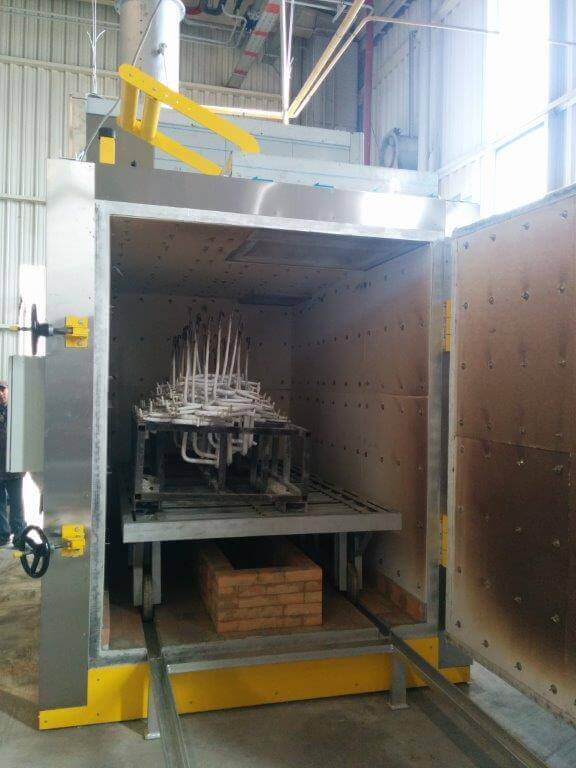
Fours Pyrox Nettoyage Industriel : Expertise Avancée dans le Nettoyage des Fours Industriels. Les procédés industriels reposant sur l’utilisation de fours jouent un rôle essentiel dans de nombreuses industries, allant de la métallurgie à l’industrie alimentaire. Cependant, au fil du temps, l’accumulation de résidus, de dépôts et de contaminants peut compromettre l’efficacité opérationnelle de ces équipements cruciaux. C’est là que Fours Pyrox Nettoyage Industriel entre en jeu avec son savoir-faire avancé dans le domaine du nettoyage spécialisé des fours industriels.
1. Technologie de Nettoyage Avancée :
Fours Pyrox utilise des technologies de nettoyage de pointe pour assurer un résultat optimal. Les méthodes employées intègrent des techniques mécaniques, thermiques et chimiques, adaptées aux spécificités de chaque four industriel. Grâce à une compréhension approfondie des matériaux et des résidus impliqués, Fours Pyrox garantit un processus de nettoyage efficace sans compromettre l’intégrité structurelle des équipements.
2. Personnel Qualifié et Certifié :
L’équipe de Fours Pyrox est composée de professionnels hautement qualifiés et certifiés, spécialisés dans le nettoyage industriel des fours. Leur expertise s’étend à la manipulation sécurisée des équipements, à la connaissance des produits chimiques et à la compréhension des protocoles de sécurité, assurant une prestation fiable et conforme aux normes les plus strictes.
3. Adaptabilité aux Besoins Spécifiques :
Chaque four industriel présente des caractéristiques uniques, et Fours Pyrox reconnaît l’importance d’une approche personnalisée. Avant d’initier le processus de nettoyage, une évaluation approfondie est menée pour comprendre les exigences spécifiques du four en question. Ceci permet de concevoir un plan de nettoyage sur mesure, optimisé pour maximiser l’efficacité sans compromettre la sécurité.
4. Respect de l’Environnement :
Conscient de l’importance croissante de la durabilité, Fours Pyrox intègre des pratiques respectueuses de l’environnement dans ses opérations. Le choix des produits chimiques, la gestion des déchets et l’utilisation efficace des ressources sont tous pris en compte pour minimiser l’impact environnemental tout en assurant des résultats exceptionnels.
5. Maintenance Préventive :
Fours Pyrox ne se contente pas de nettoyer les fours existants, mais propose également des services de maintenance préventive. Cette approche proactive vise à prolonger la durée de vie utile des équipements, à minimiser les temps d’arrêt et à optimiser les performances opérationnelles, contribuant ainsi à une productivité accrue.
En conclusion, Fours Pyrox Nettoyage Industriel se positionne comme un leader dans le secteur du nettoyage des fours industriels, offrant une combinaison unique de technologie avancée, de personnel qualifié et d’engagement envers l’environnement. Leur approche personnalisée et leur focus sur la prévention font de Fours Pyrox un partenaire de confiance pour les entreprises cherchant à maintenir l’intégrité et l’efficacité de leurs équipements thermiques critiques.
Nettoyage Industriel des Fours
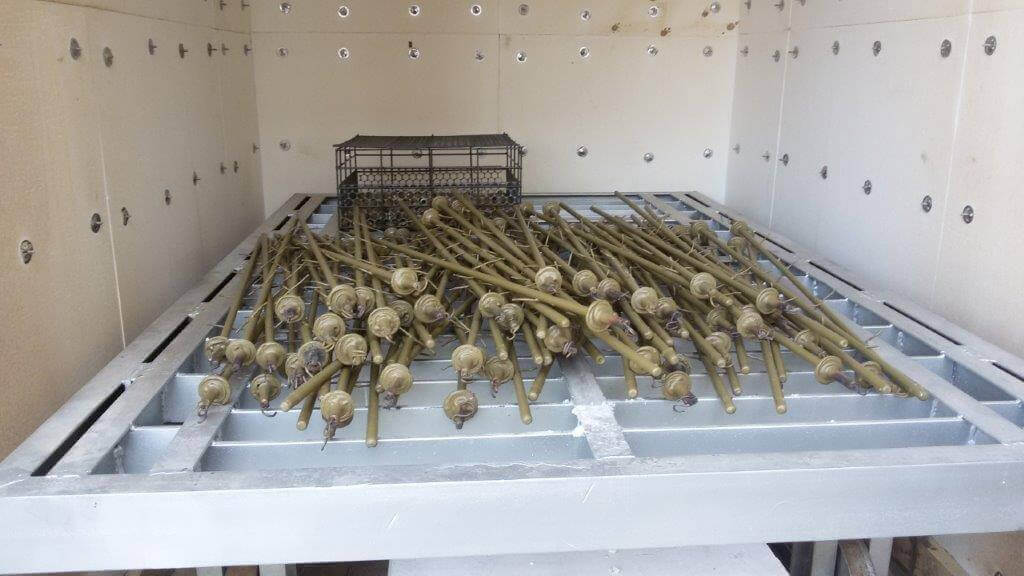
Le nettoyage industriel des fours est une étape cruciale dans le maintien de l’efficacité opérationnelle des équipements thermiques utilisés dans divers secteurs. Fours Pyrox Nettoyage Industriel excelle dans cette discipline, offrant une expertise spécialisée pour éliminer les résidus et les contaminants qui s’accumulent au fil du temps. Ce processus méticuleux garantit non seulement le respect des normes de sécurité et d’hygiène, mais il contribue également à prolonger la durée de vie utile des fours, réduisant ainsi les coûts de maintenance et minimisant les risques de dysfonctionnement.
Nettoyage industriel des fours :
Le nettoyage industriel des fours constitue un volet essentiel de la gestion proactive des équipements thermiques au sein des secteurs industriels. Dans cet aspect critique de l’entretien, Fours Pyrox Nettoyage Industriel s’impose comme un chef de file, apportant une expertise pointue et des solutions innovantes.
La démarche de nettoyage industriel déployée par Fours Pyrox transcende la simple élimination des résidus, elle incarne une fusion de connaissances techniques approfondies et de technologies de pointe. Chaque intervention est précédée d’une analyse minutieuse des spécificités du four concerné, prenant en compte les matériaux, les résidus, et les conditions opérationnelles uniques à chaque installation.
L’équipe dédiée au nettoyage industriel chez Fours Pyrox est composée de professionnels qualifiés, certifiés et expérimentés. Leur savoir-faire s’étend au-delà de la simple exécution de tâches, englobant la compréhension approfondie des principes thermiques, des réactions chimiques et des normes de sécurité industrielles.
Le processus de nettoyage industriel va au-delà de l’aspect esthétique. En éliminant les dépôts indésirables, les obstructions, et les résidus carbonisés, Fours Pyrox optimise les performances des fours. Cette approche proactive contribue à la réduction des temps d’arrêt imprévus, à l’amélioration de l’efficacité énergétique, et à la préservation des investissements industriels.
Dans un monde où la durabilité est une préoccupation majeure, Fours Pyrox s’engage à intégrer des pratiques respectueuses de l’environnement. Le choix des produits chimiques, les méthodes de gestion des déchets, et l’approche globale du nettoyage s’alignent sur les normes environnementales les plus strictes.
En conclusion, le nettoyage industriel des fours par Fours Pyrox est bien plus qu’une simple prestation de service. C’est une alliance entre la technologie de pointe, l’expertise humaine, et un engagement envers l’efficacité durable des équipements thermiques. En choisissant Fours Pyrox, les industries font le choix d’une approche intégrée du nettoyage, visant à préserver la fiabilité et la performance optimale de leurs fours industriels.
Expertise en nettoyage thermique
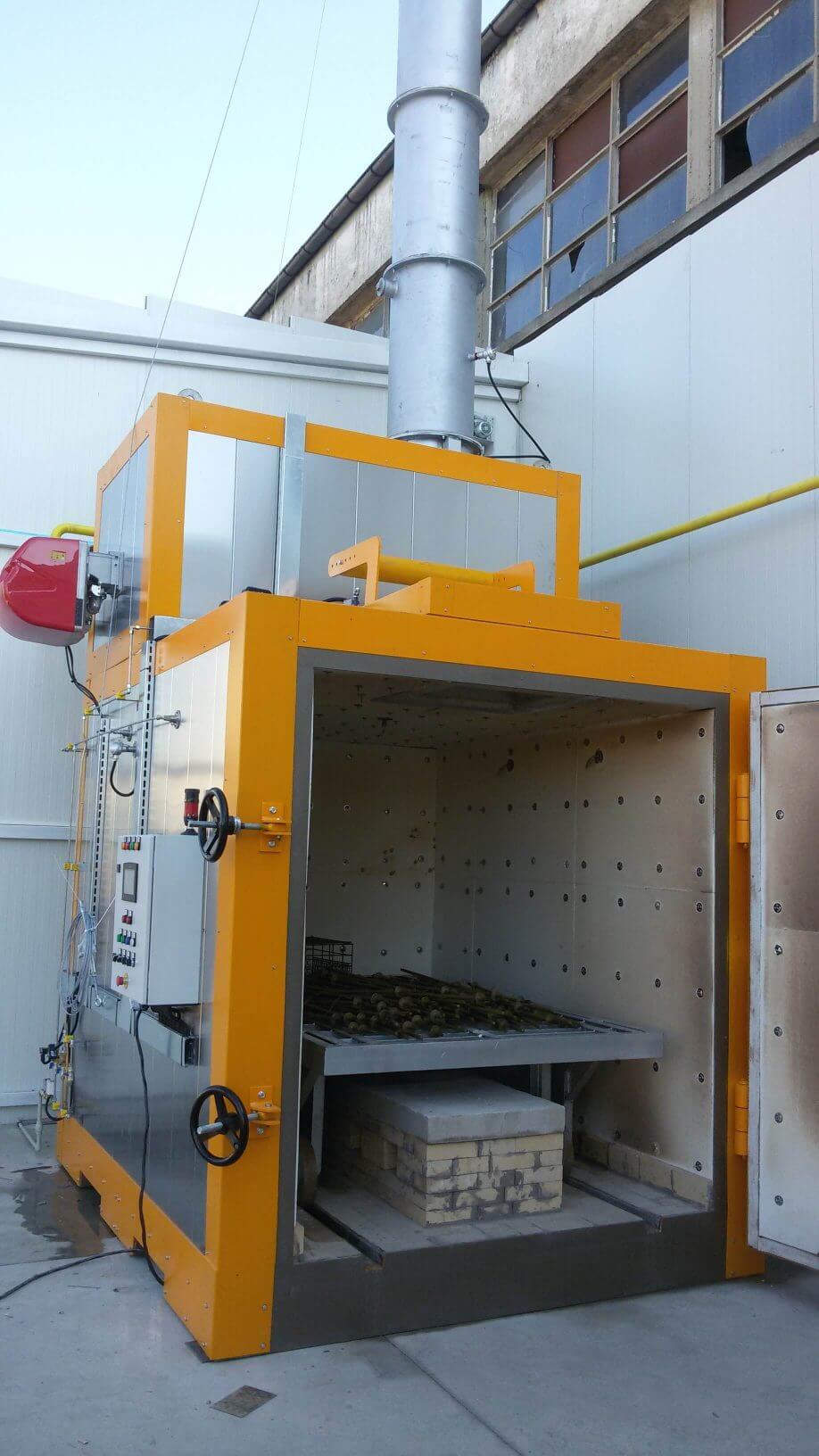
L’expertise en nettoyage thermique est le pilier central de l’approche distinctive de Fours Pyrox Nettoyage Industriel. Cette discipline exige une compréhension approfondie des processus thermiques, des matériaux utilisés dans la construction des fours, et des implications spécifiques liées à la chaleur et aux fluctuations de température. Fours Pyrox excelle dans cette expertise, offrant des solutions sur mesure pour le nettoyage thermique des équipements industriels.
L’analyse détaillée des caractéristiques thermiques des fours est une phase fondamentale de chaque intervention de nettoyage thermique réalisée par Fours Pyrox. Cette étape préliminaire permet d’ajuster les méthodes de nettoyage en fonction des réponses thermiques attendues, garantissant ainsi une élimination optimale des contaminants sans compromettre l’intégrité des matériaux.
Les professionnels de Fours Pyrox spécialisés dans le nettoyage thermique sont dotés d’une connaissance approfondie des propriétés thermiques des substances, des phénomènes de transfert de chaleur, et des protocoles de sécurité inhérents à ces processus. Leur expertise s’étend à la manipulation sécurisée des équipements, minimisant les risques de dégradation tout en assurant une efficacité maximale.
Le nettoyage thermique par Fours Pyrox ne se limite pas à la simple élimination des résidus. Il s’agit d’une optimisation minutieuse des performances thermiques des équipements, contribuant ainsi à une exploitation plus efficiente des fours industriels. Cette approche proactive a un impact significatif sur la réduction des coûts énergétiques, la minimisation des émissions, et la maximisation de la durée de vie utile des équipements thermiques.
Fours Pyrox s’engage à demeurer à la pointe des avancées technologiques dans le domaine du nettoyage thermique. En combinant une expertise humaine hautement qualifiée et une approche technologique de pointe, Fours Pyrox continue d’établir de nouvelles normes en matière de nettoyage thermique industriel, offrant ainsi à ses clients une garantie d’efficacité et de fiabilité inégalée.
Technologie avancée de nettoyage :
La technologie avancée de nettoyage est le fer de lance de l’approche innovante de Fours Pyrox Nettoyage Industriel. Cette entreprise se distingue par son utilisation de technologies de pointe pour garantir des résultats de nettoyage exceptionnels, tout en assurant la préservation de l’intégrité des équipements industriels.
Fours Pyrox intègre des techniques mécaniques, thermiques et chimiques de pointe dans son arsenal technologique. Ces méthodes sont minutieusement adaptées aux spécificités de chaque four industriel, assurant ainsi une élimination efficace des dépôts et des contaminants sans compromettre la structure ou les performances des équipements. L’utilisation de technologies avancées garantit également une réduction significative des temps d’arrêt, contribuant ainsi à optimiser la productivité des installations industrielles.
Les procédés de nettoyage par ultrasons, les méthodes thermiques à haute pression et l’application ciblée de produits chimiques spécialisés sont autant d’exemples des technologies utilisées par Fours Pyrox. Ces approches novatrices permettent une pénétration en profondeur et une élimination efficace des contaminants, même dans les zones difficiles d’accès, assurant ainsi une propreté optimale des fours industriels.
En plus de la mise en œuvre de technologies spécifiques de nettoyage, Fours Pyrox utilise également des équipements de surveillance avancés. Cela permet une évaluation en temps réel des conditions de nettoyage, garantissant une adaptation instantanée des méthodes pour répondre aux défis spécifiques rencontrés pendant le processus de nettoyage. Cette approche proactive maximise l’efficacité tout en minimisant les risques opérationnels.
En somme, la technologie avancée de nettoyage de Fours Pyrox représente l’union harmonieuse entre l’innovation technologique et les besoins spécifiques des fours industriels. Cette approche garantit des résultats de nettoyage exceptionnels, positionnant Fours Pyrox en tant que leader incontesté dans le secteur du nettoyage industriel à la pointe de la technologie.
Maintenance préventive des équipements thermiques :
La maintenance préventive des équipements thermiques est un axe stratégique essentiel au cœur de l’approche proactive de Fours Pyrox Nettoyage Industriel. Plutôt que de simplement intervenir après l’apparition de problèmes, cette approche préventive vise à anticiper les éventuelles défaillances des fours industriels, minimisant ainsi les temps d’arrêt et optimisant la fiabilité opérationnelle.
Fours Pyrox offre un programme de maintenance préventive rigoureux, adapté aux spécificités de chaque four industriel. Cette démarche débute par une analyse approfondie des performances passées et actuelles de l’équipement, identifiant ainsi les zones potentielles de dégradation ou de détérioration. L’équipe de Fours Pyrox établit ensuite un calendrier de maintenance, incluant des inspections régulières, des interventions planifiées et des mises à niveau anticipées.
Les professionnels de la maintenance préventive chez Fours Pyrox sont des experts chevronnés, possédant une connaissance approfondie des mécanismes internes des fours industriels. Ils sont formés pour identifier les signes précurseurs de défaillance, que ce soit au niveau des composants électriques, des éléments thermiques, ou des systèmes de contrôle. Cette vigilance proactive permet d’anticiper les problèmes potentiels et d’apporter des solutions avant qu’ils n’affectent la productivité.
La maintenance préventive de Fours Pyrox ne se limite pas au nettoyage. Elle inclut également la vérification des systèmes de contrôle, la calibration des instruments, et la détection précoce de tout signe de détérioration des matériaux. Cette approche holistique vise à prolonger la durée de vie utile des équipements, à minimiser les coûts de réparation imprévus, et à assurer une performance optimale à long terme.
Opter pour la maintenance préventive de Fours Pyrox, c’est investir dans la continuité opérationnelle. C’est une stratégie intelligente qui permet de maximiser la disponibilité des fours industriels, de réduire les risques d’arrêts non planifiés, et d’optimiser l’efficacité énergétique. Fours Pyrox s’engage à être un partenaire de confiance, guidant ses clients vers une gestion proactive de leurs équipements thermiques pour une performance inégalée.
Professionnels certifiés en nettoyage industriel :
L’équipe de professionnels certifiés en nettoyage industriel chez Fours Pyrox représente le socle solide sur lequel repose la qualité exceptionnelle des services de nettoyage. Ces experts hautement qualifiés apportent une combinaison unique de connaissances techniques, de compétences opérationnelles et de certifications formelles, assurant ainsi une prestation de nettoyage fiable et conforme aux normes les plus strictes de l’industrie.
