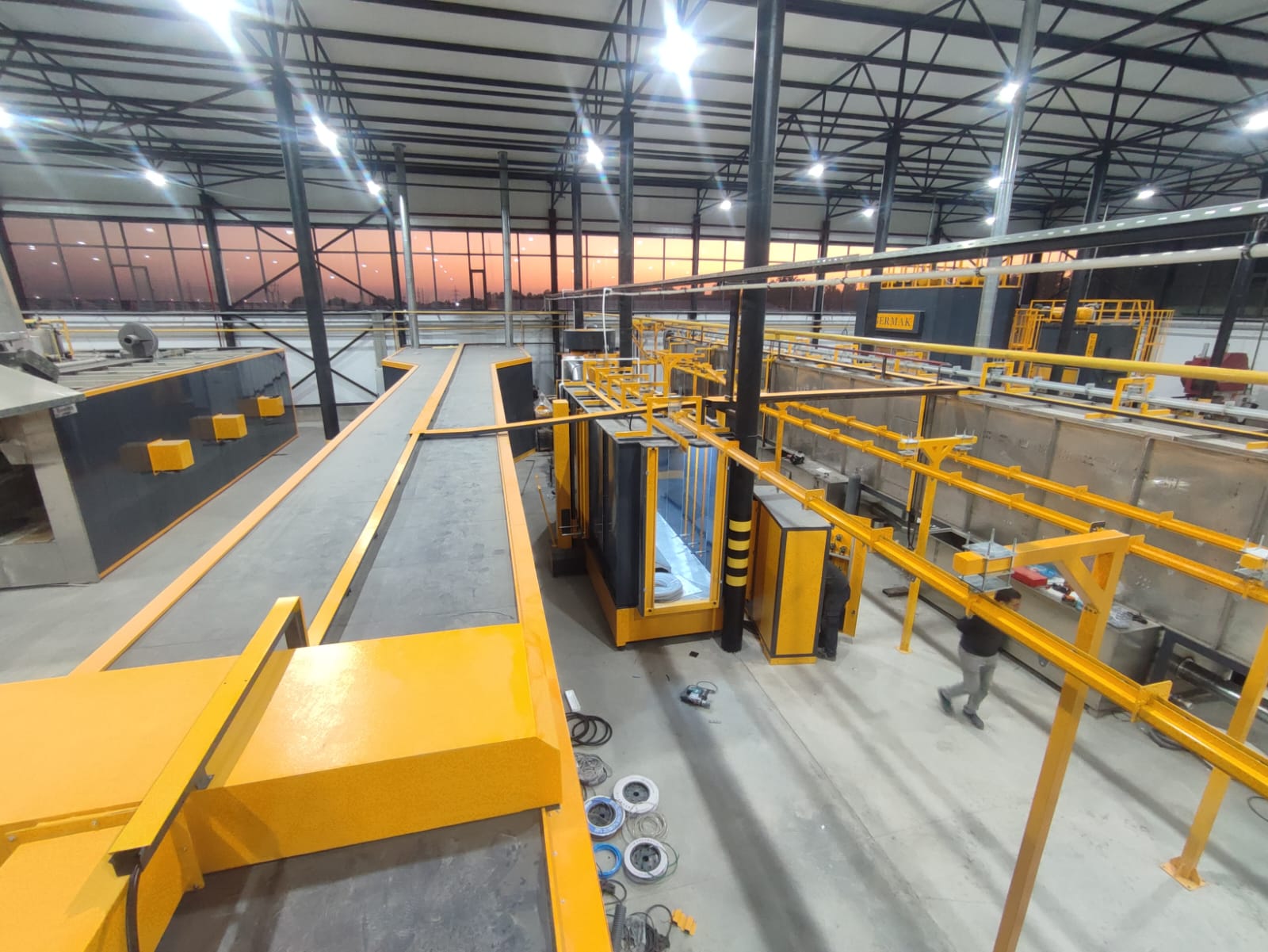
Type de Peinture Industrielle: La peinture industrielle joue un rôle crucial dans de nombreux secteurs, de l’automobile à l’aéronautique en passant par la construction et l’électronique. Ce procédé n’est pas seulement une question d’esthétique, mais il est aussi essentiel pour la protection des surfaces contre la corrosion, l’usure, et d’autres agressions extérieures. Les technologies de peinture industrielle ont considérablement évolué au fil des décennies, permettant d’améliorer la durabilité, la qualité du revêtement, et l’efficacité énergétique des processus.
Le thermolaquage, par exemple, est devenu une méthode privilégiée pour l’application de revêtements en poudre sur diverses surfaces métalliques. Ce procédé consiste à appliquer une peinture en poudre sur une surface, puis à la chauffer dans un four pour la polymériser, créant ainsi un revêtement durable et résistant. Les systèmes de peinture modernes intègrent souvent des technologies avancées telles que l’électrostatique, qui permet une application plus uniforme de la poudre et une meilleure adhérence sur les surfaces complexes.
L’utilisation des fours industriels et des pistolets à peinture électrostatiques est désormais monnaie courante dans de nombreux ateliers de peinture. Ces équipements permettent d’assurer une application homogène et de contrôler avec précision les conditions de séchage et de cuisson de la peinture, garantissant ainsi des finitions de haute qualité. Les fours de thermolaquage, en particulier, sont conçus pour atteindre des températures élevées nécessaires à la polymérisation des revêtements en poudre, tandis que les pistolets à peinture poudre epoxy sont spécialement développés pour une application efficace de la peinture en poudre.
L’évolution de ces technologies s’accompagne d’une prise de conscience croissante des enjeux environnementaux et économiques. Les procédés de poudrage peinture et de revêtement en poudre sont souvent préférés en raison de leur faible impact environnemental comparé aux peintures liquides traditionnelles. De plus, ces techniques permettent une réduction significative des déchets et une réutilisation de la poudre excédentaire, rendant le processus plus économique.
Cependant, la mise en œuvre de ces technologies nécessite des équipements spécifiques et une maintenance rigoureuse. Les filtres de cabine de peinture jouent un rôle essentiel dans la préservation de la qualité de l’air dans les ateliers, tandis que les systèmes de peinture doivent être régulièrement entretenus pour assurer leur performance optimale. De plus, l’intégration de robots de peinture industrielle et d’autres systèmes automatisés est de plus en plus courante, contribuant à améliorer la précision, la rapidité, et la sécurité des opérations.
En somme, la peinture industrielle est bien plus qu’une simple opération de finition. Elle est un élément clé de la chaîne de production, nécessitant des connaissances spécialisées et des équipements de pointe pour garantir des résultats à la hauteur des exigences de l’industrie moderne.
Introduction générale à la peinture industrielle
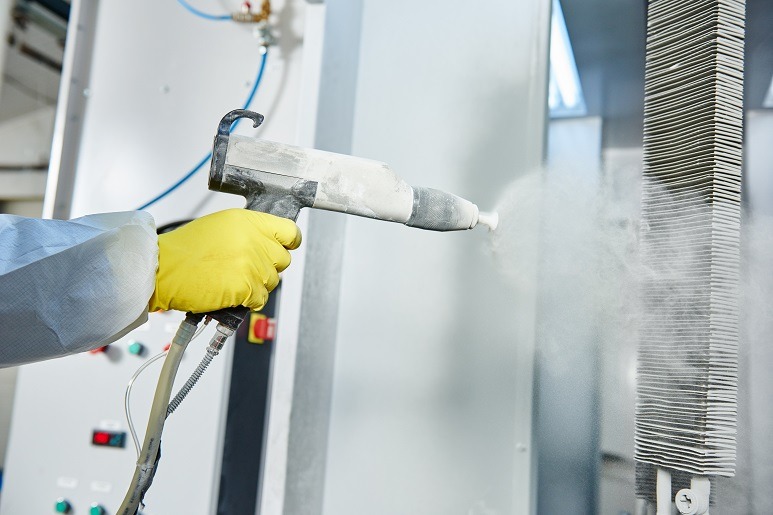
Dans le contexte industriel actuel, la diversité des matériaux et des besoins de revêtement a conduit à la multiplication des types de procédés de revêtement métallique. Chaque procédé est conçu pour répondre à des exigences spécifiques, qu’il s’agisse de résistance à la corrosion, d’amélioration de l’adhésion des couches ultérieures, ou de l’esthétique du produit fini. Parmi les techniques les plus courantes, on trouve le thermolaquage, la peinture électrostatique en poudre, et l’application de revêtements liquides spécialisés. Chacune de ces méthodes a ses propres avantages et limites, dépendant du matériau à traiter, des conditions environnementales, et des coûts de production.
Le thermolaquage est particulièrement apprécié pour sa capacité à produire un revêtement uniforme et sans défauts visibles. Ce procédé est largement utilisé dans l’industrie automobile, où la durabilité et l’esthétique des composants peints sont primordiales. Les fours de thermolaquage, capables de maintenir des températures précises et élevées, jouent un rôle clé dans la réussite de ce procédé. Ces fours assurent que la peinture en poudre se liquéfie puis se solidifie en une couche lisse et résistante. En parallèle, les pistolets de peinture thermolaquage sont conçus pour maximiser l’efficacité de l’application, en réduisant le gaspillage de peinture et en assurant une couverture uniforme des surfaces complexes.
Outre le thermolaquage, la peinture électrostatique en poudre est une autre méthode populaire, particulièrement efficace pour les objets métalliques. Ce procédé utilise des charges électrostatiques pour attirer la peinture en poudre vers l’objet à peindre, assurant une adhérence forte et une distribution homogène du matériau. Les pistolets à peinture électrostatiques sont des outils essentiels dans ce contexte, capables de manipuler différents types de poudres, y compris les poudres époxy, qui offrent une excellente résistance chimique et thermique.
En plus de ces procédés, l’industrie a vu une avancée significative dans les systèmes de séchage industriel. Traditionnellement, le séchage de la peinture impliquait des processus longs et énergivores. Aujourd’hui, les fours de revenu tunnel et les systèmes de séchage à haute température permettent un durcissement rapide des peintures, réduisant ainsi les temps d’arrêt de la production. Ces équipements sont souvent couplés à des fours pyrolyse industriels pour le nettoyage et la maintenance des outils, permettant de maintenir les équipements en excellent état de fonctionnement.
L’une des préoccupations croissantes dans le domaine de la peinture industrielle est l’impact environnemental des processus de revêtement. Les méthodes traditionnelles utilisant des solvants organiques volatils (VOC) sont progressivement remplacées par des procédés plus respectueux de l’environnement, comme le revêtement en poudre. Ce dernier ne produit pratiquement pas de COV et permet de récupérer la poudre non adhérente pour une utilisation ultérieure, minimisant ainsi les déchets. L’industrie s’oriente également vers l’utilisation de fours à gaz industriels plus efficaces sur le plan énergétique, comme ceux disponibles au Québec, qui offrent des options de chauffage plus écologiques et économiques.
En matière de maintenance, l’entretien régulier des filtres de cabine de peinture et des systèmes d’évacuation est essentiel pour garantir un environnement de travail sain et sécuritaire. Les cabines de poudrage sont particulièrement sensibles à l’accumulation de résidus de peinture, ce qui peut affecter la qualité du revêtement et la santé des opérateurs. Par conséquent, des programmes de maintenance préventive sont souvent mis en place pour s’assurer que les cabines fonctionnent à leur plein potentiel, avec des filtres régulièrement remplacés et des systèmes de ventilation optimisés.
Enfin, l’avenir de la peinture industrielle semble de plus en plus lié à l’automatisation et à l’intégration de l’intelligence artificielle. Les robots de peinture industriels sont déjà utilisés dans des environnements de production à grande échelle, où ils apportent une précision et une répétabilité impossibles à atteindre manuellement. Ces robots, associés à des systèmes de contrôle en temps réel, permettent de surveiller et d’ajuster instantanément les paramètres de peinture, réduisant ainsi les défauts et augmentant l’efficacité globale du processus.
En conclusion, la peinture industrielle n’est pas seulement une question de revêtement de surface, mais une technologie complexe qui combine chimie, physique et ingénierie pour répondre aux exigences rigoureuses de l’industrie moderne. Que ce soit par le biais du poudrage peinture, du thermolaquage, ou de la peinture électrostatique, chaque méthode offre des solutions adaptées aux besoins spécifiques des différents secteurs. Avec les avancées continues dans les équipements et les procédés, l’industrie de la peinture reste à la pointe de l’innovation technologique, tout en s’efforçant de réduire son impact environnemental et d’améliorer l’efficacité de ses opérations.
Le procédé de poudrage peinture
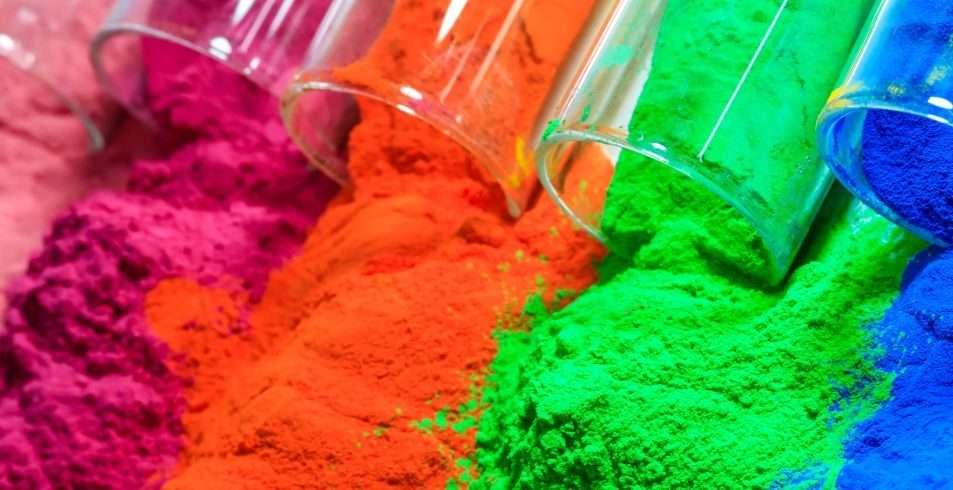
Le poudrage peinture, également connu sous le nom de revêtement en poudre, est un procédé de finition utilisé dans de nombreuses industries pour appliquer un revêtement protecteur et esthétique sur diverses surfaces, principalement métalliques. Ce procédé est particulièrement apprécié pour sa capacité à produire des finitions durables, uniformes et écologiquement responsables. Contrairement aux peintures liquides traditionnelles, qui nécessitent l’utilisation de solvants, le poudrage peinture utilise une poudre sèche qui est appliquée électrostatiquement sur la surface à traiter, puis chauffée pour former un revêtement dur et homogène.
Le poudrage peinture commence par la préparation de la surface. Cette étape est cruciale, car une surface mal préparée peut entraîner une mauvaise adhérence de la poudre, compromettant ainsi la qualité et la durabilité du revêtement. La préparation implique souvent un nettoyage minutieux pour éliminer les contaminants tels que l’huile, la graisse, et la rouille, ainsi qu’un traitement chimique ou mécanique pour créer une surface réceptive à la poudre. Une fois la surface prête, elle est chargée électrostatiquement pour attirer la poudre, qui est ensuite appliquée à l’aide d’un pistolet de peinture poudre epoxy ou un pistolet à peinture électrostatique.
L’une des principales caractéristiques du revêtement en poudre est son efficacité. La poudre adhère fermement à la surface grâce aux forces électrostatiques, ce qui permet de minimiser les pertes de matériau. De plus, tout excès de poudre peut être récupéré et réutilisé, ce qui rend ce procédé particulièrement économique et respectueux de l’environnement. Cette caractéristique fait du poudrage peinture un choix privilégié dans des industries où la gestion des déchets et l’efficacité des coûts sont essentielles.
Après l’application de la poudre, la pièce revêtue est placée dans un four de thermolaquage où elle est chauffée à des températures généralement comprises entre 160 et 200 degrés Celsius. Cette étape, connue sous le nom de polymérisation peinture, permet à la poudre de fondre et de se solidifier en un revêtement uniforme et résistant. Les fours industriels utilisés pour cette étape doivent maintenir des températures précises pour garantir une polymérisation complète sans endommager le substrat. Les fours haute température industriels sont spécialement conçus pour cette tâche, offrant des performances fiables et une efficacité énergétique.
Le poudrage peinture présente plusieurs avantages par rapport aux méthodes de revêtement traditionnelles. Tout d’abord, il est plus durable et résistant à l’usure, à la corrosion, et aux impacts, ce qui le rend idéal pour des applications exigeantes, telles que dans l’industrie automobile ou la fabrication d’équipements lourds. De plus, le revêtement en poudre offre une grande flexibilité en termes de finition. Il est disponible dans une large gamme de couleurs et de textures, permettant de personnaliser les produits selon les spécifications des clients. Enfin, le poudrage peinture est plus sûr pour les opérateurs et l’environnement, car il ne contient pas de solvants volatils et produit peu de déchets.
L’utilisation d’équipements spécialisés est essentielle pour garantir la qualité et l’efficacité du procédé. Par exemple, les pistolets à peinture poudre epoxy et les pistolets à peinture thermolaquage sont conçus pour appliquer la poudre de manière uniforme sur des surfaces complexes. Ces outils sont souvent équipés de buses réglables, comme la buse Nordson, qui permettent de contrôler avec précision le débit et la direction de la poudre. De plus, les cabines de poudrage sont équipées de systèmes de ventilation et de filtres de cabine de peinture pour capturer l’excès de poudre et maintenir un environnement de travail propre et sûr.
Les systèmes de peinture utilisés dans le poudrage peinture sont également de plus en plus automatisés, avec l’intégration de robots de peinture industriels qui permettent d’améliorer la précision, la vitesse, et la répétabilité du processus. Ces systèmes peuvent être programmés pour appliquer la poudre de manière uniforme sur des surfaces de formes variées, réduisant ainsi le besoin d’interventions manuelles et minimisant les erreurs.
Dans certains cas, il peut être nécessaire de procéder à des retouches de peinture thermolaquée après le processus initial de poudrage. Ces retouches peuvent être effectuées pour corriger des défauts mineurs ou pour ajuster la couleur et la texture du revêtement final. Les pistolets de retouche sont souvent utilisés pour appliquer une petite quantité de poudre sur les zones concernées, suivie d’une nouvelle cuisson pour polymériser la poudre ajoutée.
Le poudrage peinture n’est pas seulement utilisé pour des pièces de grande taille ou des surfaces complexes ; il est également adapté à des applications de plus petite envergure. Les petites cabines de peinture et les petits fours industriels sont souvent employés dans des ateliers où l’espace est limité ou où les volumes de production sont plus modestes. Ces équipements offrent les mêmes avantages en termes de qualité de revêtement, tout en étant plus accessibles pour les petites et moyennes entreprises.
En conclusion, le poudrage peinture est une technique de revêtement polyvalente, durable et respectueuse de l’environnement. Grâce à l’innovation continue dans les équipements et les procédés, cette méthode continue de s’imposer comme une solution de choix pour de nombreuses applications industrielles. Que ce soit pour des pièces de grande taille ou des objets plus petits, le poudrage peinture offre des performances inégalées en termes de protection, de durabilité, et d’esthétique.
Je vais maintenant rédiger la troisième section intitulée “Le thermolaquage : Un procédé essentiel”. Cette section décrira le procédé de thermolaquage, son importance, et les différents équipements impliqués.
Le thermolaquage : Un procédé essentiel
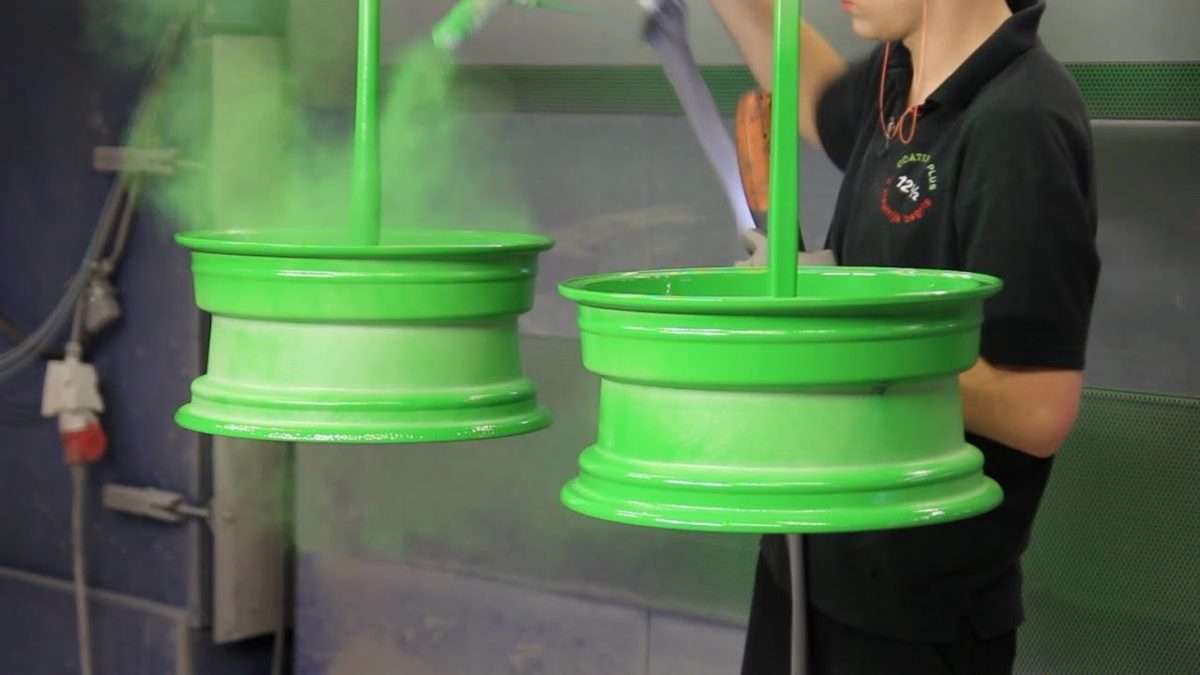
Le thermolaquage est une technique de revêtement par poudre qui s’est imposée comme un standard dans de nombreuses industries grâce à sa capacité à fournir des finitions de haute qualité, résistantes et durables. Ce procédé consiste à appliquer une peinture en poudre sur une surface, généralement métallique, puis à chauffer cette surface pour provoquer la fusion et la polymérisation de la poudre, créant ainsi un revêtement solide et uniforme. Le thermolaquage est particulièrement apprécié pour ses performances exceptionnelles en matière de protection contre la corrosion, l’abrasion, et les agressions chimiques, tout en offrant une large palette de finitions esthétiques.
L’un des éléments clés du thermolaquage est l’application de la poudre elle-même. Ce processus est généralement réalisé à l’aide de pistolets de peinture thermolaquage ou de pistolets à peinture électrostatiques. Ces pistolets chargent la poudre électrostatiquement, ce qui permet une adhérence immédiate et uniforme sur la surface cible. La peinture électrostatique en poudre est ensuite polymérisée dans un four de thermolaquage à des températures élevées, typiquement entre 160 et 200 degrés Celsius. La polymérisation peinture est un processus chimique crucial où les particules de poudre fusionnent pour former un film continu et dur, garantissant ainsi la durabilité du revêtement.
Les fours de thermolaquage jouent un rôle central dans la réussite du processus de thermolaquage. Ils sont conçus pour atteindre et maintenir des températures spécifiques qui permettent à la poudre de fondre uniformément et de s’étendre sur la surface traitée. Les fours haute température industriels sont souvent utilisés pour cette application en raison de leur capacité à maintenir des températures précises et constantes sur de longues périodes, essentielles pour assurer une cuisson homogène du revêtement. Ces fours sont dotés de systèmes de contrôle avancés qui permettent de surveiller en temps réel les conditions de température et d’ajuster les paramètres pour obtenir des résultats optimaux.
Le choix du four de thermolaquage dépend largement du type de pièces à traiter et des volumes de production. Pour des productions à grande échelle, les fours de revenu tunnel sont souvent privilégiés. Ces équipements permettent un traitement continu des pièces, augmentant ainsi l’efficacité et la rapidité du processus. En revanche, pour des pièces plus spécifiques ou des productions en petites séries, des petits fours industriels ou des fours à gaz industriels peuvent être utilisés. Les fours à gaz, en particulier, sont populaires au Québec pour leur efficacité énergétique et leur flexibilité, car ils peuvent être rapidement ajustés pour différentes tailles et types de pièces.
Le thermolaquage se distingue également par son impact environnemental réduit. Contrairement aux procédés de peinture traditionnels qui utilisent des solvants organiques volatils (COV), le thermolaquage n’en émet pratiquement aucun. De plus, la poudre non utilisée peut être facilement récupérée et réutilisée, minimisant ainsi les déchets et les coûts associés au processus. Cette caractéristique rend le thermolaquage particulièrement adapté aux industries soucieuses de réduire leur empreinte écologique tout en maintenant des standards élevés de qualité.
Le thermolaquage n’est pas seulement utilisé pour des raisons fonctionnelles ; il offre également une grande flexibilité en termes de finitions esthétiques. Les systèmes de peinture modernes permettent d’appliquer des poudres de différentes couleurs, textures et effets visuels, répondant ainsi aux exigences spécifiques des clients. Que ce soit pour des applications industrielles où la durabilité prime, ou pour des produits grand public où l’esthétique est tout aussi importante, le thermolaquage offre une solution polyvalente et efficace.
Cependant, pour tirer pleinement parti des avantages du thermolaquage, une maintenance régulière des équipements est nécessaire. Les filtres de cabine de peinture doivent être remplacés régulièrement pour garantir une qualité constante de l’air et éviter la contamination de la peinture. De même, les pistolets de peinture thermolaquage nécessitent un entretien régulier pour éviter les blocages et maintenir une application uniforme de la poudre. Les fours industriels eux-mêmes doivent être calibrés et inspectés périodiquement pour s’assurer qu’ils fonctionnent correctement et que la température est uniformément répartie à l’intérieur de la chambre de cuisson.
En outre, l’intégration de robots de peinture industriels dans le processus de thermolaquage est une tendance croissante, notamment dans les grandes installations de production. Ces robots permettent d’automatiser le processus d’application de la poudre, garantissant ainsi une précision et une répétabilité inégalées. Les robots peuvent être programmés pour suivre des trajectoires complexes et appliquer la poudre de manière uniforme, même sur des surfaces difficiles d’accès ou de formes irrégulières. Cette automatisation contribue non seulement à améliorer la qualité du revêtement, mais aussi à réduire les coûts de main-d’œuvre et les erreurs humaines.
Le thermolaquage est également un procédé qui évolue constamment grâce aux avancées technologiques. De nouvelles formulations de poudre sont régulièrement développées pour améliorer encore les performances du revêtement, qu’il s’agisse de la résistance aux intempéries, de la brillance, ou de la flexibilité du film. De plus, les technologies de peinture électrostatique continuent de s’améliorer, offrant une meilleure couverture avec moins de matière, ce qui renforce encore l’efficacité et l’économie de ce procédé.
Enfin, le thermolaquage est un choix de plus en plus populaire pour les retouches de peinture, notamment en raison de sa capacité à fournir une finition uniforme même sur des surfaces qui ont déjà été traitées. Les retouches de peinture thermolaquée peuvent être réalisées rapidement et efficacement, souvent sans avoir besoin de décaper ou de préparer à nouveau la surface de manière intensive. Cela permet de prolonger la durée de vie des pièces traitées et de maintenir leur apparence esthétique au fil du temps.
En conclusion, le thermolaquage est un procédé de revêtement essentiel dans l’industrie moderne. Il combine des performances exceptionnelles en termes de protection et de durabilité avec une flexibilité esthétique et un impact environnemental réduit. Grâce à l’innovation continue dans les technologies de peinture et les équipements, le thermolaquage reste à la pointe des solutions de revêtement, répondant aux exigences croissantes des industries pour des produits de haute qualité et durables.
Les équipements de peinture : Pistolets et cabines
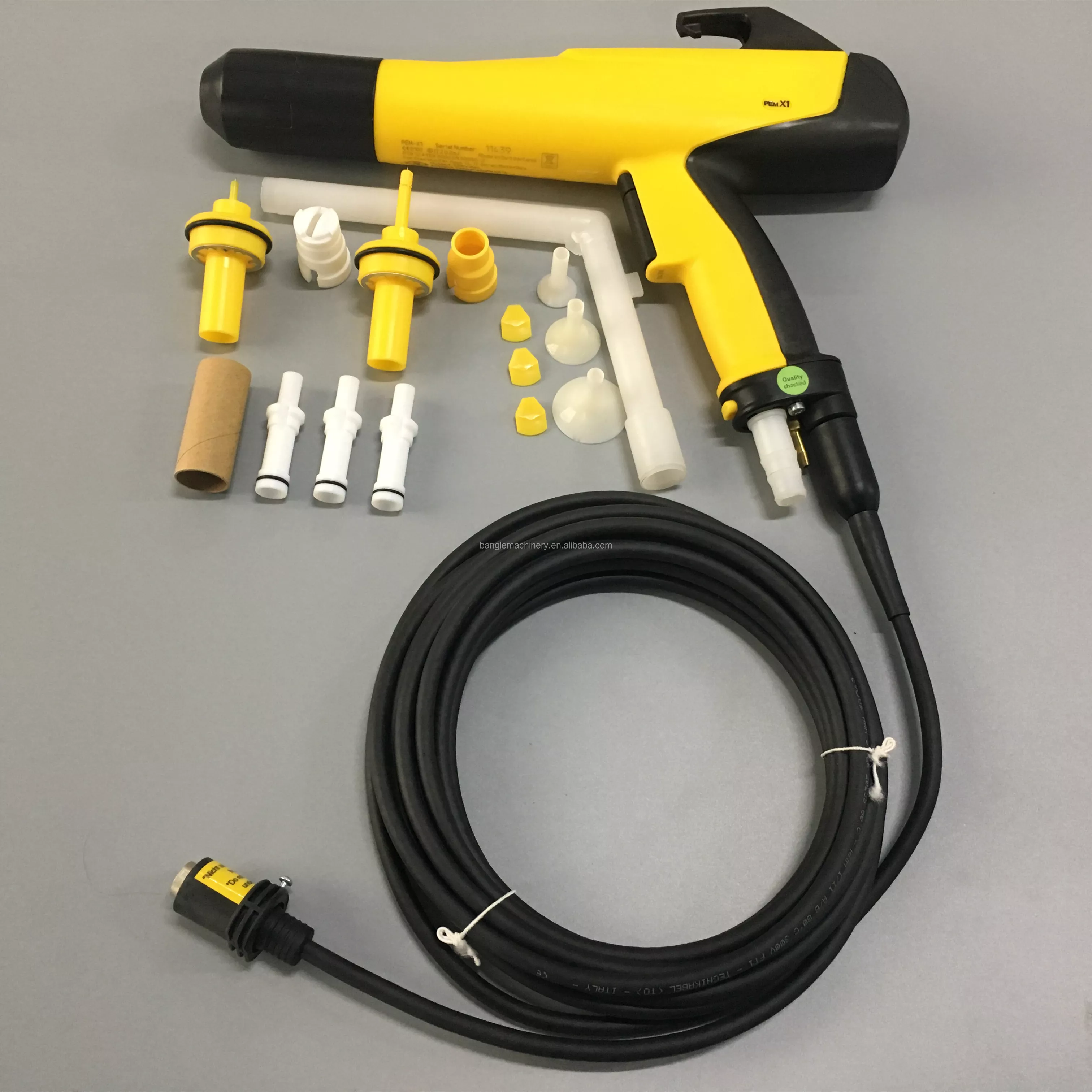
Dans l’univers de la peinture industrielle, les équipements jouent un rôle crucial pour garantir la qualité, l’efficacité et la sécurité du processus de revêtement. Parmi les outils les plus essentiels figurent les pistolets de peinture et les cabines de peinture, qui sont au cœur des opérations de poudrage et de thermolaquage. Ces équipements, bien qu’ils puissent paraître simples à première vue, intègrent des technologies sophistiquées qui permettent d’optimiser l’application de la peinture tout en assurant une utilisation économique des matériaux et une protection environnementale adéquate.
Les pistolets de peinture sont des outils spécialement conçus pour l’application précise et uniforme de la peinture en poudre sur les surfaces à traiter. Il existe plusieurs types de pistolets, chacun adapté à des besoins spécifiques. Par exemple, les pistolets à peinture poudre epoxy sont utilisés pour appliquer des revêtements en poudre époxy, connus pour leur résistance chimique et leur durabilité exceptionnelle. Ces pistolets sont souvent équipés de technologies électrostatiques qui chargent les particules de poudre avant qu’elles ne soient pulvérisées sur la surface, assurant ainsi une adhésion forte et uniforme.
Le pistolet à peinture électrostatique est un autre outil clé dans la peinture industrielle. Ce type de pistolet utilise des forces électrostatiques pour attirer la peinture en poudre vers la surface à recouvrir, minimisant ainsi le gaspillage de matériau et améliorant la couverture, même sur des surfaces complexes ou irrégulières. Les buses de ces pistolets, comme la buse Nordson, sont conçues pour offrir un contrôle précis du flux de poudre, permettant aux opérateurs de régler la pulvérisation selon les besoins spécifiques de chaque projet. Ces pistolets sont également réputés pour leur capacité à appliquer des couches fines et régulières de peinture, ce qui est essentiel pour obtenir des finitions de haute qualité.
Les cabines de peinture sont des environnements contrôlés où la peinture est appliquée sur les pièces à traiter. Ces cabines sont conçues pour contenir la peinture pulvérisée et pour protéger à la fois l’environnement de travail et les opérateurs des risques associés aux émissions de peinture. Il existe plusieurs types de cabines, allant des petites cabines de peinture pour les productions de faible volume aux cabines de poudrage de grande taille pour les opérations industrielles à grande échelle. Les cabines de peinture sont généralement équipées de systèmes de filtration d’air avancés, comme les filtres de cabine de peinture, qui capturent les particules de peinture en suspension et assurent un air propre dans l’atelier.
Un aspect crucial de la maintenance des cabines de peinture est la gestion des filtres. Les filtres de cabine de peinture doivent être régulièrement inspectés et remplacés pour garantir leur efficacité. Ces filtres jouent un rôle vital en capturant les particules de peinture en suspension dans l’air, prévenant ainsi la contamination croisée des couleurs et protégeant la santé des opérateurs. Une maintenance inadéquate des filtres peut entraîner une accumulation de peinture à l’intérieur de la cabine, réduisant la qualité du revêtement et augmentant les risques pour la sécurité.
Les cabines de poudrage sont spécifiquement conçues pour le processus de revêtement en poudre. Elles sont équipées de systèmes d’aspiration et de récupération de poudre qui permettent de recycler l’excédent de poudre pour une réutilisation ultérieure, rendant le processus plus économique et écologique. De plus, ces cabines sont souvent dotées de systèmes de ventilation qui évitent l’accumulation de poudre dans l’air, réduisant ainsi les risques d’explosion et assurant un environnement de travail sécurisé. L’achat d’une cabine de poudrage d’occasion peut être une option économique pour les entreprises cherchant à s’équiper sans engager des dépenses trop importantes, à condition que la cabine soit soigneusement inspectée et remise en état avant utilisation.
L’efficacité du processus de peinture dépend également de la qualité des pistolets de peinture. Les pistolets de peinture thermolaquage sont conçus pour fonctionner en tandem avec les systèmes de thermolaquage, permettant une application précise de la poudre avant que la pièce ne soit placée dans le four pour la cuisson. Ces pistolets doivent être calibrés pour assurer une distribution uniforme de la peinture, ce qui est essentiel pour éviter les défauts tels que les manques de couverture ou les surépaisseurs. Les pistolets modernes sont souvent équipés de systèmes de contrôle électronique qui permettent de régler avec précision les paramètres de pulvérisation, assurant ainsi une application constante et de haute qualité.
L’automatisation est une tendance croissante dans le domaine de la peinture industrielle, et les robots de peinture industriels en sont un excellent exemple. Ces robots sont capables d’exécuter des tâches répétitives avec une précision et une vitesse que l’homme ne peut égaler. En programmant les robots pour suivre des trajectoires spécifiques, il est possible d’appliquer la peinture avec une uniformité parfaite, même sur des pièces aux formes complexes. Les robots peuvent également être équipés de pistolets de peinture et programmés pour ajuster automatiquement les paramètres de pulvérisation en fonction des caractéristiques de la pièce, réduisant ainsi le besoin de supervision constante et augmentant l’efficacité du processus.
Enfin, il est important de noter que l’investissement dans des machines de peinture et des fours industriels de qualité est essentiel pour garantir la pérennité et la rentabilité des opérations de peinture. Une machine de peinture bien entretenue peut fonctionner de manière fiable pendant de nombreuses années, réduisant ainsi les coûts de remplacement et les temps d’arrêt de production. De même, un four de thermolaquage bien calibré et correctement entretenu assurera une polymérisation uniforme de la peinture, garantissant ainsi des finitions durables et résistantes.
En conclusion, les pistolets de peinture et les cabines de peinture sont des équipements essentiels dans le domaine de la peinture industrielle. Leur choix, leur utilisation et leur entretien jouent un rôle déterminant dans la qualité du revêtement final, l’efficacité du processus de peinture, et la sécurité des opérateurs. Avec l’essor de l’automatisation et des technologies avancées, ces équipements continuent d’évoluer, offrant des performances améliorées et des solutions adaptées aux besoins spécifiques de chaque industrie.
Maintenance et dépannage des installations
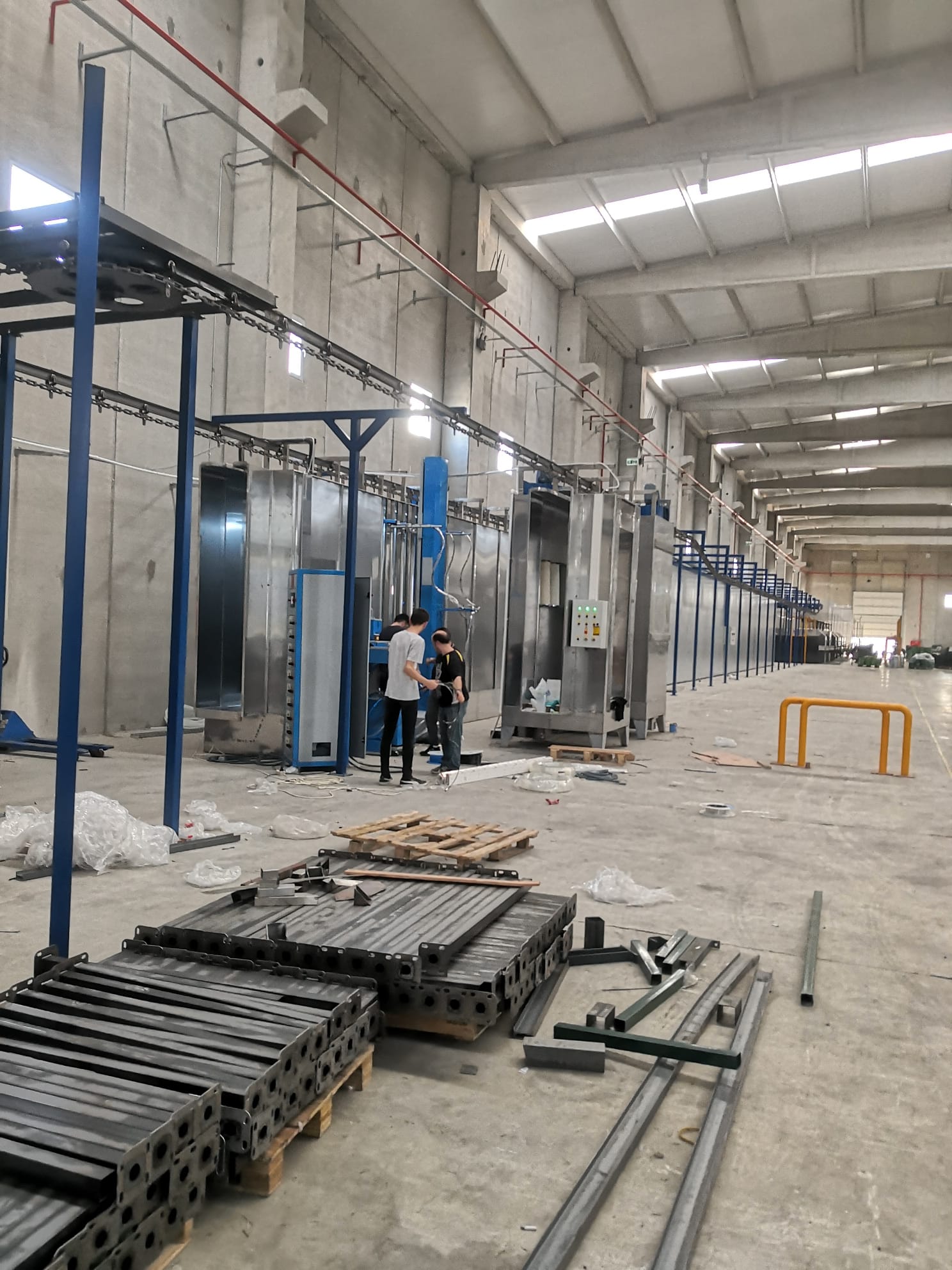
La maintenance des installations de peinture industrielle est un aspect crucial pour assurer la longévité, la sécurité et l’efficacité des opérations. Que ce soit pour des pistolets de peinture, des fours de thermolaquage, ou des cabines de poudrage, un entretien régulier et rigoureux est essentiel pour éviter les pannes, maintenir la qualité du revêtement, et minimiser les temps d’arrêt de production. La maintenance proactive permet non seulement de prolonger la durée de vie des équipements, mais aussi de prévenir des défaillances coûteuses qui pourraient interrompre la chaîne de production.
