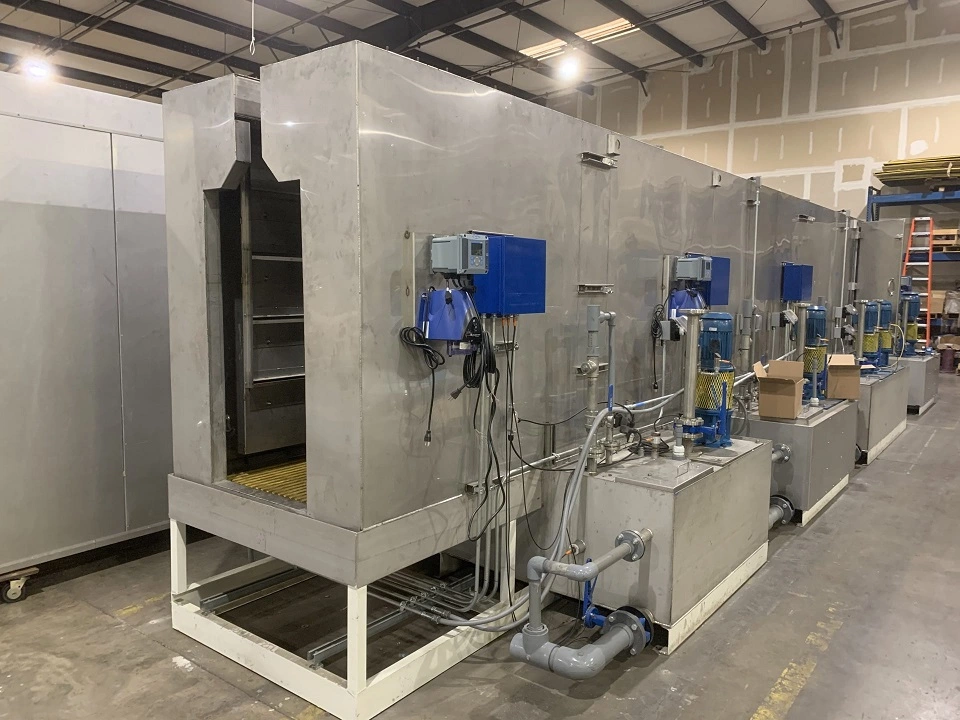
Le lavage au phosphate avant le revêtement en poudre est une étape courante dans le processus de prétraitement de surface. Cette méthode est utilisée pour préparer les pièces métalliques avant l’application du revêtement en poudre, en améliorant l’adhérence du revêtement et en augmentant la résistance à la corrosion. Voici les points clés du lavage au phosphate dans le contexte du revêtement en poudre :
Objectifs du Lavage au Phosphate :
- Élimination des Contaminants : Le lavage au phosphate élimine les contaminants tels que les résidus d’huile, les particules de poussière, les oxydes et autres impuretés de la surface des pièces métalliques. Cela crée une surface propre et préparée pour le revêtement.
- Conversion de Surface : Le phosphate forme une couche de conversion de surface, généralement sous la forme d’une couche de phosphate de zinc, qui améliore l’adhérence du revêtement en poudre à la surface métallique.
- Augmentation de la Résistance à la Corrosion : La couche de phosphate agit comme une barrière protectrice contre la corrosion, améliorant la durabilité et la résistance des pièces métalliques aux environnements corrosifs.
Étapes du Processus de Lavage au Phosphate :
- Dégraissage : Avant le lavage au phosphate, les pièces métalliques peuvent subir un dégraissage pour éliminer les huiles et graisses.
- Prétraitement Acide : Certaines lignes de prétraitement de surface incluent une étape de prétraitement acide avant le lavage au phosphate pour nettoyer la surface métallique en profondeur.
- Lavage au Phosphate : Les pièces sont immergées dans une solution de phosphate. Cette solution peut contenir divers composés, tels que des phosphates de zinc, de fer ou de manganèse, en fonction des exigences spécifiques du processus.
- Rinçage : Après le lavage au phosphate, les pièces sont soigneusement rincées pour éliminer tout résidu de la solution de phosphate.
- Séchage : Les pièces sont séchées correctement avant de passer à l’étape suivante du processus.
Contrôle de la Qualité :
Des tests de contrôle de la qualité peuvent être effectués pour vérifier l’efficacité du lavage au phosphate. Cela peut inclure des tests d’adhérence du revêtement, des tests de corrosion, et d’autres analyses pour s’assurer que la surface est correctement préparée.
Considérations Importantes :
- Variation des Solutions de Phosphate : Les solutions de phosphate peuvent varier en composition en fonction du matériau des pièces à traiter et des spécifications du processus. Des ajustements peuvent être nécessaires pour répondre aux besoins spécifiques.
- Environnement : Le traitement au phosphate peut avoir des implications environnementales en raison des produits chimiques utilisés. Il est important de respecter les réglementations environnementales en vigueur et de mettre en place des pratiques de gestion appropriées.
Le lavage au phosphate est une étape importante dans le prétraitement de surface avant le revêtement en poudre, contribuant à améliorer l’adhérence et la durabilité du revêtement final.
Le lavage au phosphate avant le revêtement en poudre est un procédé essentiel dans la préparation des surfaces métalliques, permettant d’améliorer l’adhérence du revêtement et d’assurer une protection durable contre la corrosion. Ce processus consiste à appliquer une solution de phosphate, généralement sous forme de phosphate de zinc ou de fer, sur la surface des pièces métalliques pour créer une couche protectrice et microporeuse. Cette couche sert de base idéale pour l’application du revêtement en poudre, car elle favorise l’accroche du revêtement tout en offrant une résistance accrue aux agressions environnementales telles que l’humidité et les produits chimiques.
Le processus de lavage au phosphate commence par un dégraissage minutieux de la surface. Cette étape est cruciale, car la présence de graisses, huiles, ou autres contaminants sur la surface peut nuire à l’efficacité du traitement phosphaté et à l’adhérence du revêtement en poudre. Le dégraissage peut être effectué à l’aide de solutions alcalines, de solvants ou de nettoyants spécialisés, en fonction du type de matériau traité et de la nature des contaminants. Une fois la surface débarrassée de toute impureté, elle est prête à recevoir la solution de phosphate.
Le lavage au phosphate se fait généralement dans des bains spécifiques, où les pièces métalliques sont immergées ou pulvérisées avec la solution chimique. Le choix du type de phosphate dépend du métal traité : le phosphate de zinc est souvent utilisé pour les métaux ferreux tels que l’acier, tandis que le phosphate de fer est plus adapté aux alliages légers comme l’aluminium. L’application de la solution de phosphate crée une fine couche qui adhère fortement à la surface métallique, formant un revêtement durable et résistant. Cette couche est microscopique, mais elle améliore de manière significative la résistance à la corrosion et prépare la surface pour l’application du revêtement en poudre.
Le processus de lavage au phosphate est généralement suivi de plusieurs étapes de rinçage pour éliminer les résidus de produits chimiques, ainsi que de séchage. Le rinçage est important pour éviter que des traces de phosphate ou de détergents ne restent sur les pièces, ce qui pourrait nuire à la qualité du revêtement. Après le séchage, la pièce est prête pour l’application du revêtement en poudre. Le revêtement en poudre, une fois appliqué, est durci par un passage au four, où il fond et forme une couche lisse et uniforme qui protège la pièce tout en améliorant son aspect esthétique.
L’un des principaux avantages du lavage au phosphate avant le revêtement en poudre est la protection contre la corrosion. La couche de phosphate crée une barrière qui empêche l’humidité et les produits chimiques de pénétrer dans le métal sous-jacent, réduisant ainsi le risque d’oxydation et de détérioration. De plus, le processus améliore l’adhérence du revêtement en poudre, ce qui garantit que le revêtement reste intact pendant une période prolongée, même dans des environnements difficiles. Cette étape est donc cruciale pour assurer la durabilité des pièces traitées, en particulier dans les secteurs où la résistance à la corrosion est essentielle, comme dans l’automobile, l’aéronautique, ou l’industrie des équipements extérieurs.
En outre, le lavage au phosphate est également bénéfique pour la préparation de surfaces complexes ou difficiles d’accès. Les solutions de phosphate pénètrent bien dans les recoins et assurent un traitement uniforme de toutes les zones de la pièce. Cela est particulièrement important pour les pièces aux formes irrégulières, où une préparation de surface uniforme est indispensable pour garantir un revêtement de haute qualité.
Le lavage au phosphate avant l’application du revêtement en poudre présente également des avantages économiques. Bien que l’investissement initial pour mettre en place des systèmes de lavage et de phosphatation puisse être conséquent, les économies réalisées à long terme sont notables. En effet, un traitement de surface adéquat permet de prolonger la durée de vie des pièces, de réduire les coûts de maintenance et d’améliorer la performance des produits finis. De plus, la possibilité de récupérer et de recycler les solutions de phosphate dans un système fermé permet de réduire les consommations et de minimiser l’impact environnemental du processus.
Malgré ses nombreux avantages, le lavage au phosphate avant le revêtement en poudre nécessite une gestion rigoureuse des paramètres de traitement pour obtenir des résultats optimaux. Les bains doivent être soigneusement entretenus pour garantir leur efficacité, et des contrôles réguliers sont nécessaires pour s’assurer que la solution chimique reste dans les conditions appropriées. Un suivi précis des concentrations de phosphate, du pH de la solution et de la température des bains est essentiel pour garantir une couche uniforme et adhérente. Les pièces doivent également être correctement séchées avant le revêtement pour éviter toute contamination ou défaut dans la finition.
En somme, le lavage au phosphate avant le revêtement en poudre est un processus indispensable pour préparer les surfaces métalliques, améliorer la résistance à la corrosion et garantir une finition de haute qualité. Ce procédé combine efficacité, durabilité et rentabilité, faisant de lui une étape incontournable dans de nombreux secteurs industriels. Avec la montée en puissance des préoccupations environnementales et des normes de qualité de plus en plus strictes, le lavage au phosphate continue d’évoluer, intégrant des technologies plus écologiques et plus efficaces pour répondre aux besoins croissants des industries modernes.
Les cabines de lavage manuel se distinguent par leur flexibilité et leur simplicité d’utilisation. Ces installations permettent aux opérateurs de contrôler directement le processus de nettoyage, ce qui est particulièrement utile pour les pièces complexes ou fragiles nécessitant une attention particulière. Dotées de buses haute pression, de systèmes de filtration et parfois d’équipements d’aspiration, ces cabines garantissent un nettoyage précis et en profondeur. Elles sont généralement utilisées dans des environnements où le volume de pièces à nettoyer est modéré, ou lorsque les exigences spécifiques du nettoyage ne peuvent être entièrement automatisées. Les opérateurs, souvent protégés par des gants et des écrans de sécurité, peuvent manipuler les objets directement dans la cabine tout en utilisant des détergents, des solvants ou de l’eau sous pression. Ces cabines sont idéales pour les ateliers mécaniques, les laboratoires, ou encore les industries nécessitant une personnalisation des opérations de nettoyage.
En revanche, les tunnels de lavage automatique sont conçus pour des environnements où le débit de pièces à nettoyer est élevé. Ils sont équipés de systèmes sophistiqués qui automatisent entièrement le processus, réduisant ainsi la nécessité d’une intervention humaine. Ces équipements fonctionnent généralement par un convoyeur qui transporte les pièces à travers différentes étapes de lavage, de rinçage et de séchage. Grâce à leur conception modulaire, ils peuvent être adaptés pour répondre à des besoins spécifiques, tels que le nettoyage de grandes quantités de pièces uniformes ou le respect des normes de propreté stricte, comme celles imposées dans les industries alimentaire, pharmaceutique ou automobile. Les tunnels utilisent souvent des jets d’eau chaude, des détergents, ou des solutions chimiques spécifiques pour éliminer les contaminants. Certains systèmes intègrent également des technologies avancées telles que les ultrasons, le rayonnement UV ou des cycles de désinfection thermique.
Ces deux solutions présentent des avantages distincts qui répondent à des besoins variés. Les cabines de lavage manuel offrent une plus grande adaptabilité et sont idéales pour le traitement de petites séries ou d’objets complexes. Les tunnels automatiques, quant à eux, privilégient l’efficacité et la rapidité, ce qui les rend parfaits pour des processus à grande échelle. Toutefois, le choix entre ces deux systèmes dépendra principalement des exigences spécifiques de l’utilisateur, de la nature des pièces à nettoyer, du niveau de propreté requis, et des contraintes économiques.
En termes de durabilité, les fabricants de ces équipements cherchent de plus en plus à intégrer des technologies écologiques pour réduire la consommation d’eau, d’énergie et de produits chimiques. Les systèmes de recyclage d’eau, les pompes à haut rendement et les solutions de nettoyage à faible impact environnemental sont aujourd’hui couramment incorporés dans ces équipements. Cela reflète une tendance globale vers une industrie plus responsable et soucieuse des enjeux environnementaux.
Ainsi, qu’il s’agisse de garantir la propreté de pièces mécaniques, d’assurer une hygiène irréprochable dans l’industrie alimentaire, ou de préparer des composants pour des processus critiques, les cabines de lavage manuel et les tunnels de lavage automatique restent des éléments indispensables dans de nombreuses chaînes de production modernes.
Cabines de lavage manuel et tunnels de lavage automatique
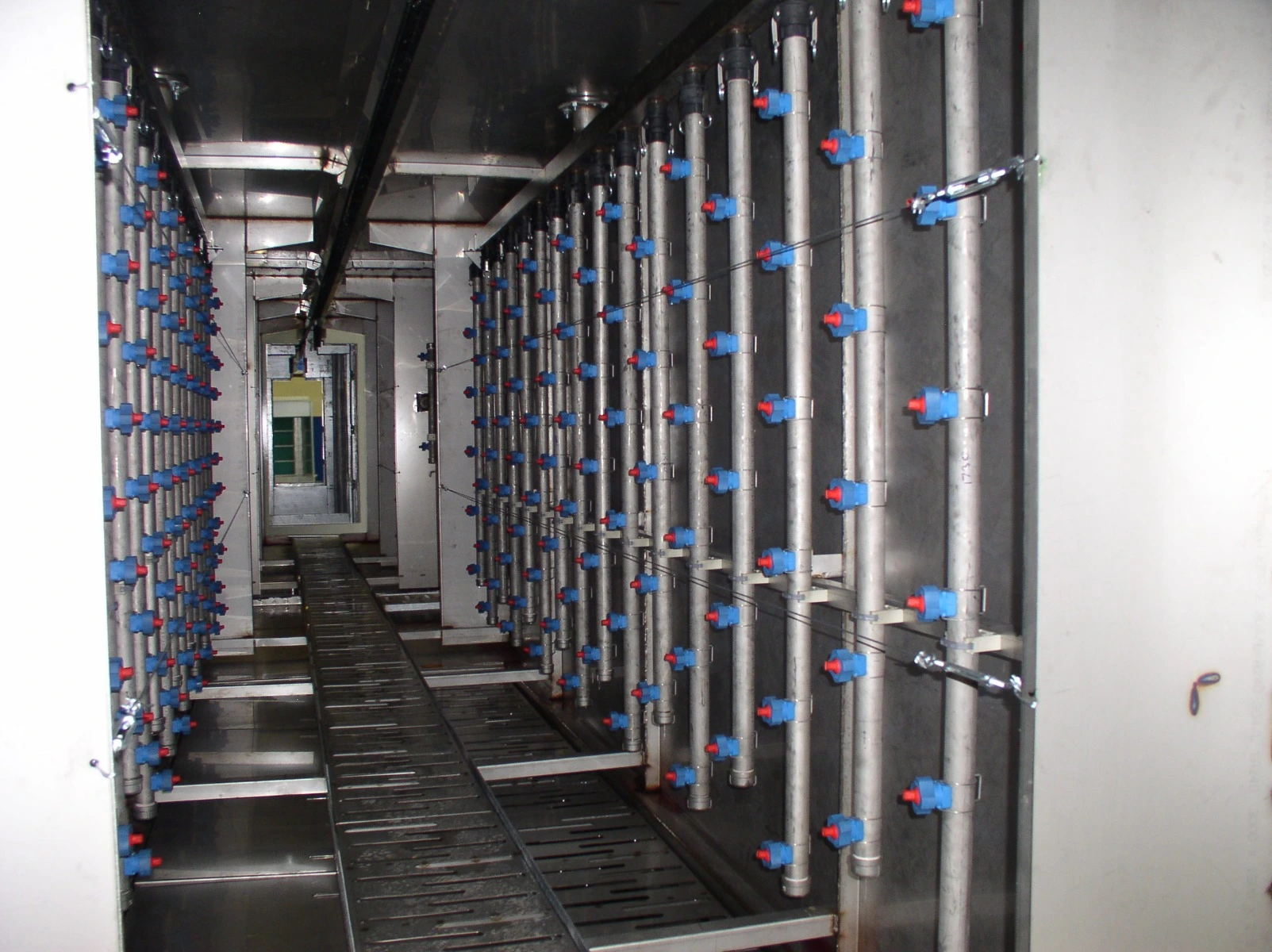
En complément, il est essentiel de souligner que le succès d’une installation de lavage, qu’il s’agisse d’une cabine de lavage manuel ou d’un tunnel de lavage automatique, repose également sur une maintenance rigoureuse et une formation appropriée des opérateurs ou techniciens. La maintenance préventive joue un rôle crucial pour assurer le bon fonctionnement des équipements et prolonger leur durée de vie. Dans le cas des cabines de lavage manuel, il est important de surveiller régulièrement l’état des buses, des systèmes de filtration et des joints pour éviter les fuites ou les baisses de pression qui pourraient affecter l’efficacité du nettoyage. Pour les tunnels automatiques, des vérifications périodiques des convoyeurs, des pompes, des capteurs et des systèmes de dosage des détergents permettent de garantir un fonctionnement optimal et d’éviter des arrêts imprévus.
Une autre dimension importante est la personnalisation de ces systèmes en fonction des besoins spécifiques des utilisateurs. Les fabricants proposent souvent des solutions modulaires permettant d’ajouter ou de modifier des fonctionnalités, telles que des options de séchage par air chaud, des systèmes de filtration avancés ou des cycles de désinfection à la vapeur. Cette flexibilité est particulièrement précieuse dans des secteurs où les exigences évoluent rapidement, comme dans l’aéronautique, la santé ou l’électronique. Par exemple, pour le nettoyage de composants électroniques sensibles, les cabines et tunnels peuvent être équipés de dispositifs empêchant toute contamination par des particules ou des résidus chimiques.
Par ailleurs, l’intégration de technologies numériques révolutionne également ce domaine. Les systèmes modernes de lavage automatique intègrent de plus en plus des capteurs IoT (Internet des objets) pour surveiller en temps réel des paramètres critiques tels que la température, la pression, le débit d’eau ou la concentration des produits de nettoyage. Ces données sont collectées et analysées pour optimiser le processus de lavage, réduire les coûts opérationnels et minimiser l’impact environnemental. Certains systèmes avancés permettent même une maintenance prédictive grâce à l’analyse des données, évitant ainsi les pannes potentielles et améliorant la fiabilité globale de l’installation.
Le choix entre une cabine de lavage manuel et un tunnel automatique repose également sur une analyse des coûts. Bien que les cabines soient généralement moins coûteuses à l’achat, leur exploitation peut nécessiter davantage de main-d’œuvre, ce qui augmente les coûts à long terme dans des environnements à forte intensité de nettoyage. Les tunnels automatiques, bien que nécessitant un investissement initial plus important, offrent des économies significatives en réduisant le temps d’opération et en améliorant la productivité, ce qui les rend rentables pour les grandes entreprises industrielles.
Enfin, il convient de considérer l’impact réglementaire et environnemental. Dans de nombreux secteurs, des réglementations strictes imposent des niveaux de propreté élevés, particulièrement dans les industries pharmaceutique et alimentaire, où la sécurité des consommateurs est primordiale. Les fabricants d’équipements de lavage adaptent leurs conceptions pour répondre à ces exigences, en utilisant des matériaux résistants à la corrosion, en garantissant une élimination complète des résidus, et en intégrant des systèmes pour réduire les émissions de déchets chimiques.
En résumé, les cabines de lavage manuel et les tunnels de lavage automatique sont des solutions complémentaires, chacune ayant des avantages et des limitations. Tandis que les cabines permettent un contrôle manuel et précis, idéal pour les petites séries ou les pièces complexes, les tunnels offrent une efficacité inégalée pour le traitement de grands volumes dans des délais courts. Ces technologies, en constante évolution, s’inscrivent dans une dynamique où l’innovation, l’écologie et l’efficacité se combinent pour répondre aux besoins diversifiés des industries modernes.
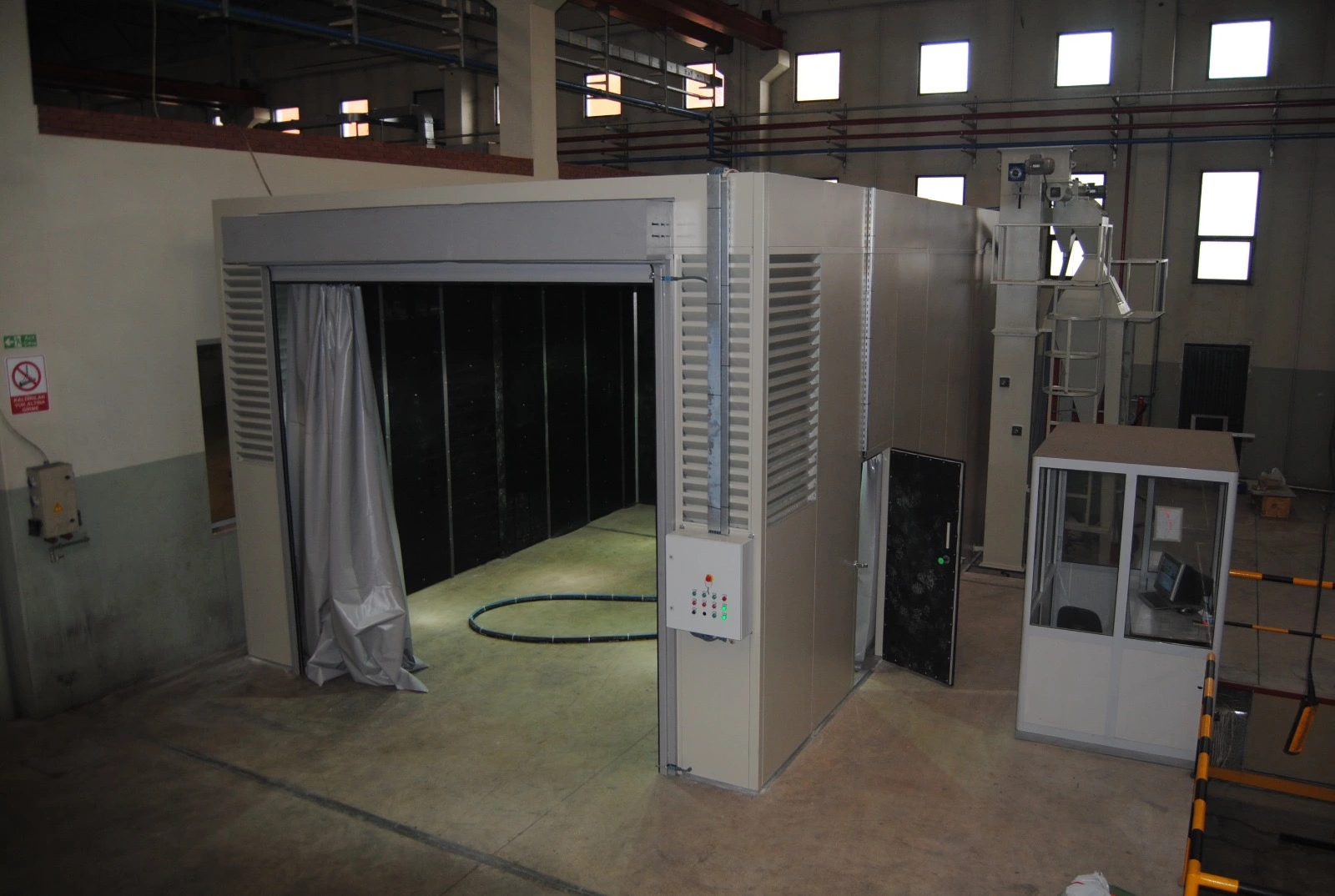
Au-delà des aspects techniques et opérationnels, l’impact environnemental des cabines de lavage manuel et des tunnels de lavage automatique mérite une attention particulière, surtout dans le contexte actuel où les préoccupations écologiques occupent une place centrale dans les politiques industrielles. La gestion responsable de l’eau, de l’énergie et des produits chimiques utilisés dans ces systèmes est un défi majeur, mais elle offre également des opportunités d’optimisation et d’innovation.
