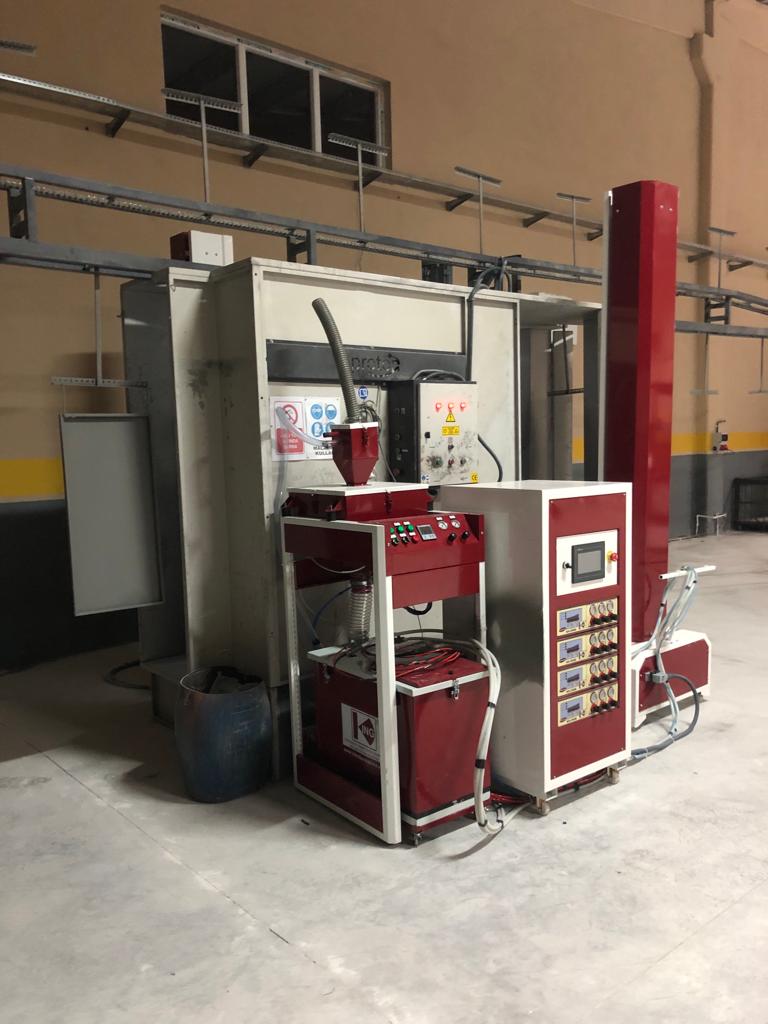
Installation Automatisée de Peinture en Poudre: Une ligne industrielle de peinture en poudre automatique est un système automatisé utilisé dans les processus de peinture pour appliquer de la peinture en poudre sur des surfaces métalliques, souvent dans des environnements de production à grande échelle. Ce type de ligne est très couramment utilisé dans des industries telles que l’automobile, la construction, l’électroménager, et l’ameublement en métal.
Voici un aperçu des étapes clés d’une ligne industrielle de peinture en poudre automatique :
- Prétraitement de la surface : Avant d’appliquer la peinture en poudre, les pièces métalliques sont souvent nettoyées et préparées pour garantir une bonne adhérence de la peinture. Cela peut inclure des étapes de dégraissage, de phosphatation ou d’activation de la surface.
- Application de la peinture en poudre : La peinture en poudre est appliquée sur la pièce via des pistolets électrostatiques. Ces pistolets chargent la poudre qui est ensuite attirée par la surface métallique en raison de la différence de charge électrique. Cette méthode permet une application uniforme de la poudre.
- Cuisson : Après l’application, les pièces peintes sont passées dans un four de cuisson à une température spécifique (généralement entre 160 et 200°C), où la peinture en poudre fond et se durcit, formant ainsi une finition résistante et durable.
- Refroidissement et contrôle de la qualité : Une fois la peinture durcie, les pièces sont refroidies et soumises à un contrôle de qualité pour vérifier l’uniformité de la finition, l’adhérence et la résistance.
- Emballage ou expédition : Après avoir passé le contrôle de qualité, les pièces finies sont prêtes à être emballées ou envoyées à leur destination finale.
Avantages des lignes automatiques de peinture en poudre :
- Efficacité énergétique : Moins de gaspillage de peinture, car la poudre peut être recyclée.
- Respect de l’environnement : La peinture en poudre ne contient pas de solvants, ce qui réduit les émissions volatiles organiques (COV).
- Finition durable : La peinture en poudre offre une finition résistante aux chocs, aux rayures et aux intempéries.
- Automatisation : Permet une production de masse avec un minimum d’intervention humaine, réduisant ainsi les coûts de main-d’œuvre.
A ligne industrielle de peinture en poudre automatique est un système utilisé pour appliquer de la peinture en poudre sur des surfaces métalliques dans un environnement industriel à grande échelle. Ce type de ligne automatise l’application de peinture, ce qui permet de traiter une grande quantité de pièces avec une finition de haute qualité. Le processus commence généralement par un prétraitement des pièces, où elles sont nettoyées et préparées pour garantir que la peinture adhère correctement. Ce prétraitement peut inclure des étapes comme le dégraissage ou la phosphatation des surfaces métalliques.
Ensuite, la peinture en poudre est appliquée à l’aide de pistolets électrostatiques. Ces pistolets chargent la peinture en poudre, qui est ensuite attirée par la pièce métallique, assurant ainsi une couverture uniforme et une application efficace. Une fois la poudre appliquée, les pièces sont passées dans un four où la peinture est chauffée à une température élevée, ce qui la fait fondre et durcir pour créer une finition solide et résistante. Ce processus de cuisson est crucial pour garantir la durabilité de la finition.
Après la cuisson, les pièces sont refroidies avant de passer par un contrôle de qualité, où des tests sont effectués pour s’assurer que la peinture est uniforme et que la finition répond aux normes de résistance et d’adhérence. Une fois ces étapes validées, les pièces finies sont prêtes à être emballées ou expédiées à leur destination.
L’un des principaux avantages d’une ligne de peinture en poudre automatique est qu’elle permet de réduire le gaspillage de peinture, car la poudre excédentaire peut être récupérée et réutilisée. De plus, la peinture en poudre est plus écologique que les peintures à base de solvant, car elle ne contient pas de composés organiques volatils (COV). La finition obtenue est également très durable, offrant une résistance accrue aux rayures, aux chocs et aux conditions climatiques. En automatisant le processus, une ligne de peinture en poudre permet d’augmenter la productivité et de réduire les coûts de main-d’œuvre, tout en maintenant une qualité constante et élevée.
Une autre caractéristique importante des lignes industrielles de peinture en poudre automatiques est leur flexibilité. Ces systèmes peuvent être ajustés pour traiter une variété de pièces de différentes tailles et formes, ce qui les rend adaptées à une gamme d’applications industrielles. Par exemple, dans l’industrie automobile, ces lignes sont utilisées pour peindre des pièces comme des châssis, des jantes et des panneaux de carrosserie, tandis que dans l’électroménager, elles sont utilisées pour des éléments tels que des réfrigérateurs, des cuisinières et des climatiseurs.
La précision et la constance de l’application de la peinture en poudre permettent également de garantir que les pièces finies sont homogènes en termes de couleur et de texture. Le contrôle de la quantité de poudre utilisée, associé à des techniques d’application avancées, permet de minimiser les défauts visuels, tels que les coulures ou les zones non couvertes, qui peuvent parfois être un problème dans les applications de peinture manuelle.
De plus, les technologies modernes utilisées dans ces lignes de production permettent d’intégrer des systèmes de contrôle et de surveillance avancés. Par exemple, des capteurs et des caméras peuvent être utilisés pour vérifier en temps réel la qualité de l’application de la peinture. En cas de problème, des ajustements automatiques peuvent être effectués pour éviter les erreurs. Ces systèmes peuvent également être connectés à un logiciel de gestion de production, permettant une gestion et un suivi en temps réel des différentes étapes de la ligne, de l’application de la peinture à la cuisson.
L’impact sur l’efficacité de la production est également significatif. La vitesse et la précision de l’application de la peinture en poudre, combinées à des systèmes de cuisson rapide, permettent d’augmenter la capacité de production tout en maintenant une qualité constante. Cela signifie que les délais de production sont considérablement réduits, ce qui est un avantage majeur pour les entreprises qui doivent répondre à une demande élevée ou gérer des volumes de production importants.
Enfin, l’automatisation complète du processus réduit considérablement le risque d’erreurs humaines et améliore la sécurité de l’environnement de travail. Moins de manipulation manuelle des produits et des produits chimiques signifie moins d’accidents et de risques pour les opérateurs, et les lignes de peinture peuvent être équipées de systèmes de filtration pour gérer les émissions de chaleur et de poussière, améliorant ainsi l’environnement de travail.
En résumé, une ligne industrielle de peinture en poudre automatique optimise à la fois l’efficacité, la qualité et la sécurité, tout en étant plus respectueuse de l’environnement. Elle permet aux entreprises d’assurer une production en grande série avec une finition uniforme et durable, tout en réduisant les coûts et en augmentant la productivité.
Système de revêtement en poudre à commande automatique
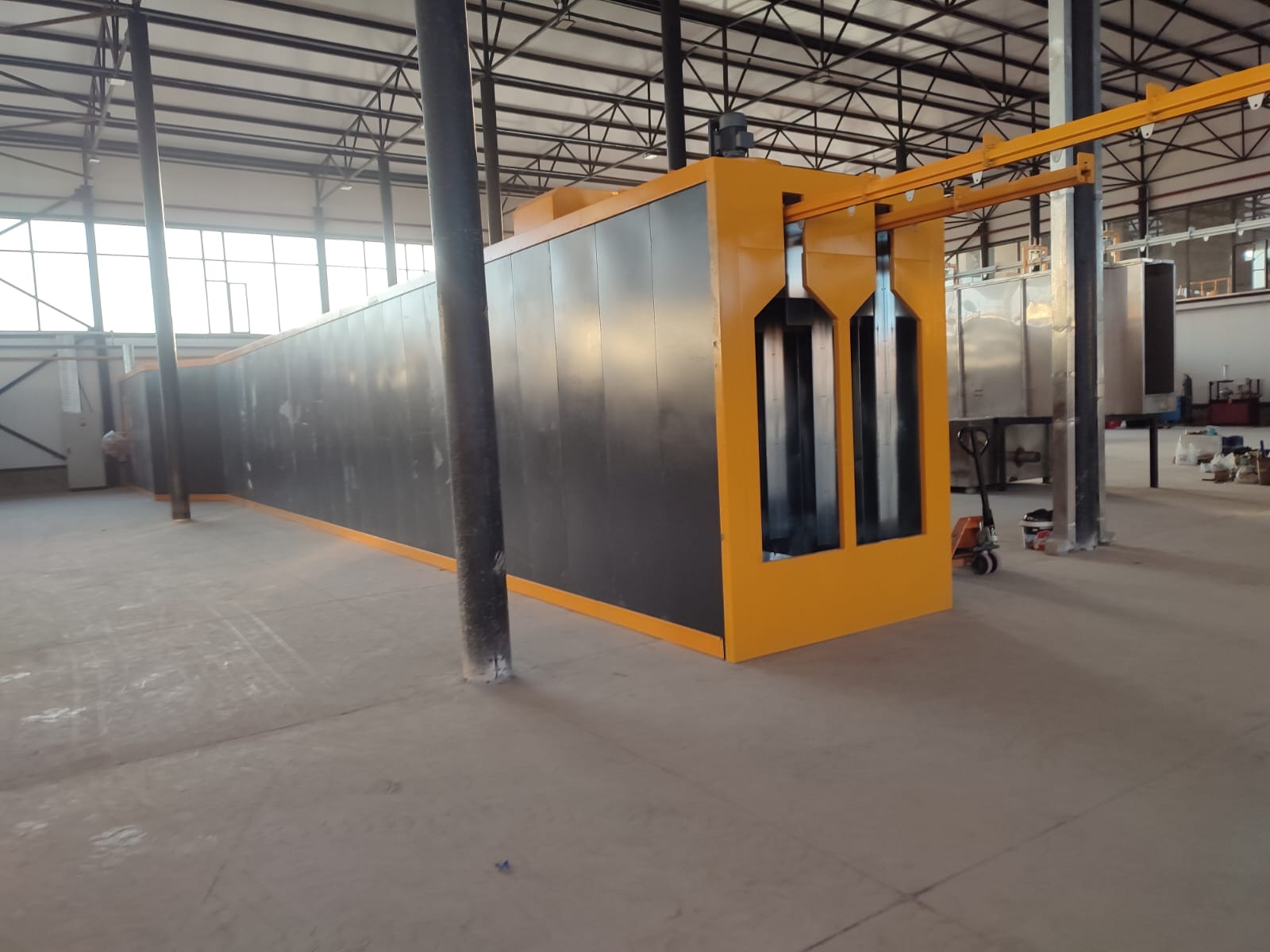
Un système de revêtement en poudre à commande automatique est une installation industrielle qui applique de la peinture en poudre sur des pièces métalliques de manière entièrement automatisée, garantissant un processus de finition cohérent et de haute qualité. Ces systèmes sont utilisés dans de nombreuses industries pour appliquer des couches de peinture durables sur des produits en métal, offrant ainsi une protection contre la corrosion, les intempéries et l’usure.
Un tel système se compose généralement de plusieurs éléments clés qui fonctionnent ensemble pour garantir une application optimale de la peinture en poudre :
- Système de préparation des pièces : Avant de pouvoir appliquer la peinture en poudre, les pièces doivent être soigneusement préparées. Cela inclut des étapes de nettoyage et de dégraissage, souvent suivies par un traitement chimique comme la phosphatation pour améliorer l’adhérence de la peinture. Un système automatisé s’assure que chaque pièce est correctement préparée, ce qui est essentiel pour garantir une finition de qualité.
- Application de la poudre : L’application de la peinture en poudre est réalisée par des pistolets électrostatiques automatisés. Ces pistolets chargent électriquement la poudre, qui est ensuite attirée par les pièces métalliques, assurant une couverture uniforme de la surface. Les systèmes de commande automatique ajustent la vitesse, l’angle, et la quantité de poudre en fonction de la taille et de la forme des pièces, garantissant une application précise et économique.
- Cuisson de la poudre : Une fois la poudre appliquée, les pièces sont envoyées dans un four à chaleur contrôlée. La température du four est régulée automatiquement pour faire fondre la poudre et la durcir, créant une couche de peinture résistante et uniforme. Les systèmes modernes permettent de contrôler précisément la température et le temps de cuisson, assurant ainsi une finition homogène.
- Contrôle de la qualité et de la gestion du processus : L’un des avantages majeurs d’un système de revêtement en poudre à commande automatique est la surveillance constante de la qualité. Des capteurs et des caméras surveillent en temps réel l’application de la poudre et la cuisson pour détecter tout défaut ou irrégularité. Si des anomalies sont détectées, des ajustements automatiques sont effectués pour corriger les problèmes immédiatement.
- Refroidissement et emballage : Après la cuisson, les pièces sont refroidies, souvent par un système de ventilation ou un bain de refroidissement. Une fois refroidies, elles sont prêtes à être emballées ou envoyées pour un contrôle final. Les étapes de refroidissement peuvent également être contrôlées de manière automatique pour éviter toute déformation ou altération de la finition due à un refroidissement trop rapide ou irrégulier.
- Recyclage de la poudre excédentaire : Une autre caractéristique d’un système de revêtement en poudre automatique est la possibilité de récupérer et de recycler la poudre excédentaire. Cela permet de minimiser les déchets et de réduire les coûts, en utilisant une partie de la poudre non adhérée sur les pièces pour la réutiliser dans le processus d’application.
L’automatisation complète de ce processus présente plusieurs avantages significatifs. Elle permet une production à grande échelle avec des coûts réduits en main-d’œuvre, tout en garantissant une qualité constante et une réduction des erreurs humaines. De plus, l’application de la peinture en poudre est plus respectueuse de l’environnement par rapport aux peintures à base de solvant, car elle ne libère pas de composés organiques volatils (COV), ce qui aide les entreprises à se conformer aux réglementations environnementales strictes.
Les systèmes de revêtement en poudre à commande automatique sont de plus en plus sophistiqués, avec des logiciels intégrés permettant un suivi détaillé de chaque étape du processus, la gestion des inventaires de peinture en poudre et l’optimisation des paramètres de production. Ces fonctionnalités rendent le système plus flexible et plus efficace, tout en améliorant la productivité et la rentabilité des entreprises.
En somme, un système de revêtement en poudre à commande automatique est une solution idéale pour les industries recherchant une finition de haute qualité, une efficacité accrue et une meilleure gestion des ressources.
Un système de revêtement en poudre à commande automatique est conçu pour garantir une application de peinture uniforme et de haute qualité, tout en optimisant les coûts et la productivité. Il repose sur des technologies avancées qui permettent de contrôler chaque étape du processus, de la préparation des pièces jusqu’à l’emballage final. L’automatisation permet de réduire l’intervention humaine, minimisant ainsi les erreurs et améliorant l’efficacité globale du système. Les pièces métalliques sont préparées soigneusement avant l’application de la peinture, garantissant que la surface est propre et prête à recevoir la couche de poudre. Une fois la peinture appliquée, la poudre est durcie dans un four à température contrôlée, assurant une finition résistante et durable.
L’automatisation s’étend également au suivi en temps réel de la qualité du revêtement, grâce à des capteurs qui mesurent l’uniformité de l’application de la peinture et de la cuisson. Si des défauts sont détectés, le système peut ajuster automatiquement les paramètres, ce qui permet de corriger rapidement les erreurs et de maintenir la qualité constante. L’option de recyclage de la poudre excédentaire est un autre avantage notable, car elle permet de récupérer et de réutiliser la poudre non utilisée, réduisant ainsi le gaspillage et les coûts.
En plus de cela, la gestion du processus est intégrée dans un système informatique qui permet de suivre les performances, de programmer des cycles de production, et de générer des rapports détaillés pour l’optimisation de la production. L’automatisation de la cuisson et du refroidissement des pièces assure également une finition parfaite sans risque de déformation ou de perte de qualité due à des conditions non maîtrisées.
L’impact environnemental est également pris en compte dans ces systèmes, car l’application de peinture en poudre génère moins de déchets et ne nécessite pas de solvants chimiques, ce qui réduit les émissions de COV et rend le processus plus écologique. Cela répond à la fois aux exigences environnementales et aux attentes des consommateurs en matière de produits plus durables.
En résumé, un système de revêtement en poudre à commande automatique offre une solution hautement efficace pour les industries de production en série. Il combine technologie de pointe et avantages écologiques pour garantir une finition de haute qualité, tout en optimisant les ressources et les coûts de production.
L’évolution des systèmes de revêtement en poudre à commande automatique continue de se concentrer sur l’amélioration de la précision, de l’efficacité et de l’intégration des technologies intelligentes. Les progrès dans l’automatisation, tels que l’intelligence artificielle et l’apprentissage machine, permettent désormais aux systèmes de s’adapter encore mieux aux conditions de production et d’anticiper les besoins de maintenance avant qu’un problème ne survienne. Par exemple, des algorithmes peuvent analyser des données en temps réel pour prédire les défaillances possibles des équipements, comme les pistolets de pulvérisation ou les systèmes de chauffage des fours, permettant ainsi de réduire les arrêts non planifiés et d’améliorer la fiabilité du processus.
Les systèmes de commande automatiques modernes intègrent également des interfaces utilisateurs avancées, souvent sous forme de tablettes ou d’écrans tactiles, permettant aux opérateurs de suivre et de contrôler facilement tous les paramètres du système, depuis l’application de la peinture jusqu’aux étapes finales de refroidissement et d’emballage. Ces interfaces peuvent offrir une visualisation en temps réel de l’état de chaque pièce à travers des caméras haute définition ou des capteurs qui analysent les détails de l’application de la peinture et la qualité de la finition, fournissant ainsi un retour immédiat pour toute correction nécessaire.
Les lignes de production modernes utilisent également des robots de peinture qui peuvent ajuster automatiquement la distance et l’angle des pistolets en fonction de la géométrie des pièces, garantissant une couverture parfaite même pour des objets complexes ou de formes irrégulières. Ce niveau de précision réduit encore les risques de surconsommation de poudre, tout en garantissant une couche de peinture uniforme et esthétique.
L’amélioration des systèmes de filtration d’air et de récupération de la poudre excédentaire contribue également à l’efficacité de ces installations. En capturant et en recyclant la poudre non utilisée, les entreprises réduisent non seulement le gaspillage mais optimisent également les coûts de matières premières, un facteur essentiel dans un environnement industriel à grande échelle. Cette gestion efficace des matériaux permet de maintenir des coûts bas tout en répondant aux normes environnementales strictes qui régissent les émissions industrielles.
Le passage à des systèmes intelligents et interconnectés permet également une meilleure gestion des données, ce qui peut conduire à une optimisation des cycles de production. Les informations collectées sur le rendement de la ligne de production peuvent être utilisées pour ajuster les paramètres de manière proactive, prévenant ainsi les défauts avant qu’ils n’affectent le produit final. Cela permet non seulement d’améliorer la qualité, mais aussi d’accélérer les délais de production tout en réduisant les coûts d’exploitation.
Enfin, l’intégration avec des systèmes de gestion de la production (ERP) permet aux entreprises de planifier, suivre et optimiser l’ensemble du processus de fabrication de manière fluide. Cela crée une transparence totale, permettant une gestion des stocks en temps réel et une planification optimisée pour répondre à la demande.
Avec ces avancées, les systèmes de revêtement en poudre à commande automatique ne se contentent pas d’améliorer l’efficacité de la production. Ils offrent aussi une plus grande flexibilité et une meilleure adaptabilité aux besoins spécifiques des entreprises, contribuant à un environnement de fabrication plus intelligent, durable et rentable.
Chaîne de poudrage électrostatique automatique
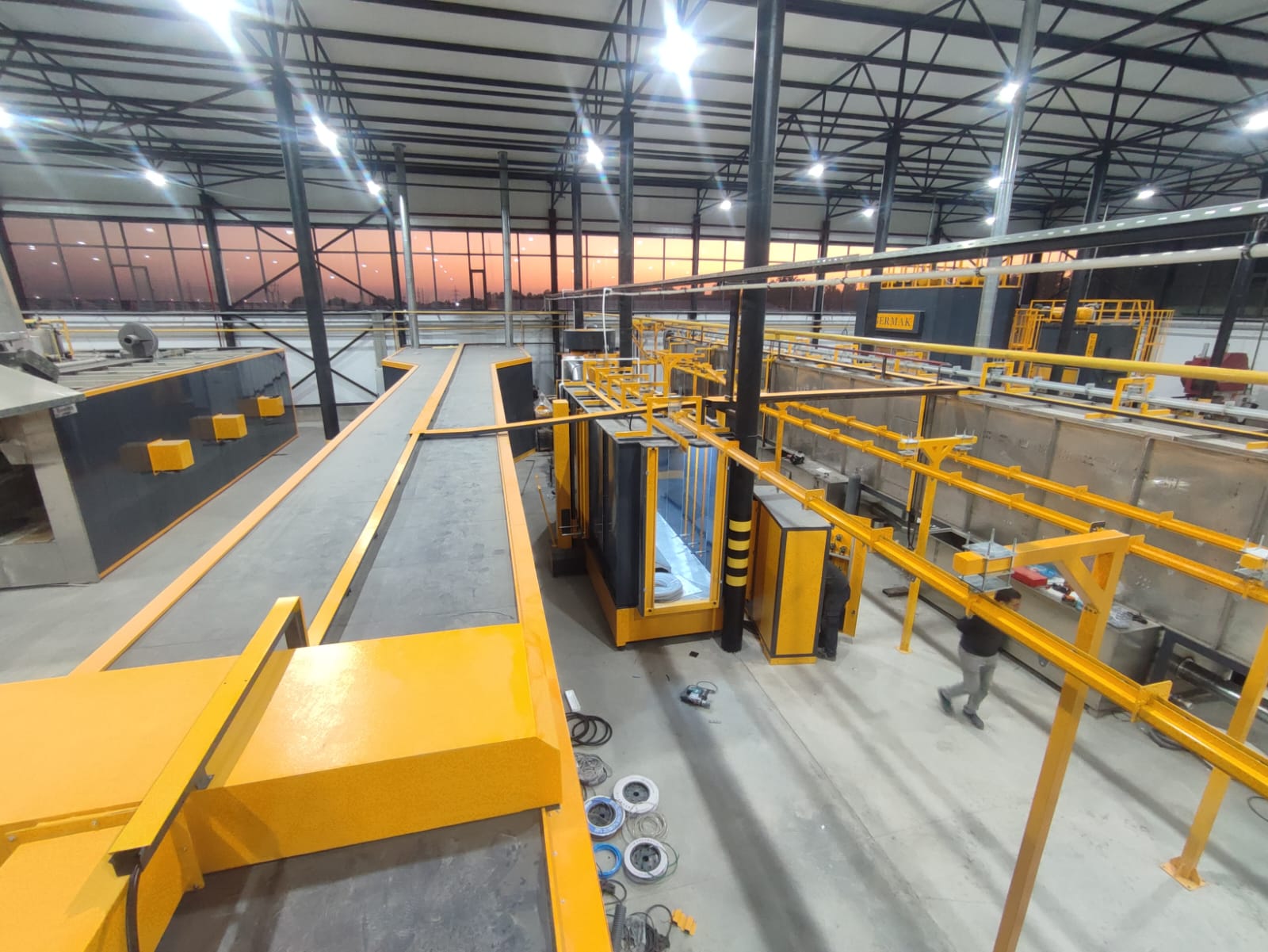
Une chaîne de poudrage électrostatique automatique est un système industriel conçu pour appliquer de la peinture en poudre sur des surfaces métalliques ou autres matériaux en utilisant un procédé électrostatique. Ce type de chaîne de production permet une application rapide, uniforme et efficace de la peinture, tout en minimisant les déchets et en réduisant l’impact environnemental par rapport à des procédés de peinture à base de solvants.
Dans ce système, les pièces à peindre sont d’abord préparées par un nettoyage et un prétraitement pour garantir une bonne adhérence de la peinture. Cela inclut des processus comme le dégraissage, la phosphatation ou l’activation de la surface, selon les exigences spécifiques de la production. Une fois les pièces prêtes, elles sont envoyées dans la zone de poudrage, où des pistolets électrostatiques appliquent la peinture en poudre sur les surfaces.
Les pistolets électrostatiques sont l’élément clé de ce système. Ils chargent la peinture en poudre avec une charge électrique négative, tandis que les pièces métalliques sont souvent mises à la terre ou chargées positivement, ce qui attire la poudre. Cela permet une application uniforme de la peinture, même sur des pièces complexes ou de formes irrégulières. La poudre adhère de manière optimale aux surfaces, réduisant ainsi le gaspillage et assurant une finition plus précise. Les pistolets peuvent ajuster automatiquement le débit de poudre et l’angle de pulvérisation en fonction de la taille et de la forme des pièces, garantissant une couverture complète.
Après l’application de la peinture, les pièces passent généralement par un four de cuisson. Ce four est conçu pour chauffer les pièces à une température spécifique (souvent entre 160 et 200°C), ce qui fait fondre la poudre et la durcit, créant ainsi une finition solide et résistante. Le contrôle de la température et du temps de cuisson est crucial pour garantir une qualité uniforme de la finition, et dans les chaînes automatisées, ces paramètres sont souvent réglés et surveillés par des systèmes informatiques.
Le système est entièrement automatisé, ce qui signifie qu’une grande partie du processus, y compris l’application de la poudre et le contrôle de la cuisson, est géré par des machines et des logiciels intégrés. Cela permet d’augmenter la vitesse de production tout en maintenant une qualité constante, tout en réduisant les erreurs humaines et les coûts associés à la main-d’œuvre.
Une autre caractéristique importante d’une chaîne de poudrage électrostatique automatique est la capacité de récupérer et de recycler la poudre excédentaire. La poudre non adhérée peut être collectée et réutilisée, ce qui permet de minimiser le gaspillage et d’améliorer l’efficacité économique du processus. Cela réduit également l’impact environnemental, car moins de déchets sont produits.
De plus, les chaînes de poudrage électrostatique modernes sont souvent équipées de systèmes de surveillance avancés qui utilisent des capteurs et des caméras pour surveiller la qualité de l’application de la peinture. Cela permet de détecter immédiatement tout défaut dans le processus, comme une application inégale de la poudre ou un problème dans le four, ce qui permet une correction rapide et garantit une finition de haute qualité.
En résumé, une chaîne de poudrage électrostatique automatique est un système très efficace et rentable pour appliquer une finition de peinture durable et résistante sur des pièces métalliques et autres matériaux. Elle combine des technologies de pointe en matière de pulvérisation électrostatique, de cuisson, et de récupération de la poudre pour offrir une solution à la fois rapide, économique et respectueuse de l’environnement.
Une chaîne de poudrage électrostatique automatique est un système avancé qui repose sur des technologies sophistiquées pour appliquer une finition de peinture uniforme et résistante, tout en optimisant l’efficacité de la production. La préparation des pièces avant l’application de la peinture est cruciale pour assurer une adhérence parfaite de la poudre. Les pièces passent par un nettoyage et un traitement de surface qui éliminent les contaminants et créent une surface idéale pour la peinture. Une fois prêtes, elles sont placées dans la zone de poudrage, où des pistolets électrostatiques chargent la peinture en poudre et la projettent sur les pièces. La charge électrique générée par ces pistolets attire la poudre sur la surface métallique, ce qui permet d’obtenir une couverture uniforme même sur des formes complexes.
Le principal avantage de ce processus électrostatique est qu’il réduit considérablement les pertes de peinture, car seule la poudre qui est attirée par la pièce est utilisée, contrairement à d’autres techniques où la peinture peut être dispersée dans l’air ou gaspillée. Une fois que la peinture est appliquée, les pièces sont envoyées dans un four de cuisson, où la poudre fond sous l’effet de la chaleur et se durcit pour former une finition robuste. Les paramètres de température et de temps de cuisson sont soigneusement régulés pour garantir que chaque pièce obtienne une couche de peinture durable et homogène.
La chaîne de poudrage électrostatique automatique va au-delà de l’application de la peinture. Elle intègre des systèmes de gestion de la production qui permettent de suivre en temps réel l’état du processus. Cela inclut des contrôles de qualité automatisés, où des capteurs ou des caméras surveillent la répartition de la poudre et la cuisson pour identifier immédiatement toute anomalie, permettant ainsi de corriger le problème avant qu’il n’affecte le produit final. Cette surveillance continue optimise l’efficacité du processus et assure une finition de haute qualité, tout en minimisant les erreurs humaines.
Un autre aspect important du système est la gestion de la poudre excédentaire. La possibilité de récupérer la peinture en poudre non utilisée et de la réutiliser dans le processus réduit non seulement le gaspillage, mais aussi les coûts liés à l’achat de nouvelles matières premières. En plus de cela, cela rend le système plus écologique, car moins de déchets sont générés, et il n’y a pas de dispersion de produits chimiques nocifs dans l’air. L’intégration de ces éléments dans un système entièrement automatisé réduit également les besoins en main-d’œuvre, ce qui permet d’optimiser les coûts de production.
Les chaînes modernes de poudrage électrostatique sont également plus flexibles et peuvent être configurées pour traiter une grande variété de pièces, des plus petites aux plus grandes, avec des formes complexes. Elles permettent une production à grande échelle tout en maintenant une qualité constante. De plus, la rapidité du processus de cuisson et la capacité à ajuster rapidement les paramètres permettent de réduire les temps d’arrêt et d’améliorer les cycles de production, ce qui contribue à une meilleure rentabilité. La capacité de contrôler les différents aspects du processus via des logiciels informatisés permet de maximiser l’efficacité et d’assurer que chaque étape de la production se déroule de manière optimale.
En résumé, une chaîne de poudrage électrostatique automatique est une solution avancée qui offre de nombreux avantages, notamment en termes de qualité, d’efficacité et de respect de l’environnement. Elle permet aux entreprises de produire des pièces peintes de manière rapide, uniforme et économique, tout en répondant aux normes strictes de performance et de durabilité des finitions. Grâce à l’automatisation, au recyclage de la poudre et à la surveillance en temps réel, ces systèmes rendent la production plus souple, moins coûteuse et plus respectueuse de l’environnement.
Les chaînes de poudrage électrostatique automatiques continuent d’évoluer avec l’intégration de nouvelles technologies qui rendent le processus encore plus précis et plus efficace. L’une de ces innovations réside dans l’amélioration de l’intelligence artificielle et de l’automatisation avancée. Ces systèmes utilisent des algorithmes pour analyser des données en temps réel, ce qui permet d’ajuster automatiquement les paramètres du processus, comme la vitesse de déplacement des pièces, la quantité de poudre appliquée, et la température du four. Cela optimise la consommation d’énergie et assure une qualité constante de la finition, tout en réduisant la variabilité due aux facteurs humains.
Un autre domaine où ces chaînes se sont améliorées est l’efficacité énergétique. Les nouvelles générations de fours utilisés dans les systèmes de poudrage sont conçues pour consommer moins d’énergie tout en maintenant des performances élevées. Ces fours peuvent être équipés de systèmes de récupération de chaleur qui captent l’énergie thermique excédentaire et la réutilisent pour préchauffer les pièces ou maintenir la température dans le four. Ce type de système réduit les coûts énergétiques et l’empreinte carbone de la production, ce qui est un avantage considérable à la fois sur le plan économique et environnemental.
Les systèmes de gestion et de contrôle de la production se sont également sophistiqués. Grâce à la collecte de données en temps réel tout au long du processus, les entreprises peuvent maintenant analyser des tendances et prédire les besoins futurs. Par exemple, ces systèmes peuvent anticiper les pannes avant qu’elles ne se produisent grâce à des outils de maintenance prédictive basés sur les données des capteurs. Cela permet de planifier les réparations avant que des problèmes majeurs n’affectent la production, réduisant ainsi les temps d’arrêt et améliorant l’efficacité opérationnelle globale.
L’intégration avec des systèmes ERP (Enterprise Resource Planning) et MES (Manufacturing Execution System) permet aux chaînes de poudrage électrostatique automatiques d’être encore plus efficaces dans la gestion des stocks et des commandes. Ces systèmes permettent une planification précise des cycles de production et une gestion plus fluide des matériaux et des produits finis. Ils peuvent, par exemple, ajuster automatiquement les quantités de poudre nécessaires en fonction de la production prévue, ou encore gérer la traçabilité des pièces à chaque étape du processus, du prétraitement à l’emballage final. Cela rend le processus non seulement plus réactif, mais aussi plus transparent, en permettant un suivi détaillé des performances de la ligne.
De plus, ces systèmes peuvent être équipés de dispositifs de personnalisation, permettant à une entreprise de répondre rapidement à des demandes spécifiques ou à des variations de produits. Par exemple, une ligne de poudrage peut être configurée pour appliquer différentes couleurs de peinture en fonction de la demande du client, sans nécessiter de changements majeurs dans la production. Cela permet aux entreprises de rester agiles et de répondre rapidement aux exigences du marché, tout en maintenant une production de haute qualité.
L’amélioration continue de ces technologies permet aussi d’augmenter la durabilité et la longévité des produits finis. Le poudrage électrostatique offre une finition plus résistante aux éraflures, à la corrosion et aux conditions climatiques extrêmes, ce qui est essentiel pour des applications extérieures ou dans des environnements industriels rigoureux. De plus, les finitions obtenues sont souvent plus homogènes, avec moins de risques de défauts visibles comme des coulures ou des variations de texture.
Ainsi, les chaînes de poudrage électrostatique automatiques représentent une solution moderne et hautement efficace pour l’application de peintures en poudre. Elles permettent non seulement d’obtenir une finition de qualité supérieure mais aussi d’optimiser les coûts de production et de réduire l’impact environnemental. Ces systèmes continuent de jouer un rôle clé dans l’industrie manufacturière, permettant aux entreprises de rester compétitives tout en répondant aux exigences de durabilité et de performance des clients.
Ligne robotisée de peinture en poudre
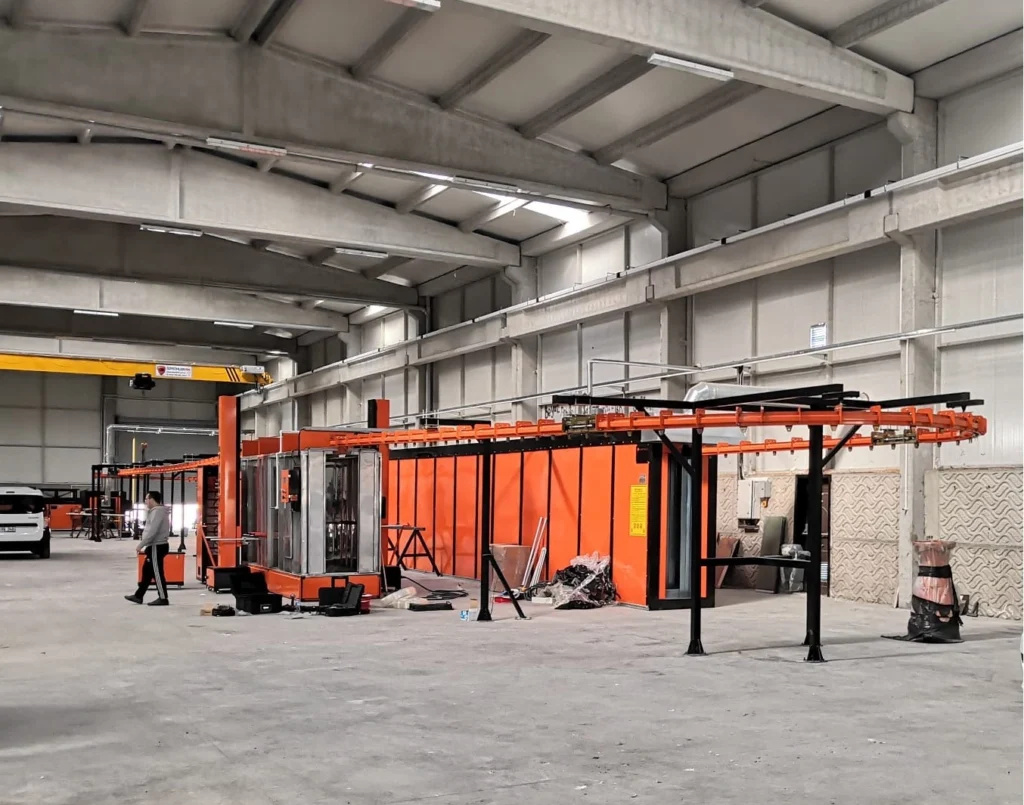
Une ligne robotisée de peinture en poudre est un système automatisé avancé utilisé pour appliquer une finition en poudre sur des pièces métalliques ou d’autres matériaux. Ce type de ligne utilise des robots industriels pour effectuer l’application de peinture, améliorant ainsi la précision, l’efficacité et la cohérence de l’application par rapport aux méthodes manuelles ou semi-automatisées. Les lignes robotisées de peinture en poudre sont de plus en plus populaires dans les secteurs industriels où la production en série de pièces de haute qualité est essentielle, comme dans les industries automobile, électroménager, et de fabrication de structures métalliques.
Dans une ligne robotisée de peinture en poudre, les robots sont généralement équipés de pistolets électrostatiques qui pulvérisent la poudre sur les pièces à traiter. Ces robots peuvent être programmés pour ajuster leur position, leur vitesse et leur angle de pulvérisation en fonction de la forme, de la taille et de la géométrie des pièces. L’utilisation des robots permet une application très précise et homogène de la peinture, ce qui garantit une finition uniforme et minimise le gaspillage de peinture.
Avant l’application de la peinture, les pièces passent par un processus de préparation, qui comprend des étapes de nettoyage et de dégraissage, et parfois un prétraitement chimique comme la phosphatation. Ce traitement assure une adhérence optimale de la peinture et améliore la durabilité du revêtement.
Les robots utilisés dans ces lignes sont souvent équipés de capteurs et de caméras qui permettent de suivre en temps réel le processus de peinture. Cela permet non seulement de garantir une application uniforme, mais aussi de détecter toute irrégularité, comme une pulvérisation insuffisante ou un excédent de poudre. Si une anomalie est détectée, le système peut ajuster automatiquement les paramètres, assurant ainsi une qualité constante de la finition.
Après l’application de la peinture, les pièces sont envoyées dans un four de cuisson à chaleur contrôlée. Ce four fait fondre la poudre et la durcit, créant une couche solide et résistante. Les robots peuvent aussi être programmés pour ajuster la vitesse des pièces entrant dans le four, permettant un contrôle optimal de la cuisson et garantissant une finition uniforme.
L’un des avantages majeurs d’une ligne robotisée de peinture en poudre est sa capacité à réduire les coûts et le temps de production. Les robots fonctionnent de manière continue et peuvent être programmés pour travailler de manière autonome sans intervention humaine, ce qui réduit le besoin en main-d’œuvre et augmente la productivité. De plus, l’application de peinture est plus précise, ce qui minimise les déchets de peinture et réduit les coûts associés.
La récupération et le recyclage de la poudre excédentaire est un autre aspect important de ces systèmes. La poudre non utilisée peut être collectée, filtrée et réutilisée dans le processus de peinture, ce qui permet de réduire le gaspillage de matériel et de faire des économies sur les coûts des matières premières.
Une ligne robotisée de peinture en poudre peut également intégrer des fonctionnalités de personnalisation. Par exemple, les robots peuvent être configurés pour appliquer différentes couleurs ou textures de peinture en fonction des besoins de la production. Ces systèmes sont extrêmement flexibles et peuvent facilement être adaptés pour produire des pièces de tailles et de formes variées, ce qui les rend idéaux pour des environnements de production où la flexibilité est essentielle.
