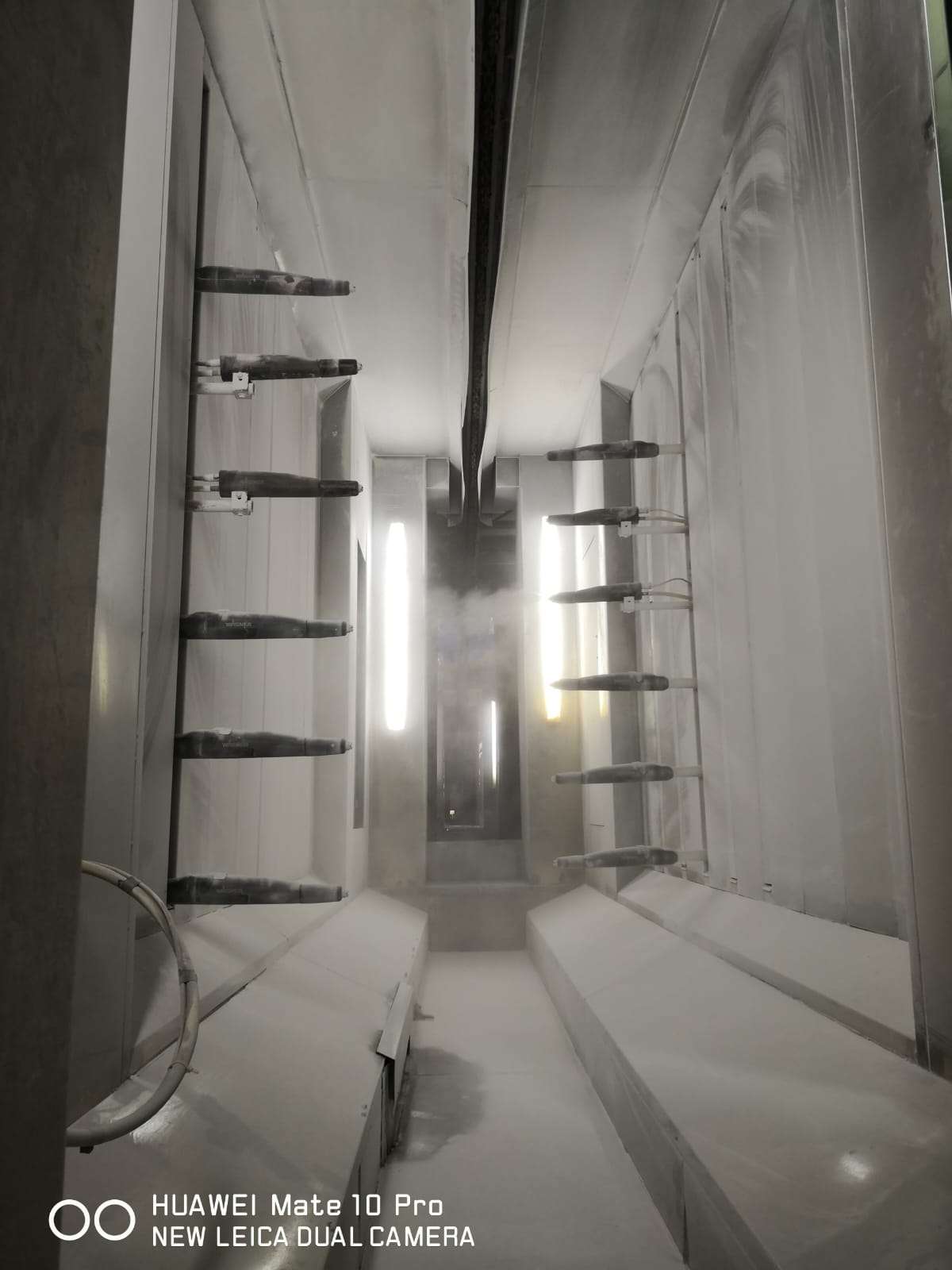
Une cabine de poudrage automatique est un dispositif essentiel dans les lignes de production modernes de revêtements en poudre, permettant l’application uniforme de peinture en poudre sur des pièces métalliques ou d’autres substrats. Elle est conçue pour assurer un environnement contrôlé où la poudre peut être appliquée de manière précise et efficace, tout en minimisant le gaspillage et en maximisant la qualité de la finition. Ces cabines sont utilisées dans divers secteurs industriels, tels que l’automobile, l’électroménager, les équipements industriels et bien d’autres, où l’esthétique et la résistance des surfaces traitées sont cruciales.
Le fonctionnement d’une cabine de poudrage automatique repose sur un système de pulvérisation électrostatique. Ce système charge électriquement la poudre de peinture, qui est ensuite projetée sur les pièces à revêtir. L’effet électrostatique attire la poudre chargée vers la pièce, ce qui permet une couverture homogène, même sur des formes complexes ou difficiles d’accès. La cabine est dotée de systèmes d’aspiration et de filtration qui recueillent la poudre excédentaire, réduisant ainsi les pertes et garantissant une réutilisation de la poudre pour d’autres applications.
Les cabines de poudrage automatiques sont conçues pour fonctionner dans des conditions de sécurité optimales, en particulier lorsqu’il s’agit de produits inflammables comme les poudres de peinture. Elles sont équipées de systèmes de ventilation pour éliminer les particules en suspension et prévenir les risques d’explosion. L’air est filtré pour éviter que les poussières fines ne se dispersent dans l’environnement, assurant ainsi non seulement la qualité de la peinture, mais aussi la sécurité des opérateurs.
Un des principaux avantages des cabines de poudrage automatiques est la réduction du gaspillage de peinture. Grâce à des systèmes de récupération intégrés, la poudre excédentaire est collectée et renvoyée dans le système de pulvérisation pour être réutilisée. Cela permet de réaliser des économies significatives sur le coût des matériaux, tout en minimisant l’impact environnemental du procédé. Ce système de récupération fonctionne généralement avec des aspirateurs, des filtres et des systèmes de cyclonage qui permettent de capturer et de filtrer la poudre excédentaire avant de la réintroduire dans le circuit.