Chacun des membres de l’équipe de nettoyage de Fours Pyrox détient des certifications reconnues dans le domaine du nettoyage industriel. Ces certifications attestent de leur expertise en matière de sécurité, de manipulation des équipements, et de connaissance approfondie des procédures de nettoyage spécifiques aux fours industriels. En restant constamment à jour avec les dernières avancées technologiques et les normes réglementaires, ces professionnels certifiés garantissent une exécution de tâches à la pointe de l’efficacité et de la sécurité.
La certification de l’équipe de nettoyage de Fours Pyrox s’étend au-delà des compétences techniques. Elle inclut également une compréhension approfondie des propriétés des matériaux, des réactions chimiques, et des spécificités opérationnelles propres à chaque type de four industriel. Ceci assure une approche adaptée et personnalisée à chaque intervention, répondant aux exigences uniques de chaque client.
Outre les certifications, Fours Pyrox investit dans la formation continue de son personnel. Cela garantit que les professionnels certifiés demeurent à la pointe des meilleures pratiques de l’industrie, intégrant les dernières innovations et technologies dans leurs méthodes de nettoyage. Cette volonté de rester à la pointe de l’expertise renforce la réputation de Fours Pyrox en tant que partenaire fiable pour les entreprises cherchant des services de nettoyage industriel de la plus haute qualité.
Choisir des professionnels certifiés en nettoyage industriel chez Fours Pyrox, c’est s’assurer que chaque étape du processus de nettoyage est gérée par des experts qualifiés, garantissant ainsi des résultats optimaux, une sécurité inégalée et une tranquillité d’esprit pour les clients industriels exigeants.
Élimination des résidus industriels :
L’élimination des résidus industriels est une composante fondamentale du savoir-faire de Fours Pyrox Nettoyage Industriel, visant à garantir un fonctionnement optimal des fours industriels. Face à l’accumulation inévitable de résidus variés au sein de ces équipements thermiques, Fours Pyrox excelle dans le développement et l’application de méthodes spécialisées pour une élimination efficace et sûre de ces matériaux indésirables.
Fours Pyrox adopte une approche systématique pour l’élimination des résidus industriels, débutant par une analyse détaillée de la composition des résidus spécifiques à chaque four. Cette évaluation précise permet d’adapter les méthodes de nettoyage en fonction des caractéristiques des résidus, assurant ainsi une élimination complète sans compromettre l’intégrité des équipements.
Les résidus industriels peuvent prendre diverses formes, notamment des dépôts carbonisés, des substances corrosives, ou des matières organiques. Fours Pyrox utilise des méthodes mécaniques, chimiques et thermiques spécifiques pour chaque type de résidu, garantissant ainsi une élimination efficace tout en minimisant les risques de dommages aux équipements.
L’équipe spécialisée dans l’élimination des résidus chez Fours Pyrox est formée pour gérer en toute sécurité ces matériaux potentiellement dangereux. Le processus d’élimination est conforme aux normes de sécurité industrielles les plus strictes, et les professionnels veillent à la gestion appropriée des déchets, contribuant ainsi à la durabilité environnementale.
Au-delà de l’aspect technique, Fours Pyrox reconnaît l’importance d’une élimination des résidus industriels efficace pour la performance à long terme des fours. En éliminant ces éléments perturbateurs, l’entreprise contribue à prévenir les obstructions, à maintenir l’efficacité énergétique, et à prolonger la durée de vie utile des équipements thermiques.
Choisir Fours Pyrox pour l’élimination des résidus industriels, c’est opter pour une approche spécialisée qui allie expertise technique, gestion sécurisée des matériaux, et engagement envers des pratiques respectueuses de l’environnement. La garantie d’une élimination efficace des résidus positionne Fours Pyrox en tant que partenaire privilégié pour les industries soucieuses de la performance optimale de leurs fours industriels.
Respect de l’environnement dans le nettoyage des fours :
Le respect de l’environnement occupe une place centrale dans l’approche de Fours Pyrox Nettoyage Industriel. L’entreprise reconnaît la nécessité impérieuse de concilier les impératifs industriels avec une responsabilité écologique accrue. Ainsi, chaque étape du processus de nettoyage des fours est soigneusement pensée pour minimiser l’impact sur l’environnement, tout en garantissant des résultats de nettoyage exceptionnels.
Fours Pyrox intègre des pratiques respectueuses de l’environnement dès la planification de chaque intervention. Cela inclut le choix judicieux des produits chimiques, privilégiant des formulations écologiques qui minimisent les risques de pollution et qui sont biodégradables. L’entreprise cherche constamment à adopter des alternatives plus durables pour assurer une empreinte écologique réduite.
Dans le cadre du nettoyage des fours, Fours Pyrox accorde une attention particulière à la gestion des déchets. Les résidus issus du processus de nettoyage sont collectés, triés et éliminés de manière responsable, conformément aux normes environnementales. L’entreprise explore également des opportunités de recyclage pour réduire la quantité de déchets envoyés vers les sites d’élimination.
L’équipe de Fours Pyrox sensibilise également ses clients aux avantages d’une approche respectueuse de l’environnement dans le nettoyage des fours. Cela inclut l’éducation sur les meilleures pratiques, l’utilisation responsable des équipements thermiques, et la promotion de l’efficacité énergétique. Cette sensibilisation vise à créer une communauté industrielle engagée dans la préservation de l’environnement.
L’engagement de Fours Pyrox envers le respect de l’environnement ne se limite pas à la conformité aux réglementations en vigueur, mais va au-delà pour intégrer des principes de durabilité dans toutes ses opérations. En choisissant Fours Pyrox pour le nettoyage des fours, les industries font le choix d’une solution qui allie performance opérationnelle et responsabilité environnementale, contribuant ainsi à un avenir durable.
Personnalisation des services de nettoyage :
La personnalisation des services de nettoyage est une caractéristique distinctive de l’approche de Fours Pyrox Nettoyage Industriel. Chaque four industriel est unique, avec ses propres spécificités en termes de matériaux, de résidus, et de conditions opérationnelles. Fours Pyrox reconnaît cette diversité et s’engage à fournir des services de nettoyage sur mesure, adaptés aux besoins spécifiques de chaque client.
Avant d’entamer le processus de nettoyage, Fours Pyrox initie une évaluation approfondie de chaque four industriel concerné. Cette analyse prend en compte la nature des résidus, les matériaux du four, les exigences de sécurité, et les objectifs spécifiques du client. Cette étape cruciale permet de concevoir un plan de nettoyage personnalisé, optimisé pour maximiser l’efficacité tout en préservant l’intégrité structurelle des équipements.
La personnalisation des services de nettoyage s’étend à la sélection des méthodes et des technologies utilisées. Fours Pyrox adapte son approche en fonction des caractéristiques uniques de chaque four, utilisant des techniques mécaniques, thermiques et chimiques spécifiques pour assurer une élimination optimale des contaminants. Cette flexibilité garantit des résultats de nettoyage exceptionnels, même dans les environnements industriels les plus exigeants.
L’équipe de Fours Pyrox comprend que les besoins de chaque client évoluent avec le temps. C’est pourquoi l’entreprise favorise une communication ouverte et continue avec ses clients. Cette approche collaborative permet d’ajuster les services de nettoyage en fonction des changements dans les processus industriels, des mises à niveau d’équipements, ou des nouvelles exigences réglementaires.
Opter pour la personnalisation des services de nettoyage de Fours Pyrox, c’est choisir une approche flexible et adaptative qui va au-delà d’une solution universelle. C’est la garantie d’un nettoyage qui répond précisément aux besoins spécifiques de chaque four industriel, assurant ainsi une performance optimale et une longévité accrue des équipements thermiques.
Optimisation des performances des fours :
L’optimisation des performances des fours est au cœur de la mission de Fours Pyrox Nettoyage Industriel. Comprendre que la propreté et l’efficacité des équipements thermiques sont intrinsèquement liées, l’entreprise se spécialise dans des interventions de nettoyage conçues pour maximiser la performance opérationnelle des fours industriels.
Fours Pyrox déploie des méthodes de nettoyage spécifiques qui vont au-delà de l’élimination des résidus visibles. L’entreprise cible les zones critiques où les dépôts peuvent entraîner une détérioration des performances, comme les conduits de chaleur, les échangeurs thermiques et les surfaces de transfert de chaleur. En optimisant ces composants, Fours Pyrox contribue à améliorer l’efficacité énergétique et à prévenir les problèmes potentiels liés à la surchauffe.
Une approche proactive de Fours Pyrox consiste également à éliminer les obstructions potentielles qui pourraient entraver la circulation de l’air ou des gaz, impactant ainsi la répartition uniforme de la chaleur. En garantissant un flux thermique optimal, l’entreprise s’efforce de minimiser les variations de température à l’intérieur des fours, assurant ainsi une production plus stable et une qualité de produit constante.
Fours Pyrox ne se limite pas au nettoyage en tant que telle, mais propose également des recommandations pour la maintenance préventive. Cela inclut des calendriers d’inspection régulière, des analyses de performances périodiques et des conseils sur les mises à niveau potentielles. Ces initiatives visent à prévenir les défaillances futures, à prolonger la durée de vie utile des équipements et à garantir un rendement optimal à long terme.
En somme, choisir Fours Pyrox pour l’optimisation des performances des fours, c’est investir dans une approche holistique du nettoyage industriel. C’est une démarche qui vise à maximiser l’efficacité opérationnelle, à réduire les coûts énergétiques et à assurer une production fiable, positionnant ainsi les clients de Fours Pyrox à la pointe de l’efficacité industrielle.
Durabilité dans les opérations de nettoyage thermique :
La durabilité dans les opérations de nettoyage thermique représente un principe fondamental de l’approche de Fours Pyrox Nettoyage Industriel. La société reconnaît que l’efficacité opérationnelle ne doit pas compromettre la durabilité environnementale. Ainsi, chaque étape du processus de nettoyage thermique est soigneusement planifiée pour minimiser l’impact écologique tout en fournissant des résultats exceptionnels.
Fours Pyrox s’engage à utiliser des méthodes de nettoyage thermique respectueuses de l’environnement. Cela inclut le recours à des technologies économes en énergie et l’utilisation de produits chimiques respectueux de l’environnement. L’entreprise privilégie également les méthodes qui nécessitent moins de ressources et qui génèrent moins de déchets, contribuant ainsi à la réduction de l’empreinte carbone.
Dans le choix des produits chimiques, Fours Pyrox opte pour des formulations biodégradables et sans danger pour l’environnement. L’entreprise favorise des alternatives respectueuses de la santé humaine et de la biodiversité, tout en maintenant une efficacité maximale dans l’élimination des résidus thermiques. Ces choix judicieux témoignent de l’engagement de Fours Pyrox envers une approche durable du nettoyage thermique.
Fours Pyrox intègre également des pratiques durables dans la gestion des déchets. Les résidus résultant du nettoyage thermique sont collectés, triés et éliminés conformément aux normes environnementales les plus strictes. L’entreprise explore également des opportunités de recyclage, contribuant ainsi à la réduction de la production de déchets et à la préservation des ressources naturelles.
Au-delà des aspects techniques, Fours Pyrox cherche à sensibiliser ses clients à l’importance de la durabilité dans les opérations de nettoyage thermique. L’entreprise encourage les pratiques responsables en matière d’utilisation des fours industriels, favorisant une consommation énergétique efficiente et une gestion responsable des équipements thermiques.
Choisir Fours Pyrox pour les opérations de nettoyage thermique, c’est opter pour une approche qui allie efficacité et responsabilité environnementale. C’est un engagement en faveur d’une durabilité à long terme, contribuant ainsi à créer un équilibre harmonieux entre les impératifs industriels et la préservation de notre environnement.
La peinture en poudre est une méthode de revêtement de surface qui utilise de la poudre sèche au lieu de peinture liquide. Ce procédé est devenu très populaire dans l’industrie en raison de ses nombreux avantages par rapport aux méthodes de peinture traditionnelles. L’équipement de poudrage joue un rôle crucial dans l’application de ce type de revêtement.
Avantages du Revêtement en Poudre
- Durabilité et résistance : Le revêtement en poudre offre une finition robuste et durable qui résiste aux égratignures, à l’usure et aux conditions climatiques difficiles.
- Écologique : Contrairement aux peintures liquides, le revêtement en poudre ne contient pas de solvants ni de composés organiques volatils (COV), ce qui en fait une option respectueuse de l’environnement.
- Coût-Efficacité : Bien que l’investissement initial dans l’équipement puisse être élevé, les économies réalisées sur le long terme grâce à la réduction des déchets et à l’efficacité du processus compensent largement ce coût.
Applications Industrielles
Le revêtement en poudre est largement utilisé dans diverses industries, notamment l’automobile, l’électronique, les appareils électroménagers, et les équipements extérieurs. Ce procédé assure non seulement une finition esthétique, mais aussi une protection contre la corrosion et d’autres formes de dégradation.
Fours de polymérisation
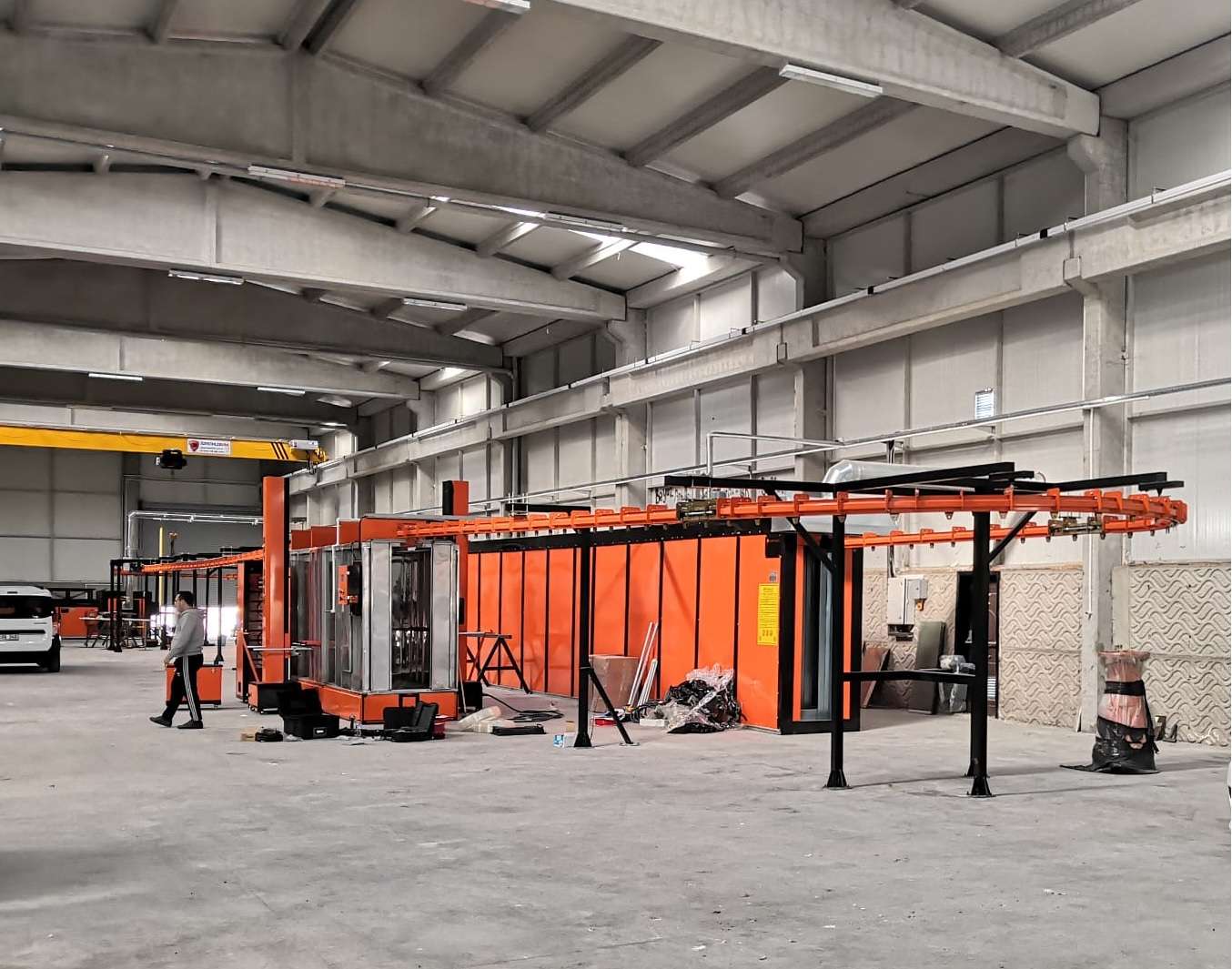
Les fours de polymérisation jouent un rôle essentiel dans le processus de revêtement en poudre, car ils permettent de chauffer la poudre appliquée pour qu’elle fonde et forme un film homogène et dur sur la surface de l’objet. Il existe plusieurs types de fours utilisés en fonction des besoins spécifiques de l’application.
Types de Fours
- Fours à convection : Ils utilisent l’air chaud pour transférer la chaleur à la pièce. Ces fours sont idéaux pour des charges lourdes et volumineuses.
- Fours infrarouges : Ils utilisent le rayonnement infrarouge pour chauffer directement la poudre, offrant un temps de polymérisation plus rapide.
- Fours à induction : Utilisés pour des applications spécifiques nécessitant un chauffage rapide et précis.
Caractéristiques Clés
Lors de la sélection d’un four de polymérisation, plusieurs caractéristiques doivent être prises en compte :
- Capacité de température : Doit correspondre aux exigences du type de poudre utilisée.
- Uniformité de la chaleur : Assure une répartition uniforme de la chaleur pour une finition uniforme.
- Efficacité énergétique : Les modèles économes en énergie permettent de réduire les coûts opérationnels.