Pour les cabines de lavage manuel, la consommation d’eau peut être réduite grâce à l’utilisation de buses à haute pression qui nécessitent moins d’eau pour un nettoyage efficace. De plus, des systèmes de recyclage d’eau peuvent être intégrés, permettant de réutiliser l’eau après filtration et séparation des résidus. Certains modèles modernes incluent des filtres avancés capables de capturer même les particules microscopiques et les huiles, garantissant ainsi une eau propre pour chaque cycle de lavage. Cette approche non seulement réduit la consommation d’eau, mais diminue également les coûts liés au traitement des eaux usées.
Les tunnels de lavage automatique, en raison de leur échelle et de leur conception, offrent un potentiel encore plus grand pour intégrer des solutions durables. Par exemple, certains tunnels sont dotés de zones de rinçage multiples où l’eau propre est utilisée en dernier, puis récupérée pour les cycles de pré-lavage. Ce système en cascade optimise l’utilisation de l’eau tout en garantissant des résultats impeccables. De plus, la récupération de chaleur issue de l’eau chaude utilisée dans les cycles de lavage peut être exploitée pour préchauffer l’eau entrante, réduisant ainsi la consommation d’énergie.
En termes de produits chimiques, la tendance est à l’utilisation de détergents biodégradables ou de solutions aqueuses à faible toxicité. Cela permet de minimiser l’impact sur l’environnement tout en respectant les réglementations de plus en plus strictes en matière de rejets industriels. Les systèmes automatisés de dosage jouent également un rôle clé, en s’assurant que la quantité de produit utilisée est précisément adaptée à chaque cycle, évitant ainsi tout gaspillage ou surdosage.
Les évolutions technologiques contribuent également à transformer ces systèmes en plateformes intelligentes et connectées. Par exemple, les logiciels de gestion de cycle permettent de configurer et de personnaliser les paramètres pour différents types de pièces ou de matériaux, garantissant ainsi un nettoyage optimal tout en évitant un usage excessif des ressources. Ces outils offrent également la possibilité de surveiller l’impact environnemental des opérations en temps réel, comme le volume d’eau utilisé, les émissions de CO₂ ou la quantité de déchets produits.
Un autre point clé est l’ergonomie et la sécurité des utilisateurs, en particulier dans les cabines de lavage manuel. Ces équipements doivent être conçus pour réduire les risques d’exposition des opérateurs aux produits chimiques et aux éclaboussures. Les cabines modernes sont souvent équipées de systèmes d’aspiration pour éliminer les vapeurs ou les particules en suspension, ainsi que de dispositifs de sécurité, tels que des interrupteurs d’arrêt d’urgence et des parois transparentes renforcées.
Dans les tunnels automatiques, la sécurité repose davantage sur des systèmes de contrôle intégrés. Des capteurs détectent la présence de pièces mal positionnées ou bloquées, tandis que des dispositifs de verrouillage empêchent l’ouverture des portes pendant les cycles en cours. Ces mesures non seulement protègent les opérateurs, mais évitent également les dommages aux pièces ou à l’équipement.
En conclusion, les cabines de lavage manuel et les tunnels de lavage automatique ne sont pas simplement des outils fonctionnels ; ils s’inscrivent dans une vision plus large de l’efficacité industrielle et de la durabilité environnementale. Leur développement continu est porté par des innovations technologiques, une adaptation aux besoins spécifiques des industries, et une prise de conscience accrue des impacts écologiques. Ces équipements restent des alliés indispensables pour garantir des standards élevés de propreté, de qualité et de sécurité, tout en répondant aux défis économiques et environnementaux du XXIe siècle.
Les cabines de lavage manuel et les tunnels de lavage automatique représentent deux solutions distinctes mais complémentaires dans le domaine du nettoyage industriel, en particulier dans les secteurs nécessitant un entretien méticuleux des équipements, des pièces et des composants. Le choix entre ces deux technologies dépend principalement des exigences spécifiques du processus de lavage, du volume de pièces à traiter, ainsi que des standards de propreté exigés par l’industrie.
Les cabines de lavage manuel offrent une solution flexible, permettant un nettoyage précis et adapté aux besoins spécifiques des pièces complexes ou délicates. Ces cabines sont généralement utilisées lorsqu’il est nécessaire d’apporter une attention particulière à des zones difficiles d’accès ou lorsque les contaminations doivent être éliminées avec un contrôle visuel rigoureux. Le lavage manuel implique souvent l’intervention d’un opérateur équipé de divers outils, tels que des lances à haute pression, des brosses ou des pistolets d’air comprimé, afin de garantir un nettoyage en profondeur. La cabine est conçue pour confiner les éclaboussures et les résidus, assurant ainsi un environnement de travail propre et sécurisé. L’utilisation de détergents ou de solutions spécifiques dépend du type de salissures à éliminer, qu’il s’agisse de graisses, d’huiles, de poussières ou de résidus métalliques.
En revanche, les tunnels de lavage automatique sont conçus pour le traitement en série de grandes quantités de pièces, offrant une solution efficace pour des besoins industriels à haut débit. Ces systèmes automatisés permettent un gain de temps considérable, car les pièces sont convoyées à travers différentes étapes de lavage sans nécessiter d’intervention humaine. Les tunnels de lavage fonctionnent généralement selon un processus multi-étapes comprenant le prélavage, le lavage principal, le rinçage et le séchage. Les jets haute pression, combinés à des détergents spécifiques, assurent l’élimination des contaminants même sur des surfaces complexes ou peu accessibles. Le réglage précis des paramètres tels que la température, la pression de l’eau et le temps de traitement permet d’atteindre des niveaux de propreté conformes aux normes les plus strictes. Les tunnels de lavage automatique sont souvent utilisés dans les industries automobile, aéronautique et mécanique, où le volume élevé et la rapidité d’exécution sont des critères essentiels.
L’avantage principal des cabines de lavage manuel réside dans leur flexibilité et leur capacité à traiter des pièces uniques, fragiles ou aux géométries complexes. Elles conviennent particulièrement aux opérations de maintenance, aux réparations ou aux petits lots de production. En revanche, leur principal inconvénient est la dépendance à la main-d’œuvre et le temps nécessaire pour effectuer chaque opération de lavage. Cette solution peut donc s’avérer moins rentable pour les entreprises nécessitant des cadences élevées.
Les tunnels de lavage automatique, quant à eux, offrent une productivité accrue grâce à leur capacité à traiter un grand nombre de pièces en un temps réduit, avec une uniformité et une régularité du nettoyage difficilement atteignables par un opérateur humain. Toutefois, l’investissement initial dans ce type d’équipement est généralement plus élevé et nécessite un espace conséquent au sein des installations. De plus, leur fonctionnement automatisé peut poser des limites dans le cas de pièces aux formes très irrégulières ou nécessitant un nettoyage spécifique.
En résumé, le choix entre une cabine de lavage manuel et un tunnel de lavage automatique dépend des besoins propres à chaque industrie ou entreprise. Les cabines manuelles sont idéales pour des tâches nécessitant de la précision et de l’adaptabilité, tandis que les tunnels automatiques sont privilégiés pour des productions en série nécessitant un haut rendement et une constance de nettoyage. Ces deux technologies peuvent d’ailleurs coexister au sein d’une même installation pour répondre à différents besoins de nettoyage, assurant ainsi une flexibilité optimale et une efficacité accrue dans les processus industriels.
Cabines de lavage manuel et tunnels de lavage automatique
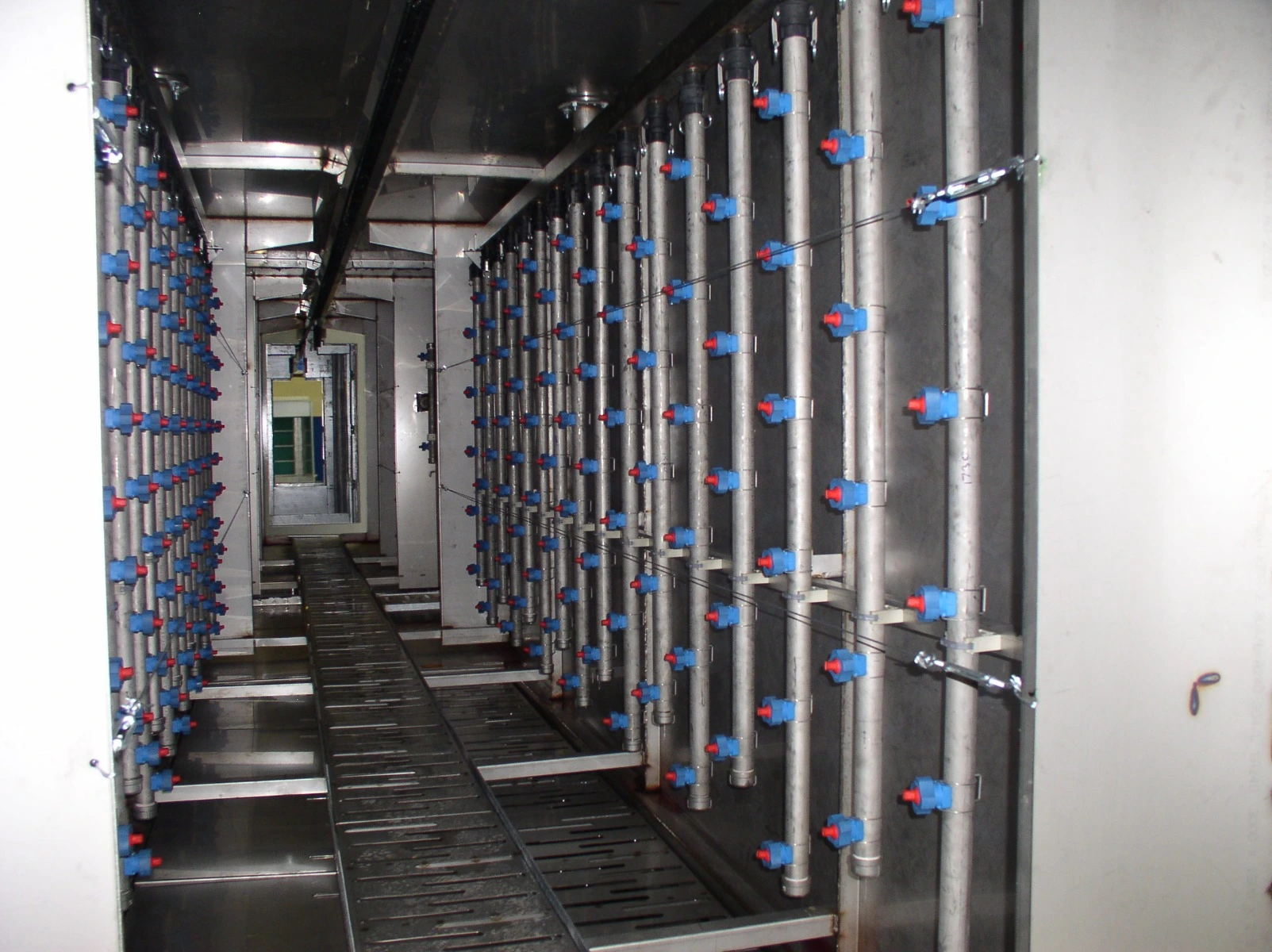
L’intégration de ces deux systèmes au sein d’une même chaîne de production permet de tirer parti des avantages de chaque technologie pour répondre aux diverses exigences du nettoyage industriel. Par exemple, les cabines de lavage manuel peuvent être utilisées pour des interventions ponctuelles ou pour traiter des pièces spécifiques nécessitant une attention particulière, tandis que les tunnels de lavage automatique assurent le traitement continu et systématique de grandes séries de pièces.
Les cabines de lavage manuel se déclinent en plusieurs variantes adaptées aux besoins industriels. Certaines cabines offrent des systèmes de recyclage de l’eau, permettant de réduire la consommation en eau et en produits chimiques. Cette fonctionnalité est particulièrement bénéfique dans les industries où les préoccupations environnementales et les coûts d’exploitation sont des priorités. Par ailleurs, les cabines peuvent être équipées de systèmes d’aspiration pour éliminer les vapeurs et les particules, améliorant ainsi les conditions de travail des opérateurs. L’éclairage intégré, souvent à LED, et les parois vitrées permettent une meilleure visibilité des zones à nettoyer, ce qui est essentiel pour garantir une qualité de lavage optimale.
Les tunnels de lavage automatique, quant à eux, continuent d’évoluer grâce à l’intégration des nouvelles technologies. Les systèmes modernes sont souvent dotés de capteurs intelligents permettant de surveiller en temps réel les paramètres de lavage, tels que la température, la pression ou encore la concentration en détergent. Ces capteurs assurent une qualité de lavage constante tout en optimisant la consommation des ressources. De plus, l’automatisation accrue des tunnels permet de réduire les coûts liés à la main-d’œuvre et d’améliorer la rentabilité globale de l’entreprise. Certains modèles sont également conçus pour s’adapter à des pièces de tailles et de formes variées grâce à des convoyeurs ajustables et des buses de lavage orientables.
L’aspect environnemental joue également un rôle clé dans le développement de ces technologies. Les industriels sont de plus en plus confrontés à des réglementations strictes concernant la gestion des eaux usées et des produits chimiques. Les fabricants de cabines et de tunnels de lavage mettent donc l’accent sur des solutions écologiques, telles que l’utilisation de détergents biodégradables, la récupération des eaux usées et leur traitement avant rejet, ainsi que la réduction de la consommation d’énergie grâce à des systèmes de chauffage optimisés.
Un autre aspect à considérer est la maintenance de ces équipements. Les cabines de lavage manuel, de par leur conception simple, nécessitent généralement un entretien réduit et peuvent être rapidement mises en service. En revanche, les tunnels de lavage automatique, plus complexes, exigent une maintenance régulière pour garantir leur bon fonctionnement sur le long terme. Cela inclut le nettoyage des buses, le remplacement des filtres et la vérification des convoyeurs et des systèmes de chauffage. Toutefois, de nombreux modèles récents intègrent des fonctionnalités d’auto-diagnostic permettant de détecter rapidement les pannes et d’anticiper les opérations de maintenance.
Enfin, la formation des opérateurs est un facteur clé pour maximiser l’efficacité des cabines de lavage manuel et des tunnels de lavage automatique. Dans le cas des cabines, les opérateurs doivent être formés à l’utilisation des équipements et à l’application des techniques de lavage appropriées pour garantir un nettoyage de qualité. Pour les tunnels automatiques, la formation se concentre sur la configuration des paramètres de lavage et sur la supervision du processus afin d’assurer un fonctionnement optimal.
En conclusion, les cabines de lavage manuel et les tunnels de lavage automatique répondent à des besoins complémentaires dans le domaine du nettoyage industriel. Leur sélection repose sur des critères tels que le volume de production, la complexité des pièces, les exigences de propreté, ainsi que les contraintes budgétaires et environnementales. Grâce aux avancées technologiques, ces solutions continuent d’évoluer pour offrir des performances accrues, une meilleure efficacité énergétique et un respect renforcé des normes environnementales. L’association judicieuse de ces deux systèmes permet aux industries de garantir un nettoyage de qualité tout en optimisant leurs processus de production.
1. Introduction aux systèmes de lavage industriel
Les systèmes de lavage industriel, tels que les cabines de lavage manuel et les tunnels de lavage automatique, sont essentiels pour garantir la propreté des pièces et équipements dans des secteurs variés comme l’automobile, l’aéronautique, la mécanique, et bien d’autres. Ces technologies assurent l’élimination des contaminants (graisses, huiles, poussières métalliques) en respectant des normes strictes de propreté.
2. Cabines de lavage manuel : caractéristiques et avantages
Les cabines de lavage manuel sont conçues pour offrir une solution flexible et précise dans le nettoyage des pièces complexes ou délicates.
Caractéristiques principales :
- Conception fermée : Évite les éclaboussures et limite les contaminants dans l’environnement de travail.
- Intervention humaine : Permet un contrôle visuel minutieux et un nettoyage ciblé des zones difficiles d’accès.
- Outils variés : Lances haute pression, brosses, air comprimé.
- Systèmes écologiques : Recyclage des eaux et des détergents pour limiter l’impact environnemental.
Avantages :
- Adaptabilité aux pièces aux formes complexes.
- Idéal pour des petites séries ou des tâches ponctuelles.
- Maintenance réduite grâce à une conception simple.
- Meilleur contrôle de la qualité de lavage grâce à l’intervention humaine.
Inconvénients :
- Dépendance à la main-d’œuvre.
- Temps de traitement plus long, limitant la productivité pour les grandes séries.
3. Tunnels de lavage automatique : fonctionnement et atouts
Les tunnels de lavage automatique sont des systèmes hautement automatisés pour le traitement en série de grandes quantités de pièces.
Fonctionnement général :
- Prélavage : Élimination des salissures superficielles.
- Lavage principal : Jets haute pression avec détergents spécifiques.
- Rinçage : Élimination des résidus de détergent.
- Séchage : Utilisation d’air chaud ou comprimé pour sécher les pièces.
Atouts principaux :
- Productivité élevée : Capacité à traiter de grandes quantités de pièces en un temps réduit.
- Uniformité : Lavage régulier et homogène grâce aux réglages précis.
- Optimisation des ressources : Capteurs intelligents pour surveiller les paramètres (température, pression).
- Automatisation : Réduction de l’intervention humaine et des coûts associés.
Inconvénients :
- Investissement initial élevé.
- Nécessité d’un espace conséquent dans les installations.
- Moins adapté aux pièces très complexes ou fragiles.
4. Comparaison entre cabines de lavage manuel et tunnels de lavage automatique
Critères | Cabines de lavage manuel | Tunnels de lavage automatique |
---|---|---|
Flexibilité | Très élevée | Limitée aux séries de pièces standard |
Volume de production | Petites séries, pièces uniques | Grandes séries, production en continu |
Investissement initial | Faible | Élevé |
Main-d’œuvre | Nécessaire | Minimisée grâce à l’automatisation |
Temps de traitement | Plus long | Très rapide |
Qualité de lavage | Dépend de l’opérateur | Uniforme et constante |
Maintenance | Simple et réduite | Plus complexe et régulière |
5. Considérations environnementales
La gestion des ressources et le respect des réglementations environnementales jouent un rôle central dans le choix des systèmes de lavage industriel.
- Recyclage des eaux usées : Les deux technologies peuvent intégrer des systèmes de filtration pour réduire la consommation d’eau.
- Détergents biodégradables : L’utilisation de produits non toxiques limite l’impact environnemental.
- Réduction de la consommation énergétique : Les tunnels modernes utilisent des technologies de chauffage optimisé et des capteurs pour minimiser l’énergie nécessaire.
Les cabines de lavage manuel permettent un meilleur contrôle de la consommation d’eau et de produits chimiques, tandis que les tunnels automatiques optimisent les ressources sur de grandes séries.
6. Maintenance et exploitation
La maintenance est un facteur déterminant pour garantir la longévité et l’efficacité des systèmes de lavage.
- Cabines de lavage manuel :
- Maintenance réduite grâce à une conception simple.
- Vérifications régulières des outils (lances, buses) et des systèmes d’évacuation.
- Tunnels de lavage automatique :
- Maintenance préventive nécessaire pour les convoyeurs, les buses et les systèmes de chauffage.
- Intégration de systèmes d’auto-diagnostic pour anticiper les pannes.
7. Applications industrielles
Les cabines de lavage manuel et les tunnels automatiques trouvent des applications dans divers secteurs :
- Industrie automobile : Lavage des pièces moteur, composants de transmission, et carrosseries.
- Aéronautique : Nettoyage de pièces complexes et précises nécessitant une haute qualité de lavage.
- Industrie mécanique : Élimination des résidus d’usinage et des huiles.
- Pharmaceutique : Nettoyage hygiénique d’équipements et de contenants.
8. Conclusion
Les cabines de lavage manuel et les tunnels de lavage automatique offrent des solutions adaptées aux besoins spécifiques des industries. Les cabines manuelles se distinguent par leur flexibilité et leur précision, tandis que les tunnels automatiques excellent dans le traitement des grandes séries avec rapidité et régularité. Le choix de l’équipement dépend des contraintes de production, des exigences de propreté et des impératifs économiques. En combinant ces deux technologies, les entreprises peuvent optimiser leurs processus de nettoyage tout en respectant les normes environnementales et industrielles les plus exigeantes.
Introduction aux systèmes de lavage industriel
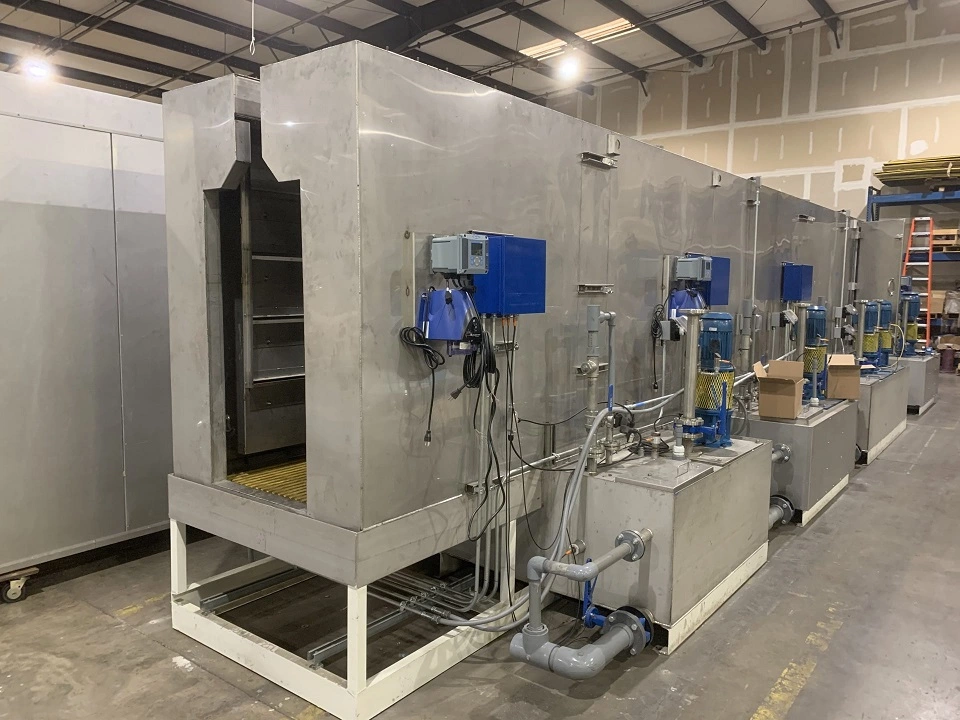
Les systèmes de lavage industriel jouent un rôle central dans de nombreux secteurs pour assurer la propreté, la durabilité et le bon fonctionnement des pièces et équipements. Ils répondent à des besoins précis en matière d’élimination des contaminants tels que les graisses, les huiles, les résidus métalliques et autres impuretés accumulées lors des processus de fabrication ou d’usinage. Que ce soit dans l’industrie automobile, aéronautique, pharmaceutique ou encore mécanique, le nettoyage industriel constitue une étape incontournable pour garantir la conformité aux normes de qualité et de sécurité les plus strictes.