Les cabines modernes sont souvent équipées de technologies avancées telles que des capteurs et des automates programmables qui contrôlent précisément l’application de la peinture. Ces capteurs peuvent surveiller des paramètres tels que la quantité de poudre pulvérisée, l’uniformité de l’application et même la qualité de la surface traitée, permettant ainsi une gestion optimisée du processus. Cette automatisation permet de réduire l’intervention humaine et de garantir des résultats constants et reproductibles, même sur des séries de production à grande échelle.
L’ergonomie et la facilité d’utilisation sont des aspects importants dans la conception des cabines de poudrage automatiques. Les opérateurs peuvent ajuster les paramètres de la cabine à l’aide de panneaux de commande numériques, permettant un contrôle précis sur les réglages de la pulvérisation, la pression de l’air, la température, et d’autres facteurs essentiels pour obtenir une finition de qualité. Certaines cabines sont également équipées de systèmes de nettoyage automatiques, ce qui facilite leur maintenance et garantit un fonctionnement optimal à long terme.
Les cabines de poudrage automatiques sont également dotées de systèmes de sécurité avancés pour protéger à la fois l’environnement de travail et les opérateurs. Outre les systèmes de ventilation et de filtration de l’air, elles peuvent être équipées de détecteurs de flammes, de systèmes d’extinction automatique, et de dispositifs de surveillance en temps réel qui garantissent que les niveaux de poussière sont sous contrôle et que les risques d’incendie sont minimisés. Cela permet aux entreprises de respecter les normes strictes de sécurité et d’environnement, tout en assurant une production continue.
L’adaptabilité des cabines de poudrage automatiques est également un élément clé de leur efficacité. Elles peuvent être configurées pour traiter une large gamme de pièces de formes et de tailles variées, grâce à des dispositifs de rotation ou de déplacement automatisés qui assurent une couverture uniforme. Certaines cabines sont également modulables et peuvent être ajustées en fonction des besoins spécifiques de production, qu’il s’agisse d’une petite série de pièces personnalisées ou d’une production en grande série.
Les cabines de poudrage automatiques sont aussi souvent équipées de systèmes de contrôle de la qualité intégrés. Par exemple, des caméras et des capteurs peuvent être utilisés pour inspecter la surface des pièces en temps réel, vérifiant l’uniformité de la couche de peinture et détectant d’éventuelles imperfections ou défauts avant que les pièces ne passent à l’étape suivante de traitement. Ces systèmes garantissent non seulement une finition de qualité, mais aussi une réduction des rejets et des retouches, ce qui optimise le temps de production et les coûts.
Le processus de poudrage dans une cabine automatique peut être adapté à divers types de poudres, notamment les poudres thermodurcissables et thermoplastiques, ce qui offre une grande flexibilité pour différents types d’applications. Les poudres peuvent être choisies en fonction de leurs propriétés, telles que la résistance aux UV, la durabilité, la finition esthétique ou la résistance à la corrosion. Cette diversité permet aux fabricants de répondre à des besoins variés tout en utilisant une seule cabine de poudrage.
Les cabines de poudrage automatiques sont également un moyen efficace de respecter les normes environnementales de plus en plus strictes. Elles permettent de réduire les émissions de substances nocives, d’éviter la dispersion de particules fines dans l’air et d’optimiser la consommation de matières premières, contribuant ainsi à un processus de production plus durable. En outre, la réduction du gaspillage de peinture grâce à la récupération et à la réutilisation de la poudre excédentaire permet de diminuer l’impact écologique de l’ensemble du processus.
Enfin, les tendances actuelles dans le domaine des cabines de poudrage automatiques se dirigent vers une meilleure intégration des technologies numériques et de l’intelligence artificielle pour améliorer la gestion de la production. Les systèmes de monitoring à distance, les analyses prédictives basées sur les données collectées en temps réel, et l’optimisation des processus à l’aide de l’IA permettront aux entreprises de gagner en efficacité, de réduire les coûts et d’assurer une gestion optimale de la qualité. L’automatisation des réglages et l’optimisation des flux de production seront des éléments clés pour les entreprises cherchant à rester compétitives dans un marché en constante évolution.
En résumé, les cabines de poudrage automatiques représentent une avancée technologique majeure dans les processus industriels de finition en poudre. Grâce à leur capacité à appliquer des revêtements uniformes, à récupérer la poudre excédentaire, à optimiser la production et à respecter les normes de sécurité et environnementales, elles offrent une solution efficace, économique et durable pour une variété d’applications industrielles. Les évolutions futures des technologies liées à ces systèmes permettront de rendre ces cabines encore plus intelligentes, flexibles et écologiques, garantissant ainsi une production de haute qualité à des coûts réduits.
Les innovations futures dans le domaine des cabines de poudrage automatiques se concentreront sur l’amélioration continue de leur efficacité, de leur sécurité et de leur capacité à répondre aux besoins diversifiés des industries modernes. L’intégration croissante de l’intelligence artificielle (IA) et de l’Internet des objets (IoT) jouera un rôle clé dans cette transformation. Ces technologies permettront une surveillance en temps réel des paramètres de production, offrant ainsi une gestion proactive des systèmes. Par exemple, des capteurs intelligents pourront surveiller la pression de pulvérisation, la température, et même la vitesse de déplacement des pièces dans la cabine. Les données recueillies pourront être analysées en temps réel pour ajuster automatiquement les paramètres, optimisant ainsi la consommation de poudre et la qualité du revêtement.
L’un des aspects les plus prometteurs de l’évolution des cabines de poudrage automatiques est l’amélioration de l’efficacité énergétique. Les cabines de poudrage consomment souvent une quantité significative d’énergie, notamment pour maintenir la circulation de l’air et le chauffage de la poudre. Les développements futurs viseront à réduire la consommation énergétique tout en maintenant des performances optimales. Cela pourrait inclure l’optimisation des systèmes de ventilation et de récupération de chaleur pour recycler l’énergie excédentaire, ou encore l’intégration de technologies de gestion énergétique avancées pour minimiser la demande en énergie pendant les phases de production.