L’un des éléments les plus importants de la maintenance est l’inspection régulière des filtres de cabine de peinture. Ces filtres jouent un rôle essentiel en capturant les particules de peinture en suspension dans l’air, évitant ainsi la contamination de l’environnement de travail et garantissant une application uniforme de la peinture. Les filtres doivent être changés régulièrement pour maintenir leur efficacité. Un filtre obstrué ou endommagé peut entraîner une mauvaise ventilation dans la cabine, ce qui peut non seulement affecter la qualité de la peinture, mais aussi poser des risques pour la santé des opérateurs en raison de l’accumulation de substances toxiques dans l’air.
Outre les filtres, la maintenance des pistolets de peinture est également cruciale. Les pistolets doivent être nettoyés régulièrement pour éviter les blocages et garantir un jet de peinture constant et uniforme. Les buses des pistolets, telles que la buse Nordson, doivent être inspectées pour détecter tout signe d’usure ou de détérioration. Une buse endommagée peut affecter la pulvérisation de la peinture, entraînant des défauts tels que des stries ou des bulles sur la surface peinte. De plus, les pistolets doivent être calibrés régulièrement pour s’assurer qu’ils fonctionnent selon les spécifications du fabricant, en garantissant une application précise de la peinture.
Les fours de thermolaquage nécessitent également une attention particulière. Ces équipements doivent être régulièrement calibrés pour maintenir une température uniforme à l’intérieur du four, ce qui est crucial pour la polymérisation peinture. Une température incorrecte peut entraîner une polymérisation incomplète, compromettant ainsi la durabilité du revêtement. De plus, les systèmes de chauffage des fours doivent être inspectés pour s’assurer qu’ils fonctionnent de manière efficace et sécuritaire. Dans certains cas, des fours pyrolyse industriels sont utilisés pour le nettoyage des composants du four, en brûlant les résidus de peinture et autres contaminants accumulés au fil du temps.
Le dépannage des installations est une autre composante essentielle de la gestion des opérations de peinture industrielle. Malgré une maintenance régulière, des pannes peuvent survenir, nécessitant une intervention rapide pour minimiser les interruptions de production. Le dépannage des brûleurs de fours industriels est souvent nécessaire, car ces composants sont soumis à des conditions de chaleur intense et peuvent s’user ou tomber en panne au fil du temps. Le remplacement des brûleurs défectueux ou le réglage des systèmes de combustion peut restaurer le bon fonctionnement du four, assurant ainsi une cuisson uniforme de la peinture.
Le dépannage des pistolets de peinture est également une tâche courante. Les pistolets peuvent parfois rencontrer des problèmes tels que des fuites, des blocages ou des problèmes de pression. Un dépannage rapide implique généralement le démontage du pistolet, le nettoyage des composants internes, et le remplacement des pièces usées. Les opérateurs doivent être formés pour identifier rapidement les signes de dysfonctionnement et effectuer des réparations mineures pour éviter des interruptions prolongées.
Dans le cadre de la maintenance préventive, il est également important de surveiller l’état des systèmes de ventilation dans les cabines de peinture et les ateliers de production. Une ventilation inadéquate peut non seulement affecter la qualité de l’air, mais aussi entraîner des risques d’explosion en raison de l’accumulation de vapeurs inflammables. Les systèmes de ventilation doivent être régulièrement inspectés, nettoyés, et calibrés pour garantir qu’ils fonctionnent de manière optimale. Cela inclut le remplacement des filtres à air, la vérification des conduits pour détecter toute obstruction, et le réglage des ventilateurs pour maintenir un flux d’air adéquat.
L’intégration de systèmes de contrôle automatisés dans les installations de peinture industrielle facilite également la maintenance et le dépannage. Ces systèmes permettent de surveiller en temps réel les performances des équipements, détectant les anomalies avant qu’elles ne provoquent des pannes majeures. Par exemple, un système automatisé peut alerter les opérateurs en cas de baisse de pression dans un pistolet de peinture ou de fluctuation de température dans un four de thermolaquage, permettant ainsi une intervention rapide. Ces systèmes peuvent également être programmés pour effectuer des diagnostics réguliers, identifier les pièces susceptibles de s’user, et planifier leur remplacement avant qu’une panne ne survienne.
L’importance de la formation des opérateurs ne peut pas être sous-estimée dans le cadre de la maintenance et du dépannage. Les opérateurs doivent être formés non seulement à l’utilisation des équipements, mais aussi à leur entretien et à leur réparation. Une formation adéquate permet aux opérateurs de détecter rapidement les signes de dysfonctionnement et de prendre les mesures nécessaires pour éviter une défaillance complète du système. De plus, une bonne compréhension des systèmes de contrôle automatisés permet aux opérateurs d’interagir efficacement avec ces technologies, maximisant ainsi leur potentiel pour prévenir les pannes.
En conclusion, la maintenance et le dépannage des installations de peinture industrielle sont des éléments essentiels pour garantir une production continue, efficace et de haute qualité. Une approche proactive, combinant une maintenance préventive rigoureuse, un dépannage réactif, et une formation continue des opérateurs, est la clé pour minimiser les temps d’arrêt, prolonger la durée de vie des équipements, et assurer la satisfaction des clients. Les entreprises qui investissent dans des programmes de maintenance bien structurés et dans des technologies de pointe sont mieux équipées pour faire face aux défis de la production industrielle et pour maintenir leur compétitivité sur le marché.
Les fours industriels : Types et applications
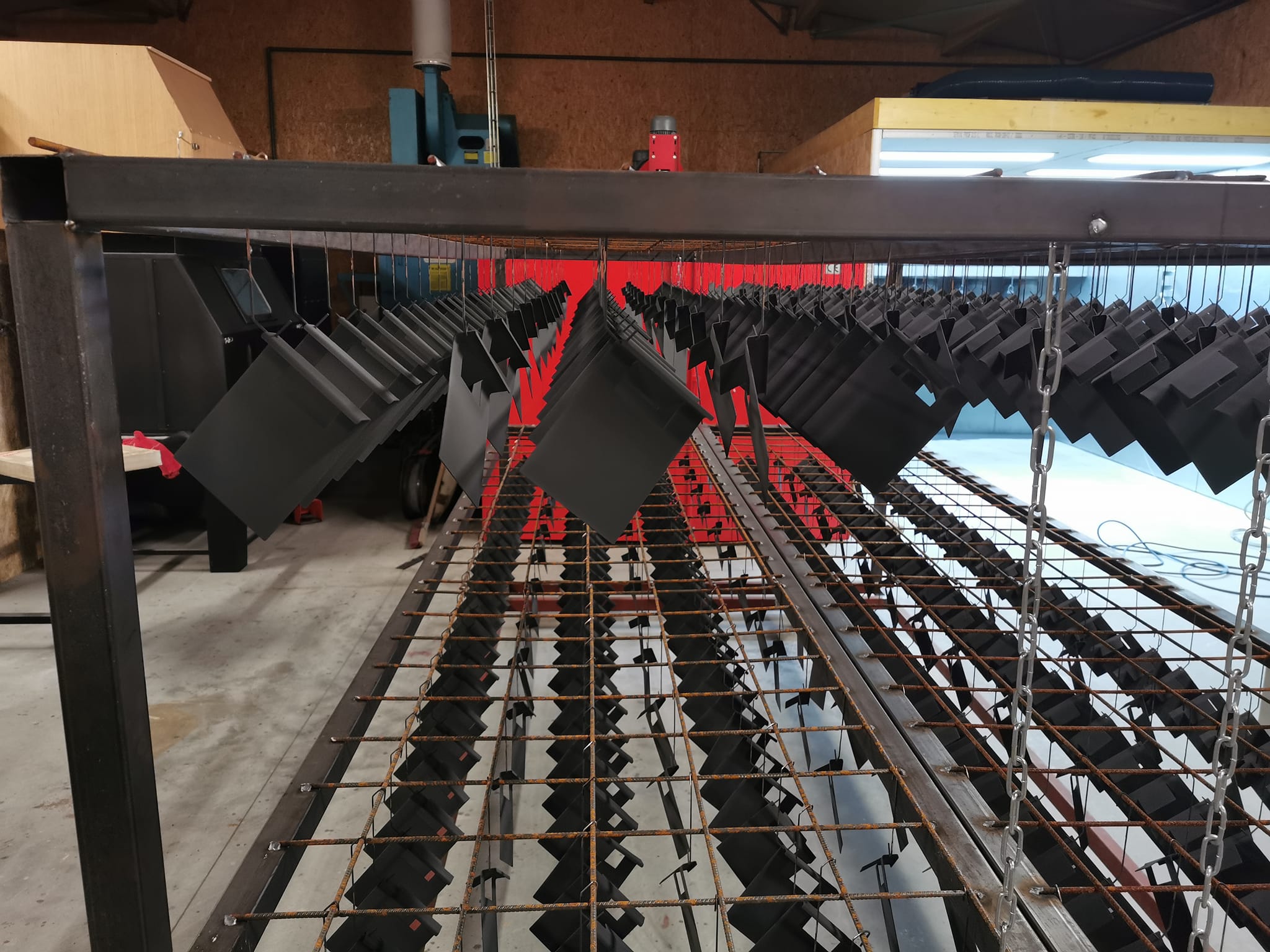
Les fours industriels jouent un rôle crucial dans les procédés de peinture, en particulier dans le thermolaquage et le séchage des revêtements. Ces équipements sont conçus pour atteindre des températures précises et uniformes, nécessaires pour la polymérisation de la peinture en poudre et pour garantir des finitions de haute qualité. Il existe plusieurs types de fours industriels, chacun adapté à des applications spécifiques, en fonction des matériaux à traiter, des volumes de production, et des exigences du processus.
Les fours de thermolaquage sont parmi les plus couramment utilisés dans l’industrie de la peinture. Ces fours sont spécialement conçus pour chauffer les pièces revêtues de peinture en poudre à des températures généralement comprises entre 160 et 200 degrés Celsius. Cette chaleur provoque la fusion de la poudre, suivie de sa polymérisation, formant ainsi un revêtement dur et homogène. Les fours haute température industriels sont particulièrement adaptés pour le thermolaquage, car ils peuvent maintenir des températures stables et uniformes sur de longues périodes, ce qui est essentiel pour obtenir une finition sans défaut.
Un autre type de four utilisé dans l’industrie est le four pyrolyse industriel. Ces fours sont principalement utilisés pour le nettoyage des équipements de peinture et des composants contaminés par des résidus de peinture. La pyrolyse est un processus thermique qui décompose les matières organiques à haute température, sans oxygène, transformant ainsi les résidus en cendres et en gaz. Les fours pyrolyse industriels sont essentiels pour maintenir les outils et les équipements en bon état de fonctionnement, en éliminant les accumulations de peinture et d’autres contaminants qui pourraient altérer la qualité des opérations de revêtement.
Les fours de revenu tunnel sont une autre catégorie de fours industriels, particulièrement adaptés aux opérations de grande échelle. Ces fours fonctionnent en continu, permettant aux pièces de passer à travers une zone de chauffage de manière contrôlée. Ce type de four est souvent utilisé dans des lignes de production automatisées, où il est nécessaire de traiter de grandes quantités de pièces rapidement et de manière homogène. Les fours de revenu tunnel sont couramment employés pour le séchage et la polymérisation des revêtements, offrant une solution efficace pour les processus de production à haut débit.
Dans certaines industries, les fours à gaz industriels sont préférés pour leur efficacité énergétique et leur flexibilité d’utilisation. Par exemple, au Québec, les fours à gaz industriels sont largement utilisés dans les secteurs nécessitant des systèmes de chauffage puissants et économiques. Ces fours utilisent des brûleurs à gaz pour chauffer les pièces à la température désirée, offrant une montée en température rapide et une excellente répartition de la chaleur. Les fours à gaz sont particulièrement appréciés dans les ateliers où la variation des types de pièces à traiter nécessite des ajustements fréquents des conditions de température.
Les petits fours industriels sont une autre option pour les entreprises ayant des besoins de production plus modestes ou pour celles qui traitent des pièces de petite taille. Ces fours offrent la même précision et fiabilité que leurs homologues plus grands, mais sont adaptés aux volumes de production plus faibles. Les petits fours sont souvent utilisés dans des environnements de prototypage ou pour des séries limitées, où la flexibilité et la précision sont essentielles.
Le thermolaquage haute température est une application spécifique qui requiert des fours industriels capables de supporter des conditions de chaleur extrême. Ces fours sont conçus pour atteindre des températures bien au-delà de celles requises pour la polymérisation standard, souvent nécessaires pour traiter des matériaux résistants à la chaleur ou pour des applications où des revêtements très durs et résistants sont nécessaires. Le thermolaquage haute température est couramment utilisé dans les industries aéronautiques, militaires, et pour des équipements soumis à des conditions environnementales sévères.
Le séchage industriel est une étape cruciale dans de nombreux procédés de peinture, et les fours de séchage sont spécialement conçus pour cette tâche. Ces fours fonctionnent en maintenant un flux d’air chaud et contrôlé autour des pièces à sécher, permettant l’évaporation rapide des solvants ou de l’humidité avant que la peinture ne soit cuite ou durcie. Le séchage industriel est particulièrement important dans les procédés de peinture liquide, où une évaporation uniforme est nécessaire pour éviter les défauts de surface, tels que des cloques ou des fissures dans le revêtement.
Les fours de thermolaquage modernes sont souvent équipés de technologies avancées pour améliorer leur efficacité et leur contrôle. Par exemple, des systèmes de contrôle numérique permettent de programmer et de surveiller les cycles de cuisson avec une grande précision, garantissant que chaque pièce est traitée dans des conditions optimales. Ces systèmes peuvent également être intégrés à des réseaux de production automatisés, permettant une coordination parfaite entre les différentes étapes du processus de peinture.
L’entretien des fours industriels est une autre considération essentielle pour garantir leur performance continue. Les fours doivent être régulièrement inspectés et calibrés pour s’assurer que la température est uniformément répartie et que les systèmes de chauffage fonctionnent efficacement. Les composants critiques, tels que les brûleurs, les ventilateurs, et les systèmes de contrôle, doivent être vérifiés et entretenus pour prévenir les pannes et prolonger la durée de vie de l’équipement. Dans certains cas, il peut être nécessaire de remplacer des pièces usées ou de moderniser les systèmes de contrôle pour maintenir les performances des fours à un niveau optimal.
Enfin, les fours industriels jouent également un rôle dans le respect des normes environnementales. En effet, les procédés de cuisson et de séchage doivent minimiser les émissions de gaz à effet de serre et de polluants. De nombreux fours modernes sont conçus avec des technologies de combustion propres et des systèmes de récupération de chaleur, qui réduisent la consommation d’énergie et les émissions. Ces améliorations non seulement respectent les régulations environnementales, mais contribuent également à réduire les coûts d’exploitation à long terme.
En conclusion, les fours industriels sont des composants indispensables des procédés de peinture industrielle, offrant des solutions adaptées à une large gamme d’applications et de besoins. Leur conception, leur maintenance, et leur utilisation correcte sont essentiels pour garantir des résultats de haute qualité, une production efficace, et un respect des normes environnementales. Les entreprises qui investissent dans des fours industriels de pointe et qui maintiennent leurs équipements en bon état sont bien positionnées pour réussir dans un marché compétitif et en constante évolution.
Automatisation et innovation dans la peinture industrielle
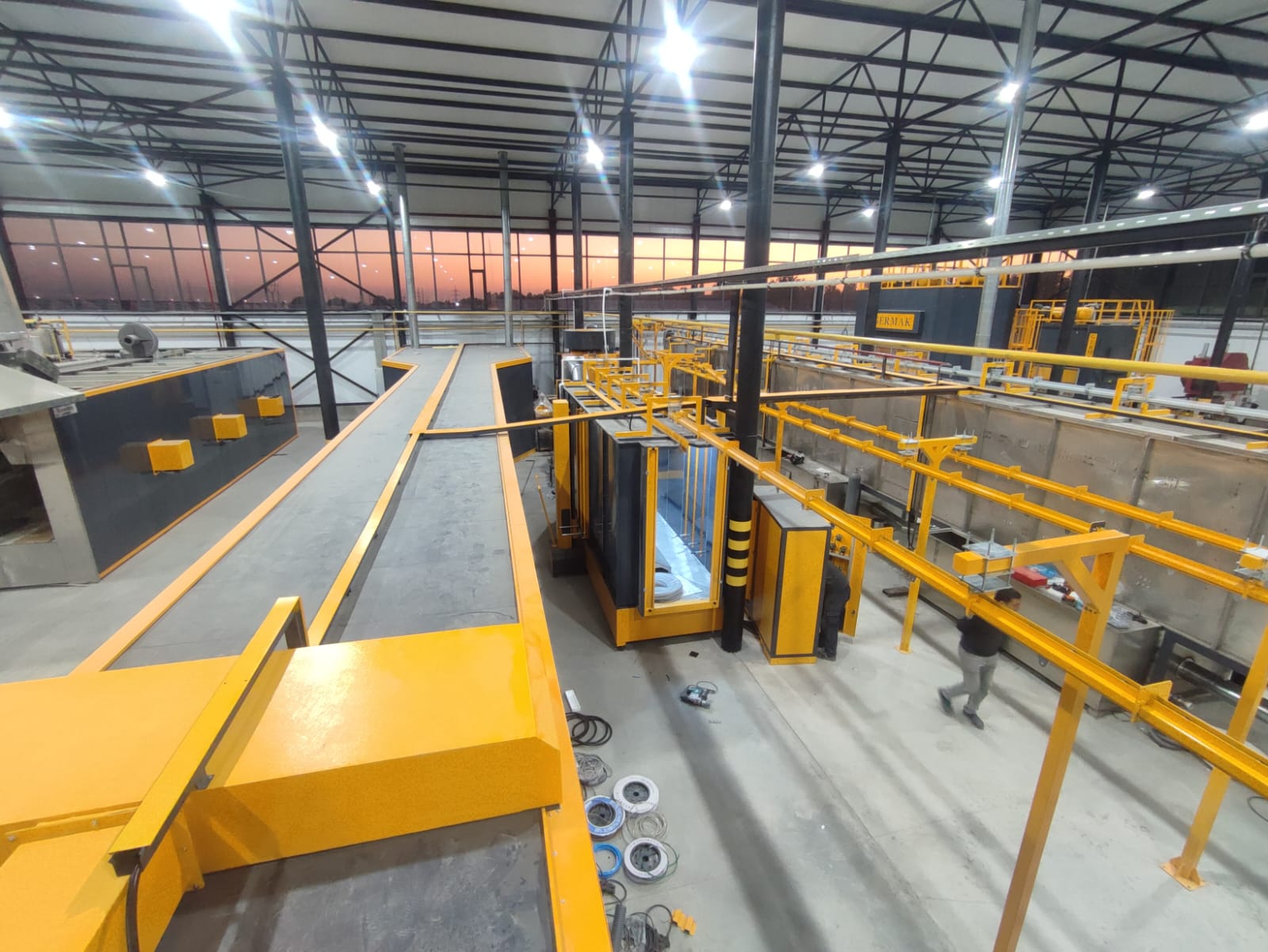
L’automatisation a profondément transformé le paysage de la peinture industrielle, permettant des gains significatifs en termes de productivité, de qualité, et de sécurité. Les avancées technologiques ont introduit des systèmes automatisés qui remplacent de plus en plus les méthodes manuelles, rendant les procédés de peinture plus efficaces et plus précis. Dans un environnement où les exigences en matière de qualité et de délais de production ne cessent d’augmenter, l’intégration de l’automatisation et des innovations technologiques est devenue indispensable pour rester compétitif.
Les robots de peinture industriels sont au cœur de cette révolution technologique. Ces robots sont conçus pour exécuter des tâches de peinture répétitives avec une précision et une rapidité inégalées par l’humain. Les robots peuvent être programmés pour suivre des trajectoires complexes, appliquer des couches de peinture uniformes, et ajuster les paramètres en temps réel en fonction des spécificités de chaque pièce à traiter. Cela permet non seulement de réduire les erreurs et les variations dans la qualité du revêtement, mais aussi d’optimiser l’utilisation des matériaux, réduisant ainsi le gaspillage de peinture et les coûts associés.
L’un des principaux avantages des robots de peinture industriels est leur capacité à travailler dans des environnements hostiles ou difficiles d’accès, où les conditions de travail pour les humains seraient dangereuses ou impraticables. Par exemple, les robots peuvent être utilisés dans des cabines de poudrage ou des fours de thermolaquage pour appliquer la peinture ou contrôler la polymérisation dans des conditions de chaleur intense ou d’exposition à des substances toxiques. Cela améliore non seulement la sécurité des opérateurs, mais augmente également la répétabilité et la précision du processus de peinture.
Les systèmes de peinture automatisés intègrent souvent des technologies de contrôle avancées qui permettent de surveiller et d’ajuster en temps réel les paramètres critiques du processus. Ces systèmes peuvent inclure des capteurs qui mesurent la température, l’humidité, et la viscosité de la peinture, ainsi que des caméras et des lasers pour contrôler la qualité de l’application de la peinture. Les données collectées par ces capteurs sont analysées en temps réel par des logiciels de gestion de la production, qui ajustent automatiquement les paramètres pour optimiser les résultats et prévenir les défauts de revêtement.
L’intégration de l’intelligence artificielle (IA) dans les procédés de peinture industrielle est une autre innovation majeure. L’IA permet d’analyser de grandes quantités de données collectées par les systèmes de contrôle, identifiant des schémas et des anomalies qui pourraient passer inaperçus pour un opérateur humain. Par exemple, l’IA peut détecter des variations subtiles dans l’épaisseur du revêtement ou des changements de température dans un four de thermolaquage, et ajuster automatiquement les paramètres pour corriger ces écarts avant qu’ils n’affectent la qualité du produit final. Cela permet de réduire les rebuts, d’améliorer la qualité des produits finis, et d’optimiser l’efficacité de la production.
Les systèmes de peinture automatisés sont également conçus pour améliorer la flexibilité de la production. Dans un environnement où les séries de production sont de plus en plus courtes et personnalisées, les systèmes automatisés peuvent être reprogrammés rapidement pour s’adapter à de nouveaux modèles ou à des spécifications de clients différentes. Cela permet aux entreprises de répondre plus rapidement aux demandes du marché sans sacrifier la qualité ou l’efficacité de la production.
L’innovation dans les technologies de revêtement va au-delà de l’automatisation des processus. De nouveaux types de revêtements en poudre et de peintures électrostatiques sont constamment développés pour offrir des performances améliorées en termes de durabilité, de résistance chimique, et de propriétés esthétiques. Par exemple, les revêtements en poudre de dernière génération peuvent offrir une résistance accrue aux UV, aux impacts, et aux produits chimiques, tout en étant disponibles dans une gamme encore plus large de couleurs et de textures. Ces revêtements innovants permettent aux fabricants de répondre aux exigences croissantes des clients pour des produits non seulement fonctionnels, mais aussi esthétiquement attrayants.
Les innovations dans les systèmes de séchage industriel sont également dignes de mention. Les nouveaux fours industriels intègrent des technologies de récupération de chaleur et de contrôle de l’humidité qui permettent de réduire les temps de séchage et de minimiser la consommation d’énergie. Ces fours sont souvent équipés de systèmes de contrôle automatisés qui ajustent en temps réel les conditions de séchage en fonction de la nature du revêtement appliqué et des spécificités de la pièce à traiter. Cette capacité à ajuster les paramètres de manière dynamique permet d’obtenir des résultats plus cohérents et de haute qualité, tout en réduisant les coûts énergétiques.
L’avenir de la peinture industrielle est également marqué par l’émergence de technologies vertes et durables. Les préoccupations environnementales poussent l’industrie à adopter des procédés et des matériaux qui réduisent l’impact écologique des opérations de peinture. Les revêtements en poudre, par exemple, sont déjà reconnus pour leur faible impact environnemental par rapport aux peintures liquides traditionnelles, car ils ne contiennent pas de solvants organiques volatils (COV) et permettent de récupérer et de réutiliser l’excédent de poudre. Les innovations futures pourraient inclure des revêtements encore plus respectueux de l’environnement, fabriqués à partir de matériaux renouvelables ou offrant une dégradabilité plus rapide.
De plus, l’automatisation et l’IA jouent un rôle clé dans l’amélioration de l’efficacité énergétique des procédés de peinture. En optimisant l’utilisation des matériaux et en réduisant les déchets, ces technologies contribuent à réduire l’empreinte carbone des opérations de production. Les entreprises qui adoptent ces innovations technologiques peuvent non seulement améliorer leur efficacité opérationnelle, mais aussi répondre aux exigences réglementaires de plus en plus strictes en matière de durabilité environnementale.
En conclusion, l’automatisation et l’innovation sont les moteurs de la transformation de la peinture industrielle. L’intégration de robots de peinture industriels, de systèmes de contrôle automatisés, et de l’intelligence artificielle permet aux entreprises de produire des revêtements de haute qualité de manière plus efficace, flexible, et durable. Ces avancées technologiques ne se contentent pas d’améliorer la productivité ; elles redéfinissent les normes de l’industrie, en offrant des solutions qui répondent aux besoins croissants en matière de qualité, de personnalisation, et de respect de l’environnement.
Les aspects économiques et écologiques de la peinture industrielle
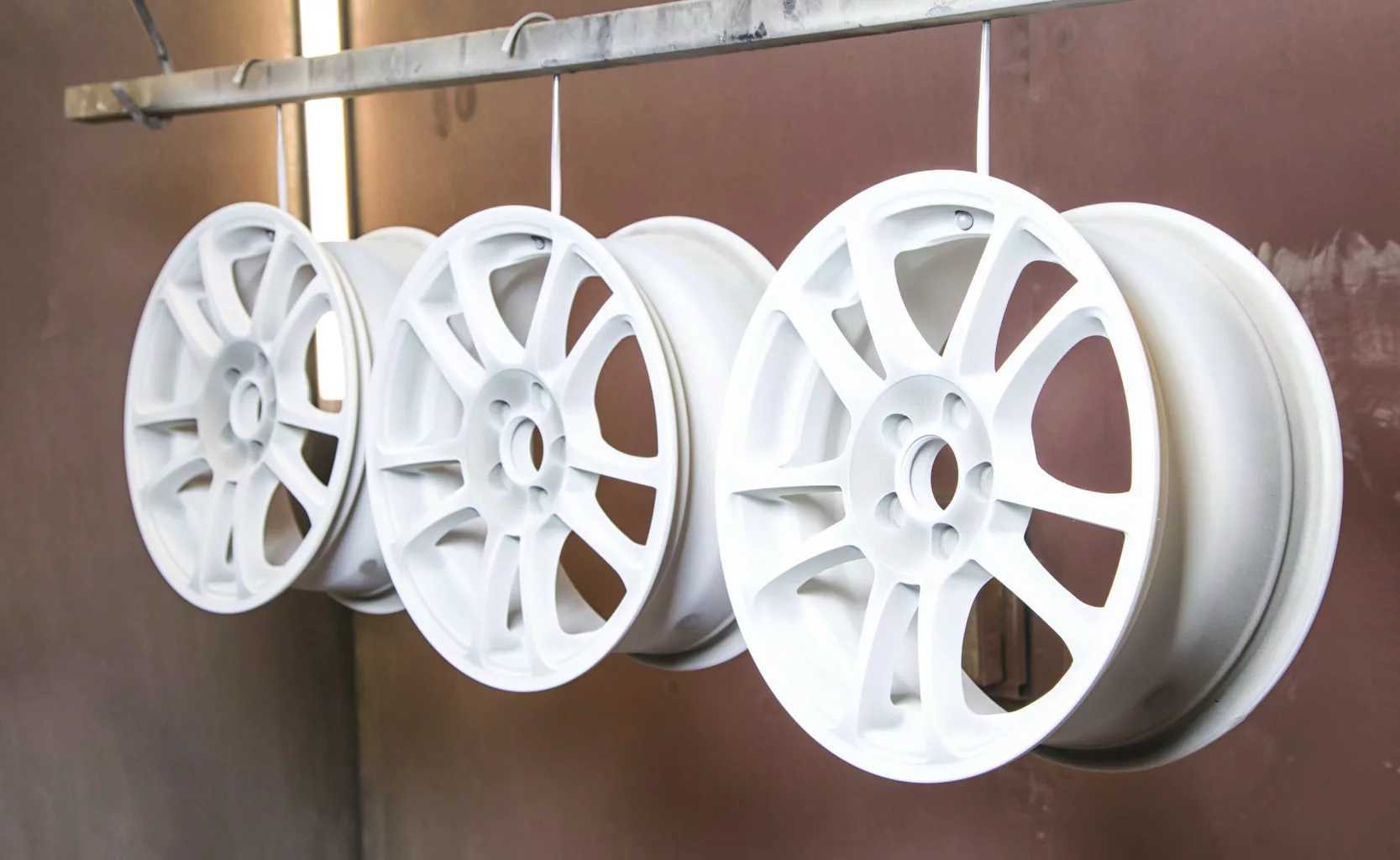
Dans l’industrie moderne, les aspects économiques et écologiques des procédés de peinture jouent un rôle de plus en plus important. Les entreprises cherchent non seulement à optimiser leurs coûts de production, mais aussi à réduire leur impact environnemental pour répondre aux régulations croissantes et aux attentes des consommateurs. La peinture industrielle, avec ses divers procédés et technologies, offre une multitude de solutions pour équilibrer ces deux aspects essentiels.
D’un point de vue économique, la peinture industrielle représente un investissement significatif en termes d’équipements, de main-d’œuvre et de matières premières. Le coût initial des installations, tels que les fours de thermolaquage, les pistolets de peinture électrostatiques, et les cabines de poudrage, peut être élevé, mais ces équipements sont conçus pour offrir une durabilité et une efficacité qui permettent de rentabiliser cet investissement sur le long terme. Par exemple, l’acquisition d’un four de thermolaquage performant permet non seulement de garantir une qualité constante du revêtement, mais aussi de réduire les coûts opérationnels grâce à une consommation d’énergie optimisée.
Les systèmes de peinture modernes sont souvent conçus pour maximiser l’utilisation des matériaux tout en minimisant les pertes. L’application de la peinture électrostatique en poudre est un excellent exemple d’efficacité économique, car ce procédé réduit considérablement le gaspillage de peinture. La poudre excédentaire, qui n’adhère pas initialement à la surface, peut être récupérée et réutilisée, réduisant ainsi le coût des matières premières et minimisant les déchets. De plus, les robots de peinture industriels et les systèmes automatisés permettent de réduire la variabilité du processus, assurant une utilisation plus efficace de la peinture et des cycles de production plus rapides.
L’un des coûts souvent sous-estimés dans la peinture industrielle est celui associé à la maintenance des équipements. Une maintenance régulière est cruciale pour éviter les pannes coûteuses et prolonger la durée de vie des installations. Par exemple, le remplacement régulier des filtres de cabine de peinture et l’entretien des pistolets de peinture thermolaquage sont essentiels pour maintenir une production fluide et éviter les arrêts imprévus. Bien que ces activités de maintenance représentent un coût récurrent, elles permettent de prévenir des dépenses bien plus importantes liées aux réparations majeures ou au remplacement prématuré des équipements.
Sur le plan écologique, la peinture industrielle a longtemps été associée à des impacts environnementaux négatifs, notamment en raison de l’utilisation de solvants organiques volatils (COV) dans les peintures liquides. Ces COV contribuent à la pollution de l’air et posent des risques pour la santé des travailleurs et des communautés environnantes. Cependant, les progrès technologiques ont conduit à l’adoption de procédés de revêtement plus écologiques, comme le poudrage peinture. Ce procédé n’émet pratiquement pas de COV, ce qui en fait une alternative beaucoup plus respectueuse de l’environnement.
Les fours de thermolaquage modernes sont également conçus avec des technologies visant à réduire la consommation d’énergie et à minimiser les émissions. Par exemple, les fours à gaz industriels utilisés au Québec intègrent souvent des systèmes de récupération de chaleur qui permettent de réutiliser l’énergie thermique, réduisant ainsi la consommation de combustible et les coûts associés. De plus, ces fours sont souvent équipés de brûleurs à haut rendement qui optimisent la combustion, réduisant les émissions de gaz à effet de serre.
Le thermolaquage lui-même est un processus relativement propre, car il ne nécessite pas de solvants et génère peu de déchets. En effet, la poudre non utilisée peut être récupérée et recyclée, ce qui réduit la quantité de déchets envoyés en décharge. De plus, le thermolaquage haute température permet de créer des revêtements durables qui prolongent la durée de vie des produits, réduisant ainsi la fréquence des repeints ou des remplacements, et contribuant à une consommation plus durable des ressources.
L’impact écologique de la peinture industrielle est également lié à la gestion des déchets et des émissions. Les entreprises doivent se conformer à des réglementations strictes en matière de gestion des déchets dangereux, qui incluent les restes de peinture, les solvants usés, et les filtres contaminés. Le respect de ces réglementations non seulement évite des amendes et des sanctions, mais contribue également à l’image de l’entreprise en tant qu’acteur responsable sur le plan environnemental. Certaines entreprises vont encore plus loin en adoptant des pratiques de dépollution et de recyclage qui minimisent leur empreinte écologique.
Les aspects économiques et écologiques de la peinture industrielle ne sont pas dissociés, mais plutôt interdépendants. Par exemple, une meilleure efficacité énergétique non seulement réduit les coûts d’exploitation, mais contribue également à réduire les émissions de gaz à effet de serre. De même, l’utilisation de technologies de revêtement plus respectueuses de l’environnement, comme la peinture en poudre, peut réduire les coûts de conformité réglementaire et améliorer l’acceptation des produits par les consommateurs soucieux de l’environnement.
L’évolution vers des pratiques plus durables dans la peinture industrielle est également motivée par les exigences du marché et les préférences des consommateurs. De plus en plus, les clients recherchent des produits qui non seulement répondent à des standards de qualité élevés, mais qui sont également fabriqués de manière durable. Les entreprises qui investissent dans des technologies de peinture écologique et qui communiquent clairement leurs efforts en matière de durabilité sont souvent mieux perçues et peuvent bénéficier d’un avantage concurrentiel sur le marché.
En conclusion, les aspects économiques et écologiques de la peinture industrielle sont des facteurs déterminants dans la stratégie globale des entreprises. L’équilibre entre la maîtrise des coûts et la réduction de l’impact environnemental est devenu un enjeu crucial dans un contexte où les régulations sont de plus en plus strictes et les attentes des consommateurs de plus en plus élevées. Les entreprises qui adoptent des solutions de peinture efficaces, durables et respectueuses de l’environnement sont mieux positionnées pour prospérer à long terme, tout en contribuant positivement à la société et à l’environnement.
Le Revêtement par Poudre : Principes, Types et Avantages
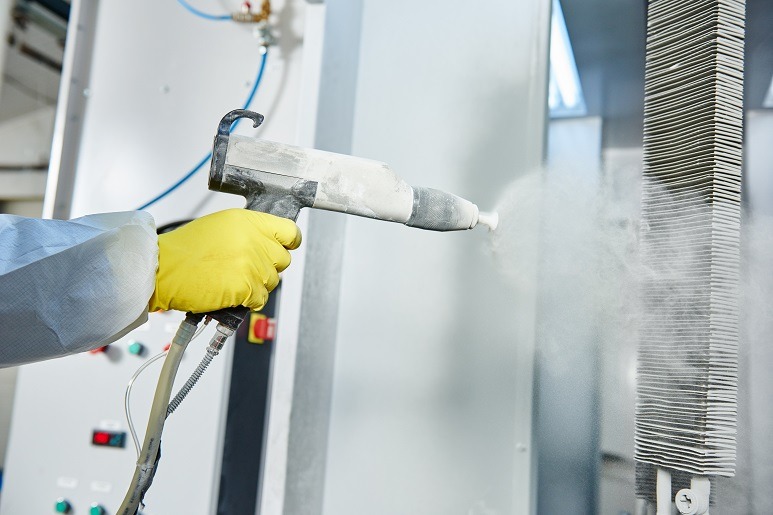
Le revêtement par poudre est une technologie de finition de surface qui s’est largement imposée dans l’industrie, en particulier pour le traitement des métaux. Cette technique, qui repose sur l’application d’une poudre sèche à la surface d’un objet, est suivie d’une cuisson dans un four à haute température pour faire fondre la poudre et former une couche protectrice et esthétique.
1.1 Principe de Fonctionnement
Le processus de revêtement par poudre commence par la préparation de la surface du métal, qui peut inclure le nettoyage, le sablage ou le traitement chimique pour garantir une adhérence optimale de la poudre. Une fois la surface prête, la poudre, composée de résines thermodurcissables ou thermoplastiques, est appliquée à l’aide d’un pistolet électrostatique.
Le pistolet de peinture thermolaquage charge électriquement les particules de poudre, qui sont attirées par la surface métallique opposée. Cette méthode permet une couverture uniforme et réduit le gaspillage de matière.
1.2 Types de Revêtements par Poudre
Il existe plusieurs types de revêtements par poudre, chacun conçu pour répondre à des besoins spécifiques :
- Revêtements en poudre époxy : Offrant une excellente adhérence et résistance chimique, ces revêtements sont souvent utilisés pour des applications où la protection contre la corrosion est essentielle.
- Revêtements en poudre polyester : Conçus pour une exposition extérieure, ces revêtements résistent bien aux UV et aux intempéries, ce qui les rend idéaux pour les équipements extérieurs et les façades.
- Revêtements hybrides époxy-polyester : Ces revêtements combinent les meilleures propriétés des époxys et des polyesters, offrant un bon équilibre entre résistance chimique et stabilité aux UV.