Ces systèmes se déclinent en plusieurs technologies adaptées aux besoins de chaque industrie, selon les spécificités des pièces à traiter, leur volume et les exigences de nettoyage. La nature des pièces, leur taille, leur complexité géométrique et les matériaux qui les composent influencent directement le choix de la méthode de lavage. Il est ainsi possible de distinguer des solutions manuelles, semi-automatiques ou entièrement automatisées, chacune offrant des avantages spécifiques en termes de flexibilité, de productivité et de coût. L’une des préoccupations majeures dans le domaine du lavage industriel est l’efficacité des systèmes utilisés pour atteindre le niveau de propreté requis tout en minimisant l’impact environnemental. Les innovations récentes ont permis de développer des technologies plus respectueuses de l’environnement, intégrant des dispositifs de recyclage d’eau, d’optimisation des produits chimiques et de réduction de la consommation énergétique.
Le lavage manuel, souvent effectué dans des cabines fermées, permet de traiter des pièces uniques ou de petites séries qui nécessitent une attention particulière. Il s’agit d’une solution particulièrement adaptée lorsque le nettoyage nécessite un contrôle visuel précis et une intervention humaine pour cibler des zones spécifiques difficiles d’accès. L’opérateur utilise des équipements variés, tels que des lances haute pression, des brosses ou encore des systèmes d’air comprimé pour éliminer efficacement les contaminants. Ce type de système présente l’avantage d’une grande flexibilité et s’adapte parfaitement aux pièces aux géométries complexes ou aux composants fragiles. Toutefois, il repose fortement sur la main-d’œuvre et peut s’avérer moins efficace pour le traitement de grandes quantités de pièces en raison du temps nécessaire pour chaque opération.
À l’inverse, les systèmes de lavage automatique, tels que les tunnels de lavage, sont conçus pour offrir une productivité élevée dans le traitement de grandes séries de pièces. Ils fonctionnent grâce à un processus continu et automatisé qui garantit une uniformité du nettoyage et une cadence élevée. Les pièces sont acheminées à travers différentes étapes de lavage, incluant généralement un prélavage, un lavage principal avec des détergents spécifiques, un rinçage et un séchage. Grâce à l’automatisation, ces systèmes réduisent considérablement l’intervention humaine, ce qui permet non seulement de gagner du temps mais également d’améliorer la rentabilité globale du processus. Leur fonctionnement repose sur des réglages précis de la température, de la pression et de la durée de traitement afin d’obtenir des résultats constants et conformes aux exigences de propreté. Néanmoins, les tunnels de lavage nécessitent un investissement initial plus conséquent, une maintenance régulière et un espace important au sein des installations de production.
Dans le contexte actuel, les entreprises industrielles font face à des défis croissants liés aux réglementations environnementales et à la gestion durable des ressources. La réduction de la consommation d’eau, l’utilisation de détergents biodégradables et l’optimisation de la consommation énergétique sont devenues des priorités. Les fabricants de systèmes de lavage développent donc des solutions innovantes pour répondre à ces enjeux tout en maintenant des performances élevées. Les systèmes modernes intègrent des technologies avancées telles que des capteurs intelligents pour surveiller en temps réel les paramètres de lavage, des dispositifs de recyclage des eaux usées et des systèmes de chauffage optimisés. Ces innovations permettent d’améliorer l’efficacité énergétique, de réduire les coûts d’exploitation et de minimiser l’empreinte environnementale.
Le choix du système de lavage dépend également des contraintes économiques et des exigences de production propres à chaque industrie. Tandis que les cabines de lavage manuel se distinguent par leur capacité à traiter des pièces complexes avec une précision inégalée, les tunnels de lavage automatique offrent une solution idéale pour les industries nécessitant un traitement rapide et continu de grandes quantités de pièces. Les deux technologies peuvent coexister au sein d’une même installation, offrant ainsi une flexibilité optimale pour s’adapter aux différents besoins de nettoyage. Cette complémentarité permet aux entreprises d’optimiser leurs processus tout en garantissant des résultats de qualité.
En somme, les systèmes de lavage industriel constituent un maillon essentiel dans la chaîne de production et d’entretien des équipements. Grâce à des avancées constantes en matière de technologie et de durabilité, ils continuent d’évoluer pour répondre aux exigences croissantes des industries modernes. Qu’il s’agisse de lavage manuel pour des opérations de précision ou de lavage automatique pour des besoins de productivité à grande échelle, ces solutions jouent un rôle fondamental dans l’amélioration de la qualité, de la performance et de l’efficacité globale des processus industriels.
Cabines de lavage manuel : caractéristiques et avantages
Les cabines de lavage manuel sont des dispositifs essentiels pour les opérations de nettoyage industriel où la précision et le contrôle humain jouent un rôle central. Ces systèmes sont conçus pour répondre aux besoins spécifiques des industries qui traitent des pièces complexes, fragiles ou de petites séries, nécessitant une attention particulière pour éliminer efficacement toutes les formes de contaminants. La conception fermée des cabines permet de maintenir un environnement de travail propre en évitant les éclaboussures, la dispersion des résidus et des particules, tout en protégeant l’opérateur. Leur structure est généralement réalisée en acier inoxydable ou en matériaux résistants à la corrosion pour assurer une durabilité optimale, même en cas d’utilisation intensive de produits chimiques ou d’eau à haute pression.
Le principal atout des cabines de lavage manuel réside dans la flexibilité qu’elles offrent aux opérateurs. Contrairement aux systèmes automatisés, elles permettent d’intervenir de manière ciblée sur les zones difficiles d’accès ou sur des pièces de géométrie complexe. L’opérateur peut ajuster ses gestes et choisir les outils les plus appropriés en fonction du type de salissure et des matériaux à traiter. Généralement, ces cabines sont équipées de lances haute pression pour projeter de l’eau ou des solutions détergentes à des niveaux de pression ajustables, ce qui permet de décoller efficacement les graisses, huiles et autres résidus incrustés. Pour les contaminants plus tenaces ou nécessitant une action mécanique supplémentaire, des brosses spécifiques peuvent être utilisées, tandis que l’air comprimé facilite le séchage partiel des zones nettoyées.
L’ergonomie des cabines de lavage manuel joue également un rôle clé dans leur efficacité. Elles sont conçues pour offrir un confort optimal aux opérateurs, en intégrant des parois vitrées offrant une bonne visibilité, un éclairage LED puissant pour surveiller les zones nettoyées, et des systèmes d’aspiration pour éliminer les vapeurs et particules générées pendant le lavage. Certaines cabines intègrent même des gants étanches directement fixés aux parois pour permettre à l’opérateur de manipuler les pièces sans contact direct avec les liquides, tout en maintenant une étanchéité parfaite de l’espace de travail. Les modèles plus avancés proposent des systèmes de récupération et de filtration des eaux usées, réduisant ainsi la consommation d’eau et de détergents tout en respectant les normes environnementales en vigueur.
Outre leur flexibilité, les cabines de lavage manuel se distinguent par leur capacité à traiter des pièces uniques ou des petites séries avec une grande précision. Cette adaptabilité est particulièrement appréciée dans les secteurs où les composants à nettoyer sont fragiles ou complexes, comme dans l’aéronautique, l’horlogerie ou encore l’industrie médicale. Les cabines manuelles permettent de répondre à des exigences strictes en matière de propreté, notamment lorsqu’il s’agit d’éliminer des contaminants susceptibles de compromettre les performances des pièces ou d’affecter la sécurité des systèmes dans lesquels elles sont intégrées. Cette capacité à s’adapter à des besoins spécifiques fait des cabines de lavage manuel un outil indispensable pour les tâches de maintenance, de réparation ou de finition.
Cependant, l’efficacité des cabines de lavage manuel repose en grande partie sur l’habileté et l’expérience de l’opérateur. Contrairement aux systèmes automatisés qui garantissent une régularité du traitement, le lavage manuel peut varier en fonction des compétences individuelles. De plus, le temps nécessaire pour nettoyer chaque pièce est généralement plus long, ce qui limite la productivité lorsqu’il s’agit de traiter de grandes quantités. Cette dépendance à la main-d’œuvre constitue l’une des principales limites des cabines manuelles, en particulier pour les entreprises confrontées à des besoins de production à haut débit.
En dépit de cette contrainte, les cabines de lavage manuel conservent une place de choix dans les processus industriels grâce à leur polyvalence et leur simplicité d’utilisation. Leur coût d’investissement initial est relativement faible par rapport aux systèmes de lavage automatisés, et leur maintenance est généralement plus aisée. Les vérifications régulières se limitent à l’inspection des outils de lavage, des systèmes d’évacuation des eaux et, dans certains cas, des filtres de récupération. Cette simplicité de maintenance contribue à réduire les coûts d’exploitation et à assurer une disponibilité constante des équipements.
Les cabines de lavage manuel représentent donc une solution de nettoyage fiable et flexible pour les industries qui nécessitent un haut niveau de précision et un contrôle humain rigoureux. Leur conception ergonomique, associée à l’utilisation d’outils adaptés, permet d’obtenir des résultats de qualité, même pour les pièces les plus exigeantes. Elles constituent un complément idéal aux systèmes de lavage automatisés dans les environnements où la diversité des pièces et des besoins de nettoyage impose une intervention manuelle. Grâce aux innovations technologiques et environnementales, ces cabines continuent d’évoluer pour offrir des performances optimisées tout en respectant les contraintes économiques et écologiques des industries modernes.
Tunnels de lavage automatique : fonctionnement et atouts
Les tunnels de lavage automatique représentent une solution essentielle pour le nettoyage industriel lorsque des volumes importants de pièces doivent être traités de manière rapide, uniforme et efficace. Conçus pour fonctionner en continu, ces équipements sont particulièrement adaptés aux lignes de production à grande échelle, où la cadence et la régularité du nettoyage sont des critères primordiaux. Le fonctionnement des tunnels repose sur un convoyeur qui transporte les pièces à travers une série d’étapes de lavage successives, automatisant ainsi l’ensemble du processus pour minimiser l’intervention humaine et maximiser la productivité. Les tunnels de lavage sont capables de traiter des pièces de différentes tailles, formes et matériaux grâce à des réglages personnalisables qui adaptent la pression de lavage, la température et la durée de chaque étape en fonction des besoins spécifiques.
Le processus commence généralement par une phase de prélavage destinée à éliminer les contaminants superficiels tels que la poussière, les huiles ou les graisses légères. Cette étape prépare les pièces pour le lavage principal, qui utilise des détergents spécialisés projetés à haute pression par des buses orientables. Ces buses, stratégiquement positionnées, assurent une couverture complète des pièces, même dans les zones les plus difficiles d’accès. La pression et la température de l’eau sont soigneusement contrôlées pour garantir l’élimination optimale des salissures sans endommager les surfaces sensibles. Après le lavage, les pièces passent par une phase de rinçage qui permet de supprimer les résidus de détergent. Certains tunnels intègrent un système de rinçage à l’eau déminéralisée pour éviter les dépôts de calcaire ou de minéraux, particulièrement dans les applications exigeant un niveau de propreté élevé. Enfin, le processus se termine par une étape de séchage où de puissants jets d’air comprimé ou d’air chaud éliminent l’humidité résiduelle pour permettre une manipulation immédiate des pièces.
Les tunnels de lavage automatique offrent des atouts majeurs pour les entreprises industrielles grâce à leur capacité à traiter de grandes séries en un temps réduit tout en garantissant une qualité de nettoyage constante et uniforme. Cette régularité est assurée par l’automatisation complète du processus, qui réduit les erreurs humaines et les variations de performance liées à l’intervention manuelle. L’utilisation de capteurs intelligents permet de surveiller en temps réel les paramètres critiques tels que la température, la pression, la concentration en détergent et le débit d’eau, assurant ainsi une optimisation des ressources et un contrôle précis de la qualité. Ces technologies avancées permettent également de réduire la consommation d’eau, d’énergie et de produits chimiques, ce qui contribue à la fois à une diminution des coûts opérationnels et à un meilleur respect des normes environnementales.
Un autre avantage majeur des tunnels de lavage automatique réside dans leur productivité élevée. Grâce au fonctionnement en continu, les pièces sont acheminées de manière fluide et rapide, ce qui permet de répondre aux besoins des lignes de production à haute cadence. Cette rapidité de traitement est particulièrement avantageuse dans des secteurs comme l’industrie automobile, l’aéronautique ou l’électronique, où les délais de production sont serrés et la demande en volumes importants est constante. Par ailleurs, la configuration modulaire des tunnels de lavage permet de les adapter aux spécificités des pièces à traiter. Il est possible de régler la vitesse du convoyeur, la durée des cycles et l’orientation des buses pour s’assurer que chaque pièce reçoit un traitement optimal.
En dépit de ces nombreux atouts, les tunnels de lavage automatique présentent également certaines contraintes, notamment en termes d’investissement initial et d’espace requis pour leur installation. En raison de leur taille et de leur complexité, ces systèmes nécessitent un espace conséquent au sein des installations industrielles, ce qui peut constituer un frein pour certaines entreprises. De plus, la maintenance des tunnels de lavage est plus exigeante que celle des systèmes manuels, car il est essentiel de vérifier régulièrement les buses, les filtres, les convoyeurs et les systèmes de chauffage pour garantir leur bon fonctionnement sur le long terme. Toutefois, les modèles les plus récents intègrent des systèmes d’auto-diagnostic capables de détecter les anomalies en temps réel, facilitant ainsi les opérations de maintenance préventive et réduisant les arrêts imprévus.
Les considérations environnementales jouent également un rôle clé dans l’évolution des tunnels de lavage automatique. Face aux réglementations de plus en plus strictes en matière de gestion des eaux usées et de consommation énergétique, les fabricants ont développé des technologies innovantes pour minimiser l’impact écologique de ces systèmes. Les dispositifs de recyclage des eaux permettent de filtrer et réutiliser l’eau utilisée pendant le lavage, tandis que les systèmes de chauffage optimisés réduisent la consommation d’énergie. De plus, l’utilisation de détergents biodégradables et de rinçage à faible consommation contribue à renforcer la durabilité des tunnels de lavage.
En conclusion, les tunnels de lavage automatique constituent une solution incontournable pour les industries nécessitant un nettoyage rapide, précis et continu de grandes séries de pièces. Grâce à leur automatisation complète, leur capacité à garantir une qualité de lavage constante et leurs technologies avancées d’optimisation des ressources, ces systèmes offrent des performances exceptionnelles et une rentabilité élevée. Bien que leur coût d’acquisition et leurs besoins en maintenance puissent représenter un défi, les bénéfices en termes de productivité, d’efficacité et de respect des normes environnementales en font un investissement stratégique pour les entreprises modernes.
Comparaison entre cabines de lavage manuel et tunnels de lavage automatique
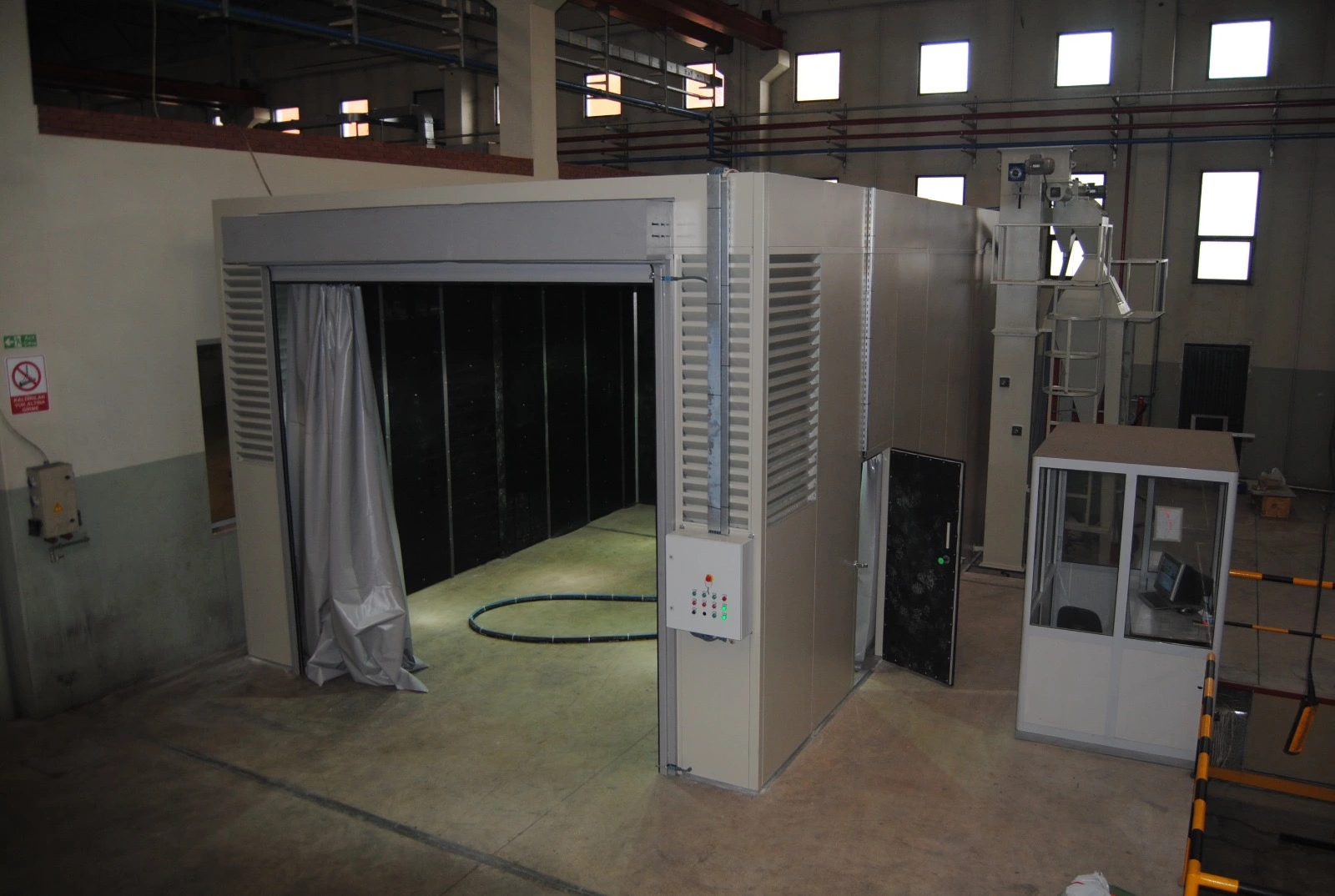
La comparaison entre les cabines de lavage manuel et les tunnels de lavage automatique met en évidence des différences majeures en termes de fonctionnement, d’efficacité, de flexibilité et d’applications industrielles. Ces deux systèmes de lavage répondent à des besoins distincts, selon la nature des pièces à traiter, le volume de production, les exigences de précision et les contraintes économiques. D’un côté, les cabines de lavage manuel se distinguent par leur polyvalence et leur capacité à permettre une intervention humaine ciblée, tandis que les tunnels de lavage automatique excellent dans la rapidité et l’uniformité du nettoyage pour les grandes séries.
Les cabines de lavage manuel sont particulièrement adaptées aux opérations nécessitant une attention précise et un contrôle visuel rigoureux. Elles permettent de traiter des pièces uniques ou de petites séries, souvent complexes ou fragiles, qui ne pourraient pas être nettoyées efficacement avec des systèmes automatisés. L’opérateur joue un rôle central dans ce processus, en utilisant des outils comme des lances haute pression, des brosses ou des systèmes d’air comprimé pour éliminer les contaminants présents sur les pièces. Cette flexibilité est l’un des principaux atouts des cabines manuelles, car elle permet d’ajuster les gestes et les outils en fonction des besoins spécifiques de chaque pièce, y compris les zones difficiles d’accès ou les surfaces délicates. Toutefois, cette méthode repose sur la compétence de l’opérateur, ce qui peut entraîner des variations de qualité et limiter la cadence de production, en particulier pour des volumes importants.
En revanche, les tunnels de lavage automatique offrent une solution idéale pour le nettoyage de grandes séries de pièces grâce à leur capacité à fonctionner en continu et à garantir une uniformité parfaite des résultats. Le processus automatisé permet de standardiser les opérations de lavage, du prélavage au séchage, tout en réduisant l’intervention humaine au minimum. Les pièces sont acheminées sur un convoyeur à travers plusieurs étapes successives, incluant le lavage avec des détergents projetés à haute pression, le rinçage et le séchage. Cette automatisation assure une cadence élevée et des résultats constants, ce qui est particulièrement avantageux pour les industries nécessitant une production à grande échelle, comme l’automobile, l’aéronautique ou l’électronique. Néanmoins, ces tunnels nécessitent un investissement initial plus important et demandent un espace conséquent pour leur installation. De plus, leur maintenance est plus complexe, car il est essentiel de surveiller régulièrement les buses, les filtres et les systèmes de convoyage pour garantir leur efficacité sur le long terme.
Sur le plan économique, les cabines de lavage manuel se révèlent plus accessibles en termes de coût d’acquisition et d’exploitation. Elles nécessitent un investissement initial plus faible et leur entretien est généralement plus simple, ce qui les rend particulièrement adaptées aux petites entreprises ou aux applications spécifiques où la productivité n’est pas une priorité. En revanche, les tunnels de lavage, bien que plus coûteux à l’achat, offrent un retour sur investissement significatif pour les entreprises ayant besoin de traiter de grandes quantités de pièces de manière rapide et efficace. Leur automatisation permet de réduire les coûts liés à la main-d’œuvre tout en optimisant l’utilisation des ressources, comme l’eau, les détergents et l’énergie, grâce aux technologies de recyclage et de contrôle avancé intégrées dans les modèles modernes.
Un autre facteur important dans cette comparaison concerne la qualité du nettoyage. Les cabines de lavage manuel permettent une intervention ciblée et un contrôle visuel précis, ce qui est particulièrement utile pour les pièces complexes ou les zones difficiles d’accès. Toutefois, la qualité du nettoyage peut varier en fonction de l’habileté et de l’expérience de l’opérateur, et les opérations peuvent être plus longues pour des pièces aux formes complexes. À l’inverse, les tunnels de lavage garantissent une qualité constante grâce à l’automatisation du processus, mais ils peuvent s’avérer moins efficaces pour les pièces nécessitant un nettoyage très ciblé ou un traitement manuel spécifique.