Les technologies de fabrication additive, telles que l’impression 3D, commenceront également à avoir un impact sur les cabines de poudrage automatiques. À mesure que la fabrication additive se développe, la demande de traitements de surface spécifiques pour des pièces imprimées en 3D augmentera. Ces pièces ont souvent des géométries complexes qui nécessitent une application de poudre uniforme et précise. Les cabines de poudrage devront s’adapter pour gérer ces nouvelles formes et dimensions, offrant une couverture homogène même sur des surfaces irrégulières ou tridimensionnelles. Les systèmes de poudrage automatisés devront être capables de gérer des processus encore plus personnalisés tout en optimisant l’utilisation de la poudre.
Un autre domaine en plein essor est l’amélioration de la connectivité des systèmes. L’intégration des cabines de poudrage dans des environnements de production entièrement automatisés et connectés permettra une gestion plus fluide et plus flexible des opérations. Les cabines pourront être reliées à d’autres équipements de production, tels que des systèmes de contrôle de la qualité, des machines de nettoyage, ou des lignes de transport, pour une gestion centralisée et en temps réel de la chaîne de production. Cela permettra non seulement d’optimiser les performances des cabines, mais aussi de réduire les erreurs humaines et d’améliorer la traçabilité des produits finis.
Les entreprises mettront également davantage l’accent sur l’aspect écologique des cabines de poudrage automatiques. Avec l’augmentation des pressions réglementaires concernant la gestion des ressources et la réduction des émissions, les fabricants chercheront à concevoir des cabines encore plus écologiques, en améliorant les systèmes de filtration, en réduisant les émissions de CO2 et en augmentant la recyclabilité des poudres. Les cabines de poudrage pourront être équipées de nouveaux matériaux de filtration, plus durables et efficaces, permettant de capturer un plus grand nombre de particules fines tout en réduisant la consommation d’énergie des systèmes de filtration. La gestion des déchets industriels sera également améliorée grâce à des technologies de tri avancées, garantissant que les matériaux récupérés soient réutilisés efficacement dans le processus.
En termes de flexibilité et de personnalisation, les cabines de poudrage automatiques évolueront pour pouvoir traiter une gamme encore plus large de types de pièces et de finitions. Par exemple, des systèmes plus sophistiqués pourront être configurés pour des processus de poudrage multicouleurs, permettant l’application simultanée de plusieurs couleurs de poudre sans contamination croisée, ou des techniques de finition complexes comme des effets métalliques ou texturés. Les entreprises pourront ainsi diversifier leur production sans avoir à investir dans de multiples systèmes de poudrage.
De plus, l’augmentation de l’utilisation de systèmes robotisés dans les cabines de poudrage automatiques permettra non seulement de garantir une couverture uniforme sur des surfaces complexes, mais aussi d’accroître la productivité. Les robots pourront être programmés pour appliquer la peinture avec une grande précision et efficacité, réduisant le besoin de réajustements manuels et améliorant la constance de la finition. Ils pourront également être utilisés pour automatiser d’autres tâches, comme le nettoyage des surfaces avant ou après le poudrage, ou le déplacement des pièces à revêtir dans la cabine, augmentant ainsi la flexibilité et l’efficacité des lignes de production.
L’automatisation du processus de maintenance sera également un aspect clé de l’évolution des cabines de poudrage automatiques. Les systèmes de maintenance prédictive, alimentés par des données collectées en temps réel par des capteurs, permettront d’anticiper les besoins en maintenance avant qu’une panne ne se produise. Cela garantira un fonctionnement ininterrompu des lignes de production et minimisera les coûts liés aux réparations urgentes. Les capteurs de surveillance pourront alerter les responsables de la production dès que l’état d’une pièce nécessite une attention particulière, permettant une gestion proactive des équipements.
Les cabines de poudrage automatiques du futur permettront également une personnalisation accrue des processus de revêtement. En plus des paramètres classiques tels que la pression d’air, la température ou la vitesse de passage, des ajustements plus fins pourront être effectués en fonction de l’analyse des données de production. Cela inclut la possibilité de modifier les paramètres en temps réel pour compenser les variations de qualité de la poudre ou de la surface des pièces à traiter, assurant ainsi une finition optimale à chaque cycle de production.
Enfin, l’utilisation de technologies de réalité augmentée (RA) pour la formation et le dépannage pourrait devenir courante dans les cabines de poudrage automatiques. Les opérateurs pourraient utiliser des lunettes de réalité augmentée pour recevoir des instructions interactives et des informations en temps réel, facilitant ainsi l’entretien et la réparation des équipements. Cette approche pourrait également être utilisée pour la formation des nouveaux opérateurs, permettant un apprentissage plus rapide et plus efficace des procédures complexes.
En conclusion, les cabines de poudrage automatiques continueront d’évoluer en intégrant des technologies avancées, telles que l’intelligence artificielle, la robotique, et la connectivité, pour répondre aux exigences croissantes des industries modernes. Ces innovations permettront non seulement d’optimiser l’efficacité, la sécurité et la flexibilité des processus de poudrage, mais aussi de réduire l’impact environnemental de la production, en rendant ces systèmes plus écologiques et économes en ressources. Le futur des cabines de poudrage automatiques réside dans leur capacité à s’adapter aux besoins variés des entreprises, tout en offrant une solution durable et de haute qualité pour une production industrielle de plus en plus performante.
Les cabines de poudrage automatiques se rapprochent de plus en plus de leur intégration totale dans des systèmes de production intelligents et interconnectés, un mouvement qui devrait marquer l’avenir de la fabrication. En effet, l’augmentation de la digitalisation et de l’automatisation dans le secteur manufacturier permettra de mieux synchroniser toutes les étapes du processus de production, y compris l’application de la peinture en poudre. Cette interconnexion permettra d’optimiser encore davantage les performances des cabines de poudrage, en garantissant que chaque élément de la ligne de production fonctionne en harmonie pour atteindre des résultats parfaits.
