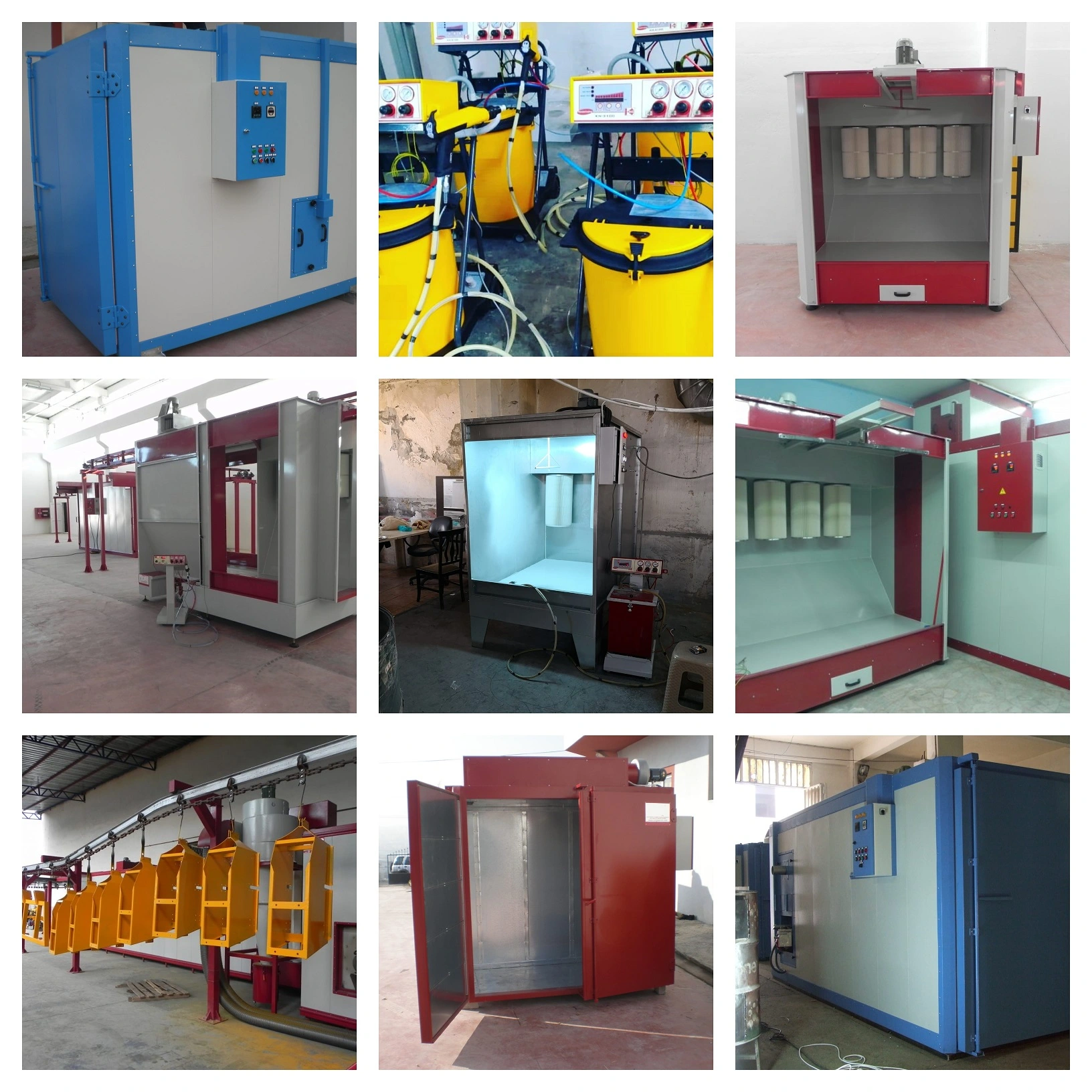
Les équipements de revêtement en poudre sont essentiels pour de nombreuses industries, offrant une solution efficace et durable pour la finition des surfaces métalliques et autres matériaux. Parmi les principaux équipements de ce type, on trouve les fours de revêtement, les cabines de pulvérisation et les pistolets de revêtement en poudre.
Ces machines jouent un rôle crucial dans la création d’une finition uniforme, résistante et esthétique sur les produits traités. Les fours de revêtement en poudre permettent de chauffer les pièces à des températures spécifiques, ce qui permet à la poudre de fondre et d’adhérer de manière homogène sur la surface. Les cabines de pulvérisation offrent un environnement contrôlé pour appliquer la poudre sur les pièces, en minimisant les risques de contamination et en assurant une application précise et efficace.
Quant aux pistolets de revêtement en poudre, ils sont utilisés pour pulvériser la poudre sur les surfaces de manière fine et uniforme, grâce à un système électrostatique qui charge la poudre et améliore son adhésion. Ces équipements sont disponibles dans une large gamme de modèles et de configurations, offrant des options adaptées à des besoins spécifiques en termes de volume, de type de produits et de qualité de finition. De plus, il est possible de trouver des machines de revêtement en poudre de haute qualité à des prix compétitifs, ce qui permet aux entreprises d’investir dans des équipements performants tout en maîtrisant leurs coûts de production. Ces équipements sont de plus en plus populaires grâce à leurs avantages en matière de durabilité, de rentabilité et de respect de l’environnement, car le processus de revêtement en poudre génère moins de déchets et utilise des produits moins polluants par rapport à d’autres techniques de finition.
Équipement de Revêtement en Poudre
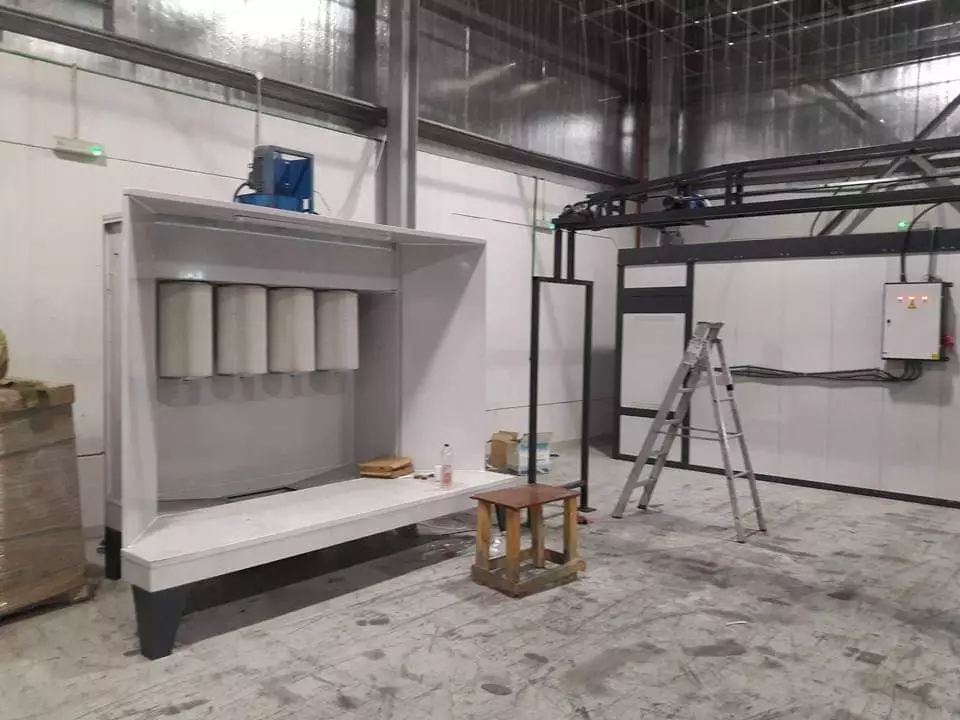
Les équipements de revêtement en poudre jouent un rôle fondamental dans de nombreux secteurs industriels, notamment l’automobile, l’électroménager, la construction et l’équipement industriel. Leur efficacité et leur capacité à offrir des finitions durables et de haute qualité ont fait d’eux un choix incontournable pour les entreprises cherchant à améliorer leurs processus de production. Ces équipements sont conçus pour appliquer une fine couche de poudre thermoplastique ou thermodurcissable sur les surfaces, qui, une fois chauffée dans un four, forme une couche lisse, uniforme et résistante.
Les fours de revêtement en poudre sont des éléments essentiels de ce processus. Ils sont utilisés pour chauffer les pièces revêtues de poudre à une température spécifique, généralement entre 180 et 220 °C, en fonction du type de poudre utilisée. Cette chaleur permet à la poudre de fondre et de se fixer solidement sur la surface, créant ainsi une finition lisse et résistante aux rayures, aux produits chimiques et aux intempéries. Les fours peuvent être de différentes tailles et configurations, allant des modèles à chambre simple pour des volumes plus petits aux modèles à convection forcée ou à circulation d’air pour des productions plus importantes. De plus, les technologies modernes permettent une meilleure gestion de la consommation énergétique, ce qui rend ces équipements plus écologiques et rentables.
Les cabines de pulvérisation sont des environnements contrôlés qui permettent une application optimale de la poudre. Elles sont équipées de systèmes de filtration avancés pour éviter que la poudre ne soit dispersée dans l’air, ce qui non seulement améliore la qualité du revêtement, mais assure également la sécurité des opérateurs. Les cabines de pulvérisation modernes sont souvent dotées de systèmes de récupération de la poudre excédentaire, ce qui permet de minimiser les pertes et de réduire les coûts de matière première. Ces cabines peuvent être ajustées en fonction de la taille des pièces à traiter et du type de finition recherchée. Elles sont particulièrement utiles pour des applications où la précision est essentielle, comme le revêtement de petites pièces complexes ou de grandes surfaces nécessitant une application homogène.
Les pistolets de revêtement en poudre sont utilisés pour appliquer la poudre sur les pièces à revêtir. Ils fonctionnent selon un principe électrostatique, qui charge la poudre et permet à celle-ci de s’attacher à la surface de manière plus efficace. Le pistolet génère une fine brume de poudre qui se fixe sur les pièces métalliques, créant ainsi une couverture uniforme. Il existe différents types de pistolets, y compris des modèles manuels et automatiques. Les pistolets automatiques sont particulièrement adaptés aux lignes de production à grande échelle, où un revêtement rapide et précis est nécessaire. Les modèles manuels, quant à eux, offrent plus de flexibilité et sont souvent utilisés pour des travaux plus spécialisés ou des petits lots.
Les machines de revêtement en poudre de haute qualité sont désormais disponibles à des prix compétitifs, ce qui permet aux petites et moyennes entreprises d’accéder à cette technologie avancée sans compromettre la qualité de leur production. Bien que les équipements de revêtement en poudre représentent un investissement initial significatif, leur rentabilité à long terme est indiscutable. En effet, ils permettent non seulement de réduire les coûts liés aux matériaux et aux déchets, mais aussi de diminuer le temps de production et d’améliorer la durabilité des produits finis. Les revêtements en poudre, contrairement aux peintures liquides, ne contiennent pas de solvants et émettent donc moins de composés organiques volatils (COV), ce qui les rend plus écologiques.
De plus, l’entretien de ces équipements est relativement simple, et leur durée de vie est longue grâce à la robustesse des matériaux utilisés dans leur fabrication. Les avancées technologiques ont permis d’améliorer l’efficacité énergétique des fours, ce qui réduit la consommation d’électricité et contribue ainsi à une réduction des coûts de fonctionnement. Les machines modernes sont également dotées de systèmes de contrôle automatisés, permettant de suivre en temps réel la température, l’humidité et d’autres paramètres essentiels pour garantir un revêtement parfait.
Un autre avantage des équipements de revêtement en poudre réside dans leur flexibilité. Ils peuvent être utilisés pour une large gamme de matériaux, notamment l’acier, l’aluminium, le zinc, et même certains plastiques. Cette polyvalence en fait un choix de premier plan pour les entreprises qui doivent traiter une variété de produits ou qui cherchent à diversifier leurs lignes de production. De plus, le choix de couleurs et de finitions est pratiquement illimité, ce qui permet aux fabricants de répondre aux demandes spécifiques de leurs clients, qu’il s’agisse de couleurs standard ou de nuances personnalisées.
En résumé, l’équipement de revêtement en poudre, comprenant les fours, les cabines de pulvérisation et les pistolets, représente une solution efficace et économique pour les entreprises souhaitant améliorer la qualité et la durabilité de leurs produits tout en optimisant leur processus de fabrication. Grâce à des machines de haute qualité à des prix compétitifs, il est désormais possible pour un large éventail d’industries d’intégrer ces technologies dans leurs opérations. Cela permet non seulement d’augmenter la productivité et de réduire les coûts, mais aussi de répondre aux préoccupations environnementales grâce à des méthodes de finition plus écologiques.
Technologies de Revêtement en Poudre
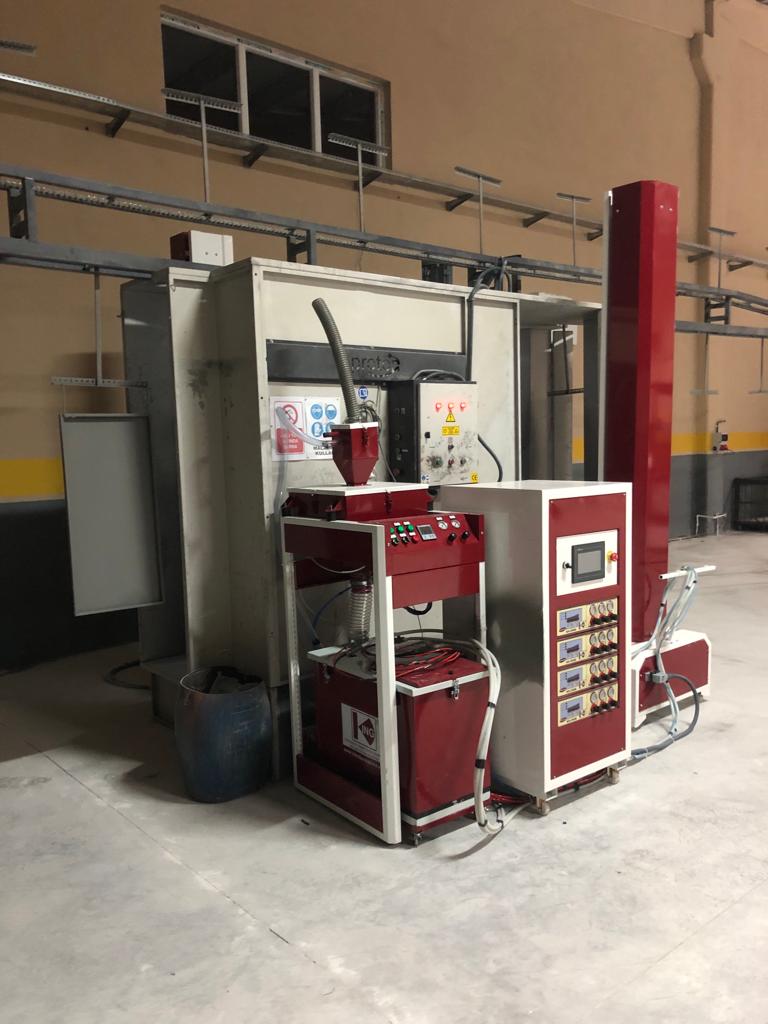
L’évolution des technologies de revêtement en poudre continue de repousser les limites de ce processus en termes d’efficacité, de flexibilité et de durabilité. Les améliorations constantes apportées aux fours et systèmes de pulvérisation rendent cette technologie encore plus adaptée aux exigences industrielles contemporaines, où la qualité et la rapidité de production sont primordiales. Les fours de revêtement en poudre modernes ne se contentent plus de chauffer les pièces, mais intègrent également des systèmes de contrôle précis de la température et de la circulation de l’air. Cela permet de garantir que chaque pièce soit chauffée uniformément, ce qui réduit les risques de défauts tels que des finitions inégales ou des zones sous-revêtues. Certains modèles de fours sont également dotés de dispositifs de préchauffage, permettant d’optimiser le temps de traitement des pièces et de réduire ainsi le cycle de production.
Les systèmes de récupération de poudre jouent un rôle crucial dans l’efficacité des cabines de pulvérisation modernes. En récupérant et en filtrant la poudre excédentaire, ces systèmes permettent non seulement de réduire les déchets, mais aussi de réutiliser la poudre pour de futurs cycles, ce qui réduit les coûts des matériaux. Ce processus est particulièrement important dans les environnements de production à grande échelle, où les volumes de poudre utilisés peuvent être considérables. Les avancées dans la technologie des systèmes de filtration garantissent également que les émissions de poussière et les risques pour la santé des opérateurs sont minimisés, ce qui rend ces équipements encore plus sûrs à utiliser.
Le pistolet de revêtement en poudre constitue également un élément en constante évolution. Les modèles les plus récents sont équipés de systèmes de contrôle numérique sophistiqués qui permettent de réguler précisément la quantité de poudre appliquée, la pression d’air et l’intensité de la charge électrostatique. Cela permet d’optimiser l’application de la poudre, en s’assurant que la couche est parfaitement uniforme et adhère correctement, même sur des pièces complexes ou de formes irrégulières. De plus, les pistolets de nouvelle génération sont conçus pour être plus ergonomiques, facilitant ainsi leur utilisation pendant de longues périodes et réduisant la fatigue des opérateurs.
La flexibilité de ces systèmes est également un atout majeur. Les équipements de revêtement en poudre peuvent être adaptés à différents types de productions, des petites séries aux grandes séries industrielles. En intégrant des lignes de production automatisées, les entreprises peuvent augmenter leur efficacité et réduire les erreurs humaines tout en maintenant une qualité de finition constante. Cette automatisation est facilitée par des logiciels de gestion avancés, qui permettent de contrôler l’ensemble du processus de revêtement, depuis la préparation des pièces jusqu’à leur sortie du four. Cela permet non seulement de garantir des résultats de haute qualité, mais aussi d’optimiser l’utilisation des ressources humaines et matérielles, contribuant ainsi à la rentabilité de l’entreprise.
Les machines de revêtement en poudre de haute qualité à des prix compétitifs sont désormais accessibles à une gamme plus large d’entreprises, des petites sociétés aux grandes industries. L’accessibilité de ces équipements permet de démocratiser l’usage de la technologie du revêtement en poudre, permettant à des entreprises de différentes tailles d’adopter cette méthode plus écologique et plus rentable. Cette évolution a été facilitée par la mondialisation de la production de ces équipements, permettant aux fabricants d’optimiser leurs processus et de réduire les coûts. En conséquence, de nombreuses entreprises peuvent désormais se doter de machines performantes sans avoir à investir des sommes colossales.
Il est également important de souligner que l’adoption du revêtement en poudre contribue à des objectifs environnementaux importants. Contrairement aux peintures traditionnelles, qui nécessitent l’utilisation de solvants et qui émettent des COV (composés organiques volatils) nuisibles à la santé et à l’environnement, le revêtement en poudre est exempt de ces substances chimiques dangereuses. En outre, la possibilité de récupérer et de réutiliser la poudre excédentaire permet de limiter les déchets et de réduire l’empreinte écologique de l’ensemble du processus. Ce faible impact environnemental fait du revêtement en poudre une option privilégiée pour les entreprises qui cherchent à réduire leur empreinte carbone et à respecter des normes écologiques strictes.
Les revêtements en poudre sont également très appréciés pour leur résistance et leur durabilité. Une fois appliquée et durcie, la couche de poudre forme un revêtement solide et résistant à l’usure, aux impacts, aux rayures, aux produits chimiques, à la chaleur et aux conditions climatiques extrêmes. Cela en fait une solution idéale pour les applications extérieures ou dans des environnements industriels difficiles, où les pièces doivent résister à des conditions sévères. De plus, les revêtements en poudre sont disponibles dans une large gamme de couleurs et de finitions, y compris des options métalliques, texturées, mates et brillantes, offrant ainsi une grande variété d’esthétiques pour répondre aux besoins spécifiques de chaque client.
Le marché des équipements de revêtement en poudre continue de croître, porté par l’augmentation de la demande dans divers secteurs tels que l’automobile, l’électroménager, le mobilier et la construction. Les consommateurs et les entreprises recherchent de plus en plus des produits finis de haute qualité, résistants et respectueux de l’environnement. L’investissement dans des équipements de revêtement en poudre de qualité devient ainsi une stratégie gagnante pour les entreprises qui souhaitent rester compétitives sur le marché tout en offrant des produits finis de plus en plus performants.
Ainsi, les équipements de revêtement en poudre — du four à la cabine de pulvérisation, en passant par le pistolet de pulvérisation — sont devenus des instruments incontournables dans de nombreux secteurs industriels. Leur capacité à offrir une finition de haute qualité, leur durabilité, leur respect de l’environnement, ainsi que leur flexibilité et leur rentabilité, font de ces machines des investissements judicieux pour toutes les entreprises cherchant à améliorer leur production et à répondre aux demandes croissantes du marché.
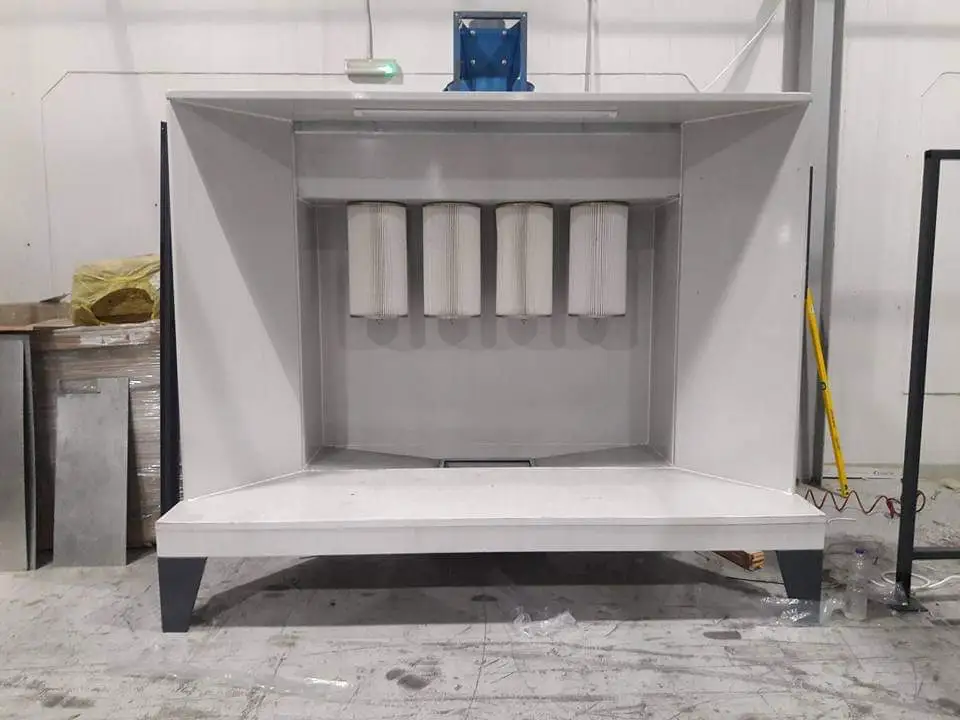
L’avenir des équipements de revêtement en poudre semble prometteur, avec des innovations continues qui visent à rendre ces systèmes encore plus efficaces, flexibles et respectueux de l’environnement. Par exemple, les systèmes de contrôle numérique avancés pour les pistolets de revêtement et les systèmes de gestion automatisée pour les lignes de production permettent de personnaliser davantage le processus, tout en garantissant une constance dans la qualité du revêtement. Ces systèmes peuvent ajuster en temps réel les paramètres de pulvérisation, comme la vitesse de l’air, la tension électrostatique et la quantité de poudre projetée, afin d’optimiser l’application sur des pièces de formes complexes ou de tailles variées. Cette capacité à répondre instantanément aux besoins de production permet de réduire les erreurs humaines et d’améliorer la productivité globale.
Les équipements de revêtement en poudre intelligents intègrent des technologies de surveillance et d’analyse des données en temps réel. Par exemple, des capteurs intelligents peuvent être utilisés pour surveiller la température du four, la vitesse de la circulation de l’air et même la composition de la poudre pendant le processus. Ces données sont ensuite analysées pour garantir que chaque lot de production respecte des critères stricts de qualité. Les systèmes de maintenance prédictive sont également de plus en plus utilisés, permettant de détecter les signes de défaillance avant qu’ils ne se produisent, ce qui réduit les temps d’arrêt et améliore la rentabilité globale de l’équipement.
Les nouveaux types de poudres qui sont développés pour le revêtement en poudre jouent également un rôle dans l’évolution de cette technologie. Par exemple, des poudres à base de résines hybrides ou des formulations spéciales de poudre permettent d’obtenir des finitions de plus en plus résistantes aux conditions climatiques extrêmes, telles que l’humidité, les fortes températures et les rayons UV. Ces poudres sont souvent utilisées dans des secteurs comme l’automobile, où la durabilité et l’apparence esthétique sont essentielles, mais aussi dans les secteurs industriels où les pièces sont soumises à des conditions de travail difficiles. La diversité des poudres disponibles permet également de répondre à des besoins de finitions spécifiques, comme des textures particulières ou des couleurs métalliques brillantes.
Un autre domaine de développement concerne les technologies de recyclage de la poudre excédentaire. Les systèmes de récupération de poudre se sont améliorés au fil des ans, et désormais, une proportion significative de la poudre excédentaire peut être récupérée et réutilisée dans le processus de pulvérisation. Ce recyclage contribue non seulement à réduire les coûts, mais aussi à diminuer l’empreinte écologique du processus. Les entreprises peuvent ainsi minimiser les déchets et maximiser l’utilisation des matériaux, ce qui leur permet de rester compétitives tout en répondant aux exigences écologiques modernes. Ces innovations contribuent à la réalisation des objectifs de durabilité, en réduisant les émissions de CO2 et en utilisant moins de matières premières.
Les machines de revêtement en poudre à des prix compétitifs sont également accompagnées d’un support technique de plus en plus sophistiqué, ce qui permet aux entreprises d’optimiser leur utilisation au maximum. Les fabricants d’équipements de revêtement en poudre offrent des services de formation, des diagnostics à distance, ainsi que des conseils pour l’optimisation des processus. Cette assistance aide les entreprises à mieux comprendre les réglages nécessaires pour chaque type de projet, en fonction des exigences spécifiques de finition, des matériaux utilisés et des conditions de production. De plus, de nombreuses entreprises bénéficient de l’intégration de solutions logicielles qui permettent une gestion complète de la production, de la préparation des pièces à la gestion de la qualité du revêtement. Ces outils permettent une traçabilité complète du processus, ce qui est particulièrement important dans des secteurs réglementés ou pour des clients exigeants en termes de qualité.
L’importance croissante des revêtements écologiques dans les industries de consommation pousse les entreprises à adopter des équipements de revêtement en poudre. En effet, cette technologie est souvent perçue comme une alternative plus « verte » par rapport aux techniques de peinture traditionnelles qui utilisent des solvants chimiques. Les revêtements en poudre ne génèrent pas de composés organiques volatils (COV), ce qui réduit considérablement l’impact environnemental. De plus, le processus de revêtement en poudre génère moins de déchets et nécessite moins de ressources, ce qui en fait une option idéale pour les entreprises cherchant à réduire leur empreinte carbone et à respecter des normes environnementales strictes.
Une autre dimension importante de l’avenir des équipements de revêtement en poudre est l’intégration de solutions énergétiques plus efficaces. De nombreuses entreprises cherchent à réduire leur consommation d’énergie, non seulement pour des raisons économiques, mais aussi pour répondre à des exigences environnementales de plus en plus strictes. Les innovations dans les technologies de chauffage des fours, telles que l’utilisation d’énergies renouvelables ou des technologies de récupération thermique, permettent de réduire la consommation d’énergie tout en maintenant une performance optimale. L’introduction de fours à haute efficacité énergétique est une réponse directe aux préoccupations croissantes concernant l’impact énergétique de la production industrielle.
Le développement de machines compactes et de systèmes modulaires représente également une tendance importante, car il permet aux entreprises d’adapter leurs installations de revêtement en fonction de la taille de leur production. Ces solutions permettent de personnaliser les équipements pour répondre aux besoins spécifiques d’une ligne de production ou d’une application donnée. Les petites entreprises ou celles qui ont des espaces de production limités peuvent ainsi bénéficier de la même technologie de revêtement en poudre de haute qualité que les grandes industries, tout en optimisant leur espace et leurs ressources.
Les machines de revêtement en poudre continuent donc d’évoluer pour répondre aux besoins diversifiés des marchés modernes. En combinant des technologies de pointe avec une conscience environnementale accrue, ces équipements deviennent des outils incontournables pour les industries cherchant à offrir des produits finis de haute qualité tout en réduisant leur impact environnemental et en améliorant leur rentabilité. Les fours, cabines de pulvérisation et pistolets de revêtement en poudre sont désormais plus accessibles, plus performants et plus respectueux de l’environnement, offrant ainsi une solution de finition robuste et économique pour un large éventail d’applications industrielles.
Équipement de revêtement en poudre – Four, cabine de pulvérisation, pistolet de revêtement en poudre – et machines de revêtement en poudre de haute qualité à des prix compétitifs
L’équipement de revêtement en poudre est utilisé pour appliquer une fine couche de poudre sur une surface métallique. Ce type de revêtement est appliqué par un procédé électrostatique et constitue une méthode très populaire pour la finition des pièces métalliques.
Ce type d’équipement peut être divisé en deux grandes catégories : automatiques et manuels. Les cabines automatiques sont plus populaires car elles offrent de meilleurs taux de production, mais elles sont également plus chères.
Une cabine à poudre est une enceinte dans laquelle se déroule le processus de revêtement en poudre. L’équipement de revêtement en poudre comprend un four dans lequel les pièces sont chauffées pour activer la poudre, un pistolet qui pulvérise ou brosse la poudre, une bande transporteuse qui déplace les pièces à travers le four et des pistolets de type cartouche pour appliquer des revêtements plus épais avec moins de pulvérisation.
Le revêtement en poudre est une technique utilisée pour donner une finition aux pièces métalliques. Cette technique est utilisée depuis de nombreuses années et reste aujourd’hui l’une des techniques les plus populaires.
L’équipement de revêtement en poudre comprend des cabines, des fours, des pistolets, des machines, des lignes et des convoyeurs. Une cabine peut être automatique ou manuelle. Une cabine automatique est plus chère qu’une cabine manuelle mais elle est aussi plus rapide et plus efficace.
Les équipements de revêtement en poudre sont essentiels pour de nombreuses industries, offrant une solution efficace et durable pour la finition des surfaces métalliques et autres matériaux. Parmi les principaux équipements de ce type, on trouve les fours de revêtement, les cabines de pulvérisation et les pistolets de revêtement en poudre. Ces machines jouent un rôle crucial dans la création d’une finition uniforme, résistante et esthétique sur les produits traités.
Les fours de revêtement en poudre permettent de chauffer les pièces à des températures spécifiques, ce qui permet à la poudre de fondre et d’adhérer de manière homogène sur la surface. Les cabines de pulvérisation offrent un environnement contrôlé pour appliquer la poudre sur les pièces, en minimisant les risques de contamination et en assurant une application précise et efficace. Quant aux pistolets de revêtement en poudre, ils sont utilisés pour pulvériser la poudre sur les surfaces de manière fine et uniforme, grâce à un système électrostatique qui charge la poudre et améliore son adhésion.
Ces équipements sont disponibles dans une large gamme de modèles et de configurations, offrant des options adaptées à des besoins spécifiques en termes de volume, de type de produits et de qualité de finition. De plus, il est possible de trouver des machines de revêtement en poudre de haute qualité à des prix compétitifs, ce qui permet aux entreprises d’investir dans des équipements performants tout en maîtrisant leurs coûts de production. Ces équipements sont de plus en plus populaires grâce à leurs avantages en matière de durabilité, de rentabilité et de respect de l’environnement, car le processus de revêtement en poudre génère moins de déchets et utilise des produits moins polluants par rapport à d’autres techniques de finition.
Équipement de Revêtement en Poudre
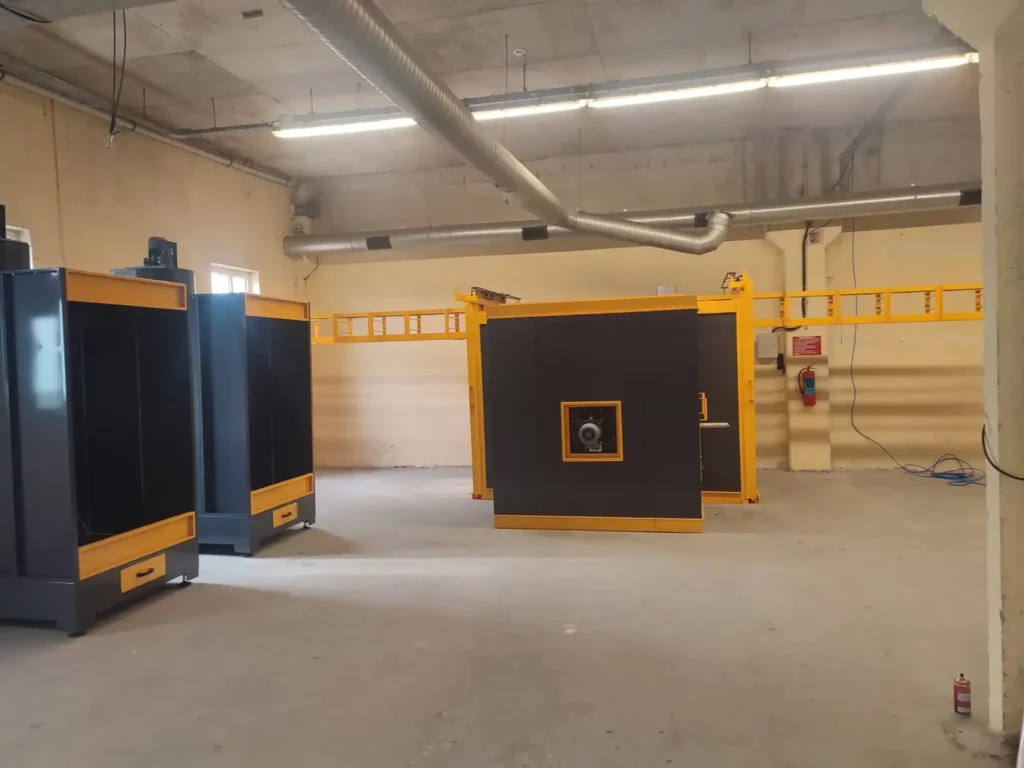
Les équipements de revêtement en poudre jouent un rôle fondamental dans de nombreux secteurs industriels, notamment l’automobile, l’électroménager, la construction et l’équipement industriel. Leur efficacité et leur capacité à offrir des finitions durables et de haute qualité ont fait d’eux un choix incontournable pour les entreprises cherchant à améliorer leurs processus de production. Ces équipements sont conçus pour appliquer une fine couche de poudre thermoplastique ou thermodurcissable sur les surfaces, qui, une fois chauffée dans un four, forme une couche lisse, uniforme et résistante.
Les fours de revêtement en poudre sont des éléments essentiels de ce processus. Ils sont utilisés pour chauffer les pièces revêtues de poudre à une température spécifique, généralement entre 180 et 220 °C, en fonction du type de poudre utilisée. Cette chaleur permet à la poudre de fondre et de se fixer solidement sur la surface, créant ainsi une finition lisse et résistante aux rayures, aux produits chimiques et aux intempéries. Les fours peuvent être de différentes tailles et configurations, allant des modèles à chambre simple pour des volumes plus petits aux modèles à convection forcée ou à circulation d’air pour des productions plus importantes. De plus, les technologies modernes permettent une meilleure gestion de la consommation énergétique, ce qui rend ces équipements plus écologiques et rentables.
Les cabines de pulvérisation sont des environnements contrôlés qui permettent une application optimale de la poudre. Elles sont équipées de systèmes de filtration avancés pour éviter que la poudre ne soit dispersée dans l’air, ce qui non seulement améliore la qualité du revêtement, mais assure également la sécurité des opérateurs. Les cabines de pulvérisation modernes sont souvent dotées de systèmes de récupération de la poudre excédentaire, ce qui permet de minimiser les pertes et de réduire les coûts de matière première. Ces cabines peuvent être ajustées en fonction de la taille des pièces à traiter et du type de finition recherchée. Elles sont particulièrement utiles pour des applications où la précision est essentielle, comme le revêtement de petites pièces complexes ou de grandes surfaces nécessitant une application homogène.
Les pistolets de revêtement en poudre sont utilisés pour appliquer la poudre sur les pièces à revêtir. Ils fonctionnent selon un principe électrostatique, qui charge la poudre et permet à celle-ci de s’attacher à la surface de manière plus efficace. Le pistolet génère une fine brume de poudre qui se fixe sur les pièces métalliques, créant ainsi une couverture uniforme. Il existe différents types de pistolets, y compris des modèles manuels et automatiques. Les pistolets automatiques sont particulièrement adaptés aux lignes de production à grande échelle, où un revêtement rapide et précis est nécessaire. Les modèles manuels, quant à eux, offrent plus de flexibilité et sont souvent utilisés pour des travaux plus spécialisés ou des petits lots.
Les machines de revêtement en poudre de haute qualité sont désormais disponibles à des prix compétitifs, ce qui permet aux petites et moyennes entreprises d’accéder à cette technologie avancée sans compromettre la qualité de leur production. Bien que les équipements de revêtement en poudre représentent un investissement initial significatif, leur rentabilité à long terme est indiscutable. En effet, ils permettent non seulement de réduire les coûts liés aux matériaux et aux déchets, mais aussi de diminuer le temps de production et d’améliorer la durabilité des produits finis. Les revêtements en poudre, contrairement aux peintures liquides, ne contiennent pas de solvants et émettent donc moins de composés organiques volatils (COV), ce qui les rend plus écologiques.
De plus, l’entretien de ces équipements est relativement simple, et leur durée de vie est longue grâce à la robustesse des matériaux utilisés dans leur fabrication. Les avancées technologiques ont permis d’améliorer l’efficacité énergétique des fours, ce qui réduit la consommation d’électricité et contribue ainsi à une réduction des coûts de fonctionnement. Les machines modernes sont également dotées de systèmes de contrôle automatisés, permettant de suivre en temps réel la température, l’humidité et d’autres paramètres essentiels pour garantir un revêtement parfait.
Un autre avantage des équipements de revêtement en poudre réside dans leur flexibilité. Ils peuvent être utilisés pour une large gamme de matériaux, notamment l’acier, l’aluminium, le zinc, et même certains plastiques. Cette polyvalence en fait un choix de premier plan pour les entreprises qui doivent traiter une variété de produits ou qui cherchent à diversifier leurs lignes de production. De plus, le choix de couleurs et de finitions est pratiquement illimité, ce qui permet aux fabricants de répondre aux demandes spécifiques de leurs clients, qu’il s’agisse de couleurs standard ou de nuances personnalisées.
En résumé, l’équipement de revêtement en poudre, comprenant les fours, les cabines de pulvérisation et les pistolets, représente une solution efficace et économique pour les entreprises souhaitant améliorer la qualité et la durabilité de leurs produits tout en optimisant leur processus de fabrication. Grâce à des machines de haute qualité à des prix compétitifs, il est désormais possible pour un large éventail d’industries d’intégrer ces technologies dans leurs opérations. Cela permet non seulement d’augmenter la productivité et de réduire les coûts, mais aussi de répondre aux préoccupations environnementales grâce à des méthodes de finition plus écologiques.
Technologies de revêtement en poudre
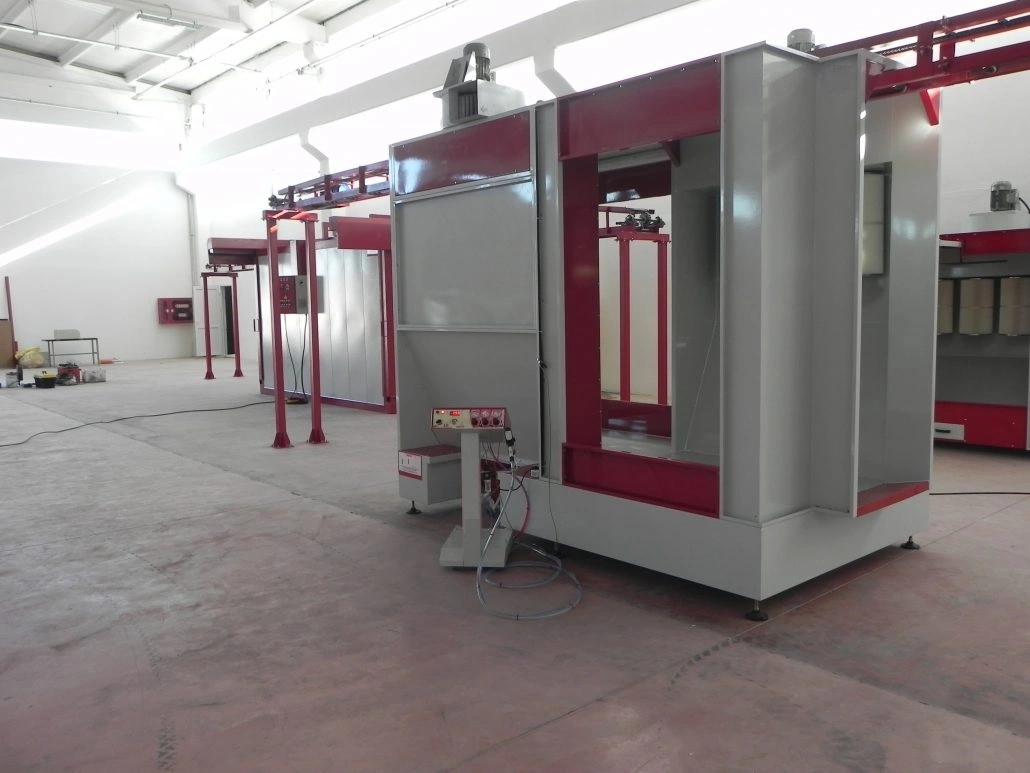
L’évolution des technologies de revêtement en poudre continue de repousser les limites de ce processus en termes d’efficacité, de flexibilité et de durabilité. Les améliorations constantes apportées aux fours et systèmes de pulvérisation rendent cette technologie encore plus adaptée aux exigences industrielles contemporaines, où la qualité et la rapidité de production sont primordiales. Les fours de revêtement en poudre modernes ne se contentent plus de chauffer les pièces, mais intègrent également des systèmes de contrôle précis de la température et de la circulation de l’air. Cela permet de garantir que chaque pièce soit chauffée uniformément, ce qui réduit les risques de défauts tels que des finitions inégales ou des zones sous-revêtues. Certains modèles de fours sont également dotés de dispositifs de préchauffage, permettant d’optimiser le temps de traitement des pièces et de réduire ainsi le cycle de production.
Les systèmes de récupération de poudre jouent un rôle crucial dans l’efficacité des cabines de pulvérisation modernes. En récupérant et en filtrant la poudre excédentaire, ces systèmes permettent non seulement de réduire les déchets, mais aussi de réutiliser la poudre pour de futurs cycles, ce qui réduit les coûts des matériaux. Ce processus est particulièrement important dans les environnements de production à grande échelle, où les volumes de poudre utilisés peuvent être considérables. Les avancées dans la technologie des systèmes de filtration garantissent également que les émissions de poussière et les risques pour la santé des opérateurs sont minimisés, ce qui rend ces équipements encore plus sûrs à utiliser.
Le pistolet de revêtement en poudre constitue également un élément en constante évolution. Les modèles les plus récents sont équipés de systèmes de contrôle numérique sophistiqués qui permettent de réguler précisément la quantité de poudre appliquée, la pression d’air et l’intensité de la charge électrostatique. Cela permet d’optimiser l’application de la poudre, en s’assurant que la couche est parfaitement uniforme et adhère correctement, même sur des pièces complexes ou de formes irrégulières. De plus, les pistolets de nouvelle génération sont conçus pour être plus ergonomiques, facilitant ainsi leur utilisation pendant de longues périodes et réduisant la fatigue des opérateurs.
La flexibilité de ces systèmes est également un atout majeur. Les équipements de revêtement en poudre peuvent être adaptés à différents types de productions, des petites séries aux grandes séries industrielles. En intégrant des lignes de production automatisées, les entreprises peuvent augmenter leur efficacité et réduire les erreurs humaines tout en maintenant une qualité de finition constante. Cette automatisation est facilitée par des logiciels de gestion avancés, qui permettent de contrôler l’ensemble du processus de revêtement, depuis la préparation des pièces jusqu’à leur sortie du four. Cela permet non seulement de garantir des résultats de haute qualité, mais aussi d’optimiser l’utilisation des ressources humaines et matérielles, contribuant ainsi à la rentabilité de l’entreprise.
Les machines de revêtement en poudre de haute qualité à des prix compétitifs sont désormais accessibles à une gamme plus large d’entreprises, des petites sociétés aux grandes industries. L’accessibilité de ces équipements permet de démocratiser l’usage de la technologie du revêtement en poudre, permettant à des entreprises de différentes tailles d’adopter cette méthode plus écologique et plus rentable. Cette évolution a été facilitée par la mondialisation de la production de ces équipements, permettant aux fabricants d’optimiser leurs processus et de réduire les coûts. En conséquence, de nombreuses entreprises peuvent désormais se doter de machines performantes sans avoir à investir des sommes colossales.
Il est également important de souligner que l’adoption du revêtement en poudre contribue à des objectifs environnementaux importants. Contrairement aux peintures traditionnelles, qui nécessitent l’utilisation de solvants et qui émettent des COV (composés organiques volatils) nuisibles à la santé et à l’environnement, le revêtement en poudre est exempt de ces substances chimiques dangereuses. En outre, la possibilité de récupérer et de réutiliser la poudre excédentaire permet de limiter les déchets et de réduire l’empreinte écologique de l’ensemble du processus. Ce faible impact environnemental fait du revêtement en poudre une option privilégiée pour les entreprises qui cherchent à réduire leur empreinte carbone et à respecter des normes écologiques strictes.
Les revêtements en poudre sont également très appréciés pour leur résistance et leur durabilité. Une fois appliquée et durcie, la couche de poudre forme un revêtement solide et résistant à l’usure, aux impacts, aux rayures, aux produits chimiques, à la chaleur et aux conditions climatiques extrêmes. Cela en fait une solution idéale pour les applications extérieures ou dans des environnements industriels difficiles, où les pièces doivent résister à des conditions sévères. De plus, les revêtements en poudre sont disponibles dans une large gamme de couleurs et de finitions, y compris des options métalliques, texturées, mates et brillantes, offrant ainsi une grande variété d’esthétiques pour répondre aux besoins spécifiques de chaque client.
Le marché des équipements de revêtement en poudre continue de croître, porté par l’augmentation de la demande dans divers secteurs tels que l’automobile, l’électroménager, le mobilier et la construction. Les consommateurs et les entreprises recherchent de plus en plus des produits finis de haute qualité, résistants et respectueux de l’environnement. L’investissement dans des équipements de revêtement en poudre de qualité devient ainsi une stratégie gagnante pour les entreprises qui souhaitent rester compétitives sur le marché tout en offrant des produits finis de plus en plus performants.
Ainsi, les équipements de revêtement en poudre — du four à la cabine de pulvérisation, en passant par le pistolet de pulvérisation — sont devenus des instruments incontournables dans de nombreux secteurs industriels. Leur capacité à offrir une finition de haute qualité, leur durabilité, leur respect de l’environnement, ainsi que leur flexibilité et leur rentabilité, font de ces machines des investissements judicieux pour toutes les entreprises cherchant à améliorer leur production et à répondre aux demandes croissantes du marché.
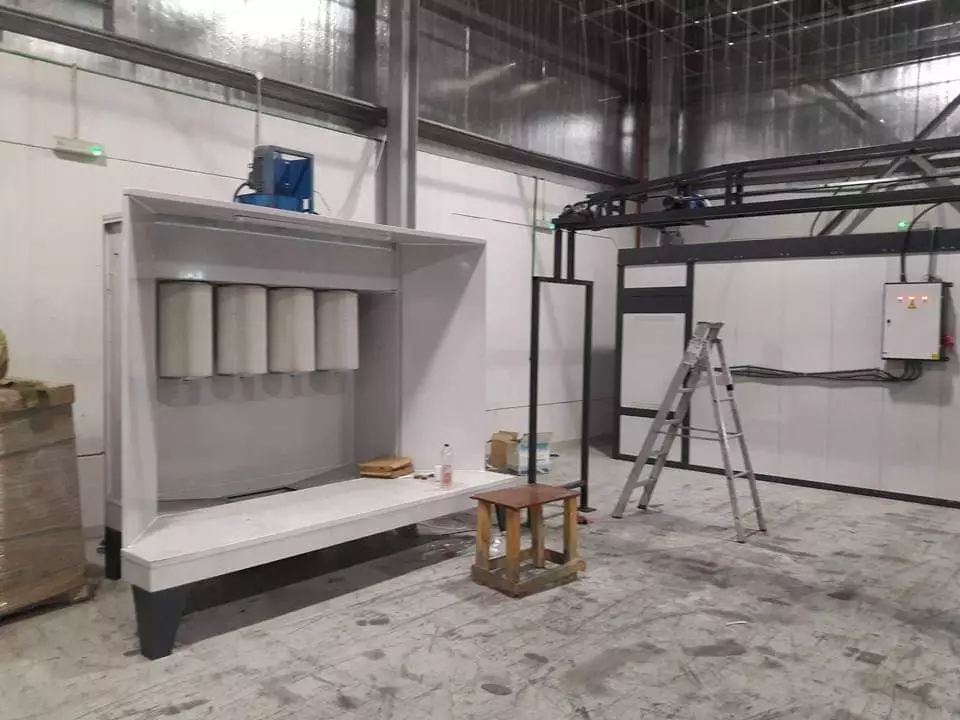
L’avenir des équipements de revêtement en poudre semble prometteur, avec des innovations continues qui visent à rendre ces systèmes encore plus efficaces, flexibles et respectueux de l’environnement. Par exemple, les systèmes de contrôle numérique avancés pour les pistolets de revêtement et les systèmes de gestion automatisée pour les lignes de production permettent de personnaliser davantage le processus, tout en garantissant une constance dans la qualité du revêtement. Ces systèmes peuvent ajuster en temps réel les paramètres de pulvérisation, comme la vitesse de l’air, la tension électrostatique et la quantité de poudre projetée, afin d’optimiser l’application sur des pièces de formes complexes ou de tailles variées. Cette capacité à répondre instantanément aux besoins de production permet de réduire les erreurs humaines et d’améliorer la productivité globale.
Les équipements de revêtement en poudre intelligents intègrent des technologies de surveillance et d’analyse des données en temps réel. Par exemple, des capteurs intelligents peuvent être utilisés pour surveiller la température du four, la vitesse de la circulation de l’air et même la composition de la poudre pendant le processus. Ces données sont ensuite analysées pour garantir que chaque lot de production respecte des critères stricts de qualité. Les systèmes de maintenance prédictive sont également de plus en plus utilisés, permettant de détecter les signes de défaillance avant qu’ils ne se produisent, ce qui réduit les temps d’arrêt et améliore la rentabilité globale de l’équipement.
Les nouveaux types de poudres qui sont développés pour le revêtement en poudre jouent également un rôle dans l’évolution de cette technologie. Par exemple, des poudres à base de résines hybrides ou des formulations spéciales de poudre permettent d’obtenir des finitions de plus en plus résistantes aux conditions climatiques extrêmes, telles que l’humidité, les fortes températures et les rayons UV. Ces poudres sont souvent utilisées dans des secteurs comme l’automobile, où la durabilité et l’apparence esthétique sont essentielles, mais aussi dans les secteurs industriels où les pièces sont soumises à des conditions de travail difficiles. La diversité des poudres disponibles permet également de répondre à des besoins de finitions spécifiques, comme des textures particulières ou des couleurs métalliques brillantes.
Un autre domaine de développement concerne les technologies de recyclage de la poudre excédentaire. Les systèmes de récupération de poudre se sont améliorés au fil des ans, et désormais, une proportion significative de la poudre excédentaire peut être récupérée et réutilisée dans le processus de pulvérisation. Ce recyclage contribue non seulement à réduire les coûts, mais aussi à diminuer l’empreinte écologique du processus. Les entreprises peuvent ainsi minimiser les déchets et maximiser l’utilisation des matériaux, ce qui leur permet de rester compétitives tout en répondant aux exigences écologiques modernes. Ces innovations contribuent à la réalisation des objectifs de durabilité, en réduisant les émissions de CO2 et en utilisant moins de matières premières.
Les machines de revêtement en poudre à des prix compétitifs sont également accompagnées d’un support technique de plus en plus sophistiqué, ce qui permet aux entreprises d’optimiser leur utilisation au maximum. Les fabricants d’équipements de revêtement en poudre offrent des services de formation, des diagnostics à distance, ainsi que des conseils pour l’optimisation des processus. Cette assistance aide les entreprises à mieux comprendre les réglages nécessaires pour chaque type de projet, en fonction des exigences spécifiques de finition, des matériaux utilisés et des conditions de production. De plus, de nombreuses entreprises bénéficient de l’intégration de solutions logicielles qui permettent une gestion complète de la production, de la préparation des pièces à la gestion de la qualité du revêtement. Ces outils permettent une traçabilité complète du processus, ce qui est particulièrement important dans des secteurs réglementés ou pour des clients exigeants en termes de qualité.
L’importance croissante des revêtements écologiques dans les industries de consommation pousse les entreprises à adopter des équipements de revêtement en poudre. En effet, cette technologie est souvent perçue comme une alternative plus « verte » par rapport aux techniques de peinture traditionnelles qui utilisent des solvants chimiques. Les revêtements en poudre ne génèrent pas de composés organiques volatils (COV), ce qui réduit considérablement l’impact environnemental. De plus, le processus de revêtement en poudre génère moins de déchets et nécessite moins de ressources, ce qui en fait une option idéale pour les entreprises cherchant à réduire leur empreinte carbone et à respecter des normes environnementales strictes.
Une autre dimension importante de l’avenir des équipements de revêtement en poudre est l’intégration de solutions énergétiques plus efficaces. De nombreuses entreprises cherchent à réduire leur consommation d’énergie, non seulement pour des raisons économiques, mais aussi pour répondre à des exigences environnementales de plus en plus strictes. Les innovations dans les technologies de chauffage des fours, telles que l’utilisation d’énergies renouvelables ou des technologies de récupération thermique, permettent de réduire la consommation d’énergie tout en maintenant une performance optimale. L’introduction de fours à haute efficacité énergétique est une réponse directe aux préoccupations croissantes concernant l’impact énergétique de la production industrielle.