Enfin, les enjeux environnementaux influencent également le choix entre ces deux systèmes. Les cabines de lavage manuel consomment généralement moins d’eau et d’énergie que les tunnels, mais leur dépendance à l’intervention humaine peut entraîner une utilisation moins optimale des ressources. Les tunnels de lavage automatique, quant à eux, intègrent souvent des dispositifs avancés de recyclage des eaux et d’optimisation de la consommation énergétique, ce qui contribue à réduire leur impact environnemental, malgré leur plus grande capacité de traitement.
En conclusion, le choix entre une cabine de lavage manuel et un tunnel de lavage automatique dépend des besoins spécifiques de chaque industrie. Les cabines manuelles offrent une flexibilité et une précision inégalées pour les pièces complexes ou de petites séries, mais elles sont limitées en termes de productivité et de régularité. Les tunnels automatiques, en revanche, excellent dans le traitement de grandes séries grâce à leur rapidité, leur uniformité et leur capacité à optimiser les ressources, bien qu’ils nécessitent un investissement plus important et un entretien régulier. Ces deux systèmes peuvent coexister au sein d’une même installation pour offrir une solution complète et adaptée à différents besoins de nettoyage industriel.
Considérations environnementales
Les considérations environnementales occupent aujourd’hui une place centrale dans les processus industriels, notamment en ce qui concerne les systèmes de lavage. Face aux défis posés par le changement climatique, la raréfaction des ressources et les réglementations de plus en plus strictes, les entreprises doivent repenser leurs méthodes pour réduire leur impact écologique tout en maintenant un haut niveau de performance et d’efficacité. Dans ce contexte, l’optimisation de la consommation d’eau, d’énergie et de produits chimiques, ainsi que la gestion responsable des déchets, sont des priorités essentielles dans le développement et l’utilisation des systèmes de lavage industriel.
La consommation d’eau constitue l’un des principaux enjeux environnementaux. Les systèmes de lavage, qu’ils soient manuels ou automatisés, utilisent de grandes quantités d’eau pour éliminer les contaminants présents sur les pièces. Pour réduire cette consommation, les fabricants intègrent désormais des dispositifs de recyclage et de filtration des eaux usées. Ces systèmes permettent de récupérer, traiter et réutiliser l’eau utilisée pendant les cycles de lavage, limitant ainsi le gaspillage tout en respectant les réglementations en matière de rejets industriels. De plus, l’utilisation d’eau déminéralisée dans certaines applications permet d’éviter les dépôts de minéraux, réduisant ainsi le besoin en rinçage supplémentaire. Ces innovations garantissent non seulement une économie significative des ressources en eau, mais également une diminution des coûts d’exploitation pour les entreprises.
En parallèle, la consommation énergétique des systèmes de lavage constitue un autre point critique. Le chauffage de l’eau, le fonctionnement des pompes, des convoyeurs et des systèmes de séchage nécessitent une quantité importante d’énergie, ce qui peut entraîner une empreinte carbone élevée. Pour y remédier, les fabricants développent des solutions technologiques visant à optimiser la consommation énergétique. Cela inclut l’intégration de systèmes de récupération de chaleur, qui permettent de réutiliser l’énergie générée lors du lavage ou du séchage pour préchauffer l’eau des cycles suivants. Les systèmes modernes sont également dotés de moteurs à haute efficacité énergétique et de capteurs intelligents capables d’ajuster automatiquement les paramètres de lavage, comme la pression, la température et la durée, en fonction des besoins réels. Ces avancées contribuent à une utilisation plus rationnelle de l’énergie, tout en limitant les émissions de gaz à effet de serre.
L’utilisation de produits chimiques dans les systèmes de lavage représente un autre défi majeur sur le plan environnemental. Les détergents et solvants, souvent nécessaires pour éliminer les contaminants tenaces tels que les graisses et huiles, peuvent être nocifs pour l’environnement s’ils ne sont pas correctement traités avant leur rejet. Afin de limiter leur impact, les industriels privilégient désormais l’utilisation de produits biodégradables, moins toxiques et plus respectueux de l’environnement. Les avancées dans le domaine de la chimie verte ont permis de développer des détergents performants à base de composants naturels, réduisant ainsi la pollution et les risques pour les écosystèmes aquatiques. De plus, les systèmes de lavage modernes intègrent des dispositifs de dosage précis pour minimiser la quantité de produits chimiques utilisés, évitant ainsi le gaspillage tout en garantissant l’efficacité du nettoyage.
La gestion des déchets issus des systèmes de lavage constitue également une priorité dans une perspective environnementale. Les eaux usées, chargées de contaminants et de produits chimiques, doivent être traitées avant leur rejet afin de respecter les normes en vigueur. Pour ce faire, des systèmes de traitement des effluents sont intégrés aux équipements de lavage, incluant des technologies telles que la filtration, la décantation, les séparateurs d’huiles ou encore l’évaporation sous vide. Ces dispositifs permettent de séparer les polluants solides et liquides, tout en récupérant une eau propre pouvant être réutilisée dans les cycles de lavage. Cette approche contribue à réduire les rejets dans l’environnement tout en limitant les coûts liés à l’évacuation des déchets.
Enfin, la durabilité des équipements et leur conception jouent un rôle essentiel dans les considérations environnementales. Les fabricants s’efforcent de concevoir des systèmes de lavage robustes et durables, fabriqués à partir de matériaux recyclables et résistants à la corrosion pour prolonger leur durée de vie. Une maintenance simplifiée et des pièces facilement remplaçables permettent également de réduire les déchets liés à l’obsolescence des machines. L’intégration de technologies connectées et d’outils de diagnostic à distance facilite la maintenance préventive, limitant ainsi les arrêts de production, l’usure prématurée des composants et la consommation inutile de ressources.
En conclusion, les considérations environnementales dans les systèmes de lavage industriel sont devenues incontournables pour les entreprises souhaitant allier performance et responsabilité écologique. La réduction de la consommation d’eau et d’énergie, l’utilisation de produits chimiques respectueux de l’environnement, la gestion optimisée des déchets et la durabilité des équipements représentent les principaux axes d’amélioration pour limiter l’impact écologique des opérations de lavage. Grâce aux innovations technologiques et à la prise de conscience croissante des enjeux environnementaux, les systèmes de lavage évoluent vers des solutions plus durables, permettant aux industries de répondre aux défis écologiques tout en respectant les normes réglementaires et économiques.
Applications industrielles
Les applications industrielles des systèmes de lavage jouent un rôle crucial dans un grand nombre de secteurs, répondant à des besoins spécifiques en matière de propreté, de qualité et de performance. Le nettoyage industriel est une étape indispensable pour assurer le bon fonctionnement des équipements, la durabilité des produits et la conformité aux normes en vigueur. Les systèmes de lavage, qu’ils soient manuels ou automatisés, trouvent ainsi leur place dans des domaines variés tels que l’industrie automobile, l’aéronautique, la métallurgie, l’agroalimentaire, l’électronique et bien d’autres, chaque secteur ayant ses propres exigences techniques et réglementaires.
Dans l’industrie automobile, les systèmes de lavage sont largement utilisés pour nettoyer les pièces mécaniques telles que les moteurs, les boîtes de vitesses, les composants de freinage et les éléments de transmission. Ces pièces, souvent soumises à des salissures tenaces comme les huiles, graisses et résidus métalliques, nécessitent un nettoyage rigoureux avant leur assemblage ou leur maintenance. Les tunnels de lavage automatique sont particulièrement adaptés à ce secteur, car ils permettent de traiter de grandes séries de pièces avec une rapidité et une régularité exemplaires. Les cabines de lavage manuel, quant à elles, sont utilisées pour les opérations de nettoyage ciblées sur des pièces complexes ou de petite taille nécessitant une intervention humaine précise.
Dans le secteur aéronautique, où les exigences en matière de propreté sont extrêmement strictes, les systèmes de lavage industriel assurent le nettoyage des composants critiques comme les pièces de turbines, les carters, les systèmes hydrauliques et les éléments électroniques. Ces pièces doivent être exemptes de la moindre particule ou contamination pour garantir leur bon fonctionnement et éviter les défaillances en vol. Les systèmes automatisés, équipés de technologies de lavage haute pression et de rinçage à l’eau déminéralisée, offrent des résultats impeccables et répondent aux normes rigoureuses imposées par les constructeurs aéronautiques.
L’industrie agroalimentaire représente un autre domaine majeur d’application pour les systèmes de lavage. Dans ce secteur, le nettoyage des équipements de production est essentiel pour garantir l’hygiène, la sécurité alimentaire et la conformité aux réglementations sanitaires. Les cabines de lavage manuel sont souvent utilisées pour nettoyer des pièces spécifiques comme les outils de découpe, les moules et les convoyeurs, tandis que les tunnels de lavage automatique permettent de traiter en continu des bacs, caisses, plateaux et autres contenants utilisés dans les lignes de production. L’accent est mis sur l’élimination des résidus organiques, des graisses et des contaminants microbiens afin d’éviter toute contamination croisée.
En métallurgie et dans l’industrie mécanique, les systèmes de lavage industriel jouent un rôle clé dans l’élimination des résidus d’usinage, des copeaux et des produits de lubrification appliqués lors des processus de fabrication. Le nettoyage est indispensable avant les opérations de traitement de surface, comme le revêtement, la peinture ou le traitement thermique, afin de garantir l’adhérence des matériaux et d’éviter les défauts. Les tunnels de lavage haute pression, souvent combinés à des solutions de séchage performant, assurent une propreté optimale tout en respectant les cadences de production élevées.
Dans le domaine de l’électronique, où les composants sont souvent petits et délicats, le nettoyage industriel revêt une importance particulière. Les circuits imprimés, par exemple, doivent être débarrassés des résidus de flux de soudure et autres contaminants pouvant compromettre leur fonctionnement. Les systèmes de lavage utilisant des technologies telles que les ultrasons ou les solutions de lavage à base d’eau déminéralisée offrent un nettoyage en douceur tout en respectant l’intégrité des pièces. Les cabines de lavage manuel sont également employées pour des opérations de nettoyage spécifiques nécessitant un contrôle visuel rigoureux.
L’industrie pharmaceutique et médicale utilise également des systèmes de lavage sophistiqués pour assurer la propreté des équipements et des composants en contact avec les produits sensibles. Le nettoyage de flacons, seringues, dispositifs médicaux ou équipements de laboratoire doit répondre à des normes d’hygiène extrêmement strictes pour garantir la sécurité des patients et la qualité des médicaments. Les systèmes automatisés, dotés de cycles de lavage, de rinçage et de stérilisation contrôlés, assurent une propreté parfaite et répétable.
Enfin, d’autres secteurs comme l’énergie, la pétrochimie et les transports font également appel aux systèmes de lavage industriel pour entretenir et nettoyer des pièces spécifiques. Dans le secteur énergétique, par exemple, les turbines, échangeurs de chaleur et autres composants critiques doivent être nettoyés régulièrement pour maintenir leur performance optimale. Les cabines de lavage manuel sont utilisées pour des opérations de maintenance ponctuelles, tandis que les tunnels automatisés traitent de grandes séries d’éléments en un minimum de temps.
En conclusion, les applications industrielles des systèmes de lavage sont nombreuses et diversifiées, s’adaptant aux besoins spécifiques de chaque secteur. Qu’il s’agisse de traiter de grandes séries de pièces en continu grâce à des tunnels de lavage automatique ou de réaliser des opérations ciblées avec des cabines de lavage manuel, ces équipements jouent un rôle essentiel pour assurer la propreté, la performance et la conformité des composants industriels. Grâce aux avancées technologiques, les systèmes de lavage continuent d’évoluer pour répondre aux exigences croissantes en matière de qualité, d’efficacité et de respect des normes environnementales dans tous les secteurs d’activité.
Lavage au phosphate avant le revêtement en poudre
Le lavage au phosphate avant le revêtement en poudre est une étape essentielle dans les processus de préparation de surface des matériaux métalliques afin d’assurer l’adhérence optimale du revêtement et d’améliorer la résistance à la corrosion. Cette méthode de traitement chimique consiste à appliquer une couche de phosphate sur la surface métallique pour la préparer à recevoir le revêtement en poudre. Elle joue un rôle clé dans l’obtention d’un résultat final durable, uniforme et esthétique, tout en répondant aux exigences de performance dans de nombreuses industries telles que l’automobile, l’aéronautique, la construction métallique ou encore l’électroménager.
Le processus de lavage au phosphate commence par un nettoyage approfondi des pièces métalliques afin d’éliminer les impuretés telles que les huiles, les graisses, les poussières et les résidus d’oxydation. Cette phase initiale, souvent réalisée avec des détergents spécifiques et des solutions dégraissantes, est indispensable pour garantir une surface propre et réactive pour les étapes suivantes. Une surface contaminée peut compromettre la qualité du traitement au phosphate et entraîner des problèmes d’adhérence du revêtement, ce qui réduirait la durabilité du produit fini.
Une fois les pièces parfaitement nettoyées, le processus de phosphatation est mis en œuvre. Cette étape repose sur l’application d’une solution chimique contenant des sels de phosphate, souvent appliquée sous forme de bain ou de pulvérisation. Les phosphates de zinc, de fer ou de manganèse sont couramment utilisés selon les exigences techniques et le type de matériau traité. Le phosphate de zinc est particulièrement apprécié pour les applications nécessitant une protection anticorrosion élevée et une excellente adhérence du revêtement en poudre. Le phosphate de fer, quant à lui, est souvent privilégié pour des applications moins exigeantes où la performance anticorrosion peut être légèrement réduite, mais où le coût et la simplicité du processus sont des avantages majeurs.
Au cours de la phosphatation, une réaction chimique se produit entre la surface métallique et la solution de phosphate, formant une couche cristalline fine et uniforme. Cette couche, composée de cristaux de phosphate insolubles, agit comme une barrière protectrice contre la corrosion et constitue une base idéale pour l’application du revêtement en poudre. Elle offre une excellente adhérence en créant une surface légèrement rugueuse qui permet au revêtement de mieux s’accrocher et de résister aux contraintes mécaniques ou thermiques. De plus, la couche de phosphate assure une distribution homogène du revêtement en poudre, ce qui contribue à une finition esthétique de haute qualité.
L’étape suivante consiste à rincer soigneusement les pièces après le traitement au phosphate afin d’éliminer les résidus chimiques et de neutraliser la surface. Dans certains cas, un passivant est appliqué pour renforcer la protection anticorrosion et stabiliser la couche de phosphate. Une fois le rinçage terminé, les pièces sont séchées complètement pour éviter toute présence d’humidité avant l’application du revêtement en poudre. Le séchage est une phase critique, car une surface humide peut nuire à la qualité d’adhérence du revêtement et compromettre le résultat final.
L’application du revêtement en poudre intervient ensuite sur la surface préparée. Cette technique utilise une poudre électrostatiquement chargée qui est projetée sur les pièces métalliques à l’aide de pistolets spécialement conçus. Grâce à la préparation au phosphate, la poudre adhère de manière optimale à la surface et forme une couche uniforme avant d’être polymérisée dans un four à haute température. Le processus de polymérisation permet à la poudre de fondre et de former une couche protectrice dure et résistante, offrant à la pièce une finition durable, esthétique et hautement performante.
L’un des principaux avantages du lavage au phosphate réside dans sa capacité à améliorer la résistance à la corrosion des matériaux métalliques. La couche de phosphate agit comme une barrière qui retarde la propagation de la rouille et protège la surface contre les agressions extérieures telles que l’humidité, les produits chimiques ou les variations de température. Cette propriété est particulièrement importante dans des secteurs où les pièces sont exposées à des environnements exigeants et corrosifs.
En outre, le lavage au phosphate permet d’optimiser la durabilité et la performance des revêtements en poudre. En améliorant l’adhérence entre la surface métallique et le revêtement, il contribue à prévenir les décollements, les fissures et les écaillages qui peuvent apparaître sous l’effet de contraintes mécaniques ou thermiques. Cela garantit une protection à long terme, même dans des conditions d’utilisation intenses.
Cependant, le processus de lavage au phosphate nécessite une gestion rigoureuse des paramètres pour assurer un résultat optimal. La température, la concentration des solutions chimiques, le temps de traitement et la qualité des rinçages doivent être soigneusement contrôlés afin d’éviter les défauts de phosphatation, tels qu’une couche inégale ou des zones non traitées. De plus, les considérations environnementales jouent un rôle croissant dans l’utilisation de ce procédé. Les solutions de phosphatation peuvent générer des effluents contenant des métaux lourds et des composés chimiques qui nécessitent un traitement approprié avant leur rejet. Les industriels investissent donc dans des systèmes de traitement des eaux et dans des procédés plus écologiques pour minimiser leur impact environnemental.
En conclusion, le lavage au phosphate avant le revêtement en poudre est une étape fondamentale dans la préparation des surfaces métalliques pour assurer une protection anticorrosion efficace, une adhérence optimale et une finition de haute qualité. Grâce à ce processus, les industries peuvent répondre aux exigences croissantes en matière de durabilité, de performance et d’esthétique, tout en s’adaptant aux contraintes économiques et environnementales. Ce traitement reste un choix incontournable dans de nombreux secteurs pour garantir la longévité et la fiabilité des pièces métalliques revêtues.
Introduction au lavage au phosphate avant le revêtement en poudre
Le lavage au phosphate avant l’application du revêtement en poudre est une étape cruciale dans les processus de traitement de surface des matériaux métalliques. Ce traitement chimique permet de préparer la surface du métal, favorisant l’adhérence du revêtement et améliorant la résistance à la corrosion. Cette méthode est largement utilisée dans l’industrie automobile, l’électroménager, la construction métallique et d’autres secteurs nécessitant des finitions métalliques durables et esthétiques.
Processus de lavage au phosphate
Le processus de lavage au phosphate se décompose en plusieurs étapes fondamentales, chacune ayant un rôle spécifique dans la préparation des pièces métalliques.
- Nettoyage préalable : Avant d’appliquer le phosphate, les pièces doivent être débarrassées de toutes les impuretés comme les huiles, graisses et autres contaminants. Cette étape est cruciale pour assurer l’efficacité du traitement au phosphate. Un nettoyage avec des solutions dégraissantes ou à l’aide de machines de lavage haute pression est souvent utilisé.
- Phosphatation : Une fois les pièces nettoyées, elles sont plongées dans une solution de phosphate, généralement composée de sels de zinc, de fer ou de manganèse. Cette solution réagit avec la surface métallique pour créer une fine couche de cristaux de phosphate. La composition de la solution et les conditions de traitement (température, concentration, durée) sont des facteurs clés pour garantir une bonne qualité de la couche.
- Rinçage et passivation : Après la phosphatation, les pièces sont soigneusement rincées pour éliminer les résidus chimiques. Dans certains cas, un passivant est appliqué pour renforcer la protection anticorrosion et améliorer la stabilité de la couche de phosphate.
- Séchage : Les pièces doivent être parfaitement sèches avant l’application du revêtement en poudre. Un séchage complet permet d’éviter que l’humidité interfère avec l’adhérence du revêtement.
Avantages du lavage au phosphate
Le lavage au phosphate présente plusieurs avantages indéniables dans le processus de préparation de surface avant le revêtement en poudre.
- Amélioration de l’adhérence : La couche de phosphate crée une surface rugueuse qui favorise l’adhérence du revêtement en poudre, garantissant ainsi une finition homogène et durable.
- Protection contre la corrosion : La couche de phosphate, en plus de favoriser l’adhérence, offre une protection efficace contre la corrosion. Elle agit comme une barrière contre les facteurs externes tels que l’humidité et les produits chimiques, prolongeant ainsi la durée de vie des pièces traitées.
- Optimisation de la performance des revêtements : La préparation de la surface au phosphate permet de prévenir les défauts comme les fissures, les décollements ou les écaillages, en assurant que le revêtement en poudre adhère de manière uniforme.
- Amélioration esthétique : En favorisant une répartition uniforme du revêtement, la phosphatation contribue à l’apparence esthétique des pièces, avec une finition de qualité supérieure.
Enjeux environnementaux du lavage au phosphate
Le processus de lavage au phosphate, bien que bénéfique pour la qualité des revêtements, soulève des préoccupations environnementales. Les solutions de phosphate peuvent générer des effluents contenant des métaux lourds, ce qui nécessite un traitement adéquat des eaux usées avant leur rejet. Pour répondre à ces enjeux, de nombreuses entreprises investissent dans des systèmes de filtration et de traitement des eaux pour réduire l’impact environnemental. De plus, des solutions de phosphate moins polluantes et des technologies plus écologiques sont constamment développées pour minimiser l’empreinte environnementale.
Applications industrielles du lavage au phosphate avant le revêtement en poudre
Le lavage au phosphate est couramment utilisé dans plusieurs secteurs industriels où les exigences de durabilité et de protection des surfaces sont cruciales. Voici quelques exemples :
- Industrie automobile : Le nettoyage au phosphate est utilisé pour préparer les pièces métalliques avant l’application de revêtements en poudre, garantissant ainsi une protection contre la rouille et une finition esthétique.
- Électroménager : Les composants métalliques des appareils électroménagers, comme les grilles, les panneaux et les châssis, bénéficient également de ce traitement pour améliorer leur résistance à la corrosion et leur apparence.
- Construction métallique : Les structures métalliques, telles que les cadres en acier ou les supports, sont souvent traitées au phosphate avant d’être recouvertes de peinture en poudre, assurant ainsi leur durabilité et leur protection.
Conclusion
Le lavage au phosphate avant l’application du revêtement en poudre est un processus industriel clé qui garantit la durabilité, la résistance à la corrosion et la qualité esthétique des produits métalliques. Grâce à ses avantages indéniables, ce traitement est largement utilisé dans divers secteurs industriels, bien que des efforts continus soient nécessaires pour minimiser son impact environnemental. En combinant des solutions de traitement de surface efficaces et écologiques, les industriels peuvent répondre aux exigences croissantes de performance tout en respectant les normes environnementales strictes.
Le lavage au phosphate avant le revêtement en poudre est une étape essentielle dans de nombreux processus industriels, en particulier dans les secteurs nécessitant une protection de surface et une adhérence optimales des revêtements. Ce traitement chimique est utilisé pour préparer les pièces métalliques, telles que celles utilisées dans l’automobile, l’électroménager, la construction métallique, l’aéronautique et bien d’autres domaines, avant l’application de revêtements en poudre. La préparation de la surface métallique au phosphate crée une couche intermédiaire qui améliore l’adhérence du revêtement, tout en renforçant la protection contre la corrosion.
Lors du processus de lavage au phosphate, les pièces métalliques sont traitées avec une solution contenant des sels de phosphate, comme le phosphate de zinc, de fer ou de manganèse, qui réagissent avec la surface métallique pour former une couche de phosphate cristallin. Cette couche a pour fonction de créer une surface rugueuse, favorisant ainsi l’adhésion du revêtement en poudre tout en offrant une protection supplémentaire contre l’humidité et d’autres agents corrosifs. Ce procédé est couramment utilisé pour traiter des pièces qui seront ensuite recouvertes d’une couche de peinture en poudre, une méthode qui est de plus en plus prisée dans l’industrie pour ses avantages en termes de durabilité, de finition esthétique et de respect de l’environnement.
L’une des raisons principales pour lesquelles le lavage au phosphate est si important réside dans le fait qu’il améliore considérablement la durabilité des produits métalliques traités. En formant une barrière contre la rouille, le phosphate agit comme un agent protecteur, empêchant la corrosion et prolongeant ainsi la durée de vie des pièces. De plus, cette préparation chimique améliore la résistance du revêtement en poudre contre l’usure et les chocs, et assure une application uniforme du revêtement. La couche de phosphate empêche également l’apparition de défauts tels que les fissures, les éclats ou le décollement du revêtement, garantissant ainsi une finition esthétique et performante sur le long terme.