Cabines de poudrage
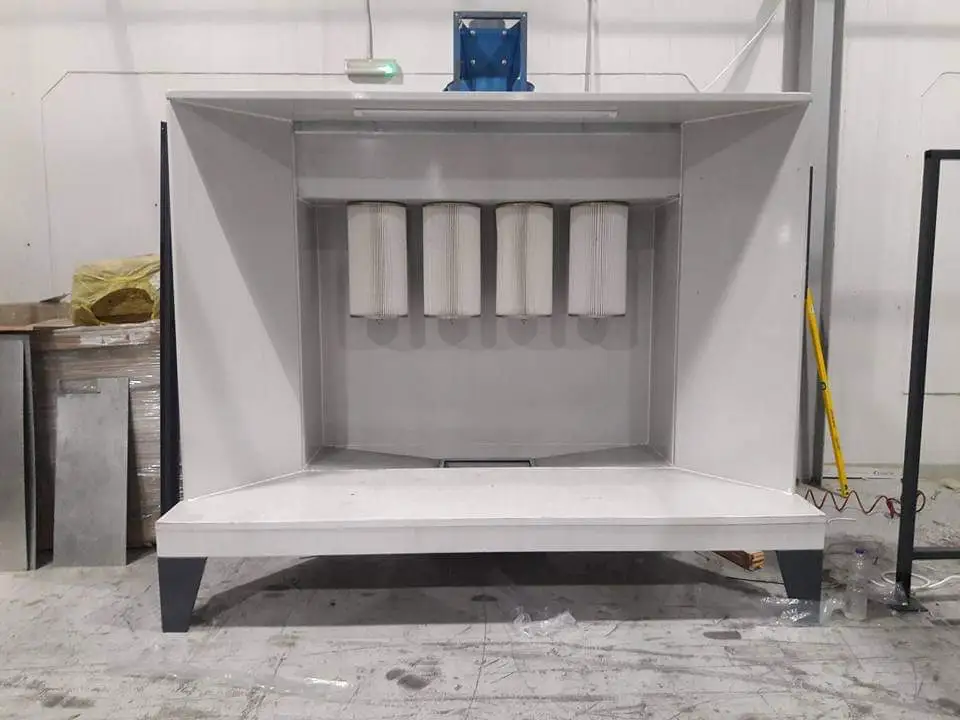
Les cabines de poudrage sont des environnements contrôlés où la poudre est appliquée sur les pièces. Elles sont conçues pour assurer une application efficace et sûre, tout en minimisant la contamination.
Conception et Structure
- Cabines ouvertes : Idéales pour les petites pièces et une production à petite échelle.
- Cabines fermées : Conviennent aux grandes pièces et à la production en série.
- Systèmes de récupération de poudre : Intégrés pour récupérer et réutiliser l’excès de poudre.
Importance de la Ventilation et de la Sécurité
Une ventilation adéquate est cruciale pour éviter l’accumulation de particules de poudre, réduisant ainsi les risques d’incendie et d’explosion. De plus, les cabines doivent être équipées de systèmes de filtration pour protéger les travailleurs contre l’inhalation de poudre.
Pistolets de pulvérisation
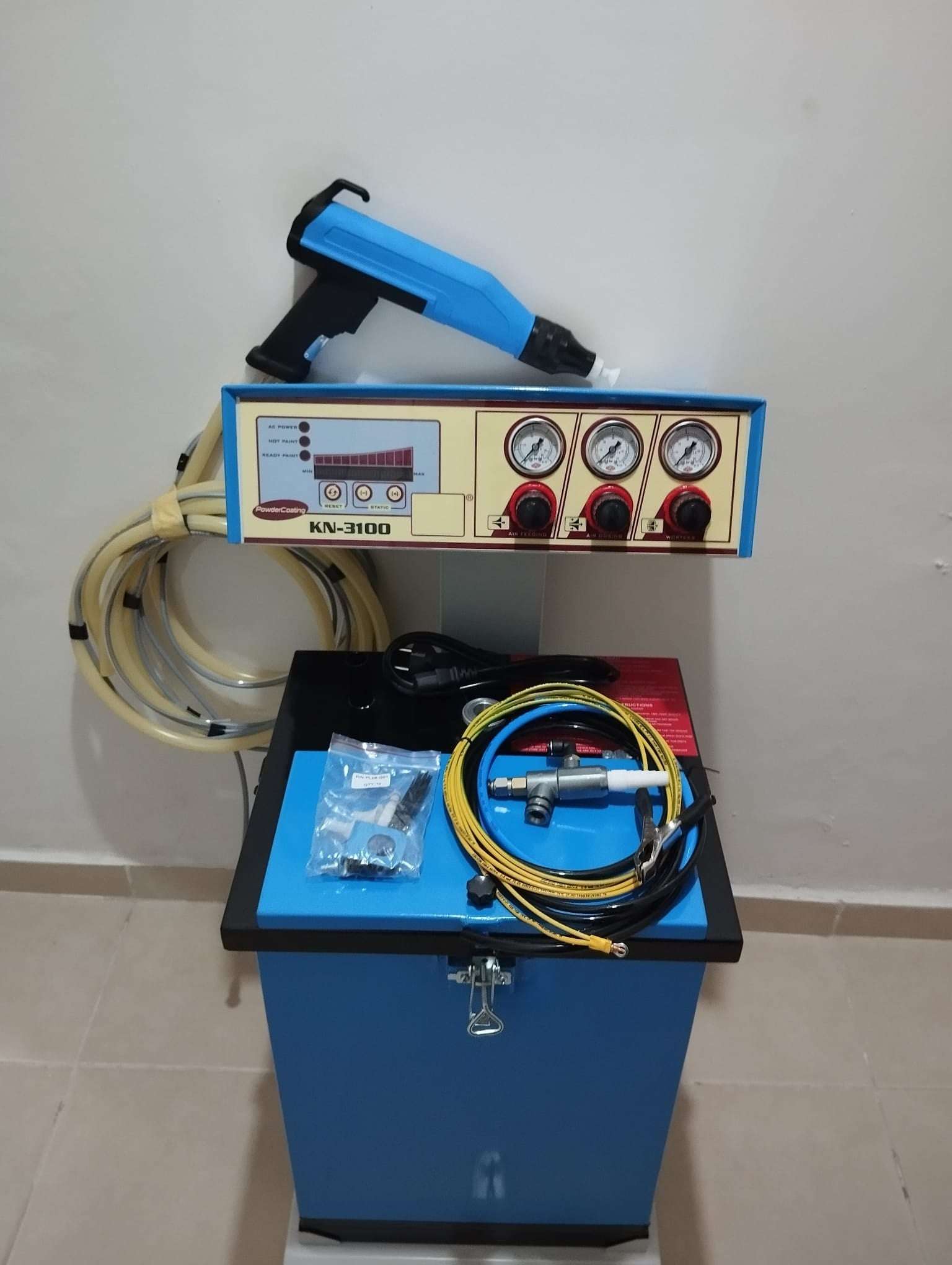
Les pistolets de pulvérisation de poudre sont des dispositifs utilisés pour appliquer la poudre sur la surface de l’objet. Ils utilisent un champ électrostatique pour attirer la poudre vers la pièce, assurant une couverture uniforme.
Types de Pistolets de Pulvérisation
- Pistolets à corona : Utilisent une charge électrique pour ioniser la poudre.
- Pistolets tribo : La poudre est chargée par friction, idéale pour les surfaces complexes.
Fonctionnement et Avantages
Les pistolets de pulvérisation sont appréciés pour leur capacité à appliquer la poudre de manière uniforme et efficace. Leur utilisation réduit le gaspillage de poudre et offre une finition de haute qualité.
Maintien de l’équipement de poudrage
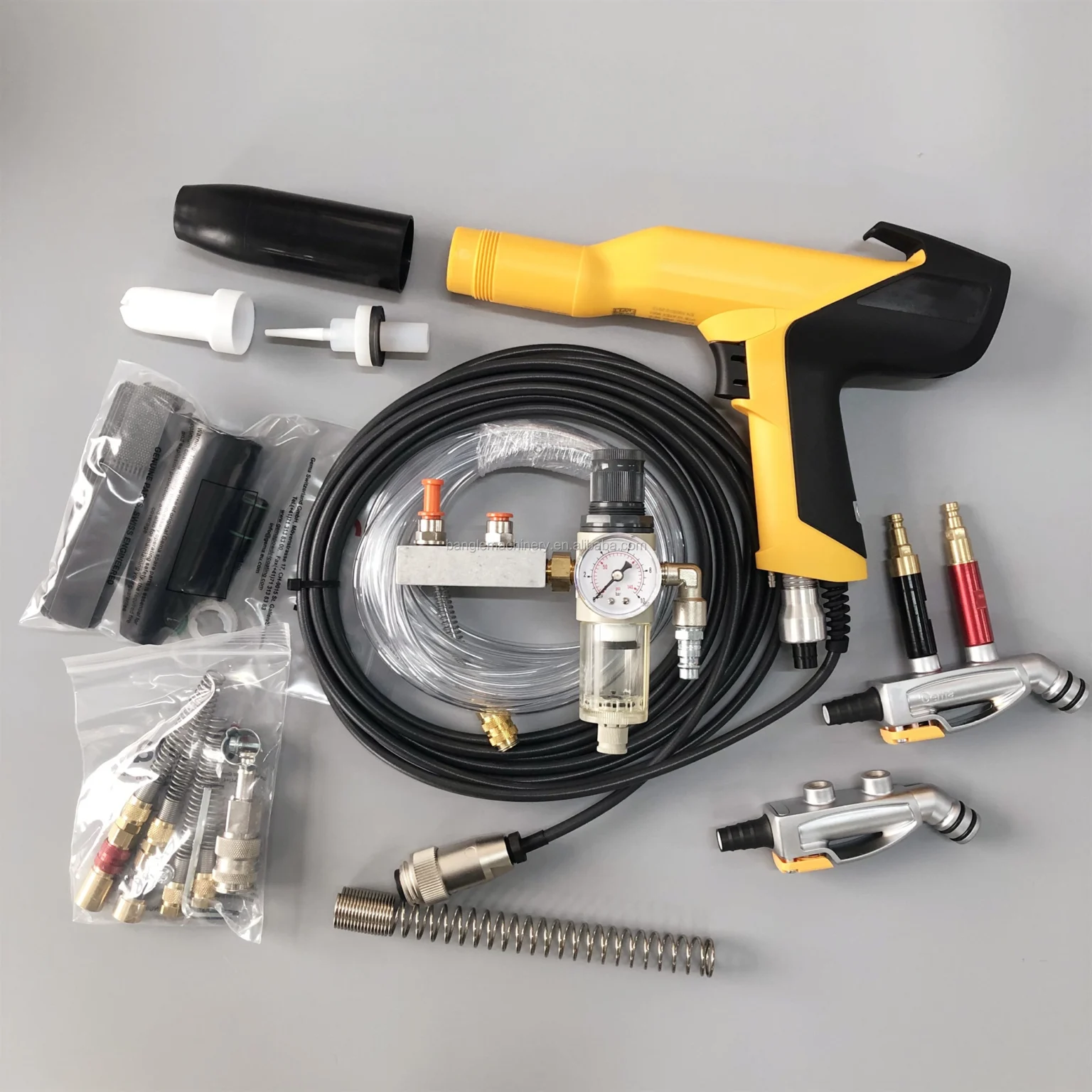
Le maintien de l’équipement de poudrage en bon état de fonctionnement est essentiel pour garantir une production continue et de haute qualité. Avoir des pièces de rechange à portée de main est crucial pour minimiser les temps d’arrêt.
Importance des Pièces de Rechange
Les pièces de rechange assurent la continuité des opérations en cas de défaillance de l’équipement. Cela inclut les filtres, les buses de pistolet, et les éléments chauffants.
Conseils d’Entretien
- Inspection régulière : Vérifiez les pièces pour détecter tout signe d’usure ou de dommage.
- Nettoyage : Maintenez les cabines et les pistolets propres pour éviter la contamination croisée.
- Formation du personnel : Assurez-vous que les opérateurs sont formés pour identifier et résoudre les problèmes potentiels.
Conseils d’entretien d’équipement
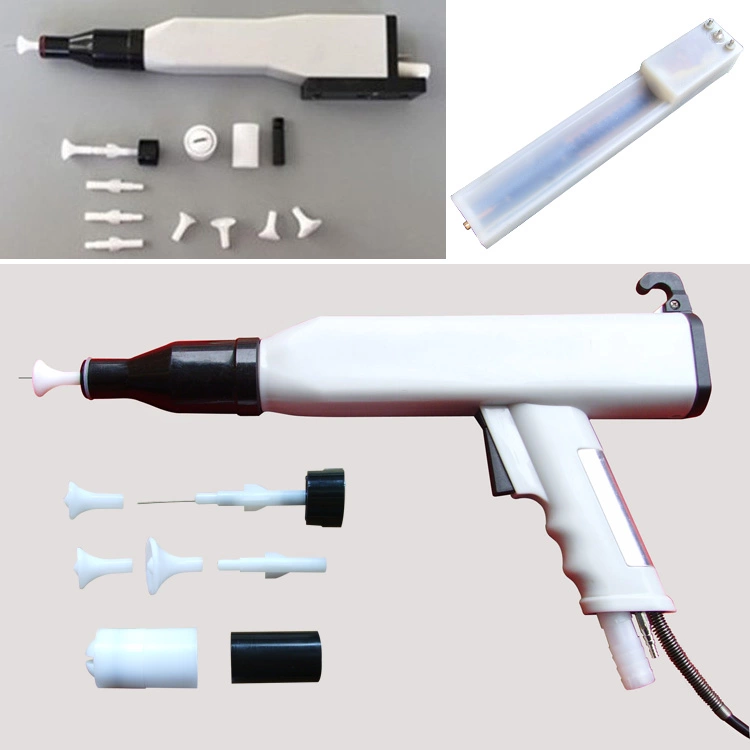
- Inspection Régulière
- Vérification Visuelle : Inspectez visuellement l’équipement régulièrement pour détecter des signes d’usure, de corrosion ou de dommages physiques. Cela inclut les câbles, les connexions électriques, et les composants mécaniques.
- Suivi des Composants : Tenez un registre des inspections régulières pour chaque pièce de l’équipement, ce qui vous permettra de détecter les tendances d’usure et de planifier les remplacements nécessaires.
- Nettoyage des Équipements
- Nettoyage des Pistolets de Pulvérisation : Démontage et nettoyage régulier des pistolets de pulvérisation pour éviter l’accumulation de poudre, qui peut obstruer les buses et affecter la qualité de l’application. Utilisez de l’air comprimé et des solvants recommandés pour le nettoyage.
- Entretien des Cabines de Poudrage : Nettoyez régulièrement l’intérieur des cabines pour éviter la contamination croisée des couleurs. Les systèmes de récupération de poudre doivent être vidés et nettoyés selon les instructions du fabricant.
- Filtres et Ventilation : Remplacez les filtres des systèmes de ventilation selon les recommandations du fabricant pour assurer une ventilation optimale et éviter l’accumulation de particules de poudre.
- Maintenance Préventive
- Lubrification des Composants Mécaniques : Appliquez régulièrement de la lubrification aux pièces mécaniques mobiles pour réduire l’usure et éviter les blocages.
- Calibration des Systèmes Électrostatiques : Assurez-vous que les systèmes de charge électrostatique sont correctement calibrés pour une application uniforme de la poudre. Vérifiez les connexions électriques et remplacez les pièces usées.
- Vérification des Températures de Four : Contrôlez régulièrement les températures des fours de polymérisation pour garantir qu’elles restent dans les limites recommandées pour la poudre utilisée. Des températures incorrectes peuvent entraîner des finitions de mauvaise qualité.
- Formation du Personnel
- Formation Continue : Assurez-vous que le personnel est correctement formé pour utiliser et entretenir l’équipement. Organisez des sessions de formation régulières pour actualiser les connaissances sur les nouvelles technologies et méthodes d’entretien.
- Sécurité au Travail : Éduquez le personnel sur les protocoles de sécurité, y compris l’utilisation d’équipements de protection individuelle (EPI) pour éviter les accidents et l’exposition aux particules de poudre.
- Gestion des Pièces de Rechange
- Inventaire des Pièces de Rechange : Maintenez un stock adéquat de pièces de rechange essentielles comme les buses de pulvérisation, les filtres, et les éléments chauffants pour réduire les temps d’arrêt en cas de panne.
- Commande de Pièces : Prévoyez à l’avance les commandes de pièces de rechange pour éviter les ruptures de stock qui pourraient perturber la production.
- Analyse des Performances
- Suivi des Indicateurs Clés : Surveillez les indicateurs de performance tels que l’efficacité énergétique, la qualité de la finition, et le taux de défauts pour identifier les domaines nécessitant des améliorations.
- Retour d’Expérience : Sollicitez des retours d’expérience du personnel opérant l’équipement pour identifier les problèmes récurrents et ajuster les procédures d’entretien en conséquence.
Conclusion
L’entretien adéquat des équipements de poudrage est essentiel pour garantir une production efficace, sûre et de haute qualité. En mettant en œuvre un programme de maintenance préventive et en formant le personnel aux meilleures pratiques, vous pouvez prolonger la durée de vie de vos équipements et optimiser vos opérations de revêtement en poudre. Assurez-vous de suivre les recommandations du fabricant pour chaque composant de l’équipement afin d’assurer leur bon fonctionnement.
N’hésitez pas à me dire si vous avez besoin de plus de détails sur un aspect particulier de l’entretien ou si vous souhaitez que d’autres sujets soient abordés.
Quelles pièces de rechange
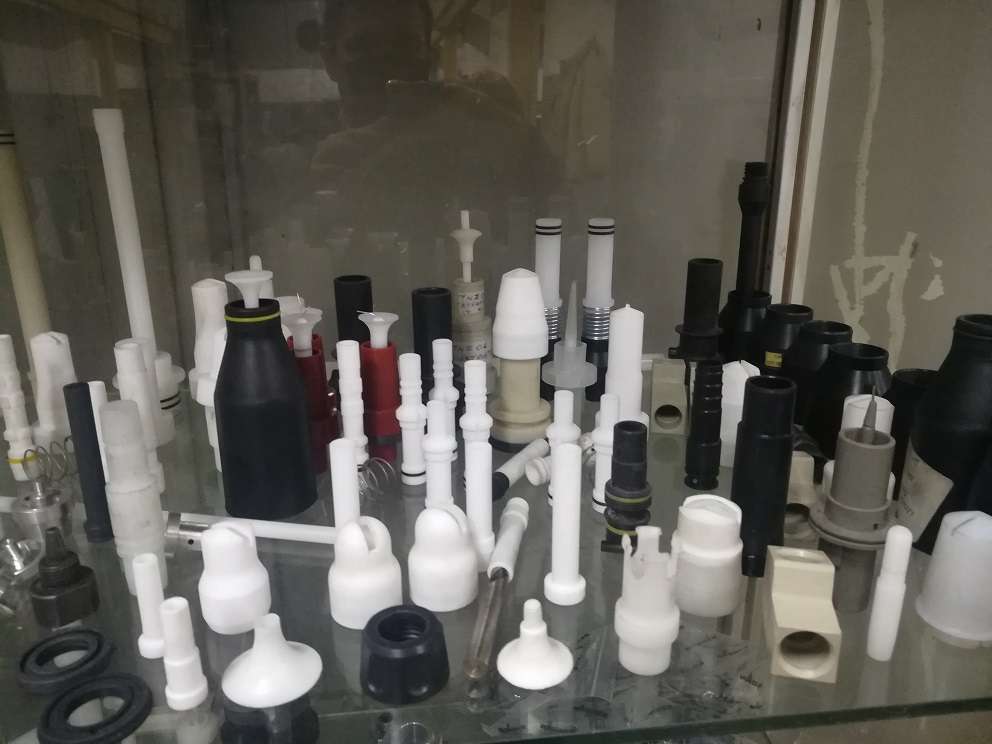
La maintenance efficace de l’équipement de poudrage implique la gestion proactive des pièces de rechange. Avoir les bonnes pièces à portée de main peut réduire considérablement les temps d’arrêt et maintenir la qualité de production. Voici une liste des pièces de rechange essentielles pour les équipements de poudrage :
Pièces de Rechange Essentielles pour l’Équipement de Poudrage
- Buses de Pistolet de Pulvérisation
- Types de Buses : Disponibles en différentes tailles et formes (rondes, plates, coniques) pour s’adapter aux divers types d’application et de finitions souhaitées.
