
Four Thermolaquage est un important équipement de revêtement en poudre. Pour cela, EMS Powder Coating Equipment propose une large gamme de services et de solutions aux clients de divers secteurs. Ce document présente un aperçu complet des services, de l’expertise technique et des engagements de Four Thermolaquage en matière de qualité et d’innovation.
Le four thermolaquage est un élément clé dans le processus de finition des pièces recouvertes de peinture en poudre, également connu sous le nom de revêtement en poudre. Une fois que la poudre est appliquée sur la surface de la pièce, elle doit être durcie par chauffage dans un four. Ce processus de durcissement est essentiel pour assurer l’adhésion de la peinture, sa résistance et ses propriétés esthétiques. Le four thermolaquage assure une polymérisation uniforme de la peinture en poudre, permettant à celle-ci de fondre, de se lier à la surface de la pièce et de durcir de manière stable.
Le fonctionnement du four thermolaquage repose sur l’application d’une chaleur contrôlée pour faire fondre la peinture en poudre appliquée sur les pièces. Cette chaleur permet à la poudre de se lier chimiquement avec la surface sous-jacente, formant ainsi une couche résistante. La température et le temps de cuisson sont cruciaux pour obtenir un revêtement homogène et de haute qualité. En général, la température du four varie entre 160 et 200°C, et les pièces doivent y rester pendant une durée suffisante pour garantir un durcissement complet, qui peut durer de 10 à 30 minutes, en fonction de la taille des pièces et du type de peinture utilisé.
Les fours thermolaquage sont souvent équipés de différents éléments pour garantir une distribution uniforme de la chaleur. Ces éléments incluent des résistances électriques, des générateurs de chaleur infrarouge ou des brûleurs à gaz. Le but est d’assurer une température stable tout au long du processus, sans variations qui pourraient affecter la qualité du revêtement.
Un des aspects importants du four thermolaquage est la gestion de la circulation de l’air. Les pièces doivent être exposées à une chaleur uniforme pour garantir que la poudre fond et durcit de manière homogène. De ce fait, les systèmes de ventilation sont essentiels pour la circulation de l’air chaud autour des pièces. Cette circulation permet de maintenir une température constante et d’éviter la formation de zones froides ou surchauffées qui pourraient compromettre la qualité du revêtement.
Les systèmes de contrôle jouent également un rôle crucial dans le four thermolaquage. Les appareils de mesure de température, souvent reliés à un système automatisé, permettent de surveiller et de réguler la température intérieure du four tout au long du processus de polymérisation. Ces systèmes de régulation permettent de s’assurer que les pièces reçoivent la chaleur nécessaire pendant le temps requis, ni plus, ni moins. L’objectif est d’éviter des surchauffes qui pourraient altérer le revêtement ou des températures trop basses qui pourraient ne pas permettre un durcissement complet.
Un autre aspect des fours thermolaquage modernes est leur efficacité énergétique. Pour réduire la consommation d’énergie et minimiser l’impact environnemental, certains fours sont équipés de technologies permettant de récupérer l’air chaud qui sort du four pour le réutiliser dans le processus. Cela permet d’optimiser l’utilisation de l’énergie et de réduire les coûts opérationnels à long terme.
Dans le cadre de la maintenance d’un four thermolaquage, il est essentiel de procéder à un entretien régulier pour garantir son bon fonctionnement et prolonger sa durée de vie. Cela inclut le nettoyage des éléments chauffants, la vérification des systèmes de ventilation, ainsi que l’inspection des commandes et des thermostats. Un entretien adéquat assure non seulement la performance optimale du four, mais aussi la qualité constante des revêtements réalisés.
Les fours thermolaquage sont adaptés à une variété d’industries, allant de la fabrication automobile à la production de meubles en métal, en passant par les équipements industriels. Leur capacité à produire des revêtements durables, résistants et esthétiques, associés à leur efficacité énergétique et à leur flexibilité, fait d’eux un choix privilégié pour les entreprises nécessitant des revêtements en poudre de haute qualité.
Four Thermolaquage
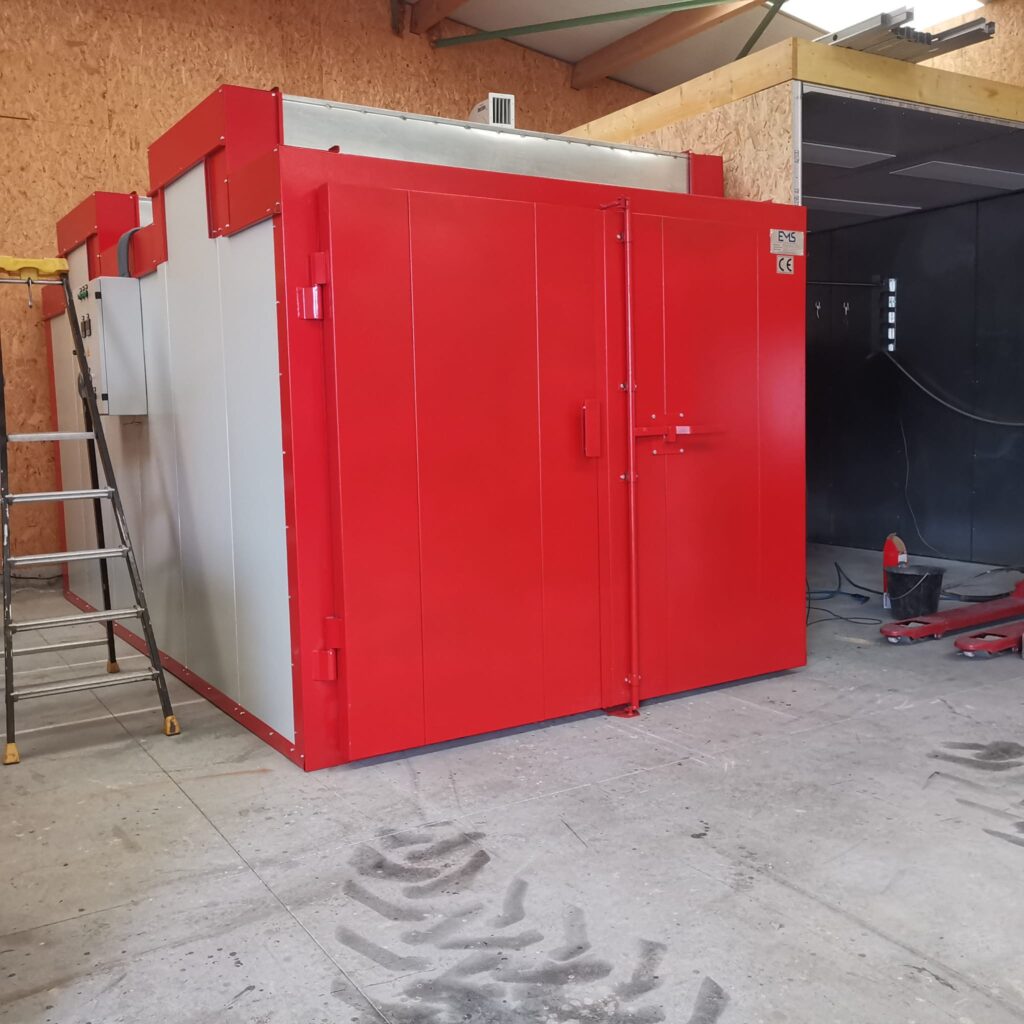
Le processus de thermolaquage, également connu sous le nom de revêtement en poudre, est une méthode de revêtement de surface largement utilisée dans diverses industries pour améliorer la durabilité et l’esthétique des produits métalliques. Au cœur de ce processus se trouve le “Four Thermolaquage”, un équipement essentiel qui joue un rôle clé dans la réussite de cette technique.
Le Four Thermolaquage est conçu pour catalyser le durcissement du revêtement en poudre appliqué sur la surface du matériau. Il se compose généralement d’une chambre de cuisson, d’un système de circulation d’air, d’un dispositif de contrôle de la température et d’une source de chaleur. La température de fonctionnement du four varie en fonction du type de poudre utilisé et des propriétés spécifiques du matériau à revêtir.
Le processus commence par l’application uniforme de la poudre sur la surface du matériau, généralement par pulvérisation électrostatique. La pièce préalablement revêtue est ensuite placée dans la chambre de cuisson du Four Thermolaquage. À mesure que la température augmente dans le four, la poudre fond et réagit chimiquement pour former un revêtement solide et résistant.
La qualité du processus dépend en grande partie de la précision du contrôle de la température et du temps de cuisson. Des paramètres incorrects peuvent entraîner des défauts tels que des bulles, des craquelures ou un manque d’adhérence du revêtement. C’est pourquoi les fours modernes sont équipés de systèmes avancés de régulation thermique et de contrôle, permettant une précision optimale pour garantir des résultats de revêtement de haute qualité.
Les Fours Thermolaquage sont utilisés dans une variété d’applications industrielles, de la fabrication de pièces automobiles à la production de mobilier métallique. Leur efficacité énergétique et leur capacité à produire des revêtements durables en font un choix populaire pour de nombreuses entreprises cherchant à améliorer la résistance à la corrosion et l’esthétique de leurs produits.
En conclusion, le Four Thermolaquage est un élément essentiel du processus de thermolaquage, offrant un contrôle précis de la température pour garantir la qualité et la durabilité des revêtements en poudre appliqués sur divers matériaux métalliques.
Thermolaquage
Le thermolaquage est un procédé de revêtement de surface largement utilisé dans l’industrie pour améliorer la résistance et l’esthétique des produits métalliques. Ce processus de finition implique l’application d’une couche de poudre thermoplastique sur une pièce, suivie de son durcissement à haute température. Le Four Thermolaquage joue un rôle central dans cette opération, offrant un environnement contrôlé pour garantir la réaction chimique adéquate.
La première étape du thermolaquage consiste à appliquer la poudre sur la surface de la pièce, souvent par pulvérisation électrostatique. Cette poudre est généralement constituée de résines thermodurcissables, de pigments, et d’additifs divers. Une fois appliquée, la pièce est transférée dans le Four Thermolaquage, où elle est soumise à des températures élevées.
À l’intérieur du four, la poudre fond, s’écoule, puis réagit chimiquement pour former un revêtement homogène, durable et esthétiquement plaisant. Le contrôle précis de la température dans le Four Thermolaquage est essentiel pour assurer une polymérisation optimale de la poudre, évitant ainsi des défauts tels que les bulles, les craquelures ou un manque d’adhérence.
Le thermolaquage présente de nombreux avantages, notamment une excellente résistance à la corrosion, aux rayures et aux produits chimiques. De plus, il offre une variété de finitions et de couleurs, répondant aux besoins esthétiques des applications industrielles et commerciales. Le processus respectueux de l’environnement, avec peu de déchets et de solvants, en fait également un choix durable.
En résumé, le thermolaquage, avec son processus intégrant le Four Thermolaquage, est une méthode de revêtement avancée, offrant des performances exceptionnelles, une durabilité accrue, et une esthétique personnalisée pour une gamme variée de produits métalliques.
Four de cuisson
Le “Four de cuisson” dans le contexte du thermolaquage est un élément essentiel du processus global, jouant un rôle central dans le durcissement du revêtement en poudre appliqué sur les surfaces métalliques. Cet équipement est conçu pour fournir un environnement contrôlé, garantissant des conditions thermiques optimales pour la réaction chimique de la poudre et assurant ainsi la formation d’un revêtement durable.
La chambre de cuisson du Four de cuisson est spécifiquement conçue pour résister à des températures élevées, souvent atteignant plusieurs centaines de degrés Celsius. La pièce préalablement revêtue est placée à l’intérieur, et le processus de durcissement commence lorsque la température augmente progressivement. Le contrôle précis de la température est crucial pour éviter tout défaut de revêtement et garantir des résultats uniformes.
Le Four de cuisson est équipé d’un système de circulation d’air qui assure une répartition homogène de la chaleur, contribuant ainsi à la cohérence du durcissement sur toute la surface de la pièce. Les systèmes modernes intègrent des dispositifs de contrôle sophistiqués qui permettent aux opérateurs de surveiller et d’ajuster en temps réel les paramètres de cuisson, assurant ainsi une précision maximale.
Les fours de cuisson sont disponibles dans différentes tailles et configurations pour s’adapter à diverses applications industrielles. Ils sont également dotés de fonctionnalités de sécurité pour garantir le bon déroulement du processus. En outre, la conception ergonomique de ces fours facilite le chargement et le déchargement des pièces, optimisant ainsi l’efficacité opérationnelle.
En conclusion, le “Four de cuisson” est un composant essentiel du processus de thermolaquage, fournissant les conditions thermiques nécessaires pour transformer la poudre en un revêtement durable et esthétiquement attrayant sur les surfaces métalliques. Son rôle central dans le processus en fait une pièce maîtresse de l’efficacité et de la qualité du thermolaquage.
Revêtement en poudre
Le “Revêtement en poudre” est la première étape cruciale du processus de thermolaquage, et il s’agit d’une méthode de finition de surface qui offre une protection durable et une esthétique améliorée aux produits métalliques. Ce processus implique l’application d’une fine couche de poudre sur la surface de la pièce, généralement par pulvérisation électrostatique.
La poudre utilisée pour le revêtement est constituée de particules fines comprenant des résines thermodurcissables, des pigments, et éventuellement des additifs spécifiques selon les propriétés recherchées. La technique de pulvérisation électrostatique assure une répartition uniforme de la poudre sur la pièce, créant ainsi un film homogène avant le passage au “Four de cuisson”.
Le choix de la poudre dépend de divers facteurs tels que les propriétés mécaniques requises, la résistance chimique, la couleur, et l’esthétique finale. Les applications du revêtement en poudre sont vastes, allant des composants automobiles aux meubles, en passant par les équipements industriels.
L’avantage majeur du revêtement en poudre est son adhérence exceptionnelle à la surface métallique, créant ainsi une barrière protectrice contre la corrosion, les rayures et les produits chimiques. De plus, le processus de revêtement en poudre génère peu de déchets, ce qui en fait une option respectueuse de l’environnement par rapport à d’autres méthodes de revêtement.
En résumé, le “Revêtement en poudre” constitue la première étape fondamentale du thermolaquage, offrant une solution de finition polyvalente, résistante et esthétiquement plaisante pour une variété d’applications industrielles et commerciales. Son application précise et son adhérence exceptionnelle posent les bases pour le succès du processus global de thermolaquage.
Durcissement thermique
Le “Durcissement thermique” est le processus clé qui se produit dans le “Four de cuisson” lors du thermolaquage, où la poudre appliquée sur la surface d’une pièce métallique subit des changements chimiques et physiques sous l’effet de la chaleur. Ce processus de durcissement thermique transforme la poudre fondue en un revêtement solide, résistant et durable.
Lorsque la pièce préalablement revêtue est placée dans le Four de cuisson, la température augmente progressivement. Cela déclenche la fusion de la poudre, suivie d’une réaction chimique de polymérisation. Ce processus crée des liaisons chimiques entre les molécules de la poudre, formant ainsi une structure tridimensionnelle solide qui adhère étroitement à la surface métallique.
La précision du contrôle de la température est essentielle pendant le durcissement thermique pour éviter des défauts potentiels tels que des bulles, des craquelures ou une adhérence insuffisante du revêtement. Les températures utilisées dépendent du type de poudre utilisé et des propriétés du matériau de base, nécessitant souvent une combinaison de températures élevées et de temps de traitement spécifiques.
Le résultat du durcissement thermique est un revêtement en poudre qui offre une excellente résistance à la corrosion, aux rayures et aux produits chimiques. Cette méthode confère également une finition esthétiquement attrayante et uniforme. L’intégration d’une technologie de durcissement thermique avancée dans le processus global de thermolaquage contribue à garantir des performances optimales du revêtement final.
En résumé, le “Durcissement thermique” est une étape critique du thermolaquage, où la poudre appliquée subit une transformation chimique sous l’effet de la chaleur dans le Four de cuisson. Ce processus joue un rôle fondamental dans la création d’un revêtement solide, durable et esthétiquement satisfaisant sur les surfaces métalliques.
Peinture électrostatique
La “Peinture électrostatique” est une technique essentielle dans le processus de thermolaquage, utilisée pour appliquer la poudre de revêtement de manière uniforme sur la surface d’une pièce métallique. Cette méthode de pulvérisation électrostatique assure une répartition précise de la poudre, favorisant une adhérence maximale et contribuant ainsi à la qualité du revêtement final.
Dans la peinture électrostatique, la poudre est chargée électriquement avant d’être pulvérisée sur la pièce. La pièce métallique, quant à elle, est mise à la terre. En raison de la charge électrique, la poudre est attirée magnétiquement vers la surface de la pièce, assurant ainsi une couverture uniforme même sur des formes complexes ou des zones difficiles d’accès.
Cette technique présente plusieurs avantages, dont une utilisation efficace de la poudre avec moins de pertes, une réduction des retouches nécessaires, et une meilleure adhérence. De plus, elle permet d’obtenir des finitions plus homogènes, contribuant ainsi à la qualité esthétique du produit final.
La peinture électrostatique est particulièrement adaptée au processus de thermolaquage, où la précision de l’application de la poudre est cruciale pour garantir la réussite du revêtement. Elle est largement utilisée dans diverses industries, allant de la fabrication de pièces automobiles à la production de mobilier métallique, en raison de ses avantages en termes de qualité, d’efficacité et d’esthétique.
En résumé, la “Peinture électrostatique” constitue une étape clé du thermolaquage, assurant une application précise et uniforme de la poudre de revêtement sur la surface des pièces métalliques. Son utilisation efficace contribue à la qualité globale du revêtement, tant du point de vue technique qu’esthétique.
Régulation de température
La “Régulation de température” joue un rôle essentiel dans le processus de thermolaquage, en particulier dans le “Four de cuisson”. Ce processus nécessite un contrôle précis de la température pour garantir une polymérisation optimale de la poudre, assurant ainsi la formation d’un revêtement en poudre durable et esthétiquement satisfaisant sur les surfaces métalliques.
Les fours modernes de thermolaquage sont équipés de systèmes avancés de régulation de température qui permettent aux opérateurs de surveiller et d’ajuster les paramètres thermiques en temps réel. Ces systèmes assurent une distribution uniforme de la chaleur dans la chambre de cuisson, minimisant les variations de température et évitant ainsi les défauts potentiels du revêtement.
La température de cuisson dépend du type de poudre utilisé et des propriétés du matériau à revêtir. Un contrôle précis est crucial pour éviter des problèmes tels que la formation de bulles, les craquelures, ou une adhérence insuffisante du revêtement. Les systèmes de régulation modernes intègrent des capteurs sophistiqués et des algorithmes de contrôle pour maintenir des conditions optimales.
Un aspect important de la régulation de température est la capacité d’adapter les paramètres en fonction de la géométrie et de la taille des pièces à traiter. Cela garantit une consistance dans la qualité du revêtement, indépendamment des variations dans la production.
En résumé, la “Régulation de température” dans le contexte du thermolaquage, et en particulier dans le “Four de cuisson”, est cruciale pour garantir la réussite du processus en créant des conditions thermiques optimales. Les systèmes modernes offrent un contrôle précis, contribuant ainsi à la qualité et à la cohérence des revêtements en poudre appliqués sur les surfaces métalliques.
Adhérence du revêtement
L'”Adhérence du revêtement” est un aspect critique du processus de thermolaquage, déterminant la capacité du revêtement en poudre à se lier de manière stable à la surface métallique. Une adhérence adéquate est essentielle pour assurer la durabilité et l’efficacité du revêtement, résistant ainsi aux conditions environnementales, aux rayures et aux manipulations ultérieures.
La qualité de l’adhérence dépend de plusieurs facteurs, dont la préparation de la surface avant l’application du revêtement, la composition de la poudre, et surtout, du processus de durcissement thermique dans le “Four de cuisson”. Un contrôle précis de la température et du temps de cuisson est nécessaire pour permettre une liaison chimique optimale entre la poudre et la surface métallique.
Des paramètres incorrects ou des défauts dans le processus peuvent entraîner une adhérence insuffisante, conduisant à des problèmes tels que l’écaillage du revêtement, la corrosion prématurée ou une dégradation de l’aspect esthétique. Les systèmes modernes de thermolaquage intègrent des techniques avancées pour évaluer et garantir l’adhérence du revêtement, minimisant ainsi les risques de défaillance.
La préparation de la surface avant l’application du revêtement joue également un rôle crucial dans l’assurance de l’adhérence. Elle implique souvent des étapes de nettoyage, de dégraissage et de traitement de la surface métallique pour éliminer les contaminants et assurer une adhérence maximale.
En résumé, l'”Adhérence du revêtement” est un élément vital du processus de thermolaquage, garantissant que le revêtement en poudre forme une liaison durable avec la surface métallique. Un contrôle précis du processus de durcissement thermique et une préparation adéquate de la surface contribuent à assurer une adhérence optimale, fournissant ainsi des résultats de revêtement fiables et durables.
Procédé de polymérisation
Le “Procédé de polymérisation” est une étape fondamentale du thermolaquage, intervenant lors du durcissement thermique dans le “Four de cuisson”. C’est au cours de cette phase que la poudre de revêtement, préalablement appliquée sur la surface métallique, subit des transformations chimiques spécifiques, formant ainsi un réseau polymérique tridimensionnel.
La polymérisation est le processus par lequel les molécules de la poudre réagissent entre elles pour former des liaisons chimiques fortes, créant ainsi une structure solide et résistante. La température élevée dans le four déclenche cette réaction, assurant une fusion complète de la poudre et favorisant la création d’un revêtement homogène.
La réussite du procédé de polymérisation dépend de la précision du contrôle de la température et du temps de cuisson dans le four. Des conditions thermiques inappropriées peuvent entraîner des défauts tels que des bulles, des craquelures ou une adhérence insuffisante du revêtement. Les avancées technologiques dans les systèmes de régulation de température permettent d’optimiser ce processus, garantissant ainsi des résultats de polymérisation cohérents.
Le revêtement résultant de la polymérisation offre des propriétés exceptionnelles, notamment une résistance accrue à la corrosion, aux chocs, et aux produits chimiques. Cette transformation chimique confère également au revêtement une durabilité supérieure, en faisant une solution idéale pour la protection des surfaces métalliques dans diverses applications industrielles et commerciales.
En résumé, le “Procédé de polymérisation” est une phase cruciale du thermolaquage, se produisant pendant le durcissement thermique dans le “Four de cuisson”. Cette réaction chimique crée un réseau polymérique solide, conférant au revêtement en poudre des propriétés exceptionnelles de durabilité et de résistance.
Chambre de cuisson
La “Chambre de cuisson” est une composante essentielle du “Four Thermolaquage” utilisé dans le processus de thermolaquage. Cette chambre constitue l’environnement contrôlé où la réaction chimique de durcissement thermique se produit, transformant la poudre de revêtement appliquée sur la surface métallique en un revêtement solide, durable et esthétiquement attrayant.
La conception de la chambre de cuisson est cruciale pour assurer une distribution uniforme de la chaleur sur la pièce, évitant ainsi les variations de température qui pourraient entraîner des défauts dans le revêtement final. Elle doit également permettre un accès facile pour le chargement et le déchargement des pièces, tout en maintenant des conditions thermiques stables.
Les matériaux utilisés pour construire la chambre de cuisson doivent résister aux températures élevées nécessaires au durcissement thermique. Ces matériaux sont souvent choisis pour leur conductivité thermique, leur durabilité et leur capacité à maintenir une température constante sur toute la surface de la pièce.
La “Chambre de cuisson” dans un “Four Thermolaquage” est généralement équipée d’un système de circulation d’air pour assurer une répartition homogène de la chaleur. Des avancées technologiques dans la conception de ces chambres permettent un contrôle précis de la température, garantissant ainsi des résultats cohérents et de haute qualité pour les revêtements en poudre.
En résumé, la “Chambre de cuisson” est un élément crucial du processus de thermolaquage, fournissant un environnement contrôlé où la réaction chimique de durcissement thermique se produit. La conception soigneuse de cette chambre est essentielle pour garantir des conditions thermiques optimales et une distribution uniforme de la chaleur, contribuant ainsi à la qualité du revêtement final.
Qualité du revêtement
La “Qualité du revêtement” est l’aspect ultime du processus de thermolaquage, représentant la mesure dans laquelle le revêtement en poudre appliqué sur la surface métallique atteint les normes requises en termes d’adhérence, de durabilité, d’esthétique et de résistance. La réalisation d’une haute qualité de revêtement dépend de la maîtrise de chaque étape du processus, en mettant l’accent sur des aspects tels que la préparation de surface, l’application de la poudre, et le durcissement thermique.
La “Qualité du revêtement” est étroitement liée à l’adhérence, à la résistance à la corrosion, à l’uniformité de la couleur et de la texture, ainsi qu’à la résistance mécanique du revêtement final. Des contrôles stricts et des normes de qualité sont généralement établis pour s’assurer que chaque pièce traitée répond aux exigences spécifiées.
La préparation minutieuse de la surface avant l’application du revêtement est une première étape cruciale pour garantir une qualité optimale. Un nettoyage approfondi, le dégraissage, et d’autres techniques peuvent être utilisés pour éliminer les contaminants qui pourraient compromettre l’adhérence du revêtement.
L’utilisation de la “Peinture électrostatique” pour appliquer la poudre contribue également à la qualité du revêtement en assurant une répartition uniforme sur la surface de la pièce, même dans les zones difficiles d’accès. La régulation précise de la température pendant le durcissement thermique est tout aussi cruciale pour éviter les défauts qui pourraient compromettre la qualité du revêtement.
En résumé, la “Qualité du revêtement” est l’objectif ultime du processus de thermolaquage. Il résulte de la combinaison harmonieuse de chaque étape, de la préparation de la surface à l’application de la poudre, en passant par le durcissement thermique. Un contrôle rigoureux à chaque étape garantit des revêtements en poudre de haute qualité, durables et esthétiquement satisfaisants sur une variété de surfaces métalliques.
Expertise technique inégalée:
Four Thermolaquage détient un savoir-faire et une expérience inégalés dans le domaine du thermolaquage. L’entreprise utilise des technologies de pointe pour garantir une application précise et uniforme des poudres de différentes compositions et couleurs. Son équipe technique composée d’ingénieurs et de techniciens expérimentés assure un contrôle qualité rigoureux à chaque étape du processus, garantissant ainsi la durabilité et l’esthétique des revêtements.
Services complets répondant à tous vos besoins:
Four Thermolaquage propose une gamme complète de services allant du prétraitement à la finition, répondant à tous les besoins des clients :
- Prétraitement de surface: Dégraissage, phosphatation, sablage, etc., pour une adhérence optimale du revêtement.
- Application de poudre: Utilisation de cabines automatisées et manuelles pour une application précise et uniforme.
- Cuisson au four: Fours de dernière génération assurant une polymérisation parfaite de la poudre, offrant une résistance et une longévité accrues.
- Contrôle qualité: Contrôles visuels et dimensionnels stricts pour garantir la conformité aux spécifications strictes.
- Finitions spéciales: Texturées, antidérapantes, brillantes, mates, etc., pour répondre aux exigences esthétiques et fonctionnelles spécifiques.
Four Thermolaquage : Un leader dans le domaine du revêtement par poudre
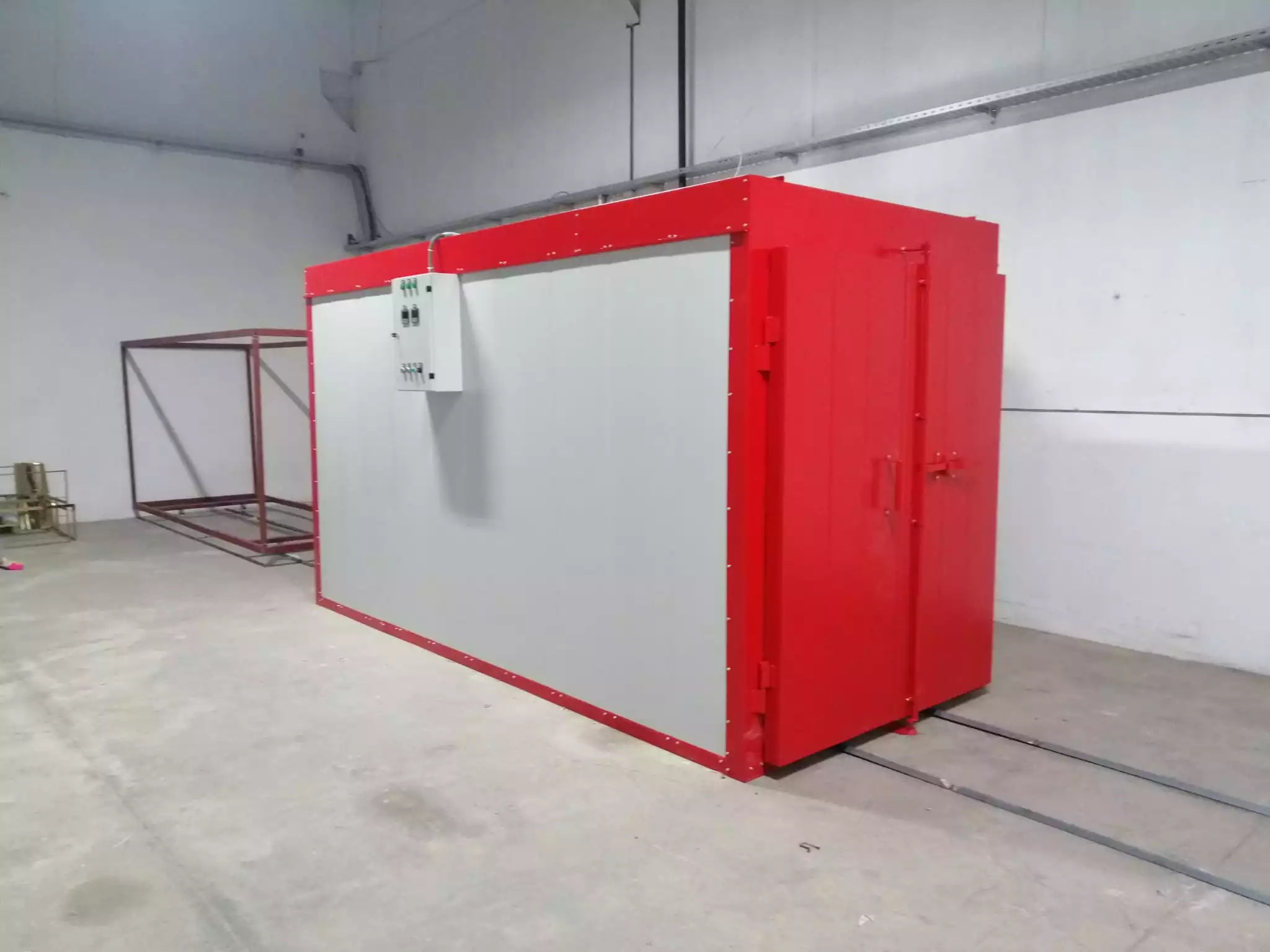
Four Thermolaquage s’engage à fournir des revêtements de la plus haute qualité à ses clients. L’entreprise investit constamment dans la recherche et le développement pour améliorer ses processus et proposer des solutions innovantes. En outre, elle respecte scrupuleusement les normes environnementales les plus strictes, en utilisant des poudres sans solvants et en mettant en œuvre des systèmes de gestion des déchets efficaces.
Avantages pour les clients:
En choisissant Four Thermolaquage, vous bénéficiez de plusieurs avantages :
- Revêtements durables et résistants : Protection contre la corrosion, les UV, les produits chimiques et les rayures.
- Esthétique soignée : Large choix de couleurs et de finitions pour répondre à vos goûts.
- Respect de l’environnement : Utilisation de technologies et de produits respectueux de l’environnement.
- Expertise et conseils techniques : Assistance personnalisée pour répondre à vos questions et vos besoins spécifiques.
- Délais de production respectés : Engagement à livrer vos projets dans les délais impartis.
Four Thermolaquage est le partenaire idéal pour tous vos besoins en matière de revêtement par poudre. Son expertise technique, sa large gamme de services, son engagement envers la qualité et l’innovation en font un leader incontournable dans son domaine.
N’hésitez pas à contacter Four Thermolaquage pour discuter de vos projets et obtenir un devis gratuit !
Remarque: Ce document constitue une base pour votre texte. Vous pouvez l’enrichir en ajoutant des informations spécifiques sur les services proposés par Four Thermolaquage en Turquie, des exemples de réalisations, des certifications obtenues, etc. En fonction de votre cible et de l’espace disponible, vous pouvez également inclure des photos, des graphiques ou des tableaux pour illustrer vos propos.
- Haute qualité (Haute qualité) : Souligne l’engagement de Four Thermolaquage envers des revêtements durables et performants.
- Expertise technique (Expertise technique) : Met en avant le savoir-faire et l’expérience de l’entreprise dans le domaine du thermolaquage.
- Large gamme de services (Large gamme de services) : Indique la capacité de Four Thermolaquage à répondre à des besoins variés grâce à son offre complète.
- Innovation (Innovation) : Fait référence à l’investissement continu de l’entreprise dans la recherche et le développement de nouvelles solutions.
- Respect de l’environnement (Respect de l’environnement) : Met en valeur l’utilisation de technologies et produits écologiques par Four Thermolaquage.
- Délais respectés (Délais respectés) : Assure les clients de la fiabilité et du professionnalisme de l’entreprise en matière de gestion des délais.
- Solutions sur mesure (Solutions sur mesure) : Souligne la capacité de Four Thermolaquage à adapter ses services aux besoins spécifiques de chaque client.
- Finitions esthétiques (Finitions esthétiques) : Met en avant le large choix de couleurs et de textures disponibles pour répondre aux exigences esthétiques des clients.
- Partenaire de confiance (Partenaire de confiance) : Positionne Four Thermolaquage comme un acteur fiable et solide dans le secteur du thermolaquage.
- Technologie de pointe (Technologie de pointe) : Fait référence à l’utilisation d’équipements et de procédés modernes par Four Thermolaquage.