Le processus de lavage au phosphate se compose de plusieurs étapes distinctes, chacune ayant son propre rôle spécifique. Tout d’abord, les pièces doivent être nettoyées pour éliminer toutes les impuretés telles que les huiles, les graisses et les résidus d’oxydation qui pourraient interférer avec la réaction chimique du phosphate. Un nettoyage rigoureux est donc essentiel pour garantir l’efficacité du traitement au phosphate. Ensuite, les pièces sont immergées ou pulvérisées avec une solution de phosphate qui réagit avec la surface métallique pour créer la couche protectrice. Une fois la phosphatation effectuée, les pièces sont soigneusement rincées pour éliminer toute trace de solution chimique et séchées avant d’être prêtes pour l’application du revêtement en poudre.
Cette phase de lavage au phosphate, bien que relativement simple, est cruciale pour assurer la performance et la durabilité des produits finis. Elle garantit non seulement une excellente adhérence du revêtement, mais elle protège également les pièces contre les risques de corrosion et d’usure prématurée. Le phosphate utilisé peut varier en fonction des besoins spécifiques du produit final, et le type de phosphate choisi influencera la qualité de la protection anticorrosion et l’adhérence du revêtement.
En dépit de ses nombreux avantages, le lavage au phosphate soulève également certaines préoccupations environnementales. En effet, les solutions de phosphate utilisées dans le processus de traitement peuvent contenir des produits chimiques qui nécessitent un traitement et une gestion appropriée des effluents pour éviter toute contamination de l’environnement. Les entreprises sont donc de plus en plus incitées à mettre en place des systèmes de récupération et de filtration des eaux usées pour minimiser leur impact écologique. De plus, des efforts sont en cours pour développer des produits chimiques moins polluants, contribuant ainsi à rendre ce processus plus respectueux de l’environnement.
Dans l’ensemble, le lavage au phosphate avant le revêtement en poudre est un procédé incontournable dans l’industrie pour assurer la qualité, la durabilité et la performance des revêtements appliqués sur les pièces métalliques. En combinant une préparation chimique de haute qualité avec une technologie de revêtement moderne, ce processus permet de répondre aux exigences strictes des secteurs industriels tout en offrant des solutions plus durables et esthétiques.
Revêtement en Poudre
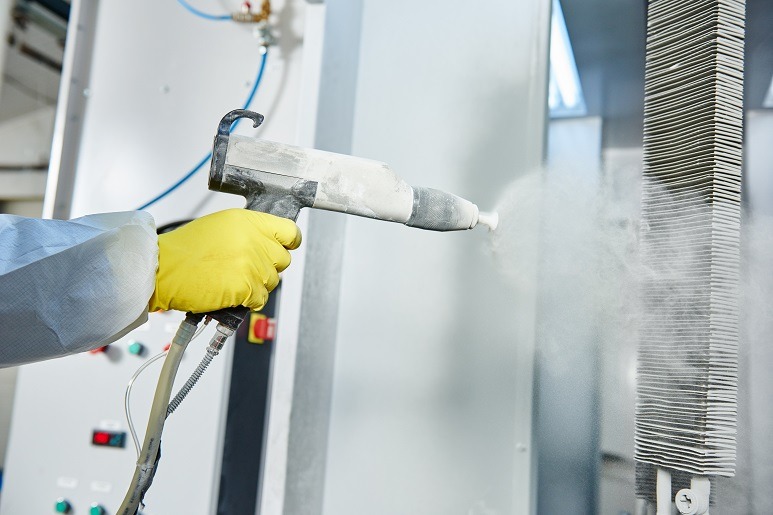
Le revêtement en poudre est une technique de finition de surface largement utilisée dans divers secteurs industriels, en particulier pour les pièces métalliques. Ce procédé consiste à appliquer une couche de peinture sous forme de poudre sèche sur la surface d’un objet, généralement à l’aide d’un pistolet électrostatique. Contrairement aux peintures liquides traditionnelles, qui nécessitent un solvant pour dissoudre la peinture et la rendre fluide, le revêtement en poudre est appliqué sous forme de poudre sèche, sans solvant, ce qui le rend plus respectueux de l’environnement. Cette méthode présente de nombreux avantages, tant en termes de performance que d’efficacité, et est utilisée dans des secteurs aussi variés que l’automobile, l’électroménager, la construction métallique, et bien d’autres.
L’un des principaux avantages du revêtement en poudre réside dans sa capacité à offrir une finition durable et résistante. Une fois appliquée, la poudre est chauffée dans un four à haute température, où elle fond et se lie à la surface du métal, formant une couche homogène, lisse et résistante. Ce processus de fusion, appelé polymérisation, permet de créer un revêtement solide et très adhérent. Le revêtement en poudre est ainsi particulièrement adapté aux pièces qui doivent résister à des conditions difficiles, telles que l’humidité, les produits chimiques, les rayures, l’usure et les températures élevées. Cette résistance supérieure explique pourquoi ce procédé est souvent privilégié pour les pièces exposées à des environnements industriels ou extérieurs exigeants.
Une autre caractéristique importante du revêtement en poudre est son aspect esthétique. Ce procédé permet d’obtenir une finition uniforme, sans coulures ni traces de pinceau, offrant ainsi une surface lisse et parfaitement mate ou brillante, selon le type de poudre utilisé. Les revêtements en poudre sont disponibles dans une large gamme de couleurs et de textures, permettant une personnalisation poussée des produits finis. De plus, contrairement aux peintures liquides, le revêtement en poudre ne s’écaille pas facilement et ne nécessite pas de retouches fréquentes, ce qui permet de maintenir une apparence esthétique de longue durée.
L’aspect écologique du revêtement en poudre est également un avantage considérable. En effet, cette méthode ne nécessite pas de solvants chimiques, ce qui réduit les émissions de composés organiques volatils (COV), responsables de la pollution de l’air. De plus, la poudre non utilisée peut être récupérée et réutilisée, ce qui réduit les déchets et optimise l’utilisation des matériaux. Cela en fait une solution plus respectueuse de l’environnement par rapport aux méthodes traditionnelles de peinture en raison de la réduction des risques de pollution et de la diminution des déchets. Cela contribue également à une meilleure sécurité dans l’atelier, en réduisant l’exposition des travailleurs aux produits chimiques dangereux.
Le revêtement en poudre est particulièrement adapté aux pièces métalliques, car la poudre adhère très bien aux surfaces métalliques et leur confère une protection efficace contre la rouille et la corrosion. Ce processus est couramment utilisé pour traiter des pièces telles que des châssis de véhicules, des meubles en métal, des équipements industriels, des pièces de machines et des éléments architecturaux extérieurs. Dans l’industrie automobile, par exemple, les composants métalliques tels que les jantes, les grilles et les châssis sont souvent traités par revêtement en poudre pour garantir leur durabilité et leur résistance aux conditions climatiques difficiles.
Une fois la poudre appliquée, le revêtement est chauffé dans un four à température élevée, généralement entre 160 et 200°C. Cela permet à la poudre de fondre et de se lier chimiquement à la surface de l’objet, formant ainsi une couche solide et lisse. Ce processus de polymérisation confère au revêtement une résistance exceptionnelle aux conditions de stress mécanique, thermique et chimique. En outre, la finition obtenue est généralement plus épaisse et plus durable que celle d’une peinture liquide traditionnelle.
Cependant, bien que le revêtement en poudre présente de nombreux avantages, il existe aussi certaines limitations. Par exemple, ce procédé est particulièrement adapté aux objets de formes simples, mais peut s’avérer plus complexe pour les objets de formes irrégulières ou les zones difficilement accessibles. De plus, le revêtement en poudre nécessite un équipement spécialisé, comme des pistolets électrostatiques et des fours de polymérisation, ce qui peut entraîner un coût initial relativement élevé pour les entreprises. Toutefois, ces coûts sont compensés par la durabilité et la résistance accrues des produits finis, ce qui permet de réduire les coûts de maintenance à long terme.
En conclusion, le revêtement en poudre est une méthode de finition de surface très efficace, offrant une combinaison de durabilité, d’esthétique et de respect de l’environnement. En raison de ses nombreuses qualités, il est largement utilisé dans des secteurs industriels variés, offrant une solution fiable pour la protection et la personnalisation des pièces métalliques. Bien que l’investissement initial pour la mise en place de ce processus puisse être conséquent, les bénéfices à long terme, notamment en termes de performance et de réduction des coûts de maintenance, font du revêtement en poudre une option privilégiée pour de nombreuses industries.
Processus de lavage au phosphate
Le processus de lavage au phosphate est une étape clé dans le traitement de surface des matériaux métalliques, visant à améliorer l’adhérence des revêtements et à offrir une protection contre la corrosion. Ce procédé chimique est couramment utilisé avant l’application de peintures, de revêtements en poudre ou d’autres types de finitions. Il consiste à appliquer une solution de phosphate sur la surface métallique, créant ainsi une couche de phosphate cristallin qui joue un rôle fondamental dans la préparation de la surface pour le revêtement final. Le lavage au phosphate est particulièrement utilisé dans des secteurs comme l’automobile, l’électroménager, la construction métallique et d’autres industries où la durabilité et la résistance des produits sont essentielles.
Le processus commence par un nettoyage approfondi des pièces métalliques. Cette étape est primordiale car la présence de contaminants tels que les huiles, les graisses, les poussières ou les oxydes peut compromettre l’efficacité du traitement. Les pièces sont donc débarrassées de ces impuretés à l’aide de solutions détergentes ou par des méthodes mécaniques comme le lavage à haute pression. Un nettoyage rigoureux permet d’obtenir une surface propre, ce qui garantit une meilleure réactivité lors de l’application de la solution de phosphate et assure un bon résultat final.
Une fois les pièces nettoyées, elles sont immergées dans une solution contenant des sels de phosphate, généralement sous forme de phosphate de zinc, de fer ou de manganèse, selon les besoins spécifiques du processus et les caractéristiques des pièces à traiter. La solution de phosphate réagit avec la surface métallique pour former une fine couche de cristaux de phosphate qui adhèrent à la pièce. Cette couche, bien que très mince, joue un rôle crucial en offrant une protection anticorrosion, en améliorant l’adhérence du revêtement qui sera appliqué par la suite et en créant une surface légèrement rugueuse, ce qui permet au revêtement d’adhérer plus efficacement.
La durée d’application de la solution de phosphate et la température de la solution sont des facteurs déterminants dans la qualité du traitement. En fonction des exigences du processus, la température et la concentration de la solution peuvent être ajustées. Un contrôle précis de ces paramètres est essentiel pour éviter les défauts de phosphatation, tels qu’une couche trop épaisse ou inégale. Après cette phase de traitement chimique, les pièces sont soigneusement rincées pour éliminer toute trace résiduelle de solution de phosphate, et elles peuvent être passivées, c’est-à-dire traitées avec un produit chimique supplémentaire qui améliore la protection contre la corrosion et stabilise la couche de phosphate.
Le processus de lavage au phosphate se termine par un séchage minutieux des pièces. Cette étape est cruciale, car une pièce humide peut compromettre l’adhérence du revêtement et entraîner des défauts dans le produit final. Le séchage est effectué à une température contrôlée pour garantir que les pièces sont totalement sèches avant l’application du revêtement en poudre, de la peinture liquide ou d’un autre type de finition. L’absence d’humidité sur la surface métallique est un facteur clé pour obtenir une bonne qualité d’adhésion du revêtement.
Les avantages du processus de lavage au phosphate sont nombreux. Tout d’abord, il permet de renforcer la résistance à la corrosion des pièces métalliques en créant une barrière protectrice qui empêche l’humidité et d’autres agents corrosifs d’atteindre le métal. De plus, la couche de phosphate améliore l’adhérence du revêtement appliqué ultérieurement, qu’il s’agisse de peinture en poudre, de peinture liquide ou d’autres types de revêtements. Cela permet d’obtenir une finition plus durable et plus résistante aux agressions extérieures. Le processus est également relativement simple à mettre en œuvre, ce qui le rend rentable et efficace pour une large gamme de pièces métalliques.
Cependant, ce processus présente également des défis, notamment sur le plan environnemental. Les solutions de phosphate utilisées dans le traitement peuvent contenir des métaux lourds, comme le zinc ou le manganèse, et doivent donc être traitées correctement pour éviter la contamination de l’environnement. Cela nécessite des systèmes de traitement des eaux usées afin de neutraliser les résidus chimiques et de limiter les impacts sur l’environnement. Certaines entreprises investissent dans des technologies plus écologiques, telles que des solutions de phosphate sans métaux lourds, pour réduire leur empreinte écologique et se conformer aux normes environnementales strictes.
En conclusion, le lavage au phosphate est une étape fondamentale dans la préparation des surfaces métalliques avant l’application de revêtements protecteurs. Ce traitement chimique garantit une meilleure adhérence des revêtements et renforce la résistance des pièces métalliques à la corrosion. Grâce à sa simplicité et à son efficacité, le processus est largement utilisé dans de nombreux secteurs industriels. Toutefois, il est essentiel d’adopter des pratiques respectueuses de l’environnement pour minimiser les impacts de ce processus et garantir sa durabilité à long terme.
Avantages du lavage au phosphate
Le lavage au phosphate présente de nombreux avantages pour le traitement des surfaces métalliques avant l’application de revêtements protecteurs, ce qui en fait un processus incontournable dans diverses industries. Tout d’abord, l’un des principaux avantages de ce procédé est sa capacité à améliorer considérablement l’adhérence des revêtements appliqués par la suite. En créant une fine couche de phosphate sur la surface métallique, le processus permet d’obtenir une texture légèrement rugueuse, ce qui facilite l’adhésion des revêtements en poudre, des peintures liquides ou d’autres types de finitions. Cette adhérence renforcée est cruciale pour garantir une finition uniforme et durable, ainsi qu’une protection à long terme contre les facteurs externes.
Le lavage au phosphate est également reconnu pour sa capacité à offrir une protection accrue contre la corrosion. La couche de phosphate formée lors du processus agit comme une barrière entre le métal et les éléments extérieurs, notamment l’humidité, les produits chimiques et l’air, réduisant ainsi le risque de rouille et de dégradation du métal. Cette protection contre la corrosion est particulièrement importante dans les secteurs où les pièces métalliques sont exposées à des conditions climatiques difficiles ou à des environnements agressifs, comme dans l’industrie automobile, la construction métallique et l’électroménager. De plus, cette couche de phosphate n’est pas seulement un bouclier contre la corrosion, elle contribue également à la durabilité globale des pièces traitées, prolongeant ainsi leur durée de vie et leur performance.
Un autre avantage majeur du lavage au phosphate est sa capacité à améliorer l’aspect esthétique des pièces traitées. Le processus permet d’obtenir une surface homogène, sans irrégularités ni imperfections visibles, ce qui assure un résultat final de haute qualité. Cette finition soignée est particulièrement recherchée dans des secteurs où l’apparence des produits est un critère important, comme dans l’industrie du design et de la décoration ou dans la fabrication de produits haut de gamme. La protection supplémentaire contre les agressions extérieures permet également de conserver l’aspect esthétique des pièces sur une période prolongée, sans que des retouches fréquentes ne soient nécessaires.
Le lavage au phosphate présente également des avantages en termes de coûts et d’efficacité. Par rapport à d’autres méthodes de préparation de surface, le processus de lavage au phosphate est relativement rapide et facile à mettre en œuvre. Il nécessite peu d’équipement et d’opérations manuelles, ce qui permet d’optimiser les coûts de production tout en garantissant une haute qualité de finition. De plus, le processus est facilement automatisable, ce qui augmente l’efficacité et la constance des résultats, tout en réduisant les erreurs humaines.
Un autre point important est l’aspect environnemental du lavage au phosphate. Bien que le processus utilise des produits chimiques spécifiques, il est possible de minimiser l’impact environnemental en adoptant des pratiques de gestion responsables. Par exemple, les solutions de phosphate peuvent être filtrées et traitées pour réduire leur toxicité, et les eaux usées peuvent être recyclées et réutilisées, ce qui permet de diminuer la consommation de ressources et de réduire les déchets. En outre, certaines formulations de phosphate sont désormais sans métaux lourds, ce qui permet de rendre ce processus plus respectueux de l’environnement.
En résumé, les avantages du lavage au phosphate sont nombreux et variés. Il améliore l’adhérence des revêtements, protège les pièces métalliques contre la corrosion, améliore l’aspect esthétique des produits finis, et est une méthode à la fois rentable et efficace pour préparer les surfaces métalliques. Bien que des considérations environnementales doivent être prises en compte, ce processus continue de jouer un rôle clé dans de nombreux secteurs industriels, en offrant des solutions de haute qualité pour garantir la performance et la durabilité des produits métalliques.
Enjeux environnementaux du lavage au phosphate
Le lavage au phosphate, bien qu’efficace pour la préparation des surfaces métalliques avant l’application de revêtements, soulève plusieurs enjeux environnementaux qui nécessitent une attention particulière. L’un des principaux défis réside dans la gestion des produits chimiques utilisés dans ce processus, notamment les sels de phosphate, qui peuvent contenir des métaux lourds tels que le zinc, le manganèse ou le fer. Ces substances chimiques, bien qu’efficaces pour traiter les surfaces métalliques, peuvent être nocives pour l’environnement si elles ne sont pas gérées correctement. Les résidus de phosphate, lorsqu’ils sont rejetés dans l’environnement sans un traitement adéquat, peuvent entraîner la pollution des sols et des eaux. Par exemple, le phosphate dans les cours d’eau peut provoquer une eutrophisation, un phénomène où un excès de nutriments entraîne une prolifération d’algues, perturbant ainsi l’équilibre des écosystèmes aquatiques.
Un autre enjeu majeur est celui de la gestion des effluents générés par le lavage au phosphate. Les solutions de phosphate utilisées pour le traitement des surfaces métalliques sont généralement accompagnées d’autres produits chimiques, comme des détergents ou des agents de dégraissage. Ces substances peuvent se retrouver dans les eaux usées, ce qui pose un problème de pollution. Il est donc essentiel d’installer des systèmes de traitement des eaux usées afin de neutraliser ou de filtrer ces produits chimiques avant leur rejet dans l’environnement. Sans un système de filtration adéquat, ces substances peuvent contaminer les nappes phréatiques et affecter la qualité de l’eau, avec des répercussions potentiellement graves pour la faune et la flore locales.
De plus, les processus de lavage au phosphate peuvent également entraîner la production de déchets solides, tels que les boues générées par la réaction chimique entre les phosphates et les métaux présents sur les surfaces. Ces boues, qui contiennent des résidus de métaux lourds, doivent être gérées avec soin pour éviter leur accumulation et leur dispersion dans l’environnement. Une gestion inefficace de ces déchets peut entraîner des risques de contamination des sols, ce qui peut affecter les cultures, la végétation et la biodiversité dans les zones proches des sites industriels.
Les préoccupations environnementales ont conduit à l’adoption de certaines pratiques visant à rendre le lavage au phosphate plus respectueux de l’environnement. Par exemple, de nombreuses entreprises investissent dans des systèmes de filtration avancés pour traiter les eaux usées et réduire leur impact sur les écosystèmes. De plus, l’utilisation de phosphates sans métaux lourds devient de plus en plus courante, ce qui réduit la toxicité du processus et permet une gestion plus simple des déchets. Certaines solutions de phosphate sont désormais formulées pour être plus facilement biodégradables et moins polluantes, contribuant ainsi à limiter les effets négatifs sur l’environnement.
Un autre aspect environnemental du lavage au phosphate est lié à l’empreinte énergétique du processus. En effet, bien que le lavage au phosphate soit relativement simple en termes d’équipement, il nécessite souvent un chauffage pour maintenir la température de la solution à un niveau optimal. Ce chauffage peut entraîner une consommation énergétique importante, surtout si les procédés ne sont pas optimisés. Une gestion plus efficace de l’énergie, comme l’utilisation de chauffages à faible consommation ou la récupération de chaleur, pourrait permettre de réduire l’impact environnemental du processus de lavage au phosphate.
En résumé, bien que le lavage au phosphate soit un procédé essentiel dans de nombreux secteurs industriels pour garantir la qualité et la durabilité des revêtements, il présente des enjeux environnementaux significatifs. La gestion des produits chimiques, des effluents et des déchets, ainsi que la consommation d’énergie, nécessitent une vigilance particulière. Cependant, avec l’adoption de technologies plus propres et de pratiques de gestion responsables, il est possible de réduire l’impact écologique de ce processus tout en continuant à bénéficier de ses avantages industriels.
Applications industrielles du lavage au phosphate avant le revêtement en poudre
Le lavage au phosphate avant l’application de revêtements en poudre est un processus couramment utilisé dans de nombreuses applications industrielles, principalement dans les secteurs où la résistance à la corrosion et la durabilité des produits sont essentielles. Ce traitement de surface est appliqué à des pièces métalliques pour garantir une bonne adhérence du revêtement en poudre, améliorer la résistance à la corrosion et prolonger la durée de vie des produits finis. Il est particulièrement utilisé dans l’industrie automobile, la fabrication de produits électroménagers, l’industrie de la construction métallique, ainsi que dans d’autres secteurs nécessitant des matériaux métalliques durables et de haute qualité.
Dans l’industrie automobile, le lavage au phosphate est largement utilisé pour traiter les pièces métalliques telles que les châssis, les jantes, les composants de carrosserie et les éléments de suspension avant d’appliquer un revêtement en poudre. Ces pièces sont souvent soumises à des conditions environnementales extrêmes, telles que l’humidité, le sel, les températures élevées et les produits chimiques, ce qui rend leur protection contre la corrosion particulièrement importante. Le processus de lavage au phosphate crée une couche de phosphate qui protège ces pièces métalliques contre la rouille et la dégradation, tout en assurant que le revêtement en poudre adhère de manière optimale. Ce traitement est donc essentiel pour garantir la longévité et la performance des composants automobiles.
Dans le secteur de la fabrication d’appareils électroménagers, le lavage au phosphate est également utilisé pour traiter les composants métalliques avant l’application d’un revêtement en poudre. Des produits comme les réfrigérateurs, les lave-linge, les micro-ondes et les cuisinières bénéficient de ce traitement pour améliorer leur résistance à l’humidité, aux produits chimiques et à l’usure. Les surfaces métalliques de ces appareils, telles que les cadres, les portes et les composants internes, sont d’abord nettoyées et traitées au phosphate pour améliorer l’adhérence du revêtement en poudre, ce qui leur confère une finition esthétique et résistante, tout en les protégeant contre la corrosion et les dommages liés à l’utilisation quotidienne.
Le lavage au phosphate est également couramment utilisé dans l’industrie de la construction métallique, où il est appliqué à des éléments comme les poutres, les colonnes, les structures en acier, ainsi que les équipements de stockage et les éléments architecturaux. Les pièces métalliques utilisées dans la construction, notamment les structures extérieures soumises aux intempéries, doivent résister à la rouille et à la dégradation pour garantir la sécurité et la stabilité des bâtiments. En appliquant un traitement au phosphate avant d’appliquer un revêtement en poudre, les fabricants de structures métalliques peuvent s’assurer que les pièces sont correctement protégées et que le revêtement adhère bien, augmentant ainsi leur longévité et leur efficacité dans des environnements extérieurs.