En termes de contrôle de la qualité, les lignes robotisées de peinture en poudre sont souvent équipées de systèmes de surveillance sophistiqués qui enregistrent et analysent chaque étape du processus. Les données collectées peuvent être utilisées pour ajuster les paramètres du système en temps réel et pour générer des rapports détaillés sur la qualité de la production, permettant ainsi une gestion de la production plus précise et proactive.
Enfin, l’utilisation de robots dans la peinture en poudre offre aussi des avantages en matière de sécurité. En réduisant l’intervention humaine dans des environnements où la peinture en poudre est pulvérisée, les risques associés à l’inhalation de poussières ou aux accidents sont réduits. Les robots peuvent travailler dans des environnements automatisés et contrôlés, assurant ainsi une sécurité accrue pour les opérateurs humains qui supervisent le processus à distance.
En résumé, une ligne robotisée de peinture en poudre combine les avantages de la robotisation, de la précision et de l’automatisation pour offrir une solution efficace, rapide et de haute qualité pour les applications industrielles. Elle permet d’améliorer la productivité, de réduire les coûts et de garantir une finition de qualité constante, tout en étant plus respectueuse de l’environnement grâce au recyclage de la poudre excédentaire et à la réduction des déchets.
Les lignes robotisées de peinture en poudre sont également conçues pour s’adapter aux exigences modernes de production, avec une capacité d’intégration fluide dans des processus de fabrication plus larges. Elles peuvent être connectées à des systèmes de gestion de la production ou à des systèmes ERP (Enterprise Resource Planning) pour une gestion optimale des ressources et une meilleure planification des cycles de fabrication. Cela permet d’optimiser la production, de suivre en temps réel les performances de chaque machine et de prévoir les besoins futurs en matière de matériaux, de main-d’œuvre et de maintenance.
L’automatisation complète des lignes de peinture en poudre avec des robots permet également de garantir une répétabilité exceptionnelle d’un lot à l’autre, ce qui est essentiel lorsque les produits doivent respecter des normes strictes de qualité. Les robots peuvent appliquer une quantité précise de peinture à chaque cycle, ce qui élimine la variabilité liée aux erreurs humaines et assure que chaque pièce reçoit la même couverture et finition.
La capacité à personnaliser la ligne en fonction des besoins spécifiques de production est un autre grand avantage. Par exemple, les robots peuvent être reprogrammés rapidement pour traiter différents types de pièces ou appliquer des couleurs différentes sans nécessiter de longues périodes d’arrêt ou des ajustements complexes. Cela réduit non seulement le temps d’arrêt, mais augmente également la flexibilité de la ligne de production, permettant aux fabricants de répondre plus facilement aux demandes changeantes du marché ou de gérer des productions en petites séries.
En matière de durabilité, ces lignes sont également bien adaptées aux normes écologiques modernes. Comme les systèmes de poudrage électrostatique, elles réduisent la quantité de solvant et de produits chimiques utilisés, ce qui les rend plus respectueuses de l’environnement. De plus, le système de récupération et de recyclage de la poudre permet de réduire la quantité de déchets générés, contribuant ainsi à une production plus verte et plus économique.
L’adoption de ces systèmes robotisés s’accompagne également d’un renforcement de la sécurité dans les environnements de travail. La robotisation réduit l’exposition des travailleurs à des substances potentiellement dangereuses, comme les poussières de peinture, et minimise les risques liés à des opérations manuelles répétitives ou à des environnements de travail potentiellement polluants. Les opérateurs humains sont principalement responsables de la surveillance et de la gestion à distance, ce qui leur permet de se concentrer sur des tâches de supervision et de maintenance, plutôt que sur l’intervention directe dans le processus de peinture.
De plus, les avancées technologiques permettent à ces lignes de devenir de plus en plus intelligentes, avec l’introduction de la maintenance prédictive. Les capteurs embarqués sur les robots ou dans les équipements de la ligne de production permettent de détecter des anomalies de fonctionnement avant qu’elles ne deviennent des problèmes majeurs. Par exemple, si un robot rencontre une résistance accrue pendant l’application de la peinture, il peut ajuster automatiquement la vitesse ou l’angle du pistolet, ou alerter les techniciens de la nécessité d’une intervention.
L’utilisation de ces lignes robotisées contribue également à l’amélioration de l’esthétique des produits finis. La précision de l’application de la peinture permet d’obtenir des surfaces parfaitement lisses et uniformes, sans traces ni irrégularités, ce qui améliore la qualité perçue du produit. Cela est particulièrement important dans les secteurs où l’apparence du produit final joue un rôle essentiel, comme dans l’automobile ou les appareils électroménagers.
En conclusion, les lignes robotisées de peinture en poudre ne se contentent pas d’améliorer la productivité et l’efficacité des processus industriels. Elles représentent une avancée majeure en termes de flexibilité, de qualité de finition, de sécurité et de respect de l’environnement. En réduisant le gaspillage, en optimisant les ressources et en permettant des ajustements rapides aux besoins de production, ces systèmes contribuent à une fabrication plus agile, plus durable et plus rentable.
L’impact des lignes robotisées de peinture en poudre sur la compétitivité des entreprises est considérable. Elles permettent non seulement de réduire les coûts de production en éliminant les erreurs humaines et en améliorant l’efficacité du processus, mais elles offrent aussi un avantage concurrentiel en termes de rapidité de production et de flexibilité. Les entreprises qui adoptent ces technologies peuvent répondre plus rapidement aux demandes du marché, lancer de nouveaux produits plus efficacement et ajuster la production pour répondre à des fluctuations de la demande.
La rapidité et la flexibilité d’une ligne robotisée permettent de s’adapter à différents types de pièces, qu’elles soient de tailles variées ou de formes complexes, ce qui est un avantage dans les industries où la diversification des produits est fréquente. Les robots peuvent être programmés pour effectuer des ajustements minutieux en fonction des spécifications de chaque pièce, sans nécessiter d’interventions manuelles fastidieuses. Cela permet de traiter des séries de produits différentes sur une même ligne sans les contraintes associées aux systèmes manuels ou semi-automatiques.
Les lignes robotisées de peinture en poudre permettent également une gestion de la production beaucoup plus transparente. Grâce à l’intégration de systèmes de suivi des performances, les fabricants peuvent obtenir des informations précises sur chaque étape du processus de peinture, de l’application de la poudre à la cuisson. Cette transparence permet une meilleure prise de décision en temps réel et facilite la gestion des stocks, la planification de la production et la gestion des ressources.
En matière de contrôle de qualité, les avancées technologiques dans les lignes robotisées permettent une inspection continue et en temps réel des pièces peintes. Des caméras et des capteurs haute définition peuvent être utilisés pour détecter les défauts minimes sur les pièces, comme des irrégularités dans l’application de la poudre ou des défauts de finition. Si un problème est détecté, le système peut ajuster automatiquement les paramètres du robot ou alerter les opérateurs, ce qui réduit le besoin de reprises manuelles et améliore la qualité globale du produit.
Les lignes robotisées sont également une réponse aux défis posés par les exigences de plus en plus strictes en matière de durabilité et de performance des revêtements. Par exemple, dans des secteurs comme l’automobile, où les pièces doivent résister à des conditions extrêmes (chaleur, humidité, frottement), l’application précise de la peinture en poudre assure une finition résistante et durable. Les robots permettent une application homogène de la peinture sur des surfaces complexes, garantissant une finition plus durable et plus résistante à l’usure, aux rayures et aux conditions climatiques difficiles.
L’automatisation des lignes de peinture en poudre réduit également le besoin de main-d’œuvre spécialisée. Les robots sont capables d’effectuer des tâches complexes avec une grande précision, ce qui permet de réduire les coûts de main-d’œuvre associés à la manipulation manuelle et aux ajustements constants. Ce gain d’efficacité permet aux entreprises d’allouer leurs ressources humaines à des tâches à plus forte valeur ajoutée, comme la maintenance, l’analyse des données ou l’optimisation continue du processus.
De plus, la possibilité de recycler et de réutiliser la poudre excédentaire dans ces systèmes robotisés est un avantage économique et écologique significatif. En récupérant la poudre non utilisée, les entreprises peuvent réduire les coûts de matières premières, tout en diminuant la quantité de déchets produits et en réduisant l’impact environnemental de leur production. Cela répond à la demande croissante des consommateurs et des régulations industrielles pour des pratiques plus durables.
En somme, l’introduction de lignes robotisées de peinture en poudre transforme non seulement la manière dont les produits sont fabriqués, mais elle ouvre aussi la voie à une production plus agile, plus durable et plus compétitive. Ces systèmes permettent aux fabricants d’améliorer leur performance tout en respectant les standards de qualité, de sécurité et de durabilité requis dans les industries modernes. Grâce à l’automatisation, à la réduction des déchets et à l’optimisation de la gestion des ressources, les entreprises peuvent offrir des produits de haute qualité à des prix compétitifs, tout en respectant les exigences environnementales et en répondant aux besoins changeants des consommateurs.
L’avenir des lignes robotisées de peinture en poudre semble très prometteur, avec l’introduction de technologies encore plus avancées et l’évolution vers des systèmes plus intelligents et interconnectés. L’une des tendances majeures est l’intégration de l’Internet des objets (IoT) et des capacités de connectivité dans ces systèmes. Les capteurs IoT peuvent collecter des données en temps réel sur chaque aspect du processus de peinture, permettant aux opérateurs de surveiller et d’analyser les performances de la ligne à distance via des plateformes cloud. Cela offre une visibilité accrue sur les paramètres de production, tout en permettant une gestion proactive de la maintenance et des ressources.
En parallèle, l’intelligence artificielle (IA) joue un rôle croissant dans l’optimisation des lignes robotisées de peinture en poudre. L’IA peut analyser les données collectées par les capteurs et prendre des décisions en temps réel pour ajuster automatiquement les paramètres du système. Par exemple, si des variations dans l’application de la peinture sont détectées, l’IA peut ajuster la vitesse du robot, la quantité de poudre pulvérisée ou la distance d’application sans intervention humaine. Cela permet d’atteindre des niveaux de précision et de régularité encore plus élevés, tout en réduisant les risques d’erreurs humaines.
De plus, les robots eux-mêmes deviennent de plus en plus flexibles et adaptatifs. Par exemple, l’utilisation de robots collaboratifs (cobots) dans le processus de peinture est une tendance en plein essor. Ces robots sont conçus pour travailler de manière sûre aux côtés des opérateurs humains, offrant ainsi une assistance pour des tâches spécifiques tout en restant suffisamment flexibles pour traiter une variété de pièces. En combinant l’agilité des robots collaboratifs avec la puissance des systèmes robotisés classiques, les lignes de peinture en poudre pourront gérer des productions de plus en plus diversifiées sans sacrifier la qualité.
Les avancées en matière de matériaux de peinture sont également susceptibles de jouer un rôle clé dans le développement de ces lignes. Les nouvelles formulations de poudres, plus respectueuses de l’environnement, plus durables et offrant une gamme plus large de finitions (par exemple, textures, couleurs et effets spéciaux) seront de plus en plus compatibles avec les systèmes robotisés. Cela permettra aux fabricants d’offrir des produits innovants tout en maintenant une production de haute qualité.
L’intégration de la réalité augmentée (RA) et de la réalité virtuelle (RV) est également en train de transformer la façon dont les opérateurs et les techniciens interagissent avec ces lignes de production. Grâce à des systèmes de RA, les opérateurs peuvent superposer des informations en temps réel sur leur environnement de travail, comme les données de performance des robots ou des alertes concernant des ajustements à faire dans le processus. Cela simplifie la gestion de la ligne et réduit le besoin de formations longues et coûteuses, tout en rendant le travail plus intuitif. Les systèmes de RV, quant à eux, permettent de simuler des changements dans la production ou de former des techniciens à l’entretien des équipements dans un environnement virtuel avant de les exposer à de réelles opérations.
Une autre évolution importante sera l’augmentation de l’interconnexion entre les lignes de production. L’idée est de créer des chaînes de production totalement intégrées où les lignes robotisées de peinture en poudre communiquent avec d’autres équipements et machines, de la fabrication de la pièce à son emballage final. Ce type de système connecté permet non seulement d’optimiser la production en temps réel, mais aussi de garantir que chaque étape du processus est parfaitement synchronisée, ce qui maximise l’efficacité et réduit les temps d’arrêt.
L’approfondissement de l’automatisation dans la gestion de la qualité sera également un domaine clé. De plus en plus, des systèmes de vision par ordinateur alimentés par l’intelligence artificielle pourront analyser chaque pièce à la fin du processus de peinture, détectant des imperfections ou des défauts dans l’application de la poudre. Ces systèmes de contrôle qualité automatisés peuvent garantir une finition parfaite pour chaque pièce, réduisant ainsi le besoin de vérifications manuelles et accélérant le passage à l’étape suivante de la production.
L’adoption de ces technologies avancées transforme également la manière dont les entreprises gèrent leur impact environnemental. Les lignes robotisées de peinture en poudre deviennent non seulement plus efficaces en termes de consommation de ressources, mais elles permettent aussi une gestion optimale des déchets. Les systèmes de filtration et de recyclage de la poudre sont de plus en plus performants, ce qui réduit les pertes et limite l’impact environnemental. En outre, la capacité d’optimiser la consommation d’énergie dans le processus de cuisson et d’adapter les paramètres de la ligne de manière dynamique réduit encore l’empreinte carbone de la production.
En somme, l’avenir des lignes robotisées de peinture en poudre repose sur une interconnexion plus poussée, une intelligence accrue grâce à l’IA et l’IoT, ainsi qu’une plus grande flexibilité et adaptabilité. Ces systèmes ne se contenteront pas d’optimiser la production, mais contribueront à une industrie plus durable, plus intelligente et plus réactive aux besoins changeants des consommateurs. Ces avancées technologiques ouvrent la voie à une nouvelle ère dans la fabrication industrielle, où l’innovation et l’efficacité sont au cœur de la compétitivité.
Unité de peinture en poudre automatisée
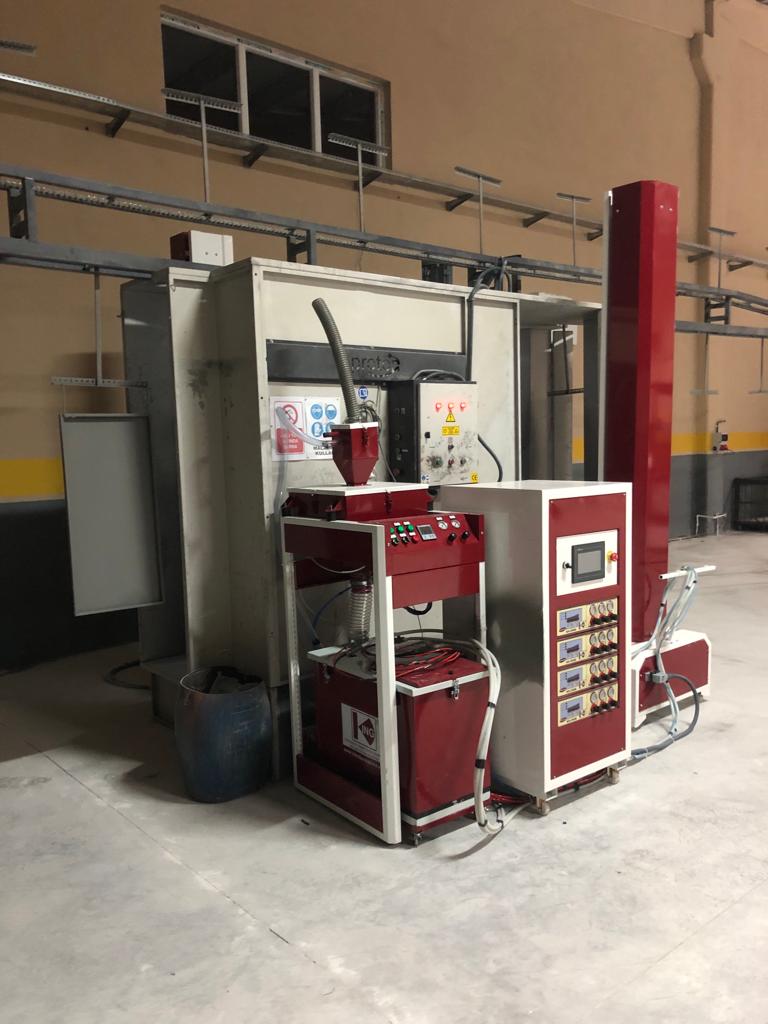
Une unité de peinture en poudre automatisée est un système complet de traitement et de finition des surfaces qui applique de la peinture en poudre sur des pièces métalliques ou d’autres matériaux, en utilisant des processus automatisés pour garantir la qualité, l’efficacité et la répétabilité. Ce type d’unité est conçu pour offrir une solution clé en main dans des environnements industriels où la production en série et la précision sont essentielles. L’automatisation dans ce contexte signifie une réduction significative des interventions humaines tout en augmentant la productivité, la qualité du produit fini et la sécurité.
Les unités de peinture en poudre automatisées comprennent plusieurs étapes clés du processus de peinture, chacune optimisée pour maximiser la performance et la durabilité du revêtement final. Le système peut être intégré à d’autres lignes de production ou être autonome, selon les besoins de l’entreprise.
Préparation des pièces : Avant l’application de la peinture en poudre, les pièces doivent être préparées de manière adéquate pour garantir une adhésion optimale de la poudre. Cette préparation inclut des étapes de nettoyage, de dégraissage et parfois un prétraitement chimique comme la phosphatation. Ces étapes sont souvent réalisées dans des chambres automatisées de nettoyage ou de traitement, où les pièces sont immergées dans des solutions spécifiques ou soumises à des jets de haute pression pour éliminer les impuretés.
Application de la poudre : L’application de la peinture en poudre elle-même est réalisée à l’aide de pistolets électrostatiques qui pulvérisent la poudre sur les pièces. Ces pistolets sont alimentés par des robots ou des bras articulés automatisés, qui peuvent ajuster leur angle, leur vitesse et leur distance par rapport à la surface à traiter pour garantir une couverture uniforme. La poudre est chargée électrostatiquement, ce qui permet de l’attirer efficacement sur les surfaces métalliques, assurant ainsi une couche homogène.
Les unités de peinture en poudre automatisées sont souvent équipées de robots intelligents capables de travailler sur des pièces de formes complexes, en ajustant les paramètres en temps réel pour chaque pièce en fonction de sa géométrie. Cela garantit que chaque pièce reçoit une application uniforme de la poudre, tout en minimisant les pertes de matériau.
Cuisson : Après l’application de la peinture, les pièces sont envoyées dans un four pour cuire la poudre. La cuisson fait fondre la poudre, la transformant en une finition dure et résistante. Les fours utilisés dans les unités automatisées sont souvent à température contrôlée et peuvent être programmés pour fonctionner à des températures spécifiques en fonction du type de poudre utilisée. L’automatisation de cette étape permet d’ajuster précisément la durée de cuisson et la température pour chaque lot, assurant une finition homogène et de haute qualité.
Systèmes de récupération de poudre : Une caractéristique clé des unités de peinture en poudre automatisées est le système de récupération et de recyclage de la poudre excédentaire. La poudre qui n’est pas fixée sur la pièce est aspirée et filtrée, puis renvoyée dans le système pour être réutilisée. Cela permet de réduire le gaspillage de peinture, d’économiser sur les coûts des matériaux et de rendre le processus plus respectueux de l’environnement.
Contrôle et surveillance de la qualité : L’une des caractéristiques les plus importantes des unités automatisées est l’intégration de systèmes de contrôle et de surveillance de la qualité. Des caméras et des capteurs peuvent être installés sur la ligne pour inspecter en temps réel la couverture de la peinture et détecter toute irrégularité ou défaut de finition, comme des zones manquantes ou une application trop épaisse. Ces systèmes sont capables de signaler immédiatement toute déviation par rapport aux critères définis, permettant ainsi un ajustement automatique du processus.
Systèmes de gestion et de traçabilité : Les unités de peinture en poudre automatisées sont souvent équipées de logiciels de gestion de la production. Ces systèmes assurent la traçabilité des pièces à chaque étape du processus, du nettoyage initial à la finition. Cela permet de suivre la qualité de la production, de gérer les stocks de poudre et de prévoir les besoins futurs en matières premières. De plus, ils offrent des rapports détaillés sur la performance de la ligne, ce qui permet d’optimiser continuellement les processus et d’identifier les points de dysfonctionnement.
Avantages de l’automatisation dans la peinture en poudre :
- Efficacité accrue : L’automatisation permet un fonctionnement continu de la ligne de peinture, réduisant les arrêts et maximisant la production. Les pièces peuvent être peintes en série à une vitesse constante, et l’automatisation permet de traiter des volumes élevés sans compromettre la qualité.
- Réduction des coûts de production : En réduisant le gaspillage de peinture, en augmentant l’efficacité des processus et en diminuant le besoin en main-d’œuvre, les unités automatisées permettent de réduire les coûts de production. Le recyclage de la poudre excédentaire est particulièrement avantageux à cet égard.
- Consistance de la qualité : L’application automatisée garantit une finition uniforme et constante à chaque cycle de production, réduisant les variations dues à l’intervention humaine. Les systèmes de contrôle de qualité permettent d’intervenir immédiatement en cas de défaut, ce qui assure une qualité constante.
- Sécurité accrue : L’automatisation diminue le nombre d’interventions humaines dans des environnements de travail où les risques liés aux solvants et à la poussière de peinture peuvent être présents. Cela réduit les risques pour les travailleurs et améliore les conditions de sécurité dans l’usine.
- Flexibilité et personnalisation : Les systèmes automatisés peuvent être facilement reconfigurés pour traiter différentes formes, tailles et types de pièces, ou pour appliquer des finitions de peinture différentes en fonction des besoins des clients. Les logiciels de gestion permettent une personnalisation des processus en temps réel pour répondre aux demandes de production spécifiques.
En conclusion, une unité de peinture en poudre automatisée offre une solution extrêmement efficace pour les fabricants cherchant à améliorer la qualité, la productivité et la rentabilité de leurs processus de finition. L’intégration des robots, de la surveillance en temps réel et des systèmes de gestion intelligents fait de ces unités des outils de production puissants, capables de répondre aux défis de l’industrie moderne tout en respectant les normes environnementales et de sécurité.
Une unité de peinture en poudre automatisée offre des avantages considérables en termes de précision, d’efficacité et de flexibilité. La technologie permet de réduire la nécessité d’interventions humaines et d’améliorer la constance de la finition des produits. L’une des grandes forces de ces systèmes automatisés réside dans leur capacité à gérer des productions de grande envergure tout en maintenant des standards de qualité élevés. Les robots et les systèmes automatisés sont capables de travailler sans relâche, appliquant des couches uniformes de peinture en poudre sur une variété de pièces, tout en ajustant les paramètres en temps réel en fonction des spécifications de chaque produit.
L’automatisation permet également de mieux gérer les différentes étapes de la production, du nettoyage des pièces avant l’application de la peinture, jusqu’à la cuisson de la poudre et au contrôle qualité final. Grâce aux systèmes de récupération de poudre excédentaire, une grande quantité de matériau peut être récupérée et réutilisée, ce qui réduit les déchets et les coûts liés aux matières premières, tout en minimisant l’impact environnemental. Cela permet également une utilisation optimale des ressources, rendant le processus plus durable.
De plus, l’intégration de technologies avancées comme l’Internet des objets (IoT) et l’intelligence artificielle (IA) dans ces unités permet un suivi en temps réel de chaque étape du processus de peinture. Cela fournit des données précieuses sur la performance de la ligne de production et sur la qualité des pièces peintes, permettant aux responsables de la production d’effectuer des ajustements instantanés pour corriger toute anomalie. Par exemple, si un défaut est détecté dans l’application de la peinture, le système peut automatiquement ajuster les paramètres, comme la vitesse ou la pression des pistolets électrostatiques, pour garantir une finition optimale.
L’optimisation de la production est également soutenue par des systèmes logiciels sophistiqués qui permettent de planifier, de suivre et d’analyser les performances de la ligne. Ces logiciels peuvent être utilisés pour prévoir les besoins en matières premières, gérer les stocks de peinture en poudre et maintenir une traçabilité complète des pièces à chaque étape de leur traitement. Cette capacité de gestion intelligente de la production permet non seulement d’améliorer l’efficacité opérationnelle, mais aussi d’offrir une meilleure prévision des coûts et des besoins de maintenance.
Le processus automatisé élimine également les erreurs humaines, souvent responsables de variations dans la finition des produits ou d’interruptions dans le processus de production. En automatisant l’application de la peinture, le risque de surcharge ou d’application irrégulière de la poudre est considérablement réduit, ce qui assure des produits finis de haute qualité à chaque lot. La reproductibilité de la finition est l’un des principaux atouts des systèmes de peinture automatisée, ce qui est particulièrement précieux dans des industries comme l’automobile, où la précision et la constance des finitions sont cruciales.
Enfin, une unité de peinture en poudre automatisée offre une plus grande sécurité dans l’usine en réduisant l’exposition des travailleurs aux produits chimiques et aux poussières de peinture. En automatisant les étapes les plus dangereuses, comme la pulvérisation de la peinture et la cuisson, les risques liés à l’inhalation de vapeurs toxiques ou à l’exposition à des surfaces chaudes sont réduits, créant ainsi un environnement de travail plus sûr et plus respectueux des normes de sécurité.
En somme, les unités de peinture en poudre automatisées représentent une évolution majeure dans le domaine de la fabrication, combinant efficacité, précision et durabilité. Ces systèmes permettent aux entreprises d’améliorer leur compétitivité en augmentant la productivité, en réduisant les coûts et en assurant une qualité constante, tout en répondant aux exigences environnementales modernes. La capacité d’adaptation aux besoins spécifiques de chaque production et la gestion optimisée des ressources offrent des avantages considérables pour l’industrie moderne, rendant ces unités essentielles pour les fabricants souhaitant rester à la pointe de la technologie.
L’évolution continue des unités de peinture en poudre automatisées les rend de plus en plus intelligentes, modulables et interconnectées. Dans les environnements industriels actuels, il devient essentiel d’adapter les lignes de production non seulement à la cadence mais aussi à la complexité croissante des produits. Les unités automatisées modernes répondent à cette demande grâce à une flexibilité accrue. Elles peuvent s’ajuster rapidement pour traiter des séries variées, avec des changements de couleur ou de pièces quasiment instantanés, sans devoir interrompre complètement le cycle de production. Cela est rendu possible par des systèmes de nettoyage rapide, des modules de changement de poudre automatisés, et une programmation robotisée avancée.
Cette capacité à changer rapidement de configuration permet à une seule unité de servir plusieurs lignes de production ou de traiter des commandes personnalisées sans compromettre la qualité ou les délais. Le pilotage centralisé permet également une communication en temps réel entre la chaîne de peinture et les autres départements de production, tels que l’assemblage, le contrôle qualité ou la logistique. Cela crée un flux de production plus fluide, mieux synchronisé, où chaque pièce est suivie numériquement depuis sa préparation jusqu’à son emballage final. La traçabilité totale renforce la transparence et facilite l’identification de l’origine d’un défaut en cas de non-conformité, ce qui est crucial pour des secteurs exigeants comme l’aéronautique, l’automobile ou l’électroménager.
En parallèle, le rôle des données devient central. Les capteurs intégrés à tous les niveaux de l’unité collectent une quantité massive d’informations : températures, humidité, vitesse de convoyage, épaisseur de couche, taux de récupération de poudre, consommation énergétique, temps de cycle, etc. Ces données peuvent être traitées localement ou envoyées dans le cloud pour une analyse avancée. Grâce à cela, les superviseurs de production disposent de tableaux de bord détaillés qui leur permettent de surveiller les performances, de repérer les écarts ou de détecter les signes avant-coureurs de pannes. Cela ouvre la voie à la maintenance prédictive, qui anticipe les interventions nécessaires avant même qu’une panne ne survienne, réduisant ainsi les arrêts non planifiés.
Par ailleurs, l’expérience utilisateur est grandement améliorée. Les interfaces homme-machine (IHM) des unités automatisées deviennent plus intuitives, souvent tactiles, multilingues et accompagnées de systèmes d’assistance virtuelle ou de tutoriels embarqués. Les opérateurs peuvent ainsi surveiller ou ajuster les paramètres sans avoir besoin de connaissances techniques poussées, ce qui facilite la formation et le transfert de compétences. Dans certains cas, la réalité augmentée permet même aux techniciens de visualiser directement sur l’équipement les zones à inspecter, les pièces à remplacer ou les performances en temps réel, rendant les interventions plus rapides et plus sûres.
L’intégration croissante de solutions durables renforce aussi l’attractivité de ces unités. Outre la réduction de la consommation de poudre et d’énergie, on observe un développement constant de poudres plus écologiques, sans solvants ni composants toxiques, et compatibles avec une large gamme de matériaux, y compris les alliages légers ou les composites. Combinées aux unités automatisées, ces nouvelles poudres ouvrent des perspectives inédites pour le traitement de pièces sensibles ou complexes, sans compromettre la qualité du revêtement.
Ainsi, les unités de peinture en poudre automatisées ne sont plus seulement des outils de production : elles deviennent des plateformes intelligentes, connectées, durables et hautement performantes. Elles permettent aux entreprises de répondre aux exigences du marché moderne, qui impose des délais courts, une qualité constante, une grande diversité de produits et une production responsable. Dans cette dynamique, elles s’inscrivent parfaitement dans la logique de l’Industrie 4.0, où l’usine devient un écosystème digitalisé et agile, capable de s’adapter instantanément aux changements et d’optimiser en permanence ses performances.
La tendance vers des unités de peinture en poudre automatisées encore plus intelligentes s’accentue avec l’arrivée de solutions intégrant l’intelligence artificielle avancée, capables non seulement de réagir à des situations prédéfinies, mais aussi d’apprendre et d’optimiser les processus de manière autonome. Par exemple, un système peut analyser les historiques de production pour détecter des motifs de défauts liés à certaines configurations ou conditions environnementales, et ajuster automatiquement les paramètres pour éviter que ces défauts ne se reproduisent. Cette capacité d’auto-apprentissage transforme l’unité de peinture en un véritable système expert, capable de prendre des décisions en temps réel sans intervention humaine, améliorant ainsi la qualité finale tout en réduisant les pertes.
De plus, ces unités tendent à s’intégrer dans des écosystèmes de fabrication entièrement connectés. Dans ce type d’organisation, chaque machine communique avec les autres, partageant des données sur l’état de production, les délais, ou les exigences spécifiques de chaque commande. Une pièce entrant dans l’unité de peinture peut être automatiquement identifiée par RFID ou vision industrielle, ce qui déclenche la configuration automatique de la ligne selon le programme associé : choix du type de poudre, épaisseur désirée, température de cuisson, etc. Cela permet une personnalisation de masse à grande échelle, rendant possible la fabrication de pièces uniques dans un flux industriel continu, sans ralentissement.
La réduction de l’empreinte énergétique et environnementale reste également un axe de développement central. Les fours sont désormais conçus avec des technologies de récupération thermique, utilisant la chaleur des gaz d’échappement pour préchauffer les pièces entrantes ou l’air du four. Les ventilations sont pilotées de manière dynamique en fonction du besoin réel, et les cycles sont optimisés pour consommer juste ce qu’il faut d’énergie sans compromis sur la qualité. Du côté des cabines d’application, les systèmes à changement rapide de couleur sont repensés pour éliminer totalement les résidus de poudre entre deux productions, réduisant les pertes tout en évitant les contaminations croisées. Le tout est automatisé, surveillé et contrôlé par des algorithmes d’optimisation.
On note aussi l’émergence de concepts hybrides combinant différents types de finition dans une même unité, par exemple en associant la peinture en poudre à des traitements laser ou plasma pour améliorer l’adhérence ou modifier localement l’aspect de surface. Ces innovations permettent de créer des effets visuels ou fonctionnels très précis, tout en restant dans un cadre industriel automatisé. Cela ouvre de nouvelles perspectives dans des secteurs où l’esthétique et la performance de surface sont critiques, comme l’électroménager haut de gamme, le mobilier design ou l’électronique.
Enfin, le facteur humain reste présent, mais dans un rôle transformé. Les opérateurs ne manipulent plus directement les équipements mais supervisent les flux, analysent les données et interviennent en cas de scénario non prévu par l’automate. Leur poste évolue vers celui de pilote de ligne intelligente ou de coordinateur d’environnement de production connecté. Cela implique de nouvelles compétences, souvent liées à la data, à la maintenance préventive, à la programmation robotique ou à la gestion des systèmes intégrés. La formation continue et la digitalisation des savoir-faire deviennent donc des leviers essentiels pour exploiter pleinement le potentiel de ces unités.
En résumé, les unités automatisées de peinture en poudre évoluent vers des systèmes autonomes, intelligents, éco-efficients et hautement personnalisables. Elles s’inscrivent au cœur de l’usine du futur, où la flexibilité n’est plus un compromis mais un standard, et où la qualité, l’agilité et la durabilité sont atteintes grâce à la synergie entre technologie avancée et expertise humaine. Cette transformation progressive redéfinit non seulement la manière dont les produits sont finis, mais aussi la place de la finition dans la chaîne de valeur industrielle.
Système automatique de peinture par poudrage
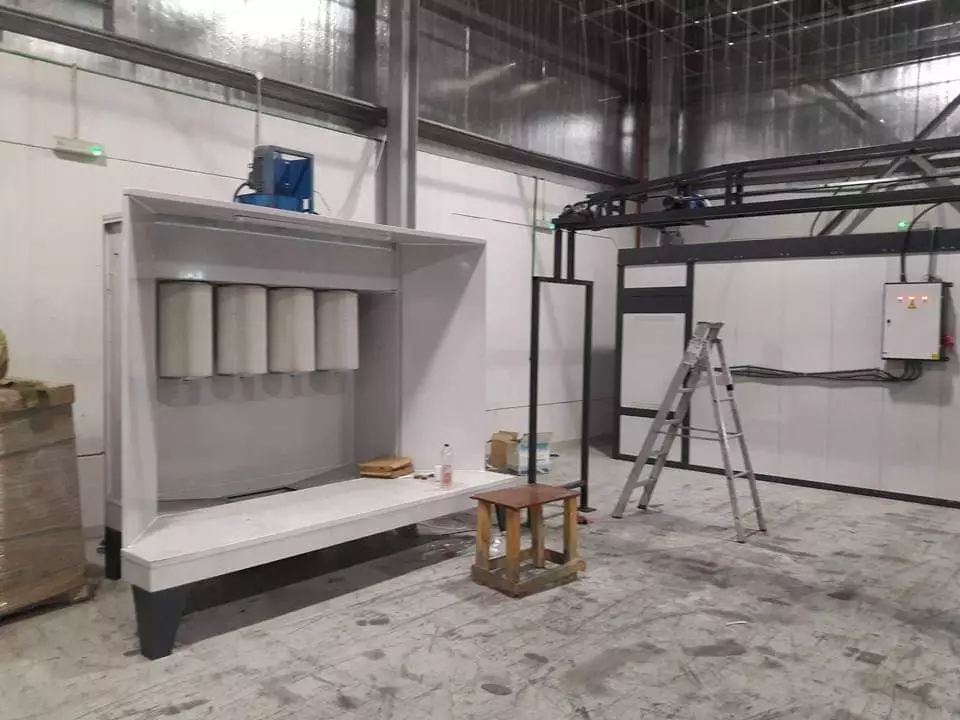
Un système automatique de peinture par poudrage est une solution moderne et hautement efficace pour appliquer une finition de peinture en poudre sur des pièces métalliques, plastiques ou autres matériaux. Ce système repose sur un processus automatisé où la poudre de peinture est appliquée sur les surfaces des pièces à traiter de manière uniforme et précise, sans l’utilisation de solvants, ce qui offre une finition durable, résistante et écologique. Les systèmes automatiques de peinture par poudrage sont largement utilisés dans des secteurs industriels variés, tels que l’automobile, l’électroménager, les équipements métalliques, et la production de meubles, en raison de leur efficacité et de leur respect de l’environnement.
Le système repose sur plusieurs étapes clés, chacune optimisée pour garantir un résultat de haute qualité tout en minimisant les coûts et en améliorant l’efficacité de production.
Prétraitement des pièces : Avant l’application de la poudre, il est essentiel de préparer la surface des pièces pour garantir une bonne adhésion de la peinture. Cela inclut souvent des processus de nettoyage (dégraissage, désoxydation, décontamination), de prétraitement chimique ou de sablage. Ces étapes sont automatisées dans des cabines de prétraitement ou des tunnels qui garantissent que chaque pièce est préparée de manière uniforme et selon les standards exigés par la production.
Application de la peinture en poudre : L’application proprement dite de la peinture en poudre est réalisée à l’aide de pistolets électrostatiques automatisés. Ces pistolets chargent électrostatiquement la poudre, ce qui fait que celle-ci est attirée par la surface de la pièce. L’automatisation de cette étape garantit une application précise, même sur des pièces aux formes complexes ou irrégulières. Les pistolets sont montés sur des robots ou des bras articulés qui peuvent ajuster leur position et leur angle en fonction de la forme de la pièce à peindre, assurant ainsi une couverture uniforme.
Les systèmes de pulvérisation sont souvent équipés de technologies avancées pour optimiser l’application de la poudre, comme des capteurs qui mesurent l’épaisseur de la couche de peinture ou des logiciels qui ajustent les paramètres de pulvérisation en temps réel en fonction des variables telles que la forme ou la taille des pièces.
Cuisson de la poudre : Une fois la poudre appliquée, les pièces passent dans un four à haute température où la peinture est durcie. La cuisson permet de fondre la poudre et de la lier chimiquement à la surface de la pièce, créant ainsi un revêtement solide, durable et résistant. Le four est généralement alimenté par des systèmes automatisés qui régulent la température et le temps de cuisson pour garantir que chaque pièce reçoit un traitement homogène et optimal. Cette étape est essentielle pour obtenir une finition résistante à l’usure, aux produits chimiques et aux intempéries.
Récupération et recyclage de la poudre : L’une des caractéristiques les plus importantes des systèmes de peinture par poudrage automatisés est leur capacité à récupérer et recycler la poudre excédentaire. La poudre non utilisée est aspirée par des systèmes de filtration et récupérée pour être réutilisée. Ce processus permet non seulement de réduire les coûts de production en maximisant l’utilisation de la poudre, mais également de minimiser l’impact environnemental de la production en réduisant les déchets.
Contrôle qualité automatisé : Le contrôle de la qualité est un aspect crucial du système de peinture par poudrage automatisé. Des capteurs et des caméras sont souvent utilisés pour inspecter les pièces en temps réel pendant et après l’application de la poudre. Ces systèmes vérifient l’uniformité de la couverture, l’épaisseur du revêtement, et détectent toute anomalie, comme des défauts de finition ou des imperfections. Si une pièce présente un défaut, elle peut être automatiquement redirigée pour une nouvelle application ou être signalée pour inspection manuelle.
Gestion du processus de production : L’ensemble du processus est contrôlé par un système centralisé de gestion de la production. Ce système permet de programmer, de suivre et d’optimiser chaque étape du processus, de la préparation des pièces jusqu’au contrôle final. Les données de production, telles que le nombre de pièces traitées, la consommation de poudre, la consommation d’énergie, et les paramètres de chaque étape, sont collectées et analysées pour améliorer l’efficacité et optimiser les coûts.
Avantages du système automatique de peinture par poudrage :
- Efficacité et productivité accrues : L’automatisation permet de traiter un grand nombre de pièces en peu de temps tout en maintenant une qualité constante. Les systèmes peuvent fonctionner 24 heures sur 24, augmentant ainsi la capacité de production sans compromettre la qualité.
- Finition uniforme et de haute qualité : L’application automatisée de la poudre assure une finition homogène, sans variations liées à des erreurs humaines. Cela est particulièrement important dans des secteurs où l’apparence et la durabilité du revêtement sont cruciales.
- Réduction des coûts : En minimisant le gaspillage de peinture et en permettant le recyclage de la poudre excédentaire, ces systèmes permettent de réduire les coûts de matériaux. De plus, l’automatisation réduit le besoin de main-d’œuvre, ce qui entraîne également des économies sur les coûts de production.
- Respect de l’environnement : La peinture en poudre est une solution écologique car elle ne contient pas de solvants, ce qui réduit les émissions de COV (composés organiques volatils) et contribue à un environnement de travail plus sain. De plus, le recyclage de la poudre excédentaire et la réduction de la consommation d’énergie grâce à l’optimisation des systèmes de cuisson sont des éléments qui participent à une approche durable.
- Flexibilité : Les systèmes automatiques de peinture par poudrage sont très flexibles et peuvent être ajustés pour s’adapter à une large variété de pièces, de tailles et de couleurs. Grâce aux logiciels de gestion et aux paramètres programmables, il est facile de reconfigurer la ligne pour différents produits sans nécessiter de changements manuels complexes.
- Amélioration de la sécurité : L’automatisation permet de réduire les risques pour les travailleurs en les éloignant des zones à risque, telles que celles où les pistolets électrostatiques ou les fours à haute température sont utilisés. De plus, l’environnement de travail devient plus sûr, car il y a moins d’exposition aux produits chimiques et aux risques liés à la poussière de peinture.
En résumé, un système automatique de peinture par poudrage offre une solution idéale pour les entreprises cherchant à combiner efficacité, qualité, et durabilité dans leurs processus de finition. Grâce à l’automatisation, ces systèmes permettent d’optimiser la production, de réduire les coûts et les déchets, tout en respectant les normes environnementales. La flexibilité et la précision de ces systèmes permettent de répondre aux besoins de divers secteurs industriels tout en garantissant une finition de haute qualité à chaque cycle de production.