Haute Qualité : L’Engagement de Four Thermolaquage pour des Revêtements Durables et Performants
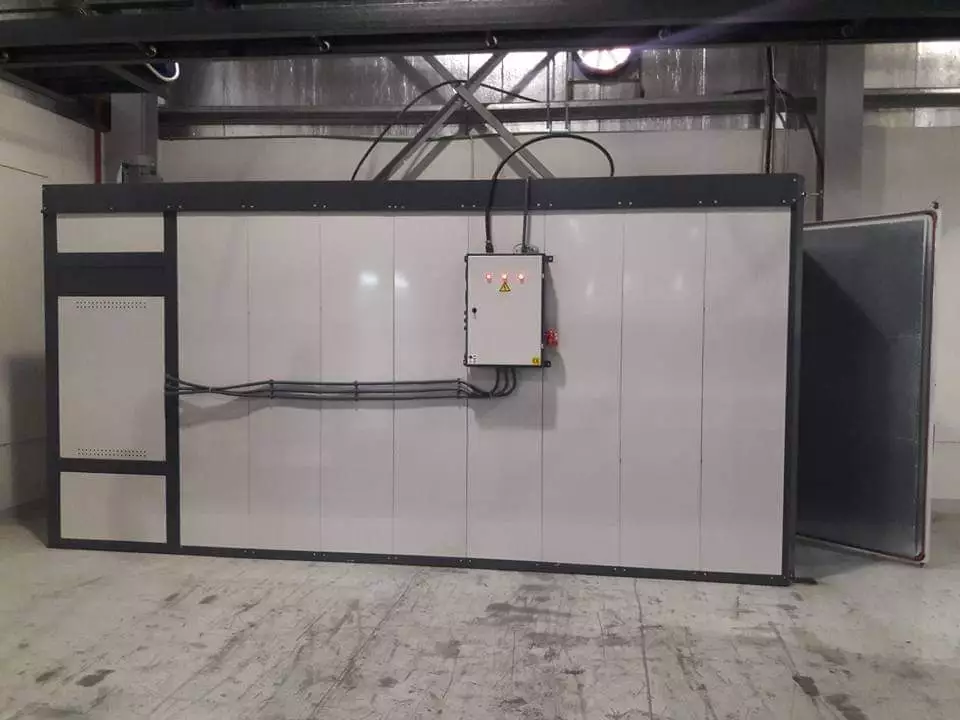
Four Thermolaquage place la haute qualité au cœur de sa philosophie d’entreprise. Cet engagement se traduit par une multitude de pratiques et de contrôles rigoureux à chaque étape du processus de thermolaquage, garantissant des revêtements durables, résistants et esthétiques pour tous types de pièces et d’applications.
Techniques de pointe pour une application optimale:
- Utilisation de poudres thermodurcissantes de première qualité, sélectionnées pour leurs performances en termes de résistance à la corrosion, aux UV, aux produits chimiques et aux rayures.
- Cabines automatisées et manuelles équipées de technologies avancées pour une application uniforme et précise de la poudre, évitant les défauts de surface et garantissant une épaisseur de couche régulière.
- Contrôle numérique des paramètres de cuisson permettant une polymérisation parfaite de la poudre, optimisant la dureté, l’adhérence et la longévité du revêtement.
Contrôle qualité rigoureux pour des résultats irréprochables:
- Inspection visuelle minutieuse après chaque étape du processus pour détecter et corriger immédiatement tout défaut potentiel.
- Mesures dimensionnelles précises pour garantir le respect des spécifications techniques des pièces.
- Tests de résistance effectués en laboratoire selon des normes internationales strictes, évaluant la durabilité et les performances du revêtement dans des conditions extrêmes.
Engagement continu pour l’amélioration:
- Investissement constant dans la recherche et le développement de nouvelles technologies et techniques de thermolaquage.
- Formation continue des équipes pour garantir leur expertise et leur maîtrise des processus les plus récents.
- Mise en place de systèmes de management de la qualité certifiés conformes aux normes ISO.
Avantages pour les clients:
- Revêtements durables et résistants qui conservent leur aspect et leurs performances au fil du temps.
- Protection optimale contre les agressions extérieures, allongeant la durée de vie des pièces.
- Finitions impeccables et conformes aux exigences esthétiques les plus strictes.
- Tranquillité d’esprit grâce à la garantie de qualité offerte par Four Thermolaquage.
En choisissant Four Thermolaquage, vous optez pour un partenaire engagé à vous fournir des revêtements de la plus haute qualité, répondant à vos besoins les plus exigeants.
N’hésitez pas à contacter Four Thermolaquage pour en savoir plus sur leurs engagements en matière de qualité et discuter de vos projets spécifiques.
Expertise Technique : Le Savoir-Faire et l’Expérience de Four Thermolaquage
L’expertise technique est un pilier fondamental de Four Thermolaquage. L’entreprise détient un savoir-faire inégalé dans le domaine du thermolaquage, acquis grâce à de nombreuses années d’expérience et à un investissement continu dans la formation et la recherche. Cette expertise se traduit par :
Une maîtrise parfaite des procédés de thermolaquage:
- Connaissance approfondie des différents types de poudres et de leurs propriétés spécifiques.
- Expertise dans la sélection des paramètres de prétraitement, d’application et de cuisson adaptés à chaque type de pièce et de matériau.
- Capacité à réaliser des finitions complexes et exigeantes, répondant aux besoins techniques et esthétiques les plus pointus.
Une équipe technique hautement qualifiée:
- Ingénieurs et techniciens expérimentés disposant d’une solide formation théorique et pratique.
- Maîtrise des outils et des technologies de pointe utilisées dans le processus de thermolaquage.
- Capacité à résoudre les problèmes techniques complexes et à proposer des solutions innovantes aux clients.
Un engagement continu dans la formation et la recherche:
- Participation à des formations et des conférences pour rester à la pointe des dernières technologies et innovations du secteur.
- Collaboration avec des universités et des centres de recherche pour développer de nouveaux procédés et matériaux de thermolaquage.
- Mise en place de programmes de formation interne pour transmettre le savoir-faire et l’expérience aux nouvelles générations de techniciens.
Avantages pour les clients:
- Revêtements fiables et performants, répondant aux exigences techniques les plus strictes.
- Solutions techniques sur mesure adaptées à chaque projet spécifique.
- Conseils d’experts pour optimiser le choix des matériaux et des procédés de thermolaquage.
- Tranquillité d’esprit grâce à la garantie d’un travail réalisé par des professionnels hautement qualifiés.
Four Thermolaquage se positionne comme un leader dans le domaine du thermolaquage grâce à son expertise technique de pointe.
N’hésitez pas à contacter Four Thermolaquage pour discuter de vos projets et bénéficier de leur expertise technique reconnue.
Innovation : Four Thermolaquage à la pointe des technologies du thermolaquage
L’innovation est un moteur clé de Four Thermolaquage. L’entreprise s’engage continuellement à développer de nouvelles technologies et solutions pour améliorer ses processus, proposer des revêtements toujours plus performants et répondre aux besoins évolutifs de ses clients.
Investissement constant dans la recherche et le développement:
- Une équipe dédiée à la recherche et au développement travaille sur des projets innovants visant à améliorer l’efficacité, la durabilité et les performances des revêtements par poudre.
- Collaboration avec des fournisseurs et des universités pour explorer de nouvelles technologies et matériaux.
- Participation à des programmes de financement et de subventions pour soutenir ses activités de recherche et développement.
Exemples d’innovations développées par Four Thermolaquage:
- Utilisation de poudres thermodurcissantes écologiques et biodégradables.
- Mise en place de systèmes de récupération de chaleur pour réduire la consommation d’énergie.
- Développement de procédés de thermolaquage à basse température pour une meilleure efficacité énergétique et une réduction des émissions de CO2.
- Création de revêtements fonctionnels dotés de propriétés antibactériennes, autonettoyantes ou anti-corrosion.
- Utilisation de technologies numériques pour la surveillance et le contrôle en temps réel du processus de thermolaquage.
Avantages pour les clients:
- Accès à des revêtements de pointe offrant des performances accrues et des fonctionnalités innovantes.
- Respect de l’environnement grâce à l’utilisation de technologies écologiques et durables.
- Réduction des coûts grâce à une meilleure efficacité énergétique et une optimisation des processus.
- Image de marque valorisée en choisissant un partenaire engagé dans l’innovation.
En choisissant Four Thermolaquage, vous êtes assuré de bénéficier des dernières innovations du secteur du thermolaquage et de solutions sur mesure adaptées à vos besoins les plus spécifiques.
N’hésitez pas à contacter Four Thermolaquage pour en savoir plus sur leurs innovations et découvrir comment elles peuvent répondre à vos exigences.
Respect de l’environnement : L’engagement éco-responsable de Four Thermolaquage
Respect de l’environnement est une valeur fondamentale de Four Thermolaquage. L’entreprise s’engage à minimiser son impact sur l’environnement tout au long du processus de thermolaquage, en adoptant des pratiques et des technologies éco-responsables.
Engagement sur tous les fronts:
- Sélection de poudres thermodurcissantes: Utilisation de poudres sans solvants, sans composés organiques volatils (COV) et à base de résines écologiques et biodégradables.
- Processus de prétraitement optimisé: Minimisation de la consommation d’eau et d’énergie grâce à des techniques de nettoyage avancées et à des produits chimiques respectueux de l’environnement.
- Systèmes de filtration performants: Capture et traitement efficaces des émissions de poussière et de composés organiques volatils pour garantir la qualité de l’air et protéger la santé des employés et de l’environnement.
- Gestion responsable des déchets: Recyclage ou valorisation des déchets générés lors du processus de thermolaquage, réduisant leur impact sur les décharges et l’environnement.
- Optimisation énergétique: Utilisation d’équipements à faible consommation énergétique et mise en place de systèmes de récupération de chaleur pour réduire l’empreinte carbone de l’entreprise.
Certifications et labels environnementaux:
Four Thermolaquage est certifié selon des normes environnementales strictes telles que l’ISO 14001 et possède des labels environnementaux reconnus pour ses pratiques éco-responsables.
Avantages pour les clients:
- Contribution à la protection de l’environnement en choisissant un partenaire éco-responsable.
- Respect des réglementations environnementales de plus en plus strictes.
- Image de marque positive associée à des pratiques durables.
- Réduction des coûts grâce à une meilleure efficacité énergétique et une gestion responsable des déchets.
Four Thermolaquage démontre son engagement concret pour le développement durable en proposant des solutions de thermolaquage respectueuses de l’environnement, sans compromis sur la qualité et la performance.
N’hésitez pas à contacter Four Thermolaquage pour en savoir plus sur leurs initiatives éco-responsables et découvrir comment elles s’alignent avec vos valeurs environnementales.
J’espère que ce texte technique répond à vos attentes. N’hésitez pas à me donner d’autres numéros de mots-clés pour que je puisse vous fournir des textes similaires.
La peinture en poudre est une méthode de revêtement de surface qui utilise de la poudre sèche au lieu de peinture liquide. Ce procédé est devenu très populaire dans l’industrie en raison de ses nombreux avantages par rapport aux méthodes de peinture traditionnelles. L’équipement de poudrage joue un rôle crucial dans l’application de ce type de revêtement.
Avantages du Revêtement en Poudre
- Durabilité et résistance : Le revêtement en poudre offre une finition robuste et durable qui résiste aux égratignures, à l’usure et aux conditions climatiques difficiles.
- Écologique : Contrairement aux peintures liquides, le revêtement en poudre ne contient pas de solvants ni de composés organiques volatils (COV), ce qui en fait une option respectueuse de l’environnement.
- Coût-Efficacité : Bien que l’investissement initial dans l’équipement puisse être élevé, les économies réalisées sur le long terme grâce à la réduction des déchets et à l’efficacité du processus compensent largement ce coût.
Applications Industrielles
Le revêtement en poudre est largement utilisé dans diverses industries, notamment l’automobile, l’électronique, les appareils électroménagers, et les équipements extérieurs. Ce procédé assure non seulement une finition esthétique, mais aussi une protection contre la corrosion et d’autres formes de dégradation.
Fours de polymérisation
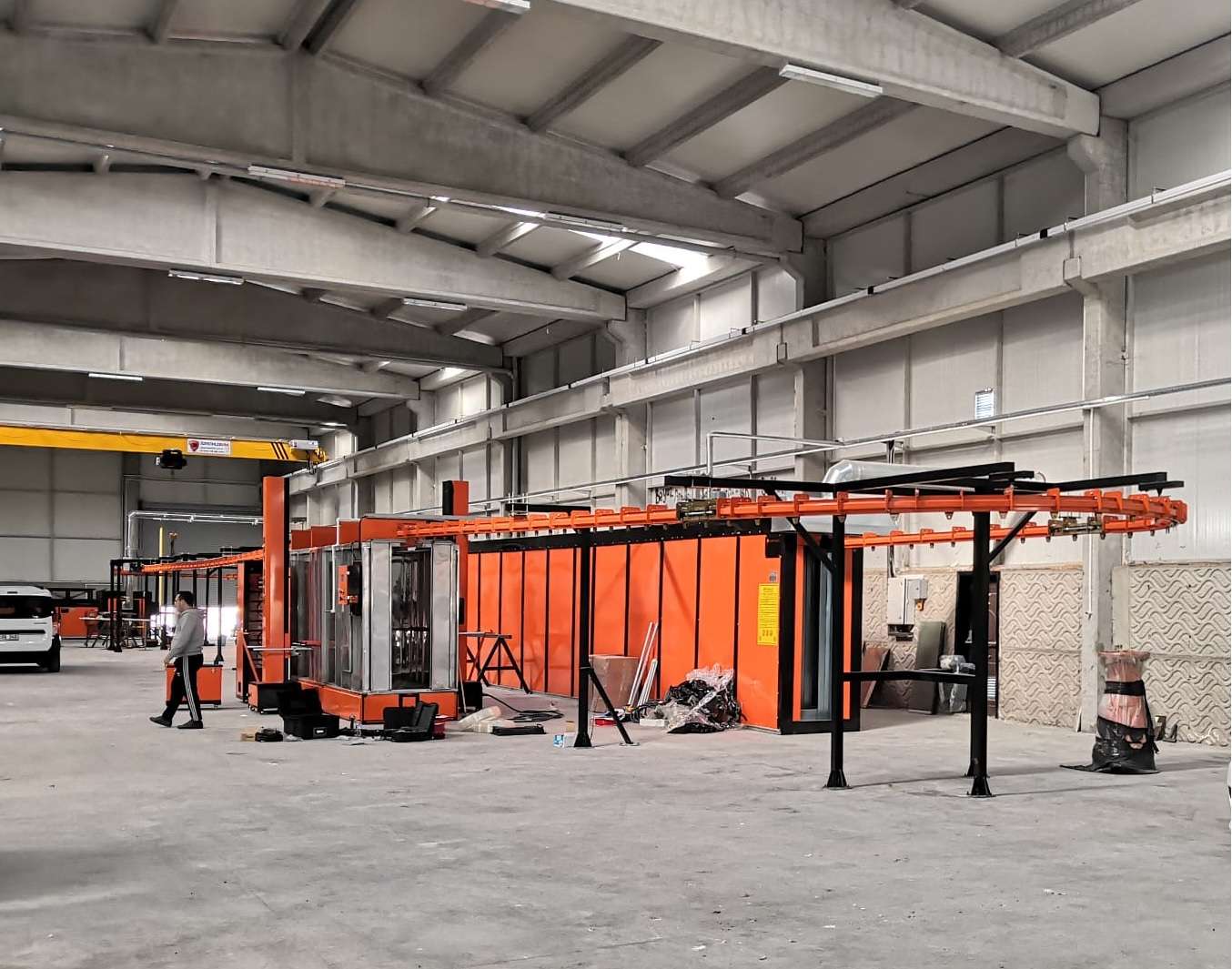
Les fours de polymérisation jouent un rôle essentiel dans le processus de revêtement en poudre, car ils permettent de chauffer la poudre appliquée pour qu’elle fonde et forme un film homogène et dur sur la surface de l’objet. Il existe plusieurs types de fours utilisés en fonction des besoins spécifiques de l’application.
Types de Fours
- Fours à convection : Ils utilisent l’air chaud pour transférer la chaleur à la pièce. Ces fours sont idéaux pour des charges lourdes et volumineuses.
- Fours infrarouges : Ils utilisent le rayonnement infrarouge pour chauffer directement la poudre, offrant un temps de polymérisation plus rapide.
- Fours à induction : Utilisés pour des applications spécifiques nécessitant un chauffage rapide et précis.
Caractéristiques Clés
Lors de la sélection d’un four de polymérisation, plusieurs caractéristiques doivent être prises en compte :
- Capacité de température : Doit correspondre aux exigences du type de poudre utilisée.
- Uniformité de la chaleur : Assure une répartition uniforme de la chaleur pour une finition uniforme.
- Efficacité énergétique : Les modèles économes en énergie permettent de réduire les coûts opérationnels.
Cabines de poudrage
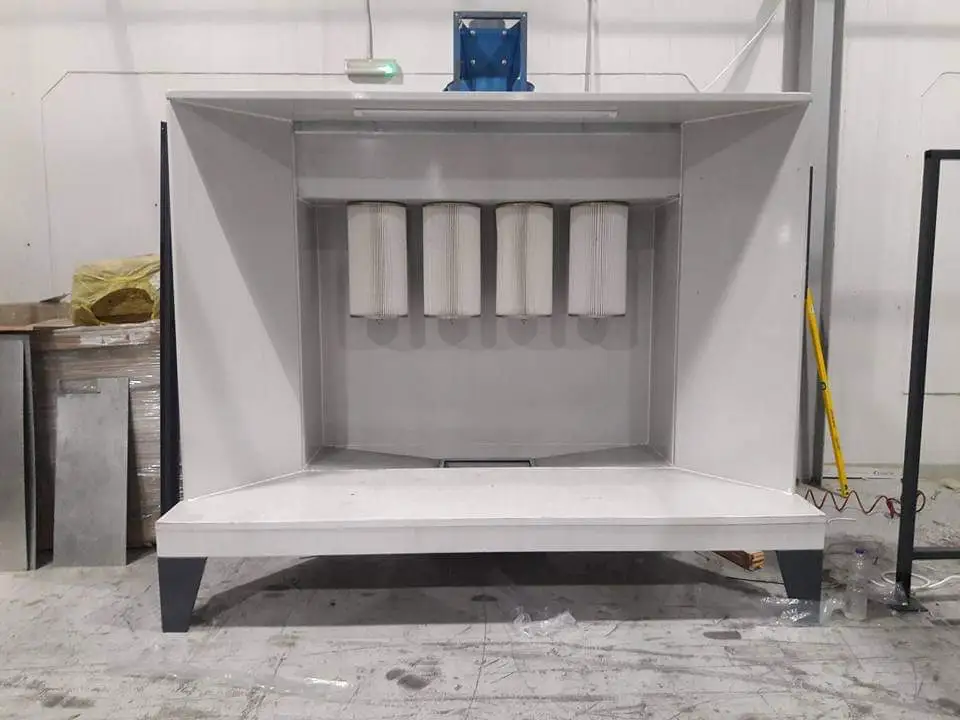
Les cabines de poudrage sont des environnements contrôlés où la poudre est appliquée sur les pièces. Elles sont conçues pour assurer une application efficace et sûre, tout en minimisant la contamination.
Conception et Structure
- Cabines ouvertes : Idéales pour les petites pièces et une production à petite échelle.
- Cabines fermées : Conviennent aux grandes pièces et à la production en série.
- Systèmes de récupération de poudre : Intégrés pour récupérer et réutiliser l’excès de poudre.
Importance de la Ventilation et de la Sécurité
Une ventilation adéquate est cruciale pour éviter l’accumulation de particules de poudre, réduisant ainsi les risques d’incendie et d’explosion. De plus, les cabines doivent être équipées de systèmes de filtration pour protéger les travailleurs contre l’inhalation de poudre.
Pistolets de pulvérisation
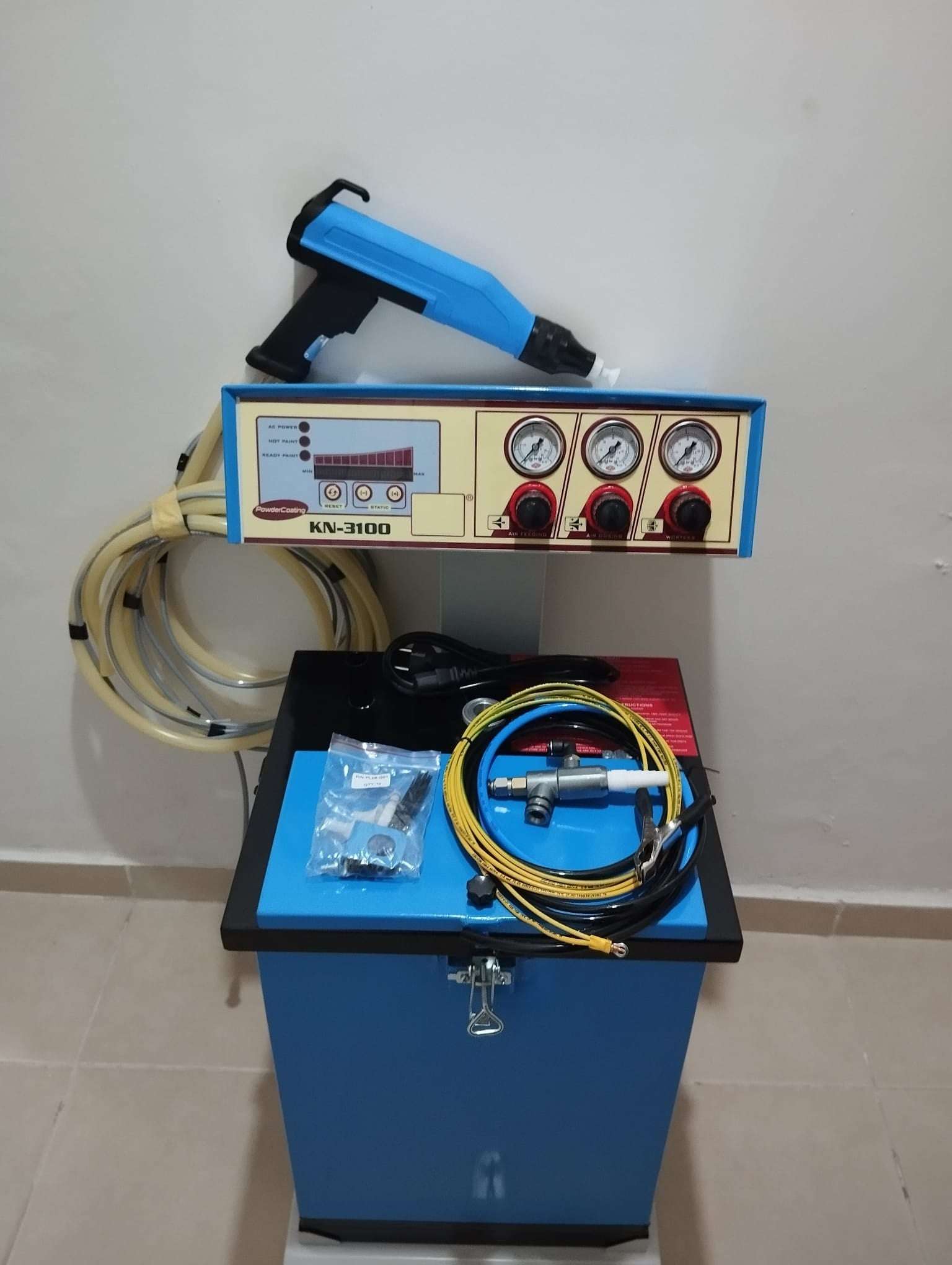
Les pistolets de pulvérisation de poudre sont des dispositifs utilisés pour appliquer la poudre sur la surface de l’objet. Ils utilisent un champ électrostatique pour attirer la poudre vers la pièce, assurant une couverture uniforme.
Types de Pistolets de Pulvérisation
- Pistolets à corona : Utilisent une charge électrique pour ioniser la poudre.
- Pistolets tribo : La poudre est chargée par friction, idéale pour les surfaces complexes.
Fonctionnement et Avantages
Les pistolets de pulvérisation sont appréciés pour leur capacité à appliquer la poudre de manière uniforme et efficace. Leur utilisation réduit le gaspillage de poudre et offre une finition de haute qualité.
Maintien de l’équipement de poudrage
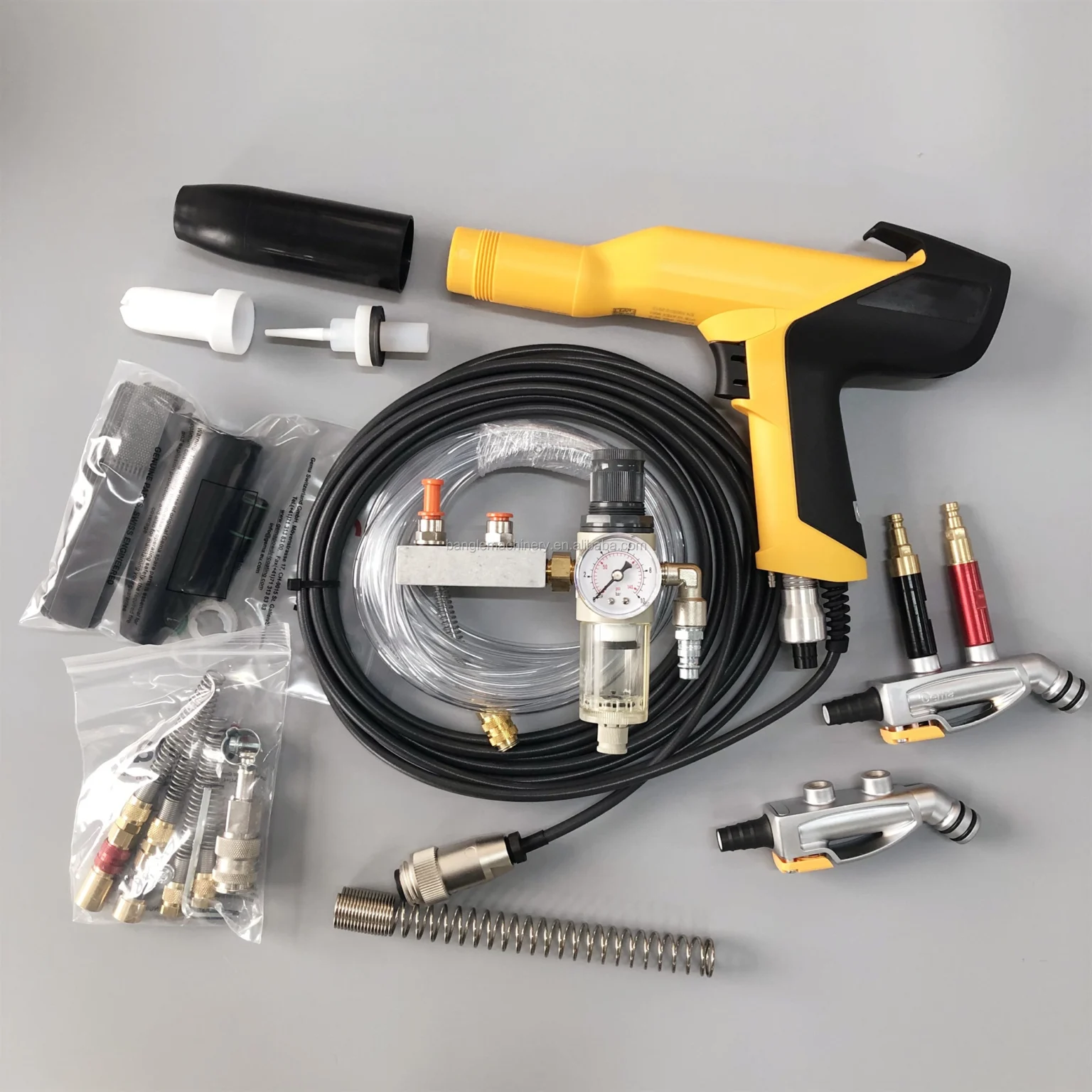
Le maintien de l’équipement de poudrage en bon état de fonctionnement est essentiel pour garantir une production continue et de haute qualité. Avoir des pièces de rechange à portée de main est crucial pour minimiser les temps d’arrêt.
Importance des Pièces de Rechange
Les pièces de rechange assurent la continuité des opérations en cas de défaillance de l’équipement. Cela inclut les filtres, les buses de pistolet, et les éléments chauffants.
Conseils d’Entretien
- Inspection régulière : Vérifiez les pièces pour détecter tout signe d’usure ou de dommage.
- Nettoyage : Maintenez les cabines et les pistolets propres pour éviter la contamination croisée.
- Formation du personnel : Assurez-vous que les opérateurs sont formés pour identifier et résoudre les problèmes potentiels.
Conseils d’entretien d’équipement
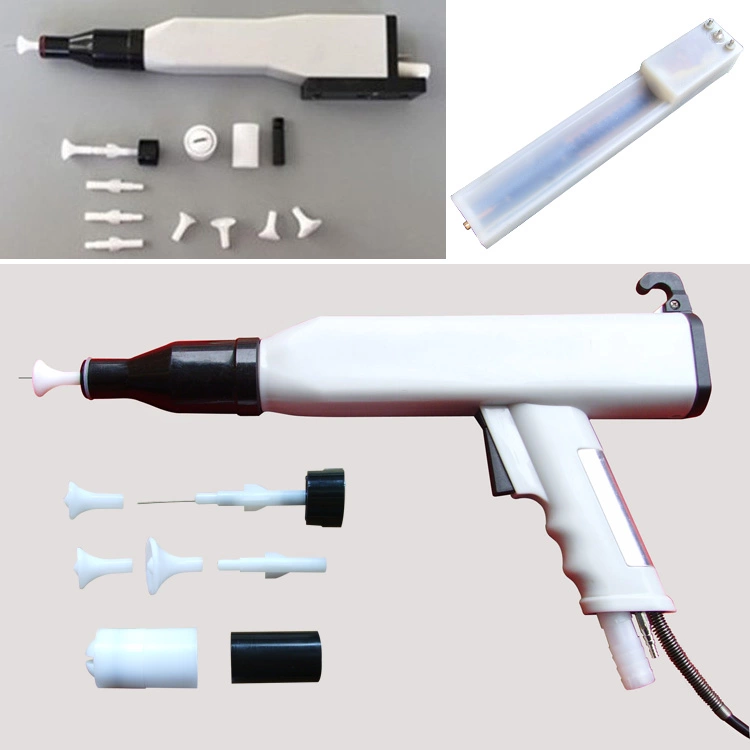
- Inspection Régulière
- Vérification Visuelle : Inspectez visuellement l’équipement régulièrement pour détecter des signes d’usure, de corrosion ou de dommages physiques. Cela inclut les câbles, les connexions électriques, et les composants mécaniques.
- Suivi des Composants : Tenez un registre des inspections régulières pour chaque pièce de l’équipement, ce qui vous permettra de détecter les tendances d’usure et de planifier les remplacements nécessaires.
- Nettoyage des Équipements
- Nettoyage des Pistolets de Pulvérisation : Démontage et nettoyage régulier des pistolets de pulvérisation pour éviter l’accumulation de poudre, qui peut obstruer les buses et affecter la qualité de l’application. Utilisez de l’air comprimé et des solvants recommandés pour le nettoyage.
- Entretien des Cabines de Poudrage : Nettoyez régulièrement l’intérieur des cabines pour éviter la contamination croisée des couleurs. Les systèmes de récupération de poudre doivent être vidés et nettoyés selon les instructions du fabricant.
- Filtres et Ventilation : Remplacez les filtres des systèmes de ventilation selon les recommandations du fabricant pour assurer une ventilation optimale et éviter l’accumulation de particules de poudre.
- Maintenance Préventive
- Lubrification des Composants Mécaniques : Appliquez régulièrement de la lubrification aux pièces mécaniques mobiles pour réduire l’usure et éviter les blocages.
- Calibration des Systèmes Électrostatiques : Assurez-vous que les systèmes de charge électrostatique sont correctement calibrés pour une application uniforme de la poudre. Vérifiez les connexions électriques et remplacez les pièces usées.
- Vérification des Températures de Four : Contrôlez régulièrement les températures des fours de polymérisation pour garantir qu’elles restent dans les limites recommandées pour la poudre utilisée. Des températures incorrectes peuvent entraîner des finitions de mauvaise qualité.
- Formation du Personnel
- Formation Continue : Assurez-vous que le personnel est correctement formé pour utiliser et entretenir l’équipement. Organisez des sessions de formation régulières pour actualiser les connaissances sur les nouvelles technologies et méthodes d’entretien.
- Sécurité au Travail : Éduquez le personnel sur les protocoles de sécurité, y compris l’utilisation d’équipements de protection individuelle (EPI) pour éviter les accidents et l’exposition aux particules de poudre.
- Gestion des Pièces de Rechange
- Inventaire des Pièces de Rechange : Maintenez un stock adéquat de pièces de rechange essentielles comme les buses de pulvérisation, les filtres, et les éléments chauffants pour réduire les temps d’arrêt en cas de panne.
- Commande de Pièces : Prévoyez à l’avance les commandes de pièces de rechange pour éviter les ruptures de stock qui pourraient perturber la production.
- Analyse des Performances
- Suivi des Indicateurs Clés : Surveillez les indicateurs de performance tels que l’efficacité énergétique, la qualité de la finition, et le taux de défauts pour identifier les domaines nécessitant des améliorations.
- Retour d’Expérience : Sollicitez des retours d’expérience du personnel opérant l’équipement pour identifier les problèmes récurrents et ajuster les procédures d’entretien en conséquence.
Conclusion
L’entretien adéquat des équipements de poudrage est essentiel pour garantir une production efficace, sûre et de haute qualité. En mettant en œuvre un programme de maintenance préventive et en formant le personnel aux meilleures pratiques, vous pouvez prolonger la durée de vie de vos équipements et optimiser vos opérations de revêtement en poudre. Assurez-vous de suivre les recommandations du fabricant pour chaque composant de l’équipement afin d’assurer leur bon fonctionnement.
N’hésitez pas à me dire si vous avez besoin de plus de détails sur un aspect particulier de l’entretien ou si vous souhaitez que d’autres sujets soient abordés.