Les industries de l’énergie, notamment celles impliquées dans la production d’électricité et d’équipements industriels, utilisent également le lavage au phosphate avant le revêtement en poudre pour traiter des pièces métalliques destinées à des environnements difficiles. Par exemple, les équipements électriques et les composants exposés à des conditions extrêmes, tels que les transformateurs, les câbles métalliques et les dispositifs de protection, bénéficient de ce processus. Le lavage au phosphate assure une protection supplémentaire contre la corrosion et permet une meilleure performance du revêtement, garantissant que ces équipements conservent leur intégrité et leur fonctionnement sur le long terme.
En outre, le lavage au phosphate est utilisé dans de nombreuses autres industries, telles que l’aéronautique, la fabrication de meubles en métal, les équipements de loisirs et les produits métalliques de consommation. Dans ces secteurs, le processus de lavage au phosphate permet de garantir que les produits métalliques sont correctement préparés pour l’application d’un revêtement en poudre, ce qui leur confère une finition esthétique et fonctionnelle tout en assurant leur protection contre la rouille et l’usure. Par exemple, les meubles en métal, comme les chaises, les tables et les étagères, sont souvent traités au phosphate avant d’être revêtus de peinture en poudre pour garantir une durabilité et une résistance aux conditions d’utilisation.
Dans tous ces secteurs industriels, le lavage au phosphate joue un rôle crucial dans l’amélioration de la qualité des produits finis. En garantissant une surface propre et bien préparée avant l’application du revêtement en poudre, ce processus assure non seulement une meilleure adhésion et une finition plus homogène, mais il renforce également la résistance à la corrosion et augmente la durabilité des pièces métalliques. Ce traitement est donc essentiel pour la production d’articles métalliques de haute qualité, capables de résister aux conditions les plus exigeantes tout en offrant une esthétique soignée et durable.
Lavage au phosphate
Le lavage au phosphate avant le revêtement en poudre continue d’évoluer avec l’intégration de nouvelles technologies et pratiques qui visent à optimiser le processus, améliorer l’efficacité et réduire l’impact environnemental. Par exemple, l’adoption de systèmes automatisés et de contrôle en temps réel permet de surveiller de manière plus précise les paramètres critiques du processus, comme la température, la concentration des solutions et le temps d’exposition des pièces. Cela assure non seulement une meilleure uniformité du traitement, mais aussi une réduction des erreurs humaines et une plus grande fiabilité du processus global.
L’un des grands avantages des technologies récentes est l’optimisation des consommations d’énergie et de ressources. Des équipements plus performants permettent de réduire la quantité d’énergie nécessaire pour chauffer les solutions de phosphate et sécher les pièces. En parallèle, des innovations telles que les systèmes de filtration et de recyclage des solutions de phosphate permettent de prolonger la durée de vie des bains et de limiter leur rejet dans l’environnement. Cela représente une économie substantielle en termes de produits chimiques et d’eau, tout en répondant aux normes environnementales de plus en plus strictes.
Le lavage au phosphate avant le revêtement en poudre présente également des défis liés à la gestion des effluents et des déchets chimiques. Bien que des solutions de traitement des eaux usées existent, il est important de noter que le processus doit être intégré dans une démarche de gestion durable. De nombreuses entreprises adoptent désormais des approches de réduction des déchets en amont, comme l’utilisation de solutions de phosphate à faible teneur en chrome ou encore l’application de procédés sans métaux lourds, contribuant ainsi à limiter l’impact sur l’environnement tout en respectant les réglementations locales et internationales.
Un autre aspect important du lavage au phosphate est l’innovation continue dans les formulations des solutions de phosphate. Les fabricants développent des solutions de plus en plus efficaces et écologiques, qui offrent des résultats optimaux tout en réduisant la consommation de produits chimiques. Ces nouvelles solutions sont souvent moins agressives pour l’environnement et peuvent offrir des performances équivalentes à celles des solutions traditionnelles. Par exemple, des phosphatations à froid ou à température modérée permettent de diminuer la consommation d’énergie tout en maintenant une efficacité élevée.
Dans le cadre du processus de revêtement en poudre, la préparation de surface joue un rôle essentiel dans la qualité du produit final. Le lavage au phosphate assure que la surface soit prête à recevoir le revêtement de manière optimale, garantissant ainsi une meilleure adhérence et une résistance accrue aux conditions climatiques, aux chocs ou aux abrasions. En offrant une protection renforcée contre la corrosion, il prolonge la durée de vie des produits finis, ce qui est particulièrement crucial pour des applications en extérieur ou dans des environnements industriels difficiles.
De plus, la couche de phosphate agissant comme une base permet non seulement de renforcer la résistance mécanique du revêtement, mais elle améliore aussi l’esthétique des pièces traitées. En effet, un traitement de surface soigné et une préparation adéquate avant l’application du revêtement en poudre contribuent à un fini plus lisse et plus uniforme, ce qui est essentiel pour des applications où l’apparence joue un rôle primordial, comme dans l’industrie automobile ou l’électroménager.
Il est important de souligner que, bien que le processus de lavage au phosphate soit largement utilisé, il nécessite une expertise technique pour obtenir les meilleurs résultats. Les paramètres de traitement doivent être ajustés en fonction des matériaux traités, de la géométrie des pièces, ainsi que des caractéristiques du revêtement en poudre choisi. Une attention particulière doit être portée à chaque étape pour éviter toute contamination croisée ou des résidus de phosphate qui pourraient compromettre l’adhérence du revêtement.
En conclusion, le lavage au phosphate avant le revêtement en poudre est un processus clé dans la préparation des surfaces métalliques, apportant des bénéfices en termes de durabilité, de performance et d’esthétique. L’évolution technologique dans ce domaine continue de renforcer l’efficacité et la durabilité des traitements, tout en prenant en compte les impératifs environnementaux et économiques. Alors que les normes industrielles deviennent de plus en plus strictes, ce processus reste un pilier incontournable pour garantir la qualité et la longévité des produits finis.
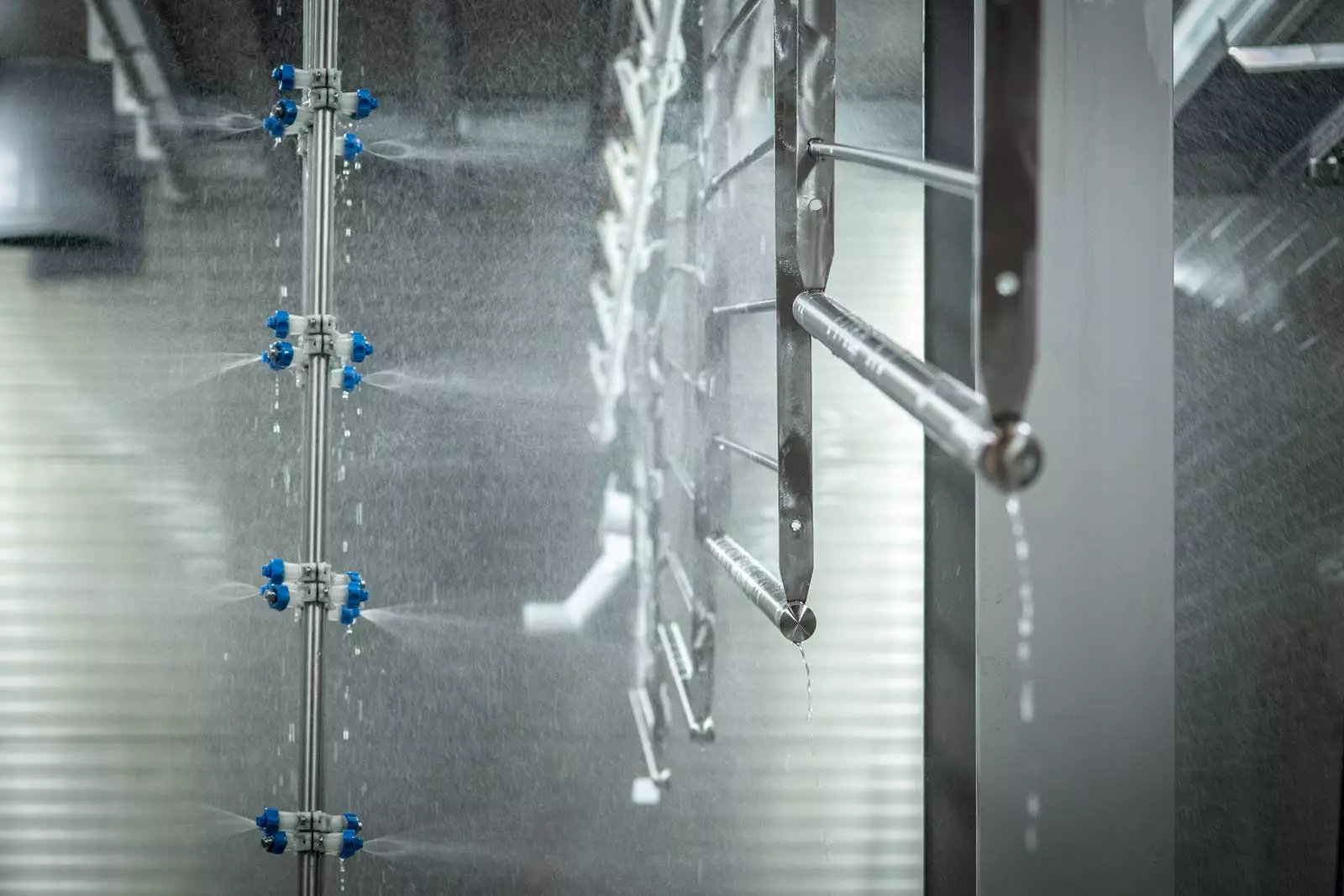
Le lavage au phosphate avant le revêtement en poudre continue d’évoluer et s’adapte aux nouveaux défis et exigences des industries modernes. L’optimisation des processus et l’intégration de nouvelles technologies permettent d’améliorer encore l’efficacité, la durabilité et la rentabilité du procédé, tout en répondant aux préoccupations environnementales croissantes.
L’une des grandes tendances actuelles dans le domaine du lavage au phosphate est l’introduction de solutions chimiques plus écologiques et respectueuses de l’environnement. Les régulations environnementales strictes, ainsi que la pression pour réduire l’empreinte écologique des processus industriels, incitent de nombreuses entreprises à se tourner vers des solutions sans phosphate ou avec des niveaux très faibles de métaux lourds. Ces solutions alternatives permettent de maintenir des performances de traitement élevées tout en réduisant la pollution et en facilitant le recyclage des effluents. Par exemple, certaines entreprises ont développé des produits de phosphatation à base de biotechnologie qui n’utilisent aucun phosphate et qui peuvent être entièrement biodégradables.
Parallèlement, des techniques telles que la phosphatation sans eau ou la phosphatation à froid gagnent en popularité. Ces technologies permettent de traiter les pièces métalliques sans utiliser d’eau chaude ou de produits chimiques à haute température, réduisant ainsi la consommation d’énergie et l’empreinte environnementale du processus. L’application de ces procédés à des températures plus basses non seulement diminue l’empreinte écologique mais offre également des avantages en termes de consommation d’énergie, ce qui représente un atout considérable dans un contexte où la réduction des coûts énergétiques est une priorité.
Les équipements de lavage au phosphate ont eux aussi évolué, devenant plus efficaces et plus automatisés. L’intégration de systèmes de contrôle avancés permet de gérer de manière précise la concentration des solutions de phosphate et la durée de l’exposition des pièces, assurant ainsi une qualité constante et réduisant les déchets chimiques. Ces systèmes automatisés permettent une production à plus grande échelle, avec une plus grande flexibilité et une meilleure traçabilité des processus, facilitant ainsi la conformité aux normes qualité et environnementales.
Le secteur de l’automobile, par exemple, utilise largement ce type de traitement pour préparer les composants métalliques avant l’application de revêtements en poudre, particulièrement dans le cas des pièces exposées aux intempéries, telles que les jantes, les châssis ou les éléments de carrosserie. Grâce au lavage au phosphate, ces pièces bénéficient d’une protection accrue contre la rouille et les autres formes de corrosion, ce qui est essentiel pour garantir leur longévité et leur performance dans des environnements difficiles.
Dans l’industrie de l’électroménager, le lavage au phosphate avant le revêtement en poudre est aussi utilisé pour des applications telles que les portes de réfrigérateurs, les châssis de machines à laver, ou les pièces métalliques exposées à des conditions d’humidité constante. La protection anticorrosion qu’il offre permet d’allonger la durée de vie des appareils tout en maintenant leur esthétique, même après plusieurs années d’utilisation.
Les innovations récentes dans le domaine de la gestion des effluents et des déchets du processus de lavage au phosphate sont également significatives. De plus en plus d’entreprises investissent dans des technologies de récupération et de traitement des effluents permettant de recycler les produits chimiques, d’éliminer les métaux lourds et de traiter les eaux usées de manière plus écologique. Ces technologies permettent de réduire les coûts liés à l’achat de nouvelles solutions de phosphate et de minimiser les risques de contamination de l’environnement.
Enfin, à mesure que les industries se tournent vers des pratiques de fabrication plus durables, l’intégration de processus de lavage au phosphate dans des chaînes de production « vertes » devient un atout stratégique. La réduction des déchets, l’optimisation des ressources et la mise en place de circuits de traitement fermés permettent aux entreprises de se conformer aux normes environnementales tout en préservant leur compétitivité sur le marché. Le lavage au phosphate avant le revêtement en poudre, bien qu’un processus traditionnel, continue de jouer un rôle clé dans cette transition vers une production plus respectueuse de l’environnement, alliant performance et développement durable.
Ainsi, bien que les principes fondamentaux du lavage au phosphate restent inchangés, le procédé a su évoluer pour répondre aux besoins actuels des industries modernes. L’introduction de solutions chimiques plus sûres, l’amélioration de l’automatisation, et la recherche de méthodes de traitement plus économes en énergie et en ressources en font un élément indispensable pour garantir des produits de qualité, durables et respectueux de l’environnement.
Revêtement de conversion de l’usine de prétraitement de revêtement en poudre
Le revêtement de conversion dans une usine de prétraitement de revêtement en poudre joue un rôle crucial dans la préparation des surfaces métalliques avant l’application du revêtement en poudre. Ce processus, qui fait partie intégrante des étapes de traitement de surface, a pour objectif de modifier les propriétés physiques et chimiques de la surface du métal, créant ainsi une couche de conversion qui améliore l’adhérence du revêtement en poudre, la résistance à la corrosion et l’aspect esthétique des pièces traitées.
Le revêtement de conversion est une réaction chimique contrôlée qui transforme la surface métallique en une couche fine et adhérente, souvent composée de sels métalliques. Cette couche est microporeuse et est généralement constituée de phosphate de zinc, de phosphate de fer ou d’autres types de composés chimiques, en fonction du métal sous-jacent et des propriétés recherchées. Elle sert de lien entre le métal brut et le revêtement en poudre, favorisant une meilleure adhérence et contribuant à la résistance globale de la pièce.
Le processus de conversion se réalise en plusieurs étapes. Tout d’abord, la surface métallique doit être soigneusement nettoyée et dégraissée pour éliminer toute contamination, comme les huiles, les graisses, ou les impuretés. Cela est généralement effectué par un lavage ou un dégraissage dans une solution chimique spécifique, qui prépare la pièce à recevoir la couche de conversion. Une fois la surface nettoyée, la pièce est immergée ou pulvérisée avec une solution de conversion, composée principalement de phosphates ou d’autres traitements chimiques adaptés à la nature du métal traité.
Les produits de conversion, comme le phosphate de zinc ou le phosphate de fer, réagissent avec la surface du métal pour former une couche protectrice. Cette couche est très fine, mais elle améliore de manière significative la résistance à la corrosion en créant une barrière contre l’humidité et les agents corrosifs. Par ailleurs, cette couche améliore l’adhésion du revêtement en poudre, qui est appliqué par la suite. L’adhérence est essentielle pour que le revêtement en poudre adhère uniformément et de manière durable à la pièce, garantissant ainsi sa performance à long terme.
Un des avantages majeurs du revêtement de conversion est sa capacité à améliorer la résistance à la corrosion des pièces traitées. La couche de conversion agit comme un bouclier protecteur, empêchant l’humidité et l’oxygène de pénétrer dans le métal et de provoquer des phénomènes de rouille ou d’oxydation. En combinaison avec le revêtement en poudre, qui offre une couche supplémentaire de protection, la pièce devient fortement résistante aux conditions environnementales, notamment dans des environnements industriels ou extérieurs où la corrosion peut être un problème majeur.
L’application d’un revêtement de conversion est souvent suivie de plusieurs étapes de rinçage pour éliminer les résidus chimiques de la surface, ainsi que d’un séchage soigneux avant l’application du revêtement en poudre. Le séchage permet de garantir que la surface est exempte d’humidité, ce qui est crucial pour éviter toute dégradation du revêtement en poudre lorsqu’il est appliqué. Ce processus peut être automatisé dans de nombreuses usines modernes, où des systèmes de convoyage et des chambres de séchage à température contrôlée permettent de traiter de grandes quantités de pièces de manière rapide et efficace.
Le revêtement de conversion offre également une solution adaptée pour les applications où des pièces métalliques sont soumises à des exigences esthétiques rigoureuses. En effet, ce traitement permet de créer une base uniforme, lisse et bien adhérente, qui prépare la surface à recevoir un revêtement en poudre d’une qualité supérieure. Le revêtement en poudre, une fois durci par chauffage, forme une finition lisse, durable et souvent plus esthétique que d’autres types de revêtements.
En plus de ses avantages en termes de performance, le revêtement de conversion présente des bénéfices économiques. Bien qu’il nécessite un investissement initial dans des équipements de traitement et des produits chimiques spécifiques, ce procédé permet d’améliorer la durabilité des pièces, réduisant ainsi les coûts liés à l’entretien et à la maintenance. De plus, la couche de conversion assure une meilleure efficacité du revêtement en poudre, ce qui peut également réduire la quantité de produit nécessaire pour obtenir une couverture complète et uniforme.
Le revêtement de conversion dans le cadre du prétraitement pour le revêtement en poudre est également de plus en plus adapté aux préoccupations environnementales. Les produits chimiques utilisés dans ce processus sont souvent modulables et de plus en plus respectueux de l’environnement. Par exemple, des solutions de conversion à faible teneur en chrome ou sans chrome hexavalent sont désormais largement disponibles. Ces solutions permettent de répondre aux normes environnementales de plus en plus strictes tout en offrant une performance de traitement équivalente, voire supérieure.
Il convient de noter que la gestion des effluents issus de ces traitements de conversion est également un enjeu majeur. Les entreprises investissent dans des systèmes de recyclage des solutions de conversion et de traitement des eaux usées, ce qui contribue à réduire l’impact environnemental du procédé. Le recyclage des solutions permet non seulement de réduire les coûts liés à l’achat de produits chimiques, mais également de diminuer les volumes d’effluents générés, en ligne avec les objectifs de durabilité de nombreuses entreprises.
En conclusion, le revêtement de conversion est une étape indispensable dans le processus de prétraitement avant l’application d’un revêtement en poudre. Il améliore l’adhérence du revêtement, renforce la résistance à la corrosion et contribue à la durabilité des pièces métalliques traitées. Avec l’évolution des technologies et la prise en compte des enjeux environnementaux, le revêtement de conversion continue de s’adapter et de jouer un rôle clé dans la qualité et la performance des revêtements en poudre dans divers secteurs industriels, de l’automobile à l’électroménager en passant par l’industrie de la construction et des équipements extérieurs.
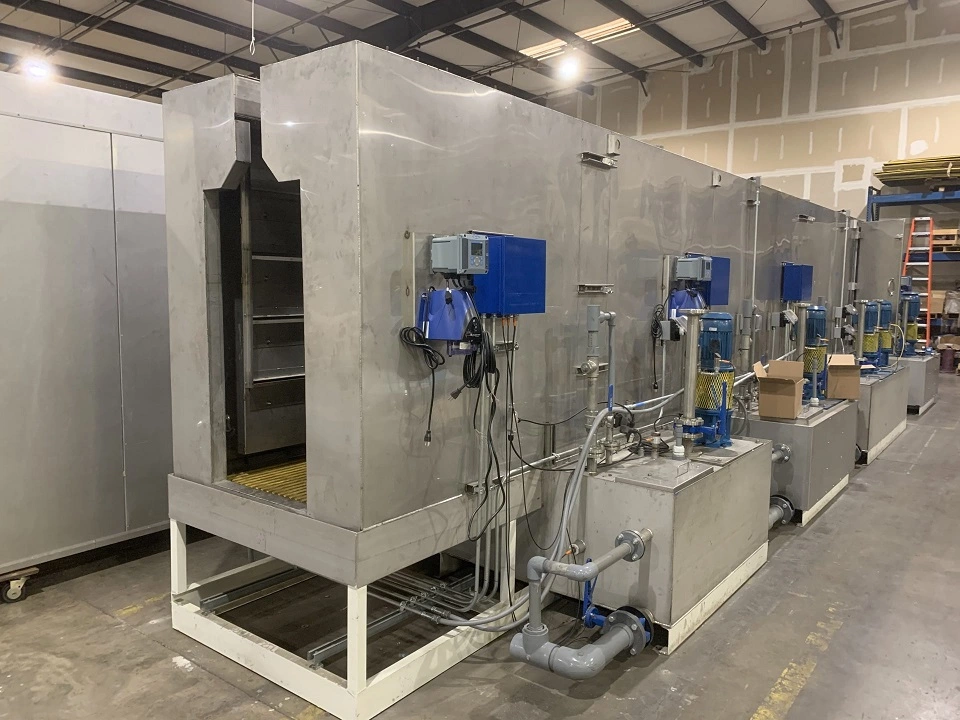
Le revêtement de conversion joue également un rôle fondamental dans l’optimisation des processus de production. En préparant les surfaces métalliques de manière homogène et efficace, il permet une meilleure gestion de la chaîne de production, réduisant ainsi les coûts liés à des défauts de fabrication, comme la mauvaise adhérence ou l’apparition de défauts dans le revêtement final. Cela se traduit par une réduction des rebuts et des retouches, ce qui améliore la rentabilité des opérations de revêtement en poudre.
Une autre évolution importante dans le domaine du revêtement de conversion est l’automatisation croissante des lignes de prétraitement. L’utilisation de robots et de systèmes automatisés pour appliquer les solutions de conversion, contrôler les paramètres de traitement et surveiller la qualité des pièces traitées permet de garantir une uniformité maximale, de réduire les variations liées aux erreurs humaines et d’accélérer le processus. Ces systèmes sont souvent équipés de capteurs sophistiqués et de dispositifs de surveillance en temps réel, qui ajustent les paramètres en fonction des conditions spécifiques de chaque lot de production, assurant ainsi un traitement optimal pour chaque pièce.
De plus, l’adoption de la numérisation et des systèmes de gestion de données dans les processus de prétraitement permet de collecter des informations précieuses sur les cycles de traitement. Ces données peuvent ensuite être utilisées pour analyser les tendances, détecter des anomalies et affiner les paramètres de production pour optimiser l’efficacité et la qualité. Par exemple, les données recueillies sur la température des bains de conversion, le temps d’exposition ou la concentration des produits chimiques peuvent être analysées pour maximiser l’efficacité du procédé, réduire la consommation de produits chimiques et améliorer les performances des revêtements finaux.