Le système automatique de peinture par poudrage offre une solution idéale pour l’industrie moderne en recherchant à la fois performance, flexibilité et respect de l’environnement. Grâce à son automatisation complète, il permet une gestion optimisée de chaque étape du processus, garantissant ainsi des résultats uniformes et de haute qualité, tout en réduisant les coûts et l’impact environnemental. L’efficacité du système est renforcée par sa capacité à fonctionner en continu, offrant ainsi une production de grande envergure sans compromettre la précision ou la constance des finitions.
La clé du succès de ces systèmes réside dans leur capacité à s’adapter rapidement aux exigences de chaque production. En automatisant les étapes critiques, comme l’application de la peinture, la cuisson et la récupération de la poudre excédentaire, les entreprises peuvent répondre à des volumes de production élevés tout en maintenant des normes de qualité strictes. Cette flexibilité permet également d’exécuter des séries courtes ou des productions personnalisées sans ralentir les délais de fabrication, ce qui est particulièrement utile dans des secteurs exigeants comme l’automobile ou l’électronique, où la rapidité et la personnalisation sont essentielles.
De plus, l’introduction de technologies avancées comme la robotisation, l’intelligence artificielle et la vision industrielle permet de surveiller en temps réel l’ensemble du processus de peinture. Les capteurs et les systèmes de contrôle assurent que chaque pièce est traitée avec les bonnes conditions (température, épaisseur du revêtement, et orientation), garantissant ainsi une finition uniforme et sans défaut. En cas de détection d’un problème, comme une variation dans l’épaisseur de la couche ou un défaut visuel, le système peut automatiquement ajuster les paramètres ou signaler l’anomalie pour une intervention rapide.
L’aspect environnemental est également un facteur clé. La peinture en poudre ne nécessite pas de solvants, ce qui réduit l’émission de composés organiques volatils (COV) et contribue à la création d’un environnement de travail plus sain. En outre, l’efficience énergétique des systèmes est améliorée grâce à la récupération thermique et à l’optimisation de la consommation d’énergie dans les processus de cuisson. L’intégration de solutions de recyclage de la poudre excédentaire réduit les déchets, augmentant ainsi la rentabilité de l’opération tout en contribuant à une production plus durable.
Sur le plan économique, ces systèmes permettent de réduire les coûts en minimisant la quantité de peinture utilisée grâce à la récupération et au recyclage, ce qui fait baisser les dépenses liées aux matériaux tout en assurant une gestion optimisée des ressources. Les économies générées par la réduction des déchets et la récupération de la poudre excédentaire se traduisent également par une diminution de l’empreinte écologique, faisant de ces systèmes une option de plus en plus populaire dans un contexte où les entreprises cherchent à se conformer à des normes environnementales de plus en plus strictes.
L’automatisation de la peinture par poudrage transforme le rôle des opérateurs dans l’usine. Ces derniers sont désormais responsables de la supervision des systèmes, de la gestion des flux de production et de l’analyse des données collectées tout au long du processus. Les technologies d’interface homme-machine (IHM) offrent une interaction simple et intuitive, permettant aux opérateurs de suivre les performances de la ligne de production et d’intervenir de manière proactive en cas de besoin. Cela contribue à une gestion plus réactive et plus agile des problèmes tout en réduisant les risques humains et les erreurs.
En outre, le système de peinture par poudrage automatisé s’adapte également à l’évolution des demandes des consommateurs, qui recherchent de plus en plus des produits personnalisés et durables. La possibilité de changer facilement les couleurs, d’ajuster les finitions et de traiter des pièces de tailles et de formes variées tout en conservant une qualité constante est un atout majeur dans les industries où la demande varie rapidement, comme l’électroménager ou les équipements de sport.
Enfin, le système peut être intégré dans un cadre plus large d’Industrie 4.0, où chaque machine de la ligne de production est connectée à un réseau numérique. Cela permet de collecter, d’analyser et d’utiliser des données en temps réel pour prendre des décisions informées qui optimisent les processus. Cette interconnexion permet également une gestion à distance, ce qui offre une plus grande souplesse aux responsables de la production qui peuvent piloter la ligne de peinture sans avoir à être sur place en permanence.
En résumé, les systèmes automatiques de peinture par poudrage représentent l’avenir de la finition industrielle, offrant des avantages considérables en termes d’efficacité, de flexibilité, de rentabilité et de durabilité. Ces systèmes permettent aux entreprises de répondre à la demande croissante pour des produits personnalisés, tout en maintenant des standards de qualité élevés et en respectant les normes environnementales. Grâce à l’intégration de technologies avancées et à l’automatisation complète, ces solutions garantissent un processus de production optimal et durable, tout en offrant un retour sur investissement intéressant.
L’évolution continue des systèmes automatiques de peinture par poudrage repose également sur l’intégration de technologies émergentes telles que la robotique avancée, l’Internet des objets (IoT) et la réalité augmentée (AR). Ces innovations permettent non seulement d’améliorer l’efficacité de la production, mais aussi d’optimiser la gestion de la maintenance, de prédire les pannes, et de mieux former les opérateurs.
Les robots de peinture, équipés de capteurs et d’algorithmes d’intelligence artificielle, peuvent désormais ajuster en temps réel la position du pistolet de pulvérisation pour s’adapter à des géométries complexes des pièces. Par exemple, un robot peut ajuster l’angle du pistolet en fonction de la forme et de l’orientation d’une pièce, garantissant ainsi une application uniforme et précise de la peinture sur toutes les surfaces. Cela permet de traiter des pièces très complexes, comme celles rencontrées dans l’aéronautique ou l’automobile, sans sacrifier la qualité du revêtement. En parallèle, l’intelligence artificielle analyse les données en temps réel pour ajuster automatiquement la vitesse de convoyage des pièces, la pression de pulvérisation et même les paramètres de température pour répondre aux variations de la production.
L’intégration de l’IoT permet une gestion centralisée et une surveillance en temps réel de l’ensemble de la ligne de peinture. Chaque machine, chaque capteur et chaque actionneur dans le processus de peinture est connecté à un réseau qui permet une communication continue entre les différents composants du système. Cela donne aux gestionnaires de production un contrôle total sur les performances du système, avec la possibilité de détecter des anomalies avant qu’elles ne deviennent des problèmes majeurs. Par exemple, des capteurs peuvent signaler une variation de la température ou une déviation de la pression de pulvérisation, permettant une intervention immédiate pour rectifier la situation et éviter un défaut sur les pièces. En outre, les données collectées peuvent être analysées pour identifier des modèles de défaillances récurrentes ou des inefficacités dans le processus de production, ce qui permet une amélioration continue du système.
La maintenance prédictive, rendue possible par l’IoT, permet de réduire les coûts liés aux pannes imprévues et aux arrêts non planifiés. Plutôt que de réagir à une panne après qu’elle se soit produite, les données recueillies sur l’état des machines et des composants permettent de prédire quand une intervention sera nécessaire, permettant ainsi de planifier la maintenance avant que des problèmes majeurs n’affectent la production. Cela prolonge la durée de vie des équipements, optimise leur performance et réduit les interruptions de la chaîne de production.
La réalité augmentée (AR) transforme également l’interaction avec le système de peinture. En combinant l’AR avec des systèmes de vision industrielle, il devient possible de superposer des informations en temps réel sur les équipements et les pièces à traiter. Par exemple, un technicien de maintenance peut porter des lunettes AR qui lui fournissent des instructions détaillées et des informations sur les composants de la ligne de peinture en surimpression, ce qui facilite l’identification des zones à réparer ou à ajuster. Cette technologie permet une intervention plus rapide et plus précise, tout en réduisant les risques d’erreur humaine.
Les systèmes automatiques de peinture par poudrage peuvent également être couplés avec des technologies de personnalisation de masse. Les consommateurs recherchent de plus en plus des produits personnalisés et adaptés à leurs besoins spécifiques, qu’il s’agisse de couleurs spécifiques, de finitions particulières ou d’éléments graphiques. L’automatisation permet de répondre à cette demande sans perte d’efficacité ni de qualité, en permettant des changements de configurations rapides. Un système de gestion avancé peut identifier chaque commande unique et ajuster automatiquement les paramètres de peinture pour garantir que chaque produit est fini selon les spécifications demandées. Cela permet de combiner des séries de production de masse avec la flexibilité nécessaire pour satisfaire les demandes personnalisées, un atout majeur pour les entreprises confrontées à une concurrence accrue et des cycles de vie de produits plus courts.
En termes de durabilité, la technologie des systèmes de peinture par poudrage continue d’évoluer vers des solutions encore plus respectueuses de l’environnement. Par exemple, les innovations en matière de poudres de peinture écologiques, avec des formulations sans COV et à base de matériaux recyclés, permettent de réduire l’impact environnemental tout en maintenant des performances de revêtement élevées. L’optimisation des cycles de cuisson, notamment avec des fours basse consommation et la récupération d’énergie, contribue également à une réduction significative de la consommation d’énergie, renforçant ainsi l’engagement des entreprises envers la durabilité.
Enfin, les systèmes automatiques de peinture par poudrage permettent de renforcer la traçabilité et la transparence tout au long du processus de production. Grâce à la numérisation, chaque pièce peut être suivie depuis son entrée sur la ligne de peinture jusqu’à sa sortie, avec une documentation complète de son traitement. Cela permet non seulement d’assurer un contrôle qualité rigoureux, mais aussi de répondre aux exigences croissantes des clients et des autorités de régulation en matière de traçabilité et de conformité des produits. Dans des secteurs sensibles comme l’aéronautique, l’automobile ou la pharmacie, cette traçabilité devient un atout majeur pour garantir la qualité et la sécurité des produits finis.
En somme, les systèmes automatiques de peinture par poudrage représentent une avancée technologique majeure dans l’industrie de la finition. Grâce à l’intégration de la robotique, de l’IoT, de la réalité augmentée et de l’intelligence artificielle, ces systèmes deviennent de plus en plus intelligents, efficaces et flexibles. Ils permettent non seulement de répondre aux exigences croissantes de productivité et de personnalisation, mais aussi de contribuer à une production plus durable et respectueuse de l’environnement.
L’avenir des systèmes automatiques de peinture par poudrage continue de se diriger vers une plus grande intégration de technologies avancées et une flexibilité accrue pour répondre aux défis industriels de demain. L’un des domaines les plus prometteurs est l’intégration de la fabrication additive (impression 3D) dans le processus de peinture par poudrage. Cela pourrait révolutionner la manière dont les pièces sont traitées et peintes. Par exemple, des pièces complexes, souvent difficiles à traiter avec des méthodes traditionnelles, pourraient être fabriquées en 3D et peintes immédiatement après leur création, sans nécessiter de processus de préparation longs et coûteux. Cette approche permettrait une personnalisation encore plus poussée tout en maintenant une grande efficacité.
De plus, les systèmes autonomes en développement ne se limitent pas à l’application de la peinture mais intègrent des capacités d’analyse avancée, avec des systèmes de diagnostic autonomes capables de détecter des problèmes avant qu’ils n’affectent la production. En combinant les capteurs de température, de pression, de vibration, ainsi que des technologies de vision artificielle, ces systèmes peuvent évaluer l’état de chaque composant en temps réel et prédire l’usure de certaines parties critiques. Cela permet de planifier les interventions et de réduire les périodes d’inactivité non planifiées.
Dans le même ordre d’idées, l’introduction de la simulation numérique dans le processus de peinture est une autre avancée majeure. Les simulations permettent d’optimiser le processus avant même qu’il ne soit mis en œuvre sur la ligne de production. Cela inclut des simulations de la distribution de la peinture, de la température dans le four de cuisson, et de l’interaction entre les différents matériaux des pièces. Cette approche permet de mieux comprendre le comportement du revêtement avant sa mise en œuvre, ce qui réduit les risques de défauts et optimise l’efficacité des processus.
Les systèmes intelligents de gestion de la production permettront également aux lignes de peinture de s’adapter dynamiquement à la demande et aux conditions de production fluctuantes. Grâce à des algorithmes de planification avancés, ces systèmes peuvent ajuster automatiquement les horaires de travail, le taux de production et la répartition des tâches en fonction des priorités, des commandes et des variations de stock. Cela permet non seulement d’optimiser l’utilisation des ressources, mais aussi de garantir une réactivité maximale face à des demandes changeantes.
La sécurité et la protection des opérateurs continueront d’être une priorité majeure. Les lignes de peinture en poudre de demain intégreront encore plus de technologies de détection des risques et des systèmes de protection automatisés. Les robots et machines, tout en prenant en charge une grande partie du travail, devront être conçus de manière à assurer la sécurité des travailleurs. Cela inclut des systèmes de sécurité avancés comme la détection de présence humaine dans des zones à risque ou des mécanismes d’arrêt d’urgence encore plus réactifs. Le contrôle à distance des lignes de production, facilité par des interfaces utilisateurs simplifiées et des technologies de réalité augmentée, permettra de minimiser les risques d’accidents tout en permettant aux opérateurs d’intervenir efficacement et en toute sécurité.
L’intensification de la demande pour des solutions écologiques continuera de guider les innovations dans les systèmes automatiques de peinture. Les nouvelles formulations de peinture, comme les poudres à base de matériaux recyclés, et l’utilisation de technologies de réduction des émissions (notamment pour les fumées générées lors de la cuisson) deviendront des éléments essentiels pour respecter les normes environnementales strictes. L’intégration d’énergies renouvelables, comme l’énergie solaire ou éolienne, dans le fonctionnement des installations de peinture pourrait également réduire l’empreinte carbone de ces systèmes.
En parallèle, la traçabilité et la gestion des données seront de plus en plus intégrées dans des systèmes centralisés. Les technologies de blockchain, par exemple, pourraient être utilisées pour garantir l’intégrité des données tout au long du processus de production. Cela pourrait inclure des informations sur la provenance des matériaux, les conditions de traitement, et même des données sur les performances des pièces après leur sortie de la ligne de peinture. Ces systèmes de traçabilité permettront aux entreprises de renforcer la confiance de leurs clients, en particulier dans les industries où la qualité et la sécurité des produits sont primordiales.
La personnalisation de la production continuera également à être un axe clé de l’innovation. Les clients, qu’ils soient dans l’industrie automobile, l’électronique ou le mobilier, demandent des produits de plus en plus uniques. La capacité des lignes de peinture automatiques à s’adapter à des volumes de production variés, tout en offrant une personnalisation rapide et précise, devient un atout stratégique majeur. Par exemple, des machines équipées de technologies de vision artificielle pourraient reconnaître des motifs spécifiques, des logos ou des couleurs personnalisées sur chaque pièce et ajuster instantanément les paramètres de pulvérisation en fonction des exigences spécifiques.
Enfin, la formation des opérateurs évoluera également avec l’implémentation de technologies d’apprentissage en ligne et de simulations immersives. Grâce à la réalité virtuelle (RV) ou la réalité augmentée (RA), les opérateurs pourront suivre des formations interactives et immersives sur la gestion des lignes de peinture, la maintenance prédictive, et la résolution de problèmes, sans avoir besoin d’arrêter la production. Ces technologies offriront une formation plus flexible et plus engageante, tout en réduisant les coûts associés à la formation traditionnelle.
En somme, les systèmes automatiques de peinture par poudrage se tournent résolument vers l’avenir avec une interconnexion accrue, une intelligence artificielle toujours plus présente et une durabilité au cœur de leur conception. Ces avancées transformeront le secteur de la finition industrielle, rendant les processus de production plus rapides, plus intelligents, plus flexibles et plus respectueux de l’environnement. L’intégration de nouvelles technologies continuera de redéfinir la manière dont les pièces sont peintes, permettant une personnalisation de masse tout en optimisant l’efficacité et la qualité.
Ligne automatisée de revêtement en poudre
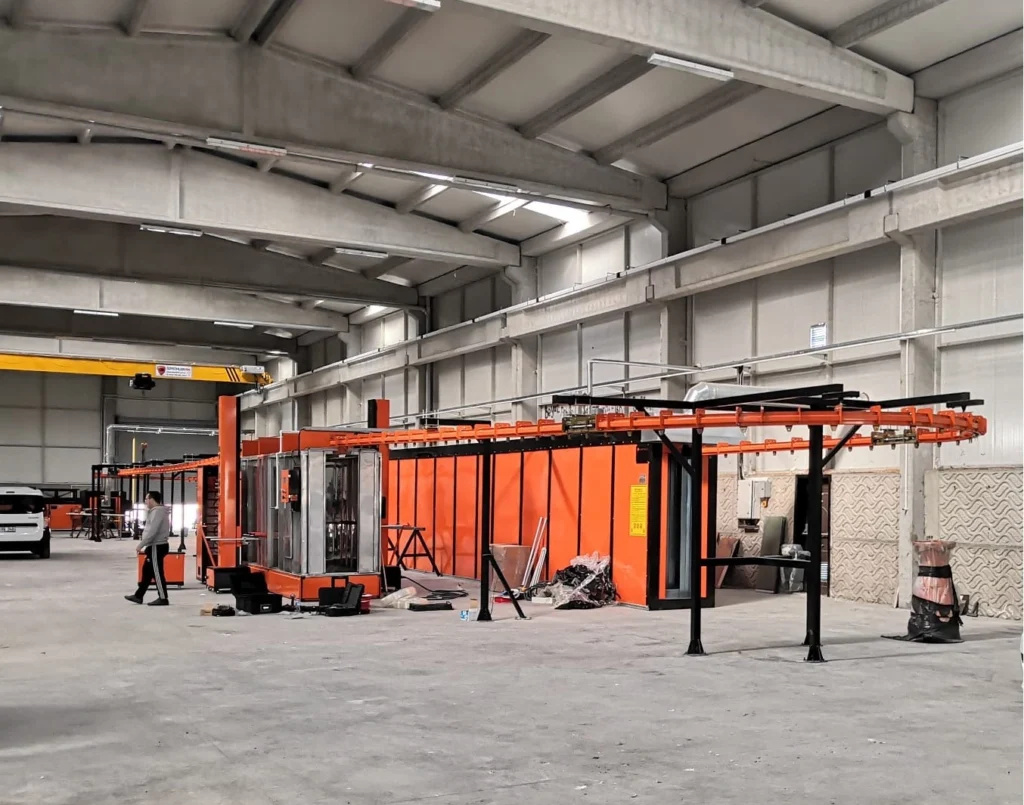
Une ligne automatisée de revêtement en poudre est un système de production hautement sophistiqué et efficace utilisé dans diverses industries pour appliquer un revêtement en poudre sur des pièces métalliques ou autres substrats. Le revêtement en poudre est une technique de finition qui offre une durabilité supérieure, une finition esthétique et une excellente résistance à la corrosion, tout en étant plus respectueuse de l’environnement que les peintures à base de solvants. Ces lignes sont conçues pour fonctionner de manière autonome, avec un minimum d’intervention humaine, garantissant ainsi des performances optimales et une production efficace.
Principaux éléments d’une ligne automatisée de revêtement en poudre :
- Système de préparation des pièces :
Avant l’application du revêtement, les pièces doivent être correctement préparées pour garantir l’adhésion optimale de la poudre. Ce processus peut inclure plusieurs étapes, telles que :- Le nettoyage des pièces, qui peut être effectué par un jet de haute pression, un bain de dégraissage, ou un traitement chimique.
- Le sablage ou la grenaillage pour créer une texture de surface qui facilite l’adhésion du revêtement.
- Le traitement de surface (par exemple, passivation, phosphatation) pour améliorer la corrosion et la résistance à l’usure.
- Système de transport :
Une fois préparées, les pièces sont transportées tout au long de la ligne de production à l’aide de convoyeurs. Ces convoyeurs sont souvent automatiques et permettent un flux continu de pièces, ce qui minimise le temps d’arrêt et optimise l’efficacité de la production. Ils peuvent être suspendus (dans le cas de grandes pièces ou de produits de taille similaire) ou utiliser des convoyeurs à rouleaux pour des pièces plus petites. - Application de la poudre :
L’application du revêtement en poudre est l’étape clé du processus. Cela peut être effectué via deux techniques principales :- Pulvérisation électrostatique : Les pistolets de pulvérisation électrostatiques chargent la poudre et la projettent sur la pièce. L’électricité statique attire la poudre vers la surface, assurant une couverture uniforme. Cette méthode est idéale pour des pièces complexes et garantit une couche de peinture homogène.
- Pulvérisation triboélectrique : Ici, la poudre est chargée par friction, et bien qu’elle soit généralement moins précise que l’électrostatique, elle peut être utilisée pour des applications à plus grande échelle où des vitesses de production élevées sont nécessaires.
- Système de cuisson :
Après l’application de la poudre, les pièces doivent être cuites dans un four à haute température pour permettre à la poudre de fondre et de former une couche lisse et dure. Ce processus de polymérisation peut prendre de 10 à 20 minutes en fonction de la température et du type de poudre utilisée. Les fours peuvent être de type convectif, infrarouge ou mixte, selon les besoins spécifiques de production. - Refroidissement :
Après la cuisson, les pièces doivent être refroidies avant d’être manipulées ou envoyées pour des contrôles qualité. Un système de refroidissement rapide est souvent intégré pour réduire le temps d’attente et augmenter la productivité. - Système de récupération de la poudre excédentaire :
Une partie de la poudre appliquée n’adhère pas à la surface des pièces. Ce surplus est récupéré par un système de récupération (souvent des cyclones ou des filtres) et peut être réutilisé, ce qui contribue à la réduction des déchets et des coûts de matériaux. Ce système est crucial pour maintenir l’efficacité du processus et pour être respectueux de l’environnement. - Contrôle qualité et inspection :
Les lignes automatisées de revêtement en poudre sont équipées de dispositifs de contrôle qualité pour assurer que chaque pièce respecte les normes de finition. Cela peut inclure des inspections visuelles automatisées, des tests d’épaisseur de couche, des tests de durabilité et de résistance à la corrosion. Ces tests sont souvent effectués à l’aide de systèmes de vision industrielle, qui utilisent des caméras et des algorithmes pour détecter les défauts sur les surfaces peintes. - Système de gestion et de supervision :
Une interface de gestion centralisée permet de superviser l’ensemble de la ligne de production, de l’alimentation des pièces à leur finition. Les opérateurs peuvent surveiller en temps réel l’état des machines, l’application de la peinture, la température de cuisson et d’autres paramètres essentiels. Des algorithmes et des systèmes d’intelligence artificielle peuvent être utilisés pour optimiser les processus en fonction des données en temps réel, garantissant ainsi la meilleure performance possible.
Avantages d’une ligne automatisée de revêtement en poudre :
- Efficacité accrue : L’automatisation permet un processus continu, avec une réduction significative des arrêts de production et un contrôle constant de la qualité.
- Réduction des déchets : Grâce à la récupération et la réutilisation de la poudre excédentaire, les pertes de matériaux sont minimisées.
- Personnalisation et flexibilité : Les lignes automatisées peuvent être adaptées pour peindre une grande variété de formes et de tailles de pièces, offrant ainsi une flexibilité importante, notamment pour des productions à petite échelle ou sur mesure.
- Réduction de l’impact environnemental : Le revêtement en poudre est une méthode écologique, car elle ne nécessite pas de solvants et génère moins de COV (composés organiques volatils).
- Durabilité du produit : Le revêtement en poudre offre une finition extrêmement résistante, notamment contre la corrosion, l’usure et les produits chimiques, ce qui en fait un choix populaire dans des secteurs comme l’automobile, l’électroménager, et l’industrie du mobilier.
En conclusion, une ligne automatisée de revêtement en poudre combine technologie de pointe, flexibilité et durabilité, offrant aux entreprises une solution de finition efficace, rentable et respectueuse de l’environnement. Elle est idéale pour des applications industrielles où la rapidité, la qualité et la personnalisation sont des facteurs clés de compétitivité.
Les lignes automatisées de revêtement en poudre représentent une avancée significative dans le domaine de la production industrielle, permettant une productivité accrue tout en garantissant une qualité de finition exceptionnelle. En réduisant au minimum l’intervention humaine, ces systèmes permettent d’optimiser les processus, de réduire les erreurs et d’assurer une uniformité constante dans le revêtement des pièces. L’automatisation permet également d’ajuster rapidement les paramètres de production en fonction des besoins spécifiques, ce qui permet de répondre aux demandes des clients tout en maintenant une efficacité maximale.
Les améliorations dans les technologies de contrôle permettent aux systèmes de s’adapter aux changements dans les matériaux, les conditions environnementales ou même les types de pièces à traiter, ce qui assure une flexibilité totale. Cela permet non seulement de répondre aux besoins de production de masse, mais aussi de s’adapter à des séries de production plus petites et plus diversifiées. L’utilisation d’algorithmes avancés pour la gestion de la ligne, l’intégration de capteurs pour détecter les anomalies en temps réel et les systèmes d’analyse prédictive pour la maintenance améliorent la fiabilité et l’efficacité de la production. La capacité de ces systèmes à détecter des problèmes potentiels avant qu’ils ne deviennent des défauts de production est un atout majeur pour les entreprises qui cherchent à minimiser les risques et à maintenir des standards de qualité élevés.
Les technologies avancées de gestion de la poudre, comme les systèmes de récupération et de réutilisation de la poudre excédentaire, contribuent à l’efficience de la production tout en respectant l’environnement. La possibilité de récupérer et de réintroduire la poudre non utilisée dans le processus permet de réduire la consommation de matériaux, ce qui diminue les coûts opérationnels tout en minimisant les déchets. Ce processus améliore également la durabilité des matériaux et réduit l’impact environnemental en diminuant la quantité de peinture rejetée dans l’environnement.
Par ailleurs, les systèmes automatisés de revêtement en poudre permettent une réduction de la consommation énergétique, en particulier avec l’introduction de fours à basse consommation et de technologies de récupération thermique. Ces avancées contribuent à rendre le processus de revêtement plus écologique tout en réduisant les coûts liés à la consommation d’énergie. L’utilisation de nouvelles formulations de poudres écologiques, souvent sans COV, garantit que l’application de la peinture reste propre et respectueuse de l’environnement.
L’intégration de l’Internet des objets (IoT) dans ces lignes de production permet une surveillance et un contrôle en temps réel des équipements, facilitant la gestion de la production et la planification des maintenances. En collectant des données sur chaque aspect de la production, du processus de peinture au fonctionnement des machines, les gestionnaires peuvent prendre des décisions éclairées basées sur des informations précises, ce qui aide à minimiser les erreurs et à garantir un contrôle qualité optimal.
Une autre évolution prometteuse concerne l’utilisation de la réalité augmentée (RA) pour assister les opérateurs dans la gestion de la ligne de production. Par exemple, les techniciens peuvent recevoir des instructions détaillées et des informations visuelles directement sur leur dispositif de RA, facilitant les interventions techniques et réduisant le risque d’erreurs humaines. Cette technologie permet également de former les nouveaux opérateurs plus rapidement en leur offrant une expérience immersive et interactive qui reproduit les situations réelles qu’ils rencontreront sur le terrain.
L’automatisation continue de transformer les industries grâce à une plus grande précision, une meilleure gestion des ressources et une capacité à s’adapter rapidement aux exigences du marché. Les lignes automatisées de revêtement en poudre représentent une composante essentielle de cette évolution, offrant une solution de finition moderne et efficace qui répond aux défis industriels contemporains. En intégrant des technologies comme l’intelligence artificielle, la robotique, la gestion des données en temps réel et la simulation avancée, ces systèmes offrent une souplesse et une performance qui redéfinissent les standards de qualité et d’efficacité dans le domaine du revêtement industriel.
Les avancées récentes dans les lignes automatisées de revêtement en poudre portent également sur la personnalisation de la production. Les systèmes modernes permettent de configurer et d’adapter facilement les paramètres de production pour des lots de pièces variées. L’intégration de logiciels de gestion de la production intelligente et de systèmes de contrôle avancés permet aux entreprises de gérer des demandes spécifiques en matière de couleur, de finition ou de design, tout en maintenant des niveaux élevés de productivité. Cette flexibilité est cruciale pour les secteurs comme l’automobile, l’électroménager, le mobilier et bien d’autres, où les demandes de personnalisation se multiplient sans compromettre les délais de production.
Les systèmes de vision industrielle jouent un rôle essentiel dans cette personnalisation. Ils permettent de scanner les pièces en continu et de détecter des défauts de peinture ou des irrégularités dans l’application. En utilisant des caméras haute résolution et des algorithmes de traitement d’image, ces systèmes peuvent analyser la qualité du revêtement en temps réel, et ajuster automatiquement les paramètres d’application (tels que la pression de pulvérisation ou l’épaisseur de la couche) pour garantir une finition parfaite à chaque étape. Cela permet de maintenir des standards de qualité très élevés et d’éviter toute re-traitement coûteux.
Les systèmes automatisés de peinture en poudre n’ont pas seulement une influence sur la qualité et la productivité, mais aussi sur la gestion des coûts. L’automatisation réduit la dépendance à la main-d’œuvre et minimise les erreurs humaines, ce qui peut entraîner une baisse significative des coûts de production. De plus, la récupération et la réutilisation de la poudre excédentaire, comme mentionné précédemment, réduit le gaspillage de matériaux, tout en permettant de diminuer l’empreinte carbone du processus.
L’introduction de la maintenance prédictive est un autre avantage majeur des lignes automatisées de revêtement en poudre. Les capteurs IoT et les systèmes de surveillance en temps réel permettent de collecter des données précieuses sur l’état des équipements. Ces informations sont ensuite analysées par des logiciels d’intelligence artificielle qui peuvent anticiper les défaillances des machines avant qu’elles n’affectent la production. Cela permet de planifier les interventions de maintenance de manière plus efficace, réduisant ainsi les temps d’arrêt et prolongeant la durée de vie des équipements. Cette approche proactives permet également de réduire les coûts associés aux réparations urgentes et aux remplacements d’équipement.
Un autre domaine en pleine évolution est l’utilisation de nouveaux matériaux dans le revêtement en poudre. Les chercheurs travaillent sur des poudres plus performantes, offrant des caractéristiques améliorées telles que des propriétés antioxydantes, une meilleure résistance aux conditions climatiques extrêmes ou même des finitions auto-cicatrisantes. Ces innovations ouvrent de nouvelles possibilités pour l’application dans des secteurs comme l’aéronautique, l’automobile, ou encore les infrastructures extérieures, où la résistance aux conditions environnementales est essentielle.
L’accent mis sur la durabilité et la réduction de l’impact environnemental continue de croître. Les lignes de revêtement en poudre de demain seront encore plus écologiques. En plus de l’utilisation de matériaux moins polluants et de technologies de récupération de la chaleur, ces systèmes intègreront des solutions permettant de réduire la consommation d’énergie tout en maintenant des standards élevés de qualité. Les fours basse consommation, utilisant des technologies de récupération thermique ou d’autres systèmes énergétiques alternatifs comme l’énergie solaire ou géothermique, pourraient être utilisés pour rendre le processus de cuisson des pièces plus économe en énergie.
En parallèle, des normes de plus en plus strictes en matière de durabilité et de gestion des ressources poussent les entreprises à se tourner vers des solutions de production plus écologiques et plus respectueuses des réglementations environnementales. Les avancées dans la récupération des matériaux, les systèmes de filtration des émissions et l’optimisation de l’empreinte carbone des lignes de production sont des aspects essentiels pour répondre aux exigences actuelles des industries.
En somme, l’automatisation des lignes de revêtement en poudre est un processus en constante évolution, caractérisé par l’introduction de nouvelles technologies, des améliorations dans les processus de production et une prise en compte accrue des enjeux environnementaux. Ces systèmes ne sont plus seulement des outils de production, mais des leviers stratégiques qui permettent aux entreprises de répondre à des demandes plus complexes, d’améliorer leur compétitivité et de garantir la qualité de leurs produits tout en minimisant leur impact sur l’environnement. Les tendances actuelles laissent entrevoir des systèmes de production de plus en plus intelligents, interconnectés et responsables, capables de relever les défis d’un marché mondial de plus en plus exigeant.
Les lignes automatisées de revêtement en poudre de demain intégreront également des innovations liées à l’intelligence artificielle (IA) et au machine learning pour aller encore plus loin dans l’optimisation des processus. Ces technologies permettront aux systèmes de production de s’adapter de manière autonome aux conditions de fabrication, d’apprendre des données historiques et de prévoir les ajustements nécessaires en fonction des besoins futurs. Par exemple, un système pourrait ajuster automatiquement les paramètres de pulvérisation pour compenser les variations dans l’humidité ou la température ambiante, assurant ainsi une qualité de revêtement constante quel que soit l’environnement de production. Cela permettrait non seulement de maintenir des standards de qualité élevés, mais aussi d’améliorer l’efficacité des processus, réduisant ainsi les gaspillages de matériaux et d’énergie.
Le recours à des systèmes de gestion de la production basés sur le cloud devient aussi une tendance croissante. Ces systèmes permettent de centraliser les données provenant de l’ensemble de la ligne de production, offrant aux gestionnaires une vue d’ensemble en temps réel de l’ensemble du processus de revêtement. Grâce à des outils d’analyse avancée, les responsables peuvent prendre des décisions stratégiques fondées sur des informations actualisées instantanément, ce qui optimise la prise de décision et l’allocation des ressources. Ces solutions offrent également une meilleure collaboration entre différents sites de production et une gestion améliorée des stocks, permettant aux entreprises de réduire les coûts opérationnels et d’améliorer la traçabilité des produits.
Une autre évolution passionnante concerne l’interaction homme-machine. Avec la montée en puissance des interfaces utilisateurs intuitives et des technologies de réalité augmentée (RA), les opérateurs pourront désormais contrôler et ajuster les lignes de production de manière plus immersive et interactive. Par exemple, un technicien pourrait utiliser des lunettes de réalité augmentée pour afficher des informations en temps réel directement sur la machine ou la pièce qu’il manipule, facilitant ainsi les diagnostics et la maintenance. Ces technologies permettent de réduire les erreurs humaines, d’accélérer la formation des nouveaux employés et de rendre le travail plus sécurisé.
En ce qui concerne l’automatisation des contrôles qualité, l’utilisation de technologies avancées telles que la vision artificielle, les capteurs intelligents et l’analyse de données permettra d’atteindre des niveaux de précision inégalés. Les systèmes de vision industrielle, alimentés par des algorithmes d’intelligence artificielle, seront capables de détecter des défauts invisibles à l’œil nu, comme des microfissures dans le revêtement ou des irrégularités dans l’épaisseur de la couche. Cela ouvrira la voie à des processus de contrôle qualité plus efficaces et plus rapides, ce qui réduira considérablement les risques de rejet de production ou de non-conformité.
La connectivité accrue entre les équipements au sein d’une ligne de production et les autres systèmes industriels, comme les ERP (Enterprise Resource Planning) ou les systèmes de gestion de la chaîne d’approvisionnement, favorisera une optimisation continue des processus. Par exemple, l’intégration des données des machines avec celles des fournisseurs et des clients permettra de mieux anticiper les besoins en matières premières et en délais de livraison, contribuant à une logistique intelligente. Les lignes de production seront donc non seulement optimisées au niveau local, mais également en fonction de l’ensemble du flux de production de l’entreprise, ce qui offrira une flexibilité accrue et une meilleure réactivité face aux fluctuations du marché.
La sécurité et la protection des travailleurs continueront d’être des priorités clés. Les nouvelles technologies permettront de rendre les environnements de production plus sûrs, avec des dispositifs de surveillance en temps réel pour détecter les anomalies de fonctionnement, les risques de défaillance ou même les situations dangereuses pour les opérateurs. Des systèmes de protection intelligents pourront déclencher des alertes et, dans certains cas, arrêter automatiquement les machines en cas de détection d’un problème, protégeant ainsi les travailleurs tout en minimisant les pertes de production. Par ailleurs, l’amélioration des interfaces de contrôle, associée à des technologies de commande vocale et de réalité augmentée, permettra aux opérateurs de contrôler la ligne de production tout en ayant les mains libres, réduisant ainsi les risques d’accidents liés à l’interaction physique avec les machines.
L’évolutivité des lignes de production est également un facteur de plus en plus important dans les industries modernes. Les entreprises cherchent à installer des lignes de revêtement en poudre capables de s’adapter rapidement aux évolutions de la demande, de la taille des productions et des types de pièces traitées. Cela inclut la possibilité d’ajouter facilement de nouveaux équipements, de modifier les configurations de la ligne ou de remplacer des composants sans perturber l’ensemble du processus de production. Cette flexibilité est cruciale pour répondre aux besoins d’une économie de plus en plus axée sur l’agilité et la capacité à s’adapter aux tendances du marché.
Enfin, l’importance croissante des normes écologiques et des réglementations environnementales va continuer de façonner l’évolution des lignes de revêtement en poudre. Les exigences de durabilité, de recyclabilité et de réduction des émissions seront de plus en plus strictes. À cet égard, les technologies de gestion des émissions de poussières, les systèmes de filtration avancés, et l’utilisation de matériaux de revêtement écologiques seront des critères de plus en plus déterminants pour les choix technologiques. La capacité à répondre aux exigences environnementales tout en maintenant une efficacité de production optimale deviendra un avantage concurrentiel majeur pour les entreprises.
En conclusion, les lignes automatisées de revêtement en poudre vont continuer d’évoluer, intégrant des technologies de pointe pour optimiser les performances, améliorer la qualité des produits finis et réduire l’impact environnemental. Grâce à l’automatisation, l’intelligence artificielle, la connectivité et l’intégration d’innovations écologiques, ces systèmes offriront des solutions toujours plus intelligentes, flexibles et durables pour répondre aux défis de l’industrie moderne.
Installation automatisée de peinture en poudre
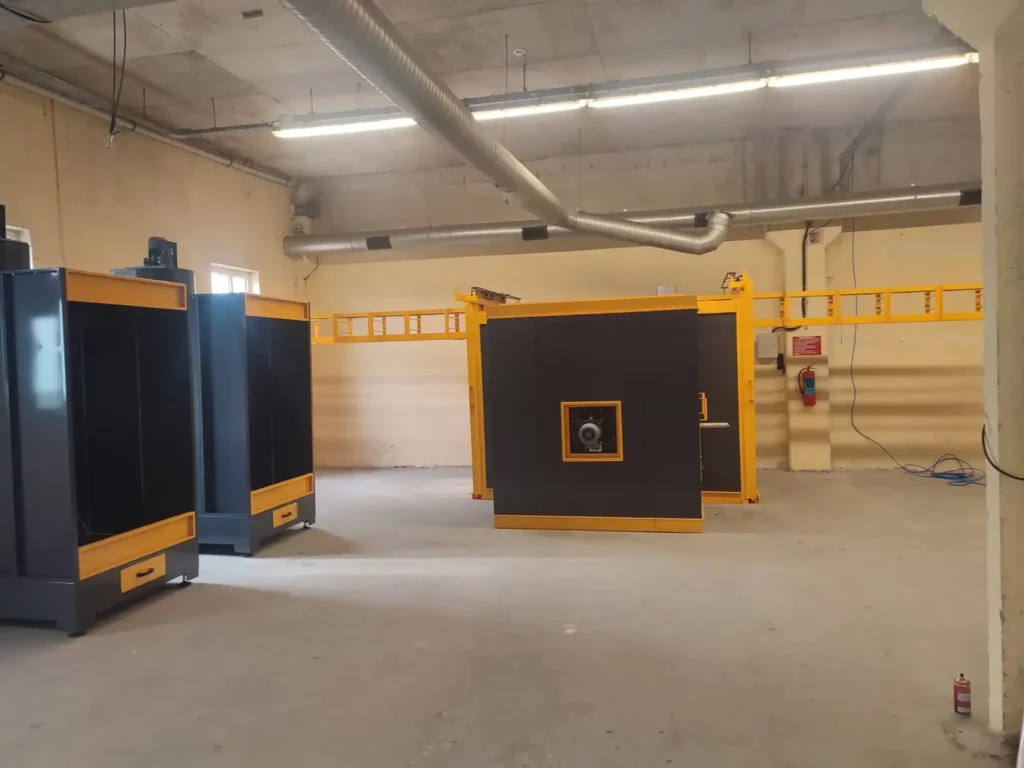
Une installation automatisée de peinture en poudre est un système de production avancé utilisé pour appliquer un revêtement en poudre sur des pièces industrielles de manière automatique et continue. Cette technologie est largement adoptée dans divers secteurs, tels que l’automobile, l’électroménager, les équipements industriels, et le mobilier, en raison de ses avantages en termes de qualité, d’efficacité, de respect de l’environnement et de réduction des coûts.
Le processus de peinture en poudre est un procédé de finition par pulvérisation de poudre, suivi d’une cuisson pour durcir la couche appliquée. Il est très apprécié pour sa capacité à produire des finitions durables, résistantes aux conditions climatiques, à la corrosion et à l’usure. L’installation automatisée assure la production en grande série, avec un minimum d’intervention humaine, ce qui permet de maintenir un haut niveau de qualité tout en maximisant la productivité.