Quelles pièces de rechange
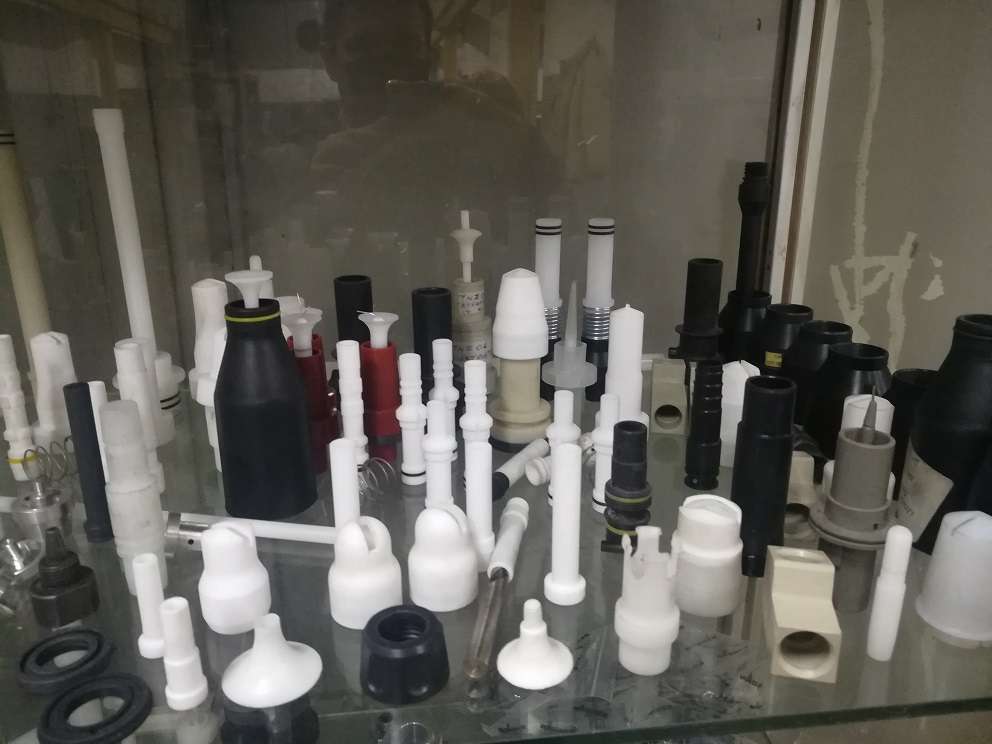
La maintenance efficace de l’équipement de poudrage implique la gestion proactive des pièces de rechange. Avoir les bonnes pièces à portée de main peut réduire considérablement les temps d’arrêt et maintenir la qualité de production. Voici une liste des pièces de rechange essentielles pour les équipements de poudrage :
Pièces de Rechange Essentielles pour l’Équipement de Poudrage
- Buses de Pistolet de Pulvérisation
- Types de Buses : Disponibles en différentes tailles et formes (rondes, plates, coniques) pour s’adapter aux divers types d’application et de finitions souhaitées.
- Usure : Les buses s’usent avec le temps en raison de l’abrasion de la poudre. Avoir des buses de rechange garantit que la qualité de la pulvérisation reste constante.
- Électrodes de Pistolet
- Fonction : Les électrodes chargent électrostatiquement la poudre pour l’application. Elles peuvent s’user ou s’endommager, ce qui affecte l’efficacité de l’application.
- Remplacement : Des électrodes de rechange sont cruciales pour maintenir une charge électrostatique efficace et une application uniforme.
- Filtres de Cabine
- Fonction des Filtres : Captent les particules de poudre en excès, évitant la contamination de l’air et l’accumulation de poudre à l’intérieur de la cabine.
- Types de Filtres : Incluent les filtres à cartouche et les filtres à sac, chacun ayant des besoins de remplacement réguliers pour garantir un environnement de travail propre et sûr.
- Pompes à Poudre
- Rôle des Pompes : Transportent la poudre du réservoir à l’applicateur. Les pompes peuvent s’user avec le temps et nécessitent des pièces de rechange comme des joints, des tuyaux, et des joints toriques.
- Maintenance : Un entretien régulier et la disponibilité de pièces de rechange sont essentiels pour éviter les interruptions de flux de poudre.
- Éléments Chauffants des Fours de Polymérisation
- Importance : Maintiennent la température nécessaire pour durcir la poudre. Les éléments chauffants peuvent s’user, nécessitant des remplacements pour maintenir la température uniforme dans le four.
- Types : Incluent les éléments chauffants électriques et les brûleurs à gaz.
- Joints et Joints Toriques
- Fonction : Assurent l’étanchéité des systèmes pneumatiques et hydrauliques. Les joints et les joints toriques peuvent se détériorer avec le temps, provoquant des fuites et des pertes d’efficacité.
- Disponibilité : Garder un stock de différents types et tailles de joints et de joints toriques est essentiel pour éviter les temps d’arrêt imprévus.
- Composants Électroniques
- Panneaux de Contrôle : Les cartes de circuits imprimés, les écrans de contrôle, et les capteurs peuvent nécessiter des remplacements en cas de panne.
- Capteurs et Commutateurs : Surveillent et contrôlent divers aspects de l’équipement. Les pièces de rechange aident à maintenir la précision et le contrôle des opérations.
- Pièces de Rechange pour Systèmes de Transport
- Chaînes et Rouleaux : Pour les systèmes de convoyage qui transportent les pièces à travers les différentes étapes du processus de revêtement.
- Moteurs et Réducteurs : Nécessitent des remplacements pour éviter les pannes des systèmes de transport.
- Agitateurs et Mélangeurs de Poudre
- Fonction : Maintiennent la poudre en mouvement pour éviter la sédimentation et assurer une distribution homogène. Les pièces mobiles, comme les pales d’agitation, peuvent s’user avec le temps.
Importance de la Gestion des Pièces de Rechange
Planification Proactive : Anticiper les besoins en pièces de rechange et maintenir un stock adéquat peut éviter des interruptions coûteuses de la production. Établir un calendrier de maintenance préventive permet de prédire les besoins en remplacements.
Fournisseurs de Confiance : Travailler avec des fournisseurs de pièces de rechange fiables garantit l’accès à des composants de haute qualité qui prolongent la durée de vie de l’équipement.
Consignation des Pièces : Mettre en place un système de consignation de pièces pour suivre l’utilisation des pièces de rechange et les réapprovisionner automatiquement.
Conclusion
La disponibilité de pièces de rechange essentielles et un programme de maintenance bien structuré sont cruciaux pour le bon fonctionnement des équipements de poudrage. La gestion proactive des pièces de rechange assure non seulement une production fluide mais aussi une qualité de revêtement constante. En ayant une stratégie d’entretien et de gestion des pièces bien définie, les entreprises peuvent réduire les temps d’arrêt et maximiser l’efficacité de leurs opérations de revêtement en poudre.
Si vous avez besoin de détails supplémentaires ou d’informations spécifiques sur l’un des composants ou des procédures, n’hésitez pas à me le faire savoir !
Pièces pour pistolets
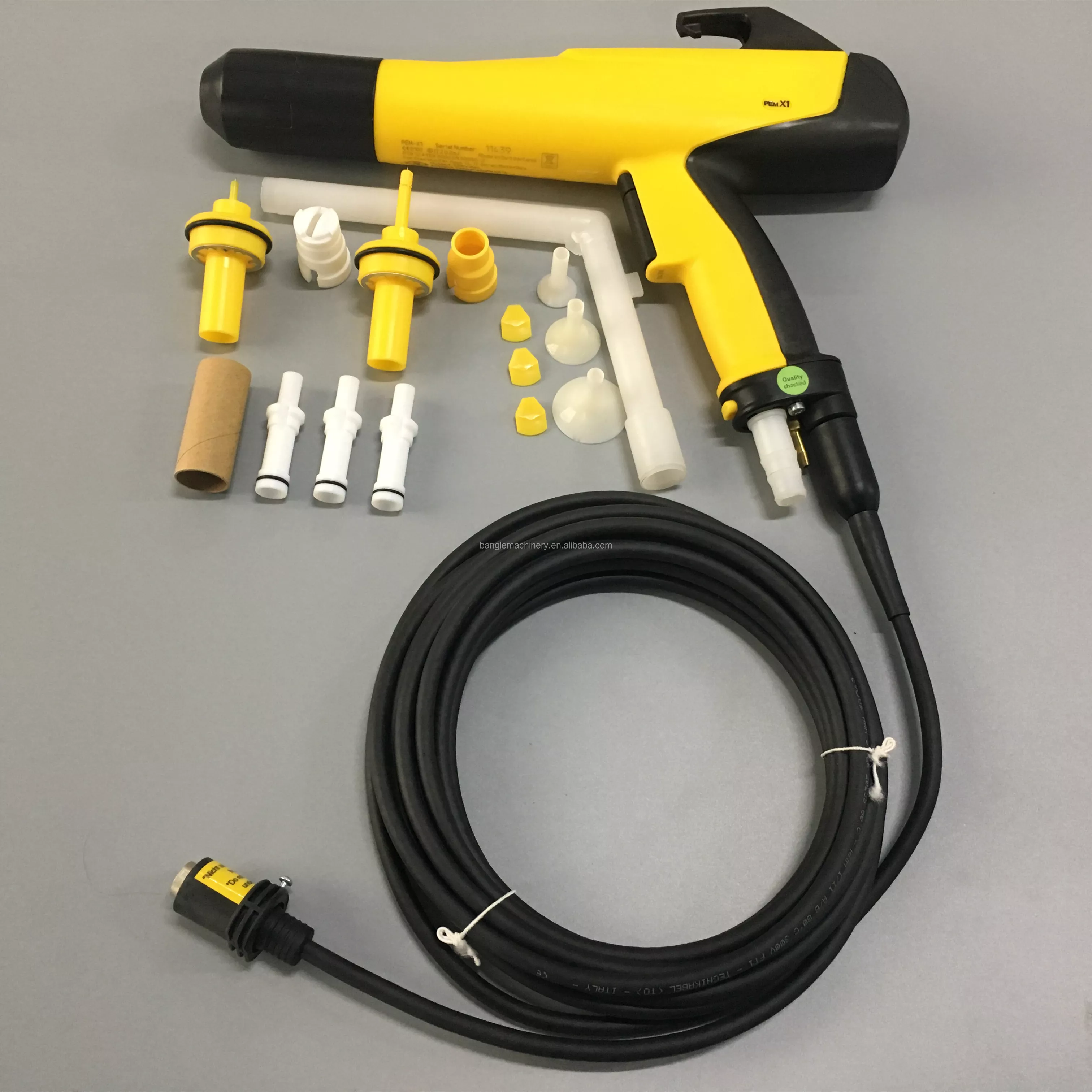
Lorsqu’il s’agit de l’entretien et de la maintenance des pistolets de pulvérisation pour le revêtement en poudre, il est essentiel de disposer d’un stock adéquat de pièces de rechange spécifiques pour éviter des interruptions de production et maintenir une application uniforme et de haute qualité. Voici une liste des principales pièces de rechange pour les pistolets de pulvérisation de poudre, avec une description de leur fonction et des raisons pour lesquelles elles sont importantes :
Pièces de Rechange Essentielles pour Pistolets de Pulvérisation
- Buses de Pulvérisation
- Fonction : Les buses contrôlent la taille et la forme du motif de pulvérisation de poudre, influençant directement la couverture et l’uniformité de l’application.
- Types : Disponibles en différentes formes et tailles, telles que rondes ou plates, pour diverses applications et finitions.
- Remplacement : Les buses s’usent avec le temps en raison de l’abrasion de la poudre, ce qui peut altérer le motif de pulvérisation. Un stock de buses de rechange garantit une qualité constante.
- Électrodes
- Fonction : Chargent électrostatiquement la poudre pour assurer une adhésion uniforme à la surface de l’objet à revêtir.
- Usure : Les électrodes peuvent se corroder ou s’user, ce qui réduit leur efficacité de charge et peut entraîner une mauvaise adhésion de la poudre.
- Remplacement Régulier : Disposer d’électrodes de rechange assure que le pistolet maintient une charge électrostatique optimale.
- Chambres de Charge
- Rôle : La chambre de charge est où la poudre est ionisée avant d’être pulvérisée. Elle joue un rôle clé dans le processus de charge électrostatique.
- Usure : L’accumulation de poudre peut affecter l’efficacité de la charge, nécessitant un nettoyage régulier et, parfois, le remplacement de la chambre.
- Joints et Joints Toriques
- Fonction : Assurent l’étanchéité des systèmes pneumatiques et empêchent les fuites d’air qui pourraient affecter la performance du pistolet.
- Importance : Les joints et joints toriques peuvent se détériorer avec le temps, provoquant des pertes de pression et une application inégale.
- Maintenance : Vérifiez régulièrement l’état des joints et remplacez-les pour éviter les dysfonctionnements.
- Housses de Pistolet et Capots
- Rôle : Protègent les composants internes du pistolet contre la poudre et la poussière.
- Remplacement : Les capots peuvent être endommagés ou usés avec le temps, nécessitant un remplacement pour maintenir le pistolet propre et fonctionnel.
- Flexibles de Poudre
- Fonction : Transportent la poudre du réservoir au pistolet de pulvérisation.
- Usure : Les flexibles peuvent se boucher ou s’user, affectant le flux de poudre.
- Entretien : Des flexibles de rechange sont essentiels pour garantir un flux continu et éviter les interruptions.
- Cartouches de Filtration
- Utilisation : Les cartouches filtrantes intégrées dans certains systèmes de pistolet purifient l’air comprimé utilisé pour la pulvérisation.
- Maintenance : Un remplacement régulier est nécessaire pour assurer la propreté de l’air comprimé et éviter la contamination de la poudre.
- Connecteurs et Raccords
- Rôle : Connectent les différentes parties du système de pulvérisation, y compris les flexibles et les réservoirs.
- Vérification : Les connecteurs et raccords doivent être contrôlés régulièrement pour s’assurer qu’ils ne sont pas desserrés ou usés, ce qui pourrait entraîner des fuites.
- Pompes et Régulateurs d’Air
- Fonction : Régulent la pression de l’air pour une pulvérisation efficace et contrôlée.
- Usure : Les pompes et régulateurs peuvent se détériorer, nécessitant des pièces de rechange pour maintenir la pression correcte.
- Disponibilité : Avoir des pompes et régulateurs de rechange est crucial pour éviter des variations de pression qui affectent la qualité de l’application.
- Unités de Contrôle
- Rôle : Les panneaux de contrôle électroniques et les unités de commande régulent le fonctionnement du pistolet, y compris le débit de poudre et la charge électrostatique.
- Maintenance : Des problèmes électriques peuvent survenir, nécessitant des pièces de rechange pour garantir un fonctionnement sans interruption.
Importance de la Gestion des Pièces de Rechange
- Réduction des Temps d’Arrêt : Avoir un stock de pièces de rechange critique permet de minimiser les interruptions de production en cas de panne ou de défaillance.
- Qualité de Production : L’utilisation de pièces usées ou endommagées peut affecter la qualité de la pulvérisation, entraînant des défauts dans le revêtement. Les pièces de rechange assurent que la qualité reste constante.
- Économies de Coût à Long Terme : En entretenant régulièrement les pistolets avec des pièces de rechange, vous réduisez les risques de dommages plus graves qui pourraient nécessiter des réparations coûteuses ou le remplacement complet de l’équipement.
- Amélioration de la Sécurité : Assurer le bon fonctionnement des composants critiques contribue à la sécurité globale de l’environnement de travail, en réduisant le risque de fuites, de surchauffe, ou d’autres dangers.
Conclusion
La disponibilité et la gestion proactive des pièces de rechange pour les pistolets de pulvérisation sont essentielles pour maintenir une production efficace et de haute qualité dans les opérations de revêtement en poudre. En investissant dans un programme de maintenance préventive et en gardant un stock adéquat de pièces critiques, vous pouvez prolonger la durée de vie de votre équipement et optimiser vos processus de production.
Si vous avez besoin de plus d’informations sur l’une de ces pièces ou d’une autre assistance, n’hésitez pas à me le faire savoir !
Fours à thermolaquage
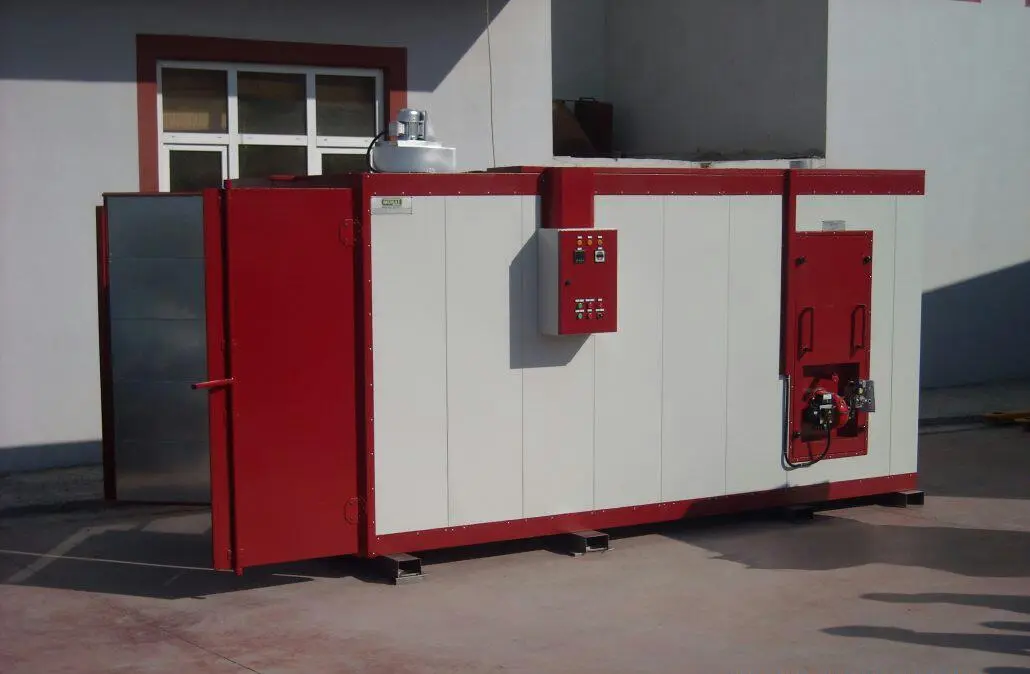
Les fours à thermolaquage, également appelés fours de polymérisation, jouent un rôle essentiel dans le processus de revêtement en poudre, en assurant une finition de qualité et durable. Ce procédé implique l’application de poudre thermodurcissable sur une surface qui est ensuite chauffée dans un four pour faire fondre et durcir la poudre, créant ainsi une couche uniforme et résistante. Voici un aperçu détaillé des fours à thermolaquage, de leur fonctionnement, des types disponibles, et des critères à considérer lors de leur sélection :
Fonctionnement des Fours à Thermolaquage
- Étapes du Processus de Thermolaquage
- Application de la Poudre : La poudre est appliquée sur la surface de l’objet à l’aide d’un pistolet de pulvérisation électrostatique. La charge électrostatique attire la poudre sur la surface, assurant une couverture uniforme.
- Polymérisation dans le Four : L’objet revêtu est ensuite placé dans un four à thermolaquage, où il est chauffé à une température spécifique pour fondre la poudre et la faire durcir.
- Durcissement : La chaleur permet aux particules de poudre de fusionner et de former une couche lisse et continue. Le processus de polymérisation dépend du type de poudre utilisée et des spécifications du fabricant.
- Caractéristiques des Fours à Thermolaquage
- Température : La plupart des poudres nécessitent des températures comprises entre 160°C et 230°C pour une polymérisation efficace.
- Durée : Le temps de polymérisation peut varier de 10 à 30 minutes, selon la taille de l’objet et le type de poudre.
- Uniformité de la Chaleur : Une distribution uniforme de la chaleur est cruciale pour éviter les défauts de surface, tels que des bulles ou des irrégularités.
Types de Fours à Thermolaquage
- Fours à Convection
- Principe : Utilisent l’air chaud pour chauffer les objets. Les ventilateurs répartissent la chaleur uniformément à l’intérieur du four.
- Avantages : Idéaux pour les objets volumineux et les lignes de production à grande échelle. Offrent une uniformité de chaleur efficace.
- Inconvénients : Peuvent être moins efficaces en termes de consommation d’énergie par rapport aux autres types de fours.
- Fours Infrarouges
- Principe : Utilisent des rayons infrarouges pour chauffer directement la surface de l’objet.
- Avantages : Réchauffement rapide, ce qui réduit le temps de polymérisation. Idéal pour les objets de formes complexes.
- Inconvénients : Moins efficace pour les objets très épais ou ceux avec des masses thermiques importantes.
- Fours à Induction
- Principe : Utilisent des champs électromagnétiques pour chauffer directement les objets métalliques.
- Avantages : Chauffage rapide et précis, idéal pour des applications spécifiques nécessitant un contrôle thermique précis.
- Inconvénients : Généralement plus coûteux et limités aux matériaux conducteurs.
- Fours Hybrides
- Principe : Combinent des technologies de chauffage à convection et infrarouge pour maximiser l’efficacité.
- Avantages : Permettent une flexibilité dans le traitement de différents types de pièces avec une consommation d’énergie optimisée.
- Inconvénients : Coût initial plus élevé dû à la complexité de la technologie intégrée.
Critères de Sélection d’un Four à Thermolaquage
- Capacité et Taille
- Dimensions du Four : Doivent correspondre à la taille des objets à traiter. Des fours plus grands sont nécessaires pour des pièces volumineuses ou des productions en série.
- Capacité de Charge : Évaluer la capacité de charge en termes de poids et de volume pour assurer que le four peut accueillir vos produits sans compromettre l’efficacité.
- Consommation Énergétique
- Efficacité Énergétique : Optez pour des modèles qui offrent une faible consommation d’énergie pour réduire les coûts d’exploitation.
- Isolation Thermique : Une bonne isolation aide à conserver la chaleur à l’intérieur du four, améliorant ainsi l’efficacité énergétique.
- Contrôle de Température
- Précision : La capacité à contrôler et maintenir précisément la température est essentielle pour la qualité de la finition.
- Systèmes de Contrôle Avancés : Recherchez des fours équipés de systèmes de contrôle numériques permettant un réglage précis et facile.
- Uniformité de la Chaleur
- Ventilation et Circulation d’Air : Assurez-vous que le four dispose de systèmes efficaces de circulation d’air pour garantir une distribution uniforme de la chaleur.
- Tests de Performance : Vérifiez les spécifications des tests de performance du fabricant pour l’uniformité thermique.
- Sécurité et Conformité
- Normes de Sécurité : Le four doit être conforme aux normes de sécurité locales et internationales, incluant des dispositifs de protection contre la surchauffe et des systèmes de verrouillage de sécurité.
- Émissions : Assurez-vous que le four respecte les réglementations concernant les émissions pour éviter les problèmes environnementaux.
Avantages des Fours à Thermolaquage
- Durabilité : Les finitions obtenues par thermolaquage sont extrêmement durables et résistantes aux éraflures, à la corrosion, et aux produits chimiques.
- Écologique : Ce procédé ne nécessite pas de solvants, ce qui réduit l’émission de composés organiques volatils (COV).
- Flexibilité de Design : Offre une large gamme de couleurs et de textures, ce qui permet une grande flexibilité en termes de design et de personnalisation.
Conclusion
Les fours à thermolaquage sont un élément crucial dans le processus de revêtement en poudre, assurant que la finition appliquée est à la fois esthétique et fonctionnelle. Le choix du bon type de four, combiné à une maintenance appropriée et à un contrôle rigoureux des paramètres de fonctionnement, peut considérablement améliorer la qualité de la production et réduire les coûts opérationnels.
Si vous avez besoin de plus de détails sur un aspect spécifique des fours à thermolaquage ou si vous souhaitez explorer d’autres éléments, n’hésitez pas à me le faire savoir !
Comparaison des Types de Fours à Thermolaquage
Lorsqu’il s’agit de choisir un four à thermolaquage pour le revêtement en poudre, il est crucial de comprendre les différences entre les différents types de fours disponibles. Chaque type de four a ses propres avantages et inconvénients, qui peuvent influencer la qualité de la finition, l’efficacité énergétique, le coût d’exploitation, et la flexibilité d’application. Voici une comparaison détaillée des principaux types de fours à thermolaquage :
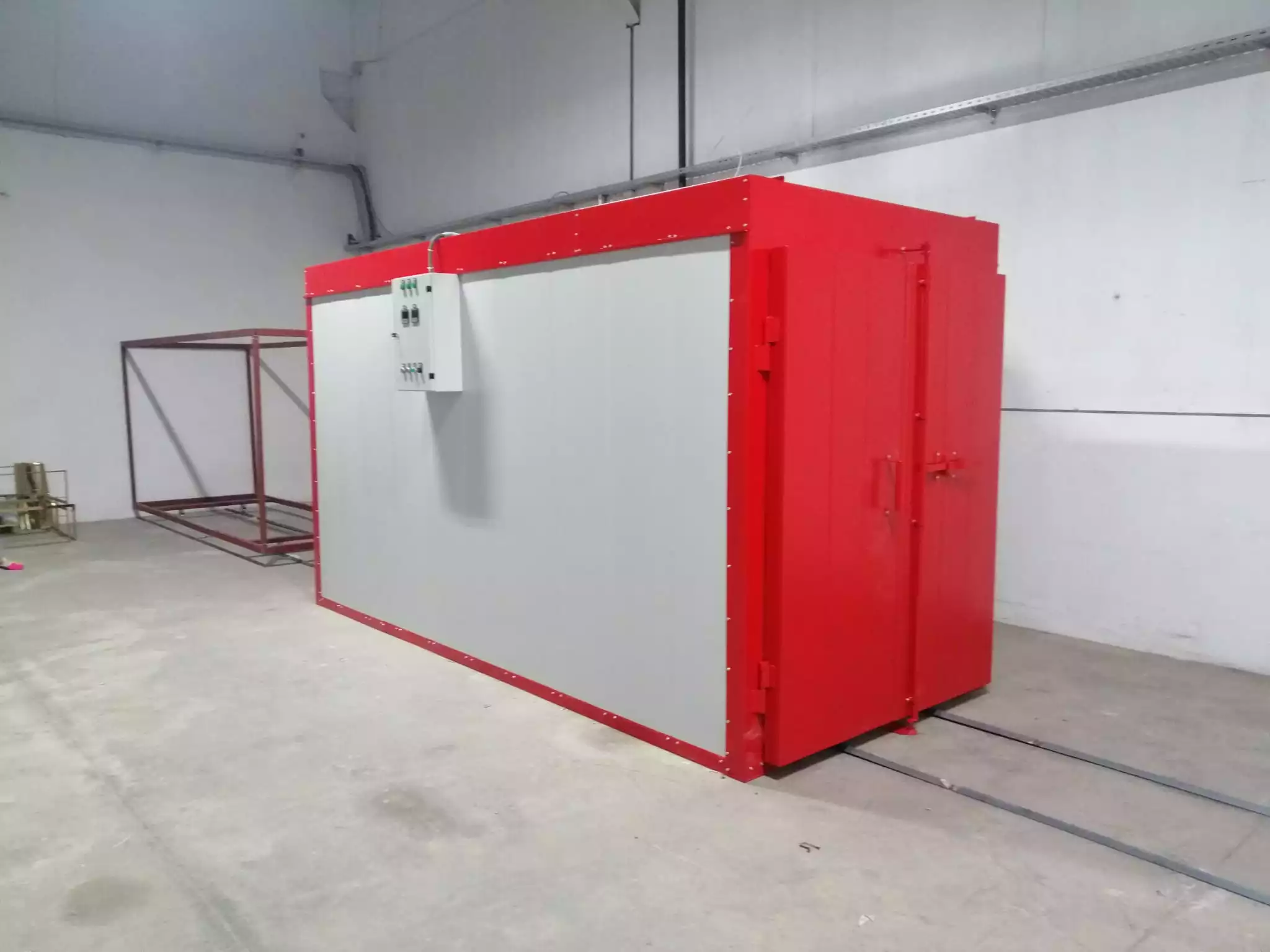
1. Fours à Convection
Principe de Fonctionnement :
Les fours à convection chauffent l’air à l’intérieur du four, qui est ensuite distribué uniformément autour des pièces à l’aide de ventilateurs. Ce type de four est l’un des plus couramment utilisés dans l’industrie du thermolaquage.
Avantages :
- Uniformité de la Chaleur : Grâce à la circulation d’air, les fours à convection offrent une distribution uniforme de la chaleur, réduisant les risques de défauts dans le revêtement.
- Adaptabilité : Convient à une large gamme de tailles et de formes de pièces, y compris les objets volumineux.
- Coût Initial : Généralement, ces fours ont un coût initial plus bas par rapport aux autres technologies de chauffage plus avancées.
Inconvénients :
- Consommation Énergétique : Peut être moins efficace en termes d’énergie par rapport aux fours infrarouges ou à induction, surtout pour les grandes charges.
- Temps de Chauffage : Le temps de montée en température peut être plus long, ce qui peut affecter la rapidité du cycle de production.
2. Fours Infrarouges
Principe de Fonctionnement :
Les fours infrarouges utilisent des rayons infrarouges pour chauffer directement la surface des pièces. Ce type de chauffage est basé sur le transfert de chaleur par rayonnement.
Avantages :
- Rapidité de Chauffage : Les fours infrarouges chauffent rapidement les surfaces, ce qui réduit considérablement le temps de cycle.
- Efficacité Énergétique : Consomment généralement moins d’énergie puisqu’ils chauffent directement la pièce sans chauffer tout le volume d’air autour.
- Finitions Complexes : Idéal pour les pièces avec des formes complexes et des géométries difficiles, où un chauffage direct est avantageux.
Inconvénients :
- Uniformité de la Chaleur : Peut avoir des difficultés à chauffer uniformément des pièces très épaisses ou denses, car la chaleur ne pénètre pas aussi profondément.
- Coût Initial : Le coût d’installation peut être plus élevé, surtout si une personnalisation spécifique est requise pour l’application.
3. Fours à Induction
Principe de Fonctionnement :
Les fours à induction utilisent des champs électromagnétiques pour chauffer les objets métalliques directement. Ce type de chauffage est extrêmement rapide et précis.
Avantages :
- Précision : Offre un contrôle précis de la température, idéal pour des applications nécessitant une gestion thermique rigoureuse.
- Rapidité : Très rapide à chauffer, ce qui réduit les temps de cycle de production.
- Efficacité Énergétique : Chauffe directement le matériau conducteur, ce qui réduit les pertes énergétiques.
Inconvénients :
- Limitation des Matériaux : Ne peut être utilisé que sur des matériaux conducteurs, ce qui limite son utilisation aux métaux.
- Coût Élevé : Le coût initial est généralement plus élevé que les autres types de fours, et le coût de l’équipement peut être prohibitif pour certaines petites et moyennes entreprises.
4. Fours Hybrides
Principe de Fonctionnement :
Les fours hybrides combinent la technologie de convection et infrarouge pour offrir une flexibilité et une efficacité accrues.
Avantages :
- Flexibilité : Peut traiter une variété de pièces et de matériaux, maximisant ainsi la polyvalence des applications.
- Efficacité Améliorée : Combine les avantages des deux systèmes de chauffage pour une efficacité énergétique et de traitement améliorée.
- Optimisation de la Qualité : Peut offrir une meilleure qualité de finition en ajustant les méthodes de chauffage selon les besoins.
Inconvénients :
- Coût Initial : L’investissement initial peut être élevé en raison de la complexité accrue du système.
- Maintenance : Peut nécessiter un entretien plus régulier et complexe en raison de la présence de deux systèmes de chauffage différents.
Tableau Comparatif
Voici un tableau qui résume les principales caractéristiques de chaque type de four à thermolaquage :
Type de Four | Avantages | Inconvénients | Applications Idéales |
---|---|---|---|
Convection | – Uniformité de chaleur<br>- Adaptabilité<br>- Coût initial bas | – Consommation énergétique<br>- Temps de chauffage long | Objets volumineux, production en série |
Infrarouge | – Chauffage rapide<br>- Efficacité énergétique<br>- Finitions complexes | – Uniformité pour pièces épaisses<br>- Coût initial | Pièces complexes, temps de cycle rapide |
Induction | – Précision thermique<br>- Rapidité<br>- Efficacité énergétique | – Limité aux matériaux conducteurs<br>- Coût élevé | Applications précises, matériaux conducteurs |
Hybride | – Flexibilité<br>- Efficacité améliorée<br>- Qualité optimisée | – Coût initial élevé<br>- Maintenance complexe | Diversité de matériaux et de formes |
Conclusion
Le choix du type de four à thermolaquage dépend de plusieurs facteurs, notamment la nature des pièces à traiter, les exigences de production, le budget disponible, et l’efficacité énergétique souhaitée.
- Fours à Convection : Recommandés pour les opérations à grande échelle nécessitant une uniformité de chaleur sur des pièces volumineuses.
- Fours Infrarouges : Idéaux pour des cycles de production rapides et des pièces de formes complexes.
- Fours à Induction : Conviennent aux applications nécessitant un contrôle thermique précis, mais limités aux métaux.
- Fours Hybrides : Offrent une polyvalence maximale pour traiter divers matériaux et formes.
En évaluant soigneusement vos besoins spécifiques et en tenant compte des avantages et des inconvénients de chaque type de four, vous pouvez faire un choix éclairé qui optimisera vos opérations de revêtement en poudre. Si vous avez besoin de plus d’informations ou de conseils supplémentaires, n’hésitez pas à demander !