1.3 Avantages du Revêtement par Poudre
Les avantages du revêtement par poudre par rapport aux peintures liquides traditionnelles sont nombreux :
- Respect de l’environnement : Sans solvants ni COV, le revêtement par poudre est plus respectueux de l’environnement. Les entreprises adoptent de plus en plus cette technologie pour répondre aux réglementations environnementales strictes.
- Efficacité des matériaux : La poudre excédentaire peut être récupérée et réutilisée, ce qui réduit les coûts et minimise les déchets.
- Résistance accrue : Les revêtements par poudre offrent une résistance exceptionnelle aux chocs, à l’abrasion et à la corrosion, prolongeant la durée de vie des produits.
La Peinture Poudre Electrostatique : Une Révolution Technologique
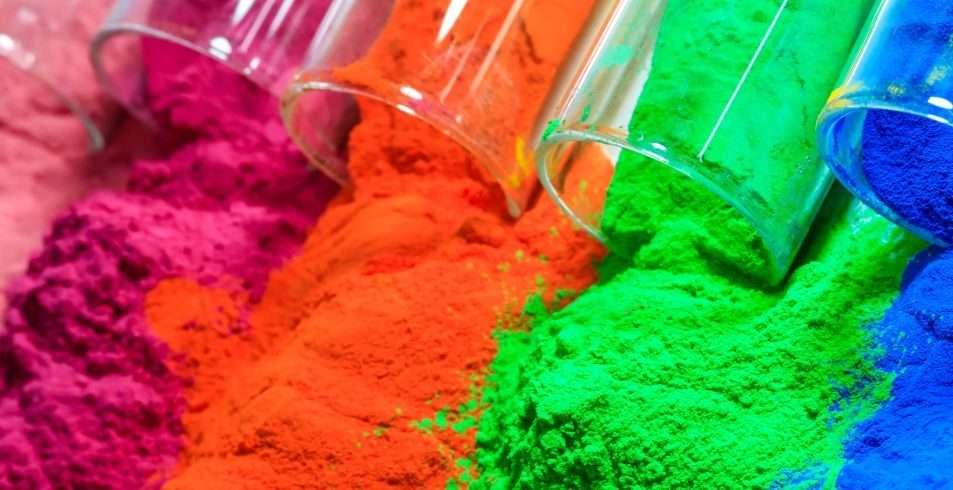
La peinture poudre électrostatique a révolutionné l’industrie du revêtement métallique. En utilisant des forces électrostatiques pour attirer la poudre sur la surface du matériau, cette méthode garantit une application plus précise et efficace.
2.1 Application Électrostatique
L’application électrostatique est rendue possible grâce à un pistolet qui charge électriquement la poudre. Les particules, une fois chargées, sont attirées par les surfaces conductrices, ce qui permet une couverture uniforme même sur les formes complexes. Cela est particulièrement avantageux pour les pièces avec des recoins difficiles à atteindre par d’autres méthodes.
2.2 Polymérisation et Durcissement
Après l’application de la poudre, les pièces sont introduites dans un four de thermolaquage, où elles sont chauffées à des températures allant de 160 à 200 degrés Celsius. Ce processus de polymérisation fait fondre la poudre, qui se transforme en une couche solide et uniforme. Le durcissement de cette couche renforce ses propriétés mécaniques et sa résistance chimique.
2.3 Applications de la Peinture Poudre Electrostatique
Les applications de la peinture poudre électrostatique sont vastes :
- Industrie automobile : Utilisée pour les châssis, les jantes et autres composants, la peinture en poudre offre une protection durable contre la rouille et les dommages mécaniques.
- Équipements électroménagers : Les appareils tels que les réfrigérateurs, les lave-linge et les fours sont souvent revêtus de poudre pour une finition durable et esthétique.
- Mobilier métallique : Les meubles en métal, qu’ils soient destinés à un usage intérieur ou extérieur, bénéficient de la durabilité et de la variété de finitions offertes par la peinture poudre.
3. Les Systèmes de Peinture et Machines Associées : Équipements Essentiels
Les systèmes de peinture modernes sont conçus pour offrir une flexibilité maximale, en permettant des ajustements rapides en fonction des besoins spécifiques de production. Ces systèmes peuvent inclure des cabines de peinture, des pistolets, des fours, et d’autres équipements auxiliaires.
3.1 Cabines de Peinture Professionnelles
Les cabines de peinture professionnelles sont conçues pour créer un environnement contrôlé, où les conditions de température, d’humidité et de ventilation peuvent être ajustées pour garantir une application parfaite du revêtement.
- Types de cabines : Les cabines peuvent être à flux d’air horizontal ou vertical, en fonction de la taille et de la configuration des pièces à peindre.
- Filtres de cabine : Les filtres cabine de peinture sont essentiels pour capturer les particules de poudre excédentaires et pour maintenir la qualité de l’air à l’intérieur de la cabine.
3.2 Machines à Peinture et Équipements
Les machines à peinture jouent un rôle crucial dans l’automatisation du processus de peinture, en améliorant l’efficacité et en réduisant les erreurs humaines.
- Pistolets de peinture : Les pistolets de peinture epoxy poudre sont des outils indispensables pour une application précise et uniforme de la peinture. Ils sont disponibles en versions manuelles et automatiques.
- Robots de peinture industriels : Ces robots permettent d’automatiser complètement le processus, garantissant une application cohérente et répétable, ce qui est particulièrement utile pour les productions à grande échelle.
3.3 Fours de Thermolaquage
Les fours de thermolaquage sont conçus pour polymériser les revêtements en poudre appliqués sur les surfaces métalliques. Ils existent en différentes tailles et configurations, notamment :
- Fours à gaz industriels : Utilisés pour leur efficacité énergétique, ces fours sont souvent préférés pour les grandes installations.
- Fours électriques industriels : Ils offrent une précision de température supérieure, ce qui est crucial pour certaines applications spécialisées.
- Fours industriels haute température : Capables de fonctionner à des températures extrêmes, ces fours sont utilisés pour des applications nécessitant une résistance thermique élevée.
Fabricants de Cabines et Fours : Innovateurs et Leaders du Marché
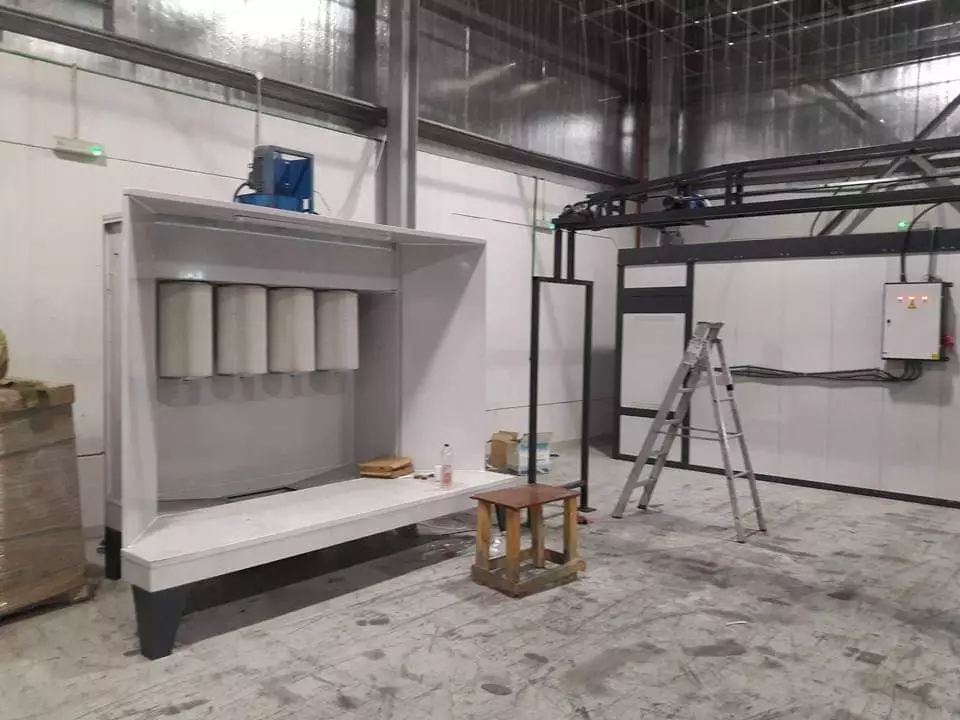
Les fabricants de cabines de peinture et de fours industriels sont au cœur de l’innovation dans ce secteur. Ils développent des équipements qui répondent aux besoins évolutifs de l’industrie, en se concentrant sur l’efficacité énergétique, la durabilité et la compatibilité environnementale.
Cabines de Poudrage
Les cabines de poudrage sont spécifiquement conçues pour l’application de revêtements en poudre. Elles intègrent des systèmes de récupération de poudre pour minimiser les déchets et maximiser l’efficacité.
- Caractéristiques techniques : Ces cabines sont équipées de systèmes de filtration avancés pour capturer les particules de poudre non adhérentes, qui peuvent ensuite être réutilisées.
- Options de personnalisation : Les fabricants offrent souvent des options de personnalisation pour répondre aux besoins spécifiques de leurs clients, qu’il s’agisse de dimensions spécifiques, de configurations de flux d’air, ou d’intégration avec d’autres systèmes automatisés.
4.2 Fours de Cuisson
Les fours de cuisson utilisés dans le processus de thermolaquage doivent offrir une distribution uniforme de la chaleur pour garantir une polymérisation homogène du revêtement.
- Fours à gaz : Populaires pour leur coût opérationnel réduit, les fours à gaz industriels sont souvent utilisés dans les grandes installations où l’efficacité énergétique est une priorité.
- Fours électriques : Bien qu’ils puissent être plus coûteux à l’achat, les fours électriques industriels offrent une meilleure régulation de la température, ce qui est essentiel pour certaines applications précises.
- Fours personnalisés : Les fabricants peuvent concevoir des fours industriels sur mesure pour répondre à des exigences spécifiques en matière de taille, de température, ou de configuration.
Maintenance et Dépannage : Garantir une Performance et une Durabilité Optimales
Pour assurer une longue durée de vie et une performance optimale des équipements, il est crucial de mettre en place un programme de maintenance régulier et d’être prêt à intervenir en cas de dysfonctionnement.
5.1 Maintenance des Filtres de Cabine de Peinture
Les filtres cabine de peinture jouent un rôle clé dans la qualité de l’air à l’intérieur des cabines. Un entretien régulier est essentiel pour éviter les accumulations qui peuvent obstruer les filtres et compromettre la qualité du revêtement.
- Fréquence de remplacement : Les filtres doivent être inspectés régulièrement et remplacés selon les recommandations du fabricant, qui varient en fonction du volume de production.
- Techniques de nettoyage : Certains filtres peuvent être nettoyés et réutilisés, tandis que d’autres nécessitent un remplacement complet. Le choix du filtre dépendra des spécificités de l’application et de la fréquence d’utilisation.
5.2 Dépannage des Brûleurs de Fours Industriels
Les brûleurs de fours industriels sont des composants essentiels pour maintenir la température à l’intérieur du four. Les pannes de brûleurs peuvent entraîner des interruptions de production coûteuses.
- Signes de dysfonctionnement : Les signes de dysfonctionnement d’un brûleur incluent des températures irrégulières, des bruits inhabituels, ou une augmentation des émissions de gaz. Une inspection régulière peut aider à détecter ces problèmes avant qu’ils ne provoquent une panne majeure.
- Réparation et remplacement : En fonction de la gravité du problème, le brûleur peut nécessiter une réparation ou un remplacement complet. Il est crucial d’avoir des pièces de rechange à portée de main pour minimiser les temps d’arrêt.
5.3 Réparations et Retouches
Même avec les meilleurs équipements et les meilleures pratiques, des retouches peuvent parfois être nécessaires pour corriger des imperfections mineures sur les pièces finies.
- Techniques de retouche : Les retouches de peinture thermolaquée peuvent être effectuées à l’aide de petites quantités de poudre appliquées manuellement, suivies d’une nouvelle cuisson pour assurer l’intégrité du revêtement.
- Contrôle de qualité : Un processus de contrôle de qualité rigoureux doit être en place pour identifier les pièces nécessitant des retouches avant qu’elles ne quittent l’usine.
Types de Procédés de Revêtement Métallique : Sélectionner la Méthode Appropriée
Le choix du procédé de revêtement métallique dépend largement de l’application finale et des exigences en matière de durabilité, d’apparence, et de coût.
6.1 Thermolaquage
Le thermolaquage est particulièrement apprécié pour sa capacité à produire des finitions durables et esthétiques. Ce procédé est souvent utilisé dans l’industrie automobile, les équipements industriels, et les meubles métalliques.
- Avantages : Outre la durabilité et la résistance à la corrosion, le thermolaquage offre une large gamme de finitions, y compris des options brillantes, mates, texturées, et métalliques.
- Limitations : Bien que très efficace pour de nombreuses applications, le thermolaquage peut ne pas être idéal pour certaines surfaces non métalliques ou pour des pièces nécessitant une flexibilité extrême après application.
6.2 Peinture Epoxy Poudre
La peinture epoxy poudre est une autre méthode couramment utilisée pour les revêtements industriels, offrant une excellente adhérence et résistance chimique.
- Applications : Utilisée pour les équipements électriques, les structures en acier, et les composants de machines, la peinture epoxy poudre est idéale pour les environnements où la protection contre les produits chimiques agressifs est essentielle.
- Caractéristiques techniques : La peinture epoxy offre également une bonne isolation électrique, ce qui la rend utile dans les applications où les propriétés isolantes sont requises.
6.3 Étuve de Laquage
L’étuvage de laquage est une étape essentielle dans le processus de finition, assurant que la peinture ou le revêtement adhère parfaitement à la surface.
- Procédé : Après l’application du revêtement, les pièces sont placées dans une étuve où elles sont chauffées à des températures précises pour durcir le revêtement. Ce procédé est crucial pour assurer la longévité et la durabilité du revêtement.
- Équipements associés : Les étuves industrielles varient en taille et en capacité, avec des modèles disponibles pour des productions en masse ou pour des pièces de grande taille nécessitant un traitement prolongé.
Équipements Spécialisés et Accessoires : Optimiser les Performances
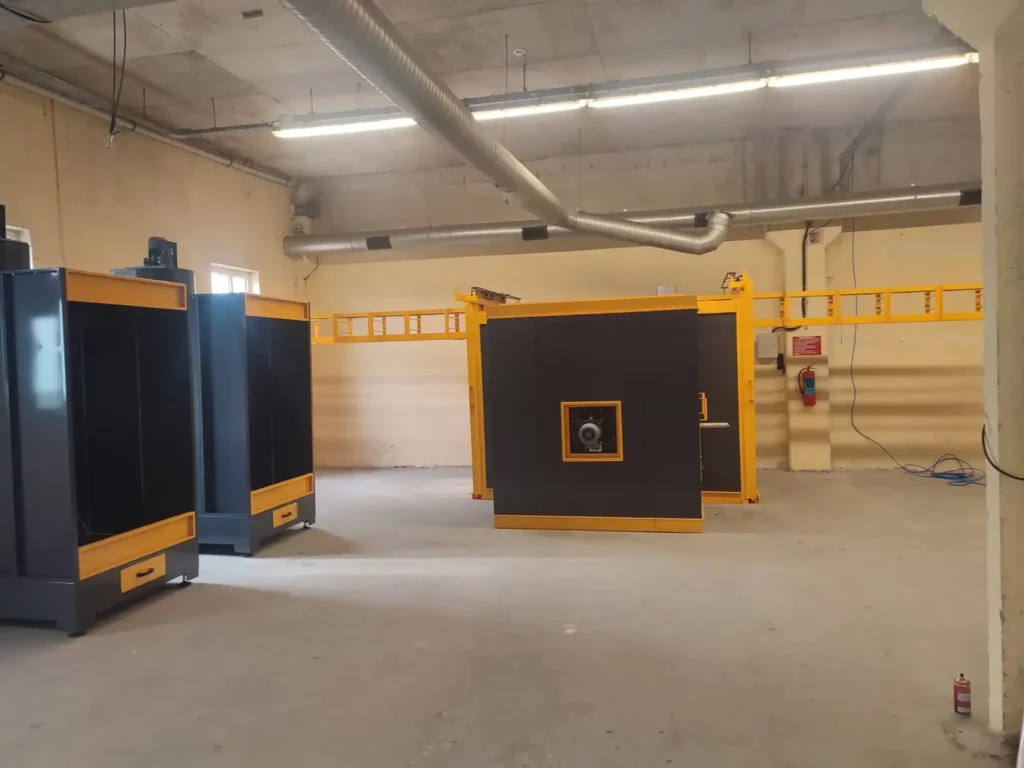
Le succès du processus de revêtement dépend non seulement des équipements principaux, mais aussi des accessoires et équipements spécialisés qui assurent une performance optimale.
7.1 Pistolets de Peinture Epoxy et Thermolaquage
Les pistolets de peinture sont essentiels pour une application précise de la poudre.
- Caractéristiques techniques : Les pistolets modernes offrent une large gamme de réglages permettant d’ajuster la taille de la pulvérisation, la pression, et la charge électrostatique, en fonction des exigences spécifiques de l’application.
- Maintenance et entretien : Pour garantir une performance optimale, les pistolets doivent être nettoyés régulièrement pour éviter les obstructions et les défaillances mécaniques.
7.2 Étuves Industrielles Grand Volume
Pour les entreprises qui traitent de grandes quantités de pièces, les étuves industrielles grand volume sont indispensables.
- Avantages : Ces étuves permettent de traiter simultanément un grand nombre de pièces, réduisant ainsi les coûts de production et augmentant l’efficacité.
- Personnalisation : Certaines étuves peuvent être personnalisées pour s’adapter à des configurations spécifiques, y compris des options pour un contrôle précis de la température et de l’humidité.
7.3 Cabines de Poudrage d’Occasion
L’achat de cabines de poudrage d’occasion peut être une option rentable pour les entreprises cherchant à réduire leurs coûts d’investissement.
- Considérations : Avant d’acheter des cabines d’occasion, il est important de vérifier l’état des systèmes de filtration, des systèmes de récupération de poudre, et des composants structurels pour s’assurer qu’ils sont en bon état de fonctionnement.
- Avantages : En plus de réduire les coûts, les cabines d’occasion offrent une solution rapide pour les entreprises qui ont besoin de démarrer leur production rapidement.
8. La Polyvalence des Fours Industriels : Choisir le Bon Équipement
Les fours industriels sont des équipements polyvalents utilisés dans une variété de processus de fabrication, allant du thermolaquage à la pyrolyse.
8.1 Fours de Pyrolyse Industriels
Les fours de pyrolyse industriels sont utilisés pour nettoyer les pièces en éliminant les résidus organiques par combustion à haute température.
- Applications : Utilisés principalement pour le nettoyage des outils de production et des moules, ces fours sont essentiels dans les industries où la propreté des pièces est cruciale pour la qualité du produit fini.
- Sécurité : Les fours de pyrolyse doivent être équipés de systèmes de contrôle de température précis et de dispositifs de sécurité pour éviter tout risque d’incendie ou de surchauffe.
8.2 Fours de Thermolaquage
Les fours de thermolaquage sont spécifiquement conçus pour polymériser les revêtements en poudre.
- Technologie de chauffage : Les technologies de chauffage utilisées dans ces fours, qu’elles soient à gaz ou électriques, doivent garantir une répartition homogène de la chaleur pour éviter les défauts de polymérisation.
- Capacité : Les fours de thermolaquage sont disponibles en différentes tailles, allant des petits fours pour les productions en série limitée aux fours industriels haute température capables de traiter de grandes quantités de pièces simultanément.
8.3 Fours de Revenu Tunnel
Les fours de revenu tunnel sont utilisés principalement dans les grandes installations industrielles pour le traitement continu des pièces.
- Fonctionnement : Ces fours permettent une production en continu, où les pièces passent à travers une série de zones à différentes températures pour un traitement thermique précis.
- Avantages : Le principal avantage de ces fours est leur capacité à traiter de grandes quantités de pièces en un temps réduit, tout en assurant une régularité dans le traitement thermique.
9. Le Séchage et l’Étuve dans le Processus de Revêtement : Etapes Cruciales
Le séchage et l’étuvage sont des étapes essentielles dans le processus de revêtement, assurant que le produit fini répond aux standards de qualité les plus élevés.
9.1 Séchage Industriel
Le séchage industriel intervient après l’application du revêtement pour éliminer toute humidité résiduelle.
- Techniques de séchage : Les techniques de séchage peuvent varier en fonction du type de revêtement utilisé. Certaines installations utilisent des tunnels de séchage, tandis que d’autres préfèrent des chambres de séchage statiques.
- Temps de séchage : Le temps de séchage doit être contrôlé avec précision pour éviter les défauts tels que les cloques ou les fissures dans le revêtement.
9.2 Étuve de Laquage
L’étuve de laquage est une étape critique pour durcir et stabiliser les revêtements appliqués.
- Contrôle de la température : Une température précise est essentielle pour garantir que le revêtement atteint sa dureté maximale sans compromettre son adhérence ou sa flexibilité.
- Durée d’étuvage : La durée d’étuvage peut varier en fonction de l’épaisseur du revêtement et du matériau de la pièce, et doit être ajustée pour chaque application spécifique.
10. Conclusion : Un Secteur en Évolution Permanente
Le secteur du revêtement par poudre et de la peinture poudre électrostatique est en constante évolution, avec des innovations continues dans les technologies et les équipements utilisés. Les entreprises doivent rester informées des dernières avancées pour maintenir leur compétitivité et garantir la qualité de leurs produits. En investissant dans des équipements modernes, en assurant une maintenance régulière, et en choisissant les bons procédés pour chaque application, elles peuvent non seulement améliorer leur efficacité opérationnelle, mais aussi répondre aux exigences croissantes en matière de durabilité et de respect de l’environnement.
Revêtement par Poudre
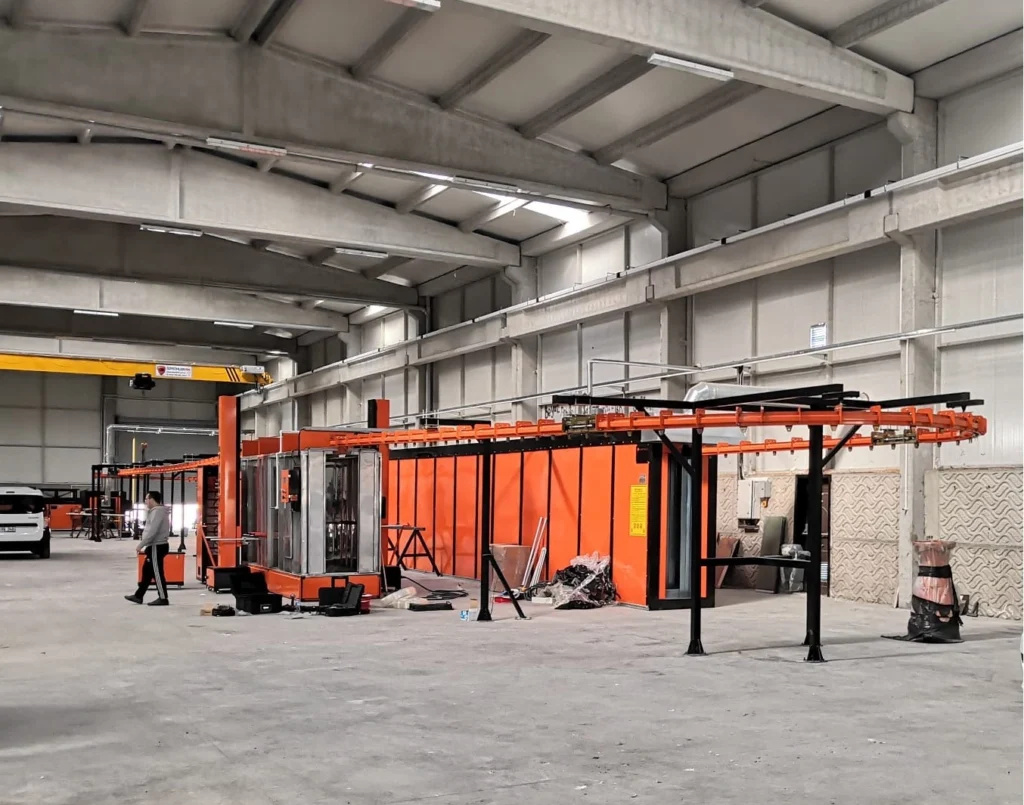
Le revêtement par poudre est une technologie de finition de surface de plus en plus populaire, utilisée principalement pour le traitement des surfaces métalliques. Ce procédé consiste à appliquer une poudre thermodurcissable sur une surface préalablement préparée, généralement métallique. La poudre est ensuite chauffée dans un four, où elle fond et forme un revêtement uniforme, durable et résistant aux chocs, à l’abrasion, et aux intempéries.
L’un des principaux avantages du revêtement par poudre est son respect de l’environnement. Contrairement aux peintures liquides traditionnelles, ce procédé n’utilise pas de solvants, ce qui réduit les émissions de composés organiques volatils (COV) et minimise les déchets. De plus, la poudre excédentaire peut être récupérée et réutilisée, ce qui en fait un choix économique et écologique.
Les secteurs industriels tels que l’automobile, l’électroménager, et le mobilier métallique utilisent largement le revêtement par poudre en raison de sa durabilité et de sa finition de haute qualité. Ce procédé est également apprécié pour sa capacité à offrir une grande variété de textures et de couleurs, permettant aux entreprises de personnaliser leurs produits selon les besoins des clients.
Peinture Poudre Electrostatique
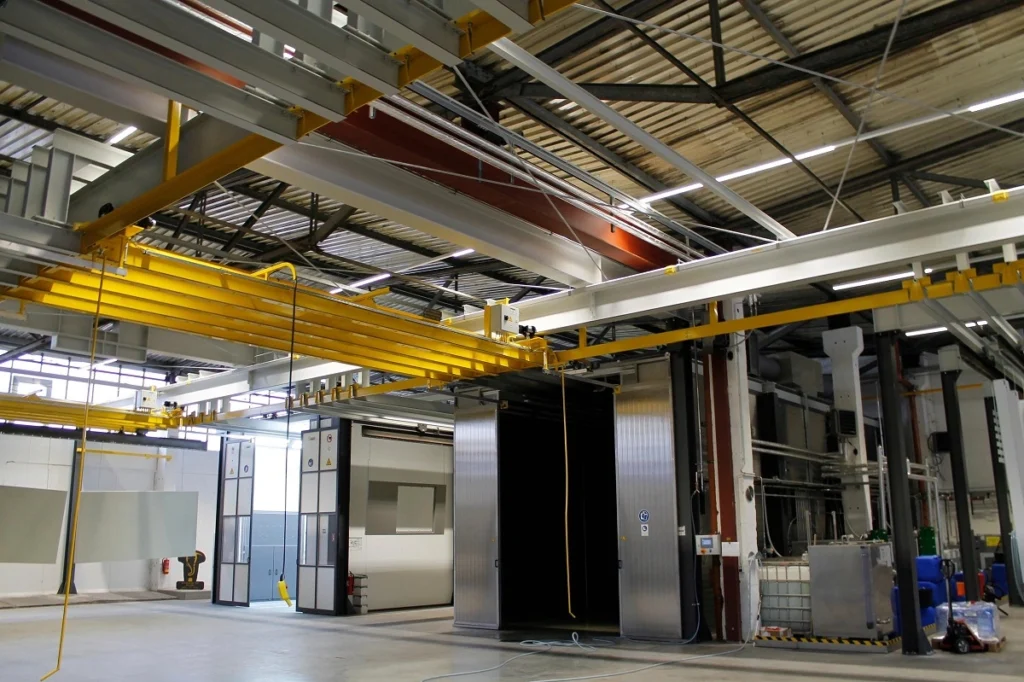
La peinture poudre électrostatique est une technique d’application de peinture en poudre qui utilise les propriétés électrostatiques pour assurer une adhésion uniforme de la poudre sur la surface de l’objet à traiter. Cette méthode est particulièrement efficace pour recouvrir des surfaces complexes ou irrégulières.
Le processus commence par la pulvérisation de la poudre à travers un pistolet électrostatique, qui charge électriquement les particules de poudre. Ces particules sont ensuite attirées par la surface métallique, qui est mise à la terre, créant ainsi une adhérence forte et uniforme. Une fois appliquée, la pièce est chauffée dans un four pour que la poudre fonde et se polymérise, formant une couche protectrice et esthétique.
La peinture poudre électrostatique est largement utilisée dans des industries où la qualité et la durabilité du revêtement sont essentielles, telles que l’automobile, l’électronique, et les équipements de construction. Les avantages de ce procédé incluent une meilleure couverture, une réduction des pertes de matière, et un résultat final qui offre une résistance supérieure aux agressions extérieures.
Système de Peinture
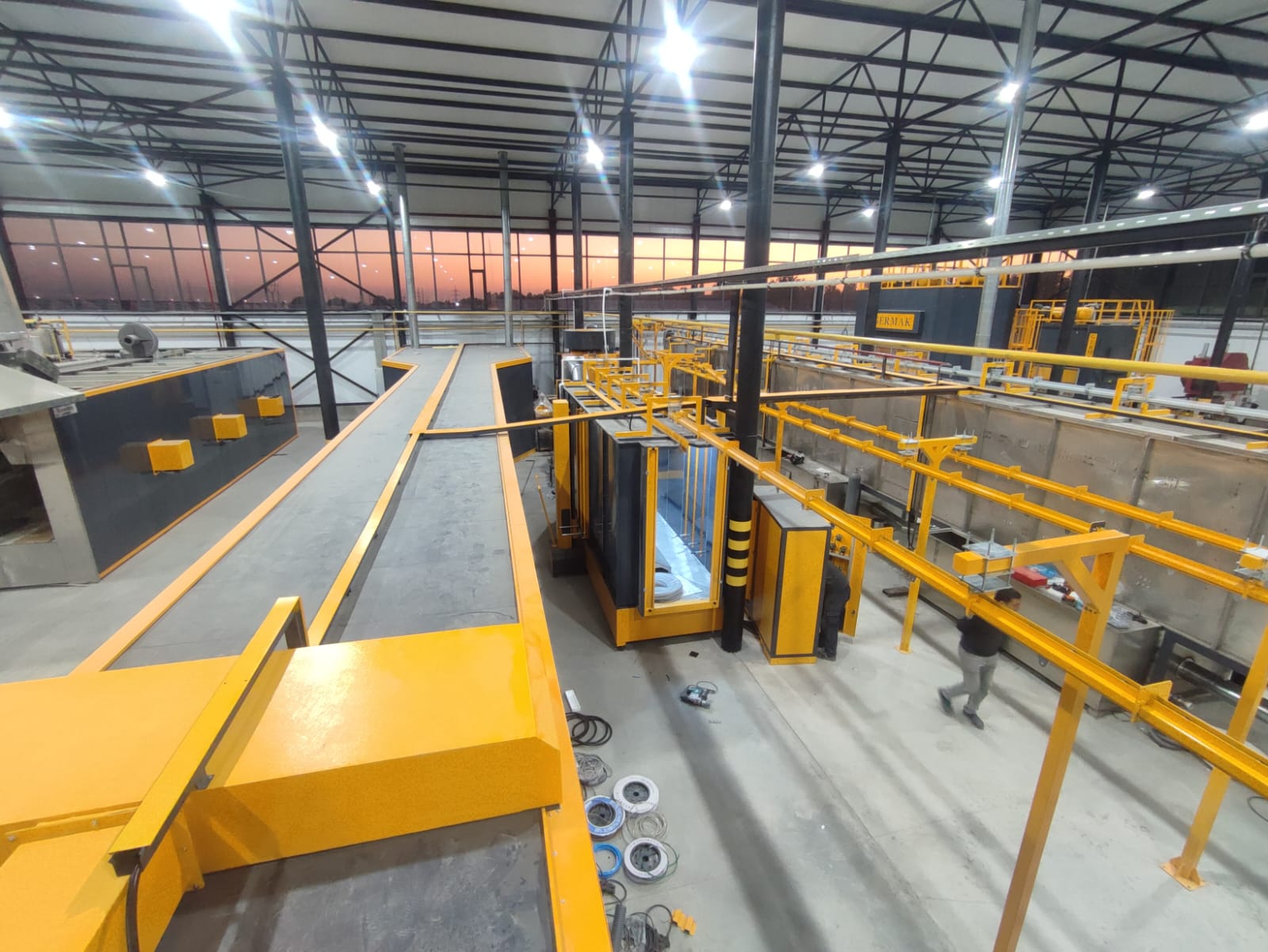
Un système de peinture se compose d’une série d’équipements et de procédés conçus pour appliquer des revêtements de peinture sur des surfaces spécifiques. Dans le contexte industriel, ces systèmes peuvent être très complexes, incluant des cabines de peinture, des pistolets, des fours de séchage et des systèmes de convoyage automatisés.
Les systèmes de peinture sont souvent personnalisés en fonction des besoins spécifiques de chaque entreprise, qu’il s’agisse de la nature des matériaux à peindre, du type de peinture utilisé, ou des exigences de production. Un système bien conçu peut améliorer l’efficacité, réduire les coûts de production, et assurer une qualité constante des produits finis.
Les systèmes de peinture modernes intègrent souvent des technologies avancées, telles que la robotique et l’automatisation, pour augmenter la précision et réduire les temps d’arrêt. Ils sont également équipés de dispositifs de sécurité et de contrôle de l’environnement, essentiels pour garantir des conditions de travail sûres et conformes aux normes environnementales.
Machine à Peinture
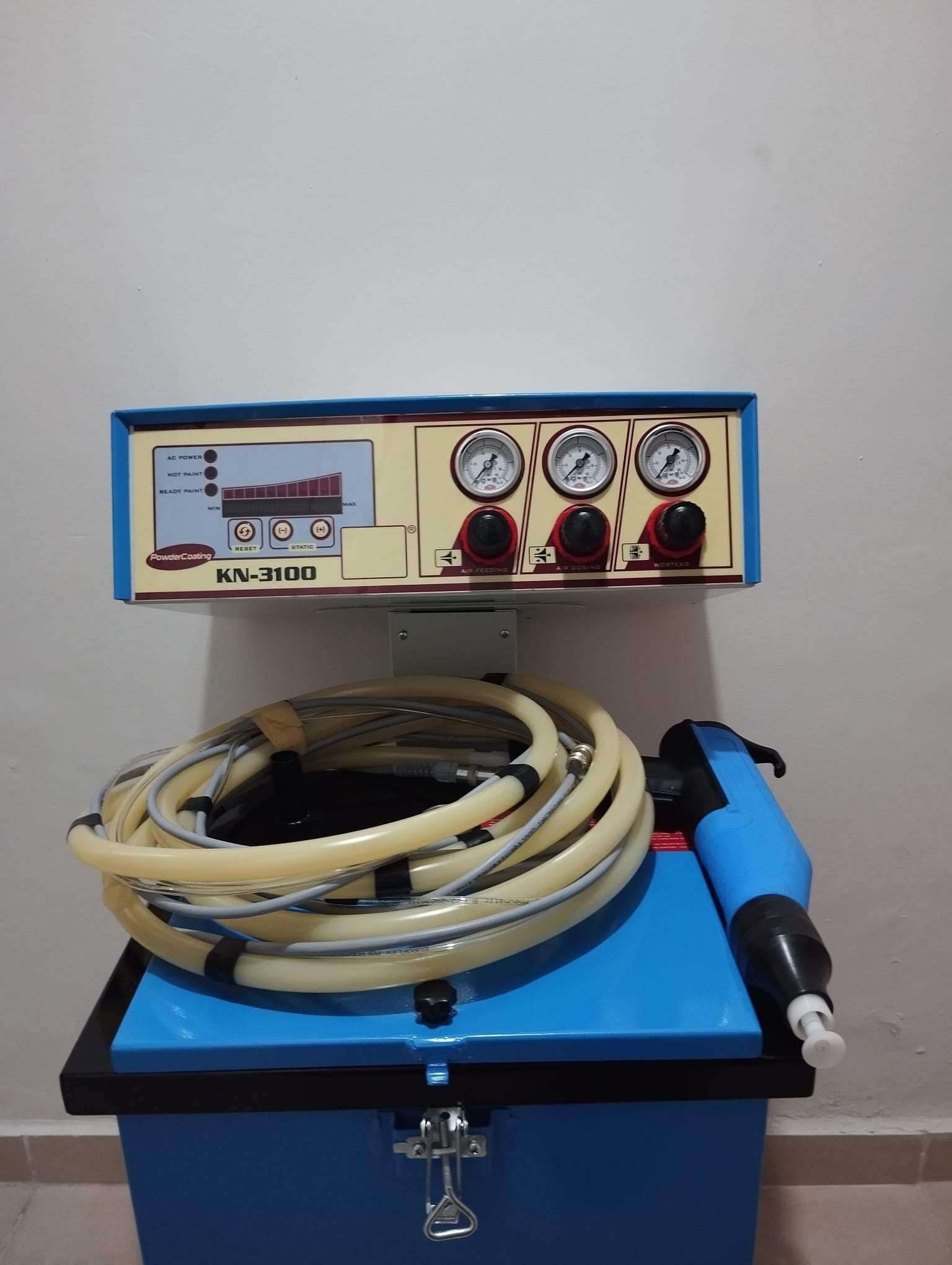
Une machine à peinture est un équipement utilisé pour appliquer de la peinture sur diverses surfaces, principalement dans des contextes industriels ou de production en série. Ces machines peuvent être conçues pour appliquer de la peinture liquide ou en poudre, selon les besoins spécifiques de l’application.
Les machines à peinture modernes sont souvent équipées de technologies avancées telles que les systèmes électrostatiques, qui permettent une application plus uniforme et efficace de la peinture, réduisant ainsi les pertes de matière et améliorant la qualité du revêtement. Elles peuvent être manuelles ou automatisées, avec des versions robotisées pour les grandes lignes de production.
L’utilisation de machines à peinture présente de nombreux avantages, notamment l’augmentation de la productivité, la réduction des coûts de main-d’œuvre, et l’amélioration de la qualité et de la cohérence des finitions. Elles sont couramment utilisées dans l’industrie automobile, l’électronique, et la production de biens de consommation durables.
Fabricant Cabine Peinture
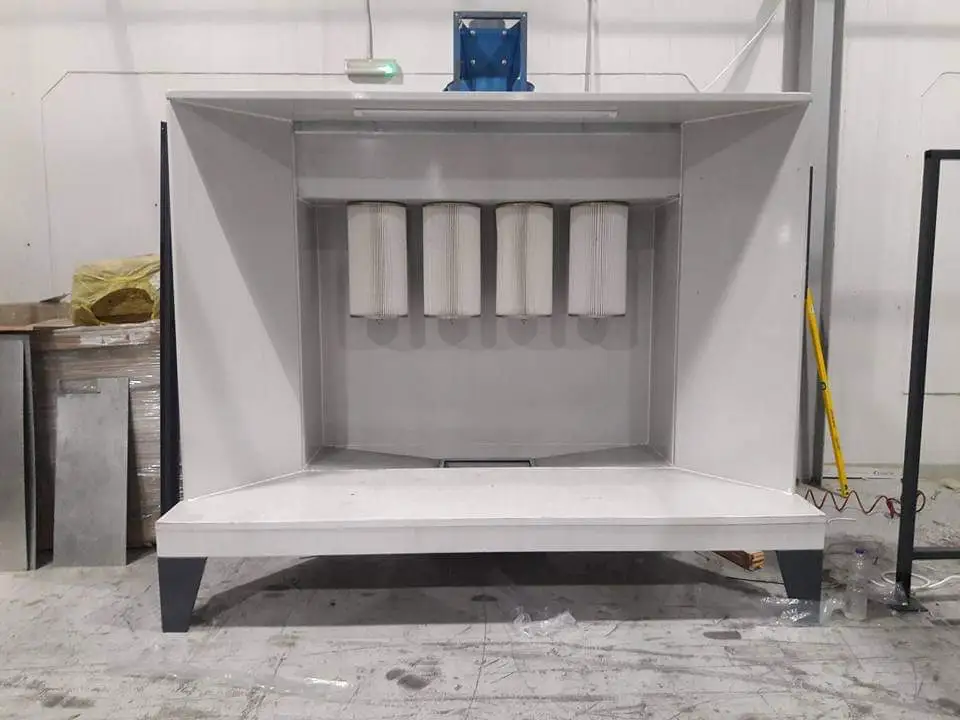
Les fabricants de cabines de peinture jouent un rôle crucial dans l’industrie du revêtement, fournissant des équipements spécialisés pour l’application de peinture dans des environnements contrôlés. Une cabine de peinture est une structure fermée où les objets à peindre sont placés pour être recouverts de peinture, en garantissant que les particules de peinture ne se dispersent pas dans l’air ambiant.