Fonctionnement d’une installation automatisée de peinture en poudre
- Préparation des pièces :
Avant de commencer l’application de la poudre, les pièces doivent être soigneusement préparées. Cela inclut des étapes de nettoyage pour éliminer les impuretés comme l’huile, la graisse, la rouille et les autres contaminants. Des méthodes telles que le nettoyage par jet haute pression, l’immersion dans des solutions de dégraissage ou l’utilisation de sablage sont utilisées. Parfois, un traitement de surface, comme la passivation ou la phosphatation, peut être réalisé pour améliorer l’adhérence du revêtement. - Système de transport :
Les pièces préparées sont transportées tout au long de la ligne de production à l’aide de convoyeurs automatiques. Ces convoyeurs peuvent être suspendus ou à rouleaux, et ils transportent les pièces de manière continue, ce qui permet de maximiser l’efficacité et de réduire les temps d’arrêt. Le convoyeur peut être programmé pour ajuster la vitesse en fonction du type de produit, de la taille des pièces ou de la quantité à produire. - Application de la poudre :
L’application du revêtement en poudre est effectuée par pistolets électrostatiques qui chargent la poudre et la projettent sur la surface de la pièce. L’électricité statique attire la poudre, ce qui permet de garantir une couverture uniforme de la pièce. La poudre est pulvérisée en fine brume, ce qui permet de pénétrer dans les détails et les coins de la pièce. L’application peut être effectuée en plusieurs passes pour obtenir une épaisseur uniforme, selon les spécifications du produit. - Récupération de la poudre excédentaire :
Une partie de la poudre appliquée ne se fixe pas à la pièce. Cette poudre excédentaire est récupérée par un système de filtration et de récupération, tel qu’un cyclone ou un système de filtration à cartouche. La poudre récupérée peut être filtrée et réutilisée, ce qui contribue à la réduction des déchets et à l’optimisation des coûts de production. - Cuisson dans un four :
Après l’application de la poudre, les pièces sont envoyées dans un four de cuisson où la poudre est chauffée à une température élevée (généralement entre 160 et 200°C). La chaleur fait fondre la poudre, qui forme une couche lisse et dure. Cette étape est essentielle pour obtenir une finition durable, résistante et de qualité. La durée et la température de cuisson dépendent du type de poudre utilisée et des spécifications des pièces à traiter. - Refroidissement :
Après la cuisson, les pièces sont refroidies rapidement pour stabiliser la couche de revêtement et éviter toute déformation. Des systèmes de refroidissement peuvent être intégrés à la ligne, assurant que la température des pièces redescende rapidement à des niveaux sûrs et efficaces avant qu’elles ne soient manipulées davantage. - Contrôle qualité automatisé :
Des systèmes de vision industrielle et de capteurs intelligents sont souvent intégrés à l’installation pour effectuer des contrôles qualité en temps réel. Ces systèmes peuvent inspecter la surface des pièces, détecter les défauts visuels (comme les irrégularités de surface, les coulures ou les manques de revêtement) et vérifier l’épaisseur du film de peinture. Ils peuvent automatiquement ajuster les paramètres de l’application ou de la cuisson pour garantir que toutes les pièces répondent aux normes de qualité. - Emballage et stockage :
Une fois que les pièces sont refroidies et inspectées, elles sont prêtes à être emballées et expédiées. Le système automatisé peut inclure une station d’emballage pour assurer une gestion efficace du produit fini, avant son expédition vers le client ou l’entrepôt.
Avantages d’une installation automatisée de peinture en poudre
- Haute efficacité et productivité :
L’automatisation réduit les temps de cycle et augmente la capacité de production tout en maintenant un contrôle strict de la qualité. Le processus continu assure des résultats homogènes à grande échelle, ce qui est essentiel pour les industries nécessitant une production de masse. - Réduction des coûts :
En réduisant la dépendance à la main-d’œuvre, en maximisant l’utilisation des matériaux grâce à la récupération de la poudre excédentaire, et en optimisant l’utilisation de l’énergie dans le processus de cuisson, les installations automatisées permettent une réduction significative des coûts de production. - Qualité constante :
Les systèmes automatisés assurent une application précise et uniforme du revêtement, ce qui garantit une finition de haute qualité sur toutes les pièces produites. Les contrôles de qualité automatisés permettent également de détecter les défauts immédiatement, évitant les erreurs et le besoin de retraitement. - Respect de l’environnement :
Le revêtement en poudre est une solution écologique, car il ne nécessite pas de solvants ni d’autres produits chimiques dangereux. L’utilisation de poudres sans COV (composés organiques volatils) et la récupération des matériaux excédentaires contribuent à un processus de production plus respectueux de l’environnement. - Flexibilité :
Les installations automatisées peuvent être configurées pour traiter différentes tailles de pièces et offrir une grande variété de finitions, de couleurs et de textures. Cela permet aux entreprises de répondre à des demandes variées sans avoir à modifier drastiquement la ligne de production. - Durabilité et résistance du revêtement :
Le revêtement en poudre offre une finition extrêmement durable, résistante aux rayures, à l’humidité, à la chaleur et aux produits chimiques. Il est idéal pour les pièces exposées à des conditions difficiles, ce qui le rend particulièrement adapté à des secteurs comme l’automobile, les équipements extérieurs, et l’électroménager.
En résumé, une installation automatisée de peinture en poudre est une solution hautement efficace, flexible et écologiquement responsable pour appliquer des finitions de qualité à grande échelle. Elle permet de répondre aux défis de la production industrielle moderne, en offrant des résultats homogènes et en minimisant les coûts, tout en garantissant une conformité stricte aux normes de qualité et environnementales.
Une installation automatisée de peinture en poudre transforme radicalement la manière dont les industries appliquent des finitions sur leurs produits. Grâce à l’automatisation, les processus sont optimisés pour garantir une production rapide et précise tout en réduisant les risques d’erreur humaine. Les machines et les systèmes intelligents de ces lignes assurent une uniformité de qualité qui est difficile à obtenir avec des processus manuels. Cela permet non seulement d’améliorer la productivité, mais aussi d’assurer une finition parfaite à chaque cycle de production.
La capacité à récupérer la poudre excédentaire et à la réutiliser est une autre caractéristique importante des installations automatisées. Non seulement cela réduit les coûts liés aux matériaux, mais cela permet aussi de minimiser l’impact environnemental en réduisant les déchets. Cela va de pair avec la gestion optimisée de l’énergie, car les systèmes automatisés sont souvent conçus pour consommer moins d’énergie tout en maintenant un rendement élevé. Les fours basse consommation et les techniques de récupération de chaleur, intégrées dans ces lignes de production, permettent de réduire l’empreinte énergétique tout en maintenant des niveaux de qualité constants.
En outre, l’automatisation permet une grande flexibilité. Les lignes de peinture en poudre peuvent facilement s’adapter aux variations des besoins de production. Que ce soit pour un petit lot de production ou pour une grande série, le système peut être ajusté pour s’adapter à différentes tailles de pièces, formes et couleurs sans perturber le flux de production. La rapidité des ajustements est un atout majeur pour les industries qui doivent répondre à des demandes de plus en plus spécifiques et diversifiées. Cela se traduit également par une réduction du temps de préparation, car les configurations peuvent être modifiées à distance via des interfaces utilisateur simples et intuitives.
La qualité du revêtement est également améliorée grâce à des systèmes de contrôle automatisés de la qualité. Des technologies de vision industrielle et des capteurs peuvent détecter des défauts invisibles à l’œil nu, comme des imperfections dans l’application de la poudre ou des variations d’épaisseur du film de peinture. Ces systèmes assurent que chaque pièce est inspectée en temps réel, permettant de détecter immédiatement les défauts et d’ajuster les paramètres de la ligne pour corriger toute erreur. Cela améliore l’efficacité en éliminant les reprises et les retouches qui peuvent ralentir la production.
L’automatisation permet également une meilleure gestion des ressources humaines. Avec moins de dépendance à la main-d’œuvre, les opérateurs sont libérés des tâches répétitives et peuvent se concentrer sur la supervision du processus, la gestion des alertes ou des anomalies, et l’entretien préventif des équipements. De plus, la formation des employés est simplifiée, car l’interface des machines est conçue pour être conviviale, permettant aux opérateurs d’interagir facilement avec les systèmes de contrôle et de surveillance. L’évolution des interfaces utilisateurs vers des écrans tactiles ou des commandes vocales rend l’interaction avec les machines plus intuitive et plus rapide.
Les technologies de maintenance prédictive sont également un point fort des installations automatisées. Grâce à la collecte continue de données sur les performances des équipements, le système peut détecter les signes avant-coureurs de défaillances potentielles et alerter les techniciens avant que des problèmes majeurs ne surviennent. Cela permet de réduire les temps d’arrêt imprévus et de planifier les opérations de maintenance de manière plus efficace, ce qui améliore la disponibilité de la ligne de production et réduit les coûts de réparation d’urgence.
En termes d’impact environnemental, l’automatisation des lignes de peinture en poudre joue également un rôle essentiel. Les technologies permettent non seulement de réduire la consommation de matériaux et d’énergie, mais elles facilitent également le respect des réglementations environnementales. L’absence de solvants et de produits chimiques dangereux dans les peintures en poudre est un avantage majeur pour la santé des travailleurs et la réduction des émissions de polluants. Les systèmes de filtration et de récupération des particules de peinture excédentaires assurent que les émissions de poussières de peinture sont minimisées, ce qui contribue à un environnement de travail plus propre.
L’automatisation dans ce domaine représente aussi une opportunité pour les entreprises de se démarquer sur le marché en offrant une plus grande consistance et rapidité dans leurs cycles de production. Cela est particulièrement important dans des secteurs où les exigences de qualité et de délai de livraison sont cruciales, comme dans l’automobile ou l’électronique. Les clients peuvent ainsi bénéficier de produits finis d’une qualité homogène, qui répondent strictement aux spécifications, et ce, dans des délais plus courts.
La combinaison de flexibilité, réduction des coûts, amélioration de la qualité et responsabilité environnementale fait des installations automatisées de peinture en poudre un investissement stratégique pour les entreprises qui cherchent à renforcer leur compétitivité. L’évolution continue de ces systèmes, en particulier avec l’intégration de nouvelles technologies comme l’intelligence artificielle, la robotique avancée et la connectivité, permet d’anticiper les besoins futurs du marché tout en maintenant une productivité élevée et un impact minimal sur l’environnement.
En résumé, l’installation automatisée de peinture en poudre est un système clé pour l’industrie moderne, offrant un haut niveau de performance, d’efficacité et de durabilité. Elle incarne l’avenir de la finition de surface industrielle en alliant innovation technologique, rentabilité et respect des normes environnementales.
L’évolution continue des technologies dans les installations de peinture en poudre automatisées ouvre la voie à une personnalisation accrue des produits finis. À mesure que les capacités des machines augmentent, il devient plus facile pour les fabricants de proposer des finitions sur mesure, que ce soit en termes de textures, de couleurs ou d’effets spéciaux (par exemple, des finitions métalliques, mates, ou satinées). Ces options sont non seulement possibles pour de grandes séries de production, mais aussi pour des lots plus petits et des demandes spécifiques. Cela permet aux entreprises de répondre à une demande plus large et plus diversifiée, tout en maintenant des niveaux de production élevés.
Une autre grande avancée dans ce domaine concerne l’optimisation de la chaîne logistique. En intégrant des systèmes de gestion des données en temps réel, les installations automatisées permettent une meilleure gestion des stocks de matériaux et des délais de production. Par exemple, la gestion intelligente des flux de travail permet de prévoir et d’anticiper les besoins en matériaux en fonction des prévisions de production et de la demande du marché. De plus, avec la connectivité accrue, les fournisseurs peuvent être directement intégrés dans la chaîne de production, facilitant ainsi l’approvisionnement en matières premières. Les lignes automatisées peuvent, grâce à ces technologies, ajuster instantanément les quantités de matériaux nécessaires en fonction de la vitesse de production ou des spécifications de chaque commande.
Les solutions de maintenance prédictive ont également un impact significatif sur la performance globale de l’installation. Plutôt que de se fier à une maintenance réactive ou planifiée à des intervalles réguliers, les technologies modernes permettent de surveiller en continu les conditions de fonctionnement des équipements, de collecter des données à partir de capteurs et de prédire les défaillances avant qu’elles ne se produisent. Cela permet non seulement de réduire les temps d’arrêt imprévus, mais aussi de minimiser les coûts liés aux réparations. Par exemple, un système de détection des vibrations peut alerter un opérateur si un moteur est sur le point de tomber en panne, permettant ainsi de planifier une intervention avant que l’équipement ne soit hors service.
En termes de traçabilité et de conformité, les installations automatisées offrent également un grand avantage. Grâce à la numérisation des données de production, chaque étape du processus est enregistrée et peut être suivie en temps réel. Cela est particulièrement important pour répondre aux normes de qualité, aux exigences réglementaires et pour assurer une traçabilité des produits dans des secteurs où la conformité est essentielle, comme l’aéronautique, l’automobile et les produits de consommation. Chaque pièce est équipée d’un identifiant unique qui permet de suivre sa progression dans la ligne de production, garantissant ainsi que chaque produit respecte les spécifications et les critères de qualité.
Les systèmes de gestion de la production basés sur l’intelligence artificielle (IA) vont encore plus loin en permettant une planification dynamique et automatisée des tâches. L’IA peut analyser les données provenant de différentes machines et ajuster en temps réel les paramètres de la ligne de production pour répondre aux besoins spécifiques de chaque commande. Par exemple, elle pourrait ajuster automatiquement la température de cuisson en fonction du type de poudre utilisé ou optimiser la vitesse de la ligne pour maximiser le rendement sans compromettre la qualité. Cela permet d’adapter la production en fonction des conditions du moment tout en optimisant les ressources disponibles.
L’impact sur la flexibilité de la production est particulièrement notoire. Les installations automatisées peuvent désormais s’adapter à des changements de taille, de type de pièce ou de spécifications de finition presque instantanément. Cela permet aux entreprises de réagir rapidement aux évolutions des demandes du marché, de produire des séries plus petites ou personnalisées, tout en maintenant une efficacité optimale. Un autre avantage notable est la réduction des temps d’arrêt lors du changement de configuration. Les systèmes modernes permettent de reprogrammer la ligne de manière plus rapide et plus fluide, ce qui maximise le temps de production utile et minimise les pertes de temps liées à la préparation et à la configuration des équipements.
Un aspect particulièrement important de l’automatisation est l’amélioration des conditions de travail. La réduction de la nécessité d’une intervention humaine directe dans les processus de peinture diminue non seulement le risque d’erreurs humaines, mais aussi les risques physiques associés à des tâches répétitives et souvent dangereuses, comme la manipulation de produits chimiques ou l’exposition à des températures élevées. Les opérateurs peuvent se concentrer sur des tâches plus stratégiques, comme la surveillance des systèmes ou la gestion des données de production, ce qui améliore la sécurité au travail tout en rendant les processus plus fluides et plus efficaces.
Avec le focus croissant sur la durabilité et la réduction de l’empreinte carbone, les technologies écologiques se développent rapidement dans ce domaine. Des innovations telles que l’utilisation de poudres sans solvant, de systèmes de filtration plus performants et de recyclage amélioré de la poudre excédentaire contribuent à rendre l’installation plus respectueuse de l’environnement. L’intégration de systèmes de réduction des émissions et de recyclage de la chaleur dans la phase de cuisson des pièces optimise encore davantage les processus en réduisant les émissions et les consommations d’énergie.
Enfin, l’intégration de la numérisation dans les lignes de production permet une gestion plus agile des délais de livraison. En ayant accès à des informations en temps réel, les responsables de production peuvent ajuster rapidement les plannings de travail pour répondre aux urgences, tout en optimisant l’utilisation des ressources. Cela rend l’entreprise plus agile et capable de répondre à des commandes plus flexibles, notamment pour des marchés qui exigent des délais de livraison courts et des produits personnalisés.
En conclusion, les installations automatisées de peinture en poudre représentent l’avenir de l’industrie des revêtements en raison de leur capacité à offrir une production plus rapide, flexible, écologique et rentable. Elles permettent non seulement de maintenir des standards de qualité élevés, mais aussi de répondre aux défis contemporains de durabilité et d’efficacité. L’intégration des nouvelles technologies, telles que l’intelligence artificielle, la maintenance prédictive et l’optimisation énergétique, transforme ces installations en systèmes intelligents capables de s’adapter en temps réel aux besoins du marché, tout en garantissant des performances et une sécurité accrues.
Les installations automatisées de peinture en poudre continuent d’évoluer grâce à l’intégration de technologies de pointe et à l’innovation continue dans le domaine de la production industrielle. Une des avancées majeures est la connectivité industrielle, permettant aux lignes de production de devenir une partie intégrante des usines intelligentes. Les équipements, les capteurs et les contrôleurs sont désormais reliés à des plateformes numériques, ce qui facilite l’accès à des données en temps réel, la gestion à distance et l’optimisation continue des processus de production.
L’Internet des objets (IoT) joue un rôle clé dans cette évolution en permettant une surveillance constante des équipements. Les capteurs IoT installés sur chaque machine mesurent des variables critiques telles que la température, l’humidité, la vitesse de transport, la consommation d’énergie, etc. Ces données sont collectées et analysées à distance, permettant aux techniciens et aux responsables de production de détecter des anomalies ou de prévoir des défaillances avant qu’elles n’impactent la production. Les alertes automatiques sont envoyées en cas de dysfonctionnements, réduisant ainsi les interruptions et améliorant la productivité globale.
Dans le même sens, l’intégration de l’intelligence artificielle (IA) dans les installations de peinture en poudre permet une gestion plus optimisée des flux de production. L’IA peut analyser des données provenant de diverses sources en temps réel et prendre des décisions automatisées pour ajuster les paramètres de la ligne en fonction des besoins spécifiques du processus. Par exemple, en fonction des données collectées, l’IA peut ajuster la quantité de poudre appliquée, la vitesse de la ligne, ou la température du four pour garantir une finition parfaite tout en minimisant la consommation de ressources et d’énergie. Ce niveau de personnalisation et d’adaptabilité permet aux entreprises de réduire les gaspillages et d’améliorer la rentabilité de leurs installations.
Un autre domaine d’amélioration se trouve dans les technologies de traitement de la surface avant l’application de la peinture. Les systèmes de préparation de surface automatisés, tels que les traitements de sablage ou de nettoyage par plasma, sont désormais utilisés pour assurer une adhésion maximale de la poudre. Ces technologies garantissent que les surfaces des pièces sont parfaitement nettoyées et prêtes à recevoir le revêtement en poudre, ce qui améliore la durabilité et l’aspect esthétique des produits finis.
Les systèmes de robotique avancée sont également au cœur de ces progrès. L’utilisation de robots de peinture permet une flexibilité exceptionnelle dans le traitement de pièces aux formes complexes ou de tailles variées. Ces robots peuvent s’adapter rapidement à différents types de produits, ajustant leur trajectoire, leur vitesse et leur distance pour optimiser la couverture et la qualité du revêtement. Leur capacité à atteindre des zones difficiles d’accès ou des géométries spécifiques améliore la qualité du travail, réduit les erreurs humaines et optimise le temps de production.
L’évolution des systèmes de cuisson dans les installations de peinture en poudre est également significative. Les fours à radiation infrarouge ou à air pulsé permettent des temps de cuisson plus courts tout en maintenant une température uniforme à travers la pièce. Cela se traduit par des économies d’énergie, car ces technologies ciblent directement la surface des pièces à traiter, réduisant ainsi la perte de chaleur. Les systèmes de cuisson à basse température sont aussi de plus en plus populaires, car ils permettent de traiter des matériaux plus sensibles à la chaleur, comme les plastiques ou certains métaux légers, tout en préservant la qualité du revêtement.
Dans une optique d’économie circulaire, certaines installations sont également équipées de systèmes de recyclage de la poudre encore plus efficaces. Les systèmes de récupération ne se contentent pas de collecter la poudre excédentaire, mais ils la traitent pour la réutiliser dans des conditions optimales. La recyclabilité des poudres utilisées dans les installations automatisées est un élément clé de la durabilité de ces processus. La réduction des déchets de peinture et la possibilité de recycler la poudre excédentaire permettent aux entreprises de réaliser des économies substantielles tout en contribuant à la réduction de leur empreinte environnementale.
Les systèmes de vision artificielle et de contrôle qualité automatisé sont de plus en plus utilisés pour garantir des finitions impeccables. Ces systèmes peuvent inspecter la surface des pièces après application de la peinture en poudre, détecter les défauts minimes ou les variations d’épaisseur et, dans certains cas, ajuster immédiatement le processus de peinture pour corriger le problème. Cela permet d’assurer une qualité constante, réduisant les taux de rejet et garantissant que les produits finaux respectent les spécifications exactes.
Le développement de nouvelles générations de poudres a également révolutionné le secteur. Les poudres thermodurcissables et les poudres à base de polymères de nouvelle génération offrent des caractéristiques améliorées, comme une plus grande résistance aux rayures, une meilleure résistance aux intempéries et des performances accrues dans des environnements extrêmes. En parallèle, des poudres à faible impact environnemental sont désormais disponibles, répondant à des préoccupations croissantes concernant les émissions de COV (composés organiques volatils) et la toxicité des matériaux utilisés dans les processus de finition.
La maintenance à distance et le diagnostic à distance sont désormais possibles grâce à des systèmes de gestion centralisés. Les installations peuvent être surveillées, diagnostiquées et même mises à jour en ligne. Cela réduit la nécessité d’interventions physiques sur site, optimise le temps des techniciens et permet aux entreprises de maintenir leurs lignes de production à un niveau optimal, en réduisant le coût de maintenance global.
Enfin, la tendance vers des installations modulaires de peinture en poudre est en forte croissance. Ces installations offrent une flexibilité accrue, permettant aux entreprises de commencer avec un système de production de taille modeste et d’agrandir ou de modifier facilement la ligne en fonction des besoins futurs. Cela permet aux petites et moyennes entreprises de profiter des avantages des technologies de pointe sans avoir à investir dans des installations trop coûteuses dès le départ.
Ainsi, les progrès technologiques et les innovations dans le domaine de la peinture en poudre automatisée continuent d’améliorer l’efficacité, la flexibilité, la qualité et la durabilité des processus industriels. En intégrant des technologies de pointe telles que l’intelligence artificielle, la robotique avancée, la connectivité IoT et les nouvelles solutions de recyclage, les installations automatisées permettent aux entreprises de répondre aux demandes croissantes du marché tout en minimisant leur impact environnemental. Ces évolutions redéfinissent le futur des processus de finition industrielle, offrant une combinaison d’efficacité, de personnalisation, de durabilité et de rentabilité.
Chaîne automatique de peinture en poudre
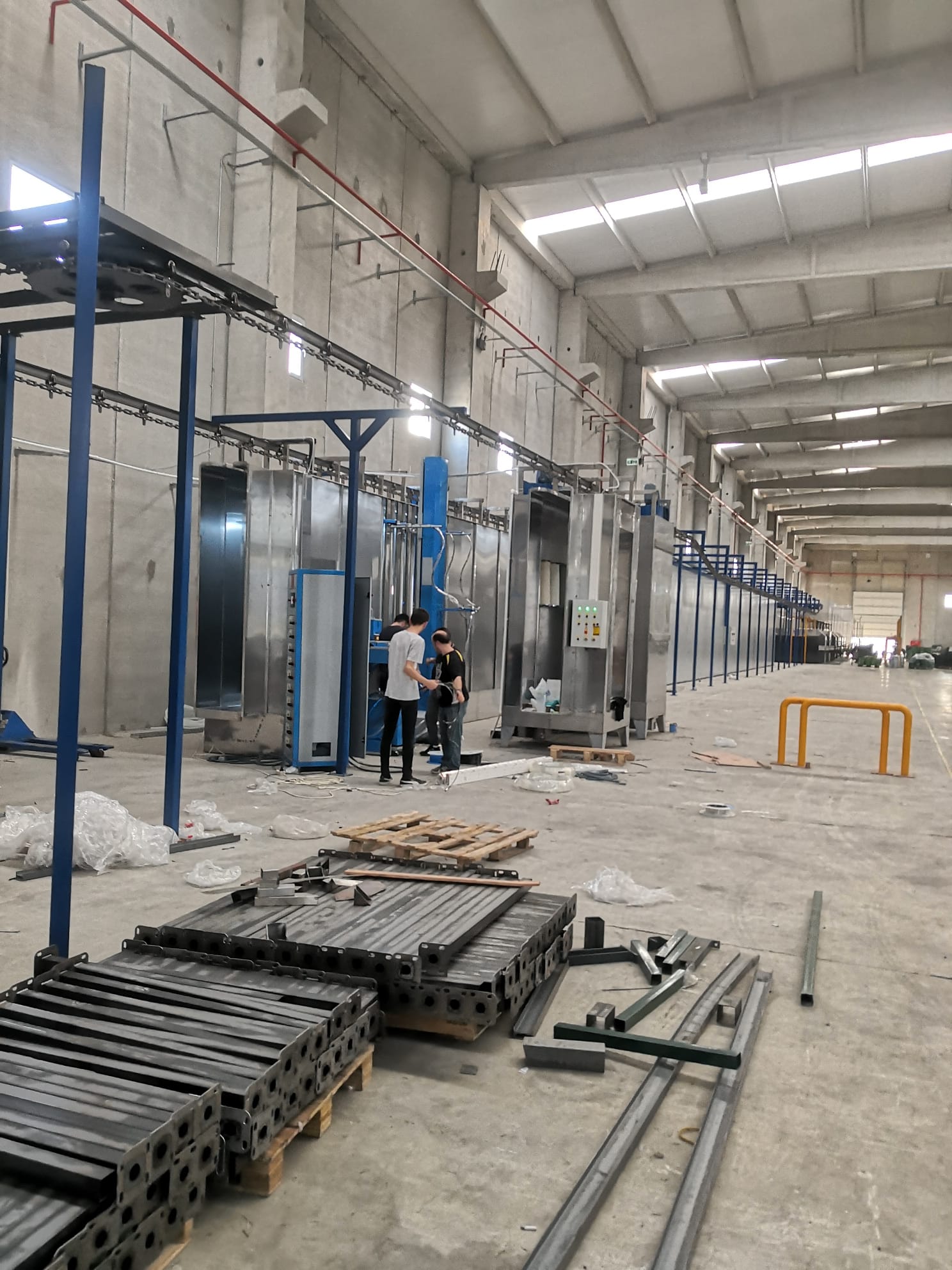
Une chaîne automatique de peinture en poudre est un système intégré utilisé dans les industries pour appliquer une finition en poudre sur des pièces métalliques ou autres substrats. Ce type de système est conçu pour fournir un revêtement uniforme et de haute qualité, tout en optimisant les processus de production. La chaîne de peinture en poudre fonctionne par un procédé électrostatique qui permet d’appliquer la poudre de manière précise et contrôlée, suivie par un processus de durcissement thermique pour fixer la peinture.
Fonctionnement de la chaîne automatique de peinture en poudre :
- Préparation des pièces : La chaîne commence par un processus de préparation des pièces, essentiel pour garantir l’adhérence de la peinture. Cela inclut le nettoyage des pièces, souvent réalisé par des systèmes de dégraissage, sablage ou nettoyage par plasma, qui éliminent les contaminants et oxydes de la surface avant l’application du revêtement en poudre.
- Application de la poudre : Après le nettoyage, les pièces sont transportées dans la cabine de peinture. Ici, la peinture en poudre est pulvérisée sur les pièces à l’aide de pistolets électrostatiques. Ces pistolets chargent électriquement la poudre qui est ensuite attirée par la surface de la pièce, assurant ainsi un dépôt uniforme et une couverture totale, même dans les zones difficiles d’accès.
- Contrôle de la quantité et de la qualité de la poudre : Les systèmes automatiques intègrent souvent des technologies avancées pour réguler la quantité de poudre appliquée et éviter le gaspillage. Des systèmes de contrôle en temps réel, parfois associés à des caméras ou capteurs de vision industrielle, permettent d’ajuster automatiquement le processus pour garantir une application uniforme et de haute qualité.
- Cuisson ou durcissement : Après l’application de la poudre, les pièces sont ensuite transférées dans un four de durcissement, où elles sont chauffées à une température spécifique pour faire fondre et durcir la poudre. Cette étape est cruciale pour fixer le revêtement et lui conférer sa résistance, sa durabilité, et sa finition. Le temps et la température de cuisson sont ajustés en fonction du type de poudre utilisé et du matériau de la pièce.
- Refroidissement : Une fois que la pièce est correctement cuite, elle est ensuite refroidie pour permettre à la peinture de se solidifier complètement. Les systèmes automatiques de peinture en poudre intègrent souvent des systèmes de refroidissement rapides ou des ventilateurs pour accélérer cette phase.
- Contrôle de la qualité et inspection finale : Enfin, après la cuisson et le refroidissement, les pièces passent par un processus d’inspection de qualité. Ce contrôle garantit que le revêtement est conforme aux spécifications, sans défauts comme des éclats, des bavures, ou des variations d’épaisseur. Les systèmes automatisés peuvent utiliser des capteurs de vision artificielle pour détecter automatiquement toute imperfection sur la surface des pièces.
Avantages d’une chaîne automatique de peinture en poudre :
- Efficacité et Productivité : L’automatisation permet une production continue et rapide, réduisant les délais de fabrication tout en maintenant une qualité constante. La capacité à automatiser l’application de la poudre, le durcissement et la gestion de la chaîne logistique assure une efficacité accrue.
- Réduction des Coûts : L’automatisation optimise l’utilisation des matériaux, minimise le gaspillage de peinture et réduit les coûts liés à la main-d’œuvre. De plus, la possibilité de récupérer la poudre excédentaire et de la recycler diminue considérablement les coûts de production.
- Amélioration de la Qualité : Les systèmes de peinture en poudre automatisés garantissent une application uniforme de la peinture, ce qui améliore la finition des produits et réduit le nombre de pièces défectueuses. La précision des réglages et des contrôles réduit le risque d’erreurs humaines et permet de maintenir un standard élevé de qualité.
- Durabilité et Respect de l’Environnement : La peinture en poudre est une alternative plus écologique aux peintures à base de solvants, car elle ne dégage pas de COV (composés organiques volatils). L’automatisation permet également une gestion efficace des déchets de peinture, contribuant à une meilleure performance environnementale.
- Flexibilité de Production : Les chaînes de peinture en poudre automatiques peuvent être facilement adaptées pour traiter différentes tailles de pièces et pour appliquer une variété de couleurs et de finitions. Cette flexibilité est essentielle pour les industries qui doivent répondre à des besoins variés, comme l’automobile, l’électronique ou l’ameublement.
- Maintenance et Surveillance : Les installations automatisées sont généralement équipées de systèmes de maintenance prédictive, permettant de surveiller l’état des équipements en temps réel et de prévenir les pannes avant qu’elles n’affectent la production. Cela augmente la disponibilité des équipements et minimise les interruptions.
Applications typiques de la chaîne de peinture en poudre :
- Industrie automobile : Pour le revêtement de pièces de véhicules, telles que les jantes, les châssis, ou les composants extérieurs.
- Électroménagers : Pour les appareils comme les réfrigérateurs, les machines à laver, et les autres équipements de cuisine ou de blanchisserie.
- Mobilier métallique : Pour des meubles comme des chaises, des tables et des étagères, souvent utilisés dans des environnements intérieurs et extérieurs.
- Secteur de la construction : Pour les revêtements de fenêtres, de portes et d’autres structures métalliques.
- Matériel industriel et équipements : Pour les pièces métalliques utilisées dans des machines, des outils et d’autres équipements industriels.
Conclusion
La chaîne automatique de peinture en poudre est un système clé dans l’industrie moderne, offrant un revêtement durable et uniforme tout en améliorant l’efficacité, la productivité et la qualité. Grâce à son automatisation, elle réduit les coûts de production, augmente la flexibilité et contribue à la durabilité des produits, ce qui en fait un atout stratégique pour les fabricants de tous secteurs confondus.
La chaîne automatique de peinture en poudre est conçue pour maximiser l’efficacité et réduire les erreurs humaines tout en offrant des finitions de haute qualité. En éliminant les étapes manuelles et en automatisant l’application, le durcissement et le refroidissement, cette solution permet une production continue et rapide. Elle améliore également la constance du produit fini, garantissant une finition uniforme à travers toutes les pièces traitées. Cette capacité à produire rapidement et de manière fiable permet aux fabricants de répondre à la demande du marché avec flexibilité, tout en réduisant les coûts associés à des erreurs humaines ou à des écarts de qualité.
Les systèmes automatisés sont souvent équipés de technologies avancées, telles que des capteurs de température et des caméras pour surveiller en temps réel chaque étape du processus. Ces technologies permettent non seulement un contrôle de la qualité, mais aussi l’ajustement instantané des paramètres de la ligne de production pour répondre aux besoins spécifiques de chaque lot. Par exemple, les systèmes peuvent automatiquement ajuster la vitesse de la ligne de production en fonction de la taille des pièces ou de la couleur de la peinture utilisée, ce qui permet une flexibilité dans la gestion des commandes personnalisées ou des petites séries.
Un autre aspect clé de la chaîne de peinture en poudre est l’intégration des technologies de recyclage. Les poudres excédentaires sont récupérées et filtrées avant d’être réutilisées, réduisant ainsi le gaspillage de matériaux. Cette capacité à recycler la poudre non utilisée contribue à réduire les coûts de production tout en minimisant l’impact environnemental. De plus, avec l’utilisation de poudres sans solvant, le processus de peinture en poudre est bien plus écologique que les méthodes traditionnelles de peinture liquide, car il génère moins d’émissions de COV et est exempt de produits chimiques toxiques.
L’un des grands avantages de cette chaîne automatique réside dans la maintenance préventive et la surveillance en temps réel des équipements. Grâce à des systèmes intelligents, les performances des machines peuvent être surveillées continuellement, permettant aux gestionnaires de production de détecter rapidement tout dysfonctionnement avant qu’il n’affecte la production. Cela permet d’éviter des arrêts imprévus et de prolonger la durée de vie des équipements.
Avec l’évolution continue de la technologie, les installations de peinture en poudre deviennent de plus en plus intelligentes. L’introduction de l’intelligence artificielle et du machine learning permet d’optimiser encore davantage les paramètres de la ligne en fonction des données collectées pendant la production. Ces systèmes peuvent apprendre des tendances passées pour prédire les besoins futurs, ajustant ainsi automatiquement les processus pour maximiser l’efficacité et la qualité tout en réduisant l’utilisation des ressources.
La chaîne automatique de peinture en poudre est également un outil essentiel pour répondre aux demandes croissantes en matière de personnalisation. Grâce à l’automatisation, il est possible de réaliser des séries plus petites avec des finitions spécifiques, répondant ainsi aux besoins des clients qui recherchent des produits distincts, que ce soit en termes de couleur, de texture ou d’effets visuels. Cela permet une plus grande diversité de produits tout en maintenant une production rapide et rentable.
En somme, la chaîne de peinture en poudre automatique transforme le processus de finition industrielle en une opération plus rapide, plus propre et plus fiable. Elle permet aux entreprises de répondre efficacement aux défis de production modernes, tout en offrant des produits de haute qualité à un coût réduit. Avec la constante amélioration des technologies, ces installations continueront de jouer un rôle clé dans l’avenir de l’industrie de finition, en optimisant la performance et en minimisant l’impact environnemental.
La chaîne automatique de peinture en poudre joue un rôle crucial dans l’industrie moderne en raison de sa capacité à garantir non seulement la qualité mais aussi la flexibilité et l’efficacité. L’un des développements les plus intéressants dans cette technologie est l’intégration des systèmes de gestion des flux de travail, qui permettent une coordination fluide entre chaque phase du processus. Grâce à une gestion centralisée, chaque étape, depuis l’application de la poudre jusqu’au durcissement et à la vérification de la qualité, est parfaitement synchronisée, garantissant une production continue et optimisée.
L’un des autres grands avantages de la chaîne de peinture en poudre est sa capacité à s’adapter aux variations de production. Dans de nombreux secteurs, comme l’automobile, l’électronique ou les équipements industriels, la demande peut fluctuer, et des pièces spécifiques doivent être peintes en fonction de configurations particulières. L’automatisation permet d’ajuster facilement la ligne pour traiter des produits de tailles ou formes variées, tout en maintenant une qualité uniforme. Les lignes automatisées modernes sont conçues pour être modulables, ce qui permet une adaptation rapide aux besoins spécifiques de chaque client ou de chaque produit.
Les systèmes de peinture en poudre automatisés intègrent également des solutions avancées pour le contrôle de la consommation énergétique. Les technologies modernes permettent de surveiller et de réduire la consommation d’énergie tout au long du processus de peinture, de la pulvérisation à la cuisson. Par exemple, certains systèmes ajustent automatiquement les paramètres de température des fours en fonction de la charge et du type de pièces, évitant ainsi une surconsommation d’énergie. De plus, la possibilité de récupérer la chaleur des fours pour des applications internes ou externes contribue à rendre l’ensemble du système plus durable.
Un autre aspect intéressant est l’évolution vers des systèmes de peinture en poudre plus spécialisés, conçus pour des applications spécifiques nécessitant des propriétés particulières du revêtement. Cela comprend des poudres qui offrent une résistance accrue aux conditions environnementales extrêmes, telles que la chaleur intense, l’humidité, les produits chimiques agressifs ou même l’abrasion. Ces systèmes sont largement utilisés dans les industries aérospatiale, automobile et électronique, où la durabilité et la longévité des revêtements sont primordiales. Ces innovations ouvrent la voie à une personnalisation accrue des produits finis et à des applications dans des secteurs où la performance du revêtement est essentielle.
L’un des défis constants dans l’optimisation de ces systèmes automatisés est l’adaptation aux matériaux variés. Certains matériaux, comme l’acier inoxydable, l’aluminium ou les plastiques, peuvent poser des défis particuliers en termes de préparation de surface et de fixation de la peinture. Cependant, les systèmes modernes sont capables de s’adapter à différents types de matériaux, grâce à des réglages dynamiques de la température, de la vitesse de la ligne et des paramètres de pulvérisation. Cela permet de traiter une large gamme de produits tout en maintenant un haut niveau de performance et de qualité.
Les systèmes de contrôle et d’automatisation des chaînes de peinture en poudre continuent d’évoluer pour inclure des outils de maintenance prédictive. Ces outils reposent sur l’analyse des données en temps réel recueillies par les capteurs et les logiciels de surveillance pour prévoir quand une machine ou un composant risque de défaillir. Cela permet de planifier les réparations ou le remplacement de pièces avant qu’une panne ne survienne, minimisant ainsi les arrêts non planifiés et améliorant la disponibilité de la ligne de production.
La traçabilité et la gestion des données sont également des éléments clés dans ces systèmes modernes. Chaque étape du processus de peinture est enregistrée et suivie numériquement, ce qui permet de disposer de rapports détaillés pour chaque produit fini. Cela offre une visibilité totale sur le processus de production, facilitant l’audit et la certification des produits, tout en permettant une gestion efficace de la qualité.
La chaîne automatique de peinture en poudre continue d’évoluer vers des solutions de plus en plus durables et économes en ressources. L’amélioration de la récupération de la poudre excédentaire, la réduction des émissions de gaz nocifs, l’utilisation de poudres écologiques, et l’optimisation des consommations d’énergie et d’eau sont des axes de développement essentiels. Les entreprises cherchent à rendre leurs lignes de production plus durables tout en maintenant une haute productivité, dans un contexte où les exigences environnementales deviennent de plus en plus strictes.
Dans l’avenir, les chaînes de peinture en poudre devraient également intégrer davantage de solutions numériques et d’intelligence artificielle, ce qui permettra de personnaliser encore plus les processus en fonction des besoins spécifiques des clients, et d’automatiser davantage l’ensemble de la production. Ces technologies permettront non seulement d’améliorer l’efficacité et la flexibilité, mais aussi de transformer les chaînes de production en systèmes entièrement intelligents et autonomes, capables de réagir en temps réel aux évolutions des demandes du marché.
En somme, la chaîne automatique de peinture en poudre n’est pas seulement une solution de finition efficace, mais aussi un élément central de la transition vers des processus industriels plus intelligents, durables et rentables. Grâce aux avancées technologiques continues, ces systèmes joueront un rôle clé dans l’optimisation des performances des entreprises tout en répondant à des défis environnementaux et de production toujours plus complexes.
L’avenir des chaînes automatiques de peinture en poudre est prometteur, avec l’intégration croissante de technologies de pointe et l’évolution vers des solutions encore plus flexibles et performantes. La prochaine génération de ces installations pourrait intégrer des innovations liées à la robotique avancée, la vision par ordinateur, et la connectivité de l’Internet des objets (IoT). Ces avancées permettront d’optimiser encore davantage les processus, d’assurer un contrôle de qualité en temps réel et de maximiser la personnalisation des revêtements. Voici quelques directions potentielles pour l’avenir des chaînes de peinture en poudre.
Les robots de peinture deviennent de plus en plus sophistiqués, avec des capacités accrues pour manipuler des pièces de tailles variées, appliquer des couches plus fines et traiter des surfaces complexes. Ils peuvent être programmés pour s’adapter à différents types de géométries et à des spécifications détaillées, offrant ainsi une flexibilité jamais vue auparavant dans les lignes de production. En intégrant des algorithmes d’intelligence artificielle, ces robots peuvent également améliorer la précision et l’efficacité de l’application de la peinture en apprenant des données de production antérieures et en ajustant les paramètres en temps réel.
En parallèle, l’utilisation de la vision par ordinateur pour le contrôle de la qualité deviendra encore plus courante. Des caméras et des capteurs optiques avancés peuvent déjà détecter des défauts microscopiques dans les revêtements, comme des irrégularités d’épaisseur ou des bulles d’air, avant que les pièces ne quittent la ligne de production. Dans l’avenir, ces systèmes seront capables d’effectuer des inspections en continu tout au long du processus de peinture, éliminant ainsi les erreurs humaines et réduisant le besoin de contrôles manuels. De plus, la vision par ordinateur pourrait aussi être utilisée pour surveiller l’application de la poudre en temps réel, ajustant instantanément les conditions pour garantir une couverture parfaite à chaque fois.