Le développement de machines compactes et de systèmes modulaires représente également une tendance importante, car il permet aux entreprises d’adapter leurs installations de revêtement en fonction de la taille de leur production. Ces solutions permettent de personnaliser les équipements pour répondre aux besoins spécifiques d’une ligne de production ou d’une application donnée. Les petites entreprises ou celles qui ont des espaces de production limités peuvent ainsi bénéficier de la même technologie de revêtement en poudre de haute qualité que les grandes industries, tout en optimisant leur espace et leurs ressources.
Les machines de revêtement en poudre continuent donc d’évoluer pour répondre aux besoins diversifiés des marchés modernes. En combinant des technologies de pointe avec une conscience environnementale accrue, ces équipements deviennent des outils incontournables pour les industries cherchant à offrir des produits finis de haute qualité tout en réduisant leur impact environnemental et en améliorant leur rentabilité. Les fours, cabines de pulvérisation et pistolets de revêtement en poudre sont désormais plus accessibles, plus performants et plus respectueux de l’environnement, offrant ainsi une solution de finition robuste et économique pour un large éventail d’applications industrielles.
Équipement de revêtement en poudre pour roues et jantes en alliage
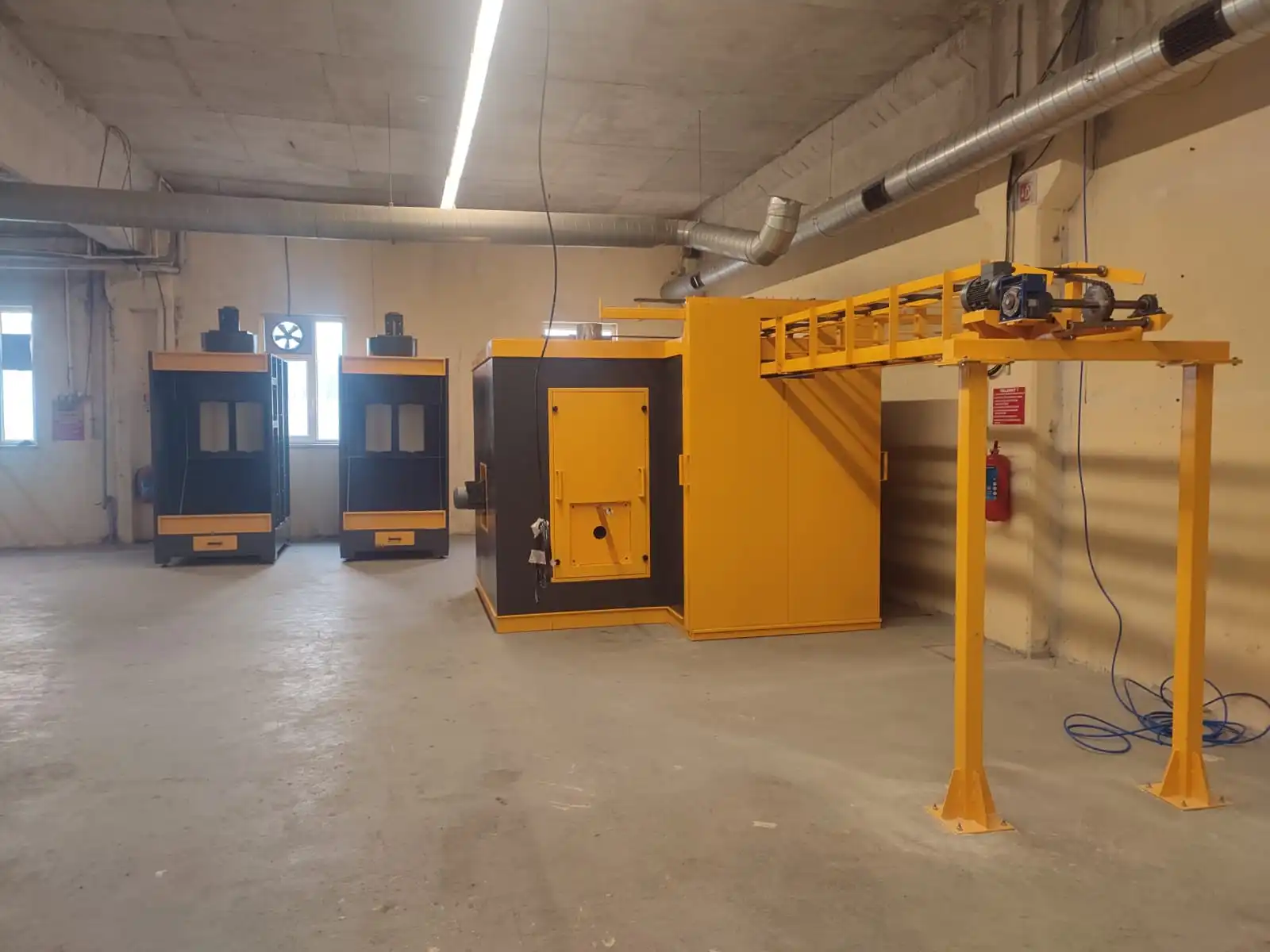
Les équipements de revêtement en poudre peuvent être largement classés en équipements de type cartouche et sans cartouche. Les équipements de revêtement en poudre de type cartouche disposent généralement d’un système automatisé pour charger la poudre des cartouches dans le pistolet, tandis que les équipements de revêtement en poudre sans cartouche disposent généralement d’un système automatisé pour charger la poudre des conteneurs dans le pistolet.
Le revêtement en poudre est un type de peinture qui est appliqué en soufflant de la poudre d’un pistolet sur la surface à recouvrir. Il est utilisé pour la protection contre la corrosion et la décoration.
L’équipement de revêtement en poudre comprend une cabine, un four, une machine, une ligne et un convoyeur. Les machines de revêtement en poudre sont divisées en cabines à cartouche et automatiques. Les cabines automatiques sont plus populaires car elles peuvent traiter plus de produits en un seul cycle.
Notre gamme de machines de revêtement en poudre a été développée au cours des plus de 30 années au service de l’industrie du revêtement en poudre. Dans notre usine en Turquie, nous fabriquons des machines de revêtement en poudre techniquement avancées et robustes pour fournir aux revêtements en poudre l’équipement dont ils ont besoin pour produire un volume élevé de travail de haute qualité aussi efficacement que possible. Notre expertise dans ce domaine et notre adhésion aux principes d’ingénierie de la valeur nous ont permis de constituer une clientèle fidèle dans les pays du monde entier.
Afin de fournir à nos clients les équipements les plus compétitifs, nous fabriquons nos machines dans une gamme de tailles standard.
Toutes nos machines sont marquées CE, garanties et peuvent être vues en personne par les clients potentiels. Il y a également des photos et des vidéos sur ce site montrant les machines utilisées.
Nous concevons, fabriquons et assemblons des fours de revêtement en poudre, des cabines automatiques et manuelles, des équipements de revêtement en poudre automatiques et manuels, des pistolets, des lignes de revêtement en poudre automatiques et à transfert de barres, des filtres de revêtement en poudre et des pièces de rechange pour pistolets de revêtement en poudre.
Revêtement en poudre :
Le revêtement en poudre est un processus de finition de surface largement utilisé dans l’industrie pour appliquer une couche protectrice ou décorative sur divers substrats, y compris les roues et les jantes en alliage. Ce processus implique l’application d’une poudre de revêtement à base de polymères, de résines, de pigments et d’additifs sur la surface préparée du matériau à revêtir.
La poudre de revêtement est appliquée à l’aide d’un équipement spécialisé, tel qu’un pistolet de pulvérisation électrostatique, qui charge électriquement les particules de poudre, les faisant adhérer uniformément à la surface du substrat. Une fois la poudre appliquée, le matériau est ensuite chauffé dans un four pour polymériser et fusionner la poudre, formant ainsi un revêtement durable, résistant aux chocs, à la corrosion et aux intempéries.
Ce processus de revêtement en poudre offre de nombreux avantages par rapport aux autres méthodes de finition de surface, notamment une excellente adhérence, une large gamme de couleurs et de finitions, une application uniforme sans coulures ni bulles, et une efficacité environnementale accrue grâce à la réduction des émissions de solvants. En ce qui concerne les roues et les jantes en alliage, le revêtement en poudre offre également une protection supplémentaire contre les rayures, les impacts et la décoloration due aux conditions routières et aux éléments extérieurs.
L’équipement de revêtement en poudre pour roues et jantes en alliage est une solution de finition de plus en plus populaire dans l’industrie automobile, car il permet de protéger ces composants essentiels contre l’usure, la corrosion et les conditions climatiques extrêmes tout en offrant un fini esthétique et durable. Le processus de revêtement en poudre pour les roues et jantes en alliage repose sur les mêmes principes fondamentaux que pour les autres applications industrielles, mais il nécessite des équipements spécialement conçus pour traiter les particularités de ces pièces, telles que leur forme complexe, leurs dimensions variées et leur exposition à des conditions sévères.
Fours de revêtement pour roues et jantes en alliage
Le four de revêtement en poudre utilisé pour les roues et jantes en alliage doit être capable de gérer des pièces relativement grandes, souvent de formes irrégulières, tout en assurant une application uniforme de la poudre. Les fours à convection forcée ou les fours à circulation d’air sont idéaux pour ce type de revêtement, car ils permettent un contrôle précis de la température, garantissant ainsi que chaque roue ou jante soit chauffée uniformément. La température dans le four doit être suffisamment élevée pour faire fondre la poudre et lui permettre de s’agglutiner correctement sur la surface, généralement autour de 180 à 200 °C, en fonction de la poudre utilisée.
De plus, les fours modernes sont conçus pour être économes en énergie et peuvent inclure des systèmes de récupération thermique pour réduire les coûts d’exploitation. Certains fours à profil bas sont spécialement adaptés aux roues et jantes de petite et moyenne taille, permettant un traitement plus rapide et plus efficace de plusieurs pièces simultanément. Ces systèmes sont également dotés de dispositifs de contrôle automatisés qui ajustent la température et l’humidité en temps réel pour garantir une finition parfaite à chaque cycle de production.
Cabines de pulvérisation adaptées aux roues et jantes en alliage
Les cabines de pulvérisation utilisées pour les roues et jantes en alliage sont conçues pour garantir une application précise de la poudre, en particulier sur des surfaces complexes et tridimensionnelles. Les jantes, par exemple, possèdent souvent des formes et des courbes qui rendent le processus de pulvérisation plus délicat que pour des pièces plus simples. Les cabines de pulvérisation de haute qualité sont équipées de systèmes de filtration avancés et de récupération de poudre excédentaire, ce qui permet de récupérer efficacement la poudre non appliquée et de la réutiliser, réduisant ainsi les coûts de matériaux et l’impact environnemental.
Les systèmes de pulvérisation électrostatique sont particulièrement adaptés pour cette application, car ils chargent la poudre électriquement, ce qui améliore l’adhésion de la poudre sur les surfaces métalliques de la jante, même dans les zones difficiles d’accès. Cette méthode garantit une couverture uniforme et permet d’atteindre des zones de la jante comme l’intérieur des rayons et les bords, qui seraient autrement difficiles à atteindre avec des méthodes de pulvérisation conventionnelles. Les cabines sont également conçues pour être faciles à nettoyer, ce qui est essentiel lorsque de la poudre de différentes couleurs est utilisée, surtout dans les grandes installations où des changements fréquents de couleur sont nécessaires.
Pistolets de revêtement en poudre pour roues et jantes
Les pistolets de pulvérisation pour le revêtement des roues et jantes en alliage sont des équipements clés dans le processus, car ils déterminent la précision et la qualité de l’application de la poudre. Les pistolets électrostatiques sont particulièrement efficaces pour ce type de finition, car la charge électrostatique qu’ils génèrent permet à la poudre de mieux adhérer aux surfaces métalliques des jantes, même si ces pièces présentent des formes complexes ou sont dotées de surfaces irrégulières. De plus, la technologie des pistolets modernes permet de contrôler finement la quantité de poudre projetée, la taille des particules et l’angle de pulvérisation, ce qui permet d’obtenir un revêtement uniforme et de haute qualité, sans perte excessive de matériau.
Les pistolets manuels et automatiques sont disponibles pour ce type d’application, avec des pistolets automatiques souvent utilisés dans les lignes de production à grande échelle où des volumes importants de roues et jantes doivent être traités rapidement. Les pistolets automatiques peuvent être intégrés dans des lignes de production robotisées, permettant une application de poudre constante et uniforme à grande vitesse. En revanche, les pistolets manuels sont idéaux pour des travaux plus spécialisés ou pour des petites séries où la personnalisation et l’attention aux détails sont essentielles.
Durabilité et performance des revêtements pour roues et jantes
Le processus de revêtement en poudre sur les roues et jantes en alliage offre plusieurs avantages en termes de durabilité et de résistance. Les revêtements en poudre créent une surface plus résistante aux rayures, à la rouille et à l’usure que les peintures liquides traditionnelles. Cela est particulièrement important pour les roues et jantes, qui sont exposées à des conditions de conduite rigoureuses, telles que les changements climatiques, les débris de la route, le sel utilisé en hiver, ainsi que l’humidité et les produits chimiques de lavage. En outre, les revêtements en poudre sont plus résistants aux rayons UV, ce qui empêche la décoloration ou le ternissement des jantes exposées au soleil.
Le revêtement en poudre peut également être formulé pour offrir des propriétés spéciales, comme une résistance améliorée aux produits chimiques ou une finition texturée qui masque les petites imperfections et améliore l’adhérence du revêtement. Par exemple, des poudres spécifiques peuvent être utilisées pour rendre le revêtement plus résistant aux effets de la chaleur générée par les freins, ce qui est essentiel pour les jantes de véhicules de performance.
Avantages environnementaux du revêtement en poudre pour roues et jantes
En plus de ses avantages en termes de durabilité et de performance, le revêtement en poudre est également plus respectueux de l’environnement par rapport aux méthodes de peinture traditionnelles. Il ne nécessite pas l’utilisation de solvants chimiques, ce qui réduit les émissions de composés organiques volatils (COV) et améliore la qualité de l’air dans les installations de production. De plus, la poudre excédentaire peut être récupérée et réutilisée, ce qui réduit les déchets et améliore l’efficacité globale du processus.
L’absence de solvants et la capacité de recycler la poudre excédentaire font de cette technologie une solution plus durable et écologique pour les fabricants de roues et jantes, qui doivent de plus en plus répondre aux exigences strictes en matière de réduction des émissions et de respect de l’environnement.
Conclusion
L’équipement de revêtement en poudre pour roues et jantes en alliage permet aux fabricants de produire des pièces non seulement esthétiques et résistantes, mais aussi respectueuses de l’environnement. En combinant des fours de revêtement, des systèmes de pulvérisation et des pistolets électrostatiques, ces équipements offrent une solution robuste et efficace pour créer des revêtements de haute qualité, capables de résister aux rigueurs de l’utilisation automobile. Avec les avantages en termes de durabilité, de performance, de flexibilité et d’impact environnemental réduit, le revêtement en poudre reste une technologie incontournable pour l’industrie automobile et autres secteurs nécessitant des revêtements de qualité supérieure pour des pièces métalliques complexes.
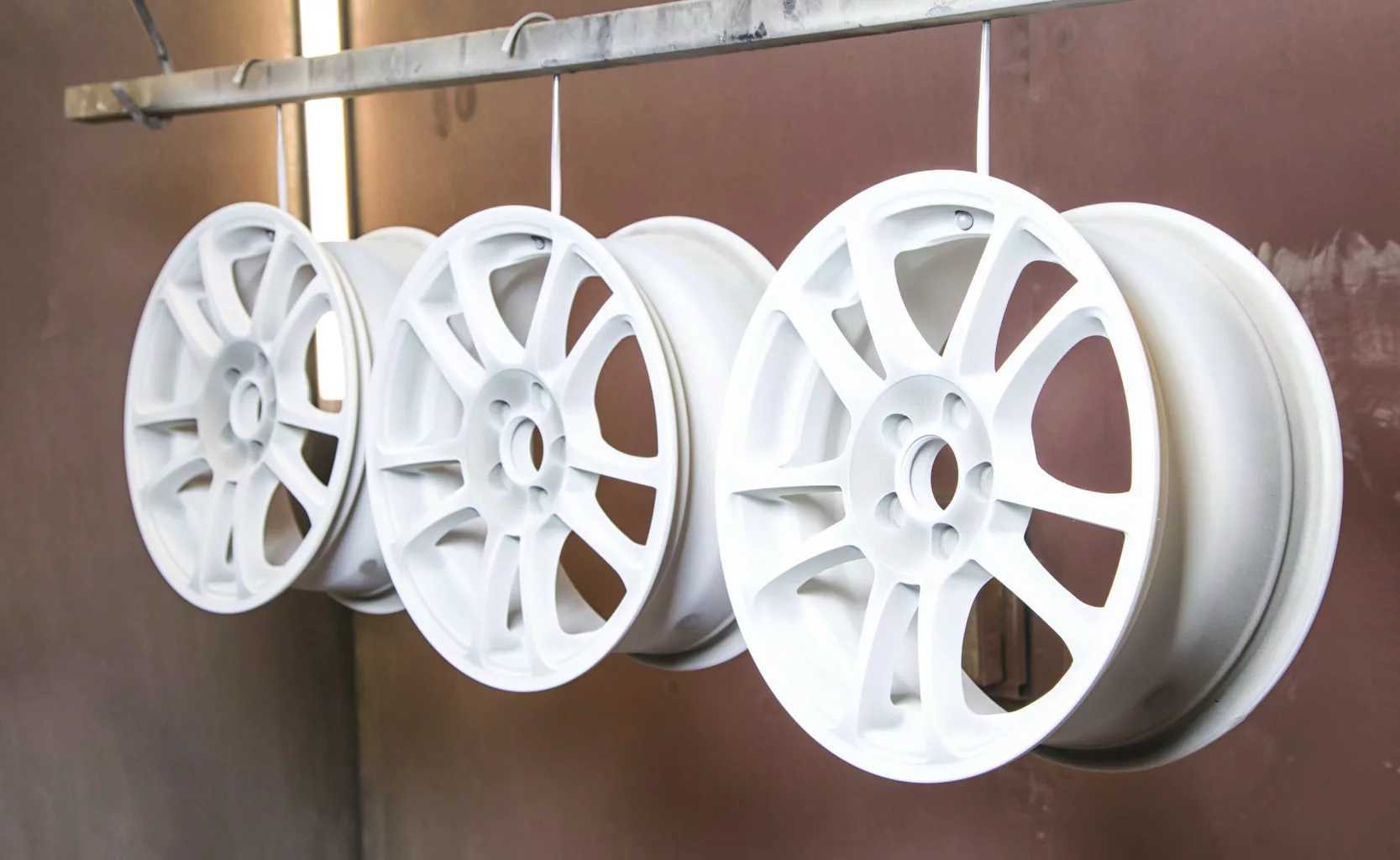
L’équipement de revêtement en poudre pour roues et jantes en alliage continue de transformer l’industrie automobile, offrant une finition de haute qualité qui combine esthétique et résistance. Ce processus est particulièrement prisé pour sa capacité à protéger les jantes contre les conditions climatiques sévères, la rouille, les rayures et l’usure, tout en maintenant une finition uniforme et durable. Le revêtement en poudre est appliqué sur les jantes en alliage à l’aide de divers équipements spécialisés, notamment des fours de revêtement, des cabines de pulvérisation et des pistolets électrostatiques, chacun étant conçu pour maximiser l’efficacité du processus tout en minimisant les pertes de matière.
Le four joue un rôle crucial en chauffant la poudre appliquée, permettant à celle-ci de fondre et de s’agglutiner de manière homogène sur la surface de la jante. L’application uniforme de la poudre est essentielle, notamment pour les pièces aux formes complexes, comme les jantes qui possèdent souvent des courbes et des crevasses difficiles à atteindre. Pour garantir un résultat parfait, les systèmes de pulvérisation électrostatique sont utilisés, car ils permettent à la poudre de mieux adhérer à la surface métallique, même dans les zones difficilement accessibles. L’électrostatique crée une charge qui attire la poudre, assurant ainsi une couverture uniforme.
La durabilité des revêtements en poudre est l’un de leurs atouts majeurs. Les jantes en alliage, exposées aux débris de la route, à l’humidité, au sel utilisé en hiver et à d’autres éléments agressifs, bénéficient grandement de l’application de cette technologie. Les revêtements en poudre sont non seulement résistants à la chaleur, mais aussi à la corrosion et aux rayures. Cela permet d’augmenter considérablement la longévité des jantes, tout en conservant leur apparence esthétique même après une utilisation prolongée dans des conditions difficiles.
En plus de leur résistance, les revêtements en poudre sont également plus écologiques que les méthodes traditionnelles de peinture, car ils ne nécessitent pas de solvants chimiques et génèrent moins de déchets. L’absence de composés organiques volatils (COV) contribue à améliorer la qualité de l’air et à réduire l’empreinte carbone des processus de fabrication. De plus, la possibilité de récupérer et de réutiliser la poudre excédentaire permet de rendre le processus encore plus économique et respectueux de l’environnement.
Le processus de revêtement en poudre pour les roues et jantes en alliage offre également une grande flexibilité. Les fabricants peuvent choisir parmi une large gamme de couleurs et de finitions, y compris des couleurs métalliques, mates ou brillantes, pour répondre aux exigences spécifiques des consommateurs et du marché. Cette diversité permet d’obtenir des résultats esthétiques très variés, tout en garantissant une qualité constante. Les revêtements en poudre peuvent être formulés pour offrir des propriétés spécifiques, comme une résistance accrue aux produits chimiques ou une finition texturée, selon les besoins particuliers des clients.
Les équipements de revêtement en poudre modernes sont conçus pour être plus efficaces, plus rapides et plus adaptés aux exigences de production à grande échelle. En intégrant des technologies avancées, telles que des systèmes de contrôle automatisés et des solutions de surveillance en temps réel, ces équipements permettent de maximiser l’efficacité de chaque cycle de production tout en assurant une qualité constante. Ces innovations permettent aux fabricants de produire des jantes avec des revêtements parfaitement uniformes et résistants tout en réduisant les coûts de production.
L’équipement de revêtement en poudre pour roues et jantes en alliage continue donc de jouer un rôle central dans l’industrie automobile et au-delà. Grâce à ses nombreux avantages, tels que la durabilité, la résistance, la flexibilité esthétique et l’impact environnemental réduit, il reste une solution privilégiée pour les fabricants de roues et jantes cherchant à offrir des produits de haute qualité. L’évolution des technologies de revêtement en poudre, avec des équipements toujours plus performants et adaptés aux besoins spécifiques de l’industrie, va sans aucun doute continuer à façonner l’avenir des finitions métalliques et à répondre aux exigences de plus en plus strictes en matière de qualité et d’environnement.
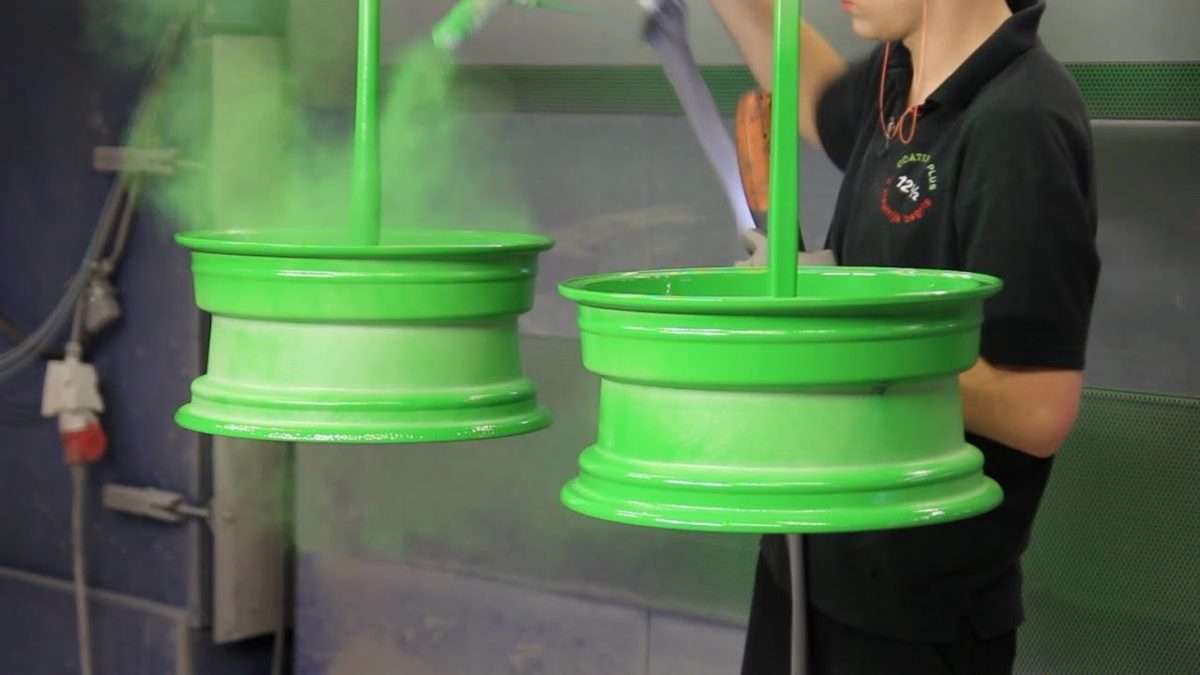
L’évolution continue de la technologie des équipements de revêtement en poudre permet d’élargir davantage les possibilités d’application dans des secteurs variés, tout en répondant à des critères de plus en plus exigeants en matière de durabilité et de performance. Le développement de nouveaux types de poudres spécifiquement adaptées aux roues et jantes en alliage permet d’augmenter encore la résistance aux conditions extrêmes. Par exemple, les formulations de poudre à base de polymères haute performance offrent des avantages considérables, telles que des revêtements anti-abrasion ou des finitions particulièrement résistantes aux impacts, ce qui est crucial pour les jantes exposées aux chocs fréquents, comme ceux rencontrés lors de la conduite sur des routes de mauvaise qualité.
En outre, les avancées dans la robotisation des lignes de production permettent d’automatiser le processus de pulvérisation et de cuisson, réduisant ainsi les erreurs humaines tout en augmentant la rapidité et l’efficacité des cycles de production. L’automatisation facilite également l’adaptation à des séries de production plus petites ou plus personnalisées, offrant ainsi une flexibilité accrue pour répondre aux demandes spécifiques des clients tout en maintenant une qualité constante.
Le contrôle numérique et informatique dans les équipements de revêtement en poudre permet une gestion de plus en plus précise des paramètres de production. Les systèmes de contrôle de la qualité automatisés surveillent en temps réel des critères tels que la température du four, la vitesse de la pulvérisation et l’épaisseur du revêtement, garantissant que chaque roue ou jante reçoive un traitement optimal. Cette précision est essentielle pour maintenir la constance de la finition sur chaque pièce, en particulier dans un environnement de production où les demandes de qualité sont élevées.
Les systèmes de nettoyage et de maintenance des équipements de revêtement en poudre ont également fait des progrès significatifs. Le nettoyage régulier des cabines de pulvérisation et des pistolets est crucial pour éviter toute contamination croisée entre différentes couleurs de poudre ou formulations chimiques. Les nouveaux systèmes de nettoyage automatisé permettent un entretien rapide et efficace, réduisant ainsi les temps d’arrêt et les coûts associés aux processus de maintenance. Par ailleurs, les capteurs et technologies de diagnostic à distance permettent de détecter rapidement les problèmes techniques avant qu’ils ne deviennent des défaillances majeures, garantissant une productivité optimale.
L’aspect environnemental reste au cœur des préoccupations des fabricants d’équipements de revêtement en poudre. En plus de l’absence de solvants chimiques et de la possibilité de récupérer la poudre excédentaire, les nouvelles technologies de recyclage de chaleur et de gestion des émissions contribuent à rendre les processus de fabrication encore plus respectueux de l’environnement. Par exemple, les fours à faible consommation d’énergie et les systèmes de ventilation améliorés permettent de minimiser les émissions de gaz à effet de serre tout en réduisant la consommation d’énergie.
L’innovation continue dans la formulation des poudres elle-même, avec des développements dans les revêtements à base de céramique ou de nanoparticules, permet de créer des revêtements offrant des propriétés encore plus avancées. Ces poudres techniques sont spécialement conçues pour augmenter la résistance thermique, l’adhérence ou la protection contre les produits chimiques, et elles répondent aux normes strictes de l’industrie automobile, où la performance et la durabilité des pièces sont primordiales. De telles innovations permettent également d’augmenter les capacités de personnalisation, en offrant des finitions spéciales qui répondent à des exigences de design spécifiques, comme des couleurs mates ou métalliques, des effets texturés ou même des finitions haute brillance qui répondent aux attentes des consommateurs.
À l’échelle mondiale, la demande de revêtements en poudre pour roues et jantes en alliage ne cesse de croître, particulièrement dans les marchés émergents où la demande pour des véhicules plus durables et esthétiques est en augmentation. Les innovations en matière de finition et de conception jouent un rôle crucial pour capter cette demande, en offrant des solutions de revêtement adaptées aux exigences locales tout en conservant les normes internationales de qualité.
Les équipements de revêtement en poudre pour roues et jantes en alliage ont ainsi un rôle clé dans la production de pièces automobiles de haute performance, durables et esthétiques. L’évolution des technologies permet de répondre à des besoins toujours plus sophistiqués, que ce soit en termes de design, de performance ou de respect de l’environnement. Grâce à ces avancées, le revêtement en poudre continue d’être une solution privilégiée pour les fabricants cherchant à allier innovation, durabilité et qualité tout en minimisant l’impact écologique de leurs processus de production. En offrant des produits finis résistants, de haute qualité et personnalisés, le revêtement en poudre pour roues et jantes en alliage s’impose comme une solution incontournable dans l’industrie automobile moderne.
Roues en alliage
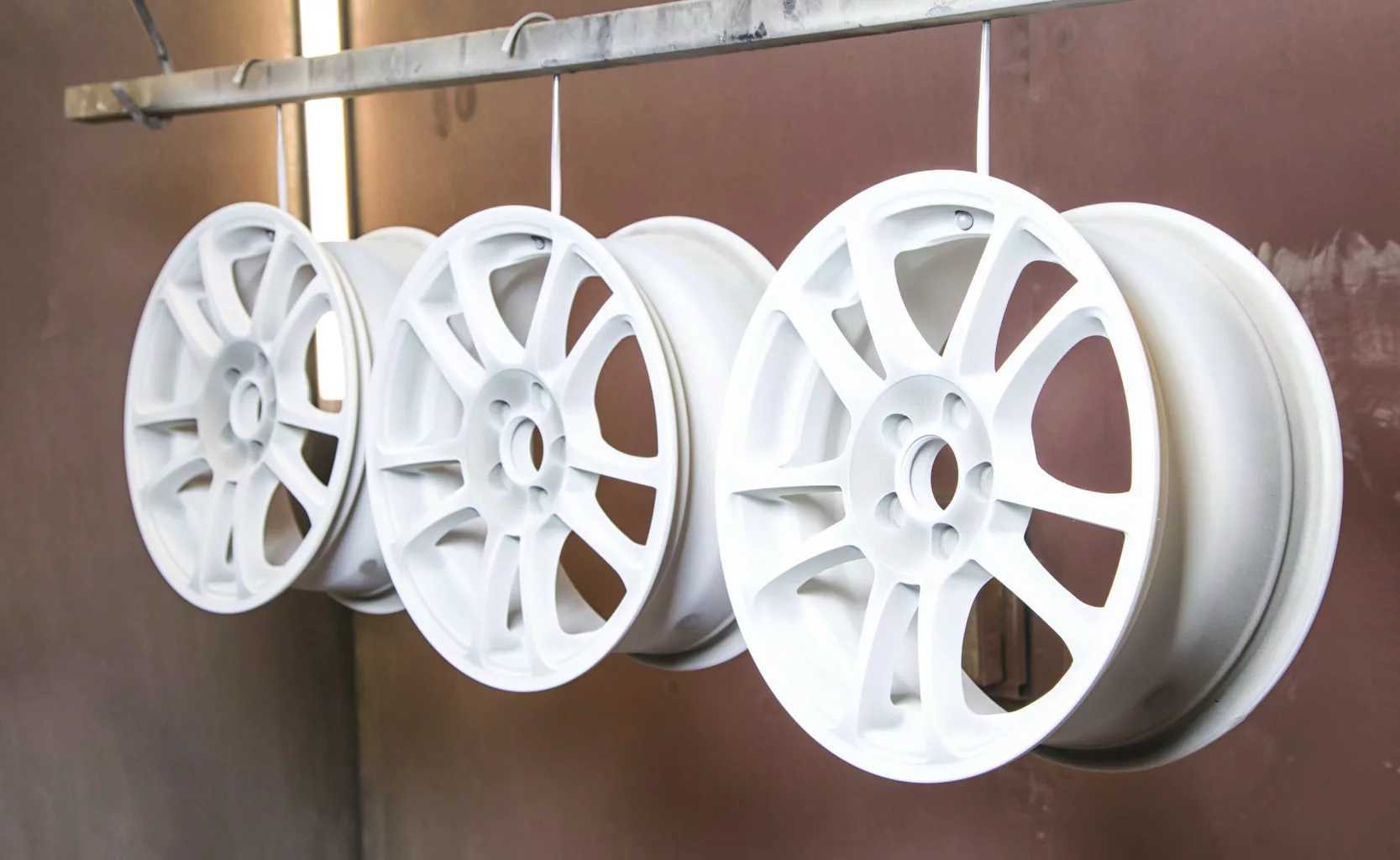
Les roues en alliage sont des composants de véhicules fabriqués à partir d’un alliage métallique léger, généralement constitué d’aluminium ou de magnésium et de traces d’autres métaux. Contrairement aux roues en acier traditionnelles, les roues en alliage offrent plusieurs avantages en termes de performance, de poids et d’esthétique.
L’utilisation d’alliages légers permet de réduire significativement le poids non suspendu du véhicule, améliorant ainsi la maniabilité, l’efficacité énergétique et la réponse de la suspension. De plus, les propriétés spécifiques des alliages utilisés dans la fabrication des roues en alliage offrent une résistance accrue à la corrosion, ce qui contribue à prolonger la durée de vie des roues et à maintenir leur apparence esthétique.
Les roues en alliage sont disponibles dans une variété de designs, de finitions et de tailles pour répondre aux besoins et aux préférences esthétiques des propriétaires de véhicules. Elles sont largement utilisées sur les voitures de tourisme, les véhicules tout-terrain, les motos et même les véhicules de compétition en raison de leur combinaison unique de légèreté, de résistance et de style.
Cependant, bien que les roues en alliage offrent de nombreux avantages, elles peuvent être plus coûteuses à fabriquer et à remplacer que les roues en acier. De plus, en raison de leur construction plus légère, elles peuvent être plus sensibles aux dommages causés par les nids-de-poule, les chocs et les conditions routières difficiles. Par conséquent, il est essentiel de les entretenir régulièrement et de les inspecter pour assurer leur bon fonctionnement et leur sécurité.
Jantes en Alliage
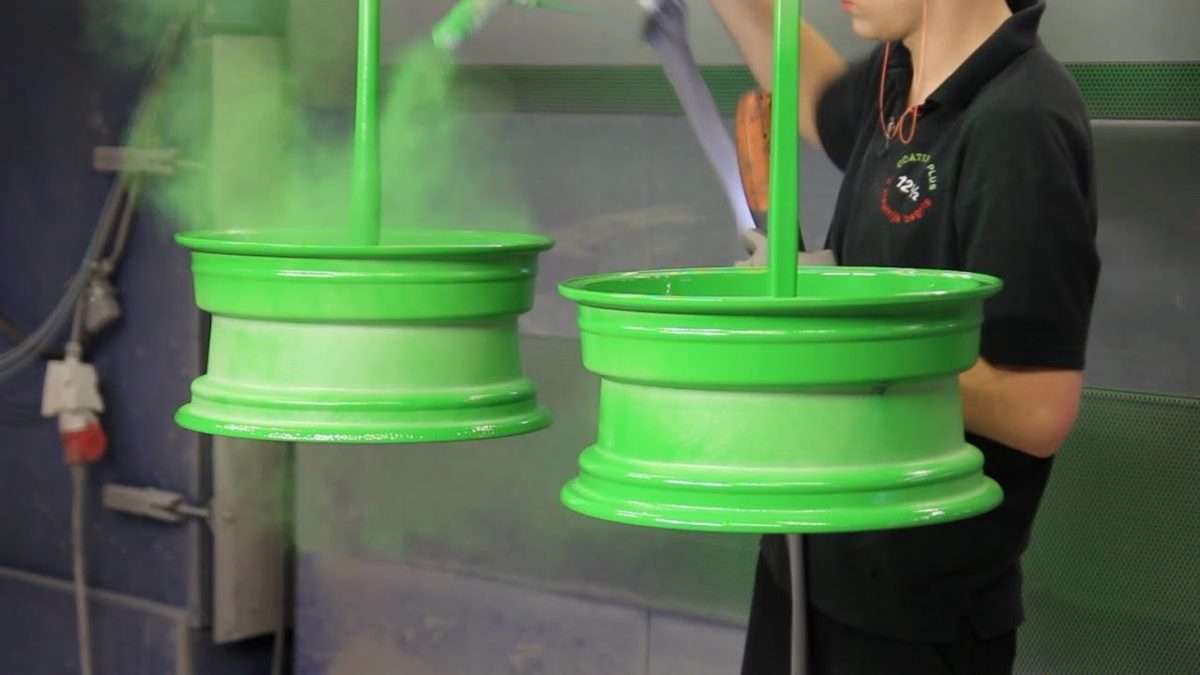
Les jantes en alliage sont des composants essentiels des roues de véhicules qui supportent le pneu et assurent sa fixation sur le moyeu de la voiture. Contrairement aux jantes en acier, qui sont fabriquées à partir de tôles d’acier embouties, les jantes en alliage sont réalisées à partir d’un alliage métallique léger, généralement de l’aluminium ou du magnésium, avec des propriétés spécifiques pour répondre aux exigences de performance et d’esthétique.
L’utilisation d’alliages légers dans la fabrication des jantes offre plusieurs avantages. Tout d’abord, cela contribue à réduire le poids non suspendu du véhicule, ce qui améliore la maniabilité, la tenue de route et l’économie de carburant. De plus, les jantes en alliage sont souvent conçues avec des motifs et des finitions esthétiques attrayants, ce qui permet aux propriétaires de personnaliser l’apparence de leur véhicule.
En termes de performance, les jantes en alliage offrent une meilleure dissipation de la chaleur que les jantes en acier, ce qui peut contribuer à une meilleure gestion de la température des freins, en particulier lors de la conduite à haute vitesse ou en conditions de conduite difficiles. De plus, les jantes en alliage sont généralement plus résistantes à la corrosion que les jantes en acier, ce qui prolonge leur durée de vie et maintient leur apparence esthétique au fil du temps.
Cependant, les jantes en alliage peuvent être plus coûteuses à fabriquer et à remplacer que les jantes en acier, et elles peuvent être plus sensibles aux dommages causés par les chocs et les nids-de-poule en raison de leur construction plus légère. Par conséquent, il est important de choisir des jantes en alliage de haute qualité et de les entretenir régulièrement pour assurer leur bon fonctionnement et leur durabilité.
Équipement de revêtement
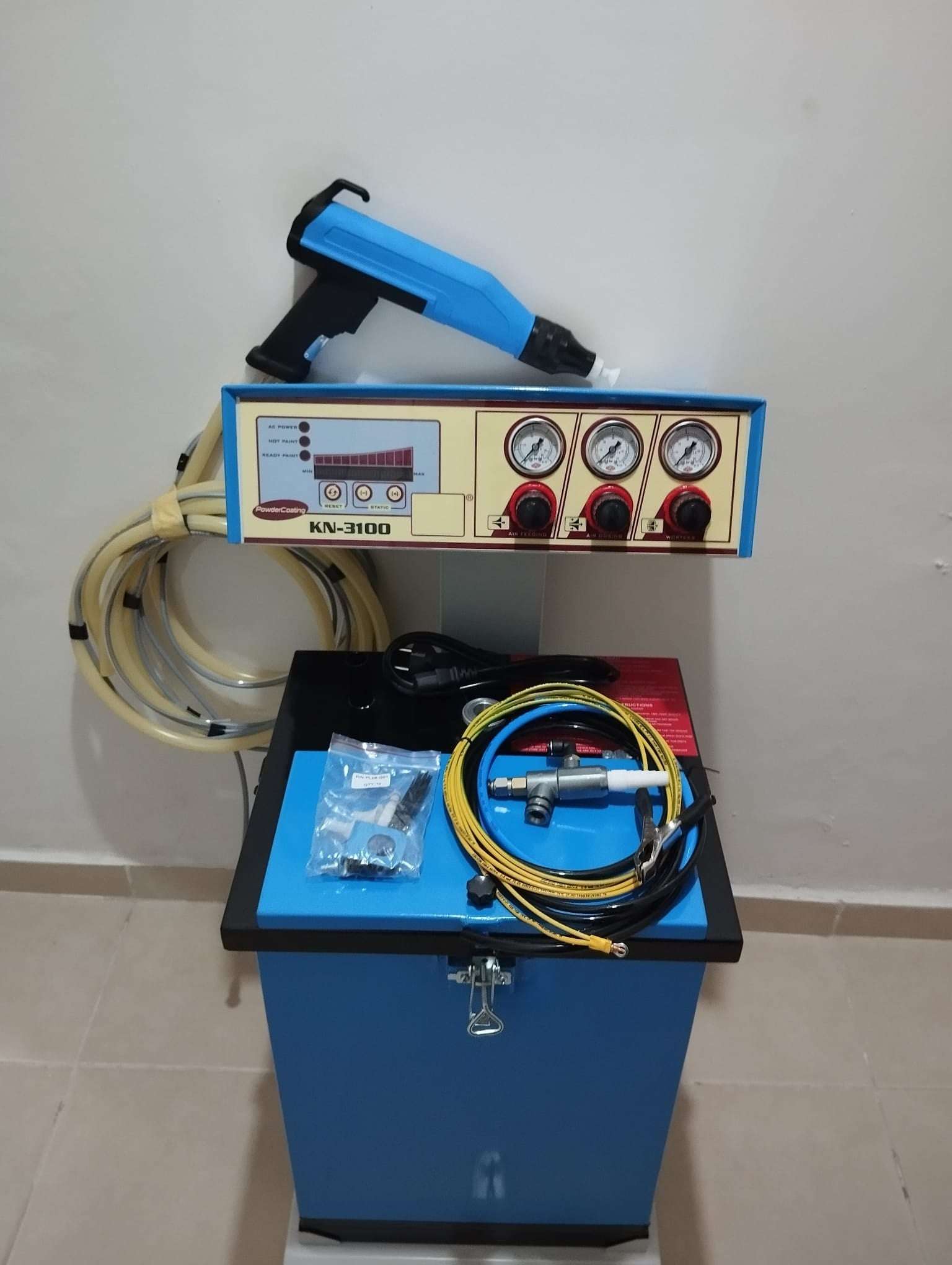
L’équipement de revêtement désigne l’ensemble des outils, machines et dispositifs utilisés dans le processus de revêtement, que ce soit pour l’application de peinture, de vernis, de revêtements en poudre ou d’autres types de revêtements sur divers substrats. Dans le contexte spécifique du revêtement en poudre pour les roues et les jantes en alliage, l’équipement de revêtement comprend généralement plusieurs éléments essentiels.
Tout d’abord, il y a le pistolet de pulvérisation, qui est l’outil principal utilisé pour appliquer la poudre de revêtement sur la surface des roues et des jantes. Ces pistolets peuvent être de différents types, tels que les pistolets de pulvérisation électrostatique qui chargent électriquement les particules de poudre pour assurer une adhérence optimale.
Ensuite, il y a le système de récupération de poudre, qui collecte l’excès de poudre non utilisée pendant le processus de pulvérisation afin de la réutiliser, réduisant ainsi les déchets et les coûts de matières premières.
De plus, l’équipement de revêtement comprend généralement un four de polymérisation, où les roues et les jantes revêtues de poudre sont chauffées à des températures élevées pour permettre à la poudre de fondre et de polymériser, formant ainsi un revêtement solide et durable.
Enfin, d’autres équipements tels que des cabines de pulvérisation, des systèmes de filtration d’air et des équipements de manipulation des pièces peuvent également faire partie de l’équipement de revêtement, contribuant à assurer un processus de revêtement efficace, sûr et de haute qualité.
Dans l’ensemble, un équipement de revêtement bien conçu et correctement utilisé est essentiel pour garantir la qualité, la durabilité et l’esthétique des revêtements appliqués sur les roues et les jantes en alliage, tout en maximisant l’efficacité opérationnelle et en réduisant les coûts de production.
Équipement de revêtement
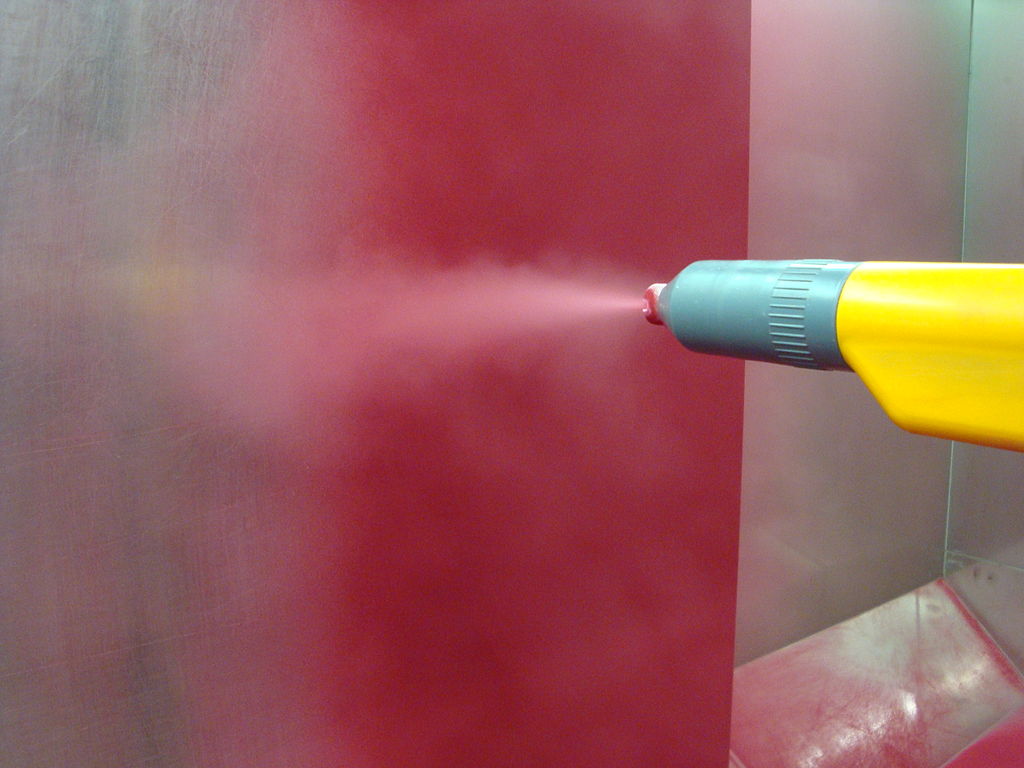
L’équipement de revêtement en poudre joue un rôle fondamental dans de nombreuses industries, notamment dans la fabrication de composants automobiles, d’articles électroménagers, de meubles métalliques et d’autres produits nécessitant une finition durable et esthétique. Ce processus de revêtement est utilisé pour appliquer une fine couche de poudre sur une surface métallique ou autre, qui est ensuite durcie sous l’effet de la chaleur, créant ainsi un revêtement solide et résistant. L’équipement utilisé pour ce type de revêtement comprend des fours de durcissement, des cabines de pulvérisation, des pistolets électrostatiques et des systèmes de filtration et de récupération de la poudre.
Le four de revêtement en poudre est l’élément central du processus. Après l’application de la poudre sur la pièce, celle-ci est chauffée dans un four pour fondre et adhérer uniformément à la surface. Ce four peut être conçu pour différents types de revêtements, tels que des poudres époxy, polyester ou hybrides, et il est équipé de systèmes de contrôle de température précis pour assurer que la poudre soit correctement durcie sans endommager la pièce. L’efficacité énergétique des fours modernes est une priorité, avec des modèles utilisant des technologies de récupération thermique et de gestion de l’énergie pour réduire la consommation et l’impact environnemental.
Les cabines de pulvérisation sont des espaces où la poudre est projetée sur les pièces à l’aide de pistolets de pulvérisation électrostatiques. Ces pistolets chargent électriquement la poudre, ce qui permet à celle-ci d’adhérer plus facilement à la surface métallique de la pièce. Les cabines de pulvérisation sont équipées de systèmes de filtration de l’air et de récupération de la poudre excédentaire, ce qui permet de minimiser la perte de matière et de rendre le processus plus économique et respectueux de l’environnement.
Les pistolets de pulvérisation électrostatiques sont utilisés pour appliquer la poudre de manière uniforme et précise sur les surfaces à revêtir. Ces pistolets fonctionnent en générant un champ électrostatique qui charge les particules de poudre, créant une attraction vers la surface métallique à revêtir. Ce procédé permet d’obtenir une couverture homogène, même sur des surfaces complexes ou irrégulières, et garantit une excellente adhésion du revêtement.
Enfin, les systèmes de filtration et de récupération de la poudre jouent un rôle clé dans l’efficacité et la durabilité du processus. La poudre non utilisée est récupérée à travers des filtres et peut être réutilisée, ce qui réduit le gaspillage et diminue les coûts des matériaux. Ces systèmes contribuent également à maintenir un environnement de travail propre et sûr en éliminant la poudre excédentaire de l’air dans les cabines de pulvérisation.
L’équipement de revêtement en poudre a évolué au fil des années pour devenir plus efficace, plus écologique et plus adapté aux besoins de production à grande échelle. Les équipements modernes sont souvent automatisés et peuvent intégrer des technologies avancées, telles que la robotisation, les systèmes de contrôle numérique, et des diagnostics en temps réel, ce qui permet de maximiser la productivité tout en maintenant une qualité de finition constante.

L’évolution continue de l’équipement de revêtement en poudre permet de répondre à des demandes toujours plus complexes, tout en optimisant les processus de production. Un des principaux axes d’amélioration réside dans l’automatisation et la robotisation des lignes de revêtement, qui permettent d’accroître la vitesse et la précision des applications tout en réduisant l’intervention humaine. Les robots de pulvérisation sont de plus en plus utilisés pour appliquer la poudre sur des pièces de tailles variées, offrant une couverture uniforme et une réduction des erreurs humaines. Ces robots peuvent être programmés pour ajuster la quantité de poudre appliquée, la vitesse de pulvérisation et l’angle de projection, ce qui garantit un résultat constant et de haute qualité, même sur des pièces de forme complexe.
Un autre aspect fondamental de l’équipement de revêtement en poudre moderne est l’amélioration de la gestion thermique dans les fours de durcissement. Les fours à convection forcée et les fours à circulation d’air optimisés permettent de maintenir une température stable et uniforme à travers tout le four, assurant ainsi que la poudre adhère correctement à la pièce et qu’aucune partie ne soit surchauffée ou mal durcie. Ces systèmes modernes sont également équipés de technologies de récupération thermique, ce qui permet de réutiliser la chaleur générée pendant le processus, réduisant ainsi la consommation énergétique et les coûts de production.
Les technologies de contrôle avancé sont devenues indispensables pour garantir la performance de l’équipement de revêtement en poudre. Les systèmes de contrôle numérique permettent aux opérateurs de suivre et de gérer l’ensemble du processus de revêtement en temps réel, ajustant les paramètres de pulvérisation, de température et de durée de durcissement pour optimiser les résultats. Ces contrôles permettent également de surveiller la qualité du revêtement, en mesurant des critères comme l’épaisseur du film de poudre, la régularité de l’application et la finition de surface. En outre, les équipements peuvent être équipés de systèmes de surveillance de la qualité intégrés, qui détectent immédiatement toute irrégularité ou défaut dans le processus de pulvérisation ou de durcissement, garantissant ainsi que chaque pièce est conforme aux normes de qualité strictes.
Le nettoyage et l’entretien des équipements de revêtement en poudre sont également des domaines clés d’amélioration. Les nouvelles générations de systèmes de nettoyage automatisé permettent de maintenir les cabines de pulvérisation et les pistolets en parfait état de fonctionnement avec une intervention minimale. Ce nettoyage automatisé est crucial pour éviter la contamination des couleurs de poudre ou l’accumulation de résidus qui pourrait nuire à la qualité du revêtement. Le nettoyage rapide et efficace des équipements contribue également à réduire les temps d’arrêt et à maintenir une production continue. Les systèmes de filtration dans les cabines de pulvérisation ont également été améliorés pour récupérer encore plus efficacement la poudre excédentaire, permettant ainsi un recyclage maximal et réduisant les déchets, ce qui est essentiel dans une perspective environnementale et économique.
Du côté de la durabilité et de l’impact environnemental, l’équipement de revêtement en poudre a évolué pour devenir de plus en plus respectueux de l’environnement. En plus de l’absence de solvants chimiques, qui est un des avantages majeurs du revêtement en poudre, les nouvelles technologies permettent de limiter les émissions de gaz à effet de serre et de réduire les consommations d’eau et d’énergie. Les systèmes de gestion des émissions et de filtration améliorée dans les cabines de pulvérisation aident à garder l’air de travail propre et à respecter les normes environnementales strictes. L’optimisation de la récupération de la poudre excédentaire permet également de limiter les pertes et de recycler une grande partie des matériaux, contribuant ainsi à une production plus durable.
En outre, la diversité des poudres disponibles pour le revêtement a considérablement évolué, offrant des solutions de plus en plus spécialisées pour répondre à des besoins spécifiques en matière de résistance, d’esthétique et de durabilité. Des poudres à base de polymères haute performance, de céramique, ou même de nanoparticules permettent de créer des revêtements résistants à la chaleur extrême, aux produits chimiques ou à l’abrasion. Ces innovations ouvrent de nouvelles possibilités dans des secteurs comme l’aérospatiale, l’automobile, l’industrie électronique et bien d’autres, où des performances spécifiques sont requises.
Les finitions offertes par le revêtement en poudre ont également évolué pour répondre aux attentes croissantes des consommateurs en termes d’esthétique. Des finitions métalliques, texturées, mattes ou brillantes peuvent être obtenues, ainsi que des effets spéciaux, tels que des couleurs à effet perlé ou irisé. Ces finitions sont non seulement esthétiques mais offrent également des propriétés supplémentaires comme une meilleure résistance aux rayons UV, une protection contre la rouille et une meilleure protection contre les rayures.