Ces cabines sont conçues pour répondre à des normes strictes de qualité et de sécurité, avec des systèmes de ventilation, de filtration, et de contrôle de température intégrés. Les fabricants de cabines de peinture offrent souvent des solutions sur mesure, adaptées aux besoins spécifiques des clients, qu’il s’agisse de cabines pour la peinture liquide ou pour le revêtement en poudre.
Les cabines de peinture sont essentielles dans les industries où la qualité de la finition est primordiale, telles que l’automobile, l’aéronautique, et la fabrication de meubles. Elles permettent d’obtenir des finitions uniformes et sans défauts, tout en protégeant les travailleurs et l’environnement des émanations toxiques.
Machine de Peinture
Les machines de peinture sont des équipements sophistiqués utilisés pour l’application de peinture sur divers types de surfaces, principalement dans le cadre de processus industriels. Ces machines peuvent être conçues pour appliquer à la fois des peintures liquides et des revêtements en poudre, selon les exigences de l’application.
Les machines de peinture modernes sont souvent automatisées, intégrant des technologies telles que la pulvérisation électrostatique et la robotique pour assurer une application précise et uniforme. Elles peuvent être utilisées pour peindre des objets de toutes tailles, des petites pièces électroniques aux grandes structures métalliques.
L’utilisation de machines de peinture présente plusieurs avantages, notamment une productivité accrue, une qualité de finition améliorée, et une réduction des coûts de production. Elles sont essentielles dans des secteurs comme l’automobile, l’électronique, et la production industrielle, où la qualité et la cohérence des revêtements sont des critères clés.
Four Peinture Thermolaquage
Le four de peinture thermolaquage est un équipement essentiel dans le processus de revêtement en poudre, utilisé pour polymériser la peinture en poudre appliquée sur des surfaces métalliques. Ce four chauffe les objets à des températures spécifiques, généralement entre 160 et 200 degrés Celsius, pour faire fondre la poudre et former une couche uniforme et durable.
Les fours de thermolaquage peuvent être alimentés au gaz ou à l’électricité, avec des versions disponibles pour différentes tailles et types de production, allant des petits ateliers aux grandes usines. Ils sont conçus pour offrir une distribution uniforme de la chaleur, essentielle pour garantir une qualité de finition élevée et éviter les défauts tels que les cloques ou les fissures.
L’utilisation de fours de thermolaquage est courante dans des industries telles que l’automobile, l’électroménager, et la fabrication de meubles métalliques, où la durabilité et l’esthétique du revêtement sont primordiales. Ces fours sont également appréciés pour leur efficacité énergétique et leur capacité à traiter de grandes quantités de pièces en une seule fois.
Petit Four Industriel
Un petit four industriel est un équipement utilisé dans diverses applications industrielles, y compris le séchage, la cuisson, et la polymérisation de peintures et de revêtements. Ces fours sont de plus petite taille que les fours industriels standards, ce qui les rend adaptés aux ateliers de production de petite à moyenne échelle ou aux entreprises ayant des besoins spécifiques en matière de traitement thermique.
Les petits fours industriels sont souvent utilisés pour des productions en série limitée, des tests de produits, ou des applications nécessitant un contrôle précis de la température. Ils sont disponibles en différentes configurations, y compris les modèles à convection, à rayonnement, ou à induction, selon les besoins spécifiques du processus.
Ces fours sont largement utilisés dans des industries telles que l’électronique, la bijouterie, et la fabrication de petites pièces métalliques. Leur petite taille et leur efficacité en font un choix populaire pour les entreprises cherchant à maximiser leur espace tout en maintenant une capacité de production élevée.
Peinture Electrostatique en Poudre
La peinture électrostatique en poudre est une technique d’application de revêtement en poudre qui utilise un champ électrostatique pour attirer les particules de poudre sur une surface métallique. Cette méthode est particulièrement efficace pour obtenir une couverture uniforme et une adhésion solide, même sur des surfaces complexes.
Le processus de peinture électrostatique en poudre commence par la pulvérisation de la poudre à travers un pistolet qui charge électriquement les particules. Ces particules sont ensuite attirées par la surface opposée, qui est mise à la terre, créant ainsi une adhérence forte et uniforme. La pièce est ensuite chauffée dans un four pour faire fondre et polymériser la poudre, formant un revêtement durable et esthétique.
Cette technique est couramment utilisée dans des secteurs tels que l’automobile, l’électronique, et les équipements industriels, où la qualité du revêtement est essentielle. Les avantages incluent une réduction des pertes de matière, une amélioration de la qualité de la finition, et une meilleure résistance aux agressions extérieures.
Pistolet Peinture Thermolaquage
Le pistolet de peinture thermolaquage est un outil essentiel dans l’application de revêtement en poudre. Ce pistolet est conçu pour pulvériser de la poudre sur une surface métallique de manière uniforme, en utilisant la technologie électrostatique pour assurer une adhésion optimale.
Le pistolet charge électriquement les particules de poudre, qui sont ensuite attirées par la surface à peindre, créant ainsi une couverture uniforme, même sur des surfaces complexes ou difficiles d’accès. Après l’application, la pièce est chauffée dans un four de thermolaquage, où la poudre fond et forme un revêtement solide et durable.
Les pistolets de peinture thermolaquage sont largement utilisés dans l’industrie automobile, l’électronique, et la production de biens de consommation durables, où la qualité et la cohérence du revêtement sont des critères clés. Ils permettent une application précise, réduisant ainsi les pertes de matière et améliorant l’efficacité du processus de peinture.
Cabine de Peinture Professionnelle
Une cabine de peinture professionnelle est une structure fermée spécialement conçue pour l’application de peinture dans un environnement contrôlé. Ces cabines sont utilisées pour éviter la dispersion de la peinture dans l’air ambiant et pour garantir que la peinture est appliquée de manière uniforme et sans défaut.
Les cabines de peinture professionnelles sont équipées de systèmes de ventilation et de filtration pour capturer les particules de peinture excédentaires et maintenir un environnement propre à l’intérieur de la cabine. Elles peuvent être utilisées pour l’application de peintures liquides ou en poudre, selon les besoins de l’entreprise.
Ces cabines sont indispensables dans des industries où la qualité de la finition est primordiale, telles que l’automobile, l’aéronautique, et la fabrication de meubles. Elles permettent d’obtenir des finitions uniformes et sans défauts, tout en protégeant les travailleurs et l’environnement des émanations toxiques.
Cabine Poudrage
Une cabine de poudrage est une installation spécialisée utilisée pour l’application de revêtement en poudre. Ces cabines sont conçues pour créer un environnement contrôlé où la poudre peut être appliquée uniformément sur une surface métallique, avant d’être chauffée pour former un revêtement durable.
Les cabines de poudrage sont équipées de systèmes de récupération de poudre qui permettent de capturer la poudre excédentaire et de la réutiliser, ce qui réduit les déchets et améliore l’efficacité du processus. Elles sont également dotées de systèmes de filtration avancés pour maintenir la propreté de l’air à l’intérieur de la cabine.
Ces cabines sont largement utilisées dans l’industrie automobile, l’électronique, et la fabrication de meubles, où la qualité du revêtement est essentielle. Elles permettent d’obtenir des finitions uniformes et résistantes, tout en minimisant les pertes de matière et les impacts environnementaux.
Étuve de Laquage
L’étuve de laquage est un équipement utilisé pour durcir et stabiliser les revêtements appliqués sur des surfaces métalliques. Après l’application de la peinture ou du revêtement en poudre, les pièces sont placées dans l’étuve, où elles sont chauffées à des températures précises pour garantir une adhérence optimale et une durabilité accrue.
L’étuvage est une étape cruciale dans le processus de finition, car il permet de renforcer les propriétés mécaniques du revêtement, notamment sa résistance à l’usure, aux chocs, et aux intempéries. Les étuves de laquage sont disponibles en différentes tailles et configurations, en fonction des besoins spécifiques de l’entreprise.
Ces équipements sont couramment utilisés dans des industries telles que l’automobile, l’électroménager, et la production de biens de consommation durables, où la qualité et la durabilité du revêtement sont des critères essentiels.
Polymérisation Peinture
La polymérisation de la peinture est un processus chimique essentiel dans le revêtement par poudre, où la poudre appliquée sur une surface est chauffée pour former une couche solide et durable. Ce processus se déroule généralement dans un four, à des températures comprises entre 160 et 200 degrés Celsius.
Pendant la polymérisation, les résines thermodurcissables contenues dans la poudre fondent et réagissent chimiquement pour former une structure réticulée, ce qui confère au revêtement ses propriétés mécaniques et chimiques. La qualité de la polymérisation est cruciale pour garantir que le revêtement offre une protection efficace contre la corrosion, les chocs, et l’abrasion.
Le processus de polymérisation est utilisé dans de nombreuses industries, notamment l’automobile, l’électronique, et la fabrication de meubles, où la durabilité et la qualité de la finition sont primordiales. Les fours de polymérisation doivent être soigneusement calibrés pour garantir une température uniforme et un temps de cuisson adéquat, assurant ainsi un résultat optimal.
Peinture Thermolaquage
La peinture thermolaquage est une technique de revêtement en poudre où la poudre est appliquée sur une surface métallique, puis chauffée pour former un revêtement durable et résistant. Ce procédé est largement utilisé dans l’industrie pour protéger et embellir les pièces métalliques.
Le thermolaquage offre plusieurs avantages par rapport aux méthodes traditionnelles de peinture liquide, notamment une meilleure adhérence, une résistance accrue à l’usure, et une réduction des émissions de COV. De plus, le thermolaquage permet de réaliser des finitions variées, allant des surfaces lisses et brillantes aux textures mates et rugueuses.
Cette technique est couramment utilisée dans des secteurs tels que l’automobile, l’électroménager, et la construction métallique, où la qualité et la durabilité du revêtement sont des critères essentiels. Le thermolaquage est également apprécié pour sa flexibilité, permettant d’appliquer des revêtements sur des pièces de toutes formes et tailles.
Types de Procédé de Revêtement Métallique
Il existe plusieurs types de procédés de revêtement métallique, chacun adapté à des applications spécifiques et offrant différents niveaux de protection et de finition. Parmi les procédés les plus courants, on trouve le thermolaquage, la galvanisation, le chromage, et la peinture liquide.
- Thermolaquage : Utilisé pour son excellente adhérence et sa durabilité, le thermolaquage est idéal pour les applications où la résistance à la corrosion et aux intempéries est essentielle.
- Galvanisation : Ce procédé consiste à appliquer une couche de zinc sur une surface métallique pour la protéger contre la corrosion. Il est largement utilisé dans la construction et l’industrie automobile.
- Chromage : Le chromage est un procédé de placage utilisé pour améliorer l’apparence et la résistance à la corrosion des pièces métalliques. Il est couramment utilisé pour les pièces décoratives et fonctionnelles dans l’industrie automobile.
- Peinture liquide : Traditionnellement utilisée pour une variété de matériaux, la peinture liquide offre une large gamme de couleurs et de finitions, mais peut être moins durable que les autres procédés.
Le choix du procédé dépend des exigences spécifiques de l’application, telles que la résistance souhaitée, l’environnement d’utilisation, et les contraintes budgétaires. Les industries qui exigent des finitions de haute qualité et durables privilégient souvent le thermolaquage et la galvanisation.
Type de Peinture Industrielle
Il existe plusieurs types de peinture industrielle, chacun conçu pour répondre à des besoins spécifiques en termes de protection, d’esthétique, et de durabilité. Les peintures industrielles sont largement utilisées pour protéger les structures métalliques, les équipements, et les véhicules contre la corrosion, l’usure, et les conditions environnementales extrêmes.
- Peinture époxy : Très résistante à l’abrasion, aux produits chimiques, et à l’humidité, la peinture époxy est souvent utilisée pour les sols industriels, les équipements marins, et les réservoirs de stockage.
- Peinture polyuréthane : Offrant une excellente résistance aux UV et aux intempéries, la peinture polyuréthane est idéale pour les applications extérieures, telles que les structures en acier et les véhicules.
- Peinture acrylique : Facile à appliquer et à sécher rapidement, la peinture acrylique est utilisée pour une variété d’applications, y compris les machines industrielles et les équipements de construction.
- Peinture en poudre : Utilisée pour sa durabilité et son respect de l’environnement, la peinture en poudre est couramment utilisée dans l’industrie automobile et la fabrication de meubles.
Le choix du type de peinture dépend de l’application spécifique et des conditions auxquelles le revêtement sera exposé. Les peintures industrielles doivent offrir une protection durable tout en répondant aux exigences esthétiques et aux normes environnementales.
Four à Gaz Industriel Québec
Le four à gaz industriel au Québec est un équipement essentiel dans de nombreuses industries, utilisé pour une variété de processus thermiques, tels que le séchage, la cuisson, et la polymérisation des peintures et des revêtements. Les fours à gaz sont particulièrement appréciés pour leur efficacité énergétique et leur capacité à atteindre des températures élevées rapidement.
Au Québec, les industries telles que l’automobile, l’aéronautique, et la fabrication de produits métalliques utilisent des fours à gaz industriels pour traiter de grandes quantités de pièces tout en maintenant une qualité constante. Ces fours sont souvent personnalisés pour répondre aux exigences spécifiques des processus de production, avec des options pour le contrôle précis de la température, de l’humidité, et du flux d’air.
Les fabricants de fours à gaz industriels au Québec offrent une large gamme de solutions, allant des petits fours pour les ateliers de production aux grands fours de tunnel pour les lignes de production en série. La maintenance régulière et le dépannage sont essentiels pour assurer le bon fonctionnement de ces équipements et maximiser leur durée de vie.
Étuvage Peinture
L’étuvage de la peinture est une étape cruciale dans le processus de finition, où la peinture fraîchement appliquée est chauffée pour durcir et se stabiliser. Cette étape est essentielle pour assurer une adhérence optimale de la peinture à la surface et pour renforcer ses propriétés mécaniques, telles que la résistance à l’usure et à la corrosion.
L’étuvage est généralement effectué dans des étuves spécialisées, qui sont conçues pour maintenir une température et une humidité constantes tout au long du processus. Le temps et la température d’étuvage varient en fonction du type de peinture utilisée et des spécifications du revêtement.
Les industries qui utilisent des peintures à haute performance, comme l’automobile, l’aéronautique, et l’électronique, dépendent de l’étuvage pour garantir la qualité et la durabilité de leurs produits. Un étuvage bien contrôlé peut améliorer la résistance aux intempéries, la dureté de la surface, et la longévité du revêtement.
Étuve Industrielle Grand Volume
Une étuve industrielle grand volume est un équipement utilisé pour le traitement thermique de grandes quantités de pièces ou de composants, principalement dans des applications industrielles. Ces étuves sont conçues pour gérer des lots de production de grande taille, offrant un contrôle précis de la température et de l’humidité pour assurer une qualité uniforme du traitement.
Les étuves industrielles grand volume sont couramment utilisées dans des industries telles que l’automobile, l’aéronautique, et la fabrication de produits métalliques, où la capacité de traiter simultanément de grandes quantités de pièces est essentielle pour maintenir des délais de production serrés.
Ces étuves peuvent être personnalisées pour répondre aux besoins spécifiques de chaque entreprise, avec des options pour le flux d’air, le chauffage par convection ou rayonnement, et la récupération de chaleur. La maintenance régulière de ces étuves est cruciale pour assurer leur bon fonctionnement et maximiser leur durée de vie.
Thermolaquage Haute Température
Le thermolaquage haute température est une technique de revêtement en poudre utilisée pour appliquer des revêtements qui doivent résister à des températures élevées. Ce procédé est particulièrement utile dans des applications où les pièces finies seront exposées à des conditions thermiques extrêmes, comme dans les moteurs, les échappements, ou les équipements industriels.
Le thermolaquage haute température implique l’application d’une poudre thermodurcissable qui est ensuite cuite à des températures allant de 200 à 450 degrés Celsius, selon le type de poudre utilisé. Ce processus garantit que le revêtement offre une excellente adhérence, résistance à la corrosion, et durabilité, même dans des environnements à haute température.
Cette technique est largement utilisée dans l’industrie automobile, l’aéronautique, et la fabrication d’équipements industriels, où les pièces doivent souvent résister à des cycles thermiques intenses sans dégrader leur protection ou leur apparence.
Fabricant de Four Industriel
Les fabricants de fours industriels jouent un rôle clé dans la fourniture d’équipements essentiels pour divers processus thermiques utilisés dans les industries de production. Ces fours sont conçus pour répondre à des besoins spécifiques, tels que la cuisson, le séchage, la polymérisation, ou la chaleur de traitement, et sont disponibles dans une large gamme de tailles et de configurations.
Les fours industriels peuvent être alimentés au gaz, à l’électricité, ou par d’autres sources d’énergie, selon les besoins de l’application. Les fabricants de fours industriels offrent souvent des solutions personnalisées, adaptées aux spécifications exactes des processus de production des clients, incluant des systèmes de contrôle avancés pour réguler précisément la température, l’humidité, et le flux d’air.
Les industries qui dépendent des fours industriels incluent l’automobile, l’aéronautique, la métallurgie, et la production de biens de consommation durables. Le choix d’un four industriel adapté est crucial pour garantir l’efficacité, la qualité, et la rentabilité des processus de production.
Filtres Cabine de Peinture
Les filtres de cabine de peinture sont des composants essentiels dans le fonctionnement des cabines de peinture, utilisés pour capturer les particules de peinture excédentaires et maintenir un environnement propre et sûr à l’intérieur de la cabine. Ces filtres jouent un rôle crucial dans la prévention des contaminations croisées et dans la garantie d’une finition de haute qualité.
Il existe différents types de filtres de cabine de peinture, y compris les filtres à air primaire, les filtres plissés, et les filtres HEPA, chacun étant conçu pour capturer des particules de tailles spécifiques. La maintenance régulière et le remplacement des filtres sont essentiels pour assurer leur efficacité et prolonger la durée de vie de la cabine de peinture.
Les industries qui utilisent des cabines de peinture, telles que l’automobile, l’aéronautique, et la fabrication de meubles, dépendent de filtres de haute qualité pour garantir que leurs produits finis sont exempts de défauts et répondent aux normes de qualité les plus élevées.
Peinture Cuite au Four
La peinture cuite au four est une technique de finition qui implique l’application d’une peinture liquide ou en poudre sur une surface, suivie d’un processus de cuisson pour durcir et stabiliser le revêtement. Cette méthode est largement utilisée dans l’industrie pour obtenir des finitions durables et résistantes.
La cuisson de la peinture dans un four permet au revêtement de polymériser, ce qui améliore ses propriétés mécaniques et chimiques, telles que la résistance à l’abrasion, aux produits chimiques, et aux intempéries. Les températures de cuisson varient en fonction du type de peinture utilisé, mais elles sont généralement comprises entre 150 et 250 degrés Celsius.
Les industries qui utilisent la peinture cuite au four incluent l’automobile, l’électroménager, et la fabrication de meubles métalliques. Cette technique permet d’obtenir des finitions de haute qualité avec une excellente adhérence et durabilité, ce qui est essentiel pour les produits destinés à des environnements exigeants.
Maintenance Filtres Cabines Peinture
La maintenance des filtres de cabine de peinture est une tâche cruciale pour garantir le bon fonctionnement des cabines de peinture et la qualité des finitions. Les filtres de cabine de peinture capturent les particules de peinture excédentaires et empêchent leur dispersion dans l’air, ce qui protège à la fois les travailleurs et l’environnement.
Un entretien régulier des filtres est essentiel pour éviter l’accumulation de particules qui pourraient obstruer les filtres et réduire leur efficacité. Cela inclut le nettoyage ou le remplacement des filtres à intervalles réguliers, selon les recommandations du fabricant et le volume de production.
Les industries qui dépendent des cabines de peinture, telles que l’automobile, l’aéronautique, et la fabrication de meubles, doivent s’assurer que leurs filtres sont bien entretenus pour garantir que leurs produits finis répondent aux normes de qualité les plus élevées. Une maintenance adéquate des filtres peut également prolonger la durée de vie des équipements et réduire les coûts de production.
Four Électrique Industriel
Un four électrique industriel est un équipement essentiel utilisé pour diverses applications thermiques dans les industries de production. Contrairement aux fours à gaz, les fours électriques offrent un contrôle précis de la température et sont souvent préférés pour les processus nécessitant une régulation thermique stricte.
Les fours électriques industriels sont disponibles en différentes tailles et configurations, y compris les fours de polymérisation, de séchage, et de revenu. Ils sont utilisés dans une variété d’industries, telles que l’automobile, l’électronique, et la métallurgie, où un contrôle précis de la température est crucial pour garantir la qualité et la cohérence des produits finis.
Les avantages des fours électriques incluent une efficacité énergétique supérieure, une réduction des émissions de gaz, et une capacité à atteindre des températures très élevées, ce qui les rend idéaux pour des applications spécialisées. La maintenance régulière des composants électriques et des éléments de chauffage est essentielle pour assurer un fonctionnement fiable et prolonger la durée de vie de l’équipement.
Cabine de Poudrage Occasion
L’achat d’une cabine de poudrage d’occasion peut être une solution rentable pour les entreprises cherchant à optimiser leurs coûts d’investissement. Ces cabines, bien que d’occasion, peuvent offrir les mêmes performances que les modèles neufs, à condition qu’elles soient bien entretenues et en bon état de fonctionnement.
Lors de l’achat d’une cabine de poudrage d’occasion, il est important de vérifier l’état des systèmes de récupération de poudre, des filtres, et de la structure de la cabine. Une inspection minutieuse et, si nécessaire, une mise à niveau des composants critiques peuvent garantir que la cabine répond aux normes de production et de sécurité actuelles.
Les entreprises qui choisissent d’investir dans des cabines de poudrage d’occasion bénéficient d’une réduction significative des coûts initiaux tout en conservant une capacité de production efficace. Cette option est particulièrement attrayante pour les petites et moyennes entreprises qui cherchent à améliorer leur production sans engager des dépenses excessives.
Les petites cabines de pulvérisation sont une solution idéale pour les petites applications de peinture. Elles sont abordables, faciles à utiliser et compactes.
La petite cabine de pulvérisation est un équipement indispensable dans les processus de revêtement, en particulier pour les entreprises ou ateliers de petite taille, les productions à faible volume ou les applications nécessitant un traitement localisé. Conçue pour offrir une solution compacte et économique, elle est parfaitement adaptée aux espaces restreints tout en garantissant une qualité optimale dans l’application de peintures ou de poudres. Son utilisation est particulièrement répandue dans les domaines de la personnalisation, de la réparation, et des finitions sur des pièces spécifiques ou des lots réduits.
Les petites cabines de pulvérisation se distinguent par leur simplicité d’installation et d’utilisation. Elles sont souvent fabriquées en matériaux légers mais robustes, tels que l’acier galvanisé ou l’aluminium, assurant une résistance à la corrosion et une durabilité à long terme. Ces cabines sont généralement équipées de systèmes de ventilation efficaces pour capturer les particules de peinture ou de poudre en excès, garantissant ainsi un environnement de travail propre et sécurisé. Cette fonctionnalité est essentielle pour protéger les opérateurs des émanations nocives et maintenir une atmosphère de travail saine.
L’un des principaux atouts des petites cabines de pulvérisation est leur polyvalence. Elles peuvent être utilisées avec différents types de peintures, qu’elles soient à base de solvants, à base d’eau ou sous forme de poudre. Cela les rend idéales pour une variété d’applications, qu’il s’agisse de projets artistiques, de la restauration d’objets anciens, ou de la finition de pièces industrielles de petite taille. De plus, leur conception modulaire permet souvent d’ajouter des fonctionnalités supplémentaires, comme des filtres spécifiques pour différents types de produits ou des systèmes de récupération de poudre pour minimiser les pertes et réduire les coûts.
Les cabines compactes offrent également un contrôle précis du processus de pulvérisation. Grâce à des systèmes de filtration avancés, elles capturent les particules excédentaires, réduisant ainsi les risques de contamination croisée entre les couleurs ou les types de revêtements. Certaines cabines sont équipées de parois transparentes ou semi-transparentes, permettant aux opérateurs de surveiller visuellement le processus sans compromettre la sécurité. Ces caractéristiques font des petites cabines de pulvérisation un choix idéal pour des travaux exigeant une finition impeccable et un contrôle strict des paramètres.
Pour les artisans et les petites entreprises, ces cabines représentent une solution économique et accessible. Leur coût d’acquisition est généralement inférieur à celui des grandes installations industrielles, tout en offrant des performances comparables pour des volumes de production réduits. De plus, leur faible encombrement permet de les installer dans des ateliers standards sans nécessiter d’importantes modifications de l’infrastructure existante. Cela est particulièrement avantageux pour les entreprises souhaitant optimiser leur espace tout en intégrant un processus de pulvérisation professionnel dans leur production.
Sur le plan écologique, les petites cabines de pulvérisation modernes sont souvent conçues pour minimiser leur impact sur l’environnement. Les systèmes de récupération de poudre permettent de réutiliser les excédents, réduisant ainsi le gaspillage de matériaux. Par ailleurs, les filtres intégrés limitent les émissions de particules et les rejets dans l’air, contribuant à un environnement de travail plus propre et respectueux des réglementations environnementales. Ces aspects sont de plus en plus importants dans un contexte où les entreprises cherchent à adopter des pratiques durables tout en maintenant des coûts compétitifs.
Dans le cadre de productions à faible volume, les petites cabines de pulvérisation se révèlent également idéales pour les changements fréquents de couleurs ou de matériaux. Leur conception permet un nettoyage rapide et facile, réduisant ainsi les temps d’arrêt entre les lots. Cela est particulièrement utile pour les entreprises travaillant sur des commandes personnalisées ou produisant des prototypes nécessitant des ajustements fréquents. Les fabricants proposent également des options de personnalisation pour ces cabines, permettant aux utilisateurs de les adapter à leurs besoins spécifiques.
En termes de sécurité, ces cabines sont conçues pour respecter des normes strictes. Les systèmes de ventilation intégrés empêchent l’accumulation de particules inflammables ou explosives dans l’air, réduisant les risques d’accidents. De plus, les matériaux ignifuges utilisés dans leur fabrication augmentent la sécurité globale de l’installation. Les opérateurs peuvent ainsi travailler en toute confiance, sachant que leur environnement de travail est bien protégé contre les dangers potentiels.
Le transport et l’installation des petites cabines de pulvérisation sont également simplifiés grâce à leur taille réduite et à leur conception légère. De nombreuses cabines sont livrées sous forme de kits faciles à assembler, permettant une mise en service rapide. Cette modularité est particulièrement utile pour les entreprises ou les artisans qui ont besoin d’une solution portable ou temporaire, comme lors de salons professionnels, d’expositions, ou d’interventions sur site.
Les secteurs qui bénéficient particulièrement des petites cabines de pulvérisation incluent la réparation automobile, la personnalisation de vélos, la restauration de meubles, et même la fabrication de bijoux ou d’objets décoratifs. Ces industries requièrent souvent une précision et une qualité de finition élevées, que les petites cabines de pulvérisation sont parfaitement capables de fournir. Elles permettent aux opérateurs de travailler sur des pièces uniques ou de petits lots sans compromettre la qualité ou l’efficacité du processus.
En conclusion, les petites cabines de pulvérisation offrent une solution pratique, économique et polyvalente pour une large gamme d’applications. Elles combinent des performances professionnelles avec une conception compacte et accessible, répondant aux besoins des petites entreprises, des artisans et des ateliers spécialisés. Avec leur capacité à offrir une finition de haute qualité, à optimiser les matériaux et à garantir un environnement de travail sûr et écologique, ces cabines sont un outil indispensable pour ceux qui recherchent des solutions de revêtement efficaces et abordables.
Les petites cabines de pulvérisation jouent également un rôle essentiel dans les projets de recherche et développement. Dans les laboratoires et les départements de prototypage, où la création de nouveaux produits ou matériaux exige des essais fréquents, ces cabines permettent d’effectuer des tests rapides et précis. Grâce à leur flexibilité, elles s’adaptent à une variété de scénarios expérimentaux, qu’il s’agisse de tester de nouvelles formulations de peinture, d’évaluer l’adhérence de revêtements sur différents matériaux, ou d’observer le comportement des produits dans des conditions simulées.
Un autre avantage significatif réside dans leur efficacité énergétique. Comparées aux installations de plus grande taille, les petites cabines nécessitent moins d’énergie pour fonctionner, ce qui réduit les coûts opérationnels tout en limitant l’impact environnemental. De plus, leur utilisation efficace de l’espace et des ressources s’inscrit parfaitement dans les démarches visant à rendre les processus industriels plus durables. Les fabricants intègrent de plus en plus des technologies écoénergétiques, telles que des systèmes LED pour l’éclairage et des ventilateurs basse consommation, afin d’optimiser leur performance globale.
Les petites cabines sont également un excellent choix pour les amateurs et les artisans passionnés qui souhaitent apporter des finitions professionnelles à leurs créations. Que ce soit pour peindre des objets décoratifs, restaurer des pièces anciennes ou personnaliser des articles comme des casques ou des instruments de musique, ces cabines offrent un contrôle total sur le processus d’application. Elles permettent aux utilisateurs de travailler dans des conditions similaires à celles des professionnels, tout en restant abordables et adaptées aux espaces domestiques ou aux petits ateliers.
Dans le domaine de l’enseignement et de la formation, les petites cabines de pulvérisation sont de plus en plus utilisées pour initier les étudiants et les apprentis aux techniques de revêtement. Leur simplicité et leur sécurité en font un outil pédagogique idéal pour comprendre les principes de base de la pulvérisation, tout en permettant d’expérimenter avec différents matériaux et procédés. Les écoles techniques, les universités et les centres de formation professionnelle intègrent souvent ces cabines dans leurs équipements pour offrir des expériences pratiques aux apprenants.
La maintenance de ces cabines est relativement simple, ce qui constitue un autre atout majeur. Les filtres, qui jouent un rôle crucial dans la capture des particules, sont faciles à remplacer ou à nettoyer, prolongeant ainsi la durée de vie de l’équipement. Les surfaces internes, souvent recouvertes de matériaux antiadhésifs, facilitent le nettoyage des dépôts de peinture ou de poudre. Cette facilité d’entretien contribue à maintenir un haut niveau de performance tout en réduisant les coûts d’exploitation.
Enfin, avec l’évolution constante des technologies de revêtement, les petites cabines de pulvérisation continuent de bénéficier d’améliorations. Les systèmes modernes intègrent des fonctionnalités telles que le contrôle numérique des paramètres de pulvérisation, la connectivité IoT pour le suivi à distance et l’analyse des données de production, ainsi que des interfaces utilisateur intuitives pour une utilisation simplifiée. Ces avancées rendent ces cabines encore plus attractives pour un large éventail d’utilisateurs, des amateurs aux professionnels.
En somme, les petites cabines de pulvérisation représentent une solution fiable et efficace pour répondre aux besoins diversifiés des industries, des ateliers d’artisanat et des projets individuels. Leur adaptabilité, leur simplicité et leur coût abordable les placent parmi les équipements les plus polyvalents et accessibles pour le revêtement et la finition. Avec des innovations continues et une demande croissante pour des outils performants et respectueux de l’environnement, elles continueront d’occuper une place centrale dans le paysage industriel et artisanal.
Les petites cabines de pulvérisation, en dépit de leur taille réduite, offrent également des possibilités de personnalisation avancées, ce qui les rend particulièrement intéressantes pour des secteurs aux exigences spécifiques. Par exemple, dans l’industrie de la mode ou du design, elles sont utilisées pour appliquer des finitions innovantes sur des matériaux non conventionnels, comme les tissus ou les composites. Ces applications nécessitent souvent des réglages précis pour garantir une répartition uniforme et une adhérence optimale des revêtements, ce que ces cabines permettent grâce à des systèmes de pulvérisation ajustables et des options de contrôle fin des paramètres.
Dans les applications artistiques et artisanales, ces cabines favorisent la créativité tout en offrant une protection essentielle contre les émanations et les particules en suspension. Les artistes qui travaillent sur des sculptures, des toiles ou des objets en trois dimensions peuvent bénéficier d’un environnement contrôlé qui leur permet de se concentrer sur les détails de leurs projets sans craindre pour leur santé ou la propreté de leur atelier. Les cabines peuvent être équipées de supports modulaires et réglables pour accueillir des objets de formes et de tailles variées, ce qui élargit leur champ d’utilisation.
Leur rôle dans les processus de réparation est également crucial. Dans des secteurs comme l’automobile ou l’électronique, les petites cabines de pulvérisation permettent d’effectuer des réparations ciblées sans nécessiter d’installations de grande envergure. Par exemple, pour réparer des rayures sur une carrosserie ou appliquer une nouvelle couche de protection sur des composants électroniques, elles offrent une solution rapide, propre et efficace. Cela en fait un outil essentiel pour les ateliers spécialisés dans les réparations, qui doivent souvent travailler sur des pièces uniques ou en série limitée.
Un autre domaine où ces cabines se révèlent indispensables est celui des laboratoires de test de qualité. Lorsqu’il s’agit d’évaluer la résistance ou les propriétés esthétiques de différents revêtements, les petites cabines permettent de créer des échantillons sous des conditions contrôlées. Cela garantit une analyse précise et répétable des performances des produits, un aspect clé pour les fabricants qui cherchent à innover ou à améliorer leurs offres. La possibilité de tester rapidement différentes formulations dans une cabine dédiée réduit également les coûts et les délais associés au développement de nouveaux produits.
La mobilité des petites cabines est un autre avantage important. Certaines sont conçues pour être facilement transportables, permettant ainsi leur utilisation sur des sites temporaires ou dans des contextes où la flexibilité est essentielle. Par exemple, elles peuvent être déployées sur des chantiers de construction pour des finitions directement sur place, évitant ainsi les coûts et les délais liés au transport des pièces à un atelier. Cette portabilité est également appréciée lors de démonstrations ou de foires commerciales, où les fabricants et les prestataires peuvent montrer leur savoir-faire dans un environnement pratique et contrôlé.
Les innovations dans le domaine de la filtration et de la gestion des flux d’air ont également contribué à améliorer la performance des petites cabines de pulvérisation. Les nouveaux systèmes de filtration multicouches capturent de manière encore plus efficace les particules et les solvants, tout en permettant une recirculation de l’air purifié à l’intérieur de la cabine. Ces technologies non seulement réduisent les émissions environnementales, mais elles prolongent également la durée de vie des filtres et diminuent les besoins en maintenance. Cela se traduit par des économies pour les utilisateurs et un impact environnemental moindre.
Enfin, les petites cabines de pulvérisation se positionnent comme un choix stratégique pour les entreprises cherchant à adopter des pratiques de production respectueuses de l’environnement. En limitant le gaspillage de matériaux grâce à des systèmes de récupération de poudre ou en optimisant l’application des peintures pour réduire les excédents, ces cabines participent activement à la transition vers des processus plus durables. Elles répondent ainsi aux attentes croissantes des clients et des régulateurs en matière de responsabilité écologique.
En conclusion, les petites cabines de pulvérisation ne se contentent pas d’offrir une solution technique pour l’application de revêtements. Elles incarnent une approche polyvalente, durable et accessible pour les professionnels et les particuliers à la recherche de performances élevées dans un format compact. Que ce soit pour des projets artistiques, des réparations, des tests de laboratoire ou des petites productions, elles continuent de se démarquer par leur capacité à répondre à des besoins variés tout en s’adaptant aux défis technologiques et environnementaux de notre époque.
Cabine de Poudre Pulvérisation
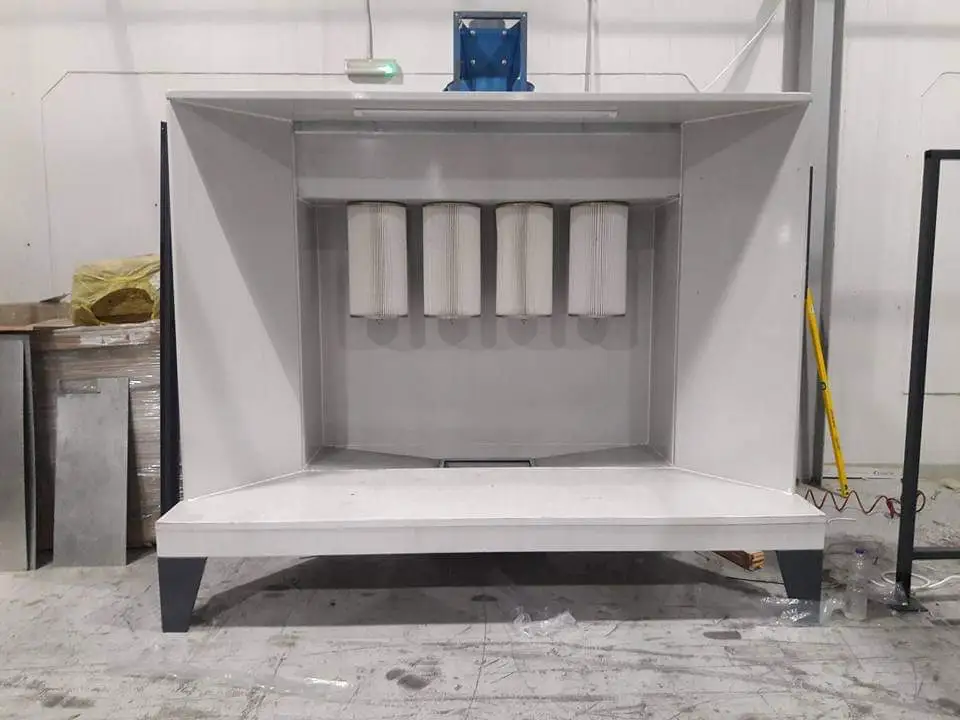
La cabine de poudre pulvérisation est un équipement clé dans le processus de thermolaquage, offrant un environnement contrôlé pour l’application uniforme de la peinture en poudre sur des pièces métalliques ou autres matériaux conducteurs. Elle joue un rôle central dans l’industrie du revêtement, garantissant une efficacité accrue, une qualité optimale et un respect des normes environnementales. Ce type de cabine est conçu pour capturer les particules de poudre excédentaires tout en protégeant les opérateurs et en minimisant les pertes de matériau.
Les cabines de poudre pulvérisation sont souvent fabriquées en acier ou en matériaux composites résistants à la corrosion, garantissant une durabilité à long terme. Leur conception modulaire permet de s’adapter à différents volumes de production et à des pièces de tailles variées, des composants industriels massifs aux objets plus petits et détaillés. Ces cabines sont équipées de systèmes de ventilation et de filtration avancés qui maintiennent un flux d’air constant, éliminant les particules en suspension pour éviter toute contamination et assurer une finition parfaite.