Exemples d’applications
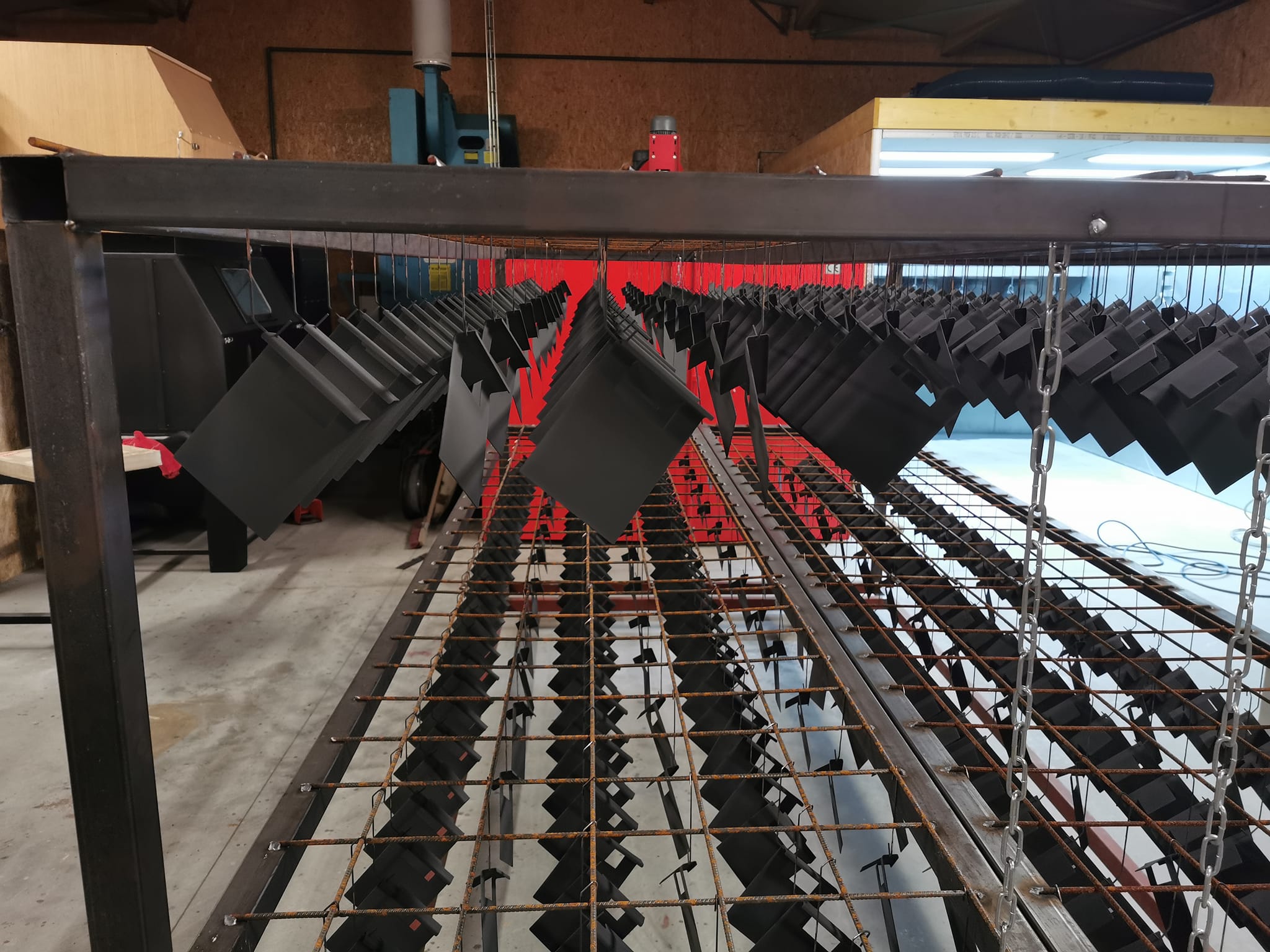
Les fours à thermolaquage sont utilisés dans une variété d’industries en raison de leurs capacités à fournir des finitions durables, esthétiques, et résistantes. Voici quelques exemples d’applications industrielles et commerciales où les fours à thermolaquage sont couramment utilisés :
Exemples d’Applications des Fours à Thermolaquage
1. Industrie Automobile
- Composants Peints : Les pièces automobiles comme les jantes, les châssis, et les éléments de suspension sont souvent thermolaqués pour améliorer leur résistance à la corrosion et leur apparence esthétique.
- Accessoires et Pièces : Les rétroviseurs, poignées de porte, et autres accessoires sont également revêtus pour offrir une protection supplémentaire contre les rayures et les intempéries.
2. Équipements Électroménagers
- Appareils de Cuisine : Les fours, réfrigérateurs, et autres appareils ménagers utilisent le thermolaquage pour protéger les surfaces métalliques contre l’usure et offrir des finitions brillantes et colorées.
- Machines à Laver et Sèche-linge : Les panneaux extérieurs de ces appareils bénéficient du revêtement en poudre pour leur résistance accrue à l’humidité et aux produits chimiques ménagers.
3. Mobilier Métallique
- Meubles de Bureau : Les cadres de chaises, bureaux, et autres meubles de bureau en métal utilisent le thermolaquage pour améliorer la durabilité et offrir une finition élégante.
- Mobilier d’Extérieur : Les meubles d’extérieur, tels que les chaises de jardin et les tables, sont thermolaqués pour résister aux intempéries et aux rayons UV, ce qui prévient la décoloration et la corrosion.
4. Industrie Électronique
- Boîtiers d’Équipements : Les boîtiers pour ordinateurs, téléviseurs, et autres appareils électroniques bénéficient du thermolaquage pour protéger les composants internes de la poussière et de l’humidité.
- Composants Intérieurs : Les dissipateurs de chaleur et autres pièces métalliques internes sont également revêtus pour améliorer leur longévité et leur performance thermique.
5. Équipements de Construction
- Machines de Chantier : Les pièces de machines telles que les grues, bulldozers, et excavateurs sont souvent thermolaquées pour résister aux environnements difficiles et prolonger leur durée de vie.
- Outils et Équipements : Les outils manuels et électriques, ainsi que les équipements de sécurité, utilisent le thermolaquage pour offrir une résistance accrue à l’usure et une meilleure apparence.
6. Industrie du Transport
- Vélos et Motocyclettes : Les cadres de vélos et de motos sont thermolaqués pour améliorer la résistance à la rouille et offrir une finition durable.
- Trains et Wagons : Les composants métalliques des trains, comme les bogies et les structures de carrosserie, sont revêtus pour protéger contre la corrosion et améliorer l’apparence.
7. Infrastructure et Urbanisme
- Poteaux de Signalisation et Barrières de Sécurité : Utilisent le thermolaquage pour garantir une longue durée de vie et une visibilité accrue grâce à des couleurs vives et durables.
- Équipements de Jeux et Parcs : Les structures de jeux pour enfants et les équipements de parcs sont revêtus pour assurer sécurité et durabilité contre les éléments extérieurs.
8. Industrie de l’Aéronautique
- Composants Intérieurs et Extérieurs : Les avions utilisent le thermolaquage pour les composants intérieurs, comme les panneaux et les sièges, ainsi que pour les pièces extérieures, comme les capots et les structures de fuselage.
- Finitions Anti-Corrosion : Le revêtement en poudre est utilisé pour protéger les pièces critiques contre la corrosion due à l’exposition aux éléments.
Avantages du Thermolaquage pour ces Applications
- Résistance aux Intempéries et à la Corrosion : Le revêtement en poudre offre une protection exceptionnelle contre la rouille, la corrosion, et les éléments extérieurs, prolongeant ainsi la durée de vie des pièces revêtues.
- Durabilité et Résistance : Les finitions obtenues par thermolaquage sont extrêmement durables et résistantes aux éraflures, aux chocs, et aux produits chimiques.
- Flexibilité Esthétique : Une large gamme de couleurs et de finitions est disponible, permettant aux designers de personnaliser l’apparence des produits selon les besoins spécifiques.
- Écologique : Le processus de thermolaquage est respectueux de l’environnement car il ne nécessite pas de solvants et réduit les émissions de composés organiques volatils (COV).
Conclusion
Les fours à thermolaquage jouent un rôle clé dans diverses industries, fournissant des solutions de revêtement efficaces et durables pour une multitude d’applications. En sélectionnant le bon type de four et en optimisant les paramètres de processus, les entreprises peuvent garantir des résultats de haute qualité et économiquement viables.
Si vous avez besoin de plus d’informations sur une application spécifique ou souhaitez discuter d’autres aspects du thermolaquage, n’hésitez pas à me le faire savoir !
Coût des fours
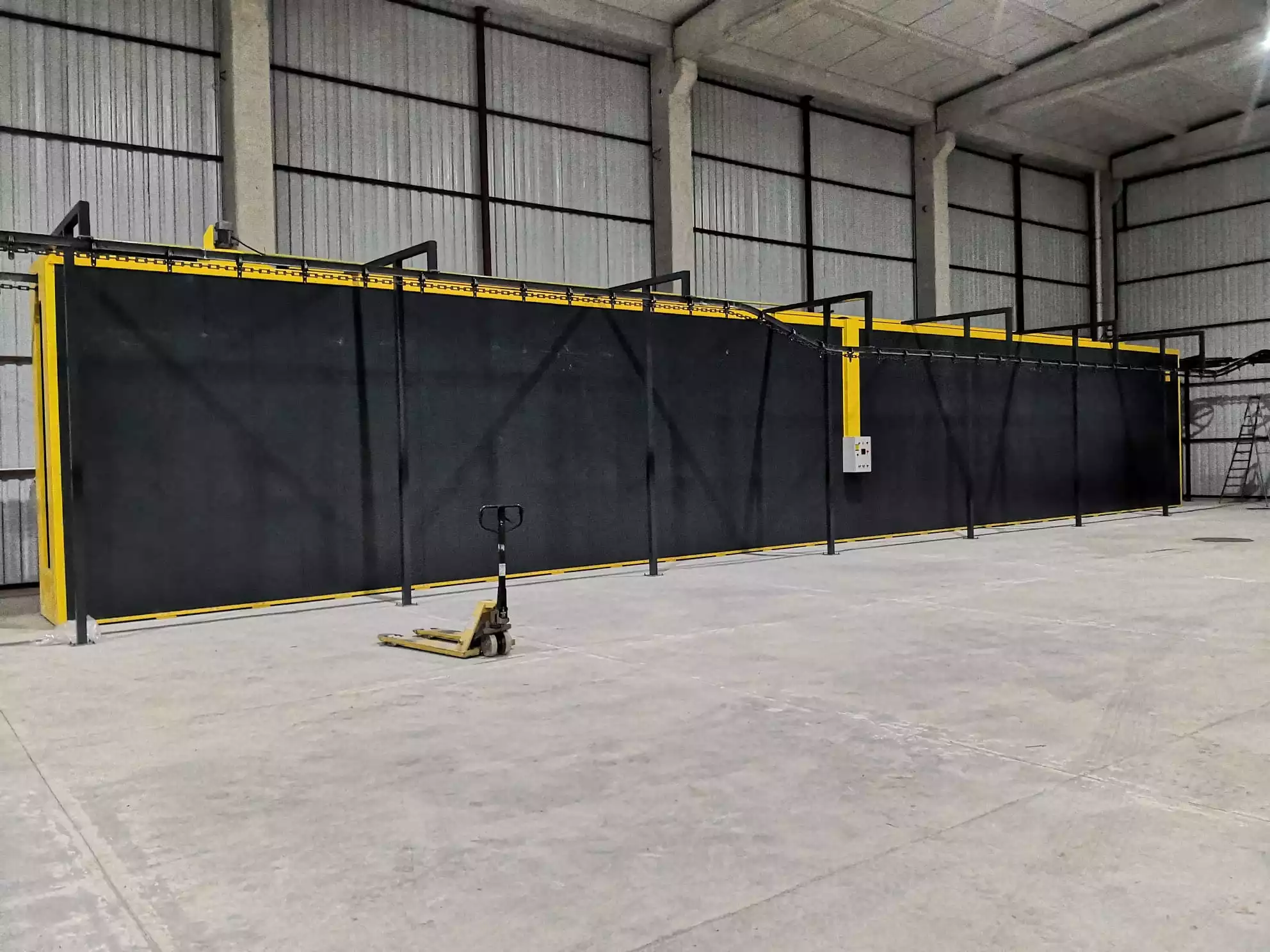
Le coût des fours à thermolaquage peut varier considérablement en fonction de plusieurs facteurs, notamment la taille, la capacité, le type de technologie utilisée, et les caractéristiques spécifiques du four. Voici une analyse détaillée des coûts associés aux différents types de fours à thermolaquage, ainsi que des facteurs qui influencent ces coûts.
Facteurs Influant sur le Coût des Fours à Thermolaquage
- Taille et Capacité
- Petits Fours de Laboratoire : Les petits fours utilisés pour des tests et des productions en faible volume sont généralement moins coûteux, avec des prix pouvant commencer autour de 5 000 à 15 000 euros.
- Fours de Production Moyenne : Ces fours, utilisés pour des productions à échelle moyenne, coûtent généralement entre 20 000 et 50 000 euros.
- Grands Fours Industriels : Les grands fours utilisés pour des productions industrielles de masse peuvent coûter entre 50 000 et 200 000 euros, voire plus selon la capacité et les spécifications.
- Type de Technologie
- Fours à Convection : Ces fours sont souvent moins chers en termes de coût initial, avec des prix pouvant varier de 10 000 à 100 000 euros, selon la taille et les caractéristiques.
- Fours Infrarouges : En raison de leur technologie de chauffage rapide et ciblé, les fours infrarouges peuvent être plus coûteux, généralement entre 15 000 et 150 000 euros.
- Fours à Induction : Les fours à induction, qui nécessitent des composants spécifiques pour chauffer les matériaux conducteurs, peuvent coûter entre 20 000 et 200 000 euros.
- Fours Hybrides : En combinant plusieurs technologies, les fours hybrides peuvent être les plus chers, avec des prix allant de 30 000 à 250 000 euros, en fonction des caractéristiques intégrées.
- Caractéristiques Spécifiques
- Contrôles Avancés : Les systèmes de contrôle numérique et les automatisations intégrées augmentent généralement le coût des fours, ajoutant entre 5 000 et 20 000 euros au prix de base.
- Isolation et Efficacité Énergétique : Les fours dotés d’une isolation thermique avancée pour améliorer l’efficacité énergétique peuvent avoir un coût initial plus élevé.
- Options Personnalisées : Les personnalisations spécifiques pour répondre à des besoins uniques d’application peuvent ajouter des coûts supplémentaires.
- Marque et Fabricant
- Réputation de la Marque : Les fours fabriqués par des entreprises réputées et établies dans l’industrie peuvent coûter plus cher en raison de leur fiabilité et de leur qualité éprouvée.
- Service et Support : Les fournisseurs offrant des services après-vente étendus et un support technique peuvent justifier des prix plus élevés.
- Installation et Maintenance
- Coûts d’Installation : L’installation professionnelle d’un four, surtout pour les grandes installations industrielles, peut ajouter de 2 000 à 10 000 euros au coût total.
- Entretien et Réparations : Les coûts d’entretien continu, y compris le remplacement des pièces et les réparations, doivent être pris en compte dans le calcul des coûts à long terme.
Coût Global de Possession
En plus du coût initial du four, il est important de considérer le coût global de possession, qui inclut :
- Consommation Énergétique : Les fours plus efficaces peuvent réduire les coûts opérationnels à long terme en consommant moins d’énergie.
- Durabilité et Longévité : Investir dans un four de haute qualité peut offrir des économies à long terme grâce à une durée de vie prolongée et à une fiabilité accrue.
- Retour sur Investissement (ROI) : Calculer le retour sur investissement en fonction de l’augmentation de la productivité, de l’amélioration de la qualité des produits, et de la réduction des déchets.
Estimation des Coûts par Type de Four
Type de Four | Coût Estimé | Applications |
---|---|---|
Convection | 10 000 à 100 000 euros | Production à grande échelle |
Infrarouge | 15 000 à 150 000 euros | Cycles rapides, formes complexes |
Induction | 20 000 à 200 000 euros | Applications précises, métaux |
Hybride | 30 000 à 250 000 euros | Flexibilité maximale |
Conseils pour Optimiser l’Achat
- Évaluation des Besoins Spécifiques
- Analysez vos besoins spécifiques en matière de production pour choisir le type de four le plus adapté à votre activité.
- Considérez la capacité requise, le type de pièces à traiter, et les exigences de qualité.
- Comparaison des Fournisseurs
- Demandez des devis à plusieurs fournisseurs pour comparer les options disponibles.
- Évaluez les offres en fonction des coûts initiaux et des coûts d’exploitation à long terme.
- Considérations Financières
- Recherchez des options de financement ou des subventions industrielles qui pourraient alléger le coût initial d’achat.
- Prenez en compte les incitations fiscales pour l’achat d’équipements éco-énergétiques.
- Préparation pour l’Entretien
- Assurez-vous d’avoir un plan de maintenance préventive en place pour minimiser les coûts de réparation imprévus.
- Investissez dans la formation du personnel pour garantir une utilisation optimale et sûre de l’équipement.
Conclusion
Le choix et l’achat d’un four à thermolaquage impliquent une analyse approfondie des coûts, des besoins spécifiques, et des caractéristiques des différentes technologies disponibles. En considérant à la fois le coût initial et les coûts à long terme, vous pouvez faire un choix éclairé qui améliorera la qualité de votre production et maximisera le retour sur investissement. Si vous avez besoin de conseils supplémentaires ou d’une assistance pour un cas spécifique, n’hésitez pas à me le faire savoir !
Temps installation four
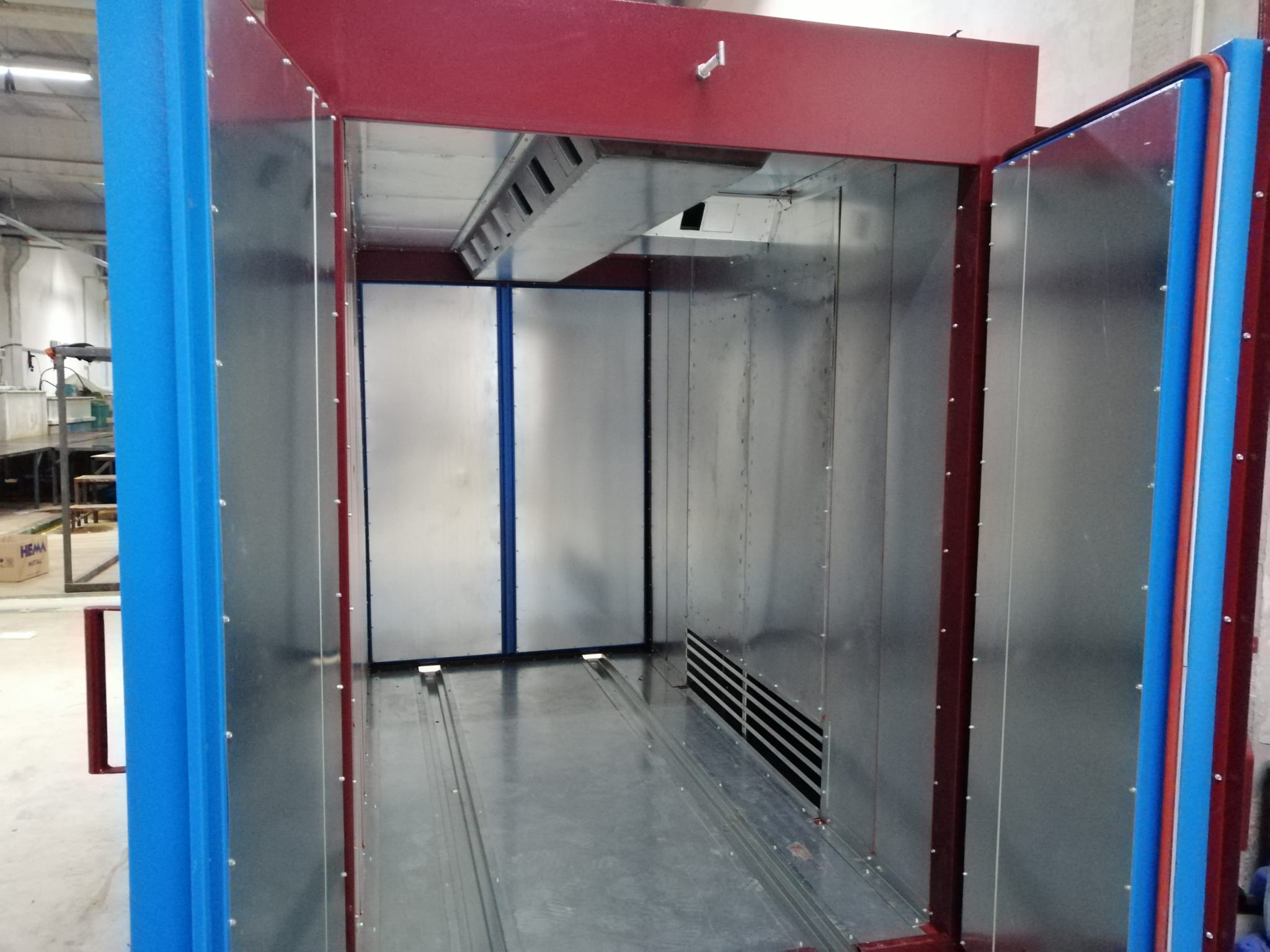
L’installation d’un four à thermolaquage est un processus qui nécessite une planification minutieuse et une coordination efficace. Le temps requis pour installer un four peut varier considérablement en fonction de plusieurs facteurs, notamment la taille du four, la complexité du système, et les conditions spécifiques du site d’installation. Voici une analyse détaillée des différents aspects qui influencent le temps d’installation d’un four à thermolaquage :
Facteurs Influant sur le Temps d’Installation
- Taille et Complexité du Four
- Petits Fours de Laboratoire : Les petits fours, souvent utilisés pour des tests ou de petites productions, peuvent être installés en quelques jours. La simplicité de ces unités signifie qu’elles nécessitent moins de travail pour l’installation.
- Fours de Production Moyenne : Les fours de taille moyenne, utilisés pour des productions à échelle moyenne, peuvent prendre de 1 à 2 semaines pour être installés, en fonction de leur configuration et des besoins de connexion.
- Grands Fours Industriels : Les installations industrielles de grande envergure, qui incluent des systèmes complexes, peuvent nécessiter entre 2 et 4 semaines pour une installation complète. Cela inclut souvent la construction de structures de support et l’intégration dans des lignes de production existantes.
- Type de Technologie
- Fours à Convection : Ces fours, avec des systèmes de ventilation et de circulation d’air, peuvent être relativement simples à installer, mais le temps peut augmenter avec la taille et les spécificités de l’installation.
- Fours Infrarouges : L’installation de systèmes infrarouges peut être plus rapide que d’autres technologies, mais nécessite une attention particulière à l’alignement des émetteurs infrarouges pour garantir une distribution homogène de la chaleur. L’installation typique peut prendre environ 1 à 2 semaines.
- Fours à Induction : Ces fours nécessitent une installation spécialisée en raison des systèmes électromagnétiques complexes. L’installation peut prendre de 2 à 3 semaines, en particulier si des modifications structurelles sont nécessaires.
- Fours Hybrides : Les fours qui combinent plusieurs technologies de chauffage peuvent nécessiter un temps d’installation plus long, souvent de 3 à 4 semaines, en raison de la complexité accrue de l’équipement et de l’intégration requise.
- Préparation du Site
- Infrastructure Électrique : La préparation et la mise à jour des installations électriques pour accueillir un four à thermolaquage peuvent prendre plusieurs jours à quelques semaines, selon la nécessité de nouvelles connexions ou de mises à niveau.
- Systèmes de Ventilation : La mise en place ou la modification des systèmes de ventilation existants pour répondre aux normes de sécurité peut prolonger le temps d’installation. Cela est particulièrement crucial pour les grands fours industriels.
- Fondations et Structures de Support : Pour les grands fours, il peut être nécessaire de construire des structures de support ou de renforcer le sol, ce qui ajoute au temps total d’installation.
- Personnel et Logistique
- Disponibilité de l’Équipe : La disponibilité d’une équipe qualifiée pour réaliser l’installation joue un rôle clé dans le temps nécessaire. Un personnel expérimenté peut accélérer le processus.
- Logistique de Transport : La livraison des composants du four au site d’installation peut également affecter le calendrier global, surtout si des éléments personnalisés ou de grande taille doivent être transportés.
- Tests et Mise en Service
- Tests de Fonctionnalité : Une fois le four installé, il est crucial de réaliser des tests de fonctionnalité pour s’assurer que toutes les parties de l’équipement fonctionnent correctement et en toute sécurité. Cela peut prendre 2 à 5 jours supplémentaires.
- Formation du Personnel : La formation des opérateurs et du personnel de maintenance peut ajouter quelques jours au processus global d’installation. Cela garantit que le personnel est capable d’opérer le four efficacement et en toute sécurité.
Estimation Générale du Temps d’Installation
Type de Four | Temps d’Installation Estimé |
---|---|
Petits Fours de Laboratoire | 1 à 3 jours |
Fours de Production Moyenne | 1 à 2 semaines |
Grands Fours Industriels | 2 à 4 semaines |
Fours à Convection | 1 à 3 semaines |
Fours Infrarouges | 1 à 2 semaines |
Fours à Induction | 2 à 3 semaines |
Fours Hybrides | 3 à 4 semaines |
Conseils pour Optimiser l’Installation
- Planification Précoce
- Évaluation du Site : Effectuez une évaluation précoce du site pour identifier les besoins en infrastructure et anticiper les défis potentiels.
- Coordination Logistique : Coordonnez à l’avance la livraison des composants et la disponibilité du personnel d’installation pour éviter les retards.
- Engagement de Professionnels
- Entreprises Spécialisées : Collaborez avec des entreprises spécialisées dans l’installation de fours industriels pour assurer une installation efficace et conforme aux normes.
- Support Technique : Assurez-vous d’avoir un support technique disponible pour résoudre rapidement les problèmes qui pourraient survenir pendant l’installation.
- Intégration avec les Systèmes Existants
- Systèmes de Production : Intégrez le four dans les systèmes de production existants pour minimiser les interruptions et maximiser l’efficacité.
- Mise en Réseau : Assurez-vous que le four est compatible avec les systèmes de contrôle et de gestion de la production pour un fonctionnement optimal.
- Préparation pour les Tests
- Élaboration de Procédures de Test : Établissez des procédures de test claires pour vérifier le bon fonctionnement du four après l’installation.
- Formation et Sécurité : Formez le personnel aux pratiques de sécurité et à l’utilisation de l’équipement avant la mise en service.
Le thermolaquage, également connu sous le nom de peinture en poudre, est un procédé de finition de surface utilisé pour appliquer un revêtement durable et esthétique sur diverses pièces métalliques. L’une des applications clés de ce procédé est la cabine de thermolaquage, qui joue un rôle crucial dans l’application uniforme de la peinture en poudre. Cette cabine est un espace fermé et contrôlé où les pièces à traiter sont placées avant d’être soumises à un jet de poudre électrostatique. L’objectif est de garantir que chaque surface de la pièce soit recouverte d’une couche de peinture fine, uniforme et résistante.
Le fonctionnement de la cabine de thermolaquage repose sur une combinaison de plusieurs éléments technologiques. La peinture en poudre, qui est un mélange de pigments et de résines polymères, est chargée électrostatiquement avant d’être pulvérisée sur la pièce. L’électricité statique permet aux particules de poudre de s’adhérer fermement à la surface métallique. Une fois que la pièce est recouverte de poudre, elle est placée dans un four de cuisson à haute température. Ce processus fait fondre la poudre et la transforme en un revêtement solide et durable qui adhère fortement à la surface du métal, offrant ainsi une protection contre la corrosion, l’usure et d’autres formes de dégradation.
Les cabines de thermolaquage sont dotées de systèmes sophistiqués de filtration de l’air, conçus pour garantir que l’environnement reste propre et exempt de poussières et d’impuretés qui pourraient affecter la qualité du revêtement. Elles sont également équipées de systèmes de ventilation pour éliminer les vapeurs et gaz générés lors du processus de cuisson, assurant ainsi la sécurité de l’opérateur et le respect des normes environnementales.
L’un des principaux avantages du thermolaquage dans une cabine est sa capacité à produire des finitions durables et résistantes tout en étant respectueux de l’environnement. Contrairement aux peintures liquides traditionnelles, la peinture en poudre ne contient pas de solvants chimiques, ce qui minimise les émissions de composés organiques volatils (COV) et réduit ainsi l’impact environnemental. De plus, tout excédent de poudre qui ne se fixe pas sur la pièce peut être récupéré et réutilisé, ce qui améliore l’efficacité du procédé et réduit les déchets.
Les cabines de thermolaquage sont utilisées dans de nombreuses industries, notamment l’automobile, les équipements industriels, les meubles en métal, ainsi que pour la fabrication de pièces d’architectures extérieures comme les fenêtres et les portails. La capacité à appliquer des revêtements colorés et des finitions texturées, ainsi que la possibilité de choisir des formulations spécifiques de poudre, permettent une personnalisation poussée des produits finis.
Le processus de thermolaquage est également apprécié pour sa rapidité. Comparé à d’autres méthodes de peinture, il permet une production en série plus rapide, avec une réduction significative du temps de séchage, car le durcissement se fait dans un four à une température plus élevée, généralement entre 160 et 200°C. Cela rend le procédé plus adapté aux chaînes de production à grande échelle, où l’efficacité est essentielle.
Cependant, la gestion d’une cabine de thermolaquage demande une attention particulière en ce qui concerne le maintien des équipements, le contrôle des conditions de température et d’humidité, et la surveillance de la qualité des pièces traitées. Une cabine mal entretenue ou mal régulée peut entraîner des défauts de finition, comme des irrégularités dans le revêtement ou des problèmes d’adhésion. Il est donc essentiel de suivre des procédures de maintenance rigoureuses et de former correctement les opérateurs pour garantir une qualité constante.
En résumé, la cabine de thermolaquage est un élément clé dans le processus de finition industrielle, offrant à la fois des avantages en termes de qualité de revêtement, de respect de l’environnement et d’efficacité de production. Son rôle dans la création de pièces métalliques est indispensable dans de nombreux secteurs industriels, faisant d’elle une technologie incontournable pour les applications modernes de peinture en poudre.
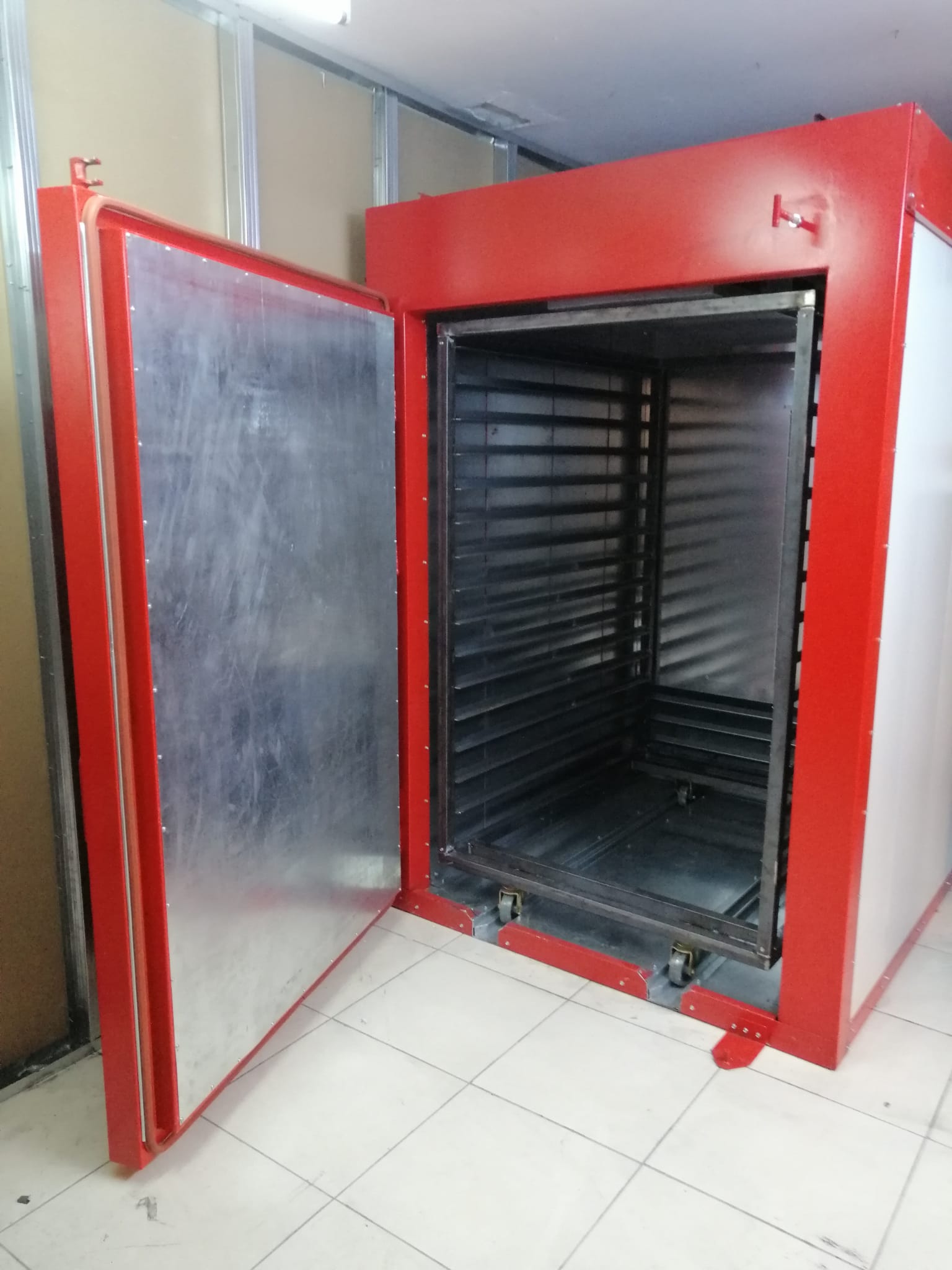
L’optimisation des cabines de thermolaquage passe par l’amélioration continue des équipements et des processus. Des technologies avancées, telles que les systèmes de contrôle automatisés, sont de plus en plus intégrées pour garantir une précision maximale. Ces systèmes permettent d’ajuster en temps réel la quantité de poudre appliquée, la vitesse de traitement des pièces et la température du four, assurant ainsi une uniformité parfaite du revêtement sur toutes les pièces traitées.
De plus, la conception de la cabine de thermolaquage évolue pour répondre aux défis modernes. Des cabines plus compactes et plus modulaires sont désormais disponibles, ce qui permet d’optimiser l’espace dans les ateliers et de réduire les coûts énergétiques. Les nouvelles générations de cabines intègrent également des technologies de récupération de chaleur, ce qui permet de réutiliser la chaleur excédentaire générée par le four pour préchauffer l’air entrant dans la cabine, réduisant ainsi la consommation d’énergie et les coûts d’exploitation.
Le marché des peintures en poudre a également connu des progrès considérables. De nos jours, il existe une grande variété de poudres, allant des formulations époxy, polyester, hybridées ou encore les poudres à base de fluoropolymères, chaque type ayant des propriétés spécifiques adaptées à des usages différents. Les formulations époxy, par exemple, sont particulièrement adaptées aux applications où une résistance chimique et mécanique est requise, tandis que les poudres polyester sont privilégiées pour les applications extérieures en raison de leur résistance aux intempéries et aux rayons UV.
L’une des grandes tendances dans le domaine du thermolaquage est l’augmentation de la demande pour des produits aux propriétés esthétiques particulières. Des finitions brillantes, mates, métalliques ou même des effets texturés comme le « hammertone » ou le « wrinkle » sont de plus en plus populaires. Les fabricants cherchent ainsi à offrir une personnalisation poussée pour répondre aux attentes des consommateurs en matière de design et de visuel tout en préservant la durabilité du revêtement.
Une autre avancée majeure dans le domaine du thermolaquage est la prise en compte accrue des exigences environnementales et de la durabilité. Outre la réduction des émissions de COV, les fabricants développent de plus en plus des peintures en poudre à base de ressources renouvelables et des procédés plus écologiques. Cela s’inscrit dans une tendance globale vers des pratiques industrielles plus vertes et responsables. De nombreux secteurs cherchent ainsi à certifier leurs processus et produits selon des normes environnementales comme ISO 14001 ou des labels écologiques spécifiques, ce qui influence fortement l’innovation dans les technologies de thermolaquage.