L’intégration de l’Internet des objets (IoT) et des systèmes cloud permettra une gestion de production à distance et une analyse de données en temps réel. Cela offrira une transparence totale sur l’ensemble du processus de peinture en poudre, de l’application initiale au durcissement final. Les utilisateurs pourront surveiller les performances des lignes de production depuis n’importe où dans le monde, ce qui permettra une réaction plus rapide aux problèmes et une optimisation continue des processus. Les données collectées tout au long du processus permettront également de créer des rapports détaillés sur la productivité, la qualité et la consommation de ressources, offrant ainsi une tracabilité complète.
La maintenance prédictive deviendra également plus courante avec l’intégration de l’IoT. Grâce aux capteurs embarqués sur les équipements, il sera possible de détecter des anomalies dans le fonctionnement des machines avant qu’elles ne provoquent des pannes. Ces capteurs mesureront des variables telles que la température, les vibrations, et l’usure des composants, et des algorithmes prédictifs détermineront quand une intervention est nécessaire. Cela permettra de planifier les réparations de manière proactive, réduisant ainsi les temps d’arrêt et les coûts de maintenance.
Les matériaux de peinture en poudre eux-mêmes continueront à évoluer. Des poudres encore plus résistantes aux conditions extrêmes, à base de matériaux écologiques et durables, seront développées pour répondre aux exigences des industries les plus exigeantes, comme l’automobile, l’aérospatiale, et la construction. Les avancées dans les formulations de peinture en poudre permettront de créer des revêtements avec des propriétés spécifiques, telles que des finitions anti-corrosion, anti-rayures, ou ultra résistantes à la chaleur, tout en maintenant des standards environnementaux élevés.
L’accent mis sur la durabilité et la réduction des déchets sera également renforcé. L’optimisation des systèmes de récupération de poudre permettra de réutiliser une proportion encore plus élevée de la peinture excédentaire, réduisant ainsi la quantité de matière première nécessaire et minimisant les déchets. De plus, l’amélioration des systèmes de filtration et de recyclage dans les installations de peinture contribuera à rendre le processus encore plus respectueux de l’environnement, en réduisant la consommation d’eau et en éliminant les émissions nocives associées aux anciennes méthodes de peinture.
L’évolution des systèmes d’automatisation dans les chaînes de peinture en poudre tend également vers une plus grande personnalisation des produits. Grâce à des lignes de production flexibles, il sera possible de produire des petites séries ou des produits personnalisés sans compromis sur la qualité. Les ajustements automatiques de la ligne en fonction des spécifications de chaque produit permettront aux entreprises de répondre aux demandes des clients tout en maintenant un haut niveau de productivité.
Enfin, les chaînes de peinture en poudre devraient également devenir plus intelligentes et autonomes. L’intelligence artificielle et les algorithmes d’apprentissage automatique offriront une gestion dynamique de la production, en ajustant automatiquement les paramètres de la ligne de production pour maximiser la productivité tout en garantissant une qualité constante. Ces systèmes intelligents pourront anticiper les problèmes potentiels, optimiser les performances des équipements, et ajuster les processus en fonction des conditions réelles de la production.
En résumé, l’avenir des chaînes automatiques de peinture en poudre repose sur une combinaison d’innovations technologiques qui permettront de rendre les processus de production plus flexibles, efficaces et durables. De l’intelligence artificielle à la robotique avancée, en passant par la gestion des données et l’optimisation des matériaux, les lignes de peinture en poudre de demain seront plus intelligentes, plus respectueuses de l’environnement et capables de répondre à des exigences de production toujours plus complexes.
Ligne de peinture en poudre automatique
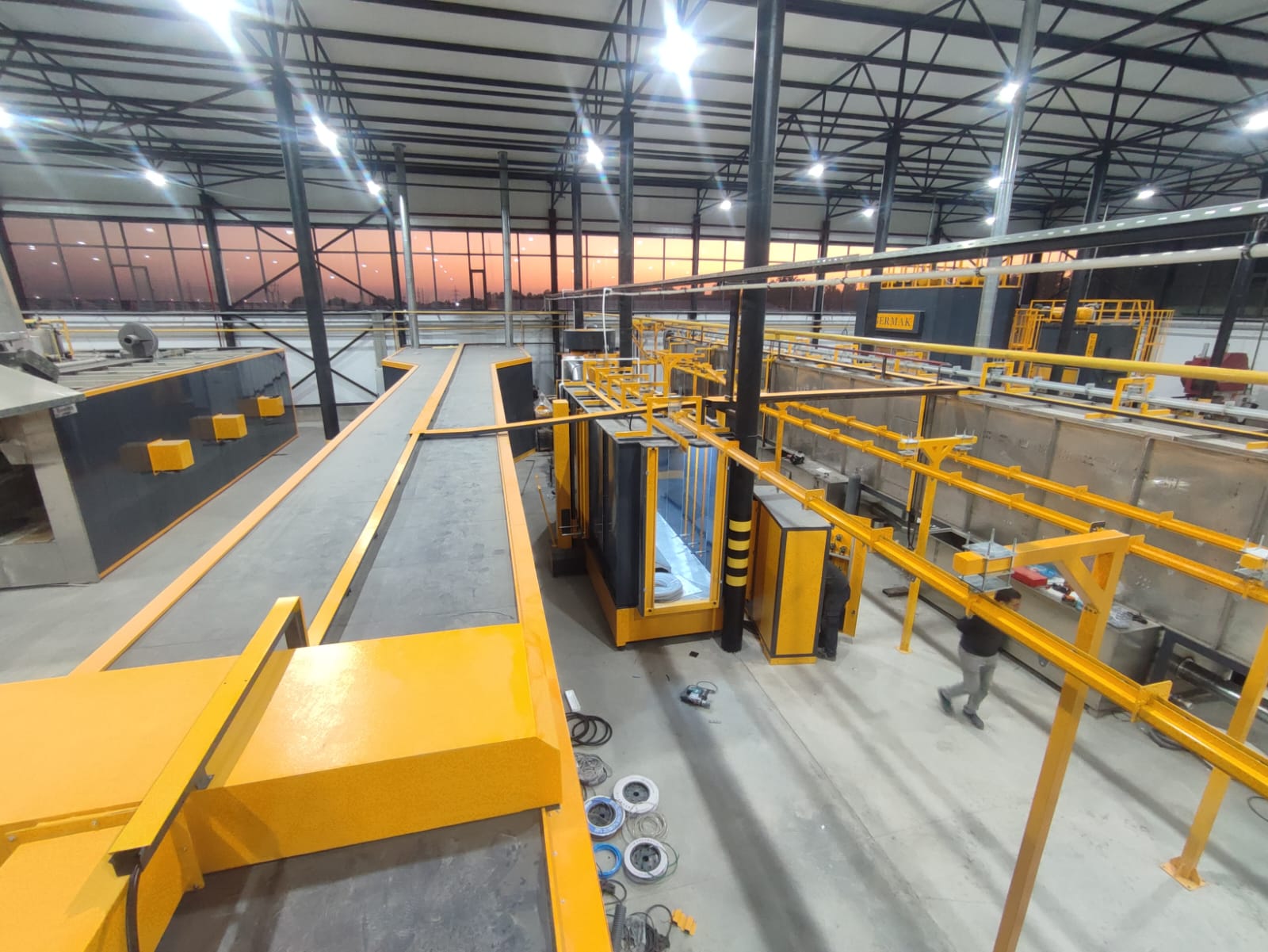
Une ligne de peinture en poudre automatique est un système hautement technologique utilisé pour appliquer un revêtement en poudre sur des pièces métalliques ou autres matériaux. Ce procédé est largement employé dans les industries pour fournir des finitions durables et uniformes sur une variété de produits, tout en optimisant la productivité, la qualité et l’efficacité des processus de production.
Le système fonctionne grâce à une combinaison d’automatisation et de contrôle électronique pour effectuer les différentes étapes du processus de peinture, depuis la préparation des pièces jusqu’à la cuisson finale du revêtement. Ce type de ligne est conçu pour assurer une production continue, réduire les erreurs humaines, et minimiser les coûts liés à la main-d’œuvre et aux matériaux.
Le processus d’une ligne de peinture en poudre automatique se déroule généralement en plusieurs étapes clés :
- Préparation des pièces : Les pièces à peindre sont d’abord préparées afin de garantir une bonne adhérence de la peinture. Cela peut inclure des étapes comme le nettoyage (dégraissage ou lavage), le sablage ou l’utilisation de traitements de surface comme le passivation ou le plasma, qui éliminent les contaminants et préparent les surfaces.
- Application de la poudre : Une fois les pièces nettoyées et préparées, elles passent dans la cabine de peinture, où la poudre est appliquée par des pistolets électrostatiques. Ces pistolets chargent électriquement les particules de peinture, qui sont alors attirées par les surfaces métalliques des pièces, assurant une couverture uniforme. Le contrôle de la quantité et de la répartition de la poudre est souvent automatisé grâce à des systèmes de dosage et de surveillance.
- Cuisson du revêtement : Après l’application de la poudre, les pièces passent dans un four de cuisson, où la poudre est chauffée à une température spécifique, généralement entre 160 et 200°C, pour être durcie. La cuisson fait fondre la poudre et forme une finition lisse et robuste. La durée et la température de cuisson sont ajustées en fonction du type de poudre et des caractéristiques des pièces à revêtir.
- Refroidissement : Après la cuisson, les pièces doivent être refroidies pour solidifier le revêtement. Ce processus est également automatisé, et des systèmes de refroidissement à air forcé ou des tunnels de refroidissement sont souvent utilisés pour accélérer cette étape.
- Contrôle de la qualité : Une fois les pièces refroidies, elles sont inspectées pour vérifier la qualité du revêtement. Cela peut être effectué à l’aide de capteurs visuels, des systèmes de caméra haute définition ou des équipements de test automatisés qui analysent l’épaisseur du revêtement, la finition et la conformité aux spécifications. Certaines lignes sont également équipées de systèmes de contrôle en ligne qui ajustent automatiquement les paramètres du système pour garantir une finition parfaite.
- Emballage ou stockage : Une fois que les pièces ont réussi le contrôle qualité, elles sont prêtes à être emballées ou envoyées vers d’autres étapes de production. Cette partie peut être également automatisée, avec des robots ou des convoyeurs pour déplacer les pièces finies.
Avantages des lignes de peinture en poudre automatiques :
- Productivité élevée : L’automatisation permet un fonctionnement continu sans intervention humaine, ce qui augmente considérablement la vitesse de production tout en maintenant une qualité constante.
- Réduction des déchets : Les systèmes de récupération de poudre permettent de récupérer et de réutiliser la poudre excédentaire, réduisant ainsi le gaspillage de matériau et les coûts associés à l’achat de nouvelles poudres.
- Qualité uniforme et précise : L’application automatisée de la peinture garantit un revêtement uniforme et précis sur chaque pièce, évitant les défauts courants comme les coulures, les irrégularités d’épaisseur et les variations de couleur.
- Réduction des coûts de production : En plus de réduire le besoin de main-d’œuvre, les lignes de peinture en poudre automatiques offrent un meilleur rendement énergétique et une gestion optimisée des matériaux, ce qui permet de réduire les coûts globaux de production.
- Amélioration de la sécurité : L’automatisation permet de limiter l’exposition aux produits chimiques et à la chaleur pour les opérateurs, réduisant ainsi les risques pour la santé et la sécurité des travailleurs.
- Flexibilité et adaptabilité : Les lignes automatiques peuvent être adaptées pour peindre différents types de pièces, de formes et de tailles variées, et sont capables de traiter un large éventail de couleurs et de finitions, allant des couleurs standards aux effets spéciaux (texture, métallisé, etc.).
- Impact environnemental réduit : Les lignes de peinture en poudre sont plus écologiques que les systèmes de peinture liquide, car elles ne génèrent pas de solvants ni de COV (composés organiques volatils), et la poudre excédentaire peut être récupérée et recyclée. De plus, le procédé ne génère que peu de déchets.
Applications courantes de la ligne de peinture en poudre automatique :
- Industrie automobile : Peinture des pièces automobiles telles que les jantes, les châssis, les boîtiers, et les composants intérieurs et extérieurs.
- Électroménagers : Peinture des composants métalliques des réfrigérateurs, machines à laver, cuisinières, etc.
- Matériel industriel : Application de peinture sur des équipements industriels tels que les machines, les outils et les structures métalliques.
- Mobilier métallique : Peinture de meubles en métal pour des environnements intérieurs et extérieurs.
- Construction : Revêtement de profilés métalliques, fenêtres, portes et autres éléments en métal utilisés dans la construction.
En résumé, une ligne de peinture en poudre automatique est une solution de finition industrielle extrêmement efficace et flexible qui permet de produire des pièces revêtues de manière uniforme, rapide et économique, tout en offrant des avantages considérables en termes de réduction des coûts, d’efficacité énergétique et de respect de l’environnement.
Une ligne de peinture en poudre automatique permet non seulement de répondre à des volumes de production élevés, mais aussi de garantir une qualité constante, ce qui est essentiel dans des secteurs exigeants. L’automatisation permet également de réduire considérablement les erreurs humaines, assurant ainsi une finition uniforme et un taux de rejet minimal. Les systèmes de contrôle avancés, tels que les capteurs et les systèmes de vision, permettent de détecter instantanément les défauts sur les pièces, comme des irrégularités dans le revêtement, permettant des ajustements en temps réel sans arrêter la ligne de production.
Les systèmes d’application de peinture en poudre sont équipés de technologies de dosage précises, ce qui permet de réduire les pertes de matière et d’assurer une utilisation optimale des poudres. L’utilisation de robots de peinture et de pistolets électrostatiques permet non seulement de maximiser l’efficacité de l’application, mais aussi de réduire les coûts liés aux matériaux. La poudre excédentaire est souvent récupérée et recyclée pour être réutilisée, ce qui est un atout majeur pour réduire les coûts de production et minimiser l’impact environnemental.
Les lignes de peinture en poudre automatiques peuvent également être équipées de systèmes de gestion de la production basés sur des logiciels intelligents qui suivent et analysent les performances en temps réel. Ces systèmes offrent une visibilité complète sur l’état de chaque machine, la quantité de poudre utilisée, les conditions de cuisson et le temps de production. En utilisant des données en temps réel, ces systèmes permettent une gestion proactive et une prise de décision éclairée pour optimiser la productivité et la qualité tout en minimisant les coûts opérationnels.
Les progrès dans l’intégration de l’intelligence artificielle (IA) et des systèmes de contrôle avancés permettront à l’avenir d’améliorer encore la flexibilité des lignes de peinture en poudre. Par exemple, l’intelligence artificielle pourrait permettre de prédire les ajustements nécessaires dans les paramètres de peinture, tels que la température de cuisson, la vitesse de la ligne ou le dosage de la poudre, en fonction des conditions de production précédentes et des spécifications des pièces. Cela permettrait d’adapter en temps réel le processus de peinture en fonction des variables de production pour garantir des résultats optimaux à chaque cycle.
Les lignes de peinture en poudre sont également de plus en plus conçues pour être modulables et flexibles, permettant aux fabricants de s’adapter à des besoins de production variés, des séries longues aux petites séries personnalisées. Cette capacité à s’adapter à des demandes de production spécifiques est rendue possible grâce à des programmes de production automatisés qui ajustent la vitesse de la ligne, l’application de la poudre et les températures de cuisson pour chaque type de pièce.
Dans le cadre de l’évolution vers des systèmes de production durables, les lignes de peinture en poudre sont également de plus en plus intégrées à des solutions écologiques, en utilisant des poudres sans solvant et des matériaux qui réduisent les émissions polluantes. Les systèmes modernes réduisent l’usage de substances chimiques dangereuses tout en maximisant l’efficacité énergétique des équipements. Par ailleurs, certaines installations mettent en œuvre des systèmes de récupération d’énergie pour réutiliser la chaleur produite par les fours de cuisson, ce qui permet de réduire la consommation d’énergie globale.
Les lignes de peinture en poudre automatiques sont également plus efficaces en matière de gestion des déchets. L’application de la peinture en poudre génère moins de déchets qu’avec des peintures liquides, et la possibilité de récupérer et de réutiliser la poudre excédentaire permet d’optimiser encore davantage le rendement des matériaux. En réduisant la quantité de peinture gaspillée et en réutilisant les excédents, les entreprises peuvent réaliser des économies importantes tout en étant plus responsables vis-à-vis de l’environnement.
Les applications industrielles des lignes de peinture en poudre vont au-delà de la simple peinture de composants métalliques. Elles s’étendent également aux secteurs de la fourniture d’accessoires pour la construction, l’équipement de télécommunications, et même l’industrie aérospatiale, où la précision et la résistance du revêtement sont cruciales. L’utilisation de peintures spécialisées, telles que des finitions résistantes aux rayures, aux produits chimiques, ou aux conditions climatiques extrêmes, permet d’adapter le produit fini à des besoins spécifiques et à des environnements de travail difficiles.
En conclusion, une ligne de peinture en poudre automatique représente une révolution dans le processus de finition industrielle. Elle combine efficacité, flexibilité, rentabilité et respect de l’environnement, répondant ainsi aux exigences croissantes des industries modernes. Grâce à l’automatisation, aux technologies avancées et à l’optimisation des ressources, ces lignes permettent non seulement de produire à grande échelle, mais aussi d’offrir une personnalisation des produits tout en maintenant un haut niveau de qualité. À mesure que la technologie continue d’évoluer, ces systèmes deviendront encore plus sophistiqués, intelligents et respectueux de l’environnement, consolidant ainsi leur rôle dans les processus industriels de demain.
Les innovations continues dans les lignes de peinture en poudre automatiques promettent de transformer encore plus profondément l’industrie de la finition. À mesure que l’intelligence artificielle (IA) et la robotique deviennent plus avancées, ces systèmes deviendront plus autonomes et capables de réagir instantanément aux changements de conditions de production, améliorant ainsi la réactivité et la précision. Les algorithmes d’IA peuvent analyser une multitude de variables en temps réel, comme la température, l’humidité, la vitesse de la ligne et la qualité de la poudre, pour ajuster automatiquement les paramètres afin d’optimiser chaque cycle de peinture.
L’intégration de systèmes de maintenance prédictive sera également une évolution majeure. Ces systèmes, équipés de capteurs IoT, seront capables de surveiller en continu l’état de santé des équipements, anticipant les défaillances potentielles avant qu’elles ne surviennent. Grâce à cette approche proactive, les lignes de peinture en poudre pourront éviter des arrêts imprévus et optimiser la durée de vie des équipements, ce qui réduira les coûts de maintenance et améliorera la disponibilité des machines.
Un autre domaine qui connaît des progrès significatifs est la gestion de l’énergie et des ressources naturelles. Les lignes de peinture en poudre du futur seront équipées de technologies encore plus efficaces pour minimiser la consommation d’énergie et optimiser l’utilisation de l’eau et des matériaux. Les systèmes de récupération thermique dans les fours, par exemple, permettront de réutiliser l’énergie thermique pour préchauffer l’air ou l’eau utilisée dans le processus, ce qui contribuera à réduire la consommation énergétique globale.
Les avancées dans la technologie des poudres ouvriront également de nouvelles perspectives. Des poudres spéciales seront développées pour offrir des propriétés encore plus performantes, telles que des revêtements ultra-durables, des finishes résistants aux rayures, ou des revêtements avec des effets spéciaux comme des effets texturés ou métalliques. De plus, les poudres écologiques continueront à gagner en popularité, avec des formulations sans solvants et fabriquées à partir de matériaux recyclés ou d’ingrédients naturels, ce qui contribuera à un avenir plus durable pour les industries utilisant ces systèmes.
Un autre aspect important de cette évolution sera la connectivité. Les lignes de peinture en poudre seront de plus en plus intégrées dans des réseaux industriels intelligents, où toutes les machines, équipements et processus seront connectés pour faciliter la gestion de la production. Grâce à des plateformes cloud et des systèmes de gestion de la production basés sur les données, les responsables de la production pourront suivre en temps réel les performances de chaque ligne, optimiser les cycles de production et prendre des décisions éclairées grâce à l’analyse des données collectées.
L’automatisation des ajustements pendant le processus de peinture deviendra également une norme avec l’introduction de systèmes adaptatifs. Par exemple, en fonction des caractéristiques spécifiques des pièces à peindre (comme la taille, la forme, le matériau ou la finition souhaitée), la ligne de peinture pourra ajuster automatiquement des paramètres tels que la pression des pistolets, le débit de poudre, la température du four, ou la durée de cuisson pour garantir que chaque pièce soit revêtue de manière optimale.
L’intégration de solutions mobiles pour la gestion des lignes de peinture en poudre offrira également plus de flexibilité. Les responsables de la production et les techniciens pourront accéder aux données et contrôler les paramètres de la ligne de peinture depuis des appareils mobiles, ce qui facilitera la gestion des lignes de production à distance et permettra de résoudre les problèmes plus rapidement, même en dehors des zones de production.
Enfin, l’émergence de concepts de production flexible et agile va transformer la manière dont les lignes de peinture en poudre sont configurées. Les lignes de production pourraient être conçues pour s’adapter plus rapidement aux demandes de marché fluctuantes, permettant des changements rapides de configurations pour passer d’une production en série à une production de petites séries ou de prototypes personnalisés. Cela offrira une plus grande souplesse pour répondre aux besoins des clients, qui exigent de plus en plus des produits personnalisés et adaptés à des spécifications précises, tout en maintenant une efficacité de production maximale.
L’évolution de la ligne de peinture en poudre automatique ne se limite pas uniquement à l’optimisation du processus. Elle va également de pair avec des nouvelles approches en termes de design de produit, où les tendances du marché de plus en plus vertes et éco-responsables joueront un rôle majeur dans la conception et l’exploitation de ces installations. La demande de revêtements plus écologiques, associés à des pratiques de fabrication durable, encouragera l’industrie à adopter des technologies qui réduisent l’empreinte écologique tout en maintenant des performances élevées.
En conclusion, l’avenir des lignes de peinture en poudre automatiques sera marqué par une plus grande intelligence, une flexibilité accrue, et une durabilité renforcée. La combinaison de technologies avancées, telles que la robotique, l’IA, les capteurs IoT, et la connectivité, permettra de créer des lignes de production non seulement plus efficaces et rentables, mais aussi plus adaptées aux exigences de personnalisation et d’impact environnemental des marchés modernes. Ces progrès ouvriront la voie à des solutions de peinture toujours plus innovantes et respectueuses de l’environnement, répondant aux besoins d’une production industrielle de demain plus intelligente et plus durable.
En poursuivant cette dynamique d’innovation, les lignes de peinture en poudre automatiques de demain se caractériseront par des avancées dans les systèmes de contrôle avancés, permettant de maximiser la productivité, la qualité et l’efficacité tout en répondant aux besoins croissants de personnalisation et de durabilité. Une des grandes tendances futures dans l’industrie sera l’intégration de la fabrication additive dans les processus de peinture. Cela pourrait révolutionner la manière dont les pièces sont traitées avant d’être peintes, permettant des designs plus complexes et des possibilités de finition plus précises.
Les lignes de peinture en poudre intelligentes seront capables de collecter et d’analyser une grande quantité de données, non seulement pour optimiser le processus en temps réel, mais aussi pour effectuer des prévisions basées sur des modèles de données historiques. Par exemple, l’analyse des performances passées pourrait aider à prédire les ajustements nécessaires en cas de changements dans les conditions de production ou dans les spécifications des produits. Cela permettrait de réduire les temps d’arrêt et de garantir que les lignes fonctionnent toujours de manière optimale sans intervention humaine.
Une autre évolution sera la généralisation de la personnalisation dans les revêtements. Les clients demandent de plus en plus des produits spécifiques, avec des couleurs, des textures ou des propriétés de finition uniques. Les lignes de peinture en poudre seront alors capables d’adapter les réglages pour chaque produit sans perdre en efficacité. Grâce à l’automatisation et à des technologies telles que les robots de peinture multi-axes, ces lignes pourront gérer des séries de productions diverses, allant de grandes quantités à des petites séries, tout en maintenant un haut niveau de qualité.
Le processus de peinture en poudre deviendra également plus flexible grâce aux nouvelles solutions logicielles. Par exemple, des plateformes de gestion de la production basées sur le cloud permettront de suivre la performance de plusieurs lignes de peinture en temps réel, partout dans le monde. Ces plateformes offriront aux gestionnaires un accès à des analyses avancées, permettant de surveiller les performances des lignes, de planifier les maintenances préventives et d’améliorer les processus en fonction des données collectées. De plus, la possibilité de se connecter à un réseau industriel intelligent permettra de lier les lignes de peinture en poudre à d’autres machines et systèmes de l’usine, créant ainsi une chaîne de production parfaitement intégrée.
Les systèmes de vision et les capteurs intelligents joueront un rôle encore plus crucial dans la qualité du revêtement. Ces technologies permettront une détection en temps réel des défauts sur les pièces avant et après l’application de la peinture. Par exemple, des caméras haute résolution et des capteurs de mesure d’épaisseur pourront vérifier l’uniformité du revêtement, détecter les impuretés ou les irrégularités et ajuster automatiquement les paramètres de la ligne pour corriger les défauts sans interrompre la production. Cela permettra non seulement d’améliorer la qualité du produit final, mais aussi de réduire le nombre de pièces défectueuses, contribuant ainsi à un meilleur rendement et à moins de gaspillage.
À l’ère de la production durable, la réduction de l’empreinte écologique des lignes de peinture en poudre est primordiale. L’optimisation de la consommation d’énergie dans les processus de cuisson et l’amélioration des technologies de recyclage des poudres sont des objectifs clés pour les fabricants. De plus, de nombreuses entreprises se tournent vers des solutions de peinture sans solvant et des matériaux recyclés pour réduire l’impact environnemental de leurs produits. L’industrie des revêtements en poudre a également fait des progrès significatifs en matière de technologies sans COV (composés organiques volatils), une avancée qui contribue à réduire l’impact environnemental des peintures tout en améliorant la sécurité au travail.
Les technologies de stockage et de gestion des matériaux vont également se perfectionner. Les silos automatisés pour le stockage de la poudre et les systèmes de gestion des stocks en temps réel permettront aux lignes de peinture en poudre de gérer plus efficacement les approvisionnements et d’éviter le gaspillage. Ces solutions permettront également de garantir la disponibilité des bonnes quantités de matériaux, réduisant ainsi les coûts de stockage et assurant une gestion optimale des ressources.
Les solutions robotisées et collaboratives continueront de se développer. Alors que les robots industriels sont déjà courants dans les lignes de peinture en poudre, l’intégration des robots collaboratifs (cobots) dans des tâches plus complexes comme la préparation des pièces avant peinture ou la gestion de certaines étapes du processus apportera plus de flexibilité et d’agilité à la production. Ces cobots, capables de travailler aux côtés des opérateurs humains, optimiseront les processus en réduisant les risques d’erreurs humaines et en améliorant l’efficacité de l’ensemble de la chaîne de production.
Une autre innovation prometteuse réside dans l’usage de matériaux de revêtement intelligents. Ces matériaux pourraient contenir des capteurs intégrés capables de détecter des changements environnementaux, comme des variations de température ou de pression, et d’adapter automatiquement la comportance du revêtement en conséquence. Cette technologie pourrait être utilisée pour des applications très spécifiques dans des industries telles que l’aérospatiale, l’automobile et la construction, où des revêtements capables de réagir à l’environnement extérieur apporteraient une valeur ajoutée significative en termes de durabilité et de performance.
L’intégration de solutions de gestion de la chaîne d’approvisionnement dans les lignes de peinture en poudre apportera une visibilité complète sur l’ensemble du cycle de production. Les entreprises pourront anticiper les besoins en matières premières, ajuster leurs volumes de production en fonction de la demande du marché et même ajuster leurs chaînes d’approvisionnement pour être plus réactives aux fluctuations économiques. Cette intégration permettra de réduire les coûts de production et d’améliorer la gestion des délais de livraison.
À long terme, une reconfiguration des lignes de production pourrait devenir possible grâce à l’usage de technologies modulaires, offrant une adaptabilité accrue aux fluctuations du marché et aux demandes spécifiques des clients. Les lignes de peinture en poudre automatiques pourront être réorganisées en fonction des types de produits à peindre, avec des équipements faciles à adapter pour traiter différents types de matériaux ou de finitions.
En conclusion, les lignes de peinture en poudre automatiques sont appelées à devenir de plus en plus intelligentes, durables, flexibles et connectées. Les avancées dans les technologies de fabrication intelligente, les matériaux écologiques et l’automatisation de la production redéfiniront le paysage de la finition industrielle. Alors que les industries cherchent à réduire leur empreinte écologique tout en maximisant la qualité et la productivité, ces lignes de peinture continueront d’évoluer pour répondre à ces défis et offrir des solutions innovantes, rentables et respectueuses de l’environnement.
Poudrage électrostatique
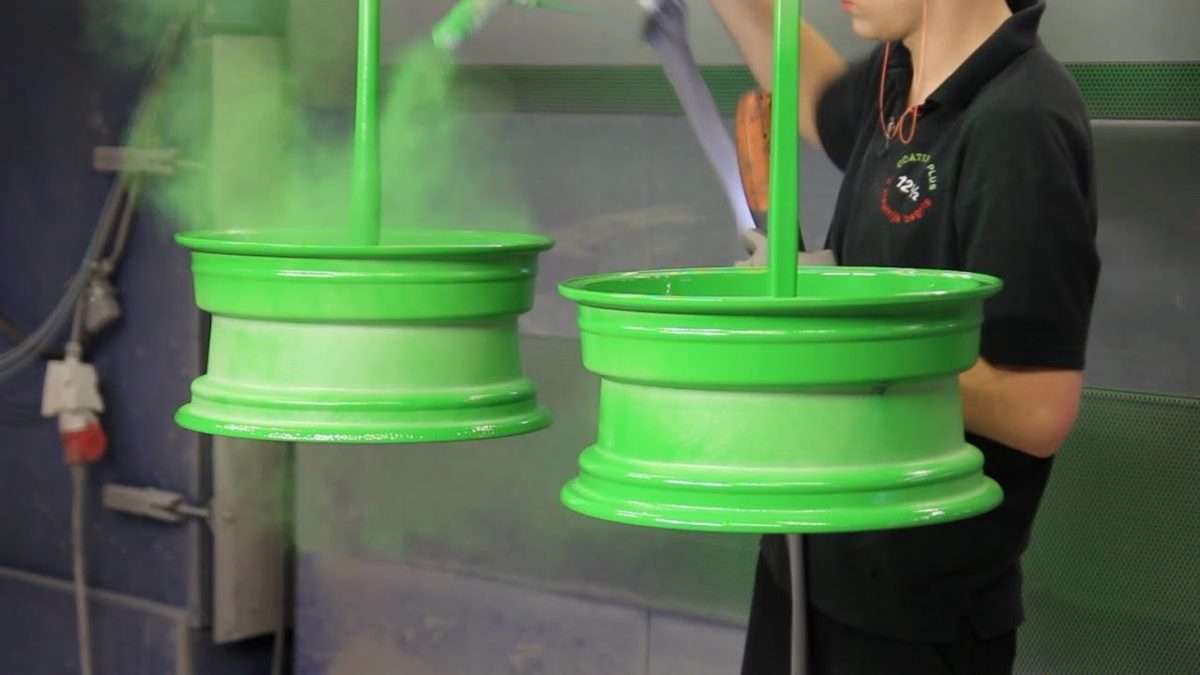
Le poudrage électrostatique est un procédé de revêtement de surface qui utilise des particules de poudre de peinture chargées électrostatiquement pour adhérer à des pièces métalliques ou autres matériaux conducteurs. Ce procédé est largement utilisé dans les industries pour créer des finitions résistantes, durables et esthétiques. Voici une explication détaillée de ce processus, de ses avantages et de ses applications.
Principe du poudrage électrostatique
Le poudrage électrostatique repose sur l’utilisation de la charge électrique pour faire adhérer la poudre de peinture à une pièce. Le processus fonctionne généralement de la manière suivante :
- Chargement de la poudre : La peinture en poudre est chargée électriquement à l’aide d’un pistolet électrostatique. Cela se fait généralement en appliquant une tension sur l’air ou la poudre elle-même, ce qui crée une charge électrique négative (ou positive, selon le système).
- Attraction à la pièce : La pièce à peindre, souvent en métal, est reliée à la terre (chargée positivement ou neutre). La poudre chargée électrostatiquement est attirée vers la surface de la pièce en raison de l’interaction entre charges opposées.
- Application uniforme : Les particules de peinture se déposent de manière uniforme sur la surface de l’objet, y compris les zones difficiles d’accès. Cela garantit une couverture complète et homogène de la surface.
- Cuisson : Après l’application de la poudre, la pièce est passée dans un four à haute température, où la poudre fond et se durcit, créant ainsi une finition solide, durable et résistante aux rayures.
Avantages du poudrage électrostatique
- Efficacité de la couverture : Le procédé électrostatique permet d’appliquer une couche de peinture très uniforme, même sur les zones difficiles d’accès. Les particules chargées électriquement se déposent sur la pièce de manière plus uniforme que dans les procédés de peinture traditionnels, ce qui réduit les zones de “manque de peinture”.
- Réduction du gaspillage : Le poudrage électrostatique minimise les déchets de peinture. La poudre excédentaire qui n’adhère pas à la pièce peut être récupérée et réutilisée, ce qui rend ce procédé très économique et respectueux de l’environnement.
- Durabilité des revêtements : Les revêtements réalisés par poudrage électrostatique sont plus résistants aux impacts, aux rayures et à l’usure que les peintures liquides. De plus, ils sont souvent plus résistants aux conditions climatiques extrêmes, aux produits chimiques et à l’humidité.
- Moins polluant : Contrairement aux peintures liquides traditionnelles qui contiennent des solvants, les peintures en poudre ne libèrent pas de composés organiques volatils (COV), ce qui est plus sûr pour l’environnement et les travailleurs.
- Économie d’énergie et réduction des coûts : L’utilisation de la peinture en poudre ne nécessite pas l’utilisation de solvants et est souvent plus économique à long terme grâce à la possibilité de recycler la poudre excédentaire.
- Finition esthétique et variée : Les peintures en poudre sont disponibles dans une large gamme de couleurs, textures et finitions. Elles peuvent produire des effets de surface lisse, texturé, brillant, satiné ou mat, selon les préférences du client.
Applications du poudrage électrostatique
Le poudrage électrostatique est utilisé dans de nombreuses industries en raison de ses avantages en termes de durabilité, d’esthétique et d’efficacité. Voici quelques-unes de ses principales applications :
- Industrie automobile : Il est couramment utilisé pour la peinture de pièces métalliques telles que les roues, les pare-chocs, les grilles, ainsi que pour les éléments intérieurs et extérieurs des véhicules. Les revêtements créés par poudrage électrostatique sont résistants aux conditions climatiques et aux produits chimiques présents dans les véhicules.
- Appareils électroménagers : Les appareils tels que les réfrigérateurs, les lave-vaisselle et les machines à laver bénéficient de revêtements en poudre électrostatique, qui assurent une finition esthétique et résistante à l’usure.
- Mobilier et décoration : Le poudrage électrostatique est souvent utilisé pour appliquer des finitions métalliques sur le mobilier, y compris des meubles de bureau, des chaises et des tables. Il est également utilisé pour des décorations en métal, en particulier pour l’extérieur, car il offre une excellente résistance aux intempéries.
- Équipements industriels : Des équipements tels que les armoires électriques, les structures métalliques et les machines industrielles bénéficient de la résistance et de la durabilité des revêtements en poudre. Cela protège les pièces contre la corrosion et l’usure.
- Produits en métal et en aluminium : Le poudrage électrostatique est également utilisé pour peindre des produits en métal, tels que les portes, les fenêtres, les grilles et autres éléments architecturaux.
- Applications en extérieur : Étant donné la résistance de la peinture en poudre aux conditions climatiques extrêmes, elle est idéale pour des applications extérieures, comme les clôtures métalliques, les équipements urbains, les supports publicitaires, et les structures métalliques exposées aux intempéries.
Conclusion
Le poudrage électrostatique est une technologie de revêtement avancée qui présente de nombreux avantages par rapport aux méthodes traditionnelles, notamment une meilleure qualité de finition, une réduction des déchets et des coûts, et un impact environnemental moindre. Il est utilisé dans diverses industries allant de l’automobile à la fabrication d’appareils électroménagers, en passant par les équipements industriels et les produits décoratifs. Son adoption croissante est une réponse à la demande de solutions plus écologiques et plus durables dans les procédés industriels.
Le poudrage électrostatique présente des caractéristiques qui le rendent particulièrement attractif pour de nombreuses industries, offrant à la fois des avantages écologiques et économiques. Ce procédé, de plus en plus utilisé dans le monde entier, a connu une évolution rapide grâce à l’intégration de technologies plus avancées, telles que la robotisation et les systèmes de contrôle automatisés.
Une des évolutions majeures réside dans la technologie de récupération de la poudre. Le système permet de collecter la poudre excédentaire qui n’a pas adhéré à la surface de la pièce et de la réinjecter dans le processus. Ce recyclage de la poudre non utilisée améliore non seulement l’efficacité du processus, mais réduit aussi le gaspillage de matériaux. Les systèmes de récupération modernes utilisent des filtres haute performance pour s’assurer que seules les particules de poudre de bonne qualité soient récupérées, évitant ainsi toute contamination qui pourrait affecter la finition du revêtement.
Le contrôle de la qualité a également été amélioré grâce à l’intégration de technologies de vision artificielle. Ces systèmes sont capables de surveiller en temps réel l’uniformité de l’application de la poudre et de détecter immédiatement toute anomalie, comme les zones non couvertes ou l’application excessive. Cela permet non seulement de garantir une qualité optimale, mais aussi d’éviter les défauts coûteux qui nécessiteraient une reprise.
Les systèmes de nettoyage automatisés ont également évolué pour garantir des opérations sans interruption. En effet, les lignes de poudrage sont souvent soumises à des changements fréquents de couleur ou de type de finition. La capacité à nettoyer rapidement et efficacement les équipements permet de réduire considérablement le temps d’arrêt de la production, améliorant ainsi la productivité globale.
Une autre tendance notable est l’utilisation de peintures en poudre de plus en plus spécialisées. De nouvelles formulations sont développées pour répondre à des exigences spécifiques, telles que des revêtements résistants à des températures extrêmes, des peintures antirouille pour des environnements très corrosifs ou des produits à finition métallique ou texturée. Ces peintures permettent de créer des revêtements à la fois esthétiques et fonctionnels, adaptés à une large gamme d’applications.
Les systèmes de cuisson des revêtements en poudre ont également évolué, avec des fours à haute efficacité énergétique qui permettent une meilleure gestion thermique et réduisent les coûts énergétiques. Les fours modernes sont souvent équipés de systèmes de récupération de chaleur, ce qui permet de réduire la consommation d’énergie en réutilisant la chaleur excédentaire pour réchauffer l’air ou les composants du système. Cela contribue non seulement à la réduction des coûts d’exploitation, mais aussi à la durabilité du processus.
Le développement des interfaces utilisateur a aussi progressé, les lignes de poudrage étant désormais contrôlées par des systèmes informatiques intuitifs qui permettent aux opérateurs de suivre et d’ajuster les paramètres de production en temps réel. Ces systèmes sont de plus en plus connectés, offrant une gestion à distance et la possibilité de surveiller les lignes de production à partir de n’importe quel endroit via des applications mobiles ou des logiciels basés sur le cloud. Cela permet aux entreprises de gérer plus efficacement la production, de réduire les erreurs humaines et de s’assurer que les lignes fonctionnent toujours à leur capacité optimale.
L’impact environnemental de la peinture en poudre est également pris en compte dans les innovations récentes. Avec des formulations sans solvant et une réduction de l’utilisation de produits chimiques dangereux, le poudrage électrostatique est désormais plus respectueux de l’environnement. Les revêtements en poudre écologiques deviennent plus courants, les fabricants cherchant à répondre aux normes strictes de durabilité et de sécurité tout en offrant des produits de qualité. Cette transition vers des peintures en poudre plus vertes s’accompagne souvent d’une réduction significative des émissions de COV (composés organiques volatils) et d’une réduction du recyclage des matériaux.
En matière de flexibilité de production, l’introduction des robots collaboratifs dans le processus de poudrage est un autre exemple de l’évolution technologique. Ces robots peuvent travailler en étroite collaboration avec les opérateurs humains, offrant ainsi une plus grande précision et adaptabilité dans le processus de peinture. Par exemple, ils peuvent être utilisés pour des ajustements fins des paramètres de pulvérisation, garantissant des applications encore plus homogènes et ajustées aux exigences spécifiques de chaque pièce. Ces robots permettent aussi de manipuler des pièces plus lourdes ou plus complexes, réduisant ainsi la charge de travail pour les opérateurs et augmentant l’efficacité du processus.
En outre, l’amélioration des systèmes de surveillance de l’environnement a permis d’obtenir des résultats encore plus précis en termes de qualité de finition. Les capteurs modernes mesurent en continu des facteurs tels que la température, l’humidité, la vitesse de l’air et la qualité de la poudre, ajustant automatiquement les paramètres du système pour garantir que les conditions restent optimales pour l’application de la peinture.
Le poudrage électrostatique reste un choix privilégié pour de nombreuses industries, notamment en raison de son faible coût opérationnel à long terme, de sa simplicité et de son efficacité. Les avancées continues en robotique, en automatisation et en technologie de contrôle des processus permettront de continuer à améliorer la qualité, la durabilité et la productivité des lignes de peinture en poudre.
En somme, le poudrage électrostatique offre des avantages non seulement en termes de coût, qualité et efficacité, mais il contribue également à une approche de fabrication plus durable et respectueuse de l’environnement. Les progrès technologiques futurs ne feront qu’augmenter la compétitivité de ce procédé, en rendant les lignes de production de peinture en poudre encore plus efficaces, adaptables et écologiques.