Une tendance marquante à cet égard sera l’adoption des “usines connectées”, où chaque composant de la chaîne de production communique en temps réel avec les autres. Dans ce contexte, les cabines de poudrage automatiques ne seront pas seulement des stations indépendantes, mais des éléments clés de réseaux industriels intelligents. Les systèmes de gestion de la production basés sur le cloud collecteront et analyseront des données provenant de plusieurs sources au sein de la cabine de poudrage et au-delà, ce qui permettra une meilleure planification, un contrôle qualité avancé et une gestion en temps réel de la production. L’analyse de ces données facilitera des ajustements immédiats du processus de poudrage pour améliorer la qualité de finition, réduire les déchets et maximiser l’utilisation des ressources.
Les progrès en matière de machine learning et d’analytique prédictive auront un impact significatif sur le fonctionnement des cabines de poudrage automatiques. Par exemple, les algorithmes d’apprentissage automatique peuvent analyser les performances des équipements, identifier les anomalies et prévoir des défaillances avant qu’elles ne surviennent. En utilisant ces outils d’intelligence prédictive, les entreprises pourront maintenir des niveaux de production élevés sans interruption, réduire les coûts d’entretien et optimiser les cycles de maintenance.
En plus de ces avancées technologiques, les cabines de poudrage automatiques devront également prendre en compte les préoccupations sociales et environnementales qui deviennent de plus en plus présentes dans le secteur industriel. L’attention portée à la durabilité, la réduction des émissions et le respect des normes écologiques continuera de croître, ce qui influencera la conception des équipements. De nouvelles solutions seront développées pour réduire l’empreinte carbone des cabines de poudrage, notamment à travers l’optimisation des systèmes énergétiques et l’intégration de matériaux plus écologiques et recyclables.
Les fabricants de cabines de poudrage devront également répondre à la pression croissante en matière de durabilité sociale. Les consommateurs et les régulations exigent de plus en plus que les produits industriels soient fabriqués de manière éthique et responsable. Cela inclut non seulement la réduction de l’impact environnemental mais aussi l’amélioration des conditions de travail et la sécurité des opérateurs. Les cabines de poudrage automatiques modernes intègreront des systèmes de sécurité renforcés, notamment des capteurs pour détecter les niveaux de poussière dans l’air et des dispositifs d’extinction automatique pour prévenir tout risque d’incendie. En outre, les améliorations ergonomiques des cabines permettront de réduire les risques pour les travailleurs et d’améliorer leur confort, avec des interfaces intuitives et des dispositifs de commande à distance pour minimiser les déplacements physiques autour des machines.
La réduction du gaspillage et l’optimisation des ressources deviendront des priorités de plus en plus présentes dans le design des cabines de poudrage. De nouvelles technologies de recyclage de la poudre permettront non seulement de récupérer la poudre excédentaire mais aussi d’optimiser son taux de réutilisation sans perte de qualité. Les systèmes de filtration de plus en plus sophistiqués élimineront efficacement les particules fines et amélioreront la qualité de l’air ambiant dans les environnements de travail, contribuant ainsi à un processus de production plus propre et plus sain.
En ce qui concerne les applications spécifiques, les cabines de poudrage automatiques joueront un rôle de plus en plus important dans des secteurs émergents, tels que les technologies de surface avancées pour les pièces de haute précision et les produits personnalisés. L’utilisation de technologies de poudrage multifonctionnelles permettra de traiter des substrats plus variés et de réaliser des finitions de plus en plus spécialisées, par exemple pour des pièces utilisées dans l’aérospatiale, la biomédecine ou l’électronique, où des exigences de performance strictes sont de mise.
L’essor des matériaux composites et des nouvelles substances de revêtement, comme les poudres à base de nanoparticules ou les matériaux conducteurs, ouvrira également de nouvelles possibilités pour les cabines de poudrage. Ces nouvelles poudres présenteront des défis particuliers en termes de manipulation, de dispersion et de durabilité, ce qui nécessitera des ajustements techniques dans la conception des cabines pour garantir une application optimale et une bonne adhérence à des matériaux souvent plus sensibles que les poudres classiques.
En outre, la diversification des couleurs, des effets spéciaux (comme les effets métalliques, mats, ou nacrés) et des finitions fonctionnelles (résistance à la chaleur, aux produits chimiques, à l’usure) influencera l’évolution des cabines de poudrage automatiques. Ces systèmes devront offrir une flexibilité accrue pour répondre à une demande croissante de personnalisation et de diversité dans les produits finis. Cela impliquera non seulement une plus grande flexibilité en termes de contrôle des paramètres de pulvérisation, mais également la capacité à traiter plusieurs types de poudres simultanément, avec des dispositifs de nettoyage rapides pour éviter toute contamination entre différentes applications de finition.
Les cabines de poudrage automatiques du futur devront aussi s’adapter à des cycles de production de plus en plus courts, dans un environnement où la rapidité et l’agilité sont essentielles pour rester compétitif. Les processus devront être capables de s’ajuster dynamiquement pour répondre aux exigences de fabrication à grande échelle tout en maintenant une qualité constante. Cela pourra inclure des systèmes modulaires qui permettent aux cabines de s’adapter à différents types de production, en ajustant la taille, le type de pièce et la complexité des finitions à traiter.
En conclusion, l’avenir des cabines de poudrage automatiques se dessine autour de plusieurs axes majeurs : l’optimisation continue des performances, l’intégration des technologies avancées pour la collecte et l’analyse des données, la durabilité accrue des procédés de fabrication, et une meilleure flexibilité pour répondre à la diversité des besoins de production. Ces équipements se transformeront en véritables centres de production intelligents, où la gestion automatisée et les avancées technologiques permettront non seulement de garantir des finitions de haute qualité, mais aussi de respecter les exigences environnementales et économiques croissantes.