- Usure : Les buses s’usent avec le temps en raison de l’abrasion de la poudre. Avoir des buses de rechange garantit que la qualité de la pulvérisation reste constante.
- Électrodes de Pistolet
- Fonction : Les électrodes chargent électrostatiquement la poudre pour l’application. Elles peuvent s’user ou s’endommager, ce qui affecte l’efficacité de l’application.
- Remplacement : Des électrodes de rechange sont cruciales pour maintenir une charge électrostatique efficace et une application uniforme.
- Filtres de Cabine
- Fonction des Filtres : Captent les particules de poudre en excès, évitant la contamination de l’air et l’accumulation de poudre à l’intérieur de la cabine.
- Types de Filtres : Incluent les filtres à cartouche et les filtres à sac, chacun ayant des besoins de remplacement réguliers pour garantir un environnement de travail propre et sûr.
- Pompes à Poudre
- Rôle des Pompes : Transportent la poudre du réservoir à l’applicateur. Les pompes peuvent s’user avec le temps et nécessitent des pièces de rechange comme des joints, des tuyaux, et des joints toriques.
- Maintenance : Un entretien régulier et la disponibilité de pièces de rechange sont essentiels pour éviter les interruptions de flux de poudre.
- Éléments Chauffants des Fours de Polymérisation
- Importance : Maintiennent la température nécessaire pour durcir la poudre. Les éléments chauffants peuvent s’user, nécessitant des remplacements pour maintenir la température uniforme dans le four.
- Types : Incluent les éléments chauffants électriques et les brûleurs à gaz.
- Joints et Joints Toriques
- Fonction : Assurent l’étanchéité des systèmes pneumatiques et hydrauliques. Les joints et les joints toriques peuvent se détériorer avec le temps, provoquant des fuites et des pertes d’efficacité.
- Disponibilité : Garder un stock de différents types et tailles de joints et de joints toriques est essentiel pour éviter les temps d’arrêt imprévus.
- Composants Électroniques
- Panneaux de Contrôle : Les cartes de circuits imprimés, les écrans de contrôle, et les capteurs peuvent nécessiter des remplacements en cas de panne.
- Capteurs et Commutateurs : Surveillent et contrôlent divers aspects de l’équipement. Les pièces de rechange aident à maintenir la précision et le contrôle des opérations.
- Pièces de Rechange pour Systèmes de Transport
- Chaînes et Rouleaux : Pour les systèmes de convoyage qui transportent les pièces à travers les différentes étapes du processus de revêtement.
- Moteurs et Réducteurs : Nécessitent des remplacements pour éviter les pannes des systèmes de transport.
- Agitateurs et Mélangeurs de Poudre
- Fonction : Maintiennent la poudre en mouvement pour éviter la sédimentation et assurer une distribution homogène. Les pièces mobiles, comme les pales d’agitation, peuvent s’user avec le temps.
Importance de la Gestion des Pièces de Rechange
Planification Proactive : Anticiper les besoins en pièces de rechange et maintenir un stock adéquat peut éviter des interruptions coûteuses de la production. Établir un calendrier de maintenance préventive permet de prédire les besoins en remplacements.
Fournisseurs de Confiance : Travailler avec des fournisseurs de pièces de rechange fiables garantit l’accès à des composants de haute qualité qui prolongent la durée de vie de l’équipement.
Consignation des Pièces : Mettre en place un système de consignation de pièces pour suivre l’utilisation des pièces de rechange et les réapprovisionner automatiquement.
Conclusion
La disponibilité de pièces de rechange essentielles et un programme de maintenance bien structuré sont cruciaux pour le bon fonctionnement des équipements de poudrage. La gestion proactive des pièces de rechange assure non seulement une production fluide mais aussi une qualité de revêtement constante. En ayant une stratégie d’entretien et de gestion des pièces bien définie, les entreprises peuvent réduire les temps d’arrêt et maximiser l’efficacité de leurs opérations de revêtement en poudre.
Si vous avez besoin de détails supplémentaires ou d’informations spécifiques sur l’un des composants ou des procédures, n’hésitez pas à me le faire savoir !
Pièces pour pistolets
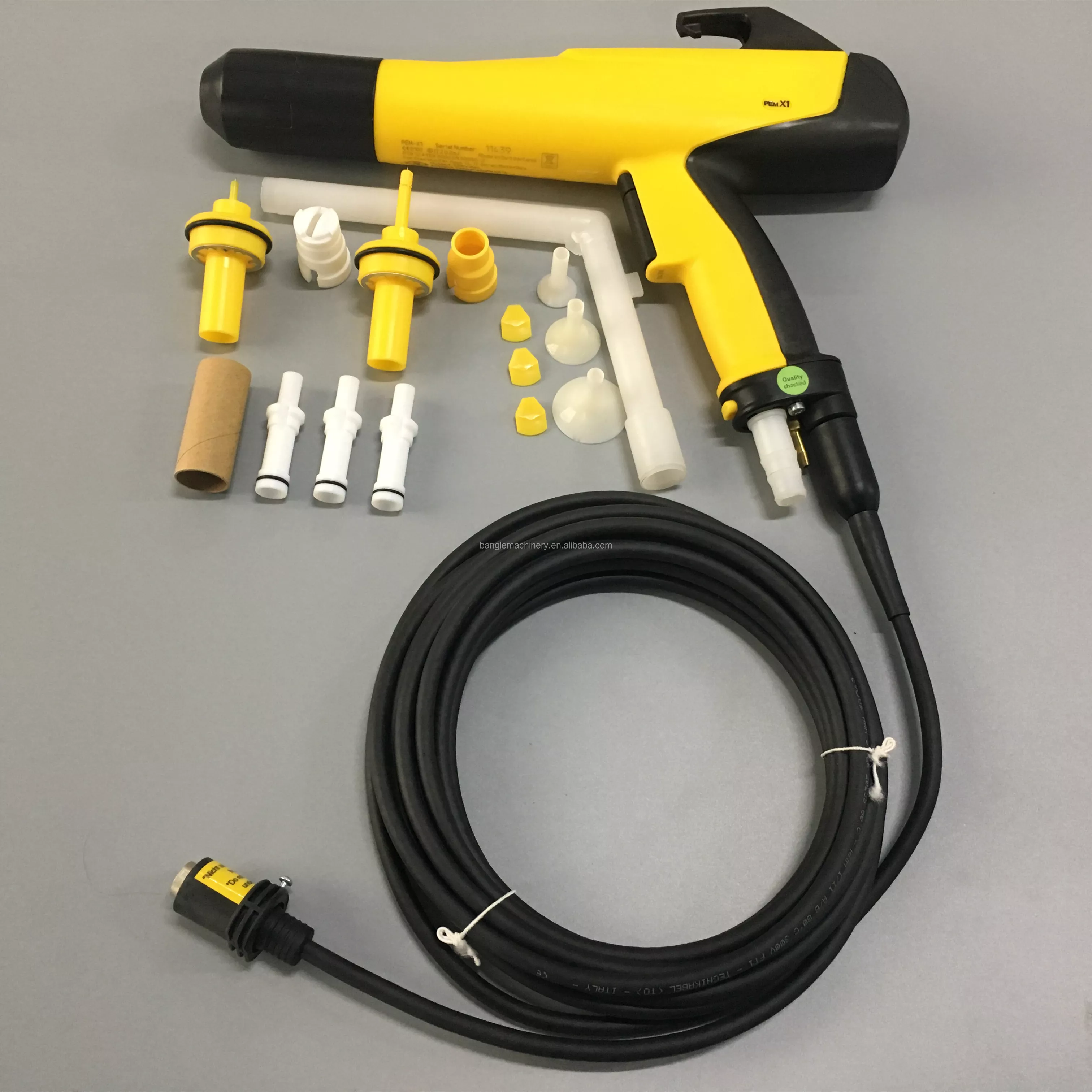
Lorsqu’il s’agit de l’entretien et de la maintenance des pistolets de pulvérisation pour le revêtement en poudre, il est essentiel de disposer d’un stock adéquat de pièces de rechange spécifiques pour éviter des interruptions de production et maintenir une application uniforme et de haute qualité. Voici une liste des principales pièces de rechange pour les pistolets de pulvérisation de poudre, avec une description de leur fonction et des raisons pour lesquelles elles sont importantes :
Pièces de Rechange Essentielles pour Pistolets de Pulvérisation
- Buses de Pulvérisation
- Fonction : Les buses contrôlent la taille et la forme du motif de pulvérisation de poudre, influençant directement la couverture et l’uniformité de l’application.
- Types : Disponibles en différentes formes et tailles, telles que rondes ou plates, pour diverses applications et finitions.
- Remplacement : Les buses s’usent avec le temps en raison de l’abrasion de la poudre, ce qui peut altérer le motif de pulvérisation. Un stock de buses de rechange garantit une qualité constante.
- Électrodes
- Fonction : Chargent électrostatiquement la poudre pour assurer une adhésion uniforme à la surface de l’objet à revêtir.
- Usure : Les électrodes peuvent se corroder ou s’user, ce qui réduit leur efficacité de charge et peut entraîner une mauvaise adhésion de la poudre.
- Remplacement Régulier : Disposer d’électrodes de rechange assure que le pistolet maintient une charge électrostatique optimale.
- Chambres de Charge
- Rôle : La chambre de charge est où la poudre est ionisée avant d’être pulvérisée. Elle joue un rôle clé dans le processus de charge électrostatique.
- Usure : L’accumulation de poudre peut affecter l’efficacité de la charge, nécessitant un nettoyage régulier et, parfois, le remplacement de la chambre.
- Joints et Joints Toriques
- Fonction : Assurent l’étanchéité des systèmes pneumatiques et empêchent les fuites d’air qui pourraient affecter la performance du pistolet.
- Importance : Les joints et joints toriques peuvent se détériorer avec le temps, provoquant des pertes de pression et une application inégale.
- Maintenance : Vérifiez régulièrement l’état des joints et remplacez-les pour éviter les dysfonctionnements.
- Housses de Pistolet et Capots
- Rôle : Protègent les composants internes du pistolet contre la poudre et la poussière.
- Remplacement : Les capots peuvent être endommagés ou usés avec le temps, nécessitant un remplacement pour maintenir le pistolet propre et fonctionnel.
- Flexibles de Poudre
- Fonction : Transportent la poudre du réservoir au pistolet de pulvérisation.
- Usure : Les flexibles peuvent se boucher ou s’user, affectant le flux de poudre.
- Entretien : Des flexibles de rechange sont essentiels pour garantir un flux continu et éviter les interruptions.
- Cartouches de Filtration
- Utilisation : Les cartouches filtrantes intégrées dans certains systèmes de pistolet purifient l’air comprimé utilisé pour la pulvérisation.
- Maintenance : Un remplacement régulier est nécessaire pour assurer la propreté de l’air comprimé et éviter la contamination de la poudre.
- Connecteurs et Raccords
- Rôle : Connectent les différentes parties du système de pulvérisation, y compris les flexibles et les réservoirs.
- Vérification : Les connecteurs et raccords doivent être contrôlés régulièrement pour s’assurer qu’ils ne sont pas desserrés ou usés, ce qui pourrait entraîner des fuites.
- Pompes et Régulateurs d’Air
- Fonction : Régulent la pression de l’air pour une pulvérisation efficace et contrôlée.
- Usure : Les pompes et régulateurs peuvent se détériorer, nécessitant des pièces de rechange pour maintenir la pression correcte.
- Disponibilité : Avoir des pompes et régulateurs de rechange est crucial pour éviter des variations de pression qui affectent la qualité de l’application.
- Unités de Contrôle
- Rôle : Les panneaux de contrôle électroniques et les unités de commande régulent le fonctionnement du pistolet, y compris le débit de poudre et la charge électrostatique.
- Maintenance : Des problèmes électriques peuvent survenir, nécessitant des pièces de rechange pour garantir un fonctionnement sans interruption.
Importance de la Gestion des Pièces de Rechange
- Réduction des Temps d’Arrêt : Avoir un stock de pièces de rechange critique permet de minimiser les interruptions de production en cas de panne ou de défaillance.
- Qualité de Production : L’utilisation de pièces usées ou endommagées peut affecter la qualité de la pulvérisation, entraînant des défauts dans le revêtement. Les pièces de rechange assurent que la qualité reste constante.
- Économies de Coût à Long Terme : En entretenant régulièrement les pistolets avec des pièces de rechange, vous réduisez les risques de dommages plus graves qui pourraient nécessiter des réparations coûteuses ou le remplacement complet de l’équipement.
- Amélioration de la Sécurité : Assurer le bon fonctionnement des composants critiques contribue à la sécurité globale de l’environnement de travail, en réduisant le risque de fuites, de surchauffe, ou d’autres dangers.
Conclusion
La disponibilité et la gestion proactive des pièces de rechange pour les pistolets de pulvérisation sont essentielles pour maintenir une production efficace et de haute qualité dans les opérations de revêtement en poudre. En investissant dans un programme de maintenance préventive et en gardant un stock adéquat de pièces critiques, vous pouvez prolonger la durée de vie de votre équipement et optimiser vos processus de production.
Si vous avez besoin de plus d’informations sur l’une de ces pièces ou d’une autre assistance, n’hésitez pas à me le faire savoir !
Fours à thermolaquage
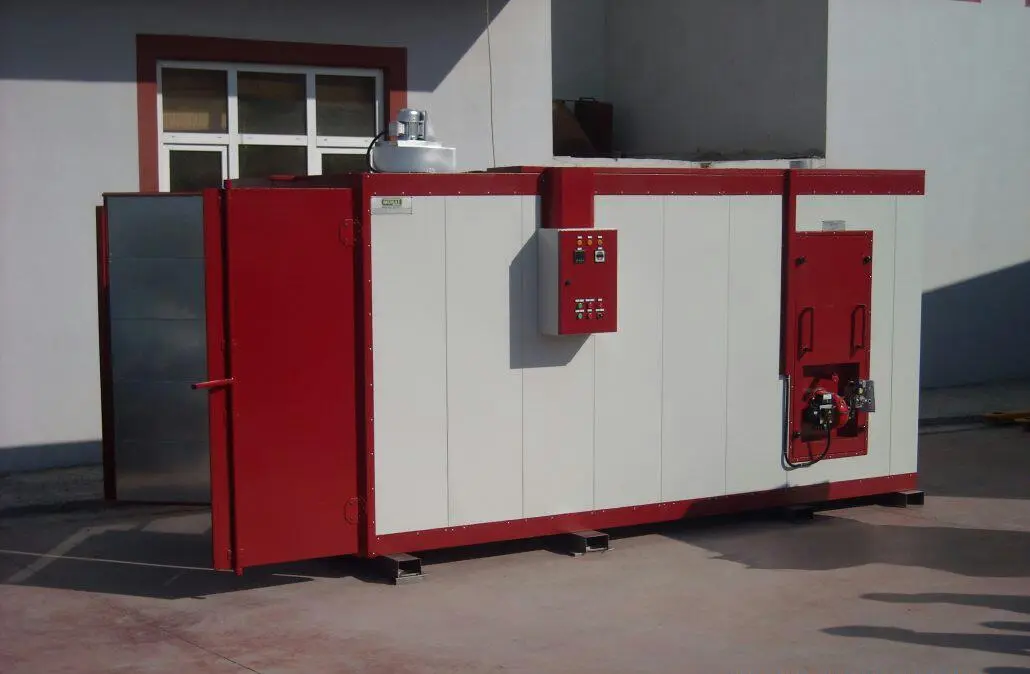
Les fours à thermolaquage, également appelés fours de polymérisation, jouent un rôle essentiel dans le processus de revêtement en poudre, en assurant une finition de qualité et durable. Ce procédé implique l’application de poudre thermodurcissable sur une surface qui est ensuite chauffée dans un four pour faire fondre et durcir la poudre, créant ainsi une couche uniforme et résistante. Voici un aperçu détaillé des fours à thermolaquage, de leur fonctionnement, des types disponibles, et des critères à considérer lors de leur sélection :
Fonctionnement des Fours à Thermolaquage
- Étapes du Processus de Thermolaquage
- Application de la Poudre : La poudre est appliquée sur la surface de l’objet à l’aide d’un pistolet de pulvérisation électrostatique. La charge électrostatique attire la poudre sur la surface, assurant une couverture uniforme.
- Polymérisation dans le Four : L’objet revêtu est ensuite placé dans un four à thermolaquage, où il est chauffé à une température spécifique pour fondre la poudre et la faire durcir.
- Durcissement : La chaleur permet aux particules de poudre de fusionner et de former une couche lisse et continue. Le processus de polymérisation dépend du type de poudre utilisée et des spécifications du fabricant.
- Caractéristiques des Fours à Thermolaquage
- Température : La plupart des poudres nécessitent des températures comprises entre 160°C et 230°C pour une polymérisation efficace.
- Durée : Le temps de polymérisation peut varier de 10 à 30 minutes, selon la taille de l’objet et le type de poudre.
- Uniformité de la Chaleur : Une distribution uniforme de la chaleur est cruciale pour éviter les défauts de surface, tels que des bulles ou des irrégularités.
Types de Fours à Thermolaquage
- Fours à Convection
- Principe : Utilisent l’air chaud pour chauffer les objets. Les ventilateurs répartissent la chaleur uniformément à l’intérieur du four.
- Avantages : Idéaux pour les objets volumineux et les lignes de production à grande échelle. Offrent une uniformité de chaleur efficace.
- Inconvénients : Peuvent être moins efficaces en termes de consommation d’énergie par rapport aux autres types de fours.
- Fours Infrarouges
- Principe : Utilisent des rayons infrarouges pour chauffer directement la surface de l’objet.
- Avantages : Réchauffement rapide, ce qui réduit le temps de polymérisation. Idéal pour les objets de formes complexes.
- Inconvénients : Moins efficace pour les objets très épais ou ceux avec des masses thermiques importantes.
- Fours à Induction
- Principe : Utilisent des champs électromagnétiques pour chauffer directement les objets métalliques.
- Avantages : Chauffage rapide et précis, idéal pour des applications spécifiques nécessitant un contrôle thermique précis.
- Inconvénients : Généralement plus coûteux et limités aux matériaux conducteurs.
- Fours Hybrides
- Principe : Combinent des technologies de chauffage à convection et infrarouge pour maximiser l’efficacité.