Enfin, la mise en œuvre du thermolaquage dans un cadre industriel nécessite également une gestion efficace des déchets. Bien que la poudre excédentaire puisse être récupérée et réutilisée, le procédé génère tout de même des déchets en termes de nettoyage de la cabine et des équipements. L’industrie met en place des solutions pour recycler ces déchets et réduire leur impact environnemental. Par exemple, les poudres de peinture usées peuvent être récupérées, filtrées et réutilisées dans d’autres applications, ou encore, des systèmes de filtration avancés permettent de capter les fines particules de peinture qui pourraient autrement être rejetées dans l’air.
La sécurité des opérateurs est également un enjeu majeur. Les cabines de thermolaquage modernes sont équipées de dispositifs de sécurité pour prévenir les risques d’incendie ou d’explosion, notamment en raison des poussières de peinture inflammables. Ces dispositifs incluent des systèmes de détection de gaz et de chaleur, ainsi que des systèmes de ventilation d’urgence. Les opérateurs doivent également être formés pour travailler en toute sécurité dans ces environnements, en portant des équipements de protection appropriés et en respectant les procédures de sécurité établies.
Dans l’ensemble, le thermolaquage continue de se développer en tant que procédé de finition polyvalent, efficace et respectueux de l’environnement. Les cabines de thermolaquage, en tant qu’éléments centraux de ce procédé, jouent un rôle essentiel dans la production de pièces métalliques de haute qualité. Grâce à l’innovation technologique et aux efforts constants pour améliorer la durabilité et l’efficacité des procédés, le thermolaquage reste un choix privilégié dans de nombreuses industries modernes, offrant une finition esthétique et performante tout en minimisant son impact environnemental.
En parallèle, l’intégration des technologies de l’Industrie 4.0 dans les cabines de thermolaquage est une tendance qui gagne en popularité. Les capteurs intelligents et les systèmes de surveillance à distance permettent de suivre en temps réel les conditions de fonctionnement de la cabine, tels que la température du four, l’humidité ambiante, la pression de l’air et la concentration de poudre. Ces données sont ensuite utilisées pour ajuster automatiquement les paramètres du processus, ce qui optimise l’efficacité et réduit les risques de défauts de finition. Les solutions basées sur l’Internet des objets (IoT) permettent ainsi une gestion proactive de la production et une maintenance préventive, réduisant les pannes imprévues et améliorant la productivité.
Le recours à des systèmes de gestion de la production (MES – Manufacturing Execution System) intégrés aux cabines de thermolaquage permet également d’améliorer la traçabilité et la gestion des lots de production. Grâce à l’enregistrement détaillé des paramètres du processus pour chaque pièce traitée, il est possible de garantir la qualité constante du produit fini. Ce type de gestion informatisée facilite également l’analyse des données de production pour identifier les tendances, optimiser les ressources et minimiser les gaspillages.
La digitalisation des cabines de thermolaquage s’accompagne d’une évolution de la formation des opérateurs. Ceux-ci peuvent désormais bénéficier d’outils de simulation et de réalité augmentée (AR) pour se former à l’utilisation des équipements. Cela permet d’améliorer la compréhension des différents paramètres de la cabine, d’accélérer le processus d’apprentissage et de réduire les erreurs humaines. La réalité augmentée peut également être utilisée pour assister les opérateurs pendant la production, en leur fournissant des instructions en temps réel directement sur leurs lunettes intelligentes, par exemple.
En outre, l’optimisation du processus de thermolaquage passe par l’amélioration des techniques de prétraitement des pièces avant leur revêtement. Le prétraitement, qui comprend le nettoyage et la préparation de la surface des pièces métalliques, est une étape essentielle pour garantir une bonne adhésion de la peinture en poudre. Les méthodes de prétraitement varient en fonction du type de métal, des conditions de production et des exigences de qualité. Les technologies de nettoyage comme le sablage, le dégraissage ou encore les bains chimiques sont utilisées pour éliminer les impuretés et créer une surface idéale pour l’application de la peinture. Les innovations dans ce domaine visent à réduire la consommation de produits chimiques et d’eau, en favorisant des solutions plus écologiques et plus efficaces.
Les cabines de thermolaquage ne se limitent pas aux métaux ferreux; elles sont également adaptées pour des matériaux comme l’aluminium, l’acier inoxydable, et même certains plastiques, à condition que ceux-ci puissent supporter les températures élevées du four. Cela étend considérablement les applications du thermolaquage dans des secteurs comme l’aérospatial, la fabrication de produits électroniques, ou même l’industrie du mobilier de bureau et des équipements extérieurs.
Une autre évolution notable concerne la réduction des coûts liés à l’utilisation des cabines de thermolaquage. La recherche sur de nouveaux matériaux de poudre plus abordables, couplée à l’amélioration des techniques de récupération et de réutilisation de la poudre excédentaire, permet de rendre le procédé plus économique, tout en maintenant un niveau élevé de performance et de qualité. Par ailleurs, les systèmes de filtration améliorés contribuent également à abaisser les coûts en prolongeant la durée de vie des filtres et en réduisant la fréquence des remplacements.
En termes d’innovation produit, de nouvelles générations de revêtements thermolaqués sont conçues pour répondre à des exigences toujours plus spécifiques. Par exemple, des peintures en poudre à haute résistance thermique, capables de supporter des températures extrêmes, sont utilisées pour des applications comme les composants de moteurs ou les pièces exposées à des conditions climatiques sévères. Il existe aussi des revêtements avec des propriétés antibactériennes ou antistatiques, qui sont de plus en plus demandés dans des domaines tels que la santé ou l’électronique. Ces innovations permettent d’élargir encore l’éventail des secteurs et des applications susceptibles de bénéficier du thermolaquage.
Le thermolaquage se distingue ainsi comme une solution de plus en plus incontournable dans le monde industriel moderne. Grâce à son efficacité, sa durabilité et ses avantages écologiques, il est en passe de se généraliser dans de nouveaux secteurs tout en offrant une finition esthétique et fonctionnelle sans compromis. En ce sens, les cabines de thermolaquage, au cœur de ce processus, continueront d’évoluer pour répondre aux besoins croissants de personnalisation, de durabilité, de sécurité et de respect de l’environnement.
Étuve Thermolaquage
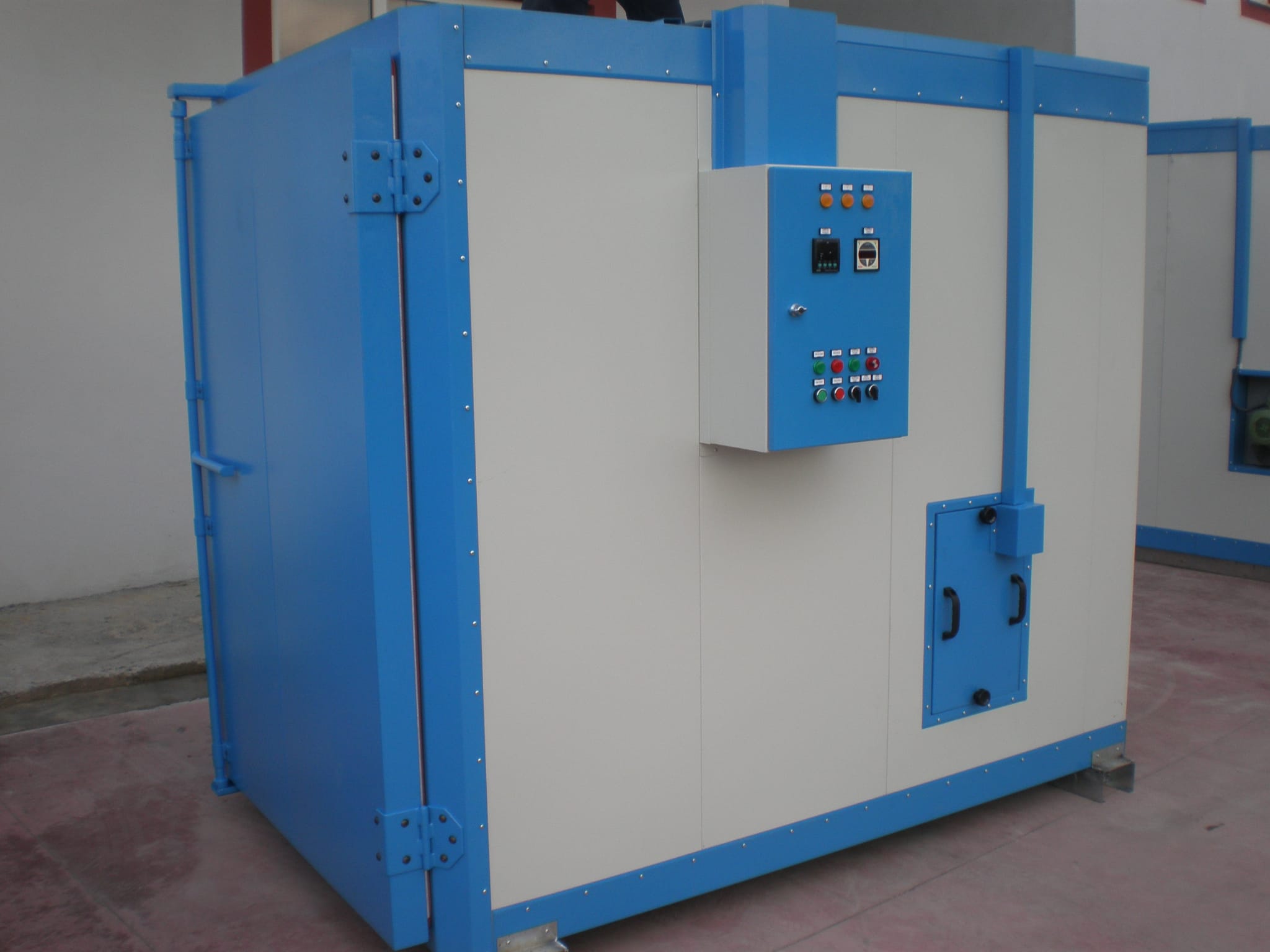
L’étuve de thermolaquage, également appelée four de cuisson ou four de polymérisation, est un élément essentiel du processus de thermolaquage, jouant un rôle clé dans la transformation de la poudre appliquée en un revêtement solide et durable. Une fois que la pièce est recouverte de poudre de peinture, l’étuve assure le durcissement de cette couche, en la chauffant à une température précise pour qu’elle fonde et se lie chimiquement au substrat métallique. Ce processus est crucial pour garantir que le revêtement présente les propriétés souhaitées, telles que la résistance aux chocs, la durabilité, la résistance à la chaleur et la stabilité chimique.
Les étuves de thermolaquage fonctionnent généralement à des températures comprises entre 160 et 200 °C, en fonction du type de peinture utilisée. Une fois la pièce placée à l’intérieur du four, la chaleur fait fondre la poudre, qui se transforme en un film lisse et homogène. Ce film durcit en refroidissant, formant une couche de peinture robuste et uniforme sur la surface de la pièce traitée. Le temps de cuisson dépend de la taille et de la composition de la pièce, ainsi que de la poudre de peinture utilisée. Ce processus est relativement rapide par rapport aux méthodes de peinture liquide traditionnelles, et il ne nécessite pas de temps de séchage long, ce qui améliore l’efficacité de la production.
Les étuves peuvent être équipées de diverses technologies pour optimiser le processus de polymérisation. Par exemple, certains fours utilisent des systèmes de convection forcée pour assurer une répartition uniforme de la chaleur dans la chambre de cuisson. Cela permet d’éviter les zones froides ou chaudes, garantissant que chaque partie de la pièce soit traitée de manière homogène. D’autres étuves sont équipées de systèmes de contrôle de la température et de la ventilation qui permettent de réguler précisément les conditions de cuisson, offrant ainsi un contrôle optimal du processus.
Il existe également des étuves à tunnel, où les pièces traversent le four de manière continue, ce qui est particulièrement adapté aux chaînes de production à grande échelle. Dans ce type de four, les pièces sont transportées par un convoyeur à travers une zone de chauffage, où elles sont exposées à des températures élevées pendant une période déterminée. Ces étuves sont généralement plus longues et plus complexes, mais elles permettent une production de masse rapide tout en maintenant une qualité uniforme des revêtements.
Une autre variation des étuves de thermolaquage est l’étuve infrarouge, qui utilise des lampes à infrarouge pour chauffer la surface de la pièce rapidement. Les étuves à infrarouge sont particulièrement efficaces pour les petites séries ou les applications nécessitant une montée en température très rapide. Elles permettent un contrôle précis de la température de surface, ce qui peut être avantageux pour les matériaux sensibles à la chaleur ou lorsque des couches de peinture très fines sont appliquées.
Les étuves modernes sont également conçues pour être écoénergétiques. L’une des préoccupations majeures dans l’industrie du thermolaquage est la consommation d’énergie liée au chauffage des grandes chambres de cuisson. De nouvelles technologies, comme l’utilisation de récupération de chaleur, permettent de capter et de réutiliser la chaleur excédentaire générée pendant le processus de cuisson. Cela contribue à réduire la consommation énergétique globale et les coûts opérationnels, tout en améliorant l’efficacité du procédé.
En ce qui concerne l’entretien des étuves de thermolaquage, il est essentiel de maintenir une température uniforme et stable, ce qui nécessite un contrôle constant du système de chauffage et des éléments de ventilation. Les fourneaux doivent être régulièrement nettoyés pour éliminer les résidus de peinture et de poussière, afin d’éviter toute contamination croisée entre les couleurs ou des anomalies dans les couches de peinture appliquées. Les joints et les portes doivent également être inspectés pour garantir l’étanchéité et éviter les fuites de chaleur, qui pourraient compromettre l’efficacité du processus.
Les étuves modernes sont aussi équipées de systèmes de surveillance avancés. Ces systèmes peuvent inclure des capteurs de température et d’humidité qui permettent aux opérateurs de suivre en temps réel les conditions du four et d’ajuster les paramètres si nécessaire. Cela assure un contrôle précis et constant de la cuisson, garantissant une qualité uniforme pour chaque lot de production.
L’utilisation de l’étuve de thermolaquage est donc essentielle pour assurer la finition et la durabilité des produits. Elle permet non seulement de garantir la qualité des revêtements, mais aussi d’améliorer l’efficacité de la production et de réduire les coûts énergétiques. Le développement technologique continue d’optimiser les performances des étuves, contribuant ainsi à l’avancement de l’industrie du thermolaquage, en offrant des solutions plus rapides, plus écologiques et plus rentables tout en maintenant des standards élevés de qualité.
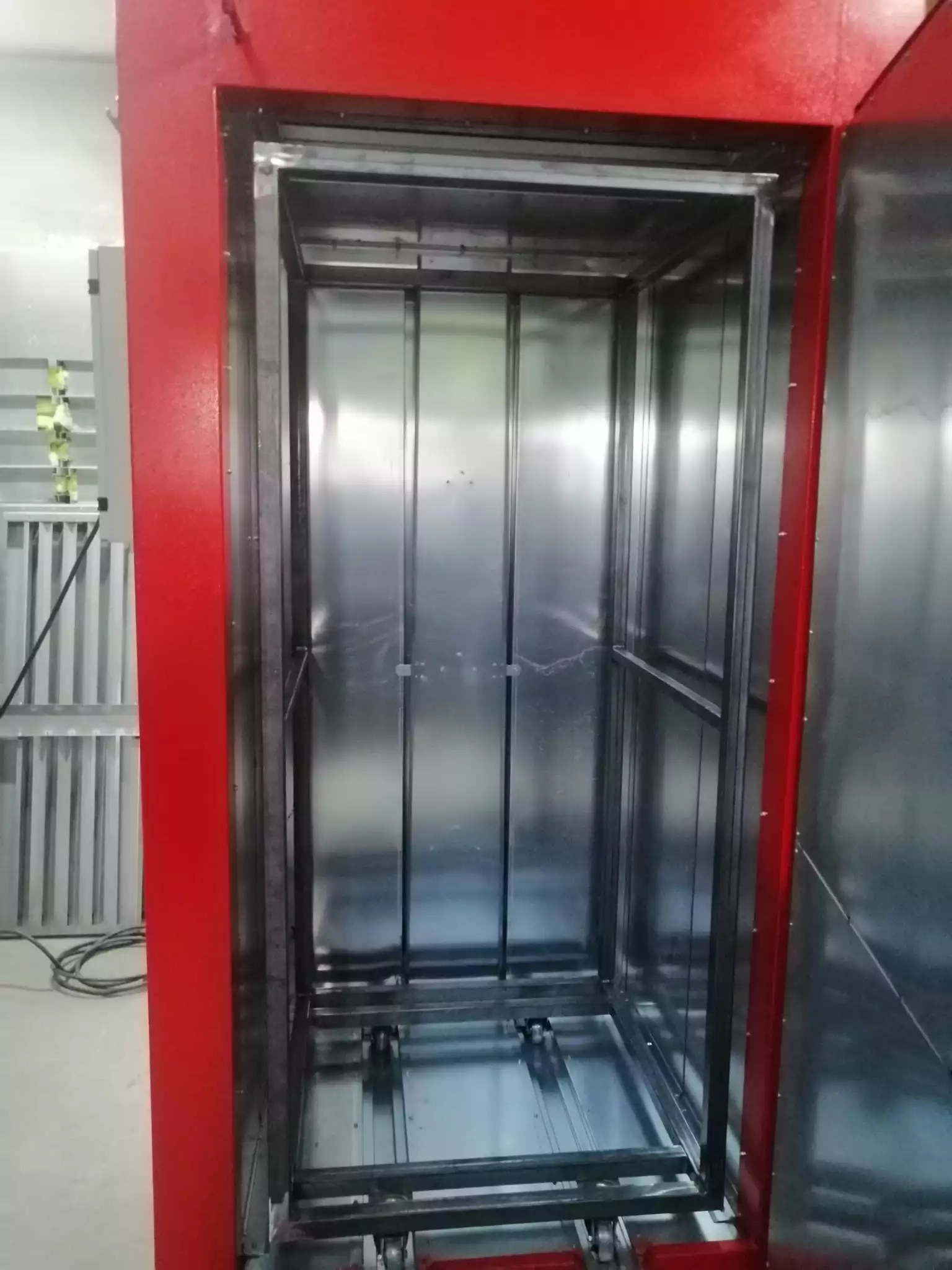
L’évolution des étuves de thermolaquage s’accompagne également d’une tendance vers une personnalisation accrue des équipements en fonction des besoins spécifiques des utilisateurs. Par exemple, des étuves à température contrôlée avec des capacités de préchauffage ou de refroidissement rapide peuvent être adaptées pour des pièces nécessitant un traitement thermique particulier. Certaines applications industrielles requièrent des cycles de cuisson très spécifiques pour obtenir des propriétés mécaniques ou esthétiques particulières, comme des revêtements à haute résistance thermique ou des finitions spéciales.
Les étuves peuvent également être équipées de systèmes de contrôle de l’atmosphère interne pour gérer les conditions de cuisson en fonction des exigences des matériaux ou des types de revêtements appliqués. Par exemple, pour des applications sensibles, certains processus peuvent nécessiter un contrôle précis du niveau d’oxygène ou de l’humidité dans la chambre de cuisson. Ces ajustements permettent de préserver la qualité du revêtement, d’éviter des effets indésirables comme la formation de bulles ou de fissures et d’assurer une bonne adhésion de la peinture à la surface du métal.
Les nouvelles générations d’étuves sont aussi de plus en plus orientées vers des solutions automatisées. Grâce à des systèmes de robotisation et à des logiciels de gestion de la production, il est désormais possible de gérer de manière autonome le chargement et le déchargement des pièces, le suivi des paramètres de cuisson, ainsi que le contrôle de la qualité en temps réel. Les systèmes automatisés réduisent les risques d’erreur humaine, augmentent la constance des résultats et permettent une intégration plus facile dans des lignes de production automatisées, contribuant ainsi à l’optimisation des processus industriels.
Un autre domaine où l’innovation joue un rôle clé dans les étuves de thermolaquage est la réduction de l’empreinte écologique du procédé. En plus des systèmes de récupération de chaleur, de nouveaux matériaux réfractaires à faible émission de chaleur et des technologies de cuisson à faible consommation d’énergie sont en cours de développement pour améliorer encore l’efficacité énergétique des étuves. L’intégration de panneaux solaires ou d’autres sources d’énergie renouvelable pour alimenter les étuves constitue également une piste pour rendre le processus de thermolaquage plus vert.
Il convient aussi de mentionner la compatibilité croissante des étuves de thermolaquage avec des poudres de peinture plus respectueuses de l’environnement. Les formulations à base de résines biodégradables ou de matériaux recyclés deviennent de plus en plus courantes, et les étuves sont conçues pour être adaptées à ces nouveaux types de poudres, qui peuvent avoir des exigences de cuisson différentes. Cela nécessite une flexibilité accrue des équipements de cuisson, ainsi qu’une capacité à ajuster finement la température et le temps de cuisson en fonction des propriétés spécifiques des matériaux.
La durée de vie des équipements et la minimisation des coûts d’entretien sont des considérations essentielles dans l’achat d’une étuve de thermolaquage. En raison de l’intensité de l’utilisation des étuves dans le processus de thermolaquage, il est crucial que ces équipements soient robustes et nécessitent peu de maintenance. Pour ce faire, les fabricants d’étuves développent des systèmes de protection contre l’usure, tels que des revêtements réfractaires pour les parois internes du four ou des dispositifs de nettoyage automatiques pour éviter l’accumulation de résidus de peinture, ce qui peut altérer les performances du four. Ces innovations prolongent la durée de vie des équipements tout en réduisant les coûts liés à leur entretien.
La gestion des émissions de gaz et de particules est une autre préoccupation croissante dans les étuves de thermolaquage modernes. Les systèmes de filtration et de purification de l’air jouent un rôle essentiel pour capter les vapeurs et les particules de peinture qui sont libérées pendant la cuisson. Ces systèmes contribuent à maintenir un environnement de travail plus sûr et respectueux de l’environnement, en empêchant la propagation de substances potentiellement dangereuses dans l’atmosphère et en minimisant l’impact écologique de l’opération.
Pour répondre aux besoins de flexibilité, certaines étuves sont équipées de configurations modulaires permettant une personnalisation en fonction des tailles et des types de pièces à traiter. Par exemple, pour des pièces de tailles variables ou des lots de production spécifiques, une étuve modulaire peut être ajustée en termes de capacité et de configuration interne. Ce type d’adaptabilité permet d’optimiser l’utilisation de l’espace et de réduire le gaspillage énergétique, en limitant la taille de la chambre de cuisson à celle strictement nécessaire pour traiter un lot donné.
Les étuves à haute technologie intégrant des interfaces utilisateurs intelligentes permettent également un meilleur suivi et une gestion facilitée des processus. Par exemple, les écrans tactiles et les logiciels de contrôle de processus offrent une vue en temps réel de tous les paramètres de cuisson, tels que la température, l’humidité, la durée et les cycles de refroidissement. Ces outils peuvent être connectés à des bases de données centrales permettant un reporting détaillé, une gestion de la production optimisée et un contrôle qualité rigoureux à chaque étape du processus de thermolaquage.
En résumé, l’étuve de thermolaquage, en tant qu’élément clé du processus de peinture en poudre, a connu de nombreuses innovations visant à améliorer l’efficacité, la sécurité, la durabilité et l’impact environnemental du procédé. Ces avancées technologiques permettent non seulement d’optimiser la qualité des revêtements, mais aussi de rendre les processus de production plus rapides, plus rentables et plus respectueux de l’environnement. Dans un marché toujours plus compétitif et soucieux de la qualité, l’étuve moderne est donc un atout majeur pour toute ligne de production de thermolaquage.
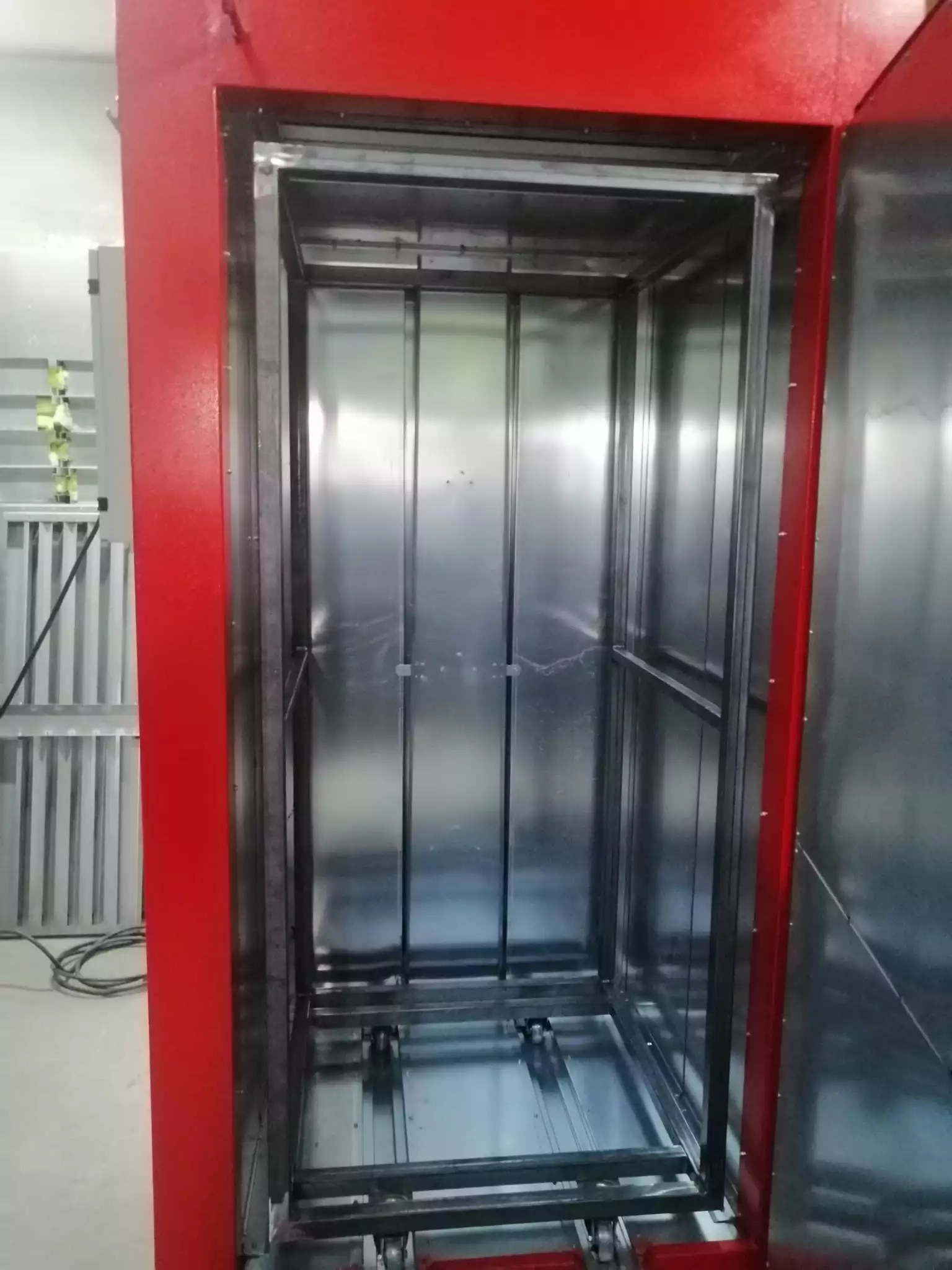
L’optimisation des étuves de thermolaquage ne se limite pas seulement à des améliorations technologiques sur le plan énergétique ou environnemental. Elle inclut également une meilleure gestion des coûts de production, ce qui est un enjeu crucial dans les secteurs industriels où la compétitivité et les marges sont souvent serrées. L’introduction de logiciels de gestion avancée permet une analyse en temps réel des performances des étuves, identifiant ainsi les zones susceptibles de nécessiter des améliorations ou des ajustements pour réduire les coûts d’exploitation tout en maintenant la qualité des produits. Par exemple, en détectant des anomalies de température ou de flux d’air, ces systèmes peuvent alerter les opérateurs pour effectuer des ajustements avant que des problèmes majeurs ne surviennent, ce qui aide à éviter des pannes coûteuses ou des pertes de production.
Le rôle de l’étuve dans le processus de thermolaquage va au-delà de la simple polymérisation des peintures en poudre; elle joue également un rôle stratégique dans la gestion des volumes de production. Les étuves modernes sont capables de traiter des pièces en continu grâce à des systèmes de convoyeurs et des étuves à tunnel, ce qui permet de maximiser la capacité de production tout en minimisant les périodes d’arrêt. Ces systèmes automatisés de convoyage assurent un passage fluide et rapide des pièces tout en maintenant des températures constantes et bien régulées, ce qui garantit une qualité homogène du revêtement sur chaque pièce traitée.
Les nouvelles étuves de thermolaquage, en particulier celles utilisées dans les grandes lignes de production, sont également conçues pour être compatibles avec des systèmes de production flexibles. Cela permet aux fabricants d’ajuster rapidement les paramètres en fonction des types de pièces à traiter ou des couleurs et finitions requises. De cette manière, le processus de thermolaquage devient plus adaptable et capable de répondre à des demandes de production variables sans perte d’efficacité.
Dans cette optique, certains fabricants d’étuves mettent en place des processus de maintenance prédictive basés sur des technologies IoT (Internet of Things) pour suivre l’état des équipements de manière continue. En surveillant des indicateurs clés de performance (KPI) tels que la température, l’humidité, le débit d’air et même les vibrations, ces systèmes peuvent anticiper les problèmes potentiels, signaler les anomalies et planifier les interventions de maintenance avant qu’un dysfonctionnement majeur ne survienne. Cela permet non seulement de réduire les coûts de réparation, mais aussi de prolonger la durée de vie des équipements et d’éviter les interruptions imprévues de la production.
Un autre aspect crucial des étuves modernes est la conformité avec les normes de sécurité et de réglementation en vigueur. Les fabricants de thermolaquage doivent respecter des normes strictes concernant les émissions, la sécurité au travail et la gestion des substances potentiellement dangereuses. Par exemple, les étuves sont souvent équipées de systèmes de filtration haute performance pour capturer les gaz et particules produits lors de la cuisson de la peinture, notamment les COV (composés organiques volatils). De plus, pour prévenir les risques d’incendie, des systèmes de détection et d’extinction automatique sont intégrés, notamment en raison de la nature inflammable des poudres de peinture et des gaz produits pendant le processus. Ces mesures sont d’autant plus cruciales dans les industries où la sécurité des travailleurs et la protection de l’environnement sont des priorités absolues.
Avec l’augmentation de la demande pour des revêtements plus performants, les étuves de thermolaquage sont également conçues pour gérer une gamme plus large de poudres, incluant des formulations spéciales telles que les poudres thermoplastiques ou les poudres à base de polymères plus résistants aux températures extrêmes. Ces types de poudres peuvent nécessiter des températures de cuisson différentes ou des conditions d’atmosphère ajustées dans l’étuve, ce qui souligne la nécessité de flexibilité et de précision dans les équipements de cuisson. Les étuves de nouvelle génération, équipées de technologies de contrôle avancées, sont capables d’adapter rapidement ces paramètres pour s’adapter à de nouveaux matériaux ou formulations de peinture, tout en garantissant des résultats homogènes et de haute qualité.
L’innovation continue dans le domaine des étuves de thermolaquage ne concerne pas uniquement les performances techniques, mais aussi la gestion des espaces de production. De plus en plus de fabricants optent pour des étuves à faible encombrement et modulaires, qui peuvent être intégrées dans des espaces de travail plus restreints sans sacrifier la capacité de production ou la qualité des revêtements. Ces systèmes compacts sont conçus pour offrir une flexibilité maximale, notamment en permettant des extensions ou des modifications faciles selon les besoins spécifiques de production.
Le recyclage et la réutilisation des matériaux jouent également un rôle important dans l’évolution des étuves. Le processus de thermolaquage génère inévitablement de la poudre excédentaire qui, dans les modèles traditionnels, est souvent gaspillée. Les étuves modernes sont désormais dotées de systèmes permettant de récupérer et de réutiliser cette poudre excédentaire, ce qui réduit les déchets, les coûts des matériaux et les impacts environnementaux. Ces systèmes incluent des dispositifs de filtration et de collecte de la poudre excédentaire, qui permettent non seulement de récupérer la poudre de manière efficace mais aussi d’éviter sa dispersion dans l’environnement, réduisant ainsi les risques de contamination de l’air.
Dans un contexte où l’industrie évolue constamment vers des pratiques plus responsables et plus durables, l’étuve de thermolaquage devient un instrument clé dans la transformation des processus de fabrication. Grâce à l’adoption de technologies plus intelligentes, plus écologiques et plus économes en énergie, elle contribue à améliorer la compétitivité des entreprises tout en réduisant leur empreinte écologique. L’étuve ne se contente pas de cuire la peinture en poudre, elle devient un moteur d’innovation dans un secteur en pleine transformation.