Chaîne de Peinture Poudre
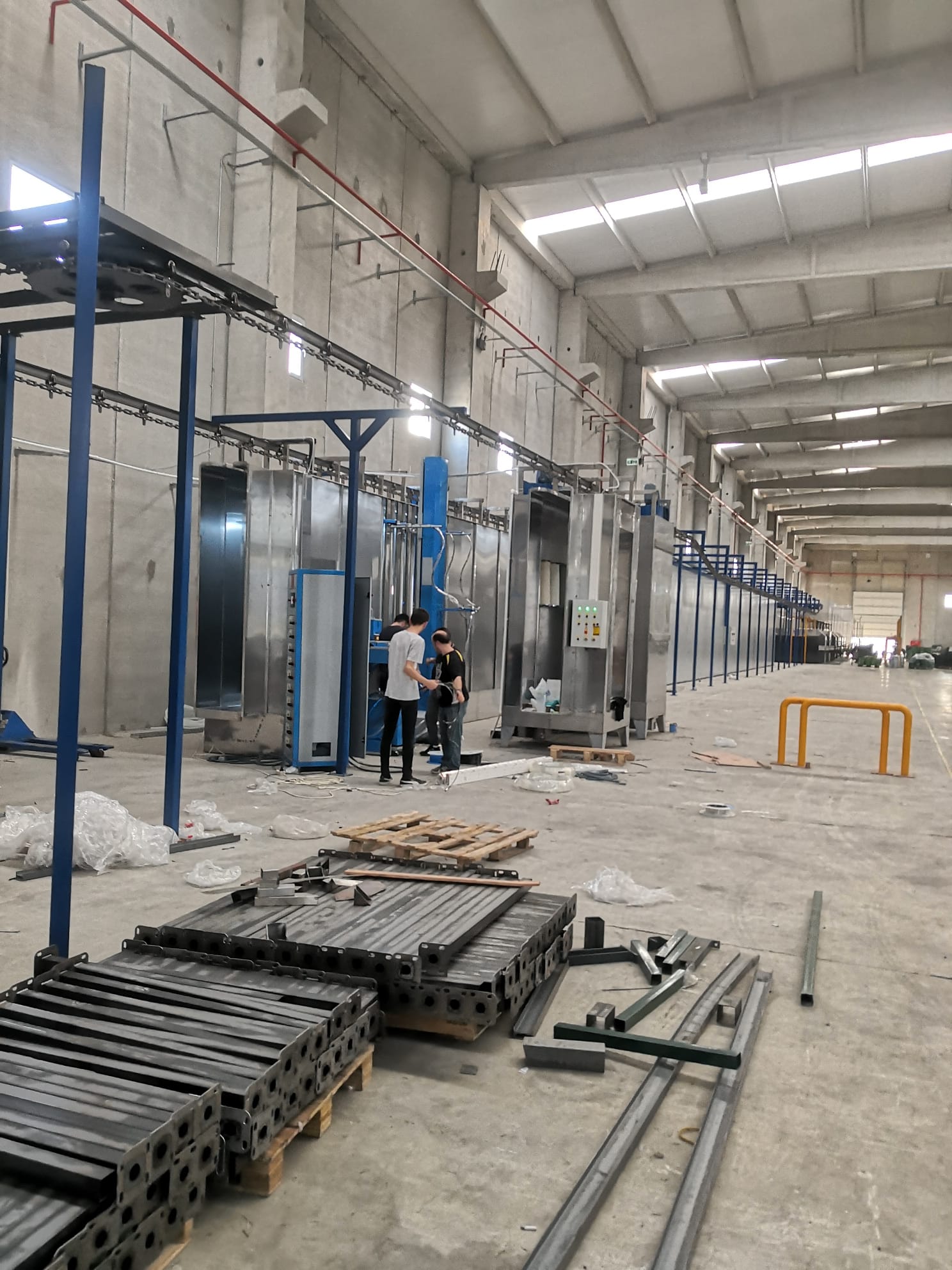
La chaîne de peinture en poudre est un système automatisé utilisé dans les lignes de production industrielles pour appliquer une couche uniforme de peinture en poudre sur divers types de substrats. Elle est largement utilisée dans les secteurs tels que l’automobile, la construction, l’électroménager, et l’industrie métallurgique, en raison de sa capacité à offrir une finition esthétique et durable, tout en étant plus respectueuse de l’environnement que les méthodes traditionnelles de peinture liquide. Le processus de peinture en poudre est une solution économique, efficace et écologique, contribuant à la réduction des déchets et des émissions de solvants.
Le fonctionnement de la chaîne de peinture en poudre repose sur l’utilisation de plusieurs équipements interconnectés, qui permettent de préparer, appliquer et durcir la peinture sur les pièces à revêtir. La chaîne commence par une préparation minutieuse de la surface des pièces à peindre. Cela inclut le nettoyage et le dégraissage des surfaces, souvent réalisé à l’aide de traitements chimiques ou de systèmes de lavage haute pression. Cette étape est cruciale pour garantir une bonne adhérence de la peinture en poudre et pour éviter la formation de défauts sur la surface.
Une fois les pièces nettoyées et séchées, elles sont transportées vers la cabine de poudrage, un élément clé de la chaîne de peinture en poudre. Dans cette cabine, des pistolets électrostatiques pulvérisent la poudre sur les surfaces des pièces. La poudre est électriquement chargée, ce qui crée une attraction entre la peinture et la surface des pièces. L’effet électrostatique assure une couverture uniforme, même sur des surfaces complexes ou de formes irrégulières. La poudre excédentaire est récupérée par un système d’aspiration et de filtration, ce qui réduit le gaspillage et permet de réutiliser la poudre collectée pour de futures applications.
Après l’application de la peinture en poudre, les pièces sont transportées vers un four de durcissement. Ce four chauffé à haute température permet de fondre et de polymériser la poudre, transformant ainsi la peinture en un revêtement solide et durable. La durée et la température du processus de durcissement dépendent du type de poudre utilisé et des spécifications du produit fini. Ce processus confère au revêtement de peinture une résistance élevée aux rayures, aux produits chimiques et aux intempéries, en plus de lui donner une finition lisse et esthétique.