En conclusion, l’équipement de revêtement en poudre est en constante évolution pour répondre aux exigences croissantes de performance, de durabilité et d’efficacité dans une variété d’industries. Grâce à l’intégration de technologies avancées, l’automatisation accrue, et une attention constante à la durabilité environnementale, les processus de revêtement en poudre continuent de jouer un rôle essentiel dans la fabrication de pièces métalliques et autres composants, tout en offrant des solutions esthétiques et résistantes aux défis contemporains.
Revêtement de surface
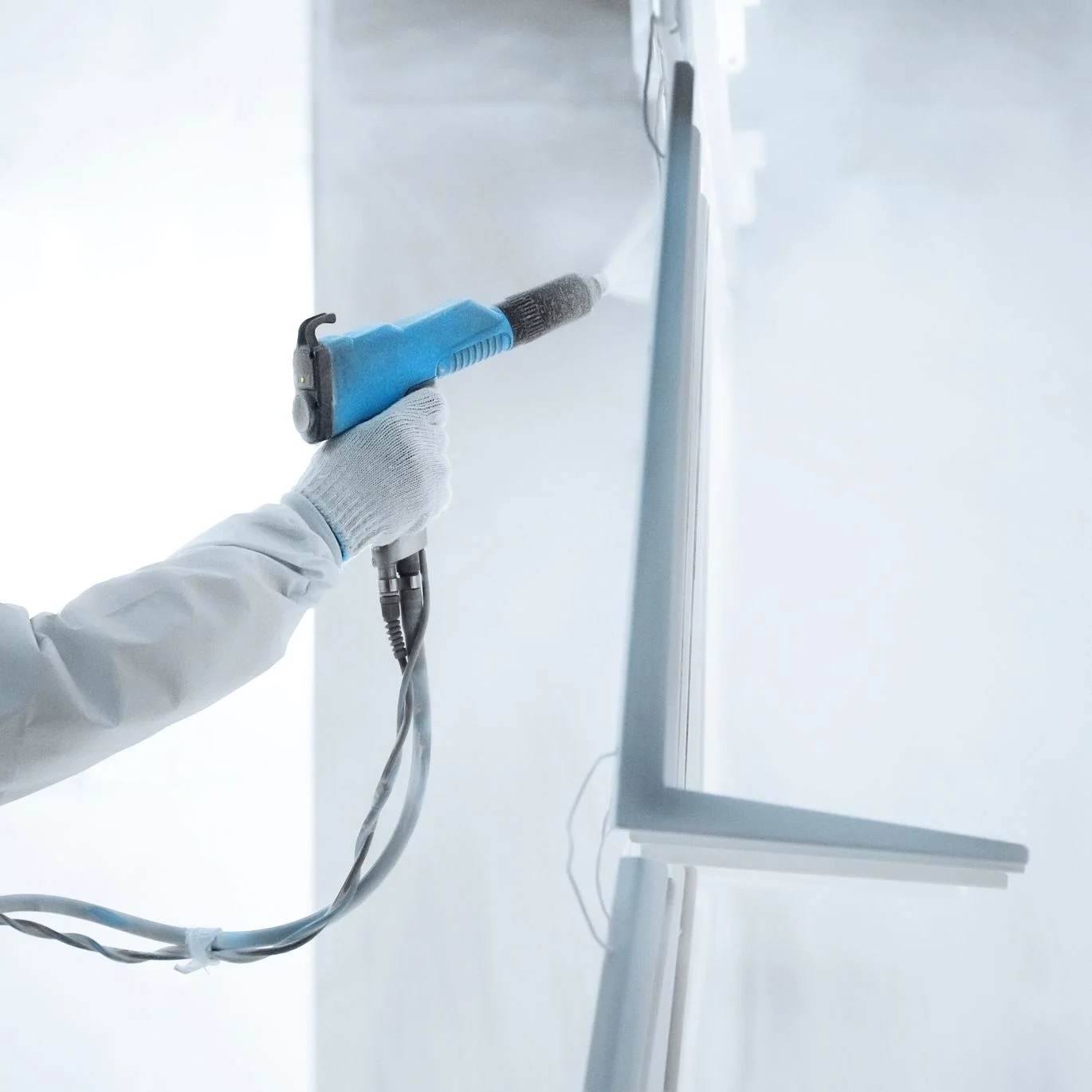
Le revêtement de surface est un processus appliqué à divers matériaux et produits pour améliorer leurs propriétés physiques, chimiques et esthétiques. Dans le contexte des roues et des jantes en alliage, le revêtement de surface joue un rôle crucial pour assurer la durabilité, la résistance à la corrosion et l’esthétique des composants.
Le revêtement de surface peut être réalisé à l’aide de différentes techniques, telles que la peinture, la galvanisation, l’anodisation et le revêtement en poudre. Chaque méthode offre des avantages spécifiques en termes de performance et d’aspect final.
Dans le cas du revêtement en poudre, une fine couche de poudre de revêtement est appliquée sur la surface préparée des roues et des jantes en alliage. Cette poudre est ensuite fondue et polymérisée à haute température pour former un revêtement durable et uniforme. Le revêtement en poudre offre une excellente adhérence, une résistance élevée à la corrosion et une large gamme de finitions esthétiques.
Outre la protection contre la corrosion et les intempéries, le revêtement de surface peut également être utilisé pour améliorer d’autres propriétés des roues et des jantes en alliage, telles que la conductivité électrique, la résistance à l’abrasion et la facilité de nettoyage.
En résumé, le revêtement de surface joue un rôle essentiel dans la fabrication et la finition des roues et des jantes en alliage, assurant à la fois leur durabilité et leur esthétique tout en répondant aux exigences spécifiques de performance et de fonctionnalité.
Processus de revêtement
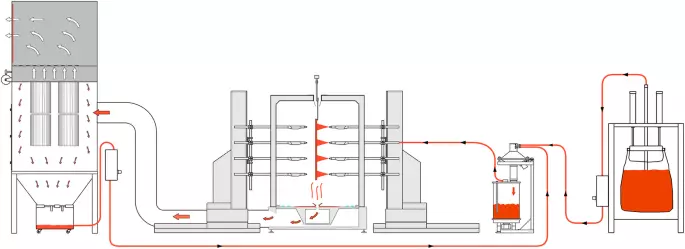
Le processus de revêtement fait référence à l’ensemble des étapes et des opérations nécessaires pour appliquer un revêtement protecteur ou décoratif sur la surface des roues et des jantes en alliage. Ce processus implique plusieurs étapes clés, chacune jouant un rôle crucial dans la qualité et la durabilité du revêtement final.
La première étape du processus de revêtement consiste généralement à préparer la surface des roues et des jantes en alliage. Cela peut inclure le nettoyage, le dégraissage et le décapage pour éliminer les contaminants et assurer une adhérence optimale du revêtement.
Une fois la surface préparée, la poudre de revêtement est appliquée à l’aide d’un équipement de pulvérisation spécialisé, tel qu’un pistolet de pulvérisation électrostatique. La poudre est généralement chargée électriquement pour assurer une adhérence uniforme et une couverture complète de la surface.
Après l’application de la poudre, les roues et les jantes en alliage sont placées dans un four de polymérisation, où elles sont chauffées à des températures élevées pour permettre à la poudre de fondre et de polymériser. Ce processus de fusion crée un revêtement solide, durable et uniforme sur la surface des roues et des jantes.
Une fois le processus de polymérisation terminé, les roues et les jantes revêtues sont généralement refroidies, inspectées et éventuellement soumises à des opérations supplémentaires, telles que le sablage ou le polissage, pour améliorer encore l’aspect final du revêtement.
En résumé, le processus de revêtement est une série d’étapes précises et contrôlées qui garantissent l’application efficace d’un revêtement de qualité sur les roues et les jantes en alliage, assurant ainsi leur durabilité, leur résistance et leur esthétique.
Application de poudre
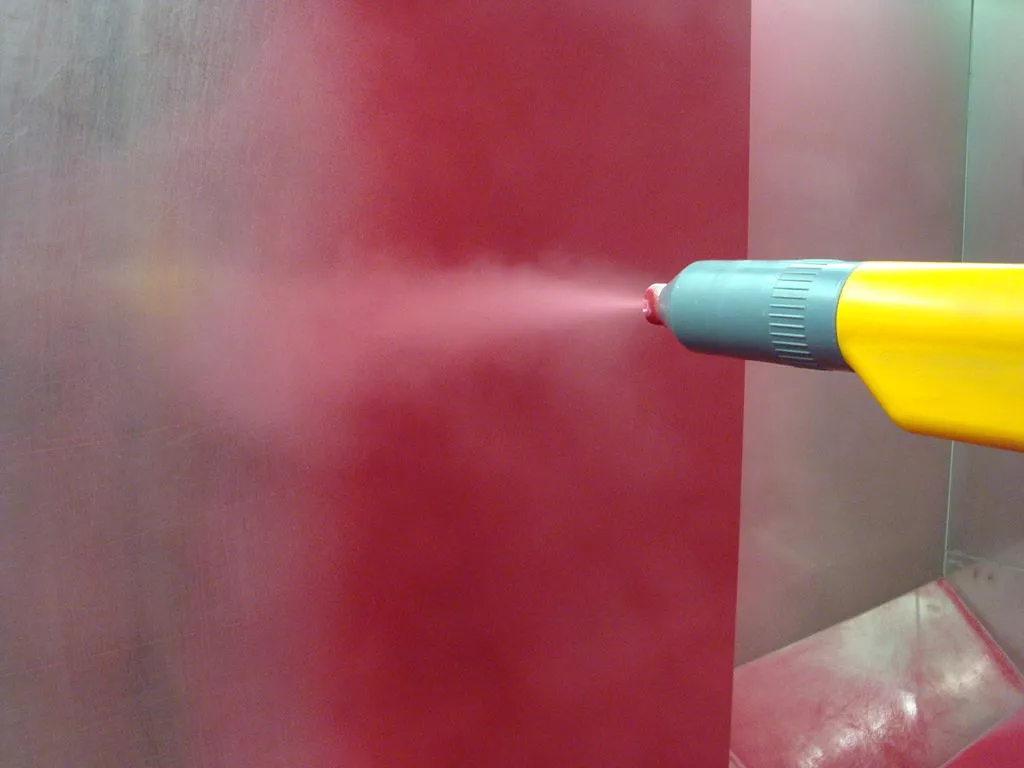
L’application de poudre est une étape cruciale du processus de revêtement en poudre des roues et des jantes en alliage. Ce processus implique l’utilisation d’un équipement spécialisé pour appliquer uniformément une fine couche de poudre de revêtement sur la surface préparée des composants.
Pour commencer, la poudre de revêtement est chargée dans un réservoir ou une trémie, prête à être pulvérisée. Le pistolet de pulvérisation, souvent un pistolet électrostatique, est utilisé pour projeter la poudre sur la surface des roues et des jantes.
Lors de l’application, la poudre est chargée électriquement, ce qui lui permet d’être attirée magnétiquement vers la surface métallique des composants. Cette charge électrostatique favorise une adhérence uniforme de la poudre sur toute la surface, y compris les zones difficiles d’accès ou les creux.
Une fois la poudre appliquée, les roues et les jantes revêtues sont généralement transportées vers un four de polymérisation, où elles sont chauffées à des températures élevées. Cela permet à la poudre de fondre et de se lier chimiquement pour former un revêtement solide et durable.
L’application de poudre offre plusieurs avantages par rapport à d’autres méthodes de revêtement, notamment une application plus uniforme, une adhérence améliorée, une faible émission de composés organiques volatils (COV) et une capacité à couvrir efficacement les contours complexes des roues et des jantes.
En résumé, l’application de poudre est une étape critique du processus de revêtement en poudre, assurant une couverture uniforme et une adhérence optimale de la poudre sur les roues et les jantes en alliage, ce qui garantit un revêtement de qualité, durable et esthétique.
Procédé de revêtement en poudre
Le procédé de revêtement en poudre est une méthode de finition de surface qui implique l’application d’une fine couche de poudre de revêtement sur les roues et les jantes en alliage. Ce procédé comprend plusieurs étapes distinctes, chacune jouant un rôle crucial dans la création d’un revêtement de qualité durable et esthétique.
La première étape du procédé de revêtement en poudre est la préparation de la surface des roues et des jantes en alliage. Cela implique généralement le nettoyage, le dégraissage et le décapage pour éliminer toute trace de contaminants et assurer une adhérence optimale du revêtement.
Une fois la surface préparée, la poudre de revêtement est appliquée à l’aide d’un équipement spécialisé, tel qu’un pistolet de pulvérisation électrostatique. Cette poudre est généralement composée de résines thermodurcissables, de pigments et d’additifs, et est chargée électriquement pour assurer une adhérence uniforme sur toute la surface.
Après l’application de la poudre, les roues et les jantes revêtues sont placées dans un four de polymérisation, où elles sont chauffées à des températures élevées. Cela permet à la poudre de fondre et de se lier chimiquement pour former un revêtement solide et durable.
Une fois le processus de polymérisation terminé, les roues et les jantes revêtues sont refroidies, inspectées et éventuellement soumises à des opérations supplémentaires, telles que le sablage ou le polissage, pour améliorer l’aspect final du revêtement.
En résumé, le procédé de revêtement en poudre est une méthode efficace et durable pour protéger et embellir les roues et les jantes en alliage. En combinant une préparation minutieuse de la surface, une application précise de la poudre et une polymérisation contrôlée, ce procédé garantit la création de revêtements de haute qualité qui résistent aux intempéries, à la corrosion et à l’usure.
Équipement de pulvérisation de poudre
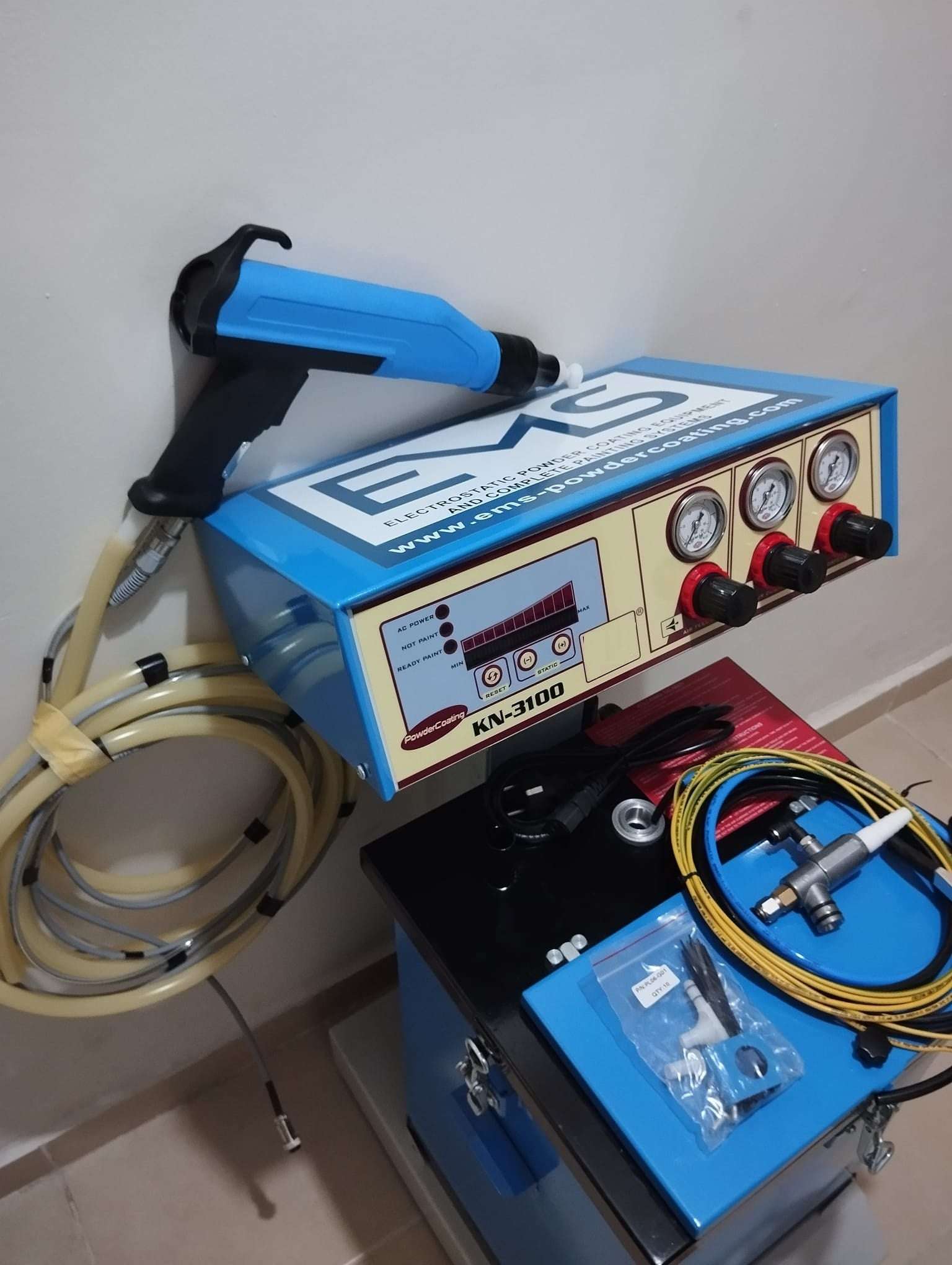
L’équipement de pulvérisation de poudre est une composante essentielle du processus de revêtement en poudre des roues et des jantes en alliage. Il est spécialement conçu pour appliquer de manière précise et uniforme la poudre de revêtement sur la surface des composants.
Cet équipement se compose généralement d’un pistolet de pulvérisation, d’une source de poudre, d’un système de transport de poudre et parfois d’un dispositif de récupération de poudre.
Le pistolet de pulvérisation est l’élément central de l’équipement. Il est conçu pour projeter la poudre de revêtement sur la surface des roues et des jantes de manière contrôlée. Différents types de pistolets de pulvérisation sont disponibles, notamment les pistolets électrostatiques qui chargent électriquement les particules de poudre pour assurer une adhérence optimale.
La source de poudre fournit un approvisionnement constant en poudre de revêtement au pistolet de pulvérisation. La poudre peut être stockée dans une trémie ou un réservoir et être acheminée vers le pistolet par un système de transport, tel qu’un système de fluidisation ou de transport pneumatique.
En outre, certains équipements de pulvérisation de poudre sont équipés d’un dispositif de récupération de poudre. Ce dispositif permet de collecter l’excès de poudre non utilisée pendant le processus de pulvérisation, ce qui permet de réduire les déchets et d’optimiser l’utilisation de la poudre.
L’équipement de pulvérisation de poudre joue un rôle crucial dans la qualité et la précision du revêtement en poudre des roues et des jantes en alliage. En utilisant des technologies avancées de pulvérisation et de contrôle, cet équipement permet d’obtenir des revêtements uniformes, durables et esthétiques qui répondent aux exigences les plus élevées en termes de performance et d’apparence.
Finition des roues
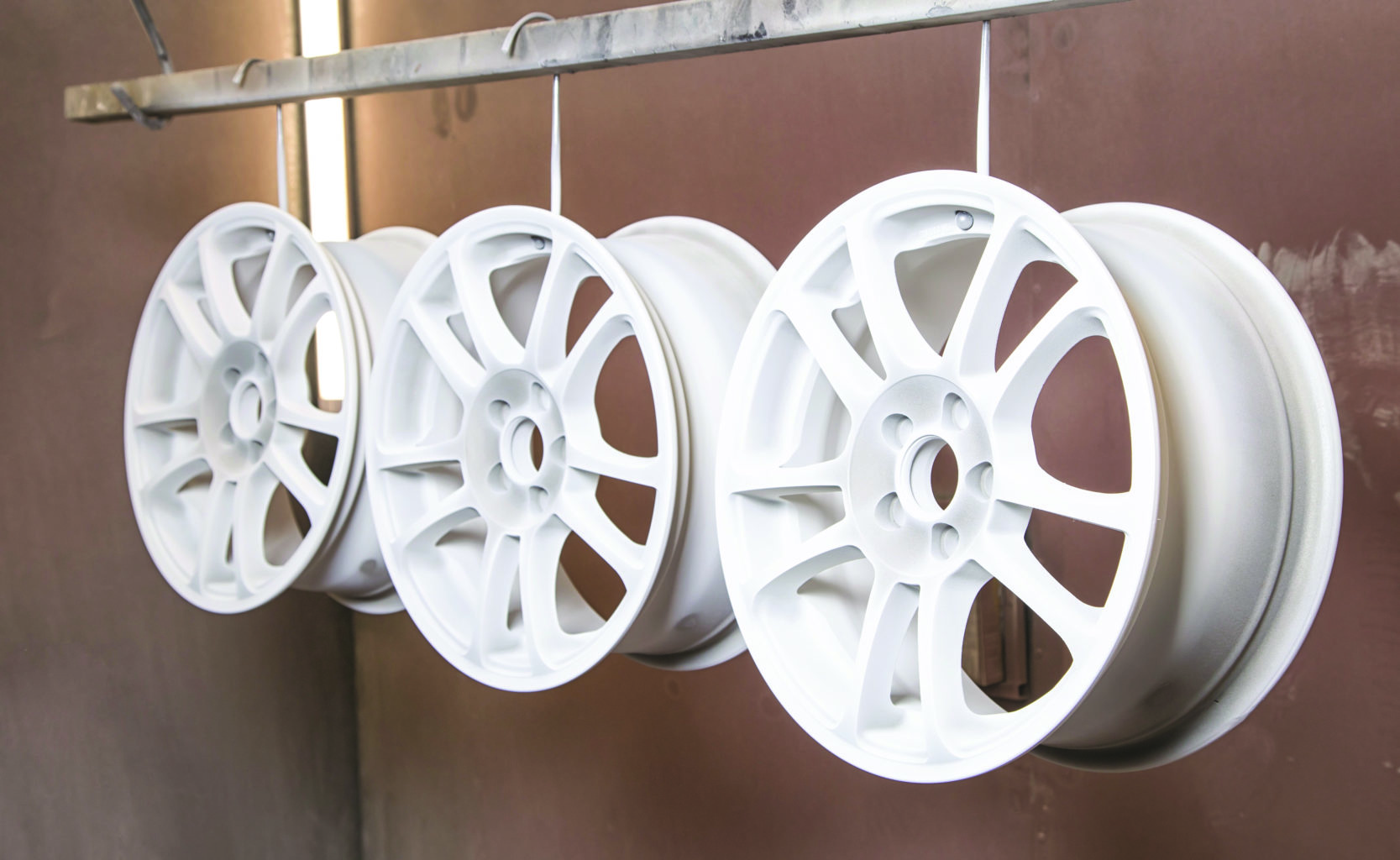
La finition des roues fait référence aux processus et techniques utilisés pour améliorer l’aspect esthétique des roues en alliage après leur fabrication ou leur réparation. Ces processus visent à donner aux roues une apparence attrayante tout en assurant leur protection contre la corrosion, les rayures et d’autres dommages.
Il existe plusieurs méthodes de finition des roues, chacune offrant des résultats esthétiques uniques :
- Peinture : La peinture est l’une des méthodes les plus courantes de finition des roues. Elle permet de créer une gamme infinie de couleurs et de finitions, du brillant au mat, en passant par le métallisé. La peinture protège également les roues contre la corrosion et les dommages causés par les intempéries.
- Polissage : Le polissage consiste à lisser la surface des roues pour leur donner un aspect brillant et lisse. Cette méthode est souvent utilisée pour les roues chromées ou en aluminium poli, et elle peut être complétée par un revêtement protecteur pour prévenir la corrosion.
- Anodisation : L’anodisation est un processus électrochimique qui crée une couche protectrice d’oxyde sur la surface des roues en aluminium. Cette couche peut être teintée dans une variété de couleurs et offre une excellente résistance à la corrosion et à l’abrasion.
- Revêtement en poudre : Le revêtement en poudre est une méthode de finition durable qui implique l’application d’une couche de poudre de revêtement sur la surface des roues, suivie d’une polymérisation à haute température pour former un revêtement solide et uniforme.
Chaque méthode de finition des roues présente ses propres avantages et inconvénients en termes de coût, de durabilité et d’esthétique. Le choix de la méthode appropriée dépendra des préférences esthétiques du propriétaire, ainsi que des conditions environnementales et d’utilisation auxquelles les roues seront exposées.
Cabine de Poudrage
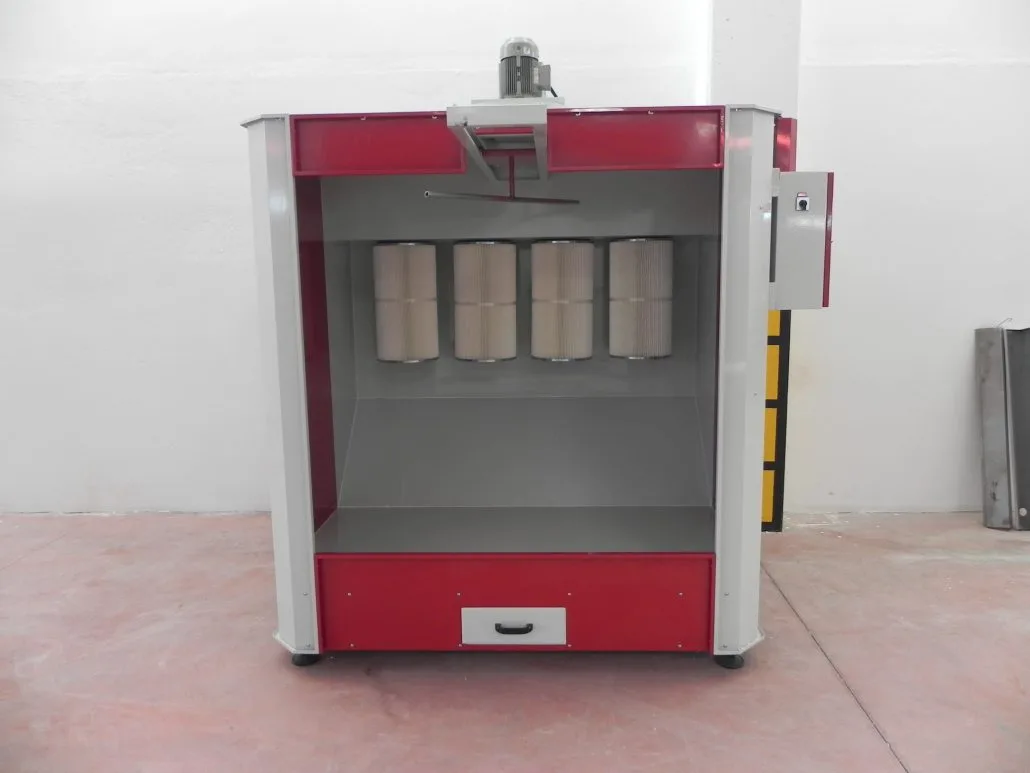
Une cabine de poudrage est une enceinte fermée dans laquelle une peinture poudre est appliquée sur une pièce. La peinture poudre est une peinture sèche qui est appliquée sous forme de particules fines. Elle est ensuite cuite à une température élevée pour fondre les particules et créer une couche de peinture solide.
Les cabines de poudrage sont utilisées dans une variété d’industries, notamment l’automobile, l’aéronautique, l’électronique et le mobilier. Elles permettent d’appliquer une peinture poudre de manière uniforme et précise, ce qui donne un résultat de qualité supérieure.
Une cabine de poudrage est composée des éléments suivants
- Une enceinte : l’enceinte est la structure qui entoure la pièce à peindre. Elle est généralement en acier ou en aluminium.
- Un système de ventilation : le système de ventilation aspire l’air de l’enceinte et le filtre pour éliminer les particules de peinture.
- Un pistolet de pulvérisation : le pistolet de pulvérisation est utilisé pour appliquer la peinture poudre sur la pièce.
- Un système de chauffage : le système de chauffage cuit la peinture poudre pour la solidifier.
Le fonctionnement d’une cabine de poudrage est le suivant :
- La pièce à peindre est placée dans l’enceinte.
- Le système de ventilation est mis en marche pour aspirer l’air de l’enceinte.
- Le pistolet de pulvérisation est utilisé pour appliquer la peinture poudre sur la pièce.
- Le système de chauffage est mis en marche pour cuire la peinture poudre.
Une fois la peinture poudre cuite, la pièce est prête à être retirée de la cabine.
Les cabines de poudrage sont disponibles dans une variété de tailles et de configurations. La taille de la cabine doit être adaptée aux dimensions des pièces à peindre. La configuration de la cabine dépend du type de pièces à peindre et du système de ventilation utilisé.
Les cabines de poudrage sont des équipements importants pour les industries qui utilisent la peinture poudre. Elles permettent d’appliquer une peinture poudre de manière uniforme et précise, ce qui donne un résultat de qualité supérieure.
Types de cabines de poudrage
Il existe deux principaux types de cabines de poudrage : les cabines ouvertes et les cabines fermées.
- Les cabines ouvertes sont les plus simples et les moins coûteuses. Elles sont composées d’une enceinte ouverte et d’un système de ventilation. Les pièces à peindre sont placées dans l’enceinte et le pistolet de pulvérisation est utilisé pour appliquer la peinture poudre. L’air de l’enceinte est ensuite aspiré par le système de ventilation et filtré pour éliminer les particules de peinture.
- Les cabines fermées sont plus complexes et plus coûteuses que les cabines ouvertes. Elles sont composées d’une enceinte fermée, d’un système de ventilation et d’un système de compensation. Les pièces à peindre sont placées dans l’enceinte et le pistolet de pulvérisation est utilisé pour appliquer la peinture poudre. L’air de l’enceinte est ensuite aspiré par le système de ventilation et filtré pour éliminer les particules de peinture. Le système de compensation permet de maintenir une pression positive dans l’enceinte, ce qui empêche les particules de peinture de s’échapper.
La cabine de poudrage est un élément clé de l’équipement utilisé dans le processus de revêtement en poudre. C’est dans cette cabine que la poudre est appliquée sur la surface des pièces à traiter. Les cabines de poudrage modernes sont conçues pour optimiser l’efficacité de la pulvérisation tout en garantissant un environnement de travail propre et sécurisé. Elles sont dotées de plusieurs fonctionnalités avancées qui assurent une application uniforme de la poudre et permettent une récupération efficace de la poudre excédentaire pour réduire les pertes et améliorer l’efficacité économique du processus.
Fonctionnement des cabines de poudrage
Le processus commence par l’introduction de la pièce dans la cabine, où elle sera pulvérisée avec de la poudre électrostatiquement chargée. Les pistolets de poudrage ou pistolets électrostatiques sont utilisés pour charger la poudre avec une charge négative, ce qui permet à la poudre de s’attirer électriquement vers la surface de la pièce, généralement en métal. Cette charge assure une couverture uniforme, même sur des surfaces complexes et irrégulières. L’efficacité de l’application dépend de nombreux facteurs, notamment la qualité du pistolet de pulvérisation, la configuration de la cabine et les paramètres du système de ventilation.
Récupération de la poudre excédentaire
Un des principaux avantages des cabines de poudrage modernes est la récupération de la poudre excédentaire. Au lieu de laisser la poudre inutilisée se perdre dans l’air ou dans des zones non recouvertes, les cabines sont équipées de systèmes de filtration et de systèmes de récupération de poudre. Cela permet de collecter la poudre non adhérente qui peut être récupérée, filtrée et réutilisée dans de futurs cycles de pulvérisation. Ce processus non seulement réduit le gaspillage de matériau, mais il permet également de maintenir l’environnement de travail propre et de réduire les coûts de production.
Les systèmes de filtration sont souvent constitués de filtres à haute capacité, qui capturent efficacement la poudre excédentaire tout en maintenant une bonne circulation de l’air dans la cabine. Les filtres peuvent être de types divers, y compris des filtres à cartouche ou des filtres à poche, qui sont conçus pour séparer la poudre des particules d’air et les récupérer sans compromettre l’efficacité de la cabine.
Sécurisation et efficacité
La sécurisation de l’environnement de travail est une priorité dans les cabines de poudrage. Étant donné que la poudre de peinture est un matériau inflammable, les cabines de poudrage sont équipées de systèmes de ventilation adaptés pour éviter l’accumulation de poussière explosive. Des dispositifs de contrôle de la pression et de filtration sont également mis en place pour garantir que l’air à l’intérieur de la cabine reste propre et exempt de contaminants. Ces systèmes de ventilation permettent de maintenir un flux d’air constant et contrôlé, évacuant efficacement les particules fines et créant un environnement sain pour les opérateurs.
En outre, certaines cabines de poudrage sont également équipées de systèmes de protection des opérateurs, comme des extracteurs d’air ou des cascades de filtration qui permettent d’éliminer les particules fines de poudre avant qu’elles n’atteignent la zone respirable. Ces mesures garantissent que les opérateurs ne sont pas exposés à des risques potentiels, créant ainsi un environnement de travail plus sûr.
Caractéristiques avancées
Les cabines de poudrage modernes peuvent intégrer une gamme de fonctionnalités avancées qui améliorent leur efficacité et leur convivialité :
- Automatisation et contrôle numérique : Les systèmes informatiques permettent un contrôle précis du processus de pulvérisation, avec des ajustements automatiques pour garantir la consistance de l’application de la poudre. Des systèmes de suivi en temps réel peuvent également signaler des problèmes de pulvérisation ou de qualité, offrant ainsi des mesures correctives immédiates.
- Réglage de la pression et du débit d’air : Les cabines permettent de réguler la pression et le débit de l’air, ce qui est essentiel pour assurer une pulvérisation régulière et sans défaut. Cela permet d’obtenir un revêtement uniforme, en particulier pour les pièces ayant des formes complexes.
- Eclairage et visibilité : Un bon éclairage est crucial pour garantir une couverture uniforme de la poudre. Les cabines sont souvent équipées de lampes à LED ou d’éclairage haute performance pour fournir une excellente visibilité pendant l’application. Cela permet à l’opérateur de surveiller le processus et d’ajuster les paramètres si nécessaire.
- Aménagements ergonomiques : De nombreuses cabines sont conçues pour offrir un confort maximal aux opérateurs. Cela inclut des portes coulissantes ou des systèmes de rotation automatique pour faciliter l’accès et le mouvement des pièces, ainsi que des zones de travail ajustables pour adapter l’ergonomie en fonction des besoins.
Types de cabines de poudrage
Il existe plusieurs types de cabines de poudrage, adaptés aux besoins spécifiques des différentes industries :
- Cabines à flux vertical : Dans ce type de cabine, l’air et la poudre circulent du bas vers le haut, permettant une récupération efficace de la poudre excédentaire. Ce système est souvent utilisé dans les applications où de grandes quantités de poudre sont utilisées.
- Cabines à flux horizontal : Ces cabines sont souvent utilisées dans des configurations où les pièces sont plus petites ou lorsque la pièce est amenée dans la cabine de manière horizontale. Le flux d’air traverse la cabine horizontalement, permettant une pulvérisation efficace et une bonne récupération de la poudre.
- Cabines à circulation fermée : Ces systèmes sont dotés d’un système de ventilation intégré qui assure une circulation d’air constante et un environnement de travail propre. Cela permet d’améliorer l’efficacité énergétique et de réduire les coûts liés à la gestion de la poussière.
Conclusion
Les cabines de poudrage jouent un rôle essentiel dans le processus de revêtement en poudre en garantissant une application uniforme, une récupération efficace de la poudre et un environnement de travail sécurisé. L’intégration de technologies modernes telles que l’automatisation, le contrôle numérique, et les systèmes de filtration avancés permet de maximiser l’efficacité et de minimiser les coûts, tout en offrant des résultats de qualité constante. Que ce soit pour des applications industrielles à grande échelle ou pour des productions plus petites et spécialisées, les cabines de poudrage sont un élément clé pour assurer la qualité, la durabilité et la rentabilité du processus de revêtement en poudre.
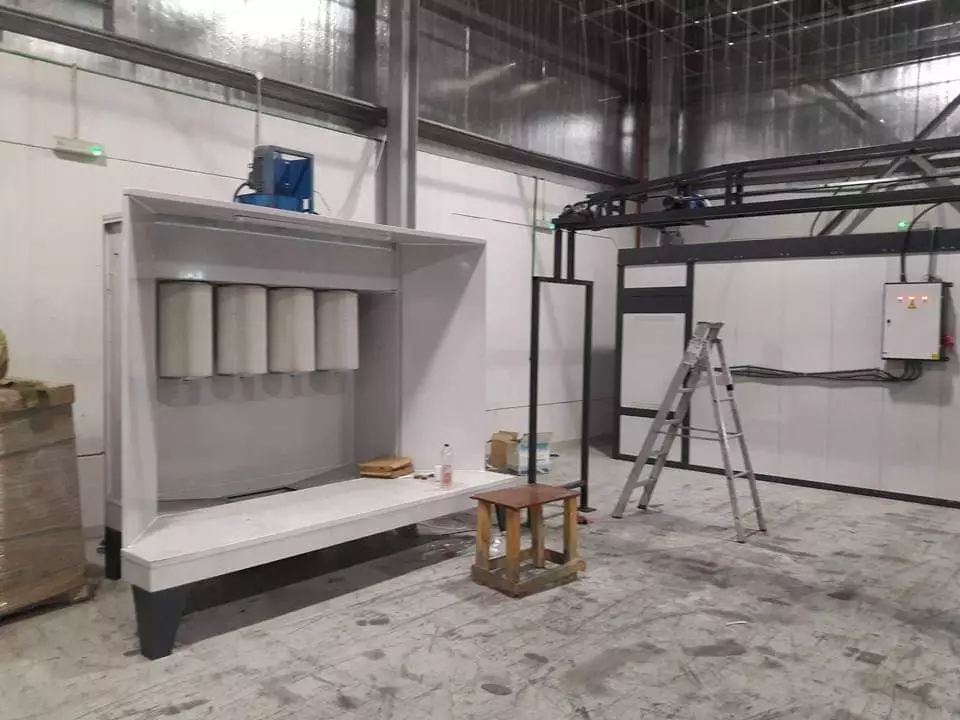
Les cabines de poudrage, au cœur du processus de revêtement en poudre, sont conçues pour appliquer la poudre de manière efficace et uniforme tout en garantissant un environnement de travail propre et sûr. Elles permettent d’appliquer une fine couche de poudre sur des pièces métalliques ou autres, avant que celles-ci ne soient durcies dans un four. Le processus de pulvérisation est rendu possible grâce à des pistolets électrostatiques qui chargent la poudre de manière à ce qu’elle adhère efficacement à la surface des pièces. Ce chargement électrostatique garantit une couverture uniforme, même sur des surfaces de formes complexes. Les cabines de poudrage modernes sont dotées de systèmes de récupération et de filtration qui maximisent l’utilisation de la poudre en permettant de récupérer celle qui n’adhère pas à la pièce. Cela permet de réduire les coûts de matériau tout en minimisant les déchets et l’impact environnemental du processus.
Les systèmes de filtration jouent un rôle clé dans le maintien d’un environnement de travail propre. Ils capturent la poudre excédentaire dans l’air, évitant ainsi qu’elle ne se disperse dans l’atelier et réduisant les risques de contamination croisée entre différentes couleurs ou types de poudre. Cela permet non seulement de maintenir une atmosphère saine mais aussi d’assurer que la poudre excédentaire soit récupérée et réutilisée, ce qui rend le processus plus économique et plus respectueux de l’environnement. La gestion des flux d’air à l’intérieur des cabines est également un facteur déterminant dans le bon fonctionnement de l’équipement. Un flux d’air bien régulé permet de garantir une pulvérisation efficace et d’éliminer les particules fines de poudre qui pourraient nuire à la qualité du revêtement. Cela permet également de réduire la poussière et d’empêcher l’accumulation de matériaux indésirables qui pourraient affecter la finition des pièces.
L’un des principaux avantages des cabines de poudrage modernes est la sécurité qu’elles offrent aux opérateurs. Ces cabines sont conçues pour minimiser l’exposition à la poussière de poudre, qui peut être inflammable et représenter un risque pour la santé si elle est inhalée. Des systèmes de ventilation efficaces et des mécanismes de contrôle de la pression permettent de maintenir l’air dans la cabine propre et exempt de poussière excessive, réduisant ainsi les risques d’accidents et garantissant un environnement de travail plus sûr. La sécurité des opérateurs est également renforcée par des dispositifs de surveillance qui détectent toute anomalie dans les niveaux de concentration de poudre ou d’autres paramètres de l’environnement de travail.
En termes d’efficacité, les cabines de poudrage ont beaucoup évolué avec l’intégration de technologies avancées. Les systèmes informatisés permettent un contrôle précis de la pulvérisation, ajustant automatiquement les paramètres pour garantir une application de poudre optimale. Les robots de pulvérisation sont souvent utilisés dans les grandes installations, permettant de traiter des volumes élevés de pièces avec une grande précision et à une vitesse accrue, tout en minimisant l’intervention humaine. Cela permet également une meilleure uniformité du revêtement, même pour des pièces de formes complexes ou irrégulières. L’intégration d’outils de diagnostic et de capteurs dans les cabines permet également une surveillance en temps réel du processus, garantissant ainsi que les pièces reçoivent un traitement de qualité constante.
Le contrôle de la qualité dans les cabines de poudrage ne se limite pas seulement à l’application de la poudre. Il s’étend également à l’entretien des équipements. Les cabines modernes sont conçues pour être faciles à entretenir, avec des systèmes de nettoyage automatisés qui réduisent les temps d’arrêt nécessaires pour maintenir les équipements en bon état. Cela permet de garantir que les cabines restent fonctionnelles et efficaces sur de longues périodes tout en réduisant les coûts d’entretien. Les filtres et autres composants peuvent souvent être remplacés ou nettoyés rapidement, ce qui contribue à maintenir un flux de production continu.
Les cabines de poudrage sont également de plus en plus modulables et adaptables aux besoins spécifiques des utilisateurs. Selon les exigences de production, les cabines peuvent être conçues pour des opérations à petite échelle ou de grande envergure. Par exemple, certaines cabines peuvent être spécifiquement configurées pour le traitement de petites pièces, tandis que d’autres sont adaptées pour le revêtement de grandes pièces ou d’ensembles complexes. Cette flexibilité permet aux entreprises de s’adapter rapidement à des commandes personnalisées ou à des variations dans les volumes de production.
Enfin, la conception des cabines de poudrage a également évolué pour être plus écologique. De nombreux modèles sont maintenant conçus pour être plus efficaces énergétiquement, avec des technologies permettant de minimiser la consommation d’énergie tout en maintenant des performances optimales. Les progrès dans la gestion des émissions et la récupération de la chaleur contribuent également à réduire l’empreinte carbone des installations de poudrage, rendant le processus encore plus respectueux de l’environnement. Cela fait des cabines de poudrage non seulement un choix pratique pour la production, mais aussi une option plus durable pour les industries cherchant à réduire leur impact environnemental tout en conservant une haute qualité de finition.
En résumé, les cabines de poudrage représentent un élément essentiel de l’équipement de revêtement en poudre, offrant des solutions innovantes et efficaces pour l’application de finitions durables et esthétiques. Grâce à l’intégration de technologies avancées, à une meilleure gestion des matériaux et à une plus grande sécurité pour les opérateurs, elles jouent un rôle clé dans la production moderne, tout en répondant aux exigences environnementales croissantes et aux standards de qualité les plus élevés.
Avantages des cabines de poudrage
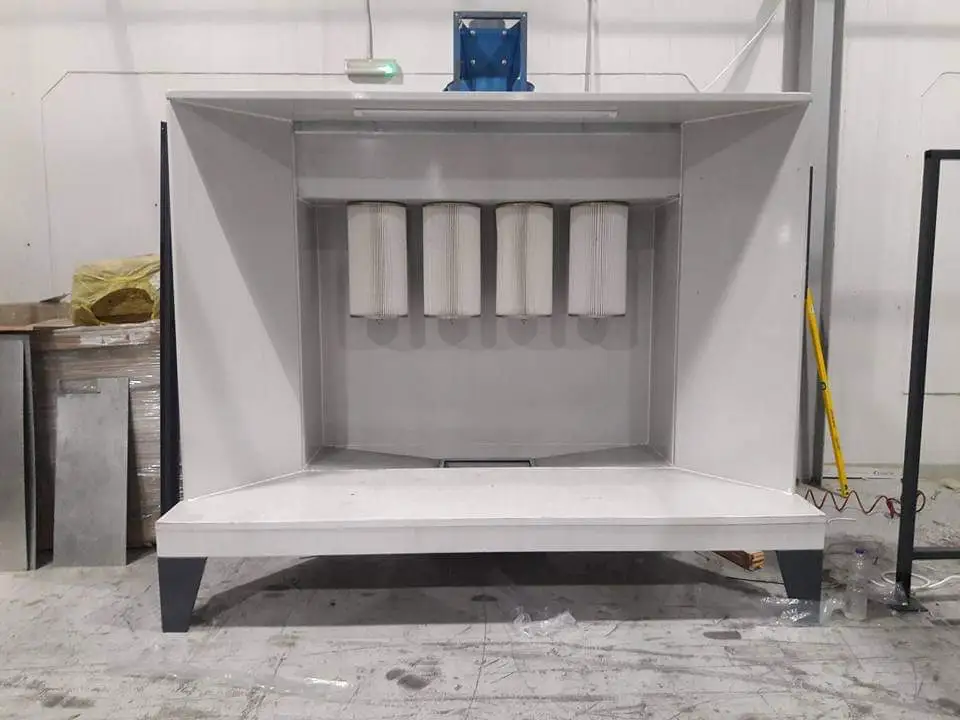
Les cabines de poudrage présentent de nombreux avantages, notamment :
- Elles permettent d’appliquer une peinture poudre de manière uniforme et précise.
- Elles donnent un résultat de qualité supérieure.
- Elles sont plus respectueuses de l’environnement que les peintures liquides, car elles ne contiennent pas de solvants.
Inconvénients des cabines de poudrage
Les cabines de poudrage présentent quelques inconvénients, notamment :
- Elles sont plus coûteuses que les cabines de peinture liquide.
- Elles nécessitent un entretien régulier.
Conclusion
Les cabines de poudrage sont des équipements importants pour les industries qui utilisent la peinture poudre. Elles permettent d’appliquer une peinture poudre de manière uniforme et précise, ce qui donne un résultat de qualité supérieure.
Cabine de Poudrage
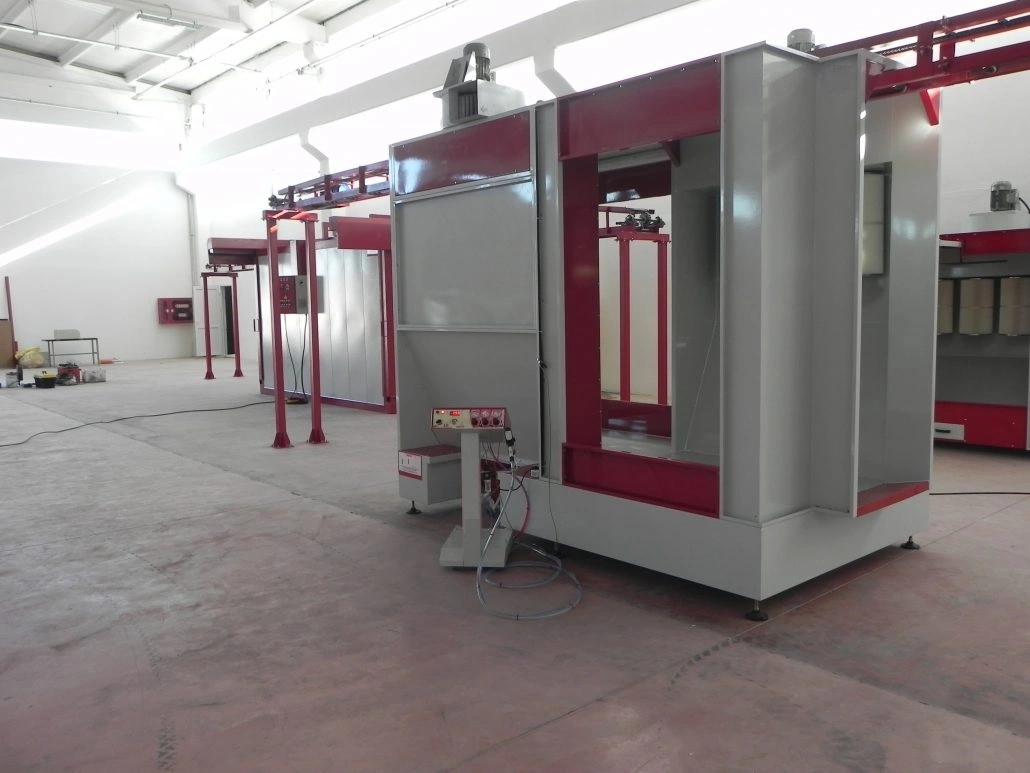
Une cabine de poudrage est un équipement essentiel dans le processus de revêtement par poudre. Elle offre un environnement contrôlé où la poudre est appliquée sur la surface d’un objet de manière uniforme et efficace. Cette cabine est conçue pour contenir le processus de pulvérisation de la poudre, garantissant ainsi un travail propre et sécurisé.
La cabine de poudrage est généralement équipée de filtres pour capturer les particules de poudre non utilisées, permettant ainsi leur recyclage. De plus, elle est souvent dotée d’un système d’évacuation pour éliminer les excès de poudre et maintenir un environnement de travail sûr. Certains modèles intègrent également des dispositifs d’éclairage et de ventilation pour une meilleure visibilité et une meilleure circulation de l’air.
Le processus de poudrage dans la cabine commence par la préparation de la surface de l’objet, suivie de l’application électrostatique de la poudre. Cette dernière est chargée électriquement, ce qui lui permet d’être attirée par la surface de l’objet de manière uniforme. Une fois la poudre appliquée, l’objet est généralement placé dans un four de polymérisation pour fusionner et durcir le revêtement.
En résumé, la cabine de poudrage joue un rôle crucial dans la fabrication de revêtements par poudre, en fournissant un environnement contrôlé et sécurisé pour l’application de la poudre, contribuant ainsi à la qualité et à la durabilité des produits finis.
Revêtement en Poudre :
Le revêtement en poudre est un processus de finition de surface largement utilisé dans de nombreux secteurs industriels pour appliquer un revêtement protecteur ou décoratif sur une variété de substrats. Ce processus implique l’application d’une fine couche de poudre de polymère sur la surface de l’objet, suivi de sa fusion et de son durcissement pour former un revêtement solide et uniforme.
La poudre utilisée dans ce processus est généralement composée de résines thermodurcissables ou thermoplastiques, qui sont pulvérisées sur la surface de l’objet à l’aide d’une pistolet de pulvérisation électrostatique dans une cabine de poudrage. L’électricité statique est utilisée pour charger les particules de poudre, ce qui les attire vers la surface de l’objet de manière uniforme.
Une fois la poudre appliquée, l’objet est placé dans un four de polymérisation où il est chauffé à une température contrôlée. Sous l’effet de la chaleur, la poudre fond, s’écoule et se fusionne pour former un film continu sur la surface de l’objet. Ce film polymérisé durcit ensuite en refroidissant, créant ainsi un revêtement durable et résistant aux intempéries, à la corrosion et à d’autres dommages.
Le revêtement en poudre offre de nombreux avantages par rapport aux autres méthodes de revêtement, notamment une excellente adhérence, une résistance chimique et mécanique élevée, ainsi qu’une variété de finitions et de couleurs disponibles. De plus, ce processus est respectueux de l’environnement car il ne génère pas de solvants volatils ni de composés organiques volatils (COV).
En conclusion, le revêtement en poudre est une méthode polyvalente et efficace pour protéger et décorer une grande variété d’objets, allant des pièces automobiles et des meubles métalliques aux équipements industriels et aux structures architecturales, offrant ainsi des performances durables et une esthétique attrayante.
Application de Peinture en Poudre
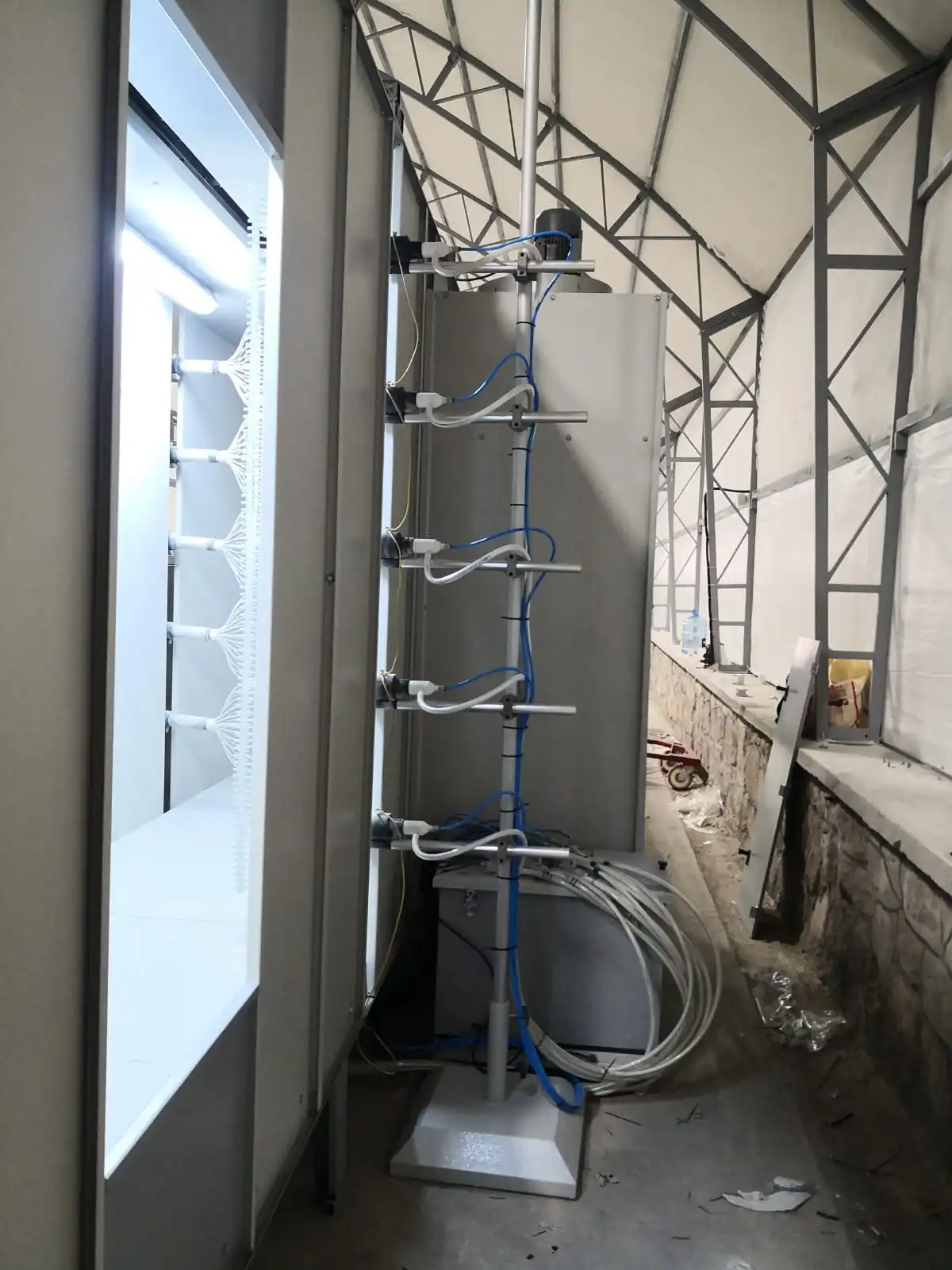
L’application de peinture en poudre est une étape cruciale dans le processus de revêtement par poudre. Cette étape vise à déposer de manière uniforme une fine couche de poudre de peinture sur la surface de l’objet à revêtir. L’objectif est d’assurer une couverture complète et homogène tout en minimisant les pertes de matériau.