En termes d’impact environnemental, le secteur du revêtement de conversion s’efforce de se conformer aux normes de plus en plus strictes concernant les substances chimiques utilisées dans le traitement des surfaces métalliques. Le passage à des traitements sans chrome hexavalent, qui est reconnu comme un agent chimique particulièrement dangereux pour la santé et l’environnement, représente un changement majeur dans l’industrie. De plus, de nouvelles formulations de solutions de conversion sont développées pour être plus respectueuses de l’environnement, tout en offrant une efficacité comparable ou supérieure à celle des traitements traditionnels.
Les revêtements de conversion sans chrome hexavalent, par exemple, sont de plus en plus populaires dans les industries où la conformité aux réglementations environnementales est essentielle, comme dans l’automobile ou l’aéronautique. Ces traitements sont non seulement plus sûrs pour les opérateurs, mais ils permettent également aux entreprises de se conformer aux exigences de certification environnementale, telles que celles définies par le règlement REACH de l’Union Européenne. L’adoption de traitements alternatifs comme les solutions de conversion à base de zirconium ou de titane, qui sont également efficaces pour améliorer l’adhérence et la résistance à la corrosion, est en constante progression dans l’industrie.
Dans un contexte plus large, la tendance à la durabilité et à la responsabilité sociale des entreprises (RSE) influence directement le développement de solutions plus écologiques dans le secteur du revêtement de conversion. Les entreprises cherchent non seulement à minimiser leur impact environnemental en choisissant des produits et des procédés plus sûrs, mais aussi à intégrer des pratiques de recyclage et de réutilisation des ressources, y compris dans le traitement des effluents issus des bains de conversion. Les progrès dans la gestion des effluents, avec des technologies de traitement et de purification avancées, permettent de recycler une partie significative des solutions de conversion et de réduire la quantité de déchets générés.
En termes de performance des revêtements, le revêtement de conversion contribue de manière significative à la durabilité des pièces traitées. La résistance à la corrosion est particulièrement améliorée, ce qui est crucial dans les secteurs où les produits sont exposés à des conditions climatiques extrêmes ou à des environnements agressifs, comme dans l’industrie pétrolière et gazière, l’aéronautique, l’automobile ou même dans le domaine des équipements industriels en extérieur. Cette résistance accrue permet de prolonger la durée de vie des produits tout en réduisant les besoins en maintenance et en remplacement, offrant ainsi des économies substantielles sur le long terme.
Le processus de revêtement de conversion améliore également l’adhérence des revêtements en poudre, ce qui permet une finition esthétique plus uniforme et de meilleure qualité. La pièce métallique, après traitement, présente une surface plus lisse et plus homogène, ce qui est particulièrement important pour des applications visibles, comme les équipements de consommation, l’électroménager ou les produits de décoration. Le revêtement en poudre, une fois appliqué sur cette base de conversion, crée une finition résistante, lisse et esthétique, répondant aux exigences visuelles et fonctionnelles des clients.
Il est également essentiel de souligner l’importance du contrôle qualité dans le processus de revêtement de conversion. La qualité du traitement de conversion doit être surveillée en permanence pour garantir que la couche de conversion est uniformément appliquée et que ses propriétés sont optimales. Des techniques telles que les tests de résistance à l’adhérence, la vérification de l’épaisseur de la couche de conversion, et la mesure de la résistance à la corrosion sont couramment utilisées pour s’assurer que le processus respecte les normes strictes de qualité.
En résumé, le revêtement de conversion dans le cadre du prétraitement pour le revêtement en poudre est un élément clé pour assurer la qualité et la durabilité des produits métalliques. Il prépare la surface à recevoir le revêtement, améliore l’adhérence, protège contre la corrosion et permet d’obtenir une finition esthétique et fonctionnelle. Grâce à l’innovation technologique, à l’adoption de solutions plus écologiques et à l’automatisation accrue, le processus de revêtement de conversion devient de plus en plus efficace, rentable et respectueux de l’environnement, répondant aux exigences des industries modernes en termes de performance, de durabilité et de responsabilité sociale.
La prochaine étape du processus de prétraitement est le revêtement de conversion. Un revêtement de conversion est utilisé sur un substrat métallique pour assurer l’adhérence et la résistance à la corrosion.
Il existe trois types de base de revêtements de conversion :
- Phosphatation
- Revêtement de conversion chromique
Comment phosphater?
Le processus de phosphatation est une méthode de conversion de surface qui implique la formation d’une couche de phosphate sur le métal. La phosphatation est couramment utilisée dans le prétraitement de surface des métaux avant des processus tels que la peinture, le revêtement en poudre ou d’autres applications similaires. Voici une vue d’ensemble des étapes générales du processus de phosphatation :
- Préparation de la Surface :
- Avant le processus de phosphatation, il est essentiel de nettoyer soigneusement la surface métallique pour éliminer les contaminants tels que la graisse, l’huile, la rouille et autres impuretés. Cela peut impliquer une étape de dégraissage suivie d’un rinçage.
- Prétraitement Acide (en option) :
- Certains processus de phosphatation commencent par une étape de prétraitement acide pour nettoyer davantage la surface du métal. Cette étape peut utiliser des acides tels que l’acide phosphorique ou d’autres solutions acides.
- Lavage :
- Les pièces nettoyées sont ensuite lavées pour éliminer tout résidu de la phase de préparation. Le lavage est généralement effectué à l’eau.
- Phosphatation :
- Les pièces sont immergées dans une solution de phosphate. Cette solution peut contenir des composés de phosphate tels que des phosphates de zinc, de fer ou de manganèse, en fonction des exigences du processus. La phosphatation peut être réalisée à chaud ou à froid en fonction de la méthode choisie.
- Rinçage :
- Après la phosphatation, les pièces sont soigneusement rincées pour éliminer tout excès de solution de phosphate. Un rinçage approprié est crucial pour éviter tout résidu chimique qui pourrait affecter le revêtement ultérieur.
- Séchage :
- Les pièces sont ensuite séchées correctement avant de passer à la prochaine étape du processus. Un séchage adéquat est essentiel pour garantir la qualité du revêtement ultérieur.
Variantes de la Phosphatation :
- Phosphatation au Zinc : Utilise des composés de phosphate de zinc pour former une couche de conversion de surface de phosphate de zinc.
- Phosphatation au Fer : Utilise des composés de phosphate de fer pour former une couche de conversion de surface de phosphate de fer.
- Phosphatation au Manganèse : Utilise des composés de phosphate de manganèse pour former une couche de conversion de surface de phosphate de manganèse.
- Phosphatation à Froid : La phosphatation à froid peut être utilisée à température ambiante, tandis que la phosphatation à chaud nécessite des températures plus élevées.
Contrôle de la Qualité :
Le processus de phosphatation est souvent soumis à des tests de contrôle de la qualité pour s’assurer que la couche de phosphate est uniforme, adhérente et conforme aux spécifications requises.
Il est important de noter que le choix des composés de phosphate, des températures et des étapes spécifiques peut varier en fonction des matériaux des pièces, des exigences du revêtement final et des spécifications du processus. En outre, des considérations environnementales doivent être prises en compte lors de l’utilisation de produits chimiques dans ces processus.
Phosphatation au Zinc
La phosphatation au zinc est un processus de conversion de surface qui utilise des composés de phosphate de zinc pour former une couche de conversion de surface sur des pièces métalliques. Ce processus est couramment utilisé dans le prétraitement de surface avant des applications telles que la peinture, le revêtement en poudre ou d’autres revêtements protecteurs. Voici les étapes générales du processus de phosphatation au zinc :
- Préparation de la Surface :
- Les pièces métalliques sont d’abord nettoyées soigneusement pour éliminer les contaminants tels que la graisse, l’huile, la rouille et d’autres impuretés. Une étape de dégraissage suivie d’un rinçage est souvent réalisée.
- Prétraitement Acide (en option) :
- Certains processus de phosphatation au zinc peuvent commencer par une étape de prétraitement acide pour nettoyer davantage la surface du métal. Cette étape peut utiliser des acides tels que l’acide phosphorique ou d’autres solutions acides.
- Lavage :
- Les pièces sont ensuite lavées pour éliminer tout résidu de la phase de préparation. Le lavage est généralement effectué à l’eau.
- Phosphatation au Zinc :
- Les pièces sont immergées dans une solution de phosphate de zinc. Cette solution contient des composés de phosphate de zinc qui réagissent avec la surface du métal pour former une couche de conversion de phosphate de zinc. La phosphatation peut être réalisée à chaud ou à froid en fonction des spécifications du processus.
- Rinçage :
- Après la phosphatation, les pièces sont soigneusement rincées pour éliminer tout excès de solution de phosphate de zinc. Un rinçage approprié est crucial pour éviter tout résidu chimique qui pourrait affecter le revêtement ultérieur.
- Séchage :
- Les pièces sont séchées correctement avant de passer à la prochaine étape du processus. Un séchage adéquat est essentiel pour garantir la qualité du revêtement ultérieur.
Contrôle de la Qualité :
Le processus de phosphatation au zinc est souvent soumis à des tests de contrôle de la qualité pour s’assurer que la couche de phosphate de zinc est uniforme, adhérente et conforme aux spécifications requises. Des tests d’adhérence du revêtement, des tests de corrosion et d’autres analyses peuvent être effectués.
La phosphatation au zinc offre plusieurs avantages, notamment une meilleure adhérence des revêtements ultérieurs, une résistance à la corrosion accrue et une amélioration des propriétés mécaniques de la surface métallique. Elle est couramment utilisée dans l’industrie automobile, l’industrie des appareils électroménagers, et d’autres applications nécessitant une protection anticorrosion efficace.
Phosphatation au Fer
La phosphatation au fer est un processus de conversion de surface qui utilise des composés de phosphate de fer pour former une couche de conversion de surface sur des pièces métalliques. Ce processus est fréquemment utilisé dans le prétraitement de surface avant des applications telles que la peinture, le revêtement en poudre ou d’autres revêtements protecteurs. Voici une vue d’ensemble des étapes générales du processus de phosphatation au fer :
- Préparation de la Surface :
- Les pièces métalliques sont d’abord nettoyées soigneusement pour éliminer les contaminants tels que la graisse, l’huile, la rouille et d’autres impuretés. Une étape de dégraissage suivie d’un rinçage est souvent réalisée.
- Prétraitement Acide (en option) :
- Certains processus de phosphatation au fer peuvent commencer par une étape de prétraitement acide pour nettoyer davantage la surface du métal. Cette étape peut utiliser des acides tels que l’acide phosphorique ou d’autres solutions acides.
- Lavage :
- Les pièces sont ensuite lavées pour éliminer tout résidu de la phase de préparation. Le lavage est généralement effectué à l’eau.
- Phosphatation au Fer :
- Les pièces sont immergées dans une solution de phosphate de fer. Cette solution contient des composés de phosphate de fer qui réagissent avec la surface du métal pour former une couche de conversion de phosphate de fer. La phosphatation peut être réalisée à chaud ou à froid en fonction des spécifications du processus.
- Rinçage :
- Après la phosphatation, les pièces sont soigneusement rincées pour éliminer tout excès de solution de phosphate de fer. Un rinçage approprié est crucial pour éviter tout résidu chimique qui pourrait affecter le revêtement ultérieur.
- Séchage :
- Les pièces sont séchées correctement avant de passer à la prochaine étape du processus. Un séchage adéquat est essentiel pour garantir la qualité du revêtement ultérieur.
Contrôle de la Qualité :
Le processus de phosphatation au fer est souvent soumis à des tests de contrôle de la qualité pour s’assurer que la couche de phosphate de fer est uniforme, adhérente et conforme aux spécifications requises. Des tests d’adhérence du revêtement, des tests de corrosion et d’autres analyses peuvent être effectués.
La phosphatation au fer offre des avantages similaires à celle au zinc, tels qu’une meilleure adhérence des revêtements ultérieurs, une résistance à la corrosion accrue et une amélioration des propriétés mécaniques de la surface métallique. Ce processus est utilisé dans diverses industries, notamment l’automobile, la construction, l’aérospatiale et d’autres domaines où une protection anticorrosion et une amélioration des propriétés de la surface sont essentielles.
Rinçage après lavage au phosphate avant revêtement en poudre
Le rinçage après lavage au phosphate est une étape essentielle dans le processus de prétraitement avant le revêtement en poudre. Après que les pièces métalliques aient été nettoyées et traitées avec une solution de phosphate pour améliorer l’adhérence et la résistance à la corrosion, il est crucial d’éliminer toute solution résiduelle de phosphate sur les surfaces pour garantir que la couche de conversion ne soit pas contaminée et que le revêtement en poudre puisse adhérer correctement. Le rinçage permet non seulement d’éliminer les résidus chimiques mais aussi de prévenir la formation de taches ou de dépôts qui pourraient affecter la qualité finale du revêtement.
Le processus de rinçage après le lavage au phosphate commence généralement par l’utilisation d’eau de qualité contrôlée, afin d’éviter tout contaminant supplémentaire. L’eau de rinçage doit être propre, exempte de minéraux et d’impuretés qui pourraient interférer avec l’adhésion du revêtement en poudre. Souvent, des systèmes de filtration et des adoucisseurs d’eau sont utilisés pour garantir la pureté de l’eau utilisée lors de cette étape. Le rinçage est effectué dans des bains ou des jets d’eau, où les pièces sont exposées à un flux constant d’eau pour éliminer efficacement les restes de phosphate.
Une fois les résidus de phosphate éliminés, il est essentiel de s’assurer que l’eau de rinçage ne contient pas de produits chimiques ou d’impuretés qui pourraient compromettre la qualité du revêtement en poudre. Dans certains cas, un rinçage final est effectué avec de l’eau déminéralisée ou distillée, particulièrement pour les applications où une finition parfaite et une protection accrue contre la corrosion sont requises. Cela garantit que les pièces sont exemptes de contaminants avant de passer à l’étape suivante du processus.
Le rinçage après le lavage au phosphate joue également un rôle important dans la préparation de la surface des pièces pour l’application du revêtement en poudre. Une surface propre et parfaitement rinçée permet à la poudre de mieux adhérer et de former une couche homogène, sans imperfections ni bulles d’air. Cela est particulièrement important pour des applications où l’aspect esthétique est essentiel, comme dans l’industrie automobile ou l’électroménager.
Une fois les pièces rincées, elles doivent être séchées soigneusement pour éliminer toute trace d’humidité. Un séchage inapproprié peut entraîner la formation de moisissures ou d’autres défauts qui compromettraient la qualité du revêtement. Le séchage peut être réalisé à l’aide de séchoirs à air chaud ou dans des chambres de séchage spécialement conçues pour maintenir une température constante et contrôler le temps de séchage. Cela permet de s’assurer que les pièces sont complètement sèches avant qu’elles ne soient soumises à l’application de la poudre.
L’efficacité du rinçage après lavage au phosphate dépend de plusieurs facteurs, y compris la conception du système de rinçage, la qualité de l’eau utilisée, la durée de l’exposition et la température de l’eau. Pour améliorer l’efficacité et la durabilité du processus, certaines entreprises mettent en place des systèmes de rinçage en plusieurs étapes, où chaque bain successive est conçu pour éliminer les impuretés restantes. Ces systèmes peuvent inclure des rinçages à faible pression, des rinçages par pulvérisation ou des rinçages en cascade, en fonction de la taille et de la complexité des pièces à traiter.
Une autre amélioration du processus de rinçage consiste à l’intégration de systèmes de contrôle automatique, qui régulent les paramètres du rinçage en fonction de la charge de pièces traitées et de la concentration de produits chimiques dans l’eau. L’automatisation permet de garantir un rinçage uniforme, de réduire la consommation d’eau et de minimiser les erreurs humaines.
En plus de l’aspect technique, il est important de considérer l’impact environnemental du rinçage après le lavage au phosphate. L’élimination efficace des produits chimiques utilisés dans le processus de lavage est essentielle pour éviter la contamination de l’environnement. De nombreuses entreprises optent pour des solutions de traitement des eaux usées, telles que la filtration, la décontamination chimique ou l’utilisation de réacteurs biologiques, pour purifier l’eau de rinçage avant de la rejeter dans l’environnement. Cela permet non seulement de respecter les normes environnementales locales mais aussi de réduire la consommation de ressources naturelles, en permettant le recyclage de l’eau de rinçage dans le processus de production.
En conclusion, le rinçage après le lavage au phosphate est une étape cruciale pour garantir la qualité du revêtement en poudre et pour assurer que les pièces métalliques traitées bénéficient d’une protection optimale contre la corrosion. Cette phase permet de préparer les surfaces pour l’application du revêtement, d’éviter les défauts d’adhérence et de préserver l’aspect esthétique des pièces. En optimisant le processus de rinçage, tant sur le plan technique qu’environnemental, il est possible d’améliorer la productivité, la rentabilité et la durabilité des produits finis tout en minimisant l’impact écologique.
Le rinçage après le lavage au phosphate est une étape cruciale dans le processus de prétraitement de surface avant le revêtement en poudre. Après la phosphatation, les pièces métalliques sont généralement rincées soigneusement pour éliminer tout résidu de la solution de phosphate et préparer la surface pour le revêtement en poudre. Voici quelques points importants à considérer concernant le rinçage après le lavage au phosphate
- Élimination des Résidus :
- Le rinçage a pour objectif d’éliminer efficacement tous les résidus de la solution de phosphate de la surface des pièces. Cela garantit que la surface est propre et prête à recevoir le revêtement en poudre.
- Prévention de la Contamination du Revêtement :
- Les résidus de la solution de phosphate peuvent affecter négativement l’adhérence et la qualité du revêtement en poudre. Le rinçage minutieux réduit le risque de contamination du revêtement par des substances étrangères.
- Utilisation d’Eau Propre :
- L’eau utilisée pour le rinçage doit être propre et exempte de contaminants. Des systèmes de traitement de l’eau peuvent être mis en place pour garantir la pureté de l’eau de rinçage.
- Contrôle de la Qualité :
- Le processus de rinçage doit être contrôlé et surveillé pour s’assurer de son efficacité. Des tests de contrôle de la qualité peuvent être effectués pour vérifier la propreté de la surface après le rinçage.
- Conservation de l’Énergie et de l’Eau :
- L’efficacité du rinçage est importante, mais il est également essentiel de minimiser la consommation d’eau et d’énergie. Les systèmes de rinçage peuvent être conçus pour être écoénergétiques et respectueux de l’environnement.
- Séchage :
- Après le rinçage, les pièces doivent être correctement séchées avant de passer à l’étape suivante du processus. Un séchage adéquat est nécessaire pour éviter la formation de taches d’eau et d’assurer une surface propre.
- Automatisation :
- Dans les installations de traitement de surface modernes, le rinçage peut être automatisé pour assurer la cohérence et l’efficacité du processus. Des systèmes de contrôle automatisés peuvent être utilisés pour réguler le débit d’eau, le temps de rinçage, et d’autres paramètres.
- Conformité aux Normes Environnementales :
- L’utilisation d’eau de rinçage doit être conforme aux normes environnementales locales. Certains systèmes de traitement des eaux de rinçage peuvent être nécessaires pour garantir la conformité.
Le rinçage après le lavage au phosphate est une étape critique dans le processus de prétraitement de surface, et son efficacité a un impact direct sur la qualité du revêtement en poudre final. Un rinçage bien réalisé contribue à assurer une adhérence optimale, une résistance à la corrosion accrue et une durabilité du revêtement en poudre.
L’équipement de revêtement en poudre est utilisé pour appliquer une fine couche de poudre sur une surface métallique. Ce type de revêtement est appliqué par un procédé électrostatique et constitue une méthode très populaire pour la finition des pièces métalliques.
Ce type d’équipement peut être divisé en deux grandes catégories : automatiques et manuels. Les cabines automatiques sont plus populaires car elles offrent de meilleurs taux de production, mais elles sont également plus chères.
Une cabine à poudre est une enceinte dans laquelle se déroule le processus de revêtement en poudre. L’équipement de revêtement en poudre comprend un four dans lequel les pièces sont chauffées pour activer la poudre, un pistolet qui pulvérise ou brosse la poudre, une bande transporteuse qui déplace les pièces à travers le four et des pistolets de type cartouche pour appliquer des revêtements plus épais avec moins de pulvérisation.
Le revêtement en poudre est une technique utilisée pour donner une finition aux pièces métalliques. Cette technique est utilisée depuis de nombreuses années et reste aujourd’hui l’une des techniques les plus populaires.
L’équipement de revêtement en poudre comprend des cabines, des fours, des pistolets, des machines, des lignes et des convoyeurs. Une cabine peut être automatique ou manuelle. Une cabine automatique est plus chère qu’une cabine manuelle mais elle est aussi plus rapide et plus efficace
Prétraitement phosphatant :
Le prétraitement phosphatant est une étape cruciale dans le processus de revêtement en poudre. Il implique l’application d’une fine couche de phosphate métallique sur la surface du matériau, généralement à base de zinc ou de fer. Ce traitement vise à améliorer l’adhérence du revêtement en poudre, à fournir une protection anticorrosion et à favoriser l’uniformité du revêtement. Le phosphate créé sert de base réactive pour la liaison chimique avec le revêtement ultérieur. Ce processus est essentiel pour garantir la durabilité et la qualité esthétique des produits finis.
Revêtement en poudre :
Le revêtement en poudre est une technique de finition de surface largement utilisée dans l’industrie pour appliquer une couche protectrice ou décorative sur des objets en métal. Cette méthode implique l’application électrostatique d’une poudre de résine polymère sur la surface du matériau, suivie de la cuisson à haute température pour fusionner et durcir la poudre, formant ainsi un revêtement durable et résistant. Le revêtement en poudre offre une excellente adhérence, une résistance à la corrosion et une finition uniforme, en faisant un choix populaire pour diverses applications industrielles et commerciales.
Dégraissage :
Le dégraissage est une étape fondamentale du processus de prétraitement avant le revêtement en poudre. Il vise à éliminer les contaminants tels que les huiles, graisses et autres impuretés présentes à la surface du matériau. Cela se fait généralement par immersion dans des bains dégraissants chimiques ou par des procédés de nettoyage mécaniques. Le dégraissage assure une surface propre, exempt de toute substance qui pourrait compromettre l’adhérence du revêtement en poudre, garantissant ainsi une application homogène et une protection accrue contre la corrosion.
Conversion chimique :
La conversion chimique est une étape de prétraitement qui transforme la surface du matériau en une couche chimiquement réactive, favorisant l’adhérence du revêtement ultérieur. Ce processus implique souvent l’application de solutions contenant des agents chimiques tels que des phosphates, des chromates ou des oxydes métalliques. La conversion chimique crée une surface propice à la liaison moléculaire du revêtement, améliorant ainsi la durabilité, la résistance à la corrosion et l’uniformité de la finition. Cette étape joue un rôle crucial dans l’optimisation des performances du revêtement en poudre.
Nettoyage de surface :
Le nettoyage de surface est une étape essentielle du prétraitement visant à éliminer les contaminants présents à la surface du matériau avant l’application du revêtement en poudre. Ce processus peut inclure des méthodes mécaniques telles que le sablage ou le brossage, ainsi que des traitements chimiques pour éliminer les particules indésirables. Un nettoyage approfondi garantit une adhérence maximale du revêtement, prévient la formation de défauts tels que les bulles ou les éclats, et contribue à la qualité esthétique et fonctionnelle du produit final.