Les chaînes de peinture en poudre modernes intègrent des technologies avancées pour améliorer l’efficacité et la qualité du processus. Les pistolets de pulvérisation sont souvent dotés de systèmes de contrôle automatisés, permettant d’ajuster précisément la quantité de poudre projetée en fonction des caractéristiques des pièces. Des capteurs et des automates peuvent être utilisés pour surveiller en temps réel la qualité de l’application de la peinture, détecter les défauts éventuels et ajuster automatiquement les paramètres de pulvérisation pour garantir une finition parfaite.
Un autre aspect important des chaînes de peinture en poudre modernes est l’efficacité énergétique. Le processus de durcissement dans les fours peut consommer beaucoup d’énergie, mais les progrès technologiques ont permis de concevoir des systèmes de chauffage plus efficaces, utilisant moins d’énergie pour atteindre la température de durcissement requise. L’utilisation de chauffages à induction, de systèmes de récupération de chaleur et d’autres technologies de pointe permet de réduire la consommation d’énergie et de rendre le processus de peinture en poudre plus respectueux de l’environnement.
Les chaînes de peinture en poudre sont également conçues pour offrir une flexibilité maximale dans le traitement des pièces. Certaines chaînes permettent de peindre des pièces de tailles et de formes variées, grâce à des systèmes de transport modifiables et à des réglages flexibles des équipements de pulvérisation et de durcissement. Les lignes de peinture en poudre sont souvent configurées pour traiter des séries de production en grande quantité, mais elles peuvent également être ajustées pour traiter des lots de plus petite taille ou des produits spécifiques, ce qui permet aux fabricants de répondre à des besoins diversifiés tout en maintenant une efficacité maximale.
Les systèmes de récupération de la poudre excédentaire jouent également un rôle crucial dans l’efficacité des chaînes de peinture en poudre. Ces systèmes permettent de capturer et de recycler la poudre non utilisée, réduisant ainsi les coûts de matériaux et minimisant l’impact environnemental du processus. La récupération de la poudre excédentaire est rendue possible grâce à des dispositifs comme les filtres à air, les cyclones, ou les aspirateurs industriels, qui séparent les particules de poudre excédentaires de l’air avant de les rediriger vers le système de pulvérisation.
Un autre avantage important des chaînes de peinture en poudre est la réduction des émissions de composés organiques volatils (COV). Contrairement aux peintures liquides, qui contiennent souvent des solvants chimiques, la peinture en poudre est une solution sans solvant, ce qui réduit considérablement les émissions de COV et l’impact environnemental de la production. Cela permet aux entreprises de respecter plus facilement les réglementations environnementales strictes tout en améliorant la qualité de l’air dans l’atelier de production.
La maintenance des chaînes de peinture en poudre est facilitée par l’automatisation et la conception modulaire des équipements. Les systèmes de nettoyage automatisés, par exemple, permettent de nettoyer les pistolets de pulvérisation et les filtres sans interrompre le processus de production. Cela réduit les temps d’arrêt et améliore l’efficacité globale de la chaîne. De plus, les technologies de maintenance prédictive basées sur des capteurs et des systèmes d’analyse de données permettent d’anticiper les pannes et de planifier les entretiens avant que des défaillances majeures ne surviennent, ce qui réduit les coûts de maintenance et les interruptions de production.
Une autre caractéristique des chaînes de peinture en poudre modernes est leur capacité à garantir une finition de haute qualité sur une large gamme de matériaux. La peinture en poudre est utilisée non seulement sur les métaux, mais aussi sur des matériaux comme le plastique, le verre et le bois, à condition que la préparation de la surface soit adéquate. Les chaînes de peinture en poudre sont donc de plus en plus polyvalentes, ce qui permet aux entreprises de traiter différents types de pièces en fonction des exigences spécifiques du client.
Les cabines de peinture et les équipements associés sont également conçus pour garantir un environnement de travail propre et sécurisé. Des systèmes de filtration sophistiqués sont utilisés pour capturer la poussière de peinture et maintenir un air pur dans l’atelier de production. Les entreprises sont également de plus en plus conscientes de la sécurité des travailleurs, et de nombreuses chaînes de peinture en poudre sont équipées de dispositifs de sécurité comme des alarmes en cas de détection de niveaux élevés de poussière ou de chaleur.
Les chaînes de peinture en poudre sont également de plus en plus adaptées aux besoins de personnalisation des clients. Avec l’évolution des tendances et l’augmentation de la demande pour des finitions spécifiques (comme des effets texturés, métalliques ou nacrés), les équipements de peinture en poudre peuvent désormais être ajustés pour appliquer une large gamme de couleurs, de textures et d’effets spéciaux. Cela permet aux fabricants de répondre à des demandes variées et d’offrir des produits hautement personnalisés, tout en maintenant des coûts de production compétitifs.
Enfin, l’avenir des chaînes de peinture en poudre sera marqué par une amélioration continue de la connectivité et de l’intégration des systèmes. L’usage de la réalité augmentée (RA) et de l’intelligence artificielle (IA) pour le contrôle qualité et la gestion des opérations pourrait devenir plus courant. Ces technologies permettront d’analyser les données en temps réel, de détecter des anomalies dans l’application de la peinture et de prendre des décisions instantanées pour ajuster les paramètres de la ligne. Cela contribuera à améliorer l’efficacité et la constance de la production tout en réduisant les déchets et en optimisant la consommation des matériaux.
En résumé, la chaîne de peinture en poudre est un système de production de plus en plus sophistiqué, offrant des avantages significatifs en termes de qualité, d’efficacité et d’impact environnemental. Grâce à l’automatisation, la récupération de poudre, l’amélioration de la flexibilité et des performances énergétiques, ces chaînes continueront à évoluer pour répondre aux besoins des industries modernes et offrir des solutions durables et économiques pour l’application de revêtements en poudre.