Le processus d’application de peinture en poudre débute généralement par la préparation de la surface de l’objet. Cela peut impliquer le nettoyage, le dégraissage et le traitement préalable pour garantir une bonne adhérence de la peinture. Ensuite, l’objet est suspendu dans une cabine de poudrage équipée d’un système de pulvérisation électrostatique.
Dans la cabine de poudrage, la poudre de peinture est aspirée depuis un réservoir puis transportée vers un pistolet de pulvérisation. Les particules de poudre de peinture sont chargées électriquement par le pistolet, ce qui les rend attirées vers la surface de l’objet de manière uniforme. Grâce à l’électricité statique, la poudre adhère efficacement à la surface, couvrant même les zones les plus difficiles d’accès.
Un contrôle précis du débit de poudre et de la pression d’air est crucial pour garantir une application uniforme et une épaisseur de revêtement constante. Après l’application de la peinture en poudre, l’objet est généralement transporté vers un four de polymérisation où la poudre fond et se fusionne pour former un revêtement durable.
L’application de peinture en poudre offre de nombreux avantages, notamment une excellente adhérence, une résistance accrue à la corrosion, aux produits chimiques et aux intempéries, ainsi qu’une variété de finitions et de couleurs disponibles. De plus, ce processus est écologique car il réduit les émissions de COV par rapport aux méthodes de peinture liquide traditionnelles.
En conclusion, l’application de peinture en poudre est une étape essentielle dans la fabrication de produits revêtus par poudre, offrant une protection durable et une esthétique de haute qualité pour une variété d’applications industrielles et commerciales.
Électrostatique
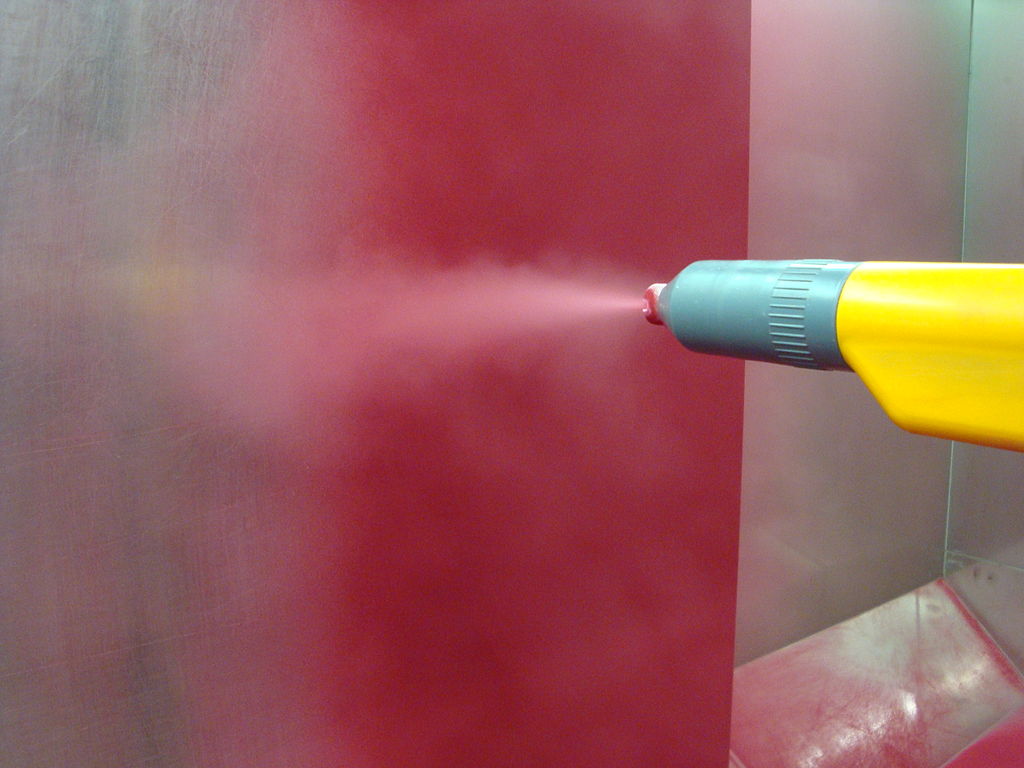
Le terme “électrostatique” se réfère à un phénomène électrique statique dans lequel les charges électriques sont immobiles et ne circulent pas à travers un conducteur. Ce phénomène est largement utilisé dans divers domaines, y compris l’application de peinture en poudre, où il joue un rôle crucial dans le processus de pulvérisation.
Dans le contexte de l’application de peinture en poudre, l’électrostatique est utilisée pour charger les particules de poudre de peinture lors de leur pulvérisation. Le pistolet de pulvérisation est équipé d’un système de charge électrique qui transfère une charge électrique aux particules de poudre au moment de leur éjection. Ces particules chargées sont ensuite attirées vers la surface de l’objet à revêtir, qui est maintenue à un potentiel électrique opposé ou à la terre.
L’attraction électrostatique entre les particules chargées et la surface de l’objet garantit une adhérence uniforme de la poudre sur toute la surface, y compris les zones difficiles d’accès. Cela permet une application efficace et homogène de la peinture en poudre, même sur des formes complexes ou des pièces tridimensionnelles.
L’utilisation de l’électrostatique dans le processus de pulvérisation de peinture en poudre présente de nombreux avantages. Elle permet une réduction significative des pertes de matériau, car la poudre est attirée directement vers la surface de l’objet sans dispersion dans l’air. De plus, elle permet d’obtenir un revêtement uniforme avec une épaisseur de film contrôlée, ce qui garantit une qualité de finition élevée et une utilisation efficace des matériaux.
En résumé, l’électrostatique est une technique fondamentale dans le processus d’application de peinture en poudre, offrant une méthode efficace et précise pour garantir une adhérence optimale de la poudre et une finition de haute qualité sur une variété de substrats.
Pulvérisation de Poudre
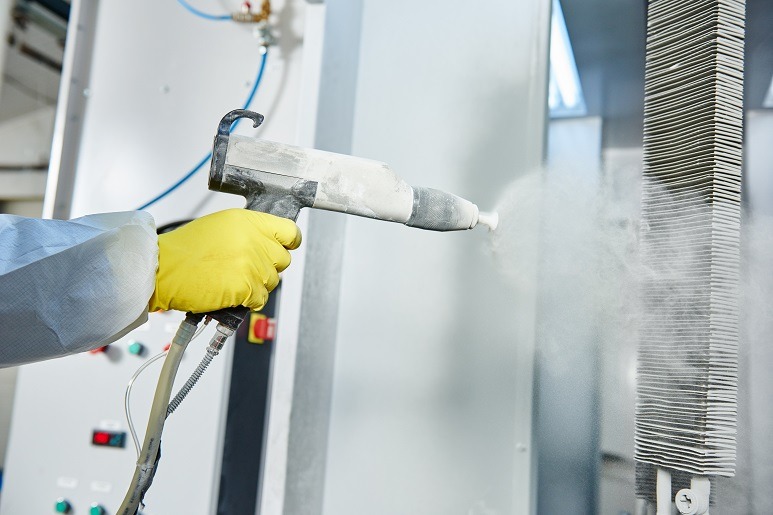
La pulvérisation de poudre est une étape clé dans le processus d’application de revêtements par poudre. Ce processus consiste à projeter de manière contrôlée des particules de poudre sur la surface d’un objet à revêtir afin de créer un film uniforme et adhérent.
La pulvérisation de poudre est généralement réalisée à l’aide d’un pistolet de pulvérisation spécialement conçu pour ce type d’application. Ce pistolet est relié à un système de distribution de poudre qui fournit un flux régulier de matériau à pulvériser.
Lorsque la poudre est introduite dans le pistolet de pulvérisation, elle est transportée vers la buse du pistolet où elle est atomisée en de fines particules. Ces particules de poudre sont ensuite projetées sur la surface de l’objet à l’aide d’un flux d’air comprimé.
Pour améliorer l’efficacité du processus, les particules de poudre peuvent être chargées électriquement à l’aide d’un système d’électrostatique intégré au pistolet de pulvérisation. Cette charge électrique aide à attirer les particules de poudre vers la surface de l’objet, améliorant ainsi l’adhérence et la distribution de la poudre.
Une fois que la poudre est pulvérisée sur la surface de l’objet, elle forme un revêtement en poudre uniforme. L’objet peut ensuite être transféré vers un four de polymérisation où la poudre fond et se fusionne pour former un revêtement solide et durable.
La pulvérisation de poudre offre de nombreux avantages par rapport aux autres méthodes de revêtement, notamment une excellente adhérence, une résistance élevée à la corrosion et aux produits chimiques, ainsi qu’une efficacité de production accrue grâce à une application rapide et automatisée.
En résumé, la pulvérisation de poudre est une étape essentielle dans le processus d’application de revêtements par poudre, offrant une méthode efficace et précise pour créer des revêtements de haute qualité sur une variété de substrats.
Cabine de Peinture en Poudre
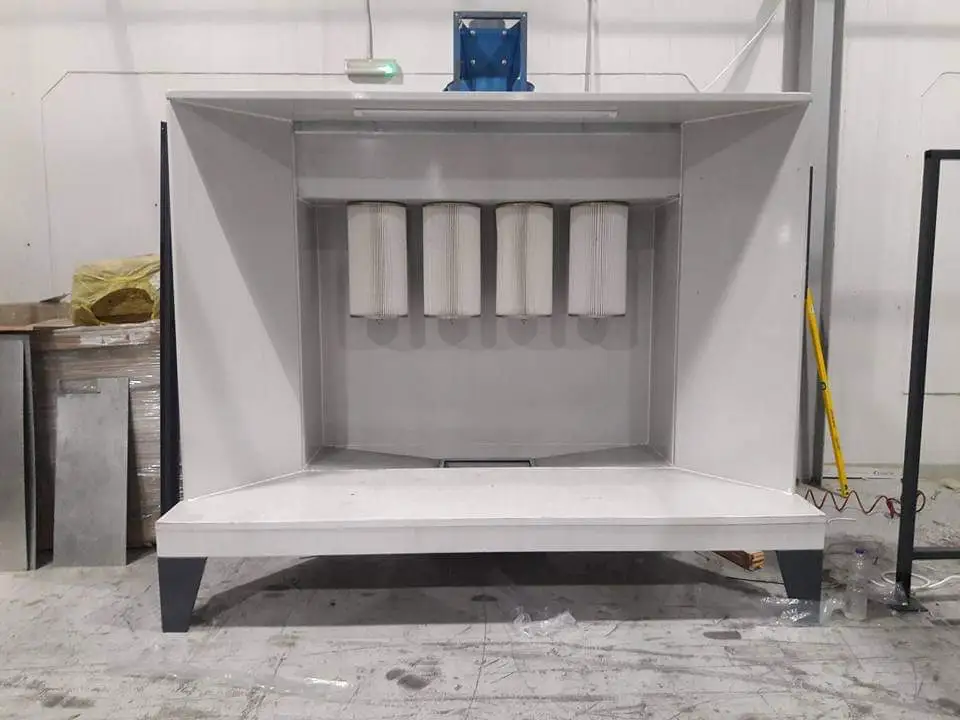
La cabine de peinture en poudre est une infrastructure spécialement conçue pour abriter le processus d’application de revêtements en poudre sur diverses surfaces. Elle offre un environnement contrôlé et sécurisé pour garantir une application efficace et uniforme de la peinture en poudre.
Les cabines de peinture en poudre sont généralement construites en acier ou en aluminium et sont équipées de panneaux isolants pour maintenir une température et une humidité stables. Elles sont également dotées de systèmes de ventilation pour assurer une circulation d’air adéquate et éliminer les excès de particules de poudre.
L’intérieur de la cabine est agencé de manière à faciliter le processus d’application de la peinture en poudre. Des rails suspendus sont souvent installés pour suspendre les pièces à revêtir, permettant ainsi un accès facile et une manipulation pratique pendant le processus de pulvérisation.
Les cabines de peinture en poudre sont équipées de systèmes de filtration pour capturer les particules de poudre non utilisées et les recycler, réduisant ainsi les déchets et les coûts de production. Elles peuvent également être équipées de systèmes d’éclairage intégrés pour améliorer la visibilité pendant le processus d’application.
Pour optimiser l’efficacité du processus, les cabines de peinture en poudre peuvent être équipées de dispositifs d’électrostatique pour charger les particules de poudre pendant la pulvérisation. Cela améliore l’adhérence de la poudre sur la surface de l’objet et garantit une couverture uniforme.
En résumé, la cabine de peinture en poudre est un élément essentiel dans le processus d’application de revêtements en poudre, offrant un environnement contrôlé et sécurisé pour garantir des résultats de haute qualité. Elle contribue à optimiser l’efficacité de la production tout en minimisant les pertes de matériau et en assurant la sécurité des opérateurs.
Revêtement par Poudrage :
Le revêtement par poudrage est une technique de finition de surface largement utilisée dans diverses industries pour appliquer un revêtement protecteur ou décoratif sur des pièces métalliques, plastiques et autres substrats. Ce processus implique l’application d’une fine couche de poudre de revêtement sur la surface de l’objet, suivie de sa fusion et de son durcissement pour former un revêtement solide et durable.
Le processus de revêtement par poudrage débute généralement par la préparation de la surface de l’objet, qui peut inclure le nettoyage, le dégraissage et le traitement préalable pour assurer une bonne adhérence du revêtement. Ensuite, l’objet est suspendu dans une cabine de poudrage spécialement conçue pour cette application.
Dans la cabine de poudrage, la poudre de revêtement est pulvérisée sur la surface de l’objet à l’aide d’un pistolet de pulvérisation électrostatique. Les particules de poudre sont chargées électriquement lors de leur pulvérisation, ce qui les attire vers la surface de l’objet de manière uniforme. Cette charge électrique facilite l’adhérence de la poudre sur la surface et garantit une répartition uniforme du revêtement.
Après l’application de la poudre de revêtement, l’objet est généralement transféré dans un four de polymérisation où il est chauffé à une température spécifique pendant une durée déterminée. Sous l’effet de la chaleur, la poudre de revêtement fond, s’écoule et se polymérise pour former un film continu et homogène sur la surface de l’objet. Une fois refroidi, le revêtement durci offre une protection efficace contre la corrosion, l’usure, les rayures et d’autres dommages.
Le revêtement par poudrage présente de nombreux avantages par rapport aux autres méthodes de revêtement, notamment une excellente adhérence, une résistance élevée à la corrosion et aux produits chimiques, une durabilité accrue et une variété de finitions et de couleurs disponibles. De plus, ce processus est respectueux de l’environnement car il ne génère pas de solvants ni de composés organiques volatils (COV).
En résumé, le revêtement par poudrage est une méthode efficace et polyvalente pour protéger et embellir une grande variété de produits, offrant des performances durables et une esthétique de haute qualité pour une gamme d’applications industrielles et commerciales.
Processus de Poudrage
Le processus de poudrage, également connu sous le nom de revêtement par poudrage, est une méthode de finition de surface largement utilisée dans l’industrie pour appliquer un revêtement protecteur ou décoratif sur divers substrats. Ce processus comprend plusieurs étapes clés, depuis la préparation de la surface jusqu’à la polymérisation du revêtement, garantissant ainsi un résultat final durable et de haute qualité.
- Préparation de la Surface : Le processus débute par la préparation de la surface de l’objet à revêtir. Cette étape peut inclure le nettoyage, le dégraissage et le traitement préalable pour éliminer les contaminants et assurer une adhérence optimale du revêtement.
- Application de la Poudre : Une fois la surface préparée, la poudre de revêtement est appliquée sur l’objet à l’aide d’un pistolet de pulvérisation électrostatique. Les particules de poudre sont chargées électriquement lors de leur pulvérisation, ce qui les attire vers la surface de manière uniforme.
- Fixation et Fusion : Après l’application de la poudre, l’objet est généralement transféré dans un four de polymérisation où il est chauffé à une température spécifique. Sous l’effet de la chaleur, la poudre de revêtement fond, s’écoule et se polymérise pour former un film continu et homogène sur la surface de l’objet.
- Refroidissement et Durcissement : Une fois que le revêtement a fondu et s’est fusionné, l’objet est refroidi pour permettre au revêtement de durcir. Ce processus de refroidissement peut être accéléré à l’aide de systèmes de refroidissement, garantissant ainsi une polymérisation complète et une adhérence optimale du revêtement.
- Inspection et Finition : Une fois refroidi et durci, l’objet revêtu est inspecté pour vérifier la qualité du revêtement et l’absence de défauts. Des finitions supplémentaires peuvent être apportées, telles que le polissage ou le lustrage, pour améliorer l’aspect esthétique du revêtement.
En résumé, le processus de poudrage est une méthode efficace et polyvalente pour appliquer des revêtements protecteurs ou décoratifs sur une variété de substrats. Grâce à ses nombreuses étapes et à son contrôle précis, ce processus offre des résultats durables, résistants et esthétiquement attrayants pour une gamme d’applications industrielles et commerciales.
Équipement de Poudrage
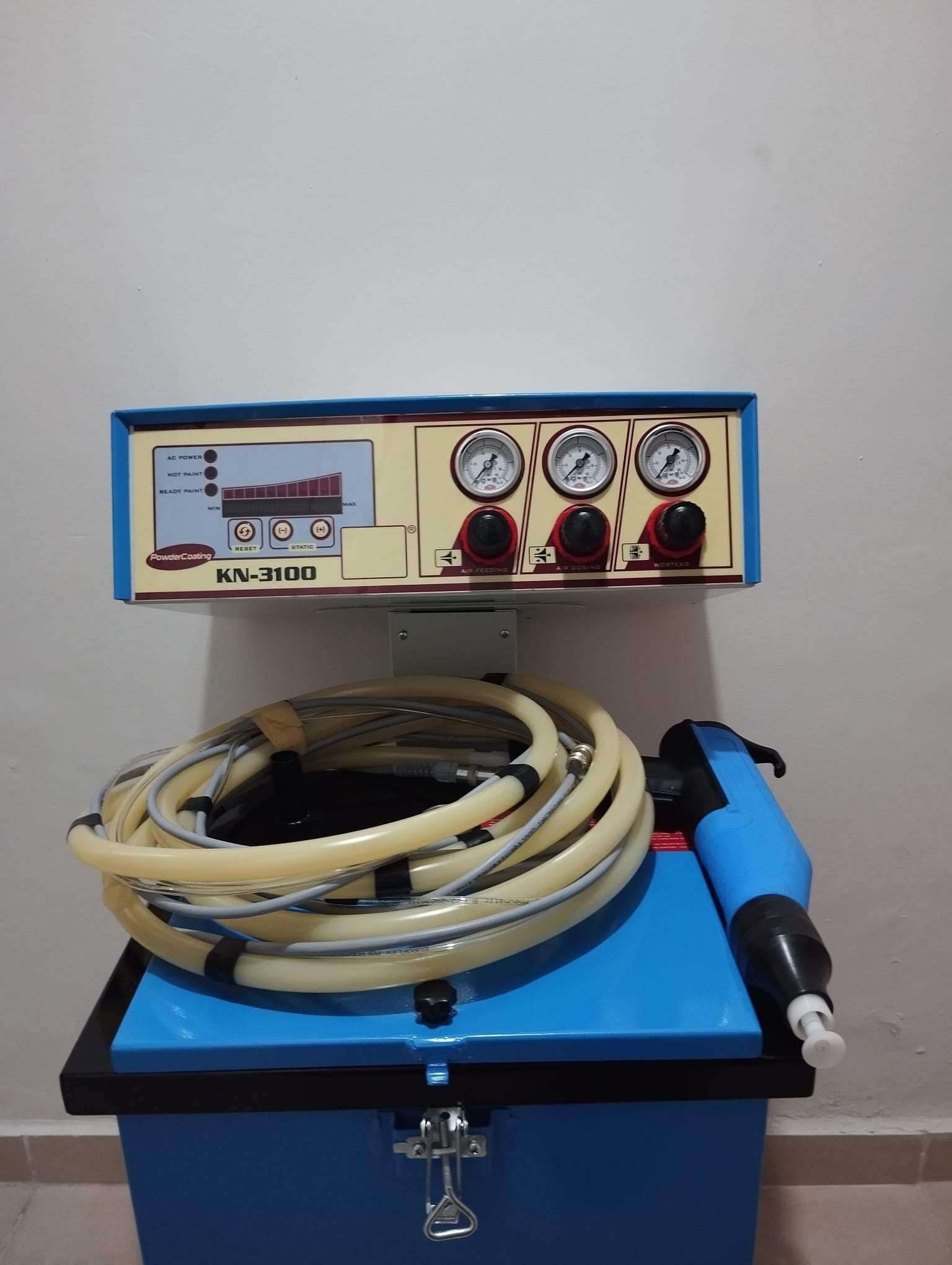
L’équipement de poudrage comprend une gamme d’outils et de machines utilisés dans le processus d’application de revêtements par poudre. Ces équipements sont conçus pour pulvériser la poudre de manière contrôlée, assurant ainsi une distribution uniforme sur la surface de l’objet à revêtir. Voici quelques-uns des équipements couramment utilisés dans le processus de poudrage :
- Pistolet de Pulvérisation : Le pistolet de pulvérisation est l’élément central de l’équipement de poudrage. Il est utilisé pour projeter la poudre de revêtement sur la surface de l’objet. Les pistolets de pulvérisation sont souvent équipés de systèmes électrostatiques pour charger les particules de poudre, facilitant ainsi leur adhérence à la surface.
- Cabine de Poudrage : La cabine de poudrage est un espace clos où le processus d’application de la poudre a lieu. Elle est équipée de systèmes de filtration pour capturer les particules de poudre non utilisées et les recycler, minimisant ainsi les déchets. La cabine de poudrage peut également être équipée de systèmes d’éclairage et de ventilation pour améliorer la visibilité et la circulation de l’air pendant le processus.
- Fours de Polymérisation : Une fois la poudre appliquée, l’objet revêtu est transféré dans un four de polymérisation pour permettre au revêtement de fondre et de durcir. Les fours de polymérisation sont chauffés à des températures spécifiques pour assurer une polymérisation complète du revêtement, garantissant ainsi sa durabilité et sa résistance.
- Équipement de Prétraitement : Avant l’application de la poudre, la surface de l’objet doit être préparée pour assurer une adhérence optimale du revêtement. L’équipement de prétraitement peut inclure des systèmes de nettoyage, de dégraissage et de traitement chimique pour éliminer les contaminants et préparer la surface à recevoir le revêtement.
- Équipement de Manipulation : Pour déplacer et suspendre les pièces à revêtir pendant le processus, divers équipements de manipulation sont utilisés, tels que des chariots, des crochets et des rails suspendus. Ces équipements permettent un accès facile et une manipulation sécurisée des pièces pendant le processus de poudrage.
En résumé, l’équipement de poudrage joue un rôle essentiel dans le processus d’application de revêtements par poudre, offrant les outils et les machines nécessaires pour garantir des résultats de haute qualité et une efficacité de production optimale.
Séchage par Poudrage
Le séchage par poudrage est une étape cruciale dans le processus de revêtement par poudre, intervenant après l’application de la poudre et avant la polymérisation finale du revêtement. Cette étape vise à éliminer l’excès de solvant ou d’eau contenu dans la poudre de revêtement, assurant ainsi une adhérence optimale et un durcissement efficace du revêtement.
Après l’application de la poudre de revêtement sur la surface de l’objet, celui-ci est généralement transféré dans une zone de séchage spécialement conçue. Cette zone de séchage peut être un espace ouvert équipé de ventilateurs pour assurer une circulation d’air adéquate, ou un four de séchage à température contrôlée pour accélérer le processus de séchage.
Pendant le séchage par poudrage, la chaleur et/ou l’air chaud sont généralement utilisés pour évaporer les solvants ou l’eau présents dans la poudre de revêtement. Ce processus permet de réduire le temps de séchage et d’assurer une polymérisation efficace du revêtement lors de l’étape suivante.
Le temps de séchage nécessaire peut varier en fonction de divers facteurs, tels que le type de poudre de revêtement utilisée, l’épaisseur du revêtement appliqué et les conditions environnementales telles que la température et l’humidité. Un contrôle précis de ces paramètres est essentiel pour garantir un séchage efficace et uniforme du revêtement.
Une fois le processus de séchage terminé, l’objet est prêt à être transféré dans le four de polymérisation pour achever le durcissement du revêtement. Le séchage par poudrage contribue ainsi à assurer une adhérence optimale, une résistance accrue et une finition de haute qualité pour les revêtements par poudre.
En résumé, le séchage par poudrage est une étape essentielle dans le processus de revêtement par poudre, assurant une préparation adéquate de la surface et des conditions optimales pour garantir des résultats de haute qualité et une performance durable du revêtement final.
Cabines de Poudre Pulvérisation
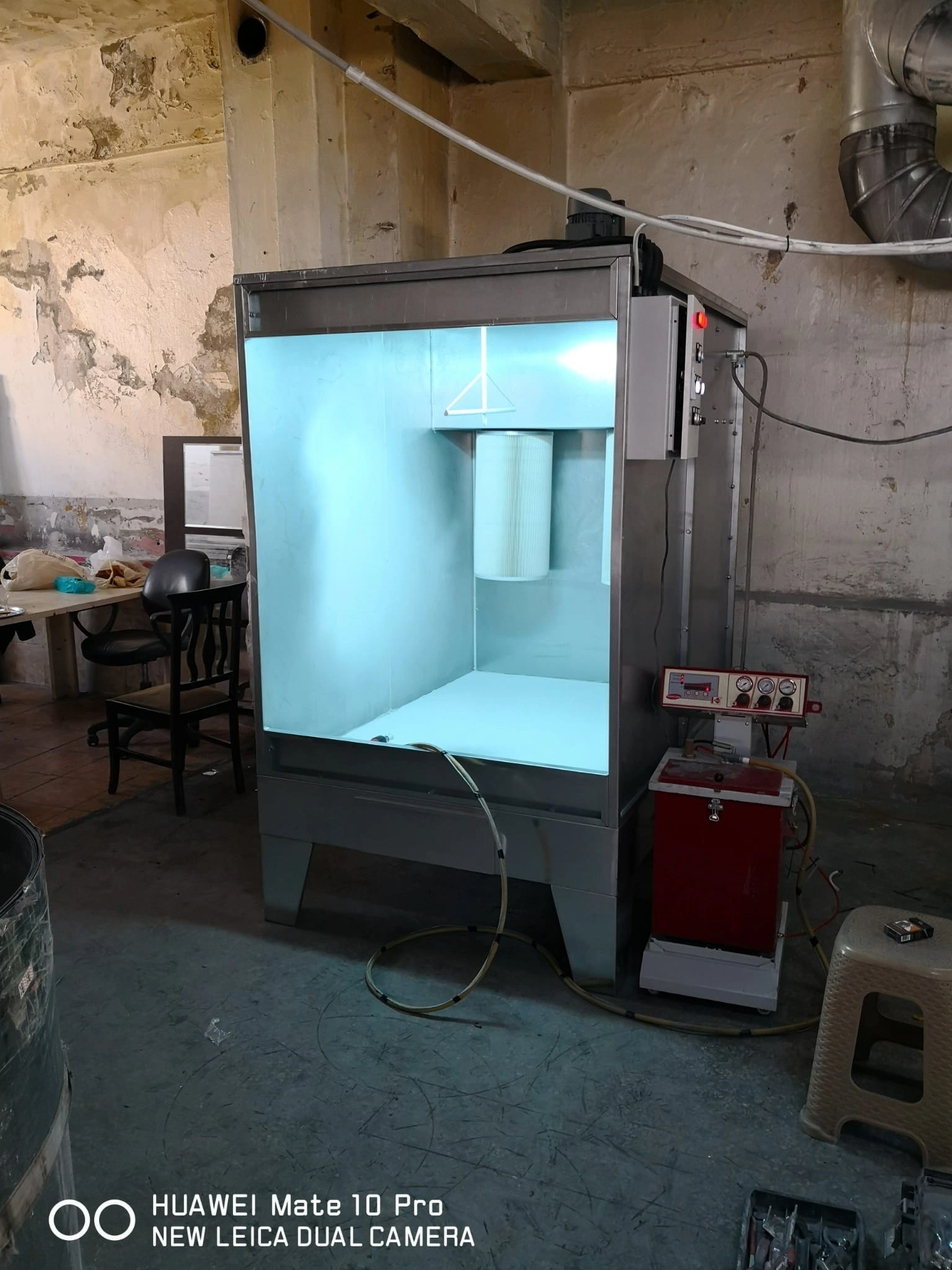
Les cabines de poudrage ouvertes sont les plus simples et les moins coûteuses. Elles sont composées d’une enceinte ouverte et d’un système de ventilation. Les pièces à peindre sont placées dans l’enceinte et le pistolet de pulvérisation est utilisé pour appliquer la peinture poudre. L’air de l’enceinte est ensuite aspiré par le système de ventilation et filtré pour éliminer les particules de peinture.
Les cabines de poudrage fermées sont plus complexes et plus coûteuses que les cabines ouvertes. Elles sont composées d’une enceinte fermée, d’un système de ventilation et d’un système de compensation. Les pièces à peindre sont placées dans l’enceinte et le pistolet de pulvérisation est utilisé pour appliquer la peinture poudre. L’air de l’enceinte est ensuite aspiré par le système de ventilation et filtré pour éliminer les particules de peinture. Le système de compensation permet de maintenir une pression positive dans l’enceinte, ce qui empêche les particules de peinture de s’échapper.
Les cabines de poudre pulvérisation, également connues sous le nom de cabines de pulvérisation de poudre, sont des équipements essentiels dans le domaine du revêtement par poudre. Elles constituent l’environnement contrôlé où s’opère le processus d’application de revêtements en poudre sur une variété de substrats. Ces cabines sont spécialement conçues pour garantir une application uniforme et efficace de la poudre, tout en assurant la sécurité des opérateurs et la protection de l’environnement.
Les cabines de poudre pulvérisation sont généralement construites en acier ou en aluminium, offrant ainsi une structure robuste et durable. Elles sont équipées de panneaux isolants pour maintenir une température constante à l’intérieur de la cabine, ce qui est crucial pour assurer des conditions optimales pendant le processus d’application de la poudre. De plus, ces cabines sont dotées de systèmes de ventilation sophistiqués pour garantir une circulation d’air adéquate, évacuer les vapeurs de solvant et les excès de particules de poudre, et maintenir un environnement de travail sûr et sain pour les opérateurs.
L’intérieur des cabines de poudre pulvérisation est aménagé de manière à faciliter le processus d’application de la poudre. Des rails suspendus sont souvent installés pour suspendre les pièces à revêtir, permettant ainsi un accès facile et une manipulation pratique pendant le processus de pulvérisation. De plus, les cabines sont équipées de systèmes d’éclairage intégrés pour améliorer la visibilité pendant le processus d’application, ce qui est essentiel pour garantir une application précise et uniforme de la poudre.
Le processus d’application de la poudre dans les cabines de pulvérisation de poudre commence par la préparation de la surface de l’objet à revêtir. Cette étape implique souvent le nettoyage, le dégraissage et le traitement préalable de la surface pour assurer une adhérence optimale du revêtement en poudre. Une fois la surface préparée, l’objet est suspendu dans la cabine et la poudre de revêtement est pulvérisée sur sa surface à l’aide d’un pistolet de pulvérisation électrostatique. Les particules de poudre sont chargées électriquement lors de leur pulvérisation, ce qui les attire vers la surface de l’objet de manière uniforme, assurant ainsi une couverture complète et homogène.
Après l’application de la poudre, l’objet est généralement transféré dans un four de polymérisation où il est chauffé à une température spécifique. Sous l’effet de la chaleur, la poudre fond, s’écoule et se fusionne pour former un revêtement solide et durable sur la surface de l’objet. Une fois refroidi, le revêtement durci offre une protection efficace contre la corrosion, l’usure et d’autres dommages, assurant ainsi la durabilité et la longévité des produits finis.
En résumé, les cabines de poudre pulvérisation jouent un rôle crucial dans le processus d’application de revêtements en poudre, offrant un environnement contrôlé et sécurisé pour garantir des résultats de haute qualité et une performance durable des revêtements finaux. Ces équipements sont essentiels pour les industries où la précision, la qualité et la fiabilité sont primordiales, et ils contribuent à assurer le succès et la compétitivité des entreprises dans un marché en constante évolution.
Fours de Séchage et de Durcissement
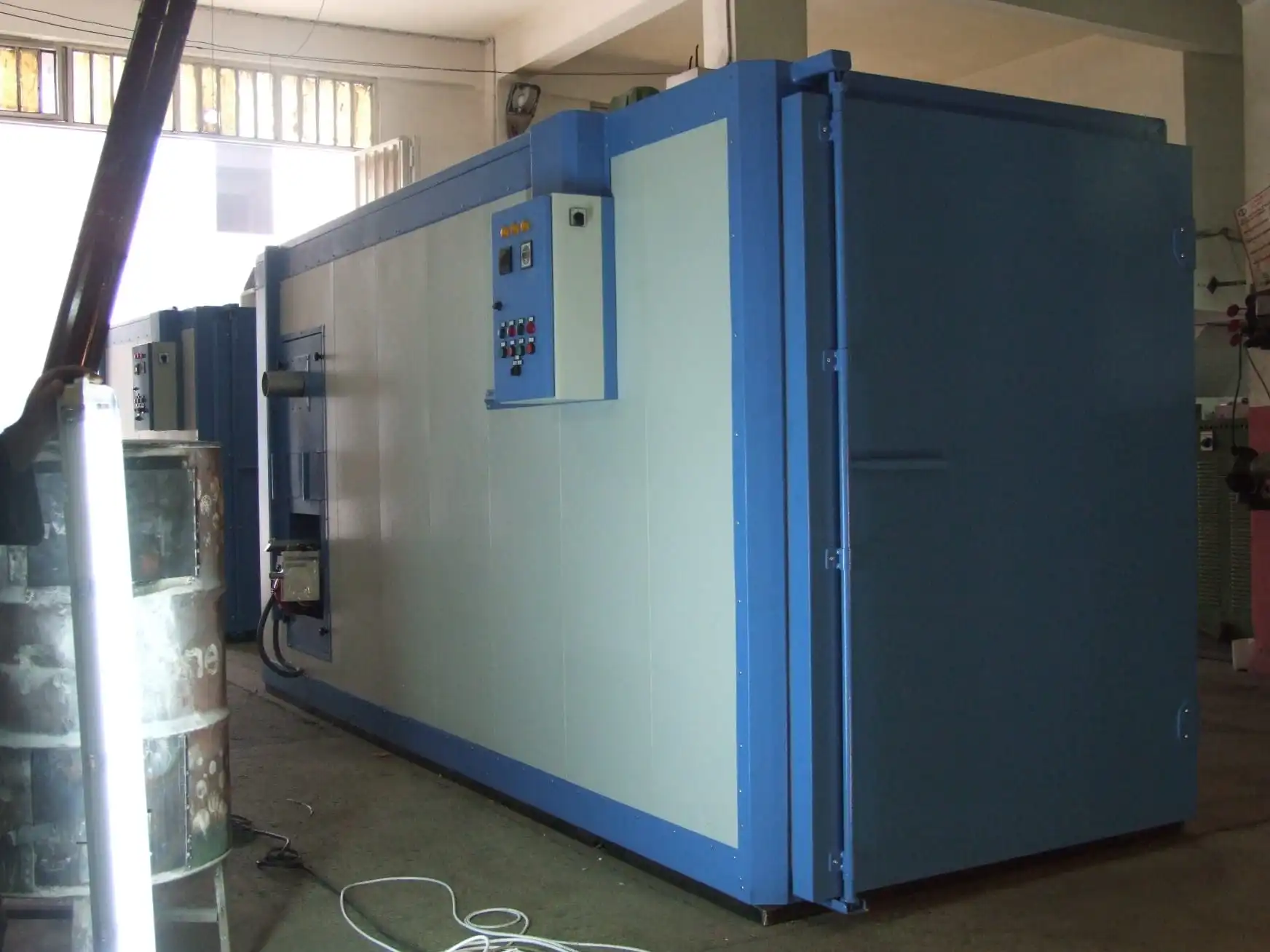
Les fours de séchage et de durcissement sont des équipements industriels utilisés pour sécher et durcir des matériaux. Ils sont utilisés dans une variété d’industries, notamment l’automobile, l’aéronautique, l’électronique et la fabrication.
Les fours de séchage utilisent la chaleur pour éliminer l’humidité des matériaux. Ils sont utilisés pour sécher des matériaux tels que le bois, le papier, le textile et les plastiques.
Les fours de durcissement utilisent la chaleur pour durcir les matériaux. Ils sont utilisés pour durcir des matériaux tels que le métal, le plastique et la céramique.
Les fours de séchage et de durcissement sont généralement constitués des composants suivants :
- Une enceinte : l’enceinte est la structure qui entoure le matériau à sécher ou à durcir. Elle est généralement en acier ou en aluminium.
- Un système de chauffage : le système de chauffage fournit la chaleur nécessaire pour sécher ou durcir le matériau. Le type de système de chauffage utilisé varie en fonction du matériau à sécher ou à durcir.
- Un système de contrôle : le système de contrôle permet de réguler la température et le temps de séchage ou de durcissement.
Le processus de séchage ou de durcissement dans un four est le suivant :
- Le matériau à sécher ou à durcir est placé dans l’enceinte.
- Le système de chauffage est mis en marche pour chauffer le matériau.
- Le matériau est séché ou durci à la température et au temps spécifiés.
La température de séchage ou de durcissement varie en fonction du matériau à sécher ou à durcir. Les matériaux thermoplastiques, comme le plastique, sèchent généralement à des températures inférieures à 200 degrés Celsius. Les matériaux thermodurcissables, comme la résine époxy, sèchent généralement à des températures supérieures à 200 degrés Celsius.
Le temps de séchage ou de durcissement varie également en fonction du matériau à sécher ou à durcir. Les matériaux thermoplastiques sèchent généralement en quelques minutes. Les matériaux thermodurcissables sèchent généralement en quelques heures ou quelques jours.
Les fours de séchage et de durcissement sont des équipements importants pour les industries qui ont besoin de sécher ou de durcir des matériaux. Ils offrent un moyen efficace et fiable de produire des matériaux secs et durcis.
Fours de séchage :
Les fours de séchage sont des équipements industriels utilisés pour éliminer l’humidité des matériaux solides. Ces fours sont essentiels dans de nombreux secteurs industriels tels que l’agroalimentaire, la céramique, la métallurgie, et la fabrication de produits chimiques, entre autres. Leur fonction principale est de chauffer les matériaux à des températures contrôlées afin de permettre l’évaporation de l’humidité sans altérer les propriétés physiques ou chimiques des matériaux traités.
Les fours de séchage peuvent fonctionner selon différents principes, notamment la convection, la conduction et le rayonnement thermique. La convection implique le déplacement de l’air chaud à travers le four pour transférer la chaleur aux matériaux, tandis que la conduction se produit lorsque la chaleur est transférée directement des parois du four aux matériaux. Le rayonnement thermique consiste en l’émission de rayonnement électromagnétique à partir des parois chaudes du four, chauffant ainsi les matériaux.
Ces fours sont souvent équipés de systèmes de contrôle avancés pour surveiller et réguler précisément la température, l’humidité et d’autres paramètres du processus de séchage. Les matériaux traités dans les fours de séchage comprennent une large gamme de produits tels que les aliments, les produits céramiques, les produits pharmaceutiques, les textiles, et bien d’autres.
En résumé, les fours de séchage jouent un rôle crucial dans de nombreuses industries en permettant la production de matériaux secs de haute qualité, en augmentant leur durabilité et en réduisant les coûts de production associés à l’humidité.
Fours de durcissement
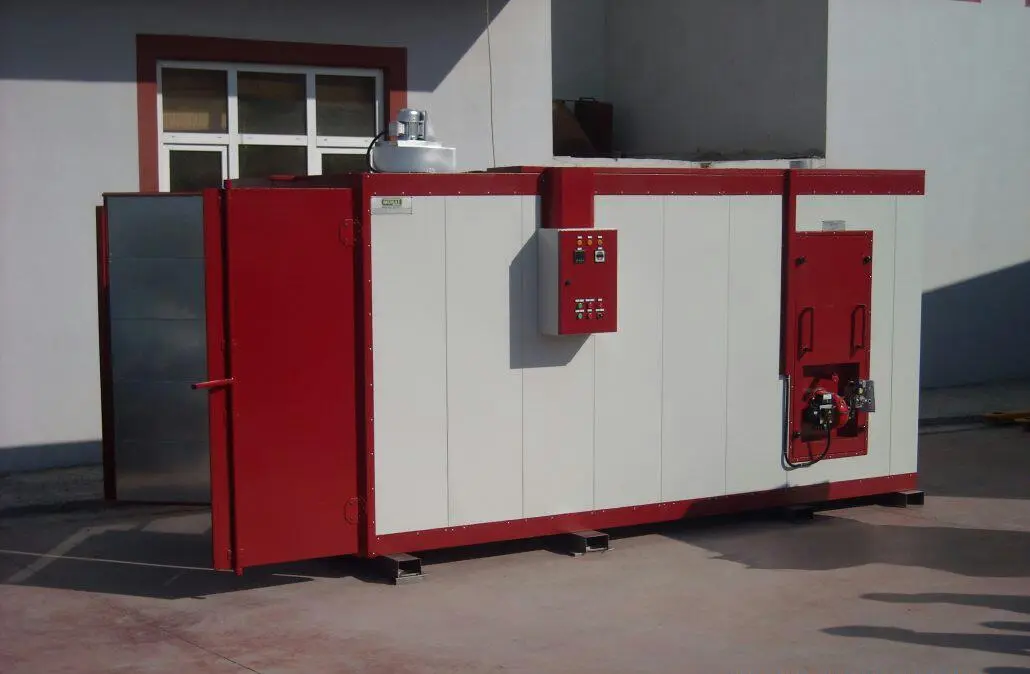
Les fours de durcissement sont des équipements industriels utilisés pour durcir les matériaux par l’application de chaleur contrôlée. Ces fours sont essentiels dans de nombreux processus de fabrication où le durcissement thermique est nécessaire pour améliorer les propriétés physiques des matériaux. Ils sont largement utilisés dans des secteurs tels que la métallurgie, la céramique, l’industrie électronique et les composites.
Le principe de fonctionnement des fours de durcissement implique généralement le chauffage des matériaux à des températures spécifiques pour induire des changements structuraux ou chimiques qui renforcent les matériaux et améliorent leurs propriétés mécaniques. Ces changements peuvent inclure la formation de liaisons interatomiques plus fortes, la cristallisation des polymères, ou la décomposition de composés pour former des phases plus stables.
Les fours de durcissement peuvent utiliser différents modes de transfert de chaleur, tels que la convection, la conduction et le rayonnement thermique, en fonction des exigences du processus et des propriétés des matériaux à durcir. Les paramètres de température, de temps et de vitesse de chauffage peuvent être soigneusement contrôlés pour obtenir les propriétés désirées des matériaux.
Ces fours sont souvent équipés de systèmes de contrôle avancés, de capteurs et de dispositifs de sécurité pour garantir des conditions de durcissement optimales et sécurisées. Les matériaux couramment durcis dans ces fours comprennent les métaux, les polymères, les céramiques, les composites et les revêtements.
En conclusion, les fours de durcissement jouent un rôle crucial dans de nombreuses industries en permettant l’amélioration des propriétés des matériaux, en augmentant leur résistance, leur durabilité et leur performance dans une variété d’applications industrielles et commerciales.
Séchage industriel :
Le séchage industriel est un processus crucial dans de nombreux secteurs industriels où l’élimination de l’humidité des matériaux solides est nécessaire pour assurer leur qualité, leur durabilité et leur conformité aux normes de production. Ce processus est largement utilisé dans des industries telles que l’alimentation, la chimie, la pharmacie, la céramique, le bois, le papier, le textile, et bien d’autres.
L’objectif principal du séchage industriel est d’éliminer l’excès d’humidité des matériaux de manière efficace tout en préservant leurs propriétés physiques, chimiques et biologiques. Cela peut inclure l’élimination de l’eau libre et de l’eau liée, ainsi que le contrôle de l’humidité résiduelle pour éviter la détérioration ultérieure des produits.
Le séchage industriel peut être réalisé à l’aide de différents équipements tels que des séchoirs à air chaud, des séchoirs à lit fluidisé, des séchoirs sous vide, des séchoirs par atomisation, des séchoirs par rayonnement, et bien d’autres. Chaque type de séchoir est adapté à des applications spécifiques en fonction des caractéristiques des matériaux à sécher, de la quantité d’humidité à éliminer, et des exigences de production.
Les paramètres de séchage tels que la température, la pression, la vitesse de l’air, le temps de séjour, et l’humidité relative doivent être soigneusement contrôlés pour garantir un processus de séchage efficace et uniforme. Des systèmes de surveillance et de contrôle avancés sont souvent utilisés pour suivre et ajuster ces paramètres en temps réel.
En résumé, le séchage industriel est un processus essentiel dans de nombreuses industries pour garantir la qualité et la durabilité des produits finaux. En optimisant les processus de séchage, les entreprises peuvent améliorer leur efficacité opérationnelle, réduire les coûts de production, et offrir des produits de meilleure qualité à leurs clients.
Durcissement thermique :
Le durcissement thermique est un processus de traitement thermique utilisé pour renforcer les matériaux en modifiant leur structure cristalline ou leur composition chimique à des températures élevées. Ce processus est largement utilisé dans l’industrie pour améliorer les propriétés mécaniques, la résistance à la corrosion, la conductivité électrique, et d’autres caractéristiques des matériaux.
Le durcissement thermique peut être réalisé selon différents procédés, notamment la trempe, le revenu, la cémentation, la carbonitruration, la recristallisation, et d’autres techniques spécifiques à chaque matériau. Chaque procédé implique des conditions de température et de temps spécifiques, ainsi que des méthodes de refroidissement contrôlées pour obtenir les propriétés désirées du matériau.
L’objectif principal du durcissement thermique est d’augmenter la résistance et la dureté des matériaux en favorisant la formation de structures cristallines plus compactes et résistantes aux contraintes mécaniques. Cela peut impliquer la diffusion d’atomes étrangers dans la matrice cristalline, la transformation de phases cristallines, ou la modification des liaisons interatomiques.
Les matériaux couramment durcis par le durcissement thermique comprennent les métaux, les alliages, les céramiques, les polymères, et les composites. Ce processus est largement utilisé dans des industries telles que l’automobile, l’aérospatiale, l’électronique, la construction, et la fabrication d’outils et d’équipements industriels.
En conclusion, le durcissement thermique est un processus essentiel dans l’industrie pour améliorer les propriétés des matériaux et garantir leur performance dans une variété d’applications. En comprenant les principes et les techniques du durcissement thermique, les ingénieurs et les fabricants peuvent concevoir des matériaux plus résistants, durables et adaptés à leurs besoins spécifiques.
Traitement thermique :
Le traitement thermique est un ensemble de procédés industriels qui impliquent l’exposition contrôlée des matériaux à des températures élevées pour modifier leurs propriétés physiques et/ou chimiques. Ce processus est largement utilisé dans diverses industries pour améliorer la résistance, la durabilité, la ductilité et d’autres caractéristiques des matériaux.
Les principaux objectifs du traitement thermique sont de modifier la structure cristalline des matériaux, d’augmenter leur dureté, de réduire leur fragilité, d’améliorer leur usinabilité, et de soulager les contraintes internes résultant des processus de fabrication. Ces objectifs sont atteints en exposant les matériaux à des températures spécifiques pendant des périodes de temps définies, suivies de refroidissements contrôlés à des vitesses appropriées.
Il existe plusieurs techniques de traitement thermique, dont les plus courantes sont la trempe, le revenu, la recuit, la cémentation, la carbonitruration, et la nitruration. Chaque technique est adaptée à des matériaux spécifiques et à des exigences de performance particulières.
Par exemple, la trempe implique le chauffage rapide du matériau à une température critique, suivie d’un refroidissement rapide pour obtenir une structure cristalline métastable qui confère une dureté élevée. Le revenu consiste à chauffer le matériau à une température inférieure à celle de la trempe pour réduire la fragilité tout en maintenant une dureté acceptable. Le recuit, quant à lui, vise à réduire la dureté excessive et à améliorer la ductilité en favorisant la recristallisation des grains.
Le traitement thermique est largement utilisé dans des industries telles que l’automobile, l’aérospatiale, la construction, la fabrication d’outils, et la production d’équipements industriels. Il est essentiel pour garantir la qualité et la performance des pièces métalliques et des composants dans ces secteurs.
En conclusion, le traitement thermique joue un rôle crucial dans l’optimisation des propriétés des matériaux et dans la fabrication de produits de haute qualité. En comprenant les principes et les techniques du traitement thermique, les ingénieurs et les fabricants peuvent concevoir et produire des matériaux adaptés à une large gamme d’applications industrielles et commerciales.
Cuisson industrielle
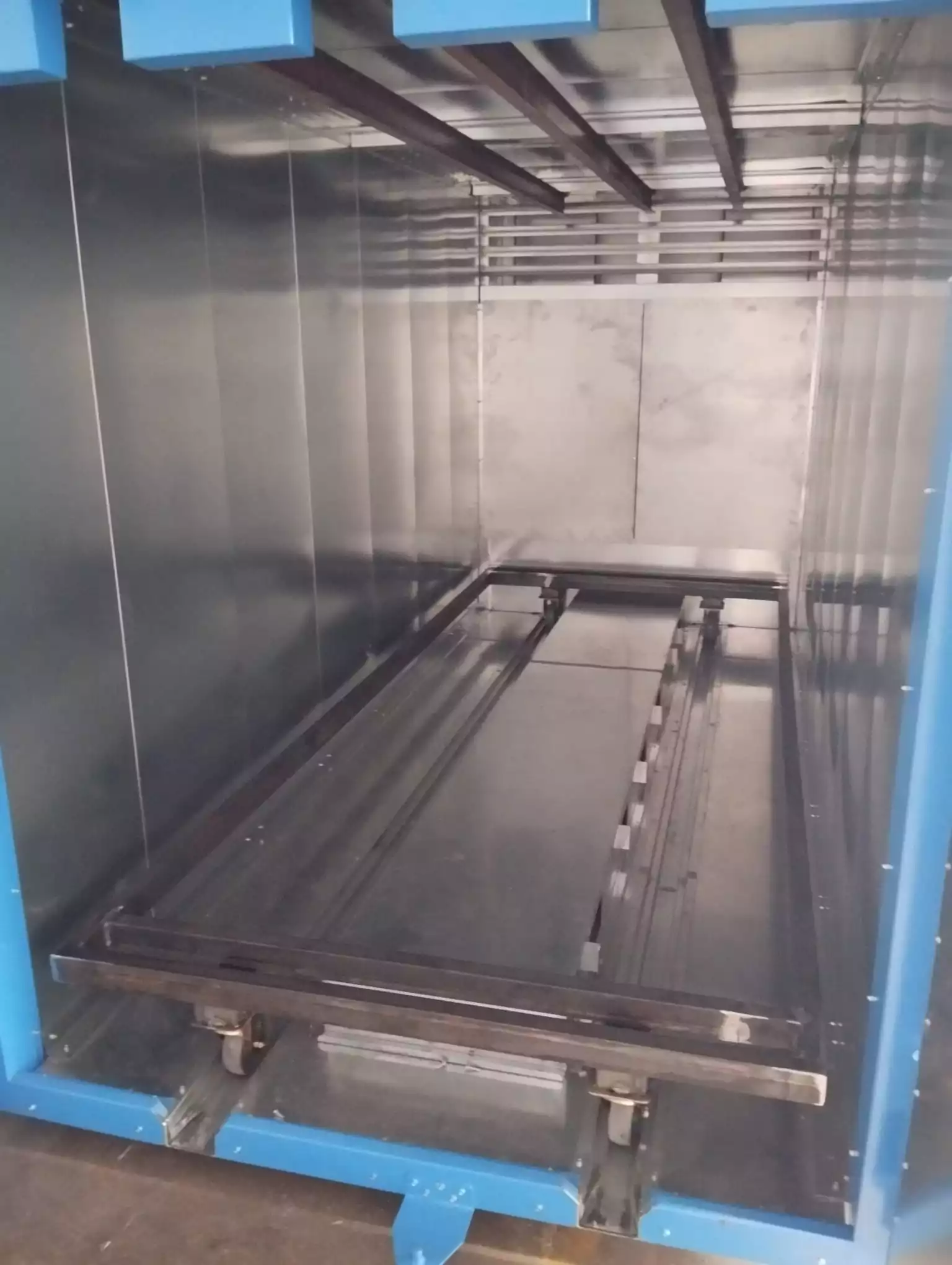
La cuisson industrielle est un processus de traitement thermique utilisé dans diverses industries pour transformer les matériaux à des températures élevées en vue de modifier leurs propriétés physiques, chimiques ou biologiques. Ce processus est essentiel dans des secteurs tels que l’alimentation, la céramique, la métallurgie, le verre, les polymères, et d’autres.
Dans l’industrie alimentaire, par exemple, la cuisson est utilisée pour stériliser les aliments, dénaturer les protéines, éliminer les micro-organismes pathogènes, améliorer la digestibilité, et développer des arômes et des textures spécifiques. Des équipements spécialisés tels que les fours, les autoclaves, les séchoirs, et les friteuses sont utilisés pour contrôler précisément les températures, les temps de cuisson, et d’autres paramètres du processus.