Le poudrage électrostatique continue de se développer avec de nouvelles innovations technologiques qui visent à améliorer la qualité, la productivité et l’impact environnemental du procédé. Parmi ces innovations, l’introduction de technologies intelligentes et de systèmes de suivi en temps réel est l’une des plus marquantes. Ces technologies permettent de surveiller et de contrôler précisément l’ensemble du processus de poudrage, du début à la fin, garantissant des performances optimales tout au long de la production.
Les systèmes d’intelligence artificielle (IA) et d’apprentissage automatique sont désormais intégrés dans les lignes de poudrage pour améliorer l’automatisation et la prise de décision. Ces systèmes peuvent analyser les données collectées par les capteurs et caméras pour ajuster automatiquement les paramètres de la ligne en fonction des variations des conditions environnementales ou des spécifications des pièces. Par exemple, un système de vision avancé peut détecter des irrégularités dans la distribution de la poudre et ajuster immédiatement la pulvérisation pour corriger la couverture avant même que le processus de cuisson ne commence.
Les lignes de production entièrement automatisées deviennent de plus en plus courantes, offrant une gestion optimisée des stocks et une réduction des coûts de main-d’œuvre. Les robots sont capables d’interagir non seulement avec les opérateurs, mais aussi avec d’autres machines et systèmes informatiques via des réseaux de communication industrielle. Cela permet une coordination parfaite entre les différentes étapes de la production, de l’application de la poudre jusqu’à la cuisson et le stockage des pièces finies. En intégrant ces technologies, les fabricants peuvent augmenter leur production tout en maintenant des coûts fixes bas et en répondant aux demandes de personnalisation des clients.
Une autre avancée importante est l’usage de nouveaux types de poudres qui élargissent les possibilités d’application du poudrage électrostatique. Ces poudres peuvent inclure des matériaux ayant des propriétés spécifiques, comme la résistance à des températures plus élevées, la protection contre la corrosion, ou des finitions particulières comme les effets métalliques ou texturés. Les recherches se poursuivent pour développer des poudres encore plus respectueuses de l’environnement, fabriquées à partir de matériaux recyclés ou ayant un impact carbone réduit, ce qui répond aux préoccupations croissantes concernant l’empreinte écologique des procédés industriels.
Le contrôle de la couleur est un autre domaine qui bénéficie des technologies modernes. Aujourd’hui, des systèmes de contrôle avancés permettent de garantir une uniformité parfaite dans la teinte et la finition des produits, même lors de changements fréquents entre différentes couleurs ou types de finition. Les algorithmes de gestion des couleurs aident à calibrer les machines en temps réel, réduisant ainsi les erreurs humaines et les temps d’arrêt associés aux changements de production.
En termes de maintenance, les lignes de poudrage modernes sont désormais équipées de systèmes de diagnostic à distance, permettant de détecter les problèmes avant qu’ils ne causent des pannes importantes. Les capteurs intelligents surveillent en continu l’état des équipements, comme les buses de pulvérisation, les moteurs des robots ou les systèmes de chauffage. Lorsqu’un problème potentiel est détecté, le système avertit les opérateurs et peut même recommander des actions de maintenance ou planifier des interventions. Cela permet de réduire les temps d’arrêt non planifiés et d’optimiser la durée de vie des équipements.
Les systèmes de gestion de la chaîne logistique jouent également un rôle clé dans l’optimisation du processus de poudrage. Les outils de planification et de gestion des stocks automatisent l’approvisionnement en matériaux et garantissent que la production se déroule sans interruption. En intégrant des technologies telles que le Blockchain et les systèmes ERP (Enterprise Resource Planning), les fabricants peuvent non seulement suivre l’état de leur production, mais aussi garantir une traçabilité complète des matériaux, depuis leur approvisionnement jusqu’à leur transformation en produits finis.
En termes de durabilité, les technologies de réduction de la consommation énergétique dans le processus de cuisson sont également en évolution. De nouveaux systèmes de chauffage à basse consommation et de recirculation de l’air permettent d’économiser de l’énergie pendant la phase de cuisson, ce qui représente une économie substantielle sur les coûts énergétiques et réduit l’empreinte carbone globale du processus. L’intégration de panneaux solaires ou de systèmes de gestion thermique plus avancés dans les installations permet également d’optimiser la consommation d’énergie tout en respectant les normes écologiques plus strictes.
Une autre tendance en matière de durabilité est la recyclabilité des produits finis. En plus des efforts de recyclage de la poudre excédentaire, certains fabricants développent des revêtements en poudre recyclables qui peuvent être récupérés et retraités pour d’autres cycles de production. Ces innovations permettent de minimiser le gaspillage de matériaux et d’encourager une approche plus circulaire dans l’industrie de la peinture en poudre.
Les revêtements fonctionnels prennent également de l’ampleur dans les applications industrielles. Par exemple, les poudres antibactériennes ou anti-UV sont de plus en plus demandées dans des secteurs comme la santé, l’aéronautique et les équipements extérieurs. Ces poudres sont conçues pour apporter des propriétés supplémentaires aux surfaces peintes, offrant ainsi des solutions plus techniques et spécialisées pour des environnements exigeants.
Enfin, la formation des opérateurs est un aspect crucial de l’évolution des lignes de poudrage électrostatique. Les entreprises investissent dans des programmes de formation et des simulations virtuelles pour permettre aux opérateurs de se familiariser avec les technologies avancées sans perturber la production. Grâce à des formations en réalité augmentée ou virtuelle, les opérateurs peuvent apprendre à manipuler les machines, effectuer des réglages fins et résoudre des problèmes en temps réel, tout en ayant accès à des bases de données de maintenance et de support technique.
En conclusion, le poudrage électrostatique continue de se perfectionner grâce à l’intégration de technologies avancées qui permettent une amélioration continue de l’efficacité, une réduction des coûts et une meilleure gestion de l’impact environnemental. Ces innovations permettent non seulement de répondre aux exigences croissantes des clients en termes de qualité et de personnalisation, mais aussi de promouvoir des pratiques de production plus durables et plus respectueuses de l’environnement. Le poudrage électrostatique reste une méthode de revêtement de choix pour de nombreuses industries, et ses avancées futures promettent de rendre ce procédé encore plus innovant, flexible et écologique.
Le poudrage électrostatique continue de s’imposer comme une solution de revêtement de plus en plus polyvalente, intégrant des innovations technologiques pour répondre à la demande croissante d’efficacité, de durabilité et de performance. Le procédé, qui reste un choix privilégié dans diverses industries, connaît une expansion en raison de l’amélioration continue des technologies associées à son utilisation.
Évolution de l’automatisation et de l’intelligence artificielle
L’intégration de l’intelligence artificielle (IA) dans les lignes de poudrage électrostatique a transformé le processus en le rendant plus réactif et autonome. Les systèmes d’IA, couplés avec des capteurs intelligents, permettent une surveillance en temps réel de l’ensemble du processus de peinture. Ces technologies permettent non seulement de détecter des anomalies dans l’application du revêtement, mais aussi de prédire des ajustements nécessaires avant qu’un problème ne survienne. Cela réduit non seulement le risque de défauts dans la finition mais aussi les coûts liés aux erreurs et à la reprise de pièces.
L’automatisation avancée, associée à des systèmes de robotique collaborative, permet aux robots et aux opérateurs humains de travailler en parfaite harmonie. Les robots peuvent effectuer des tâches répétitives et complexes, telles que l’application de la poudre, tout en s’ajustant en temps réel en fonction de la géométrie de chaque pièce, de sa couleur et des exigences de finition spécifiques. Ces robots collaboratifs ne se contentent pas de peindre des pièces, mais peuvent aussi interagir avec des systèmes de gestion de la production, optimisant ainsi les flux de travail et réduisant les temps d’arrêt pour la maintenance ou le changement de production.
Personnalisation et flexibilité accrue
Une des avancées majeures des systèmes modernes de poudrage électrostatique est la flexibilité qu’ils offrent en termes de personnalisation des revêtements. Les fabricants peuvent désormais ajuster les paramètres de pulvérisation pour obtenir des finitions spécifiques, comme des textures uniques ou des effets visuels particuliers. De plus, avec l’introduction des poudres métallisées, des finishes brillants, ou des couleurs personnalisées, le procédé de poudrage électrostatique est de plus en plus utilisé dans des secteurs nécessitant des finishes esthétiques de haute qualité. Cela permet aux entreprises de répondre à des demandes de plus en plus complexes et variées.
Les systèmes de gestion de la production basés sur le cloud permettent aux entreprises d’accéder à des données de production en temps réel, et ce, à distance. Cela permet une gestion plus agile et un suivi plus détaillé de chaque phase de la production, offrant ainsi une réactivité accrue en cas de besoin de modifications ou d’ajustements dans la production.
Processus de maintenance et optimisation
La maintenance prédictive, soutenue par l’utilisation de technologies IoT (Internet des Objets), joue également un rôle crucial dans les progrès du poudrage électrostatique. Grâce aux capteurs qui surveillent en continu les composants clés de l’équipement, les entreprises peuvent anticiper des pannes potentielles et effectuer une maintenance avant qu’un problème ne survienne. Les systèmes peuvent non seulement détecter les défauts dans les machines, mais aussi fournir des recommandations pour éviter des défaillances graves, ce qui permet de prolonger la durée de vie des équipements et de réduire les coûts associés aux arrêts imprévus.
Les systèmes de maintenance assistée par réalité augmentée (RA) sont aussi en train de prendre de l’ampleur. Grâce à des lunettes de RA, les techniciens peuvent recevoir des instructions en temps réel et visualiser des informations utiles concernant l’état des machines, la procédure de nettoyage, ou même les codes d’erreur pour un dépannage plus rapide et plus précis. Cela permet de réduire les erreurs humaines et améliore l’efficacité de la maintenance tout en minimisant les interruptions dans la production.
Réduction de l’empreinte écologique
L’un des principaux avantages du poudrage électrostatique reste son faible impact environnemental, surtout par rapport aux méthodes de peinture liquides traditionnelles. Le recyclage de la poudre excédentaire, la réduction des émissions de COV (composés organiques volatils) et la possibilité d’utiliser des matériaux plus écologiques sont des éléments essentiels pour répondre aux normes environnementales de plus en plus strictes. Les poudres sans solvant et les peintures en poudre recyclées contribuent à une approche plus durable et à une réduction des déchets dans le processus de production.
Des initiatives pour réduire la consommation d’énergie ont également vu le jour avec des fours à basse consommation énergétique et des technologies de recirculation de chaleur dans les installations de cuisson. Ces innovations permettent de réduire la consommation globale d’énergie, un facteur clé pour les industries qui cherchent à optimiser leur rentabilité tout en respectant les objectifs de développement durable.
Les revêtements à faible émission sont également en développement, et plusieurs fabricants ont mis au point des solutions de revêtement en poudre à base de matières premières naturelles ou recyclées. Ces solutions répondent non seulement aux attentes des consommateurs en matière de durabilité, mais sont également conformes aux nouvelles régulations environnementales.
Perspectives futures
Le futur du poudrage électrostatique semble être étroitement lié à l’évolution des technologies de fabrication telles que la fabrication additive (impression 3D) et les systèmes intégrés de production intelligente. Ces technologies devraient permettre une personnalisation encore plus poussée des produits et ouvrir la voie à des applications dans des secteurs comme l’aéronautique, l’électronique ou la médecine, où des exigences très spécifiques de finition et de protection des surfaces sont nécessaires.
L’avenir du poudrage électrostatique sera également marqué par la connexion des machines à des systèmes de gestion de la production plus sophistiqués, permettant une gestion totalement intégrée des lignes de production. Grâce à des algorithmes de gestion avancée, les entreprises pourront optimiser leur production en fonction de la demande, tout en minimisant les coûts et l’impact environnemental.
Conclusion
Le poudrage électrostatique a sans aucun doute un avenir prometteur, surtout avec les évolutions technologiques récentes qui ont transformé le processus de manière significative. Grâce à des innovations dans l’automatisation, la personnalisation, la maintenance prédictive, et la réduction de l’empreinte écologique, le procédé continue de s’imposer comme une solution incontournable pour les industries modernes cherchant à produire des revêtements de haute qualité tout en restant compétitives et respectueuses de l’environnement. Son intégration avec d’autres technologies émergentes, comme l’intelligence artificielle, la robotique collaborative, et la fabrication additive, assurera son développement futur en tant que procédé de revêtement à la fois efficace, durable et innovant.
Four industriel
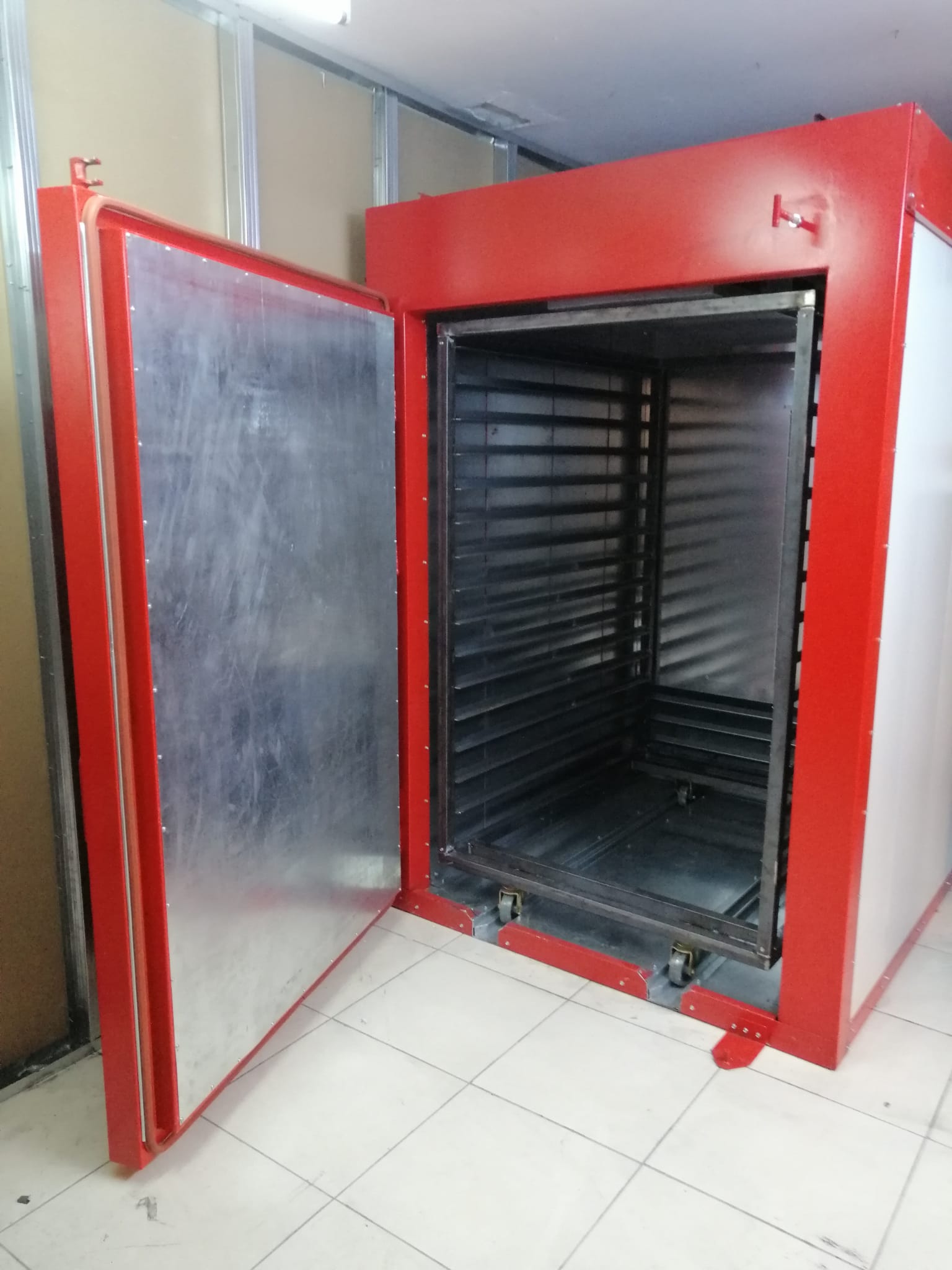
Le terme “Four industriel” fait référence à un appareil de chauffage utilisé dans une large gamme d’industries pour chauffer, cuire, sécher, ou traiter des matériaux à des températures élevées dans des environnements contrôlés. Ces fours sont essentiels dans divers processus de fabrication, y compris dans l’industrie de la métallurgie, de la céramique, du verre, de la peinture, de l’alimentation, et bien d’autres encore.
Les fours industriels peuvent être classifiés selon plusieurs critères, notamment :
Types de Fours Industriels
- Fours à convection : Ces fours utilisent des circulations d’air chaud pour chauffer les matériaux. Ils sont souvent utilisés dans les processus de cuisson de produits alimentaires ou pour des applications de séchage dans les industries chimiques et pharmaceutiques.
- Fours à induction : Utilisés principalement dans la métallurgie et le traitement des métaux, ces fours chauffent les matériaux grâce à un champ magnétique induit. Ils sont efficaces pour chauffer les métaux de manière rapide et uniforme.
- Fours à haute température : Ces fours sont utilisés pour des processus nécessitant des températures très élevées, comme dans l’industrie de la céramique, du verre ou du traitement thermique des métaux.
- Fours électriques : Ces modèles utilisent l’électricité pour produire de la chaleur. Ils sont couramment utilisés pour le traitement des matériaux sensibles ou dans des environnements où il est nécessaire de contrôler précisément la température.
- Fours à gaz : Ces fours sont alimentés par du gaz naturel ou d’autres combustibles fossiles. Ils sont fréquemment utilisés dans les industries où des températures modérées à élevées sont nécessaires pour des processus comme la cuisson ou le séchage.
- Fours à rayonnement : Ces fours utilisent des ondes infrarouges pour chauffer directement les objets, réduisant ainsi les pertes de chaleur et permettant un chauffage très rapide et efficace.
Applications des Fours Industriels
- Métallurgie : Traitement thermique des métaux, fonte, forgeage, ou pour la fusion des métaux.
- Céramique et verre : Utilisés pour la cuisson des poteries, des carreaux en céramique, des briques ou la fabrication du verre.
- Peinture industrielle : Dans les processus de curation de peinture ou de revêtement en poudre, les fours sont utilisés pour cuire la peinture à des températures élevées.
- Industrie alimentaire : Utilisés pour cuire, griller ou sécher les produits alimentaires, les fours industriels jouent un rôle clé dans la production de produits de consommation de masse.
- Chimie et pharmacie : Pour la réaction de matériaux dans des conditions de chaleur contrôlées, ainsi que pour le séchage des produits chimiques.
Caractéristiques techniques des Fours Industriels
- Contrôle de température précis : De nombreux fours industriels sont équipés de systèmes de régulation de température permettant de maintenir des conditions constantes et précises pour des procédés sensibles.
- Isolation thermique : Une bonne isolation est essentielle pour garantir l’efficacité énergétique et minimiser les pertes de chaleur.
- Dimensions et capacité : Les fours industriels peuvent être de différentes tailles, allant des petites unités pour des applications spécifiques aux grandes installations capables de traiter des volumes importants de matériaux.
- Efficacité énergétique : Les avancées récentes incluent des systèmes de récupération de chaleur et des technologies de contrôle de la consommation d’énergie pour réduire les coûts opérationnels.
- Sécurité : Les fours industriels sont souvent équipés de systèmes de sécurité, comme des capteurs de température, des alertes en cas de surchauffe, ou des systèmes d’arrêt d’urgence pour éviter tout accident.
Avantages et défis des Fours Industriels
Avantages :
- Haute efficacité énergétique, particulièrement avec les modèles modernes qui intègrent des technologies avancées de gestion thermique.
- Capacité de traitement à des températures très élevées, essentielle dans des secteurs comme la métallurgie ou la céramique.
- Flexibilité d’application, avec des solutions adaptées à une grande variété de matériaux et de procédés industriels.
Défis :
- Coût d’investissement initial élevé, en particulier pour les modèles à haute technologie.
- Entretien et maintenance nécessaires pour garantir la longévité et les performances du four.
- Impact environnemental, surtout pour les fours fonctionnant au gaz ou utilisant des combustibles fossiles, bien que des alternatives plus écologiques soient en développement.
En somme, les fours industriels jouent un rôle fondamental dans une multitude de secteurs industriels, assurant des processus de production efficaces, mais nécessitent une gestion adéquate de leur consommation d’énergie et de leur maintenance pour maximiser leur performance et leur durabilité.
Les fours industriels sont des équipements essentiels dans de nombreuses industries, servant à des processus de chauffage, de cuisson, de séchage ou de traitement des matériaux. Ils sont utilisés pour transformer des matières premières en produits finis ou semi-finis en appliquant de la chaleur de manière contrôlée. Grâce à leur capacité à fonctionner à des températures élevées, les fours industriels sont présents dans des secteurs aussi variés que la métallurgie, la céramique, le traitement thermique des métaux, la fabrication de verre, ainsi que dans l’industrie alimentaire et pharmaceutique.
Dans l’industrie métallurgique, les fours industriels sont utilisés pour la fusion des métaux, la refonte ou le traitement thermique des alliages. Ces fours doivent être capables d’atteindre des températures très élevées tout en maintenant une température uniforme à l’intérieur, afin d’assurer un traitement homogène du métal. Les fours à induction sont couramment utilisés dans ces applications en raison de leur efficacité et de leur capacité à chauffer rapidement le métal grâce à des champs magnétiques.
Dans l’industrie de la céramique et du verre, les fours industriels servent à cuire les matériaux à haute température pour les durcir, les vitrifier ou les transformer en une forme stable. Par exemple, dans la production de carreaux en céramique ou de briques, le processus de cuisson dans un four permet d’obtenir des produits résistants et durables. De même, dans la fabrication du verre, le four est crucial pour faire fondre les matières premières comme le sable et le carbonate de soude pour obtenir du verre fondu, qui est ensuite façonné en produits finis comme des bouteilles ou des fenêtres.
Les fours à convection sont largement utilisés dans des processus de cuisson et de séchage dans l’industrie alimentaire. Ces fours fonctionnent en chauffant l’air, puis en faisant circuler cet air chaud autour des produits à cuire ou à sécher. Cela permet d’assurer une cuisson uniforme, ce qui est particulièrement important dans des industries où la qualité du produit fini est primordiale, comme dans la production de pain, de biscuits, ou de snacks. De plus, les fours à infrarouge sont de plus en plus populaires dans certaines applications de cuisson rapide, notamment pour des produits comme les pizzas ou les repas pré-cuits, en raison de leur capacité à chauffer rapidement les surfaces des aliments.
Dans l’industrie pharmaceutique et chimique, les fours industriels sont utilisés pour le séchage de produits ou pour la réaction thermique de certaines matières premières. Les processus de séchage des poudres, des granulés ou des solutions nécessitent une température précise et un contrôle rigoureux de l’humidité. Les fours à température contrôlée jouent également un rôle clé dans la fabrication de médicaments, où des températures élevées ou bien ajustées sont nécessaires pour la stérilisation ou la dégradation de certains composés chimiques.
La technologie derrière les fours industriels a beaucoup évolué au fil des ans. Aujourd’hui, de nombreux fours industriels sont équipés de systèmes de gestion de la température ultra-précis, qui peuvent être réglés et contrôlés automatiquement, permettant ainsi un suivi en temps réel du processus de chauffage. Les systèmes de régulation électronique et les capteurs thermiques intégrés permettent d’optimiser la consommation d’énergie et d’éviter les variations de température qui pourraient affecter la qualité du produit.
L’un des enjeux majeurs dans la gestion des fours industriels reste la consommation d’énergie. Ces équipements, surtout lorsqu’ils fonctionnent à des températures très élevées pendant de longues périodes, peuvent représenter une part significative des coûts d’exploitation. C’est pourquoi de nombreux fabricants cherchent à améliorer l’efficacité énergétique des fours industriels en intégrant des systèmes de récupération de chaleur ou en utilisant des technologies de chauffage plus économes en énergie, comme les fours à induction ou les fours électriques.
La durabilité et l’impact environnemental des fours industriels sont également des considérations importantes, notamment pour ceux qui utilisent des combustibles fossiles comme source d’énergie. L’intégration de technologies vertes, telles que des systèmes de chauffage solaire ou l’utilisation de biomasse comme source d’énergie, est en pleine expansion. De plus, les revêtements thermiques avancés et les systèmes de gestion des gaz d’échappement peuvent réduire les émissions de polluants et améliorer l’empreinte carbone des équipements.
Les fours industriels modernes sont également conçus pour être plus flexibles et adaptables aux besoins changeants des processus de production. Ils peuvent désormais être reconfigurés pour traiter différents matériaux ou pour répondre à des exigences de production spécifiques, tout en maintenant une consommation d’énergie optimale. Par exemple, dans les industries du revêtement et de la peinture en poudre, les fours de cuisson sont capables de traiter une large gamme de produits tout en garantissant des résultats uniformes et de haute qualité.
La maintenance des fours industriels est également cruciale pour garantir leur bon fonctionnement à long terme. Les fabricants mettent en place des systèmes de surveillance à distance et de diagnostic intelligent pour surveiller l’état de l’équipement et anticiper les besoins de réparation avant que des pannes majeures ne se produisent. Ces technologies permettent de minimiser les temps d’arrêt et d’assurer la fiabilité des processus industriels.
En conclusion, les fours industriels jouent un rôle fondamental dans une multitude de secteurs de production, et leur évolution continue permet de répondre à des exigences toujours plus strictes en termes de performance, efficacité énergétique, et impact environnemental. Leurs applications variées, combinées à l’essor des technologies modernes, rendent ces équipements essentiels pour des industries cherchant à améliorer leurs procédés de fabrication tout en respectant des normes de durabilité et d’efficacité.
L’évolution des fours industriels se poursuit avec l’intégration de technologies de pointe qui transforment la manière dont ces équipements sont utilisés. À l’avenir, les fours industriels deviendront encore plus intelligents et autonomes, avec des capacités de connexion à des réseaux intelligents pour une gestion optimisée de la production. L’une des grandes tendances actuelles est l’introduction de la connectivité IoT (Internet des objets) dans les systèmes de chauffage industriels. Cela permet de surveiller et de contrôler les fours à distance, offrant ainsi une gestion en temps réel et des données précises sur les performances et les conditions de fonctionnement.
Les algorithmes prédictifs et l’analyse des données en temps réel permettent de détecter des anomalies ou des déviations par rapport aux normes de fonctionnement, avant qu’elles ne causent des dysfonctionnements ou des pertes de qualité. Par exemple, un four industriel doté de ces technologies peut alerter les opérateurs d’une augmentation anormale de la température ou d’une variabilité de la consommation énergétique, signalant un problème potentiel avant qu’il ne devienne critique.
En parallèle, l’automatisation des processus de gestion de la production s’améliore. Les robots et les systèmes d’intelligence artificielle peuvent désormais gérer non seulement l’alimentation des matériaux dans le four, mais aussi la programmation des températures et la surveillance de l’environnement interne du four. Cela permet une réduction des erreurs humaines et une gestion optimale des cycles de production.
Un autre domaine dans lequel les fours industriels continuent d’évoluer est la réduction de leur impact environnemental. Le recours à des technologies écoénergétiques et à des sources d’énergie plus durables, comme les fours à induction ou les fours à haute efficacité, devient une priorité pour les fabricants. De plus, certains fours industriels modernes utilisent des matériaux recyclés ou des revêtements écologiques qui minimisent les déchets et contribuent à la protection de l’environnement.
L’optimisation énergétique passe également par l’amélioration de l’isolation thermique des fours industriels. Les matériaux d’isolation de nouvelle génération, plus légers et plus efficaces, permettent de conserver la chaleur plus longtemps et de réduire la perte d’énergie, ce qui diminue la consommation d’énergie et les coûts opérationnels. De plus, l’intégration de systèmes de récupération de chaleur permet de récupérer l’énergie excédentaire du four pour chauffer d’autres parties de l’usine ou pour des processus adjacents, créant ainsi un système énergétique circulaire plus durable.
La maintenance prédictive devient aussi de plus en plus courante grâce à l’intégration de la technologie des capteurs intelligents dans les fours. Ces capteurs sont capables de surveiller des paramètres tels que la température, la vibrations, l’humidité et l’usure des composants en temps réel. En cas de déviation de l’un de ces paramètres par rapport aux seuils normaux, le système de gestion du four peut déclencher des alertes pour informer les techniciens de la nécessité d’une intervention avant que des pannes majeures ne se produisent. Cela non seulement réduit les coûts de maintenance, mais prolonge également la durée de vie des équipements, ce qui est crucial pour maximiser l’investissement dans des installations de production.
Le système de contrôle automatisé des fours industriels permet aussi une personnalisation accrue des processus de cuisson ou de traitement thermique. Cela permet de répondre à des demandes spécifiques de la production, comme la variation de la température en fonction de la taille des matériaux ou la variation de la composition chimique des produits à traiter. L’adaptabilité des systèmes de contrôle rend les fours industriels encore plus flexibles et performants dans des environnements de production à haute exigence.
Enfin, l’impact social et économique des fours industriels ne doit pas être sous-estimé. Le passage à des technologies plus intelligentes et écoénergétiques permet aux entreprises non seulement de réduire leurs coûts opérationnels, mais aussi de se conformer à des normes environnementales de plus en plus strictes, ce qui peut offrir un avantage compétitif sur le marché. La durabilité et l’efficacité des fours industriels sont désormais des critères clés dans le choix de la technologie à adopter pour les manufacturiers soucieux de leur responsabilité sociétale.
L’intégration de nouvelles technologies, telles que l’intelligence artificielle et la robotique avancée, ainsi que les efforts pour rendre les processus industriels plus durables et écoénergétiques, sont des éléments clés qui continueront à définir l’avenir des fours industriels. Ces avancées permettront de répondre aux besoins croissants des industries pour des solutions de chauffage et de traitement thermique plus intelligentes, plus efficaces et plus respectueuses de l’environnement, tout en offrant un retour sur investissement amélioré et en soutenant la transition vers des pratiques industrielles plus durables.
Le futur des fours industriels semble résolument tourné vers l’intégration des technologies numériques, de l’intelligence artificielle (IA) et de l’automatisation avancée. Ces avancées permettront d’améliorer encore davantage l’efficacité, la productivité, et la durabilité des processus industriels tout en réduisant les coûts d’exploitation. La capacité à interconnecter les fours avec d’autres équipements industriels au sein d’un environnement usine intelligente permettra aux entreprises de surveiller en temps réel la performance de leurs installations, de prédire les défaillances potentielles et de prendre des décisions basées sur des données précises.
Systèmes de Contrôle Avancés
Les systèmes de contrôle avancés associés aux fours industriels permettront non seulement d’améliorer la qualité du produit final, mais aussi d’assurer une optimisation énergétique constante. Grâce à des algorithmes de machine learning, ces systèmes apprendront des données historiques et des modèles thermiques pour ajuster automatiquement les paramètres de fonctionnement du four en fonction des conditions environnementales changeantes ou des exigences spécifiques de la production. Par exemple, un système basé sur l’IA pourra ajuster la température ou la vitesse de circulation de l’air dans un four de peinture en poudre en fonction de l’humidité ambiante ou de la taille des pièces à traiter, garantissant une finition de haute qualité tout en économisant de l’énergie.
Technologies de Récupération et de Gestion de l’Énergie
Un des grands enjeux dans le domaine des fours industriels est la gestion de l’énergie, notamment dans un contexte où les coûts de l’énergie et les préoccupations environnementales ne cessent de croître. Les systèmes de récupération de chaleur permettent de capter l’énergie excédentaire générée lors du chauffage ou du processus de cuisson pour la réutiliser dans d’autres parties du processus de production ou pour chauffer les installations adjacentes. Ces solutions permettront aux entreprises de réduire leur consommation énergétique et d’améliorer leur rentabilité tout en minimisant leur impact environnemental.
Par exemple, dans le cadre des fours à haute température utilisés pour la métallurgie ou la fabrication de verre, une bonne gestion de l’énergie est essentielle. En utilisant des systèmes de récupération de chaleur intelligents, la chaleur excédentaire peut être convertie en énergie électrique ou utilisée pour préchauffer les matières premières, réduisant ainsi la consommation d’énergie fossile et contribuant à un processus plus écologique.
Maintenance Prédictive et Internet des Objets (IoT)
Les fours industriels seront de plus en plus équipés de capteurs IoT pour collecter des données en temps réel sur leur état. Ces capteurs pourront surveiller des facteurs tels que la température, l’humidité, la pression et l’usure des composants, et transmettre ces informations à un système centralisé. Grâce à l’analyse de ces données, les fabricants pourront prédire avec une grande précision quand un composant du four est susceptible de se détériorer et planifier des interventions de maintenance avant qu’une panne ne survienne. Cela réduira les temps d’arrêt imprévus, augmentera la productivité et réduira les coûts associés aux réparations urgentes.
De plus, l’intégration de technologies de maintenance prédictive permet de maximiser la durée de vie des équipements, ce qui est crucial pour les entreprises investissant dans des installations coûteuses comme des fours industriels. En optimisant les intervalles de maintenance, les entreprises peuvent réduire le nombre de réparations majeures et améliorer l’efficacité de leurs lignes de production.
Fours à Énergie Renouvelable et Écologique
L’innovation dans le domaine des fours industriels se dirige également vers l’utilisation de sources d’énergie renouvelables. Les fours à induction, déjà populaires dans les applications métallurgiques, sont un excellent exemple de la tendance à l’électrification des processus industriels. Ceux-ci peuvent être alimentés par des énergies renouvelables, telles que l’énergie solaire ou l’énergie éolienne, ce qui permet de réduire les émissions de carbone associées à l’utilisation d’énergies fossiles.
Dans des secteurs comme la fabrication de verre ou la production de céramique, où les températures élevées sont nécessaires, des recherches sont en cours pour remplacer les fours à gaz par des systèmes alimentés par biomasse ou des fours électriques à haute efficacité. En combinant ces technologies avec des systèmes de récupération de chaleur et des matériaux d’isolation thermique de haute performance, il est possible de créer des processus de fabrication industriels beaucoup plus écologiques et économiquement viables.
Fours Adaptatifs et Flexibles
Les besoins des industries évoluent, et les fours industriels doivent être capables de s’adapter à des volumes de production variables et à des produits de plus en plus diversifiés. Les fours modulaires et flexibles permettent une personnalisation rapide du processus de chauffage en fonction des caractéristiques spécifiques des matériaux ou des exigences du produit final. Par exemple, un four utilisé pour la peinture en poudre peut être reconfiguré pour traiter différents types de matériaux ou différentes tailles de pièces, tout en maintenant des paramètres thermiques constants pour une finition uniforme. Cette flexibilité est d’autant plus importante dans un contexte industriel où les demandes du marché peuvent changer rapidement.
L’avenir des Fours Industriels
L’avenir des fours industriels est indéniablement tourné vers une plus grande interconnexion, une efficacité énergétique accrue, et une durabilité renforcée. Le passage à des technologies de production intelligentes et écologiques permettra aux entreprises de mieux répondre aux défis contemporains liés à la conformité environnementale, à la réduction des coûts et à la réalisation de produits de haute qualité.
À mesure que les systèmes automatisés, l’analyse des données, et les énergies renouvelables deviennent des éléments de plus en plus intégrés aux processus industriels, les fours industriels continueront à jouer un rôle central dans la transformation numérique des industries, apportant des solutions à la fois innovantes et durables pour les générations futures.
Température de polymérisation
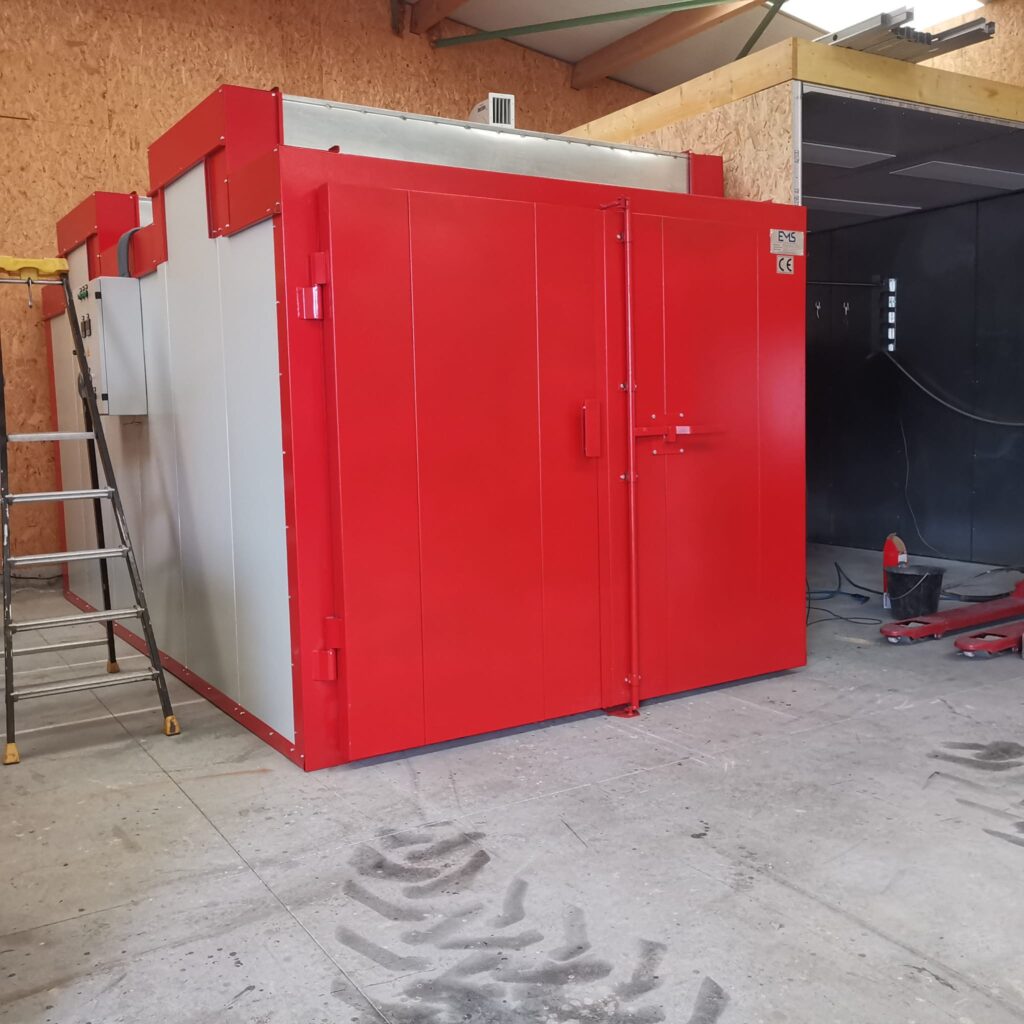
La température de polymérisation fait référence à la température à laquelle les réactions chimiques nécessaires pour former un polymère (ou un matériau polymérisé) se produisent. Cette température est cruciale pour les procédés de polymérisation, car elle influence directement la vitesse de réaction, la structure du polymère final et ses propriétés physiques. La polymérisation est le processus par lequel de petites molécules appelées monomères se lient entre elles pour former une chaîne longue et stable, créant ainsi un polymère.
Types de Polymérisation et Températures Associées
Les températures de polymérisation peuvent varier en fonction du type de polymérisation et du matériau à traiter. Voici quelques exemples courants :
- Polymérisation par ajout :
- Ce type de polymérisation, également appelé polymérisation en chaîne, implique des monomères insaturés (c’est-à-dire qui ont une double liaison) qui réagissent en chaîne sous l’effet d’un initiateur (souvent une chaleur ou un agent chimique).
- La température idéale de polymérisation varie en fonction du monomère et de l’initiateur utilisé. Par exemple, pour des polymères comme le polyéthylène (PE), la polymérisation peut se produire entre 60 et 120°C, tandis que pour des polymères comme le polystyrène, les températures de polymérisation peuvent être autour de 90 à 130°C.
- Polymérisation par condensation :
- Ce type de polymérisation est caractérisé par l’élimination d’une petite molécule (souvent de l’eau ou de l’alcool) lors de la réaction entre les monomères.
- La température de polymérisation pour la polycondensation est souvent plus basse que pour la polymérisation par ajout. Par exemple, la polycondensation de l’acide téréphtalique et du éthylène glycol (pour produire le PET – polyéthylène téréphtalate) se déroule généralement autour de 250 à 300°C.
- Polymérisation radicalaire :
- C’est un type de polymérisation où un radical libre initie la réaction. Cette méthode est utilisée pour des matériaux comme les résines époxy, les acryliques, et certains polymères thermoplastiques.
- Les températures de polymérisation pour ce processus varient, mais pour des matériaux comme les résines époxy, la température de polymérisation peut se situer entre 100°C et 200°C, selon la formulation de la résine et l’initiateur.
- Polymérisation en solution ou en suspension :
- Dans la polymérisation en solution, un monomère est dissous dans un solvant, tandis que dans la polymérisation en suspension, les monomères sont suspendus dans une phase liquide sous forme de gouttelettes.
- Les températures de polymérisation pour ces méthodes peuvent également varier, mais typiquement, elles se situent entre 60 et 130°C, selon les conditions spécifiques et les caractéristiques du solvant ou du milieu utilisé.
Importance de la Température de Polymérisation
La température joue un rôle essentiel dans la qualité et les caractéristiques du polymère final :
- Vitesse de réaction : Une température trop basse peut ralentir la réaction, ce qui entraîne des temps de polymérisation plus longs. Une température trop élevée peut conduire à une réaction trop rapide, créant des propriétés inégales dans le polymère.
- Propriétés du polymère : La température de polymérisation affecte des caractéristiques importantes comme la résistance mécanique, la résistance thermique, et la viscosité du polymère formé.