L’un des aspects les plus appréciés des cabines de poudre pulvérisation est leur capacité à réduire le gaspillage. Grâce à des systèmes de récupération efficaces, les particules de poudre excédentaires sont capturées et réutilisées, ce qui diminue considérablement les coûts de production. Ces cabines sont souvent équipées de filtres haute performance ou de cyclones qui séparent les particules de poudre de l’air, permettant ainsi une récupération optimale. Cela contribue également à maintenir un environnement de travail propre et à respecter les réglementations environnementales.
L’application de la peinture en poudre dans ces cabines repose sur des pistolets électrostatiques qui chargent la poudre avec une charge électrique. Cette charge permet à la poudre d’adhérer fermement à la surface conductrice de la pièce, assurant une couverture uniforme même sur des formes complexes ou des zones difficiles d’accès. Les cabines sont conçues pour maximiser cette efficacité, en optimisant le flux d’air et en réduisant les perturbations qui pourraient affecter la répartition de la poudre.
Les cabines de poudre pulvérisation modernes intègrent souvent des technologies numériques pour améliorer leur performance. Les systèmes de contrôle permettent de régler avec précision les paramètres tels que le débit d’air, la pression de pulvérisation et les cycles de nettoyage automatique. Ces fonctionnalités simplifient l’utilisation de la cabine, réduisent les erreurs humaines et garantissent une répétabilité élevée, ce qui est essentiel pour les productions en série. De plus, certaines cabines sont équipées de systèmes de surveillance en temps réel qui alertent les opérateurs en cas de problème, minimisant ainsi les temps d’arrêt.
Un autre avantage notable de ces cabines est leur polyvalence. Elles peuvent être utilisées pour une large gamme d’applications, des revêtements industriels robustes pour les équipements lourds aux finitions décoratives sur des objets du quotidien comme les meubles ou les accessoires de maison. Leur flexibilité permet également de changer rapidement de couleur ou de type de poudre, ce qui est idéal pour les productions personnalisées ou les petites séries.
En termes de sécurité, les cabines de poudre pulvérisation sont conçues pour minimiser les risques liés à l’accumulation de particules inflammables. Les systèmes de ventilation empêchent la formation de poches de poudre dans l’air, réduisant ainsi les risques d’incendie ou d’explosion. Les matériaux utilisés pour leur construction sont souvent ignifuges, et des capteurs intégrés surveillent en permanence les conditions internes pour détecter tout problème potentiel.
L’entretien des cabines de poudre pulvérisation est également relativement simple. Les surfaces internes lisses et les systèmes de nettoyage automatique facilitent l’élimination des résidus de poudre, réduisant ainsi le temps et les efforts nécessaires pour préparer la cabine pour une nouvelle opération. De plus, les filtres et les autres composants critiques sont facilement accessibles pour un remplacement rapide, minimisant les interruptions dans la production.
Pour les entreprises cherchant à intégrer ces cabines dans leurs lignes de production, leur conception modulaire permet une installation rapide et une compatibilité avec des équipements connexes tels que les fours de polymérisation ou les convoyeurs automatisés. Cela simplifie l’intégration dans des systèmes existants tout en permettant des mises à niveau futures en fonction des besoins croissants de production.
Dans le contexte de la durabilité, les cabines de poudre pulvérisation s’alignent parfaitement avec les objectifs environnementaux modernes. Contrairement aux peintures liquides traditionnelles, les poudres ne contiennent pas de solvants, réduisant ainsi les émissions de composés organiques volatils (COV). Cette caractéristique, combinée à la récupération efficace de la poudre excédentaire, fait de ces cabines un choix écologique pour les industries cherchant à minimiser leur empreinte carbone.
En conclusion, la cabine de poudre pulvérisation est un équipement essentiel pour quiconque cherche à obtenir des revêtements de haute qualité avec une efficacité maximale. Grâce à leur conception innovante, leurs systèmes avancés de récupération de poudre et leur adaptabilité à divers contextes industriels, ces cabines offrent une solution fiable et économique pour les besoins de revêtement modernes. Que ce soit pour des productions à grande échelle ou des applications spécialisées, elles représentent un investissement judicieux pour toute entreprise souhaitant optimiser ses processus de finition.
Les cabines de poudre pulvérisation continuent d’évoluer pour répondre aux exigences croissantes des industries modernes en termes de performance, de productivité et de durabilité. Les fabricants rivalisent d’ingéniosité pour introduire de nouvelles fonctionnalités qui simplifient encore davantage les opérations tout en garantissant une qualité irréprochable des revêtements appliqués. Ces avancées sont particulièrement perceptibles dans l’intégration de technologies intelligentes et dans l’optimisation des processus de changement de couleur.
L’un des défis majeurs dans l’utilisation des cabines de poudre est le passage d’une couleur de poudre à une autre, qui peut être une opération chronophage si elle n’est pas bien gérée. Les modèles récents intègrent des systèmes de nettoyage automatisé qui réduisent considérablement le temps nécessaire pour éliminer la poudre résiduelle de l’intérieur de la cabine. Ces systèmes utilisent des jets d’air comprimé ou des dispositifs à vide pour atteindre même les zones les plus difficiles d’accès, garantissant un changement rapide et propre. Cela permet aux entreprises de passer facilement d’une commande à l’autre sans compromettre la productivité.
L’automatisation des cabines de poudre pulvérisation ne se limite pas au nettoyage. Les systèmes de commande intelligents permettent de surveiller et d’ajuster en temps réel des paramètres tels que la vitesse du flux d’air, l’intensité de la charge électrostatique et la pression d’application de la poudre. Ces ajustements dynamiques assurent une application uniforme sur des surfaces complexes, même lorsque les conditions environnementales ou les spécificités des pièces changent. De plus, les données collectées par ces systèmes peuvent être analysées pour identifier des opportunités d’amélioration et optimiser l’utilisation des ressources.
En matière de durabilité, les cabines de poudre pulvérisation modernes intègrent des solutions encore plus respectueuses de l’environnement. Par exemple, les systèmes de filtration évolués utilisent des matériaux recyclables et ont une durée de vie prolongée, réduisant ainsi la fréquence de leur remplacement. Par ailleurs, les fabricants développent des poudres à base de matériaux renouvelables ou recyclés, qui fonctionnent parfaitement avec ces cabines, offrant ainsi une solution globale respectueuse de l’écosystème.
La polyvalence reste un point fort des cabines de poudre pulvérisation. Alors que certaines industries, comme l’automobile ou l’aéronautique, exigent des finitions extrêmement robustes et précises, d’autres, comme la décoration intérieure ou les biens de consommation, privilégient des options esthétiques et personnalisées. Les cabines modernes répondent à ces besoins variés en proposant des configurations sur mesure, telles que des systèmes de convoyeurs ajustables pour traiter des pièces de tailles et de formes variées. Elles peuvent aussi être combinées avec des équipements périphériques, comme des robots de pulvérisation, pour augmenter encore leur flexibilité.
Dans les ateliers à faible volume ou spécialisés, les cabines compactes restent une solution de choix. Elles offrent une qualité similaire à celle des grands systèmes industriels tout en occupant un espace réduit, ce qui les rend idéales pour les entreprises émergentes ou les projets à échelle réduite. Ces modèles peuvent être installés rapidement et nécessitent peu d’investissement initial, permettant aux petites entreprises de profiter des avantages de la pulvérisation de poudre sans les contraintes associées aux installations plus complexes.
L’entretien des cabines reste un aspect primordial pour garantir leur performance à long terme. Les utilisateurs sont encouragés à effectuer des vérifications régulières des systèmes de filtration, des buses des pistolets de pulvérisation et des surfaces internes de la cabine. Les fabricants proposent souvent des contrats de maintenance ou des kits spécifiques pour simplifier ces tâches. De plus, la disponibilité de pièces détachées standardisées facilite les réparations, réduisant ainsi les temps d’arrêt et les coûts associés.
Enfin, l’impact esthétique et fonctionnel des cabines de poudre pulvérisation sur les produits finis ne peut être sous-estimé. En permettant l’application de couches uniformes et durables, elles assurent une protection optimale contre les éléments, tels que la corrosion, tout en offrant une large gamme de finitions visuelles. Cela est particulièrement important dans des secteurs où l’apparence et la qualité perçue des produits influencent directement les décisions des consommateurs.
En conclusion, les cabines de poudre pulvérisation représentent une technologie incontournable pour toute industrie nécessitant des revêtements de qualité supérieure. Grâce à des innovations continues, elles offrent des performances accrues, une adaptabilité remarquable et un impact environnemental réduit. Ces caractéristiques en font un pilier essentiel dans les processus de finition modernes, combinant efficacité, durabilité et esthétisme pour répondre aux exigences des marchés contemporains.
Cabine de Peinture Poudre
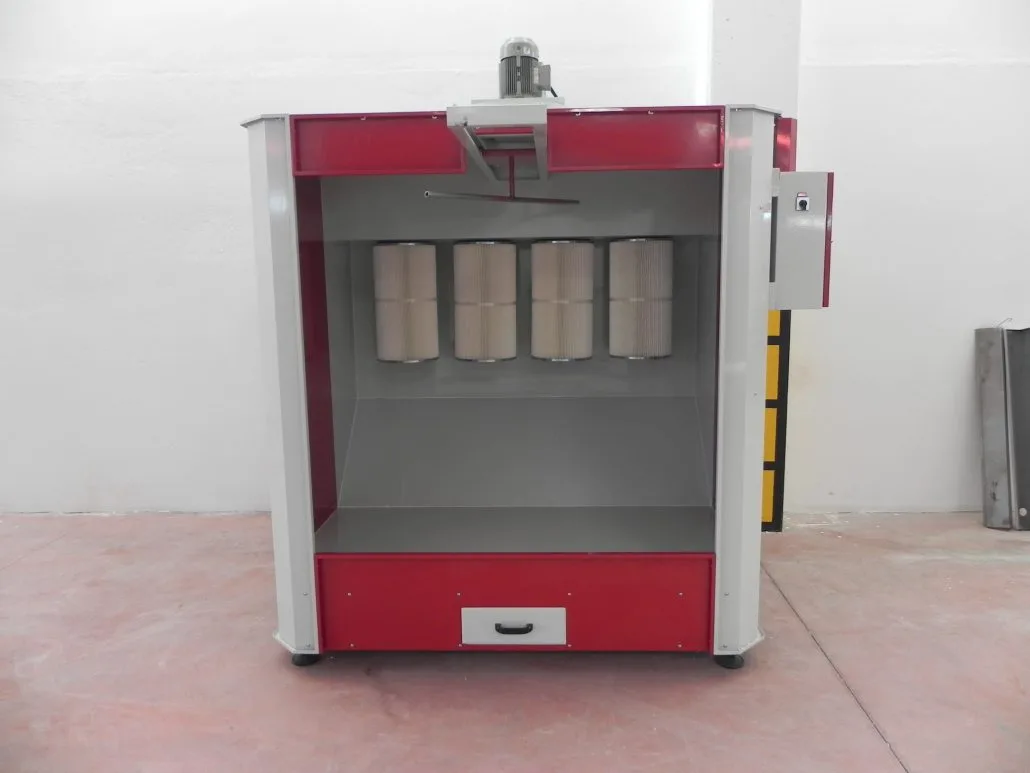
La cabine de peinture poudre est un élément central dans le processus de finition des surfaces, notamment dans le cadre du thermolaquage. Elle constitue un environnement spécialement conçu pour l’application uniforme de peintures en poudre sur divers substrats, principalement des métaux, mais aussi d’autres matériaux conducteurs. Grâce à sa conception avancée et à son intégration dans des systèmes industriels ou artisanaux, elle garantit une qualité de finition exceptionnelle, une efficacité optimale et une conformité avec les normes environnementales les plus strictes.
Une cabine de peinture poudre se distingue par sa structure soigneusement étudiée, souvent réalisée en acier ou en matériaux composites, pour assurer sa durabilité et sa résistance aux conditions exigeantes de l’application de peinture. Elle est équipée de parois lisses qui minimisent l’adhérence de la poudre, facilitant ainsi le nettoyage et le changement de couleurs. La conception ergonomique de ces cabines leur permet de s’adapter à une large gamme de pièces, qu’elles soient grandes, petites, plates ou complexes.
Le principe de fonctionnement repose sur l’utilisation de pistolets électrostatiques qui chargent les particules de peinture en poudre. Ces particules, grâce à leur charge, adhèrent uniformément à la surface de la pièce, garantissant une couverture homogène, même sur des géométries complexes ou des zones difficilement accessibles. La cabine est dotée de systèmes de ventilation sophistiqués qui contrôlent le flux d’air pour éviter la dispersion des particules et assurer un environnement propre et sûr pour les opérateurs.
Un des avantages clés de la cabine de peinture poudre est sa capacité à récupérer la poudre excédentaire. Les systèmes de récupération, tels que les cyclones ou les filtres haute efficacité, capturent les particules non déposées sur les pièces pour les réutiliser. Ce procédé réduit considérablement le gaspillage de matériau, rendant le processus à la fois économique et écologique. Les cabines modernes atteignent des taux de récupération très élevés, maximisant ainsi l’utilisation de la peinture en poudre.
Les cabines de peinture poudre sont également conçues pour répondre aux besoins variés des industries. Dans les grandes productions, elles peuvent être intégrées à des lignes automatisées où des robots appliquent la peinture avec une précision inégalée. Dans les ateliers plus petits, elles sont utilisées en mode manuel, offrant une flexibilité pour les séries limitées ou les pièces uniques. Cette adaptabilité en fait un équipement essentiel pour des secteurs aussi divers que l’automobile, la construction, l’électroménager, ou encore l’artisanat et le design.
En termes d’écologie, les cabines de peinture poudre se distinguent par leur faible impact environnemental. Contrairement aux peintures liquides, les poudres ne contiennent pas de solvants, ce qui élimine les émissions de composés organiques volatils (COV). Cette caractéristique, combinée à la récupération des excédents de poudre, contribue à réduire l’empreinte carbone des entreprises tout en respectant les normes environnementales de plus en plus strictes.
La sécurité est un autre aspect crucial dans la conception des cabines de peinture poudre. Les systèmes de ventilation et de filtration empêchent l’accumulation de particules en suspension, réduisant ainsi les risques d’incendie ou d’explosion. Les cabines sont souvent équipées de capteurs qui surveillent en temps réel les conditions internes, alertant les opérateurs en cas de problème potentiel. Ces dispositifs garantissent un environnement de travail sûr pour les utilisateurs tout en maintenant une performance optimale.
L’entretien des cabines de peinture poudre est facilité par leur conception modulaire. Les filtres, les buses des pistolets et les systèmes de récupération sont facilement accessibles pour le nettoyage ou le remplacement, minimisant ainsi les interruptions de production. Les fabricants proposent souvent des kits d’entretien et des contrats de maintenance pour assurer la longévité de l’équipement et sa conformité aux normes en vigueur.
Les innovations récentes ont permis d’améliorer encore les performances des cabines. Des systèmes de contrôle numérique permettent de régler et de surveiller avec précision les paramètres d’application, comme la vitesse de pulvérisation, l’intensité de la charge électrostatique ou le flux d’air. Ces ajustements garantissent une qualité constante, même dans des environnements de production exigeants ou lors de l’utilisation de différents types de poudre.
Enfin, les cabines de peinture poudre jouent un rôle essentiel dans l’obtention de finitions de haute qualité. Elles permettent d’appliquer des revêtements uniformes, esthétiquement attrayants et résistants à l’usure, à la corrosion et aux conditions climatiques. Ces propriétés en font un choix privilégié pour les fabricants cherchant à valoriser leurs produits et à répondre aux attentes croissantes des clients en matière de durabilité et d’apparence.
En conclusion, la cabine de peinture poudre est un équipement indispensable pour les industries et les ateliers cherchant à allier efficacité, économie et respect de l’environnement. Son rôle central dans le processus de thermolaquage, sa capacité d’adaptation à divers besoins et ses innovations constantes en font une solution de choix pour les applications de revêtement modernes. Que ce soit pour des productions à grande échelle ou des projets plus spécifiques, elle offre une performance inégalée et une qualité irréprochable.
Les cabines de peinture poudre continuent d’évoluer grâce à l’intégration de technologies avancées et à des améliorations constantes en matière d’efficacité, de sécurité et de flexibilité. Ces innovations répondent aux besoins croissants des industries modernes et permettent de relever les défis liés à la qualité des revêtements, à la réduction des coûts et à la durabilité environnementale.
L’une des tendances notables dans les cabines de peinture poudre modernes est l’automatisation accrue. Les cabines sont désormais équipées de systèmes de contrôle intelligents qui permettent une gestion précise et personnalisée des paramètres d’application. Ces systèmes peuvent adapter automatiquement les réglages en fonction de la forme, de la taille et des matériaux des pièces à peindre, garantissant ainsi une application uniforme et efficace. De plus, ces technologies permettent de surveiller en temps réel les performances de la cabine, offrant des données précieuses pour optimiser le processus et détecter rapidement les éventuelles anomalies.
Les changements rapides de couleur, qui étaient autrefois une opération complexe et chronophage, ont été considérablement simplifiés grâce aux cabines modernes. Des systèmes de nettoyage automatisés utilisent des flux d’air comprimé ou des technologies innovantes pour éliminer les résidus de poudre de manière rapide et complète. Cela réduit les temps d’arrêt entre deux productions, permettant aux entreprises d’être plus réactives face à des commandes variées ou à des séries limitées. Ces systèmes réduisent également le risque de contamination croisée entre les couleurs, garantissant ainsi une qualité irréprochable pour chaque application.
En termes de conception, les cabines sont devenues plus compactes et modulaires, ce qui facilite leur installation et leur intégration dans divers environnements de production. Cette modularité permet également une mise à jour ou une extension facile pour répondre à une augmentation de la demande ou à des besoins spécifiques. Par exemple, une cabine manuelle peut être transformée en cabine semi-automatique ou entièrement automatisée avec l’ajout de convoyeurs ou de robots de pulvérisation, offrant ainsi une flexibilité maximale pour l’utilisateur.
Les systèmes de récupération de poudre, qui sont essentiels pour minimiser le gaspillage et maximiser l’efficacité, ont également été perfectionnés. Les technologies de filtration avancées, comme les filtres HEPA ou les séparateurs cycloniques, permettent de capturer presque toutes les particules excédentaires et de les réintroduire dans le processus. Ces améliorations réduisent non seulement les coûts de production, mais elles renforcent également l’engagement des entreprises envers des pratiques industrielles durables.
Dans les grandes installations, les cabines de peinture poudre peuvent être intégrées à des lignes de production complètes, comprenant des systèmes de prétraitement, des fours de polymérisation et des convoyeurs automatisés. Ces lignes entièrement synchronisées permettent une production continue et rationalisée, minimisant les temps d’arrêt et maximisant la productivité. Cette intégration garantit également une meilleure traçabilité des produits et une gestion optimisée des ressources.
Pour les petites entreprises ou les ateliers spécialisés, les cabines de peinture poudre offrent une opportunité de rivaliser avec les grandes installations grâce à leur accessibilité et à leur efficacité. Les modèles compacts, faciles à installer et à entretenir, permettent d’obtenir des résultats professionnels sans nécessiter des investissements lourds. Cela ouvre la voie à une adoption plus large de la technologie de thermolaquage, même pour des productions à petite échelle ou personnalisées.
L’impact esthétique et fonctionnel des cabines de peinture poudre sur les produits finis reste un point fort indéniable. Elles permettent d’appliquer des revêtements aux finitions variées, allant des surfaces brillantes et lisses aux textures plus rugueuses ou mates, en fonction des préférences ou des exigences du client. En plus de leur attrait visuel, ces revêtements offrent une protection supérieure contre la corrosion, les rayures, et les conditions climatiques extrêmes, augmentant ainsi la durabilité des produits.
Enfin, la recherche et le développement dans ce domaine continuent de repousser les limites des performances des cabines de peinture poudre. Les nouvelles générations de poudres, plus légères et plus écologiques, sont spécialement conçues pour fonctionner avec ces cabines, offrant des finitions encore plus résistantes et des couleurs plus éclatantes. Cette synergie entre matériaux innovants et équipements avancés assure que les cabines de peinture poudre resteront à la pointe des technologies de revêtement pour les décennies à venir.
En résumé, la cabine de peinture poudre est un équipement indispensable pour les industries cherchant à combiner qualité, durabilité et rentabilité. Avec ses nombreuses fonctionnalités, son adaptabilité à divers besoins et ses performances accrues, elle représente un investissement stratégique pour optimiser les processus de finition et répondre aux exigences croissantes des marchés modernes. Que ce soit pour des productions à grande échelle ou des projets plus spécifiques, la cabine de peinture poudre continue d’être un pilier essentiel de l’industrie du revêtement.
Dépannage Brûleur Four Industriels
Le dépannage des brûleurs de fours industriels est une tâche essentielle pour maintenir le bon fonctionnement des équipements de chauffage utilisés dans les processus industriels. Les brûleurs sont des composants critiques qui contrôlent la génération de chaleur dans les fours à gaz, et toute défaillance peut entraîner des interruptions de production coûteuses.
Les signes de dysfonctionnement d’un brûleur incluent des températures irrégulières, des bruits inhabituels, ou une combustion inefficace. Une inspection régulière et un entretien préventif peuvent aider à identifier ces problèmes avant qu’ils ne provoquent une panne majeure.
Le dépannage des brûleurs peut inclure le nettoyage des composants, le réglage des systèmes de contrôle de la flamme, ou le remplacement des pièces usées. Les entreprises doivent également s’assurer d’avoir des pièces de rechange disponibles pour minimiser les temps d’arrêt en cas de panne. Une maintenance régulière des brûleurs est essentielle pour garantir une production continue et efficace.
Four Haute Température Industriel
Un four haute température industriel est un équipement spécialisé conçu pour des applications nécessitant des températures extrêmement élevées, souvent supérieures à 1000 degrés Celsius. Ces fours sont utilisés dans des processus industriels tels que la métallurgie, la céramique, et le traitement thermique des matériaux, où la résistance à la chaleur est cruciale.
Les fours haute température peuvent être alimentés au gaz, à l’électricité, ou par d’autres sources d’énergie, selon les besoins spécifiques de l’application. Ils sont équipés de systèmes de contrôle avancés pour réguler précisément la température et garantir des conditions de traitement constantes.
Ces fours sont essentiels dans des industries où les matériaux doivent subir des traitements thermiques intenses pour atteindre les propriétés mécaniques ou chimiques souhaitées. La maintenance régulière de ces fours, y compris l’inspection des éléments chauffants et des systèmes de contrôle, est essentielle pour assurer leur bon fonctionnement et prolonger leur durée de vie.
Robot Peinture Industriel
Les robots de peinture industriels sont des systèmes automatisés utilisés pour appliquer de la peinture sur des surfaces dans des processus de production à grande échelle. Ces robots sont programmés pour pulvériser de la peinture de manière précise et uniforme, réduisant ainsi les erreurs humaines et augmentant l’efficacité.
Les robots de peinture sont largement utilisés dans l’industrie automobile, l’électronique, et la fabrication de biens de consommation, où la qualité de la finition est essentielle. Ils permettent une application rapide et cohérente de la peinture, même sur des surfaces complexes ou difficiles d’accès.
L’utilisation de robots de peinture présente plusieurs avantages, notamment une augmentation de la productivité, une réduction des coûts de main-d’œuvre, et une amélioration de la qualité des produits finis. Les robots peuvent être programmés pour appliquer différentes couches de peinture, ajuster la pression de pulvérisation, et effectuer des tâches de retouche, ce qui en fait un outil précieux dans les lignes de production modernes.
Séchage Industriel
Le séchage industriel est un processus crucial dans de nombreuses applications de production, où l’élimination de l’humidité des matériaux ou des produits est nécessaire pour garantir la qualité et la durabilité du produit fini. Le séchage est couramment utilisé après l’application de peintures, de revêtements, ou de traitements chimiques pour durcir et stabiliser les surfaces.
Les systèmes de séchage industriel varient en fonction des matériaux à traiter et des spécifications du processus. Ils peuvent inclure des tunnels de séchage, des chambres de séchage statiques, ou des systèmes de séchage à air chaud. Le contrôle précis de la température et de l’humidité est essentiel pour éviter les défauts tels que les fissures, les cloques, ou les variations de couleur.
Les industries qui dépendent du séchage industriel incluent l’automobile, l’aéronautique, et la fabrication de biens de consommation durables. Un séchage bien contrôlé peut améliorer la qualité du produit fini, prolonger la durée de vie des matériaux, et augmenter l’efficacité globale de la production.
Revêtement en Poudre
Le revêtement en poudre est une technique de finition de surface largement utilisée pour protéger et décorer les objets métalliques. Contrairement aux peintures liquides, le revêtement en poudre utilise une poudre sèche appliquée sur la surface à l’aide d’un pistolet électrostatique. Une fois appliquée, la pièce est chauffée dans un four, où la poudre fond et se polymérise pour former une couche uniforme et durable.
Les avantages du revêtement en poudre incluent une meilleure résistance à l’abrasion, aux produits chimiques, et aux intempéries, ainsi qu’une réduction des émissions de composés organiques volatils (COV). De plus, la poudre excédentaire peut être récupérée et réutilisée, ce qui en fait un choix économique et écologique.
Le revêtement en poudre est couramment utilisé dans des industries telles que l’automobile, l’électroménager, et la fabrication de meubles métalliques. Il permet d’obtenir des finitions de haute qualité avec une large gamme de couleurs et de textures, adaptées aux besoins spécifiques des clients.
Les Types des Fours Industriels
Il existe plusieurs types de fours industriels, chacun conçu pour répondre à des besoins spécifiques en matière de traitement thermique. Ces fours sont utilisés dans diverses applications, telles que la cuisson, le séchage, la polymérisation, et le traitement thermique des matériaux.
- Fours de polymérisation : Utilisés pour durcir les revêtements en poudre ou les résines appliquées sur des surfaces métalliques, ces fours maintiennent des températures précises pour garantir une finition uniforme.
- Fours de séchage : Ces fours sont utilisés pour éliminer l’humidité des matériaux ou des produits après l’application de revêtements ou de traitements chimiques.
- Fours à haute température : Conçus pour des applications nécessitant des températures extrêmes, ces fours sont utilisés dans la métallurgie, la céramique, et d’autres industries exigeant des conditions thermiques intenses.
- Fours à gaz : Populaires pour leur efficacité énergétique, les fours à gaz sont souvent utilisés dans les grandes installations industrielles.
- Fours électriques : Ces fours offrent un contrôle précis de la température et sont souvent utilisés pour des applications nécessitant une régulation thermique stricte.
Le choix du type de four dépend des exigences spécifiques de l’application, telles que la température de traitement, la capacité de production, et les considérations environnementales. Les industries qui dépendent des fours industriels incluent l’automobile, l’aéronautique, et la fabrication de biens de consommation durables.
Fours de Revenu Tunnel
Les fours de revenu tunnel sont des équipements utilisés principalement dans les grandes installations industrielles pour le traitement thermique continu des pièces. Ces fours permettent de traiter de grandes quantités de pièces en un temps réduit, tout en assurant une régularité dans le traitement thermique.
Le fonctionnement des fours de revenu tunnel implique le passage des pièces à travers une série de zones à différentes températures, ce qui permet de réaliser un traitement thermique précis et contrôlé. Ces fours sont couramment utilisés dans l’industrie automobile, l’aéronautique, et la métallurgie, où la rapidité et la cohérence du traitement sont essentielles.
Les avantages des fours de revenu tunnel incluent une production en continu, une réduction des temps d’arrêt, et une amélioration de l’efficacité globale du processus. Ces équipements sont essentiels pour les entreprises cherchant à maximiser leur capacité de production tout en maintenant des normes de qualité élevées.
Four Pyrolyse Industriel
Le four pyrolyse industriel est un équipement utilisé pour nettoyer les pièces en éliminant les résidus organiques par combustion à haute température. Ce procédé, appelé pyrolyse, décompose les matériaux organiques en les chauffant à des températures élevées en l’absence d’oxygène.
Les fours de pyrolyse industriels sont couramment utilisés dans des industries où la propreté des pièces est cruciale pour la qualité du produit fini, telles que la fabrication de moules, l’industrie chimique, et le recyclage des métaux. Ces fours permettent d’éliminer les résidus de peinture, de plastique, ou de caoutchouc, laissant les pièces métalliques propres et prêtes pour le traitement ultérieur.
Les avantages des fours de pyrolyse incluent une réduction des déchets, une amélioration de la qualité du nettoyage, et une réduction des coûts de maintenance des équipements. La sécurité et le contrôle précis de la température sont essentiels pour garantir un fonctionnement sûr et efficace de ces fours.
Four de Thermolaquage
Le four de thermolaquage est un équipement essentiel dans le processus de revêtement en poudre, utilisé pour polymériser la peinture en poudre appliquée sur des surfaces métalliques. Ce four chauffe les objets à des températures spécifiques pour faire fondre la poudre et former un revêtement uniforme et durable.
Les fours de thermolaquage sont disponibles en différentes tailles et configurations, y compris les modèles à gaz et électriques, adaptés aux besoins spécifiques de chaque application. Ils sont conçus pour offrir une distribution uniforme de la chaleur, essentielle pour garantir une qualité de finition élevée et éviter les défauts tels que les cloques ou les fissures.
Ces fours sont couramment utilisés dans des industries telles que l’automobile, l’électroménager, et la fabrication de meubles métalliques. Ils sont également appréciés pour leur efficacité énergétique et leur capacité à traiter de grandes quantités de pièces en une seule fois, ce qui en fait un choix idéal pour les grandes lignes de production.
Filtres de Cabine de Peinture
Les filtres de cabine de peinture sont des composants critiques dans les cabines de peinture, utilisés pour capturer les particules de peinture excédentaires et maintenir un environnement propre et sûr à l’intérieur de la cabine. Ces filtres jouent un rôle crucial dans la prévention des contaminations croisées et dans la garantie d’une finition de haute qualité.
Il existe différents types de filtres de cabine de peinture, y compris les filtres à air primaire, les filtres plissés, et les filtres HEPA, chacun étant conçu pour capturer des particules de tailles spécifiques. La maintenance régulière et le remplacement des filtres sont essentiels pour assurer leur efficacité et prolonger la durée de vie de la cabine de peinture.
Les industries qui utilisent des cabines de peinture, telles que l’automobile, l’aéronautique, et la fabrication de meubles, dépendent de filtres de haute qualité pour garantir que leurs produits finis sont exempts de défauts et répondent aux normes de qualité les plus élevées.
Retouche Peinture Thermolaquée
La retouche de peinture thermolaquée est une opération réalisée pour corriger les défauts ou imperfections sur les pièces revêtues de peinture thermolaquée. Ces retouches peuvent être nécessaires pour réparer les éclats, les rayures, ou les zones où la peinture n’a pas adhéré correctement.
Les retouches de peinture thermolaquée sont effectuées en appliquant une petite quantité de poudre sur la zone endommagée, suivie d’une nouvelle cuisson pour polymériser la poudre et intégrer la retouche au revêtement existant. Cette opération nécessite une précision et une expertise pour garantir que la retouche est invisible et que la qualité du revêtement est maintenue.
Les industries qui utilisent la peinture thermolaquée, telles que l’automobile, l’électroménager, et la fabrication de meubles métalliques, dépendent de ces retouches pour assurer que leurs produits finis répondent aux normes de qualité les plus élevées. Une retouche bien réalisée prolonge la durée de vie du revêtement et améliore l’esthétique du produit final.
Pistolet Peinture Epoxy Poudre
Le pistolet de peinture epoxy poudre est un outil essentiel dans l’application de revêtement en poudre, spécifiquement conçu pour pulvériser de la poudre époxy sur des surfaces métalliques. Ce pistolet utilise la technologie électrostatique pour assurer une adhésion uniforme de la poudre, même sur des surfaces complexes ou irrégulières.
Le pistolet charge électriquement les particules de poudre, qui sont ensuite attirées par la surface opposée, créant ainsi une couverture uniforme. Une fois la poudre appliquée, la pièce est chauffée dans un four pour faire fondre et polymériser la poudre, formant un revêtement solide et durable.
Les pistolets de peinture epoxy poudre sont largement utilisés dans l’industrie automobile, l’électronique, et la production de biens de consommation durables, où la qualité et la cohérence du revêtement sont des critères clés. Ils permettent une application précise, réduisant ainsi les pertes de matière et améliorant l’efficacité du processus de peinture.
Peinture Poudre Electrostatique
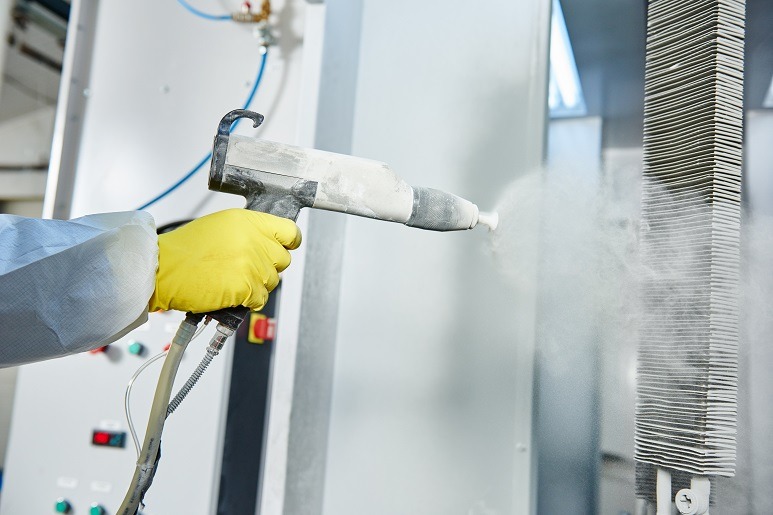
La peinture poudre électrostatique est une technique avancée d’application de revêtement en poudre qui repose sur l’utilisation de forces électrostatiques pour assurer une adhésion uniforme de la poudre sur une surface, généralement métallique. Cette méthode est devenue incontournable dans l’industrie du revêtement, en particulier pour les objets nécessitant une finition durable, esthétique et résistante aux conditions environnementales difficiles.
1. Principe de Fonctionnement
Le processus de peinture poudre électrostatique commence par la préparation de la surface à peindre. Il est essentiel que la surface soit propre, exempte de poussière, de graisse et d’autres contaminants pour garantir une bonne adhérence du revêtement. Une fois la surface prête, la peinture en poudre est appliquée à l’aide d’un pistolet électrostatique.
Le pistolet électrostatique fonctionne en chargeant électriquement les particules de poudre. Cette charge est généralement négative, tandis que la surface métallique à peindre est mise à la terre, ce qui la rend positive. Cette différence de potentiel électrostatique attire les particules de poudre vers la surface, assurant une application uniforme, même sur des formes complexes ou des recoins difficiles d’accès.
2. Polymérisation et Durcissement
Une fois la poudre appliquée, la pièce est placée dans un four de polymérisation, où elle est chauffée à des températures allant de 160 à 200 degrés Celsius. La chaleur fait fondre la poudre, qui se transforme en une couche liquide, puis la polymérisation commence. Ce processus chimique solidifie le revêtement, le rendant résistant et durable.
Le durcissement est une étape cruciale car il détermine les propriétés finales du revêtement, telles que sa résistance à la corrosion, à l’abrasion, aux produits chimiques, et aux UV. Un contrôle précis de la température et du temps de cuisson est nécessaire pour garantir une qualité de revêtement optimale.
3. Avantages de la Peinture Poudre Electrostatique
La peinture poudre électrostatique présente plusieurs avantages par rapport aux méthodes traditionnelles de peinture liquide :
- Efficacité de l’application : Grâce à la technologie électrostatique, la poudre adhère uniformément à la surface, réduisant ainsi les pertes de matière et assurant une couverture homogène. Les zones difficiles à atteindre, comme les coins et les bords, sont également bien couvertes.
- Respect de l’environnement : Contrairement aux peintures liquides, la peinture poudre ne contient pas de solvants, ce qui réduit considérablement les émissions de composés organiques volatils (COV). De plus, l’excédent de poudre peut être récupéré et réutilisé, minimisant ainsi les déchets.
- Durabilité : Les revêtements en poudre sont réputés pour leur résistance supérieure aux chocs, aux rayures, aux produits chimiques, et aux conditions météorologiques difficiles. Cela prolonge la durée de vie des pièces peintes et réduit les besoins en retouches ou en maintenance.
- Variété de finitions : La peinture poudre électrostatique permet de réaliser une large gamme de finitions, y compris les textures lisses, mates, brillantes, et même des effets métalliques. Cela offre une grande flexibilité aux concepteurs et aux fabricants pour répondre aux exigences esthétiques spécifiques.
4. Applications Industrielles
La peinture poudre électrostatique est largement utilisée dans de nombreuses industries en raison de ses nombreux avantages. Voici quelques exemples d’applications courantes :
- Automobile : Les châssis, les jantes, et d’autres composants automobiles sont souvent peints avec de la poudre électrostatique pour garantir une finition durable qui résiste aux conditions rigoureuses de la route.
- Électroménager : Les appareils tels que les réfrigérateurs, les lave-linge, et les fours bénéficient d’une couche de peinture poudre pour une finition esthétique et résistante aux produits de nettoyage et à l’humidité.
- Mobilier métallique : Les meubles en métal, qu’ils soient destinés à un usage intérieur ou extérieur, sont souvent revêtus de peinture poudre pour une protection contre la rouille et une apparence soignée.
- Équipements industriels : De nombreux équipements industriels, y compris les machines-outils et les structures métalliques, sont revêtus de peinture poudre pour les protéger contre l’usure et les conditions d’exploitation difficiles.
5. Conclusion
La peinture poudre électrostatique est une solution de revêtement moderne et efficace, offrant une combinaison inégalée de durabilité, de qualité de finition, et de respect de l’environnement. Grâce à ses nombreuses applications dans divers secteurs industriels, elle continue de gagner en popularité et reste une technologie clé pour les entreprises cherchant à améliorer la qualité et la longévité de leurs produits.
Système de Peinture
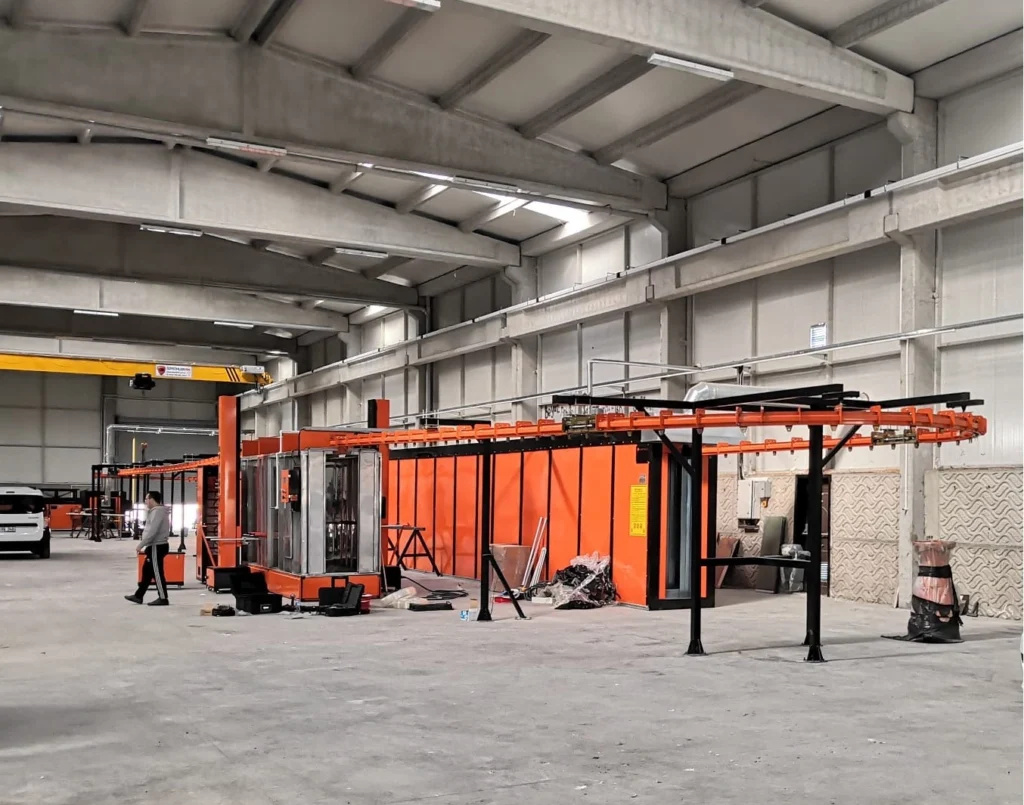
Un système de peinture est un ensemble de technologies, d’équipements, et de processus conçus pour appliquer un revêtement protecteur et/ou décoratif sur une surface, généralement métallique ou plastique. Ces systèmes sont essentiels dans de nombreuses industries, y compris l’automobile, l’aéronautique, l’électronique, et la fabrication de biens de consommation durables. Ils permettent non seulement d’améliorer l’esthétique des produits, mais aussi de les protéger contre la corrosion, l’usure, et les intempéries.