Phosphate de zinc :
Le phosphate de zinc est un composé chimique utilisé fréquemment dans le processus de prétraitement avant le revêtement en poudre. Appliqué sur la surface du matériau métallique, le phosphate de zinc crée une couche réactive qui favorise l’adhérence du revêtement ultérieur. En plus de cette fonction clé, le phosphate de zinc offre une protection anticorrosion, améliorant la durabilité du matériau. Ce traitement chimique contribue également à uniformiser la surface, assurant une répartition homogène du revêtement en poudre et optimisant ainsi les propriétés finales du produit.
Processus de lavage :
Le processus de lavage dans le contexte du prétraitement avant le revêtement en poudre implique l’élimination des résidus de traitements chimiques précédents, tels que les phosphates, les dégraissants, ou autres contaminants. Ce lavage assure une surface propre, prête à recevoir le revêtement. Les méthodes de lavage peuvent varier, allant du rinçage à l’eau à des procédés plus complexes. L’efficacité du processus de lavage influe directement sur l’adhérence du revêtement en poudre et la qualité globale du produit fini.
Préparation de surface :
La préparation de surface englobe l’ensemble des procédés visant à rendre la surface du matériau propice à recevoir un revêtement en poudre. Cela inclut le dégraissage, le nettoyage, la conversion chimique et d’autres traitements préliminaires. L’objectif est de créer une surface propre, uniforme et réactive, favorisant une adhérence optimale du revêtement. Une préparation de surface adéquate est cruciale pour garantir la durabilité, la résistance à la corrosion, et l’esthétique du produit final, tout en minimisant les défauts potentiels du revêtement en poudre.
Traitement préalable :
Le traitement préalable est une phase préliminaire avant l’application du revêtement en poudre, visant à préparer la surface du matériau de manière à optimiser l’efficacité du processus. Il comprend diverses étapes telles que le dégraissage, le nettoyage, la conversion chimique, et peut également impliquer l’application de produits spécifiques pour améliorer l’adhérence du revêtement. Un traitement préalable bien exécuté garantit non seulement une meilleure liaison du revêtement, mais contribue également à la résistance à la corrosion et à la durabilité du produit final.
Revêtement anticorrosion :
Le revêtement anticorrosion est un élément clé du processus de revêtement en poudre, destiné à protéger la surface du matériau contre les effets néfastes de la corrosion. Les traitements préalables, tels que la conversion chimique avec des composés anticorrosion, contribuent à créer une barrière protectrice. Le revêtement en poudre appliqué par la suite offre une couche supplémentaire de protection, empêchant la corrosion et assurant la longévité du matériau dans des environnements divers, de l’extérieur industriel aux applications intérieures.
Adhérence du revêtement :
L’adhérence du revêtement est la capacité du revêtement en poudre à se lier de manière solide à la surface du matériau de base. Les étapes de prétraitement, telles que le dégraissage, la conversion chimique et le nettoyage de surface, jouent un rôle crucial dans l’amélioration de cette adhérence. Une adhérence efficace garantit la stabilité du revêtement, prévient le décollement prématuré, et contribue à la résistance aux contraintes mécaniques. C’est un paramètre essentiel pour assurer la durabilité et la qualité esthétique du produit final revêtu en poudre.
Phosphatation :
La phosphatation est un processus de conversion chimique où une fine couche de phosphate est déposée sur la surface métallique du matériau. Cela se fait souvent en utilisant des solutions contenant des phosphates métalliques, tels que le phosphate de zinc. La phosphatation améliore l’adhérence du revêtement en poudre en créant une surface réactive, favorisant ainsi la liaison moléculaire du revêtement. De plus, elle offre une protection anticorrosion, contribuant à la durabilité du matériau. Ce processus est essentiel pour optimiser les performances du revêtement en poudre dans diverses applications industrielles.
Décapage :
Le décapage est une étape du processus de prétraitement qui vise à éliminer les revêtements existants, les oxydations, ou d’autres contaminants présents à la surface du matériau. Cela peut être réalisé mécaniquement, chimiquement ou thermiquement, selon la nature des revêtements ou des substances à éliminer. Le décapage prépare la surface du matériau de base pour les étapes suivantes du traitement, comme la phosphatation ou le revêtement en poudre, en assurant une adhérence optimale et en garantissant la qualité du résultat final.
Revêtement métallique :
Le revêtement métallique consiste à appliquer une couche métallique sur la surface d’un matériau de base. Ce processus peut être réalisé par diverses méthodes, y compris l’électrodéposition ou l’évaporation sous vide. Dans le contexte du prétraitement avant le revêtement en poudre, le revêtement métallique peut jouer un rôle dans l’amélioration de la conductivité, de l’adhérence du revêtement en poudre, ou encore dans l’esthétique finale du produit. La nature du revêtement métallique peut varier, par exemple avec des métaux tels que le zinc pour une protection anticorrosion.
Protection contre la corrosion :
La protection contre la corrosion est un objectif majeur du processus de revêtement en poudre. Les étapes de prétraitement, telles que la conversion chimique et l’application de phosphates, contribuent à créer une barrière protectrice sur la surface du matériau. Le revêtement en poudre lui-même offre une protection supplémentaire en formant une couche solide et durable. La combinaison de ces mesures garantit une résistance accrue contre les effets corrosifs, assurant la longévité des produits dans des environnements variés, de l’extérieur industriel aux applications intérieures.
Prétraitement métallique :
Le prétraitement métallique englobe l’ensemble des procédures préliminaires appliquées à une surface métallique avant l’application du revêtement en poudre. Ces procédures visent à préparer la surface en éliminant les contaminants, en favorisant l’adhérence du revêtement, et en fournissant une protection contre la corrosion. Le dégraissage, le nettoyage, la conversion chimique, et l’application de revêtements métalliques, tels que les phosphates de zinc, sont des éléments clés de ce processus, garantissant une préparation adéquate pour un revêtement en poudre réussi.
Revêtement électrostatique :
Le revêtement électrostatique est une méthode d’application de revêtements, dont la poudre, qui tire avantage de charges électriques. L’objet à revêtir est chargé électriquement, et la poudre de revêtement est chargée oppositement, créant une attraction électrostatique. Cela favorise une répartition uniforme de la poudre sur la surface, même dans les zones difficiles d’accès. Après l’application, le revêtement est fusionné lors de la cuisson, formant une couche solide et uniforme. Cette technique est largement utilisée pour sa précision, son efficacité et sa capacité à minimiser le gaspillage de matériau.
Phosphate de fer :
Le phosphate de fer est un composé chimique utilisé dans le processus de prétraitement avant le revêtement en poudre, similaire au phosphate de zinc. Appliqué sur la surface métallique, le phosphate de fer crée une couche réactive qui favorise l’adhérence du revêtement en poudre. En plus de son rôle d’amélioration de l’adhérence, le phosphate de fer offre une protection anticorrosion, renforçant ainsi la résistance à la corrosion du matériau traité. Ce type de phosphate est particulièrement utilisé lorsque des propriétés spécifiques liées au fer sont requises dans l’application finale.
Élimination des contaminants :
L’élimination des contaminants est une étape clé du prétraitement visant à retirer toute substance indésirable de la surface du matériau avant l’application du revêtement en poudre. Cela inclut les huiles, les graisses, les oxydes et d’autres impuretés susceptibles d’entraver l’adhérence du revêtement. Des méthodes mécaniques, chimiques ou une combinaison des deux sont utilisées pour garantir une surface propre et réactive. L’efficacité de l’élimination des contaminants influence directement la qualité du revêtement final, assurant une adhérence maximale et une résistance accrue contre la corrosion.
Prétraitement chimique :
Le prétraitement chimique constitue une série de procédés chimiques appliqués à la surface du matériau avant le revêtement en poudre. Il englobe des étapes telles que la conversion chimique et l’application de phosphates, visant à créer une surface réactive favorable à l’adhérence du revêtement. Ce traitement chimique contribue également à la protection contre la corrosion en formant des composés résistants. Le prétraitement chimique, par son action spécifique sur la composition de la surface, joue un rôle crucial dans l’amélioration des propriétés mécaniques et de la durabilité du revêtement en poudre.
Amélioration de l’adhérence :
L’amélioration de l’adhérence est une considération centrale du prétraitement avant le revêtement en poudre. Des procédures telles que la conversion chimique, l’application de phosphates, et d’autres méthodes spécifiques, sont mises en œuvre pour créer une surface texturée et réactive. Ces caractéristiques favorisent une liaison moléculaire robuste entre la surface du matériau et le revêtement en poudre ultérieur. Une adhérence améliorée assure une cohésion optimale du revêtement, minimisant les risques de décollement et garantissant une performance durable du produit final.
Revêtement de protection :
Le revêtement de protection est la couche appliquée sur la surface du matériau pour assurer une barrière physique contre les éléments environnementaux, les dommages mécaniques et la corrosion. Dans le contexte du prétraitement avant le revêtement en poudre, des traitements comme la conversion chimique et l’application de phosphates contribuent à renforcer cette couche de protection. Le revêtement en poudre final, en fusionnant avec la surface prétraitée, offre une protection supplémentaire, assurant la durabilité et la résistance du matériau aux conditions extérieures ou aux contraintes spécifiques de l’application.
Nettoyage des métaux :
Le nettoyage des métaux est une étape fondamentale du prétraitement visant à éliminer les contaminants de la surface métallique. Il peut inclure des techniques mécaniques, chimiques ou une combinaison des deux pour assurer une élimination efficace des huiles, des poussières et d’autres impuretés. Un nettoyage méticuleux crée une surface propice à l’adhérence du revêtement en poudre, contribuant ainsi à la qualité du résultat final. Un prétraitement de nettoyage approprié garantit également une meilleure résistance à la corrosion et une performance durable du revêtement en poudre.
Phosphatation des métaux :
La phosphatation des métaux est un processus de conversion chimique appliqué spécifiquement aux métaux. Il implique la formation d’une fine couche de phosphate métallique sur la surface du matériau. Dans le cadre du prétraitement avant le revêtement en poudre, la phosphatation des métaux, tels que le zinc ou le fer, joue un rôle crucial. Ce traitement non seulement favorise l’adhérence du revêtement en poudre, mais offre également une protection anticorrosion, améliorant ainsi la durabilité du matériau traité. La phosphatation des métaux est un maillon essentiel pour garantir les performances optimales du revêtement en poudre dans diverses applications industrielles.
Procédé de phosphatation :
Le procédé de phosphatation est une méthode spécifique de conversion chimique utilisée dans le prétraitement avant le revêtement en poudre. Il implique l’application de solutions contenant des phosphates, créant ainsi une couche de phosphate métallique réactive à la surface du matériau. Ce procédé favorise l’adhérence du revêtement en poudre en fournissant une base chimique pour la liaison moléculaire. De plus, la phosphatation offre une protection contre la corrosion, renforçant ainsi la résistance du matériau aux facteurs environnementaux. Le choix précis du procédé de phosphatation dépend souvent du type de métal à traiter et des exigences spécifiques de l’application finale.
Lavage acide :
Le lavage acide est une étape du prétraitement qui implique l’utilisation de solutions acides pour nettoyer et préparer la surface du matériau avant le revêtement en poudre. Ces solutions acides éliminent les impuretés, les oxydes et les contaminants, créant une surface réactive. Le lavage acide peut également favoriser une adhérence accrue du revêtement en poudre en créant une texture favorable. C’est une méthode précise qui contribue à assurer la qualité et la durabilité du revêtement final en éliminant tout ce qui pourrait compromettre son adhérence et sa résistance.
Prétraitement de surface :
Le prétraitement de surface est une phase complète du processus avant le revêtement en poudre. Il englobe diverses étapes telles que le nettoyage, le dégraissage, la phosphatation et d’autres traitements spécifiques visant à préparer la surface du matériau. L’objectif principal est d’optimiser l’adhérence du revêtement en poudre, d’améliorer la résistance à la corrosion et de garantir une finition esthétique de haute qualité. La séquence et la nature des étapes de prétraitement de surface sont adaptées en fonction du matériau de base et des exigences de l’application finale du revêtement en poudre.
Revêtement par immersion :
Le revêtement par immersion est une méthode d’application de revêtements où l’objet à revêtir est immergé dans un bain contenant le revêtement liquide, par opposition à une application par pulvérisation ou électrostatique. Dans le contexte du prétraitement avant le revêtement en poudre, cette technique peut être utilisée pour appliquer des agents de conversion chimique ou des revêtements préliminaires. Elle assure une couverture uniforme, en particulier dans les zones difficiles d’accès, et contribue à préparer la surface du matériau pour le revêtement en poudre final.
Revêtement à sec :
Le revêtement à sec fait référence à une méthode d’application de revêtements sans utiliser de solvants liquides. Dans le contexte du prétraitement avant le revêtement en poudre, cela peut impliquer l’application de poudre sèche avant la cuisson. Cette approche réduit les émissions de solvants, ce qui est avantageux d’un point de vue environnemental. Le prétraitement avant le revêtement à sec doit garantir une surface propre et réactive pour assurer une adhérence optimale de la poudre lors du processus de cuisson, aboutissant à un revêtement final de haute qualité.
Traitement de conversion :
Le traitement de conversion est une étape du prétraitement avant le revêtement en poudre où la surface du matériau est modifiée chimiquement pour favoriser l’adhérence du revêtement. Cela peut impliquer la formation de couches converties, telles que des phosphates ou des chromates, qui fournissent une base réactive pour le revêtement en poudre ultérieur. Le traitement de conversion joue un rôle essentiel dans l’amélioration des propriétés anticorrosion du matériau tout en optimisant l’efficacité du processus de revêtement en poudre.
Traitement phosphatant :
Le traitement phosphatant est une étape spécifique du prétraitement avant le revêtement en poudre où une fine couche de phosphate est appliquée sur la surface du matériau. Cette conversion chimique, souvent réalisée avec des phosphates de métaux tels que le zinc, favorise l’adhérence du revêtement en poudre et offre une protection anticorrosion. Le traitement phosphatant crée une surface réactive, prête à recevoir le revêtement final. L’efficacité de cette étape influence directement la qualité et la durabilité du revêtement en poudre appliqué ultérieurement.
Préparation avant peinture :
La préparation avant peinture englobe l’ensemble des étapes de prétraitement visant à préparer la surface du matériau pour l’application d’une peinture ou d’un revêtement. Cela peut inclure des processus tels que le nettoyage, le dégraissage, la phosphatation et d’autres traitements spécifiques pour assurer une adhérence optimale de la peinture. Une préparation minutieuse avant la peinture est cruciale pour garantir une finition esthétique durable, résistante à la corrosion et aux facteurs environnementaux.
Étape de lavage :
L’étape de lavage dans le processus de prétraitement avant le revêtement en poudre est cruciale pour éliminer les résidus de traitements antérieurs, tels que les dégraissants ou les solutions de phosphatation. Ce lavage assure une surface propre et débarrassée de toute substance susceptible de compromettre l’adhérence du revêtement en poudre. Un lavage efficace contribue à la qualité du revêtement final en assurant une distribution homogène et une liaison solide entre la surface du matériau et le revêtement en poudre ultérieur.
Revêtement par projection électrostatique :
Le revêtement par projection électrostatique est une méthode d’application de revêtements en poudre où une charge électrostatique est utilisée pour faciliter l’adhérence de la poudre sur la surface du matériau. L’objet à revêtir est chargé électriquement, tandis que la poudre est chargée de manière opposée, créant une attraction électrostatique qui assure une répartition uniforme de la poudre. Cette technique permet une couverture efficace, même dans les zones difficiles d’accès, contribuant ainsi à la qualité et à l’uniformité du revêtement en poudre final.
Adhérence améliorée :
L’amélioration de l’adhérence est un objectif central du prétraitement avant le revêtement en poudre. Cette étape, souvent réalisée par des procédés tels que la conversion chimique et l’application de phosphates, vise à créer une surface réactive qui favorise une liaison moléculaire forte avec le revêtement en poudre. Une adhérence améliorée garantit une fixation solide, minimisant les risques de décollement du revêtement et contribuant ainsi à la durabilité et à la résistance du produit final face aux contraintes mécaniques et environnementales.
Phosphate de manganèse :
Le phosphate de manganèse est un composé chimique utilisé dans le prétraitement avant le revêtement en poudre. Appliqué sur la surface du matériau, il joue un rôle similaire à d’autres phosphates métalliques, favorisant l’adhérence du revêtement en poudre et offrant une protection anticorrosion. Le phosphate de manganèse est particulièrement utilisé lorsque des propriétés spécifiques liées au manganèse sont recherchées, et son application contribue à renforcer la résistance du matériau aux conditions environnementales adverses.
Phosphate alcalin :
Le phosphate alcalin est un composé chimique utilisé dans le prétraitement avant le revêtement en poudre. Il fait partie des solutions phosphatantes et est souvent appliqué sur la surface du matériau métallique. Cette méthode, connue sous le nom de phosphatation alcaline, vise à créer une couche de phosphate alcalin réactive. Cette couche favorise l’adhérence du revêtement en poudre tout en offrant une protection anticorrosion. Le choix du type de phosphate, y compris le phosphate alcalin, dépend des propriétés spécifiques recherchées pour le matériau traité.
Lavage final :
La phase de lavage final dans le processus de prétraitement avant le revêtement en poudre est une étape critique pour éliminer les résidus restants et assurer une surface propre. Après les traitements antérieurs tels que la phosphatation, le dégraissage et d’autres étapes chimiques, le lavage final élimine les dernières impuretés. Cela crée une surface prête à recevoir le revêtement en poudre, garantissant une adhérence maximale et contribuant à la qualité du produit final en évitant les défauts potentiels tels que les bulles ou les éclats.
Étape de préparation :
L’étape de préparation dans le processus de prétraitement avant le revêtement en poudre englobe un ensemble de procédures visant à préparer la surface du matériau pour le revêtement ultérieur. Cela inclut le nettoyage, le dégraissage, la conversion chimique, et d’autres traitements spécifiques. L’objectif est d’optimiser l’adhérence du revêtement en poudre, de renforcer la résistance à la corrosion, et de garantir une finition esthétique de haute qualité. La séquence et la nature de ces étapes varient en fonction du matériau de base et des exigences spécifiques de l’application finale du revêtement en poudre.
Revêtement en poudre thermodurcissable :
Le revêtement en poudre thermodurcissable est une méthode de revêtement qui utilise des poudres contenant des polymères thermodurcissables. Ces poudres réagissent chimiquement lors de la cuisson, formant une liaison solide et durable sur la surface du matériau. Dans le contexte du prétraitement avant ce type de revêtement en poudre, les étapes visent à assurer une surface propre et réactive pour favoriser la réaction chimique correcte lors de la cuisson, aboutissant à un revêtement final résistant et de haute qualité.
Revêtement en poudre thermoplastique :
Le revêtement en poudre thermoplastique est une méthode de revêtement qui utilise des poudres contenant des polymères thermoplastiques. Contrairement aux polymères thermodurcissables, les polymères thermoplastiques fondent lorsqu’ils sont chauffés et durcissent en refroidissant. Dans le prétraitement avant ce type de revêtement en poudre, les étapes visent à préparer la surface du matériau pour garantir une adhérence optimale de la poudre thermoplastique et à assurer une finition durable après le processus de fusion-refroidissement.
Revêtement hybride :
Un revêtement hybride combine des caractéristiques de revêtements en poudre thermodurcissables et thermoplastiques dans une seule formulation. Dans le contexte du prétraitement, les étapes sont adaptées pour préparer la surface du matériau en vue de la réaction thermique et de la fusion-refroidissement associées aux deux types de polymères. Cela nécessite une approche de prétraitement soigneusement ajustée pour assurer une adhérence optimale et une finition de haute qualité lors de l’application du revêtement hybride en poudre.
Revêtement en poudre transparent :
Le revêtement en poudre transparent est une formulation spécifique utilisée pour des applications où la visibilité de la surface du matériau est souhaitée. Dans le cadre du prétraitement, les étapes visent à assurer une surface propre et réactive tout en minimisant les impuretés et les défauts qui pourraient altérer la transparence du revêtement. La transparence peut être recherchée pour des raisons esthétiques ou fonctionnelles, permettant ainsi aux caractéristiques de la surface du matériau de rester visibles après l’application du revêtement en poudre.
Dépoussiérage :
L’étape de dépoussiérage dans le processus de prétraitement avant le revêtement en poudre vise à éliminer toute poussière ou particule fine présente à la surface du matériau. Cela garantit une surface propre et exempte de contaminants avant l’application du revêtement en poudre. Le dépoussiérage contribue à assurer une adhérence optimale du revêtement, à éviter les défauts potentiels tels que les inclusions de poussière, et à garantir la qualité esthétique et fonctionnelle du produit final.
Il semble y avoir une répétition du numéro de mot-clé. Si vous avez une autre demande ou un autre mot-clé en tête, n’hésitez pas à me le faire savoir !
Revêtement en poudre à effet métallique :
Le revêtement en poudre à effet métallique est une formulation spéciale qui confère à la surface une apparence métallique. Dans le prétraitement avant l’application de ce type de revêtement, les étapes sont adaptées pour garantir une surface propre et réactive tout en prenant en compte les caractéristiques esthétiques uniques associées à l’effet métallique. L’objectif est d’assurer une adhérence optimale de la poudre tout en préservant les propriétés visuelles distinctives du revêtement en poudre à effet métallique après le processus de cuisson.
Revêtement en poudre isolant électrique :
Le revêtement en poudre isolant électrique est conçu pour fournir une isolation électrique sur la surface du matériau. Dans le cadre du prétraitement avant l’application de ce type de revêtement, les étapes visent à créer une surface propre et réactive tout en assurant que le revêtement en poudre isolant adhère correctement. Ces précautions sont essentielles pour garantir l’efficacité de l’isolation électrique après le durcissement du revêtement en poudre.
Revêtement en poudre antibactérien :
Le revêtement en poudre antibactérien intègre des agents antimicrobiens dans sa formulation pour inhiber la croissance des bactéries sur la surface du matériau. Dans le prétraitement avant l’application de ce type de revêtement, les étapes sont adaptées pour garantir une surface propre et réactive tout en maintenant l’efficacité des agents antibactériens. Ces précautions sont essentielles pour assurer la fonction antibactérienne du revêtement en poudre après le processus de cuisson.
Revêtement en poudre ignifuge :
Le revêtement en poudre ignifuge est formulé pour fournir une résistance accrue au feu à la surface du matériau. Dans le prétraitement avant l’application de ce type de revêtement, les étapes sont adaptées pour assurer une surface propre et réactive tout en préservant les propriétés ignifuges du revêtement en poudre. Ces précautions sont cruciales pour garantir que le matériau traité conserve ses caractéristiques ignifuges après le durcissement du revêtement en poudre.
Revêtement en poudre conducteur électrique :
Le revêtement en poudre conducteur électrique est formulé pour permettre la conduction électrique à travers la surface du matériau. Dans le prétraitement avant l’application de ce type de revêtement, les étapes sont adaptées pour garantir une surface propre et réactive tout en préservant la conductivité électrique du revêtement en poudre. Ces précautions sont essentielles pour assurer que le matériau traité conserve ses propriétés conductrices après le durcissement du revêtement en poudre.
Revêtement en poudre à faible émission de COV :
Le revêtement en poudre à faible émission de COV est formulé pour minimiser les émissions de composés organiques volatils (COV) lors du processus de cuisson. Dans le prétraitement avant l’application de ce type de revêtement, les étapes sont adaptées pour garantir une surface propre et réactive tout en contribuant à la réduction des émissions de COV pendant le durcissement du revêtement en poudre. Ces précautions sont importantes pour répondre aux normes environnementales et assurer une application respectueuse de l’environnement.