Dans l’industrie céramique, la cuisson est un processus crucial pour transformer les matières premières en produits finis tels que la vaisselle, les carreaux, les briques, et la porcelaine. Les fours à haute température sont utilisés pour fritter les matériaux, fusionner les glaçures, et développer des propriétés mécaniques et esthétiques spécifiques.
Dans l’industrie métallurgique, la cuisson est souvent associée à des processus tels que la fusion, la trempe, le recuit, et le revenu pour traiter les métaux et alliages et produire des pièces de haute qualité avec les propriétés requises.
La cuisson industrielle implique souvent des environnements de travail extrêmes et des procédés complexes nécessitant une expertise technique et des équipements spécialisés. Des systèmes de contrôle avancés sont souvent utilisés pour surveiller et réguler les paramètres du processus afin d’assurer une production efficace et de haute qualité.
En conclusion, la cuisson industrielle est un processus essentiel dans de nombreuses industries pour transformer les matériaux et produire une large gamme de produits finis avec des propriétés spécifiques. En comprenant les exigences et les défis associés à ce processus, les entreprises peuvent optimiser leurs opérations de fabrication et offrir des produits de haute qualité à leurs clients.
Procédés de séchage :
Les procédés de séchage désignent l’ensemble des méthodes et des techniques utilisées pour éliminer l’humidité des matériaux solides. Ces procédés sont largement utilisés dans de nombreuses industries pour préparer, traiter ou conserver divers produits tout en garantissant leur qualité, leur durabilité et leur sécurité.
Il existe plusieurs procédés de séchage, chacun adapté à des applications spécifiques en fonction des propriétés des matériaux à sécher, des exigences de production et des contraintes environnementales. Parmi les principaux procédés de séchage, on trouve :
- Le séchage à l’air : Ce procédé consiste à exposer les matériaux à sécher à l’air ambiant pour permettre l’évaporation naturelle de l’humidité. Bien que simple, ce procédé est souvent lent et peu efficace, et il est généralement utilisé pour des matériaux sensibles à la chaleur ou pour des applications de séchage à petite échelle.
- Le séchage par convection : Ce procédé implique l’utilisation d’air chaud ou de gaz pour accélérer le processus d’évaporation. Les matériaux à sécher sont exposés à un courant d’air chaud dans des séchoirs spécialement conçus, ce qui permet une évaporation rapide et efficace de l’humidité.
- Le séchage par contact : Ce procédé repose sur le contact direct des matériaux à sécher avec une surface chauffée, telle qu’un tambour ou une plaque chauffante. L’humidité est transférée des matériaux vers la surface chauffée, où elle s’évapore rapidement.
- Le séchage par rayonnement : Ce procédé utilise des sources de chaleur radiante, telles que des radiateurs infrarouges, pour chauffer les matériaux à sécher et provoquer l’évaporation de l’humidité. Ce procédé est souvent utilisé pour sécher des matériaux sensibles à la convection ou au contact direct avec une surface chauffée.
- Le séchage sous vide : Ce procédé implique la réduction de la pression atmosphérique autour des matériaux à sécher, ce qui abaisse leur point d’ébullition et accélère l’évaporation de l’humidité. Le séchage sous vide est souvent utilisé pour sécher des matériaux sensibles à la chaleur ou pour éliminer l’humidité de manière délicate.
Ces procédés de séchage peuvent être utilisés seuls ou en combinaison, en fonction des exigences spécifiques de chaque application. Ils sont essentiels dans de nombreux secteurs industriels, notamment l’alimentation, la pharmacie, la chimie, la céramique, la métallurgie et bien d’autres, où ils jouent un rôle crucial dans la fabrication de produits de haute qualité.
Procédés de durcissement :
Les procédés de durcissement font référence à un ensemble de techniques utilisées pour renforcer les matériaux en modifiant leur structure interne ou leurs propriétés chimiques. Ces procédés sont largement utilisés dans diverses industries pour améliorer la résistance, la durabilité et d’autres caractéristiques des matériaux, les rendant ainsi adaptés à une gamme d’applications.
Voici quelques-uns des principaux procédés de durcissement utilisés dans l’industrie :
- Durcissement par traitement thermique : Ce procédé implique le chauffage des matériaux à des températures élevées suivies d’un refroidissement contrôlé pour modifier leur structure cristalline et améliorer leurs propriétés mécaniques. Des techniques telles que la trempe, le revenu, le recuit et la cémentation sont utilisées pour durcir les métaux, les alliages et d’autres matériaux.
- Durcissement par traitement de surface : Ce procédé consiste à modifier la surface des matériaux pour améliorer leur résistance à l’usure, à la corrosion ou à d’autres types de dégradation. Des techniques telles que le placage, la nitruration, la carbonitruration et le revêtement sont utilisées pour appliquer des couches protectrices sur la surface des matériaux.
- Durcissement par polymérisation : Ce procédé consiste à durcir les matériaux polymères en les exposant à des agents chimiques, à la chaleur ou à la lumière, ce qui provoque la polymérisation des monomères et la formation de liaisons chimiques entre les chaînes polymères. Des techniques telles que la polymérisation radicalaire, la polymérisation ionique et la polymérisation par rayonnement UV sont utilisées pour durcir les plastiques et autres polymères.
- Durcissement par traitement mécanique : Ce procédé implique l’application de contraintes mécaniques aux matériaux pour améliorer leur résistance et leur durabilité. Des techniques telles que la déformation plastique, le grenaillage et le martelage sont utilisées pour durcir les métaux et d’autres matériaux par déformation plastique et par renforcement de la structure cristalline.
- Durcissement par traitement chimique : Ce procédé consiste à modifier la composition chimique des matériaux pour améliorer leurs propriétés. Des techniques telles que la carbonatation, la cémentation et la nitridation sont utilisées pour introduire des éléments chimiques dans la structure des matériaux et améliorer leur résistance et leur durabilité.
Ces procédés de durcissement sont essentiels dans de nombreuses industries telles que l’automobile, l’aérospatiale, la construction, l’électronique et la fabrication d’outils, où ils sont utilisés pour produire des matériaux et des composants de haute qualité adaptés à des applications exigeantes. En comprenant les principes et les techniques de durcissement, les ingénieurs et les fabricants peuvent concevoir des produits plus résistants, plus durables et plus performants.
Thermoséchage :
Le thermoséchage est un processus de séchage qui utilise la chaleur pour éliminer l’humidité des matériaux de manière contrôlée. Ce processus est largement utilisé dans diverses industries pour sécher des produits sensibles à la chaleur tout en préservant leur qualité et leurs propriétés.
Le thermoséchage implique généralement l’utilisation de séchoirs spécialement conçus qui fournissent une source de chaleur contrôlée pour accélérer le processus d’évaporation de l’humidité. Ces séchoirs peuvent fonctionner selon différents principes de transfert de chaleur, tels que la convection, la conduction et le rayonnement, en fonction des caractéristiques des matériaux à sécher et des exigences du processus.
Lors du thermoséchage, les matériaux sont placés à l’intérieur du séchoir et exposés à des températures élevées pendant des périodes de temps définies. L’humidité présente dans les matériaux s’évapore sous l’effet de la chaleur, et l’air chaud circulant à l’intérieur du séchoir évacue l’humidité évaporée, assurant ainsi un processus de séchage efficace.
Le thermoséchage est utilisé dans de nombreuses applications industrielles, telles que la production alimentaire, la fabrication de produits pharmaceutiques, la transformation du bois, la céramique, et d’autres. Dans l’industrie alimentaire, par exemple, le thermoséchage est utilisé pour sécher des produits tels que les fruits, les légumes, les céréales, les viandes et les poissons, permettant ainsi de prolonger leur durée de conservation tout en préservant leur valeur nutritionnelle et leur qualité organoleptique.
En résumé, le thermoséchage est un processus essentiel dans de nombreuses industries pour éliminer l’humidité des matériaux de manière efficace et contrôlée. En comprenant les principes du thermoséchage et en utilisant des équipements appropriés, les entreprises peuvent améliorer leur efficacité de production et garantir la qualité de leurs produits finaux.
Durcissement des matériaux :
Le durcissement des matériaux est un processus fondamental dans l’industrie visant à renforcer les propriétés mécaniques des matériaux en modifiant leur structure interne ou leur composition chimique. Ce processus est essentiel pour améliorer la résistance, la durabilité et la performance des matériaux dans une variété d’applications industrielles et commerciales.
Il existe plusieurs méthodes de durcissement des matériaux, chacune adaptée à des types de matériaux spécifiques et à des exigences de performance particulières. Parmi les méthodes les plus couramment utilisées, on peut citer :
- Le durcissement par traitement thermique : Ce processus implique le chauffage des matériaux à des températures élevées suivies d’un refroidissement contrôlé pour modifier leur structure cristalline et améliorer leurs propriétés mécaniques. Des techniques telles que la trempe, le revenu, le recuit et la cémentation sont utilisées pour durcir les métaux, les alliages et d’autres matériaux.
- Le durcissement par traitement de surface : Ce procédé consiste à modifier la surface des matériaux pour améliorer leur résistance à l’usure, à la corrosion ou à d’autres types de dégradation. Des techniques telles que le placage, la nitruration, la carbonitruration et le revêtement sont utilisées pour appliquer des couches protectrices sur la surface des matériaux.
- Le durcissement par polymérisation : Ce processus consiste à durcir les matériaux polymères en les exposant à des agents chimiques, à la chaleur ou à la lumière, ce qui provoque la polymérisation des monomères et la formation de liaisons chimiques entre les chaînes polymères. Des techniques telles que la polymérisation radicalaire, la polymérisation ionique et la polymérisation par rayonnement UV sont utilisées pour durcir les plastiques et autres polymères.
- Le durcissement par traitement mécanique : Ce procédé implique l’application de contraintes mécaniques aux matériaux pour améliorer leur résistance et leur durabilité. Des techniques telles que la déformation plastique, le grenaillage et le martelage sont utilisées pour durcir les métaux et d’autres matériaux par déformation plastique et par renforcement de la structure cristalline.
- Le durcissement par traitement chimique : Ce procédé consiste à modifier la composition chimique des matériaux pour améliorer leurs propriétés. Des techniques telles que la carbonatation, la cémentation et la nitridation sont utilisées pour introduire des éléments chimiques dans la structure des matériaux et améliorer leur résistance et leur durabilité.
En conclusion, le durcissement des matériaux est un processus essentiel dans de nombreuses industries pour garantir la qualité et la performance des produits finaux. En comprenant les principes et les techniques de durcissement, les ingénieurs et les fabricants peuvent concevoir des matériaux adaptés à une large gamme d’applications industrielles et commerciales, offrant ainsi des avantages significatifs en termes de résistance, de durabilité et de fiabilité.
Four de Polymérisation au Gaz
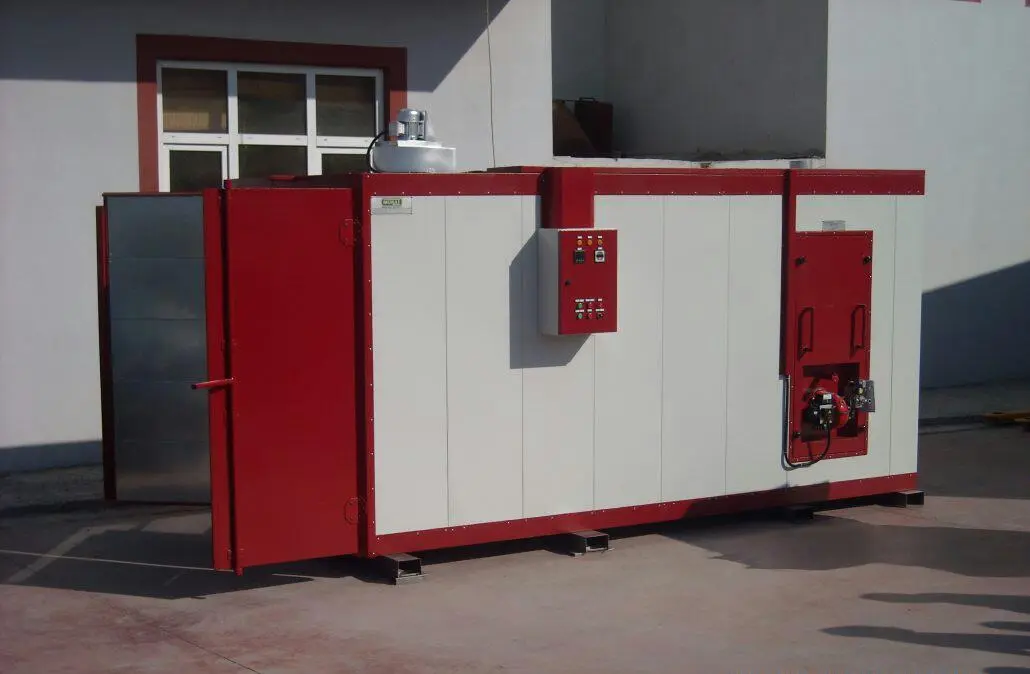
Un four de polymérisation est un type de four industriel qui est utilisé pour chauffer des matériaux à des températures élevées afin de les solidifier ou de les durcir. Les fours de polymérisation sont utilisés dans une variété d’industries, notamment l’automobile, l’aéronautique, l’électronique et la fabrication.
Un four de polymérisation au gaz est un type de four industriel qui utilise le gaz naturel pour chauffer des matériaux à des températures élevées afin de les solidifier ou de les durcir. Les fours de polymérisation au gaz sont utilisés dans une variété d’industries, notamment l’automobile, l’aéronautique, l’électronique et la fabrication.
Les fours de polymérisation au gaz sont généralement constitués des composants suivants :
- Une enceinte : l’enceinte est la structure qui entoure le matériau à polymériser. Elle est généralement en acier ou en aluminium.
- Un système de chauffage : le système de chauffage fournit la chaleur nécessaire pour polymériser le matériau. Le type de système de chauffage utilisé est un brûleur au gaz naturel.
- Un système de contrôle : le système de contrôle permet de réguler la température et le temps de polymérisation.
Le processus de polymérisation dans un four au gaz est le suivant :
- Le matériau à polymériser est placé dans l’enceinte.
- Le brûleur au gaz naturel est allumé pour chauffer le matériau.
- Le matériau polymérise à la température et au temps spécifiés.
La température de polymérisation varie en fonction du matériau à polymériser. Les matériaux thermoplastiques, comme le plastique, polymérisent généralement à des températures inférieures à 200 degrés Celsius. Les matériaux thermodurcissables, comme la résine époxy, polymérisent généralement à des températures supérieures à 200 degrés Celsius.
Le temps de polymérisation varie également en fonction du matériau à polymériser. Les matériaux thermoplastiques polymérisent généralement en quelques minutes. Les matériaux thermodurcissables polymérisent généralement en quelques heures ou quelques jours.
Les fours de polymérisation au gaz offrent les avantages suivants :
- Ils sont généralement plus efficaces que les fours électriques.
- Ils sont moins coûteux à installer et à entretenir que les fours électriques.
- Ils sont moins susceptibles de causer des problèmes de pollution de l’air que les fours électriques.
Cependant, les fours de polymérisation au gaz présentent également quelques inconvénients :
- Ils peuvent être dangereux s’ils ne sont pas correctement entretenus.
- Ils peuvent produire des émissions de gaz à effet de serre.
Les fours de polymérisation au gaz sont un choix populaire pour les industries qui ont besoin de polymériser des matériaux à des températures élevées. Ils offrent une efficacité, une fiabilité et un coût de possession compétitifs.
Four de durcissement avec chauffage électrique
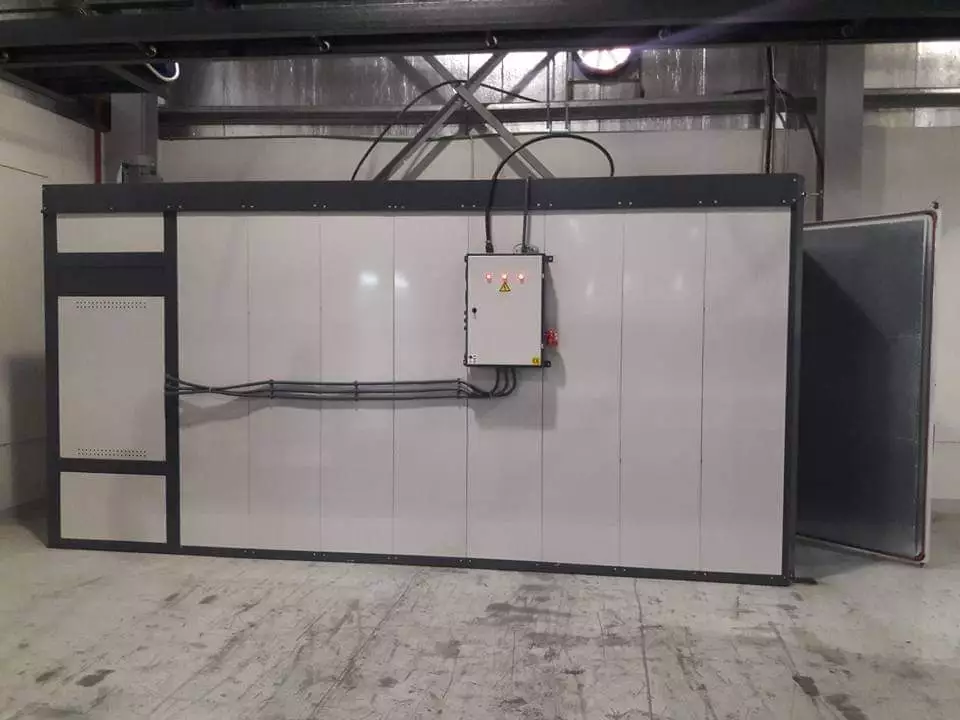
Un four de durcissement avec chauffage électrique est un type de four industriel qui utilise l’électricité pour chauffer les matériaux à des températures élevées afin de les durcir. Les fours de durcissement électriques sont utilisés dans une variété d’industries, notamment l’automobile, l’aéronautique, l’électronique et la fabrication.
Les fours de durcissement électriques sont généralement constitués des composants suivants :
- Une enceinte : l’enceinte est la structure qui entoure le matériau à durcir. Elle est généralement en acier ou en aluminium.
- Un système de chauffage : le système de chauffage fournit la chaleur nécessaire pour durcir le matériau. Le type de système de chauffage utilisé est un élément chauffant électrique.
- Un système de contrôle : le système de contrôle permet de réguler la température et le temps de durcissement.
Le processus de durcissement dans un four électrique est le suivant :
- Le matériau à durcir est placé dans l’enceinte.
- L’élément chauffant électrique est mis en marche pour chauffer le matériau.
- Le matériau durcit à la température et au temps spécifiés.
La température de durcissement varie en fonction du matériau à durcir. Les métaux, tels que l’acier et l’aluminium, sont généralement durcis à des températures supérieures à 200 degrés Celsius.
Le temps de durcissement varie également en fonction du matériau à durcir. Les métaux, tels que l’acier et l’aluminium, sont généralement durcis en quelques heures ou quelques jours.
Les fours de durcissement électriques offrent les avantages suivants :
- Ils sont généralement plus propres que les fours à gaz.
- Ils sont plus sûrs que les fours à gaz.
- Ils sont plus faciles à maintenir que les fours à gaz.
Cependant, les fours de durcissement électriques présentent également quelques inconvénients :
- Ils peuvent être plus chers que les fours à gaz.
- Ils peuvent être moins efficaces que les fours à gaz.
Les fours de durcissement électriques sont un choix populaire pour les industries qui ont besoin de durcir des matériaux à des températures élevées. Ils offrent une efficacité, une fiabilité et un coût de possession compétitifs.
Cabine de Revêtement en Poudre avec Filtres
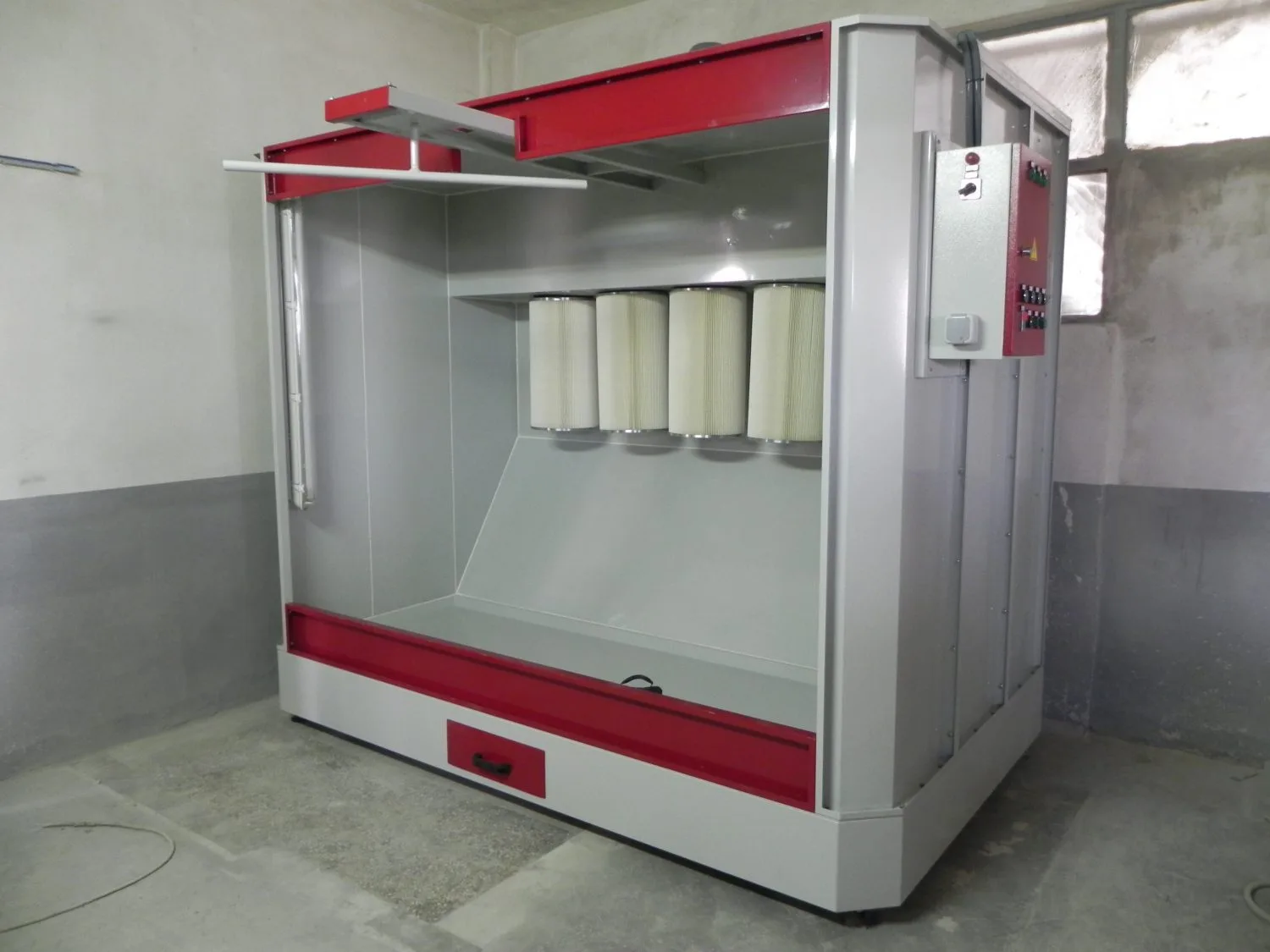
Une cabine de revêtement en poudre avec filtres est un type de cabine de pulvérisation de peinture qui utilise des filtres pour collecter la peinture en poudre non utilisée. Les cabines de revêtement en poudre sont utilisées pour appliquer des revêtements en poudre sur des pièces métalliques et autres matériaux. Les filtres sont essentiels pour garantir que la peinture en poudre non utilisée ne soit pas libérée dans l’environnement.
Les cabines de revêtement en poudre avec filtres sont généralement constituées des composants suivants :
- Une enceinte : l’enceinte est la structure qui entoure les pièces à revêtir. Elle est généralement en acier ou en aluminium.
- Un pistolet de pulvérisation : le pistolet de pulvérisation est utilisé pour appliquer la peinture en poudre sur les pièces.
- Un système de ventilation : le système de ventilation est utilisé pour aspirer la peinture en poudre non utilisée de l’enceinte.
- Un système de filtration : le système de filtration est utilisé pour collecter la peinture en poudre non utilisée.
Le processus de revêtement en poudre dans une cabine avec filtres est le suivant :
- Les pièces à revêtir sont placées dans l’enceinte.
- Le pistolet de pulvérisation est utilisé pour appliquer la peinture en poudre sur les pièces.
- La peinture en poudre non utilisée est aspirée par le système de ventilation.
- La peinture en poudre non utilisée est collectée par le système de filtration.
Les filtres utilisés dans les cabines de revêtement en poudre sont généralement en fibre de verre, en polyester ou en céramique. Les filtres en fibre de verre sont les plus courants et les moins chers. Les filtres en polyester sont plus durables que les filtres en fibre de verre, mais ils sont également plus chers. Les filtres en céramique sont les plus durables et offrent la meilleure filtration, mais ils sont également les plus chers.
Les cabines de revêtement en poudre avec filtres sont un moyen efficace et sûr d’appliquer des revêtements en poudre. Elles aident à protéger l’environnement et les travailleurs des expositions à la peinture en poudre.
Cabine :
Une cabine de revêtement est une structure spécialement conçue pour abriter le processus de revêtement de divers matériaux, notamment les peintures, les revêtements en poudre et d’autres substances similaires. Ces cabines sont souvent utilisées dans les industries manufacturières, notamment l’automobile, l’aérospatiale, la fabrication de meubles et d’autres secteurs où des finitions de haute qualité sont nécessaires.
Les cabines de revêtement sont généralement fabriquées à partir de matériaux robustes et résistants tels que l’acier galvanisé ou l’aluminium pour assurer une durabilité à long terme. Elles sont équipées de systèmes de ventilation sophistiqués pour assurer une circulation adéquate de l’air et évacuer les vapeurs potentiellement dangereuses.
De plus, les cabines de revêtement sont souvent équipées de dispositifs de filtration avancés pour capturer les particules de peinture ou de poudre en suspension dans l’air. Ces filtres sont essentiels pour maintenir un environnement de travail sûr et propre tout en réduisant les émissions nocives dans l’atmosphère.
En outre, les cabines de revêtement peuvent être équipées de systèmes de contrôle de la température et de l’humidité pour optimiser les conditions de travail et garantir des résultats de revêtement uniformes et de haute qualité. Elles peuvent également être équipées de dispositifs d’éclairage spéciaux pour permettre aux opérateurs de visualiser avec précision le processus de revêtement.
En résumé, les cabines de revêtement jouent un rôle essentiel dans le processus de finition industrielle en fournissant un environnement contrôlé où les matériaux peuvent être appliqués de manière efficace, sûre et précise pour obtenir des résultats optimaux.
Revêtement :
Le revêtement, dans le contexte industriel, fait référence à l’application d’une couche protectrice ou décorative sur la surface d’un matériau ou d’un produit. Cette couche peut être composée de divers matériaux, tels que des peintures liquides, des revêtements en poudre, des vernis, des émaux, des résines, ou d’autres substances spécifiques selon les besoins de protection, d’esthétique ou de fonctionnalité.
Les revêtements servent à protéger les surfaces contre la corrosion, l’usure, les rayures, les produits chimiques agressifs, les intempéries et d’autres agressions environnementales. Ils peuvent également être utilisés pour modifier les propriétés physiques, chimiques ou optiques des surfaces, améliorer leur adhérence, leur résistance aux UV, leur isolation électrique, leur conductivité thermique, ou encore pour leur conférer des propriétés antimicrobiennes ou ignifuges.
Le processus de revêtement peut être réalisé à l’aide de différentes techniques, telles que la pulvérisation, l’immersion, le laminage, le trempage, ou l’électrodéposition, en fonction des caractéristiques du matériau de base, de la composition du revêtement et des spécifications de l’application finale.
Les industries telles que l’automobile, l’aérospatiale, la construction, l’électronique, le mobilier, l’emballage, et bien d’autres, utilisent largement des revêtements pour améliorer la durabilité, l’aspect esthétique et les performances de leurs produits.
En conclusion, le revêtement joue un rôle essentiel dans la protection, la décoration et l’amélioration des propriétés fonctionnelles des surfaces dans de nombreux secteurs industriels, contribuant ainsi à prolonger la durée de vie des produits et à répondre aux exigences de qualité et de performance des clients.
Poudre
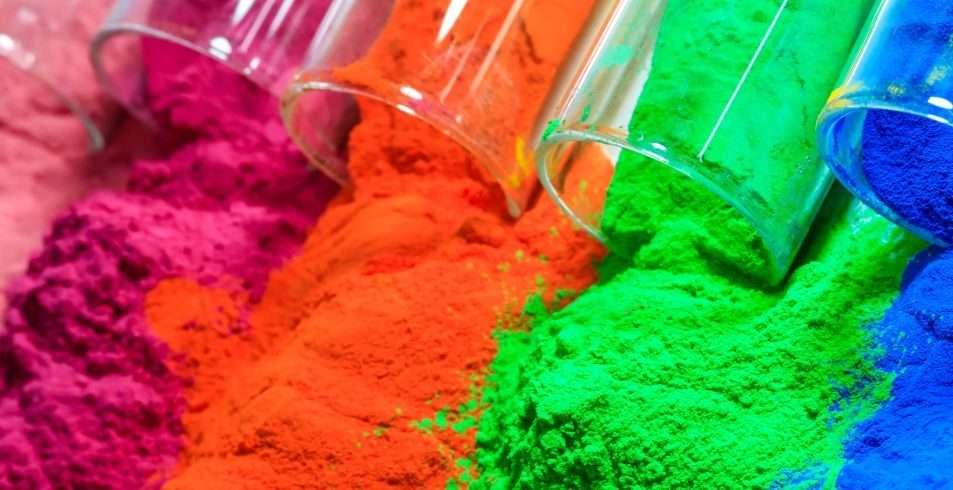
La poudre est un matériau finement divisé sous forme de particules solides, souvent utilisé dans divers processus industriels, y compris le revêtement de surface. Dans le contexte du revêtement en poudre, la poudre est généralement composée de résines thermodurcissables, de pigments, de charges et d’additifs, formant un mélange sec qui peut être appliqué sur une surface à l’aide d’un procédé de pulvérisation électrostatique.
Les revêtements en poudre offrent plusieurs avantages par rapport aux revêtements liquides traditionnels. Ils sont exempts de solvants volatils, ce qui réduit les émissions de composés organiques volatils (COV) et les risques pour l’environnement et la santé des travailleurs. De plus, les revêtements en poudre peuvent être appliqués de manière plus uniforme, avec une meilleure adhérence et une résistance supérieure à la corrosion, à l’abrasion et aux produits chimiques.
Le processus de revêtement en poudre implique la projection électrostatique de la poudre sur une pièce préalablement préparée, suivie d’une étape de cuisson où la poudre fond et se polymérise pour former un film durable et homogène. Ce processus est souvent réalisé dans une cabine de revêtement spécialement conçue pour contenir la poudre en suspension dans l’air et éviter sa dispersion dans l’environnement de travail.
Les revêtements en poudre sont largement utilisés dans divers secteurs industriels, notamment l’automobile, l’électronique, le mobilier, l’architecture, les équipements sportifs et récréatifs, en raison de leur polyvalence, de leur durabilité et de leur esthétique. Ils offrent une large gamme de couleurs, de finitions et de textures, permettant aux fabricants de personnaliser leurs produits selon les besoins et les préférences des clients.
En conclusion, le revêtement en poudre est une technique efficace et écologique pour protéger et embellir les surfaces dans de nombreux domaines industriels, offrant des performances supérieures et une esthétique attrayante tout en respectant les normes environnementales et de sécurité.
Filtres
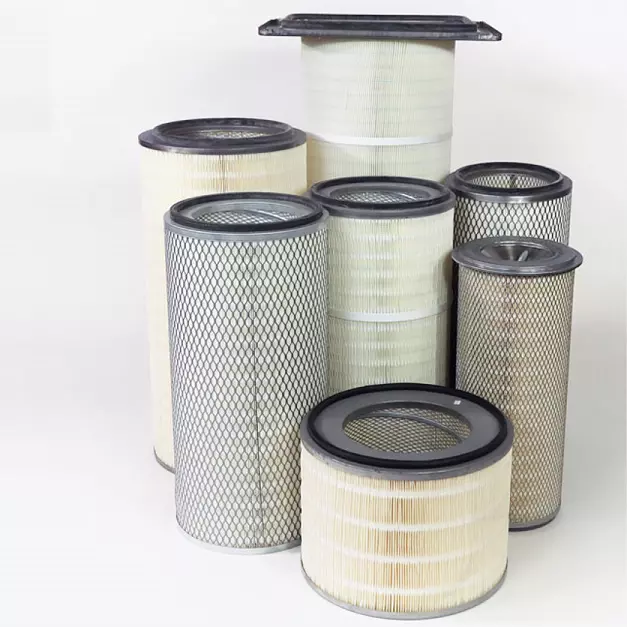
Les filtres sont des dispositifs utilisés pour séparer les particules solides ou liquides présentes dans un fluide, comme l’air ou l’eau, afin de purifier ou de filtrer le fluide. Dans le contexte des cabines de revêtement en poudre, les filtres jouent un rôle crucial dans la capture et la rétention des particules de poudre en suspension dans l’air pendant le processus de pulvérisation.
Les cabines de revêtement sont équipées de différents types de filtres conçus pour éliminer efficacement les particules de différentes tailles, allant des plus grosses aux plus fines. Les filtres grossiers, tels que les filtres préfiltres ou les filtres à particules de plus grande taille, captent les grosses particules de poudre dès leur entrée dans la cabine, tandis que les filtres fins, tels que les filtres HEPA (High Efficiency Particulate Air) ou les filtres absolus, retiennent les particules de poudre plus fines avant que l’air ne soit évacué hors de la cabine.
Les filtres utilisés dans les cabines de revêtement doivent être conçus et entretenus avec soin pour assurer une filtration efficace et prévenir toute contamination de l’environnement de travail. Un remplacement régulier des filtres est nécessaire pour maintenir des performances optimales et éviter l’accumulation excessive de particules, ce qui pourrait compromettre la qualité du revêtement et la santé des travailleurs.
En outre, les filtres utilisés dans les cabines de revêtement doivent être conformes aux normes de qualité et de sécurité en vigueur dans l’industrie pour garantir une protection adéquate contre les émissions nocives et les risques pour la santé. Des tests réguliers de performance et de conformité doivent être effectués pour s’assurer que les filtres fonctionnent correctement et respectent les exigences réglementaires.
En résumé, les filtres sont des composants essentiels des cabines de revêtement en poudre, contribuant à maintenir un environnement de travail propre et sûr en éliminant les particules de poudre en suspension dans l’air et en protégeant la santé des travailleurs et l’environnement.
Peinture :
La peinture est un mélange liquide composé de pigments colorés ou transparents, de liants, de solvants et d’additifs, utilisé pour recouvrir et protéger les surfaces des objets ou des structures, ainsi que pour leur donner une apparence esthétique. Elle est largement utilisée dans de nombreux secteurs industriels, notamment l’automobile, la construction, le mobilier, l’aérospatiale, l’art et la décoration.
Les peintures peuvent être classées en différentes catégories en fonction de leur composition et de leurs propriétés. Les peintures à base d’eau, également connues sous le nom de peintures acryliques ou latex, sont constituées de particules de résine dispersées dans l’eau et sont souvent utilisées en raison de leur faible teneur en COV (composés organiques volatils) et de leur facilité de nettoyage. Les peintures à base de solvants, telles que les peintures alkydes ou époxy, contiennent des solvants organiques qui s’évaporent lors du séchage, laissant derrière eux un film de peinture durable.
Le processus de peinture implique généralement plusieurs étapes, notamment la préparation de la surface, l’application de la peinture à l’aide de techniques telles que la pulvérisation, le brossage ou le rouleau, et le séchage ou la polymérisation du revêtement pour former un film solide et adhérent. Des finitions supplémentaires, telles que le polissage, le vernissage ou le durcissement aux UV, peuvent être réalisées pour améliorer l’aspect esthétique et les performances du revêtement.
Les peintures sont disponibles dans une large gamme de couleurs, de finitions et de textures pour répondre aux besoins et aux préférences des utilisateurs. Elles peuvent être formulées pour résister à diverses conditions environnementales, telles que l’exposition aux intempéries, aux rayons UV, à l’humidité, à la chaleur, aux produits chimiques et à l’abrasion, assurant ainsi une protection durable des surfaces.
En conclusion, la peinture joue un rôle essentiel dans la protection, la décoration et l’embellissement des surfaces dans de nombreux domaines industriels et commerciaux, offrant une solution polyvalente et esthétique pour répondre aux exigences de qualité et de performance des clients.
Pulvérisation :
La pulvérisation est un processus d’application de liquides ou de particules sous forme de fines gouttelettes ou de fines particules dispersées dans l’air. Ce processus est largement utilisé dans de nombreux domaines industriels, notamment dans l’application de revêtements, de peintures, d’engrais, de produits chimiques, de pesticides, et dans d’autres processus de traitement et de fabrication.
Dans le contexte du revêtement industriel, la pulvérisation est une technique couramment utilisée pour appliquer des peintures liquides, des revêtements en poudre et d’autres matériaux de revêtement sur des surfaces variées, telles que des métaux, du bois, du plastique, du verre et des composites. Elle permet une distribution uniforme du matériau de revêtement sur toute la surface à traiter, assurant ainsi une finition homogène et de haute qualité.
La pulvérisation peut être réalisée à l’aide de différents équipements et techniques, notamment la pulvérisation pneumatique, la pulvérisation airless, la pulvérisation électrostatique, la pulvérisation par pistolet, la pulvérisation à ultrasons, et d’autres méthodes spécifiques adaptées aux exigences particulières du processus de revêtement et du matériau utilisé.
Les avantages de la pulvérisation dans le processus de revêtement comprennent une application rapide et efficace, une couverture uniforme des surfaces complexes ou irrégulières, une réduction du gaspillage de matériau, une économie de temps et de main-d’œuvre, ainsi que la possibilité d’atteindre des épaisseurs de revêtement précises et contrôlées.
Cependant, la pulvérisation peut également présenter des défis, tels que la formation de brouillard ou de surpulvérisation, la nécessité de contrôler étroitement les paramètres de pulvérisation, tels que la pression, le débit et la distance de pulvérisation, ainsi que la nécessité de prendre des mesures pour assurer la sécurité des travailleurs et éviter la contamination de l’environnement.
En résumé, la pulvérisation est une technique polyvalente et efficace pour l’application de revêtements et d’autres matériaux dans de nombreux processus industriels, offrant des avantages significatifs en termes de qualité, de productivité et de performance des produits finaux.
Équipement :
Dans le contexte industriel, l’équipement fait référence à l’ensemble des outils, des machines, des dispositifs et des installations utilisés dans le cadre des processus de fabrication, de production, de transformation ou d’assemblage. L’équipement est un élément essentiel de toute opération industrielle, car il permet d’automatiser des tâches, d’augmenter l’efficacité, d’améliorer la qualité des produits, et de garantir la sécurité des travailleurs.
Dans le domaine du revêtement industriel, l’équipement comprend une gamme de dispositifs spécifiques conçus pour appliquer des revêtements de manière précise, efficace et sécurisée. Cela peut inclure des cabines de revêtement, des systèmes de pulvérisation, des pistolets de peinture, des fours de polymérisation, des équipements de traitement de surface, des dispositifs de contrôle de la qualité, des systèmes de gestion des déchets, et d’autres équipements spécialisés adaptés aux besoins spécifiques de l’application de revêtement.
L’équipement utilisé dans le processus de revêtement est généralement conçu pour répondre à des exigences particulières en termes de taille, de forme, de type de matériau, de spécifications de revêtement, de cadence de production, et de normes de qualité et de sécurité. Il doit être choisi avec soin pour garantir sa compatibilité avec les matériaux à revêtir, les conditions de travail et les objectifs de performance.
La maintenance et l’entretien réguliers de l’équipement sont essentiels pour assurer son bon fonctionnement, prolonger sa durée de vie utile, et éviter les interruptions de production imprévues. Cela implique des activités telles que le nettoyage, la lubrification, le remplacement des pièces usées, le calibrage des instruments de mesure, et la réalisation de tests de performance périodiques.
En outre, l’installation appropriée de l’équipement, ainsi que la formation adéquate du personnel sur son utilisation et sa maintenance, sont des aspects essentiels pour garantir la sécurité des travailleurs, la conformité aux réglementations en vigueur, et la réalisation des objectifs de production de manière efficace et rentable.
En résumé, l’équipement joue un rôle crucial dans le processus de revêtement industriel, fournissant les moyens nécessaires pour appliquer des revêtements de manière fiable, efficiente et sécurisée, tout en contribuant à l’amélioration de la qualité des produits et à la satisfaction des clients.
Industriel :
Le terme “industriel” est utilisé pour décrire tout ce qui est lié à l’industrie, c’est-à-dire à la production de biens matériels en grande quantité, souvent à l’aide de machines et de processus automatisés. Il englobe un large éventail d’activités, de secteurs et de domaines d’application, allant de la fabrication de produits manufacturés à la production d’énergie, en passant par la transformation des matières premières et la construction.
Dans le contexte du revêtement industriel, le terme “industriel” est souvent associé à des processus et à des équipements utilisés dans les environnements de fabrication et de production à grande échelle. Cela peut inclure des opérations telles que la peinture de pièces automobiles, le revêtement de structures métalliques, la protection anticorrosion des équipements industriels, la finition des produits électroniques, et d’autres applications similaires.
Les processus de revêtement industriel sont généralement caractérisés par leur haute capacité de production, leur utilisation intensive d’équipements spécialisés, leur conformité à des normes de qualité strictes, et leur nécessité de répondre à des exigences spécifiques en matière de durabilité, de résistance et d’esthétique. Ils sont souvent réalisés dans des installations industrielles dédiées, équipées de cabines de revêtement, de lignes de production automatisées, et de systèmes de contrôle et de surveillance avancés.
Les revêtements industriels peuvent être appliqués sur une grande variété de substrats, tels que des métaux, du plastique, du bois, du verre, des composites, et d’autres matériaux, pour fournir une protection contre la corrosion, l’usure, les produits chimiques, les intempéries, et pour améliorer l’esthétique et la fonctionnalité des produits finis.
En résumé, le revêtement industriel joue un rôle essentiel dans de nombreux secteurs industriels en fournissant des solutions de protection et de finition pour une grande diversité de produits et de structures, contribuant ainsi à assurer la durabilité, la qualité et la performance des produits fabriqués à grande échelle.
Traitement :
Dans le contexte industriel, le terme “traitement” fait référence à un ensemble d’opérations ou de procédés appliqués à un matériau, un produit ou une substance pour modifier ses propriétés physiques, chimiques ou mécaniques, en vue d’atteindre un objectif spécifique. Le traitement peut inclure diverses étapes telles que le nettoyage, la préparation de surface, la modification de la structure cristalline, la transformation chimique, le durcissement, la polymérisation, et d’autres processus spécialisés selon les besoins de l’application.
Dans le domaine du revêtement industriel, le traitement des surfaces joue un rôle crucial dans la préparation des substrats avant l’application du revêtement proprement dit. Cette étape vise à éliminer les contaminants, les impuretés, les oxydes, les graisses et autres substances qui pourraient compromettre l’adhérence et la qualité du revêtement. Le traitement de surface peut impliquer des techniques telles que le décapage chimique, le sablage, le dégraissage, le dérochage, la conversion de surface, le dégraissage, le dérochage, et d’autres méthodes spécifiques adaptées aux caractéristiques du matériau et aux exigences de l’application.
Une fois que la surface a été correctement préparée, elle est prête à recevoir le revêtement. Ce dernier peut être appliqué à l’aide de différentes techniques, telles que la pulvérisation, l’immersion, le laminage, le trempage, ou l’électrodéposition, selon les caractéristiques du matériau de base, les spécifications de revêtement, et les exigences de performance du produit final.
En outre, le traitement peut également faire référence à des processus post-revêtement visant à améliorer les propriétés du revêtement, telles que la polymérisation, le durcissement, le séchage, le vernissage, le polissage, le grenaillage, le meulage, ou d’autres traitements spécifiques pour obtenir les propriétés souhaitées en termes de résistance, d’adhérence, de brillance, de texture, et d’autres caractéristiques esthétiques ou fonctionnelles.
En résumé, le traitement des surfaces joue un rôle essentiel dans le processus de revêtement industriel en assurant la préparation adéquate des substrats et en optimisant les performances et la durabilité des revêtements appliqués, contribuant ainsi à la qualité et à la fiabilité des produits finis.
Protection :
Dans le contexte industriel, la protection fait référence à l’ensemble des mesures, des techniques et des matériaux utilisés pour préserver les équipements, les structures, les surfaces et les produits contre les dommages, la corrosion, l’usure, les agressions environnementales, les impacts, les chocs, et autres formes de détérioration ou de dégradation. La protection est essentielle pour prolonger la durée de vie utile des biens matériels, réduire les coûts de maintenance, assurer la sécurité des travailleurs, et garantir la qualité et la performance des produits.
Dans le domaine du revêtement industriel, la protection joue un rôle crucial dans la préservation des surfaces contre les effets nocifs de l’exposition aux intempéries, aux produits chimiques, à la corrosion, à l’abrasion, aux rayons UV, et autres agressions environnementales. Les revêtements de protection, tels que les peintures, les vernis, les revêtements en poudre, les résines époxy, les polymères, et autres matériaux spécialisés, sont appliqués sur les surfaces pour former une barrière protectrice durable qui les isole et les protège des dommages extérieurs.
Les revêtements de protection peuvent être formulés pour répondre à des exigences spécifiques en termes de résistance chimique, thermique, mécanique, électrique, ou optique, en fonction des conditions d’utilisation prévues et des propriétés du matériau de base. Ils peuvent être appliqués sur une grande variété de substrats, y compris les métaux, le béton, le bois, le plastique, le verre, les composites, et d’autres matériaux, pour fournir une protection adaptée à chaque application.
En plus des revêtements de protection, d’autres mesures peuvent être prises pour renforcer la protection des surfaces, telles que l’utilisation de revêtements anticorrosion, de revêtements ignifuges, de revêtements anti-UV, de revêtements antiadhésifs, de revêtements antimicrobiens, de systèmes de cathodique, de traitement de surface, et d’autres techniques spécialisées adaptées aux exigences spécifiques de chaque application.
En résumé, la protection des surfaces est un aspect crucial du processus de revêtement industriel, visant à préserver la durabilité, l’esthétique et la fonctionnalité des produits et des structures dans divers environnements et conditions d’utilisation. Les revêtements de protection jouent un rôle central dans cette stratégie de protection en fournissant une barrière efficace contre les dommages et en assurant une performance à long terme des surfaces revêtues.
Système de Déplacement Vertical
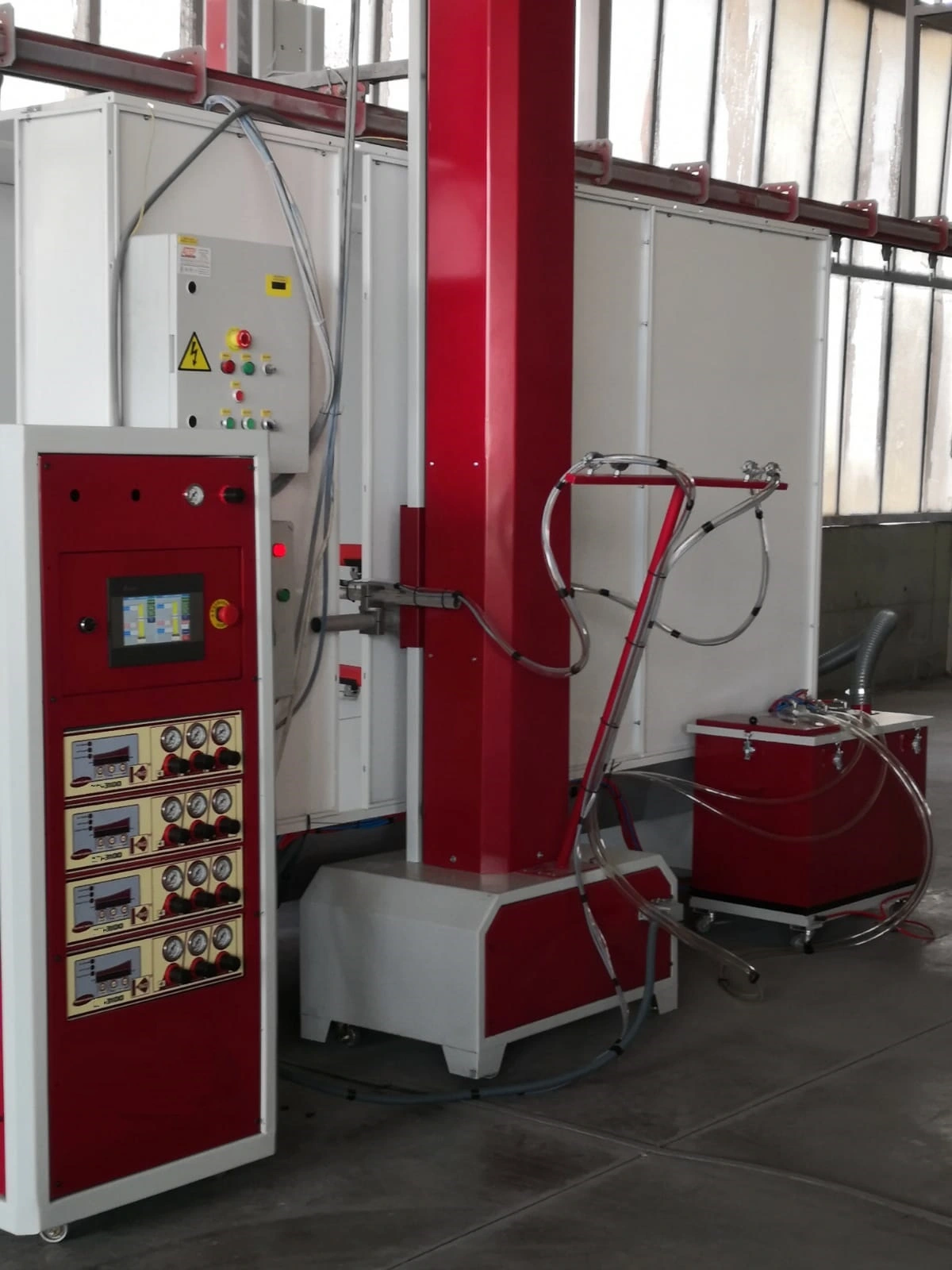
Les systèmes de déplacement vertical avec application en poudre pour les produits industriels sont utilisés pour appliquer des revêtements en poudre sur des produits industriels. Les revêtements en poudre sont des revêtements résistants et durables qui sont appliqués par électrostatique. Ils sont souvent utilisés sur des produits industriels tels que les pièces automobiles, les appareils électroménagers et les composants électroniques.
Le processus d’application en poudre dans un système de déplacement vertical se déroule comme suit :
- Les produits sont placés sur le chariot de transport.
- Le chariot de transport est déplacé dans la cabine de pulvérisation.
- Le pistolet de pulvérisation est utilisé pour appliquer le revêtement en poudre sur les produits.
- La peinture en poudre non utilisée est aspirée par le système de ventilation et collectée par le système de filtration.
- Les produits sont retirés de la cabine de pulvérisation et laissés sécher.
Les systèmes de déplacement vertical avec application en poudre pour les produits industriels offrent un certain nombre d’avantages, notamment :
- Une application uniforme du revêtement en poudre.
- Une productivité élevée.
- Une sécurité accrue pour les travailleurs.
Cependant, ces systèmes peuvent également présenter certains inconvénients, notamment :
- Un coût initial élevé.
- Un entretien régulier.
Les systèmes de déplacement vertical avec application en poudre pour les produits industriels sont un choix populaire pour les industries qui ont besoin d’appliquer des revêtements en poudre sur des produits industriels. Ils offrent un moyen efficace et sûr d’appliquer des revêtements en poudre uniformes et durables.
Pistolets Automatiques Corona
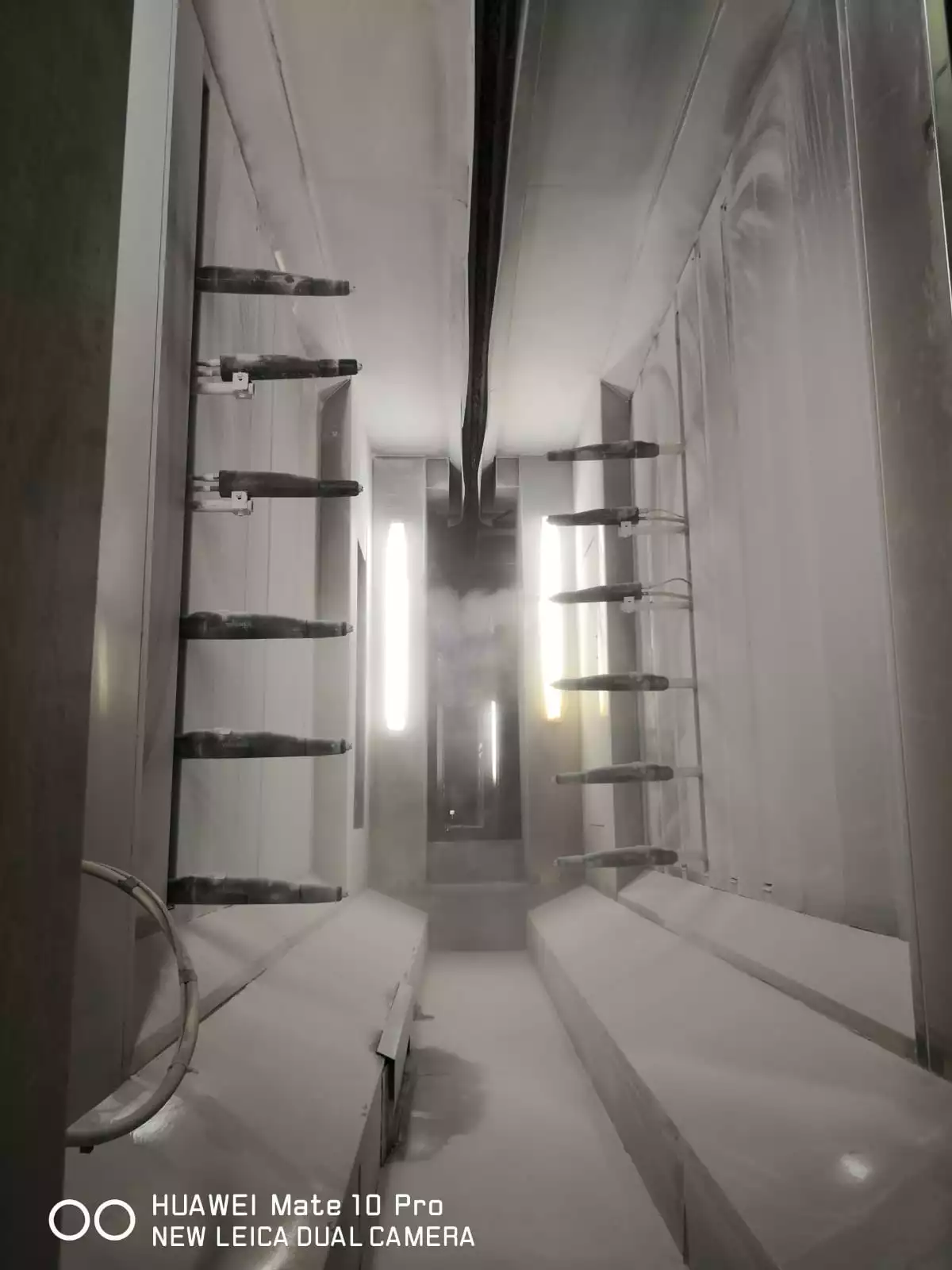
Les pistolets automatiques Corona sont des pistolets de pulvérisation électrostatiques utilisés pour appliquer des revêtements en poudre sur des pièces industrielles. Ils sont conçus pour fournir une application uniforme et efficace de la poudre, même sur des pièces complexes.