- Avantages : Permettent une flexibilité dans le traitement de différents types de pièces avec une consommation d’énergie optimisée.
- Inconvénients : Coût initial plus élevé dû à la complexité de la technologie intégrée.
Critères de Sélection d’un Four à Thermolaquage
- Capacité et Taille
- Dimensions du Four : Doivent correspondre à la taille des objets à traiter. Des fours plus grands sont nécessaires pour des pièces volumineuses ou des productions en série.
- Capacité de Charge : Évaluer la capacité de charge en termes de poids et de volume pour assurer que le four peut accueillir vos produits sans compromettre l’efficacité.
- Consommation Énergétique
- Efficacité Énergétique : Optez pour des modèles qui offrent une faible consommation d’énergie pour réduire les coûts d’exploitation.
- Isolation Thermique : Une bonne isolation aide à conserver la chaleur à l’intérieur du four, améliorant ainsi l’efficacité énergétique.
- Contrôle de Température
- Précision : La capacité à contrôler et maintenir précisément la température est essentielle pour la qualité de la finition.
- Systèmes de Contrôle Avancés : Recherchez des fours équipés de systèmes de contrôle numériques permettant un réglage précis et facile.
- Uniformité de la Chaleur
- Ventilation et Circulation d’Air : Assurez-vous que le four dispose de systèmes efficaces de circulation d’air pour garantir une distribution uniforme de la chaleur.
- Tests de Performance : Vérifiez les spécifications des tests de performance du fabricant pour l’uniformité thermique.
- Sécurité et Conformité
- Normes de Sécurité : Le four doit être conforme aux normes de sécurité locales et internationales, incluant des dispositifs de protection contre la surchauffe et des systèmes de verrouillage de sécurité.
- Émissions : Assurez-vous que le four respecte les réglementations concernant les émissions pour éviter les problèmes environnementaux.
Avantages des Fours à Thermolaquage
- Durabilité : Les finitions obtenues par thermolaquage sont extrêmement durables et résistantes aux éraflures, à la corrosion, et aux produits chimiques.
- Écologique : Ce procédé ne nécessite pas de solvants, ce qui réduit l’émission de composés organiques volatils (COV).
- Flexibilité de Design : Offre une large gamme de couleurs et de textures, ce qui permet une grande flexibilité en termes de design et de personnalisation.
Conclusion
Les fours à thermolaquage sont un élément crucial dans le processus de revêtement en poudre, assurant que la finition appliquée est à la fois esthétique et fonctionnelle. Le choix du bon type de four, combiné à une maintenance appropriée et à un contrôle rigoureux des paramètres de fonctionnement, peut considérablement améliorer la qualité de la production et réduire les coûts opérationnels.
Si vous avez besoin de plus de détails sur un aspect spécifique des fours à thermolaquage ou si vous souhaitez explorer d’autres éléments, n’hésitez pas à me le faire savoir !
Comparaison des Types de Fours à Thermolaquage
Lorsqu’il s’agit de choisir un four à thermolaquage pour le revêtement en poudre, il est crucial de comprendre les différences entre les différents types de fours disponibles. Chaque type de four a ses propres avantages et inconvénients, qui peuvent influencer la qualité de la finition, l’efficacité énergétique, le coût d’exploitation, et la flexibilité d’application. Voici une comparaison détaillée des principaux types de fours à thermolaquage :
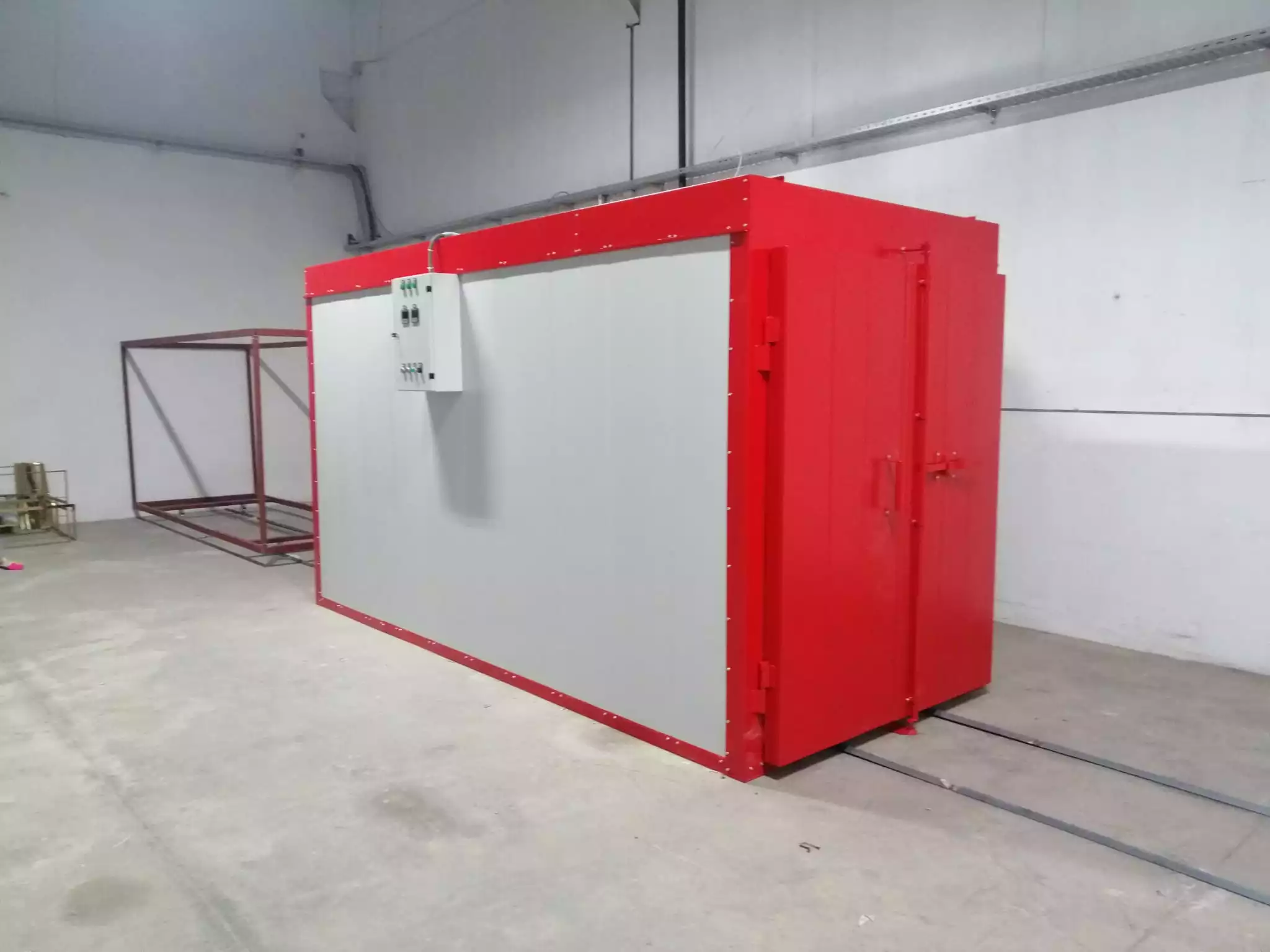
1. Fours à Convection
Principe de Fonctionnement :
Les fours à convection chauffent l’air à l’intérieur du four, qui est ensuite distribué uniformément autour des pièces à l’aide de ventilateurs. Ce type de four est l’un des plus couramment utilisés dans l’industrie du thermolaquage.
Avantages :
- Uniformité de la Chaleur : Grâce à la circulation d’air, les fours à convection offrent une distribution uniforme de la chaleur, réduisant les risques de défauts dans le revêtement.
- Adaptabilité : Convient à une large gamme de tailles et de formes de pièces, y compris les objets volumineux.
- Coût Initial : Généralement, ces fours ont un coût initial plus bas par rapport aux autres technologies de chauffage plus avancées.
Inconvénients :
- Consommation Énergétique : Peut être moins efficace en termes d’énergie par rapport aux fours infrarouges ou à induction, surtout pour les grandes charges.
- Temps de Chauffage : Le temps de montée en température peut être plus long, ce qui peut affecter la rapidité du cycle de production.
2. Fours Infrarouges
Principe de Fonctionnement :
Les fours infrarouges utilisent des rayons infrarouges pour chauffer directement la surface des pièces. Ce type de chauffage est basé sur le transfert de chaleur par rayonnement.
Avantages :
- Rapidité de Chauffage : Les fours infrarouges chauffent rapidement les surfaces, ce qui réduit considérablement le temps de cycle.
- Efficacité Énergétique : Consomment généralement moins d’énergie puisqu’ils chauffent directement la pièce sans chauffer tout le volume d’air autour.
- Finitions Complexes : Idéal pour les pièces avec des formes complexes et des géométries difficiles, où un chauffage direct est avantageux.
Inconvénients :
- Uniformité de la Chaleur : Peut avoir des difficultés à chauffer uniformément des pièces très épaisses ou denses, car la chaleur ne pénètre pas aussi profondément.
- Coût Initial : Le coût d’installation peut être plus élevé, surtout si une personnalisation spécifique est requise pour l’application.
3. Fours à Induction
Principe de Fonctionnement :
Les fours à induction utilisent des champs électromagnétiques pour chauffer les objets métalliques directement. Ce type de chauffage est extrêmement rapide et précis.
Avantages :
- Précision : Offre un contrôle précis de la température, idéal pour des applications nécessitant une gestion thermique rigoureuse.
- Rapidité : Très rapide à chauffer, ce qui réduit les temps de cycle de production.
- Efficacité Énergétique : Chauffe directement le matériau conducteur, ce qui réduit les pertes énergétiques.
Inconvénients :
- Limitation des Matériaux : Ne peut être utilisé que sur des matériaux conducteurs, ce qui limite son utilisation aux métaux.
- Coût Élevé : Le coût initial est généralement plus élevé que les autres types de fours, et le coût de l’équipement peut être prohibitif pour certaines petites et moyennes entreprises.
4. Fours Hybrides
Principe de Fonctionnement :
Les fours hybrides combinent la technologie de convection et infrarouge pour offrir une flexibilité et une efficacité accrues.
Avantages :
- Flexibilité : Peut traiter une variété de pièces et de matériaux, maximisant ainsi la polyvalence des applications.
- Efficacité Améliorée : Combine les avantages des deux systèmes de chauffage pour une efficacité énergétique et de traitement améliorée.
- Optimisation de la Qualité : Peut offrir une meilleure qualité de finition en ajustant les méthodes de chauffage selon les besoins.
Inconvénients :
- Coût Initial : L’investissement initial peut être élevé en raison de la complexité accrue du système.
- Maintenance : Peut nécessiter un entretien plus régulier et complexe en raison de la présence de deux systèmes de chauffage différents.
Tableau Comparatif
Voici un tableau qui résume les principales caractéristiques de chaque type de four à thermolaquage :
Type de Four | Avantages | Inconvénients | Applications Idéales |
---|---|---|---|
Convection | – Uniformité de chaleur<br>- Adaptabilité<br>- Coût initial bas | – Consommation énergétique<br>- Temps de chauffage long | Objets volumineux, production en série |
Infrarouge | – Chauffage rapide<br>- Efficacité énergétique<br>- Finitions complexes | – Uniformité pour pièces épaisses<br>- Coût initial | Pièces complexes, temps de cycle rapide |
Induction | – Précision thermique<br>- Rapidité<br>- Efficacité énergétique | – Limité aux matériaux conducteurs<br>- Coût élevé | Applications précises, matériaux conducteurs |
Hybride | – Flexibilité<br>- Efficacité améliorée<br>- Qualité optimisée | – Coût initial élevé<br>- Maintenance complexe | Diversité de matériaux et de formes |
Conclusion
Le choix du type de four à thermolaquage dépend de plusieurs facteurs, notamment la nature des pièces à traiter, les exigences de production, le budget disponible, et l’efficacité énergétique souhaitée.
- Fours à Convection : Recommandés pour les opérations à grande échelle nécessitant une uniformité de chaleur sur des pièces volumineuses.
- Fours Infrarouges : Idéaux pour des cycles de production rapides et des pièces de formes complexes.
- Fours à Induction : Conviennent aux applications nécessitant un contrôle thermique précis, mais limités aux métaux.
- Fours Hybrides : Offrent une polyvalence maximale pour traiter divers matériaux et formes.
En évaluant soigneusement vos besoins spécifiques et en tenant compte des avantages et des inconvénients de chaque type de four, vous pouvez faire un choix éclairé qui optimisera vos opérations de revêtement en poudre. Si vous avez besoin de plus d’informations ou de conseils supplémentaires, n’hésitez pas à demander !
Exemples d’applications
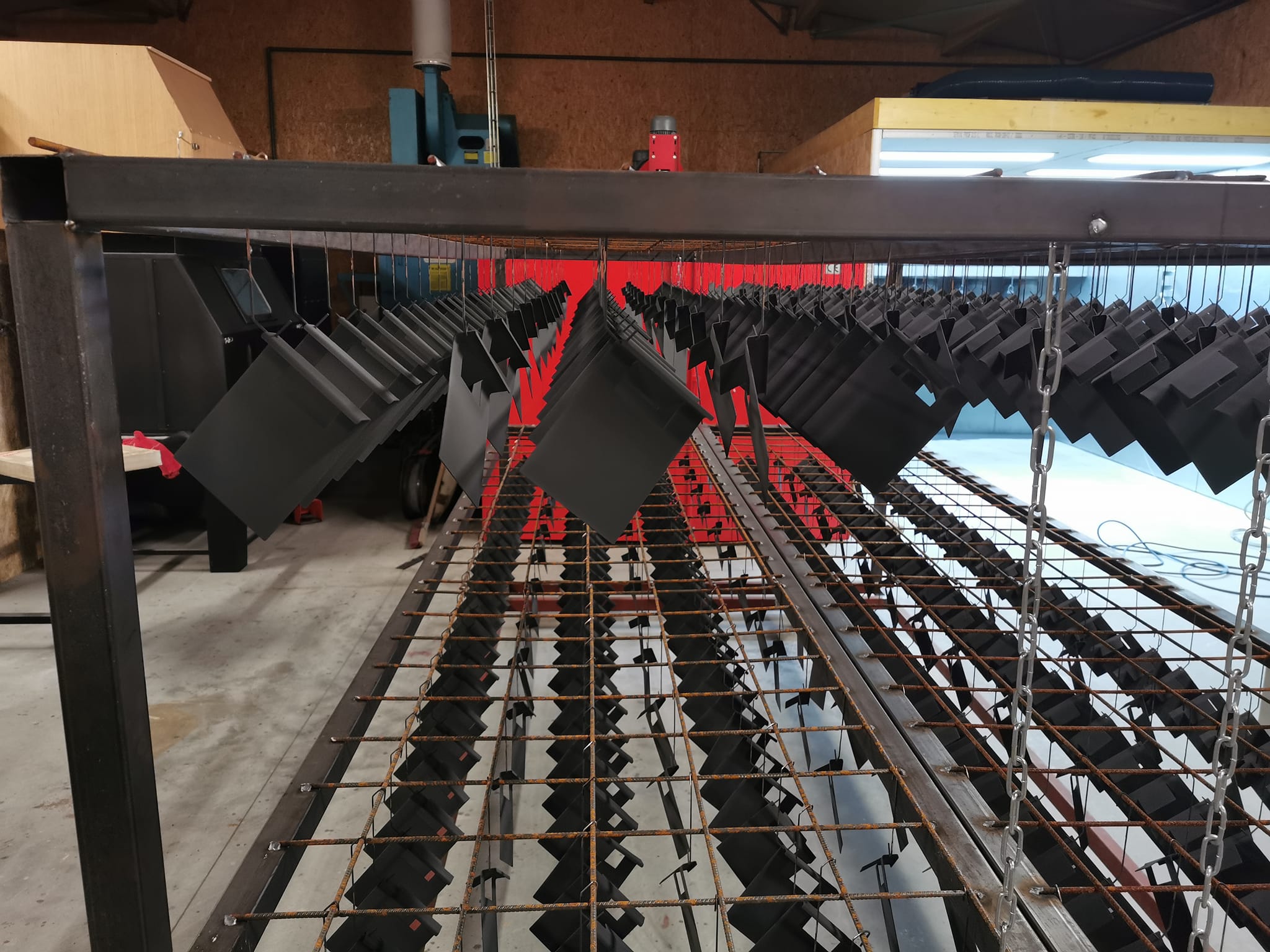
Les fours à thermolaquage sont utilisés dans une variété d’industries en raison de leurs capacités à fournir des finitions durables, esthétiques, et résistantes. Voici quelques exemples d’applications industrielles et commerciales où les fours à thermolaquage sont couramment utilisés :
Exemples d’Applications des Fours à Thermolaquage
1. Industrie Automobile
- Composants Peints : Les pièces automobiles comme les jantes, les châssis, et les éléments de suspension sont souvent thermolaqués pour améliorer leur résistance à la corrosion et leur apparence esthétique.
- Accessoires et Pièces : Les rétroviseurs, poignées de porte, et autres accessoires sont également revêtus pour offrir une protection supplémentaire contre les rayures et les intempéries.
2. Équipements Électroménagers
- Appareils de Cuisine : Les fours, réfrigérateurs, et autres appareils ménagers utilisent le thermolaquage pour protéger les surfaces métalliques contre l’usure et offrir des finitions brillantes et colorées.
- Machines à Laver et Sèche-linge : Les panneaux extérieurs de ces appareils bénéficient du revêtement en poudre pour leur résistance accrue à l’humidité et aux produits chimiques ménagers.
3. Mobilier Métallique
- Meubles de Bureau : Les cadres de chaises, bureaux, et autres meubles de bureau en métal utilisent le thermolaquage pour améliorer la durabilité et offrir une finition élégante.
- Mobilier d’Extérieur : Les meubles d’extérieur, tels que les chaises de jardin et les tables, sont thermolaqués pour résister aux intempéries et aux rayons UV, ce qui prévient la décoloration et la corrosion.
4. Industrie Électronique
- Boîtiers d’Équipements : Les boîtiers pour ordinateurs, téléviseurs, et autres appareils électroniques bénéficient du thermolaquage pour protéger les composants internes de la poussière et de l’humidité.
- Composants Intérieurs : Les dissipateurs de chaleur et autres pièces métalliques internes sont également revêtus pour améliorer leur longévité et leur performance thermique.
5. Équipements de Construction
- Machines de Chantier : Les pièces de machines telles que les grues, bulldozers, et excavateurs sont souvent thermolaquées pour résister aux environnements difficiles et prolonger leur durée de vie.
- Outils et Équipements : Les outils manuels et électriques, ainsi que les équipements de sécurité, utilisent le thermolaquage pour offrir une résistance accrue à l’usure et une meilleure apparence.
6. Industrie du Transport
- Vélos et Motocyclettes : Les cadres de vélos et de motos sont thermolaqués pour améliorer la résistance à la rouille et offrir une finition durable.