Les chaînes de peinture en poudre continueront d’évoluer avec l’intégration de nouvelles technologies qui permettront d’augmenter l’automatisation et de réduire les interventions manuelles. Une des évolutions majeures sera la mise en œuvre de la technologie de l’Internet des objets (IoT), permettant à chaque équipement de la chaîne de peinture en poudre de communiquer et de s’auto-optimiser en fonction des conditions de production en temps réel. Cela pourrait inclure des ajustements automatiques de la vitesse de transport des pièces, de l’intensité de la pulvérisation ou de la température du four, afin de garantir une qualité constante tout au long du processus de peinture.
L’une des grandes avancées attendues est l’utilisation de l’intelligence artificielle (IA) pour améliorer encore plus la qualité et la précision de la finition. Par exemple, des systèmes de vision artificielle pourraient être utilisés pour détecter les défauts de surface dès l’application de la poudre, permettant une correction instantanée des paramètres de pulvérisation, voire une reconfiguration partielle de la ligne en cas de détection d’anomalies. Ces systèmes peuvent aussi analyser la répartition de la poudre sur les pièces en temps réel, assurant ainsi un revêtement uniforme et de qualité supérieure, même sur les pièces les plus complexes.
L’automatisation des processus de nettoyage et de maintenance sera également un facteur clé pour améliorer la productivité. Les systèmes de nettoyage automatisés de la chaîne de peinture en poudre permettront de réduire considérablement les temps d’arrêt pour entretien, ce qui est essentiel dans les environnements de production à haute cadence. En outre, les capteurs et l’analyse des données de performance permettront d’identifier les besoins en maintenance avant qu’une panne ne survienne, réduisant ainsi les coûts imprévus et augmentant la durée de vie des équipements.
Le développement de matériaux de peinture plus durables et écologiques est également en pleine expansion. Les entreprises investissent de plus en plus dans des formulations de poudres sans solvant et réduisant la présence de substances chimiques nocives, dans un souci de conformité aux normes environnementales de plus en plus strictes. Ces innovations incluent l’utilisation de poudres à base de matériaux recyclés ou de produits non toxiques, qui offrent des performances équivalentes tout en étant plus respectueuses de l’environnement.
Les aspects écologiques des chaînes de peinture en poudre continueront d’être améliorés grâce à des systèmes de recyclage plus efficaces, permettant de maximiser l’utilisation de la peinture en poudre. Le recyclage de la poudre excédentaire, combiné à des processus de récupération d’énergie dans les fours de durcissement, contribuera à rendre les chaînes de peinture plus économes en ressources. Par exemple, la récupération de chaleur des fours pourra être utilisée pour préchauffer les pièces avant leur entrée dans le four de durcissement, réduisant ainsi la consommation d’énergie.
Les chaînes de peinture en poudre auront également un rôle de plus en plus central dans la fabrication de produits personnalisés à la demande. La demande de personnalisation des produits finis est en hausse dans de nombreux secteurs industriels, ce qui pousse les fabricants à concevoir des lignes de production flexibles capables de gérer des séries de production petites ou très spécifiques. Cela pourrait inclure l’application de techniques de revêtement de plus en plus diverses, telles que l’application de poudres à effet texturé, métallisé ou nacré, ou encore la peinture de pièces de plus en plus complexes.
L’optimisation de la gestion des déchets est un autre aspect crucial pour l’avenir des chaînes de peinture en poudre. Les systèmes de collecte et de tri des déchets devront être de plus en plus sophistiqués, afin de trier les matériaux excédentaires, les poussières et les filtres usagés pour un recyclage maximal. Cela permettra non seulement de réduire l’impact environnemental du processus, mais aussi de réduire les coûts liés à l’élimination des déchets.
La durabilité et l’optimisation des chaînes de peinture en poudre auront également un impact sur la manière dont les entreprises conçoivent leurs chaînes de production. Les nouveaux modèles de fabrication se concentreront sur la flexibilité, l’évolutivité et la connectivité, permettant ainsi de réagir rapidement aux fluctuations de la demande, tout en maintenant un haut niveau de qualité et d’efficacité. Par exemple, des solutions modulaires pourraient permettre de modifier facilement les lignes de production en fonction des besoins, offrant ainsi une grande capacité d’adaptation aux exigences de différents clients ou de marchés en évolution rapide.
Enfin, la prise en compte de la sécurité et du bien-être des opérateurs restera essentielle. Les chaînes de peinture en poudre devront être dotées de dispositifs de sécurité renforcés, non seulement pour protéger contre les risques d’incendie ou d’explosion liés à l’utilisation de matériaux inflammables, mais aussi pour garantir un environnement de travail sain. Les systèmes de filtration de l’air devront être capables de capturer les plus petites particules de poussière, et des dispositifs d’alarme devront avertir immédiatement les opérateurs en cas de danger. Par ailleurs, la gestion de la sécurité sera également améliorée par l’automatisation des tâches répétitives et à risque, réduisant ainsi l’exposition des travailleurs aux risques associés à l’application de la peinture en poudre.
Dans l’ensemble, la chaîne de peinture en poudre de demain sera encore plus efficace, flexible et respectueuse de l’environnement. Grâce à l’intégration des technologies numériques, à l’optimisation des ressources, à des matériaux plus écologiques et à des processus automatisés, ces chaînes répondront aux défis de production moderne tout en offrant une qualité de finition exceptionnelle et en minimisant leur empreinte environnementale. Ces avancées contribueront à rendre le processus de peinture en poudre encore plus adapté aux besoins d’une industrie en constante évolution.
L’évolution continue des chaînes de peinture en poudre marquera aussi l’intégration des principes de fabrication intelligente et de gestion intégrée des ressources. Avec l’essor de l’Industrie 4.0, les chaînes de peinture en poudre se dirigeront vers des systèmes interconnectés où chaque élément de la production sera surveillé et optimisé en temps réel à l’aide de capteurs intelligents, de l’analyse de données massives (Big Data) et de l’intelligence artificielle. L’un des principaux bénéfices de cette numérisation sera la capacité de prédire et de prévenir les dysfonctionnements avant qu’ils ne surviennent, permettant ainsi de minimiser les arrêts de production et d’optimiser les performances globales des chaînes de peinture.