Les pistolets automatiques Corona fonctionnent en utilisant un champ électrique pour charger la poudre et la faire adhérer aux pièces. Le pistolet comprend une cascade haute tension qui génère un champ électrique entre la buse et la pièce. La poudre est chargée négativement par la buse et la pièce est chargée positivement par la surface. Cette différence de charge électrique attire la poudre vers la pièce.
Les pistolets automatiques Corona offrent un certain nombre d’avantages par rapport aux pistolets manuels, notamment :
- Une productivité élevée : Les pistolets automatiques peuvent appliquer la poudre plus rapidement que les pistolets manuels.
- Une application uniforme : Les pistolets automatiques peuvent appliquer la poudre de manière plus uniforme que les pistolets manuels.
- Une sécurité accrue : Les pistolets automatiques peuvent réduire l’exposition des travailleurs à la poudre.
Les pistolets automatiques Corona sont utilisés dans une variété d’industries, notamment l’automobile, l’aéronautique, l’électronique et la fabrication. Ils sont un choix populaire pour les applications où une application uniforme et efficace de la poudre est nécessaire.
Voici quelques-uns des modèles de pistolets automatiques Corona les plus courants :
- PEA-C4 : Ce pistolet est un modèle compact et polyvalent qui convient à une variété d’applications.
- PEA-C4XL : Ce pistolet est une version plus longue du PEA-C4 qui offre une portée de pulvérisation plus grande.
- PEA-T3 : Ce pistolet est un modèle triboélectrique qui utilise un mécanisme de frottement pour charger la poudre.
- PEA-X1 : Ce pistolet est le modèle le plus récent de Corona et offre une performance et une productivité améliorées.
Le choix du pistolet automatique Corona le plus adapté à une application donnée dépend d’un certain nombre de facteurs, notamment la taille et la complexité des pièces à pulvériser, le type de revêtement en poudre utilisé et le budget.
Applicateurs de Poudre
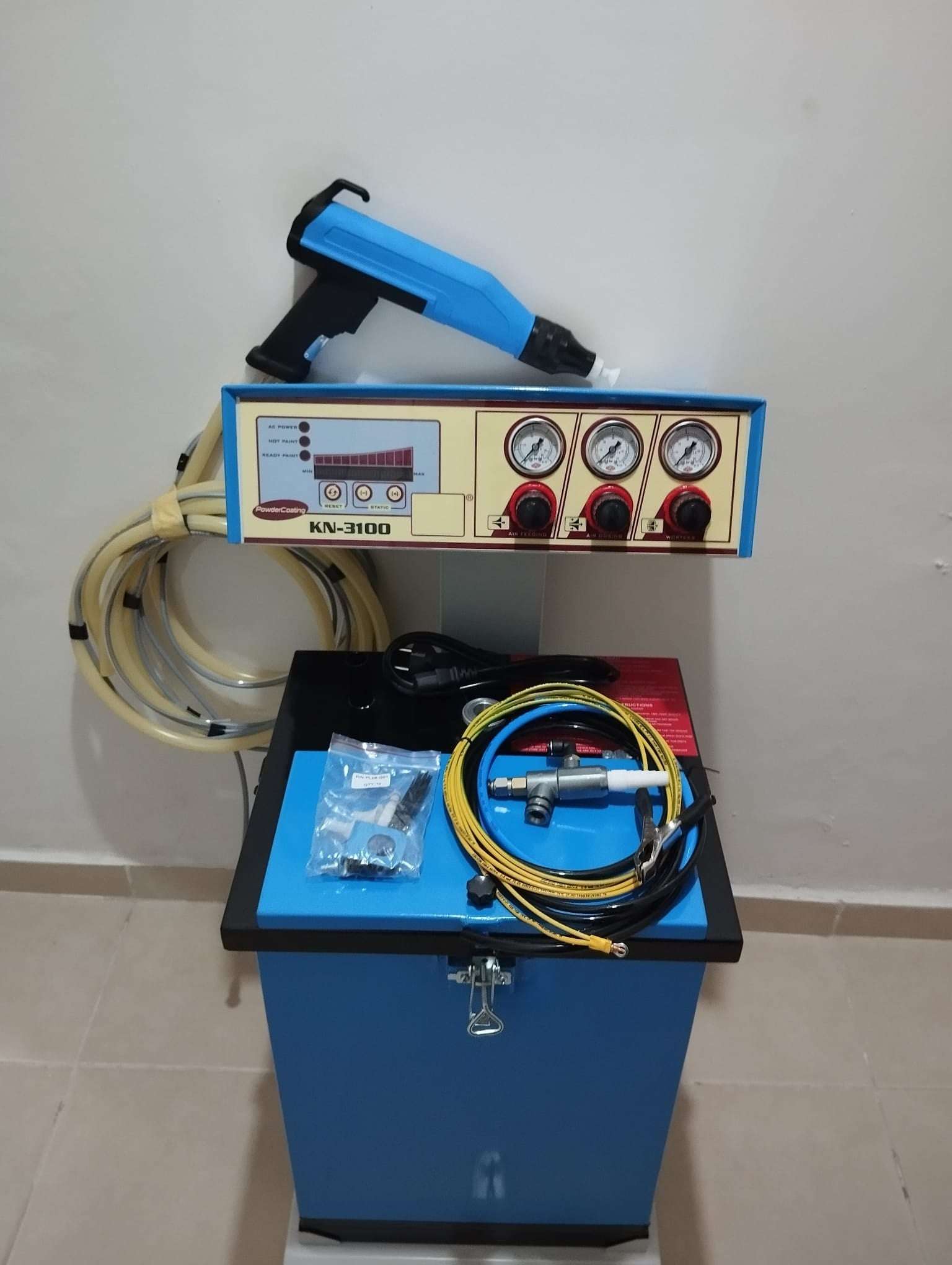
Les applicateurs de poudre sont des équipements utilisés pour appliquer des revêtements en poudre sur des pièces métalliques et autres matériaux. Les revêtements en poudre sont des revêtements résistants et durables qui sont appliqués par électrostatique. Ils sont souvent utilisés sur des produits industriels tels que les pièces automobiles, les appareils électroménagers et les composants électroniques.
Il existe deux principaux types d’applicateurs de poudre : les applicateurs manuels et les applicateurs automatiques.
Applicateurs Manuels
Les applicateurs manuels sont des pistolets de pulvérisation utilisés par un opérateur humain. Ils sont généralement utilisés pour pulvériser de petites pièces ou des pièces complexes.
Les applicateurs manuels fonctionnent en utilisant un champ électrique pour charger la poudre et la faire adhérer aux pièces. Le pistolet comprend une cascade haute tension qui génère un champ électrique entre la buse et la pièce. La poudre est chargée négativement par la buse et la pièce est chargée positivement par la surface. Cette différence de charge électrique attire la poudre vers la pièce.
Applicateurs Automatiques
Les applicateurs automatiques sont des machines qui pulvérisent des revêtements en poudre sur des pièces. Ils sont généralement utilisés pour pulvériser de grandes quantités de pièces ou des pièces simples.
Les applicateurs automatiques fonctionnent de la même manière que les applicateurs manuels, mais ils utilisent un système automatisé pour déplacer la pièce sous la buse de pulvérisation. Cela permet d’appliquer la poudre de manière plus uniforme et plus efficace.
Types d’applicateurs de poudre
Il existe de nombreux types d’applicateurs de poudre disponibles, chacun avec ses propres avantages et inconvénients. Certains des types les plus courants d’applicateurs de poudre incluent :
- Applicateurs électrostatiques : Les applicateurs électrostatiques sont le type d’applicateur de poudre le plus courant. Ils utilisent un champ électrique pour charger la poudre et la faire adhérer aux pièces.
- Applicateurs triboélectriques : Les applicateurs triboélectriques utilisent un mécanisme de frottement pour charger la poudre. Ils sont moins efficaces que les applicateurs électrostatiques, mais ils sont plus durables et moins chers à entretenir.
- Applicateurs sans charge : Les applicateurs sans charge n’utilisent pas de champ électrique pour charger la poudre. Ils utilisent un flux d’air pour déplacer la poudre vers la pièce. Ils sont moins efficaces que les applicateurs électrostatiques ou triboélectriques, mais ils sont plus faciles à utiliser et à entretenir.
Choix de l’applicateur de poudre
Le choix de l’applicateur de poudre le plus adapté à une application donnée dépend d’un certain nombre de facteurs, notamment :
- La taille et la complexité des pièces à pulvériser
- Le type de revêtement en poudre utilisé
- Le budget
Les applicateurs manuels sont généralement utilisés pour pulvériser de petites pièces ou des pièces complexes. Les applicateurs automatiques sont généralement utilisés pour pulvériser de grandes quantités de pièces ou des pièces simples.
Les applicateurs électrostatiques sont le type d’applicateur de poudre le plus courant. Ils sont efficaces pour appliquer des revêtements en poudre sur une variété de surfaces. Les applicateurs triboélectriques sont moins efficaces que les applicateurs électrostatiques, mais ils sont plus durables et moins chers à entretenir. Les applicateurs sans charge sont moins efficaces que les applicateurs électrostatiques ou triboélectriques, mais ils sont plus faciles à utiliser et à entretenir.
Poudrière
Une poudrière évoque souvent des images de mystère, de danger et de potentiel explosif. C’est un lieu où la poudre, cette substance volatile et hautement inflammable, est stockée en grande quantité. Historiquement, les poudrières étaient des installations cruciales pour les armées et les forces militaires, servant à stocker la poudre à canon nécessaire pour alimenter les armes à feu et les canons.
Dans un contexte plus contemporain, le terme “poudrière” peut également être utilisé de manière métaphorique pour décrire une situation ou un lieu où les tensions sont extrêmement élevées et où un conflit ou une explosion de violence semble imminent. Cette utilisation témoigne de la puissance symbolique de la poudre et de son association avec la destruction et le chaos.
Les poudrières sont également des sujets d’intérêt pour les historiens et les archéologues, car elles fournissent des informations précieuses sur les méthodes de stockage de la poudre à différentes époques de l’histoire. Leur étude permet de mieux comprendre l’évolution de la technologie militaire et des pratiques de guerre au fil du temps.
En résumé, une poudrière est bien plus qu’un simple entrepôt de poudre à canon. C’est un symbole de puissance, de danger et de tension, ainsi qu’un sujet d’étude fascinant pour ceux qui s’intéressent à l’histoire militaire et à la technologie des armes à feu.
Poudroyeurs
Les poudroyeurs sont des artisans spécialisés dans le métier de la pulvérisation de poudre. Leur expertise repose sur la manipulation précise et sécurisée de substances pulvérulentes, qu’elles soient destinées à des applications industrielles, artistiques ou pyrotechniques.
Dans le domaine industriel, les poudroyeurs jouent un rôle crucial dans la fabrication de produits divers, tels que les peintures en poudre, les revêtements de surface et les pigments. Leur travail consiste à transformer des matières premières en poudre fine, puis à les appliquer de manière uniforme sur les surfaces désirées, souvent à l’aide d’équipements spécialisés tels que des pistolets de pulvérisation.
Dans le domaine artistique, les poudroyeurs peuvent être sollicités pour créer des œuvres d’art en utilisant des techniques de pulvérisation de poudre. Cette méthode permet aux artistes de produire des effets uniques et texturés sur divers supports, tels que le papier, le bois ou le métal.
Enfin, dans le domaine de la pyrotechnie, les poudroyeurs sont chargés de préparer et de manipuler les compositions explosives utilisées dans les feux d’artifice et les spectacles pyrotechniques. Leur connaissance approfondie des propriétés des différents types de poudres leur permet de créer des effets visuels spectaculaires tout en garantissant la sécurité des spectateurs et des participants.
En somme, les poudroyeurs sont des professionnels hautement qualifiés dont le savoir-faire est indispensable dans de nombreux domaines, de l’industrie à l’art en passant par la pyrotechnie. Leur travail minutieux et précis contribue à la création de produits et d’expériences remarquables qui enrichissent notre vie quotidienne.
Poudreurs
Les poudreurs sont des experts dans l’application de poudres, que ce soit dans le domaine industriel, artisanal ou artistique. Leur métier consiste à maîtriser les techniques permettant de déposer de manière précise et uniforme des poudres sur différentes surfaces, afin d’obtenir des finitions de haute qualité et des effets spécifiques.
Dans l’industrie, les poudreurs sont souvent employés dans des secteurs tels que la peinture en poudre, le revêtement de métaux, la cosmétique ou encore l’industrie pharmaceutique. Leur travail est essentiel pour garantir la durabilité, l’esthétique et parfois même les propriétés fonctionnelles des produits finis. À l’aide d’équipements spécialisés tels que des pistolets électrostatiques ou des cabines de pulvérisation, ils appliquent la poudre de manière contrôlée, en veillant à minimiser les pertes et les défauts.
Dans le domaine artisanal, les poudreurs peuvent travailler sur des projets variés, allant de la restauration de meubles à la décoration d’objets en bois ou en métal. Leur savoir-faire leur permet d’obtenir des finitions fines et sophistiquées, souvent en combinant la pulvérisation de poudre avec d’autres techniques telles que le polissage, le sablage ou le brossage.
Enfin, dans le domaine artistique, les poudreurs explorent les possibilités créatives offertes par la pulvérisation de poudre pour réaliser des œuvres d’art contemporaines. Cette technique permet de jouer avec la texture, la couleur et la luminosité, offrant aux artistes une grande liberté d’expression et la possibilité de créer des œuvres uniques et innovantes.
En résumé, les poudreurs sont des professionnels polyvalents dont le savoir-faire est recherché dans de nombreux domaines. Leur capacité à maîtriser les techniques de pulvérisation de poudre leur permet de contribuer de manière significative à la qualité et à l’esthétique des produits et des œuvres dans lesquels ils interviennent.
Poudre-applicateurs
Les poudre-applicateurs sont des dispositifs spécialisés conçus pour l’application précise et uniforme de poudres sur diverses surfaces. Ces outils sont utilisés dans une variété de contextes, allant de l’industrie manufacturière à l’artisanat et à l’art.
Dans l’industrie, les poudre-applicateurs sont couramment utilisés dans le processus de revêtement en poudre, une méthode de finition de surface largement répandue pour les pièces métalliques. Ce processus implique l’application d’une fine couche de poudre sur la surface de la pièce, suivie de sa fusion et de son durcissement pour former un revêtement durable et résistant à la corrosion. Les poudre-applicateurs industriels sont souvent des équipements sophistiqués, tels que des pistolets de pulvérisation électrostatiques, qui permettent un contrôle précis du débit de poudre et de sa répartition sur la surface à revêtir.
Dans le domaine de l’artisanat, les poudre-applicateurs sont utilisés par des artisans pour diverses applications, telles que la décoration d’objets en bois, en verre ou en céramique. Ces dispositifs permettent aux artisans de créer des finitions texturées et colorées, ajoutant une touche unique à leurs créations.
Enfin, dans le domaine artistique, les poudre-applicateurs offrent aux artistes une autre possibilité d’explorer le potentiel créatif de la poudre. En combinant la pulvérisation de poudre avec d’autres techniques artistiques telles que le pochoir, le masquage et le mélange de couleurs, les artistes peuvent créer des œuvres d’art originales et expressives.
En résumé, les poudre-applicateurs sont des outils polyvalents qui jouent un rôle crucial dans de nombreux processus de fabrication, ainsi que dans la création artistique et artisanale. Leur capacité à appliquer de manière précise et contrôlée des poudres sur diverses surfaces ouvre la voie à une multitude de possibilités créatives et fonctionnelles.
Poudrissage
Le poudrissage est un processus qui consiste à appliquer de la poudre sur une surface donnée dans le but d’obtenir un revêtement protecteur, décoratif ou fonctionnel. Cette technique est largement utilisée dans divers domaines industriels, artisanaux et artistiques en raison de sa polyvalence et de ses nombreux avantages.
Dans l’industrie, le poudrissage est une méthode populaire de revêtement de surface pour les pièces métalliques. Les pièces à revêtir sont d’abord préparées en étant nettoyées et traitées, puis la poudre est appliquée à l’aide d’équipements spécialisés tels que des pistolets de pulvérisation électrostatiques. Une fois la poudre appliquée, la pièce est chauffée pour permettre à la poudre de fondre et de former un revêtement homogène et durable.
Dans le domaine artisanal, le poudrissage est utilisé pour décorer une variété de surfaces, telles que le bois, le verre, la céramique ou le métal. Les artisans peuvent expérimenter avec différentes couleurs et textures de poudre pour créer des effets visuels uniques et personnalisés.
Enfin, dans le domaine artistique, le poudrissage offre aux artistes une autre avenue pour explorer leur créativité. En combinant la pulvérisation de poudre avec d’autres techniques artistiques telles que le pochoir, le masquage et le grattage, les artistes peuvent créer des œuvres d’art multidimensionnelles et expressives.
En résumé, le poudrissage est une technique polyvalente et efficace qui trouve des applications dans de nombreux domaines. Que ce soit pour protéger des pièces métalliques contre la corrosion, décorer des objets artisanaux ou créer des œuvres d’art originales, le poudrissage offre une solution fiable et esthétique pour une variété de besoins.
Machine de Revêtement de Poudre et de Talc pour Câbles
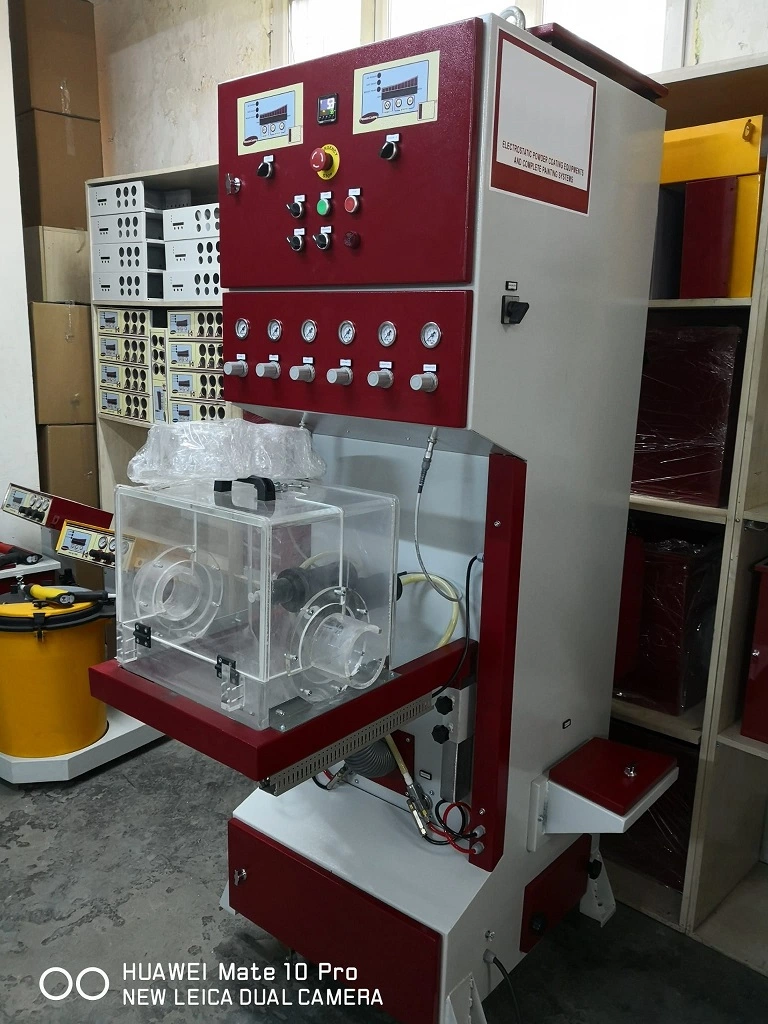
Une machine de revêtement de poudre et de talc pour câbles est un équipement utilisé pour appliquer des revêtements en poudre et de talc sur des câbles. Les revêtements en poudre et de talc sont appliqués pour protéger les câbles de la corrosion, de l’abrasion et des autres dommages.
Les machines de revêtement de poudre et de talc pour câbles sont généralement constituées des composants suivants :
- Un système de transport de câbles : Le système de transport de câbles est utilisé pour déplacer les câbles à travers la machine. Il est généralement constitué d’un convoyeur à bande ou d’un système de rails.
- Un système d’application de poudre : Le système d’application de poudre est utilisé pour appliquer la poudre sur les câbles. Il est généralement constitué d’un pistolet de pulvérisation électrostatique.
- Un système d’application de talc : Le système d’application de talc est utilisé pour appliquer le talc sur les câbles. Il est généralement constitué d’un applicateur rotatif.
- Un système de cuisson : Le système de cuisson est utilisé pour cuire les revêtements en poudre et de talc. Il est généralement constitué d’un four à air chaud.
Le processus de revêtement de poudre et de talc pour câbles se déroule comme suit :
- Les câbles sont placés sur le convoyeur à bande ou le système de rails.
- Le système d’application de poudre est utilisé pour appliquer la poudre sur les câbles.
- Le système d’application de talc est utilisé pour appliquer le talc sur les câbles.
- Les câbles sont cuits dans le four à air chaud.
Les machines de revêtement de poudre et de talc pour câbles offrent un certain nombre d’avantages, notamment :
- Une protection efficace contre la corrosion, l’abrasion et les autres dommages.
- Une amélioration de l’apparence des câbles.
- Une réduction des coûts de maintenance.
Cependant, ces machines peuvent également présenter certains inconvénients, notamment :
- Un coût initial élevé.
- Un entretien régulier.
Les machines de revêtement de poudre et de talc pour câbles sont un choix populaire pour les industries qui ont besoin de protéger les câbles de la corrosion, de l’abrasion et des autres dommages. Elles offrent une solution efficace et durable pour protéger les câbles.
Voici quelques-uns des fabricants de machines de revêtement de poudre et de talc pour câbles les plus courants :
- Corona
- Nordson
- Gema
- Powder Coating Systems
- Equipment Coating Systems
Le choix de la machine de revêtement de poudre et de talc pour câbles la plus adaptée à une application donnée dépend d’un certain nombre de facteurs, notamment :
- La taille et la complexité des câbles à traiter
- Le type de revêtement en poudre et de talc utilisé
- Le budget
Filtre à Cartouche pour Peinture Poudre
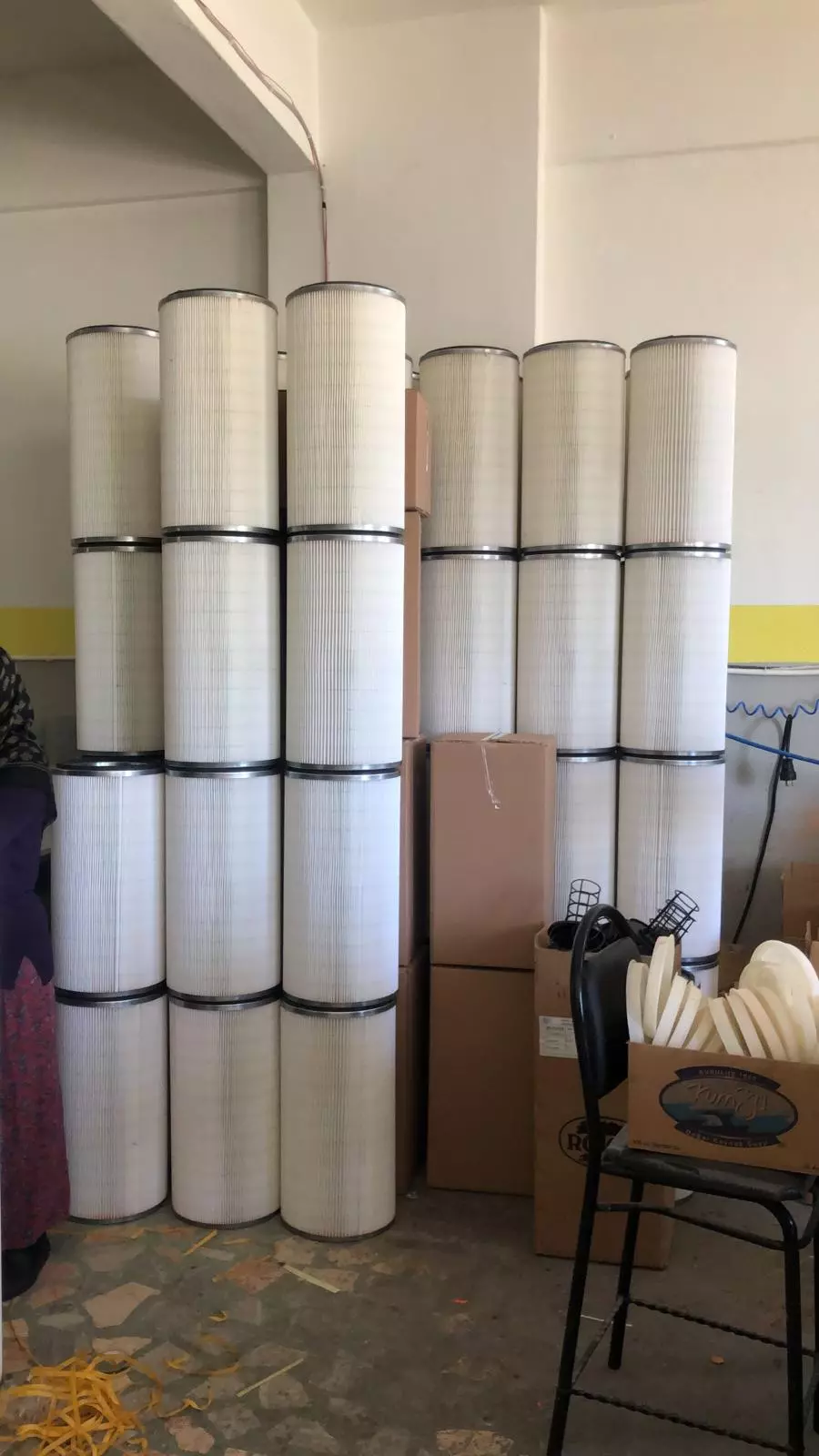
Un filtre à cartouche pour peinture poudre est un type de filtre utilisé pour collecter la peinture poudre non utilisée dans une cabine de pulvérisation. Les filtres à cartouche sont essentiels pour protéger l’environnement et les travailleurs des expositions à la peinture poudre.
Les filtres à cartouche pour peinture poudre sont généralement constitués des composants suivants :
- Une cartouche filtrante : La cartouche filtrante est le composant principal du filtre. Elle est constituée d’un matériau filtrant qui retient la peinture poudre.
- Un cadre de support : Le cadre de support maintient la cartouche filtrante en place.
- Un joint : Le joint assure l’étanchéité du filtre et empêche la peinture poudre de s’échapper.
Les filtres à cartouche pour peinture poudre sont disponibles dans une variété de tailles et de capacités. Le choix du filtre le plus adapté à une application donnée dépend d’un certain nombre de facteurs, notamment :
- Le débit d’air de la cabine de pulvérisation
- Le type de peinture poudre utilisée
- La fréquence d’utilisation de la cabine de pulvérisation
Les filtres à cartouche pour peinture poudre doivent être remplacés régulièrement, en fonction de la fréquence d’utilisation de la cabine de pulvérisation et de la quantité de peinture poudre qui y est appliquée. Un filtre usagé peut laisser passer de la peinture poudre, ce qui peut entraîner une exposition des travailleurs et une pollution de l’environnement.
Voici quelques-uns des avantages des filtres à cartouche pour peinture poudre :
- Ils protègent l’environnement et les travailleurs des expositions à la peinture poudre.
- Ils contribuent à réduire la quantité de peinture poudre rejetée dans l’atmosphère.
- Ils prolongent la durée de vie de la cabine de pulvérisation.
Les filtres à cartouche pour peinture poudre sont un élément essentiel de toute cabine de pulvérisation. Ils contribuent à protéger l’environnement et les travailleurs et à prolonger la durée de vie de la cabine.
Filtre à cartouche :
Un filtre à cartouche est un élément essentiel dans de nombreux systèmes de filtration, utilisé pour éliminer les impuretés et les particules indésirables des liquides ou des gaz. Ce type de filtre se compose d’un boîtier ou d’un cylindre contenant une cartouche filtrante spéciale. La cartouche est généralement fabriquée à partir de matériaux poreux tels que le papier, le polyester ou le polypropylène, qui permettent de piéger les particules tout en laissant passer le fluide.
Dans le contexte des peintures en poudre, les filtres à cartouche sont souvent utilisés pour garantir une qualité optimale du revêtement. Ils contribuent à éliminer les impuretés et les contaminants de l’air comprimé ou des cabines de peinture, assurant ainsi une application uniforme et une finition de haute qualité. Les filtres à cartouche sont conçus pour résister aux conditions de travail rigoureuses et sont disponibles dans une variété de tailles et de configurations pour s’adapter aux besoins spécifiques de chaque application.
En résumé, les filtres à cartouche jouent un rôle crucial dans le processus de peinture en poudre en garantissant la propreté de l’air et en assurant des résultats de revêtement optimaux. Ils offrent une solution efficace et fiable pour filtrer les particules et les contaminants, contribuant ainsi à la qualité et à la durabilité des produits finis.
Peinture poudre :
La peinture en poudre, également connue sous le nom de peinture électrostatique en poudre, est un procédé de revêtement largement utilisé dans de nombreux secteurs industriels. Contrairement aux peintures liquides traditionnelles, la peinture en poudre est appliquée sous forme de poudre sèche et fine, qui est ensuite fondue et durcie pour former un revêtement solide et uniforme.
Ce procédé de revêtement offre de nombreux avantages, notamment une excellente résistance à l’abrasion, aux produits chimiques et à la corrosion, ainsi qu’une finition esthétique de haute qualité. La peinture en poudre est également respectueuse de l’environnement, car elle produit peu de déchets et ne contient généralement pas de solvants volatils.
Dans le processus de peinture en poudre, les pièces à revêtir sont d’abord préparées et nettoyées pour éliminer toute trace de contaminants. Ensuite, la poudre est appliquée sur la surface à l’aide d’un pistolet électrostatique, qui charge électriquement les particules de poudre pour les attirer vers la pièce à revêtir. Une fois la poudre appliquée, la pièce est chauffée dans un four où la poudre fond et se solidifie pour former un revêtement durable.
La peinture en poudre est utilisée dans une grande variété d’applications, notamment dans l’industrie automobile, l’ameublement, l’électroménager, la construction et bien d’autres. Elle offre une solution de revêtement économique et polyvalente, adaptée à une large gamme de matériaux et de formes de pièces. En résumé, la peinture en poudre est un procédé de revêtement efficace, durable et respectueux de l’environnement, qui offre des performances et une esthétique exceptionnelles.
Équipement de filtration :
L’équipement de filtration joue un rôle crucial dans de nombreuses industries où la pureté des liquides ou des gaz est essentielle. Ce type d’équipement est utilisé pour éliminer les particules indésirables, les contaminants et autres impuretés afin de garantir la qualité des produits finis ainsi que le bon fonctionnement des processus de production.
Dans le contexte des peintures en poudre, l’équipement de filtration est essentiel pour maintenir la propreté de l’air comprimé, des cabines de peinture et des systèmes de circulation de la poudre. Les filtres à cartouche, les filtres à manches et d’autres types de systèmes de filtration sont utilisés pour capturer les particules fines et les contaminants qui pourraient compromettre la qualité du revêtement final.
L’équipement de filtration est disponible dans une variété de configurations pour répondre aux besoins spécifiques de chaque application. Des filtres à air pour les cabines de peinture aux filtres à liquide pour les systèmes de préparation de peinture, chaque composant est conçu pour fonctionner de manière efficace et fiable dans des environnements industriels exigeants.
En plus d’améliorer la qualité des produits finis, l’utilisation d’un équipement de filtration approprié peut également contribuer à réduire les coûts de production en prolongeant la durée de vie des équipements et en minimisant les temps d’arrêt liés à la maintenance. De plus, en éliminant les contaminants de l’air et des liquides, l’équipement de filtration contribue à créer des environnements de travail plus sûrs et plus sains pour les opérateurs.
En résumé, l’équipement de filtration est un élément essentiel dans le processus de peinture en poudre, garantissant la pureté des matériaux et la qualité des résultats finaux. Son utilisation appropriée permet de maintenir des normes élevées de performance et de fiabilité tout en offrant des avantages économiques et environnementaux significatifs.
Système de dépoussiérage :
Le système de dépoussiérage est un élément essentiel dans de nombreux environnements industriels où la suppression des poussières et des particules fines est nécessaire pour assurer la sécurité des travailleurs, la qualité des produits et le bon fonctionnement des équipements. Ces systèmes sont conçus pour capturer, collecter et éliminer les particules en suspension dans l’air, réduisant ainsi les risques de contamination et les dommages potentiels aux équipements.
Dans le contexte de la peinture en poudre, les systèmes de dépoussiérage sont utilisés pour éliminer les poussières de poudre excédentaire générées pendant le processus de pulvérisation. Ces systèmes peuvent être intégrés aux cabines de peinture pour collecter les particules de poudre non adhérentes, empêchant ainsi leur dispersion dans l’air ambiant et assurant une application efficace de la peinture.
Les systèmes de dépoussiérage sont disponibles dans une variété de configurations, y compris les dépoussiéreurs à cartouche, les dépoussiéreurs à manches, les filtres à cyclone et les séparateurs électrostatiques. Chaque système est conçu pour répondre à des exigences spécifiques en matière de débit d’air, de taille des particules et de capacité de collecte, assurant ainsi une performance optimale dans diverses applications industrielles.
En plus de leur rôle dans la protection de la santé et de la sécurité des travailleurs, les systèmes de dépoussiérage contribuent également à maintenir des environnements de travail propres et ordonnés, réduisant ainsi les risques d’incendie et de contamination croisée. De plus, en récupérant les particules de poudre excédentaire, ces systèmes permettent une utilisation plus efficace des matériaux et contribuent à réduire les coûts de production.
En résumé, les systèmes de dépoussiérage jouent un rôle crucial dans le processus de peinture en poudre, garantissant la propreté de l’air ambiant et la qualité des résultats finaux. Leur utilisation permet de maintenir des normes élevées de sécurité, de qualité et d’efficacité tout en offrant des avantages économiques et environnementaux significatifs.
Traitement des particules :
Le traitement des particules est une étape essentielle dans de nombreux processus industriels où la manipulation des matériaux en particules est nécessaire. Dans le contexte de la peinture en poudre, le traitement des particules comprend plusieurs aspects, notamment la préparation des matériaux en poudre, la gestion des particules excédentaires et la récupération des particules pour un usage ultérieur.
Tout d’abord, le traitement des particules implique la préparation des matériaux en poudre utilisés dans le processus de peinture. Cela peut inclure le mélange et le broyage des matières premières pour obtenir la bonne taille de particule et la composition chimique appropriée. Une fois préparée, la poudre est souvent soumise à des processus de tamisage et de classification pour garantir une granulométrie uniforme et des propriétés de dispersion optimales.
Ensuite, pendant le processus de pulvérisation de la peinture en poudre, le traitement des particules implique la gestion des particules excédentaires qui ne s’adhèrent pas à la surface de la pièce à revêtir. Des systèmes de dépoussiérage et de récupération sont utilisés pour collecter ces particules excédentaires, réduisant ainsi les déchets et assurant une utilisation efficace des matériaux.
Enfin, le traitement des particules comprend également la récupération et le recyclage des particules pour un usage ultérieur. Les particules de poudre excédentaires collectées peuvent être recyclées dans le processus de peinture, réduisant ainsi les coûts de production et les déchets environnementaux. Des systèmes de récupération de poudre sont utilisés pour séparer les particules recyclables des déchets et des contaminants, assurant ainsi une qualité constante du revêtement final.
En résumé, le traitement des particules est un aspect crucial du processus de peinture en poudre, garantissant la qualité et l’efficacité de la production. En optimisant la préparation des matériaux en poudre, en gérant efficacement les particules excédentaires et en recyclant les matériaux, les fabricants peuvent améliorer leur efficacité opérationnelle tout en réduisant leur empreinte environnementale.
Mini Cabine de Revêtement en Poudre pour Jantes en Alliage
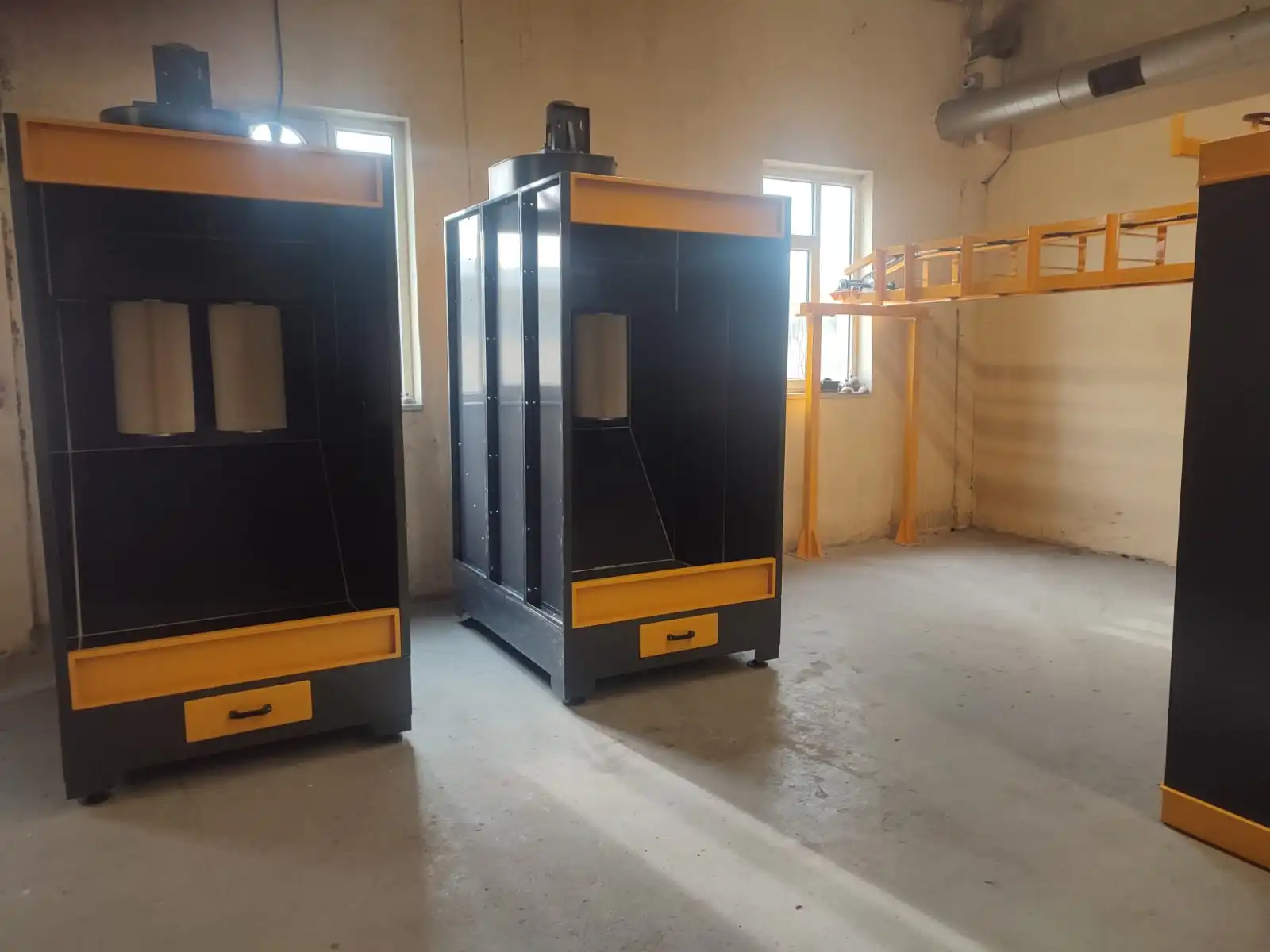
Une mini cabine de revêtement en poudre pour jantes en alliage est un type de cabine de pulvérisation conçue pour le revêtement de petites pièces, telles que des jantes en alliage. Ces cabines sont généralement plus petites et moins chères que les cabines de pulvérisation de taille normale, ce qui les rend idéales pour les petites entreprises ou les particuliers qui souhaitent appliquer des revêtements en poudre sur leurs propres jantes.
Les mini cabines de revêtement en poudre pour jantes en alliage sont généralement constituées des composants suivants :
- Un corps de cabine : Le corps de la cabine est généralement constitué d’acier ou d’aluminium. Il est conçu pour contenir la peinture poudre et les particules de poussière.
- Un système d’extraction : Le système d’extraction est utilisé pour éliminer la peinture poudre non utilisée de la cabine. Il est généralement constitué d’un ventilateur et d’un filtre.
- Un système de distribution de peinture : Le système de distribution de peinture est utilisé pour appliquer la peinture poudre sur les jantes. Il est généralement constitué d’un pistolet de pulvérisation électrostatique.
Le processus de revêtement en poudre des jantes en alliage dans une mini cabine se déroule comme suit :
- Les jantes sont nettoyées et préparées pour le revêtement.
- Les jantes sont placées dans la cabine.
- Le système d’extraction est activé pour éliminer la peinture poudre non utilisée.
- Le pistolet de pulvérisation est utilisé pour appliquer la peinture poudre sur les jantes.
- Les jantes sont séchées dans un four à air chaud.
Les mini cabines de revêtement en poudre pour jantes en alliage offrent un certain nombre d’avantages, notamment :
- Elles sont plus petites et moins chères que les cabines de pulvérisation de taille normale.
- Elles sont faciles à utiliser et à entretenir.
- Elles sont idéales pour le revêtement de petites pièces, telles que des jantes en alliage.
Cependant, ces cabines peuvent également présenter certains inconvénients, notamment :
- Elles peuvent être moins efficaces que les cabines de pulvérisation de taille normale pour les grandes pièces.
- Elles peuvent ne pas être capables de supporter les mêmes niveaux de pression que les cabines de pulvérisation de taille normale.
Les mini cabines de revêtement en poudre pour jantes en alliage sont un choix populaire pour les petites entreprises ou les particuliers qui souhaitent appliquer des revêtements en poudre sur leurs propres jantes. Elles sont un moyen efficace et abordable de redonner vie à vos jantes en alliage.
Voici quelques conseils pour choisir une mini cabine de revêtement en poudre pour jantes en alliage :
- Considérez la taille de vos jantes. Si vous avez de grandes jantes, vous aurez besoin d’une cabine plus grande.
- Pensez à la fréquence à laquelle vous utiliserez la cabine. Si vous prévoyez de l’utiliser fréquemment, vous aurez besoin d’une cabine plus durable.
- Comparez les prix des différentes cabines. Les prix des mini cabines de revêtement en poudre pour jantes en alliage peuvent varier considérablement.
En suivant ces conseils, vous pourrez choisir la mini cabine de revêtement en poudre pour jantes en alliage qui répond le mieux à vos besoins.
Mini four de Revêtement en Poudre pour Jantes en Alliage
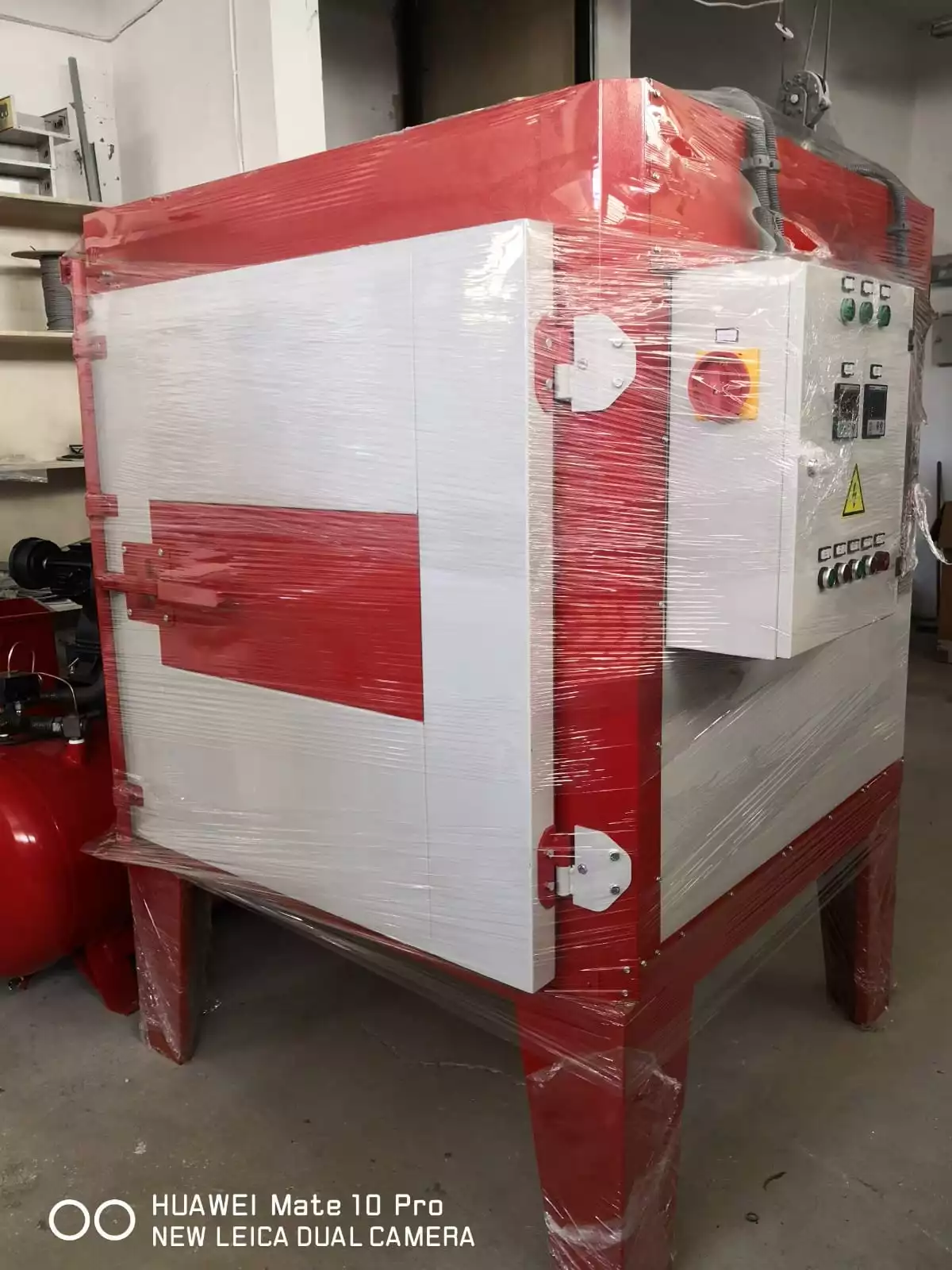
Un mini four de revêtement en poudre pour jantes en alliage est un type de four utilisé pour sécher et durcir les revêtements en poudre appliqués sur les jantes en alliage. Ces fours sont généralement plus petits et moins chers que les fours de revêtement en poudre de taille normale, ce qui les rend idéaux pour les petites entreprises ou les particuliers qui souhaitent appliquer des revêtements en poudre sur leurs propres jantes.
Les mini fours de revêtement en poudre pour jantes en alliage sont généralement constitués des composants suivants :
- Un corps de four : Le corps de four est généralement constitué d’acier ou d’aluminium. Il est conçu pour contenir les jantes et la peinture poudre.
- Un système de chauffage : Le système de chauffage est utilisé pour chauffer le four à la température requise pour le séchage et le durcissement des revêtements en poudre.
- Un système de ventilation : Le système de ventilation est utilisé pour éliminer les fumées et les odeurs du four.
Le processus de séchage et de durcissement des revêtements en poudre dans un mini four se déroule comme suit :
- Les jantes sont placées dans le four.
- Le four est chauffé à la température requise.
- Les jantes sont séchées et durcies pendant un temps spécifié.
Les mini fours de revêtement en poudre pour jantes en alliage offrent un certain nombre d’avantages, notamment :
- Ils sont plus petits et moins chers que les fours de revêtement en poudre de taille normale.
- Ils sont faciles à utiliser et à entretenir.
- Ils sont idéaux pour le revêtement de petites pièces, telles que des jantes en alliage.
Cependant, ces fours peuvent également présenter certains inconvénients, notamment :
- Ils peuvent être moins efficaces que les fours de revêtement en poudre de taille normale pour les grandes pièces.
- Ils peuvent ne pas être capables de supporter les mêmes niveaux de température que les fours de revêtement en poudre de taille normale.
Les mini fours de revêtement en poudre pour jantes en alliage sont un choix populaire pour les petites entreprises ou les particuliers qui souhaitent appliquer des revêtements en poudre sur leurs propres jantes. Ils sont un moyen efficace et abordable de redonner vie à vos jantes en alliage.
Voici quelques conseils pour choisir un mini four de revêtement en poudre pour jantes en alliage :
- Considérez la taille de vos jantes. Si vous avez de grandes jantes, vous aurez besoin d’un four plus grand.
- Pensez à la fréquence à laquelle vous utiliserez le four. Si vous prévoyez de l’utiliser fréquemment, vous aurez besoin d’un four plus durable.
- Comparez les prix des différents fours. Les prix des mini fours de revêtement en poudre pour jantes en alliage peuvent varier considérablement.
En suivant ces conseils, vous pourrez choisir le mini four de revêtement en poudre pour jantes en alliage qui répond le mieux à vos besoins.
Voici quelques-unes des caractéristiques à prendre en compte lors du choix d’un mini four de revêtement en poudre pour jantes en alliage :
- La taille du four : La taille du four doit être suffisante pour contenir les jantes que vous souhaitez recouvrir.
- La température maximale : La température maximale du four doit être suffisante pour sécher et durcir les revêtements en poudre que vous utilisez.
- Le temps de cycle : Le temps de cycle du four est le temps nécessaire pour sécher et durcir les revêtements en poudre.
- Les fonctionnalités : Certains fours de revêtement en poudre sont dotés de fonctionnalités supplémentaires, telles que des commandes numériques ou des systèmes de ventilation améliorés.
En fonction de vos besoins et de votre budget, vous pouvez choisir le mini four de revêtement en poudre pour jantes en alliage qui vous convient le mieux.tunesharemore_vert
Installations Automatiques de Peinture en Poudre
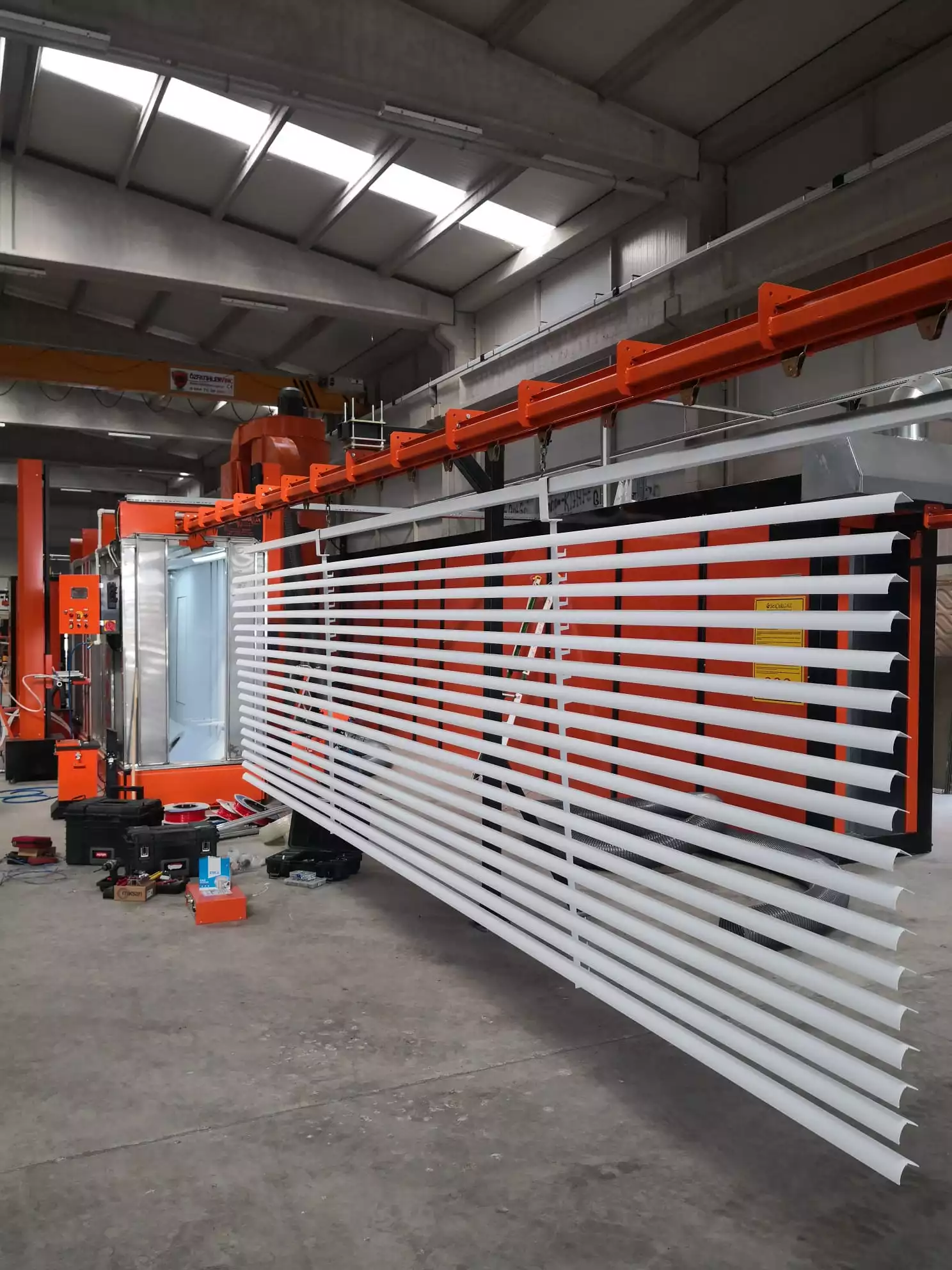
Les installations automatiques de peinture en poudre sont des systèmes qui permettent d’appliquer des revêtements en poudre sur des pièces de manière automatisée. Ces installations sont utilisées dans une variété d’industries, notamment l’automobile, l’aéronautique, l’électronique et la fabrication.