- Trains et Wagons : Les composants métalliques des trains, comme les bogies et les structures de carrosserie, sont revêtus pour protéger contre la corrosion et améliorer l’apparence.
7. Infrastructure et Urbanisme
- Poteaux de Signalisation et Barrières de Sécurité : Utilisent le thermolaquage pour garantir une longue durée de vie et une visibilité accrue grâce à des couleurs vives et durables.
- Équipements de Jeux et Parcs : Les structures de jeux pour enfants et les équipements de parcs sont revêtus pour assurer sécurité et durabilité contre les éléments extérieurs.
8. Industrie de l’Aéronautique
- Composants Intérieurs et Extérieurs : Les avions utilisent le thermolaquage pour les composants intérieurs, comme les panneaux et les sièges, ainsi que pour les pièces extérieures, comme les capots et les structures de fuselage.
- Finitions Anti-Corrosion : Le revêtement en poudre est utilisé pour protéger les pièces critiques contre la corrosion due à l’exposition aux éléments.
Avantages du Thermolaquage pour ces Applications
- Résistance aux Intempéries et à la Corrosion : Le revêtement en poudre offre une protection exceptionnelle contre la rouille, la corrosion, et les éléments extérieurs, prolongeant ainsi la durée de vie des pièces revêtues.
- Durabilité et Résistance : Les finitions obtenues par thermolaquage sont extrêmement durables et résistantes aux éraflures, aux chocs, et aux produits chimiques.
- Flexibilité Esthétique : Une large gamme de couleurs et de finitions est disponible, permettant aux designers de personnaliser l’apparence des produits selon les besoins spécifiques.
- Écologique : Le processus de thermolaquage est respectueux de l’environnement car il ne nécessite pas de solvants et réduit les émissions de composés organiques volatils (COV).
Conclusion
Les fours à thermolaquage jouent un rôle clé dans diverses industries, fournissant des solutions de revêtement efficaces et durables pour une multitude d’applications. En sélectionnant le bon type de four et en optimisant les paramètres de processus, les entreprises peuvent garantir des résultats de haute qualité et économiquement viables.
Si vous avez besoin de plus d’informations sur une application spécifique ou souhaitez discuter d’autres aspects du thermolaquage, n’hésitez pas à me le faire savoir !
Coût des fours
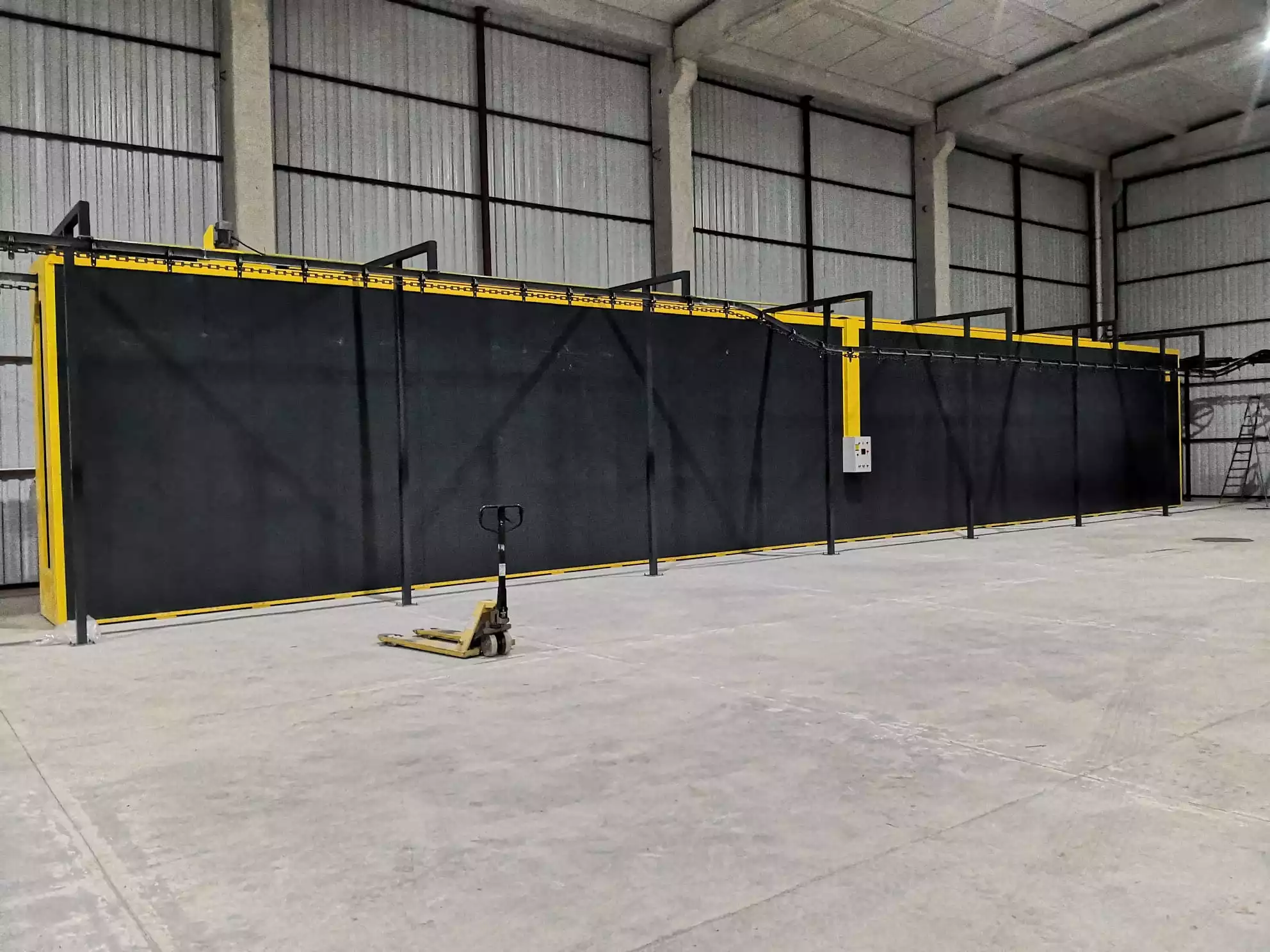
Le coût des fours à thermolaquage peut varier considérablement en fonction de plusieurs facteurs, notamment la taille, la capacité, le type de technologie utilisée, et les caractéristiques spécifiques du four. Voici une analyse détaillée des coûts associés aux différents types de fours à thermolaquage, ainsi que des facteurs qui influencent ces coûts.
Facteurs Influant sur le Coût des Fours à Thermolaquage
- Taille et Capacité
- Petits Fours de Laboratoire : Les petits fours utilisés pour des tests et des productions en faible volume sont généralement moins coûteux, avec des prix pouvant commencer autour de 5 000 à 15 000 euros.
- Fours de Production Moyenne : Ces fours, utilisés pour des productions à échelle moyenne, coûtent généralement entre 20 000 et 50 000 euros.
- Grands Fours Industriels : Les grands fours utilisés pour des productions industrielles de masse peuvent coûter entre 50 000 et 200 000 euros, voire plus selon la capacité et les spécifications.
- Type de Technologie
- Fours à Convection : Ces fours sont souvent moins chers en termes de coût initial, avec des prix pouvant varier de 10 000 à 100 000 euros, selon la taille et les caractéristiques.
- Fours Infrarouges : En raison de leur technologie de chauffage rapide et ciblé, les fours infrarouges peuvent être plus coûteux, généralement entre 15 000 et 150 000 euros.
- Fours à Induction : Les fours à induction, qui nécessitent des composants spécifiques pour chauffer les matériaux conducteurs, peuvent coûter entre 20 000 et 200 000 euros.
- Fours Hybrides : En combinant plusieurs technologies, les fours hybrides peuvent être les plus chers, avec des prix allant de 30 000 à 250 000 euros, en fonction des caractéristiques intégrées.
- Caractéristiques Spécifiques
- Contrôles Avancés : Les systèmes de contrôle numérique et les automatisations intégrées augmentent généralement le coût des fours, ajoutant entre 5 000 et 20 000 euros au prix de base.
- Isolation et Efficacité Énergétique : Les fours dotés d’une isolation thermique avancée pour améliorer l’efficacité énergétique peuvent avoir un coût initial plus élevé.
- Options Personnalisées : Les personnalisations spécifiques pour répondre à des besoins uniques d’application peuvent ajouter des coûts supplémentaires.
- Marque et Fabricant
- Réputation de la Marque : Les fours fabriqués par des entreprises réputées et établies dans l’industrie peuvent coûter plus cher en raison de leur fiabilité et de leur qualité éprouvée.
- Service et Support : Les fournisseurs offrant des services après-vente étendus et un support technique peuvent justifier des prix plus élevés.
- Installation et Maintenance
- Coûts d’Installation : L’installation professionnelle d’un four, surtout pour les grandes installations industrielles, peut ajouter de 2 000 à 10 000 euros au coût total.
- Entretien et Réparations : Les coûts d’entretien continu, y compris le remplacement des pièces et les réparations, doivent être pris en compte dans le calcul des coûts à long terme.
Coût Global de Possession
En plus du coût initial du four, il est important de considérer le coût global de possession, qui inclut :
- Consommation Énergétique : Les fours plus efficaces peuvent réduire les coûts opérationnels à long terme en consommant moins d’énergie.
- Durabilité et Longévité : Investir dans un four de haute qualité peut offrir des économies à long terme grâce à une durée de vie prolongée et à une fiabilité accrue.
- Retour sur Investissement (ROI) : Calculer le retour sur investissement en fonction de l’augmentation de la productivité, de l’amélioration de la qualité des produits, et de la réduction des déchets.
Estimation des Coûts par Type de Four
Type de Four | Coût Estimé | Applications |
---|---|---|
Convection | 10 000 à 100 000 euros | Production à grande échelle |
Infrarouge | 15 000 à 150 000 euros | Cycles rapides, formes complexes |
Induction | 20 000 à 200 000 euros | Applications précises, métaux |
Hybride | 30 000 à 250 000 euros | Flexibilité maximale |
Conseils pour Optimiser l’Achat
- Évaluation des Besoins Spécifiques
- Analysez vos besoins spécifiques en matière de production pour choisir le type de four le plus adapté à votre activité.
- Considérez la capacité requise, le type de pièces à traiter, et les exigences de qualité.
- Comparaison des Fournisseurs
- Demandez des devis à plusieurs fournisseurs pour comparer les options disponibles.
- Évaluez les offres en fonction des coûts initiaux et des coûts d’exploitation à long terme.
- Considérations Financières
- Recherchez des options de financement ou des subventions industrielles qui pourraient alléger le coût initial d’achat.
- Prenez en compte les incitations fiscales pour l’achat d’équipements éco-énergétiques.
- Préparation pour l’Entretien
- Assurez-vous d’avoir un plan de maintenance préventive en place pour minimiser les coûts de réparation imprévus.
- Investissez dans la formation du personnel pour garantir une utilisation optimale et sûre de l’équipement.
Conclusion
Le choix et l’achat d’un four à thermolaquage impliquent une analyse approfondie des coûts, des besoins spécifiques, et des caractéristiques des différentes technologies disponibles. En considérant à la fois le coût initial et les coûts à long terme, vous pouvez faire un choix éclairé qui améliorera la qualité de votre production et maximisera le retour sur investissement. Si vous avez besoin de conseils supplémentaires ou d’une assistance pour un cas spécifique, n’hésitez pas à me le faire savoir !
Temps installation four
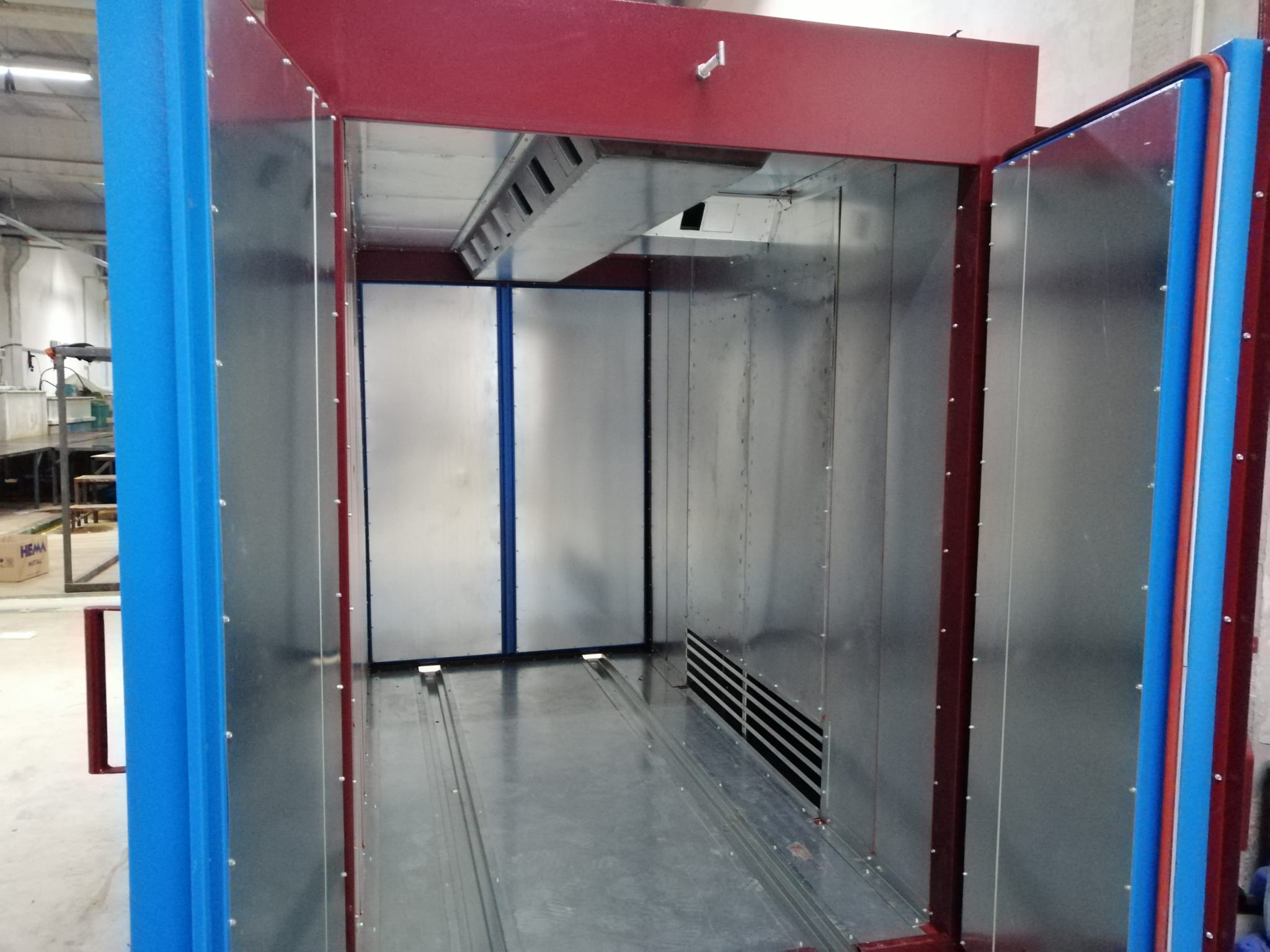
L’installation d’un four à thermolaquage est un processus qui nécessite une planification minutieuse et une coordination efficace. Le temps requis pour installer un four peut varier considérablement en fonction de plusieurs facteurs, notamment la taille du four, la complexité du système, et les conditions spécifiques du site d’installation. Voici une analyse détaillée des différents aspects qui influencent le temps d’installation d’un four à thermolaquage :
Facteurs Influant sur le Temps d’Installation
- Taille et Complexité du Four
- Petits Fours de Laboratoire : Les petits fours, souvent utilisés pour des tests ou de petites productions, peuvent être installés en quelques jours. La simplicité de ces unités signifie qu’elles nécessitent moins de travail pour l’installation.
- Fours de Production Moyenne : Les fours de taille moyenne, utilisés pour des productions à échelle moyenne, peuvent prendre de 1 à 2 semaines pour être installés, en fonction de leur configuration et des besoins de connexion.
- Grands Fours Industriels : Les installations industrielles de grande envergure, qui incluent des systèmes complexes, peuvent nécessiter entre 2 et 4 semaines pour une installation complète. Cela inclut souvent la construction de structures de support et l’intégration dans des lignes de production existantes.
- Type de Technologie
- Fours à Convection : Ces fours, avec des systèmes de ventilation et de circulation d’air, peuvent être relativement simples à installer, mais le temps peut augmenter avec la taille et les spécificités de l’installation.
- Fours Infrarouges : L’installation de systèmes infrarouges peut être plus rapide que d’autres technologies, mais nécessite une attention particulière à l’alignement des émetteurs infrarouges pour garantir une distribution homogène de la chaleur. L’installation typique peut prendre environ 1 à 2 semaines.
- Fours à Induction : Ces fours nécessitent une installation spécialisée en raison des systèmes électromagnétiques complexes. L’installation peut prendre de 2 à 3 semaines, en particulier si des modifications structurelles sont nécessaires.
- Fours Hybrides : Les fours qui combinent plusieurs technologies de chauffage peuvent nécessiter un temps d’installation plus long, souvent de 3 à 4 semaines, en raison de la complexité accrue de l’équipement et de l’intégration requise.
- Préparation du Site
- Infrastructure Électrique : La préparation et la mise à jour des installations électriques pour accueillir un four à thermolaquage peuvent prendre plusieurs jours à quelques semaines, selon la nécessité de nouvelles connexions ou de mises à niveau.
- Systèmes de Ventilation : La mise en place ou la modification des systèmes de ventilation existants pour répondre aux normes de sécurité peut prolonger le temps d’installation. Cela est particulièrement crucial pour les grands fours industriels.
- Fondations et Structures de Support : Pour les grands fours, il peut être nécessaire de construire des structures de support ou de renforcer le sol, ce qui ajoute au temps total d’installation.
- Personnel et Logistique
- Disponibilité de l’Équipe : La disponibilité d’une équipe qualifiée pour réaliser l’installation joue un rôle clé dans le temps nécessaire. Un personnel expérimenté peut accélérer le processus.
- Logistique de Transport : La livraison des composants du four au site d’installation peut également affecter le calendrier global, surtout si des éléments personnalisés ou de grande taille doivent être transportés.
- Tests et Mise en Service
- Tests de Fonctionnalité : Une fois le four installé, il est crucial de réaliser des tests de fonctionnalité pour s’assurer que toutes les parties de l’équipement fonctionnent correctement et en toute sécurité. Cela peut prendre 2 à 5 jours supplémentaires.
- Formation du Personnel : La formation des opérateurs et du personnel de maintenance peut ajouter quelques jours au processus global d’installation. Cela garantit que le personnel est capable d’opérer le four efficacement et en toute sécurité.