- Contrôle du processus : Maintenir la température dans une plage optimale permet de mieux contrôler la structure du polymère, ce qui est crucial pour des applications comme le revêtement ou la fabrication de plastiques.
Polymérisation en Peinture en Poudre
Dans le contexte des revêtements en poudre ou peinture en poudre, la température de polymérisation est un paramètre crucial. En effet, pour assurer une bonne durabilité, une bonne finition et une adhérence des couches de peinture, la température de polymérisation doit être soigneusement contrôlée :
- Pour les peintures en poudre thermodurcissables, la température de polymérisation se situe généralement entre 160°C et 200°C. Le durcissement complet des peintures en poudre prend typiquement de 15 à 30 minutes à cette température, selon l’épaisseur de la couche appliquée.
- Une température trop basse peut conduire à une polymérisation incomplète, ce qui réduit la résistance et la durabilité du film de peinture.
- En revanche, une température trop élevée peut causer des déformations ou des cicatrices sur le revêtement en raison de l’écrasement thermique ou du détachement de la peinture.
Conclusion
La température de polymérisation est un facteur clé pour assurer la qualité du produit final, qu’il s’agisse de polymères utilisés dans des applications industrielles ou de revêtements de surface. Les entreprises doivent contrôler cette température de manière précise et régulière pour garantir des résultats cohérents, optimiser la consommation d’énergie, et réduire les déchets ou défauts de fabrication.
La température de polymérisation est essentielle pour garantir la réussite des processus industriels qui impliquent des matériaux polymères, qu’il s’agisse de plastiques, de revêtements, ou de résines. En fonction de la nature des matériaux et du type de polymérisation, cette température influencera non seulement la vitesse de la réaction, mais aussi la structure chimique du polymère final, ses propriétés mécaniques et sa durabilité.
Lorsqu’un matériau polymère est exposé à des températures spécifiques, cela peut provoquer une réaction chimique où les monomères se lient entre eux pour former des chaînes de polymères. Si la température est trop basse, la réaction peut être trop lente ou incomplète, ce qui entraîne un polymère de mauvaise qualité, tandis qu’une température trop élevée peut entraîner des dégradations ou des réactions secondaires non désirées. Ainsi, trouver la température optimale est crucial.
Dans des processus industriels comme celui des revêtements en poudre, la température de polymérisation joue un rôle déterminant pour obtenir des revêtements durables et résistants. La polymérisation des revêtements en poudre se fait généralement dans des fours industriels à des températures de l’ordre de 160 à 200°C, où la peinture, sous forme de poudre, se fond, s’étale et se durcit sur la surface du produit à traiter. Le contrôle précis de la température permet d’assurer une adhérence optimale au substrat et une finition homogène, tout en évitant des défauts tels que des bullettes ou des irrégularités dans le revêtement.
La température de polymérisation affecte aussi la densité du polymère formé. Si la température est trop élevée, il peut se produire une réaction trop rapide, entraînant une polymérisation incomplète ou une formation de chaînes trop courtes, ce qui peut rendre le polymère plus fragile. Inversement, une température trop basse peut entraîner un polymère trop souple et avec une résistance réduite. Ainsi, le temps de chauffage et la maintien de la température constante pendant toute la durée du processus sont également des facteurs à prendre en compte pour assurer des propriétés uniformes et optimales du polymère final.
Dans les applications de peinture en poudre, la durée du cycle de polymérisation est également influencée par la température. Par exemple, à 160°C, la polymérisation peut prendre environ 20 minutes pour être complète, tandis qu’à des températures plus élevées, le temps de durcissement peut être réduit. Une fois le revêtement durci, les propriétés du matériau comme sa résistance à l’usure, sa résistance thermique et sa résistance chimique seront maximisées. Le contrôle de la température est donc essentiel pour éviter toute surchauffe ou sous-chauffe, garantissant ainsi un produit final qui répond aux standards de qualité requis.
Pour les matériaux utilisés dans des procédés comme la fabrication de composites ou de plastiques moulés, une température de polymérisation mal contrôlée peut entraîner des défauts comme des bulles d’air, des zones non durcies ou une répartition inégale du matériau. C’est pourquoi l’utilisation de capteurs de température et d’un contrôle automatisé dans les fours industriels est indispensable pour maintenir une température constante et assurer des produits de qualité.
De plus, la technique de polymérisation choisie a un impact direct sur la température idéale. Par exemple, la polymérisation radicalaire nécessitant souvent l’utilisation de radicaux libres peut être effectuée à des températures relativement basses, tandis que des processus comme la polymérisation par addition ou la polymérisation par condensation peuvent nécessiter des températures plus élevées pour initier et maintenir la réaction.
Ainsi, le contrôle de la température de polymérisation ne se limite pas simplement à des considérations thermiques. Il englobe également des aspects comme l’efficacité énergétique, la consommation d’énergie et l’optimisation du temps de production, ce qui peut avoir des répercussions importantes sur les coûts de fabrication. L’avènement des systèmes de contrôle numérique et des capteurs IoT dans les processus industriels permet de mieux ajuster et réguler ces paramètres pour atteindre les résultats souhaités avec une plus grande précision, ce qui est particulièrement important dans des industries où les standards de qualité sont stricts.
En résumé, la température de polymérisation est un facteur déterminant pour la production de matériaux polymères de qualité. Elle influe directement sur la vitesse de réaction, la structure du polymère et ses propriétés finales, et doit être soigneusement surveillée et régulée pour garantir des performances optimales.
La gestion de la température de polymérisation est également étroitement liée aux systèmes de contrôle utilisés dans les installations industrielles. Avec l’avancement des technologies, les entreprises ont désormais accès à des systèmes automatisés qui permettent un suivi en temps réel de la température à l’intérieur des fours industriels ou des bains de polymérisation. Ces systèmes peuvent ajuster automatiquement les paramètres de chauffage pour maintenir la température optimale tout au long du processus, ce qui améliore la précision et réduit les risques d’erreur humaine.
L’un des grands avantages de l’automatisation est la possibilité d’intégrer des algorithmes de contrôle adaptatif capables de réagir aux fluctuations de température dues aux variations de la charge thermique dans le four. Cela permet de compenser des facteurs externes tels que des changements de température ambiante ou des fluctuations de la puissance énergétique. De plus, des systèmes intelligents de surveillance et de diagnostic peuvent détecter toute anomalie, comme une montée en température trop rapide ou une chute soudaine, et ajuster le processus en conséquence pour éviter des défauts de polymérisation ou des pannes coûteuses.
Impact environnemental et réduction des coûts
Une gestion optimale de la température de polymérisation ne concerne pas seulement la qualité du produit final, mais aussi l’impact environnemental et les coûts d’exploitation. En optimisant la température et le temps de polymérisation, les entreprises peuvent réduire la consommation d’énergie, ce qui est crucial dans un contexte où les coûts énergétiques continuent de monter. Par exemple, des systèmes de récupération thermique peuvent être utilisés pour capter la chaleur excédentaire générée pendant la polymérisation et la réutiliser dans d’autres parties du processus de production, comme le préchauffage des matières premières. Cela permet non seulement d’économiser de l’énergie, mais aussi de réduire l’empreinte carbone de l’entreprise.
Les processus de polymérisation à basse température ou avec des technologies plus efficaces en termes énergétiques, comme la polymérisation UV ou LED pour certains types de revêtements en poudre, offrent aussi des possibilités d’optimisation. Ces technologies permettent une polymérisation rapide à des températures beaucoup plus basses, ce qui réduit les besoins énergétiques tout en garantissant une finition de haute qualité.
Adaptation aux nouvelles exigences industrielles
Avec les innovations constantes dans les matériaux polymères et les exigences croissantes des secteurs industriels, la température de polymérisation devra être flexible pour s’adapter aux nouvelles applications. Par exemple, les industries de l’automobile, de l’aérospatiale ou de l’électronique exigent des matériaux polymères qui sont non seulement résistants, mais aussi légers, durables et capables de résister à des températures extrêmes. Les revêtements polymères utilisés dans ces industries nécessitent souvent une polymérisation rapide et une stabilité thermique à des températures élevées.
Cela signifie que la température de polymérisation devra être ajustée en fonction de la composition du matériau, de l’application spécifique, et des exigences des clients finaux. Les systèmes de polymérisation haute performance, en particulier ceux utilisés pour des applications de haute technologie, devront offrir une précision et un contrôle thermique plus avancés, tout en respectant des délais de production serrés.
Nouvelles technologies et procédés alternatifs
Les procédés alternatifs de polymérisation, tels que la polymérisation à rayonnement (UV, infrarouge), sont en développement et permettent une réduction significative de la température nécessaire pour la réaction. Ces technologies sont particulièrement intéressantes pour les applications où la réduction du temps de durcissement est cruciale. Par exemple, dans le cas des revêtements métalliques ou des peintures automobiles, la polymérisation par rayonnement UV permet de durcir les films de peinture instantanément, à des températures bien plus basses que celles utilisées dans les méthodes thermiques conventionnelles.
Ces procédés sont également plus écologiques, car ils émettent moins de CO2 par rapport aux fours thermiques traditionnels et utilisent moins d’énergie pour la même efficacité. Cela ouvre la voie à une réduction des émissions industrielles, tout en permettant une production plus rapide et une meilleure productivité.
Conclusion
La température de polymérisation est un facteur fondamental pour l’obtention de matériaux polymères de haute qualité. Un contrôle précis de cette température permet de garantir non seulement la qualité du produit final, mais aussi d’optimiser les coûts de production, de réduire les impacts environnementaux et d’améliorer la productivité. L’évolution technologique continue dans les domaines de l’automatisation, de l’efficacité énergétique, et des procédés alternatifs permettra aux industries de répondre plus efficacement aux défis futurs tout en maintenant des standards de performance de plus en plus élevés.
L’optimisation des températures de polymérisation ne se limite pas uniquement à l’atteinte d’une qualité de produit idéale, mais elle est également un levier stratégique pour la réduction des coûts de production. L’un des principaux objectifs dans les industries modernes est d’améliorer les rendements tout en réduisant les dépenses énergétiques, ce qui est possible grâce à des techniques avancées de gestion thermique. Cela est particulièrement pertinent dans des environnements de production où la consommation énergétique représente une part importante des coûts d’exploitation.
Les systèmes de contrôle thermique de dernière génération permettent aux entreprises de maintenir des températures de polymérisation parfaitement stables, même en présence de variations dans le processus ou des conditions externes. Cela est particulièrement essentiel pour des produits où la consistance et la qualité sont primordiales, comme dans la fabrication de pièces automobiles, de revêtements décoratifs, ou d’applications électroniques, qui exigent une finition de surface extrêmement précise.
Mise en œuvre de stratégies de réduction de l’énergie
Un autre aspect clé dans le contrôle de la température de polymérisation est l’intégration des énergies renouvelables dans les processus de production. Par exemple, les panneaux solaires, les systèmes géothermiques ou même les énergies récupérées provenant des systèmes de production peuvent être utilisés pour fournir de l’énergie à des fours de polymérisation. Cela permet de réduire l’empreinte carbone de l’entreprise tout en maintenant des coûts énergétiques plus bas. Les systèmes hybrides, qui combinent des énergies traditionnelles et renouvelables, peuvent offrir une solution très performante et rentable à long terme.
Les technologies de récupération de chaleur jouent également un rôle essentiel dans la réduction de la consommation d’énergie. Par exemple, la récupération thermique des gaz chauds sortant des fours de polymérisation peut être utilisée pour chauffer l’air d’entrée ou des matières premières. Cela non seulement réduit la consommation d’énergie, mais aussi optimise le rendement thermique global de l’installation, ce qui conduit à des économies considérables sur le long terme.
Polymérisation et durabilité des matériaux
Dans un contexte où la durabilité et la performance environnementale deviennent des critères de plus en plus importants, la gestion de la température de polymérisation doit également tenir compte des propriétés écologiques des matériaux. L’évolution vers des polymères écologiques ou biopolymères nécessite des approches plus nuancées en termes de températures de polymérisation et d’additifs. Ces matériaux ont souvent des exigences spécifiques en termes de conditions de durcissement, qui ne sont pas les mêmes que celles des polymères synthétiques classiques.
La polymérisation verte, qui inclut des processus utilisant des matériaux d’origine renouvelable et moins polluants, va également de pair avec des températures de polymérisation optimisées. Les fabricants de peintures en poudre et autres produits similaires explorent activement des alternatives aux processus thermiques traditionnels en utilisant des systèmes de polymérisation à faible température, ou des techniques innovantes comme la polymérisation par lumière UV, qui réduit considérablement la consommation d’énergie tout en offrant un produit final de haute qualité.
Application dans la conception de nouveaux matériaux
L’un des domaines les plus intéressants dans l’application des températures de polymérisation est la conception de matériaux fonctionnels destinés à des applications de pointe. Par exemple, les revêtements thermorésistants, les matériaux composites utilisés dans l’aéronautique ou les revêtements anticorrosion pour l’industrie chimique, ont des exigences très strictes en matière de polymérisation. La température de polymérisation devra être précisément contrôlée pour atteindre des propriétés thermomécaniques spécifiques, telles qu’une résistance élevée aux chocs thermiques, une bonne stabilité dimensionnelle et une adhérence accrue.
Les avancées dans le contrôle thermique des processus permettent d’atteindre des propriétés mécaniques avancées, et de plus en plus de matériaux sont conçus pour offrir des performances extrêmes sous des conditions difficiles. Par exemple, dans l’aéronautique, les matériaux utilisés dans la fabrication des pièces doivent résister à des températures très élevées, tout en étant légers et robustes. De même, les revêtements en poudre pour ces secteurs sont spécialement formulés pour être durcis à des températures très spécifiques et relativement élevées, sans compromettre leur intégrité.
Tendance vers des systèmes de polymérisation flexibles
Un autre aspect innovant est la création de systèmes flexibles capables de s’adapter à une large gamme de températures et de conditions de polymérisation. Cette approche est particulièrement importante pour les industries qui fabriquent des produits personnalisés ou à faible volume, où des changements fréquents dans les conditions de production sont nécessaires. Ces systèmes permettent de moduler en fonction des matériaux spécifiques, de la taille des lots et des exigences du client. Cela augmente l’efficacité des lignes de production et améliore la réactivité des entreprises face aux nouvelles demandes du marché.
Conclusion
En résumé, la gestion de la température de polymérisation joue un rôle central dans la production de matériaux polymères de haute qualité, à la fois pour des applications courantes et pour des secteurs de haute technologie. Un contrôle précis de la température permet non seulement de garantir des produits finaux de qualité supérieure, mais aussi d’optimiser l’efficacité énergétique, de réduire les coûts de production, et d’améliorer la durabilité des matériaux. À mesure que les industries s’adaptent aux exigences environnementales et aux nouvelles technologies, le contrôle thermique des procédés de polymérisation devient de plus en plus essentiel pour rester compétitif tout en répondant aux normes écologiques strictes.
Cuisson de peinture
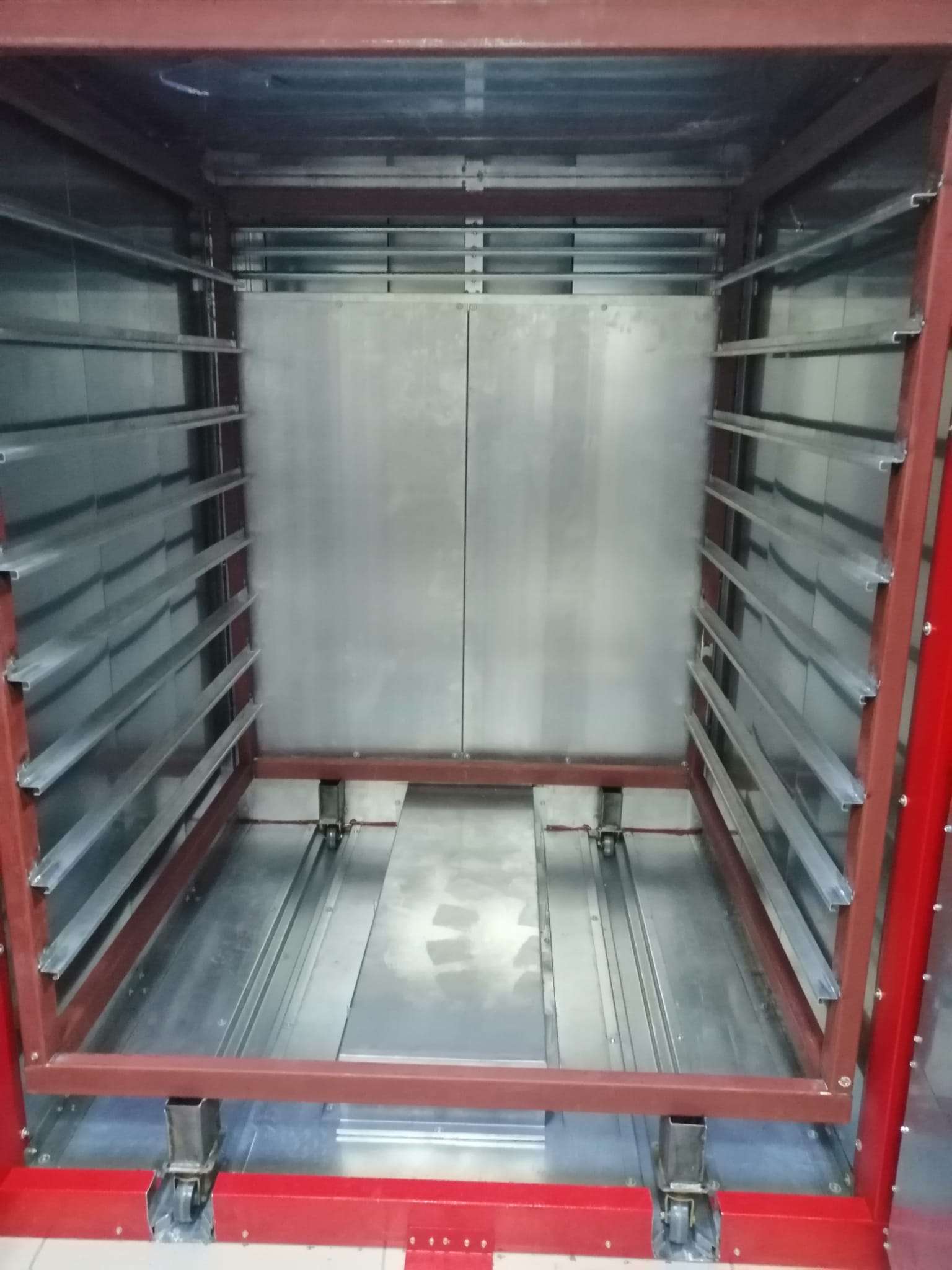
La cuisson de peinture est un processus essentiel dans de nombreuses applications industrielles, où une peinture ou un revêtement est appliqué sur une surface afin de lui donner un aspect esthétique, tout en lui conférant des propriétés fonctionnelles comme la résistance à la corrosion, la résistance thermique, ou la durabilité. Ce processus permet à la peinture de durcir et de se fixer solidement à la surface, garantissant ainsi un résultat de haute qualité.
Processus de cuisson de peinture
Le processus de cuisson se déroule généralement en plusieurs étapes, qui varient en fonction du type de peinture utilisée (liquide, en poudre, etc.) et des caractéristiques du matériau à peindre.
- Application de la peinture
La première étape consiste à appliquer la peinture sur la surface du matériau à l’aide de diverses méthodes comme la pinceau, le rouleau, la pistolet de pulvérisation, ou la poudrage électrostatique pour les revêtements en poudre. Une fois la peinture appliquée, elle est prête pour la phase de cuisson. - Phase de séchage préalable
Avant d’entrer dans le four de cuisson, certaines peintures, notamment les peintures à base de solvant, nécessitent un séchage préalable à température ambiante pour éliminer l’excès de solvant et rendre la surface moins sujette aux imperfections lors de la cuisson. Ce pré-séchage permet également d’éviter que la peinture ne se transforme en une masse trop épaisse ou que la finition ne devienne irrégulière. - Cuisson dans un four industriel
Une fois la peinture appliquée, la surface est placée dans un four de cuisson où elle subit un traitement thermique à une température contrôlée. La température de cuisson est essentielle pour garantir une polymérisation ou un durcissement optimal de la peinture. Cela varie en fonction du type de peinture :- Pour les peintures en poudre, la température de cuisson est généralement comprise entre 160 et 200°C pendant 10 à 30 minutes en fonction des spécifications du produit et des dimensions de la pièce à peindre.
- Pour les peintures à base de solvant, la cuisson peut être réalisée à une température légèrement plus basse, mais peut durer plus longtemps pour assurer l’évaporation complète des solvants et un durcissement parfait du film de peinture.
- Refroidissement
Une fois la cuisson terminée, les pièces doivent être refroidies lentement à température ambiante ou dans un environnement contrôlé pour éviter les tensions thermiques, les fissures ou les imperfections de la surface. Le refroidissement rapide peut entraîner des déformations du revêtement, alors qu’un refroidissement progressif permet d’obtenir une finition plus stable et résistante.
Types de cuisson de peinture
La cuisson de peinture peut être réalisée de différentes manières selon le type de peinture et les équipements disponibles :
- Cuisson à haute température (fours industriels)
Utilisée pour les peintures en poudre et pour des applications nécessitant un durcissement rapide et efficace, cette méthode implique des fours thermiques capables d’atteindre des températures élevées de l’ordre de 180 à 220°C. Ces fours sont souvent utilisés dans l’industrie automobile, le mobilier métallique, et d’autres secteurs nécessitant une finition durable. - Cuisson à basse température (fours infrarouges ou UV)
Pour des peintures qui ne nécessitent pas de températures aussi élevées, les fours infrarouges ou les systèmes de cuisson à UV sont utilisés. La polymérisation UV est courante dans des applications comme les revêtements décoratifs et certains types de revêtements électroniques. Les lampes UV polymérisent la peinture en un temps très court, ce qui permet une production rapide et efficace. - **Cuisson dans des fours à convection ou fours à circulation d’air
Ces fours utilisent un flux d’air chaud qui circule uniformément autour de la pièce à peindre, assurant ainsi une répartition homogène de la chaleur. Cela est particulièrement important dans des applications où une finishes uniforme est essentielle.
Objectifs et avantages de la cuisson de peinture
La cuisson de peinture permet d’obtenir plusieurs résultats cruciaux pour la performance du revêtement final :
- Durcissement et polymérisation : Pour les peintures en poudre, la cuisson permet aux polymères de se lier, formant un film solide et cohérent.
- Durabilité et résistance : Le durcissement thermique permet d’obtenir une finition qui résiste à l’usure, aux rayures, à la corrosion, et aux agressions chimiques. Cela est particulièrement important pour des secteurs comme l’automobile, où les revêtements doivent supporter des conditions climatiques extrêmes.
- Finition esthétique : La cuisson améliore la brillance, la couleur, et la texture de la peinture, assurant ainsi un aspect lisse et uniforme.
- Réduction de l’impact environnemental : Les peintures sans solvant et les revêtements en poudre sont des solutions plus écologiques, car elles génèrent moins de COV (composés organiques volatils), ce qui permet de réduire l’impact environnemental de la production.
Challenges et innovation
Bien que la cuisson de peinture soit un processus relativement standard dans de nombreuses industries, il existe des défis à surmonter :
- Énergie : La cuisson nécessite des quantités importantes d’énergie, ce qui peut être un facteur coûteux, surtout dans des systèmes de production à grande échelle. Les entreprises cherchent donc à optimiser ce processus à l’aide de nouvelles technologies, comme l’utilisation de fours à haut rendement énergétique ou l’optimisation thermique.
- Contrôle précis de la température : Un contrôle insuffisant de la température de cuisson peut entraîner des défauts de finition, des fissures, ou une mauvaise adhésion. Cela nécessite l’usage de systèmes de contrôle automatisés sophistiqués pour ajuster la température en temps réel.
- Nouveaux matériaux : L’évolution des matériaux de peinture et des substrats nécessite de nouveaux protocoles de cuisson pour garantir une qualité optimale. Par exemple, les revêtements nanotechnologiques ou les peintures thermosensibles nécessitent des ajustements particuliers du processus de cuisson.
Conclusion
La cuisson de peinture est un élément clé dans l’industrie de la finition, permettant d’obtenir des revêtements esthétiques et résistants tout en garantissant des propriétés fonctionnelles sur de nombreuses applications. Le contrôle précis de la température, l’utilisation de technologies avancées pour la cuisson, et l’optimisation des ressources énergétiques sont essentiels pour atteindre une qualité constante et durable dans la production de peintures et de revêtements.
La cuisson de la peinture est un processus vital dans l’industrie des revêtements et de la finition, garantissant non seulement la qualité esthétique du produit final, mais aussi ses caractéristiques de durabilité, de résistance et de performance. L’un des principaux défis réside dans la gestion de la chaleur et la précision de la température, car une variation même minime peut entraîner des défauts de surface ou des performances compromises. Les progrès technologiques dans les équipements de cuisson, tels que les fours à circulation d’air ou les systèmes de polymérisation UV, permettent une optimisation de la cuisson tout en réduisant la consommation d’énergie.
La cuisson des peintures en poudre, en particulier, est une étape cruciale pour garantir que le film de peinture devienne dur et résistant. La chaleur active les résines et autres agents chimiques présents dans la peinture, créant une liaison solide et durable entre la peinture et le substrat. Si la température est trop basse, la peinture peut rester fragile ou incomplètement durcie, tandis que si elle est trop élevée, elle peut entraîner une surcuisson, affectant la brillance ou la texture de la finition. C’est pourquoi les systèmes de cuisson modernes sont équipés de capteurs de température de haute précision et de contrôles automatiques permettant de réguler constamment la température à des niveaux optimaux.
Les technologies de cuisson, telles que les fours à infrarouge ou à convection forcée, sont en constante évolution. Ces systèmes sont capables de chauffer les pièces plus rapidement et plus uniformément, réduisant ainsi le temps de cuisson et l’énergie nécessaire. Cette optimisation énergétique est particulièrement importante dans un contexte industriel où les coûts énergétiques sont un facteur majeur. En outre, les innovations dans la récupération thermique permettent de récupérer la chaleur excédentaire des processus de cuisson pour préchauffer les pièces ou même réduire la consommation d’énergie dans d’autres zones de production.
Une autre tendance croissante est l’utilisation de revêtements à faible température de cuisson, qui permettent de durcir la peinture à des températures plus basses, réduisant ainsi l’impact énergétique et accélérant le cycle de production. Ces technologies sont particulièrement intéressantes dans des industries où des matériaux sensibles à la chaleur sont utilisés, ou pour des applications qui nécessitent un traitement rapide, comme dans la fabrication de produits électroniques ou de pièces automobiles. Ces peintures à basse température sont souvent basées sur des technologies de polymérisation UV ou LED, qui durcissent la peinture en quelques secondes sous l’exposition à des rayonnements spécifiques, permettant des temps de cycle ultra-courts.
Le contrôle de la température de cuisson a également des implications sur la durabilité des produits finis. Une cuisson mal contrôlée peut entraîner des défauts tels que des poches d’air, des cicatrices ou des fissures dans le revêtement, affectant l’adhérence et la longévité du produit final. Les revêtements thermorésistants utilisés dans des applications industrielles sévères, comme les pièces mécaniques ou les équipements exposés à des conditions extrêmes, nécessitent une cuisson particulièrement rigoureuse pour assurer une adhérence parfaite et une résistance accrue à l’usure et à la chaleur.
Dans des environnements industriels où les exigences en termes de finition sont très élevées, comme dans la fabrication de meubles en métal ou de composants automobiles, la consistance et la qualité des finitions doivent être impeccables. Pour cela, les lignes de production sont de plus en plus automatisées avec des systèmes qui contrôlent précisément chaque aspect du processus, de l’application de la peinture à la cuisson. Ces systèmes permettent non seulement d’améliorer la productivité en réduisant les coûts liés aux erreurs de production, mais aussi d’assurer une uniformité parfaite sur de grandes séries de produits.
En conclusion, la cuisson de peinture est un processus complexe mais essentiel pour garantir des revêtements durables, esthétiques et performants. L’évolution des technologies, le contrôle des conditions de cuisson, ainsi que l’intégration de solutions énergétiques durables sont des facteurs clés pour répondre aux besoins croissants des industries modernes tout en respectant les impératifs environnementaux et économiques.
La recherche et l’innovation dans le domaine de la cuisson de peinture continuent de progresser, en particulier avec l’introduction de technologies de cuisson plus écologiques et énergétiquement efficaces. L’un des développements notables est l’intégration de systèmes de cuisson à faible consommation énergétique, qui non seulement réduisent les coûts d’exploitation, mais également contribuent à la réduction de l’empreinte carbone des processus industriels. Les entreprises investissent de plus en plus dans des solutions telles que des fours à haute efficacité thermique et des équipements de récupération de chaleur qui permettent de réutiliser la chaleur excédentaire pour préchauffer les matériaux ou maintenir une température constante dans le four.
Un autre domaine d’innovation majeur est l’utilisation de revêtements à base d’eau ou de technologies sans solvant, qui nécessitent des températures de cuisson plus basses, réduisant ainsi non seulement la consommation d’énergie, mais aussi les émissions de COV (composés organiques volatils). Ces solutions sont particulièrement adaptées aux industries où les réglementations environnementales sont strictes, comme dans la production de mobilier, l’automobile, et l’électronique grand public. En favorisant l’utilisation de produits moins polluants, ces technologies répondent à la demande croissante d’industries soucieuses de leur impact écologique tout en conservant des performances de haute qualité.
Les processus de cuisson avancés sont également influencés par les matériaux composites modernes et les revêtements nanotechnologiques, qui offrent de nouvelles possibilités en matière de résistance mécanique, de propriétés hydrophobes ou de propriétés anti-microbiennes. Ces matériaux nécessitent des protocoles de cuisson spécifiques, souvent avec des températures optimisées pour ne pas altérer leurs propriétés uniques. Les industries de haute technologie, comme l’aéronautique et l’électronique, sont particulièrement en demande de revêtements innovants qui peuvent résister à des conditions extrêmes tout en maintenant des propriétés légères et robustes.
Dans le domaine de la fabrication de pièces automobiles, par exemple, la cuisson est un élément clé de l’application des peintures en poudre qui sont particulièrement résistantes aux intempéries et aux chocs thermiques. Les systèmes de cuisson doivent être capables de traiter des pièces de tailles et de formes variées tout en assurant une finition uniforme et durable. Cela implique des défis supplémentaires en matière de gestion thermique et d’optimisation des processus, qui sont de plus en plus abordés par des technologies de cuisson à contrôle numérique, offrant une précision maximale tout en réduisant le gaspillage énergétique.
En parallèle, la mise en place de systèmes de cuisson intelligents qui intègrent des algorithmes de gestion de la chaleur et des capteurs IoT (Internet of Things) devient une norme dans certaines industries. Ces systèmes sont capables d’ajuster la température en temps réel en fonction des données recueillies sur l’environnement du four, permettant ainsi une réduction des cycles de cuisson, un meilleur contrôle de la qualité du produit final et une minimisation des erreurs humaines. L’utilisation de la data analytics et de l’intelligence artificielle permet également de prédire et d’optimiser les conditions de cuisson en fonction des caractéristiques spécifiques de la peinture et des pièces à traiter.
En outre, la flexibilité des lignes de production devient un autre élément central dans le processus de cuisson de peinture. Les industries modernes ont besoin de flexibilité pour produire une large gamme de produits avec différentes couleurs et types de finitions, tout en maintenant une haute qualité et une efficacité énergétique. Les lignes de cuisson automatisées, capables de traiter des lots de tailles variables et de s’adapter à des demandes spécifiques, sont en forte demande. Ces systèmes permettent de réduire le temps de réinitialisation entre les cycles de production et de réduire les déchets en optimisant les temps de cuisson pour chaque type de produit.
Le rôle de l’automatisation dans la cuisson de peinture ne cesse de croître, avec l’implémentation de robots intelligents qui peuvent non seulement appliquer la peinture de manière uniforme, mais aussi superviser et ajuster les processus de cuisson en temps réel. Ces robots sont équipés de systèmes de vision artificielle pour détecter les défauts ou les irrégularités de la surface pendant la cuisson et peuvent automatiquement ajuster les paramètres de cuisson pour garantir un résultat parfait.
En conclusion, la cuisson de peinture reste un processus crucial, mais elle est en constante évolution grâce à des innovations technologiques qui améliorent non seulement la qualité des produits finis mais aussi l’efficacité énergétique et la réduction de l’impact environnemental. Ces développements permettront aux industries de répondre à la fois aux exigences de durabilité, de performance, et de productivité tout en contribuant à une production plus écologique et plus rentable.
Les avancées dans le domaine de la cuisson de peinture ne se limitent pas seulement aux technologies de contrôle thermique et à l’optimisation énergétique. L’amélioration de la qualité de la finition et la réponse aux besoins de personnalisation sont également des priorités pour de nombreuses industries. L’automatisation avancée, couplée à des algorithmes d’apprentissage machine, permet aujourd’hui de perfectionner chaque aspect du processus de cuisson. Ces innovations permettent d’obtenir des revêtements plus résistants aux chocs, plus flexibles et présentant une brillance uniforme, tout en réduisant les temps de cycle et la consommation de ressources.
Une tendance croissante dans la cuisson des peintures est l’utilisation de technologies de polymérisation UV et de durcissement LED, qui ont transformé la manière dont les revêtements sont durcis. Ces systèmes de polymérisation rapide offrent des temps de cuisson ultra-courts, parfois de l’ordre de quelques secondes, par rapport aux méthodes traditionnelles qui nécessitent plusieurs minutes voire heures de chauffage. Le durcissement UV est particulièrement adapté aux applications où la rapidité de production et la conservation des caractéristiques esthétiques (comme la brillance et la couleur) sont essentielles. Par ailleurs, les systèmes LED sont plus écologiques que les technologies UV traditionnelles car ils consomment moins d’énergie et n’émettent pas de rayons UV nocifs.
Une autre technologie en forte évolution est l’impression 3D associée à des systèmes de peinture et de revêtement automatisés. L’impression 3D permet une précision extrême dans l’application de couches de peinture, ce qui est particulièrement bénéfique pour des composants complexes ou des pièces de petites séries. Une fois les pièces imprimées, des systèmes de cuisson rapides à infrarouge ou par induction peuvent être utilisés pour durcir la peinture, offrant une solution rapide, précise et flexible. Cela est particulièrement utile dans des secteurs comme la fabrication de prototypes ou de produits hautement personnalisés, où la rapidité et la flexibilité sont cruciales.
L’intégration de capteurs intelligents dans les systèmes de cuisson joue également un rôle de plus en plus important. Ces capteurs, placés dans le four, peuvent mesurer de manière continue des paramètres tels que la température, l’humidité, et la vitesse de circulation de l’air, afin de garantir une cuisson optimale des pièces. Les données recueillies par ces capteurs sont envoyées à des systèmes intelligents qui ajustent en temps réel les conditions de cuisson pour maintenir une température uniforme et garantir une finition parfaite. Cela permet de réduire les erreurs humaines, d’améliorer la qualité et de réduire les rebuts dus à une cuisson incorrecte.
De plus, l’industrie explore également des solutions de revêtements intelligents, qui changent de couleur ou de propriétés en fonction des conditions environnementales, telles que la température, l’humidité ou l’exposition aux rayons UV. Ces revêtements réactifs peuvent être utilisés dans des applications de hautement technologiques comme les dispositifs électroniques ou les matériaux de construction intelligents, nécessitant des procédés de cuisson spécifiques pour maintenir leurs caractéristiques. Par exemple, certains revêtements peuvent être conçus pour se durcir automatiquement lorsqu’ils sont exposés à des conditions de chaleur spécifiques dans le four, réduisant ainsi la complexité du processus de cuisson.
Par ailleurs, l’optimisation de la gestion des flux de production joue un rôle clé dans la cuisson des peintures. Les systèmes modernes sont souvent associés à des systèmes ERP (Enterprise Resource Planning) et des logiciels de gestion de la production pour améliorer la planification et le suivi des processus. Cela permet de synchroniser les phases de cuisson avec les autres étapes de la chaîne de production et de garantir un temps de cycle total optimisé. Une gestion intelligente du flux de production permet également d’éviter les goulets d’étranglement et d’améliorer la productivité globale de l’usine.
L’utilisation de revêtements innovants comme les nanostructures et les matériaux auto-cicatrisants devient également une réalité dans certaines applications où la protection des surfaces contre l’usure et les rayures est essentielle. Ces types de revêtements bénéficient d’une cuisson spécifique pour activer les propriétés auto-régénératrices ou pour garantir que les nanoparticules se fixent correctement à la surface du substrat. Ces technologies sont particulièrement populaires dans les secteurs de l’électronique, de l’automobile, et de l’aéronautique, où les exigences de résistance sont particulièrement élevées.
La fabrication d’outils de cuisson sur mesure est aussi un domaine qui bénéficie des progrès de la personnalisation de la production. Par exemple, des fours modulaires peuvent être configurés pour répondre à des besoins de production spécifiques, avec des réglages personnalisés pour les différentes types de peinture ou les pièces à traiter. Ces systèmes modifiables sont souvent plus adaptés à des petites séries ou des productions nécessitant des finitions particulières, offrant ainsi une plus grande flexibilité aux entreprises.
Pour répondre à la demande croissante de production à grande échelle, tout en minimisant les coûts de production, l’automatisation à grande échelle se développe également. Les lignes de production robotisées équipées de systèmes de poussière de peinture électrostatique, de pistolets automatiques et de fours multi-zone permettent de peindre de grandes quantités de pièces tout en garantissant des finitions précises et de haute qualité. Ces systèmes automatisés permettent également de minimiser l’intervention humaine et de maximiser l’efficacité de la production tout en maintenant des coûts de fabrication compétitifs.
En conclusion, la cuisson de peinture continue de jouer un rôle essentiel dans l’optimisation des processus de fabrication. L’intégration de technologies telles que les systèmes de cuisson intelligents, la polymérisation rapide, l’impression 3D, et les revêtements intelligents transforme cette étape de production, rendant les procédés plus écologiques, efficaces, et adaptés aux besoins variés des industries modernes. Ces innovations permettent de répondre aux exigences de qualité, de durabilité et de personnalisation tout en optimisant la productivité et en réduisant les coûts de production.
Application électrostatique
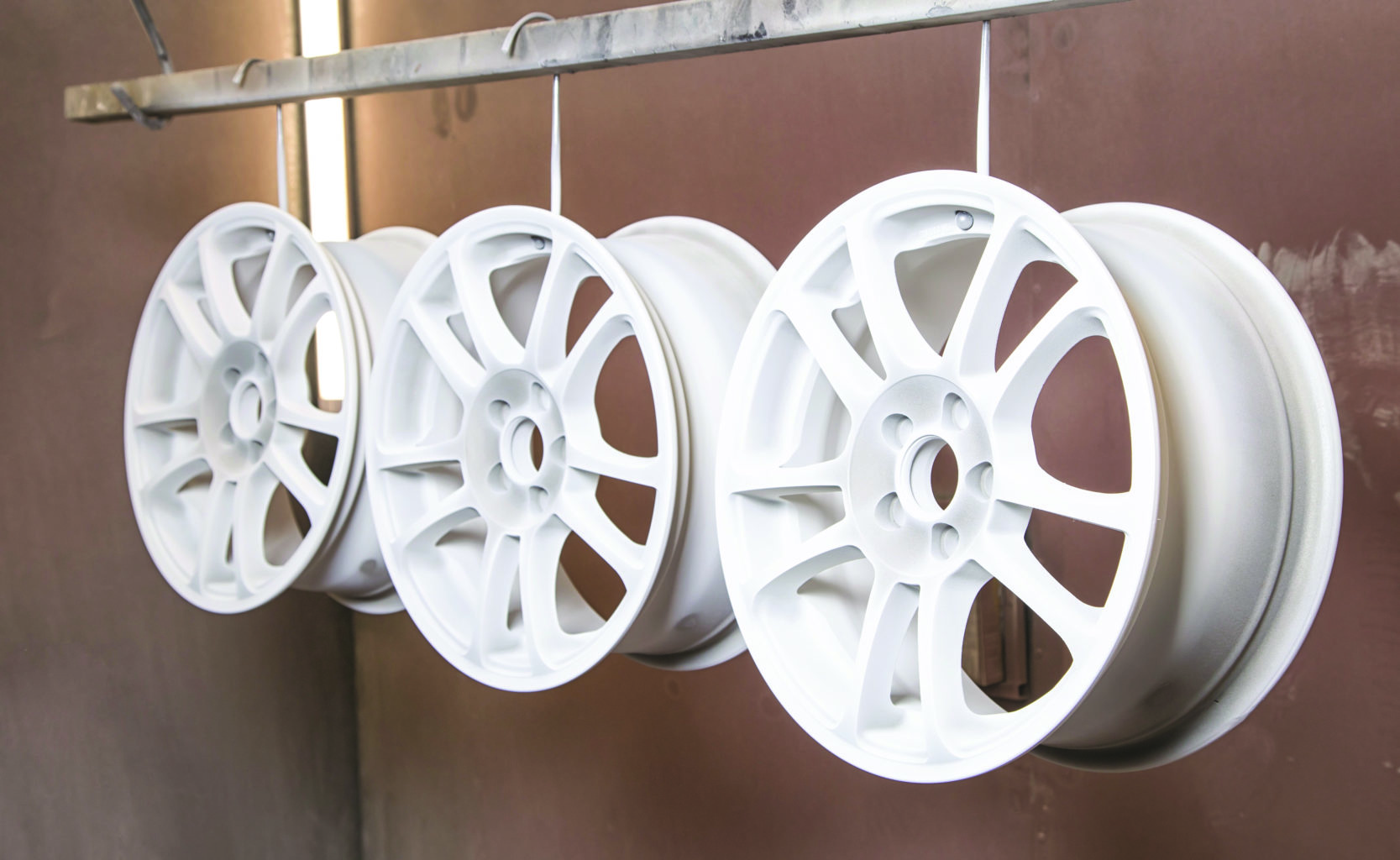
L’application électrostatique est une technique largement utilisée dans le domaine du revêtement en poudre et dans d’autres applications industrielles pour appliquer des matériaux comme des peintures, des adhésifs ou des poudres métalliques sur des surfaces. Ce procédé repose sur l’utilisation de forces électrostatiques pour attirer et fixer des particules de matière (souvent de la peinture en poudre) sur des objets métalliques ou d’autres types de substrats. C’est une méthode particulièrement populaire dans la peinture en poudre en raison de son efficacité et de sa capacité à produire une finition uniforme et durable.