Fours de Polymérisation
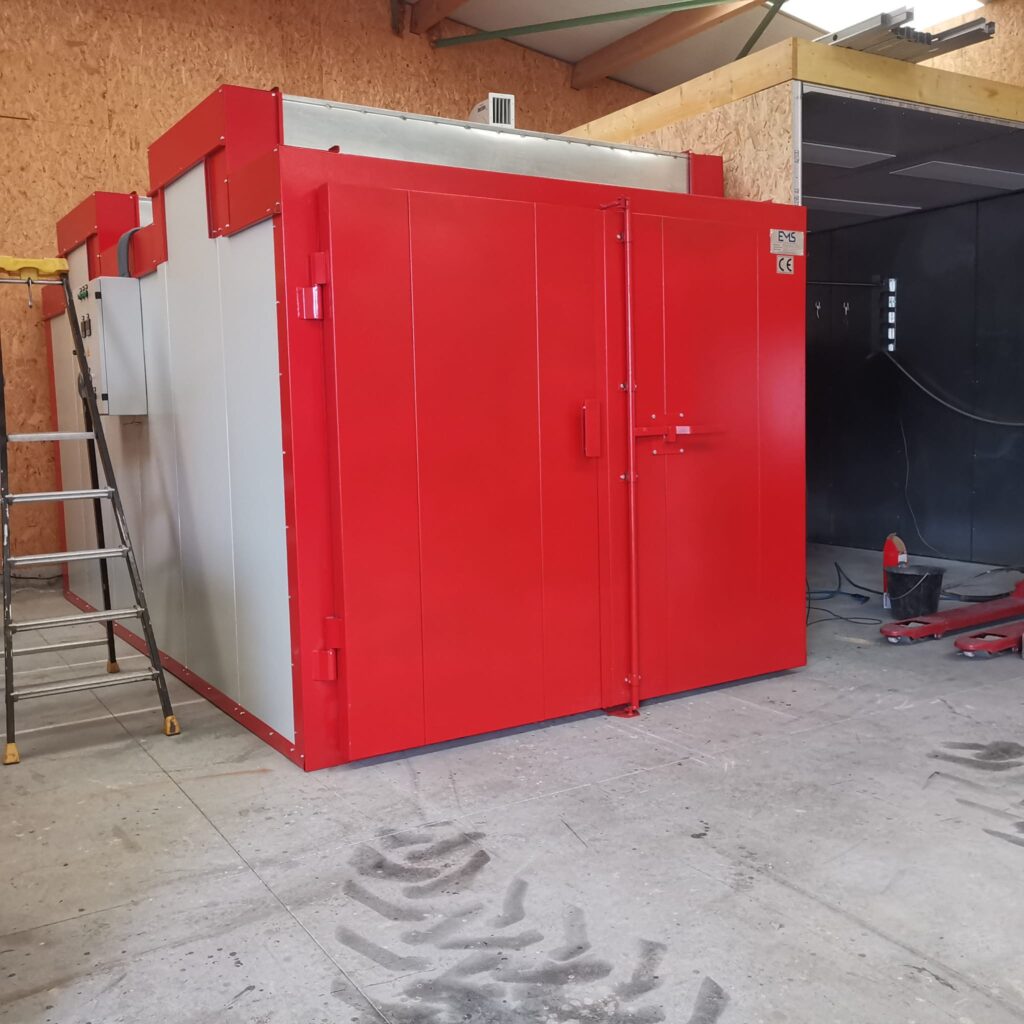
Les fours de polymérisation, également appelés fours de cuisson ou étuves de polymérisation, jouent un rôle fondamental dans le processus de thermolaquage. Leur fonction principale est de durcir la peinture en poudre après qu’elle ait été appliquée sur une surface métallique. Cette étape de cuisson, ou polymérisation, est essentielle pour garantir la durabilité, la résistance et l’adhésion de la peinture sur les pièces traitées. Lors de ce processus, la poudre de peinture, qui est initialement un matériau solide, fond et se lie chimiquement à la surface du métal, formant ainsi un revêtement solide et homogène.
Les fours de polymérisation fonctionnent généralement à des températures comprises entre 160 et 200°C, et le temps de cuisson varie en fonction de plusieurs paramètres, tels que la taille des pièces, la nature du revêtement et les spécifications du fabricant de la peinture. Une fois que la peinture a fondu et a formé un film uniforme, le four maintient cette température pendant un certain temps afin de permettre la réticulation chimique des polymères et garantir que le revêtement atteigne sa résistance et ses propriétés finales.
Le principe de base des fours de polymérisation repose sur l’utilisation d’une chaleur contrôlée pour assurer une cuisson homogène des pièces. Les fours peuvent être de différentes conceptions, notamment les modèles à convection, infrarouges ou hybrides, chacun ayant ses avantages et étant adapté à des besoins spécifiques. Par exemple, les fours à convection utilisent des ventilateurs pour faire circuler l’air chaud à l’intérieur de la chambre, assurant ainsi une répartition uniforme de la chaleur et évitant les zones froides. Les fours à infrarouge, quant à eux, utilisent des lampes spéciales pour chauffer directement la surface des pièces, ce qui permet une montée en température plus rapide et plus ciblée.
Les fours de polymérisation modernes sont souvent équipés de systèmes de contrôle avancés pour assurer une gestion précise du processus de cuisson. Des capteurs de température et des régulateurs permettent de maintenir la température idéale tout au long du cycle de cuisson, tandis que des dispositifs de surveillance peuvent alerter les opérateurs en cas de dérive des paramètres ou de déviation des conditions de cuisson. Ces systèmes garantissent non seulement une qualité uniforme du revêtement, mais aussi une sécurité accrue, en réduisant les risques de surchauffe ou de dégradation de la peinture.
Une innovation importante dans les fours de polymérisation est la possibilité de gérer la consommation d’énergie de manière plus efficace. Les fabricants de fours développent des solutions pour récupérer la chaleur excédentaire générée durant le processus de cuisson. Cela permet de réduire les coûts énergétiques tout en maintenant des conditions de cuisson optimales. Par exemple, certains modèles de fours intègrent des systèmes de récupération thermique qui captent la chaleur excédentaire et la réinjectent dans le processus de cuisson, améliorant ainsi l’efficacité énergétique du four.
De plus en plus, les fours de polymérisation sont conçus pour être plus respectueux de l’environnement. Les préoccupations écologiques, notamment la réduction des émissions de CO2 et des particules en suspension dans l’air, ont conduit au développement de systèmes de filtration de l’air sophistiqués. Ces systèmes captent les gaz et les particules générées pendant la cuisson, assurant un environnement de travail plus sain et limitant l’impact environnemental du processus. De même, les fabricants d’équipements cherchent à minimiser la consommation de ressources comme l’énergie et l’eau, tout en optimisant le processus de polymérisation pour rendre le thermolaquage plus durable.
Les fours de polymérisation sont également devenus plus flexibles et modulaires pour répondre aux besoins variés des utilisateurs. Les modèles modulaires permettent d’adapter la taille et la configuration du four en fonction des exigences de production spécifiques. Par exemple, les entreprises peuvent opter pour des chambres de cuisson plus grandes ou plus petites, ou choisir des configurations qui permettent de traiter des pièces de tailles diverses. Cette flexibilité permet aux utilisateurs de maximiser l’efficacité de leur production en fonction des types de pièces traitées, tout en optimisant les coûts de production.
Dans les environnements de production de grande échelle, les fours de polymérisation à tunnel sont souvent utilisés. Ces systèmes permettent de traiter les pièces en continu grâce à un convoyeur, ce qui permet d’optimiser les flux de production et d’augmenter la capacité de traitement. Les pièces sont transportées à travers le four en un temps déterminé, et chaque zone du four est calibrée pour garantir que la température est uniformément distribuée sur toutes les pièces traitées. Cela réduit les temps d’arrêt, accélère le processus de production et permet de traiter de grandes quantités de pièces de manière homogène.
En revanche, pour des productions plus petites ou des applications spécifiques, les fours de polymérisation à circulation d’air peuvent offrir plus de contrôle et de flexibilité. Ces fours, également appelés étuves à convection forcée, sont particulièrement adaptés pour des lots de production de tailles variées et pour des traitements de pièces plus délicates. Leur capacité à ajuster précisément les paramètres de température et de ventilation permet de s’adapter à des produits plus complexes ou des formulations de peinture spécialisées.
Le processus de polymérisation étant crucial pour garantir la durabilité et la résistance des revêtements, l’entretien des fours de polymérisation est une étape importante dans le maintien de leur performance. Un entretien régulier des éléments chauffants, des ventilateurs, des systèmes de filtration et des contrôles de température est essentiel pour garantir que le four fonctionne de manière optimale et que les pièces traitées soient uniformément polymérisées. En outre, les procédures de maintenance préventive permettent de détecter et de résoudre les problèmes avant qu’ils ne deviennent critiques, évitant ainsi des arrêts de production coûteux.
L’optimisation continue des fours de polymérisation permet d’améliorer non seulement la qualité des revêtements mais aussi la rentabilité des processus de thermolaquage. Grâce à l’introduction de technologies plus efficaces, plus écologiques et plus rentables, les entreprises peuvent produire des pièces de haute qualité tout en réduisant leur consommation énergétique, leurs coûts opérationnels et leur impact environnemental. Ces avancées, combinées à l’amélioration des technologies de contrôle et de maintenance, assurent un avenir prometteur pour les fours de polymérisation et leur rôle dans l’industrie du thermolaquage.
L’évolution des fours de polymérisation continue de s’orienter vers l’intégration de technologies de plus en plus intelligentes et connectées. Les systèmes de contrôle à distance, associés à l’Internet des objets (IoT), permettent désormais de surveiller et d’ajuster les paramètres de cuisson en temps réel à partir de n’importe quel terminal, qu’il s’agisse d’une tablette, d’un ordinateur ou même d’un smartphone. Ces systèmes intelligents offrent une visibilité complète sur le processus de polymérisation, avec des alertes automatiques pour toute variation des conditions de cuisson qui pourrait affecter la qualité du revêtement. Cette capacité à suivre les performances du four et à intervenir immédiatement permet de maintenir un haut niveau de qualité, tout en minimisant les erreurs humaines et les interruptions de production.
Les progrès dans la numérisation des fours de polymérisation permettent également de mieux gérer les cycles de production. Des logiciels de gestion de production avancés sont désormais intégrés aux équipements pour optimiser les flux de travail et maximiser les rendements. Par exemple, ces logiciels peuvent planifier automatiquement les cycles de cuisson en fonction des besoins spécifiques des pièces à traiter, ajustant les températures et les durées de cuisson selon la taille, la forme et le type de matériau. Cela permet d’augmenter la productivité tout en réduisant le gaspillage d’énergie et de ressources.
Les fabricants de fours de polymérisation s’efforcent également de répondre aux exigences des industries de plus en plus soucieuses de la durabilité et des performances écologiques. Cela inclut l’intégration de systèmes de filtration avancés, comme des filtres à charbon actif ou des systèmes à haute efficacité pour éliminer les émissions de gaz nocifs ou de poussières qui se produisent pendant le processus de cuisson. Ces technologies réduisent non seulement les risques pour la santé des travailleurs, mais elles permettent aussi aux entreprises de se conformer aux réglementations environnementales strictes qui régissent les émissions industrielles.
L’optimisation de la consommation énergétique dans les fours de polymérisation est une priorité continue, en raison de la consommation élevée d’énergie liée aux besoins de chauffage à haute température sur de longues périodes. À cet égard, des technologies de pointe telles que les systèmes de préchauffage à haute efficacité et les chambres de cuisson isolées sont utilisées pour minimiser les pertes de chaleur et réduire la consommation d’énergie. L’isolation thermique, par exemple, permet de maintenir une température stable à l’intérieur du four tout en réduisant les coûts de chauffage. De plus, les systèmes de préchauffage assurent que la température idéale est atteinte plus rapidement, ce qui permet de raccourcir les temps de cuisson et, ainsi, d’augmenter l’efficacité énergétique globale.
Les avancées dans les matériaux utilisés pour les fours de polymérisation contribuent également à leur performance et à leur longévité. L’utilisation de matériaux réfractaires de haute qualité, qui résistent mieux aux températures extrêmes, et l’amélioration des revêtements intérieurs des fours augmentent la durée de vie de ces équipements. Les matériaux réfractaires de dernière génération permettent de maintenir une température stable et uniforme tout en réduisant les coûts liés à la maintenance et aux réparations.
En plus des avancées technologiques, la flexibilité des fours de polymérisation est un autre aspect de plus en plus important pour les industries. En effet, les besoins de production varient selon les types de pièces traitées, les finitions demandées et les cycles de production. Les modèles modulaires permettent aux entreprises d’adapter la taille et la configuration du four en fonction de la production, tout en maintenant une haute qualité de cuisson. Ce type de flexibilité permet aux entreprises de s’ajuster plus rapidement aux demandes du marché, tout en optimisant l’utilisation de l’espace et des ressources.
Dans le même ordre d’idées, les options de personnalisation des fours de polymérisation permettent aux utilisateurs de répondre à des besoins spécifiques en matière de revêtements. Par exemple, pour des applications spécifiques, les fabricants peuvent proposer des solutions qui intègrent des zones de chauffage différenciées, ou des fours capables de gérer des températures très précises pour des formulations de peinture sensibles. Ce niveau de personnalisation permet aux utilisateurs de créer des conditions de cuisson parfaitement adaptées à des matériaux particuliers, tout en garantissant des résultats constants et de haute qualité.
Un autre domaine d’innovation est celui de la réduction des émissions de gaz à effet de serre, un sujet particulièrement pertinent dans l’industrie moderne. Les entreprises de fabrication mettent en place des technologies de capture et de recyclage des gaz pour limiter les émissions polluantes issues de la cuisson des peintures. Les systèmes de récupération thermique contribuent également à cette réduction en permettant de recycler la chaleur excédentaire générée lors de la cuisson. Par ailleurs, l’utilisation de peintures et de résines moins polluantes et plus écologiques est en plein essor, ce qui, associé aux technologies de filtration et de gestion thermique, permet de rendre le processus de polymérisation plus vert.
La maintenance des fours de polymérisation devient aussi de plus en plus prédictive grâce aux capteurs intégrés et aux systèmes de surveillance en temps réel. Les données collectées par ces capteurs permettent de suivre l’état des composants critiques du four (chauffage, ventilation, isolation) et de prédire les éventuelles défaillances avant qu’elles ne surviennent. En prévoyant les réparations et les remplacements nécessaires, les entreprises peuvent réduire les interruptions de production et optimiser la durée de vie des équipements, ce qui se traduit par des économies substantielles à long terme.
Les fours de polymérisation ont donc évolué bien au-delà de leur simple fonction de cuisson. Grâce à des améliorations en termes d’efficacité énergétique, de flexibilité, de connectivité et de durabilité, ils représentent désormais un pilier de l’industrie moderne, contribuant non seulement à la qualité des revêtements mais aussi à la rentabilité et à la compétitivité des entreprises. L’intégration de technologies intelligentes et d’innovations écologiques transforme le paysage du thermolaquage et permet aux entreprises de répondre aux défis du 21e siècle tout en maintenant des standards élevés de performance et de responsabilité environnementale.
Les tendances émergentes dans les fours de polymérisation continuent de souligner l’importance de l’innovation et de l’adaptation aux exigences spécifiques des différents secteurs industriels. Parmi ces évolutions, l’intégration de l’intelligence artificielle (IA) et de l’apprentissage automatique (machine learning) devient de plus en plus courante. Ces technologies permettent d’optimiser non seulement la gestion des cycles de cuisson, mais aussi la prédiction des besoins de maintenance, le contrôle de la qualité du revêtement et la réduction des erreurs humaines. Par exemple, des systèmes basés sur l’IA peuvent analyser les données recueillies par les capteurs pour ajuster les paramètres du four en temps réel, en fonction des fluctuations de température, d’humidité ou des variations de la formulation de la peinture. Cela permet une adaptation continue des conditions de cuisson pour obtenir un revêtement parfait à chaque cycle.
L’intégration de l’automatisation dans les processus de cuisson des fours de polymérisation est également un autre facteur clé dans l’optimisation de la production. Les systèmes de gestion automatisée permettent aux opérateurs de programmer des cycles de cuisson précis sans intervention manuelle, ce qui réduit le risque d’erreurs et améliore la cohérence des résultats. En outre, l’automatisation des processus permet de mieux gérer le flux de production et de réduire les délais de production, ce qui est crucial pour les industries où la demande est élevée et les délais serrés.
Les systèmes de monitoring en ligne, couplés à des plateformes cloud, facilitent également la gestion des fours de polymérisation. Les fabricants peuvent désormais accéder à des informations détaillées sur les performances des équipements à distance, leur permettant d’intervenir rapidement en cas de dysfonctionnement ou d’optimiser les processus sans avoir besoin d’une présence physique. Ces plateformes offrent des fonctionnalités telles que la visualisation en temps réel des paramètres critiques, l’analyse des tendances de performance et des recommandations sur les actions à entreprendre pour améliorer l’efficacité du four.
Par ailleurs, la maintenance prédictive, un domaine de plus en plus développé, permet de minimiser les temps d’arrêt et d’optimiser la durée de vie des fours. Grâce aux capteurs et aux systèmes IoT, chaque composant du four, qu’il s’agisse des éléments chauffants, des ventilateurs, ou des systèmes de filtration, peut être surveillé en continu. L’analyse de ces données permet d’identifier des signes précoces de défaillance, permettant ainsi d’effectuer des interventions avant qu’un problème majeur ne survienne. Ce type de maintenance réduit non seulement les coûts associés aux réparations imprévues mais augmente aussi l’efficacité globale du processus de production.
En outre, les progrès dans le domaine des matériaux pour la construction des fours de polymérisation permettent de réduire l’usure des équipements et d’améliorer leur performance thermique. Des matériaux plus légers et plus résistants à haute température, tels que les alliages métalliques spéciaux ou les céramiques avancées, permettent de fabriquer des fours plus durables et plus efficaces. Ces matériaux, associés à des revêtements anti-corrosion, augmentent la longévité des équipements tout en offrant une meilleure rétention thermique. Cela permet non seulement d’économiser de l’énergie, mais aussi d’améliorer la stabilité et la fiabilité du processus de cuisson.
Une autre tendance importante est la conception de fours de polymérisation de plus en plus modulaires et adaptés aux espaces de production flexibles. Ces modèles sont conçus pour s’adapter facilement à des configurations de production variables. Par exemple, un four peut être agrandi ou réduit en fonction des besoins de l’usine, ou bien adapté à des lignes de production spécifiques. Cette flexibilité est particulièrement avantageuse pour les entreprises ayant des volumes de production fluctuants ou traitant une grande variété de pièces de tailles et de formes différentes. La possibilité de personnaliser le four en fonction des besoins spécifiques permet aux entreprises d’optimiser l’espace de production, tout en maintenant une efficacité maximale.
Dans le domaine de la production de petites séries ou de produits personnalisés, les fours de polymérisation peuvent être équipés de technologies permettant une gestion plus fine des paramètres de cuisson. Les solutions de cuisson sur mesure permettent d’adapter précisément la température, la durée du cycle et les variations d’humidité en fonction des caractéristiques spécifiques des produits. Ces fours de polymérisation sont ainsi capables de traiter des matériaux innovants ou de nouvelles formulations de peintures sans compromettre la qualité du revêtement.
Le marché des fours de polymérisation se dirige également vers des solutions plus compactes et plus économiques pour répondre aux besoins des petites et moyennes entreprises. Les fours plus petits et modulaires sont désormais accessibles à une plus large gamme d’entreprises, tout en offrant une performance équivalente à celle des grandes installations industrielles. Ces solutions permettent aux entreprises de maximiser leurs ressources et d’être plus compétitives, même si elles traitent des volumes de production plus faibles. L’accessibilité croissante de ces équipements ouvre la voie à une plus grande diversification des applications de thermolaquage dans des secteurs comme l’automobile, l’aéronautique, la construction, et même les petites industries artisanales.
Enfin, les préoccupations écologiques, toujours croissantes dans l’industrie, poussent les fabricants de fours de polymérisation à concevoir des systèmes encore plus écologiques. Cela comprend non seulement l’optimisation de l’efficacité énergétique et des systèmes de récupération thermique, mais aussi l’adoption de technologies de filtration de plus en plus performantes pour éliminer les substances polluantes générées pendant la cuisson. Les progrès dans la gestion des déchets, tels que la récupération et le recyclage de la poudre excédentaire ou des matériaux de peinture, permettent d’assurer un processus de thermolaquage plus responsable et plus respectueux de l’environnement.
En conclusion, les fours de polymérisation évoluent rapidement pour devenir des équipements plus efficaces, plus flexibles et plus écologiques, tout en offrant des niveaux de contrôle et de connectivité avancés. Ces évolutions permettent aux entreprises de mieux répondre aux exigences modernes en termes de qualité, de performance et de durabilité, tout en optimisant les coûts opérationnels et en réduisant l’impact environnemental du processus de thermolaquage. L’avenir des fours de polymérisation s’annonce donc très prometteur, avec des innovations qui ouvrent de nouvelles possibilités pour les industries du revêtement et du thermolaquage dans leur ensemble.
Four Thermolaquage
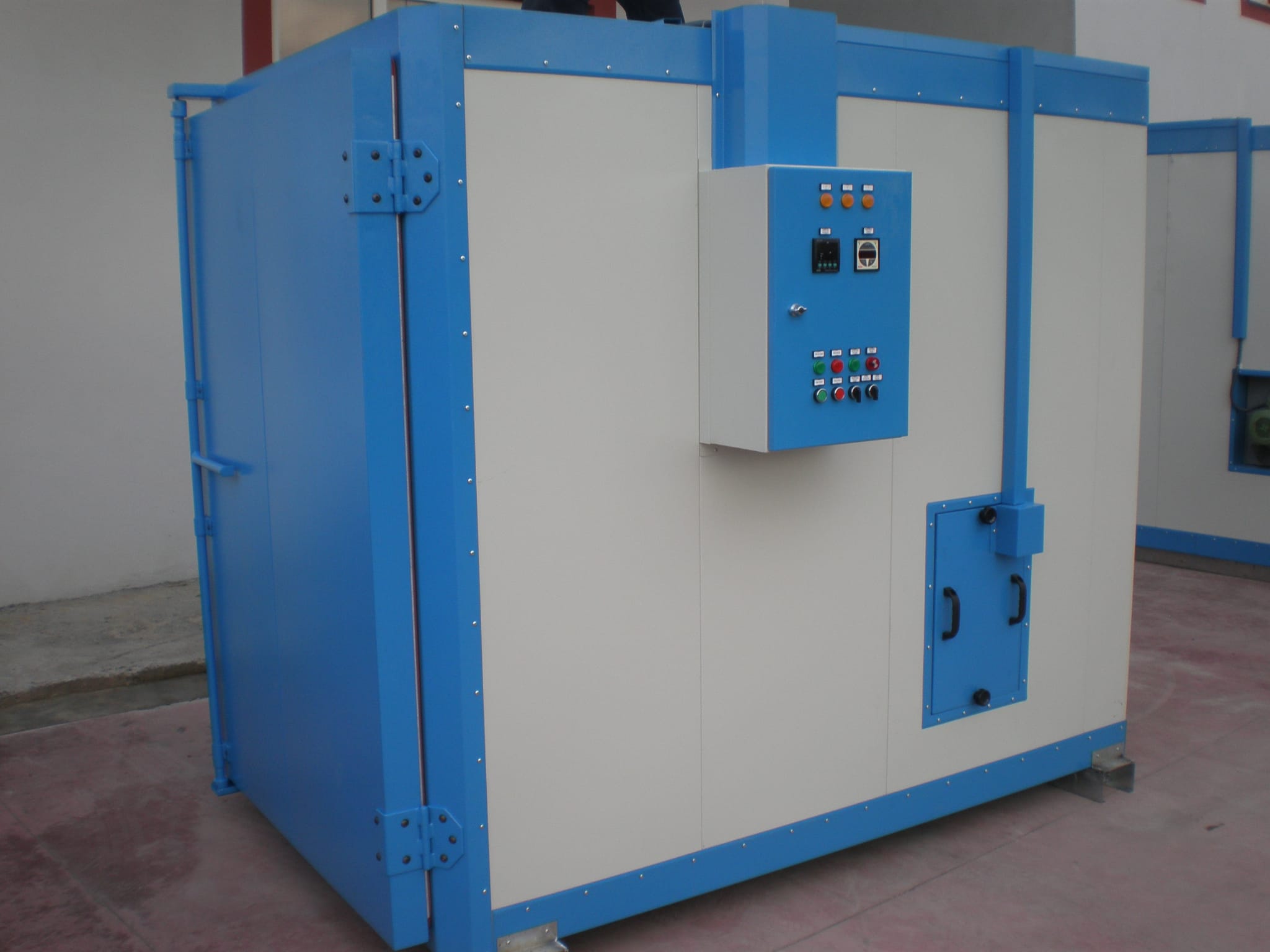
Le four de thermolaquage est un équipement clé dans le processus de peinture en poudre, également appelé thermolaquage, utilisé pour appliquer des revêtements durables sur diverses pièces métalliques. Il est essentiel pour durcir la peinture en poudre après son application, permettant ainsi de former un revêtement solide, résistant et homogène sur la surface traitée. Le four fonctionne selon le principe de polymérisation, où la chaleur est utilisée pour fusionner et lier chimiquement la peinture en poudre à la surface du métal, créant ainsi un film protecteur durable.
Les fours de thermolaquage sont généralement conçus pour atteindre des températures élevées, comprises entre 160 et 200°C, afin d’assurer une polymérisation efficace de la peinture. Le temps de cuisson varie en fonction de plusieurs facteurs, comme la taille des pièces, la nature du matériau, et les spécifications du fabricant de la peinture. Les fours doivent maintenir ces températures de manière constante pendant un certain temps pour garantir que la peinture atteint la bonne viscosité et les propriétés mécaniques nécessaires, telles que la résistance aux rayures, à la corrosion et aux produits chimiques.
Il existe plusieurs types de fours de thermolaquage, chacun conçu pour répondre à des besoins de production spécifiques. Parmi les plus courants figurent les fours à convection, les fours à infrarouge, et les fours à tunnel. Les fours à convection utilisent des ventilateurs pour faire circuler l’air chaud, assurant une distribution uniforme de la chaleur sur les pièces traitées. Cette méthode est particulièrement adaptée aux pièces de tailles variées, car elle permet de maintenir une température stable dans l’ensemble de la chambre de cuisson. Les fours à infrarouge, quant à eux, utilisent des lampes infrarouges pour chauffer directement la surface des pièces, offrant une montée en température plus rapide et un contrôle plus précis de la cuisson. Cette technologie est idéale pour des traitements plus rapides, mais peut nécessiter une surveillance plus attentive pour éviter les zones de surchauffe.
Les fours à tunnel, qui permettent un traitement continu des pièces, sont couramment utilisés dans des environnements de production à grande échelle. Ces systèmes transportent les pièces via un convoyeur à travers plusieurs zones de cuisson à température contrôlée, garantissant une cuisson uniforme et rapide. Cette configuration est très efficace pour les lignes de production à haut volume, permettant de traiter de grandes quantités de pièces en continu tout en maintenant des temps de cuisson optimaux.
Le contrôle de la température est un aspect crucial du fonctionnement d’un four de thermolaquage. Des capteurs et des régulateurs de température intégrés permettent de maintenir une température précise tout au long du cycle de cuisson. De plus, les systèmes modernes de contrôle sont souvent dotés de fonctionnalités permettant de surveiller l’humidité et d’ajuster les paramètres de cuisson en conséquence. Cette capacité à réguler avec précision les conditions de cuisson garantit des revêtements homogènes et de haute qualité. Certains modèles de fours de thermolaquage incluent également des systèmes de diagnostic qui alertent les opérateurs en cas de problème, comme une variation de température ou une défaillance d’un élément chauffant.
Les progrès dans la gestion énergétique des fours de thermolaquage ont permis de réduire la consommation d’énergie tout en maintenant des performances élevées. Les systèmes de récupération thermique permettent de capter la chaleur excédentaire générée pendant la cuisson et de la réutiliser pour préchauffer l’air entrant dans le four, réduisant ainsi la consommation d’énergie. Les nouveaux matériaux d’isolation thermique permettent également de mieux retenir la chaleur à l’intérieur du four, améliorant l’efficacité énergétique et réduisant les pertes de chaleur.
De plus, les préoccupations environnementales ont conduit à des améliorations dans la filtration des gaz et des particules émises durant le processus de cuisson. Les systèmes de filtration modernes, comme les filtres à charbon actif ou les systèmes de filtration haute efficacité, captent les émissions nocives et les particules en suspension dans l’air, réduisant ainsi l’impact environnemental du processus de thermolaquage. Ces technologies de filtration contribuent également à la sécurité des opérateurs en réduisant leur exposition aux substances potentiellement dangereuses.
Les fours de thermolaquage sont également de plus en plus modulaires et adaptables aux besoins spécifiques de chaque production. Les entreprises peuvent ainsi ajuster la taille et la configuration du four en fonction des pièces à traiter, des volumes de production et des types de revêtements. Les modèles modulaires permettent une flexibilité accrue, ce qui est particulièrement utile pour les entreprises qui doivent traiter une grande variété de pièces de tailles et de formes différentes. Ces systèmes permettent également de s’adapter à des productions de plus petite échelle, tout en offrant une qualité de cuisson similaire à celle des installations de grande taille.
L’intégration de technologies intelligentes dans les fours de thermolaquage est un autre domaine en forte croissance. Les systèmes de gestion numérique, associés à l’Internet des objets (IoT), permettent une surveillance et un contrôle à distance des processus de cuisson. Les données recueillies par les capteurs peuvent être envoyées à des plateformes cloud, où elles peuvent être analysées en temps réel pour optimiser les performances du four. Ces technologies permettent une gestion plus précise du processus de cuisson et une réduction des risques de défaillance, tout en permettant aux opérateurs de réagir rapidement en cas d’anomalie. Les systèmes intelligents offrent également des avantages en matière de maintenance préventive, en identifiant les problèmes potentiels avant qu’ils n’affectent la production.
Les évolutions technologiques dans le domaine des fours de thermolaquage ne se limitent pas à l’optimisation des processus de cuisson. Les fabricants de ces équipements ont également mis en place des solutions visant à améliorer la durabilité et la fiabilité des fours. L’utilisation de matériaux réfractaires plus résistants, tels que les alliages métalliques de haute qualité et les revêtements anti-corrosion, permet de prolonger la durée de vie des équipements, réduisant ainsi les coûts de maintenance et les interruptions de production. L’amélioration continue de la conception des fours a pour objectif d’offrir des solutions à la fois plus performantes et plus rentables pour les entreprises, qu’elles soient petites, moyennes ou grandes.
En outre, les fabricants de peintures en poudre jouent également un rôle important dans l’évolution des fours de thermolaquage. Les nouvelles formulations de peintures, souvent plus écologiques et nécessitant moins d’énergie pour leur polymérisation, contribuent à rendre les processus de thermolaquage plus durables. L’innovation dans ce domaine permet de réduire la consommation d’énergie des fours et d’améliorer la qualité des revêtements, tout en minimisant l’impact environnemental de la production.
En conclusion, les fours de thermolaquage continuent d’évoluer pour répondre aux exigences croissantes de l’industrie en matière de performance, de flexibilité et de durabilité. Les avancées en matière de technologies de contrôle, de gestion énergétique, de filtration et de connectivité offrent des solutions plus efficaces, plus écologiques et plus rentables. Les entreprises peuvent désormais bénéficier de solutions plus intelligentes et modulaires, adaptées à leurs besoins spécifiques, tout en maintenant un niveau de qualité et de sécurité élevé. Les tendances actuelles et futures dans le domaine des fours de thermolaquage laissent présager des évolutions passionnantes pour l’industrie du revêtement en poudre, avec des équipements plus performants, plus écologiques et plus adaptés aux défis du 21e siècle.
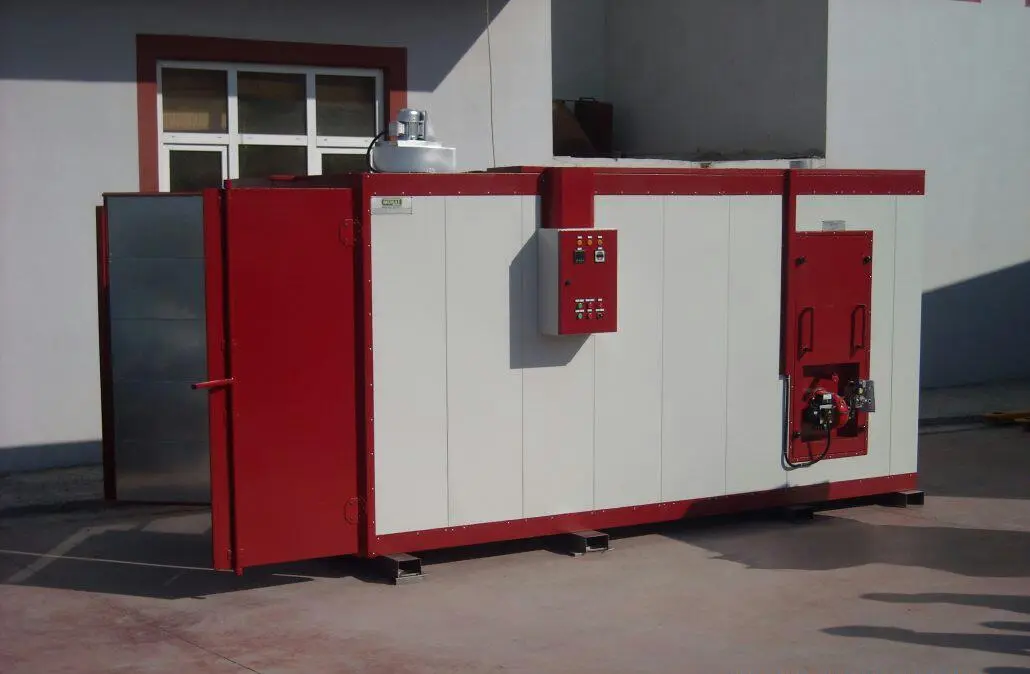
L’avenir des fours de thermolaquage semble se diriger vers des solutions encore plus personnalisées et adaptées aux exigences spécifiques des industries modernes. L’une des principales directions de développement concerne la flexibilité de production. En raison de la diversification des besoins des clients et de l’augmentation de la demande pour des produits sur mesure, les fabricants de fours de thermolaquage travaillent sur des conceptions qui permettent une adaptation rapide à des volumes de production fluctuants et à une variété de pièces de tailles et de formes différentes. Cela inclut l’intégration de systèmes de transport intelligents qui permettent de gérer efficacement le flux de pièces au sein du four, réduisant ainsi les temps d’arrêt et les pertes de matériaux.
Les progrès dans le domaine des revêtements de peinture influencent également l’évolution des fours de thermolaquage. De nouvelles formulations de peintures, souvent à base de résines plus écologiques ou à séchage rapide, modifient les conditions de cuisson requises. Certains types de peinture peuvent nécessiter une température de cuisson plus basse ou un temps de polymérisation plus court, ce qui pousse à la conception de fours capables de s’adapter à ces nouvelles exigences sans compromettre la qualité du revêtement. Ces innovations permettent de réduire la consommation d’énergie et d’augmenter l’efficacité globale du processus de thermolaquage.
L’utilisation de la robotisation et des systèmes automatisés dans les lignes de production est également une tendance croissante. Ces technologies permettent d’optimiser les opérations de traitement de pièces en réduisant le temps de manipulation et les risques d’erreurs humaines. Les robots peuvent charger et décharger les pièces dans le four, tout en assurant une précision dans leur positionnement pour garantir une cuisson uniforme. Les systèmes automatisés permettent également de programmer des cycles de cuisson et de nettoyage sans intervention manuelle, offrant ainsi une plus grande autonomie et une meilleure gestion des ressources.