Estimation Générale du Temps d’Installation
Type de Four | Temps d’Installation Estimé |
---|---|
Petits Fours de Laboratoire | 1 à 3 jours |
Fours de Production Moyenne | 1 à 2 semaines |
Grands Fours Industriels | 2 à 4 semaines |
Fours à Convection | 1 à 3 semaines |
Fours Infrarouges | 1 à 2 semaines |
Fours à Induction | 2 à 3 semaines |
Fours Hybrides | 3 à 4 semaines |
Conseils pour Optimiser l’Installation
- Planification Précoce
- Évaluation du Site : Effectuez une évaluation précoce du site pour identifier les besoins en infrastructure et anticiper les défis potentiels.
- Coordination Logistique : Coordonnez à l’avance la livraison des composants et la disponibilité du personnel d’installation pour éviter les retards.
- Engagement de Professionnels
- Entreprises Spécialisées : Collaborez avec des entreprises spécialisées dans l’installation de fours industriels pour assurer une installation efficace et conforme aux normes.
- Support Technique : Assurez-vous d’avoir un support technique disponible pour résoudre rapidement les problèmes qui pourraient survenir pendant l’installation.
- Intégration avec les Systèmes Existants
- Systèmes de Production : Intégrez le four dans les systèmes de production existants pour minimiser les interruptions et maximiser l’efficacité.
- Mise en Réseau : Assurez-vous que le four est compatible avec les systèmes de contrôle et de gestion de la production pour un fonctionnement optimal.
- Préparation pour les Tests
- Élaboration de Procédures de Test : Établissez des procédures de test claires pour vérifier le bon fonctionnement du four après l’installation.
- Formation et Sécurité : Formez le personnel aux pratiques de sécurité et à l’utilisation de l’équipement avant la mise en service.
Conclusion
Le temps nécessaire pour l’installation d’un four à thermolaquage varie en fonction de nombreux facteurs, mais une planification et une exécution soignées peuvent contribuer à optimiser le processus. En collaborant avec des professionnels expérimentés et en assurant une préparation adéquate du site et de l’équipe, les entreprises peuvent s’assurer que leur nouvel équipement est opérationnel et productif le plus rapidement possible.
Le Revêtement en Poudre
L’équipement de revêtement en poudre est utilisé pour appliquer une fine couche de poudre sur une surface métallique. Ce type de revêtement est appliqué par un procédé électrostatique et constitue une méthode très populaire pour la finition des pièces métalliques.
Ce type d’équipement peut être divisé en deux grandes catégories : automatiques et manuels. Les cabines automatiques sont plus populaires car elles offrent de meilleurs taux de production, mais elles sont également plus chères.
Une cabine à poudre est une enceinte dans laquelle se déroule le processus de revêtement en poudre. L’équipement de revêtement en poudre comprend un four dans lequel les pièces sont chauffées pour activer la poudre, un pistolet qui pulvérise ou brosse la poudre, une bande transporteuse qui déplace les pièces à travers le four et des pistolets de type cartouche pour appliquer des revêtements plus épais avec moins de pulvérisation.
Le revêtement en poudre est une technique utilisée pour donner une finition aux pièces métalliques. Cette technique est utilisée depuis de nombreuses années et reste aujourd’hui l’une des techniques les plus populaires.
L’équipement de revêtement en poudre comprend des cabines, des fours, des pistolets, des machines, des lignes et des convoyeurs. Une cabine peut être automatique ou manuelle. Une cabine automatique est plus chère qu’une cabine manuelle mais elle est aussi plus rapide et plus efficace
Non seulement nous fabriquons nos équipements de revêtement en poudre, mais nous les expédions également dans vos locaux avec soin dans le monde entier.
L’équipement de revêtement en poudre est utilisé pour appliquer une fine couche de poudre sur une surface métallique. Ce type de revêtement est appliqué par un procédé électrostatique et constitue une méthode très populaire pour la finition des pièces métalliques.
Ce type d’équipement peut être divisé en deux grandes catégories : automatiques et manuels. Les cabines automatiques sont plus populaires car elles offrent de meilleurs taux de production, mais elles sont également plus chères.
Une cabine à poudre est une enceinte dans laquelle se déroule le processus de revêtement en poudre. L’équipement de revêtement en poudre comprend un four dans lequel les pièces sont chauffées pour activer la poudre, un pistolet qui pulvérise ou brosse la poudre, une bande transporteuse qui déplace les pièces à travers le four et des pistolets de type cartouche pour appliquer des revêtements plus épais avec moins de pulvérisation.
Le revêtement en poudre est une technique utilisée pour donner une finition aux pièces métalliques. Cette technique est utilisée depuis de nombreuses années et reste aujourd’hui l’une des techniques les plus populaires.
L’équipement de revêtement en poudre comprend des cabines, des fours, des pistolets, des machines, des lignes et des convoyeurs. Une cabine peut être automatique ou manuelle. Une cabine automatique est plus chère qu’une cabine manuelle mais elle est aussi plus rapide et plus efficace
- Fours de polymérisation: Les fours de polymérisation sont des équipements industriels cruciaux dans le traitement des polymères. Ils permettent le durcissement contrôlé des matériaux polymères à travers divers processus tels que la polymérisation thermique, la réticulation chimique, et la polymérisation par rayonnement.
- Polymérisation thermique: La polymérisation thermique implique la conversion de monomères en polymères par l’application de chaleur. Les fours de polymérisation thermique maintiennent des conditions spécifiques de température, de pression, et de durée pour assurer une réaction exothermique contrôlée.
- Polymérisation par rayonnement: Cette méthode de polymérisation utilise des rayonnements tels que les ultraviolets (UV) pour initier la réaction de polymérisation. Les fours associés à cette technique assurent une exposition uniforme aux rayonnements, permettant le durcissement efficace des polymères.