1. Composants d’un Système de Peinture
Un système de peinture complet est constitué de plusieurs composants qui fonctionnent ensemble pour assurer une application efficace et uniforme du revêtement. Voici les principaux éléments d’un système de peinture industriel :
- Cabine de peinture : La cabine de peinture est un espace clos où les objets sont placés pour recevoir le revêtement. Elle est conçue pour contrôler les conditions environnementales, telles que la température, l’humidité, et la ventilation, afin de garantir une application de peinture sans défaut. Les cabines sont équipées de systèmes de filtration pour capturer les particules de peinture excédentaires et maintenir un air propre.
- Pistolet de peinture : Les pistolets de peinture, qu’ils soient manuels ou automatiques, sont utilisés pour appliquer la peinture sur la surface de l’objet. Dans les systèmes modernes, les pistolets de peinture électrostatiques sont souvent utilisés pour améliorer l’efficacité de l’application et réduire les pertes de peinture.
- Four de polymérisation : Après l’application de la peinture, les objets sont souvent chauffés dans un four pour durcir et stabiliser le revêtement. Ce processus, appelé polymérisation, est crucial pour garantir la durabilité et la résistance du revêtement.
- Système de convoyage : Dans les installations de production à grande échelle, les objets à peindre sont transportés automatiquement d’une étape à l’autre du processus grâce à un système de convoyage. Ce système permet de rationaliser la production et d’augmenter la productivité.
- Unité de mélange et de dosage de peinture : Cette unité assure le mélange homogène des composants de la peinture (liquide ou poudre) avant son application. Elle peut être équipée de systèmes de contrôle pour ajuster la composition de la peinture en fonction des spécifications de l’application.
2. Types de Systèmes de Peinture
Les systèmes de peinture peuvent être classés en plusieurs catégories en fonction du type de peinture utilisée et du niveau d’automatisation :
- Systèmes de peinture manuels : Ces systèmes sont opérés par des techniciens qui appliquent la peinture à l’aide de pistolets manuels. Bien que ces systèmes soient plus flexibles et adaptés aux productions en petite série ou aux retouches, ils nécessitent une formation et une expertise pour garantir une application uniforme.
- Systèmes de peinture automatiques : Les systèmes automatiques utilisent des robots ou des pistolets montés sur des bras automatisés pour appliquer la peinture. Ils sont idéaux pour les productions en série, où la cohérence et la rapidité sont essentielles. Ces systèmes peuvent être programmés pour appliquer différentes couches de peinture, ajuster les paramètres de pulvérisation, et même effectuer des retouches si nécessaire.
- Systèmes de peinture électrostatiques : Utilisant la technologie électrostatique, ces systèmes chargent électriquement les particules de peinture pour qu’elles adhèrent mieux à la surface à peindre. Ce type de système est particulièrement efficace pour les surfaces complexes et réduit le gaspillage de peinture.
- Systèmes de peinture à base d’eau et à base de solvants : Les systèmes de peinture peuvent également être classés en fonction du type de peinture utilisé. Les peintures à base d’eau sont plus respectueuses de l’environnement car elles contiennent moins de COV (composés organiques volatils), tandis que les peintures à base de solvants sont souvent choisies pour leur durabilité supérieure.
3. Avantages d’un Système de Peinture Automatisé
Les systèmes de peinture automatisés offrent de nombreux avantages pour les entreprises industrielles, notamment :
- Cohérence et qualité : Les systèmes automatisés appliquent la peinture de manière uniforme et constante, ce qui réduit les risques de défauts tels que les coulures ou les zones non couvertes.
- Efficacité accrue : Grâce à l’automatisation, les temps de production sont réduits, ce qui permet de traiter un plus grand nombre de pièces en moins de temps. Cela est particulièrement avantageux pour les entreprises ayant des volumes de production élevés.
- Réduction des coûts : Bien que les systèmes de peinture automatisés nécessitent un investissement initial plus important, ils permettent de réduire les coûts à long terme en minimisant le gaspillage de peinture et les besoins en main-d’œuvre.
- Sécurité améliorée : L’automatisation réduit l’exposition des travailleurs aux produits chimiques potentiellement dangereux, améliorant ainsi la sécurité sur le lieu de travail.
4. Applications Industrielles des Systèmes de Peinture
Les systèmes de peinture sont utilisés dans une variété d’industries pour répondre à des besoins spécifiques :
- Industrie automobile : Dans ce secteur, les systèmes de peinture sont utilisés pour appliquer des revêtements durables et esthétiques sur les carrosseries, les jantes, et d’autres composants. La qualité du revêtement est cruciale pour protéger les véhicules contre la corrosion et les dommages causés par les conditions climatiques.
- Aéronautique : Les systèmes de peinture dans l’aéronautique sont utilisés pour appliquer des revêtements qui protègent les avions contre la corrosion, tout en réduisant la friction pour améliorer l’aérodynamisme.
- Fabrication de meubles : Les systèmes de peinture sont utilisés pour appliquer des finitions décoratives et protectrices sur les meubles en bois, en métal, ou en plastique, améliorant ainsi leur apparence et leur durabilité.
- Électronique : Dans l’industrie électronique, les systèmes de peinture sont utilisés pour protéger les composants contre les influences environnementales telles que l’humidité, la chaleur, et les produits chimiques.
5. Conclusion
Les systèmes de peinture sont essentiels pour assurer une application efficace, uniforme, et durable des revêtements dans de nombreuses industries. Grâce à l’automatisation et aux technologies avancées, ces systèmes permettent d’optimiser les processus de production, de réduire les coûts, et d’améliorer la qualité des produits finis. Que ce soit pour des applications décoratives ou protectrices, un système de peinture bien conçu est un investissement crucial pour toute entreprise cherchant à maintenir des standards élevés de qualité et d’efficacité.
Automatisation de la Pulvérisation: La pulvérisation est une technique utilisée pour appliquer un liquide sous forme de fines gouttelettes sur une surface. Elle est essentielle dans de nombreux secteurs, notamment l’agriculture, l’industrie automobile, la construction, et bien d’autres. Cette méthode permet de répartir uniformément des substances telles que des peintures, des pesticides, des engrais, et des produits chimiques, maximisant ainsi leur efficacité et minimisant le gaspillage.
Dans le contexte industriel, la pulvérisation joue un rôle crucial pour garantir la qualité et l’uniformité des produits finis. Par exemple, dans l’industrie automobile, la pulvérisation de peinture doit être précise pour éviter les défauts et assurer une finition parfaite. En agriculture, elle est vitale pour protéger les cultures contre les ravageurs et les maladies tout en optimisant l’utilisation des ressources.
L’automatisation de la pulvérisation représente une avancée majeure dans de nombreux secteurs industriels où la précision et l’efficacité sont des priorités. Ce processus, qui consiste à appliquer un liquide, une peinture ou tout autre type de revêtement sur une surface, est depuis longtemps utilisé manuellement. Toutefois, avec l’évolution des technologies et la montée des exigences de qualité, la pulvérisation automatique est devenue un standard dans des domaines tels que l’automobile, l’aéronautique, l’agriculture et même l’industrie alimentaire.
Au cœur de cette révolution se trouvent les systèmes automatisés capables de remplacer les méthodes manuelles par des équipements sophistiqués, tels que des robots ou des machines programmables, qui effectuent les opérations de manière précise et uniforme. Cette automatisation permet non seulement de réduire le besoin en main-d’œuvre qualifiée, mais elle améliore aussi la constance des résultats, élimine les erreurs humaines et optimise l’utilisation des ressources, qu’il s’agisse de matériaux ou d’énergie.
Historiquement, la pulvérisation a été utilisée pour diverses applications, allant de l’application de peinture à l’arrosage des cultures agricoles. Cependant, les défis rencontrés avec les systèmes manuels, tels que l’inconstance de la couverture, les pertes de matériau et la dangerosité de certains produits, ont poussé l’industrie à adopter des solutions plus technologiques. L’automatisation répond à ces enjeux tout en apportant des bénéfices en termes de sécurité, de productivité et d’impact environnemental.
Les systèmes de pulvérisation automatisés reposent sur l’utilisation de robots, de buses automatiques, de capteurs et de logiciels sophistiqués pour contrôler avec précision la quantité de matériau pulvérisé, la direction du jet et la vitesse d’application. Grâce à des programmations avancées, ces systèmes peuvent s’adapter à des pièces de différentes formes et tailles, garantissant une couverture uniforme, même sur des surfaces complexes.
Les objectifs principaux de l’automatisation de la pulvérisation incluent :
- Efficacité accrue : Réduction des pertes de matériau et optimisation des ressources
- Précision : Application uniforme et contrôlée, réduisant les erreurs et les reprises
- Réduction des coûts : Moins de main-d’œuvre et d’erreurs, ce qui réduit les coûts d’exploitation
- Sécurité des travailleurs : Moins d’exposition directe à des produits dangereux
- Environnement : Réduction des émissions et des pertes de produits chimiques
L’évolution rapide des technologies a permis à l’automatisation de la pulvérisation de devenir un atout incontournable dans de nombreux secteurs. Au-delà des gains d’efficacité, elle joue également un rôle crucial dans la réponse aux préoccupations environnementales et aux régulations de plus en plus strictes concernant les émissions industrielles et l’utilisation des produits chimiques.
Technologies de Pulvérisation
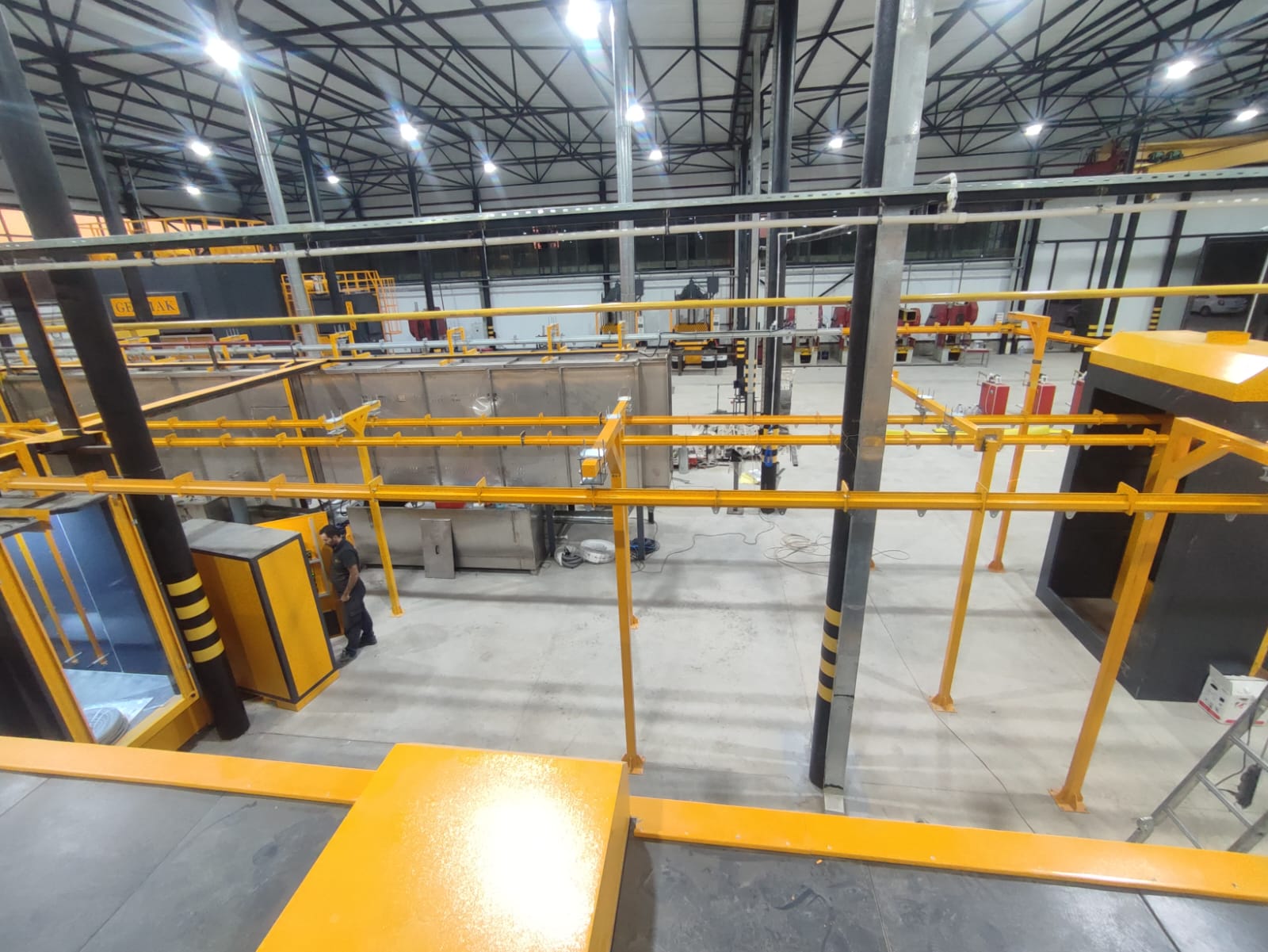
L’automatisation de la pulvérisation repose sur diverses technologies, chacune adaptée à des applications et à des environnements spécifiques. Les choix technologiques dépendent du type de matériau à pulvériser, de la surface à traiter, ainsi que des objectifs en matière de qualité et de productivité. Voici un aperçu des principales technologies de pulvérisation automatisée utilisées dans l’industrie.
2.1. Pulvérisation électrostatique
La pulvérisation électrostatique est une méthode qui utilise la force d’attraction entre des charges électriques opposées pour assurer une application plus efficace et uniforme des revêtements. Cette technologie est particulièrement efficace pour réduire les pertes de produit et garantir une couverture uniforme, même sur des surfaces complexes.
- Principe de fonctionnement : Le liquide ou la poudre est chargé électriquement lorsqu’il est pulvérisé à partir d’un pistolet. Les particules ainsi chargées sont attirées par la surface de la pièce à traiter, qui est mise à la terre. Cette attraction permet au matériau de se déposer uniformément sur la surface, même dans les zones difficiles d’accès, tout en minimisant le rebond du produit.
- Avantages :
- Réduction des pertes de matériau grâce à l’attraction électrostatique
- Couverture uniforme, même sur des formes complexes
- Application plus rapide par rapport aux méthodes traditionnelles
- Moins de déchets et un environnement de travail plus propre
- Applications : La pulvérisation électrostatique est couramment utilisée dans l’industrie automobile pour l’application de peinture sur les carrosseries, ainsi que dans la fabrication d’appareils électroménagers et de mobilier métallique.
2.2. Pulvérisation à haute pression et par air
La pulvérisation à haute pression, aussi appelée pulvérisation sans air, est une autre technologie couramment utilisée dans l’automatisation. Cette méthode permet de projeter le matériau à haute vitesse à l’aide d’une pression mécanique, sans recourir à un flux d’air comprimé.
- Pulvérisation à haute pression (Airless) : Le liquide est poussé à travers une buse à haute pression, ce qui le divise en fines particules projetées directement sur la surface à traiter. Cette méthode est efficace pour appliquer des revêtements épais et visqueux sans dilution excessive.
- Pulvérisation par air comprimé : Ici, l’air comprimé est utilisé pour pulvériser le matériau sous forme d’aérosol fin. Cela permet un contrôle précis de l’application, mais peut entraîner plus de pertes de produit en raison de l’atomisation par l’air.
- Avantages :
- Application rapide et efficace pour des matériaux épais
- Réduction du temps d’application par rapport aux méthodes manuelles
- Contrôle précis de l’épaisseur de la couche appliquée
- Moins de dilution nécessaire, ce qui améliore la qualité du revêtement
- Inconvénients :
- Nécessite un entretien régulier pour éviter l’encrassement des buses
- Perte de produit plus élevée avec la pulvérisation par air (overspray)
2.3. Robots de Pulvérisation
Les robots de pulvérisation sont devenus essentiels pour l’automatisation dans des environnements où la précision, la rapidité et la répétabilité sont cruciales. Ces robots sont équipés de bras articulés et de pistolets de pulvérisation automatisés, capables de couvrir de grandes surfaces ou de traiter des formes complexes avec une extrême précision.
- Types de robots de pulvérisation :
- Robots à bras articulés : Ils sont couramment utilisés dans l’industrie automobile pour l’application de peinture sur les carrosseries des véhicules. Ces robots peuvent accéder à des zones difficiles à atteindre et ajuster les angles de pulvérisation pour garantir une couverture complète.
- Robots montés sur rails : Souvent utilisés pour pulvériser de grands objets ou des surfaces planes, comme des panneaux ou des structures métalliques.
- Avantages :
- Répétabilité élevée et uniformité des résultats
- Réduction des temps de cycle et augmentation de la productivité
- Flexibilité pour s’adapter à différents types de pièces et de produits
- Moins de risque pour les travailleurs, car ils ne sont pas exposés directement aux produits chimiques
- Inconvénients :
- Coût initial élevé
- Nécessite une formation spécialisée pour la programmation et la maintenance
2.4. Systèmes automatiques par programmation
Les systèmes de pulvérisation programmés permettent de personnaliser le processus de pulvérisation en fonction des besoins spécifiques de chaque production. Ces systèmes utilisent des logiciels avancés pour contrôler les paramètres du processus, tels que la vitesse, la pression et la quantité de produit pulvérisé.
- Caractéristiques :
- Programmation adaptative : Les systèmes peuvent être programmés pour ajuster les paramètres en fonction de la taille, de la forme et du matériau de chaque pièce, garantissant ainsi une application optimale.
- Surveillance en temps réel : Certains systèmes sont équipés de capteurs intelligents qui surveillent les conditions de pulvérisation en temps réel et ajustent les paramètres pour garantir une qualité constante.
- Avantages :
- Flexibilité maximale pour des productions variées
- Contrôle précis des coûts en réduisant les pertes de matériau
- Surveillance en temps réel pour ajuster automatiquement les erreurs ou les variations
- Inconvénients :
- Coût d’investissement initial élevé
- Maintenance plus complexe
Conclusion
L’automatisation de la pulvérisation repose sur plusieurs technologies adaptées à des besoins industriels variés. Que ce soit à travers la pulvérisation électrostatique pour des surfaces complexes, la pulvérisation à haute pression pour des revêtements épais, ou les robots pour une précision inégalée, chaque technologie présente des avantages spécifiques. Le choix de la technologie dépendra des exigences de production, des matériaux à pulvériser et des objectifs en termes de qualité, de coûts et d’efficacité.
Applications Industrielles de la Pulvérisation Automatisée
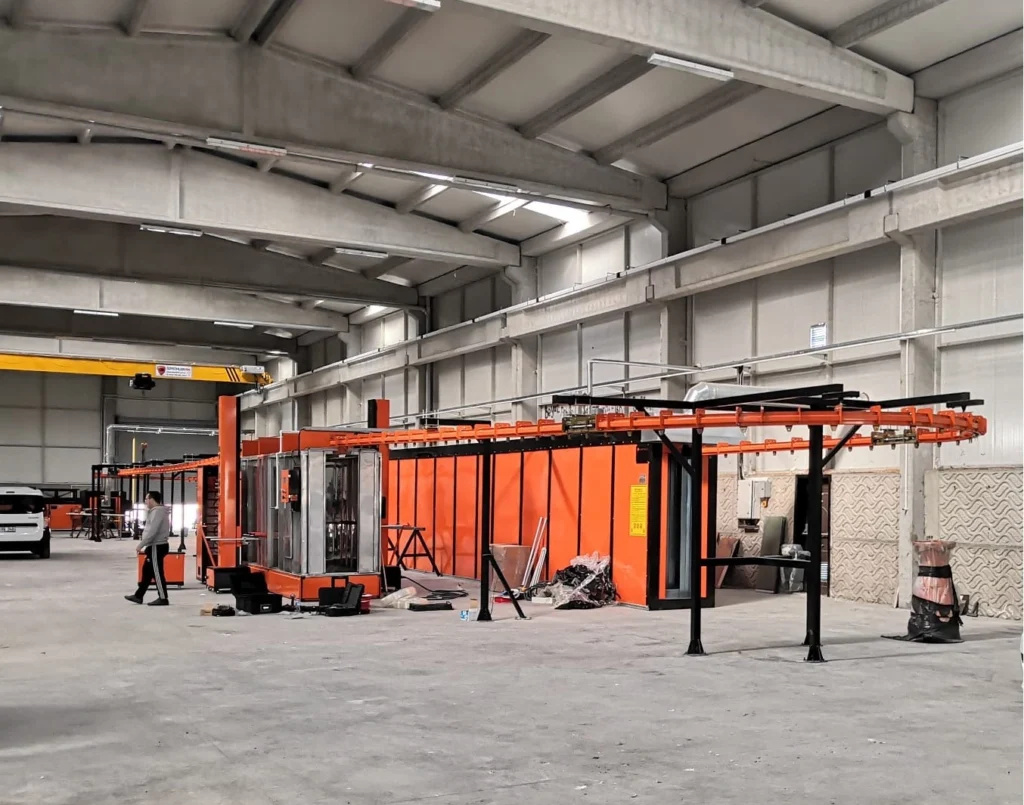
L’automatisation de la pulvérisation est devenue un pilier central dans de nombreuses industries. Que ce soit pour l’application de peintures, de revêtements protecteurs ou de produits spécifiques, les systèmes automatisés de pulvérisation améliorent la productivité, la précision et la qualité des processus. Dans cette section, nous détaillerons les principales applications industrielles de la pulvérisation automatisée, en soulignant les avantages qu’elle apporte dans chaque secteur.
3.1. Industrie Automobile
L’industrie automobile est l’un des plus grands utilisateurs de la pulvérisation automatisée. La fabrication de véhicules nécessite l’application de plusieurs couches de peinture et de revêtements protecteurs sur des surfaces complexes et variées, tout en maintenant une uniformité et une qualité constantes. Les robots de pulvérisation jouent un rôle clé dans ce processus, offrant une précision inégalée et une efficacité accrue.
Applications spécifiques :
- Peinture des carrosseries : Les robots de pulvérisation sont utilisés pour appliquer des couches de base, des couches intermédiaires et des vernis sur les carrosseries des voitures. Ces robots sont capables de pulvériser de manière uniforme sur des surfaces incurvées, des zones complexes comme les bas de caisse et les cadres de porte.
- Revêtements protecteurs : Outre la peinture, des revêtements spéciaux, comme les anticorrosions ou les revêtements anti-rayures, sont appliqués sur les composants métalliques pour protéger les pièces contre la rouille, les rayures, et d’autres types d’usure.
- Intérieurs et finitions : L’intérieur des véhicules, y compris les pièces en plastique, les tableaux de bord et les éléments décoratifs, peuvent également être revêtus avec des systèmes de pulvérisation automatisés pour garantir une finition de haute qualité et durable.
Avantages pour l’industrie automobile :
- Précision : Les robots de pulvérisation assurent une application précise et contrôlée de la peinture, garantissant une finition homogène sur toutes les voitures produites.
- Réduction des déchets : L’utilisation de la pulvérisation électrostatique dans l’automobile permet de minimiser les pertes de peinture, réduisant ainsi le gaspillage et les coûts de production.
- Productivité accrue : Les systèmes automatisés permettent de traiter plusieurs voitures en même temps, réduisant considérablement le temps de cycle par rapport aux méthodes manuelles.
3.2. Industrie Aéronautique
Dans l’industrie aéronautique, les exigences en matière de précision et de qualité sont extrêmement élevées. Les avions et les composants aéronautiques nécessitent des revêtements spécifiques pour améliorer leur durabilité, leur résistance à la corrosion, et pour des raisons esthétiques. Les systèmes automatisés de pulvérisation permettent d’appliquer des revêtements uniformes sur des surfaces complexes et de grandes tailles, comme les fuselages et les ailes d’avion.
Applications spécifiques :
- Peinture des avions : Les avions sont recouverts de peintures spéciales qui non seulement améliorent leur apparence, mais aussi protègent les matériaux contre les conditions climatiques extrêmes, les rayons UV et l’usure liée à la haute altitude.
- Revêtements anticorrosion : Les composants métalliques des avions sont souvent soumis à des environnements humides et corrosifs. Les systèmes de pulvérisation automatisés appliquent des revêtements anticorrosion sur les structures en aluminium et en acier pour prolonger la durée de vie des avions.
- Revêtements techniques : Certains revêtements appliqués dans l’aéronautique ont des propriétés spécifiques, comme la résistance aux températures élevées ou la conductivité électrique. Ces revêtements nécessitent une application précise et homogène que seule l’automatisation peut garantir.
Avantages pour l’industrie aéronautique :
- Qualité uniforme : L’utilisation de robots de pulvérisation garantit une application homogène et sans défaut sur les surfaces des avions, un facteur crucial pour la performance et la sécurité des appareils.
- Réduction des temps de cycle : Les systèmes automatisés permettent d’accélérer le processus de pulvérisation, réduisant ainsi les temps d’immobilisation des avions en maintenance ou en production.
- Économie de matériaux : Grâce à la précision de l’application, la quantité de peinture ou de revêtement utilisée est optimisée, ce qui réduit les coûts et le gaspillage.
3.3. Secteur Agricole
L’automatisation de la pulvérisation est également très répandue dans le secteur agricole, où elle est utilisée pour appliquer des engrais, des pesticides, et d’autres produits chimiques sur les cultures. Cette technologie permet de réduire l’utilisation excessive de produits, d’améliorer la couverture des plantes et d’optimiser les rendements agricoles tout en minimisant l’impact environnemental.
Applications spécifiques :
- Pulvérisation des cultures : Les machines agricoles automatisées pulvérisent des pesticides, des herbicides et des fongicides de manière uniforme sur les champs. Grâce aux capteurs intégrés, les systèmes peuvent ajuster la quantité de produit appliqué en fonction des besoins spécifiques de chaque zone du champ, évitant ainsi le surdosage.
- Fertilisation : Des systèmes de pulvérisation automatisée sont également utilisés pour appliquer des fertilisants liquides ou granulaires sur les cultures. Cette méthode garantit une distribution homogène, favorisant une croissance uniforme et des rendements accrus.
- Gestion de l’eau : L’automatisation de la pulvérisation dans l’irrigation permet de contrôler précisément l’apport d’eau aux cultures, optimisant ainsi l’utilisation des ressources hydriques tout en favorisant une agriculture plus durable.
Avantages pour le secteur agricole :
- Optimisation des ressources : En appliquant précisément la quantité nécessaire de produits chimiques ou d’eau, les systèmes automatisés réduisent le gaspillage, ce qui permet de faire des économies et de limiter l’impact environnemental.
- Productivité : Les machines de pulvérisation automatisées couvrent de grandes surfaces en peu de temps, augmentant ainsi l’efficacité et réduisant la nécessité de main-d’œuvre manuelle.
- Protection de l’environnement : En utilisant la pulvérisation automatisée, il est possible de minimiser l’utilisation de pesticides, réduisant ainsi la contamination des sols et des nappes phréatiques.
3.4. Produits Alimentaires et Emballage
Dans l’industrie alimentaire, l’automatisation de la pulvérisation est utilisée pour appliquer des enrobages, des conservateurs et des revêtements sur des aliments ou leurs emballages. Ces processus nécessitent une grande précision pour garantir l’application uniforme de produits tout en respectant les normes sanitaires strictes.
Applications spécifiques :
- Enrobage des produits alimentaires : Dans la production alimentaire, certains produits, comme les confiseries ou les pâtisseries, nécessitent l’application d’enrobages (chocolat, sucre, etc.). Les systèmes automatisés garantissent une couverture uniforme et précise des produits, améliorant à la fois leur apparence et leur durée de conservation.
- Conservateurs et additifs : Les systèmes de pulvérisation sont également utilisés pour appliquer des conservateurs alimentaires, tels que les antioxydants ou les agents antimicrobiens, directement sur les produits ou les emballages. Cela permet d’augmenter la durée de vie des produits tout en réduisant l’utilisation de conservateurs chimiques.
- Revêtements d’emballage : Dans le domaine de l’emballage, les systèmes de pulvérisation automatisée sont utilisés pour appliquer des revêtements protecteurs ou imperméables sur les emballages, garantissant ainsi une meilleure protection des aliments.
Avantages pour l’industrie alimentaire :
- Précision et uniformité : L’automatisation permet d’assurer une application précise et régulière des enrobages, évitant ainsi les excès ou les manques de produit.
- Amélioration de la durée de conservation : En garantissant une application uniforme des conservateurs, les systèmes automatisés prolongent la durée de vie des produits alimentaires.
- Respect des normes sanitaires : L’automatisation réduit le contact humain direct avec les produits alimentaires, minimisant ainsi les risques de contamination et garantissant le respect des normes d’hygiène strictes.
3.5. Peinture Industrielle et Secteur du Bâtiment
Dans l’industrie de la construction et du bâtiment, l’automatisation de la pulvérisation est utilisée pour appliquer des peintures et des revêtements sur de grandes surfaces telles que les façades, les structures métalliques ou les ponts. Cette technologie permet d’améliorer la productivité tout en garantissant une couverture uniforme, même sur des surfaces difficiles d’accès.
Applications spécifiques :
- Peinture des bâtiments et des infrastructures : Les robots de pulvérisation automatisée sont utilisés pour appliquer des couches de peinture sur les murs extérieurs et intérieurs des bâtiments, ainsi que sur des structures métalliques comme les ponts, les grattes-ciel, et les plateformes pétrolières.
- Revêtements ignifuges et anticorrosion : Des systèmes automatisés sont utilisés pour appliquer des revêtements ignifuges sur des structures en acier dans des bâtiments ou des infrastructures pour garantir leur sécurité en cas d’incendie. Ils sont également utilisés pour appliquer des revêtements anticorrosion sur des installations exposées aux intempéries, comme les ponts ou les pipelines.
- Peinture décorative et finitions : Les machines de pulvérisation automatisée sont également utilisées pour des finitions décoratives et des peintures complexes sur des surfaces architecturales, garantissant des résultats esthétiques de haute qualité.
Avantages pour le secteur du bâtiment :
- Accélération du processus : Les robots de pulvérisation automatisée peuvent couvrir de grandes surfaces en peu de temps, réduisant ainsi les délais de construction et de rénovation.
- Accès aux zones difficiles : Les bras robotiques peuvent atteindre des zones difficiles d’accès, comme les hauteurs des bâtiments, avec une grande précision et en toute sécurité.
- Réduction des coûts de main-d’œuvre : L’automatisation permet de réduire la nécessité d’une main-d’œuvre spécialisée pour la peinture des bâtiments et des infrastructures.
Conclusion
L’automatisation de la pulvérisation a révolutionné de nombreuses industries en optimisant la qualité, la précision et la productivité des processus. Que ce soit dans l’automobile, l’aéronautique, l’agriculture, l’alimentation ou le bâtiment, les systèmes de pulvérisation automatisés ont permis de répondre aux besoins croissants en matière de rapidité, d’efficacité et de sécurité. Grâce à des technologies avancées telles que la pulvérisation électrostatique, la pulvérisation à haute pression et les robots automatisés, ces systèmes offrent des solutions adaptées à une multitude d’applications industrielles, contribuant ainsi à la compétitivité des entreprises et à la réduction de leur empreinte environnementale.
Avantages de l’Automatisation de la Pulvérisation
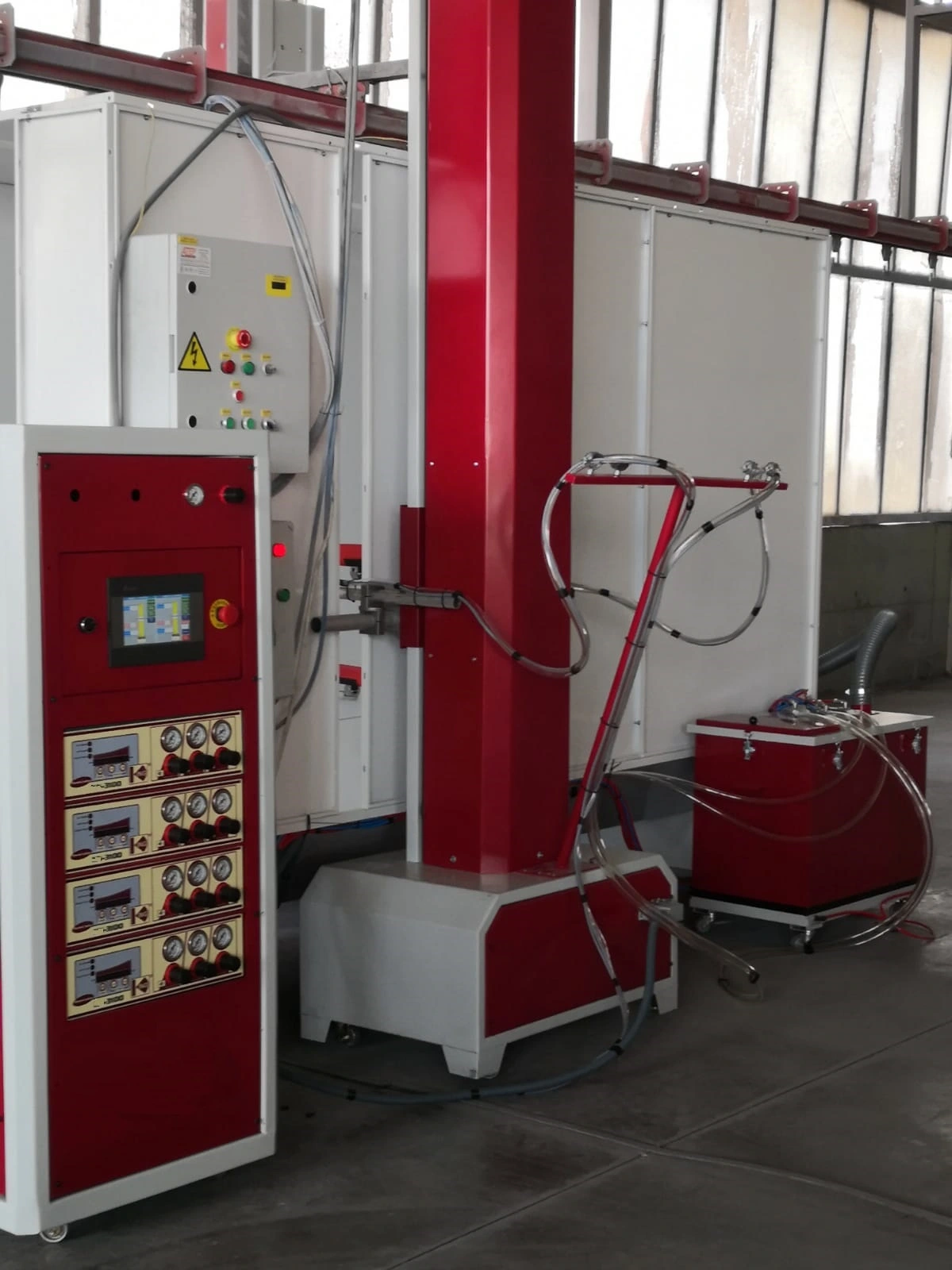
L’automatisation de la pulvérisation présente de nombreux avantages pour les entreprises industrielles en termes de précision, de productivité et de rentabilité. Dans cette section, nous allons explorer en détail ces avantages et comprendre comment l’automatisation améliore l’ensemble du processus de pulvérisation.
4.1. Précision et uniformité de l’application
L’un des principaux avantages des systèmes de pulvérisation automatisée est la précision et l’uniformité qu’ils offrent lors de l’application des revêtements. Comparé aux méthodes manuelles, où l’épaisseur du revêtement peut varier d’une zone à l’autre, les machines et les robots automatisés garantissent une application régulière et homogène.
- Couverture homogène : Les systèmes automatisés, équipés de capteurs et de contrôleurs, ajustent en temps réel la vitesse de pulvérisation, la quantité de produit et la position du pistolet de pulvérisation pour garantir une couverture parfaite. Cela permet d’éviter les surcharges de peinture ou de produit dans certaines zones et les manques dans d’autres.
- Qualité répétée : L’uniformité d’application est essentielle pour garantir une qualité constante entre les différentes pièces ou produits. Les robots et systèmes automatisés assurent cette répétabilité, un avantage crucial pour les industries où des normes strictes de qualité doivent être respectées, comme l’automobile et l’aéronautique.
Avantages de l’Automatisation de la Pulvérisation
4.2. Réduction des pertes de matériau
Un autre avantage majeur de l’automatisation de la pulvérisation est la réduction significative des pertes de matériau. Dans les systèmes de pulvérisation manuels, une grande partie de la peinture, des revêtements ou des produits pulvérisés se perd en raison d’un mauvais contrôle du jet ou d’une surapplication. Les systèmes automatisés, en revanche, sont conçus pour optimiser l’application de la peinture ou du revêtement, en ajustant la quantité pulvérisée en fonction de la surface à traiter et en minimisant les pertes.
- Pulvérisation électrostatique : Grâce à cette technologie, le matériau pulvérisé est chargé électriquement et attiré par la surface de l’objet. Cela permet de minimiser l’overspray (le matériau qui dépasse l’objet ciblé) et d’augmenter le taux de transfert, réduisant ainsi la quantité de produit gaspillée. Ce procédé est particulièrement efficace pour appliquer des revêtements sur des pièces métalliques ou des structures complexes.
- Contrôle précis des paramètres : Les systèmes automatisés utilisent des capteurs et des logiciels pour ajuster en temps réel les paramètres de pulvérisation, comme le débit de peinture et la pression, afin de garantir que seule la quantité nécessaire de produit est appliquée. Cela permet de limiter le gaspillage et d’améliorer l’efficacité globale du processus.
- Optimisation des cycles de production : En réduisant les pertes de matériau, les entreprises peuvent diminuer les coûts liés à l’achat de produits et revêtements, tout en améliorant l’efficacité de leurs cycles de production. Moins de produit perdu signifie moins de retouches ou de reprises, ce qui se traduit par des gains de temps et d’argent.
4.3. Amélioration de la qualité et de la finition
L’automatisation de la pulvérisation permet également d’améliorer la qualité et la finition des produits, un aspect particulièrement important pour les industries où l’apparence, la durabilité et la performance des revêtements sont essentiels.
- Finition uniforme et esthétique : L’un des principaux problèmes rencontrés avec la pulvérisation manuelle est l’irrégularité de l’application, ce qui peut entraîner des zones plus épaisses ou plus fines de revêtement. Les systèmes automatisés, en revanche, assurent une application constante et uniforme, offrant ainsi une finition lisse et homogène, sans traces de pinceau ou de jet de pulvérisation irrégulier.