Principe de fonctionnement
Le principe de l’application électrostatique repose sur la charge électrique. Les particules de peinture sont chargées électriquement (souvent négativement), tandis que le substrat à recouvrir (tel qu’une pièce métallique) est généralement mis à la terre ou chargé positivement. Cette différence de charge crée une force d’attraction entre les particules de peinture et la surface du substrat, ce qui permet à la peinture de s’accrocher efficacement et uniformément, même sur des surfaces complexes ou difficiles d’accès.
Le processus commence par la pulvérisation de la peinture en poudre à travers un pistolet électrostatique. Ce pistolet électrostatique applique une charge électrique à la poudre qui est alors projetée sur la pièce à recouvrir. Le substrat, souvent mis à la terre ou chargé positivement, attire les particules chargées négativement, permettant à la peinture de se fixer solidement à la surface. Une fois que la surface est uniformément recouverte, la pièce est passée à travers un four de polymérisation où la peinture est durcie à une température spécifique.
Avantages de l’application électrostatique
- Uniformité de la couverture : L’application électrostatique permet d’obtenir une couverture uniforme même sur des surfaces complexes ou difficiles d’accès, telles que des pièces avec des coins, des bords et des courbes. La capacité de la peinture à se fixer sur les surfaces de manière homogène sans coulures ni zones non couvertes est un des grands avantages de ce procédé.
- Efficacité de transfert : L’application électrostatique est plus efficace que d’autres méthodes de pulvérisation, comme la pulvérisation à air comprimé, car la charge électrostatique attire les particules de peinture vers la surface cible, réduisant ainsi la quantité de peinture perdue dans l’air. Cela permet de réaliser des économies de peinture et de réduire les émissions de solvants, ce qui est bénéfique pour l’environnement.
- Réduction des déchets : En raison de l’efficacité du processus, moins de peinture est gaspillée. La plupart des poudres non utilisées peuvent être récupérées et recyclées, ce qui permet d’optimiser les coûts de production et de réduire l’impact environnemental.
- Finitions de haute qualité : L’application électrostatique crée une finition lisse, uniforme et sans défauts. De plus, la peinture en poudre, une fois durcie, offre une surface résistante aux rayures, aux produits chimiques et aux conditions météorologiques.
- Adaptabilité : Cette technique peut être utilisée pour une grande variété de matériaux, notamment les métaux, les plastiques et les surfaces complexes. Les industries qui bénéficient de cette technologie incluent l’automobile, la construction, l’électroménager, et bien d’autres.
- Écologique : En éliminant ou réduisant l’usage de solvants, l’application électrostatique est plus respectueuse de l’environnement par rapport à d’autres procédés de peinture. De plus, les émissions de composés organiques volatils (COV) sont minimisées.
Applications de l’application électrostatique
- Peinture en poudre pour métaux : L’application électrostatique est couramment utilisée pour la peinture en poudre des pièces métalliques dans l’industrie automobile, l’électroménager, le mobilier, et l’architecture. La peinture en poudre offre une finition durable, résistante aux intempéries et à l’usure.
- Revêtements de matériaux plastiques : En plus des métaux, l’application électrostatique est également utilisée pour appliquer des revêtements sur des matériaux plastiques, offrant une finition esthétique et résistante.
- Industrie électronique : L’application électrostatique est utilisée pour appliquer des revêtements conducteurs ou isolants sur des composants électroniques, des boîtiers et des circuits imprimés, où une couverture uniforme et précise est cruciale.
- Applications décoratives : Les finitions de haute qualité obtenues grâce à l’application électrostatique sont très appréciées dans des domaines comme la décoration d’intérieur, les objets en métal et les composants de design extérieur.
- Protection contre la corrosion : L’application électrostatique est également utilisée pour appliquer des revêtements de protection sur des surfaces métalliques afin de les protéger contre la corrosion, particulièrement dans des environnements marins ou industriels.
Conclusion
L’application électrostatique est une technologie clé dans de nombreux secteurs industriels pour l’application de peintures et de revêtements. Elle offre une efficacité de transfert exceptionnelle, une uniformité de couverture, et des avantages environnementaux significatifs, tout en garantissant des finitions de haute qualité. Grâce à ses capacités de réduction des déchets et de recyclage des peintures, elle s’avère être une méthode efficace et durable pour répondre aux besoins de production modernes.
L’application électrostatique joue également un rôle essentiel dans la réduction des coûts opérationnels. En optimisant l’utilisation de la peinture et en minimisant les pertes de matériau, les entreprises peuvent réaliser des économies importantes, tout en respectant des normes environnementales de plus en plus strictes. Cette efficacité se traduit par une réduction significative des coûts de production et une amélioration de la rentabilité globale des processus de peinture. Les systèmes de récupération de peinture, souvent intégrés aux installations électrostatiques, permettent de recueillir la poudre excédentaire, de la filtrer, et de la réutiliser dans les applications suivantes, ce qui renforce encore l’aspect économique et écologique du procédé.
De plus, les technologies numériques intégrées aux équipements de pulvérisation électrostatique ont considérablement amélioré la gestion et le contrôle du processus. Les systèmes automatisés permettent une surveillance en temps réel de paramètres clés comme la vitesse de pulvérisation, la charge électrique appliquée, et la répartition uniforme de la peinture. Ces innovations permettent non seulement d’améliorer la consistance des résultats mais aussi d’adapter les paramètres en fonction des exigences spécifiques de chaque pièce à traiter. Ces systèmes peuvent aussi détecter les anomalies dans l’application et ajuster automatiquement les paramètres pour éviter tout défaut de finition.
Les équipements électrostatiques modernes sont aussi conçus pour être plus flexibles et adaptables à des lignes de production de plus en plus variées. Ils sont capables de traiter une large gamme de matériaux et de configurations géométriques, ce qui permet aux fabricants de répondre à des besoins spécifiques, tout en garantissant des résultats de qualité. Par exemple, les robots de peinture automatisés équipés de pistolets électrostatiques peuvent pulvériser la peinture en poudre de manière précise sur des objets de formes irrégulières ou complexes, garantissant une couverture complète et une finition sans défaut.
Le contrôle de la charge électrostatique est un facteur crucial dans l’application électrostatique. Un contrôle précis de la charge permet d’optimiser l’adhésion de la peinture, en évitant les zones sous-appliquées ou sur-appliquées. Un autre avantage notable est la réduction de la pollution par des poussières de peinture, grâce à l’électrostatique, qui assure que la majeure partie de la peinture atteigne directement la surface à revêtir. Cela minimise les risques de contamination de l’environnement de travail et assure une production plus propre.
En outre, l’application électrostatique présente des avantages en termes de sécurité. L’élimination ou la réduction des solvants dans la peinture en poudre réduit les risques liés à l’inhalation de vapeurs toxiques et à l’exposition à des substances chimiques dangereuses. Cela rend l’atelier de peinture plus sûr pour les travailleurs tout en réduisant l’impact des émissions dans l’atmosphère. De plus, l’absence de solvants contribue également à réduire les risques d’inflammabilité dans les installations de production, rendant les processus moins vulnérables à des accidents industriels.
À long terme, l’application électrostatique permet également de réduire l’empreinte carbone des processus de peinture. En diminuant la quantité de peinture gaspillée, en optimisant la consommation d’énergie des équipements de cuisson, et en utilisant des matériaux respectueux de l’environnement, l’industrie peut s’engager vers des pratiques plus durables et alignées avec les objectifs mondiaux de réduction des émissions de gaz à effet de serre. L’utilisation de peintures sans solvant, par exemple, qui se durcissent sous l’effet de la chaleur, diminue non seulement la pollution de l’air mais aussi l’impact écologique de la fabrication des peintures elles-mêmes.
Dans des secteurs comme l’automobile, la construction et l’électronique, où la durabilité et la qualité des revêtements sont cruciales, l’application électrostatique répond aux exigences de performance tout en permettant une production de masse efficace et économiquement viable. Par exemple, dans l’automobile, où les revêtements doivent être résistants aux conditions climatiques extrêmes et aux rayures, cette méthode garantit que chaque pièce reçoit une couche de peinture uniforme et durable, avec une finition qui améliore la résistance à la corrosion et à l’usure.
Enfin, l’évolution continue de l’application électrostatique avec l’intégration de nouvelles technologies telles que l’intelligence artificielle pour l’optimisation des paramètres de pulvérisation et des systèmes de feedback automatique permet d’affiner encore la qualité et l’efficacité du procédé. Ces outils de gestion intelligents, couplés à des systèmes de capteurs avancés, sont capables de suivre en temps réel l’état de chaque pièce et d’adapter le processus pour maximiser l’efficacité énergétique, réduire les déchets et garantir des résultats parfaits, tout en respectant les normes environnementales les plus strictes.
En somme, l’application électrostatique continue de se diversifier et de se perfectionner, devenant un outil incontournable pour répondre aux défis de qualité, de productivité, de sécurité et d’écologie dans les processus industriels. L’adoption croissante de cette technologie dans de nombreux secteurs témoigne de son efficacité à long terme, de sa rentabilité et de son impact positif sur l’environnement.
L’application électrostatique s’adapte également aux exigences croissantes de personnalisation des produits. Dans des industries comme la mode, l’automobile et l’électronique, où la personnalisation des finitions est devenue essentielle, cette technique permet une grande flexibilité. Les utilisateurs peuvent varier les couleurs, textures et effets de surface tout en maintenant une production de masse efficace. Par exemple, les entreprises du secteur automobile peuvent offrir des options de finition hautement personnalisées pour des modèles spécifiques ou des séries limitées sans compromettre la productivité. De même, dans le secteur de l’électronique, des revêtements fonctionnels comme les couches conductrices ou isolantes peuvent être appliqués de manière précise et cohérente à une large gamme de composants.
Un autre domaine où l’application électrostatique fait une grande différence est celui de la recyclabilité. Les technologies de revêtement en poudre permettent de récupérer et de réutiliser les poudres excédentaires. Cela non seulement réduit la quantité de déchets générés, mais contribue également à la durabilité du processus global. Ce recyclage des poudres de peinture non utilisées dans un cycle de production successive assure que les matériaux sont employés de manière plus efficace, réduisant les coûts de production et les impacts environnementaux associés aux déchets industriels.
L’intégration de l’application électrostatique dans des lignes de production intelligentes est une autre évolution importante. De nos jours, de nombreuses usines de peinture sont dotées de systèmes numériques avancés, qui peuvent surveiller, ajuster et optimiser en continu les paramètres de l’application. L’utilisation de capteurs IoT (Internet des objets) et de systèmes de contrôle automatisés permet une gestion proactive des équipements et des matériaux, en identifiant les problèmes avant qu’ils n’affectent la production. Cela assure non seulement un meilleur contrôle de la qualité, mais permet également une maintenance prédictive, réduisant ainsi les temps d’arrêt des équipements et prolongeant leur durée de vie.
L’utilisation des robots de peinture équipés de pistolets électrostatiques devient également plus répandue dans des secteurs où la précision et la vitesse sont des priorités. Ces robots peuvent exécuter des tâches de pulvérisation complexes avec une grande précision et répétabilité, ce qui améliore non seulement la qualité de la finition mais aussi la sécurité des travailleurs, qui sont moins exposés à des environnements potentiellement dangereux. Ces systèmes robotiques peuvent également ajuster leurs mouvements et paramètres en fonction des caractéristiques des pièces à peindre, garantissant une application homogène même sur des objets de forme irrégulière ou de grande taille.
Dans des industries où les conditions extrêmes sont courantes, telles que le secteur aéronautique ou la construction navale, l’application électrostatique est utilisée pour appliquer des revêtements résistants qui protègent contre les intempéries, la chaleur, et l’usure mécanique. Ces applications nécessitent des solutions de peinture robustes et durables, qui bénéficient de l’efficacité de la méthode électrostatique pour garantir une adhésion parfaite à la surface, même dans des conditions de traitement extrêmes.
Le développement de revêtements écologiques est également un axe majeur dans l’évolution de l’application électrostatique. Les réglementations environnementales plus strictes ont poussé de nombreuses entreprises à chercher des alternatives aux peintures à base de solvants. Les peintures en poudre et les revêtements sans solvant sont désormais largement utilisés grâce à leur faible teneur en composés organiques volatils (COV), ce qui permet de respecter les normes environnementales tout en offrant une finition de haute qualité. En outre, l’optimisation de la cuisson dans des fours à faible consommation d’énergie permet de réduire davantage l’empreinte carbone des processus de peinture.
Les systèmes électrostatiques modernes sont désormais équipés de dispositifs de contrôle et de surveillance intelligents, permettant une gestion efficace des différents paramètres du processus. Des systèmes de rétroaction automatique ajustent la pulvérisation en fonction des conditions en temps réel, comme la température, l’humidité et l’état de la surface, pour garantir une qualité optimale. De plus, la possibilité d’enregistrer et d’analyser les données de production permet d’identifier rapidement toute anomalie et d’appliquer des corrections immédiates, améliorant ainsi la performance et la constance du processus de peinture.
Dans l’ensemble, l’application électrostatique continue d’évoluer grâce à l’innovation technologique, l’intégration de systèmes de contrôle avancés, et la recherche de solutions durables et écologiques. Cette technologie, en constante amélioration, représente un atout majeur pour de nombreuses industries, offrant à la fois des avantages économiques, environnementaux et de qualité, tout en répondant aux exigences croissantes de personnalisation, de sécurité et de flexibilité. Le futur de l’application électrostatique est intrinsèquement lié à ces évolutions, offrant des opportunités d’optimisation dans la production et la finition des produits.
L’avenir de l’application électrostatique semble très prometteur grâce à l’évolution continue des technologies de pulvérisation et des matériaux. En plus des innovations dans les systèmes robotiques et les capteurs intelligents, on peut s’attendre à ce que de nouvelles avancées technologiques permettent de rendre l’application électrostatique encore plus précise, rapide et durable. Ces améliorations ouvriront la voie à des applications encore plus diversifiées et des secteurs industriels élargis.
L’un des développements les plus intéressants réside dans l’intégration de l’intelligence artificielle (IA) et de l’apprentissage machine pour affiner les processus de peinture. Les algorithmes d’IA pourraient analyser en temps réel les conditions de l’environnement de production, comme la température, l’humidité, et même les caractéristiques de la pièce à recouvrir, pour ajuster automatiquement les paramètres de pulvérisation. L’apprentissage machine pourrait également être utilisé pour prédire les ajustements nécessaires dans les équipements en fonction des tendances observées sur plusieurs cycles de production. Ces technologies permettront de réduire les erreurs humaines, d’optimiser l’utilisation des matériaux, et d’assurer une qualité constante tout au long du processus de production.
Le développement de nouveaux matériaux de revêtement pourrait également transformer l’application électrostatique. Par exemple, la recherche sur les peintures et revêtements écologiques, comme les peintures à base d’eau ou les systèmes à faible teneur en COV, permettrait d’améliorer encore l’impact environnemental du processus. Les matériaux de revêtement de haute performance, offrant une résistance accrue aux agressions extérieures, comme la corrosion, l’humidité, et l’abrasion, seraient très recherchés, en particulier dans des secteurs comme l’aéronautique, l’automobile, et la construction. Les revêtements fonctionnels, tels que les revêtements anti-bactériens ou anti-pollution, pourraient également devenir courants grâce à l’application électrostatique, ouvrant de nouvelles opportunités dans des industries sensibles à la santé publique, comme les hôpitaux, les transports et les espaces publics.
Les systèmes de peinture en poudre continueront d’être optimisés pour offrir une plus grande économie d’énergie et des cycles de cuisson plus courts dans des fours à basse consommation énergétique. L’optimisation des processus de durcissement grâce à des technologies avancées de réglage thermique pourrait également contribuer à réduire la consommation d’énergie, tout en maintenant des standards de performance et de qualité élevés pour les revêtements.
Une autre tendance qui se profile à l’horizon est l’adoption plus large de l’automatisation et des lignes de production flexibles dans l’industrie. Les systèmes robotisés de peinture continueront à se perfectionner, rendant les lignes de production encore plus autonomes, flexibles et adaptables. Les robots actuels pourront évoluer pour travailler de manière plus fluide avec des pièces de formes très complexes, tout en ajustant leurs paramètres en temps réel en fonction des caractéristiques de chaque pièce. La flexibilité dans la production, grâce à l’intégration de robots collaboratifs (cobots), permettra de réduire les coûts et d’augmenter la cadence de production sans compromettre la qualité.
Le suivi en temps réel et la maintenance prédictive via des plateformes connectées permettront une gestion optimale des ressources. L’intégration de l’Internet des objets (IoT) dans les équipements de peinture permettra de recueillir et d’analyser des données de production sur une échelle globale. Ces données fourniront des informations essentielles pour améliorer la gestion des stocks de peinture, la gestion de l’énergie, et la réduction des déchets industriels, contribuant ainsi à une production encore plus durable.
Enfin, l’adoption de solutions de récupération améliorées pour les poudres excédentaires sera un autre domaine clé. À mesure que l’industrie devient plus soucieuse de l’environnement, des technologies plus efficaces pour la récupération et le recyclage de la poudre de peinture non utilisée seront développées. Ces technologies permettront de réutiliser presque 100 % de la poudre excédentaire, rendant ainsi les systèmes de pulvérisation électrostatique encore plus écologiques et économiquement rentables.
Ainsi, les perspectives pour l’application électrostatique sont très favorables, avec des innovations constantes dans le domaine de la robotique, de l’intelligence artificielle, des matériaux et des procédés énergétiques. Les industries qui adoptent ces avancées technologiques seront en mesure de répondre de manière plus agile aux défis économiques et environnementaux du futur, tout en offrant des produits de qualité supérieure à des prix compétitifs. En conséquence, l’application électrostatique continue de s’affirmer comme un élément clé dans la quête d’une industrie plus intelligente, plus écologique et plus performante.
Four de cuisson peinture poudre
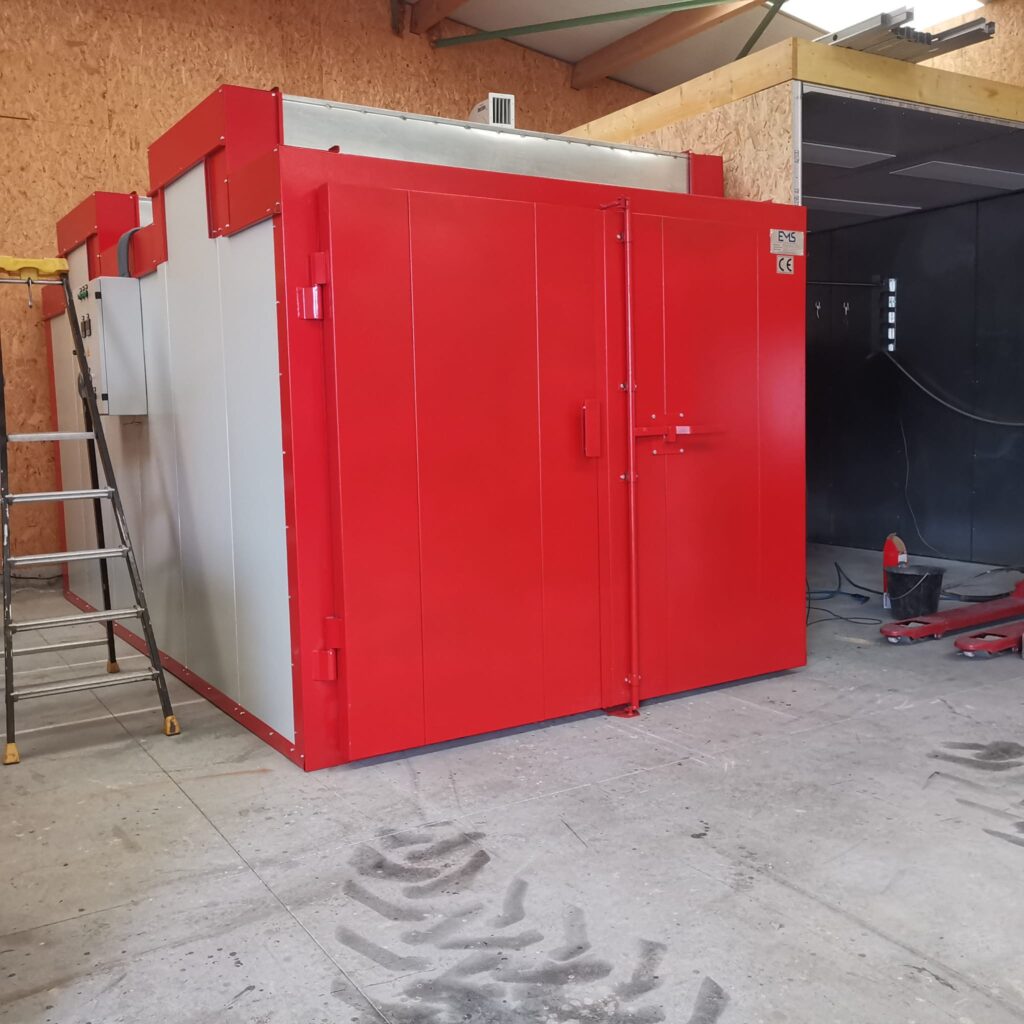
Un four de cuisson pour peinture en poudre est un équipement essentiel dans le processus de revêtement en poudre. Il permet de durcir la peinture en poudre après qu’elle ait été appliquée sur une surface. La cuisson dans le four permet à la peinture en poudre, généralement à base de résines thermodurcissables, de fondre, de s’étaler uniformément et de se lier chimiquement à la surface, créant ainsi une finition robuste et durable. Voici un aperçu des principaux types de fours de cuisson pour peinture en poudre et leurs caractéristiques :
Types de Fours de Cuisson pour Peinture en Poudre
- Fours à convection (air chaud) : Ces fours utilisent un ventilateur pour circuler l’air chaud à travers la cabine de cuisson, ce qui assure une distribution uniforme de la chaleur. Ils sont les plus couramment utilisés dans les installations de peinture en poudre. Les fours à convection sont adaptés aux productions de petites à moyennes séries et offrent un bon contrôle de la température. Cependant, leur capacité à chauffer rapidement peut être limitée par la circulation d’air.
- Fours à infrarouge (IR) : Ces fours utilisent des radiations infrarouges pour chauffer directement la surface des pièces, plutôt que de chauffer l’air autour d’elles. Cette méthode permet de réduire le temps de cuisson, car la chaleur est appliquée directement sur la couche de peinture. Les fours à infrarouge sont souvent utilisés pour des pièces plus petites et pour des productions à haute cadence. Ils offrent une chauffe plus rapide et sont généralement plus énergétiquement efficaces que les fours à convection.
- Fours mixtes (convection + infrarouge) : Ces fours combinent les deux technologies, en utilisant à la fois l’air chaud et les radiations infrarouges pour optimiser la cuisson. L’air chaud assure une distribution uniforme de la chaleur, tandis que les radiations infrarouges permettent de réduire les temps de cuisson en chauffant plus rapidement la surface des pièces.
- Fours à bande transporteuse (ou à tunnel) : Les fours à bande transporteuse sont idéaux pour les lignes de production automatisées et à grande échelle. Les pièces sont déplacées à travers le four sur une bande transporteuse, ce qui permet un processus de cuisson continu et automatisé. Ces systèmes sont particulièrement efficaces pour les productions en série où un contrôle précis de la température et une efficacité énergétique sont cruciaux.
- Fours à circulation forcée d’air : Ces fours sont équipés de ventilateurs puissants qui assurent une circulation rapide de l’air chaud, ce qui permet de chauffer rapidement les pièces. Ils sont souvent utilisés pour les grandes séries de production. Ce type de four est particulièrement adapté pour des matériaux de plus grande taille, nécessitant une répartition uniforme de la chaleur.
Paramètres de Cuisson
La température de cuisson et la durée de cuisson sont deux facteurs cruciaux pour garantir une finition de peinture de qualité. En général, la cuisson de la peinture en poudre se fait à une température d’environ 180-200°C (356-392°F) pendant 10 à 20 minutes, selon le type de poudre et l’épaisseur du revêtement. La peinture en poudre doit être chauffée suffisamment pour que les particules fondent et s’assemblent en une couche uniforme et solide, mais pas trop longtemps pour éviter de la brûler.
- Température idéale de cuisson : 180 à 200°C.
- Durée de cuisson : Environ 10 à 20 minutes.
- Objectif : Assurer la polymérisation complète de la peinture pour une finition résistante.
Avantages des Fours de Cuisson pour Peinture en Poudre
- Durabilité de la finition : La cuisson permet de créer un revêtement dur et résistant aux rayures, à la corrosion, et aux produits chimiques, ce qui est essentiel dans des secteurs tels que l’automobile, l’électroménager, et la construction.
- Finition uniforme : Les fours de cuisson permettent de chauffer les pièces de manière homogène, assurant une application uniforme de la peinture, sans effets indésirables tels que des coulures ou des zones non couvertes.
- Économie d’énergie : Les fours modernes sont souvent équipés de systèmes écoénergétiques et de technologies de récupération de chaleur qui permettent de réduire les coûts énergétiques tout en maintenant des performances optimales.
- Environnement plus propre : En éliminant l’utilisation de solvants, la cuisson dans des fours à peinture en poudre contribue à réduire les émissions de COV (composés organiques volatils), ce qui rend le processus de peinture plus respectueux de l’environnement.
- Réduction des temps de cycle de production : Les fours à infrarouge et les fours à convection améliorés permettent de raccourcir les temps de cuisson tout en garantissant des résultats de haute qualité, augmentant ainsi la productivité.
Entretien des Fours de Cuisson
Le bon entretien du four est crucial pour garantir une performance optimale et prolonger sa durée de vie. Cela inclut des vérifications régulières de l’isolation thermique, du système de ventilation, des éléments chauffants et de l’équipement de contrôle de température. Le nettoyage des filtre à air et des éléments chauffants est également essentiel pour maintenir une efficacité énergétique maximale et éviter l’accumulation de poussière de peinture qui pourrait interférer avec la circulation de l’air chaud.
Conclusion
Le four de cuisson pour peinture en poudre est un élément clé dans la réussite du procédé de peinture en poudre. Son choix dépend des besoins spécifiques de production, des types de matériaux à traiter et de la quantité d’articles à traiter. Avec les avancées technologiques, ces équipements deviennent de plus en plus écoénergétiques, rapides et performants, ce qui permet aux industries d’offrir des finitions de haute qualité tout en respectant des normes environnementales strictes.
Les fours de cuisson pour peinture en poudre jouent un rôle crucial dans la création de finitions de haute qualité. Leur fonction principale est de durcir la peinture en poudre après qu’elle ait été appliquée sur les surfaces, assurant ainsi une finition durable, résistante aux éraflures, à la corrosion, et aux conditions climatiques difficiles. Les évolutions récentes dans la technologie des fours ont permis de réduire les temps de cuisson tout en optimisant l’efficacité énergétique, ce qui est essentiel pour une production industrielle rentable et respectueuse de l’environnement.
L’utilisation de fours à convection, fours à infrarouge ou fours mixtes permet aux entreprises d’adapter le processus de cuisson en fonction de la taille des pièces, des types de peintures utilisées, et des exigences spécifiques du produit final. L’une des grandes innovations dans ce domaine est l’optimisation des temps de cuisson, qui sont désormais plus courts grâce à des systèmes de chauffage plus efficaces et des méthodes telles que l’infrarouge pour une chauffe rapide et directe des surfaces. Ce gain de temps améliore la cadence de production et réduit les coûts opérationnels. En parallèle, l’intégration de technologies intelligentes permet un contrôle précis de la température et de l’humidité dans les fours, assurant une uniformité parfaite dans le processus de durcissement de la peinture. Ces technologies de surveillance permettent également d’éviter les erreurs humaines et de maintenir une qualité constante sur toutes les pièces traitées.
Les fours à bande transporteuse et fours à tunnel permettent de traiter des lots importants de pièces en continu, ce qui est idéal pour les lignes de production automatisées. Ces systèmes sont conçus pour être flexibles et capables de s’adapter à différents types de pièces, même celles de grande taille ou de forme complexe, sans sacrifier la qualité de la finition. En outre, les fours modernes intègrent des systèmes de recirculation de chaleur, réduisant ainsi la consommation d’énergie en réutilisant la chaleur générée pendant le processus de cuisson. Cela permet non seulement de rendre le processus plus écologique, mais aussi de réaliser des économies substantielles en réduisant la consommation d’énergie.
Un autre aspect à ne pas négliger est l’impact environnemental des fours de cuisson. En éliminant l’utilisation de solvants et en minimisant la libération de composés organiques volatils (COV), les fours à peinture en poudre contribuent à rendre le processus de peinture plus respectueux de l’environnement. De plus, l’optimisation du recouvrement des poudres excédentaires et leur recyclage dans un cycle de production continu permet de réduire les déchets et d’améliorer encore la durabilité du processus. Les entreprises peuvent ainsi non seulement respecter des normes écologiques strictes, mais aussi réduire les coûts liés à l’achat de matériaux de peinture et au traitement des déchets.
Les fours de cuisson sont également conçus pour être faciles à entretenir et à ajuster en fonction des besoins spécifiques de chaque production. Les éléments chauffants et les systèmes de ventilation peuvent être réglés pour assurer une répartition homogène de la chaleur, et des capteurs de température permettent de garantir que chaque pièce bénéficie d’un traitement thermique optimal. L’entretien régulier du four est essentiel pour garantir une performance constante et éviter les pannes qui pourraient entraîner des arrêts de production coûteux.
L’avenir des fours de cuisson semble prometteur avec l’émergence de nouvelles technologies telles que l’intelligence artificielle et l’Internet des objets (IoT). Ces avancées pourraient permettre une maintenance prédictive, où les systèmes intelligents surveillent en temps réel les performances du four et prévoient les réparations avant que des problèmes ne surviennent. L’utilisation de l’IA pourrait également optimiser les paramètres de cuisson en fonction des données collectées sur la performance de chaque lot de peinture, garantissant ainsi une qualité de finition optimale pour chaque pièce.
En résumé, les fours de cuisson pour peinture en poudre sont au cœur de l’efficacité de tout processus de revêtement en poudre. Leur évolution vers des systèmes plus écologiques, énergétiquement efficaces, et technologiquement avancés ouvre de nouvelles possibilités pour une production plus rapide, plus flexible, et plus durable. Avec les améliorations constantes en matière de contrôle de la qualité, de réduction de la consommation énergétique, et d’optimisation des temps de production, les fours de cuisson continueront de jouer un rôle clé dans les industries de peinture, garantissant des finitions de haute qualité tout en respectant les normes environnementales et économiques du futur.
L’optimisation continue des fours de cuisson pour peinture en poudre se concentre également sur la réduction de l’empreinte carbone. Les technologies émergentes telles que les fours à basse consommation d’énergie et les systèmes de récupération thermique permettent de minimiser l’utilisation d’énergie tout en maintenant des performances de cuisson élevées. Ces innovations, combinées à une gestion intelligente de la chaleur, permettent aux entreprises de réduire leur consommation énergétique et d’améliorer leur rentabilité tout en respectant des objectifs environnementaux de plus en plus stricts.
De plus, la connectivité est un élément clé de l’avenir des fours de cuisson. L’intégration de technologies IoT permet un suivi en temps réel des paramètres critiques de production, comme la température et le flux d’air, ce qui permet de détecter rapidement toute anomalie et d’intervenir immédiatement. L’analyse des données collectées au sein du système peut également offrir des informations précieuses pour la maintenance prédictive, réduisant ainsi le temps d’arrêt non planifié et augmentant la durée de vie des équipements. Cela peut permettre aux usines de fonctionner de manière plus fluide, avec moins d’interruptions et une meilleure productivité.
L’évolution des systèmes automatisés de gestion de la peinture en poudre joue également un rôle dans la réduction des erreurs humaines et l’amélioration de la consistance des finitions. Des logiciels spécialisés permettent de programmer et de surveiller chaque aspect de la cuisson, garantissant que la température, la durée et les autres paramètres sont maintenus constants pour chaque lot. Cela garantit une qualité uniforme de la peinture, ce qui est particulièrement crucial dans les secteurs où la perfection du revêtement est essentielle, comme dans l’aérospatiale ou l’automobile.
Un autre domaine d’innovation est l’adoption croissante des fours modulaires, qui permettent de configurer le processus de cuisson en fonction des besoins spécifiques de chaque production. Ces systèmes permettent une flexibilité maximale, car les utilisateurs peuvent ajuster la taille et la capacité du four en fonction des volumes de production, sans avoir à investir dans de nouveaux équipements coûteux. De plus, les fours modulaires peuvent être facilement adaptés pour traiter différents types de pièces, qu’elles soient petites, grandes ou de formes irrégulières, ce qui les rend très populaires dans les lignes de production diversifiées.
En parallèle, des matériaux de peinture innovants continuent de stimuler le développement des fours de cuisson. Les nouveaux types de peintures thermodurcissables et les formulations de poudres permettent une cuisson à des températures plus basses, ce qui réduit la consommation d’énergie et peut étendre la gamme de matériaux qui peuvent être traités avec ces technologies. Les innovations dans les peintures à base d’eau ou les revêtements sans solvant permettent de réduire l’impact environnemental de la cuisson, tout en maintenant une finition de haute qualité.
Les fours de cuisson à haute capacité sont également de plus en plus utilisés dans les industries nécessitant des lignes de production à grande échelle. Ces fours sont capables de traiter des volumes de production plus élevés, ce qui est essentiel pour les entreprises qui doivent répondre à une demande accrue. Les systèmes de transport automatique, comme les bandes transporteuses, assurent un mouvement fluide des pièces à travers le four, permettant une cuisson uniforme et un contrôle précis du temps de traitement pour chaque lot.
Les fours de cuisson de dernière génération sont non seulement plus efficaces sur le plan énergétique, mais ils offrent également des solutions de contrôle de l’environnement optimisées. L’intégration de systèmes de filtration d’air et de purification des gaz permet de traiter les émanations et de maintenir une qualité d’air optimale dans les ateliers de peinture. Cela contribue à la santé des travailleurs tout en garantissant que les normes de sécurité et de qualité de l’air sont respectées.
En somme, les fours de cuisson pour peinture en poudre continueront d’évoluer avec une forte orientation vers la durabilité, la flexibilité, et l’efficacité énergétique. À mesure que les technologies avancent, il est probable que les industriels adoptront des solutions encore plus innovantes, intégrant des éléments tels que l’automatisation, l’intelligence artificielle, et l’optimisation des ressources, créant ainsi des processus de production de peinture encore plus efficaces, moins coûteux et respectueux de l’environnement.
Avec la montée en puissance des technologies vertes et de la responsabilité sociétale des entreprises (RSE), l’évolution des fours de cuisson pour peinture en poudre va sans doute inclure une intégration encore plus poussée des pratiques durables. Les fabricants de ces équipements travaillent non seulement sur des innovations techniques mais aussi sur des solutions permettant de réduire leur impact environnemental. Par exemple, les fours à convection modernes utilisent des systèmes de récupération de chaleur et des panneaux solaires pour préchauffer l’air, ce qui contribue à une réduction significative de la consommation d’énergie tout en maintenant une production efficace.
Les matériaux recyclés et durables deviennent de plus en plus une priorité pour l’industrie du revêtement en poudre, et les fours sont conçus pour s’adapter à ces changements. Par exemple, les entreprises cherchent des alternatives aux résines traditionnelles, utilisant de plus en plus de peintures à base de ressources renouvelables, ce qui pourrait influencer la conception et les paramètres de cuisson des fours pour s’adapter à ces nouvelles formulations. Le recyclage des poudres excédentaires est également un aspect clé, non seulement pour des raisons écologiques mais aussi économiques, car cela permet de réutiliser une grande partie du matériel non utilisé, réduisant ainsi les coûts de production.
Les fours de cuisson pour peinture en poudre sont également de plus en plus équipés de systèmes intelligents permettant de gérer l’ensemble du processus de production via des interfaces numériques et des plateformes de cloud computing. Ces technologies offrent des analyses en temps réel sur la performance des équipements, permettant de détecter les anomalies avant qu’elles ne deviennent des problèmes majeurs. Par exemple, grâce à la collecte de données sur la température et l’humidité, il est possible de modifier instantanément les paramètres pour optimiser le processus sans compromettre la qualité du revêtement. Cela réduit également les coûts liés à l’entretien non planifié, augmentant ainsi la rentabilité des installations industrielles.
Les systèmes de vision par caméra et les capteurs intelligents jouent également un rôle croissant dans l’automatisation de la production de peinture en poudre. Ces dispositifs peuvent surveiller la qualité du revêtement en temps réel, identifier les imperfections ou les irrégularités de la peinture, et ajuster les paramètres du four ou de l’application de la poudre pour garantir une finition parfaite. L’intégration de ces technologies permet d’atteindre une qualité constante tout en réduisant les coûts associés à la production de lots non conformes.
Un autre aspect très important dans le domaine des fours de cuisson est la capacité de ces systèmes à traiter des pièces complexes et de grande taille, notamment dans des secteurs comme l’aéronautique ou l’automobile. Les fours à taille modulable sont capables de gérer des formes irrégulières et de grandes dimensions, ce qui est crucial dans des applications industrielles spécifiques. Par exemple, dans l’industrie automobile, où les pièces de carrosserie ou les composants en métal doivent recevoir une couche uniforme de peinture en poudre, ces fours sont conçus pour garantir que même les zones difficiles à atteindre soient correctement durcies, assurant ainsi une finition impeccable.
Les fours à peinture en poudre à contrôle automatisé permettent également de personnaliser les profils de cuisson pour des produits spécifiques. Grâce à la possibilité de programmer plusieurs phases de cuisson avec des températures et des durées différentes, les utilisateurs peuvent optimiser le processus en fonction des caractéristiques de la peinture et de la pièce à traiter, ce qui améliore la qualité du produit fini tout en augmentant la productivité.
Il est important de noter que le soutien aux travailleurs est un autre aspect essentiel des fours de cuisson modernes. Les systèmes d’automatisation avancée réduisent le besoin de manipulations manuelles et minimisent ainsi l’exposition des employés à des substances chimiques potentiellement dangereuses. Ces systèmes automatisés permettent de réaliser des réglages et des contrôles à distance, offrant aux opérateurs une plus grande flexibilité et garantissant des conditions de travail plus sûres.
Enfin, le futur de la peinture en poudre pourrait être marqué par l’émergence de nouvelles technologies encore plus écologiques, comme la peinture en poudre solaire ou thermoplastique, qui peuvent réduire encore davantage l’impact environnemental des fours de cuisson. Des revêtements à séchage à froid, qui ne nécessitent pas de cuisson, sont également en développement, ce qui pourrait révolutionner la manière dont la peinture est appliquée tout en éliminant le besoin de chaleur dans le processus de durcissement. Ces avancées pourraient encore améliorer l’efficacité du processus et la durabilité des produits finis, tout en réduisant davantage la consommation d’énergie.
En résumé, les fours de cuisson pour peinture en poudre continuent de se perfectionner à travers une combinaison d’innovations technologiques, de pratiques plus respectueuses de l’environnement et d’améliorations de l’efficacité énergétique. L’intégration des technologies de connectivité et d’intelligence artificielle, combinée avec des solutions écoénergétiques, permettra à l’industrie de produire des finitions de plus en plus performantes et durables, tout en répondant aux besoins de flexibilité et de productivité des chaînes de production modernes. L’avenir du revêtement en poudre semble être axé sur l’automatisation, l’optimisation et l’amélioration de la qualité, tout en minimisant les coûts et l’impact environnemental.
4o mini
Le Revêtement en Poudre
L’équipement de revêtement en poudre est utilisé pour appliquer une fine couche de poudre sur une surface métallique. Ce type de revêtement est appliqué par un procédé électrostatique et constitue une méthode très populaire pour la finition des pièces métalliques.
Ce type d’équipement peut être divisé en deux grandes catégories : automatiques et manuels. Les cabines automatiques sont plus populaires car elles offrent de meilleurs taux de production, mais elles sont également plus chères.
Une cabine à poudre est une enceinte dans laquelle se déroule le processus de revêtement en poudre. L’équipement de revêtement en poudre comprend un four dans lequel les pièces sont chauffées pour activer la poudre, un pistolet qui pulvérise ou brosse la poudre, une bande transporteuse qui déplace les pièces à travers le four et des pistolets de type cartouche pour appliquer des revêtements plus épais avec moins de pulvérisation.
Le revêtement en poudre est une technique utilisée pour donner une finition aux pièces métalliques. Cette technique est utilisée depuis de nombreuses années et reste aujourd’hui l’une des techniques les plus populaires.
L’équipement de revêtement en poudre comprend des cabines, des fours, des pistolets, des machines, des lignes et des convoyeurs. Une cabine peut être automatique ou manuelle. Une cabine automatique est plus chère qu’une cabine manuelle mais elle est aussi plus rapide et plus efficace