Un autre domaine de développement est l’intégration de systèmes de surveillance et de diagnostic avancés, permettant de mieux prédire les performances des équipements et d’intervenir avant qu’une panne ne survienne. L’analyse prédictive, combinée à l’intelligence artificielle, peut désormais anticiper les défaillances des composants du four, comme les éléments chauffants, les ventilateurs, ou les systèmes de ventilation, en analysant en temps réel les données collectées par des capteurs intelligents. Cela permet non seulement de prolonger la durée de vie des équipements, mais aussi de réduire les coûts de maintenance et d’optimiser la production en limitant les interruptions imprévues.
Les préoccupations environnementales continuent de façonner les innovations dans les fours de thermolaquage. La réduction des émissions et l’amélioration de la recyclabilité des matériaux sont des priorités de plus en plus fortes. Les fabricants de fours travaillent à réduire les émissions de gaz à effet de serre et à intégrer des technologies de recyclage thermique plus efficaces. Par exemple, certains fours modernes sont équipés de systèmes de récupération de chaleur qui permettent de réutiliser la chaleur excédentaire générée pendant le processus de cuisson. Ce système permet de réduire les coûts énergétiques et d’augmenter l’efficacité globale du four.
D’autres innovations liées à l’impact environnemental incluent l’amélioration des systèmes de filtration pour réduire la pollution de l’air. L’utilisation de filtres à haute efficacité, de systèmes d’aspiration et de technologies de captation des émissions permet de limiter la libération de particules fines et d’autres polluants dans l’environnement. De plus, certains fours de thermolaquage sont désormais conçus pour être plus écologiques, en intégrant des matériaux et des composants qui respectent des normes environnementales strictes. Cela inclut l’utilisation de matériaux recyclables pour la construction des fours et l’adoption de technologies qui minimisent la consommation d’énergie.
Dans une optique de durabilité à long terme, les fabricants de fours de thermolaquage se concentrent également sur la conception de systèmes à faible maintenance et à longue durée de vie. Cela comprend l’utilisation de matériaux résistants à la chaleur et de revêtements protecteurs qui prolongent la durée de vie des composants internes du four. L’entretien des fours devient également plus facile grâce à des conceptions optimisées pour un accès rapide aux pièces qui nécessitent un entretien, réduisant ainsi le temps nécessaire à la maintenance et augmentant la disponibilité des équipements.
Les tendances dans le domaine du contrôle de la qualité continuent d’évoluer, avec des outils plus avancés permettant de mesurer la répartition de la chaleur, la consistance du revêtement et la résistance du film de peinture. Grâce à des systèmes de contrôle en temps réel, il est désormais possible de surveiller avec précision les paramètres du processus de cuisson et de détecter immédiatement toute anomalie pouvant affecter la qualité du revêtement. Ces outils de contrôle garantissent non seulement la cohérence du produit final, mais permettent aussi une réduction des déchets en évitant les cycles de cuisson erronés ou trop longs.
La digitalisation des équipements de thermolaquage se fait de plus en plus sentir avec l’intégration de plateformes connectées pour gérer l’ensemble du processus de production. Les données générées par les capteurs de température, de pression et d’humidité peuvent être collectées, analysées et partagées à travers des interfaces numériques permettant une gestion plus fluide et plus collaborative. Ces plateformes permettent aux gestionnaires de suivre la production à distance, de détecter des problèmes en temps réel et de prendre des décisions éclairées sur la maintenance et l’optimisation du processus.
Enfin, la tendance à la modularité des fours de thermolaquage s’intensifie avec l’intégration de systèmes évolutifs. Ces solutions permettent aux entreprises de commencer avec un four de taille modeste et d’étendre leur capacité de production à mesure que la demande augmente. Cela est particulièrement avantageux pour les petites et moyennes entreprises qui peuvent investir dans des équipements évolutifs sans avoir à procéder à des rénovations majeures ou à des investissements lourds dès le départ.
En conclusion, les avancées dans les technologies des fours de thermolaquage reflètent les besoins croissants de flexibilité, de durabilité et de connectivité dans les processus industriels modernes. L’intégration de systèmes intelligents, d’améliorations énergétiques, et de solutions respectueuses de l’environnement continuera à jouer un rôle essentiel dans l’optimisation des performances et la réduction de l’impact écologique des processus de thermolaquage. Le futur des fours de thermolaquage est donc lié à l’innovation constante, avec des équipements plus intelligents, plus écologiques et plus adaptés aux besoins spécifiques des industries de demain.
Les fours de thermolaquage continuent d’évoluer pour répondre aux défis technologiques, économiques et environnementaux de l’industrie moderne. Les demandes croissantes de produits à haute performance, de personnalisation et de durabilité poussent les fabricants de ces équipements à se concentrer sur des solutions toujours plus innovantes et adaptées à des applications diverses. Parmi les prochaines étapes de cette évolution, on peut s’attendre à l’émergence de technologies de cuisson encore plus rapides et plus efficaces, qui permettent de réduire les coûts énergétiques tout en augmentant la productivité.
Une autre direction prometteuse est celle de l’intégration de la technologie de chauffage par induction. Contrairement aux systèmes traditionnels à convection ou à infrarouge, les fours à induction utilisent des courants électromagnétiques pour chauffer directement la pièce métallique, sans chauffage de l’air ambiant. Cette méthode permet une montée en température extrêmement rapide et uniforme, réduisant ainsi les cycles de cuisson et permettant un contrôle plus précis de la température à l’échelle de la pièce. Cette technologie est particulièrement avantageuse pour les pièces de géométrie complexe ou les matériaux plus sensibles à la chaleur, car elle permet d’éviter la surchauffe et d’assurer une qualité de revêtement optimale.
Le contrôle en temps réel des paramètres de cuisson continue également de se perfectionner grâce à l’intégration de capteurs avancés et de systèmes de mesure sans contact. Ces dispositifs permettent une surveillance constante de la température, de l’humidité et de la qualité du revêtement pendant le processus de polymérisation. Grâce à l’utilisation de la vision industrielle, il est possible de détecter des défauts invisibles à l’œil nu, comme des irrégularités dans la texture du revêtement ou des zones mal durcies, et d’intervenir rapidement pour rectifier la situation. Cela garantit non seulement une meilleure qualité de la finition, mais aussi une réduction du gaspillage de matériaux et de temps.
Les systèmes de recirculation de chaleur seront également de plus en plus intégrés pour améliorer l’efficacité énergétique. Ces systèmes permettent de récupérer la chaleur excédentaire produite dans le four, la réutilisant pour préchauffer l’air entrant ou pour d’autres processus en aval. Cette approche améliore la rentabilité des installations, réduit la consommation d’énergie et contribue à des performances écologiques améliorées. De plus, la gestion thermique active devient une norme dans les équipements de thermolaquage, permettant d’adapter automatiquement les flux d’air chaud en fonction de la charge et des dimensions des pièces à traiter, garantissant ainsi une température uniforme pendant le cycle de cuisson.
Les systèmes de filtration de l’air continueront d’être un domaine d’innovation majeur pour réduire l’impact environnemental des fours de thermolaquage. En plus des filtres traditionnels, des solutions de filtration électrostatique et de technologies de décontamination de l’air plus avancées seront intégrées. Ces systèmes peuvent éliminer les particules fines, les vapeurs de peinture et d’autres substances potentiellement toxiques, contribuant à un environnement de travail plus sûr et à un processus de thermolaquage plus respectueux de l’environnement.
Les fours de thermolaquage modulaires continuent de gagner en popularité. Ces systèmes offrent la possibilité d’augmenter ou de réduire la capacité de production en fonction des besoins, ce qui est particulièrement avantageux pour les entreprises qui rencontrent des fluctuations de la demande ou qui traitent des séries limitées de produits. Les modules peuvent être ajoutés ou retirés facilement, permettant ainsi une grande flexibilité dans la gestion de la production, tout en maintenant une efficacité énergétique élevée et une qualité constante du revêtement. Cette modularité est idéale pour les petites et moyennes entreprises qui souhaitent investir progressivement tout en disposant de systèmes adaptés à l’échelle de leur production.
Une autre avancée qui va se poursuivre est l’amélioration des interfaces utilisateurs. Les panneaux de contrôle deviennent de plus en plus interactifs et intuitifs, avec l’intégration de technologies tactiles et de tableaux de bord numériques. Ces interfaces permettent non seulement un contrôle facile des paramètres de cuisson, mais elles intègrent aussi des fonctionnalités de diagnostic à distance, des alertes de maintenance, et des reportings de performance. Les opérateurs peuvent ainsi suivre en temps réel l’état du four et ajuster les paramètres en fonction des exigences de la production, tout en ayant un aperçu détaillé des données historiques pour optimiser les performances.
La transition vers des revêtements à faible température de cuisson deviendra également plus marquée, car de nombreux fabricants de peinture en poudre travaillent sur des formulations qui nécessitent des températures de cuisson plus basses et des durées de traitement réduites. Cette évolution permettra de réduire la consommation énergétique, d’accélérer les cycles de production et de traiter des matériaux plus sensibles à la chaleur, comme certains plastiques ou métaux légers.
Dans un monde de plus en plus connecté, les fours de thermolaquage intelligents feront partie intégrante de la fabrication numérique. En reliant les fours aux systèmes de gestion de production et aux plates-formes cloud, les entreprises pourront avoir une visibilité complète sur leurs opérations. Cela permettra de mieux synchroniser les flux de production et d’effectuer des ajustements en temps réel en fonction des besoins. La collecte de données en continu permettra également de mieux comprendre l’efficacité des processus de thermolaquage et d’identifier des opportunités d’amélioration pour réduire les coûts et améliorer la qualité.
À l’avenir, la réduction des déchets deviendra une priorité dans les processus de thermolaquage. Les entreprises s’orienteront davantage vers des systèmes de récupération de la poudre excédentaire et de recyclage de la peinture. Ces technologies permettront de récupérer une grande partie de la peinture en poudre non utilisée, de la traiter et de la réutiliser dans les cycles suivants, ce qui réduira considérablement le gaspillage de matériaux et l’impact écologique de la production.
En somme, l’avenir des fours de thermolaquage repose sur des avancées technologiques visant à rendre les équipements plus intelligents, plus efficaces et plus respectueux de l’environnement. La combinaison de la flexibilité de production, de l’optimisation énergétique, de la connectivité intelligente, et de l’automatisation assurera une amélioration continue des processus industriels tout en répondant aux nouvelles attentes du marché, des consommateurs et des régulations environnementales. Les innovations dans ce domaine garantiront un avenir prometteur pour l’industrie du thermolaquage, avec des équipements toujours plus performants, plus durables et plus adaptés aux défis de demain.
Four de Séchage Peinture
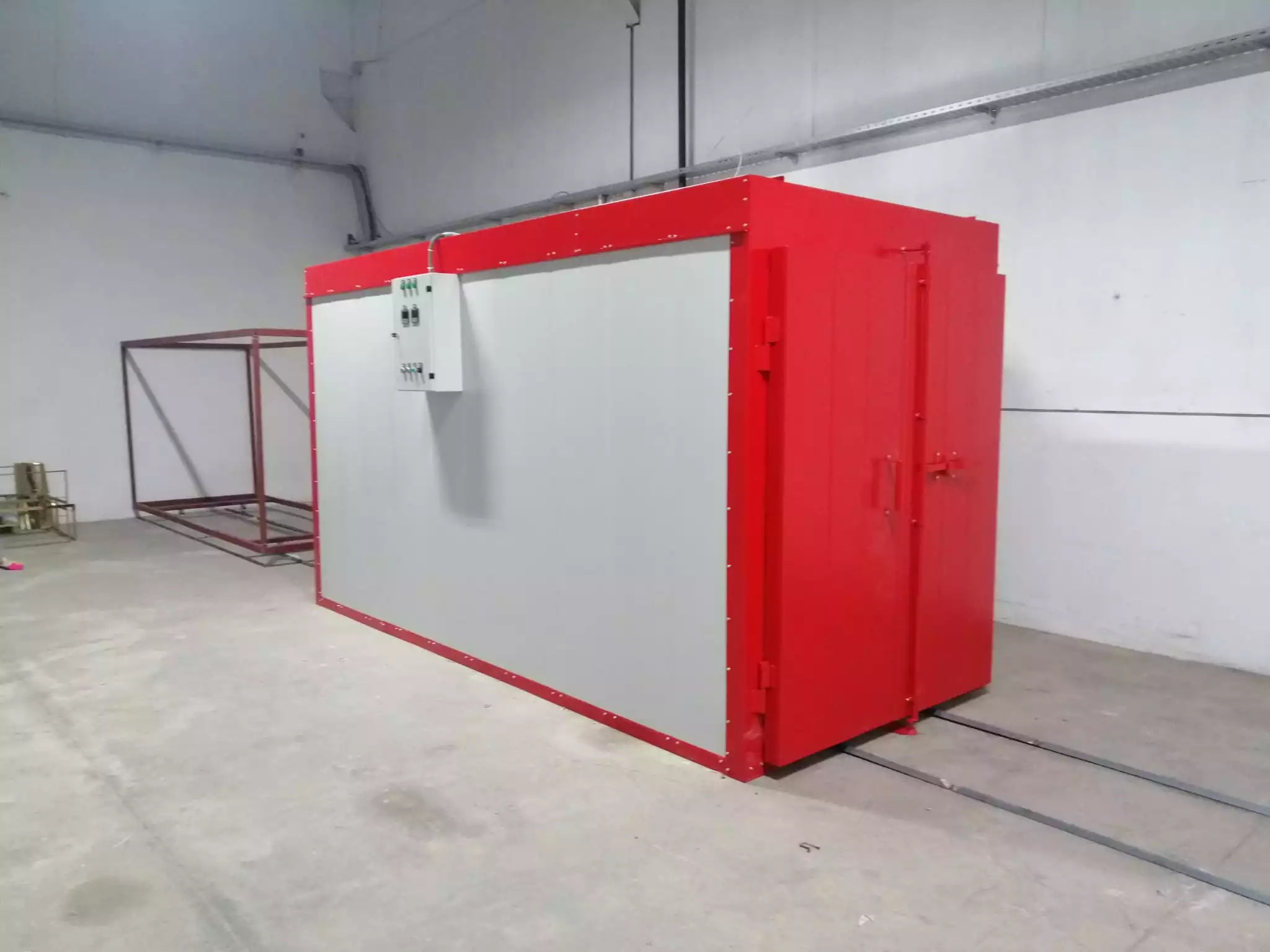
Le four de séchage peinture est un équipement essentiel dans les processus industriels de peinture, utilisé pour durcir et sécher les couches de peinture appliquées sur différentes surfaces, comme le métal, le plastique, ou le bois. Ce type de four joue un rôle crucial dans la fabrication de produits peints ayant des propriétés de résistance élevées, notamment à la chaleur, aux produits chimiques, et aux chocs. Contrairement aux systèmes de polymérisation, qui utilisent des températures plus élevées pour lier les composants chimiques de la peinture, les fours de séchage sont conçus pour éliminer l’humidité et fixer la peinture à la surface sans provoquer de réactions chimiques complexes.
Les fours de séchage fonctionnent généralement en chauffant l’air à une température précise, permettant à la peinture d’atteindre la bonne viscosité et d’adhérer efficacement à la surface du produit. Ces fours sont particulièrement utilisés dans les industries automobiles, électroniques, de la fabrication de meubles, et de la métallurgie, où des finitions de haute qualité et une durabilité des revêtements sont essentielles. Les températures de séchage varient typiquement entre 60°C et 150°C, selon le type de peinture utilisée et le matériau à traiter.
Les fours à convection sont les plus couramment utilisés pour le séchage de la peinture. Ils fonctionnent en chauffant l’air à l’intérieur du four, puis en le faisant circuler autour des pièces à l’aide de ventilateurs. Cette méthode assure un séchage uniforme et régulier des pièces. La circulation de l’air permet également de réduire le temps de séchage en maintenant une température constante autour de chaque pièce, ce qui permet de traiter une grande variété de pièces de tailles et formes différentes. De plus, les fours à convection sont efficaces pour sécher des couches de peinture relativement épaisses, car ils assurent une répartition uniforme de la chaleur sur toute la surface de la pièce.
Les fours à infrarouge sont également utilisés pour le séchage de la peinture, notamment dans les applications nécessitant un séchage rapide ou un traitement de surfaces délicates. Contrairement aux systèmes à convection, les fours à infrarouge chauffent directement la surface des pièces à travers des lampes infrarouges, qui émettent des rayonnements thermiques. Cette méthode permet un séchage plus rapide des revêtements fins, car elle chauffe directement la surface sans nécessiter de chauffer l’air ambiant. L’efficacité de ces systèmes dépend fortement de la capacité des lampes à émettre une chaleur uniforme et de la distance entre les sources de rayonnement et les pièces.
Les fours de séchage à air pulsé sont une variante des systèmes à convection qui offrent des avantages supplémentaires en termes de rapidité de séchage. Ce type de four utilise des jets d’air chauds dirigés directement sur les pièces, ce qui accélère le processus de séchage. Les jets d’air permettent également de mieux contrôler la température et l’humidité dans le four, assurant ainsi des conditions de séchage optimales pour chaque type de peinture et matériau. Ce système est idéal pour des productions de série où la vitesse de séchage est essentielle sans compromettre la qualité du revêtement.
Les fours de séchage à tunnel sont souvent utilisés dans les installations de production à grande échelle. Ces systèmes permettent un traitement continu des pièces, qui sont transportées à travers le tunnel de séchage par des convoyeurs. L’air chaud est distribué tout au long du tunnel, créant ainsi une zone de séchage à température homogène. Cette configuration est idéale pour les lignes de production à volume élevé, où le temps de traitement doit être optimisé tout en garantissant une finition uniforme. Les fours à tunnel sont utilisés dans de nombreuses industries, notamment l’automobile, les produits électroniques, et l’ameublement.
L’efficacité énergétique des fours de séchage peinture est un domaine important de développement. Les fabricants de ces équipements cherchent constamment des solutions pour réduire la consommation d’énergie tout en maintenant des performances optimales. L’un des moyens d’y parvenir est l’intégration de systèmes de récupération de chaleur, qui permettent de capter la chaleur excédentaire générée pendant le processus de séchage et de la réutiliser pour préchauffer l’air entrant dans le four. Cela permet de réduire la consommation énergétique en exploitant l’énergie déjà produite, améliorant ainsi l’efficacité globale du système. De plus, l’isolation thermique des fours est un facteur clé pour minimiser les pertes de chaleur, ce qui permet également d’économiser de l’énergie.
Les systèmes de filtration d’air jouent également un rôle crucial dans le fonctionnement des fours de séchage peinture. En effet, pendant le processus de séchage, des vapeurs et des particules peuvent se dégager de la peinture et se retrouver dans l’air ambiant. Ces émissions peuvent être nuisibles à l’environnement et à la santé des travailleurs si elles ne sont pas correctement filtrées. Les filtres à charbon actif, les filtres HEPA et les systèmes de filtration électrostatique sont couramment utilisés pour éliminer ces polluants. De plus, ces systèmes contribuent à maintenir un environnement de travail sain et à respecter les normes environnementales strictes qui régissent les émissions industrielles.
Les progrès dans la numérisation et la connectivité des fours de séchage deviennent également un élément clé de l’évolution de ces équipements. Les systèmes intelligents permettent de suivre en temps réel les paramètres de séchage, tels que la température et l’humidité, et d’ajuster automatiquement les conditions de fonctionnement pour garantir des résultats de qualité constante. Grâce à des interfaces numériques et à des systèmes de contrôle à distance, les opérateurs peuvent surveiller et ajuster les cycles de séchage depuis n’importe quel endroit, ce qui augmente la flexibilité et la réactivité. L’intégration de plateformes cloud et de technologies IoT permet également de collecter des données pour analyser les performances du système et identifier des améliorations possibles, qu’il s’agisse d’optimiser les cycles de séchage ou de détecter des anomalies dans les processus.
Les fours de séchage peinture sont également de plus en plus modulaires, permettant une adaptation flexible aux besoins spécifiques des différents types de production. Que ce soit pour des petites séries ou des productions de masse, la capacité de personnaliser le système en fonction des volumes et des caractéristiques des pièces à traiter est un atout majeur. La possibilité d’ajuster les dimensions du four ou d’ajouter des modules supplémentaires permet aux entreprises de maximiser l’efficacité de leur installation tout en réduisant les coûts d’investissement initiaux. Ce type de conception modulaire est particulièrement utile pour les entreprises qui prévoient une évolution rapide de leurs besoins de production.
Enfin, l’automatisation des processus de séchage devient une tendance de plus en plus importante. L’automatisation permet de contrôler et de suivre le processus de séchage de manière plus précise et d’optimiser le temps de traitement tout en maintenant une qualité constante. Les robots de manutention et les systèmes automatisés de transport de pièces facilitent le chargement et le déchargement des pièces dans le four, réduisant ainsi les risques d’erreur et les coûts de main-d’œuvre. Cette automatisation permet également de libérer du temps pour que les opérateurs puissent se concentrer sur des tâches à plus forte valeur ajoutée, comme la maintenance préventive ou l’analyse des données.
En conclusion, les fours de séchage peinture continuent de se moderniser pour répondre aux défis de productivité, d’efficacité énergétique, et de respect des normes environnementales. L’intégration de technologies avancées telles que les systèmes de contrôle intelligents, l’automatisation, et la récupération de chaleur, ainsi que l’amélioration des systèmes de filtration, fait des fours de séchage des outils encore plus performants et adaptés aux exigences de l’industrie moderne. Ces progrès contribuent à une réduction des coûts opérationnels, à une amélioration de la qualité du produit final, et à un impact environnemental moindre, rendant les fours de séchage peinture essentiels pour les entreprises soucieuses de répondre aux défis de demain.
Les fours de séchage peinture continuent de se perfectionner avec l’augmentation des exigences industrielles et la demande de personnalisation des produits. Alors que les technologies classiques de séchage, comme les fours à convection, les fours à infrarouge, et les fours à air pulsé, demeurent des solutions largement utilisées, de nouveaux défis et opportunités se présentent dans l’industrie de la peinture et du revêtement.
L’intégration de technologies de séchage innovantes, telles que les fours à micro-ondes et les fours à plasma, est un domaine en plein essor. Ces technologies émergentes permettent de sécher les peintures de manière beaucoup plus rapide et plus homogène. Les fours à micro-ondes, par exemple, sont capables de pénétrer dans la peinture et de chauffer les molécules d’eau à l’intérieur du revêtement, permettant un séchage rapide sans affecter la qualité du film de peinture. Cette méthode présente l’avantage de réduire considérablement les temps de cycle, ce qui est particulièrement utile dans des environnements de production à haut volume.
Les fours à plasma utilisent un champ électrique pour accélérer les réactions chimiques dans la peinture et améliorer son adhérence et sa durabilité, tout en réduisant les coûts d’énergie. Ces technologies peuvent également être utilisées pour traiter des matériaux délicats ou des pièces avec des revêtements spéciaux, qui pourraient autrement être affectés par des températures élevées. De plus, le séchage par plasma permet de préserver les propriétés des peintures à base de matériaux écologiques, souvent plus sensibles à la chaleur.
Le suivi et l’analyse des performances des fours de séchage peinture deviennent également de plus en plus sophistiqués. L’introduction de technologies d’analyse avancée telles que l’intelligence artificielle (IA) et les algorithmes d’apprentissage automatique permet de suivre en temps réel l’évolution du processus de séchage, de prédire les pannes potentielles, et de maximiser l’efficacité énergétique des installations. Ces systèmes intelligents sont capables d’apprendre des habitudes de production et de proposer des ajustements pour optimiser les temps de séchage en fonction des conditions spécifiques de chaque lot de production, tout en maintenant la qualité du revêtement.
L’évolution vers des systèmes de contrôle visuel automatisés dans les fours de séchage, utilisant des caméras thermiques et des capteurs optiques, permet de contrôler en continu la répartition de la chaleur et de détecter les anomalies. Ces technologies de vision industrielle offrent un avantage considérable pour la détection des défauts de séchage, tels que les zones non séchées ou des irrégularités dans la finition de la peinture. De plus, elles permettent de s’assurer que les revêtements sont uniformément appliqués sur la surface sans que des défauts d’application ou de séchage ne nuisent à la qualité du produit final.
La durabilité environnementale continue d’être une priorité dans la conception des nouveaux fours de séchage peinture. En plus de la réduction de la consommation énergétique et des émissions de CO2 grâce à l’intégration des technologies de récupération de chaleur, de nouveaux matériaux et procédés sont utilisés pour améliorer l’efficacité de l’isolation thermique et réduire les pertes d’énergie. Les revêtements réfractaires à haute performance et les technologies de joints étanches contribuent à limiter les déperditions de chaleur, ce qui permet de maintenir une température stable tout en optimisant l’efficacité énergétique du four.
L’évolutivité et la flexibilité des systèmes sont également des éléments clés pour les fabricants de fours de séchage peinture, qui cherchent à répondre aux besoins d’un marché en constante évolution. Les systèmes modulaires permettent aux entreprises de commencer avec un four de taille standard et d’ajouter des modules supplémentaires en fonction de l’augmentation des volumes de production. Cette approche de production à la demande offre aux entreprises la possibilité d’adapter rapidement leurs capacités de production sans avoir à investir massivement dans de nouveaux équipements, ce qui est particulièrement avantageux pour les petites et moyennes entreprises.
Les fours de séchage de demain seront également de plus en plus connectés. L’intégration de l’Internet des objets (IoT) et des solutions de maintenance prédictive permet aux opérateurs de surveiller et de diagnostiquer les performances des équipements à distance. Les capteurs IoT surveillent en temps réel les paramètres du four, tels que la température, l’humidité, et le taux de circulation de l’air, et transmettent ces données à une plateforme centralisée. Cela permet de prendre des décisions basées sur des données en temps réel, d’améliorer la gestion de la production, et d’optimiser les cycles de séchage pour chaque type de peinture ou de matériau.
L’introduction de matériaux écologiques et de peintures à faible impact environnemental influence également la conception des fours de séchage. Les peintures à base d’eau, les peintures à séchage rapide ou les peintures sans solvant nécessitent des températures de séchage plus faibles, ce qui pousse les fabricants de fours à repenser leurs systèmes de chauffage pour s’adapter à ces nouvelles formulations. Cela engendre un besoin accru de technologies de séchage plus finement contrôlées et plus adaptées à une variété de peintures et de matériaux, tout en maintenant des performances énergétiques optimisées.
Le développement de fours à séchage ultra-rapide, utilisant des systèmes combinés, comme des technologies à infrarouge et à convection, est également une tendance à surveiller. Ces technologies permettent de combiner les avantages de différents types de séchage pour des cycles plus courts et une efficacité maximale. Par exemple, les fours hybrides, qui allient la convection, l’infrarouge, et la technologie de récupération de chaleur, représentent une avancée dans l’optimisation du processus de séchage et sont particulièrement utiles pour les grandes séries de production.
Les fours de séchage peinture sont en train de devenir des outils de plus en plus intelligents, modulaires et écologiques, répondant aux impératifs de flexibilité, de réduction des coûts d’exploitation, et d’optimisation des performances de production. Les progrès dans les technologies de chauffage, les systèmes de contrôle numérique, et l’intégration des solutions de connectivité numérique sont les moteurs principaux qui transformeront la manière dont les industries abordent le séchage de peinture. En restant à la pointe de l’innovation, les entreprises pourront non seulement améliorer la qualité de leurs produits finis, mais aussi respecter les normes environnementales de plus en plus strictes tout en améliorant leur rentabilité.
Les fours de séchage peinture continuent de se transformer grâce aux nouvelles avancées technologiques, répondant ainsi aux besoins spécifiques de l’industrie tout en respectant les normes environnementales et en améliorant l’efficacité de la production. Dans cette dynamique, plusieurs domaines d’innovation se distinguent, chacun visant à rendre les processus de séchage plus rapides, plus écologiques et plus rentables.
Une des évolutions majeures concerne la réduction du temps de séchage. Les besoins de production rapide, en particulier dans les secteurs tels que l’automobile, l’électronique, et l’aéronautique, exigent des solutions qui peuvent sécher les revêtements plus rapidement tout en maintenant une qualité de finition irréprochable. Les technologies de séchage à haute fréquence et les fours à micro-ondes sont en plein essor, car elles permettent de réduire les temps de séchage tout en évitant d’endommager les matériaux. Ces technologies ont le potentiel de rendre les processus de séchage plus efficaces, ce qui est particulièrement important dans des environnements à haute demande où chaque minute de production compte.
L’optimisation énergétique reste un enjeu clé dans la conception des fours de séchage peinture. Les fabricants cherchent à réduire la consommation d’énergie des systèmes en améliorant leur efficacité thermique. L’intégration de technologies de récupération thermique dans les systèmes de séchage permet de réutiliser la chaleur excédentaire produite par les fours, diminuant ainsi la nécessité d’apport extérieur de chaleur. De plus, la possibilité d’optimiser la gestion de la chaleur à l’intérieur du four en fonction des types de matériaux traités et des caractéristiques spécifiques de la peinture permet non seulement d’économiser de l’énergie, mais aussi de garantir une performance de séchage constante et fiable.
Les fours de séchage connectés deviennent également de plus en plus populaires dans les industries modernes. Grâce à l’intégration de l’Internet des objets (IoT), les équipements peuvent désormais envoyer des données en temps réel concernant la température, l’humidité, et les performances des systèmes de circulation d’air. Cela permet une surveillance continue et un ajustement automatique des paramètres du four en fonction des besoins spécifiques de chaque cycle de production. Les systèmes de contrôle à distance offrent également aux opérateurs la possibilité de gérer plusieurs installations à partir d’un seul point de contrôle, augmentant ainsi la flexibilité et l’efficacité des processus de séchage.
De plus, l’introduction de systèmes de maintenance prédictive dans les fours de séchage peinture constitue une autre avancée technologique significative. En utilisant des capteurs pour surveiller en continu l’état des composants du four, tels que les éléments chauffants, les ventilateurs ou les systèmes de circulation d’air, il est possible de détecter les signes de défaillance avant qu’ils ne surviennent. Cela permet aux entreprises de planifier les maintenances de manière proactive, réduisant ainsi les risques de pannes imprévues et minimisant les temps d’arrêt de production. Cette approche garantit également une meilleure longévité des équipements, ce qui peut réduire les coûts liés à la maintenance et aux réparations.
Les fours de séchage peinture modulaires sont de plus en plus populaires, car ils permettent aux entreprises d’adapter rapidement leurs installations de production en fonction des besoins du marché. Ces systèmes modulaires offrent la flexibilité nécessaire pour traiter différents types de revêtements ou pour augmenter ou réduire la capacité de séchage en fonction des fluctuations de la demande. Par exemple, un fabricant peut commencer avec un système plus petit et, au fur et à mesure de l’expansion de ses activités, ajouter des modules pour augmenter sa capacité de production. Cela permet de réaliser des investissements plus petits et progressifs tout en répondant à la croissance de l’entreprise.
Une autre dimension importante dans l’évolution des fours de séchage peinture concerne l’utilisation de matériaux écologiques et durables. Les entreprises cherchent à répondre à des demandes croissantes de solutions plus vertes en optant pour des matériaux qui réduisent l’impact environnemental du processus de séchage. L’utilisation de peintures sans solvant et biologiques nécessitant des températures de séchage plus basses modifie la conception des équipements pour s’adapter à ces nouvelles formulations. De plus, la réduction des émissions polluantes générées pendant le processus de séchage est également une priorité, ce qui conduit au développement de systèmes de filtration avancés pour capturer les particules fines et les gaz nocifs.
L’automatisation est également une tendance majeure dans l’industrie des fours de séchage peinture. Les systèmes entièrement automatisés permettent de réduire la main-d’œuvre nécessaire tout en augmentant la précision et la qualité du processus de séchage. Les robots de manutention et les convoyeurs automatisés transportent les pièces peintes à travers les différentes zones de séchage sans intervention manuelle, ce qui réduit les erreurs humaines et améliore l’efficacité du système. Cette automatisation permet également d’intégrer des technologies de contrôle visuel, de sorte que chaque pièce puisse être inspectée en temps réel pour détecter des défauts dans le séchage, tels que des zones mal séchées ou des irrégularités dans la finition.
Enfin, l’introduction de systèmes de gestion de la qualité en temps réel dans les fours de séchage peinture améliore encore la capacité des entreprises à produire des produits de haute qualité tout en minimisant les déchets. En utilisant des capteurs de qualité de surface et des systèmes de mesure optique, les fabricants peuvent vérifier en continu que la couche de peinture est uniformément appliquée et correctement durcie. Ces systèmes de contrôle qualité automatisé permettent de détecter des problèmes de séchage avant qu’ils ne deviennent des défauts visibles, réduisant ainsi les taux de rejet et augmentant la productivité globale.
L’avenir des fours de séchage peinture semble donc résolument tourné vers l’intégration de technologies intelligentes, la réduction de l’empreinte écologique, et l’optimisation de la performance énergétique. Les innovations continues dans les domaines de l’automatisation, de la numérisation, et des matériaux écologiques feront des fours de séchage peinture des outils encore plus performants et flexibles, permettant aux entreprises de répondre aux défis de production tout en respectant des critères de durabilité environnementale stricts. En restant à la pointe de ces développements, les industries pourront non seulement améliorer l’efficacité de leurs processus de production, mais aussi garantir une qualité de finition de peinture irréprochable pour des applications allant des secteurs industriels lourds aux produits de consommation les plus sophistiqués.
Conclusion
Le temps nécessaire pour l’installation d’un four à thermolaquage varie en fonction de nombreux facteurs, mais une planification et une exécution soignées peuvent contribuer à optimiser le processus. En collaborant avec des professionnels expérimentés et en assurant une préparation adéquate du site et de l’équipe, les entreprises peuvent s’assurer que leur nouvel équipement est opérationnel et productif le plus rapidement possible.
Le Revêtement en Poudre
L’équipement de revêtement en poudre est utilisé pour appliquer une fine couche de poudre sur une surface métallique. Ce type de revêtement est appliqué par un procédé électrostatique et constitue une méthode très populaire pour la finition des pièces métalliques.
Ce type d’équipement peut être divisé en deux grandes catégories : automatiques et manuels. Les cabines automatiques sont plus populaires car elles offrent de meilleurs taux de production, mais elles sont également plus chères.
Une cabine à poudre est une enceinte dans laquelle se déroule le processus de revêtement en poudre. L’équipement de revêtement en poudre comprend un four dans lequel les pièces sont chauffées pour activer la poudre, un pistolet qui pulvérise ou brosse la poudre, une bande transporteuse qui déplace les pièces à travers le four et des pistolets de type cartouche pour appliquer des revêtements plus épais avec moins de pulvérisation.