- Température de polymérisation: La température de polymérisation est critique pour contrôler la vitesse et l’efficacité du processus. Les fours garantissent le maintien précis de la température requise, influençant la cinétique de polymérisation et les propriétés finales du matériau.
- Réaction exothermique: La polymérisation génère souvent de la chaleur (réaction exothermique). Les fours intègrent des systèmes de refroidissement pour éviter des températures excessives, assurant un durcissement uniforme sans compromettre l’intégrité des polymères.
- Contrôle du processus: Les fours de polymérisation intègrent des dispositifs de contrôle sophistiqués, régulant des paramètres tels que la température, la pression, et le temps. Cela garantit une polymérisation précise, répondant aux exigences spécifiques des applications industrielles.
- Durcissement des polymères: Le durcissement des polymères, facilité par les fours spécialisés, transforme les matériaux d’un état malléable à une structure solide. Les paramètres de durcissement, comme la température et le temps, sont minutieusement ajustés pour obtenir des propriétés désirées.
- Équipement de séchage: Certains fours de polymérisation fonctionnent également comme des équipements de séchage, éliminant l’humidité résiduelle des matériaux polymères. Le contrôle précis de la température et de l’humidité garantit un séchage efficace sans compromettre les caractéristiques du matériau.
- Cinétique de polymérisation: La cinétique de polymérisation étudie la vitesse des réactions de polymérisation. Les fours jouent un rôle crucial en maintenant des conditions idéales pour influencer la cinétique, permettant ainsi un contrôle optimal du processus de durcissement.
- Polymérisation en masse: La polymérisation en masse traite des grandes quantités de polymères simultanément. Les fours associés à ce processus sont conçus pour gérer des charges importantes tout en maintenant des conditions uniformes pour chaque matériau.
Fours de polymérisation: Les fours de polymérisation sont des équipements industriels essentiels utilisés dans la transformation des polymères. Ces systèmes fournissent un environnement contrôlé pour des processus tels que la polymérisation thermique, la réticulation chimique, et la polymérisation par rayonnement. Ils garantissent des conditions précises de température, de pression, et de durée, assurant ainsi le durcissement uniforme des matériaux polymères. Ces équipements jouent un rôle clé dans la fabrication de produits polymériques aux propriétés spécifiques, en influençant la cinétique de polymérisation et en permettant un contrôle fin du processus de durcissement.
Polymérisation thermique: La polymérisation thermique est un processus fondamental dans le durcissement des polymères. Ce mécanisme implique l’application de chaleur pour déclencher la réaction de conversion des monomères en polymères. Les fours de polymérisation thermique sont conçus pour maintenir des conditions spécifiques de température, de pression, et de durée, assurant ainsi une réaction exothermique contrôlée. En contrôlant ces paramètres, les fours garantissent un durcissement homogène des matériaux polymères, influençant directement leurs propriétés finales et leur utilisation dans diverses applications industrielles.
Nous ne sommes pas seulement les fabricants de vos équipements de revêtement en poudre, nous sommes également vos partenaires de livraison dans le monde entier.
Chez EMS Powder Coating Equipment, nous comprenons qu’il est tout aussi important de vous fournir votre équipement de revêtement en poudre rapidement et en toute sécurité que de le fabriquer selon les normes les plus élevées. C’est pourquoi nous proposons des services de livraison dans le monde entier à tous nos clients.
Nous travaillons avec un réseau de partenaires maritimes expérimentés et fiables pour garantir que votre équipement arrive à temps et en parfait état. Nous proposons également une variété d’options d’expédition adaptées à votre budget et à vos besoins.
Que vous ayez besoin d’expédier votre équipement à une adresse locale ou vers une destination internationale, nous pouvons vous aider. Nous travaillerons avec vous pour choisir la meilleure option d’expédition pour vos besoins et pour vous tenir informé de l’état de votre envoi à chaque étape du processus.
Ainsi, lorsque vous choisissez EMS pour votre équipement de revêtement en poudre, vous obtenez non seulement les meilleurs produits du marché, mais vous bénéficiez également de la meilleure expérience de livraison possible.
Contactez-nous dès aujourd’hui pour en savoir plus sur nos services de livraison dans le monde entier.
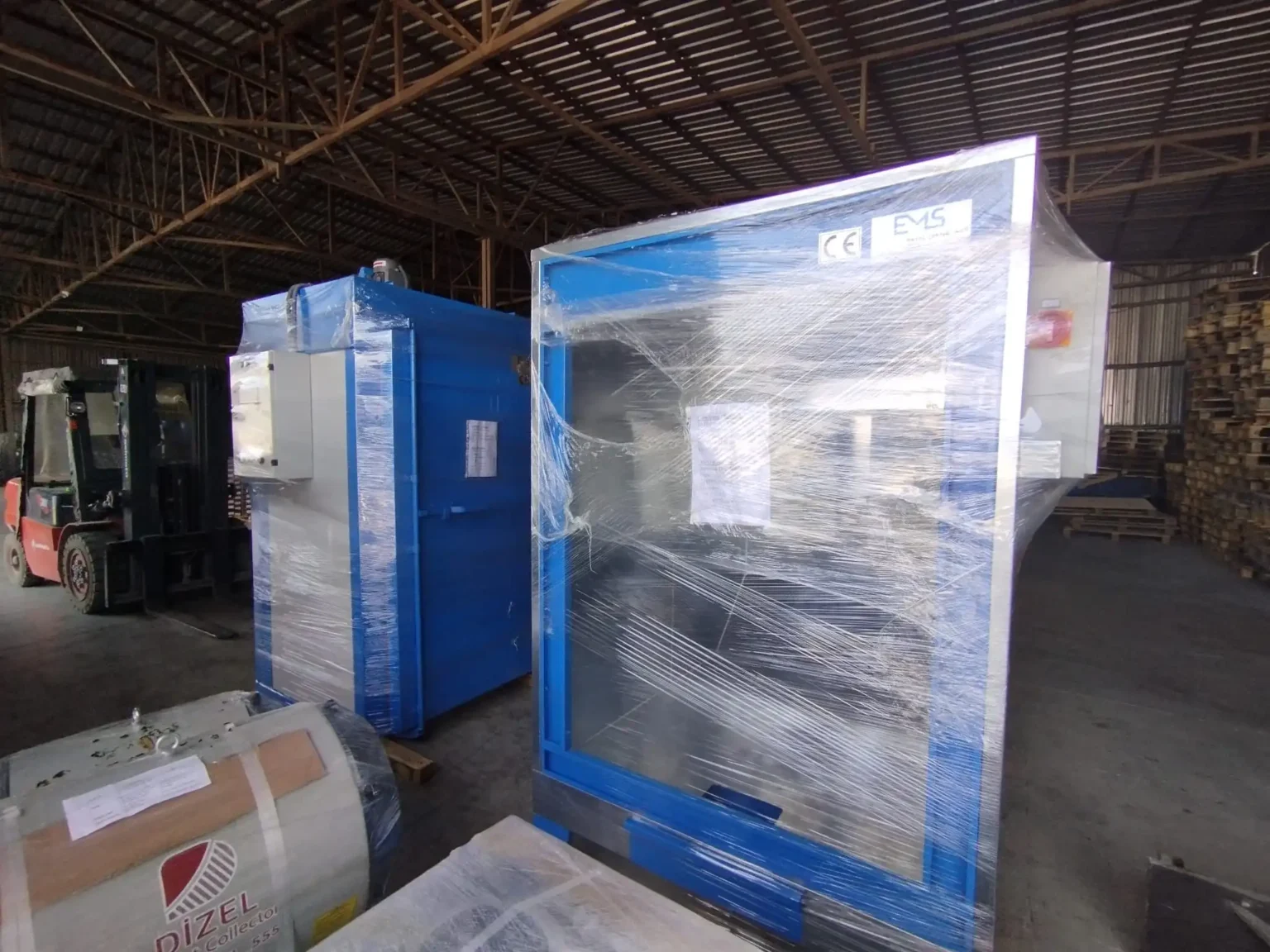

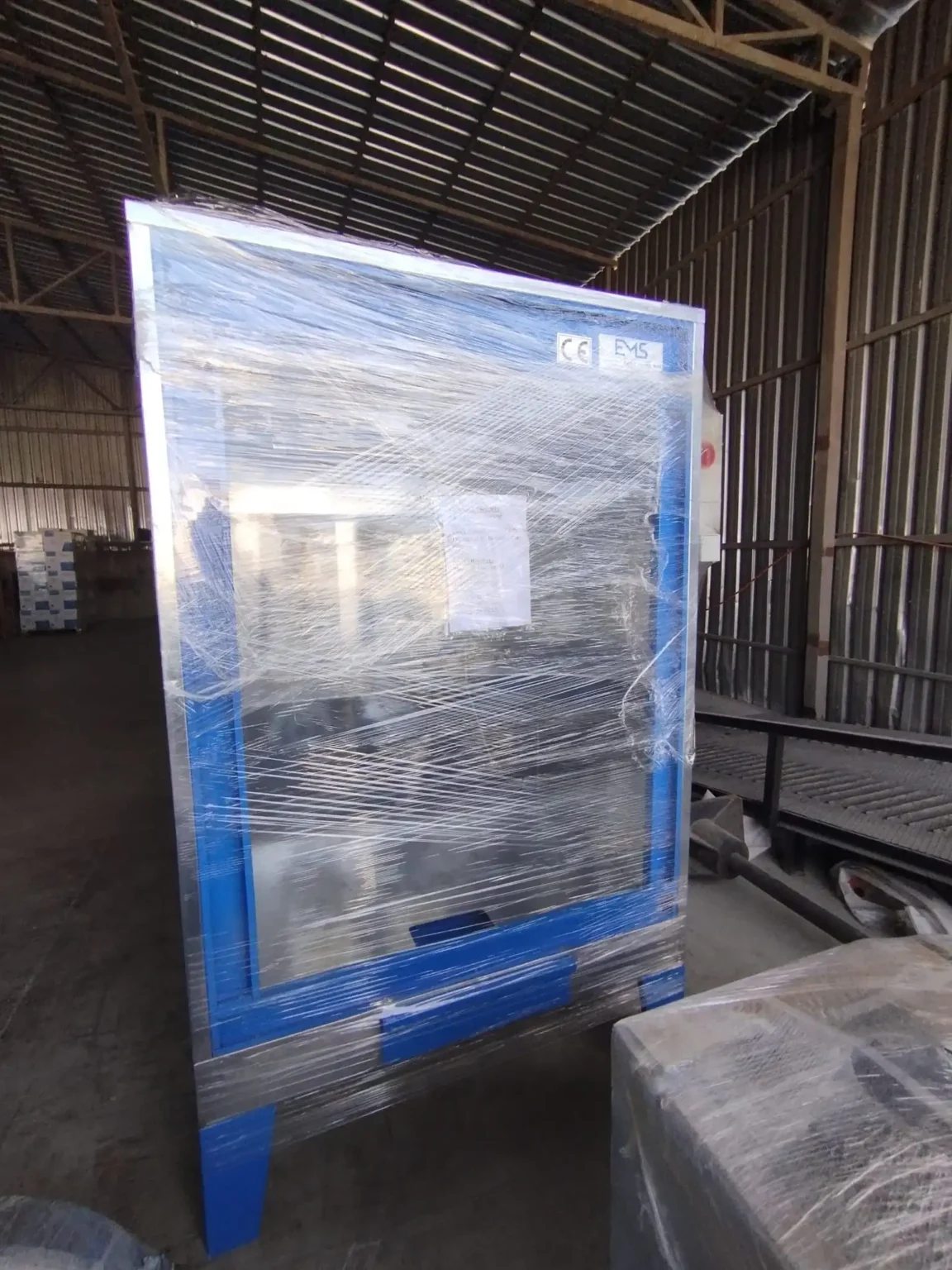
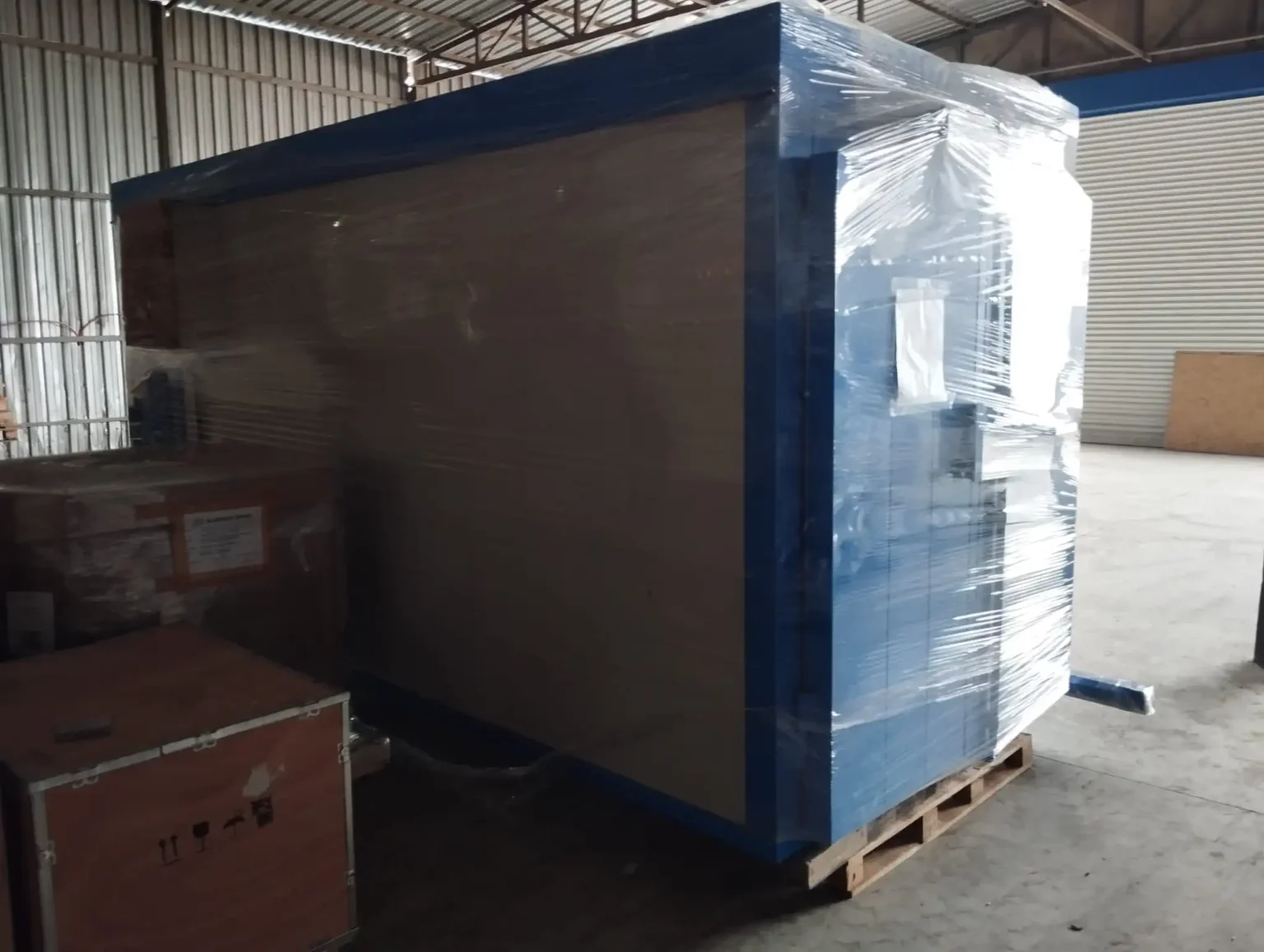
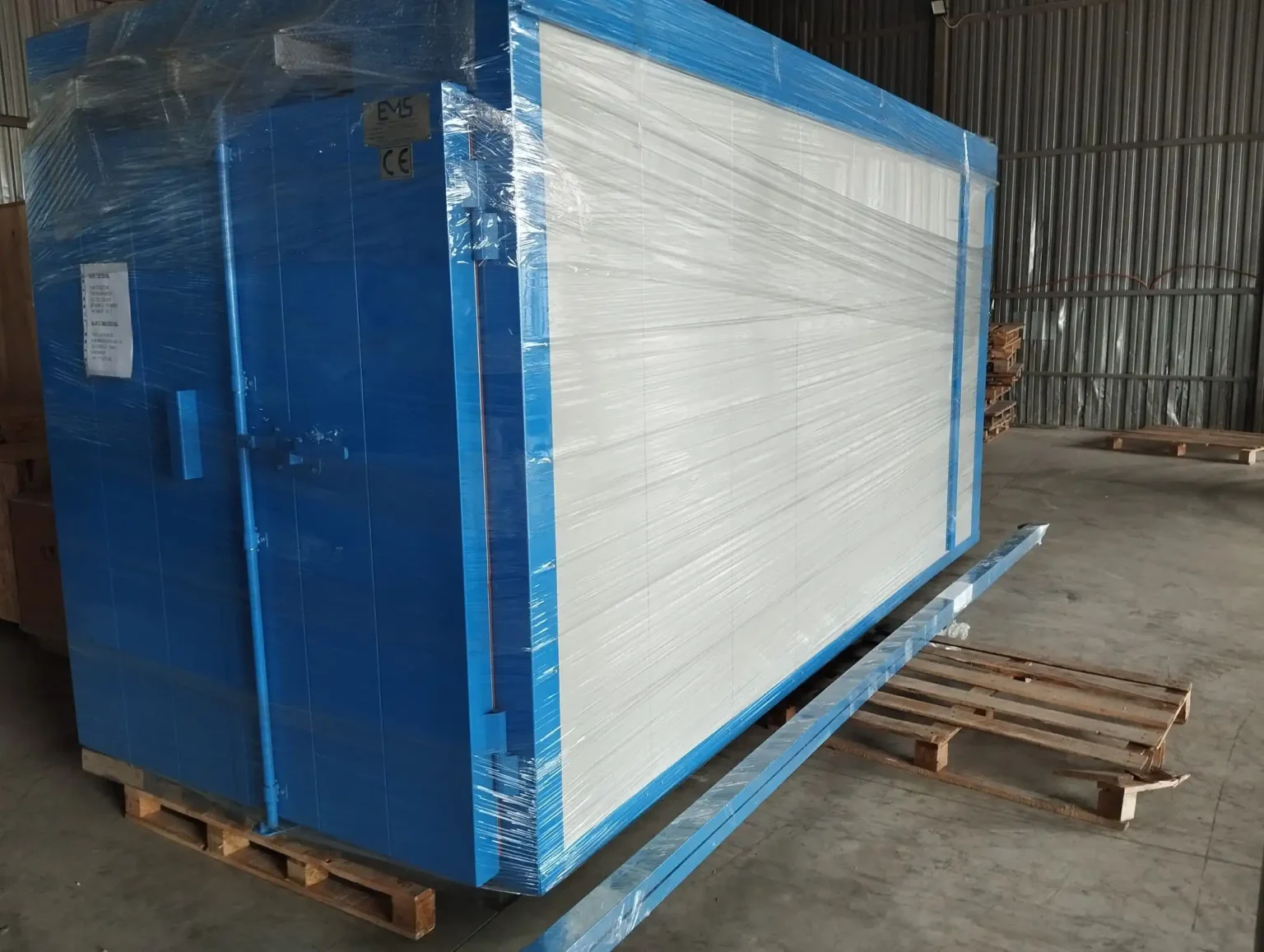
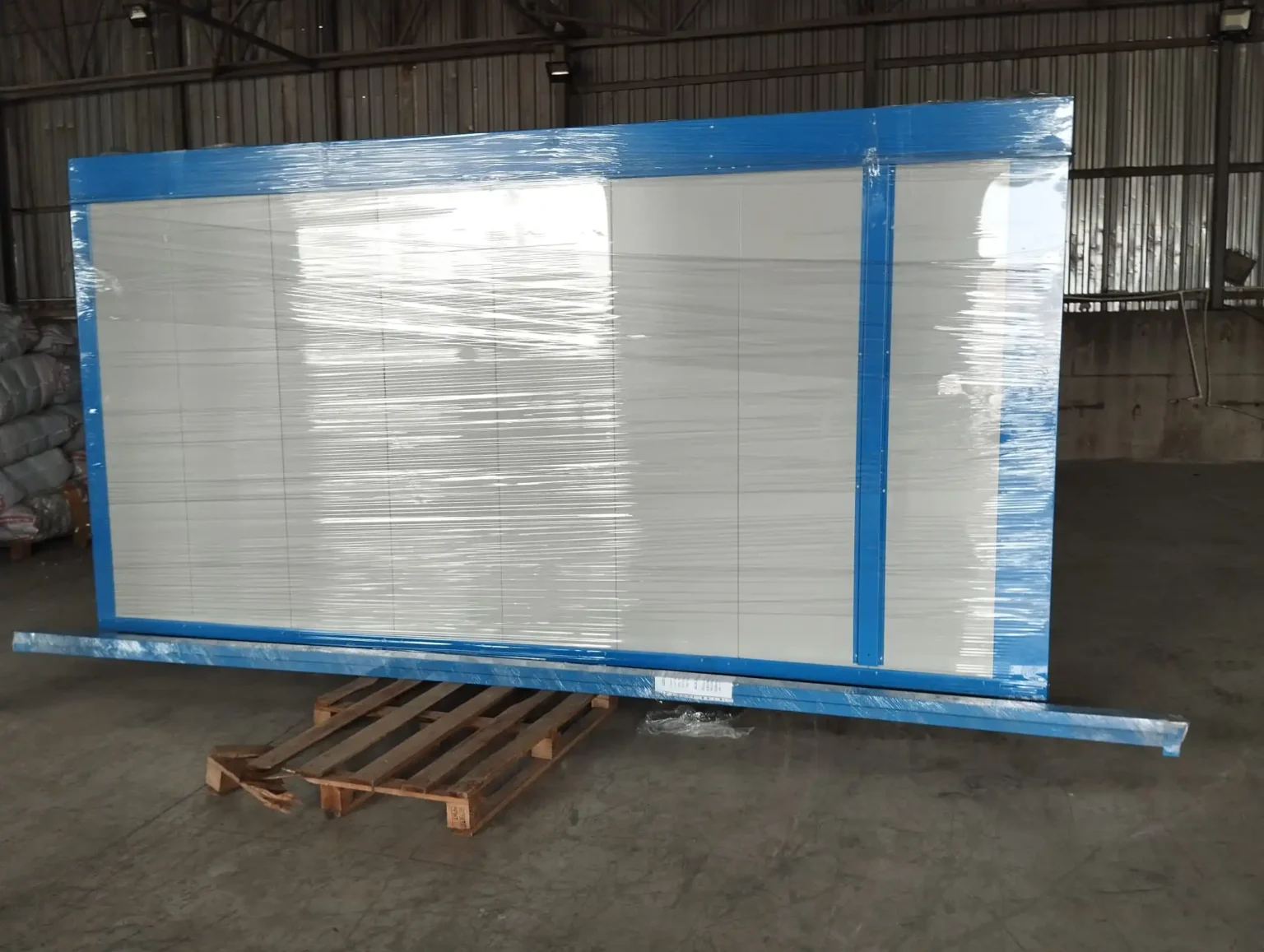
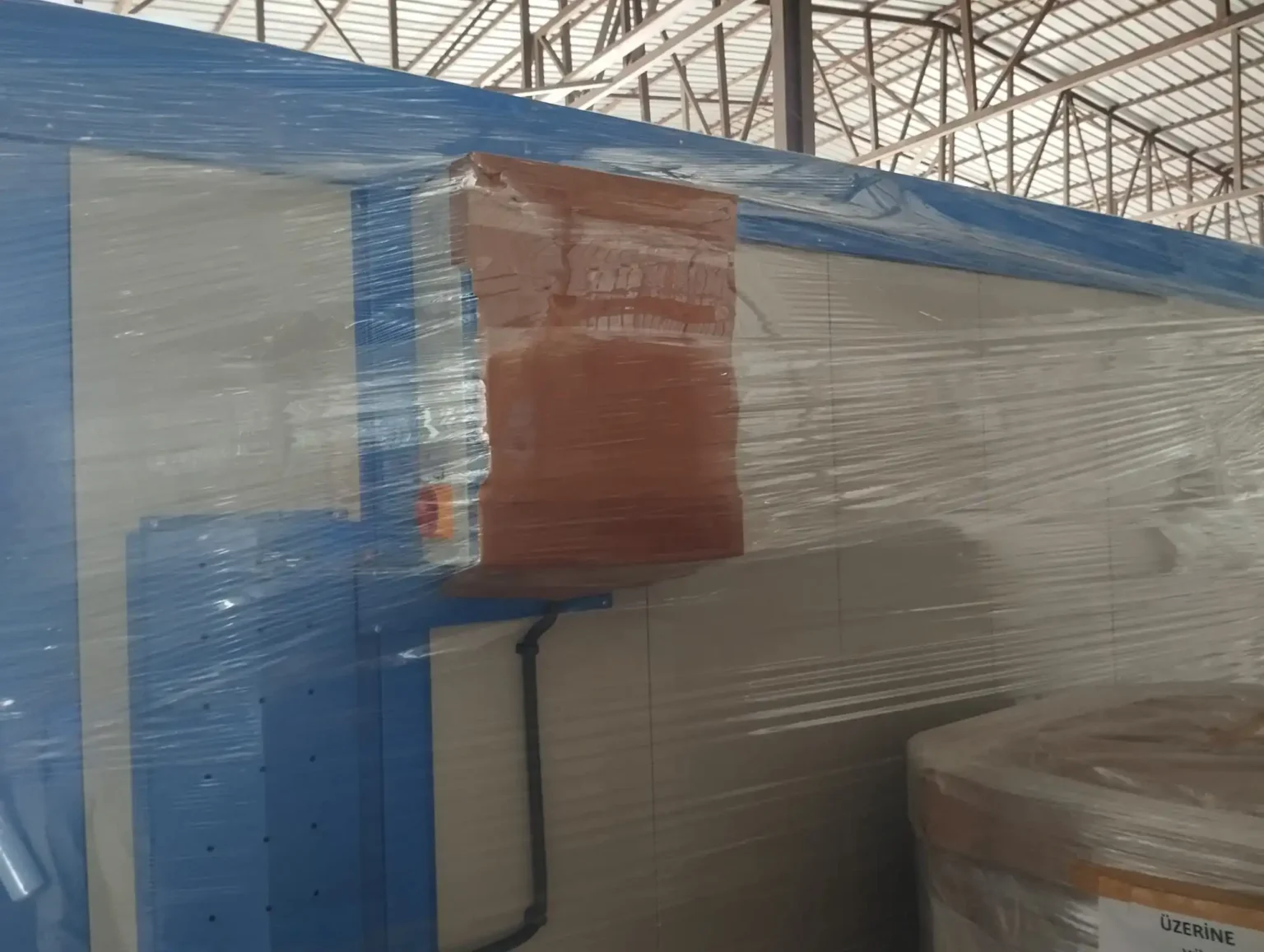
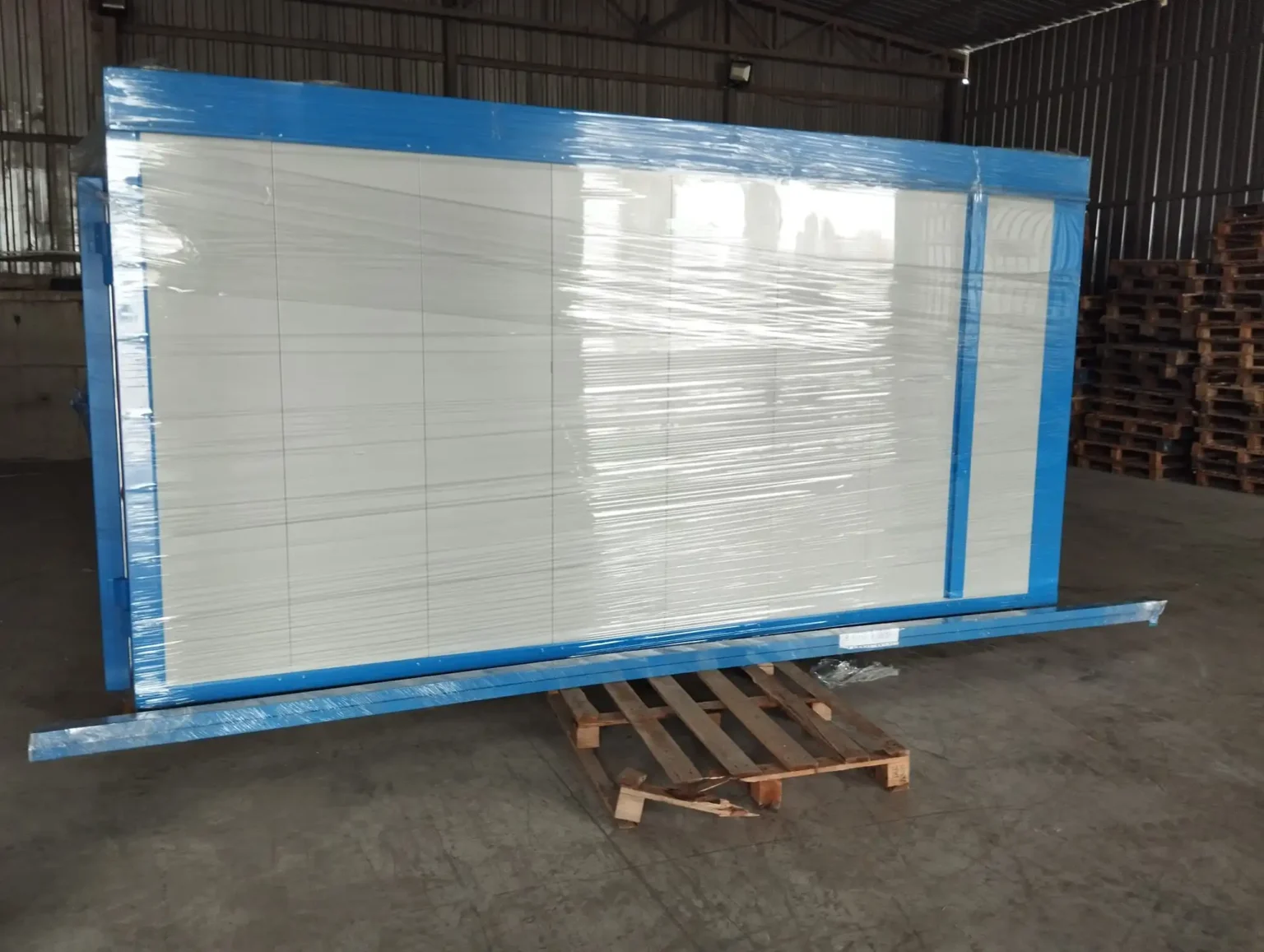
L’équipement de revêtement en poudre est utilisé pour appliquer une fine couche de poudre sur une surface métallique. Ce type de revêtement est appliqué par un procédé électrostatique et constitue une méthode très populaire pour la finition des pièces métalliques.
Ce type d’équipement peut être divisé en deux grandes catégories : automatiques et manuels. Les cabines automatiques sont plus populaires car elles offrent de meilleurs taux de production, mais elles sont également plus chères.
Une cabine à poudre est une enceinte dans laquelle se déroule le processus de revêtement en poudre. L’équipement de revêtement en poudre comprend un four dans lequel les pièces sont chauffées pour activer la poudre, un pistolet qui pulvérise ou brosse la poudre, une bande transporteuse qui déplace les pièces à travers le four et des pistolets de type cartouche pour appliquer des revêtements plus épais avec moins de pulvérisation.
Le revêtement en poudre est une technique utilisée pour donner une finition aux pièces métalliques. Cette technique est utilisée depuis de nombreuses années et reste aujourd’hui l’une des techniques les plus populaires.
L’équipement de revêtement en poudre comprend des cabines, des fours, des pistolets, des machines, des lignes et des convoyeurs. Une cabine peut être automatique ou manuelle. Une cabine automatique est plus chère qu’une cabine manuelle mais elle est aussi plus rapide et plus efficace