Les installations automatiques de peinture en poudre sont généralement constituées des composants suivants :
- Une cabine de pulvérisation : La cabine de pulvérisation est utilisée pour appliquer la peinture poudre sur les pièces.
- Un four de séchage et de durcissement : Le four de séchage et de durcissement est utilisé pour sécher et durcir les revêtements en poudre appliqués sur les pièces.
- Un système de transport : Le système de transport est utilisé pour déplacer les pièces à travers l’installation.
Le processus de peinture en poudre automatisée se déroule comme suit :
- Les pièces sont préparées pour la peinture, ce qui peut inclure le nettoyage, le dégraissage et le sablage.
- Les pièces sont placées dans la cabine de pulvérisation.
- La peinture poudre est appliquée sur les pièces à l’aide d’un pistolet de pulvérisation électrostatique.
- Les pièces sont séchées et durcies dans le four.
Les installations automatiques de peinture en poudre offrent un certain nombre d’avantages par rapport aux méthodes manuelles de peinture en poudre, notamment :
- Une productivité élevée : Les installations automatiques peuvent appliquer la peinture poudre sur des pièces beaucoup plus rapidement que les méthodes manuelles.
- Une application uniforme : Les installations automatiques peuvent appliquer la peinture poudre de manière plus uniforme que les méthodes manuelles.
- Une qualité constante : Les installations automatiques peuvent produire des résultats de qualité constante, ce qui est important pour les applications industrielles.
Cependant, les installations automatiques de peinture en poudre peuvent également présenter certains inconvénients, notamment :
- Un coût initial élevé : Les installations automatiques sont coûteuses à acheter et à installer.
- Un besoin de maintenance : Les installations automatiques nécessitent une maintenance régulière pour garantir leur bon fonctionnement.
Les installations automatiques de peinture en poudre sont un choix populaire pour les entreprises qui ont besoin de produire des pièces peintes en poudre en grande quantité et avec une qualité constante.
Voici quelques-uns des types d’installations automatiques de peinture en poudre les plus courants :
- Les installations à convoyeur : Les installations à convoyeur sont les types d’installations automatiques de peinture en poudre les plus courantes. Elles utilisent un convoyeur pour déplacer les pièces à travers l’installation.
- Les installations à carrousel : Les installations à carrousel sont similaires aux installations à convoyeur, mais elles utilisent un carrousel pour déplacer les pièces.
- Les installations à poste fixe : Les installations à poste fixe sont conçues pour des pièces de forme ou de taille spécifiques. Elles utilisent des robots ou des bras manipulateurs pour appliquer la peinture poudre sur les pièces.
Le type d’installation automatique de peinture en poudre le plus adapté à une application donnée dépend d’un certain nombre de facteurs, notamment le type de pièces à peindre, la quantité de pièces à peindre et le budget.
Cabines de Revêtement en Poudre Automatiques
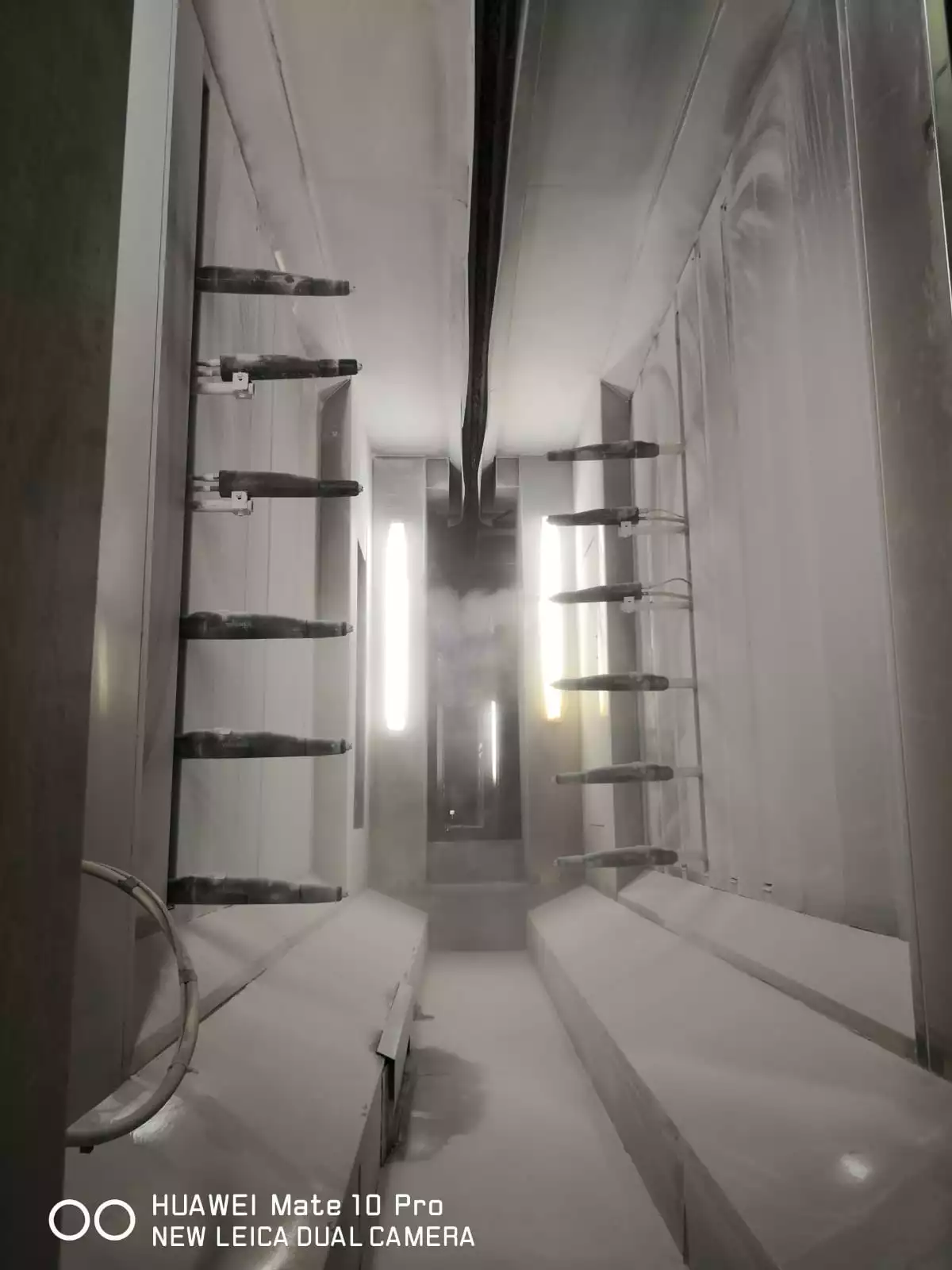
Une cabine de revêtement en poudre automatique est un type de cabine de pulvérisation conçue pour appliquer des revêtements en poudre sur des pièces de manière automatisée. Ces cabines sont utilisées dans une variété d’industries, notamment l’automobile, l’aéronautique, l’électronique et la fabrication.
Les cabines de revêtement en poudre automatiques sont généralement constituées des composants suivants :
- Un système de transport : Le système de transport est utilisé pour déplacer les pièces à travers la cabine.
- Un système d’application de poudre : Le système d’application de poudre est utilisé pour appliquer la peinture poudre sur les pièces.
- Un système de récupération de poudre : Le système de récupération de poudre est utilisé pour collecter la peinture poudre non utilisée.
Le processus de revêtement en poudre automatique dans une cabine se déroule comme suit :
- Les pièces sont préparées pour la peinture, ce qui peut inclure le nettoyage, le dégraissage et le sablage.
- Les pièces sont placées dans la cabine.
- Le système de transport déplace les pièces sous la buse de pulvérisation.
- La peinture poudre est appliquée sur les pièces à l’aide d’un pistolet de pulvérisation électrostatique.
- La peinture poudre non utilisée est collectée par le système de récupération de poudre.
Les cabines de revêtement en poudre automatiques offrent un certain nombre d’avantages par rapport aux cabines de pulvérisation manuelles, notamment :
- Une productivité élevée : Les cabines automatiques peuvent appliquer la peinture poudre sur des pièces beaucoup plus rapidement que les méthodes manuelles.
- Une application uniforme : Les cabines automatiques peuvent appliquer la peinture poudre de manière plus uniforme que les méthodes manuelles.
- Une qualité constante : Les cabines automatiques peuvent produire des résultats de qualité constante, ce qui est important pour les applications industrielles.
Cependant, les cabines de revêtement en poudre automatiques peuvent également présenter certains inconvénients, notamment :
- Un coût initial élevé : Les cabines automatiques sont coûteuses à acheter et à installer.
- Un besoin de maintenance : Les cabines automatiques nécessitent une maintenance régulière pour garantir leur bon fonctionnement.
Les cabines de revêtement en poudre automatiques sont un choix populaire pour les entreprises qui ont besoin de produire des pièces peintes en poudre en grande quantité et avec une qualité constante.
Voici quelques-uns des types de cabines de revêtement en poudre automatiques les plus courants :
- Les cabines à convoyeur : Les cabines à convoyeur sont les types de cabines de revêtement en poudre automatiques les plus courantes. Elles utilisent un convoyeur pour déplacer les pièces à travers la cabine.
- Les cabines à carrousel : Les cabines à carrousel sont similaires aux cabines à convoyeur, mais elles utilisent un carrousel pour déplacer les pièces.
- Les cabines à poste fixe : Les cabines à poste fixe sont conçues pour des pièces de forme ou de taille spécifiques. Elles utilisent des robots ou des bras manipulateurs pour appliquer la peinture poudre sur les pièces.
Le type de cabine de revêtement en poudre automatique le plus adapté à une application donnée dépend d’un certain nombre de facteurs, notamment le type de pièces à peindre, la quantité de pièces à peindre et le budget.
Caractéristiques des cabines de revêtement en poudre automatiques
Les cabines de revêtement en poudre automatiques sont généralement conçues pour répondre aux exigences suivantes :
- Une productivité élevée : Les cabines automatiques doivent être capables d’appliquer la peinture poudre sur des pièces rapidement et efficacement.
- Une application uniforme : Les cabines automatiques doivent être capables d’appliquer la peinture poudre de manière uniforme sur les pièces.
- Une qualité constante : Les cabines automatiques doivent être capables de produire des résultats de qualité constante.
Pour répondre à ces exigences, les cabines de revêtement en poudre automatiques sont généralement équipées des caractéristiques suivantes :
- Un système de transport efficace : Le système de transport doit être capable de déplacer les pièces à travers la cabine rapidement et sans interférence avec le processus d’application de la peinture.
- Un système d’application de poudre précis : Le système d’application de poudre doit être capable d’appliquer la peinture poudre de manière uniforme sur les pièces.
- Un système de récupération de poudre efficace : Le système de récupération de poudre doit être capable de collecter la peinture poudre non utilisée afin de réduire la pollution de l’environnement.
Maintenance des cabines de revêtement en poudre automatiques
Les cabines de revêtement en poudre automatiques nécessitent une maintenance régulière
Ligne de Revêtement en Poudre
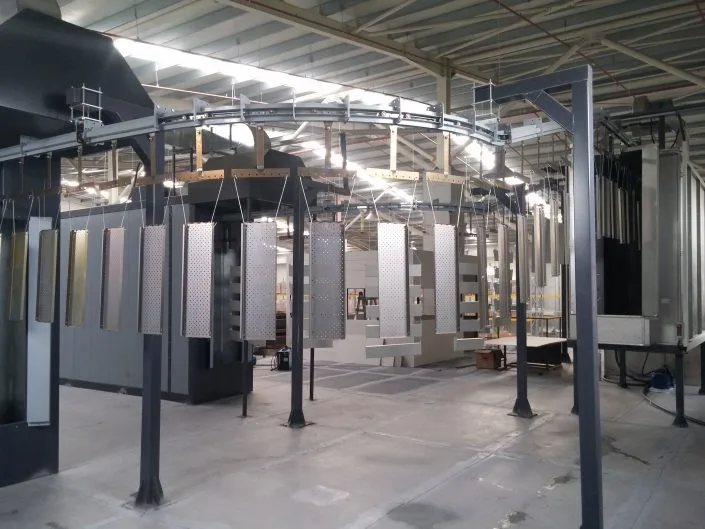
Une ligne de revêtement en poudre est un système qui permet d’appliquer des revêtements en poudre sur des pièces de manière automatisée. Une ligne de revêtement en poudre typique se compose des composants suivants :
- Une cabine de pulvérisation : La cabine de pulvérisation est utilisée pour appliquer la peinture poudre sur les pièces.
- Un four de séchage et de durcissement : Le four de séchage et de durcissement est utilisé pour sécher et durcir les revêtements en poudre appliqués sur les pièces.
- Un système de transport : Le système de transport est utilisé pour déplacer les pièces à travers la ligne.
Le processus de revêtement en poudre automatisé se déroule comme suit :
- Les pièces sont préparées pour la peinture, ce qui peut inclure le nettoyage, le dégraissage et le sablage.
- Les pièces sont placées dans la cabine de pulvérisation.
- La peinture poudre est appliquée sur les pièces à l’aide d’un pistolet de pulvérisation électrostatique.
- Les pièces sont séchées et durcies dans le four.
Les lignes de revêtement en poudre offrent un certain nombre d’avantages par rapport aux méthodes manuelles de peinture en poudre, notamment :
- Une productivité élevée : Les lignes de revêtement en poudre peuvent appliquer la peinture poudre sur des pièces beaucoup plus rapidement que les méthodes manuelles.
- Une application uniforme : Les lignes de revêtement en poudre peuvent appliquer la peinture poudre de manière plus uniforme que les méthodes manuelles.
- Une qualité constante : Les lignes de revêtement en poudre peuvent produire des résultats de qualité constante, ce qui est important pour les applications industrielles.
Cependant, les lignes de revêtement en poudre peuvent également présenter certains inconvénients, notamment :
- Un coût initial élevé : Les lignes de revêtement en poudre sont coûteuses à acheter et à installer.
- Un besoin de maintenance : Les lignes de revêtement en poudre nécessitent une maintenance régulière pour garantir leur bon fonctionnement.
Les lignes de revêtement en poudre sont un choix populaire pour les entreprises qui ont besoin de produire des pièces peintes en poudre en grande quantité et avec une qualité constante.
Types de lignes de revêtement en poudre
Il existe deux principaux types de lignes de revêtement en poudre : les lignes à convoyeur et les lignes à carrousel.
- Les lignes à convoyeur sont les types de lignes de revêtement en poudre les plus courantes. Elles utilisent un convoyeur pour déplacer les pièces à travers la ligne.
- Les lignes à carrousel sont similaires aux lignes à convoyeur, mais elles utilisent un carrousel pour déplacer les pièces.
Les lignes de revêtement en poudre peuvent également être classées en fonction de leur capacité. Les lignes de petite capacité sont conçues pour traiter des pièces de petite taille ou des quantités de pièces relativement faibles. Les lignes de grande capacité sont conçues pour traiter des pièces de grande taille ou des quantités de pièces importantes.
Choix d’une ligne de revêtement en poudre
Le choix d’une ligne de revêtement en poudre dépend d’un certain nombre de facteurs, notamment le type de pièces à peindre, la quantité de pièces à peindre et le budget.
Les entreprises qui ont besoin de produire des pièces peintes en poudre de grande taille ou en grande quantité doivent choisir une ligne de grande capacité. Les entreprises qui ont besoin de produire des pièces peintes en poudre de petite taille ou en quantité relativement faible peuvent choisir une ligne de petite capacité.
Les entreprises doivent également tenir compte du budget lors du choix d’une ligne de revêtement en poudre. Les lignes de revêtement en poudre sont coûteuses à acheter et à installer.
Maintenance des lignes de revêtement en poudre
Les lignes de revêtement en poudre nécessitent une maintenance régulière pour garantir leur bon fonctionnement. La maintenance des lignes de revêtement en poudre comprend les tâches suivantes :
- Le nettoyage des composants de la ligne
- La vérification des pièces mobiles
- Le remplacement des pièces usées
Les entreprises doivent établir un programme de maintenance régulier pour leurs lignes de revêtement en poudre afin de garantir leur bon fonctionnement.
Cabines de lavage manuel et tunnels de lavage automatique
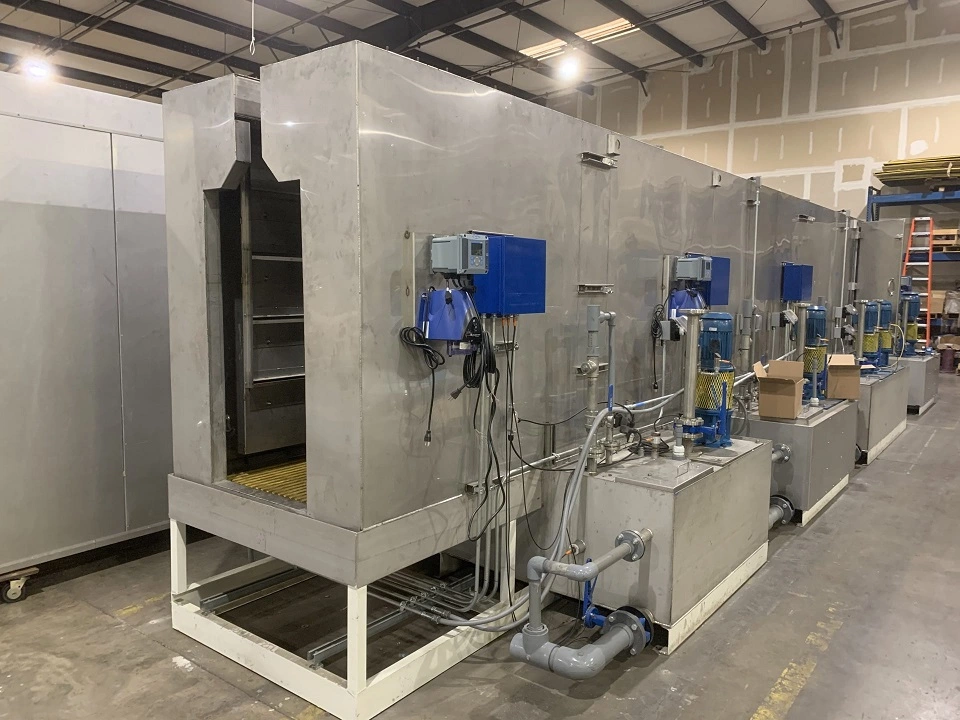
Les cabines de lavage manuel et les tunnels de lavage automatique sont deux types d’équipements utilisés pour nettoyer les pièces industrielles. Ils utilisent tous deux un mélange d’eau, de détergent et de produits chimiques pour enlever la saleté, la graisse et les contaminants des pièces.
Cabines de lavage manuel
Les cabines de lavage manuel sont des équipements simples qui sont généralement utilisés pour nettoyer des pièces de petite taille ou des quantités de pièces relativement faibles. Elles sont généralement constituées des composants suivants :
- Un bassin de lavage : Le bassin de lavage est le principal composant de la cabine de lavage. Il contient le mélange d’eau, de détergent et de produits chimiques.
- Une pompe : La pompe est utilisée pour faire circuler le mélange de nettoyage dans le bassin de lavage.
- Un pistolet de pulvérisation : Le pistolet de pulvérisation est utilisé pour appliquer le mélange de nettoyage sur les pièces.
Le processus de nettoyage dans une cabine de lavage manuel se déroule comme suit :
- Les pièces sont placées dans le bassin de lavage.
- Le mélange de nettoyage est appliqué sur les pièces à l’aide du pistolet de pulvérisation.
- Les pièces sont frottées manuellement pour enlever la saleté, la graisse et les contaminants.
- Les pièces sont rincées à l’eau claire.
Les cabines de lavage manuel sont un choix populaire pour les petites entreprises ou les particuliers qui souhaitent nettoyer leurs propres pièces. Elles sont abordables et faciles à utiliser.
Tunnels de lavage automatique
Les tunnels de lavage automatique sont des équipements plus complexes qui sont généralement utilisés pour nettoyer des pièces de grande taille ou des quantités de pièces importantes. Ils sont généralement constitués des composants suivants :
- Un convoyeur : Le convoyeur est utilisé pour déplacer les pièces à travers le tunnel de lavage.
- Un système de pulvérisation : Le système de pulvérisation est utilisé pour appliquer le mélange de nettoyage sur les pièces.
- Un système de rinçage : Le système de rinçage est utilisé pour rincer les pièces à l’eau claire.
Le processus de nettoyage dans un tunnel de lavage automatique se déroule comme suit :
- Les pièces sont placées sur le convoyeur.
- Le mélange de nettoyage est appliqué sur les pièces à l’aide du système de pulvérisation.
- Les pièces sont frottées automatiquement pour enlever la saleté, la graisse et les contaminants.
- Les pièces sont rincées à l’eau claire.
Les tunnels de lavage automatique offrent un certain nombre d’avantages par rapport aux cabines de lavage manuel, notamment :
- Une productivité élevée : Les tunnels de lavage automatique peuvent nettoyer des pièces beaucoup plus rapidement que les cabines de lavage manuel.
- Une qualité constante : Les tunnels de lavage automatique peuvent produire des résultats de qualité constante.
Cependant, les tunnels de lavage automatique peuvent également présenter certains inconvénients, notamment :
- Un coût initial élevé : Les tunnels de lavage automatique sont plus coûteux à acheter et à installer que les cabines de lavage manuel.
- Un besoin de maintenance : Les tunnels de lavage automatique nécessitent une maintenance régulière pour garantir leur bon fonctionnement.
Les tunnels de lavage automatique sont un choix populaire pour les grandes entreprises qui ont besoin de nettoyer des pièces de grande taille ou des quantités de pièces importantes.
Choix d’une cabine de lavage ou d’un tunnel de lavage
Le choix d’une cabine de lavage ou d’un tunnel de lavage dépend d’un certain nombre de facteurs, notamment le type de pièces à nettoyer, la quantité de pièces à nettoyer et le budget.
Les entreprises qui ont besoin de nettoyer des pièces de grande taille ou des quantités de pièces importantes doivent choisir un tunnel de lavage. Les entreprises qui ont besoin de nettoyer des pièces de petite taille ou des quantités de pièces relativement faibles peuvent choisir une cabine de lavage manuel.
Les entreprises doivent également tenir compte du budget lors du choix d’une cabine de lavage ou d’un tunnel de lavage. Les tunnels de lavage sont plus coûteux à acheter et à installer que les cabines de lavage manuel.
Pièces de rechange Gema
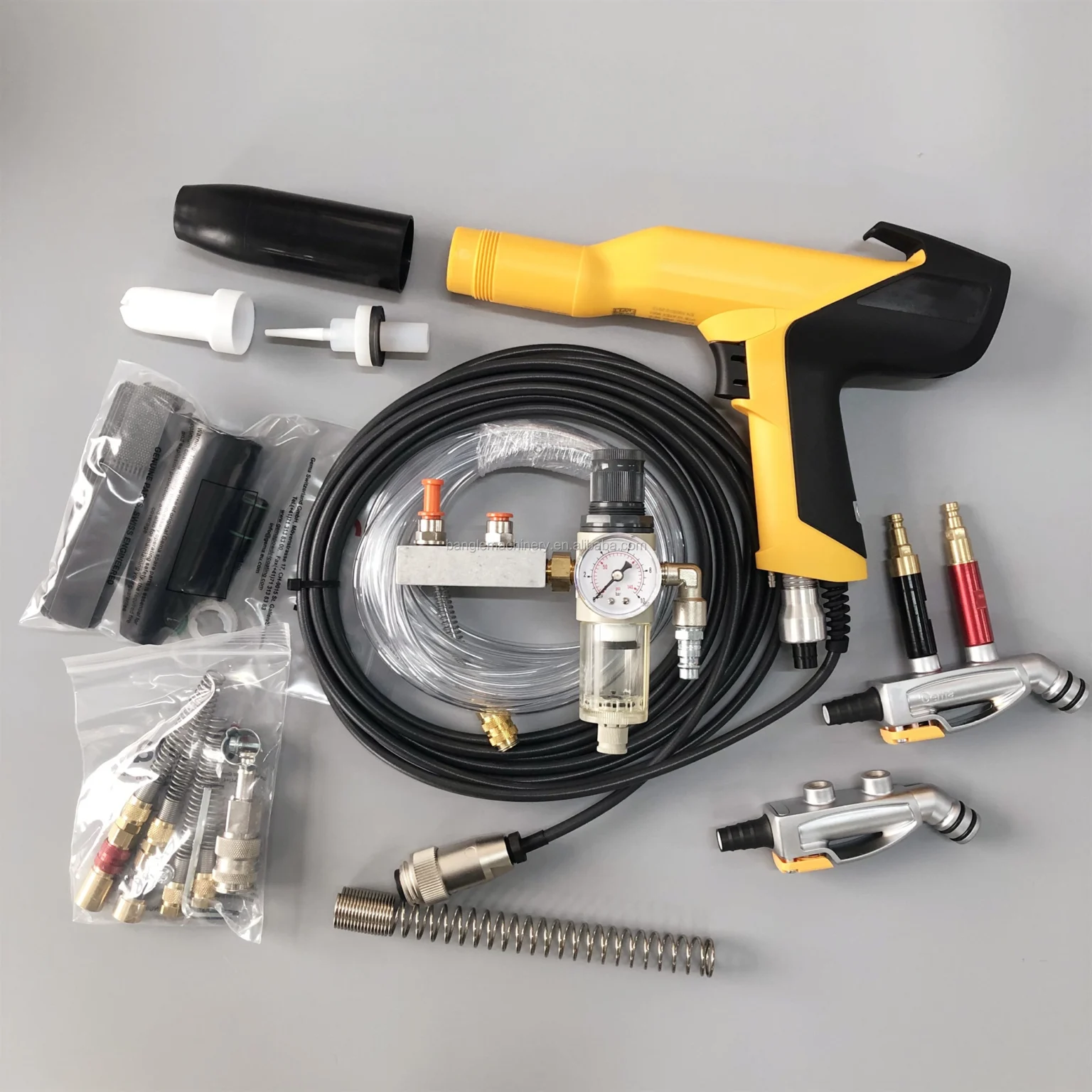
Gema est un fabricant suisse d’équipements de revêtement en poudre. La société propose une large gamme de pièces de rechange pour ses équipements, notamment :
- Pièces mécaniques : Les pièces mécaniques comprennent les pièces mobiles des équipements Gema, telles que les moteurs, les engrenages, les pompes et les vannes.
- Pièces électriques : Les pièces électriques comprennent les composants électriques des équipements Gema, tels que les moteurs électriques, les contrôleurs électroniques et les capteurs.
- Pièces de pulvérisation : Les pièces de pulvérisation comprennent les composants utilisés pour appliquer la peinture poudre sur les pièces, tels que les pistolets de pulvérisation, les buses de pulvérisation et les filtres.
- Pièces de nettoyage : Les pièces de nettoyage comprennent les composants utilisés pour nettoyer les pièces avant le revêtement en poudre, tels que les jets de lavage, les filtres et les pompes.
- Pièces de séchage : Les pièces de séchage comprennent les composants utilisés pour sécher les pièces après le revêtement en poudre, tels que les résistances, les ventilateurs et les thermostats.
Les pièces de rechange Gema sont disponibles auprès de revendeurs agréés Gema. Les revendeurs Gema peuvent fournir des conseils sur le type de pièce de rechange dont vous avez besoin et sur la façon de la remplacer.
Voici quelques conseils pour choisir des pièces de rechange Gema :
- Assurez-vous que les pièces de rechange sont compatibles avec votre équipement Gema.
- Commandez les pièces de rechange auprès d’un revendeur agréé Gema.
- Suivez les instructions de remplacement fournies par le revendeur Gema.
En suivant ces conseils, vous pouvez vous assurer que vos équipements Gema sont correctement entretenus et qu’ils fonctionnent de manière optimale.
Pièces de rechange Wagner
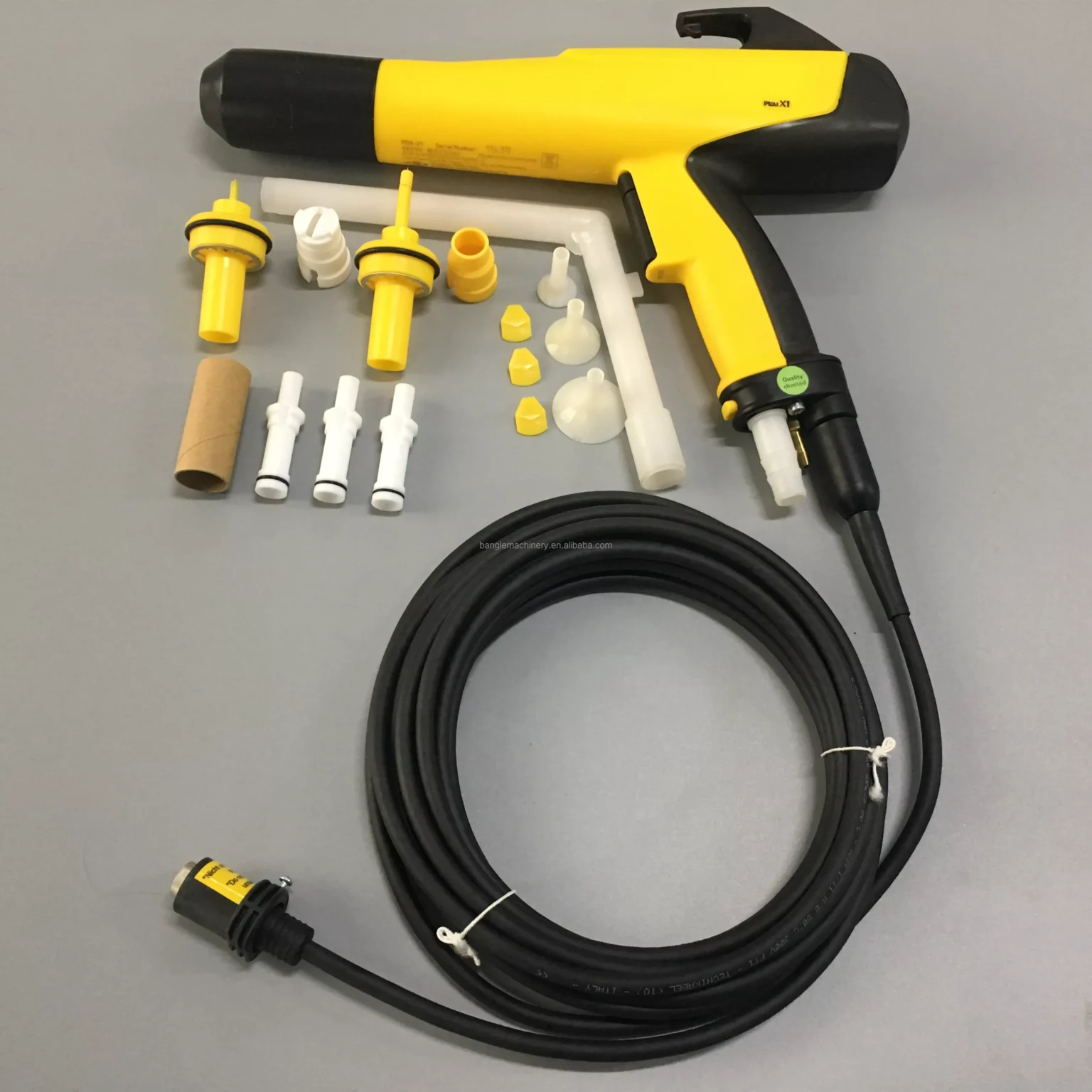
Wagner est un fabricant allemand d’équipements de pulvérisation, notamment de pistolets de pulvérisation, de pompes de pulvérisation et de cabines de pulvérisation. La société propose une large gamme de pièces de rechange pour ses équipements, notamment :
- Pièces mécaniques : Les pièces mécaniques comprennent les pièces mobiles des équipements Wagner, telles que les moteurs, les engrenages, les pompes et les vannes.
- Pièces électriques : Les pièces électriques comprennent les composants électriques des équipements Wagner, tels que les moteurs électriques, les contrôleurs électroniques et les capteurs.
- Pièces de pulvérisation : Les pièces de pulvérisation comprennent les composants utilisés pour appliquer le revêtement sur les surfaces, tels que les buses de pulvérisation, les filtres et les vannes de régulation.
Les pièces de rechange Wagner sont disponibles auprès de revendeurs agréés Wagner. Les revendeurs Wagner peuvent fournir des conseils sur le type de pièce de rechange dont vous avez besoin et sur la façon de la remplacer.
Voici quelques conseils pour choisir des pièces de rechange Wagner :
- Assurez-vous que les pièces de rechange sont compatibles avec votre équipement Wagner.
- Commandez les pièces de rechange auprès d’un revendeur agréé Wagner.
- Suivez les instructions de remplacement fournies par le revendeur Wagner.
En suivant ces conseils, vous pouvez vous assurer que vos équipements Wagner sont correctement entretenus et qu’ils fonctionnent de manière optimale.
Voici quelques exemples de pièces de rechange Wagner courantes :
- Buses de pulvérisation : Les buses de pulvérisation sont les pièces qui déterminent le motif de pulvérisation et la taille des gouttelettes. Elles sont disponibles dans une variété de tailles et de formes.
- Filtres : Les filtres sont utilisés pour empêcher les contaminants de pénétrer dans le système de pulvérisation. Ils doivent être remplacés régulièrement pour garantir une bonne performance de la pompe.
- Vannes de régulation : Les vannes de régulation sont utilisées pour contrôler le débit de peinture. Elles sont disponibles dans une variété de tailles et de pressions.
Les pièces de rechange Wagner sont généralement disponibles en stock auprès des revendeurs Wagner.
Pièces de rechange Nordson
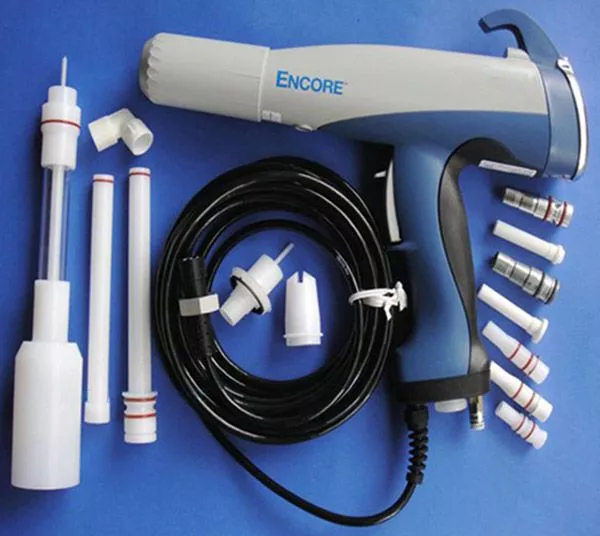
Nordson est un fabricant américain d’équipements de revêtement en poudre, notamment de pistolets de pulvérisation, de pompes de pulvérisation, de cabines de pulvérisation et de systèmes de contrôle. La société propose une large gamme de pièces de rechange pour ses équipements, notamment :
- Pièces mécaniques : Les pièces mécaniques comprennent les pièces mobiles des équipements Nordson, telles que les moteurs, les engrenages, les pompes et les vannes.
- Pièces électriques : Les pièces électriques comprennent les composants électriques des équipements Nordson, tels que les moteurs électriques, les contrôleurs électroniques et les capteurs.
- Pièces de pulvérisation : Les pièces de pulvérisation comprennent les composants utilisés pour appliquer la peinture poudre sur les pièces, tels que les pistolets de pulvérisation, les buses de pulvérisation et les filtres.
- Pièces de nettoyage : Les pièces de nettoyage comprennent les composants utilisés pour nettoyer les pièces avant le revêtement en poudre, tels que les jets de lavage, les filtres et les pompes.
- Pièces de séchage : Les pièces de séchage comprennent les composants utilisés pour sécher les pièces après le revêtement en poudre, tels que les résistances, les ventilateurs et les thermostats.
Les pièces de rechange Nordson sont disponibles auprès de revendeurs agréés Nordson. Les revendeurs Nordson peuvent fournir des conseils sur le type de pièce de rechange dont vous avez besoin et sur la façon de la remplacer.
Voici quelques conseils pour choisir des pièces de rechange Nordson :
- Assurez-vous que les pièces de rechange sont compatibles avec votre équipement Nordson.
- Commandez les pièces de rechange auprès d’un revendeur agréé Nordson.
- Suivez les instructions de remplacement fournies par le revendeur Nordson.
En suivant ces conseils, vous pouvez vous assurer que vos équipements Nordson sont correctement entretenus et qu’ils fonctionnent de manière optimale.
Voici quelques exemples de pièces de rechange Nordson courantes :
- Buses de pulvérisation : Les buses de pulvérisation sont les pièces qui déterminent le motif de pulvérisation et la taille des gouttelettes. Elles sont disponibles dans une variété de tailles et de formes.
- Filtres : Les filtres sont utilisés pour empêcher les contaminants de pénétrer dans le système de pulvérisation. Ils doivent être remplacés régulièrement pour garantir une bonne performance de la pompe.
- Vannes de régulation : Les vannes de régulation sont utilisées pour contrôler le débit de peinture. Elles sont disponibles dans une variété de tailles et de pressions.
Les pièces de rechange Nordson sont généralement disponibles en stock auprès des revendeurs Nordson.
Voici quelques ressources supplémentaires pour vous aider à trouver des pièces de rechange Nordson :
- Le site Web de Nordson : Le site Web de Nordson propose une base de données de pièces de rechange et des instructions de remplacement.
- Le service clientèle de Nordson : Le service clientèle de Nordson peut vous aider à trouver les pièces de rechange dont vous avez besoin.
- Les revendeurs agréés Nordson : Les revendeurs agréés Nordson peuvent vous aider à trouver les pièces de rechange dont vous avez besoin et à les installer.
Non seulement nous fabriquons nos équipements de revêtement en poudre, mais nous les expédions également dans vos locaux avec soin dans le monde entier.
Nous ne sommes pas seulement les fabricants de vos équipements de revêtement en poudre, nous sommes également vos partenaires de livraison dans le monde entier.
Chez EMS Powder Coating Equipment, nous comprenons qu’il est tout aussi important de vous fournir votre équipement de revêtement en poudre rapidement et en toute sécurité que de le fabriquer selon les normes les plus élevées. C’est pourquoi nous proposons des services de livraison dans le monde entier à tous nos clients.
Nous travaillons avec un réseau de partenaires maritimes expérimentés et fiables pour garantir que votre équipement arrive à temps et en parfait état. Nous proposons également une variété d’options d’expédition adaptées à votre budget et à vos besoins.
Que vous ayez besoin d’expédier votre équipement à une adresse locale ou vers une destination internationale, nous pouvons vous aider. Nous travaillerons avec vous pour choisir la meilleure option d’expédition pour vos besoins et pour vous tenir informé de l’état de votre envoi à chaque étape du processus.
Ainsi, lorsque vous choisissez EMS pour votre équipement de revêtement en poudre, vous obtenez non seulement les meilleurs produits du marché, mais vous bénéficiez également de la meilleure expérience de livraison possible.
Contactez-nous dès aujourd’hui pour en savoir plus sur nos services de livraison dans le monde entier.
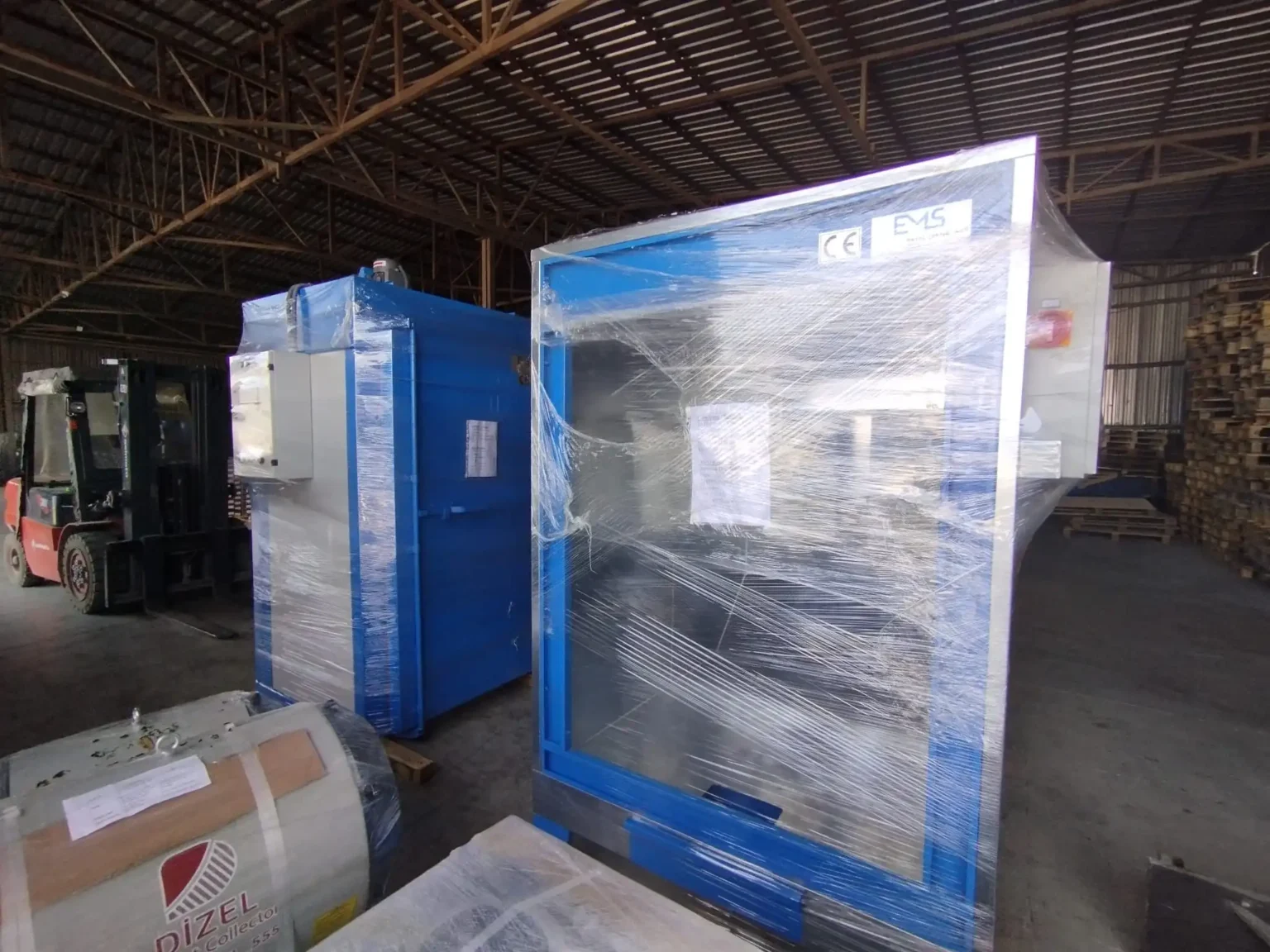

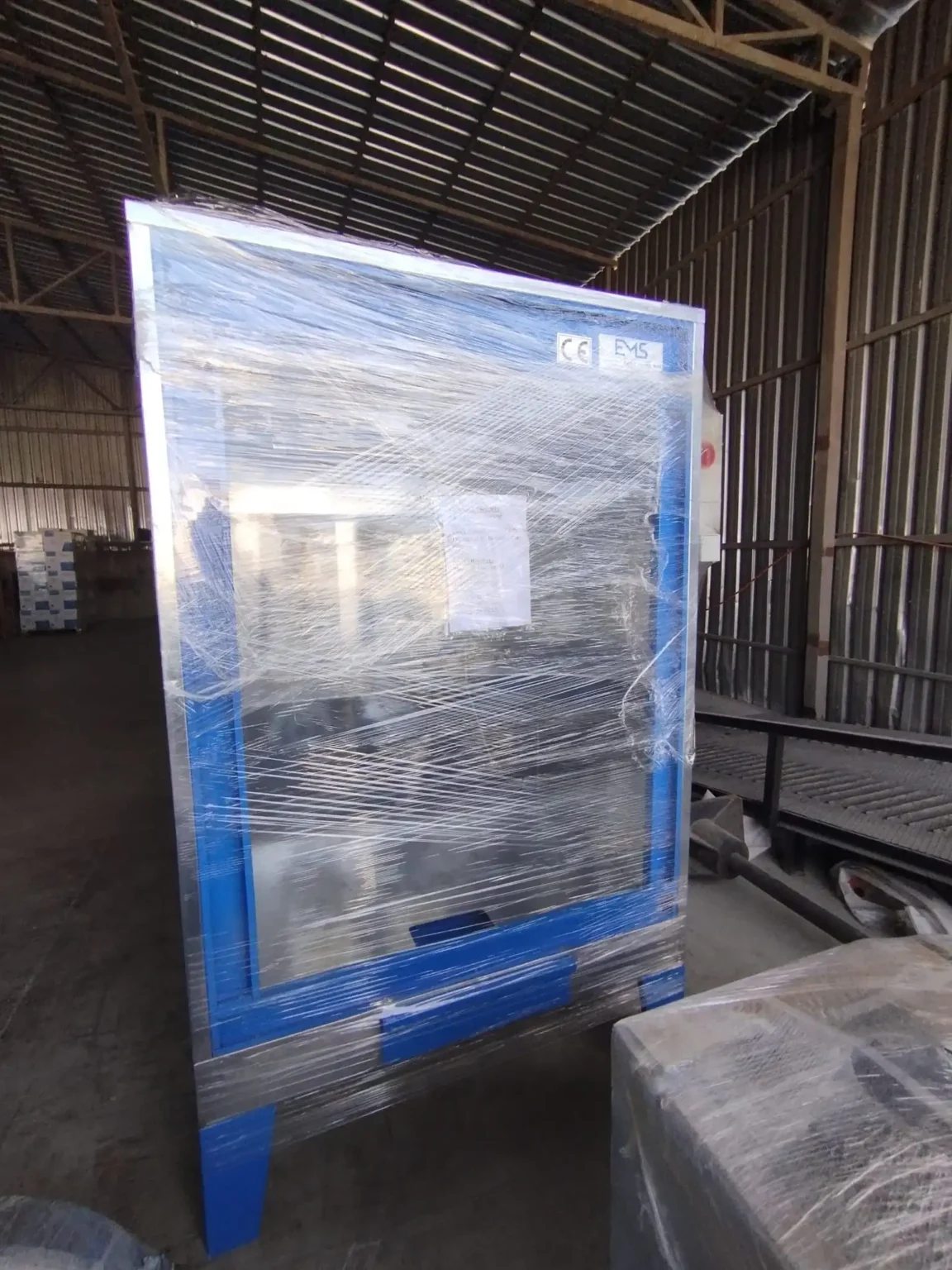
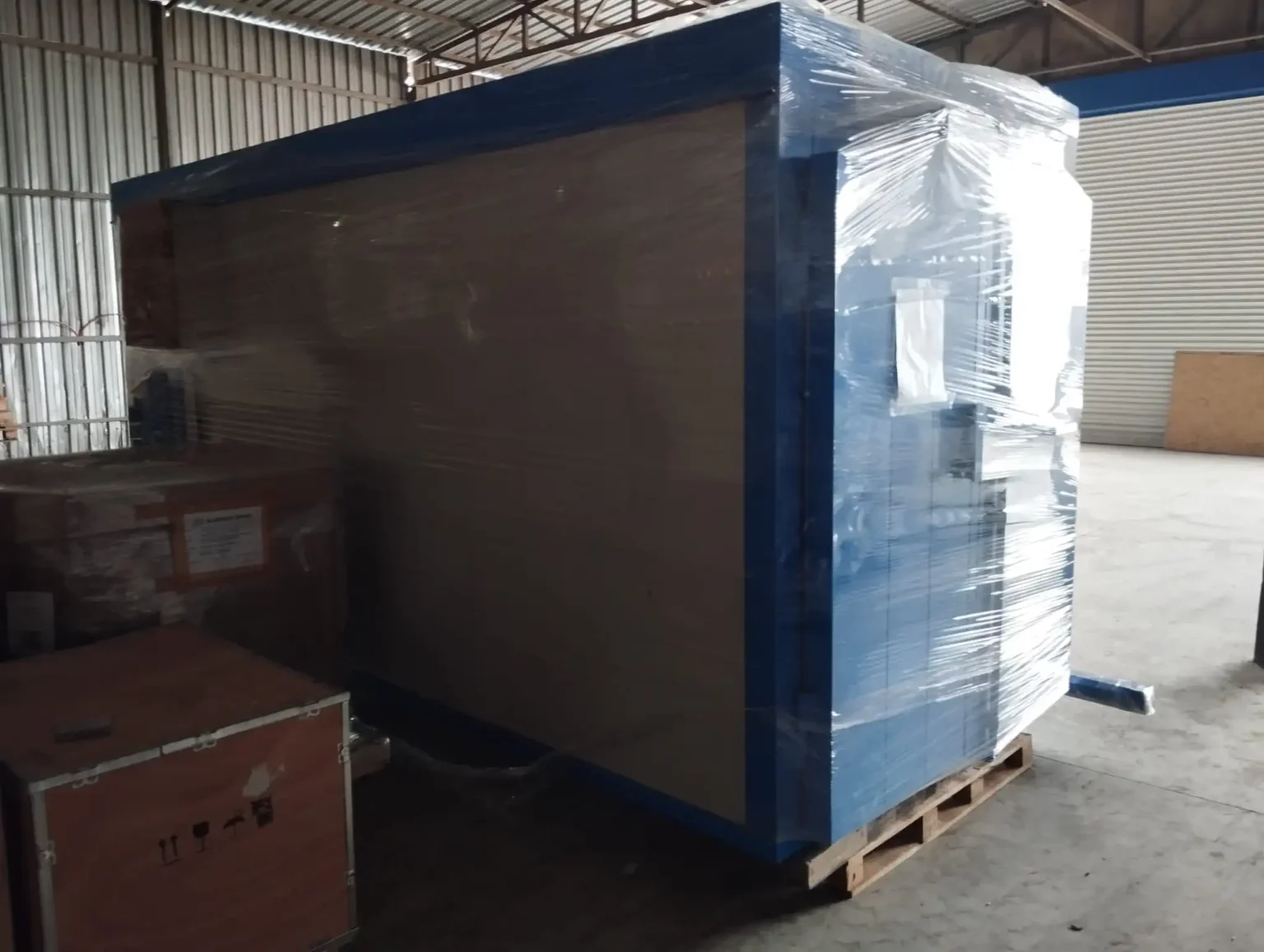
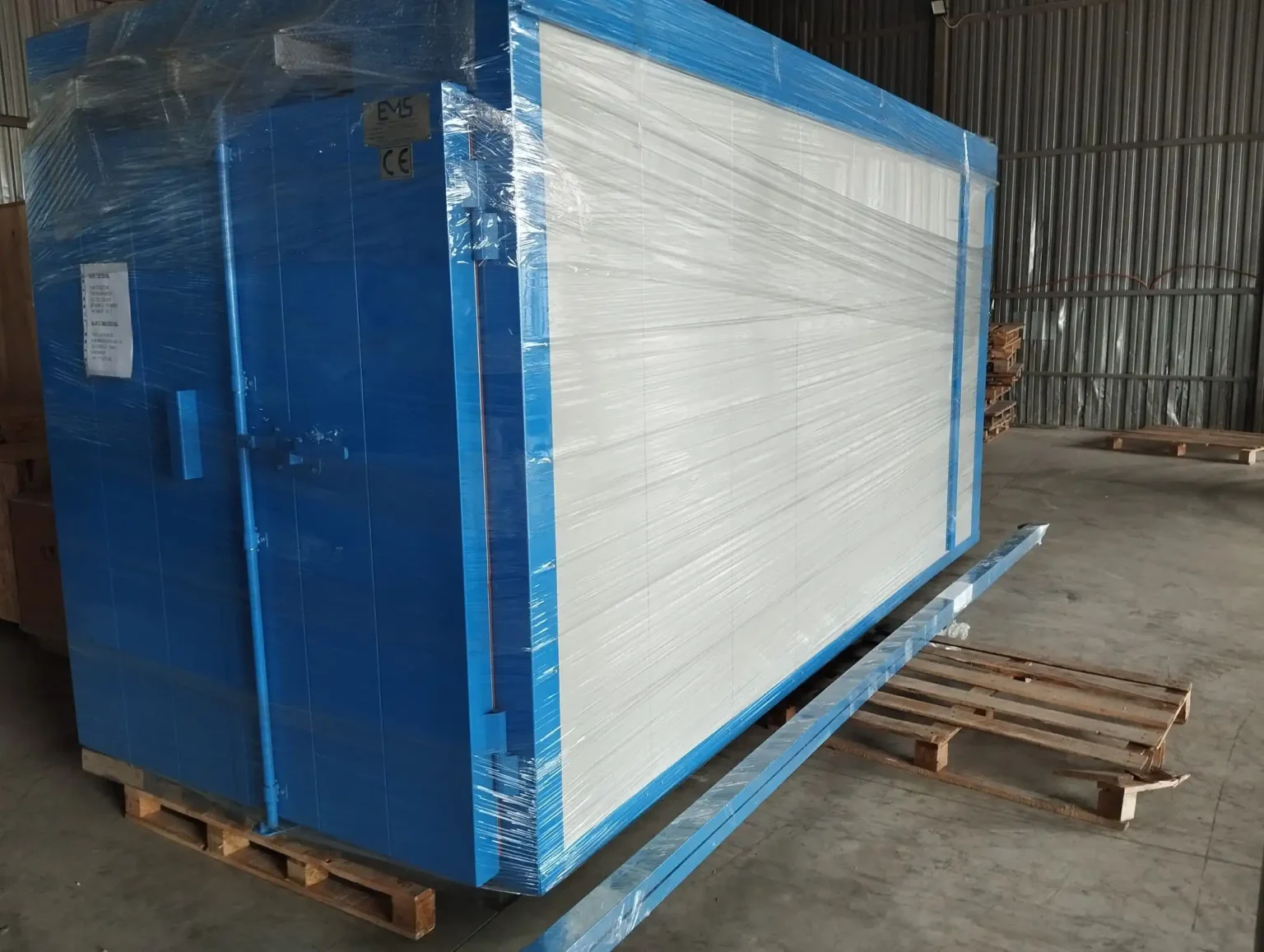
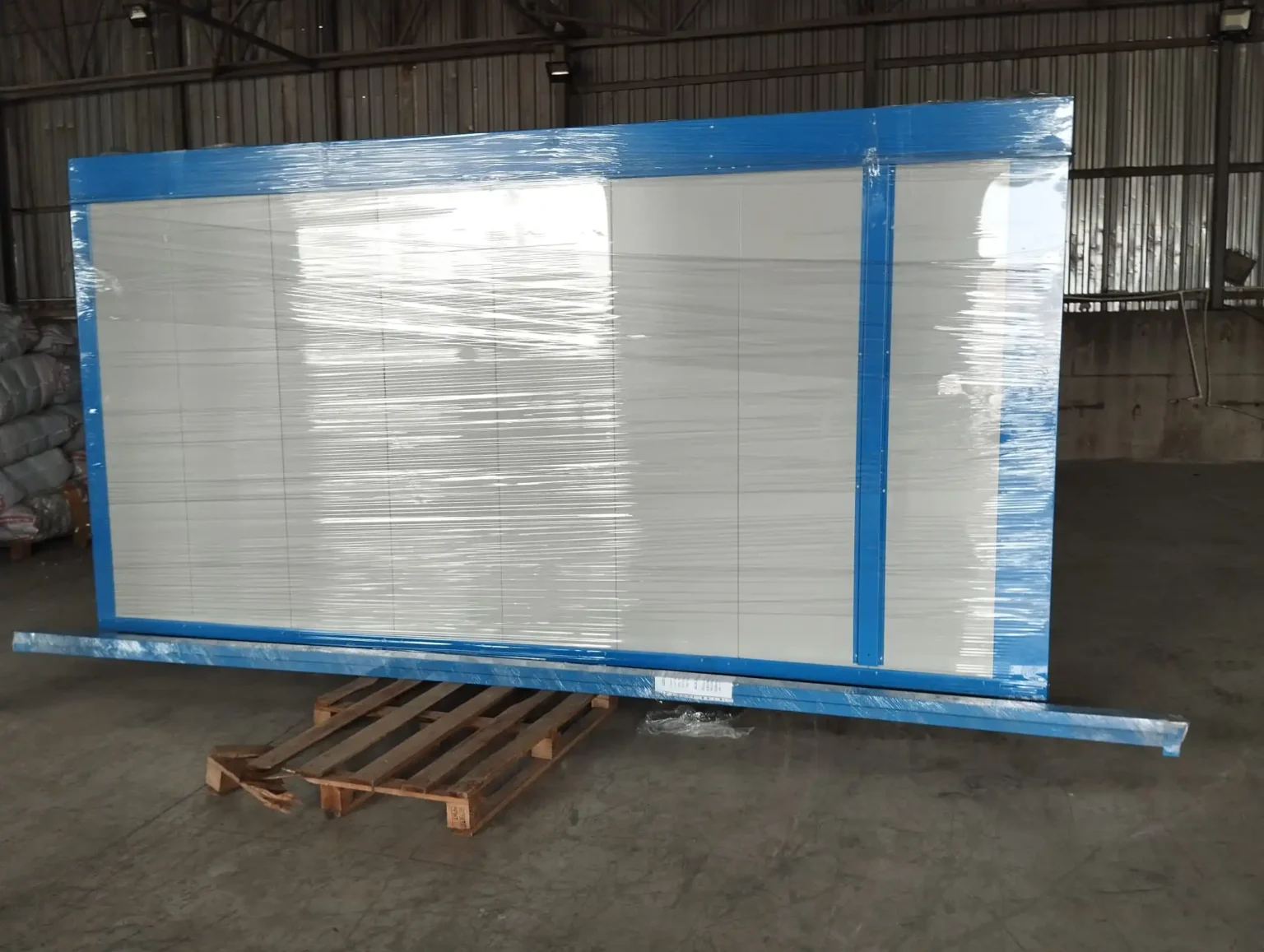
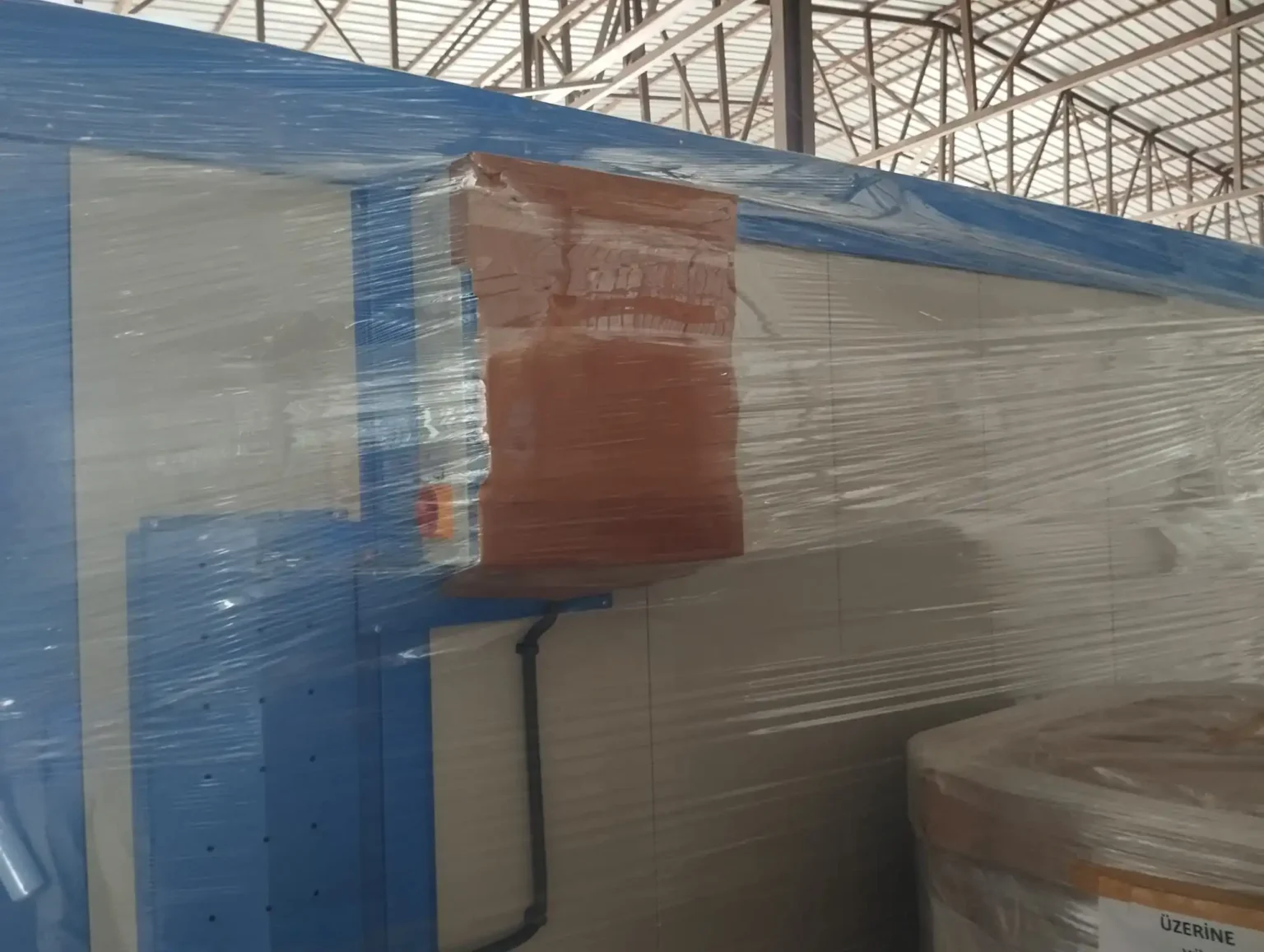
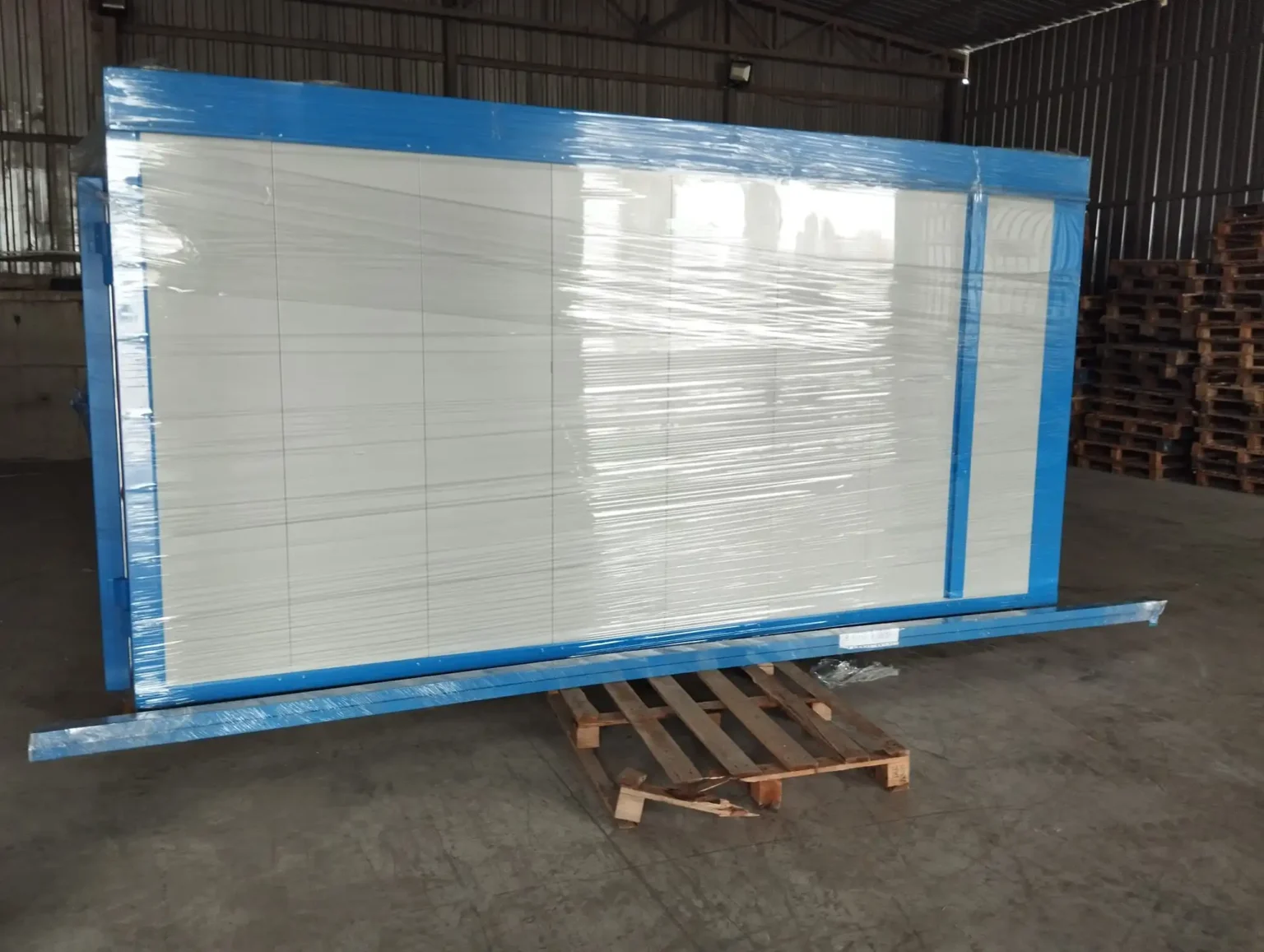
L’équipement de revêtement en poudre est utilisé pour appliquer une fine couche de poudre sur une surface métallique. Ce type de revêtement est appliqué par un procédé électrostatique et constitue une méthode très populaire pour la finition des pièces métalliques.