- Réduction des défauts : Les systèmes de pulvérisation automatisés sont programmés pour détecter et corriger les erreurs en temps réel, réduisant ainsi les défauts tels que les coulures, les bulles d’air ou les taches. Cela permet de minimiser le nombre de pièces rejetées ou nécessitant des retouches, tout en garantissant une qualité constante tout au long du processus de production.
- Adaptabilité à différents matériaux : Grâce à l’automatisation, les paramètres de pulvérisation peuvent être ajustés pour s’adapter à différents matériaux et revêtements, qu’il s’agisse de peinture, de vernis, de produits chimiques ou de revêtements protecteurs. Cela garantit que chaque matériau reçoit la bonne quantité de produit pour maximiser sa durabilité, sa résistance et son apparence.
4.4. Gains de productivité et optimisation des ressources
L’automatisation permet de considérablement augmenter la productivité en réduisant le temps nécessaire pour effectuer les tâches de pulvérisation et en optimisant l’utilisation des ressources.
- Réduction du temps de cycle : Les systèmes automatisés peuvent traiter plusieurs pièces en même temps ou travailler en continu sur des lignes de production. Cela réduit les temps d’arrêt entre les cycles de pulvérisation et accélère le processus global. Par exemple, dans l’industrie automobile, l’utilisation de robots de pulvérisation permet d’appliquer les couches de peinture plus rapidement que les systèmes manuels, augmentant ainsi le rendement de production.
- Utilisation optimale des ressources : En optimisant l’application de la peinture ou du revêtement, les systèmes automatisés réduisent non seulement le gaspillage de matériau, mais aussi la consommation d’énergie et de produits chimiques. Les entreprises peuvent ainsi améliorer leur efficacité énergétique et minimiser l’impact environnemental de leurs opérations.
- Réduction des coûts de main-d’œuvre : Les systèmes automatisés nécessitent moins d’intervention humaine. Une fois programmés, ils fonctionnent de manière autonome, avec un besoin minimal de supervision. Cela permet de réduire les coûts de main-d’œuvre liés à la formation, au contrôle et à l’exécution des tâches de pulvérisation.
4.5. Réduction des risques pour les travailleurs (santé et sécurité)
L’utilisation de produits chimiques et de revêtements, tels que les peintures, vernis et solvants, présente des risques pour la santé des travailleurs, en particulier lorsqu’ils sont exposés à ces substances pendant de longues périodes. L’automatisation de la pulvérisation permet de réduire considérablement ces risques en limitant l’exposition directe des travailleurs à ces produits potentiellement dangereux.
- Moins d’exposition aux produits chimiques : Les systèmes automatisés prennent en charge l’application des produits chimiques et des revêtements, réduisant ainsi la nécessité pour les travailleurs de manipuler ou de se trouver à proximité de substances dangereuses. Cela contribue à améliorer la santé et la sécurité sur le lieu de travail en minimisant les risques d’inhalation de fumées toxiques ou de contact direct avec des produits corrosifs ou nocifs.
- Réduction des risques liés à la répétitivité : Les tâches de pulvérisation manuelles peuvent entraîner des problèmes ergonomiques liés à la répétition des mouvements, comme les troubles musculo-squelettiques. L’automatisation élimine ces risques en remplaçant la main-d’œuvre humaine par des machines ou des robots capables de travailler en continu sans fatigue.
- Sécurité améliorée : Les robots et machines de pulvérisation sont équipés de dispositifs de sécurité avancés, tels que des arrêts d’urgence et des capteurs de détection des anomalies. Cela permet de garantir un environnement de travail sûr, réduisant ainsi le risque d’accidents ou d’incidents liés à des équipements défaillants ou mal utilisés.
Conclusion
L’automatisation de la pulvérisation présente un ensemble d’avantages considérables pour les entreprises industrielles. En optimisant l’utilisation des matériaux, en améliorant la qualité des produits et en augmentant la productivité, les systèmes automatisés contribuent à réduire les coûts de production tout en garantissant une efficacité maximale. De plus, en minimisant les risques pour la santé et la sécurité des travailleurs, l’automatisation permet de créer un environnement de travail plus sûr et plus respectueux des normes en vigueur. Ces avantages font de l’automatisation de la pulvérisation une solution incontournable pour les entreprises cherchant à rester compétitives dans des secteurs exigeants tels que l’automobile, l’aéronautique, l’agriculture et la construction.
Défis et Limitations de la Pulvérisation Automatisée
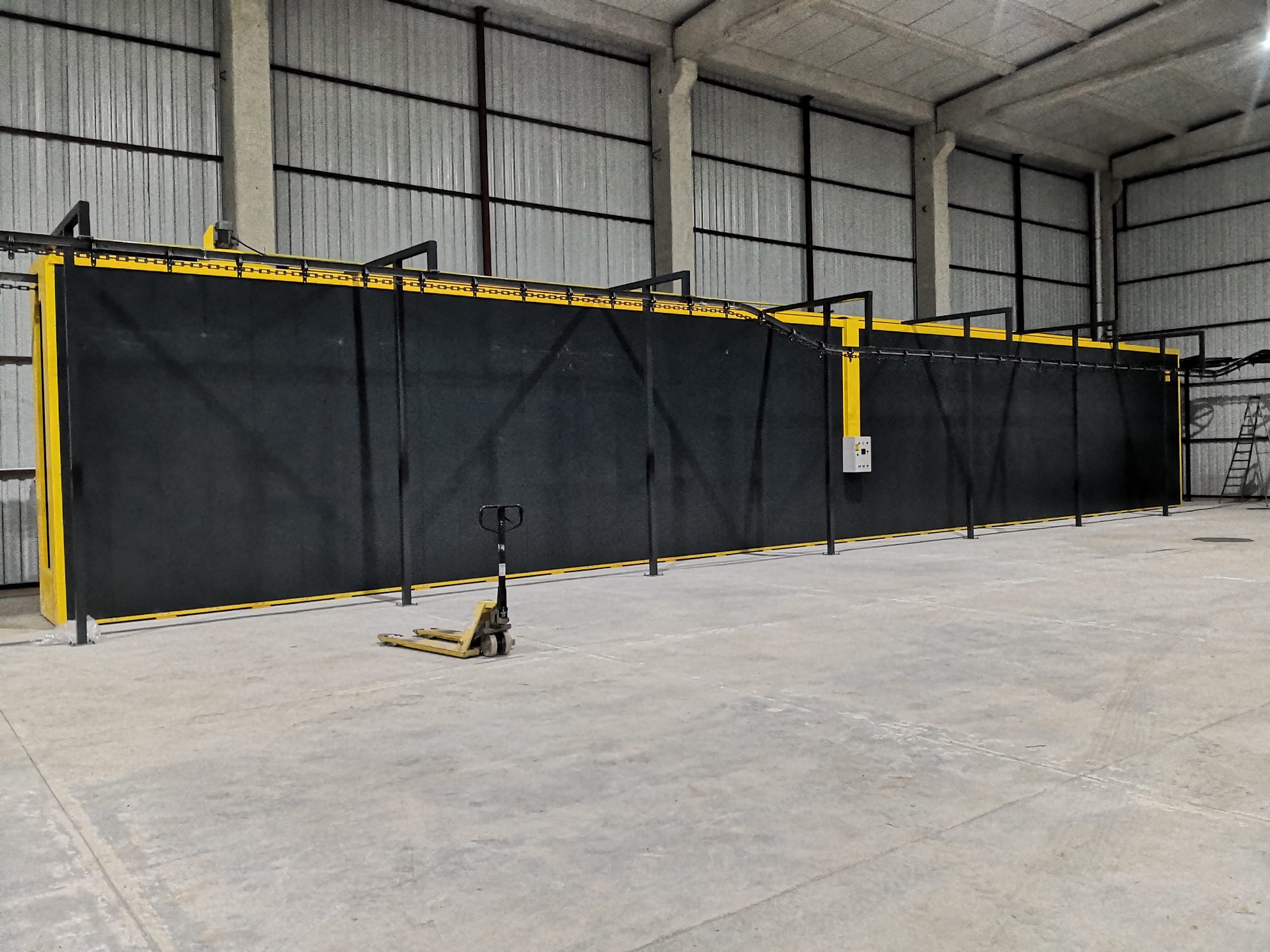
Malgré les nombreux avantages que présente l’automatisation de la pulvérisation, cette technologie comporte également des défis et des limitations qu’il convient de prendre en compte. Les entreprises qui envisagent de passer à des systèmes de pulvérisation automatisés doivent être conscientes des obstacles potentiels, qu’il s’agisse de la complexité de l’installation, des coûts initiaux, ou des besoins en maintenance. Dans cette section, nous explorerons les principaux défis et limites associés à l’automatisation de la pulvérisation.
5.1. Coûts initiaux et complexité d’installation
L’un des principaux défis auxquels les entreprises sont confrontées lorsqu’elles adoptent l’automatisation de la pulvérisation est le coût initial élevé et la complexité de l’installation des systèmes. Les robots de pulvérisation, les machines de pulvérisation programmables et les systèmes de contrôle intelligents peuvent nécessiter des investissements substantiels, surtout pour les petites et moyennes entreprises.
- Coût d’acquisition : Les robots de pulvérisation et les équipements automatisés sont coûteux à l’achat. Le prix d’un système complet, incluant les robots, les capteurs, les logiciels de gestion et les dispositifs de sécurité, peut représenter une somme importante pour les entreprises, en particulier pour celles qui n’ont pas encore investi dans des technologies d’automatisation.
- Coût d’installation et intégration : L’installation de systèmes de pulvérisation automatisés nécessite souvent des modifications de l’infrastructure existante, telles que l’ajout de rails pour les robots, la mise à jour des lignes de production, ou encore l’amélioration des systèmes de ventilation pour respecter les normes de sécurité. Ces modifications peuvent entraîner des coûts supplémentaires et nécessiter des temps d’arrêt pendant la phase d’intégration.
- Rendement à court terme : Bien que les systèmes de pulvérisation automatisés offrent des gains de productivité et de rentabilité à long terme, les entreprises doivent être prêtes à faire face à des retours sur investissement (ROI) différés. Les gains immédiats ne sont souvent pas visibles pendant les premières phases de mise en œuvre.
5.2. Maintenance des systèmes automatisés
Les systèmes de pulvérisation automatisés, bien que très efficaces, nécessitent un entretien régulier pour garantir leur bon fonctionnement. La complexité de ces systèmes peut poser des défis en termes de maintenance, d’inspections et de réparations.
- Maintenance préventive : Les robots de pulvérisation, les capteurs et les systèmes de contrôle automatisés doivent être régulièrement inspectés et entretenus pour éviter les pannes. Les entreprises doivent mettre en place des programmes de maintenance préventive pour garantir que les équipements fonctionnent de manière optimale. Cela inclut le nettoyage des buses, le calibrage des capteurs, et la vérification des logiciels de gestion.
- Coût de la maintenance : La maintenance des systèmes automatisés peut représenter un coût important, notamment en raison du besoin de techniciens spécialisés pour réparer et entretenir les équipements. De plus, le remplacement des pièces usées, telles que les buses de pulvérisation ou les composants électroniques, peut s’avérer coûteux.
- Complexité des réparations : En cas de panne, les systèmes automatisés peuvent nécessiter des réparations complexes qui demandent des compétences spécifiques. Cela peut entraîner des temps d’arrêt plus longs que pour des systèmes manuels, affectant ainsi la productivité de l’entreprise.
5.3. Programmation et formation des opérateurs
L’automatisation de la pulvérisation nécessite une programmation avancée pour garantir une application précise et personnalisée des revêtements. Cette programmation peut s’avérer complexe, en particulier pour les systèmes robotisés ou ceux intégrés dans des lignes de production automatisées.
- Programmation des systèmes : La programmation des robots de pulvérisation nécessite une expertise technique spécifique, en particulier lorsque les systèmes doivent être ajustés pour s’adapter à des pièces de formes variées ou à des revêtements spécifiques. Les entreprises doivent investir dans des ressources humaines capables de programmer et de maintenir ces systèmes.
- Formation des opérateurs : Bien que les systèmes automatisés réduisent la dépendance à la main-d’œuvre manuelle pour la pulvérisation, ils nécessitent la formation des opérateurs pour surveiller, programmer et entretenir les équipements. La formation des employés aux nouvelles technologies peut représenter un coût supplémentaire et nécessiter du temps.
5.4. Adaptation des équipements pour des formes complexes
Un autre défi auquel sont confrontées les entreprises qui adoptent l’automatisation de la pulvérisation est l’adaptation des systèmes à des pièces ou des surfaces complexes. Alors que les robots et les machines de pulvérisation automatisée sont excellents pour des surfaces plates ou des objets réguliers, ils peuvent rencontrer des difficultés avec des formes complexes ou irrégulières.
- Zones difficiles d’accès : Les pièces comportant des angles aigus, des cavités ou des formes complexes peuvent être plus difficiles à pulvériser de manière uniforme avec des systèmes automatisés. Bien que certaines technologies, telles que la pulvérisation électrostatique, puissent améliorer la couverture, ces systèmes ne sont pas toujours adaptés à toutes les situations.
- Ajustement des paramètres : Pour des formes complexes, les paramètres de pulvérisation doivent être ajustés avec précision, ce qui peut nécessiter une programmation plus complexe et plus de temps pour garantir une couverture complète. Cela peut ralentir le processus de production ou entraîner des variations dans la qualité des revêtements.
Conclusion
Bien que l’automatisation de la pulvérisation offre de nombreux avantages, elle n’est pas sans défis. Les coûts initiaux élevés, les besoins en maintenance, la formation des opérateurs et les difficultés liées aux formes complexes peuvent représenter des obstacles à l’adoption de cette technologie. Cependant, pour les entreprises qui parviennent à surmonter ces défis, les gains en termes de productivité, de qualité et d’efficacité peuvent largement compenser les coûts et les difficultés initiales. L’adoption de l’automatisation doit être soigneusement planifiée, avec une évaluation approfondie des besoins spécifiques de chaque entreprise et une préparation adéquate pour maximiser les bénéfices à long terme.
Éléments Techniques d’un Système de Pulvérisation Automatisée
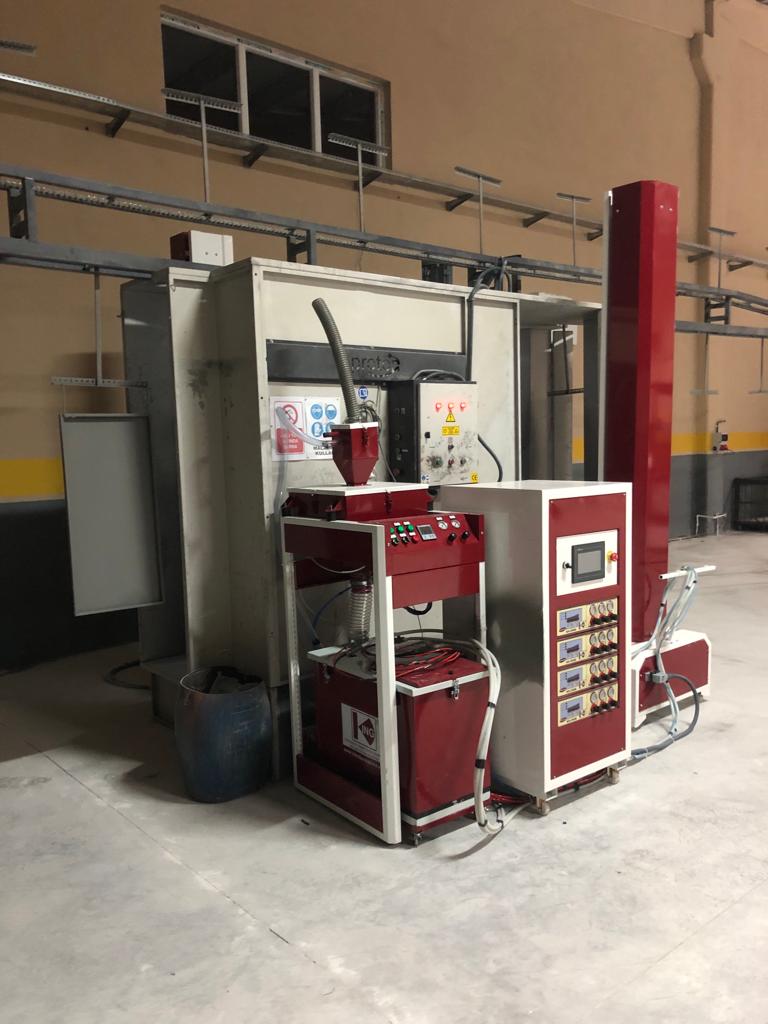
Les systèmes de pulvérisation automatisée sont composés de plusieurs éléments techniques qui interagissent de manière fluide pour garantir une application précise, efficace et uniforme des revêtements. Chaque composant a un rôle essentiel dans le processus, que ce soit pour le contrôle de la pulvérisation, l’optimisation de l’utilisation des matériaux, ou la gestion des paramètres environnementaux. Dans cette section, nous examinerons les principaux éléments techniques qui composent un système de pulvérisation automatisée.
6.1. Capteurs et systèmes de contrôle
Les capteurs jouent un rôle fondamental dans les systèmes de pulvérisation automatisés, garantissant que le processus se déroule de manière précise et contrôlée. Ces capteurs surveillent les différents paramètres de l’application, tels que la pression, la température, le débit de peinture, et la distance entre le pistolet de pulvérisation et la surface à traiter. Les systèmes de contrôle automatisés utilisent ces informations pour ajuster les réglages en temps réel et assurer une application homogène.
- Capteurs de pression : Ils mesurent la pression du fluide à l’intérieur du système de pulvérisation. Une pression constante est essentielle pour garantir que le matériau pulvérisé est atomisé correctement et appliqué uniformément. Si la pression fluctue, cela peut entraîner une sur-application ou une sous-application du revêtement.
- Capteurs de débit : Ces capteurs surveillent le débit du produit pulvérisé à travers le pistolet. Ils permettent de s’assurer que la bonne quantité de peinture ou de produit est utilisée, évitant ainsi les pertes de matériau et les défauts d’application.
- Capteurs de distance : Ils mesurent la distance entre le pistolet de pulvérisation et la surface de l’objet à pulvériser. Une distance trop courte peut entraîner une surapplication, tandis qu’une distance trop longue peut provoquer un excès de pulvérisation et une perte de produit. Ces capteurs garantissent que la distance est maintenue à un niveau optimal tout au long du processus.
- Systèmes de contrôle en boucle fermée : Les systèmes automatisés modernes utilisent des boucles de rétroaction pour ajuster en permanence les paramètres de pulvérisation. Par exemple, si un capteur détecte une baisse de pression ou une variation dans la distance, le système peut automatiquement ajuster les réglages pour maintenir une qualité constante.
6.2. Logiciels de gestion de la pulvérisation
Les logiciels jouent un rôle essentiel dans la gestion des systèmes de pulvérisation automatisée. Ils permettent de programmer, contrôler et surveiller tous les aspects du processus de pulvérisation, garantissant une optimisation maximale des paramètres pour chaque type de revêtement ou de surface.
- Programmation des cycles de pulvérisation : Les logiciels permettent aux opérateurs de configurer des programmes spécifiques en fonction du type de revêtement, de la taille des pièces à traiter, et des conditions environnementales. Ces programmes peuvent inclure des réglages sur la pression, le débit, la vitesse de pulvérisation, et la température.
- Surveillance en temps réel : Les logiciels de gestion permettent de surveiller le processus en temps réel, en affichant des informations sur les performances du système et en fournissant des alertes en cas de dysfonctionnement ou de variation des paramètres. Cela permet aux opérateurs d’intervenir rapidement en cas de problème.
- Analyse des données et optimisation : En collectant des données tout au long du processus, les logiciels peuvent analyser les performances de la machine et suggérer des ajustements pour améliorer l’efficacité. Les données peuvent être utilisées pour optimiser les cycles futurs, réduisant ainsi les pertes de matériau et améliorant la qualité du revêtement.
- Maintenance prédictive : Grâce à l’analyse des données collectées par les capteurs, les logiciels de gestion peuvent anticiper les besoins en maintenance. En identifiant les anomalies ou les tendances dans les performances du système, ils peuvent alerter les opérateurs lorsque des pièces commencent à montrer des signes d’usure, permettant ainsi d’éviter les pannes imprévues.
6.3. Pistolets et buses de pulvérisation
Le pistolet de pulvérisation est le composant clé d’un système automatisé. La qualité et la précision du pistolet, ainsi que le choix des buses de pulvérisation, déterminent la qualité du revêtement appliqué. Ces éléments sont spécialement conçus pour répondre aux besoins spécifiques des différentes applications, que ce soit pour des peintures, des vernis, ou des revêtements techniques.
- Pistolets à air comprimé : Ces pistolets utilisent de l’air comprimé pour atomiser le liquide et le pulvériser sous forme de fines particules. Ce type de pistolet est souvent utilisé pour des applications nécessitant un contrôle précis de l’épaisseur du film de peinture, comme dans l’industrie automobile.
- Pistolets airless : Ces pistolets pulvérisent le liquide à haute pression sans utiliser d’air comprimé. Ils sont utilisés pour appliquer des revêtements plus épais, comme des revêtements anti-corrosion ou des matériaux visqueux. Les pistolets airless sont souvent utilisés pour couvrir de grandes surfaces rapidement.
- Buses de pulvérisation : Le choix de la buse est crucial pour garantir une application uniforme du matériau. Les buses sont disponibles en différentes tailles et formes, selon la viscosité du produit à pulvériser et la largeur du jet souhaité. Les buses à cône plein sont utilisées pour des applications où une couverture uniforme est nécessaire, tandis que les buses à jet plat sont préférées pour des applications précises sur des surfaces planes.
- Systèmes de changement de buses automatique : Certains systèmes de pulvérisation automatisés sont équipés de dispositifs permettant de changer automatiquement de buse en fonction des besoins du processus. Cela permet d’adapter rapidement les paramètres de pulvérisation pour différentes parties d’une même pièce ou pour des pièces de tailles et formes variées sans intervention manuelle.
6.4. Intégration avec d’autres processus de production
Les systèmes de pulvérisation automatisée sont souvent intégrés dans des lignes de production complètes, où ils doivent interagir avec d’autres machines et processus. Cette intégration garantit un flux de production fluide et efficace, où chaque étape, de l’application du revêtement au séchage, est parfaitement coordonnée.
- Conveyeurs automatisés : Dans les usines de production en série, les systèmes de pulvérisation automatisée sont souvent intégrés à des convoyeurs qui transportent les pièces d’une étape à l’autre. Cette coordination permet de maximiser la productivité en évitant les interruptions entre les phases de pulvérisation, de séchage, et d’inspection.
- Systèmes de séchage : Après l’application du revêtement, certaines pièces doivent passer par un processus de séchage. Les fours de polymérisation ou les systèmes de séchage infrarouge peuvent être intégrés dans la ligne de production, permettant ainsi de traiter les pièces en continu sans qu’il soit nécessaire de les manipuler manuellement.
- Inspection et contrôle de la qualité : L’intégration avec des systèmes d’inspection automatisés, tels que des caméras ou des capteurs de vision, permet de vérifier la qualité du revêtement en temps réel. Ces systèmes peuvent détecter les défauts, comme des bulles, des irrégularités, ou des manques de couverture, et ajuster automatiquement les paramètres de pulvérisation pour corriger le problème avant que les pièces ne quittent la ligne de production.
Conclusion
Les systèmes de pulvérisation automatisée reposent sur une interaction complexe entre capteurs, logiciels de gestion, pistolets de pulvérisation et autres équipements. Chaque composant technique joue un rôle clé dans la garantie d’une application précise, uniforme et efficace des revêtements, que ce soit dans l’industrie automobile, aéronautique, ou alimentaire. L’intégration de ces systèmes dans des chaînes de production plus larges permet non seulement d’améliorer la productivité, mais aussi de garantir une qualité optimale, tout en minimisant les pertes de matériau et les coûts de production. L’évolution continue des technologies de pulvérisation automatisée, notamment avec l’utilisation croissante des capteurs intelligents et des logiciels de gestion avancés, promet d’augmenter encore plus l’efficacité et la précision des processus de pulvérisation dans les années à venir.
Robots de Pulvérisation : Types et Avancées Technologiques
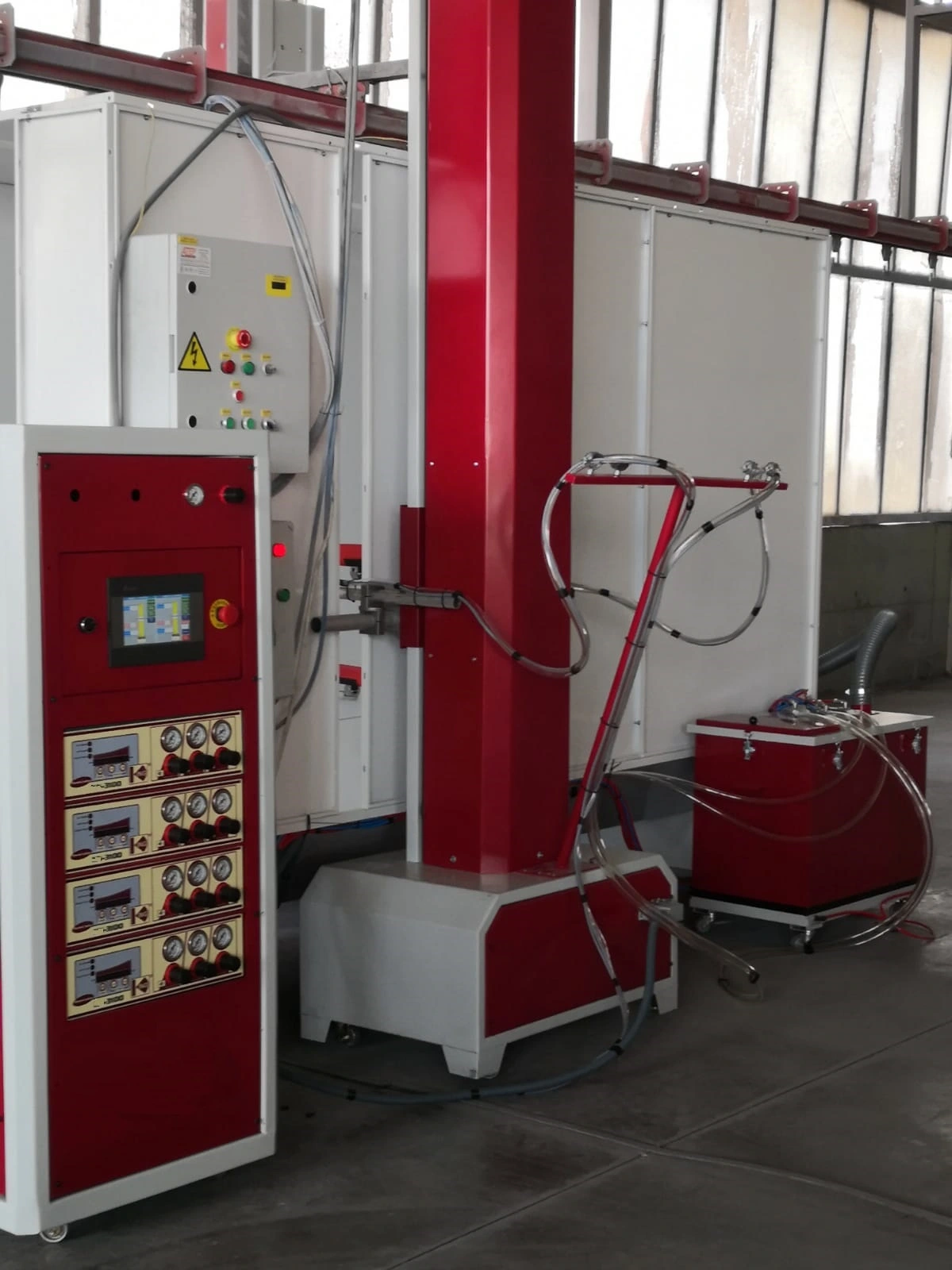
L’utilisation de robots dans les systèmes de pulvérisation automatisée a transformé les procédés industriels, offrant des niveaux de précision, d’efficacité et de répétabilité inégalés. Ces robots sont capables de pulvériser des matériaux avec une grande rapidité et une précision extrême, garantissant des finitions de haute qualité. Dans cette section, nous allons examiner les principaux types de robots de pulvérisation et les avancées technologiques qui ont permis d’améliorer ces systèmes.
7.1. Robots à bras articulés
Les robots à bras articulés sont les plus couramment utilisés dans les processus de pulvérisation automatisée, en particulier dans des industries comme l’automobile, l’aéronautique, et la fabrication de produits industriels. Ces robots sont capables de se déplacer dans plusieurs directions grâce à leurs articulations multiples, ce qui leur permet d’accéder à des zones difficiles d’accès et de pulvériser avec une précision millimétrée.
- Capacités multidimensionnelles : Les robots à bras articulés peuvent se déplacer en trois dimensions, leur permettant d’appliquer des revêtements sur des surfaces complexes, courbes, ou angulaires. Ils sont idéaux pour des pièces aux formes irrégulières, comme les carrosseries de véhicules ou les pièces d’avions.
- Programmation avancée : Ces robots peuvent être programmés pour suivre des trajectoires spécifiques, garantissant une couverture uniforme sur toute la surface à traiter. Grâce à des logiciels de gestion sophistiqués, les opérateurs peuvent ajuster la vitesse, la distance et l’angle du bras en fonction des besoins de chaque pièce.
- Flexibilité : Les robots à bras articulés peuvent être équipés de différents types de pistolets de pulvérisation (air, airless, électrostatique) en fonction des matériaux et des revêtements à appliquer. Leur flexibilité les rend adaptables à une large gamme d’applications industrielles.
7.2. Robots montés sur rails
Les robots montés sur rails sont souvent utilisés pour pulvériser de grandes surfaces planes ou des objets volumineux dans des industries telles que la construction, la peinture industrielle, ou les infrastructures métalliques. Ces robots se déplacent le long de rails, ce qui leur permet de parcourir de grandes distances tout en maintenant une application précise et régulière.
- Grande capacité de couverture : Les robots montés sur rails sont capables de couvrir de grandes surfaces avec une grande rapidité. Cela les rend particulièrement efficaces pour l’application de revêtements sur des objets tels que des bâtiments, des ponts, ou des conteneurs métalliques.
- Stabilité et précision : Le déplacement sur rails assure une grande stabilité, garantissant une application uniforme du revêtement sans tremblements ou déviations. Cette caractéristique est essentielle pour des revêtements industriels où une épaisseur régulière est cruciale pour la performance du produit final.
7.3. Robots fixes vs mobiles
Les robots de pulvérisation peuvent être fixes ou mobiles, en fonction des besoins spécifiques de l’application. Chaque type présente des avantages et des inconvénients en termes de flexibilité, de coût et d’efficacité.
- Robots fixes : Ces robots sont installés dans une position stationnaire et pulvérisent des pièces qui sont transportées devant eux via des convoyeurs ou des systèmes rotatifs. Ils sont idéaux pour des lignes de production en série où les pièces à traiter sont de tailles similaires et où la répétabilité est essentielle.
- Robots mobiles : Les robots mobiles sont capables de se déplacer autour des pièces ou des objets à traiter, ce qui leur permet de couvrir des surfaces de formes variées. Ils sont plus flexibles que les robots fixes, mais nécessitent une programmation plus complexe et un espace plus vaste pour fonctionner.
7.4. Avancées en intelligence artificielle et machine learning
L’intégration de l’intelligence artificielle (IA) et du machine learning (apprentissage automatique) dans les robots de pulvérisation représente une avancée majeure. Ces technologies permettent aux robots d’apprendre et d’adapter leur comportement en fonction des données recueillies tout au long du processus de pulvérisation.
- Optimisation en temps réel : Les robots équipés d’IA peuvent analyser les données recueillies par les capteurs en temps réel et ajuster automatiquement les paramètres de pulvérisation pour optimiser l’application du revêtement. Par exemple, si une zone est détectée comme sous-couverte, le robot peut ajuster sa trajectoire ou augmenter le débit de pulvérisation pour corriger l’erreur immédiatement.
- Apprentissage basé sur l’expérience : Grâce au machine learning, les robots peuvent améliorer leurs performances au fil du temps en apprenant à partir des cycles de production précédents. Ils peuvent identifier les tendances et les anomalies, et ajuster leurs actions pour éviter les erreurs récurrentes.
- Détection des défauts : L’IA permet aux robots de détecter des défauts tels que des bulles, des irrégularités ou des écarts dans l’épaisseur du revêtement, et de réagir instantanément pour corriger ces erreurs. Cela permet de minimiser les rejets et d’améliorer la qualité globale des produits finis.
Conclusion
Les robots de pulvérisation ont révolutionné les processus industriels, offrant des niveaux de précision, d’efficacité et de flexibilité inégalés. Les robots à bras articulés, montés sur rails, et fixes ou mobiles, offrent des solutions adaptées à une large gamme d’applications, des carrosseries automobiles aux infrastructures métalliques. Les avancées en intelligence artificielle et en machine learning ont permis d’augmenter encore l’efficacité et la qualité des robots de pulvérisation, les rendant capables d’optimiser leur performance en temps réel et d’apprendre de leurs expériences. Alors que la technologie continue de progresser, les robots de pulvérisation joueront un rôle encore plus important dans l’amélioration des processus de production industriels, offrant des solutions de plus en plus intelligentes et adaptatives.
Intégration de l’Industrie 4.0 et de l’Internet des Objets (IoT) dans la Pulvérisation Automatisée
L’intégration des technologies de l’Industrie 4.0 et de l’Internet des objets (IoT) dans la pulvérisation automatisée a permis aux entreprises de transformer leurs processus de production en des systèmes intelligents, interconnectés et hautement optimisés. L’Industrie 4.0 fait référence à la digitalisation des processus industriels, permettant aux machines et aux systèmes de communiquer entre eux pour maximiser l’efficacité, améliorer la qualité, et réduire les coûts. L’IoT, de son côté, connecte les équipements via des capteurs et des réseaux, facilitant le suivi en temps réel et la prise de décision basée sur les données. Dans cette section, nous explorerons comment l’intégration de ces technologies révolutionne la pulvérisation automatisée.
8.1. Collecte de données et contrôle en temps réel
L’un des avantages majeurs de l’intégration de l’IoT dans les systèmes de pulvérisation automatisée est la capacité à collecter des données en temps réel à partir des équipements. Ces données sont essentielles pour optimiser les performances des machines et garantir une qualité constante tout au long du processus.
- Capteurs intelligents : Les capteurs installés sur les systèmes de pulvérisation mesurent divers paramètres, tels que la pression, la température, le débit de matériau, et la distance entre le pistolet de pulvérisation et la surface. Ces capteurs transmettent ensuite les données à des systèmes de gestion centralisés via des réseaux IoT.
- Suivi et ajustements en temps réel : Grâce à la collecte de données en temps réel, les opérateurs peuvent surveiller en continu les performances du système et effectuer des ajustements si nécessaire. Si un capteur détecte un écart par rapport aux paramètres de pulvérisation programmés (par exemple, une baisse de pression ou un excès de produit appliqué), le système peut ajuster automatiquement ces paramètres pour garantir une qualité optimale.
- Prise de décision automatisée : En s’appuyant sur des algorithmes intelligents, les systèmes de pulvérisation automatisée peuvent prendre des décisions autonomes basées sur les données recueillies. Cela inclut l’ajustement automatique des cycles de pulvérisation, l’activation ou l’arrêt de certaines fonctions en fonction des besoins, et la correction des erreurs avant qu’elles ne deviennent problématiques.
8.2. Maintenance prédictive via l’IoT
L’intégration de l’IoT dans la pulvérisation automatisée a ouvert la voie à la maintenance prédictive, une approche qui permet de surveiller l’état des équipements en temps réel et d’anticiper les pannes ou les dysfonctionnements avant qu’ils ne surviennent.
- Analyse des données : Les capteurs intelligents installés sur les systèmes de pulvérisation collectent des données sur les performances des équipements (comme les vibrations, la température des composants, ou la pression interne). Ces données sont ensuite analysées pour identifier des schémas qui pourraient indiquer des signes de défaillance imminente.
- Prédiction des pannes : Grâce aux technologies d’intelligence artificielle et de machine learning, les systèmes sont capables de prévoir les pannes potentielles en se basant sur les données historiques et actuelles. Par exemple, si un capteur détecte des vibrations inhabituelles dans un robot de pulvérisation, cela peut indiquer que certains composants commencent à s’user. Le système peut alors alerter les opérateurs pour qu’ils effectuent une maintenance avant que la machine ne tombe en panne.
- Réduction des temps d’arrêt : En anticipant les pannes et en effectuant des réparations avant qu’elles ne deviennent critiques, la maintenance prédictive réduit considérablement les temps d’arrêt imprévus, ce qui permet de maintenir la continuité de la production et d’améliorer la productivité globale.
8.3. Optimisation des processus grâce à l’IA
L’intelligence artificielle (IA) joue un rôle clé dans l’optimisation des systèmes de pulvérisation automatisée, en permettant aux machines de prendre des décisions basées sur l’analyse de données complexes et d’ajuster les processus pour améliorer l’efficacité et la qualité.
- Optimisation des paramètres de pulvérisation : Les systèmes équipés d’IA peuvent analyser en temps réel les performances de la pulvérisation et ajuster automatiquement les paramètres, tels que la vitesse de pulvérisation, le débit de produit ou la distance du pistolet. Cela garantit que chaque application est optimisée pour minimiser les pertes de produit tout en garantissant une couverture uniforme et une épaisseur constante du revêtement.
- Apprentissage automatique : Grâce au machine learning, les systèmes de pulvérisation peuvent apprendre des cycles de production passés et s’améliorer avec le temps. Par exemple, si un défaut récurrent est détecté dans le processus, l’IA peut ajuster les paramètres pour éviter que ce défaut ne se reproduise.
- Amélioration continue : L’IA permet aux systèmes de pulvérisation de constamment rechercher des moyens d’améliorer les processus en fonction des données recueillies. Les systèmes peuvent analyser des milliers de cycles de pulvérisation pour identifier des inefficacités ou des anomalies subtiles et apporter des ajustements pour maximiser l’efficacité, réduire les coûts et améliorer la qualité du produit fini.
8.4. Surveillance à distance et connectivité
Avec l’IoT et l’Industrie 4.0, les systèmes de pulvérisation automatisée peuvent être surveillés et contrôlés à distance, offrant ainsi aux entreprises une flexibilité et une réactivité accrues.
- Surveillance à distance : Les données des capteurs peuvent être accessibles à distance via des tableaux de bord connectés, permettant aux opérateurs de surveiller les performances des systèmes de pulvérisation, même s’ils ne sont pas physiquement présents sur le site de production. Cette capacité est particulièrement utile pour les grandes installations où les machines de pulvérisation sont réparties sur différents sites ou zones.
- Contrôle à distance : Les opérateurs peuvent ajuster les paramètres de pulvérisation ou démarrer/arrêter les machines à distance via des systèmes connectés. Cela permet de réagir rapidement aux problèmes sans avoir besoin d’être sur place, améliorant ainsi l’efficacité et la réactivité.
- Notifications et alertes en temps réel : En cas de dysfonctionnement ou de variation dans les performances des équipements, les systèmes de gestion peuvent envoyer des notifications en temps réel aux opérateurs, qu’ils soient sur place ou à distance. Cela permet de réagir rapidement pour corriger les erreurs avant qu’elles ne perturbent le processus de production.
8.5. Avantages de l’intégration de l’Industrie 4.0 et de l’IoT
L’intégration de l’Industrie 4.0 et de l’IoT dans les systèmes de pulvérisation automatisée offre de nombreux avantages pour les entreprises, tant en termes de productivité que de qualité et de réduction des coûts.