Les solutions basées sur le cloud, associées à des systèmes d’analytique avancée, permettront aux opérateurs de visualiser et de gérer le processus de peinture en temps réel, où qu’ils se trouvent. Les données recueillies par les capteurs installés sur chaque composant de la ligne de peinture pourront être utilisées pour ajuster instantanément les paramètres du processus, tels que la vitesse du convoyeur, la quantité de poudre utilisée, ou la température du four de durcissement. Cela permettra non seulement d’améliorer la précision et la consistance du produit fini, mais aussi de rendre le processus plus réactif aux changements de conditions de production.
De plus, l’adoption de la réalité augmentée (RA) dans le cadre des opérations de maintenance et de formation pourrait transformer la manière dont les employés interagissent avec la chaîne de peinture. Les casques de réalité augmentée pourraient permettre aux techniciens de superposer des informations en temps réel directement sur leurs champs de vision pendant qu’ils effectuent des tâches de maintenance. Par exemple, un technicien pourrait voir les schémas des systèmes de pulvérisation ou du réseau de filtration projetés dans leur champ de vision, ce qui facilitera les réparations et optimisera le temps consacré à la maintenance préventive.
Une autre tendance émergente est la personnalisation en masse. L’industrie de la peinture en poudre se dirige vers un modèle de production où les chaînes peuvent rapidement s’adapter pour peindre des lots de tailles variables et des produits hautement personnalisés. Cela pourrait inclure la possibilité de changer facilement les couleurs, les textures ou les effets sur une même ligne de production sans nécessiter de réajustements complexes ou de longs temps d’arrêt. Cette flexibilité est particulièrement importante dans des secteurs comme l’automobile ou l’électroménager, où les clients recherchent des produits de plus en plus personnalisés tout en maintenant des coûts de production compétitifs.
En outre, l’efficacité de la chaîne de peinture en poudre sera renforcée par l’utilisation de matériaux de plus en plus innovants. Les fabricants se concentreront sur le développement de poudres à base de matériaux alternatifs, comme des poudres plus légères, des revêtements plus résistants, ou des formules capables de répondre à des exigences spécifiques, comme la résistance aux produits chimiques, à l’humidité ou aux températures extrêmes. Cela permettra aux chaînes de peinture de s’adapter à des besoins industriels de plus en plus diversifiés et exigeants, tout en offrant des solutions plus durables et respectueuses de l’environnement.
À mesure que les chaînes de peinture en poudre deviendront de plus en plus sophistiquées, la question de la durabilité deviendra un aspect central de leur développement. L’utilisation de matériaux recyclés, le recyclage de la poudre excédentaire et la gestion optimisée des déchets seront au cœur des préoccupations des industriels. De nouveaux systèmes de filtration et de traitement de l’air devraient être développés pour capturer encore plus efficacement les microparticules de peinture et pour garantir un environnement de travail toujours plus sûr et plus propre.
Enfin, la croissance des marchés émergents et l’internationalisation des chaînes de production vont poser de nouveaux défis pour les fabricants de chaînes de peinture en poudre. Pour répondre à la demande croissante dans des régions telles que l’Asie, l’Afrique ou l’Amérique du Sud, les équipements de peinture devront être adaptés à des conditions locales variées, comme des exigences de production plus flexibles, des contraintes économiques, ou des normes écologiques spécifiques. Les fabricants devront aussi prendre en compte les différences culturelles et les attentes des consommateurs en termes de qualité, de finitions et de personnalisation.
En conclusion, l’avenir des chaînes de peinture en poudre réside dans l’intégration des dernières technologies d’automatisation, de digitalisation, et d’optimisation énergétique. Ces avancées permettront non seulement d’améliorer l’efficacité et la durabilité des processus de peinture, mais aussi de répondre à une demande croissante pour des produits plus personnalisés, plus écologiques et plus performants. Grâce à des innovations constantes dans les matériaux, les équipements et la gestion des données, les chaînes de peinture en poudre de demain deviendront plus intelligentes, plus flexibles et plus respectueuses de l’environnement, offrant ainsi une réponse adaptée aux défis industriels modernes.
Conclusion
Le temps nécessaire pour l’installation d’un four à thermolaquage varie en fonction de nombreux facteurs, mais une planification et une exécution soignées peuvent contribuer à optimiser le processus. En collaborant avec des professionnels expérimentés et en assurant une préparation adéquate du site et de l’équipe, les entreprises peuvent s’assurer que leur nouvel équipement est opérationnel et productif le plus rapidement possible.
Le Revêtement en Poudre
L’équipement de revêtement en poudre est utilisé pour appliquer une fine couche de poudre sur une surface métallique. Ce type de revêtement est appliqué par un procédé électrostatique et constitue une méthode très populaire pour la finition des pièces métalliques.
Ce type d’équipement peut être divisé en deux grandes catégories : automatiques et manuels. Les cabines automatiques sont plus populaires car elles offrent de meilleurs taux de production, mais elles sont également plus chères.
Une cabine à poudre est une enceinte dans laquelle se déroule le processus de revêtement en poudre. L’équipement de revêtement en poudre comprend un four dans lequel les pièces sont chauffées pour activer la poudre, un pistolet qui pulvérise ou brosse la poudre, une bande transporteuse qui déplace les pièces à travers le four et des pistolets de type cartouche pour appliquer des revêtements plus épais avec moins de pulvérisation.
Le revêtement en poudre est une technique utilisée pour donner une finition aux pièces métalliques. Cette technique est utilisée depuis de nombreuses années et reste aujourd’hui l’une des techniques les plus populaires.
L’équipement de revêtement en poudre comprend des cabines, des fours, des pistolets, des machines, des lignes et des convoyeurs. Une cabine peut être automatique ou manuelle. Une cabine automatique est plus chère qu’une cabine manuelle mais elle est aussi plus rapide et plus efficace