Ce type d’équipement peut être divisé en deux grandes catégories : automatiques et manuels. Les cabines automatiques sont plus populaires car elles offrent de meilleurs taux de production, mais elles sont également plus chères.
Une cabine à poudre est une enceinte dans laquelle se déroule le processus de revêtement en poudre. L’équipement de revêtement en poudre comprend un four dans lequel les pièces sont chauffées pour activer la poudre, un pistolet qui pulvérise ou brosse la poudre, une bande transporteuse qui déplace les pièces à travers le four et des pistolets de type cartouche pour appliquer des revêtements plus épais avec moins de pulvérisation.
Le revêtement en poudre est une technique utilisée pour donner une finition aux pièces métalliques. Cette technique est utilisée depuis de nombreuses années et reste aujourd’hui l’une des techniques les plus populaires.
L’équipement de revêtement en poudre comprend des cabines, des fours, des pistolets, des machines, des lignes et des convoyeurs. Une cabine peut être automatique ou manuelle. Une cabine automatique est plus chère qu’une cabine manuelle mais elle est aussi plus rapide et plus efficace
Le Revêtement en Poudre
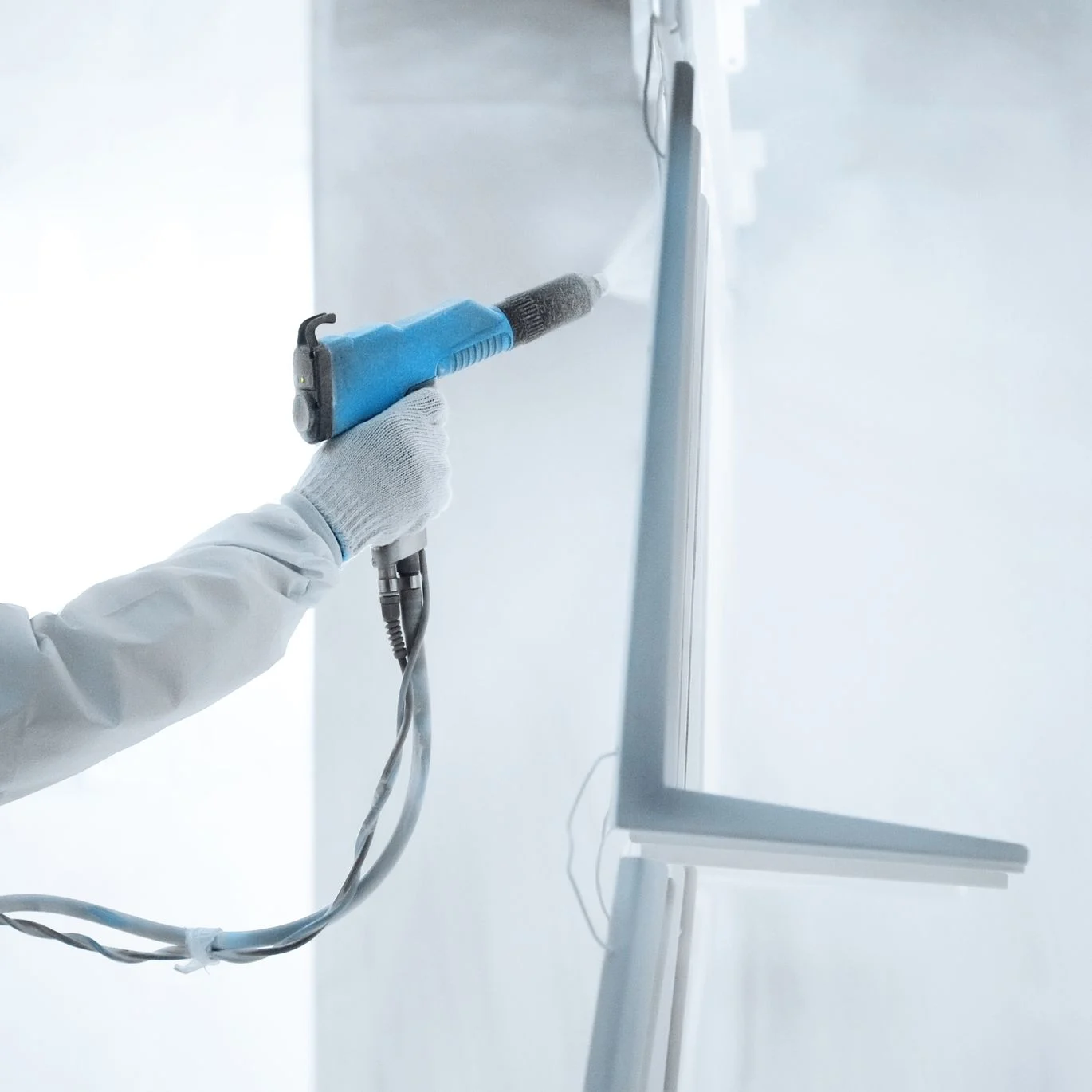
Le revêtement en poudre est une méthode de revêtement de surface de plus en plus populaire en raison de sa durabilité, de sa résistance à l’usure et de sa grande variété de couleurs et de finitions. Il existe quatre types de revêtements en poudre couramment utilisés : les époxydes, les polyesters thermodurcissables, les polyuréthanes et les acryliques.
Chacun de ces types de revêtements en poudre est utilisé pour des applications spécifiques, en fonction de leurs propriétés uniques et de leurs avantages. Dans ce billet, nous allons explorer les quatre types de revêtements en poudre et leurs domaines d’application respectifs. Que vous cherchiez à protéger les surfaces de votre équipement industriel ou à donner une nouvelle vie à vos meubles de jardin, vous trouverez ici tout ce que vous devez savoir sur les différents types de revêtements en poudre et leur utilisation.
- Introduction au revêtement en poudre
Le revêtement en poudre est une méthode de finition de surface largement utilisée dans de nombreux secteurs industriels. Il offre une alternative durable et esthétiquement attrayante aux revêtements liquides traditionnels tels que la peinture.
L’introduction au revêtement en poudre est essentielle pour comprendre les bases de cette technique de revêtement. Contrairement aux revêtements liquides, le revêtement en poudre est appliqué sous forme de poudre sèche, qui est ensuite fondue et adhère à la surface du matériau.
Il existe quatre principaux types de revêtement en poudre, chacun ayant ses propres caractéristiques et domaines d’application spécifiques :
- Revêtement en poudre époxy : Ce type de revêtement en poudre est connu pour sa durabilité et sa résistance aux produits chimiques. Il est couramment utilisé dans des applications telles que les appareils électroménagers, les équipements de jardinage, et les pièces automobiles.
- Revêtement en poudre polyester : Ce type de revêtement en poudre est apprécié pour sa résistance aux UV et sa capacité à conserver sa couleur et son éclat pendant une longue période. Il est souvent utilisé dans l’industrie du mobilier, les équipements extérieurs et les produits architecturaux.
- Revêtement en poudre polyuréthane : Ce type de revêtement en poudre offre une excellente résistance à l’abrasion et aux rayures, ce qui le rend idéal pour les surfaces soumises à un usage intensif. Il est couramment utilisé dans l’industrie automobile, les équipements sportifs et les revêtements de sol.
- Revêtement en poudre thermolaqué : Ce type de revêtement en poudre est spécialement formulé pour résister aux températures élevées, ce qui le rend adapté aux applications nécessitant une résistance à la chaleur, comme les composants électroniques, les pièces d’échappement et les équipements industriels.
En comprenant ces différents types de revêtement en poudre et leurs domaines d’application, vous serez en mesure de choisir le revêtement le mieux adapté à vos besoins spécifiques. Que ce soit pour améliorer l’aspect esthétique, la résistance aux éléments extérieurs ou la durabilité de vos produits, le revêtement en poudre offre une solution polyvalente et efficace.
- Qu’est-ce que le revêtement en poudre?
Le revêtement en poudre est une méthode de finition utilisée dans de nombreux secteurs industriels pour protéger et embellir les surfaces des produits. Il s’agit d’un processus qui consiste à appliquer une fine couche de poudre sur une surface préparée, puis à la chauffer pour la faire fondre et la fusionner, formant ainsi un revêtement solide et durable.
Cette méthode de revêtement présente de nombreux avantages par rapport aux autres techniques de finition. Tout d’abord, la poudre utilisée est exempte de solvants, ce qui la rend plus respectueuse de l’environnement et plus sûre à manipuler. De plus, le revêtement en poudre offre une meilleure résistance aux rayures, aux chocs, aux produits chimiques et aux UV par rapport aux revêtements liquides traditionnels.
Il existe quatre principaux types de revêtement en poudre, chacun ayant ses propres caractéristiques et domaines d’application spécifiques :
- Revêtement en poudre époxy : Ce type de revêtement en poudre offre une bonne adhérence, une excellente résistance à la corrosion et une grande flexibilité. Il est couramment utilisé dans l’industrie automobile, les équipements électriques et électroniques, ainsi que dans la construction.
- Revêtement en poudre polyester : Ce revêtement en poudre est connu pour sa résistance aux intempéries, aux UV et à la décoloration. Il est souvent utilisé pour les applications extérieures telles que les meubles de jardin, les clôtures et les équipements de jeu.
- Revêtement en poudre polyuréthane : Ce type de revêtement en poudre offre une excellente résistance chimique et mécanique. Il est largement utilisé dans les industries chimiques, pétrochimiques et pharmaceutiques, ainsi que pour les équipements de cuisine et les appareils électroménagers.
- Revêtement en poudre thermoplastique : Ce revêtement en poudre offre une excellente résistance chimique et thermique. Il est souvent utilisé pour les applications nécessitant une résistance élevée à la chaleur, telles que les tuyaux, les réservoirs de stockage et les pièces automobiles.
En comprenant les différents types de revêtement en poudre et leurs domaines d’application, vous pouvez choisir la meilleure option pour vos besoins spécifiques. Que ce soit pour protéger vos produits contre la corrosion, améliorer leur esthétique ou leur donner des propriétés spécifiques, le revêtement en poudre offre une solution polyvalente et fiable.
- Avantages du revêtement en poudre par rapport aux autres méthodes de revêtement
Le revêtement en poudre est devenu de plus en plus populaire en raison de ses nombreux avantages par rapport aux autres méthodes de revêtement. Si vous envisagez d’appliquer un revêtement sur vos produits ou matériaux, voici quelques avantages clés du revêtement en poudre à considérer :
- Durabilité : Le revêtement en poudre offre une excellente résistance aux rayures, aux chocs, à l’abrasion et aux produits chimiques. Il est plus durable que les revêtements liquides traditionnels, ce qui le rend idéal pour les applications nécessitant une protection à long terme.
- Écologique : Contrairement aux revêtements liquides qui contiennent souvent des solvants nocifs, le revêtement en poudre est sans solvant et respectueux de l’environnement. Il ne produit pas de déchets liquides dangereux et peut être recyclé, ce qui en fait un choix plus durable.
- Uniformité : Le revêtement en poudre offre une application uniforme et homogène, garantissant une épaisseur de revêtement constante sur toute la surface du matériau. Cela permet d’obtenir un aspect esthétique de haute qualité et une finition lisse.
- Large gamme de couleurs et de finitions : Le revêtement en poudre offre une large gamme de couleurs, de finitions et de textures. Que vous souhaitiez une finition mate, brillante, texturée ou métallisée, vous pouvez trouver le revêtement en poudre qui correspond à vos besoins esthétiques.
En résumé, le revêtement en poudre présente de nombreux avantages par rapport aux autres méthodes de revêtement, notamment sa durabilité, son caractère écologique, son application uniforme et sa variété de couleurs et de finitions. Si vous recherchez un revêtement de haute qualité pour vos produits, le revêtement en poudre est certainement une option à considérer.
- Revêtement en poudre époxy
Le revêtement en poudre époxy est l’un des types les plus populaires de revêtements en poudre utilisés dans une variété d’applications. Il est composé d’une résine époxy polymérisable et d’un durcisseur qui sont mélangés et appliqués sur la surface à revêtir sous forme de poudre fine.
Ce type de revêtement en poudre est apprécié pour sa durabilité et sa résistance à la corrosion, aux produits chimiques et aux intempéries. Il offre également une excellente adhérence et une finition lisse et uniforme.
Le revêtement en poudre époxy est largement utilisé dans l’industrie de l’automobile pour la peinture des pièces métalliques, telles que les jantes, les pare-chocs et les cadres de voiture. Il est également couramment utilisé dans l’industrie de la construction pour les portails, les clôtures et les structures métalliques extérieures.
Les meubles de jardin, les appareils électroménagers et les équipements sportifs sont d’autres exemples d’applications où le revêtement en poudre époxy est souvent utilisé en raison de sa résistance et de sa durabilité.
En résumé, le revêtement en poudre époxy est un choix populaire pour de nombreuses applications en raison de ses excellentes propriétés de protection et de finition.
- Caractéristiques et propriétés du revêtement en poudre époxy
Le revêtement en poudre époxy est l’un des types les plus couramment utilisés de revêtements en poudre. Il offre de nombreuses caractéristiques et propriétés qui en font un choix populaire dans de nombreux domaines d’application.
Tout d’abord, l’époxy est connu pour sa durabilité exceptionnelle. Il forme une couche solide et résistante qui protège la surface contre les rayures, la corrosion et les dommages causés par les produits chimiques. Cela en fait un choix idéal pour les applications industrielles, telles que les équipements lourds, les pièces automobiles et les structures métalliques.
De plus, le revêtement en poudre époxy offre une excellente adhérence. La poudre adhère efficacement à la surface, ce qui permet d’obtenir une finition uniforme et lisse. Cela en fait un choix populaire pour les applications architecturales, telles que les façades de bâtiments, les clôtures et les mobilier urbain.
Un autre avantage du revêtement en poudre époxy est sa résistance aux UV. Il ne se décolore pas et ne se détériore pas sous l’exposition prolongée au soleil, ce qui en fait un choix idéal pour les applications extérieures, telles que les panneaux de signalisation, les enseignes et les véhicules.
Enfin, l’époxy offre une large gamme de couleurs et de finitions. Des couleurs vives et éclatantes aux finitions texturées ou métalliques, il est possible de créer des designs attrayants et personnalisés avec le revêtement en poudre époxy.
En conclusion, le revêtement en poudre époxy présente de nombreuses caractéristiques et propriétés qui en font un choix polyvalent pour de nombreux domaines d’application. Sa durabilité, son adhérence, sa résistance aux UV et sa variété de couleurs en font un choix populaire dans les industries industrielles, architecturales et extérieures.
- Applications courantes du revêtement en poudre époxy
Le revêtement en poudre époxy est l’un des types les plus couramment utilisés dans l’industrie. Sa popularité est due à sa durabilité, sa résistance à la corrosion et sa facilité d’application. Les applications courantes du revêtement en poudre époxy sont nombreuses et variées.
Tout d’abord, le revêtement en poudre époxy est largement utilisé dans l’industrie automobile. Il est appliqué sur les pièces automobiles telles que les châssis, les jantes, les pare-chocs et les pots d’échappement pour les protéger contre la corrosion et les dommages causés par les intempéries. De plus, le revêtement en poudre époxy offre une finition esthétique et peut être personnalisé avec une large gamme de couleurs et de finitions.
Ensuite, le revêtement en poudre époxy est également utilisé dans l’industrie de la construction. Il est appliqué sur les structures métalliques telles que les clôtures, les rampes, les escaliers et les poutres pour les protéger contre la rouille et les dommages causés par l’exposition aux éléments. De plus, le revêtement en poudre époxy offre une excellente résistance aux produits chimiques, ce qui en fait un choix idéal pour les environnements industriels.
Dans le domaine de l’électronique, le revêtement en poudre époxy est utilisé pour protéger les composants électroniques des dommages causés par l’humidité, la poussière et les vibrations. Il est souvent appliqué sur les cartes de circuits imprimés, les boîtiers électroniques et les connecteurs pour assurer leur durabilité et leur fiabilité.
Enfin, le revêtement en poudre époxy est également utilisé dans l’industrie du mobilier et de la décoration. Il est appliqué sur les meubles, les luminaires et les accessoires pour leur donner une finition lisse, résistante aux rayures et facile à entretenir. De plus, le revêtement en poudre époxy offre une large gamme de couleurs et de finitions, ce qui permet de créer des pièces uniques et personnalisées.
En conclusion, le revêtement en poudre époxy est un choix polyvalent et durable pour de nombreuses applications. Que ce soit dans l’automobile, la construction, l’électronique ou le mobilier, ce revêtement offre une protection de haute qualité et une esthétique attrayante. Il est important de choisir le bon type de revêtement en poudre époxy en fonction des exigences spécifiques de chaque application pour assurer des résultats optimaux.
- Revêtement en poudre polyester
Le revêtement en poudre polyester est l’un des types de revêtements en poudre les plus couramment utilisés dans divers secteurs industriels. Ce type de revêtement est fabriqué à partir de résine polyester thermodurcissable mélangée à des pigments et d’autres additifs.
Le revêtement en poudre polyester offre de nombreux avantages, notamment sa résistance exceptionnelle à l’usure, aux rayures et à la corrosion. Il est également durable et offre une excellente adhérence sur une variété de surfaces.
Ce revêtement est largement utilisé dans l’industrie automobile, où il est appliqué sur les pièces extérieures des véhicules pour leur conférer une finition esthétique et une protection contre les intempéries. Il est également utilisé dans l’industrie du mobilier, où il est appliqué sur les meubles en métal pour leur donner une finition durable et attrayante.
De plus, le revêtement en poudre polyester est utilisé dans l’industrie de la construction, où il est appliqué sur les cadres de fenêtres, les portes et autres éléments en métal pour les protéger contre la corrosion et les conditions environnementales extrêmes.
En raison de sa polyvalence et de ses excellentes propriétés, le revêtement en poudre polyester est également utilisé dans d’autres domaines tels que l’électronique, l’équipement sportif et l’industrie des appareils électroménagers.
Que ce soit pour des raisons esthétiques ou de protection, le revêtement en poudre polyester est un choix populaire pour de nombreux secteurs industriels en raison de sa durabilité, de sa résistance aux intempéries et de sa finition attrayante.
- Caractéristiques et propriétés du revêtement en poudre polyester
Le revêtement en poudre polyester est l’un des types les plus courants de revêtements en poudre utilisés dans de nombreux domaines d’application. Il offre une excellente résistance à l’usure, à la corrosion et aux intempéries, ce qui en fait un choix idéal pour les applications extérieures.
Une des caractéristiques principales du revêtement en poudre polyester est sa durabilité. Il est connu pour sa capacité à résister aux rayons UV, à l’humidité, aux produits chimiques et aux impacts. Cela en fait un choix populaire pour les revêtements de mobilier de jardin, de clôtures, de portails et d’autres structures extérieures exposées aux éléments.
En plus de sa résistance, le revêtement en poudre polyester offre également une excellente adhérence. Il peut être appliqué sur une variété de surfaces, y compris le métal, le bois et même le plastique. Cette polyvalence le rend adapté à de nombreuses applications, des pièces automobiles aux appareils électroménagers.
Un autre avantage du revêtement en poudre polyester est sa capacité à offrir une finition lisse et uniforme. Il est disponible dans une large gamme de couleurs et de finitions, ce qui permet aux fabricants et aux designers de choisir la combinaison parfaite pour leurs produits.
Lorsqu’il s’agit de l’application du revêtement en poudre polyester, il est généralement pulvérisé électrostatiquement sur la surface à revêtir, puis chauffé pour fusionner et durcir la poudre, créant ainsi une couche solide et résistante.
En résumé, le revêtement en poudre polyester est un choix populaire en raison de sa durabilité, de sa résistance aux intempéries et de sa finition esthétique. Que vous ayez besoin de revêtir des meubles de jardin, des pièces automobiles ou des structures extérieures, ce type de revêtement offre de nombreuses caractéristiques et propriétés qui le rendent adapté à divers domaines d’application.
- Domaines d’application du revêtement en poudre polyester
Le revêtement en poudre polyester est l’un des types les plus populaires de revêtements en poudre utilisés dans divers domaines d’application. Sa polyvalence lui permet d’être utilisé dans une large gamme d’industries.
Tout d’abord, le revêtement en poudre polyester est couramment utilisé dans l’industrie automobile. Il offre une excellente résistance aux rayures, aux intempéries et aux produits chimiques, ce qui en fait un choix idéal pour les pièces de carrosserie et les accessoires automobiles. De plus, il peut être appliqué sur une variété de substrats tels que l’acier, l’aluminium et le plastique, offrant ainsi une flexibilité supplémentaire dans la conception et la fabrication des pièces automobiles.
En outre, ce type de revêtement en poudre est également utilisé dans l’industrie du mobilier. Sa durabilité et sa résistance à l’usure en font un choix populaire pour les meubles d’extérieur, les chaises de bureau et les armoires. De plus, le revêtement en poudre polyester peut être formulé pour offrir une large gamme de finitions, allant du mat au brillant, ce qui permet de créer des pièces de mobilier attrayantes et durables.
Dans le secteur de l’électronique, le revêtement en poudre polyester est utilisé pour protéger les composants électroniques des facteurs environnementaux tels que l’humidité, la corrosion et les chocs thermiques. Il offre également une isolation électrique, ce qui en fait un choix sûr et fiable pour les applications électroniques sensibles.
Enfin, le revêtement en poudre polyester est utilisé dans l’industrie architecturale pour les applications extérieures et intérieures. Il peut être appliqué sur des structures en acier, en aluminium et en verre pour offrir une protection contre les éléments, tout en offrant une finition esthétiquement agréable. Que ce soit pour les façades de bâtiments, les clôtures, les portes ou les fenêtres, le revêtement en poudre polyester offre une durabilité à long terme et une résistance aux intempéries, ce qui en fait un choix populaire pour les projets architecturaux.
En conclusion, le revêtement en poudre polyester est un choix polyvalent et durable pour de nombreux domaines d’application. Que ce soit dans l’industrie automobile, le mobilier, l’électronique ou l’architecture, ce type de revêtement offre une protection et une esthétique de qualité supérieure.
- Revêtement en poudre polyuréthane
Le revêtement en poudre polyuréthane est l’un des types les plus populaires de revêtements en poudre utilisés dans divers domaines d’application. Ce type de revêtement offre une excellente résistance aux intempéries, à la corrosion, aux rayures et aux UV, ce qui en fait un choix idéal pour les applications extérieures.
Le revêtement en poudre polyuréthane est également connu pour sa durabilité et sa flexibilité. Il peut être appliqué sur une variété de substrats tels que le métal, le bois, le plastique et même la céramique. Cette polyvalence en fait un choix polyvalent pour de nombreux secteurs industriels, y compris l’automobile, l’ameublement, l’électronique et bien d’autres.
En raison de sa résistance exceptionnelle aux intempéries, le revêtement en poudre polyuréthane est souvent utilisé pour les applications extérieures telles que les pièces de voiture, les équipements de jardin, les clôtures, les luminaires extérieurs, les meubles de patio, etc. Son adhérence et sa résistance à la décoloration en font également un choix populaire pour les applications architecturales, telles que les revêtements de façade, les revêtements de balcon et les panneaux solaires.
En plus de ses propriétés physiques, le revêtement en poudre polyuréthane offre également une large gamme de couleurs et de finitions. Il peut être formulé pour avoir un aspect lisse, texturé, mat, brillant ou métallisé, ce qui permet une personnalisation créative des produits finis.
En résumé, le revêtement en poudre polyuréthane est un choix populaire pour de nombreuses applications en raison de sa résistance aux intempéries, de sa durabilité, de sa polyvalence et de sa palette de couleurs étendue. Que vous ayez besoin de protéger des pièces automobiles, de créer des meubles extérieurs ou de donner une finition esthétique à des éléments architecturaux, le revêtement en poudre polyuréthane peut répondre à vos besoins de revêtement de manière efficace et esthétique.
- Caractéristiques et propriétés du revêtement en poudre polyuréthane
Le revêtement en poudre polyuréthane est l’un des types les plus populaires de revêtements en poudre utilisés dans divers domaines d’application. Il offre une combinaison unique de caractéristiques et de propriétés qui le distinguent des autres types de revêtements en poudre.
Tout d’abord, le revêtement en poudre polyuréthane se caractérise par sa durabilité exceptionnelle. Il est résistant aux chocs, aux rayures et à l’abrasion, ce qui en fait un choix idéal pour les surfaces soumises à une utilisation intensive ou à des conditions difficiles. De plus, il offre une excellente résistance aux intempéries, aux UV et aux produits chimiques, ce qui le rend adapté à une large gamme d’environnements.
En termes de finition, le revêtement en poudre polyuréthane offre une surface lisse et uniforme, avec une excellente adhérence aux substrats. Il est également disponible dans une large gamme de couleurs et de finitions, ce qui permet de créer des designs attrayants et personnalisés.
Un autre avantage majeur du revêtement en poudre polyuréthane est sa facilité d’application. Il peut être pulvérisé électrostatiquement sur les substrats, puis durci à une température élevée pour former une couche solide et résistante. Cette méthode d’application permet d’obtenir une couverture uniforme, sans coulures ni bulles, garantissant ainsi un résultat esthétiquement plaisant.
En ce qui concerne les domaines d’application, le revêtement en poudre polyuréthane est largement utilisé dans l’industrie automobile, l’ameublement, l’architecture, l’électroménager et de nombreux autres secteurs. Il peut être utilisé pour protéger et décorer une variété de surfaces, telles que les métaux, le bois, le plastique et même le verre.
En résumé, le revêtement en poudre polyuréthane offre une combinaison unique de durabilité, de finition esthétique et d’applicabilité dans de nombreux domaines. Que ce soit pour une utilisation commerciale ou résidentielle, ce type de revêtement constitue un choix fiable et polyvalent qui répondra à vos besoins en matière de protection et de décoration.
- Utilisations typiques du revêtement en poudre polyuréthane
Le revêtement en poudre polyuréthane est un choix populaire dans de nombreux domaines d’application en raison de ses excellentes propriétés et de sa durabilité. Voici quelques utilisations typiques du revêtement en poudre polyuréthane :
- Industries automobiles : Le revêtement en poudre polyuréthane est souvent utilisé dans l’industrie automobile pour protéger les pièces contre la corrosion, les rayures et les impacts. Il peut être appliqué sur des composants tels que les pare-chocs, les jantes, les cadres de voiture et les pièces de moteur, assurant ainsi une finition résistante et esthétiquement agréable.
- Mobilier d’extérieur : Grâce à sa résistance aux intempéries et aux rayons UV, le revêtement en poudre polyuréthane est un choix idéal pour les meubles d’extérieur tels que les chaises de jardin, les tables et les balançoires. Il offre une protection durable contre les éléments tout en maintenant un aspect attrayant.
- Équipements électriques : Les équipements électriques nécessitent souvent une protection supplémentaire contre les chocs, les rayures et les produits chimiques. Le revêtement en poudre polyuréthane offre une excellente adhérence et une résistance aux produits chimiques, ce qui en fait un choix courant pour les boîtiers de composants électroniques, les panneaux de contrôle et les armoires électriques.
- Applications architecturales : Le revêtement en poudre polyuréthane est également utilisé dans les applications architecturales, telles que les façades de bâtiments, les structures métalliques, les clôtures et les portails. Sa résistance aux intempéries, aux UV et aux rayures en font un choix durable et esthétiquement plaisant pour les projets de construction.
Quelle que soit l’application, le revêtement en poudre polyuréthane offre une protection supérieure et une finition de haute qualité, ce qui en fait un choix privilégié dans de nombreux secteurs industriels et commerciaux.
- Revêtement en poudre thermodurcissable
Le revêtement en poudre thermodurcissable est l’un des quatre types de revêtements en poudre les plus couramment utilisés. Ce type de revêtement est formulé à partir de résines thermodurcissables, telles que les époxydes, les polyesters et les polyuréthanes.
Le revêtement en poudre thermodurcissable offre une excellente adhérence et une résistance supérieure à l’abrasion, aux produits chimiques et aux intempéries. Il est également connu pour sa durabilité exceptionnelle, sa stabilité dimensionnelle et sa résistance à la chaleur.
Ce type de revêtement en poudre est largement utilisé dans divers domaines d’application, tels que l’automobile, l’aérospatiale, l’électronique, le mobilier, l’architecture et bien d’autres encore. Il est idéal pour les surfaces métalliques, offrant une finition lisse et uniforme qui peut améliorer l’esthétique des produits.
Le revêtement en poudre thermodurcissable est appliqué en utilisant un procédé de pulvérisation électrostatique. La poudre est chargée électrostatiquement et adhère aux surfaces métalliques préalablement préparées. Ensuite, les pièces revêtues sont chauffées dans un four, ce qui provoque la fusion et la réticulation des résines, donnant ainsi une finition durable et résistante.
Que vous ayez besoin de protéger des pièces automobiles de la corrosion, de donner un aspect attrayant à des meubles en métal ou de fournir une protection durable aux équipements électroniques, le revêtement en poudre thermodurcissable est un choix polyvalent et fiable. Sa capacité à résister aux conditions environnementales difficiles en fait un choix populaire pour de nombreuses industries.
- Qu’est-ce qu’un revêtement en poudre thermodurcissable?
Un revêtement en poudre thermodurcissable est un type de revêtement qui est appliqué sur une surface sous forme de poudre et qui durcit lorsqu’il est exposé à une température élevée. Ce processus de durcissement est appelé réticulation. Les revêtements en poudre thermodurcissables sont largement utilisés dans divers domaines d’application en raison de leurs propriétés uniques.
L’une des principales caractéristiques des revêtements en poudre thermodurcissables est leur excellente résistance à l’abrasion, aux rayures et aux chocs. Cela les rend idéaux pour une utilisation dans des environnements difficiles où la surface est sujette à des contraintes mécaniques.
De plus, les revêtements en poudre thermodurcissables offrent une excellente résistance aux produits chimiques, à la corrosion et aux intempéries. Cela les rend adaptés à une utilisation en extérieur, dans des environnements corrosifs ou exposés aux intempéries.
Les revêtements en poudre thermodurcissables offrent également une grande variété de finitions, allant du mat au brillant, en passant par les textures et les effets spéciaux. Cela permet aux fabricants de choisir le type de finition qui correspond le mieux à leurs besoins esthétiques.
En termes d’applications, les revêtements en poudre thermodurcissables sont largement utilisés dans l’industrie automobile, l’industrie du mobilier, l’industrie des équipements électriques et électroniques, ainsi que dans la construction et l’architecture.
En conclusion, les revêtements en poudre thermodurcissables offrent une combinaison unique de propriétés mécaniques, chimiques et esthétiques, ce qui en fait un choix populaire dans de nombreux domaines d’application. Leur capacité à résister à l’usure, à la corrosion et aux intempéries en fait un choix durable et fiable pour protéger les surfaces et améliorer l’apparence des produits finis.
- Applications spécifiques du revêtement en poudre thermodurcissable
Le revêtement en poudre thermodurcissable est un choix populaire pour de nombreuses applications spécifiques en raison de ses propriétés uniques et de sa durabilité. Ce type de revêtement est appliqué sous forme de poudre qui est ensuite chauffée pour fondre et adhérer à la surface du matériau. Une fois refroidi, le revêtement forme une couche solide et résistante qui offre une protection contre la corrosion, les rayures et autres dommages.
Les applications spécifiques du revêtement en poudre thermodurcissable sont vastes et variées. Voici quelques exemples courants :
- Industrie automobile : Les pièces automobiles, telles que les jantes, les pare-chocs et les grilles de radiateur, sont souvent revêtues de poudre thermodurcissable pour une protection accrue contre les éléments et une meilleure esthétique.
- Mobilier d’extérieur : Les meubles de jardin, les clôtures et les balustrades en métal sont souvent revêtus de poudre thermodurcissable pour résister aux intempéries et à l’usure.
- Équipement électrique : Les boîtiers électriques, les armoires de commande et les panneaux de contrôle sont souvent revêtus de poudre thermodurcissable pour une isolation électrique et une protection contre la corrosion.
- Équipement industriel : Les machines, les équipements de manutention et les structures métalliques utilisés dans les environnements industriels sont revêtus de poudre thermodurcissable pour une protection contre la corrosion, les produits chimiques et l’usure.
En choisissant le revêtement en poudre thermodurcissable pour ces applications spécifiques, vous pouvez vous assurer que vos matériaux restent protégés et esthétiquement agréables pendant de nombreuses années. Son adhérence solide et sa résistance aux dommages en font un choix fiable et durable pour de nombreux secteurs industriels.
- Comparaison des quatre types de revêtement en poudre
Il existe quatre types couramment utilisés de revêtement en poudre, chacun avec ses propres caractéristiques et domaines d’application spécifiques. Comprendre ces différences vous aidera à choisir le revêtement en poudre le mieux adapté à vos besoins.
- Revêtement en poudre époxy : Ce type de revêtement en poudre est connu pour sa durabilité et sa résistance aux produits chimiques. Il est souvent utilisé pour les applications industrielles nécessitant une protection contre la corrosion, telles que les pièces automobiles, les équipements électriques et les structures métalliques exposées aux intempéries.
- Revêtement en poudre polyester : Le revêtement en poudre polyester est apprécié pour sa résistance aux UV et sa stabilité des couleurs. Il est souvent utilisé dans l’industrie du mobilier de jardin, les systèmes de clôture extérieurs et les appareils électroménagers où la durabilité et l’esthétique sont des priorités.
- Revêtement en poudre polyuréthane : Ce type de revêtement en poudre offre une excellente résistance aux rayures et une adhérence supérieure. Il est couramment utilisé dans l’industrie automobile pour les jantes et les pièces soumises à des conditions de frottement élevé, ainsi que dans la fabrication de meubles haut de gamme.
- Revêtement en poudre thermoplastique : Les revêtements en poudre thermoplastiques sont connus pour leur capacité à être fondus et remodelés à plusieurs reprises sans perdre leurs propriétés. Ils sont principalement utilisés dans l’industrie électrique pour l’isolation des fils et des câbles, ainsi que dans les applications nécessitant une résistance élevée aux températures élevées.
En comprenant les caractéristiques spécifiques de chaque type de revêtement en poudre, vous pourrez choisir celui qui convient le mieux à votre projet. Que vous ayez besoin d’une protection contre la corrosion, d’une résistance aux UV, d’une durabilité accrue ou d’une résistance aux températures élevées, il existe un revêtement en poudre adapté à vos besoins.
- Différences en termes de résistance, d’aspect et de coût
Lorsque vous choisissez un revêtement en poudre, il est essentiel de comprendre les différences en termes de résistance, d’aspect et de coût. Chacun des quatre types de revêtement en poudre a ses propres caractéristiques uniques qui les rendent adaptés à différents domaines d’application.
- Revêtement en poudre époxy :
Le revêtement en poudre époxy est reconnu pour sa résistance exceptionnelle à la corrosion et aux produits chimiques. Il offre également une excellente adhérence et une protection efficace contre l’abrasion. En termes d’aspect, le revêtement en poudre époxy peut être lisse ou texturé, offrant ainsi une variété d’options de finition. Cependant, il est important de noter que les revêtements en poudre époxy peuvent jaunir avec le temps, en particulier lorsqu’ils sont exposés à la lumière UV. En ce qui concerne le coût, le revêtement en poudre époxy est généralement plus abordable que d’autres options. - Revêtement en poudre polyester :
Le revêtement en poudre polyester est apprécié pour sa durabilité et sa résistance aux intempéries, ce qui en fait un choix populaire pour les applications extérieures. Il offre également une grande variété de couleurs et une excellente rétention de la couleur, même lorsqu’il est exposé à la lumière du soleil. En termes d’aspect, le revêtement en poudre polyester peut être lisse ou texturé, offrant ainsi une flexibilité de design. Cependant, il peut être moins résistant aux produits chimiques que le revêtement en poudre époxy. En ce qui concerne le coût, il est généralement similaire à celui du revêtement en poudre époxy. - Revêtement en poudre polyuréthane :
Le revêtement en poudre polyuréthane offre une résistance accrue aux rayures et à l’abrasion par rapport aux revêtements en poudre époxy et polyester. Il est également connu pour sa résistance aux UV, ce qui le rend adapté aux applications extérieures. En termes d’aspect, le revêtement en poudre polyuréthane peut être lisse ou texturé, offrant ainsi une variété de finitions esthétiques. Cependant, il convient de noter que le revêtement en poudre polyuréthane peut être plus coûteux que les autres options en raison de ses performances supérieures. - Revêtement en poudre thermoplastique :
Le revêtement en poudre thermoplastique offre une excellente résistance chimique et une grande flexibilité en termes de température d’application. Il peut être facilement réappliqué ou réparé en cas de besoin, ce qui en fait un choix pratique pour certaines applications. En termes d’aspect, le revê
- Comment choisir le bon revêtement en poudre pour votre projet
Lorsque vous envisagez d’utiliser un revêtement en poudre pour votre projet, il est essentiel de choisir le bon type de revêtement pour obtenir les résultats souhaités. Il existe quatre types principaux de revêtement en poudre, chacun ayant ses propres caractéristiques et domaines d’application spécifiques.
- Revêtement en poudre époxy : Ce type de revêtement en poudre offre une excellente adhérence et une grande résistance à la corrosion. Il est couramment utilisé dans les applications industrielles, telles que les équipements lourds, les conduites d’eau et les structures métalliques exposées à des environnements agressifs.
- Revêtement en poudre polyester : Ce revêtement en poudre est connu pour sa résistance aux UV, aux intempéries et aux produits chimiques. Il est souvent utilisé pour les applications extérieures, telles que les clôtures, les meubles de jardin et les équipements de jeu pour enfants.
- Revêtement en poudre polyuréthane : Ce type de revêtement en poudre offre une excellente résistance aux rayures, aux taches et aux produits chimiques. Il est couramment utilisé dans les applications commerciales et résidentielles, telles que les meubles, les comptoirs de cuisine et les équipements sportifs.
- Revêtement en poudre thermoplastique : Ce revêtement en poudre est réversible, ce qui signifie qu’il peut être fondu et reformé plusieurs fois. Il est souvent utilisé dans les applications nécessitant une résistance élevée aux impacts, comme les pare-chocs de voiture, les pièces automobiles et les équipements électriques.
Lorsque vous choisissez le bon revêtement en poudre pour votre projet, tenez compte de facteurs tels que l’environnement dans lequel il sera utilisé, les propriétés spécifiques dont vous avez besoin (résistance à la corrosion, résistance aux intempéries, etc.) et les exigences esthétiques. N’hésitez pas à consulter un professionnel du revêtement en poudre pour obtenir des conseils personnalisés et vous assurer d’obtenir les meilleurs résultats pour votre projet.
- Conclusion et conseils pour un revêtement en poudre réussi
En conclusion, il est essentiel de comprendre les différents types de revêtement en poudre disponibles sur le marché et leurs domaines d’application spécifiques. Choisir le bon revêtement en poudre pour votre projet peut faire toute la différence en termes de durabilité, d’esthétique et de performance.
Voici quelques conseils pour réussir votre revêtement en poudre :
- Faites des recherches approfondies : Avant de choisir un revêtement en poudre, renseignez-vous sur les caractéristiques spécifiques de chaque type de revêtement et déterminez celui qui convient le mieux à votre application.
- Préparez correctement la surface : Une préparation adéquate de la surface est essentielle pour assurer une adhérence maximale du revêtement en poudre. Assurez-vous de nettoyer, dégraisser et dérocher correctement la surface avant l’application.
- Utilisez un équipement de pulvérisation de haute qualité : Investir dans un équipement de pulvérisation de qualité vous permettra d’obtenir un résultat plus uniforme et professionnel. Assurez-vous de choisir un pistolet de pulvérisation adapté au type de revêtement en poudre que vous utilisez.
- Respectez les instructions du fabricant : Chaque revêtement en poudre aura des instructions spécifiques fournies par le fabricant. Il est crucial de les suivre attentivement pour garantir une application correcte et un résultat final de haute qualité.
En suivant ces conseils, vous serez en mesure de réaliser un revêtement en poudre réussi, qu’il s’agisse de protéger des surfaces métalliques, d’améliorer l’esthétique des produits ou d’assurer une durabilité à long terme. N’hésitez pas à consulter un professionnel du revêtement en poudre pour obtenir des conseils spécifiques à votre projet et profiter au maximum des avantages de cette technique de revêtement polyvalente et durable.
Nous espérons que vous avez apprécié notre article sur les quatre types de revêtements en poudre et leurs domaines d’application. Il est essentiel de comprendre les différents types de revêtements en poudre disponibles sur le marché et de savoir comment les utiliser correctement dans différents domaines. Que vous soyez un professionnel dans le secteur industriel ou simplement à la recherche d’informations pour votre projet personnel, nous espérons que nos conseils vous ont été utiles. N’hésitez pas à partager vos expériences et à nous poser vos questions. Bonne application de revêtements en poudre et à bientôt !
L’équipement de revêtement en poudre est utilisé pour appliquer une fine couche de poudre sur une surface métallique. Ce type de revêtement est appliqué par un procédé électrostatique et constitue une méthode très populaire pour la finition des pièces métalliques.
Ce type d’équipement peut être divisé en deux grandes catégories : automatiques et manuels. Les cabines automatiques sont plus populaires car elles offrent de meilleurs taux de production, mais elles sont également plus chères.
Une cabine à poudre est une enceinte dans laquelle se déroule le processus de revêtement en poudre. L’équipement de revêtement en poudre comprend un four dans lequel les pièces sont chauffées pour activer la poudre, un pistolet qui pulvérise ou brosse la poudre, une bande transporteuse qui déplace les pièces à travers le four et des pistolets de type cartouche pour appliquer des revêtements plus épais avec moins de pulvérisation.
Le revêtement en poudre est une technique utilisée pour donner une finition aux pièces métalliques. Cette technique est utilisée depuis de nombreuses années et reste aujourd’hui l’une des techniques les plus populaires.
L’équipement de revêtement en poudre comprend des cabines, des fours, des pistolets, des machines, des lignes et des convoyeurs. Une cabine peut être automatique ou manuelle. Une cabine automatique est plus chère qu’une cabine manuelle mais elle est aussi plus rapide et plus efficace.