- Efficacité accrue : Grâce à la collecte de données en temps réel et à l’optimisation des processus, les systèmes de pulvérisation automatisée deviennent plus efficaces, réduisant les temps d’arrêt, les pertes de produit et les défauts de fabrication.
- Amélioration de la qualité : L’utilisation de capteurs et de technologies d’IA permet d’améliorer la qualité des revêtements appliqués, en garantissant une épaisseur uniforme et une couverture parfaite, même sur des surfaces complexes.
- Réduction des coûts : En optimisant les processus, les entreprises peuvent réduire leurs coûts liés à la consommation de matériaux, à la maintenance, et aux arrêts imprévus. La maintenance prédictive, en particulier, permet d’économiser des coûts importants en évitant les pannes et en prolongeant la durée de vie des équipements.
- Flexibilité et adaptabilité : Les systèmes de pulvérisation connectés peuvent être ajustés rapidement pour s’adapter à différents produits ou types de revêtements, offrant une grande flexibilité aux entreprises qui ont besoin de s’adapter à des exigences de production variables.
Conclusion
L’intégration de l’Industrie 4.0 et de l’Internet des objets dans les systèmes de pulvérisation automatisée a transformé la manière dont les entreprises gèrent leurs processus de pulvérisation. Grâce à la collecte de données en temps réel, à la maintenance prédictive, à l’optimisation des processus via l’IA, et à la surveillance à distance, les systèmes sont désormais plus efficaces, plus intelligents et plus flexibles que jamais. Ces avancées technologiques permettent aux entreprises d’améliorer la qualité, de réduire les coûts, et de rester compétitives dans un environnement industriel de plus en plus axé sur la performance et l’innovation.
Sélection d’un Système de Pulvérisation Automatisée : Critères et Facteurs
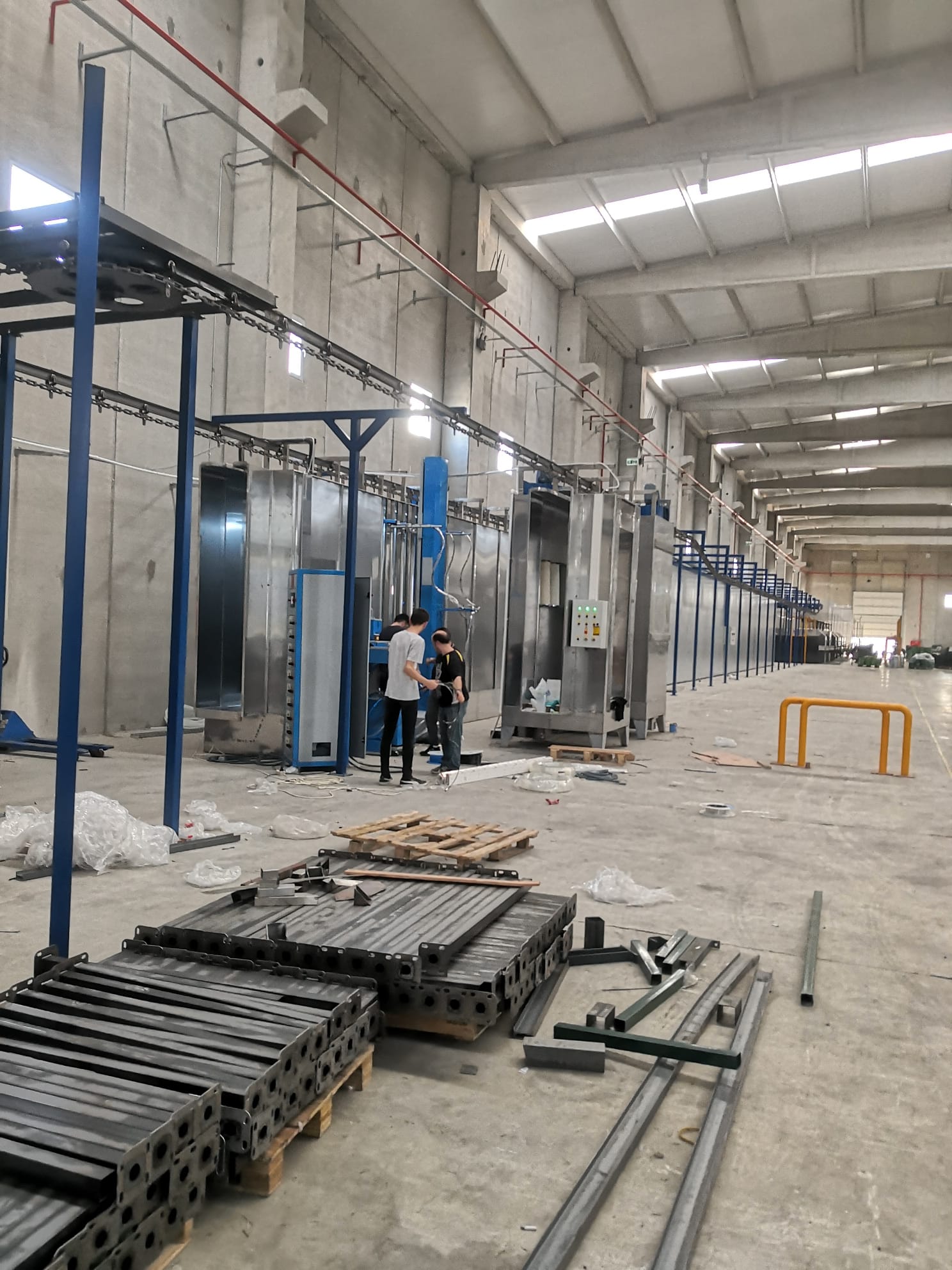
Le choix d’un système de pulvérisation automatisée est une décision stratégique pour les entreprises qui cherchent à optimiser leurs processus de production. Il existe plusieurs critères à prendre en compte pour s’assurer que le système choisi correspond aux besoins spécifiques de l’entreprise. Cette section présente les principaux facteurs à considérer pour la sélection d’un système de pulvérisation automatisée.
9.1. Type de production : petite série ou grande série
La première question à se poser lors du choix d’un système de pulvérisation automatisée est de savoir si l’entreprise se concentre sur la production en grande série ou en petite série. Les besoins en matière de vitesse, de flexibilité et d’automatisation varieront considérablement en fonction du volume de production.
- Grande série : Les entreprises produisant de grandes quantités de pièces identiques bénéficieront de systèmes automatisés capables de traiter de grands volumes avec une répétabilité élevée. Dans ces cas, l’efficacité, la vitesse, et la capacité à intégrer le système dans une ligne de production continue seront des critères clés.
- Petite série : Pour les productions en petites séries ou des pièces personnalisées, la flexibilité et l’adaptabilité du système seront plus importantes. Un système de pulvérisation automatisé capable de s’ajuster rapidement à différents types de pièces et de revêtements sera un atout pour répondre à la diversité des demandes.
9.2. Types de revêtements et matériaux à pulvériser
Le type de revêtement et le matériau à pulvériser auront également un impact sur la sélection du système. Certains systèmes de pulvérisation sont plus adaptés à des matériaux spécifiques, tandis que d’autres sont conçus pour une utilisation polyvalente.
- Revêtements liquides ou en poudre : Les systèmes de pulvérisation peuvent être conçus pour appliquer des revêtements liquides (peintures, vernis, revêtements anticorrosion) ou des revêtements en poudre. Les systèmes doivent être choisis en fonction du type de revêtement utilisé.
- Compatibilité avec différents matériaux : Certaines pièces nécessitent des revêtements spécifiques en fonction de leur matériau (métal, plastique, composite, etc.). Le système de pulvérisation doit être compatible avec le matériau à traiter pour garantir une application uniforme et durable du revêtement.
9.3. Compatibilité avec les lignes de production existantes
L’intégration du système de pulvérisation dans une ligne de production existante est un facteur clé pour éviter des modifications coûteuses ou des interruptions prolongées du processus de production.
- Systèmes de convoyage et d’automatisation : Si l’entreprise dispose déjà de systèmes de convoyage ou de robots dans sa ligne de production, il est essentiel de s’assurer que le nouveau système de pulvérisation est compatible avec ces équipements. L’interopérabilité permet de réduire les coûts d’installation et d’optimiser le flux de production.
- Espace disponible : La taille et la disposition des équipements de pulvérisation doivent également correspondre à l’espace disponible dans l’usine. Les entreprises doivent s’assurer que le système peut être installé sans perturber les autres opérations.
9.4. Coût d’acquisition et de maintenance
Le coût total d’un système de pulvérisation automatisée ne se limite pas à l’achat initial de l’équipement. Les coûts de maintenance, de formation et d’exploitation doivent également être pris en compte pour évaluer la rentabilité à long terme du système.
- Investissement initial : Le coût d’achat des robots de pulvérisation, des pistolets et des systèmes de gestion peut varier considérablement en fonction des technologies choisies et de la taille de l’installation.
- Coûts de maintenance : Les systèmes automatisés nécessitent un entretien régulier pour garantir leur bon fonctionnement. Les entreprises doivent évaluer les coûts de maintenance à long terme, y compris la maintenance préventive, les réparations et le remplacement des pièces usées.
9.5. Flexibilité pour différents produits et applications
Enfin, il est essentiel de choisir un système de pulvérisation automatisée qui offre une flexibilité suffisante pour répondre aux besoins actuels et futurs de l’entreprise.
- Adaptabilité à différents produits : Si l’entreprise produit une large gamme de produits ou doit appliquer différents types de revêtements, le système de pulvérisation doit être suffisamment flexible pour s’adapter à cette diversité sans nécessiter de changements majeurs ou coûteux.
- Programmation et personnalisation : Les systèmes offrant une programmation avancée permettent d’ajuster facilement les paramètres en fonction des pièces et des matériaux traités. Cela permet aux entreprises de personnaliser les cycles de pulvérisation et d’optimiser l’application des revêtements pour chaque type de produit.
Conclusion
La sélection d’un système de pulvérisation automatisée repose sur une évaluation minutieuse des besoins de production, des matériaux et revêtements utilisés, ainsi que des exigences spécifiques en termes de coût, de flexibilité et d’intégration dans la ligne de production. En tenant compte de ces facteurs, les entreprises peuvent choisir un système qui optimise leur productivité, améliore la qualité de leurs produits, et réduit les coûts à long terme. Un investissement bien planifié dans la pulvérisation automatisée permet d’améliorer la compétitivité de l’entreprise tout en offrant une solution flexible et adaptable aux besoins changeants du marché.
Non seulement nous fabriquons nos équipements de revêtement en poudre, mais nous les expédions également dans vos locaux avec soin dans le monde entier.
Nous ne sommes pas seulement les fabricants de vos équipements de revêtement en poudre, nous sommes également vos partenaires de livraison dans le monde entier.
Chez EMS Powder Coating Equipment, nous comprenons qu’il est tout aussi important de vous fournir votre équipement de revêtement en poudre rapidement et en toute sécurité que de le fabriquer selon les normes les plus élevées. C’est pourquoi nous proposons des services de livraison dans le monde entier à tous nos clients.
Nous travaillons avec un réseau de partenaires maritimes expérimentés et fiables pour garantir que votre équipement arrive à temps et en parfait état. Nous proposons également une variété d’options d’expédition adaptées à votre budget et à vos besoins.
Que vous ayez besoin d’expédier votre équipement à une adresse locale ou vers une destination internationale, nous pouvons vous aider. Nous travaillerons avec vous pour choisir la meilleure option d’expédition pour vos besoins et pour vous tenir informé de l’état de votre envoi à chaque étape du processus.
Ainsi, lorsque vous choisissez EMS pour votre équipement de revêtement en poudre, vous obtenez non seulement les meilleurs produits du marché, mais vous bénéficiez également de la meilleure expérience de livraison possible.
Contactez-nous dès aujourd’hui pour en savoir plus sur nos services de livraison dans le monde entier.
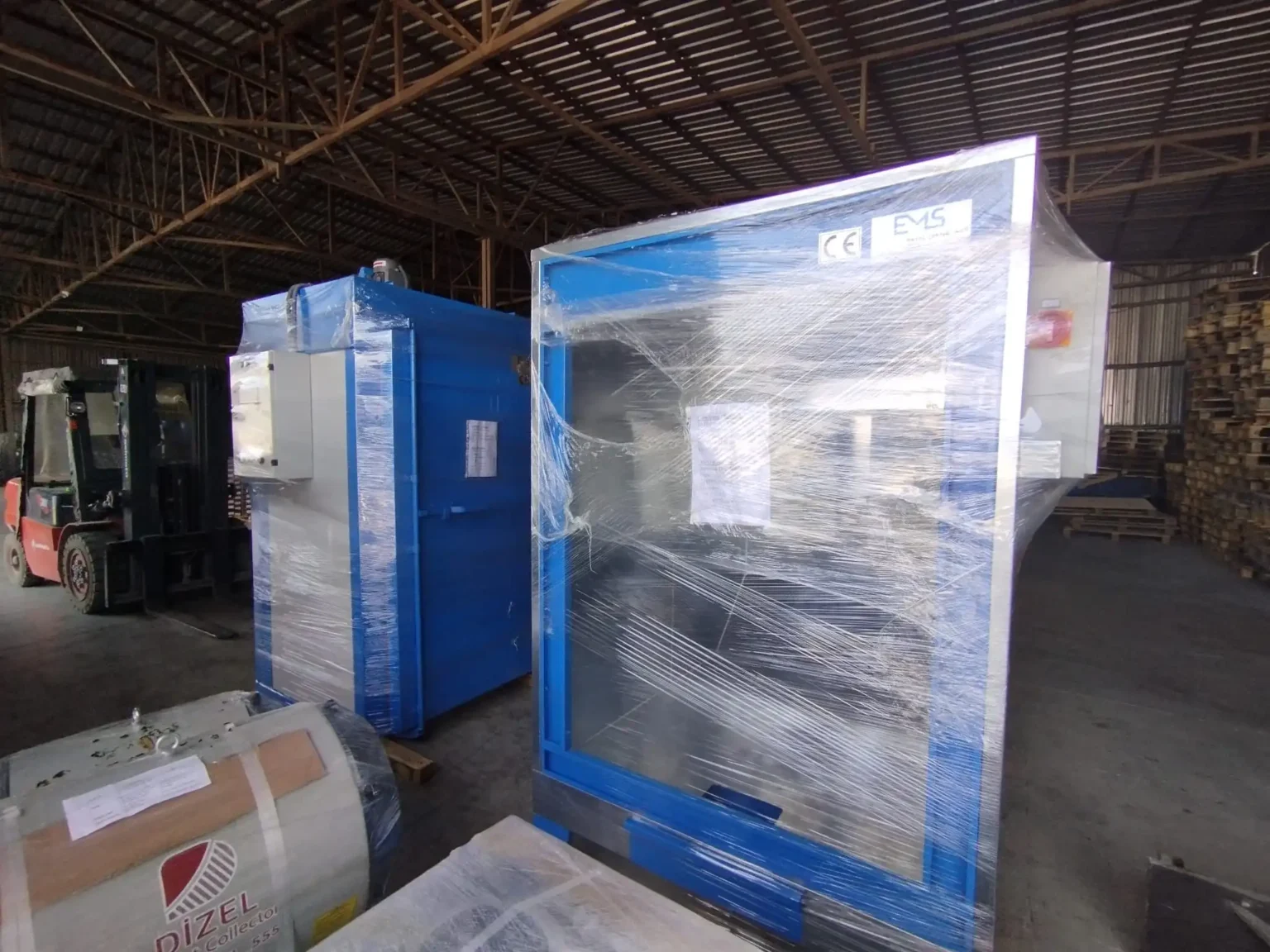

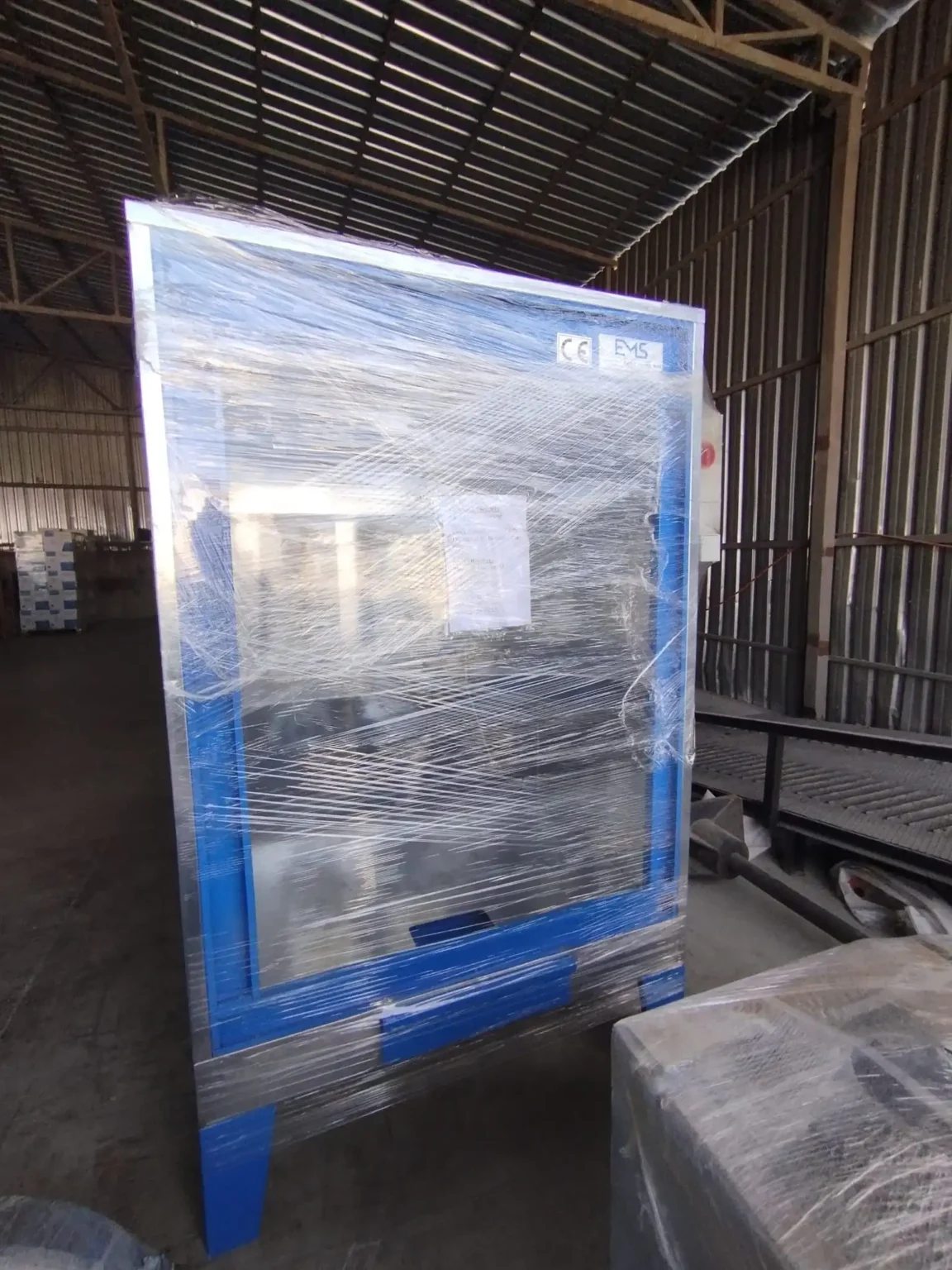
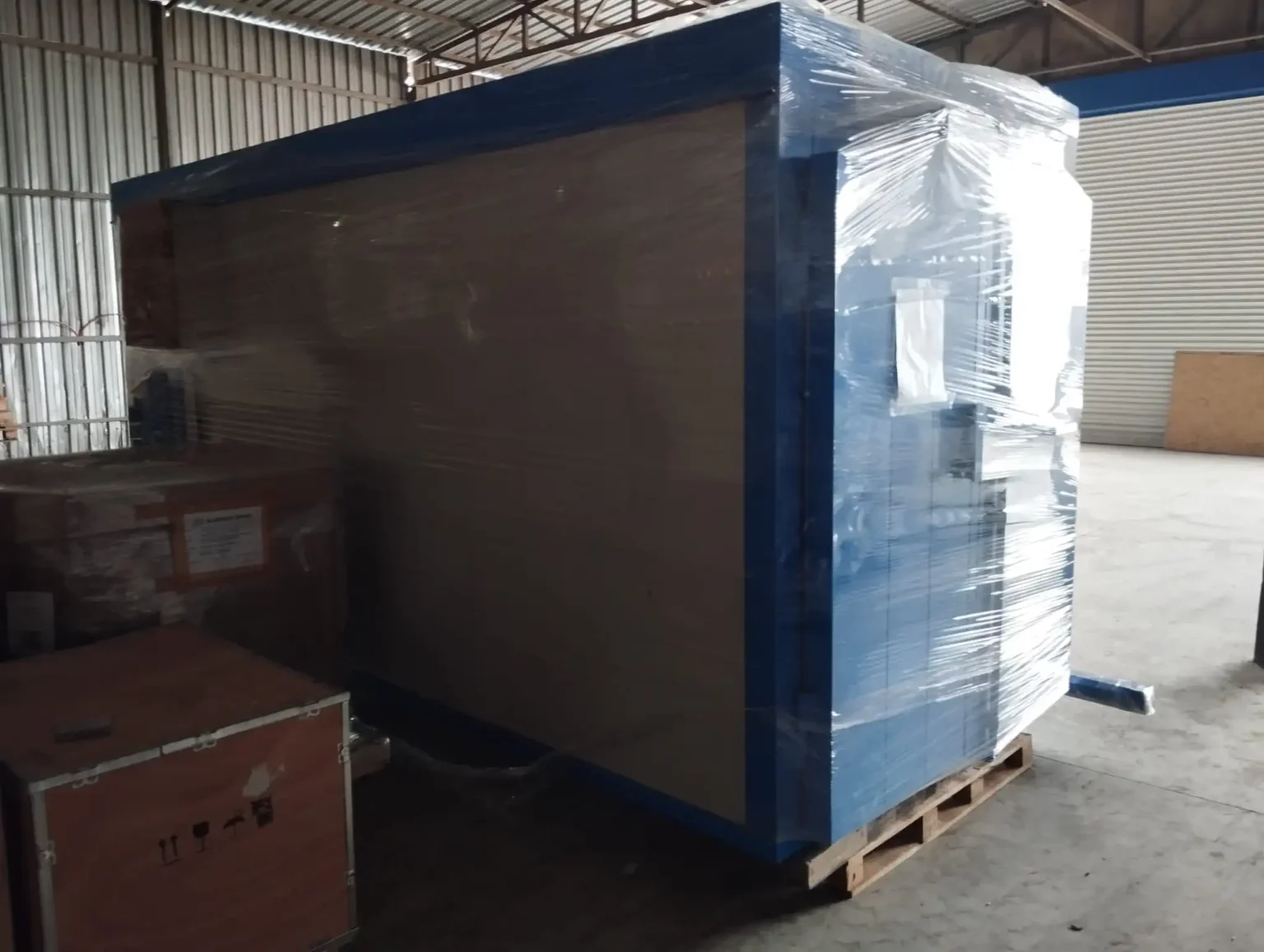
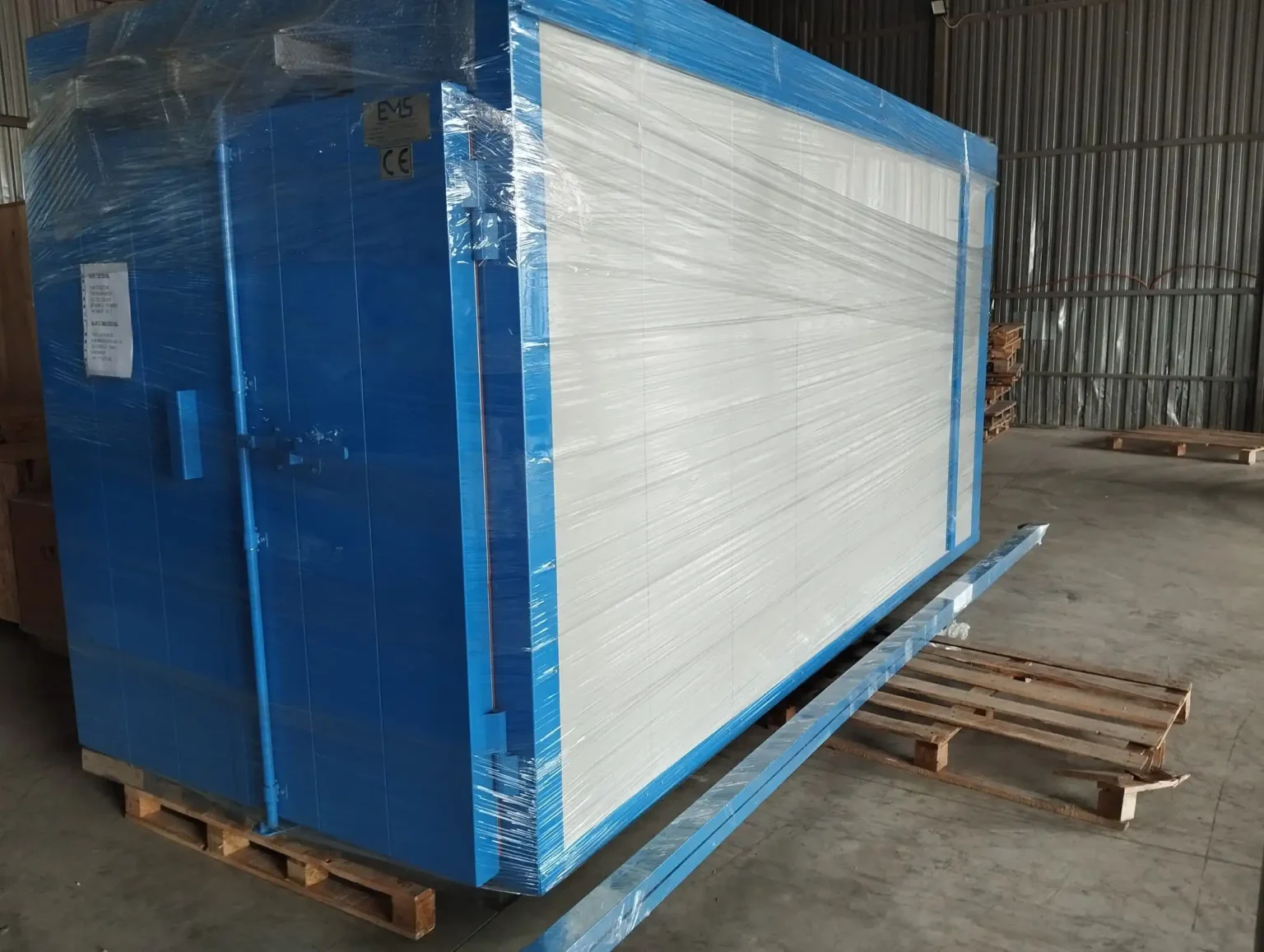
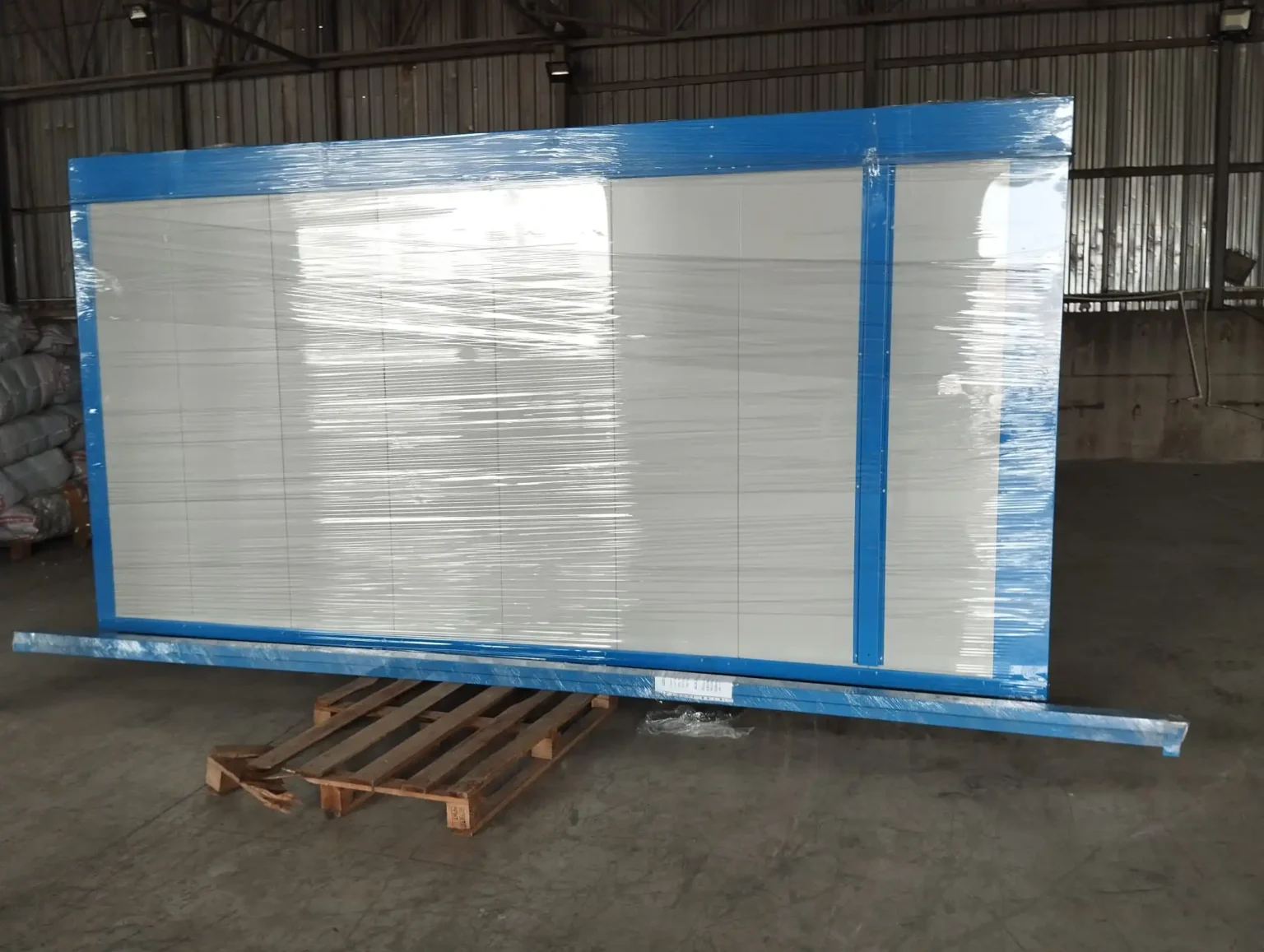
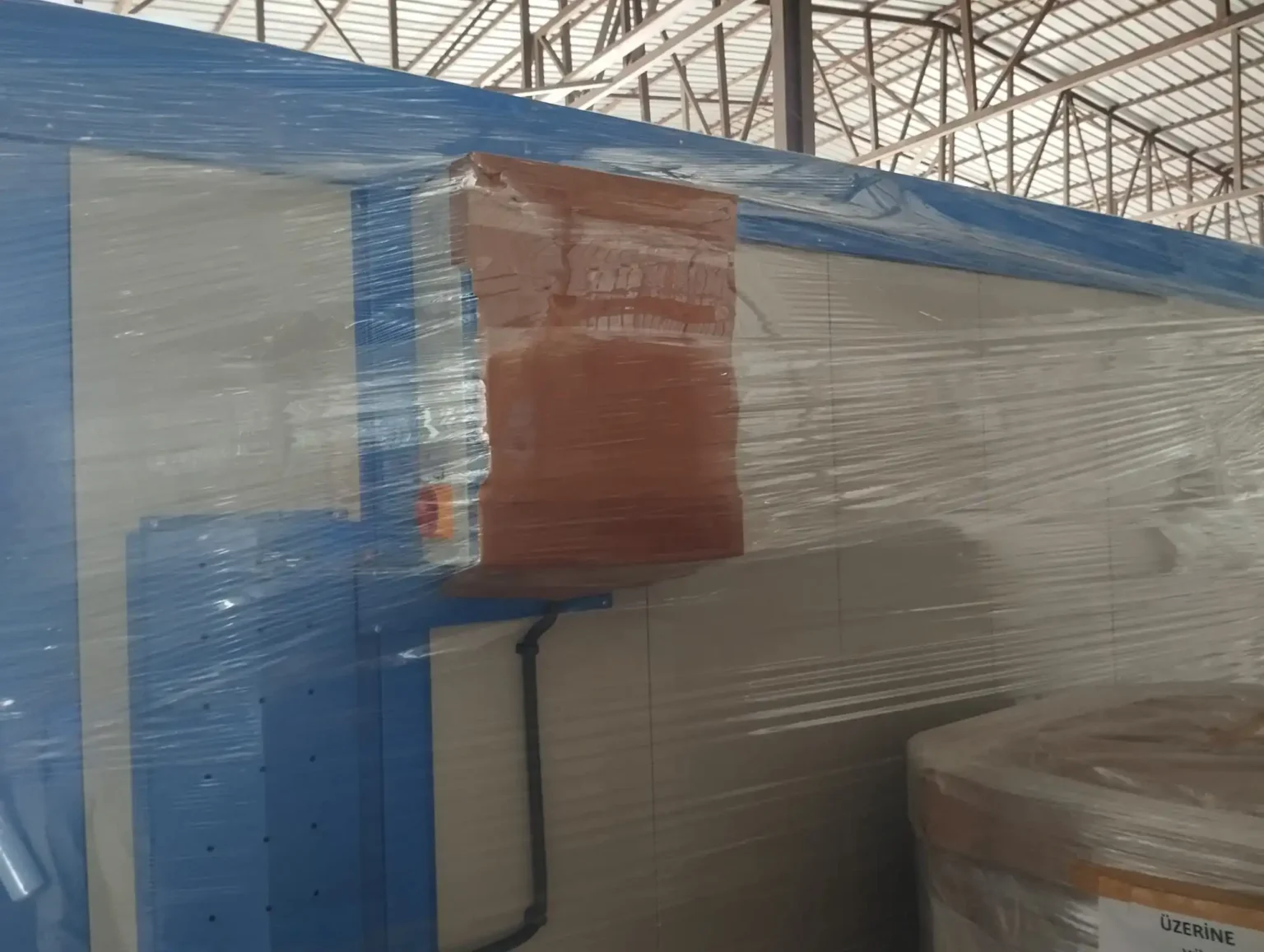
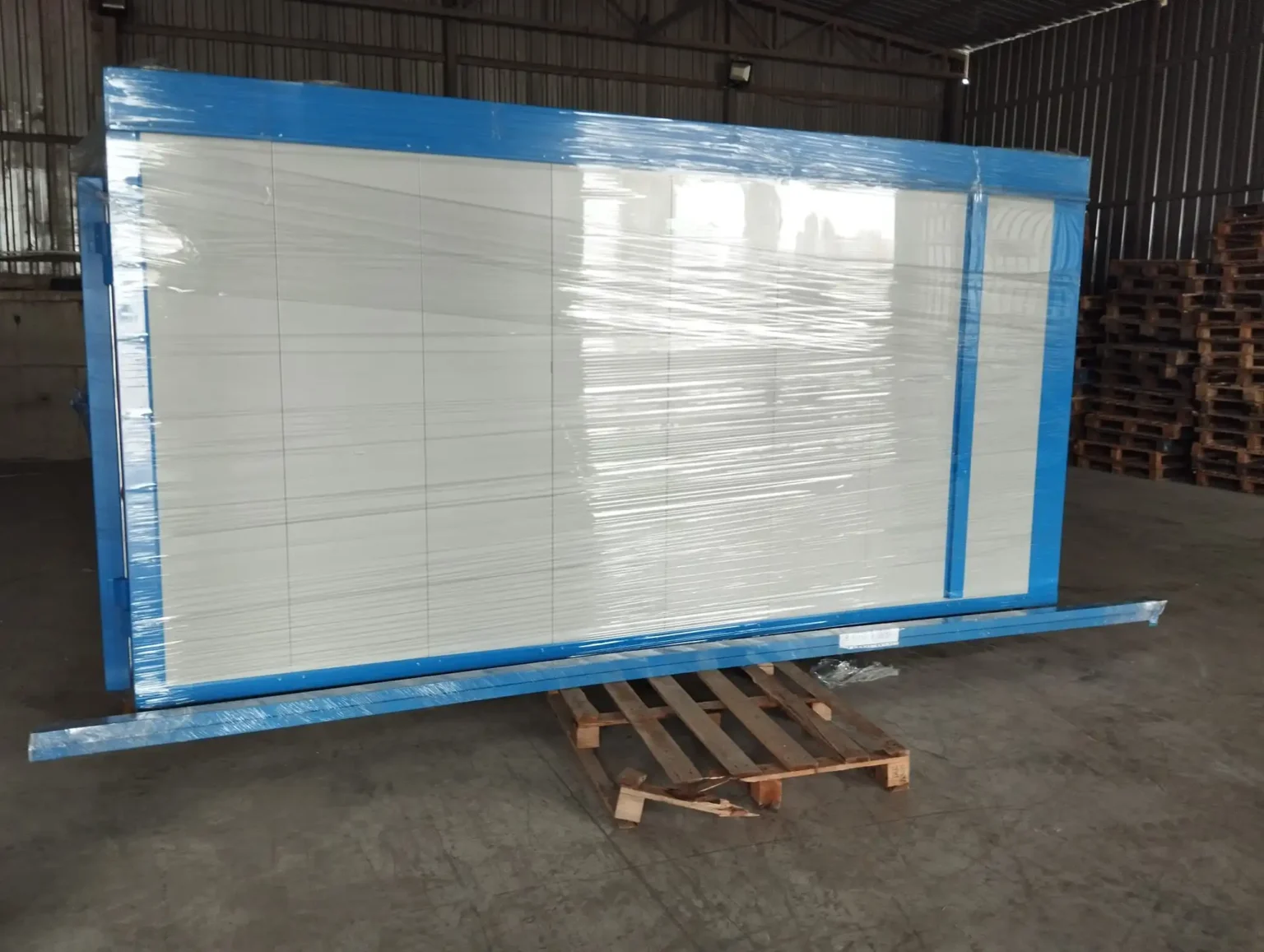
L’équipement de revêtement en poudre est utilisé pour appliquer une fine couche de poudre sur une surface métallique. Ce type de revêtement est appliqué par un procédé électrostatique et constitue une méthode très populaire pour la finition des pièces métalliques.
Ce type d’équipement peut être divisé en deux grandes catégories : automatiques et manuels. Les cabines automatiques sont plus populaires car elles offrent de meilleurs taux de production, mais elles sont également plus chères.
Une cabine à poudre est une enceinte dans laquelle se déroule le processus de revêtement en poudre. L’équipement de revêtement en poudre comprend un four dans lequel les pièces sont chauffées pour activer la poudre, un pistolet qui pulvérise ou brosse la poudre, une bande transporteuse qui déplace les pièces à travers le four et des pistolets de type cartouche pour appliquer des revêtements plus épais avec moins de pulvérisation.
Le revêtement en poudre est une technique utilisée pour donner une finition aux pièces métalliques. Cette technique est utilisée depuis de nombreuses années et reste aujourd’hui l’une des techniques les plus populaires.
L’équipement de revêtement en poudre comprend des cabines, des fours, des pistolets, des machines, des lignes et des convoyeurs. Une cabine peut être automatique ou manuelle. Une cabine automatique est plus chère qu’une cabine manuelle mais elle est aussi plus rapide et plus efficace