Le revêtement en poudre est une technique utilisée pour donner une finition aux pièces métalliques. Cette technique est utilisée depuis de nombreuses années et reste aujourd’hui l’une des techniques les plus populaires.
L’équipement de revêtement en poudre comprend des cabines, des fours, des pistolets, des machines, des lignes et des convoyeurs. Une cabine peut être automatique ou manuelle. Une cabine automatique est plus chère qu’une cabine manuelle mais elle est aussi plus rapide et plus efficace
Non seulement nous fabriquons nos équipements de revêtement en poudre, mais nous les expédions également dans vos locaux avec soin dans le monde entier.
L’équipement de revêtement en poudre est utilisé pour appliquer une fine couche de poudre sur une surface métallique. Ce type de revêtement est appliqué par un procédé électrostatique et constitue une méthode très populaire pour la finition des pièces métalliques.
Ce type d’équipement peut être divisé en deux grandes catégories : automatiques et manuels. Les cabines automatiques sont plus populaires car elles offrent de meilleurs taux de production, mais elles sont également plus chères.
Une cabine à poudre est une enceinte dans laquelle se déroule le processus de revêtement en poudre. L’équipement de revêtement en poudre comprend un four dans lequel les pièces sont chauffées pour activer la poudre, un pistolet qui pulvérise ou brosse la poudre, une bande transporteuse qui déplace les pièces à travers le four et des pistolets de type cartouche pour appliquer des revêtements plus épais avec moins de pulvérisation.
Le revêtement en poudre est une technique utilisée pour donner une finition aux pièces métalliques. Cette technique est utilisée depuis de nombreuses années et reste aujourd’hui l’une des techniques les plus populaires.
L’équipement de revêtement en poudre comprend des cabines, des fours, des pistolets, des machines, des lignes et des convoyeurs. Une cabine peut être automatique ou manuelle. Une cabine automatique est plus chère qu’une cabine manuelle mais elle est aussi plus rapide et plus efficace
- Fours de polymérisation: Les fours de polymérisation sont des équipements industriels cruciaux dans le traitement des polymères. Ils permettent le durcissement contrôlé des matériaux polymères à travers divers processus tels que la polymérisation thermique, la réticulation chimique, et la polymérisation par rayonnement.
- Polymérisation thermique: La polymérisation thermique implique la conversion de monomères en polymères par l’application de chaleur. Les fours de polymérisation thermique maintiennent des conditions spécifiques de température, de pression, et de durée pour assurer une réaction exothermique contrôlée.
- Polymérisation par rayonnement: Cette méthode de polymérisation utilise des rayonnements tels que les ultraviolets (UV) pour initier la réaction de polymérisation. Les fours associés à cette technique assurent une exposition uniforme aux rayonnements, permettant le durcissement efficace des polymères.
- Température de polymérisation: La température de polymérisation est critique pour contrôler la vitesse et l’efficacité du processus. Les fours garantissent le maintien précis de la température requise, influençant la cinétique de polymérisation et les propriétés finales du matériau.
- Réaction exothermique: La polymérisation génère souvent de la chaleur (réaction exothermique). Les fours intègrent des systèmes de refroidissement pour éviter des températures excessives, assurant un durcissement uniforme sans compromettre l’intégrité des polymères.
- Contrôle du processus: Les fours de polymérisation intègrent des dispositifs de contrôle sophistiqués, régulant des paramètres tels que la température, la pression, et le temps. Cela garantit une polymérisation précise, répondant aux exigences spécifiques des applications industrielles.
- Durcissement des polymères: Le durcissement des polymères, facilité par les fours spécialisés, transforme les matériaux d’un état malléable à une structure solide. Les paramètres de durcissement, comme la température et le temps, sont minutieusement ajustés pour obtenir des propriétés désirées.
- Équipement de séchage: Certains fours de polymérisation fonctionnent également comme des équipements de séchage, éliminant l’humidité résiduelle des matériaux polymères. Le contrôle précis de la température et de l’humidité garantit un séchage efficace sans compromettre les caractéristiques du matériau.
- Cinétique de polymérisation: La cinétique de polymérisation étudie la vitesse des réactions de polymérisation. Les fours jouent un rôle crucial en maintenant des conditions idéales pour influencer la cinétique, permettant ainsi un contrôle optimal du processus de durcissement.
- Polymérisation en masse: La polymérisation en masse traite des grandes quantités de polymères simultanément. Les fours associés à ce processus sont conçus pour gérer des charges importantes tout en maintenant des conditions uniformes pour chaque matériau.
Fours de polymérisation: Les fours de polymérisation sont des équipements industriels essentiels utilisés dans la transformation des polymères. Ces systèmes fournissent un environnement contrôlé pour des processus tels que la polymérisation thermique, la réticulation chimique, et la polymérisation par rayonnement. Ils garantissent des conditions précises de température, de pression, et de durée, assurant ainsi le durcissement uniforme des matériaux polymères. Ces équipements jouent un rôle clé dans la fabrication de produits polymériques aux propriétés spécifiques, en influençant la cinétique de polymérisation et en permettant un contrôle fin du processus de durcissement.
Polymérisation thermique: La polymérisation thermique est un processus fondamental dans le durcissement des polymères. Ce mécanisme implique l’application de chaleur pour déclencher la réaction de conversion des monomères en polymères. Les fours de polymérisation thermique sont conçus pour maintenir des conditions spécifiques de température, de pression, et de durée, assurant ainsi une réaction exothermique contrôlée. En contrôlant ces paramètres, les fours garantissent un durcissement homogène des matériaux polymères, influençant directement leurs propriétés finales et leur utilisation dans diverses applications industrielles.
Nous ne sommes pas seulement les fabricants de vos équipements de revêtement en poudre, nous sommes également vos partenaires de livraison dans le monde entier.
Chez EMS Powder Coating Equipment, nous comprenons qu’il est tout aussi important de vous fournir votre équipement de revêtement en poudre rapidement et en toute sécurité que de le fabriquer selon les normes les plus élevées. C’est pourquoi nous proposons des services de livraison dans le monde entier à tous nos clients.
Nous travaillons avec un réseau de partenaires maritimes expérimentés et fiables pour garantir que votre équipement arrive à temps et en parfait état. Nous proposons également une variété d’options d’expédition adaptées à votre budget et à vos besoins.
Que vous ayez besoin d’expédier votre équipement à une adresse locale ou vers une destination internationale, nous pouvons vous aider. Nous travaillerons avec vous pour choisir la meilleure option d’expédition pour vos besoins et pour vous tenir informé de l’état de votre envoi à chaque étape du processus.
Ainsi, lorsque vous choisissez EMS pour votre équipement de revêtement en poudre, vous obtenez non seulement les meilleurs produits du marché, mais vous bénéficiez également de la meilleure expérience de livraison possible.
Contactez-nous dès aujourd’hui pour en savoir plus sur nos services de livraison dans le monde entier.
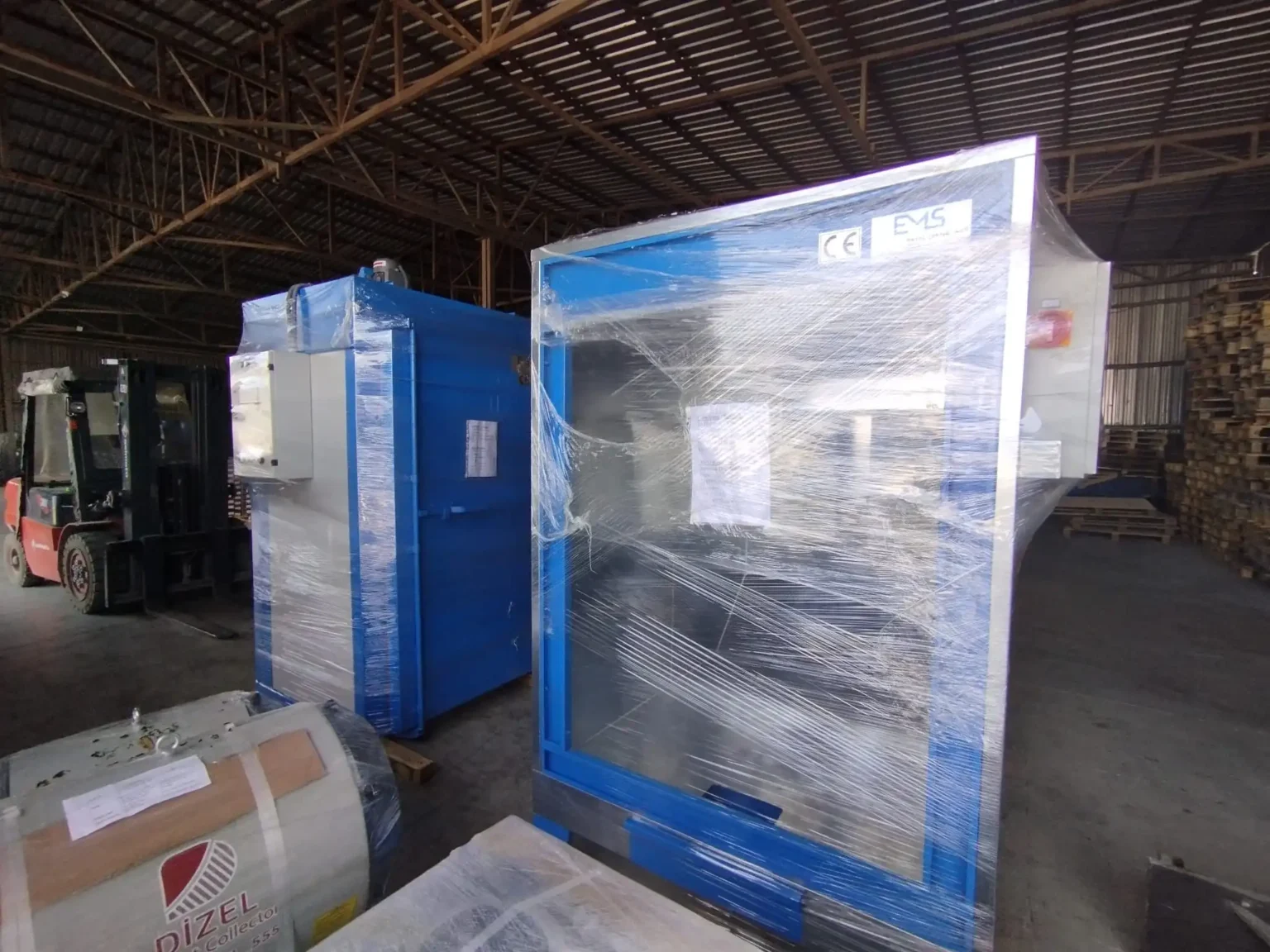

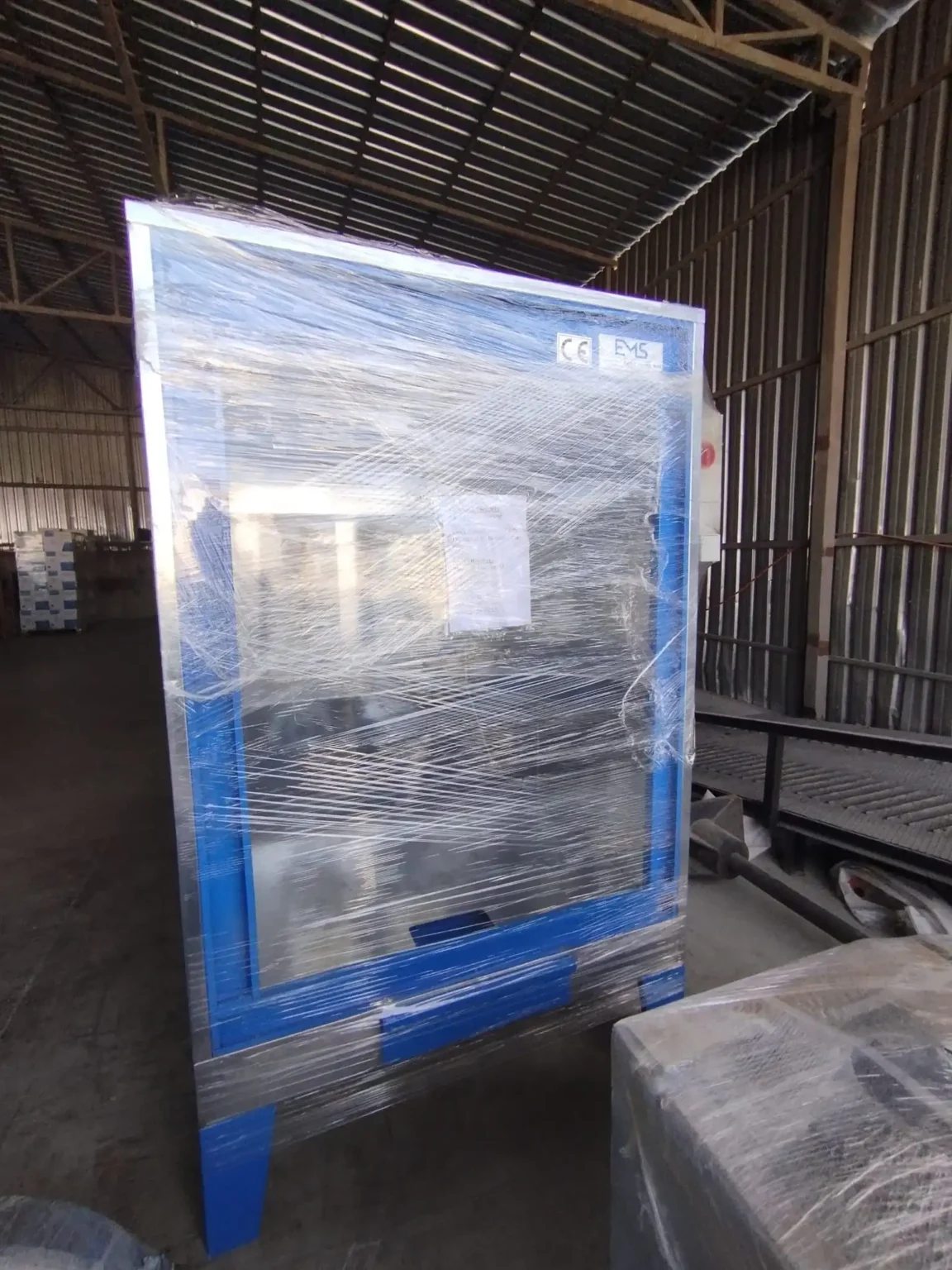
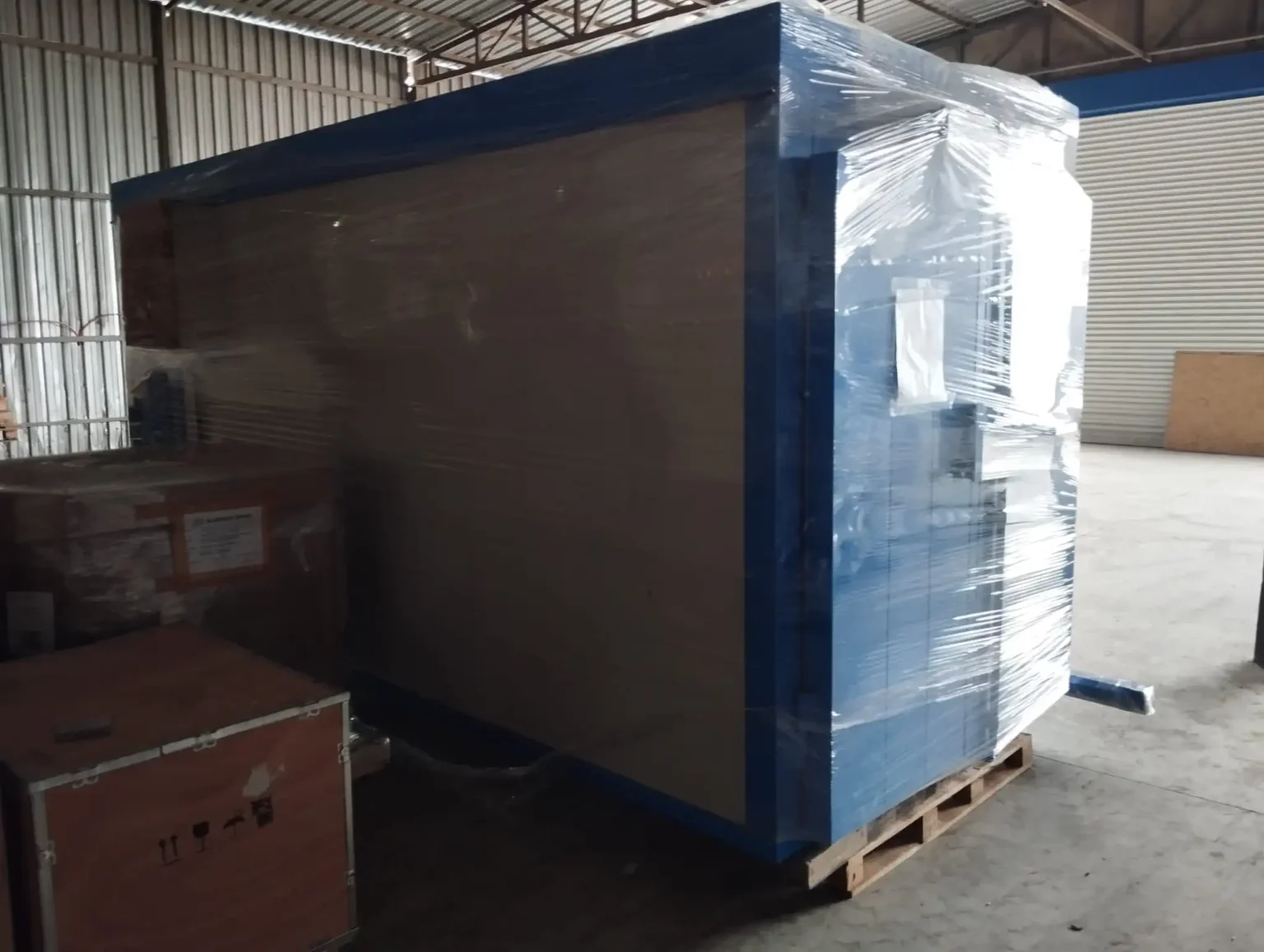
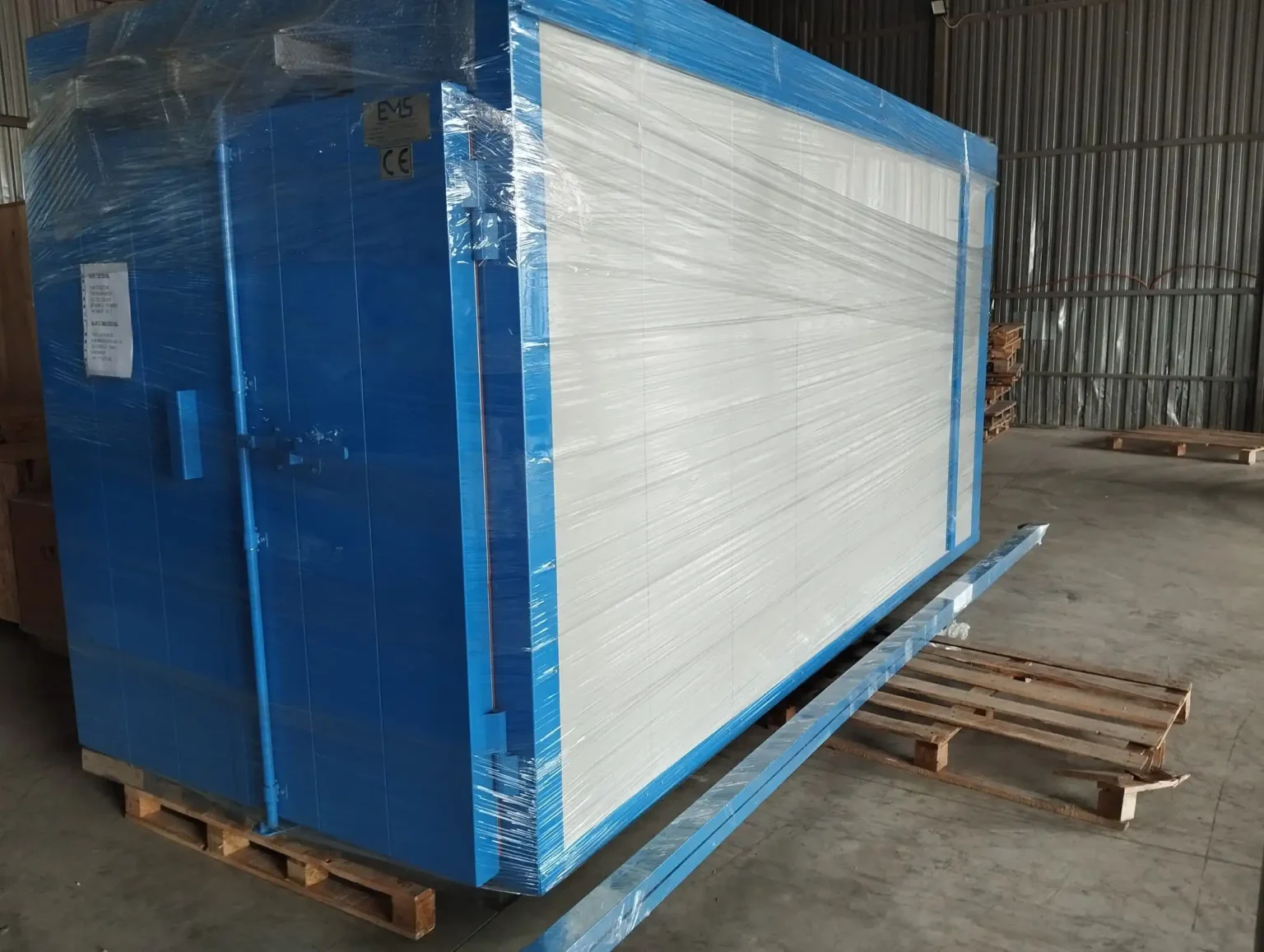
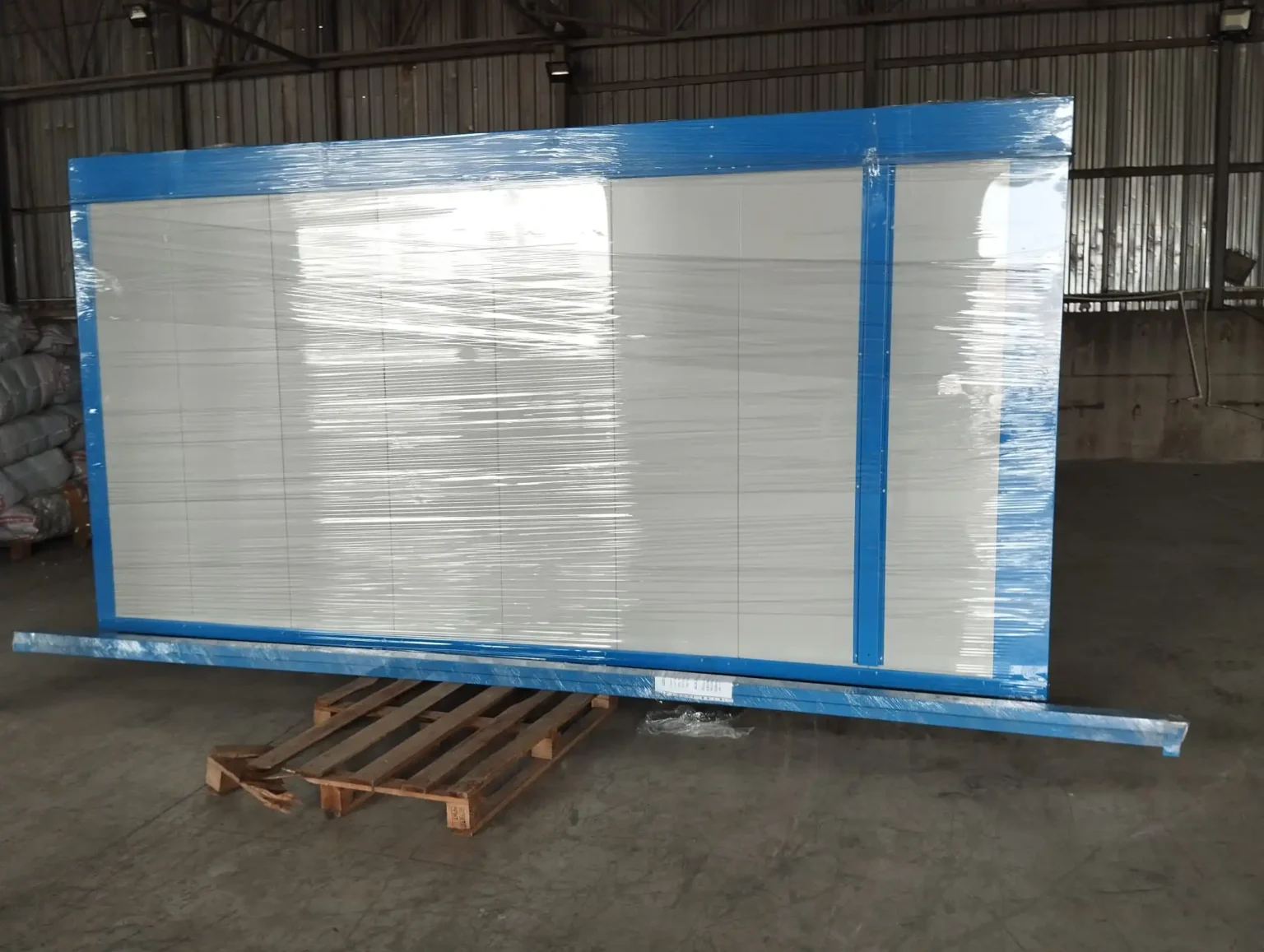
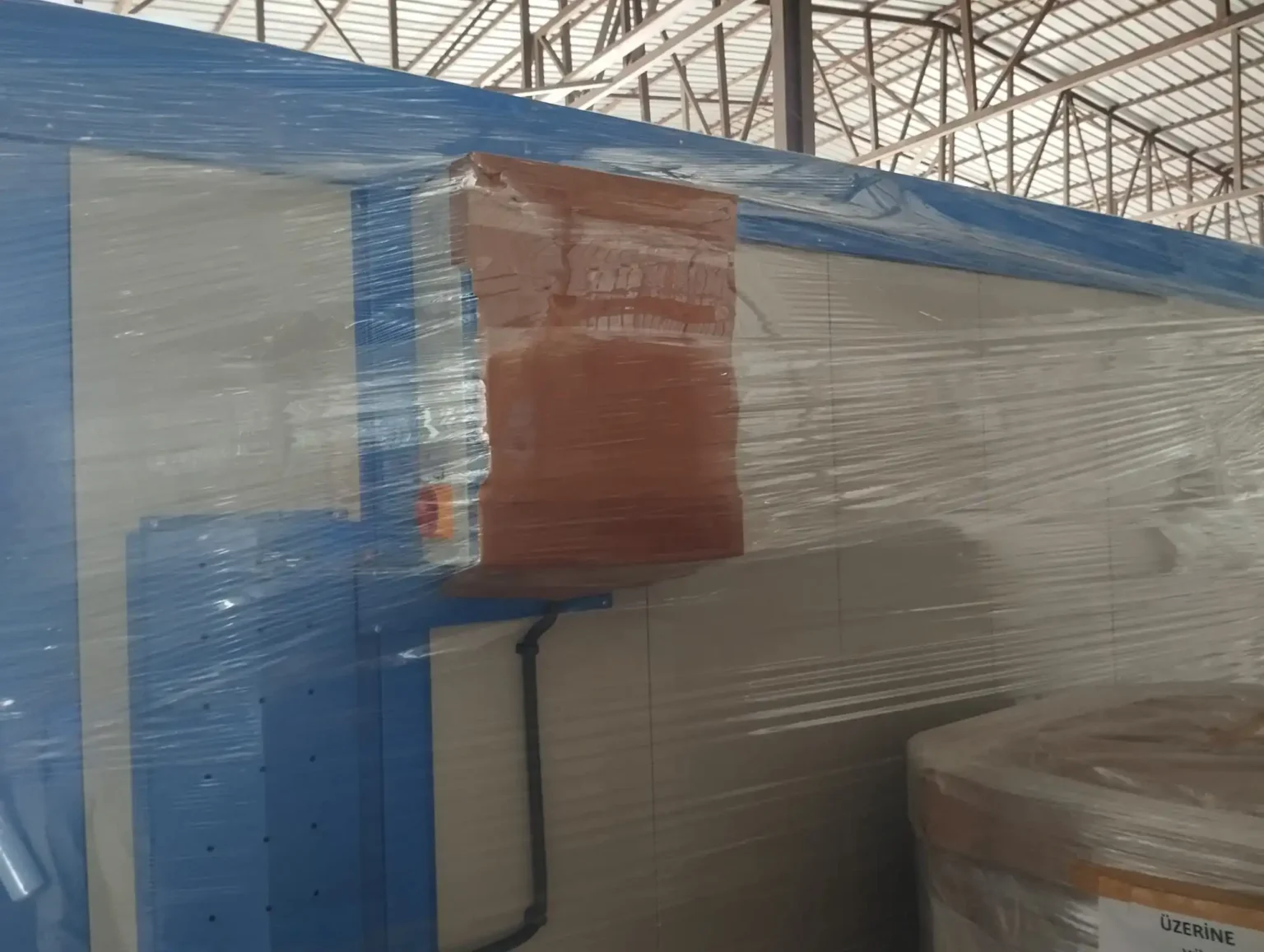
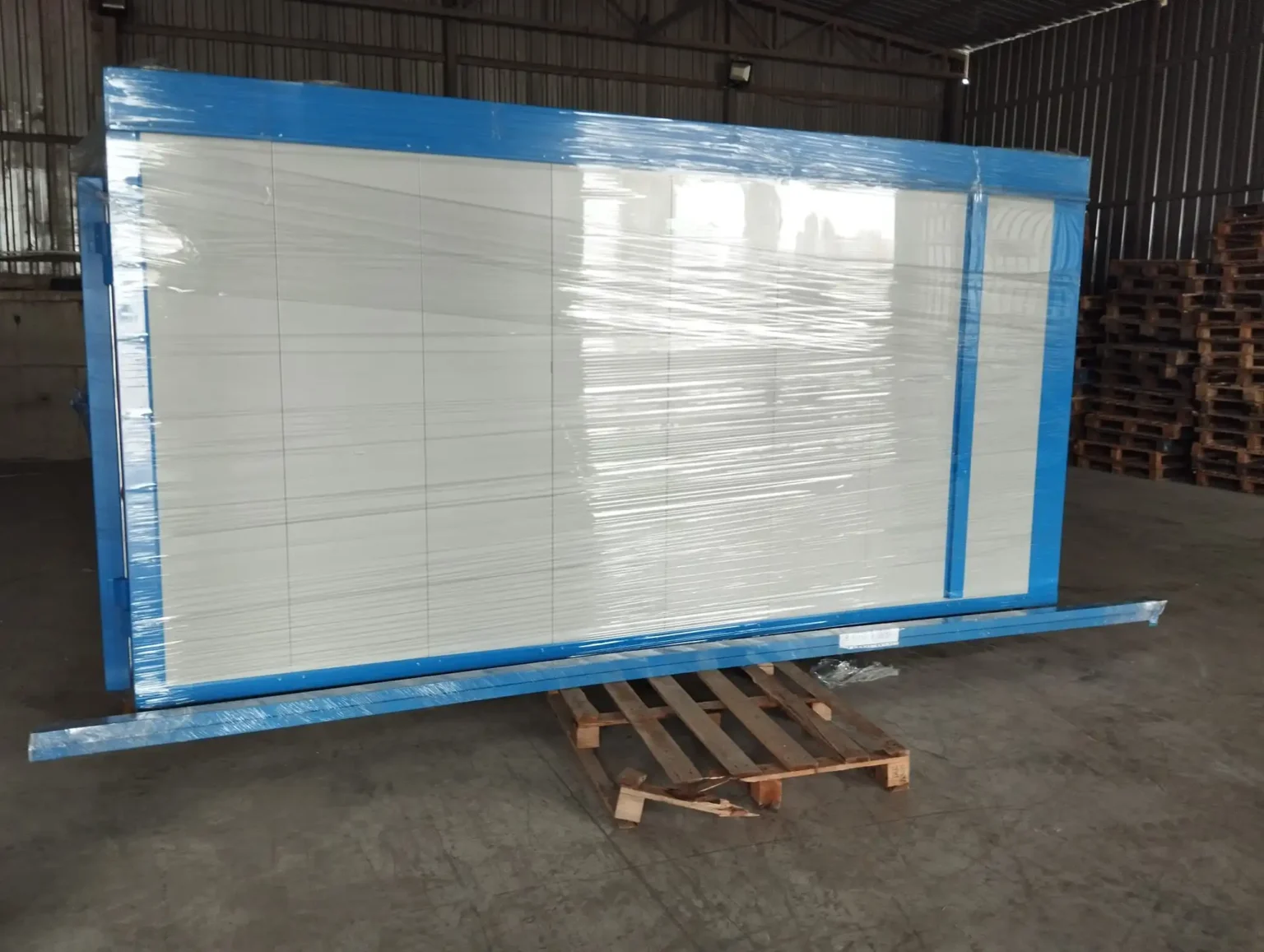
L’équipement de revêtement en poudre est utilisé pour appliquer une fine couche de poudre sur une surface métallique. Ce type de revêtement est appliqué par un procédé électrostatique et constitue une méthode très populaire pour la finition des pièces métalliques.
Ce type d’équipement peut être divisé en deux grandes catégories : automatiques et manuels. Les cabines automatiques sont plus populaires car elles offrent de meilleurs taux de production, mais elles sont également plus chères.
Une cabine à poudre est une enceinte dans laquelle se déroule le processus de revêtement en poudre. L’équipement de revêtement en poudre comprend un four dans lequel les pièces sont chauffées pour activer la poudre, un pistolet qui pulvérise ou brosse la poudre, une bande transporteuse qui déplace les pièces à travers le four et des pistolets de type cartouche pour appliquer des revêtements plus épais avec moins de pulvérisation.
Le revêtement en poudre est une technique utilisée pour donner une finition aux pièces métalliques. Cette technique est utilisée depuis de nombreuses années et reste aujourd’hui l’une des techniques les plus populaires.
L’équipement de revêtement en poudre comprend des cabines, des fours, des pistolets, des machines, des lignes et des convoyeurs. Une cabine peut être automatique ou manuelle. Une cabine automatique est plus chère qu’une cabine manuelle mais elle est aussi plus rapide et plus efficace